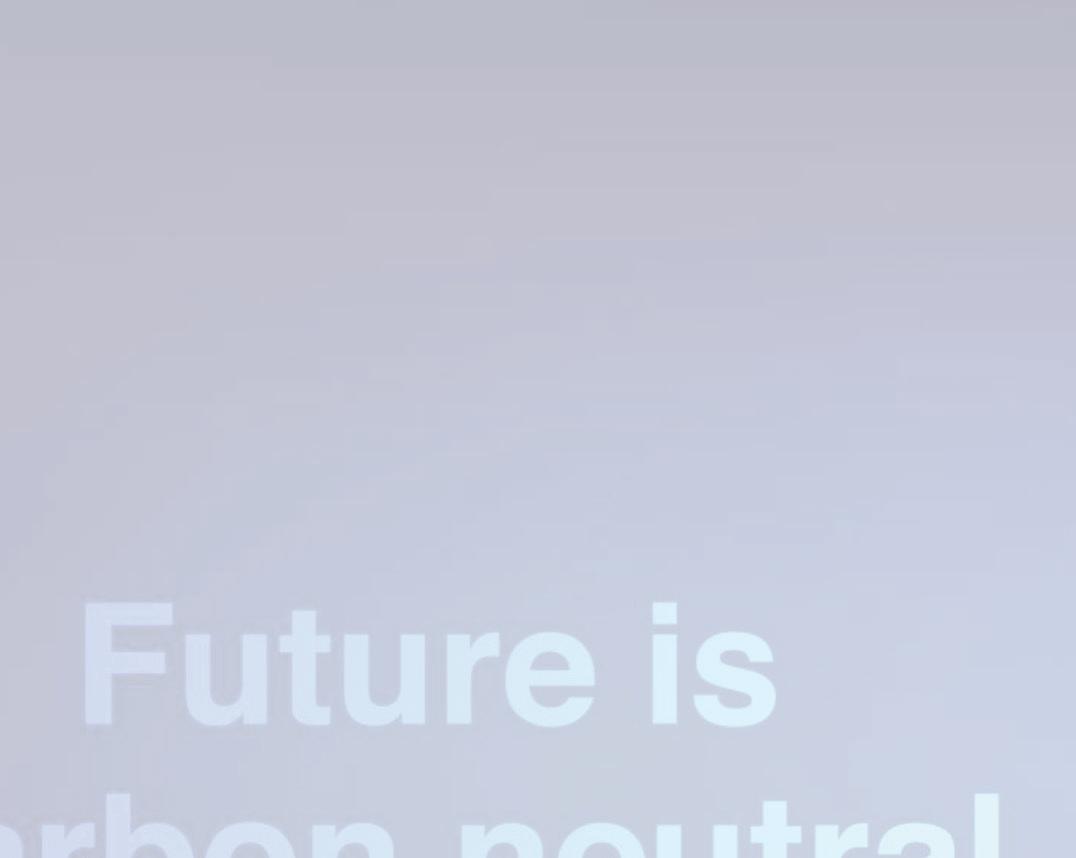
17 minute read
Decarbonisation Renewable Glass Conference 2021
Renewable Glass Conference 2021
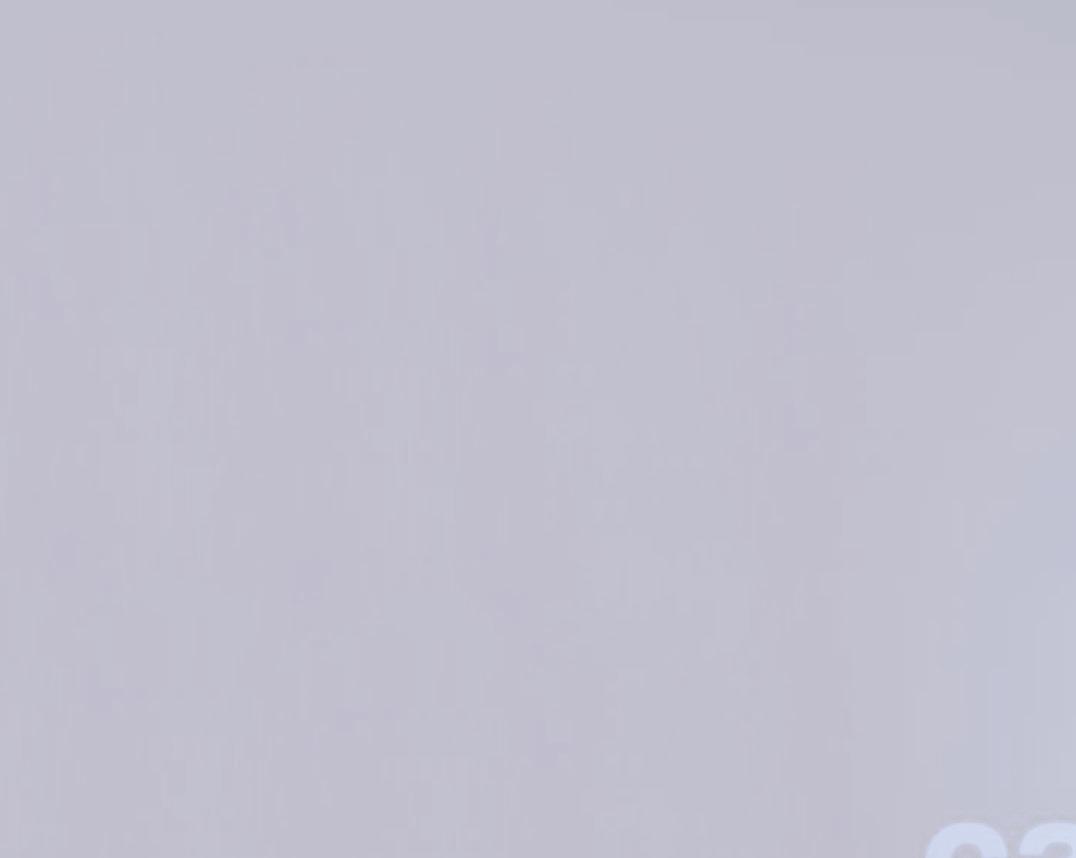
Industry experts discussed options of how the glass manufacturing sector can decarbonise at the recent Renewable Glass Manufacturing conference. Topics included hydrogen, electrical and biofuel glass production. Jess Mills reviews the event.

Topics such as decarbonisation, carbon neutrality, sustainability and alternative fuels were highlighted at the recent Renewable Glass Manufacturing conference, hosted by Glass International.
Speakers at the online event included glass manufacturers such as the NSG Group, Wiegand-Glas and Encirc, customers such as CocaCola Europacifi c Partners as well as technology suppliers such as FIC UK, Sorg and Horn Glass.
Encirc discussed the challenges of using biofuel instead of fossil fuel combustion in glassmaking, while Wiegand-Glas spoke of its Eco2Bottle brand, which uses biomethane for product lines – partly supplied by bmp-greengas.
Glass companies in attendance included O-I, Bangkok Glass, Nihon Yamamura Glass, Saint-Gobain, Sisecam, Bormioli Luigi, Guardian industries, Vetropack, Saverglass, Grupo Vical and CristalChile. Attendees were from a variety of countries such as Indonesia, South Korea, Thailand, Italy, Turkey, Mexico and the USA.
