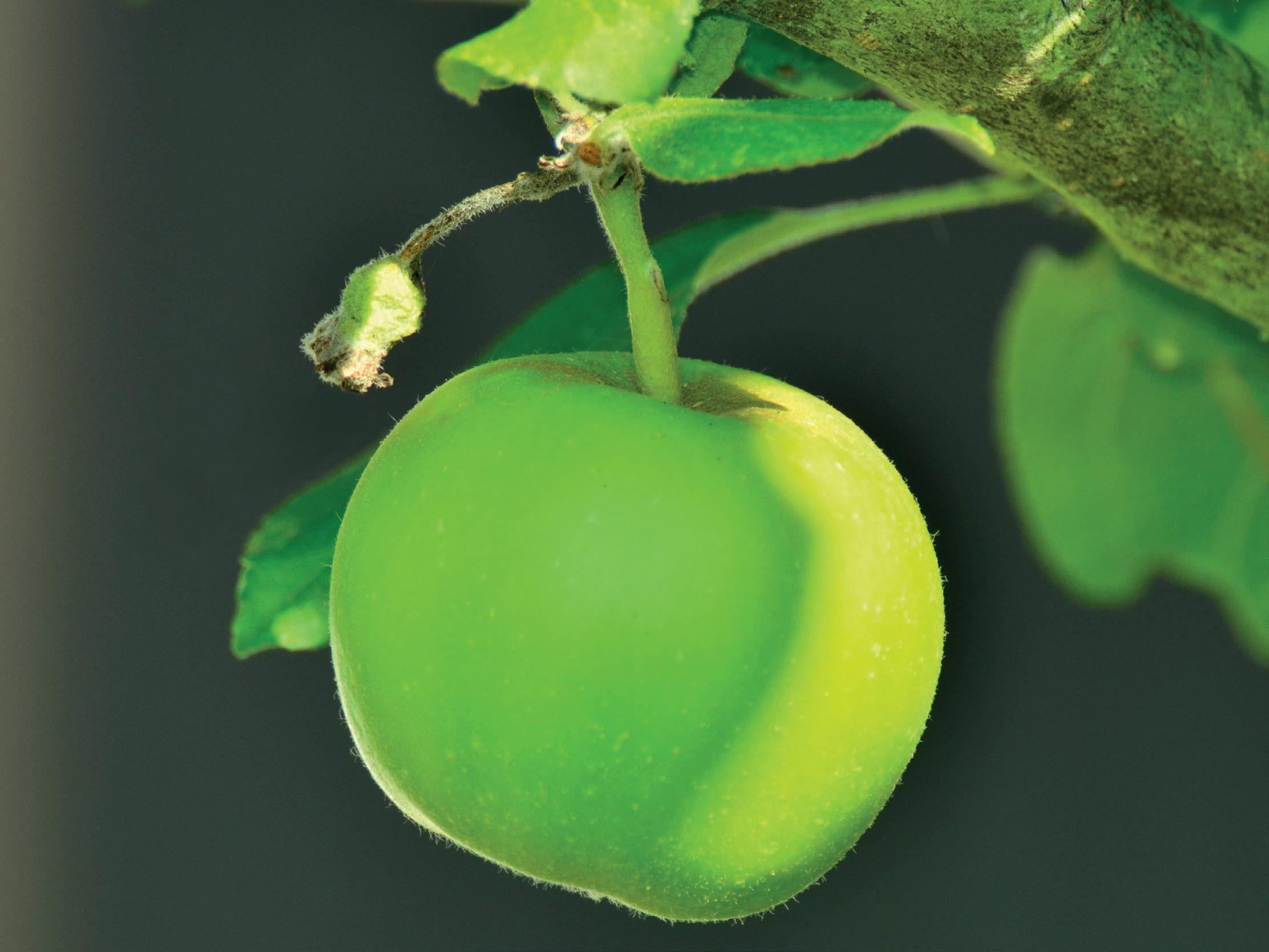
6 minute read
Aluminium’s journey to ZERO carbon
By Tim Murray*
Today sustainability and going “Green” have become of paramount importance to the world. This has challenged all companies review their business models and, in many cases, reinvent themselves. Nowhere is this more evident than in the large industrial industries such as aluminium. Being the former CEO of Aluminium Bahrain I can tell you aluminium is an amazing material that is used in almost everything we touch, whether it be your iPhone, a soda can, or the car you drive. In addition, we cannot forget the critical role aluminium will play in the Electric Vehicle (EV) revolution given its lightweight properties, conductivity and ability to be infinitely recycled.
