BARKER COLLEGE PROJECT

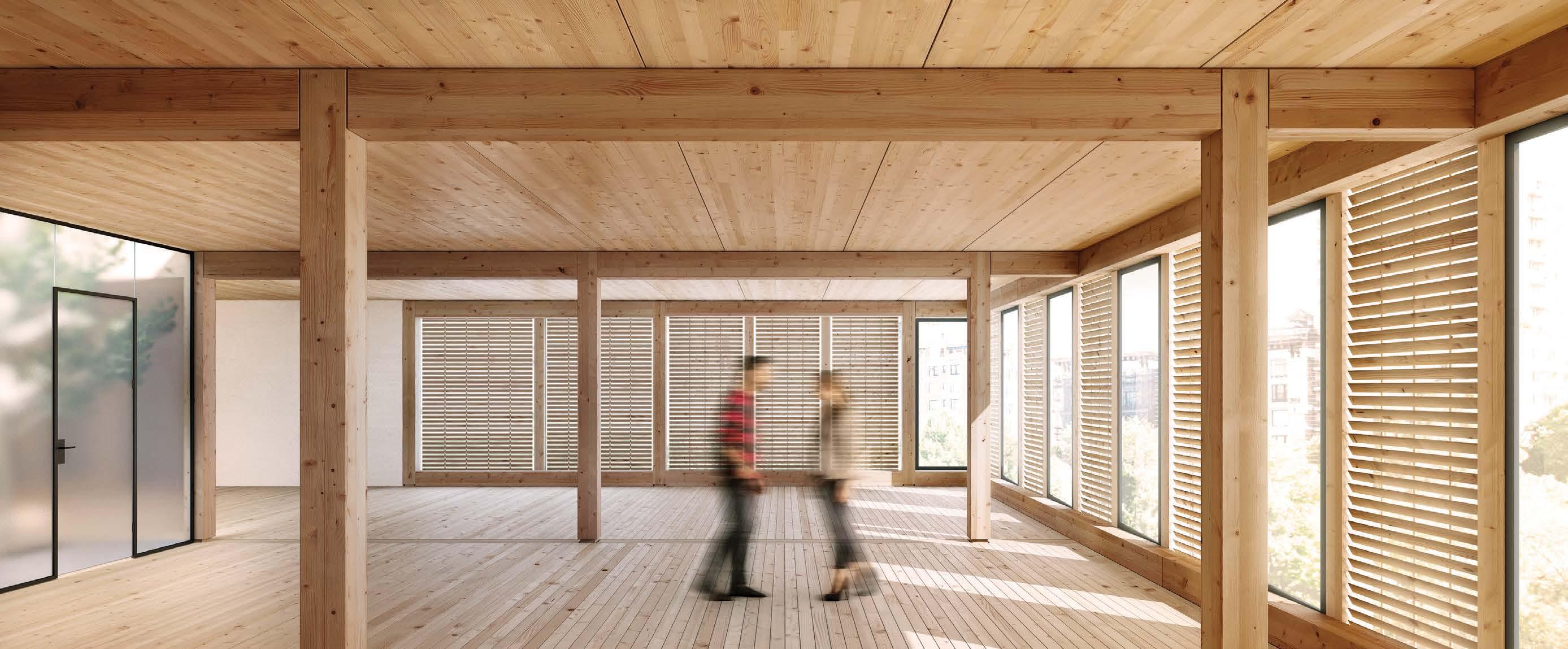
ENHANCE THE SAFETY, STORAGE AND EFFICIENCY OF YOUR LOGISTICS WITH COMBILIFT
For 25 years, Combilift has been revolutionising the way companies handle and store goods. We help companies of all sizes and from every industry to maximise the capacity, safety and efficiency of their warehouse and storage facilities.
Our pioneering product range of multidirectional, articulated and pedestrian forklifts, straddle carriers and container loaders allows you to manoeuvre long loads safely, reduce aisle widths and increase the amount of space available for storage.
CONTACT US TODAY
To find out how Combilift can help you unlock every inch of your storage space.
AUSTRALIA’S timber industry has long been a vital sector, supporting construction, manufacturing, and various other economic activities.
However, in recent years, the industry has faced a significant challenge: oversupply.
This phenomenon, characterized by an excess of timber products in the market relative to demand, has led to various economic and environmental concerns.
Understanding the causes and consequences of this over-supply is crucial for stakeholders to devise effective strategies for sustainable management.
Several factors have contributed to the over-supply of building timber in Australia. In response to growing demand, timber producers have expanded their production capacity significantly. This expansion was often fuelled by technological advancements, allowing for more efficient harvesting and processing of timber. However, the pace of capacity expansion has outstripped the growth in demand, leading to over-supply situations.
AKD Softwoods chief executive Shane Vicary said the company’s Tumut mill at Tumut was processing 500,000 cubic metres of logs but that had fallen to 250,000 cubic metres.
AKD is the largest sawmill company in the country, producing about a quarter of the nation’s timber consumption.
“This mill is doing half the volume that it used to do, and it’ll do half for the next 20-plus years, based on the fact that those logs got burnt,” Mr Vicary told The Australian recently.
Despite this dramatic reduction in production, timber continued to sit on the shelf without being sold, he said.
“We can’t get enough people to buy the timber,” he said.
“At the moment, most of our employees are earning less because there’s less activity. We’ve got overtime bans, we’ve got employment freezes.”
“The depressed housing construction sector is having a major flow through impact to timber manufacturers, who in some cases have had to mothball facilities and restructure workforces because of weak demand,” Australian Forests Products acting CEO Richard Hyett said.
“The great irony with Australia’s housing shortage is that we have timber ready to go to build new homes and be part of the solution to the crisis. But, because of market confidence and conditions, the new homes just aren’t being built right now.
“The Government has a target to build 1.2 million homes by 2029 and they need plan to achieve that goal that includes how to best position the housing construction sector out of the current economic conditions and how timber can be part of the solution, especially in light of the Government’s net zero goal,” he said.
OneFortyOne’s Jess Douglas said the problem was industry wide.
“Everybody is experiencing the same problem at the moment,” she said.
However the situation at Hyne Timber is different with a spokesperson saying demand to production was satisfactory.
“We’re servicing a strong South East Queensland and regional New South Wales and Victorian market,” the spokesperson said.
Hyne Timber, Tumbarumba Site Manager, Kristina Kaminski, said that “the mill manages all inventory levels in accordance with customer demand”.
“Sales largely correlate with a slowed single dwelling residential construction sector,” she said.
Despite Federal and State government policies aiming at increasing supply of housing in an ever more unaffordable market, construction is not moving at a pace to match. February Australian Bureau of Statistics figures show total new dwelling approvals dropped by 9.5% in December 2023
SALES of new homes nationally increased by 5.3 per cent in February from very low levels.
The HIA New Home Sales report is a monthly survey of the largest volume home builders in the five largest states and is a leading indicator of future detached home construction.
“Despite the increase in February, sales remain around the low levels that prevailed in the second half of 2023,” HIA Chief Economist Tim Reardon said.
“The slowdown in sales is caused primarily by the rise in the cash rate which has eroded the capacity of households to borrow and impaired market confidence.
“The slowing in sales and building approvals will flow through to a decade low volume of new houses commencing construction in 2024. The economic impact of this slowdown will be-come increasingly evident in 2024, as employment in the home building industry falls.”
with new houses dropping .5% on November figures.
A number of smaller mills contacted declined to comment on their specific situation, with one saying that to admit to having a surplus may encourage buyers to push for bargain, forcing prices down even further.
HIA Senior Economist Tom Devitt said that the availability of shovel-ready land was also a problem.
“Shortages of shovel ready land saw lot prices surge during the pandemic, while the volume of lots being sold has plummeted to twentyyear lows,” Mr Devitt said.
“This ties in with other data showing the number of homes commencing construction is also lower than at any point in the last decade.
“Alleviating the housing shortages in Australia will require a supply-driven approach, and National Cabinet’s ambition to build 1.2 million well-located homes
Mr Reardon said that higher borrowing costs were compounding the elevated cost of land and construction, drying up the pipeline of new home building work despite the significant pent-up demand for housing.
“The increase in sales in February was observed in most of the large states. Given the weak-ness of January data, it is not all too surprising to see an uptick in February,” he said.
New home sales saw a monthly increase in most large states, led by Queensland (+8.4 per cent), followed by New South Wales (+6.5 per cent), Victoria (+6.3 per cent) and Western Aus-tralia (+5.0 per cent). South Australia saw a 5.5 per cent decline in February.
Sales in the three months to February 2024 were stronger compared to the previous year in Western Australia (+39.9 per cent), Queensland (+20.4 per cent) and New South Wales (+16.0 per cent). Declines were recorded in Victoria (-7.7 per cent) and South Australia (-13.9 per cent).
Issue 2 – Volume 34
Incorporating Australian and New Zealand Timberman. Established 1977.
News 3-13
Strapping and racking 10
Timber Imports 15
Certification 16
Timber preservation 17
Associations 18
FRONT Cover:
The exterior of the Timber Design Award-winning Barker College project in Sydney.
PUBLISHER and Chief Executive:
Hartley Higgins
General Manager:
Robyn Haworth
Editor:
Bruce Mitchell
b.mitchell@ryanmediapl.com.au
Adelaide Office (08) 8369 9512
Advertising: Jon Andryciw j.andryciw@ryanmediapl.com.au
Adelaide Office (08) 8369 9517
Creative Services: Sudapa Rattanonda
Publication Design: Sudapa Rattanonda
Timber classifieds:
j.andryciw@ryanmediapl.com.au
Adelaide Office (08) 8369 9517
Subscriptions:
subs@forestsandtimber.com.au
Adelaide Office (08) 8369 9522
Subcription rates
One-year (6 editions) $44.65
Two-years (12 editions) $77.65
Accounts: ar@winetitles.com.au Phone: (08) 8369 9500
Postal Address: 630 Regency Road, Broadview South Australia 5083
Phone: (08) 8369 9555
Melbourne Office: Suite 2262, 442 Auburn Rd, Hawthorn VIC 3122 Phone: (03) 9810 3262
Find us on Facebook @AustralasianTimber
Website www.timberbiz.com.au
Printed by Lane Print, Adelaide, SA
Conditions
SCION has become a member of The Australian Research Council (ARC) Advance Timber Hub.
