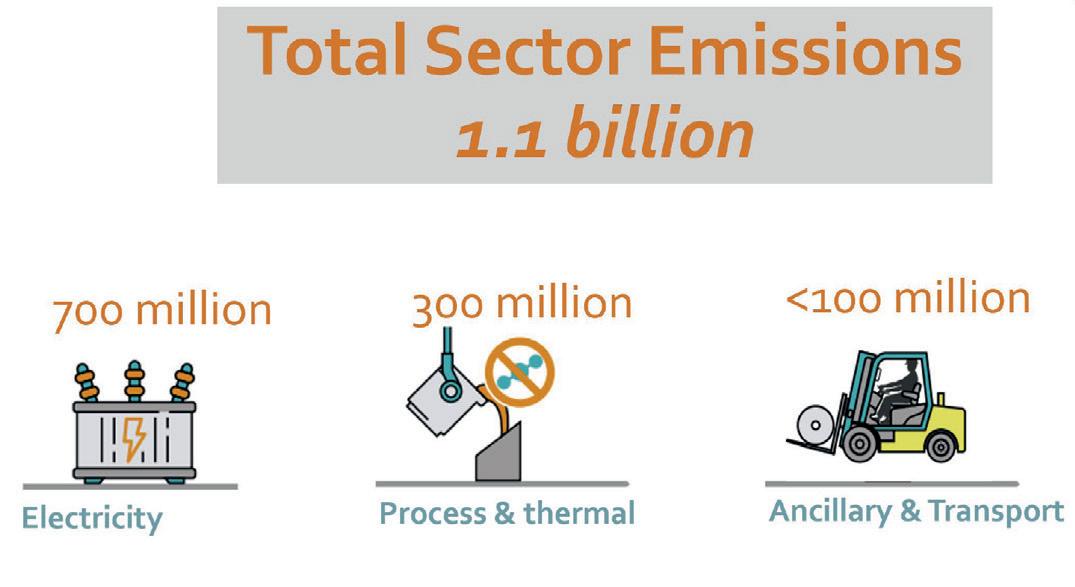
9 minute read
Aluminium decarbonisation from pathways to action
By Pernelle Nunez*
In recent years climate change has risen steadily up the business agenda; once relegated to side sessions at industry conferences, it is now an integral part of most keynote panels with climate challenges and emissions reduction plans regularly debated by executives of multinational aluminium companies. It is readily acknowledged as a major risk for organisations across many industries and the aluminium industry is no different. Climate change is by no means the only sustainability issue facing the sector, but it is widely recognised as one of the most pressing.
Within this context, the International Aluminium Institute (IAI), the association for the global aluminium industry, set out to develop greenhouse gas pathways (GHG) for the sector to 2050 to understand what alignment with climate goals means for the sector in practice. In line with its 50-year history as the go-to organisation for open-access industry data and analysis, the IAI adopted a data-driven approach, bringing together its long-standing life cycle and material flow modelling work to develop the first comprehensive aluminium sector pathways for the industry and other stakeholders.
Pathways for a hard-to-abate sector
Aluminium is often grouped with other industrial sectors that are significant emitters of greenhouse gas emissions, such as steel and cement. These are labelled as ‘hard-to-abate’ sectors because they are energy intensive, use a combination of heat and electricity, and the cost of introducing less carbon-intensive technologies is high. In order to meet global climate goals, all industries are going to have to reduce emissions from current levels and the aluminium sector pathways demonstrate the deep reductions needed across the sector to meet the objectives of the Paris agreement.
The IAI wanted to ensure its sector pathways analysis was rooted within an economy-wide context and a broader, systems-wide decarbonisation trajectory. With this in mind, two decarbonisation scenarios were developed which broadly align with the International Energy Agency’s Beyond 2 Degrees Warming Scenario1 and 1.5 Degree Warming Scenario2 which consider pathways for the global energy sector.
