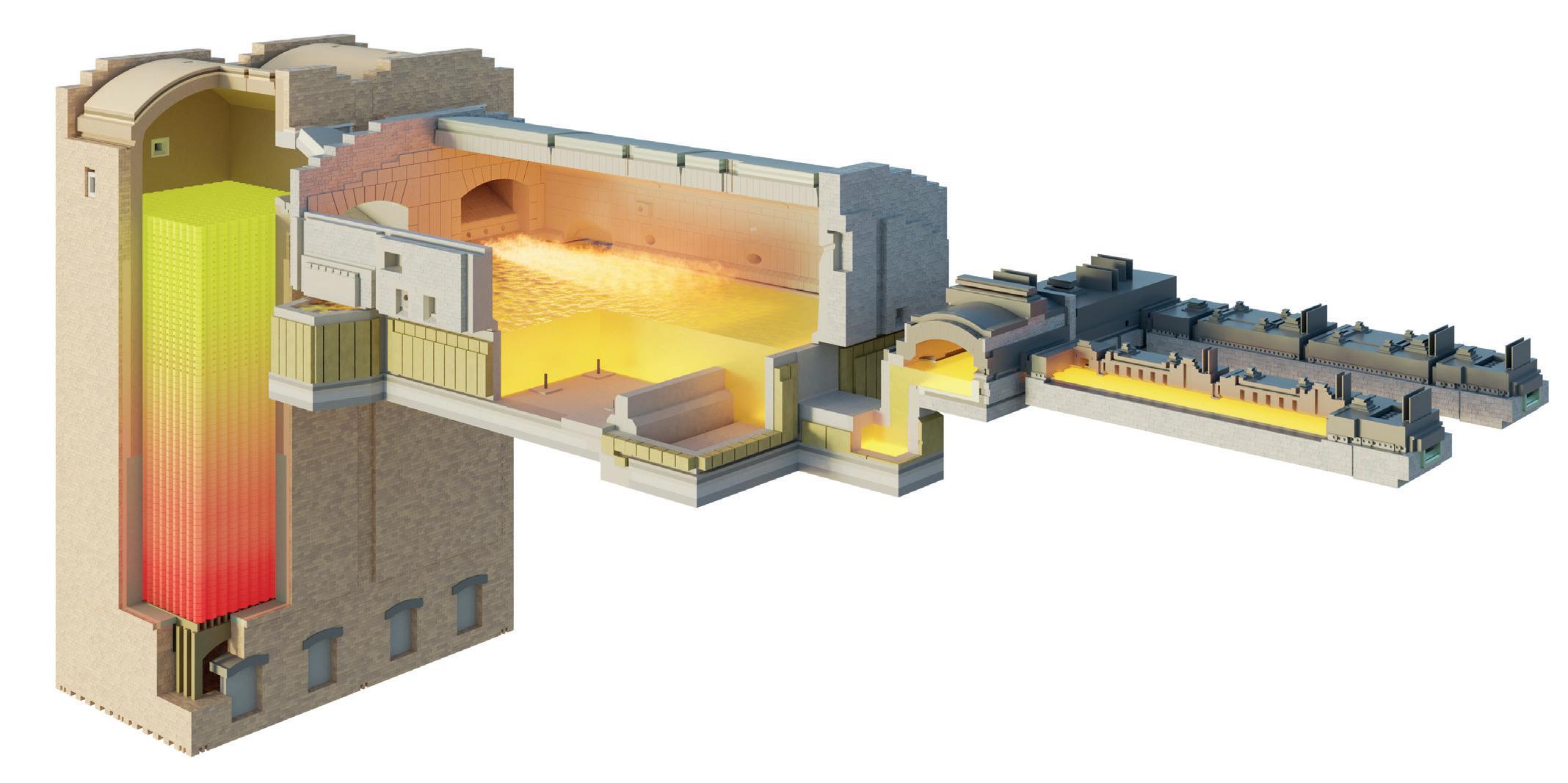
8 minute read
Decarbonisation: Horn
High electric power share in glass melting
Max Kallert* describes concepts for substituting fossil fuels for electric power, which could aid in achieving climate neutrality within the glass industry.
� A classic end-fired furnace including regenerator, distributor and forehearths furnace.