This five-year, $16.5 million research initiative was recently launched at The University of Queensland, Australia in the presence of industry leaders, academic partners, and government officials including Senator Anthony Chisholm, Assistant Minister for Education and Assistant Minister for Regional Development.
The primary objective of the ARC Advance Timber Hub is to drive innovation in the Australian mid-rise building market, which represents a significant portion of the country’s construction industry valued at approximately $80 billion annually.
This initiative has the potential to revolutionize both timber processing and construction sectors. By leveraging international expertise in advanced timber manufacturing, the Hub also presents substantial opportunities for optimizing forestry resources, including those in Aotearoa New Zealand.
At Scion, Henri Bailleres and his team, comprising Tripti Singh, Romain Meot, and
Assistant
Education and Assistant
Diego Elustondo, are eager to collaborate with the Advance Timber Hub to explore avenues that can benefit both the industry and forests of Aotearoa New Zealand. Their goal is to foster strong partnerships with the Australian timber building sector, fostering synergy between our nations in a shared market.
Administered by The University of Queensland’s School of Civil Engineering, the ARC Advance Timber Hub
brings together a diverse range of stakeholders including innovators, developers, technology providers, designers, fire engineers, forestry experts, and government representatives.
With participation from 12 Australian universities and five international universities and research institutes, the Hub is poised to drive significant advancements in timber processing and construction technologies.
Scion sees immense value in joining the Hub, as it provides a platform to contribute our innovative expertise and secure opportunities for our resources and timber products. Together, we look forward to shaping the future of timber innovation and sustainable construction practices in Australia and beyond. To learn more please visit www. advance-timber-hub.org.
AT a time when environmental consciousness has become paramount, industries are continuously seeking innovative ways to minimize their ecological footprint.
Timberlink, a leading player in the timber industry, has taken a bold step forward with NeXTimber, a revolutionary product that epitomizes sustainability and versatility.
The NeXTimber by Timberlink facility in Tarpeena in the Green Triangle will manufacture cross-laminated timber (CLT) and glue-laminated timber (GLT) products, providing an Australian-made renewable and carbon-positive timber building solution for commercial, residential, and public projects.
Timberlink’s stringent adherence to sustainable forestry practices ensures that NeXTimber is a renewable resource, contributing to the preservation of our planet’s invaluable ecosystems.
Timberlink CEO Paul O’Keefe said the company was well positioned to play its part in supporting the Australian government’s COP28 commitment to increase the use of timber in the built environment by 2030.
However, NeXTimber’s appeal transcends its ecofriendly attributes. Its innovative engineering imbues it
with unparalleled strength, durability, and dimensional stability, surpassing that of conventional timber.
Timberlink’s unwavering dedication to quality is reflected in every aspect of NeXTimber’s production. Rigorous testing and quality control measures guarantee that each piece meets the highest standards of performance and reliability.
In essence, NeXTimber by Timberlink represents a paradigm shift in the timber industry. By marrying sustainability with innovation, Timberlink has not only redefined the possibilities of engineered wood products but has also set a new standard for environmental responsibility. As the demand for sus-
tainable building materials continues to grow, NeXTimber stands poised to lead the way, paving the path towards a greener, more sustainable future.
Meanwhile, starting this month, we’re transitioning Australian Forest & Timber News to a bi-monthly publication schedule. This change allows us to dive deeper into each issue’s content, delivering richer, more comprehensive stories and features. This shift empowers us to cultivate a stronger connection with our audience, providing them with a thoughtfully curated magazine experience every other month.
TIMBERLINK has officially opened its NeXTimber by Timberlink manufacturing facility and upgraded green mill located in Tarpeena, South Australia. Timberlink CEO Paul O’Keefe said the company was well positioned to play its part in supporting the Australian government’s COP28 commitment to increase the use of timber in the built environment by 2030.
The launch event was attended by more than 300 people, including South Australian Premier Peter Malinauskas, the Minister for Primary Industries, Regional Development and Forest Industries Clare Scriven, District Council of Grant Mayor Kylie Boston, District Council of Grant CEO Darryl Whicker, Member for Mackillop, Nick McBride and CEO of the South Australian Forest Products Association, Nathan Paine.
“This unique facility in South Australia’s Limestone Coast presents tremendous opportunities for value adding, product diversification and market expansion for the state’s $1.4 billion forest industries as well as the ability to contribute to the construction of taller and more complex timber buildings,” Mr Malinauskas said.
“I congratulate the Timberlink team, and everyone involved in delivering this project which will have significant flow on benefits for the Limestone Coast economy and that of the whole state.
“The State Government is committed to a smart, sus-
• (Left to right): South Australian Premier Peter Malinauskas, Minister for Primary Industries, Regional Development and Forest Industries Clare Scriven, Timberlink CEO Paul O’Keefe, SAFPA Chair Tammy Auld, Member for Mount Gambier Troy Bell, Timberlink Chief Sales, Marketing & Corporate Affairs Officer David Oliver, and SAFPA CEO Nathan Paine inside the NeXTimber facility.
tainable and inclusive economic path for increase resilience and competitiveness for our forest industries and is why we were pleased to contribute $2 million of funding towards this new state of the art facility.”
The newly commissioned NeXTimber facility is Australia’s only combined CLT and GLT (Cross Laminated and Glue Laminated Timber) radiata pine mass timber facility, and the first in Australia to be integrated with a structural timber manufacturing plant.
The facility can produce CLT panels up to 16M long and 3.5M wide, and GLT beams up to 12M long. Mass timber products offer an exciting alternative to traditional construction materials and can help to reduce the embodied carbon of a project. These
timber structures can be built up to 12 stories and even taller when combined with other materials in a hybrid timber construction.
Timberlink’s $70M capital investment to build a mass timber production facility was announced in 2020, supported by a $2m grant awarded by the SA government under the Strategic Business Round 2020 of the Government of South Australia’s Regional Growth Fund.
The NeXTimber brand was announced in 2021 with the tagline “It’s what better tomorrows are built on.” Ground was broken with the first sod turn in Tarpeena in 2022 and construction of the site continued until late 2023. The facility has been taking orders since November 2023, a testament to the hard work
of many. The NeXTimber facility has created new jobs not only during the construction phase, but on an ongoing basis with over 30 new full-time positions.
Timberlink’s NeXTimber facility development followed their 2019 announcement of a major timber manufacturing upgrade, with over $90M invested over the following 3 years, installing a new saw line, stacker and edger, contraflow kiln and batch kiln and drying building. This project created over 200 jobs in the construction phase.
“This upgrade to the Tarpeena green mill is a testament to Timberlink’s commitment to innovation through timber manufacturing. By increasing the amount of timber that we can process here in the Limestone Coast region, we are
directly supporting the local economy and jobs in the region,” Timberlink Chief Sales, Marketing & Corporate Affairs Officer David Oliver said.
South Australian Forest Products Association CEO Nathan Paine said innovative technologies such as engineered wood products were a clear example of how timber was influencing the future of the construction industry whilst contributing to a netzero economy.
“South Australia’s forest products industries are already building the nation through growing and processing 35 per cent of the nation’s locally produced house framing timbers, 25 per cent of the nation’s particle board and now this new facility will deliver CLT and GLT products that offer a greener, more sustainable alternative to steel and concrete in mid and highrise construction projects,” Mr Paine said.
“Each year, the South Australian plantation estate sequesters 4.64 million tonnes of CO2e from the atmosphere, making timber the Ultimate Renewable. The CLT and GLT timber products that will be processed by NeXTimber will provide carbon negative mass timber products for use in mid and high-rise constrictions helping create a cleaner, greener future,” he said.
“It is investments like this which generate economic, environmental and social opportunities for the South East, further empowering the forest and timber industries in South Australia.”
AKD’S Caboolture Sawmill Expansion Project is now complete, which will support an internationally competitive sawmilling business for the Sunshine Coast gateway region.
The project was officially opened by Queensland Infrastructure, Transport, Regional Development and Local Government Minister Catherine King and Assistant Minister for Regional Development Anthony Chisholm.
As a result of the project, the site has doubled its production capacity and is currently processing 370,000m3 of locally-grown sawlog.
The upgrades have also enabled AKD to install the latest technology to improve the recovery of structural timber from the sawlog resource – making operations more efficient. The expansion project also installed an acoustic barrier, which has improved the sur-
rounding environment. This has meant production was able to move to a two-shift operation with minimal impact on the local community.
The ability to run the two shifts has created more than 100 new and permanent skilled manufacturing jobs at AKD’s Queensland site. This additional 100 jobs in Caboolture will support a further 763 jobs in the regional economy, according REMPLAN modelling.
The $41 million project was made possible thanks to $10 million from the Australian Government, with AKD providing the remaining $31 million.
“The Australian Government is committed to supporting local jobs, businesses and economies to ensure communities can thrive –which is what the Caboolture Sawmill Expansion is all about,” Ms King said.
“This project will leave a lasting legacy for the region,
by supporting skilled jobs, better environmental outcomes, and a more efficient local sawmilling business.”
AKD CEO Shane Vicary said the project had secured the future of the Caboolture sawmill in Queensland.
“The Caboolture Team has done a fantastic job in delivering the desired outcomes of this project, providing security to existing and new employment, and opening the door for further growth opportunities for the site,” he said.
THE future of sustainable forestry has received a significant boost with the official launch of the Albanese Government’s $100 million Australian Forest and Wood Innovations program.