Establishing the sector baseline
In developing the sector GHG pathways to 2050, establishing the baseline was an essential first step. In 2018, an ingot of primary aluminium had an average cradleto-gate (mine to casthouse) footprint of ~16 t CO2e/t Al based on the IAI’s life cycle work. Recycled aluminium was much less carbon intensive at 0.6 t CO2e/t Al. These figures give an emissions baseline for the sector for 2018 of 1.1 billion tonnes of CO2e – about 2% of total global annual GHG emissions3. Emissions associated with electricity constituted the largest share at approximately 700 million tonnes of CO2e, followed by process and thermal
1. https://www.iea.org/reports/energy-technology-perspectives-2017 2. https://www.iea.org/reports/net-zero-by-2050 3. https://international-aluminium.org/resource/aluminium-sector-greenhouse-gas-pathways-to-2050-2021/ 4. https://international-aluminium.org/resource/aluminium-beverage-can-study/
Fig 1. Aluminium sector emissions by type (2018) Fig 2. Aluminium sector scenarios to 2050


Fig 3. Primary aluminium emissions intensity 2018 and for the three 2050 scenarios Fig 4. Share of primary and recycled aluminium to 2050
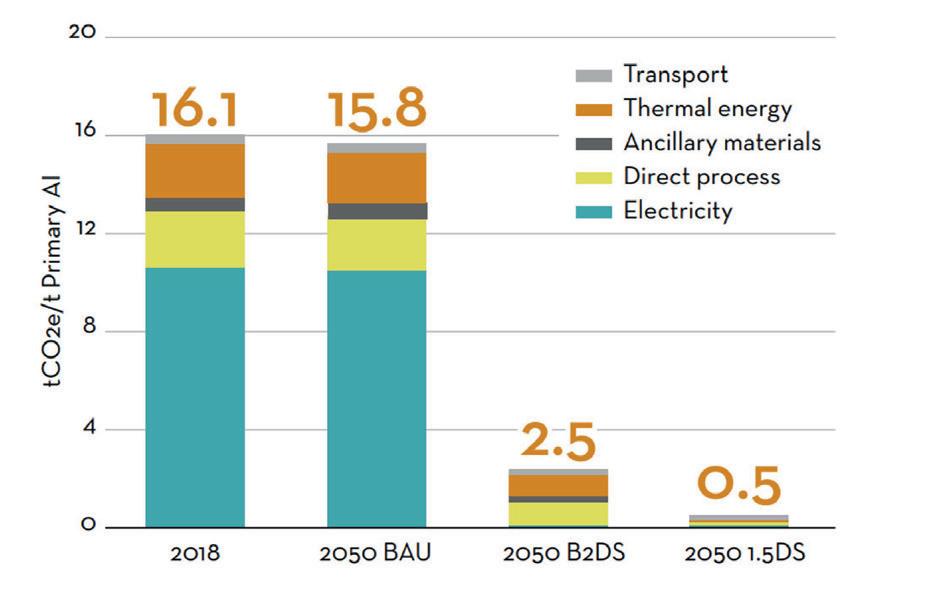
Aluminium cans are the most recycled beverage containers globally, with a 71% recycling rate. They also have the highest closed-loop recycling rate, which is when the product is recycled for use as the same product, at 33%
Fig 5. Aluminium performs well against competing materials in beverage container packaging
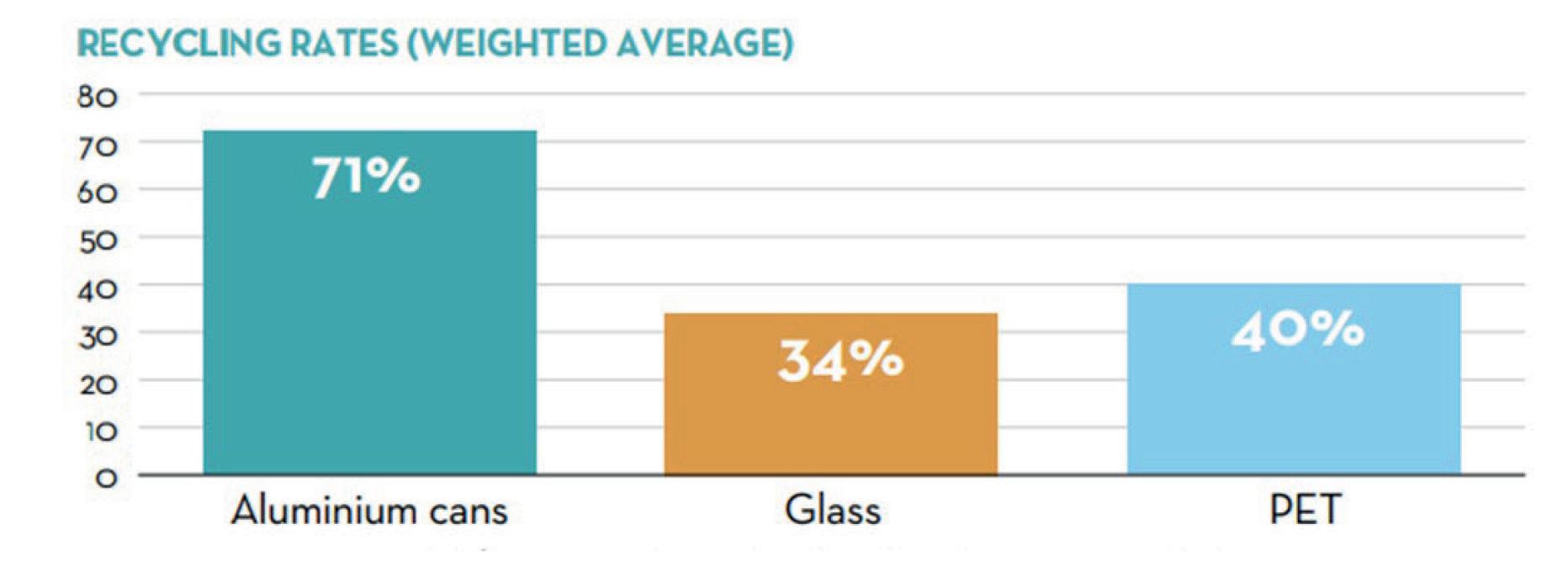
energy at 300 million tonnes of CO2e and ancillary materials production and transportation within the supply chain at 100 million tonnes (Fig 1).