In times of global warming, the push to reduce carbon dioxide emissions and reach climate neutrality is also influencing the glass industry. Right now, fossil fuels are still covering the majority of the energy consumption in the production of glass.
Current measures to cut down fuel consumption include heat recovery for batch, cullet and gas preheating as well as direct substitutions with more sustainable fuels (like hydrogen or bio gas). However, the incorporation of green electric power into the glass production could be the way to go. Compared with green fuels, electricity in the melting process has the advantage of higher availability and lower prices (due to better efficiency).
A logical, but radical, step now would be to completely switch to electric energy and use a full electrical vertical melter. This would mean huge changes in operating compared to the current fossil furnaces and their horizontal melting principle. This is due to different restrictions (e.g. for cullet, pull changes, etc.) applying for a full electric melter. Furthermore, the standard for electric furnaces right now (<200 tonnes per day) is still on the lower end needed in the container glass segment.
This is why Horn is developing several hybrid concepts as an alternative. These concepts combine an increased electric power share and the well-known principle of horizontal melting.
The word hybrid is an often-used buzzword in this context, but there are varying definitions. Does hybrid mean: � The simple existence of both kinds of power in the furnace? � Equal contribution from electric and fossil sources? � High flexibility ranging from predominantly fossil to predominantly electric contribution?
Horn defines a furnace as hybrid if both forms of power, electric and fossil, are needed for sufficient operation. Therefore, an end-fired furnace with electrical boosting up to 10-15% would not be considered a hybrid furnace, whereas a 50/50 contribution from both fossil and electric sources would clearly be a hybrid furnace.
Considerations
For hybrid furnaces, some current working standards (for fossil furnaces) have to be reconsidered.
The incorporation of a higher amount of electric power makes it necessary to increase the number of electrodes in the melting basin too. Each bottom electrode creates locally a strong vertical flow that interferes with the main horizontal convection, known from the horizontal melting process. If a high number of electrodes are positioned evenly and extensively over the basin bottom, a broad disruption of the typical convection flow is a probable consequence. That is why Horn prefers a certain positioning of
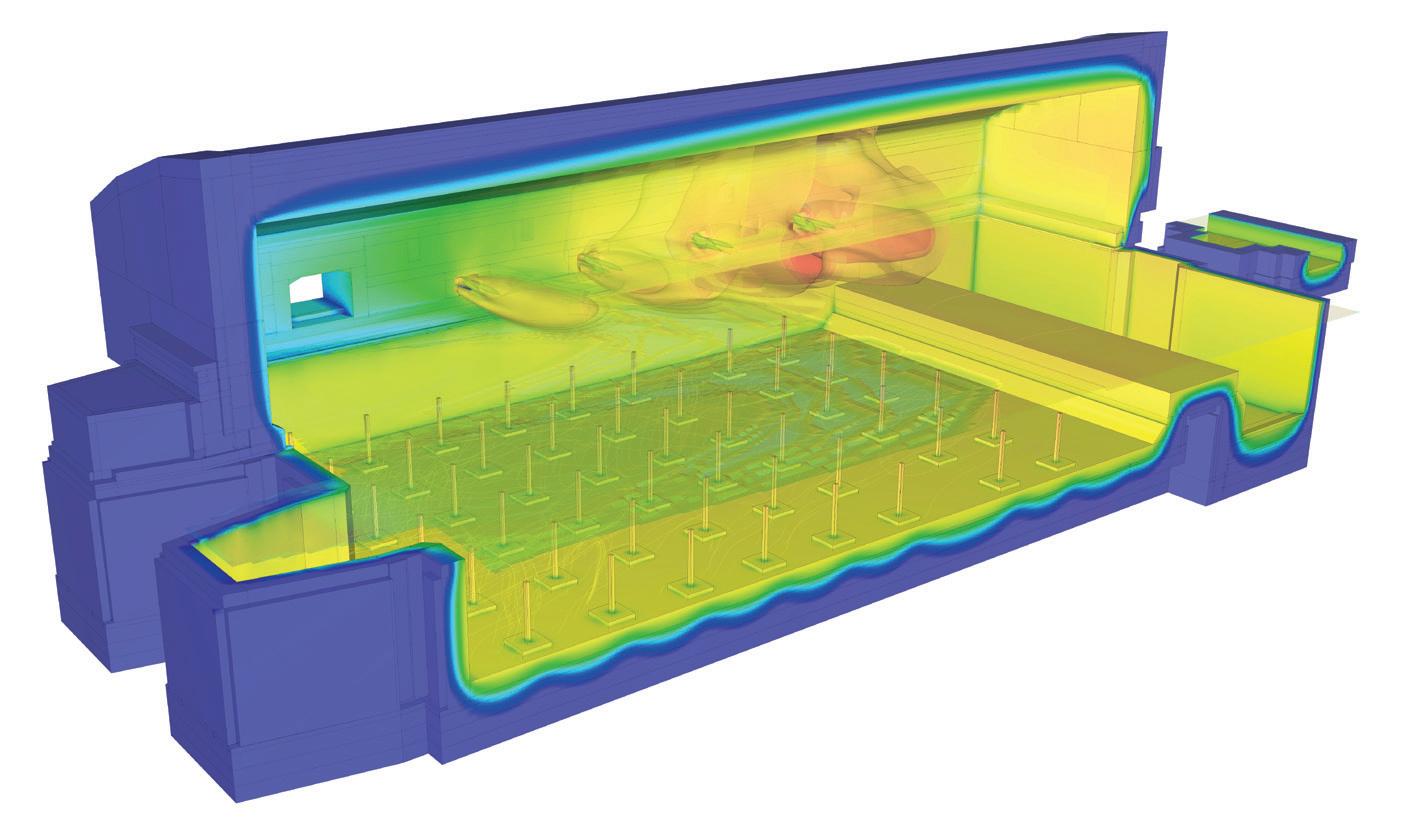
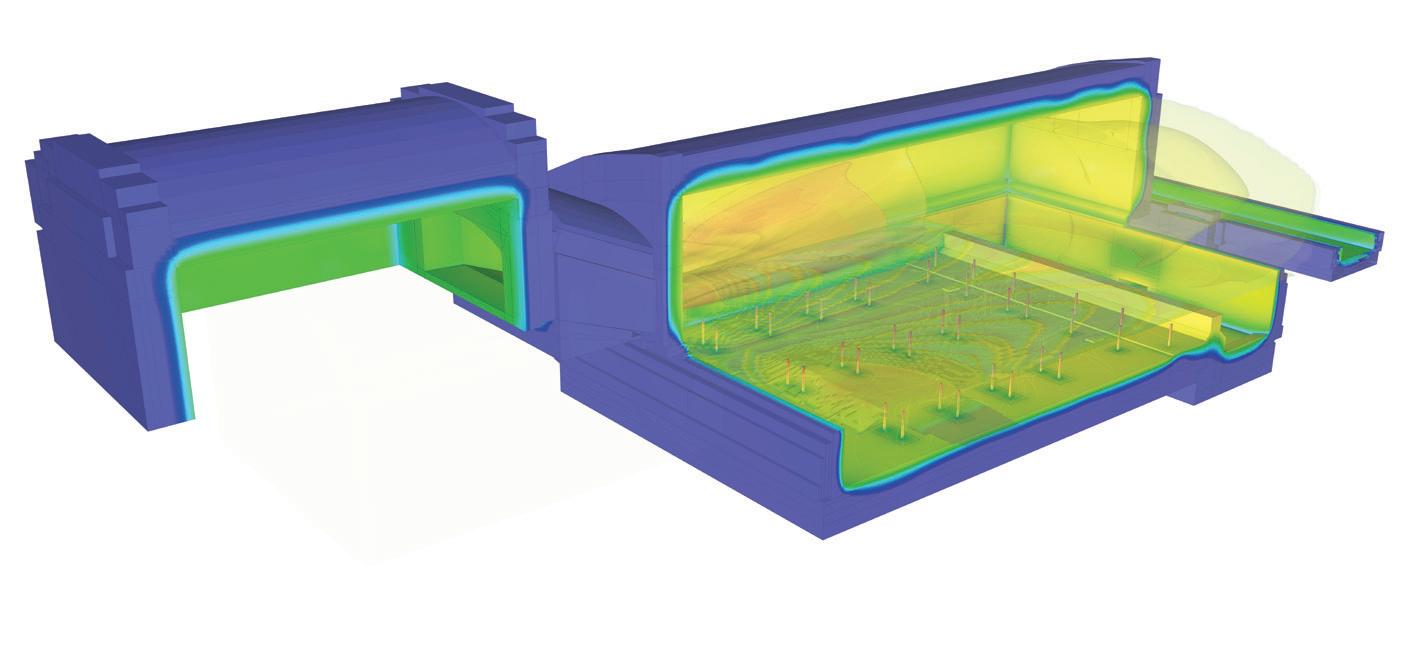
CFD model of an hybrid end fired furnace running with a 30/70 share of electric and
� fossil power fired furnace.
