BIG RIVER GROUP SMALL START, HUGE FUTURE
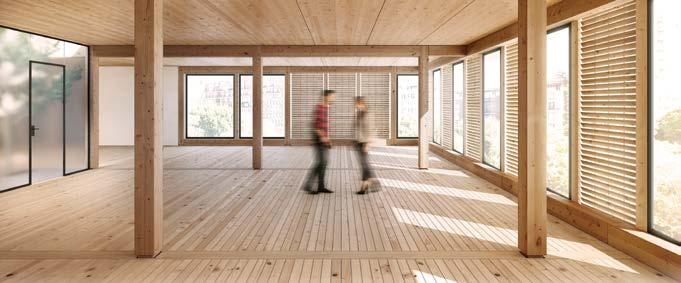
HYNE TIMBER'S CLASSIC LGL IS BACK
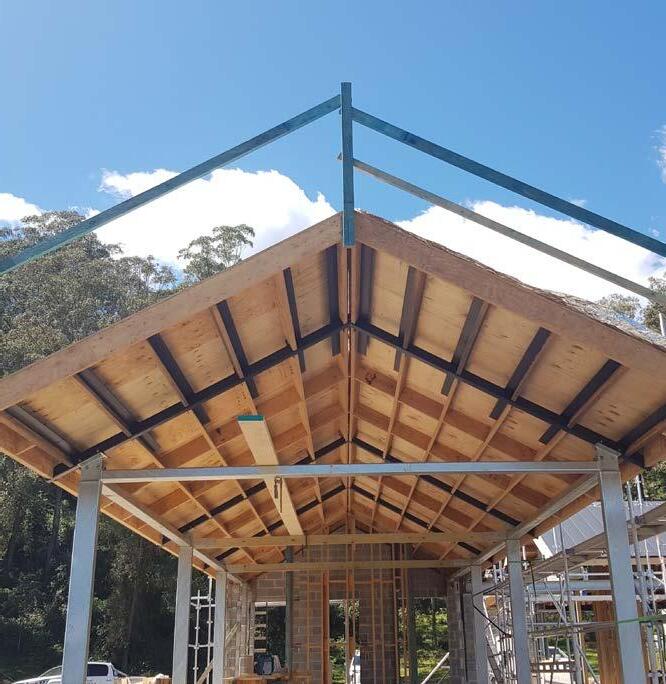

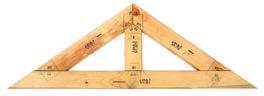
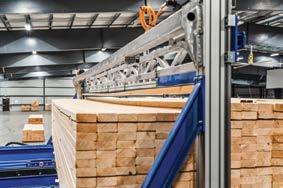

HYNE TIMBER'S CLASSIC LGL IS BACK
HYNE Timber is bringing back its proprietary-grade LGL to Queensland and New South Wales markets and Brisbane builder James Briskie couldn’t be happier.
Having had restricted availability in recent years, Hyne Timber has made the move to transition its LGL production to the state-of-the-art automated Glue Laminated Timber facility in Maryborough, Queensland.
“I’m stoked to be able to get my hands on more LGL,” Mr Briskie, of Briskie Construction Group, said.
“As a builder, having access to quality Australian made products has only become more important in recent years with imported products being so unreliable,” he said.
“The Aussie manufacturers make products that suit our harsh conditions. LGL has always performed well on my jobs. Not only that, but I also know I’m supporting local jobs.”
Hyne Timber’s GLT facility features a fully automatic rotary press with four separate press beds. The press can produce approximately four layers, each comprising multiple beam layups, every hour.
By leveraging advanced automation technology, Hyne is poised for a 30% increase in its LGL production capability, which is welcome news for the building industry.
LGL is versatile and durable, making it well-suited for a wide range of construction applications; particularly those that require long spans and a high load-bearing ca-
pacity. Its resistance to corrosion, nail-holding strength, and workability on site make it a solid wood alternative to LVL and steel that offers greater flexibility in the construction process.
“With our new GLT factory now running like a well-oiled machine, we can produce large quantities of the classic Hyne LGL,” says Stefan Gerber, Engineering and Sales Manager GLT at Hyne Timber.
“This Hyne proprietary GLT product has been widely accepted in the market for over a decade, but output volumes have been constrained due to manufacturing capacity limitations. These limitations are now lifted, so we can start supplying the broader market again, starting in Queensland and New South Wales.”
Mr Briskie said that LGL has some great properties that make it ideal to work with.
“It’s straightness, strengthto-weight ratio, and versatility for starters,” he said.
“It is also H3 treated so is durable enough for outdoor applications. Sometimes it’s the little things that make the world of difference. Like something as simple as being able to drive a nail into it – you don’t always get that with other products.”
Hyne’s LGL is produced from premium quality, sustainably grown Australian plantation pine, making it good for the planet. It is treated to Hazard Level 3 (H3) as standard, making it suitable for harsh conditions, and comes with a 25-year guarantee against structural damage caused by termites, insect borers, or fungal decay.
“I’ve used Hyne Timber’s Glue Laminated Timber for years now; in new builds, renos and even my own place. It’s lightweight, perfect for long spans and is environmentally friendly…. which is important to me and my clients,” Mr Briskie said.
In fact, because each laminate is treated to the core, LGL is ideal for internal and external (above ground) applications in humid or wet areas, as well as exposed coastal and corrosive settings. Think, lintels, bearers, joists, sub-floors, rafters, and roof beams.
As one of Australian’s largest producers of GLT products, Hyne goes above and beyond to ensure it is producing only the best quality products.
They submit their GLT to comprehensive in-house
and third-party tests to ensure consistency in performance and compliance. They have even gone as far as obtaining ‘S’ Mark certification for their LGL product, the leading assurance of GLT product performance and safety in Australasia.
“I have peace of mind when using Hyne’s GLT products, because I know they have been third-party certified and that my clients are covered against structural termite attacks with their 25year guarantee,” Mr Briskie said.
With a large volume of construction projects still in the pipeline, Hyne Timber is committed to adapting to meeting the demands of their customers through innovation and increased efficiencies, while maintaining their high standards.
TABMA Australia and Hardware Australia members have approved a merger of the two organisations.
The new body to represent the hardware and timber industries will be called the National Timber and Hardware Association (NTHA) from April 3.
Paul Stewart, formerly Hardware Australia chairman, and Peter Hutchinson, formerly Timber and Building Materials Association chairman will co-chair the new organisation.
“Both Boards are thrilled with the vote and appreciate the support of members from both Associations,” Mr Stewart said.
“This merger signifies a new chapter for the timber and hardware industries as we come together to form a stronger and united national organisation.”
The organisation will now have over 700 members located across Australia providing a truly national presence. This will provide greater opportunities to advocate for the industries with key stakeholders, in particular government.
“This merge provides new opportunities for members of both Associations as we look to build a strong future that unites both of our industries,” Mr Hutchinson said.
underpin everything we do.
Issue 2 – Volume 33
Incorporating Australian and New Zealand Timberman.
FRONT Cover:
Front cover: From one sawmill in Northern NSW which began operations in 1894, Big River Group has grown to become a national entity manufacturing a range of construction products. Story Page 6
PUBLISHER and Chief Executive:
Hartley Higgins
General Manager:
Robyn Haworth
Editor:
Bruce Mitchell
b.mitchell@ryanmediapl.com.au
Adelaide Office (08) 8369 9512
Advertising:
Adelaide Office (08) 8369 9517
Creative Services:
Tim Coleman
Publication Design:
Tim Coleman
Timber classifieds:
Adelaide Office (08) 8369 9517
Subscriptions:
subs@forestsandtimber.com.au
Adelaide Office (08) 8369 9522
Subcription rates
One-year (8 editions) $55
Two-years (16 editions) $95
Accounts: (03) 5723 0100
Postal Address: 630 Regency Road, Broadview South Australia 5083 Phone: (08) 8369 9555
Fax: (08) 8369 9501
Melbourne Office: Suite 2262, 442 Auburn Rd, Hawthorn VIC 3122 Phone: (03) 9810 3262
Find us on Facebook @AustralasianTimber
Website www.timberbiz.com.au
LABOUR shortages are still a real challenge for local businesses with a Wangaratta manufacturing company turning to machines to fill the void.
Alpine Truss in Wangaratta invested more than $2.7 million to extend its business footprint and purchase machinery that will effectively replace unavailable human resources.