Sector emissions in 2050
With the baseline established, three scenarios for the sector to 2050 were developed as part of the analysis (Fig 2): 1. Business-as-usual – assuming minimal changes from current operating practices and additional capacity coming on stream to fulfil growing demand for aluminium to 2050. 2. Beyond 2 Degrees – aligned with IEA’s Beyond 2 Degrees Analysis from which a sector budget was calculated for the full sector scope. 3. 1.5 Degrees – broadly aligned with IEA’s Net Zero Analysis from which a sector budget was calculated for the full sector scope.
Under these scenarios, total sector emissions in 2050 varied significantly from about 1.6 billion tonnes CO2e under the Business-as-usual scenario to about 50 million tonnes under the 1.5 Degrees Scenario.
Near-zero electricity related emissions
Aluminium production has always been an electricity-intensive process and under both the Beyond 2 Degrees Scenario and the 1.5 Degrees Scenario, it is the electricity-related emissions that require the greatest reduction to just 2% of 2018 levels. Whilst some moderate reductions in emissions could be made through further energy efficiency measures, the scale of the challenge – eliminating almost 700 million tonnes of CO2e emissions – should not be underestimated. In order for the sector to align with either decarbonisation scenario its overall power mix would need to be almost fully decarbonised via zerocarbon energy sources or through the installation of significant carbon capture and utilisation (CCUS) capacity.
The required reductions in overall emissions translate into a reduction in carbon intensity from 16 tCO2e/t primary aluminium in 2018 to just 2.5 tCO2e/t (2 Degrees Scenario) and 0.5 tCO2e/t (1.5 Degrees Scenario) in 2050 (Fig 3). There is minimal commercial production currently at these Paris-aligned levels; even the lowest emissions operations today will need to reduce emissions further.
Rolling out novel technologies
To achieve such reductions, three pathways have been identified and focus on a suite of different technologies to address: 1. Electricity related emissions 2. Direct and thermal energy related emissions 3. Circularity and resource efficiency
In some cases, these pathways require the adoption of existing technologies such as wind or solar generated electricity whilst others are dependent on the success of nascent technologies or those yet to be applied to aluminium production processes such as inert anodes, hydrogen, CCUS or mechanical vapour recompression. Many of these new technologies are currently at research and development or pilot scale and will require significant investment and collaboration to successfully roll out across the sector at the scale and pace required.
Climate action and sustainability
Whilst the industry continues to grapple with the challenges of climate change, it has already taken decisive action where possible and is investing in low-carbon technologies. From inert anode scaleup and testing to increased solar, wind, nuclear and hydropower electricity generation – there have been a number of notable announcements from companies across all producing regions on projects to help reduce emissions as rapidly as possible.
There have also been a number of collaborative initiatives at the R&D level which seek to build confidence and capacity in newer technologies, ultimately enabling further development and commercial deployment. Often such initiatives involve industrial partners working with research institutes cofunded by public and private sources. Such models are likely to be increasingly prevalent as corporate and national climate change strategies align over the coming years and climate-aligned finance begins to play a greater role.
Whilst this climate action has been a priority for the industry, it is clear that the conversation has evolved over the past few years from being almost exclusively carbon-focused to one which accepts that decarbonisation cannot happen at any cost.
Decarbonisation plans and technologies cannot be detrimental to the overall sustainability of operations. Similarly, it is increasingly acknowledged that climate change is not the only sustainability challenge that the industry must rise to and so efforts to address emissions need
to be part of a broader sustainability plan and approach. To that end, we have seen companies adopt more sustainable practices in areas such as mining, water management, waste management and social impacts in parallel with their work on climate action. This integrated approach is likely to be increasingly important as stakeholder expectations around responsible production and sourcing grow.