Fortunately for the world aluminium is the second most abundant element on the planet however the process to produce primary aluminium generates large amounts of CO2 emissions. The process of smelting aluminium from the processed bauxite (i.e. Alumina) is power intensive process resulting in the generation of CO2 emissions especially when using energy from fossil fuels.
Today the world produces approximately 68 million metric tons (mt) of primary aluminium annually with an average CO2 footprint of 17 mt for every 1 mt of aluminium produced (yes you read that correctly!). So this equates to 1.2 billon mt of CO2 generated from the production of primary aluminium each year.
The average CO2 footprint for a smelter varies drastically depending upon the power source used, for example aluminium produced from coal-based electricity generates around 20 mt of CO2 whereas the if it is from renewable power (e.g. Hydro or Wind) then there is only 4 mt of CO2 .
The vast majority of the 68 million mt tons of primary aluminium is produced using coal fired power stations, typically in China and India. In terms of aluminium produced from renewable power there is approximately 15 million mt produced annually (or only 22% of the total). So we have a long way to go to shift to all renewable power. Even if a smelter has renewable power there is still 4 mt of CO2 produced. Obviously, the ability of an existing smelter to change their power source is not really an option. So how can we address the 4 mt which is not related to power generation? The below chart breaks down the elements which make up the remaining 4 mt of CO2 from aluminium production. The biggest area of CO2 emission reduction relates to the use of the Carbon Anode in the aluminium electrolysis process (accounts for 1.8 mt of CO2 for every 1 mt of aluminium production). I will do my best to explain the aluminium electrolysis process in simple terms. In order produce aluminium you need to split the aluminium from the oxygen in Alumina. This is done in a reduction cell (commonly called a pot) where Alumina (which looks like sand) is continuously fed into molten liquid bath in which a Carbon Anode is submerged then hit with large amounts of electricity to complete the process (on average 15 mega-watts of power is needed to produce 1 mt of aluminium).
As a result of the electrolysis process the aluminium reduces to the bottom of the pot (hence the term Reduction Lines) and the remaining oxygen eats away the Carbon Anode in the pot. This is a continuous process which runs 365 days a year 24 hours a day and you need to replace the Carbon Anode every 27 days. Ok, I know this was way too much technical talk but hopefully you understand why a Carbon Anode is important.