While Victoria’s unemployment rate sits at a 50-year historically low 3.5 per cent, it doesn’t mean there aren’t any jobs out there for people locally.
Company managing director George Prothero said the building industry is facing a \”massive downturn\” in the
next six months but he still has jobs available for people right for the job.
“The housing market is definitely slowing so the need for more employees is not as critical as it was; however we still have scope to employ 12-15 people if they are suitable for the work.
“The business has found that numerous people, who have submitted their resumes, come in, try out and they don’t want to work.”
In light of not being able to attract a suitable workforce the business secured a building permit for a major $700,000 extension which will house state of the art equipment worth more than $2m.
been unable to address a staffing shortage.
He said the skeleton of the building is erected and the aim is for machines to be fully operational in the next few weeks.
“The equipment does the sawing and stacking of timber so it takes out a lot of the manual labour in areas we were struggling to find people to do,” he said.
“We have to continue doing that in other areas of the operation as well.”
The downturn is coming for the building industry with the lofty heights propped up by the HomeBuilders grants in 2020-21 long over, and Mr Prothero said the worst in the last 10 years is forecast off the back of inflation and rising interest rates.
The Reserve Bank’s cash rate is expected to peak at 4.1 per cent in the next few months and stay there for 18 months, thwarting the dreams of many people looking to buy their first home, or at least the home they aspired to buy.
Mr Prothero gave some solid advice to those looking to break-in to the market.
“First home buyers have to start looking at something more affordable instead of these 24-square homes with living rooms, swimming pools and ensuites - they are just not affordable,” he said.
“They have to go back to the old school 14-square three bedroom homes.”
- WANGARATTA CHRONICLEIN November 2021 former Australian Forest Products Association CEO Ross Hampton wrote that the then latest five yearly review by ABARES of Australia’s national plantation estate is more than sobering reading.
It was, Mr Hampton said, like the script of a horror film.
“The bureaucratic speak in the report notes unemotionally that Australia’s softwood plantation estate (the pine trees that we use to make our timber house frames) remains ‘stable’,” he wrote.
“ ‘Stable’, in this context, means stagnant, as it has been for more than a decade, which means it is failing to keep up with current and future housing demand. This line should be written in bold with lots of exclamation marks,” he wrote.
“And yet how do we square this picture with the fact that there is massive demand for
timber products? Our plantation estate provides the affordable timber for our homes. If you are building or renovating, you will know that timber and timber products are in huge demand. AFPA and Master Builders Australia recently calculated we will be 250,000 new house frames short by 2035. Just what do we think our children are going to do?”
He wrote that AFPA modelling suggested that another 400,000 hectares of plantations needed to be planted in this country.
Australia’s builders are struggling to find timber. For items such as laminated veneer lumber – used for frames and beams – they’ve reported waiting up to four months. For trusses – used to build walls and roofs – up to nine months.
Sadly, given what Mr Hampton wrote some 14 months ago was correct it is a horror movie.
THE number of detached houses commencing construction is set to decline this year and next to its lowest level since 2012.
HIA released its economic and industry Outlook Report yesterday and the report includes updated forecasts for new home building and renovations activity nationally and for each of the eight states and territories.
“The 2022 cash rate increases were sufficient to bring this building boom to an end and further increases in 2023 will accelerate this downturn,” HIA Chief Economist Tim Reardon said.
“There was a large volume of work in the pipeline when rates started to rise in May 2022, and there remains a record number of homes under construction, but this will shrink quickly as market confidence continues to fade.
“Lending for the purchase or construction of a new home had already fallen to its lowest level since 2012 by the end
of 2022, and the full impact of last year’s rate increases is still to flow through to households,” he said.
Mr Reardon said that this would see the number of detached housing starts fall below 100,000 starts per year for the first time in a decade to just 96,300 in 2024. This was a very rapid slowdown from the 149,000 starts in 2021.
“Multi-unit starts were impaired last year by the acute shortage of labour and materials which has seen many projects postponed until 2023. Unlike detached home construction, the number of
multi-units commencing construction should increase as the acute shortage of housing, returning migrants and students, and affordability constraints continue to drive demand for housing,” Mr Reardon said.
It was unfortunate that the RBA appeared set to repeat the cycle the building industry experienced after the GFC.
“Following an initial cut to rates, the RBA then increased rates quickly, bringing the
building industry to a stall, before being forced to cut rates again to avoid adverse impacts on the wider economy,” Mr Reardon said.
“It is also unfortunate that higher rates will further impair the ability of the market to respond to the acute shortage of housing stock.
“One policy tool at the disposal of government is to ease the barriers put in place in recent years that restrict first home buyer access to a mort-
gage. Over a decade of macro prudential restrictions have seen borrowing for those with less than a 20 per cent deposit become increasingly expensive. This inevitably leads to banks increasingly lending to those that already own a home.
“Easing the barriers to home ownership need not undermine the efforts of the RBA or the government to reduce inflationary pressures,” he said.
The $63 million upgrade of Timberlink’s Bell Bay manufacturing facility is in the final stages of planning and will be underway and expected to be commissioned by the end of 2026.
This will result in an increase of more than fifty percent in on-island sovereign timber manufactured from sustainably managed pine plantations.
Developments at the Timberlink facility include construction of Australia’s only finger-jointed and primed outdoor timber products line, which has been partially supported by a $1,063,304 grant from the Tasmanian Government’s Department of State Growth On-Island Processing Program.
The On-Island Processing Program aims to obtain greater value from Tasmania’s forest resources, including forest residues, reduce the risk from exposure to volatility in international commodity markets for woodchips and logs, reduce the need for imported forest-based products and create jobs in regional areas. The finger-jointing line is expected to be completed in late 2023.
“This new finger-jointed and primed outdoor timber products line will be the only one of its kind in Australia, and Timberlink is excited to be able to offer a locally produced product for the Australian market and reduce the need for imported timber,” Timberlink’s EGM Sales Marketing & Corporate Affairs, David Oliver, said.
“This project significantly enhances Australia’s Sovereign capability to manufacture decking and screening products from upcycled materials,” Mr Oliver said.
The wood-plastic composites plant will create new jobs and flow-on benefits for the economy. The energy to power the plant will be sourced from Tasmanian hydro power and a solar farm located on the roof of the new facility.
Rainwater tanks will be installed to harvest rainwater which will be used for cooling in the manufacturing process.
THE Big River Group had very humble beginnings.
From one sawmill in Northern NSW which began operations in 1894, the company has grown to become a national entity manufacturing a range of construction products including timber flooring, plywood and decorative panels, as well as distributing a broad range of other building products from well-known local and international suppliers, focussing primarily on the commercial and residential, civil and infrastructure construction trade market segments.
Big River now owns and manages 26 sites across Australia and New Zealand expanding Panels, Building Trade Centres and Formwork & Commercial divisions.
It was in 1928 that founder Thomas Pidcock constructed the first sawmill in NSW using hydroelectric power to mill hoop pine and eucalyptus, a revolutionary move that enabled the company to expand.
A decade later Thos. Pidcock and Sons Pty Ltd was formed, with factories opened in Grafton and Coffs Harbour, the company was then carried on by Pidcock’s four sons after his death in 1948.
It was the Grafton location, and the Clarence River which flows through it, that give the business its name.
In 1960 the family sold its considerable sawmilling operations and constructed a modern rotary veneer factory in Grafton.
In 1983 the company again moved, this time from veneer to plywood production, pioneering the use of regrowth and plantation eucalypt to make F27 hardwood Formply. To this day, all timber processed by the company is sourced from sustainably managed plantation and regrowth forests, which have Australian Forestry Standard Certification.
By 1992 sales and distribution centres were established across Brisbane, Melbourne and Sydney, Perth in 2000 and then Townsville in 2003. In 2006 the company acquired a centre in the Sunshine Coast
as well as its second manufacturing facility in Wagga Wagga.
In early 2016, private equity firm Anacacia Capital acquired a controlling interest in the Big River business.
CEO John Lorente joined Big River Industries in early 2018.
“Half of what we sell, we procure from local suppliers, all the big timber suppliers in Australia,” Mr Lorente said.
“And then about a quarter of it we manufacture through Grafton or through some of our panel sites or frame and truss sites.
“And then about a quarter of what we sell we import, but most of that is panel products. Things like foam ply and plywood and pine panel products from Europe.”
Mr Lorente said Big River’s diversified supply chain had really helped the company out during the Covid pandemic.
“Because we’re across the entire country, we were able
to move stuff around where we needed to,” he said.