AFWI is a collaboration between the Albanese Government and the University of Tasmania, committed to advancing research and innovation in Australian forest and wood products.
The University of the Sunshine Coast and University of Melbourne will be invited to form AFWI research centres, joining a third research centre being established at the University of Tasmania (UTAS) in Launceston.
Minister for Agriculture, Fisheries and Forestry, Murray Watt, said the University of Tasmania AFWI Headquarters in Launceston would support a local AFWI research centre, with further centres planned for the University of the Sunshine Coast and the University of Melbourne.
“Establishing AFWI was an election commitment which we are proud to deliver and forms part of our record $300 million investment in the Australian forestry and forest product sector,” Senator Watt said.
“This program will support sustainable forestry, while also helping to deliver a future made in Australia.
“It’s an exciting time for forestry research as we work towards unlocking the full potential of wood as the ultimate renewable material and
• Forestry Minister Senator Murray Watt and the Vice-Chancellor of the University of Tasmania, Professor Rufus Black, unveiled a plaque featuring wood from across Australia, officially launching AFWI.
growing our forests and forestry industry.
“The three research centres will undertake research to enhance our production forests and the wood products sourced from them – managing and sustainably expanding our Australian forestry resources, transforming wood residues into renewable products and energy solutions – all while helping to address the threat of climate change.
“AFWI will draw on the best researchers and facilities across the nation to ensure Australia’s forest and wood products industries remain on the front foot, supporting applied research, development and innovation.
“We saw demand for forest products significantly increase during the Covid-19 pandemic — increasing production in our sustainably managed plantation estate and product recovery from
our sawmills and wood and fibre processing plants will see us better positioned to meet demand into the future.”
The AFWI Board is chaired by Mr Bob Gordon and includes nine other members with industry and forestry research experience, an understanding of workers’ needs, First Nations perspectives and from the Commonwealth.
They include Diana Gibbs, Christine Briggs, Heidi Dungey, Brian Farmer, Michael O’Connor, Rachael Cavanagh, Andrew Leighton, Julianne O’Reilly-Wapstra and Andrew Wilson.
AFWI will create opportunities for innovation and support the development of researchers to support the sectors’ future, building on the work the existing regional National Institute for Forest Products Innovation centres have already delivered.
Senator Watt said AFWI
would also shortly be announcing the opening of the first of four, $5 million annual national open calls for forestry research projects. The annual national open calls will be open to applications from all Australian-based researchers supporting the forest industry, and not be limited to the research centres established by AFWI.
The University of Tasmania’s Vice-Chancellor, Professor Rufus Black, said the university was excited to bring world leading research to answer questions that will help accelerate the role of forestry and wood products in meeting the challenge of climate change and building a circular economy.
“AFWI will provide the skills and knowledge to support sustainable production of wood products, protect biodiversity and multiple forest values, and ensure the national
BIG River Group has announced a strategic rebranding initiative aimed at fortifying its market position by unifying the company’s diverse portfolio of brands to foster synergies and coherence across its business operations.
John Lorente, CEO of Big River Group, emphasised the rebranding is a proactive step to streamline operations, create unity across the business and unlock new opportunities for growth.
• The new Big River logo.
“By aligning our local service excellence with our national scale, we aim to enhance our operational efficiencies while driving excellence and innovation in our solutions to better serve our customers, suppliers, and shareholders,” Mr Lorente said.
“Our rebranding effort signifies more than just a visual transformation; it leverages our extensive experience and service autonomy across the group, empowering the company to adapt swiftly to evolving market dynamics while maintaining a steadfast focus on customer satisfaction.”
Key highlights of the rebranding initiative:
• Brand Architecture: Big River Group’s brand structure will adopt a hybrid approach featuring five key brands: Big Riv-
sector is at the forefront of innovation and climate action,” Professor Black said.
“We are the number one university in the world for climate action according to the Times Higher Education impact rankings and we are committing to supporting the transition to a low-emissions global economy we need to make – wood must play a big part in that future.”
UniSC Professor Mark Brown said the successful bid by the Forest Research Institute to be part of AFWI would allow it to extend its leadership, skills and expertise in this space.
The Forest Research Institute is a collaboration between eight Queensland and New South Wales universities, and three state government agencies from Queensland, New South Wales and the Northern Territory.
It has active partnerships with industries across regional Australia and research sites across tropical and subtropical forests and plantations.
“We look forward to working with the other AWFI regional research centres to make the national institute a success and welcome the strong innovation and collaboration that we will be able facilitate across the sector,” said Professor Brown, who will head the new centre at UniSC.
He said the planned key focus areas for the Queenslandbased centre would be to sustain, manage and rehabilitate Australia’s forests and find innovative solutions for the forest and wood products industry.
er Group as the Masterbrand, with Big River Commercial and Big River Trade Centre as sub-brands, and Timberwood Panels and Plytech Panels as endorsed brands.
• Unified Values: The rebranding initiative will align all Big River Group brands under shared common values, ensuring consistency in delivering exceptional products and services. This unified approach will reinforce the company’s dedication to quality and customer satisfaction.
• Visual Identity: The rebrand encompasses a new logo, website design, and name changes to existing brands, maintaining visual coherence to the Masterbrand, while reflecting the company’s renewed focus on synergy and cohesiveness.
The phased roll-out of the rebranding initiative will commence with the introduction of the new logo, followed by subsequent brand assets throughout the year.
MASS timber has the potential to be a critical building component for the cities of the near future given the need for the construction sector to reduce its reliance on concrete and steel to lower its Co2 emissions.
However, as this market grows and mass timber buildings evolve to greater heights, the construction risk landscape will also be transformed, bringing risk management challenges for companies, according to the new Emerging Risk Trend Talk report from Allianz Commercial.
“The emergence of mass timber as a sustainable construction alternative represents a significant opportunity for the building sector to reduce its carbon footprint while also satisfying a demand for a material that is more cost-efficient but as durable as steel and concrete,” says Michael Bruch, Global Head of Risk Advisory Services at Allianz Commercial.
“However, in any industry, deployment of new materi-
als or processes can result in new risk scenarios, potential defects, or unexpected safety consequences, as well as bringing benefits, and mass timber is no different. Given this market’s expected future growth, companies should do all they can to develop a greater understanding of their exposures including fire, water damage, repetitive loss scenarios and even termite infestation, and ensure they have robust loss prevention measures in place to combat these.”
The building and construction sector is among the largest contributors to Co2 emissions, accounting for over 34% of energy demand and around 37% of energy and process related Co2 emissions in 2021 [1]. Given emissions reduction is essential to meet climate change commitments around the world, the need for more sustainable solutions in the built environment has become increasingly important, driven by growing investor and consumer concerns, and legislation, regulation and reporting requirements evolving quickly
• As the market for mass timber grows the construction risk landscape will also be transformed according to a report from Allianz Commercial.
in many jurisdictions around the world.
Mass timber is a relatively new type of engineered construction in which most products comprise multiple wood pieces joined together to form larger, stronger members, which can then be used for roofs, floors, and walls. It is often combined with traditional
non-combustible structural materials to create a hybrid mass timber construction style, allowing high-rise timber structures to be built more sustainably – the height of the world’s tallest timber building has tripled in just 10 years, with 140 mass timber buildings around the world of eight stories or higher as of February
AS mass timber buildings evolve with greater height and intricate designs, they will pose new challenges in terms of risk mitigation.
The Allianz Commercial report identifies several of these hazards and challenges with Allianz Commercial risk consulting engineers also highlighting loss prevention measures to consider that could help to reduce their impact:
1. FIRE
Mass timber is still wood, and fire is the primary hazard concern, with this risk needing to be considered through all the life stages of a building – design, construction, and operation. Fire is already the most expensive cause of all construction / engineering insurance losses, accounting for more than a quarter (27%) of the value of 22,000 claims analyzed over a five-year period, according to Allianz. The risk of collapse during the cooling phase of a fire may be particularly critical for timber elements, while buildings
with combustible elements are at the highest risk of fire during construction. Once a building is in operation, the risk of fire can increase depending on factors such as the type of occupancy, storage, and interior fittings. Ongoing research and testing are being conducted to further develop a methodology for evaluating the performance of structural elements during the entire duration of a fire. This includes comprehensive studies of the heating and cooling phases as both phases are especially crucial for evaluating the behavior of timber elements and ensuring optimal fire safety.
2. NATURAL HAZARDS
Damage from natural catastrophes is already the second most expensive cause of construction claims, Allianz analysis shows. Extreme wind forces, especially during tornadoes or hurricanes can potentially affect beams, columns, and panels, posing a risk of widespread damage, while floods, including
river floods, flash floods and storm surges, pose a significant risk to timber buildings. Timber buildings exposed to floods may require structural controls, drying and repairs, impacting expected operating losses.
3. WATER DAMAGE
Similarly, water damage is already a major source of loss across the construction sector. Mass timber is highly vulnerable to water damage including flood, water ingress, and plumbing leaks. To mitigate water damage, mass timber elements can be manufactured with reduced moisture content and stored in controlled atmospheres. Water management and high-quality analysis are crucial for ensuring the durability of structures.
4. MANUFACTURING, TRANSPORTATION, AND SUPPLY CHAIN ISSUES
Mass timber construction has a unique supply chain and manufacturing process that differs from traditional concrete and steel framing.
2022, with 70% of these in Europe [2].
Although mass timber currently only represents a tiny proportion of the overall number of buildings constructed worldwide each year – for example, just over 2,000 residential, commercial, or institutional mass timber projects were in progress or built in the US, as of December 2023, according to the Wood Products Council [3], nevertheless, from mixed use developments to hotels to schools, an emerging market is underway. The global mass timber construction market generated US$857mn in 2021 and is forecast to hit $1.5bn by 2031, with a CAGR of 6.0%, according to Allied Market Research [4].