bottom electrodes, combined with the use of side electrodes, to preserve the typical horizontal convection. This way, the melting process in the batch layer can be supported and the disruption by the vertical flow around the electrodes is minimised.
A declining share of fossil power reduces the temperature in the crown and superstructure, regardless which kind of combustion is used. This can lead to problems for some of the common materials currently used, for example standard silica should be used above 1470 °C. Depending on the wanted range of energy flexibility, this problem can be intensified due to high temperature differences. Additionally, the chemical atmosphere from combustion (air fuel; oxy fuel; hydrogen firing) has to be taken into account. The refractory producers are working on options (e.g. lime free silica), but the refractory concept has to be chosen carefully for the desired hybrid furnace.
Another consequence of reduced fossil consumption is a decrease in the volume flow of the fuel itself and the oxidant as well. For end-fired furnaces, this will lead to a state of underload in the regenerators and lower velocities at the burner port, which can result in instabilities in flame formation and a generally shorter flame length. This contributes to an unfavourable temperature distribution in the superstructure and has negative influence on the glass quality. For new furnaces with limited fossil energy flexibility this is no issue, as the regenerator and superstructure can be designed accordingly.
However, for existing furnaces (which should be retrofitted for a higher electric share) and furnaces with a high electric flexibility, this can be problematic. In both cases, the volume flows differ significantly from the original state and the issues noted above will occur. As a countermeasure, the recirculation of flue gas is a possible solution. Part of the flue gas from the exhaust regenerator is added to the combustion air on the corresponding air regenerator. Therefore, the volume flow and the velocities at the burner port increase and proper flame formation is restored. Additionally, the NOx-concentration can be reduced with this measure. By controlling the recirculated volume, the flame length and position of the hot spot can be influenced as well.
Categories
To meet the needs of the customer, Horn developed the following furnace categories varying in overall electric share, energy flexibility and basic principle.
Key: end-fired furnace (EFF), cross-fired furnace (CFF), oxyfuel furnace (OXY) and vertical electric melting (VEM). � Classic-fossil furnace (up to 20% electric power; EFF; CFF; OXY). � Hybrid furnace (20 to 40/50% electric power; EFF;OXY). � Super-hybrid furnace (up to 80% electric power; OXY). (Future concept.)
� All-electric melter (100% electric power; VEM).
The furnaces from the hybrid-fossil category represent the evolutionary step from the classic-fossil furnaces in container glass towards more electric power, while the super-hybrid furnaces continue this concept to an even higher electric share.
End-fired hybrid
Currently the standard for the production of container glass is the end-fired furnace. Therefore, a lot of knowledge and routine in operating exists at the majority of glass producers. To combine this wellknown principle with the possibility of an increased electric power share, Horn developed the hybrid end-fired furnace with from 20% to 40% of electric power.
Two mechanisms ensure proper operating conditions for energy flexibility. The first one is the already mentioned recirculation of flue gas, which influences the hot spot in the combustion space (necessity depends on wanted flexibility). The second one is the individually adjustable boosting systems. As a result, the power distribution in the glass melt can be changed to correspond with the settings in the combustion space to further influence and stabilise the hot spot.
Compared to a completely fossil fuelled end-fired furnace, the CO2-emissions regarding the melting can be reduced up to 45% (not including CO2 from batch gases).
Oxyfuel hybrid
Today, oxygen for gas combustion is mostly used for high quality and special glass. This can largely be traced back
� CFD model of an hybrid oxyfuel furnace running with a 50/50 share of electric and fossil power oxyfuel furnace.
to the high price of oxygen. A cleaner combustion (especially regarding NOx) and a higher efficiency are also on the plus side. Depending on the furnace size, even some form of heat recovery from the exhaust gas is possible (preheating gas, cullet, batch, etc.).