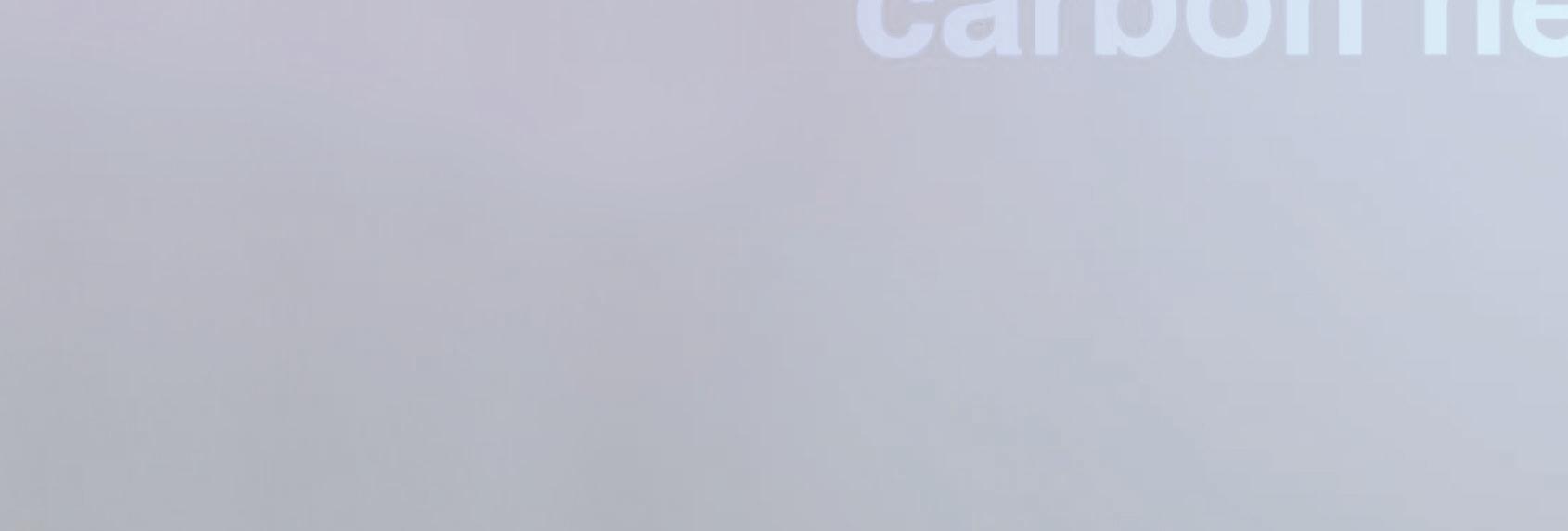
DECARBONISATION – COCA-COLA EUROPACIFIC PARTNERS
Charles Richardson, Procurement Director of Metal, Glass and Other Primary Packaging at Coca-Cola Europacifi c Partners (CCEP)1, spoke on how CCEP aims to reduce its carbon impact.
Mr Richardson discussed how CCEP’s sustainability framework ‘This is Forward’ and its ‘Action on Climate’ programme will lead the company towards net zero carbon emissions by 2040.
CCEP, the largest Coca-Cola bottler in the world by revenue, has reduced its total carbon footprint by over 30%. It plans to cut these emissions by a further 30% across its entire value chain by 2030, before reaching net zero by 2040. (Fig 1)

� Fig 1. CCEP’s carbon reduction pathway.
To do this, the company will focus on reducing its Scope 3 emissions. Scope 3 emissions are from CCEP’s suppliers and have increased to 93% of the company’s total emissions since 2010.