But he concedes it was a difficult period.
“I think it’s better. Is our supply chain is running smoothly? I’d say not yet.
“I’d say we are eighty percent through it all.”
A milestone year in 2017 saw Big River Group successfully listed on the ASX, with four business acquisitions.
Over the past four years, Big River Group has experienced accelerated growth.
Acquisitions of several businesses has grown the group to a total of 23 sites across Australia and New Zealand expanding Panels, Building Trade Centres and Formwork & Commercial divisions.
“We told the market would do two to four acquisitions a year as our target,” Mr Lorente said.
“And we’re still very much on that track.”
CUSP plantation hardwood has achieved yet another first, attaining a 120-minute plus fire resistance test with no failures.
Cusp Eucalyptus nitens load-bearing floor systems saw no failure at 121 minutes, making Cusp CLT the first and only Hardwood CLT in Australia to achieve a 120-minute fire rating.
The fire resistance test is used to assess the fire hazard of the panel system and is directly applicable to similar constructions.
Cusp General Manager Michael Lee said our 120-minute fire rating comes on the back of Cusp achieving both the strongest and thinnest CLT configurations in the world.
“120 minutes is an exceptional result and should give engineers confidence when looking at low carbon building options, without increasing or compromising panel
thickness,” he said.
“The 120-minute fire rating means the CLT floor system will keep its structural integrity for at least 2 hours in a raging fire. The floor systems may well exceed 120 minutes, but we finished the test at this point because 90 minutes is the commercial rate for all mass timber, and our panels had already massively exceeded this industry standard.”
Mr Lee explained that while the timber species, Eucalyptus nitens, undoubtedly influenced the rating, it was also Cusp’s layup design that delivered the exceptional result.
“Hardwoods generally have better fire performance than softwoods because of their dense cellular structure,” said Mr Lee. “So, we were expecting Nitens to surpass the industry standard for CLT in Australia, which, outside of Cusp, is all softwood.
“But Cusp’s unique layup design improved the result
further. CLT already has a high level of fire resistance due to its cross-sectional thickness and airtight construction, which suppresses the ability of the fire to spread. The thermal mass of the sheets also allows for no conduction between one side of the panel to the other. Cusp has taken this a step further with a design that maximises fire resistance,” he said.
The test, conducted by Warringtonfire was conducted in accordance with sections 2 and 4 of AS 1530.4:2014 appropriate for a loadbearing floor system.
The floor systems, incorporating three Eucalyptus nitens CLT panels, were 2950mm wide and 4350mm long. One floor system was 225 mm thick, and the other 175 mm thick.
The floor panels were secured together with 180mm long timber screws and then sealed with Weathertight Sealing Tape over the entire length of joints in the unexposed side and the lap joint on the edges. Wurth Fire Rated MS Bond and Seal sealant was applied to seal all the holes created during installation.
IN 2022, Australia’s sawn softwood imports lifted to 989,129m3, an increase of 48.4% over 2021. This was slightly down from the year-end peak, which was reached in November and was associated with an easing of prices which for all products averaged AUDFob732/m3 a sharp decline of 15.5%.
Annual imports have begun to soften, with further decline expected over coming months, based on recent monthly import volumes.
Despite the modest softening, December saw imports reach 67,428m3, the second highest December month since December 2017. Reading the data in the chart below to the likely position by mid-2023, we can expect imports to still be north of 900,000 m3 on an annualised basis. In many respects, this is a reflection of the huge pipeline of building work that
continues to drive consumption and prices.
There can easily be significant changes between ‘grades’ as they are reflected in import codes, over relatively short periods of time. Small changes in product can lead to a change in the import codes. Rarely however do we see such significant changes as those for Treated Structural products.
where there is supply from Europe and South America, as well as from New Zealand. Until the most recent year, with the exception of the odd shipment, supply of this grade was entirely in the hands of New Zealand, supplemented by Chile.
Estonia, Finland, Germany, Lithuania and Sweden have all joined the market in the last year.
New Zealand, for all of that, remains the stable influence and the major contributor. Its 49,372 m3 was the mar-
(31,810 m3) all very similar and receiving about 17% each of the total.
IndustryEdge subscribers seeking to do more forensic analysis can follow trade flows from port of origin to port of delivery.
If we are to identify one other grade that has shot to prominence it would be the larger dimension, roughsawn, non-Radiata. At 107,210 m3 in 2022, imports lifted an eye-watering 5,631%! In reality, it is probably better to say that the
dropped for one of the smaller dimension grades. We surmise this may then reflect a change in specification from narrow (<120cm) to wider (>120 cm) material.
What makes this more interesting is consideration around the likely application of this supply. We do not speculate publicly on these matters, but it is a worthy question to ponder.
Imports totalling 190,276 m3 in 2022, are up an incredible 366% on the year prior.
The weighted average price is clearly in retreat, with the December price at AUDFob769/ m3.
This is one of the grades
Made with the same durable materials used in our market leading STRUCTAflor particleboard flooring products, STRUCTApanel H2 12mm is a high density panelproviding superior impact resistance and screw holding capability.
ket leading volume, up a very strong 37.3% on the prior year.
Melbourne receives the majority of shipments (85,351 m3 or 45% of the total), with Sydney (32,083 m3), Brisbane (31,995 m3) and Fremantle
import code is now in use, where it really had not been previously.
The major increase in supply came from the Czech Republic and Poland (interestingly, these are the countries where supply volumes
Overall, the main countries of origin continue to be Northern European, with Germany (229,586m3), Lithuania (142,147m3), Sweden (112,023m3), Estonia (97,026m3) and Czech Republic (64,384m3) all playing a major role. They continue to be ably supported by New Zealand (109,470 m3) and Canada (38,364m3).
Learn more about Wood Market Edge online at https://industryedge.com.au/ publications/free-stuff/
FEATURES & BENEFITS
High impact resistance - Double the surface impact resistance of plywood & 9 times greater than plasterboard
Highly durable - Made with the same cuttingedge technology & high-quality raw materials as STRUCTAor ooring
High xing capacity - Ability to screw directly into sheet
Consistently at with no internal delamination
Easy to cut leaving smooth, clean edges
H2 Termite Treated APPLICATION
Used as an underlay for timber strip ooring on top of concrete, internal wall lining (in dry conditions) and as an external temporary hoarding panel
'Estonia, Finland, Germany, Lithuania and Sweden have all joined the market in the last year.'
IT started with a bold idea. It progressed because of an unwavering belief that it could be done. And in June 2021, the newly branded Cusp Building Solutions launched the first certified plantation hardwood CLT in the world.
From a resource traditionally used for woodchips, Cusp now creates a range of mass timber elements for the built environment. Cusp is now set to relocate to a larger manufacturing facility to enable an immediate increase in production of 100%, with further increases planned for the medium and long term.
“Having proven our capability and established market demand, Cusp Building Solutions is now ready to scale,” said founder.
“Up until now, Cusp has been a start-up. The start-up phase was hampered in no small part by the global pandemic. Still, we are excited to begin the commercialisation process of significantly increasing our manufacturing capacity,” he said.
In the start-up phase, Cusp has exceeded expectations, proving its R&D capability with a series of both world and national firsts, including:
The first certified plantation hardwood Cross Laminated Timber (CLT) in the world.
The strongest CLT in the world.
The only CLT certified by the Engineered Wood Products Association of Australasia (EWPAA) in Australasia.
The world’s thinnest CLT
The largest Glue Laminated Timber (GLT) beam capacity in Australia
The only curved GLT manufacturer in Australia.
The company will now strategically invest in people, machinery, and facilities to meet market demand and price expectations and has invited expressions of interest from investors who want to partner with Cusp to accelerate growth.
“The 100% increase in production is our immediate target, but by late 2024, we expect to be manufacturing four times our current monthly throughput with further increases planned beyond that time,” Mr Goldschlager said.
To facilitate the expansion, Cusp is working towards relocation to a larger facility at Deep Creek in Tasmania. The facility is designed for both GLT and CLT production volumes. It is anticipated that this will be the new home of Cusp for the medium term.
“We’ll increase staff by 25-30%, including floor staff, skilled machinists and trainees and diversify our mix of timbers,” Mr Goldschlager said.
While Eucalyptus Nitens is the plantation timber that Cusp was founded on, the company also produces products from other plantation sources, including Grandis, a eucalypt from Urofor, and Spruce, a plantationgrown European softwood.