References [1] UN Environment Programme, 2022 Global Status Report for Buildings and Construction [2] Council on Tall Buildings and Urban Habitat, The State of Tall Timber: A Global Audit, February 2022 [3] WoodWorks, Wood Products Council, Mapping Mass Timber [4] Allied Market Research, Mass Timber Construction Market to Reach $1.5 Billion, Globally, by 2031 at 6.0%CAGR, May 3, 2023
Factors such as the need to have specialized production facilities, as well as just-intime delivery, means thorough logistical planning and management of building materials are essential to avoid costly project delays. One significant disadvantage of the assembly line manufacturing process is the potential for a serial loss scenario. If a particular batch of mass timber elements has a defect, multiple elements in a structure or across project sites may be affected. Defective products is already the third costliest cause of construction /engineering insurance claims, according to Allianz.
5. FAULTY WORKMANSHIP ISSUES AND REPAIR COSTS
Construction firms may face challenges in finding experienced work crews for mass timber construction projects, given its nascent status. This can result in productivity issues and safety concerns as crews navigate the learning curve of working with mass
timber. Inadequate installation can result in damage which can have significant financial implications for repairs or replacements, while in some cases the cost of repairing or rebuilding mass timber structures could be significantly higher than those made with conventional construction materials.
6. TERMITE AND INSECT INFESTATION
While not common in all areas of the world, termites and other wood-boring insects may pose a significant threat to mass timber buildings, potentially causing extensive structural damage over time. Given termite infestation usually occurs gradually, the exposure of notable damage during the construction phase is low compared to the operational phase. However, as termites are most likely to attack decaying timber in buildings it is important to ensure timber does not have long periods of contact with water by implementing sufficient protective measures.
THE extensive use of mass timber, including CLT and Glulam, was a major factor in Barker College Senior Student Hub at Hornsby in Sydney collecting last year’s Timber Design Award for excellence in timber design.
Located in the Sydney suburb of Hornsby, the $17.83 million Student Hub boasts a distinctive structural frame constructed from engineered timber.
The architects, Architectus, said the award was great recognition of Barker College’s commitment to sustainable design. The extensive use of mass timber, including CLT and Glulam, reduced the building’s carbon footprint while creating an aesthetically pleasing and sustainable solution.
The project utilised a variety of timber types, including:
• Cross-Laminated Timber made from Australian plantation-grown Radiata Pine, was
a primary material used in the project. It was utilised in various applications such as floor systems, cores, and stairs.
• Glue-Laminated Timber made from European Spruce was used for columns, beams, and bracing elements, providing structural support and enhancing the building’s visual appeal.
• Solid Spotted Gum was chosen as a feature material in the ceilings, internal screens, stair trims and finishes. It was chosen for its durability, aesthetic appeal, and sustainability and used in combination with European Oak engineered timber flooring for the stairs and key breakout spaces.
The architects said that by incorporating timber into the design, the project not only offsets 780tCO2e of embodied carbon via sequestration, but also created a warm, inviting, and healthy learning environment for students.
The mass timber used in
the Barker College Maths and Student Hub project was supplied by XLam for the CLT products and HESS for the Glulam timber products.
Architectus says its involvement in the Barker College Maths and Student Hub project represents a continuation of its commitment to advancing mass timber construction.
“Building upon our experience with mass timber projects such as the Macquarie University Incubator and Macquarie University Ainsworth Building, both of which were full mass timber constructions, the Barker College project presented a unique opportunity to explore hybrid solutions,” the architects said.
They said that while its previous projects embraced a full mass timber construction approach, Barker College required a hybrid solution that integrated timber for the upper two levels and concrete elements at the base.
“This challenge allowed us to innovate and adapt our expertise to create a building that optimises the unique benefits of both materials,” the company said.
“We remain committed to exploring new opportunities in mass timber construction, leveraging our experi-
ence and expertise to create buildings that are not only functional and beautiful but also environmentally sustainable and inspiring.”
Architect: Architectus
Structural Engineer: TTW
Builder: Buildcorp
Fabricator:Photographer: Brett Boardman
Sponsors:Location: Kuring-gai Country, Sydney, New South Wales
THE Cathedralette House in Brunswick, Victoria – named for its cathedral ceiling and proximity to a heritage timber chapel nearby – is an example of what is possible on a narrow site with a tight budget.
Luke Middleton and his team at EME Design used sustainable timber veneers and other wood products to deliver an economical build without sacrificing comfort and warmth.
Despite the narrow block, sunlight fills the living space where it is reflected by plywood ceilings and walls. Generous plywood lined eaves provide shade in summer. When EME entered the Cathedralette in the Australian Timber Design Awards they emphasised that “Plasterboard has no place in this
PETER LLEWELLYN Technical
representative, Timber Veneer Association of Australia
eco design. There is no steel in the structure, which celebrates the strength and buildability of renewable timber”.
Walls and ceilings are plywood with a whitewashed radiata pine face veneer. Victorian ash veneer was selected for joinery throughout the home. A factor in selecting Vic ash veneer was the desire to avoid a busy or complex
grain structure which the architects considered would take away from the calm ambience desired.
Referring to Vic ash veneer, architect Luke Middleton stated that “the light honey colours and grain structure provide a timeless look”. In his opinion, “too often the calm and natural beauty of local Vic ash is overlooked”. Vic ash veneer complemented blackbutt solid timber benchtops and engineered timber flooring.
Sustainability and low embodied energy were important factors in the choice of materials, combined with careful attention to operational energy use inside the house. The house has no glazing to the western elevation and interior spaces are zoneable so heating only
needs to warm occupied areas. Strategically positioned windows allow effective cross ventilation.
The Cathedralette is an outstanding example of how a minimal carbon footprint can be paired with maximum functionality when timber ve-
neers and wood products are sensitively combined.
For more examples of the use of timber veneers in the built environment click on the “About Veneer” tab on the Timber Veneer Association of Australia’s website and go to the Project folder.
BEDFORD has officially unveiled new state of the art equipment at its timber manufacturing facility in Mount Gambier, as part of a $7m investment in the region.
The upgrade is set to double production capacity, drive greater efficiencies and broaden timber processing services at its timber manufacturing facility.
The mill has also ordered an automated grader and cross cut saw through System TM as part of the upgrade. Additional equipment in the future will include a LMC823 Speedmac moulding machine (moulder), infeed to moulder and outfeed from moulder.
Bedford chief executive Myron Mann said the investment strengthened its commitment to building capabilities, partnerships and opportunities.
“We are thrilled to officially launch major infrastructure upgrades and new facilities at our Mount Gambier site,” he said.
“Our investment in advanced manufacturing demonstrates our long-term commitment to being a sustainable supply chain partner in the local community, taking waste timber and adding value and finishing services
across a range of products.”
Mr Mann said currently Bedford partners with local industry to manufacture products such as picket fencing and decking.
“The introduction of new infrastructure including a filtration system is set to build on this and deliver additional environmentally sustainable practices into Bedford’s manufacturing process,” he said.
“The introduction of a new filtration system at our tim-
ber mill demonstrates our commitment to an environmentally sustainable model of manufacturing, where nothing goes to waste.”
The new system - supplied by Leda Machinery - collects timber extracts from the manufacturing process, which is utilised across other industry, such as materials for duck nests.
Mr Mann said included in Bedford’s investment in the region was a new Learning
Continued from Page 9
in five years is a step in the right direction.
“It would further require the release of more shovelready residential land into the market, which the data suggests has fallen to levels inconsistent with required levels of home building.”
Jay Branson from Dewllingup Mill in Western Australia just south of Perth agreed that lack of available land to build on was an issue in his State.
“And people can’t afford to pay for it to build a house,” he said. “It’s a multi-tiered problem.”
CoreLogic Economist Kaytlin Ezzy said the continued increases in land prices, despite a higher interest rates environment, growing affordability constraints and, recessionary low levels of consumer sentiment, indicated just how constrained the supply of shovel ready land is.
“The government’s plan to provide 1.2 million new homes within five years is already an ambitious goal and would exceed the current record for five-year completions, recorded over the five years to December 2019 (1.045m), by almost 15%,” she said.
“While the growth trend in construction costs appears to be normalising, helping to provide assurance for builders and potential new home buyers, without a sufficient and consistent release of shovel-ready land, it will be an increasingly difficult goal to achieve.”
As a consequence, and despite the demand for housing, construction activity remains stubbornly slow.
and Experiences Hub, which was co-located on Bedford’s timber mill site and opened last September.
“The purpose-built hub offers skill-based learning and experiences for the local community, with its core purpose to build learning and capacity across the region to support people with disability to live the life they choose,” he said.
- SE VOICE
“Yes, for all these reasons, and the availability/affordability of land, the residential construction sector is moving too slowly compared to demand for housing and population growth across Australia. This isn’t expected to improve in 2024,” said Kaminski.
Kaminski said Hyne is watching the market and prides itself in their “ability to plan for market conditions”.
“There are no planned site shutdowns in response to the slowed market. We are closely monitoring our industrial product sales which have been impacted by a general downturn in economic activity,” she said.
PHILIP HOPKINS
TWO landmark advanced manufacturing timber buildings – one in Melbourne and the other in Bendigo – have been completed using regrowth hardwood from ASH in Heyfield.
The buildings are two of the most important projects in the state’s growing use of engineered timber for construction.
Hines, a global real estate investment, development, and property manager, has completed the firm’s mass timber office building in Melbourne. Jackson Clements Burrows were the architects and ICON Construction was the builder.
In Bendigo, the Government Hub, which is mainly built from timber, is open for business and can house up to 1000 Victorian government and local government workers. Lyons Architecture designed the project, while ICON along with Fairbrother Construction were the builders. Both buildings have CLT (cross-laminated timber) from Xlam Australia in Wodonga and GLT (glue-laminated timber) from ASH.