For hybrid furnaces, firing from the side has a huge advantage. Whilst recirculation in an end-fired furnace changes the temperature distribution to a desired setting, at an oxyfuel furnace the gas distribution can be precisely adjusted. Therefore, it is easier to influence the hot spot to find ideal melting conditions.
For a high share of electric power, the gas distribution can be shifted more towards the refining area, whilst the energy in the melting area is predominantly provided via the electrodes. If the electric share is lower, the gas can be distributed more evenly along the furnace. A recent, successful start-up of a Horn hybrid oxyfuel furnace, with an electric share of 50%, has turned the concept into a reality.
The oxyfuel hybrid increases the energy flexibility even more, compared to the end-fired hybrid furnace. Starting from a continuous combustion space, the furnace can be operated with up to 50% electric power, with a minimum of around 20%. Compared to a completely fossil oxyfuel furnace, the CO2-emissions regarding the melting can be reduced up to 50%.
Oxyfuel super-hybrid
For creating an even higher degree of flexibility (up to 80%) Horn is developing the super-hybrid oxyfuel furnace. Based on the hybrid oxyfuel furnace, additional features were added.
A refining area with a depth of over 2.5m, and additional side electrodes to ensure proper refining, are provided in the glass melt. In the combustion space, a socalled ‘shadow wall’ can be implemented to separate it into two parts: a cold section, where low fossil heating takes place and the batch is ideally covering the glass surface, and a hot area where the majority of gas is combusted. The hot flue gases are discharged over the batch, to enable heat recovery onto the cold batch layer.
The necessity of this shadow wall and the position inside the surface are highly dependent on the operating of the furnace. If the flexibility should be used to its highest degree, a shadow wall will definitely be necessary. If the goal is to maintain a certain energy ratio (such as 30% fossil and 70% electric) with minor deviations, the superstructure design can be adjusted accordingly and a shadow wall is not needed. The potential for reducing CO2-emissions is even higher for this concept; up to 80% of CO2-emissions from combustion.
Conclusion
The glass industry is a very traditional branch and a furnace represents a high investment for the manufacturer. Therefore, it absolutely makes sense to do an evolutionary, intermediate step between the classic and the super-hybrid furnace categories with Horn’s hybrid end-fired furnaces and Horn’s hybrid oxyfuel furnaces.
If glass producers are willing to take it ‘all the way’ and go full electric, Horn is the right partner for large all-electric furnaces as well. �
*CFD Modelling at Horn Glass Industries, Plössberg, Germany, https://www.hornglass.com/
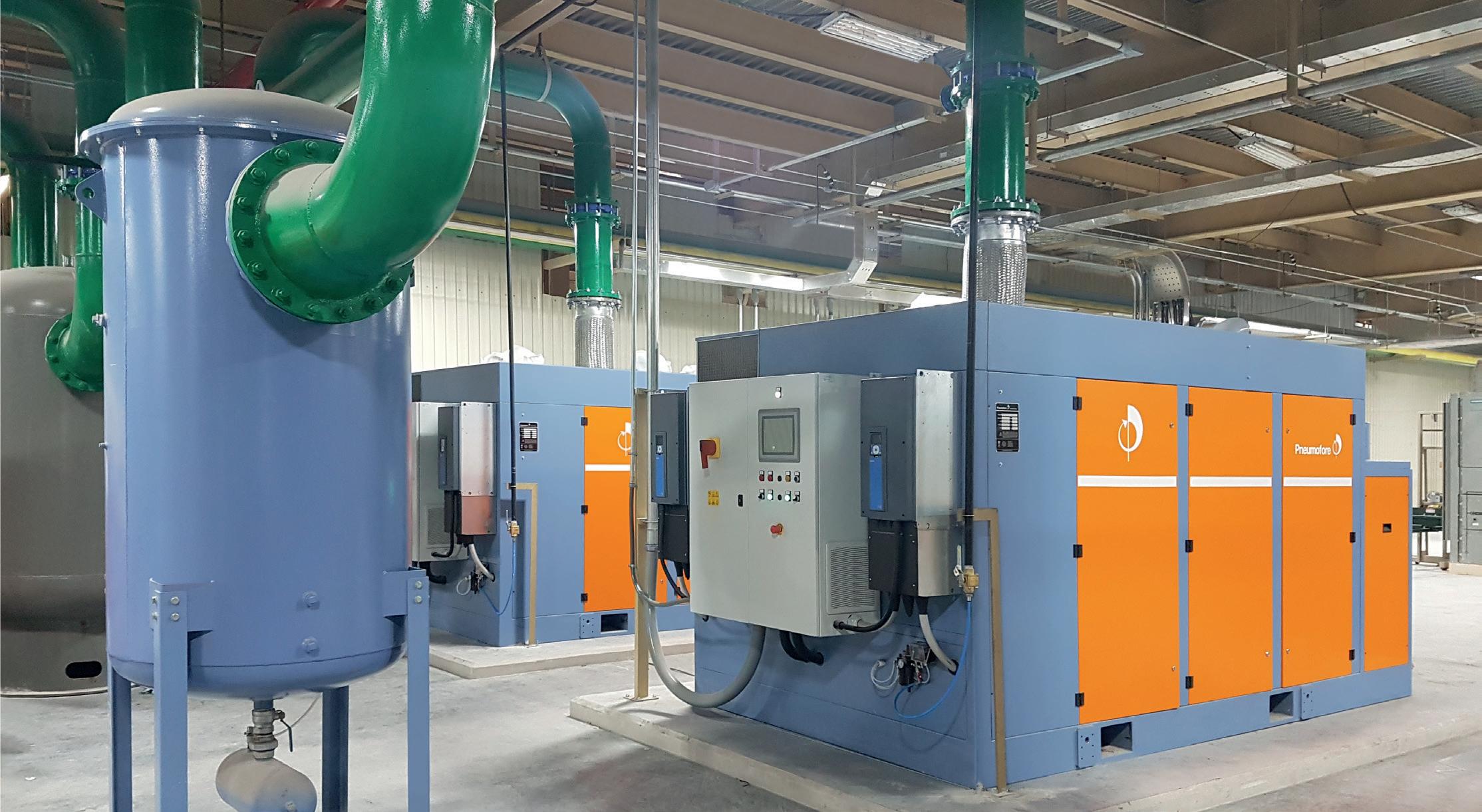
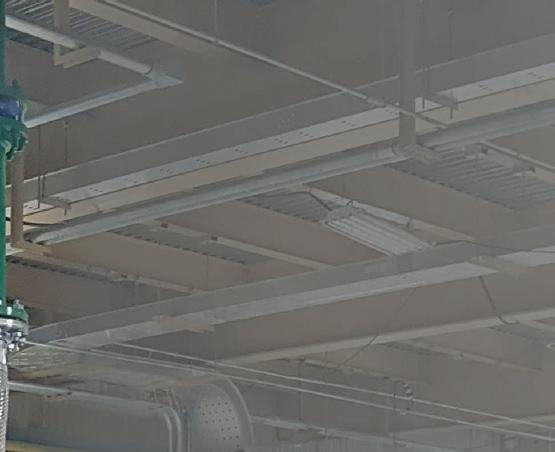
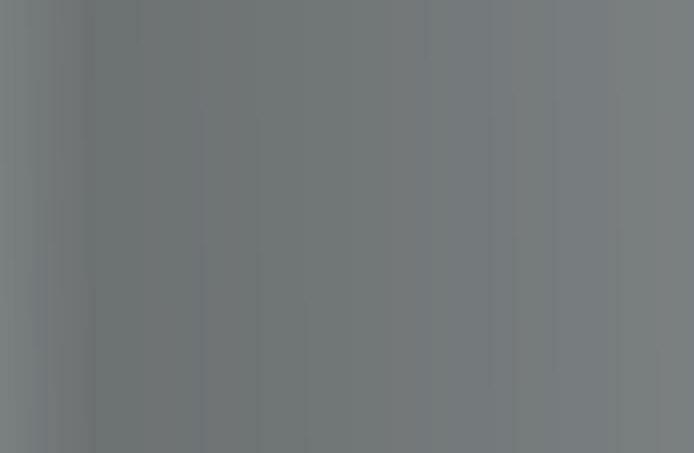