“The Hermal Group have invested heavily through the start-up phase because we strongly believe in the future of Cusp Building Solutions and the need for mass timber in the built environment,” Mr Goldschlager said.
“We know that mass timber is part of the solution to climate change, and I’m proud that this business can do its part. Most construction materials store little to no carbon and are emission-intensive to create.
“Building with mass timber, on the other hand, can replace emissionintensive construction materials, like steel and concrete, and create a carbon store.
“To substantially reduce global carbon emissions, we must both lower our carbon output and create carbon sinks to counteract the unavoidable emissions we produce and those that have already been emitted.”
Enabling sustainability... with world-class, science-based standardsCusp Building Solutions founder Ron Goldschlager.
FORESTS are the lungs of our planet, providing critical benefits to the global environment, population and economy.
They are essential in mitigating the effects of climate change and natural disasters, while also serving as one of the richest biological areas on Earth.
Additionally, forests provide food, heat, energy, medicine, and renewable raw materials to people around the world. However, despite their importance, we have lost some 178 million hectares of forest since 1990, according to the FAO Global Forest Resources Assessment 2020.
To combat global deforestation, the concept of independently certifying forest management practices was developed in the 1990s as a voluntary tool for promoting sustainable forest management and the trade of products originating in sustainably managed forests. While two major international certification schemes - the Forest Stewardship Council (FSC) and the Programme for the Endorsement of Forest Certification (PEFC) - exist, the total combined area of certified forests under both of these schemes is less than ten per cent of global forests.
In 2019, the total net certified forest area was 426 million ha. This figure is substantially less now that Russian
origin forest material is considered controversial by both schemes as a result of the invasion of Ukraine. Therefore
forest and wood products originating from Russia cannot be certified under either scheme, while the conflict continues.
Expert consultants working with certified forest management organisations and certification bodies auditing conformance of the forest certification schemes confirm both PEFC and FSC deliver excellent and improved outcomes in the forests. Further to this, around 93 million ha is dual- certified under both systems (FSC & PEFC) according to the 2020 FAO Global Forest Resources Assessment report.
Both FSC and PEFC have their own unique implementation of forest certification, and while their fundamental objectives are the same the critical question is how we can improve sustainable forest management practices globally. How can we increase the area of certified forest as a benchmark to prevent future loss of not just forest area, but forest health, and ecosystem services, and ensure a multi-generational supply of forest products? The question shouldn’t be which scheme is better (and in what ways), and what are the differences? These questions frame the whole context of this article.
The often overlooked challenge for objectively demonstrating “certified” sustainable forestry practices (more specifically ensuring that forest products are sourced sustainably) is balancing the need to protect the environment (forest values, biodiversity, soils and water), whilst ensuring cultural and social values are also protected or enhanced, and that local communities and worker needs are met; all whilst remaining economically viable. Sometimes there are nuances in the detail of balancing this equation.
FSC certification was the first cab off the rank, starting in 1993 in Costa Rica and the United States of America. From there, FSC gained momentum throughout the late 90s, and the area of FSC certification has been growing ever since.
FSC takes a “top-down approach,” meaning they develop the standards and benchmarks that forest managers and owners need to follow around the world to attain, and maintain certification. In contrast, PEFC follows a “bottom-up approach” as a mutual recognition agency, endorsing certification schemes that are based on the PEFC global standard, but have been tailored to local condi-
tions and developed through multi-stakeholder processes.
In 1999, PEFC recognised the need for an independent mechanism that would enable the development of national standards tailored to the unique political, economic, social, environmental, and cultural conditions of each country. This mechanism would ensure compliance with internationally accepted requirements and gain global recognition. To achieve this, small and family forest owners from Europe collaborated to create a forest certification system that would demonstrate their excellence in sustainable forest management.
Australia joined the PEFC system in 2002, with their system being first endorsed in 2004. In Australia, Responsible Wood is the national member of PEFC International. As an accredited standards development organisation, licenced by Standards Australia, Responsible Wood has developed an endorsed joint Australian and New Zealand standard for sustainable forest management (AS/NZS 4708-2021).
A national system has several benefits, including the ability to adapt to national forest conditions, ecology, and practices, such as the continuation of over 60,000 years of Traditional Owner management and care for country through the sustain-
able management of Australia’s native forests, including the use of fire. A national scheme can also cater to the consideration of forest ownership structures, as well as national legislation and regulations.
In Australia, the Responsible Wood logo is an ACCC approved certification trade mark, which is a special logo shows consumers that a product or service meets a particular standard. The ACCC requires that certification trade marks must have rules about how the logo can be used.
Dual (both FSC & PEFC) certified forest managers often comment that the Australian/ New Zealand standard can be more relevant to local conditions, being science-based, and supporting best practice forestry, whereas FSC tends to focus more heavily on stakeholder issues. The challenge for organisations is balancing stakeholder interests that may not be directly affected by forest management operations that are legally compliant and best-practice based on sound research.
Organisations in Australia and New Zealand also mention certification costs as a decision-making factor, sometimes having to fly in auditors from overseas. Other factors include bureaucracy and administrative differences when choosing
certification schemes. Generally speaking, both schemes provide similar domestic and overseas market entry opportunities, comply with illegal logging regulations, and are recognised by major retailers. Both schemes have also received recognition through organisations like the Green
Building Council of Australia.
Both FSC and PEFC play a vital role in promoting sustainable forest management practices around the world. With FSC being the pioneer in this field and PEFC being the largest certification scheme, together they have certified almost 400 million hectares of
forest worldwide (FAO Global Forest Resources Assessment 2020). By choosing products with FSC or PEFC certification, consumers can make a significant impact on the preservation of our planet’s forests and contribute to a sustainable future for generations to come.
WHEN large-scale Melbourne manufacturers Australian Moulding Company (AMC) looked at relocating and establishing a purpose-built factory in Melbourne, they knew they needed to tap into some serious expertise.
AMC manufactures skirtings, architraves, doors and accessory mouldings including picture rails, corner blocks and bolection moulds from all periods of Australian housing produced from Moisture Resistant Medium Density Fibreboard (MRMDF) or any timber including, Finger Jointed Pine, Clear Pine, Meranti, Oak, Western Red Cedar, Kiln Dried Hardwood (KDHW) and any other timber on request. After considering vari-
ous vendors, AMC ultimately purchased their three new moulding machines from Stirling Machinery. Having invested in new equipment technology, AMC will be one of the world’s best practised moulding operations in the southern hemisphere.
Hugh Gilchrist, AMC’s Director/Founder flew to Brisbane to meet with Craig Honeyman, Director/Founder of the Stirling Group. “I am convinced that the future for AMC is to have Stirling Machinery as our partner,” Hugh says.
“They have the products, the service and the expertise that
stand us head and shoulders above our competitors.”
AMC has been a major, longstanding customer of Stirling’s tooling division, Accurate Australia, and Craig has been highly regarded in the industry for his machinery nous for decades.
AMC’s goal was to bring their business into line with current trends and to meet increasing and changing demands for their products. “Customers been used
to AMC delivering exceptional mouldings and were also calling for shorter lead times,” Hugh explains. “Now we can achieve both of these for our customers.”
Hugh says there became a great need for automation, not just to keep up with volume, but also to cater to changing workforce trends. He had noticed that young people in his workforce would change jobs frequently, meaning there was
a constant need for training. He also identified that young people are more inclined towards computerisation than manual operation.
Following discussions with Craig, a shopping list emerged featuring three specific items: a high-speed moulder, a wide profiling moulder, and a short production run moulder. These machines cover AMC’s entire product range, and their specs will make a monumen-
tal difference to production. One of the greatest benefits of the new Stirling machines is that they all communicate with the grinding room. All the data required for the setups of the machines is managed there instead of at the individual machine, meaning there is no interruption whatsoever between production runs. Additionally, with all data and measurements being captured in the grinding room, there is no need to employ skilled labour on the floor.
An 8-head, high-speed moulder, the S230-8 runs 60m/min and is capable of processing from five hun-
dred metres to thousands of metres at a time. “Efficiencies have to be spot on the money to retain viability and profitability for higher-run lines,” Craig explains. “The S230-8 is an absolute game changer for AMC. With all finishing spindles fully jointed, the surface quality will reach a new level.”
AMC were increasingly being called upon to run wide moulders and needed a wider moulder to meet this market demand. The CNC control of all setting spindles combines with Proset control software. The M310-8 can handle mouldings up to 300mm wide.