Hines’ T3 Collingwood (T3 stands for ‘timber, talent and technology’) is the tallest mass timber office building in Melbourne and is helping to drive the demand for highquality, green office buildings.
Hines says building with timber, as opposed to concrete and steel, results in big savings in embodied carbon.
The timber stores carbon dioxide sequestered by the growing tree in contrast to the vast amounts of CO2 used to produce a concrete and steel structure.
Located at 36 Wellington Street in the suburb of Collingwood, the 18,200-square-metre, 15-storey timber office building adds to Hines’ global portfolio of 26 timber assets in various development stages across North America and Europe as of 2023.
“These ‘magnet buildings’ are sustainability-driven, well-located, technologically efficient, and adjacent to transit. They’re more than just office buildings. They’re places for building culture, collaboration, and community,” Mr Warneford said.
makes it the tallest timber structure in Australia – a mixture of certified CLT and GLT.
Ms Lees said when the timber concept was first mooted, Hines assumed it would use European spruce, but opted for ASH regrowth hardwood.
Several reasons showed that Australian timber was a viable option.
“Cost – that always comes into it. The saving on shipping was a fairly high percentage of dollars,” she said.
“Time – having it local, three hours away, was a saving. All that ties into risk; it
Technology has caught up now –you build it in the boardroom and then the robots go and make it for you
“We’re seeing a strong pivot towards ESG adherence, as well as towards core central locations, among today’s tenants both are expected to underpin growth for the prime end of the office market in Australia,” said David Warneford, country head of Australia and New Zealand at Hines.
“Demand is there, and we see good locations and premium green buildings leasing.”
In fact, the mass engineered timber in the Bendigo building inspired Hines when it was planning Wellington. “We loved the timber; we saw what they were doing,” said Hines construction manager, Jo Lees.
The Wellington St commercial building has two levels of basement, six levels of concrete podium and nine levels of timber structure, which
was a less risky proposition going local – there is better control over shipping, more quality control.”
ASH also knew the industry in Australia – the installers, the contractors and the delivery.
Ms Lees said ASH’s managed regrowth hardwood was a different colour, darker than European spruce and stiffer.
“The stiffer timber beams and columns could be more slender, using less wood for the same structural result,” she said.
The Wellington St building has 970 cubic metres of hardwood GLT as beams and columns, and 2350 m3 in CLT made from radiata pine. About 30 per cent of the GLT volume is columns and 70 per cent beams.
“The beams and columns are all exposed – a great feature,” Ms Lees said.
ASH’s national business development manager, Daniel Wright, said unlike at Bendigo, his company was involved in design and detailing at Wellington.
“How the joints and connections work – we helped with that to make sure it was cost efficient, manufactured in time and looks good,” he said. ASH also had more input into the beams and columns on Wellington.
“The structural strength in our hardwood is incredible; its strength-to-weight ratio compared to its price is internationally incredible. We have lots of data with fire testing; we understand how the wood performs in fire and how safe it is,” he said.
At ASH, production started
with CNC – ‘computer numerical control’; big robotic timber processors cut and moulded the timber to meet the requirements of the connections. The company created a 3D model, with the full building in virtual reality.
“Every member, every screw in that model is millimetre perfect. From that we take a shop drawing with every individual piece,” he said. By rotating a beam on the computer, for example, improvements were made before manufacture.
Mr Wright said the shop drawing fed through to the company’s robots.
“The robots have their own program that actually determine the best tools to use – drills, saws, milling units, chain saws,” he said.
The machine, which has 160 tools, chose the best tool to make the cut, although the technician “can override that”.
“Technology has caught up now –you build it in the boardroom and then the robots go and make it for you,” Mr Wright said.
In contrast, the Bendigo building is only four-storeys, but has a huge floor plate and big floor space – 20,000 square metres overall including a car park, with a 13,000m2 building. The vast majority of the building is also timber.
Cores anchor the building, but “everything wrapping around is timber”, said Lyons architect, Adam Pustola.
The beams and columns, as in Wellington, are Glulam from ASH, while the floor slabs in most of the building are mainly CLT from X-Lam. The building has 256 columns and 469 beams.
Sustainability is enhanced by photovoltaics on the roof that offset some of the energy usage, efficient air quality monitoring systems and water and energy monitoring. There is a lot of highperformance double-glazed glass, which is screened with louvres.
Mr Pustola said the design also exposed a lot of the timber, which is both structure and finish. “We have almost all the beams and columns on show, while half the CLT is on show,” he said.
With sustainability a key issue, showing the attractive timber structure removes the need to add materials, such as cladding and joinery, that hide the traditional structure.
“The interior, the public space, is warm and based on biophilic design,” he said.
“This ‘nature connected’ design philosophy, as explained in Planet Ark’s report, ‘Wood – Nature Inspired Design’, outlines how using wood in an office brings nature indoors. It creates a wonderful, warm natural environment to work in, spacious,” said Mr Pustola.
- GIPPSLAND TIMES
The woodworking industry thrives on precision and productivity, especially when it comes to GLT, CLT and large panel applications. Elevate your production with the game-changing Costa K-Series sanders.
Optimize your Glulam manufacturing process with Costa's robust calibrating solutions.
•Process panels up to 3700mm wide and 300mm thick
•Achieve exceptional results across a wide range of materials, including Particle Board, Fiberboard, Plywood, CLT, and even Glulam.
•Address imperfections like soiling, adhesives, and press marks with post-pressing sanding.
Discover how Costa wide belt sanders elevate mass timber sanding to unprecedented levels.
The Stirling Group proudly serves as the exclusive distributor of COSTA Sanders machines for Australia and New Zealand.
Aurecon has committed $200,000 in funding and inkind support as a Principal Partner of the $16.5 million ARC Industrial Transformation Research Hub to Advance Timber for Australia’s Future Built Environment, administered by the University of Queensland.
The aim of the hub is to develop the resources, enablers, and drivers to advance timber, as a natural resource, to be the material of choice, leading towards a net zero future for Australia’s built environment.
Aurecon is involved in various nodes including Performance of Building Components, Manufacturing Innovation, Towards a Low Carbon and Circular Economy and Building Performance for Occupants.
The HOMAG Group has announced their sales and earnings performance for the 2023 fiscal year, citing “high figures” but a decline in “order intake” that reflect the weak demand that persisted since Q3 2022.
The company said the preliminary figures showed it was able to slightly increase its sales revenue to €1,625m from the previous year of €1,602m.
The slight increase in sales is also reflected in earnings before extraordinary effects, which rose by around 4% to €129.7m from the previous year of €124.8m.
Timber Unlimited in New Zealand is seeking input to help understand the potential drivers, incentives and barriers for uptake and acceptance of engineered wood products (EWPs) across the building industry in New Zealand.
The survey will help identify where and how EWPs are being used across the New Zealand built environment, from acceptance and design through to supply and delivery of completed buildings.
The survey can be found at https://branz.syd1.qualtrics. com/jfe/form/SV_ewVRwzZUP5ZUQGG
BEST described as a customer centric business, Western Australian manufacturing company, Vekta Automation has grown to become one of the most trusted automated machine suppliers for the timber frame and truss industry – both locally and beyond our borders.
In 2007, Mechatronics Engineer (and Vekta Automation Managing Director), Ed Serrano spotted an opportunity in the Razer – a linear saw developed for the timber construction industry. After securing the rights to purchase the Razer and its IP, Ed set up Vekta Automation from an unpowered shed on his Beckenham property.
He worked to improve the functionality and performance of the Razer and to reduce the costs associated with its operation.
“We were taking on a failed product with a terrible reputation. Every time one of these machines was built, it was done so at a loss. This was a major challenge for us – to spin that around and change the reputation of our core product, but we did it and it has been a hugely challenging and satisfying process” he says.
In addition to the constant innovation of products, Vekta Automation prioritises developments that promote safety.
“This is one of our core values – ensuring that everything
we do creates safety for the user.”
Today, this family-owned business manufactures a range of automated equipment for the building industry and has over 100 employees around the globe.
In addition, the company’s flagship machine, the Razer, enjoys majority market share in Australia and New Zealand.
“We are continuously innovating and developing the Razer, improving the software, and developing the machine’s efficiency and reliability. Our competitors have not been able to replicate this,” Ed said.
The Razer enables automated, accurate and rapid cutting of timber for roofing and walling, “For our customers who supply prefabricated timber roofs and walls, this machine improves safety and enhances operations, making it possible to deliver ready-made timber products to construction sites, faster,” Ed said.
Chief among the industry challenges that Vekta Automation and the Razer address, is the current labour shortage, and the growing demand for fast turnaround times.
“One of the key issues facing our customers is access to labour. There are fewer people willing to work in the manual labour-intensive construction industry,” Ed said.
This is where the Razer (and Vekta product line) come in, carrying out the material han-
dling jobs that might otherwise require the work of many human hands.
“Another challenge for the industry is material shortages. Timber is becoming harder and harder to get, so being able to optimise the available materials and reduce waste, is a major driving factor for our customers,” he said.
Ed’s background as a robotics engineer set the foundation for Vekta Automation’s approach to innovation.
“We approach industry challenges as an engineering problem, and we set about solving those issues. This is what really keeps bringing our customers back. We’re not stagnant and we’re not replicating what others have done. We invest in R&D and innovation, developing solutions for very specific problems and needs within our industry.”
Ed is very proud of the company culture, pointing out that Vekta Automation is a family-first company, and has built strong relationships with employees as well as suppliers and customers. In spite of the company’s rapid growth, Ed and his team are committed to maintaining this distinct culture that puts people first.
“In fact, this is what we really love about SMC – the people.”
Key to Vekta Automation’s success has been the company’s partnership with leading global automation specialist,
SMC Corporation Australia New Zealand.
Ed explains that Vekta Automation has worked closely with SMC since the beginning.