It is possible to replace the Carbon Anode with what is called an Inert Anode, a technology developed by Alcoa many years ago. However, this technology has never been fully scaled for commercial production. The Inert Anode is made of specialty alloyed steel bars thereby replacing the need for the Carbon Anode in the process. I know this sounds simple and you may ask why are we not doing this? The simple answer it is not so easy! But there is a company called Elysis (located in Canada) which is a joint venture between Alcoa, Rio Tinto and the Canadian government focused
ZC
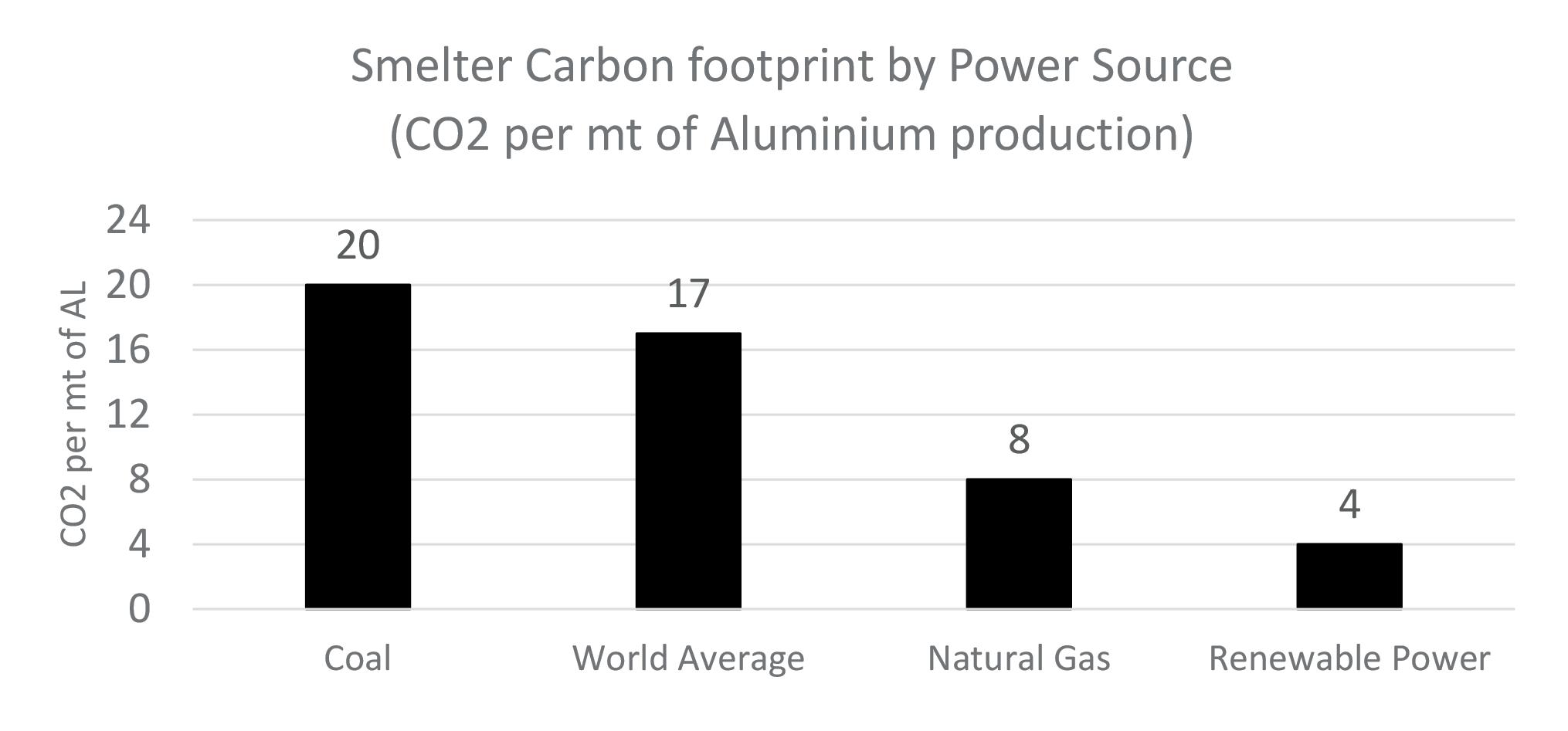

on having this technology commercially demonstrated by the end of 2023.
The next area to reduce CO2 emissions is from the production of Alumina (1.3 mt of CO2 for every 1 mt of aluminium) by replacing fossil fuels in the process by using green hydrogen. This is possible by upgrading certain production equipment in an Alumina refinery but will require CAPX investment. A lot of work is being done on this by the major Alumina producers but it will take time to implement and will also be subject to the ability to competitively source green hydrogen.
Reducing CO2 emissions from freight is the next area of focus (.6 mt of CO2 for every 1 mt of aluminium production). You may ask how is it possible to eliminate freight as smelters need raw materials? Well there are a couple of things that can be done to eliminate roughly 50% of the CO2 emissions. The first thing companies can do is optimise shipments to have more larger cargoes which lowers the total number of shipments and also saves money. You may ask why companies are not already doing this if it saves money? Again the answer it is not so easy to manage complex supply chains and the recent issues from the COVID pandemic have made it even worse. However as the world returns to normal there is a big opportunity to better optimise shipping sizes which will reduce CO2 and save money.
The second thing companies can do is focus on using cargo ships which have the ability to do backhaul shipments. Today once a ship delivers its cargo it usually brings back the ship empty. If companies are able to carry a backhaul cargo, they fully utilise their ship and avoid another ship making that journey. Torvald Klaveness out of Norway is a good example of a company utilising this strategy with their custom built Cabu ships. As example they bring Alumina from Australia to the smelters in the Middle East and then return bring back caustic soda from the Middle East to be used in Australia Alumina refineries. This again is another example of reducing CO2 emissions and saving money.
The last area of CO2 emission reduction I have labeled as “Other” (.3 mt of CO2 for every 1 mt of aluminium production). This is primarily related to the use of vehicles within a smelter which are powered by diesel as well as gas powered furnaces primarily used in the Casthouse area. In both of these areas there are solutions to have an electric option. However, this would be for new purchases whereas to replace existing equipment will be cost prohibitive.