The C230-6 is a dynamic machine that is small, flexible and adaptable to handle short-run jobs. It has a 8,000RPM feed speed and the same setting characteristics as the S230-8 and the M3108. Considering the number of setups required on a shortrun machine in a day, managing setups via the grinding room instead of the machine itself slashes time and vastly improves efficiencies.
The next Stirling Machinery acquisitions for AMC will be the grinding and measuring equipment and a CNC profile grinder.
“We wanted the same profile grinder that Craig has up
in the Stirling factory. We’ve seen it in action and can see the enormous value it will bring to our business,” Hugh explains. “That will be the final tie-in for us and then everything will be CNC controlled.”
Craig says his customers are increasingly acknowledging the need for automation. “Today’s workforce is very adaptable and they’re not afraid of computers. Adapting to the skills market is an important part of future proofing a business. And with more automation coming into play, this industry is set for an exciting future.”
Indeed, Stirling Machinery is promoting the new technology at every opportunity.
“It’s 2023 and this technology is available now!” Craig says. “Look, the economy is currently a softening market. Now is the best possible time to take stock of your processes and have a look at what can be done to get in the best shape you can for when the economy bounces back and also what opportunities can be added to your existing product offering. If you’re still using traditional moulders and spending time setting them up by hand, you really should talk to us about where this tech can be incorporated into your existing manufacturing processes. You’ll save time, achieve better quality finishes and take advantage of a ready-made skills market.”
THIS year marks a key milestone for Australian timber products manufacturing business Timberlink, as it celebrated 10 years in business.
Timberlink CEO Ian Tyson said “this is an important moment to reflect on the enormous amount of change and improvement that has happened in our business since February 2013”.
Change that can only occur when a business has a vision and plan for its future, has an ownership structure and a Board that supports this, and then most importantly, has a great team of people who can add to and deliver on that vision and plan.”
Timberlink was formed in February 2013, following the sale of Gunns Limited’s softwood sawmilling assets, and is a part of an integrated softwood forestry business that is managed by New Forests.
CEO Ian Tyson has been at the helm of Timberlink since its formation.
“Thanks to the great support we have had from our customers and through expanding our operations, we have grown as a business, and now proudly employ 600 team members compared to where we started in 2013 at
380. The majority of which are in regional areas,” Mr Tyson said.
This year Timberlink will complete two significant innovation projects: one in mass timber with CLT and GLT, and one with wood-plastic composites.
“These projects will take Timberlink from being pri-
statement, “A future made better for all” is reflective of its commitment to helping build environmentally friendlier homes and buildings that support the world being a better place for the generations that follow.
marily a structural timber manufacturer to a structural engineered timber products and solutions business, a remarkable change in ten years,” Mr Tyson said.
To reflect and support this growth, Timberlink has released a refreshed logo and a newly redeveloped website.
Timberlink’s new positioning
“It’s been a great start and a fantastic ten years, but it’s only the beginning,” Mr Tyson said.
“We will continue to build on what we’ve already done and look forward to our future. There is so much more opportunity for us.
“We thank all our customers and suppliers for their support over this journey and we are even more excited about the next 10 years.”
AKD has introduced innovative new technology that provides real time quality assurance for H2F timber treatment efficacy at its Tumut and Oberon processing facilities, to provide increased market confidence and is the first certification of its kind.
This new testing approach uses a state of the art Fourier Transform Infrared Radiation (FTIR) spectroscopy unit to demonstrate equivalence of a non-standard method of timber chemical retention verification under the recently updated timber treatment standard (AS/NZS 1604).
The innovative process has been third party certified by the Engineered Wood Products Association of Australasia (EWPAA). AKD is the first producer to achieve this certification.
FTIR applies thermal radiation to the test sample which is invisible to the human eye and interacts with matter by triggering molecular vibrations.
The usefulness of FTIR comes with the easy testing and immediate results. The unit is already deployed in many other industries including phar-
maceutical, automotive, electronic, food and feed and construction.
This innovation replaces the old method, which is common across the industry, involving treated timber products being quarantined on site and samples sent off site for external laboratory testing before product treatment can be assured and the product released for sale.
This new method is real-time, ensuring that AKD product supply is not delayed to the market. AKD plans to roll out the new technology to other sites around Australia.
As with most innovations, this new approach was only possible with collaboration between various parties, including one of AKD’s preservative suppliers, Koppers Performance Chemicals (KPC) who understood
that the past method of verification was slow and could be significantly improved.
“It was clear that AKD needed a solution for their ongoing QC of H2F treated framing. In our visits to all the AKD sites, the need to quarantine treated framing until external QC results are confirmed, was always raised with us as a less than ideal practice,” Elias Akle, KPC’s CEO, said.
KPC’s own chemist, Luke McGregor, bought the idea of FTIR spectroscopy to the problem as a possible solution.
Working with AKD’s own Wood Technologist, Marina Milic, the process of data collection, analysis and calibration of the unit took place over several years, notwithstanding the pandemic slowed down the process.
Timber ED provided support in statistical analysis. This process provided the comfort to commit to the technology by ordering the first instrument for the Oberon site and, following its successful commissioning, ordering another unit for AKD’s Tumut site.
Gavin Matthew, CEO of EWPAA, stated “EWPAA is proud to have worked with AKD to achieve the first certifica-
tion to our newly developed and JASANZ accredited preservative treated certification scheme. The certification recognises AKD’s innovative process of treating and verifying H2F structural timber to the recently updated AS/ NZS1604 standard. We look forward to delivering more certifications and increasing market confidence in the manufacturing and treatment of renewable timber products”.
Marina Milic, AKD’s National Wood Technologist who leads the company on treatment innovations, said FTIR spectroscopy is a fast and easy analytical technique that provides answers within seconds.
“It is resource friendly, requiring only a small sample and little preparation. Achieving this new certification shows AKD is always looking for continual improvement,” she said.
“I’m proud of our collaboration both within the AKD business, across our tech team with special mention going to Kim Harris, AKD National Compliance Manager, with site QC personnel, and along with industry partners (EWPAA, KPC, and TimberED) during this ground-breaking project.”
With timber frame construction expected to continue growing in popularity, it’s critical that any building made from the material is adequately protected against the spread of fire. Here, cavity barriers are imperative, and Robin Lancashire, Senior Timber Frame Consultant at BM TRADA, explains the key considerations when designing and installing these elements.
THE sustainability agenda is leading a renewed interest in the use of timber in construction. Demand is rising exponentially across both residential and commercial building sectors, and a study by MTW Research found timber frame housebuilding was expected to rise by more than £150m by 2026.
Reasons for the increased usage is clear. Highly sustainable, timber captures carbon better in comparison to other materials such as steel and aluminium that capture none at all but use tonnes upon tonnes of carbon in their production. From a commercial perspective, one of the biggest benefits is that it’s fast to build with, making it more profitable for developers. While it’s a good sign that timber construction is on an upward trend, safety is still key. In the event of a fire, cavity barriers are of fundamental importance, and they must be able to perform as intended. From design and specification through to installation, there are several key factors that must be considered so that buildings and the people within them are protected.
The performance and installation of cavity barriers has been flagged in recent
fire events across different building types. Without a properly designed barrier, cavities act much like a chimney and can allow fire and smoke to quickly travel unseen through what can often be an extensive network of connected spaces in a building.
National building regulations stipulate where cavity barriers should be installed, what they should be constructed of and how they should be fitted. In the UK, there are some regulatory differences between the nations in terminology and specific requirements, but the principles are all the same – limit the spread of fire in a cavity.
When designing timber frame external walls, one of the earliest decisions that needs to be made is how to balance ventilation with fire safety.
It is important to accommodate the requirement for cavity barriers while also ensuring timber elements remain dry and below the decay threshold (a moisture content of 20% of less). A drained and vented external wall cavity behind all types of cladding is required for any timber frame construction. This space allows moisture vapour that travels through from the warm side of the wall to the
cold side to ventilate away, without forming damaging interstitial condensation.
The external wall cavity is a line of defence to protect the timber frame from external moisture. It prevents winddriven rain or leaks through the cladding from directly wetting the timber frame structure, by letting moisture drain away freely. Therefore, the decisive challenge is delivering cavity barriers where required, while still allowing the timber frame structure to drain and vent.
For those designing and building with timber, the Timber Frame Construction (5th edition) is the go-to publication to reference. Information on various types of cladding can be found in the book’s cladding chapter, with details on how to close external wall cavities at required locations,
while still providing the necessary drainage and ventilation.