This is due to the reduction of emissions from CCEP’S own direct operations and facilities (Scope 1) and emissions from the production of energy required to run CCEP’s business (Scope 2). Emissions in these areas have decreased by 22% in Scope 1 (now 6% overall) and in Scope 2 by 98% (now less than 1% overall) over the last 11 years. (Fig 2)
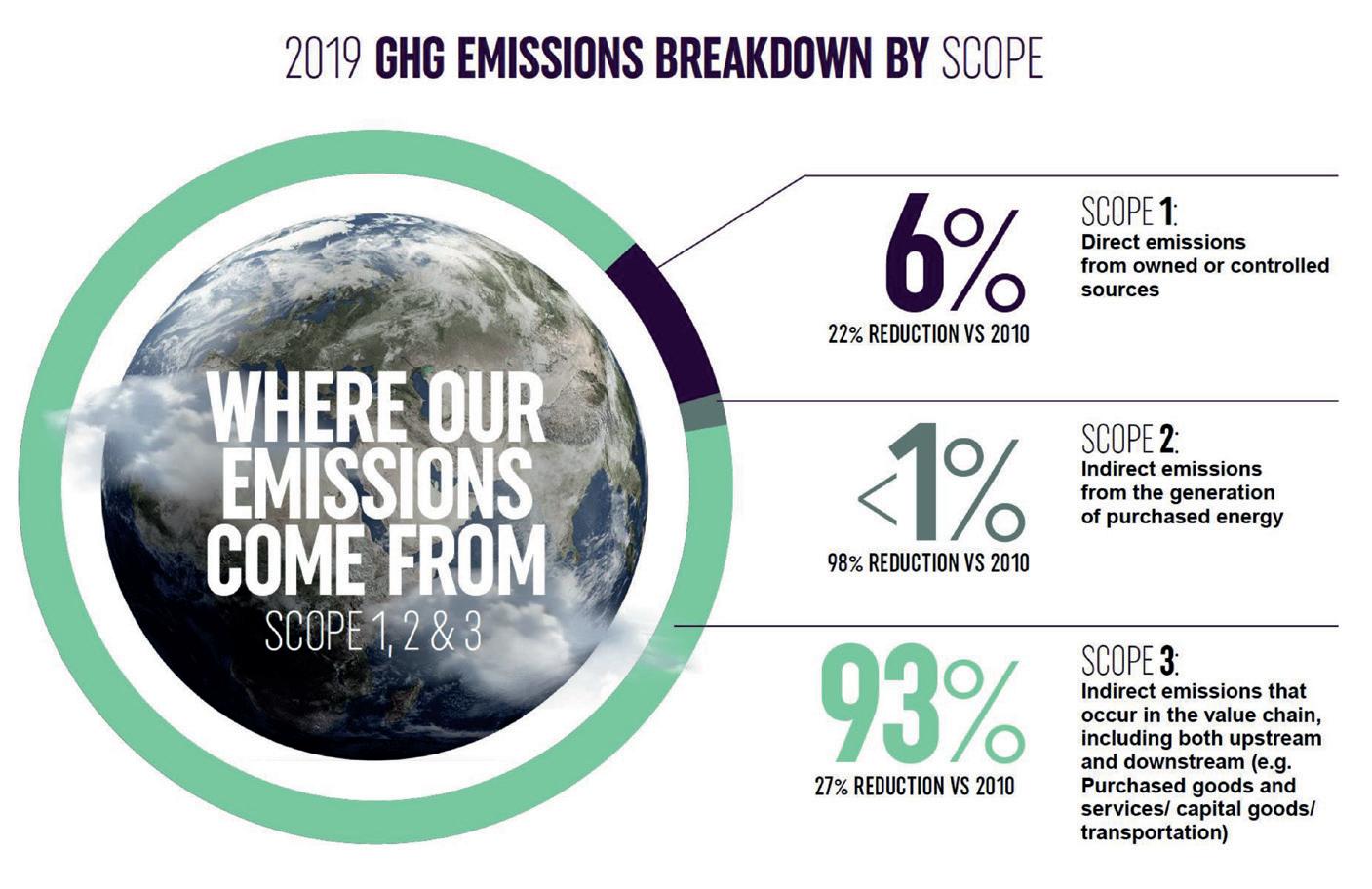
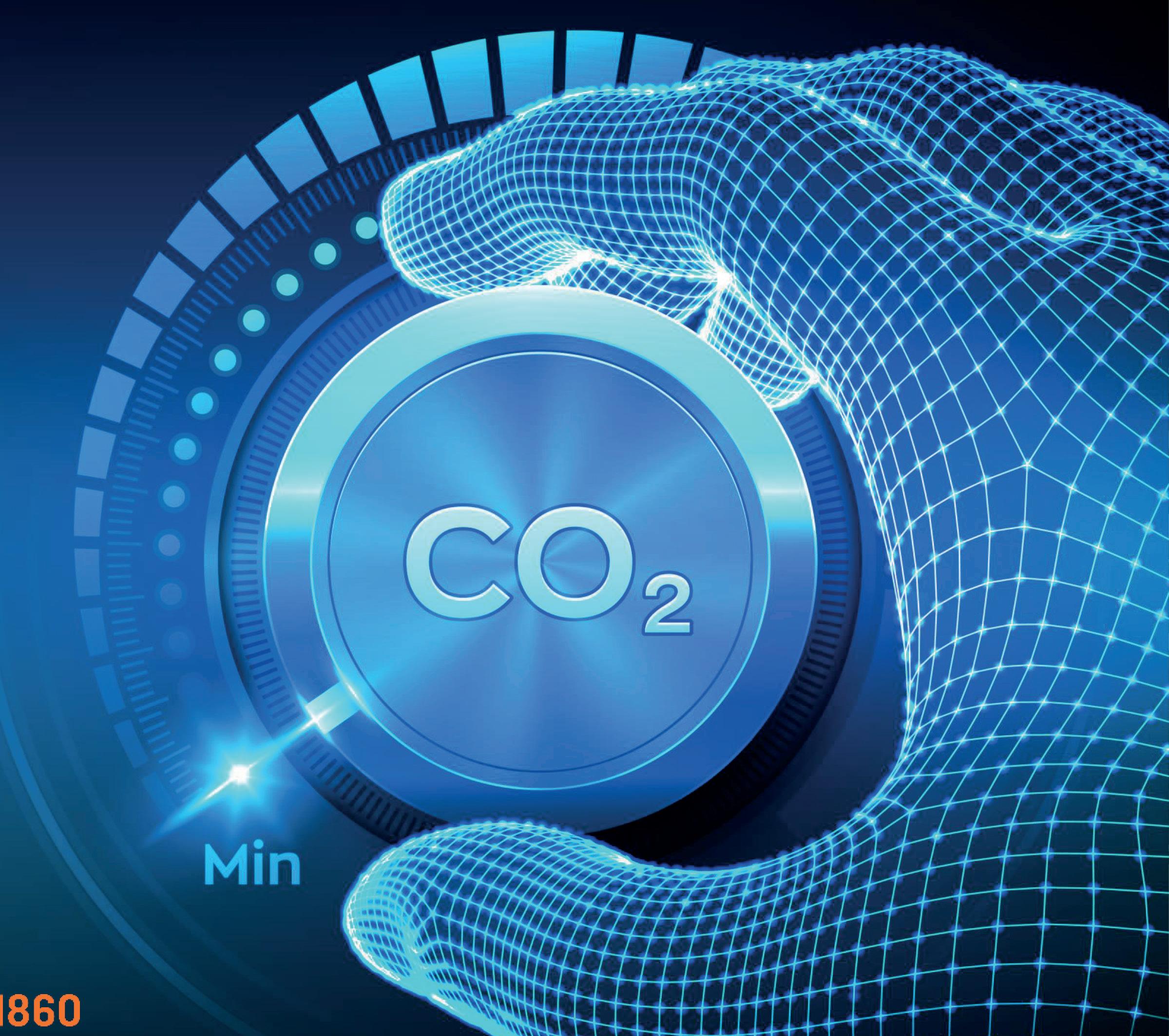
Fig 2. CCEP’s emissions breakdown by scope, 2019�
Mr Richardson stated that packaging was critical to achieving net zero, as it is responsible for 43% of the company’s Scope 3 emissions. Therefore, he believed that glass could grow in the company’s portfolio, due to its usability and sustainability.
CCEP plans to ensure that all its packaging is reusable, refillable or recyclable. Thus, Mr Richardson believes glass could dominate the ‘on the go’ market, provided it is made to be lightweight, resealable and robust.
Consequently, Coca-Cola’s most recent global campaign ‘Real Magic’ features glass bottles – the iconic packaging for coke.
Mr Richardson also outlined his hopes for the FEVE-led ‘furnace of the future’, which would be a breakthrough for reducing the carbon emissions of glass packaging production.