“We view them as a partner. They’ve always assisted us – from the early days of setting up the business, to the development of new products. It’s important for us to partner with experts who can fill the gaps in our expertise. We can rely on SMC to help us engineer solutions – particularly on the pneumatics applications. Their products are clever and innovative. Their approach to customers makes them stand out and has made us a loyal partner of theirs.”
Murray Hofstee, SMC Regional Sales Manager, said that his company’s relationship with Vekta Automation had not been based on selling more products or the latest and greatest in our catalogue, but instead, on identifying the solution that’s right for their business, and ensuring that these products are widely available and well-supported in Australia, New Zealand, and the USA.
As a result, Vekta Automation used a vast suite of products from SMC, and trusted SMC to select the right products for its needs and applications.
of Queensland researchers have found improving timber production efficiencies by just 5% could unlock supply for an extra 8000 homes to be built in Australia each year.
The industry supported modelling was carried out at the $16.5 million Australian Research Council to Advance Timber for Australia’s Future Built Environment (ARC Advance Timber Hub) at UQ.
Associate Professor Joe Gattas, who co-leads two research areas at the Hub, said supply chain efficiencies could result in more affordable and sustainable housing options for Australians.
“Early consultation with our industry partners has shown us where efficiencies can be made across all stages of the forest to building supply
chain,” Dr Gattas said.
• Supply chain efficiencies could result in more affordable and sustainable housing options for Australians.
“Our research will investigate how to deliver these improvements using new technologies such as computer vision and artificial intelligence to get more usable material out of each tree and augmented reality and robotics to enhance productivity for time-consuming and repetitive tasks.
“Every gain in the supply chain allows more houses to be built and we hope this will increase the use of Australian-grown timber as a more sustainable choice for construction.”
Hub Director, Professor Keith Crews, said the research would encourage growth in the timber industry and identify new ways the material could be used in construction.
“We all benefit from more
timber in construction – by delivering a boost for industry and supporting sustainability targets because timber removes carbon from the environment and stores it,” Professor Crews said.
“Timber has a key role in helping Australia transition to a circular and net-zero economy.
“While timber is commonly used in smaller dwellings such as housing, we are working with the State Government and industry to look at ways it can be incorporated into larger projects such as athlete accommodation for the 2032 Brisbane Olympic and Paralympic Games.
“Making more timber available will also help support the Australian Government’s National Housing Accord to deliver 10,000 affordable homes over the next 5 years.”
Federal Assistant Minister for Education, Senator Anthony Chisholm, said the Advance Timber Hub funded through the ARC’s Industrial Transformation Research Program, demonstrates the benefits of investing in publicly funded research in Australia.
“Australians want our country to be a nation that makes things through sustainable practices, but this can only be done when we back initiatives like the ARC’s Linkage Program, which promotes innovative national and international research collaboration and partnerships with global suppliers,” Senator Chisholm said.
“The Advance Timber Hub will enable an advanced manufacturing transformation of Australia’s timber and construction industries, support-
AUSTRALIAN Sustainable Hardwoods has recently purchased a new Hundegger RobotMax at its Heyfield plant in Victoria, its third robotic CNC machine.
The state-of-the-art machinery will significantly increase MASSLAM capacity and continually deliver the highest-quality mass timber solutions.
“The state-of-the-art machine will be ASH’s third robotic CNC and comes with unique processing capacity and ability which we were not able to find elsewhere. It compliments the processing ability our other CNC’s to increase our offering,” ASH’s National Business Development Manager Daniel Wright said.
“The three CNCs will be critical as we double capacity and develop our pre-fabricated mass timber social housing solutions utilising Plantation Oak.”
Hundegger’s RobotMax sets a new standard in mass timber production with unmatched performance, versatility and flexibility. Complete with an overhead 5-axis saw/slot/marking unit for higher throughput and 6-axis technology with 32 different tools, the machine provides an incredible improvement in efficiency allowing all six sides of one member to be processed in a single pass.
Arguably the greatest benefit of investing in this technology is the ability to process timber up to 610mm
x 1300mm, significantly increasing ASH’s capacity to provide larger MASSLAM member sections to meet the growing demands of the mass timber market and achieve architectural excellence.
“The addition of the Hundegger RobotMax will dramatically increase throughput as we will be able to CNC machine large member sections for a single project and/or multiple projects simultaneously,” MASSLAM Engineering Design Manager Nathan Benbow said.
The RobotMax joins two existing Hundegger robotic machines at ASH – a Speedcut 3 (built for speed via simpler CNC machining) and a K2-Industry which allows almost unlimited machine capabilities.
ing resource diversification and creating new opportunities for regional development and employment.”
Acting ARC CEO, Dr Richard Johnson said the linkage program is all about bringing together researchers and industry partners to drive innovation and translation.
“The ARC is pleased to support this Research Hub, which involves strong collaboration among national and international universities and industry partners, to stimulate rapid growth in innovation in the timber industry,” Dr Johnson said.
Partners include researchers from 12 Australian and 5 international universities and research institutes working in collaboration with 28 industry partners.
THE University of Tasmania in collaboration with WoodSolutions has launched a pilot micro-credential course on Timber Design for Residential Construction.
The micro-credential is a structured to make upskilling and stacking credentialed education accessible to busy professionals and students. The course incorporates materials and knowledge from leading industry experts to enable students to learn through real-world case studies and models.
Ideal for engineers, architects, building designers, and other professionals involved in construction planning and coordination, the microcredential is delivered online with flexible options for selfpaced learning and opportunities for networking with industry professionals.
This collaboration provides access to all the latest knowledge and practices for a cutting-edge curriculum. It also provides up-to-date information on industry standards for students to complete the course with practical knowledge that can be applied on the job.
Completion of the microcredential opens pathways to further studies at the University of Tasmania, including credit options for engineering degrees. The micro-credential units are designed to accommodate the busy lives of professionals and to ease the financial strain of traditional education and upskilling.
The micro-credential equips individuals with specialised skills and knowledge in timber design for residential construction to meet the demands of the sector. This certification can help address professional shortages in Australia by providing a pool of qualified individuals ready to contribute effectively and efficiently to projects.
The micro-credential course is funded by the Australian Government Micro-credentials Pilot in Higher Education. This means zero fees for students. You can find more information and register your interest for the course at https://www.utas.edu.au/study/ short-courses/micro-credentials/timber-design-for-residential-construction-microcredential
TIMBER, a versatile and essential material, has been a cornerstone of construction and various industries for centuries.
Timber yards play a crucial role in processing, storing, and distributing timber products. Among the myriad practices employed in timber yards, strapping and racking emerge as indispensable methods.
These techniques not only enhance efficiency in handling timber but also contribute significantly to the preservation and quality of the wood.
1. PRESERVATION OF TIMBER QUALITY:
Strapping and racking are paramount in preserving the quality of timber. Timber, being a natural material, is susceptible to external factors such as moisture, pests, and physical damage. Strapping involves binding together individual pieces of timber into compact units. This not only facilitates easier handling but also minimizes the risk of warping and twisting, which can occur when timber is left unsecured. Additionally, strapping acts as a protective barrier against environmental elements during storage and transportation, safeguarding the wood’s structural integrity and appearance.
Racking, on the other hand, is the method of stacking timber systematically on shelves
or racks. This technique ensures proper air circulation around each piece, reducing the likelihood of mold and fungal growth. Properly racked timber also minimizes the risk of insect infestations, as pests are less likely to thrive in well-ventilated and organized storage environments. In essence, strapping and racking work in tandem to enhance the longevity and quality of timber products.
2. EFFICIENT HANDLING AND LOGISTICS:
Timber yards are bustling hubs of activity, where the efficient handling of large volumes of wood is essential. Strapping plays a crucial role in bundling together similarsized and shaped timber pieces, creating manageable units for transportation and storage. This not only simplifies the loading and unloading processes but also optimizes space, allowing for more efficient use of storage areas. Racking, meanwhile, facilitates organized storage, making it easier for workers to locate and access specific timber products when needed. Properly racked timber reduces the time and effort required for inventory management and retrieval, contributing to overall operational efficiency. In the fast-paced environment of timber yards, where timely deliveries and accurate stock management
are imperative, strapping and racking emerge as key contributors to streamlined logistics.
3. SAFETY CONSIDERATIONS:
Safety is paramount in any industrial setting, and timber yards are no exception. Strapping and racking play a pivotal role in ensuring a safe working environment. Strapped bundles reduce the risk of loose timber pieces falling during handling or transportation, preventing potential injuries to workers and minimizing damage to the timber itself.
Racked timber promotes a clutter-free workspace, reducing the chances of accidents caused by tripping over scattered materials. Additionally, organized storage makes it easier to implement and maintain safety protocols, such as clear pathways and emergency exits. The value of strapping and racking in timber yards extends beyond operational efficiency; it encompasses the well-being of the workforce and the overall safety culture within the industry.
4. ENVIRONMENTAL SUSTAINABILITY:
In an era where environmental sustainability is a global priority, the practices employed in timber yards play a role in reducing the industry’s ecological foot-
print. Strapping and racking contribute to sustainability by minimizing waste and optimizing resource usage. Well-strapped timber bundles reduce the likelihood of damage during transportation, ensuring that a higher percentage of the harvested wood reaches its destination in usable condition.
Organized storage through racking reduces the need for excessive space, allowing timber yards to operate with smaller physical footprints. Additionally, the prevention of timber degradation through these practices reduces the demand for replacement materials, further contributing to environmental conservation.
The value of strapping and racking in timber yards extends far beyond mere operational processes. These practices are integral to the preservation of timber quality, efficient handling and logistics, safety considerations, and environmental sustainability. As the timber industry continues to evolve, the adoption of these methods becomes not just a matter of convenience but a strategic imperative for ensuring the longevity and relevance of the industry in a rapidly changing world. Strapping and racking stand as testament to the industry’s commitment to excellence, safety, and environmental responsibility.