As a world we need to accept that going “Green” may require investment where there is not a financial payback. There needs to be a balance between what companies (and the end consumer) are willing to pay and what are companies willing to do invest even without a clear financial payback. In addition, the industry needs to more calculated risks in embracing new technologies.
I know some people may say why do we need smelters and why can’t we just do more recycling to support market demand. Personally, I think all the new recycling initiatives are wonderful and we as a world should do our very best to maximise recycling but unfortunately it is not enough. It is not a mutually exclusive solution; the answer is we need both.
In closing, going “Green” will not be easy and require sacrifice no matter what industry you are in. We need to challenge the norm and take on the mindset “The only easy day was yesterday”! �
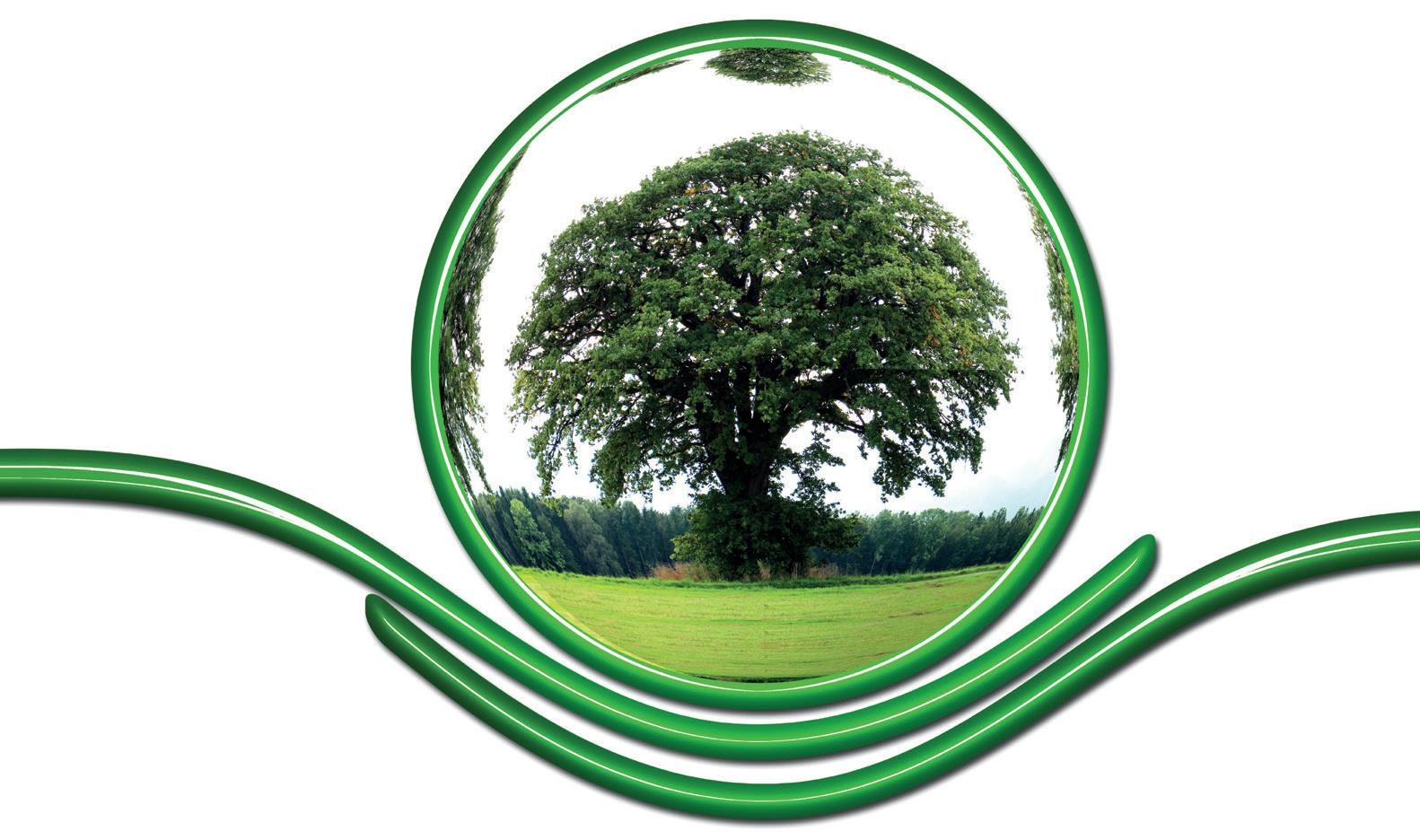