Understanding where to specify cavity barriers is just one part of the equation. The material they are made of must be tailored to the type of cladding specified.
There are a number of choices available, from using timber itself, to mineral wool, and intumescent seals.
TIMBER CAVITY BARRIERS
Surprising to some, timber is listed in the building regulations as a material that can be used to provide the necessary fire resistance of a cavity barrier. It is the material of choice for cavity barriers around window and door openings, and with claddings that are
supported by the timber frame structure.
In the event of a fire, the timber slowly chars at a predictable rate so it can provide the required period of fire resistance. Available for installation in continuous lengths, it is reasonably robust during construction, and fulfils other roles while acting as a cavity barrier.
MINERAL WOOL CAVITY BARRIERS
Mineral wool is another choice. Strips of mineral wool, typically protected in red polythene sleeves, can often be seen on many timber frame buildings under construction. As a cavity barrier, this material performs well if it is fitted in a continuous line and is sized to be installed under compression to fully close the cavity.
When designing with this building product, bear in mind that in the event of a fire, the polythene sleeve quickly burns, meaning there is no support from it to keep the cavity barrier in place. Accurate sizing to ensure a compression fit of the mineral wool core is therefore critical to stopping these strips falling down the cavity and failing. It is important to note that they can also be easily damaged or dislodged during the construction phase,
LM FASTENERS PTY. LTD.
so care must be taken during installation.
Despite being more expensive than timber or mineral wool, the use of intumescent cavity barriers is expanding. In the early stages of a fire or heat exposure, they are designed to swell up, closing the cavity against further fire and smoke. In their inactive state they can contribute to maintaining good drainage
and ventilation through a clear cavity. This can simplify detailing and reduce the need for what can be unsightly drainage slots.
External walls are not the only place where cavities are found. The other main area where they occur is in party walls. Timber frame buildings rely on cavities to reduce acoustic transfer
between areas of the same building. To prevent fire and smoke having a direct route between them, these cavities need closing at compartment lines.
Hard materials cannot be installed as cavity barriers here, as these would provide a route for acoustic transfer. Instead, wire-reinforced or polythene-sleeved mineral wool cavity barriers tend to be used in these locations. It is important that they are fixed and sized to close the cavity and remain in place at compartment lines.
Most cavity barriers are installed at edges of cavities and along compartment lines, but there are other locations where they are required by national building regulations. The relevant statutory documents should always be consulted.
Designing and building timber frame constructions ultimately needs appropriate due diligence to ensure that the resulting structures are durable and safe. The accurate specification of cavity barriers is critical to this.
It is highly recommended that designers and construction planners work with timber frame consultants at the initial design stage to ensure the project adheres to best practice. Using services such as BM TRADA’s frameCHECK allows specialists to evaluate drawing details and visit sites under construction to provide specific advice. By going down this route, the standard of timber frame construction can be raised while also helping to make the buildings of tomorrow safer than today’s.
For more about BM TRADA and its range of timber services, please visit www.bmtrada.com/timber-services
After more than 70 years supplying quality hardwood timber and timber products, Grafton native hardwood timber mill J. Notaras and Sons has been sold to Newcastle-based Marshall’s Timbers.
J. Notaras & Sons was founded in Grafton by two brothers - Lambrinos (Brinos) and Spiro Notaras – in 1952 and has continuously operated since then under the ownership of the Notaras family. Marshall’s Timbers is a family owned business, operating for over 60 years and are Newcastle’s largest supplier of timber and timber products with family commitment to quality and service aligned to the Notaras family.
AE Gibson & Sons Pty Ltd has been appointed regional Australia and New Zealand partner for Canadian company Cardinal Sawquip. Cardinal Group specialises in the design, manufacturing and distribution of equipment used in the sawmill, forestry, recycling, mineral exploration, and mining industries.
TIMBER BUILD AT CAMPUS
Specialty European timber that regenerates “in five-tosix minutes” is among the sustainable materials being used in the second stage of the University of the Sunshine Coast’s Moreton Bay campus.
Three new buildings at the Petrie location will utilise a mixture of domesticallysourced XLam Australian timbers and purpose-sought glue-laminated Hess timbers from Europe.
TYPE 17 7
TYPE 17 7
CLASSS 4
CLASSS 4
TYPE 17 CLASS 4
HEAD FLANGE & HEX HEAD FLANGE WITH SEAL
HEAD FLANGE & HEX HEAD FLANGE WITH SEAL
HEX HEAD FLANGE AND HEX HEAD FLANGE WITH SEAL
HEAD FLANGE & HEX HEAD FLANGE WITH SEAL
HEAD FLANGE & HEX HEAD FLANGE WITH SEAL
UNIT 3/64 HASSALL STREET SMITHFIELD NSW 2164 lmfasteners.com.au
UNIT 3 / 64 HASSALL STREET SMITHFIELD NSW 2164
UNIT 3 / 64 HASSALL STREET SMITHFIELD NSW 2164
UNIT 3 / 64 HASSALL STREET SMITHFIELD NSW 2164
UNIT 3 / 64 HASSALL STREET SMITHFIELD NSW 2164
PHONE: (02) 9757 4367
PHONE: (02) 9757 4367
PHONE: (02) 9757 4367
PHONE: (02) 9757 4367
PH: (02) 9757 4367
EMAIL: sales@lmfasteners.com.au
EMAIL: sales@lmfasteners.com.au
EMAIL: sales@lmfasteners.com.au
EMAIL: sales@lmfasteners.com.au
EMAIL: sales@lmfasteners.com.au
ASYDNEY company which designs and manufactures modular linear timber systems has earned Responsible Wood chain of custody certification, demonstrating the company’s commitment to sustainability.
Screenwood produces linear panels made from a selection of five timbers and are prefinished in a variety of colours.
The modules are assembled and cut to specified lengths for ease of installation. The company is fair-rated, VOC tested, acoustically rated and environmentally certified, ensuring that sustainability concerns are integrated throughout the entire value chain.
For their chain of custody certification Screenwood uses a physical separation method as a means of managing and identifying certified timbers, sourcing only Responsible Wood/PEFC timbers. The company is committed to continuous improvement and compliance with all applicable laws regarding environmental impacts and workplace health and safety.
A commitment to sustainability and responsible sourcing also helps to se-
cure a social license to operate and build brand credibility.
By demonstrating a commitment in these areas, Screenwood is not only able to attract and retain customers, but it is also able to differentiate itself from its competitors and establish itself as a leader in the industry.
By ensuring that its products are responsibly sourced and produced, Screenwood is able to demonstrate to its customers that it is a brand that they can trust and rely on for highquality products that have been produced with care for the environment.
“At Screenwood, we understand the importance of taking action towards sustainability,” Screenwood general manager Tim Russell said.
“That’s why we are committed to using only high-quality, sustainable materials and supplies in our production processes and business. Our Responsible Wood certified status is a testament to this commitment.”
Matt de Jongh, Responsible Wood’s Sustainability Manager, said certification plays a crucial role in preventing deforestation and ensuring that forests are managed sustainably.
“By choosing Responsible Wood certified products, Screenwood publicly demonstrates its commitment to sustainability and responsible resource management. This is commendable and serves as an inspiration for other companies to follow.”
In addition to its commitment to sustainability, Screenwood is also dedicated to delivering high-quality products to its customers.
The company’s responsible sourcing and sustainable practices ensure that its products meet the highest standards, both in terms of quality and environmental impact.
Screenwood’s Responsible Wood certification, provides customers and consumers with peace of mind that they are purchasing a product that has been responsibly sourced and produced sustainably with care for the environment and the workers harvesting the forest material.
TREATING products increases their structural life and allows fast growing and environmentally sustainable plantation pine to be used in many more applications. Treatment has no effect on the timber’s strength or flammability.
Timberlink uses different preservatives depending on what hazard the timber needs to be protected from. Our Timberlink Blue framing is treated to protect the timber from termite or borer attack, so plantation pine framing can be used in termite and borer risk areas.
Timberlink uses different preservative formulations for our outdoor ranges as this timber needs to be protected from decay as well as termites and borers. The treatment is different depending on whether the timber will be used above ground or in contact with the ground.
Note that timber treatment does not protect against weathering. This greying of timber over time due to exposure to the sun and rain, can only be prevented by finishing the timber with a quality paint or stain and then maintaining it.