US hardwood timber exports to Australia increased by 22 per cent in 2023 to a value of $US21million according to data from the United States Department of Agriculture.
While American white oak continues to dominate, its lesser-known cousin, American red oak, has shown extraordinary growth over the 12-month period.
In 2023 Australia imported nearly 9000 cubic metres of red oak which is the most abundant species in the American hardwood forest. Readily available, and of a consistently high quality, red oak has similar characteristics to white oak in terms of strength and stability, but its more open grain means it is more suitable for staining which makes it a more versatile choice.
“We’ve had a significant amount of interest in red oak from the savvier specifiers in Australia recently,” Regional Director for the American Hardwood Export Council Rod Wiles said.
The American Hardwood Export Council is an international trade association for the
US hardwood industry, representing exporters among U.S. hardwood companies and all the major US.
hardwood production trade associations. AHEC runs a worldwide program to promote American hardwoods in over 50 export markets, concentrating on providing architects, specifiers, designers, and end-users with technical information on the range of species, products and sources of supply. In addition, AHEC also produces a full range of
technical publications.
“They recognise its quality and value and have anticipated the shift in demand resulting from the changes in native logging that came into force this year.”
The new figures also show growth for other underutilised but available species including American cherry and American maple which have seen volume increase by 650% and 110% respectively.
“Australia and New Zealand remain important markets for
INDIA IMPORTS UP
The total value of exports of US hardwood lumber and veneers to India in 2023 was US$8.482m, according to the American Hardwood Export Council.
The statistics, which have been compiled from the latest data released by the US Department of Agriculture (USDA), were announced following AHEC’s successful participation at INDIAWOOD, which ran from 22-26 Feb 2024 at the Bangalore International Exhibition Centre (BIEC), in Bengaluru, India.
After a challenging year in 2022, the laminate industry’s sales continue to be impacted by the construction sector’s downward trend into 2023, according to the European Producers of Laminate Flooring Association (EPLF).
Among the main regions, the smallest decline in 2023 was in Western Europe with 7.65% compared to 2022 and the largest in North America, with 42.04% compared to 2022.
In 2023, sales in Western Europe decreased by 7.65% with 165,380,000m² sold.
According to data from the Vietnam’s Ministry of Agriculture and Rural Development, Department of Forestry, in the first two months of 2024, the export value of wood and forest products is estimated to have reached US$2.68bn, an increase of 47% over the same period last year.
The value of imports of wood and wood products in the first two months of this year is estimated at US$355m, up 31% over the same period in 2023. The wood product trade surplus in the first two months of the year is estimated at US$2.465bn.
us,” Mr Wiles said.
“Not only does the demand continue to be strong but the importers, manufacturers, designers and architects are very sophisticated in their understanding and use of different species.
“They appreciate the advantages and limitations and also value the strong and proven environmental credentials of US hardwoods. We are delighted that our industry can supply raw materials that meet their exacting needs.”
Carbotech Group recently expanded its business with the acquisition of the Sawquip, a manufacturing company specializing in the design and manufacture of sawmill equipment for the primary and secondary breakdown of logs into lumber. Carbotech Group plans to further broaden its expand with the fresh inclusion of the range of products that came with the integration of the Sawquip’s products and services into its own.
CERTIFICATION plays a pivotal role in fostering environmentally conscious supply chains, and Responsible Wood Sustainability Manager, Matt de Jongh, recently engaged in insightful discussions with certificate holders, Austpaper and DIY Resolutions and Australian Brushware Corporation in Melbourne.
These discussions highlighted the significance of responsible practices in promoting sustainable wood sourcing.
Robert Lane, General Manager at Austpaper, emphasised their commitment to environmental responsibility.
“We prioritise eco-friendly practices and responsible sourcing to minimise our environmental impact,” he said.
“The Responsible Wood certification aligns with our vision for a more sustainable
and responsible future.”
Luke Cerra, Group Manager Procurement at DIY Resolutions and Australian Brushware Corporation, echoed this sentiment.
“Our dedication to ethical and green initiatives is a cornerstone of our operations,”
Mr Cerra said.
“It’s not just about certifications; it’s about making a positive impact on the environment and ensuring a legacy of sustainability.”
Certification through Responsible Wood provides a credible framework for companies devoted to eco-friendly operations. Austpaper and DIY Resolutions and Australian Brushware Corporation serve as exemplary models of this dedication, contributing significantly to a greener future.
Matt, expressed his optimism about these engagements.
“It’s heartening to see organisations like Austpaper and DIY Resolutions and Australian Brushware Corporation prioritising responsible wood sourcing,” he said.
“Their commitment not only aligns with environmental goals but also enhances brand credibility and consumer trust.”
As we navigate an evolving market, sustainability transcends being a mere trend; it’s a responsibility. By supporting certified entities like Austpaper and DIY Resolutions and Australian Brushware Corporation, we collectively drive positive change and safeguard our planet. The dedication of these organisations serves as a beacon, inspiring others to champion
certification as catalysts for sustainable practices.
The collaboration between Responsible Wood and its cer-
tificate holders underscores the crucial role of certification in promoting environmental responsibility.
RESPONSIBLE Wood
has unveiled a groundbreaking initiative aligned with the joint Australian and New Zealand Standard AS/NZS 4708:2021 – Sustainable Forest Management standard.
The newly introduced guidance note aims to empower certified forest managers to enhance their scope of certification by highlighting verified ecosystem services within their operations. In the global and Austral-
ian context, the recognition of ecosystem services is gaining momentum as a comprehensive framework to describe the myriad of benefits society derives from the environment. This paradigm shift not only influences biodiversity, water resources, and regional planning but also revolutionises sustainable environmental management practices, ushering in strategies to bolster landscape resilience.
“Our commitment to sustainable forest management
goes beyond the production of renewable forest products. With the introduction of this guidance note, certified forest managers can now substantiate their claims regarding the non-wood forest values and benefits they manage within their certified forests,” Simon Dorries, CEO of Responsible Wood, said.
The guidance note outlines a meticulous process for certified forest managers to systematically integrate verified ecosystem services into their scope of certification. This involves identifying, verifying, and seamlessly incorporating these services into their forest management systems.
Matt de Jongh, Sustainability Manager at Responsible Wood, emphasised the importance of this process.
“Through rigorous auditing, we ensure that certified forest managers adhere to sustainability criteria related to verified ecosystem services, thereby fostering transparency and credibility in their practices,” he said.
The certification process involves a comprehensive approach, as outlined in the Guidance Note on Certification of Ecosystem Services under AS/NZS 4708:2021 Sustainable Forest Management. This note identifies various non-wood forest values and benefits, including biodiversity conservation, carbon storage, soil and nutrient conser-
vation, water filtration, and recreational services.
Jonathan Tibbits, Marketing and Communications Manager at Responsible Wood, highlighted the broader impact of this initiative.
“Certified organisations that include ecosystem services in their scope will be featured on Responsible Wood and PEFC certified databases, reinforcing their commitment to inclusive forest management,” he said.
The certification process outlined in the guidance note involves a step-by-step approach. Forest managers must identify and document the non-wood forest values they wish to include in their management system. This includes verifying their ability to exercise control over these values and incorporating them into the documented scope of their forest management system.
Stakeholder consultation is a crucial element, ensuring that the needs and expectations of those directly impacted by these values are considered. The forest values are then integrated into the forest manager’s management system, with senior management demonstrating leadership commitments, compliance with legal requirements, and effective monitoring and evaluation.
The audit and verification process, conducted by ac-
credited certification bodies, ensures that the forest manager’s management system effectively conforms to the requirements of AS/NZS 4708:2021. Certified organisations are listed on Responsible Wood and PEFC public databases, providing transparency to stakeholders and the public.
Certified organisations are also empowered to make specific claims about responsibly managing and certifying ecosystem services, backed by independent audits. The Responsible Wood logo can be used in conjunction with these claims, further enhancing the credibility of the organization’s commitment to sustainable forest management.
Responsible Wood’s Guidance Note on Certification of Ecosystem Services under AS/NZS 4708:2021 represents a significant stride towards promoting sustainable forest management. By incorporating verified ecosystem services into the certification process, Responsible Wood continues to lead the way in fostering a multi-generational, sustainable industry that goes beyond traditional forest product offerings.
Responsible Wood’s Guidance Note on Certification of Ecosystem Services, can be found at: https://www. responsiblewood.org.au/resources/
SCIENTISTS believe there could be a future for CCA timber at the end of its useful life.
Every year, thousands of tonnes of CCA-treated timber are sent to secure landfills.
There are currently limited disposal options for the timber, which has been treated with a mix of copper, chromium and arsenic.
One of the most widely used wood preservatives worldwide, chromated copper arsenate (CCA) enhances the durability of wood, meaning timber products are more resilient to decay and insect attack.
It is commonly used in construction, landscape gardening and horticulture with hundreds of CCA-treated posts per hectare in vineyards.
But at the end of its life the wood has limited reuse value and, due to environmental challenges with the treatment components like arsenic, limited disposal options.
Incineration or pyrolysis is technically challenging. Most of it goes to secure landfills.
Exactly how much is sent to landfill is hard to quantify because CCA makes up a portion of demolition waste which is often unsorted. A 2021 Ministry for the Environment report showed almost three million tonnes of class 2 to 5 waste is sent to landfill each year. Construction and demolition
waste could be in classes 2-4 and contain CCA timber.
Scientists at Scion have been researching removing CCA from treated timber at the end of its life and separating it into individual elements.
Senior technologist Sean Taylor discovered there could be a way to remove CCA from the timber in 2015 and began research to find an efficient removal process.
By 2017 he had figured out how to remove it from up to about 350 kilograms of hogged (shredded) timber at a time, achieving 95% removal at both bench and pilot scale.
The early successes led to a $163,000 Waste Minimisation Fund grant to continue investigating the feasibility of remediating treated timber.