Recycling is only part of the solution
The recyclability of aluminium is one of its key benefits and is crucial to the sector’s circularity and emissions challenges. Recycled metal has on average a much lower carbon footprint than primary metal and so through increased recycling, it is possible to reduce the overall sector footprint. Currently, recycling reduces the need for over 20 million tonnes of primary aluminium and so avoids approximately 300 million tonnes of associated emissions. Looking ahead to 2050, there are certainly savings to be made through more efficient use of aluminium, increased collection rates across all end-use sectors and the elimination of losses from the system, but it is important to remember that scrap is in itself a finite resource and is only a part of the sector’s decarbonisation pathways. With approximately 75% of all aluminium still in productive use – in cars, buildings and infrastructure – there will not be sufficient volumes available to completely replace primary aluminium. Recycled aluminium will increase its contribution to supply over the coming years as more scrap becomes available when products reach the end of their life and collection systems improve, but primary aluminium will continue to be needed to meet growing demand and so decarbonisation efforts across the sector must continue in parallel with initiatives to increase circularity and resource efficiency.
Opportunities in a sustainable world
Recyclability, along with its light weight and conductivity, mean that aluminium is a material valued in a number of growing end-use sectors including transportation, electrical infrastructure and packaging. Green policies provide significant opportunities for aluminium and the industry should look to maximise these, substituting where possible for other materials based on aluminium’s superior sustainability credentials. For example, in transportation, the shift towards electric vehicles is likely to increase aluminium demand by 12 million tonnes 2020-2030 as electric powered vehicles contain between 60 to 80 kg more aluminium than those powered by internal combustion engines. Similar opportunities exist in the packaging sector where both recyclability and light weight are in high demand and present potential for increased substitution of plastics and glass. In the electrical sector, aluminium’s importance in photovoltaic cells and power distribution provide further opportunities for the metal as a material of the future with increasing electrical infrastructure required as part of transitions to lowercarbon energy systems.
There are significant opportunities for aluminium in societies that are aiming to become more sustainable. Aluminium has strong credentials as a material of the future, performing well compared to competing materials in a number of enduse sectors (Fig 5). The industry is well positioned with clear pathways, guidelines and standards to help deliver on the increasing transparency and data-driven approaches demanded by stakeholders. It is clear that aluminium is an essential material for a sustainable future, but in order to continue being a material of choice, it must itself be sustainable. �
Preparation Technology for Carbon Paste
Choose the Eirich solution:
• Low investment costs
• Low operating and maintenance costs
• Simple and swift commissioning • Optimum mixing and cooling conditions • Excellent paste quality • Maximum plant availability • All key machinery is manufactured in our own workshops • Reliability for more than 150 years
eirich.com
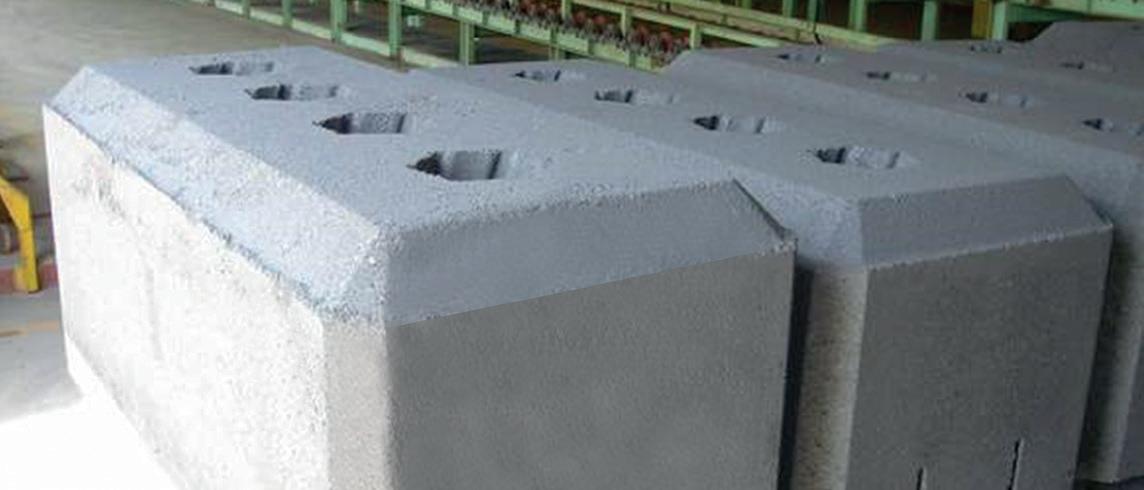