To ensure the timber’s treatment level is suitable for the application you have in mind, always check the hazard class table.
You should always look for a treatment mark when purchasing treated timber. Not only does the brand give you detail about the treatment level
and type, it is also an indication of quality, as by applying a treatment brand, the manufacturer is claiming it has been treated to Australian Standards.
A good tip when building with treated timber is to keep or photograph the treatment tags as proof of where and how the timber was treated. You will need this info if you have any issues with the timber later on.
A treatment mark can be stamped on the timber, burnt into the timber or be on a tag attached to the end of the timber. It will always follow the same format as this is specified by an Australian Standard.
The mark consists of three groups of numbers/letters.
The first three identify who treated the timber
The next two digits are the preservative code telling you what preservative the timber has been treated with
The final ‘H’ number indicates what level the timber has been treated to and therefore what applications it is suitable for
Any CCA treated timber sold in Australia, must also be marked as “Treated with Copper Chrome Arsenate”. This can appear on the treatment labels fixed to the ends of the timber or on the stamp branding along
its length. For smaller end-section timber products, labelling individual pieces isn’t practical, the packaging must be labelled.
All timber preservatives used in Australia are approved by the Australian Pesticides and Veterinary Medicines Authority (APVMA) and approval is only granted to treatments that are effective and safe to use.
When treating timber, there are a series of Australian Standards that must be adhered to. These specify the con-
centration of a particular preservative and how deep it has to penetrate into the wood to protect it from the expected biological hazard to which it will be exposed as well as labelling requirements.
When working with any timber be it treated or not, we recommend following these safety tips:
Wear gloves.
Wear eye protection and a dust mask.
Don’t burn. Off-cuts can be disposed of in landfill but check with local authorities.
FTMA Australia is an independent, national organisation representing fabricators of and suppliers to the timber prefabricated truss and wall frame industry in all Australian states & territories providing a unified voice, to protect and advance our multi-billion dollar industry.
FTMA Australia thanks our dedicated supporters and encourages you to support those who support your industry
PRINCIPAL PARTNERS
FTMA wants to support our members to become better businesses, which in turn makes them better customers for suppliers and better suppliers to the construction industry, consequently helping grow our markets.
To able to achieve this, we needed more funds to invest in various projects which helps grow and strengthen the professionalism of the timber fabrication market and viability of our members. So, we began to focus on restructuring our sponsorship as our sponsorship levels had not changed, nor had the cost, since our inception in 2007.
This was the biggest change to our association since our inception and a lot of work went into the making this happen.
increased our income from partners by 170%, which will allow us to invest more heavily in to your future and six key areas (below).
I hope you all thank the FTMA Partners for their continued efforts in supporting FTMA Australia, as their support allows us to continue our high quality support of the Australian frame and truss industry.
STRATEGIC PARTNERS
First, we brought the threenail plate CEO’s to the table to talk through the key issues they see in our industry, before bringing together all our partners in late Novem-
RECRUITMENT & RETENTION
ber 2022, to again get their feedback and input into the areas we should be focusing on.
After a lot of discussions with all of our partners, board, strategic networks and members, we created a three-year plan, which we believe will allow us to continue to support our members, whilst investing in to future programs which will help grow the sector and our markets.
As a result of the review and the creation of our three-year plan, FTMA has
• Creating online training with our Designer Short Course
• Creating job descriptions and job advertisements
• Continuing FTMA’s Rebuild & Design program.
• Developing Employee Wellbeing programs
SUPPORTING PARTNERS
For a full list of the conditions of membership and a downloadable application form visit: www.ftmanews.com.au
• Employing a TAE to support fabricators with increased training.
CARBON WARRIOR
• Promoting the environmental benefits of timber offsite fabrication
• Lobbying for policy changes recognising the benefits of timber
• Educating builders on Carbon Warrior policy
• Further developing and promoting the Carbon Warrior program
TIMBER PROJECTS
• FTMA Strategic Technical Committee
• Timber Waste program looking at the circular economy.
• Explore an independent Engineering Testing Panel for inclusion of timber in nail plate software.
• Develop targets for Timber Social Housing based on Carbon Stored
The FTMA Partners include:
Principal Partners - MiTek, Multinail & Pryda Strategic Partners – AB Phillips, AKD, Australian Panel Products, Dindas Australia, Meyer Timber, Staxa (Wespine), Timberlink Australia, Vekta Automation & Vida Wood Australia
Supporting Partners – Bliss & Reels, Combilift, Daw Trading, Hundegger Australasia, Hyne Timber, Independent Hardware Group, McCormacks Australia, OneFortyOne Wood.
RESILIENT TIMBER HOMES PROJECTS
• FTMA is one of two Research Partners for the FWPA Program
• Investing in this program on behalf of FTMA Members to ensure future resilient timber homes can be manufactured by our sector and are environmentally friendly.
FORECASTS & DATA COLLECTION
• Quarterly Trussted Insight forecasts publications
• Industry Census*
• Salary Benchmarking*
• Australian House Framing & Fabrication Review & Outlook
• An ongoing quarterly Frame & Truss Sector Outlook (FATSO)
* Industry Census & Salary Benchmarking to occur in alternating years
BUILDING BETTER BUSINESSES
• HR Platform for FTMA Members
• DFV Policy
• Employee Wellbeing Programs
• Current Wage Rate & Award Breakdowns
• Credit Application Forms
• Mental Health First Aid training
• Employment Contracts
• FTMA Safety SOP Videos with FTMA NZ
ARCHITECT James Stockwell’s design for the Croft House at Inverloch in Victoria was sonamed because it draws on the tradition of Scottish croft houses.
Crofters work in an extreme climate and their houses are generally long and low-slung. Crofting is found predominantly in the coastal fringes of the western and northern Scottish mainland.
Responding to similarities in Inverloch’s seaside location and climate, Stockwell’s Croft House is land-hugging and shielded from the prevailing wild weather.
He has described his design strategy as based on the idea
of a house as shelter, with the body of the building turning its back to the prevailing winds.
Internally, the house makes extensive used of Victorian
ash, commercially a mixture of mountain ash and alpine ash.
The two species blend together and are so similar as to be hard to tell apart. Victorian ash is particularly versatile since it is available in both veneer and solid form.
In the Croft House Victorian ash veneer and solid timber provide a light-coloured, even grained background which maintains the natural feel of the interior without dominating it.
The ash tones contrast with the exterior where the steely colour palette has been chosen to blend with the geology of the site.
As well as using sustain-
2020
ably grown, renewable wood products, the Croft House makes use of passive design principles, employing high thermal inertia, pressedsand partition walls, inside a heavily insulated and sealed building envelope, with double glazing throughout.
The Croft House has won several major awards including the Allan and Beth Coldicutt Award for Sustainable Architecture in the Australian Institute of Architects’ Victorian Architecture Awards.
The house was also a finalist in the Australian Timber Design Awards in the timber veneer category sponsored by the Timber Veneer Association of Australia.
STRONG house price expectations over the next 12 months have offset modest confidence in the economy to deliver an improved outlook for the property industry according to the ANZ / Property Council Survey for the March 2020 quarter.
National property industry confidence levels have increased by five index points from the previous survey to 123. This is slightly above the average for 2019 of 121 index points, and three index points below the survey historical average. A score above 100 index points indicates net positive sentiment among survey respondents.
2017
THE GLOBAL engineered wood market is estimated to reach $US41,273 million by 2022, growing at a compound annual growth rate (CAGR) of 24.8% from 2016 - 2022. North America and Europe, being the developed markets, account for nearly 70% of global engineered wood production, while still maintaining high CAGRs.
MGA TMA has held the position that family and domestic violence, as with all acts of violence, is an objectionable afflict on our society, creating lasting damage to individuals and communities.
In recent times the media and governments across Australia have shone a spotlight on this societal problem and debated solutions to assist those exposed.
In addition to strengthening the criminal justice system, governments have progressively implemented reforms which address the social disadvantage victims face, including consequences which flow from interruptions to being able to engage in work.
In recent years, employees gained the right to take unpaid family and domestic violence leave. Shortly after, the Australian Government
MARIE-CLAIRE MCKIERNAN NATIONAL MEMBERSHIP MANAGERbegan consultation regarding creating a paid entitlement to this form of leave. MGA TMA made a submission to the Education and Employment Legislation Committee on this matter.
In accordance with member feedback, MGA TMA agreed with the principle that work-
ers require support when addressing family and domestic violence. We voiced concern relating to the financial burden that paid family and domestic violence leave would have on members, particularly small and medium-sized businesses, if required to fund this leave themselves.