Taylor has made good progress removing CCA and recovering the copper and arsenic, but more work needs to be done recovering individual elements – particularly isolating a high enough percentage of chromium.
“The issue became how can we get the metal components out and how can we isolate them individually?” Taylor says.
While a future use for the remediated timber and recovered elements would need to be determined by users, once successfully isolated, the elements could then be reused in
things like electronics or compound metals, keeping them in the circular bioeconomy.
“If you’re just taking it out of the timber and putting it into a bucket, you’re just moving the problem around.”
Taylor says a solution to CCA timber is vital because putting it in the landfill or worse, burning it without suitable technology and infrastructure, is “not the wise or right thing to do long term”.
Taylor, and Distributed and Circular Manufacturing portfolio leader, Marc Gaugler, hope by showing industry that CCA removal is possible there will be interest in funding the solution to the problem.
Gaugler says we need to find solutions that align with circular bioeconomy goals, make the most of resources and recover materials.
“Because it’s CCA-treated it’s not going to degrade in many, many decades – that is why we make it. However, it’s an organic material going into landfill,” he says.
“Scion’s Circular Manufacturing programme aims to show wood materials can go into circularity beyond burning. We can use new technology to solve hard and old challenges.”
Gaugler says Scion has shown there are end-of-use options for CCA-treated timber, but it needs to happen on a large scale. The question is
who pays for resource recovery and waste management addressing the issue and adding value by eliminating a problem.
Taylor and Gaugler suggest selling recovered timber and chemicals could be a way to offset processing costs, and mobile technology would avoid the need to ship waste timber for processing.
Around the world, other countries have already stopped or restricted the use of CCA or established viable disposal options.
Ministry for the Environment’s Waste and Resource Efficiency director Shaun Lewis says the ministry is focused on initiatives that enable the Emissions Reduction Plan 2023-2025 actions and the current Waste Strategy. For
end-of-life wood products, this centres on reducing and diverting construction and demolition waste from landfill towards more beneficial uses.
“The ministry is collaborating across government and with industry on reducing construction waste, recovering resources, and exploring more circular options for construction materials.
“There is a particular focus on treated and non-treated timber and addressing the challenge of separating these processed wood products at the end of their life to enable more circular end-of-life options from a waste hierarchy lens.”
He says Scion’s work, supported by the Waste Minimisation Fund, helped address some of these challenges.
australasian
The extension of the HomeBuilder commencement time to 18 months has been greeted as welcome news for the housing industry, the economy and for those embracing the HomeBuilder grant.
There had been fears that many who applied for the $25,000 HomeBuilder grant would not be able to start work within the initial sixmonth construction deadline and would forfeit the grant.
The HomeBuilder scheme closed for applications on April 14, and under its rules, work had to begin on a project within six months of contracts being signed.
Latest ABS data shows that house commencements surged by 27.0 per cent in the final quarter of 2020 to their highest level since March 2000.
Quicker, cheaper and greener construction of retail shops, carparks, storage warehouses, laboratories, hospitals, schools and aged care facilities would be enabled under proposed changes contained in the draft 2019 National Construction Code (NCC).
The move would make it easier to use fire-protected timber in all buildings of up to eight storeys in height and builds on the program of work undertaken by Forest and Wood Products Australia.
ENGINEERED TIMBER systems and products such as Glulam and Cross-Laminated Timber (X-LAM) are rapidly gaining popularity in the UK, delivering award winning schemes, creating new business opportunities and creating fresh market potential.
Demand is growing and they are now regarded as cutting edge solutions for the construction and property markets.
Architects, specifiers, engineers and main contractors are establishing a new generation of buildings that blend knockout aesthetics with low environmental impact – all driven by efficient offsite prefabricated technology.
THE Federal Albanese Government passed the Fair Work Legislation (Closing Loopholes) Bill No 2 on Monday 12 February. This is the third piece of legislation changing the IR Laws and will have implications for all employers in the forest and forest products industry.
This followed on from the changes passed in December that altered union delegate rights, criminalisation of underpayment of wages, antidiscrimination measures and labour hire regulations.
The implementation of this third tranche of legislation will require businesses to give further consideration to their policies, contractual arrangements, as well as a review of workplace composition and casual employment.
During the remainder of 2024 the Fair Work Commission will facilitate the implementation of many of these new laws into modern/industrial awards such as the Federal Timber Industry Award.
The key changes are as follows:
(a) Amends the definition of ‘casual employee.’ The General Rule will be that a person can only be a casual employee if:
(i) The employment relationship is characterised by an absence of a ‘firm advance commitment to continuing and indefinite work’ – taking into consideration various indicia such as ‘the basis of the real substance, practical reality and true nature of the employment relationship’ and ‘that the firm advance commitment can be in the form of a ‘mutual understanding’ that doesn’t rise to the level of a contractual term; and (ii) the employee is entitled to a casual loading or a specific rate of pay for casual employees.
(b) Introduces a new provision that a person who commences employment as a casual employee remains so until the occurrence of a ‘specified event’. A ‘specified event’ can include an order of the FWC that the employee’s status is changed to full-time or parttime. An employee could apply for such an order if (after a qualifying period) they have
Brian Beecroft CEO, TTIA
given their employer a ‘notification’ that they believe the employment no longer meets the definition of ‘casual employee,’ and other criteria are met. Part of this process requires employers to respond to an employee’s ‘notification’ within 21 days and involves a specific dispute resolution process. These provisions are intended to create an additional pathway to change an individual’s employment status (in addition to the existing casual conversion procedure, and any mutual agreement with the employer).
(c) A requirement to re-issue the casual employment information statement after 6 months (except not for small businesses), then after 12 months and each subsequent 12 months of employment.
(d) Additional employee protections including not to dismiss or threaten to dismiss an employee to re-engage as a casual employee and not to misrepresent casual employment.
These provisions take effect six months from Royal Assent (or earlier by proclamation) although noting that other criteria may affect commencement/application dates for certain amendments in this part.
(a) Enable multiple franchisees to access the singleenterprise stream for bargaining;
(b) Allow employers who are covered by single-interest employer agreement or a supported bargaining agreement (the old multi- enterprise agreement) to transition to a single- enterprise agreement (the new singleenterprise agreement) under certain circumstances including each employee organisa-
tion party to the multi-employer agreement has agreed in writing (or the FWC has issued a voting request order) and employees are better off overall under the new singleenterprise agreement than the they were under the old multi- enterprise agreement;
(c) Make other changes to the better off overall test requiring the FWC to assess whether reasonably foreseeable employees would be better off overall if the agreement applied than if the relevant modern award applied;
(d) Include additional considerations for the model flexibility term and the model dispute terms in enterprise agreements including ‘best practice workplace relations’ as determined by the FWC;
(e) Additional provisions concerning intractable bargaining workplace determinations.
These amendments take effect from the day following Royal Assent except that the model terms amendments commence 12 months after Royal Assent.
Workplace delegates’ rights
Workplace delegates’ rights and protections, similar to those introduced in Closing Loopholes No 1 are extended to ‘regulated workers’. These amendments take effect 6 months from Royal Assent (or earlier by proclamation).
(a) Modern Awards must include a right to disconnect term allowing employees to refuse contact or attempted contact from their employer, or from a third party if the contact relates to their work, outside the employees’ working hours;
(b) Disconnect includes refusing to ‘monitor, read, or respond to contact or attempted contact outside working hours unless the employee’s refusal is unreasonable;
(c) Factors which must be taken into account in determining whether the employee’s refusal is unreasonable including the nature of the employee’s role and responsibility, whether the employee is compensated for such contact/work, the reason for the contact (or attempted contact), how the contact is made and the level of disruption to the employee, and the
employee’s personal circumstances;
(d) If there are any disputes about whether a refusal is unreasonable, the parties must attempt to resolve the dispute at the workplace level at first instance. If the dispute remains unresolved a party may make an application to the FWC for an order to ‘stop contact’ or an order to ‘stop refusing contact’;
(e) The amendments set out the factors taken into account by the FWC in making an order; and,
(f) The FWC is to publish Guidelines concerning the operation of these provisions.
The amendments are to take effect from 6 months from Royal Assent (or earlier by proclamation). Other criteria may affect commencement/ application dates for certain amendments in this part. Further amendments have been tabled in Parliament to provide that non- compliance with the new right to disconnect provisions will be a civil rather than criminal offence.
The sham arrangements provisions have been amended to reinstate certain provisions deleted by Closing Loopholes No. 1 concerning an employer’s reasonable belief that a contract was a contract for services. These amendments will commence from the day after Royal Assent
New Labour hire arrangement orders take effect from 1 November 2024 and the Criminalisation of wage theft commences on 1 January 2025. These further employment changes continue a significant shift in industrial relations and workplace changes and will create more red tape and a legislative minefield for small and medium sized business. TTIA, as the only federally registered, national Association specifically focused on industrial relations in the timber products industry, will ensure Members have the resources and support to manage these workplace changes.
In the meantime, if you require any assistance from TTIA, or would like to arrange an appointment for staff to attend your workplace, contact us on (02) 9264 0011 or by email: ttia@ttia.asn.au
The I-Joist line is a high-speed line for the manufacture of I-Joists from LVL billets and OSB sheets. Features are;
• High-speed output, producing beams in excess of 15-20m/min.
• Has the capability of cutting LVL billets into Chords for the I-Joist production but also LVL into sticks for resale.
• Webs are processed from OSB sheets, typically 2.4mx1.2m in size.
• Utilising PUR glue for the bonding (other glues can be used).
• Sensors are installed to monitor the glue flow rate and spread to ensure accurate coverage.
• Printing is available.
• I-joists are accurately cut to length.
• Finished I-Joists are stacked into packs for strapping.
• Relatively small footprint, 85m x 25m maximum. Will be smaller if certain sections not required.
• Australian Made and serviced with all backups done by MPB Engineering.