MGA TMA observed the Australian Government currently funds paid parental leave and a new form of paid leave should also be funded by the government.
Despite our concerns, the Australian Parliament proceeded to create the new paid family and domestic violence leave entitlement, to be funded by employers. This entitlement is now law and has commenced operation for businesses which employ 15 or more employees. Businesses which employ 14 or fewer employees will be re-
quired to provide this leave to employees later this year.
MGA TMA recently advised members of these changes and how they will operate, including new obligations and rights.
MGA TMA members should contact our Employment Law team on 1800 888 479 or legal@mga.asn.au to discuss this new entitlement and obligations for your particular circumstances.
Joining MGA TMA offers many benefits. Membership gives you access to our in-house employment law team, industry leading advocacy and comfort in the knowledge that you are supported by an industry group that’s been in existence for 140 years.
If you would like more information on MGA TMA membership, please contact us on (03) 9824 4111 to discuss.
Engineered wood demand is expected to remain high during the forecast period as it is an apt alternative to concrete and hardwood. Engineered wood products are widely used by architects, builders, code officials, and building designers aware of energy-efficient framing practices that conserve energy, speed-up construction, cut labor cost, and reduce waste.
THE GROWING interest in prefabrication and off-site manufacturing of timber frame and wood panel buildings seen as both an opportunity and a threat to truss and frame fabricators, will be one of the more interesting topics at Frame Australia 2012.
Until recently, these building methods were used mainly in remote areas and for individual projects. However, the economics of reduced time on site and lower building costs has changed the attitude of many builders and developers keen to develop a competitive advantage within the industry.
Conference director Kevin Ezard said these emerging markets were potentially a long-term threat to the current practice of ‘open frame’ fabrication.
IN a major decision that will pose significant difficulties for business in managing annual leave entitlements , on 22 December 2022, a Full Bench of the Fair Work Commission issued a Decision to insert a new model clause into 78 Modern Awards regarding leave during shutdowns (“the Decision”).
The Decision was made in the “plain language proceedings” as part of the continuing 4-yearly review of modern awards (which commenced in 2014), and it affects 78 Modern Awards which already contain shutdown provisions. Modern Awards affecting our Members are:
• Timber Industry Award 2020
• Clerks—Private Sector Award 2020
• Manufacturing and Associated Industries and Occupations Award 2020
• Road Transport and Distribution Award 2020
• Joinery and Building Trades Award 2020
• General Retail Industry Award 2020
EXISTING MODERN AWARD SHUTDOWN CLAUSES
Many Modern Awards currently contain clauses that permit an employer to direct employees to take annual leave during a shutdown period. Our industry award, the Timber Industry Award 2020 is one such award. Typically, under the current clauses, an employer must give employees a minimum of 4 weeks’ notice of their intention to do so. In addition to this, some Modern Awards further permit employers to direct staff to take unpaid leave during
a period of shut down if the employee does not have sufficient annual leave accrued to cover the shutdown period.
THE MODEL CLAUSE – DIRECTION TO TAKE ANNUAL LEAVE DURING SHUTDOWN
Under the new model clause, an employer may only direct employees to take annual leave during a shutdown period if the employer provides 28 days’ written notice of a temporary shutdown period (although a shorter notice period can be given by agreement between the employer and the majority of affected employees). Notice must also be given to any employees who are engaged after the date notice was initially given to other staff.
If notice was given, then an employer may direct employees to take accrued annual leave during the shutdown period. The direction must be in writing and must be reasonable (including in relation to the length and frequency of shutdowns).
The model clause will replace any existing clauses on the matter in each affected Modern Award.
There will however be adaptations to the model clause in various Modern Awards to incorporate existing prescriptions which:
• limit the application of
shutdown provisions by reference to the circumstances in which the shutdowns occur (such as restrictions relating to the time of year during which the shutdown occurs and the purpose of the shutdown (i.e. shutdowns may be limited to the Christmas/New Year holidays, and/or may be for the purpose of pre- planned maintenance); and
• prescribe a notice period of longer than 28 days for a shutdown.
In its Decision, the Full Bench concluded that a direction to take unpaid leave during a shutdown is in substance a ‘stand-down’, and modern awards are not permitted under the Fair Work Act 2009 (Cth) to contain such terms. Accordingly, the amendments will remove/ replace modern award provisions permitting an employer to direct an employee onto unpaid leave during a shutdown.
Under the amendments, an employee with insufficient accrued annual leave may take annual leave in advance during a shutdown in accordance with an agreement under the relevant Modern Award terms. Where there is a shutdown which is not the subject of a direction to take leave, an employer and an employee may agree in writing for the employee to take leave without pay.
In relation to the implications of the amendments
(and in response to concerns raised by employers), the Full Bench indicated1:
1. In some circumstances, a shutdown may be due to circumstances which qualify for standing down employees (unpaid) without needing to rely on modern award terms.
- The Full Bench gave the following example: “in the building industry, if a head contractor closes down a building site over Christmas/ New Year, that is likely to cause a stoppage of work for which a subcontractor employer cannot reasonably be held responsible and thus enable [an unpaid] stand down under s524.”
2. Employers may manage annual leave requests (including reasonable refusal of requests under s88) throughout the year so that employees have sufficient accrued leave to cover a shutdown period.
- The Full Bench stated “... where it is an established feature of an employer’s business, or a relevant part of it, to shut down in the Christmas/New Year period, it would be unlikely that a refusal to agree to a leave request which would leave the employee with insufficient accrued leave to cover the shutdown period would be unreasonable within the meaning of s88(2) unless there were some strong countervailing factors pertaining to the individual concerned.”
3. Employers may manage shortfalls of accrued annual leave in other ways including (where applicable) use of accrued rostered days off, TOIL, or granting requests to take annual leave in advance.
4. An employer could identify useful work that could be performed in a part of its operations by employees
who do not have sufficient accrued annual leave to cover all or part of a shutdown, and who do not agree to take leave without pay, provided the work is within the terms of relevant modern award provisions dealing with employer and employee duties.
TTIA advises when considering requests for annual leave during the year, an employer will need to ensure the employee will have enough leave to cover any shutdown period or obtain the employee’s agreement that they will take unpaid leave.
It is the view of TTIA that when an employee does not have enough leave to cover the shutdown, the employer will either have to find work for the employee to perform or pay the employee for the period not covered by accrued annual leave or have the employee agree to leave in advance.
The Decision states that the variations will take effect on 1 May 2023.
After a forced interruption during the COVID period, TTIA will be resuming our popular Member Briefing sessions in May/June of this year in locations throughout various States. We will be dealing with this annual leave closedown change as well as many of the other substantive industrial relations/award changes including those as a result of the change of federal government last year. If you would like details of venues and dates please phone (02) 9264 0011 or email ttia@ttia. asn.au
1 SG30 Solargas Kiln $25,000+GST
2 Weinig 6 Head Moulder, Chrome beds, good order. With $20,000 heads & $20,000 tooling $60,000+GST
3 Stenner ST100 - 18kW, has had limited use $30,000+GST
4 Dust extracters - all sizes, briquette press (POA)
5 Weinig Profimat 5 Head Moulder $5,000+GST
Location: Moss Vale NSW Contact 02 4869 1322 or sales@strade.com.au
This is a unique opportunity to purchase a fully functioning timber mill, 450km west of Brisbane and easily accessible by road and rail. Situated on a 3.63ha^ site, this mill is complete with top-ofthe-line machinery (see full list online*) including dressing yard, water tanks and water trucks.
The mill processes timbers for manufacture of furniture products, flooring, cabinetry, wood-based panels, craft and toys. The supply chain is streamlined, timber is packed and transported to the Port of Brisbane.
Classifieds advertising has long been regarded as one of the best value for money forms of advertising because it’s been proven to work, time and time again
Sustainable Hardwood Certification (SHC) is being established to provide an effective and verifiable process to assure end-users that hardwood from low-intensity managed forests is both legally and sustainably sourced. Existing certification systems do not fully consider non-industrial forest operations and therefore small-scale hardwood producers miss out on opportunities to trade their products on an equal footing with industrial, large-volume producers.
TO REGISTER YOUR SUPPORT FOR SUSTAINABLE HARDWOOD CERTIFICATION, SCAN THE QR CODE.
IS IMPORTANT TO YOU, WE NEED YOUR SUPPORT