However, Mr Richardson questioned whether the technology could be implemented in enough areas by 2030 for it to have a significant effect on emissions. He believed it would require approx. 50% of the industry to use these new furnaces within the next 10 years to achieve decarbonisation.
Continued>>
NSG PILKINGTON HYDROGEN TRIALS
Andrew Keeley, Principal Technologist at NSG Pilkington2, discussed the outcome of the hydrogen firing trials undertaken at Pilkington’s Greengate furnace in St Helens, UK. (Fig 3)
Mr Keeley spoke on how the trials were working towards NSG’s decarbonisation strategy. He said that hydrogen was ‘very attractive’ to the company due to its potential to reduce CO2 emissions substantially, without the need to drastically change furnace designs.
Firing 100% of hydrogen instead of natural gas at NSG’s Greengate float glass manufacturing site on its cross fired furnace would reduce CO2 emissions by approx. 80%, whilst the remaining CO2 would be from the decomposition of carbonates.
In August 2021, the company ran two separate programmes to test whether the furnace could run on hydrogen in any capacity.
The first trial was for port one of its furnace, where a series of six-hour tests were conducted under the manual control of an R&D team. In these tests, the hydrogen percentage was gradually increased to 100%. This was to identify the maximum percentage that could be used on the port whilst maintaining an effective operation.
The second programme was a fiveday continuous trial where 15% of hydrogen was used on all H2 ports. During this trial, the furnace was in full automatic control.
Before NSG undertook this trial, it did extensive CFD (computational fluid dynamics) modelling to understand the impact on the furnace operation and structure from firing hydrogen. Mr Keeley outlined the concerns the company had prior to the trials:
“Hydrogen burns with an invisible flame, so there is a big drop in the emissivity of the flame as you go to higher percentages of hydrogen.
“Another factor related to hydrogen is its low calorific value, so the volumes of fuel that you need to fire increase substantially. You have to fire three times the volume of fuel on a given port to get the same amount of energy into the furnace, on a firm per firm basis.”
Hazard and operability report
Mr Keeley also outlined several risks from the company’s HAZOP report (a hazard and operability study). One of the main issues was that if a hydrogen control valve failed during reversal, the backpressure produced would cut off the entire site’s gas supply. Therefore, NSG set appropriate measures in place to ensure this issue couldn’t arise.
Hydrogen also has the potential to leak through any small orifice, so a gas detector system was installed for the current pipes at Greengate - although fully welded pipes would be used for a permanent installation.
Additionally, concerns over invisible flames outside of the furnace were addressed with thermal imaging cameras, and cullet bays were converted into hydrogen delivery stations to solve layout and transportation issues.
Port one trials
The three-week long trial started on 10th August 2021. There were six hours of trials per day, with the percentage increased manually by 10% (starting from 20%) every three hours. This increased until the 18th, where the percentage remained at 100% for the rest of the trial. At full flow, a tanker of hydrogen was used every 40 minutes.
The trials progressed as expected, with the equipment performing well and the production unaffected by the trials. Mr Keeley said that the batch melted effectively underneath hydrogen flames, with no changes in furnace conditions downstream. However, even with thermal imaging cameras, the flames were often still invisible – making it one of the main challenges moving forward with hydrogen.
Despite this, 100% of hydrogen was successfully fired on port one. The company also did not see a significant increase in NOX emissions, despite this being one of the potential risks of firing hydrogen.
Mr Keeley said: “[The emissions] were well within the scope of our existing pollution control plant. Based on that, we would be comfortable in terms of firing hydrogen, at least on the upstream part of the furnace at the moment.”
Full furnace trials
From 13th September 2021, the entire furnace operated on 15% hydrogen for 4.5 days. NSG had planned to run 20% on all ports, but could only run 15% due to supply issues.
Mr Keeley said the trial was largely ‘unnoticed’ by the furnace operator due to the furnace functioning as usual. Glass quality also remained consistent throughout the trial, with good yields and no deterioration in product quality.
Unlike the port one trials, the full-furnace trials were operated automatically via a modified gas chromatograph. The chromatograph could analyse the composition of the fuel and assess the percentage of hydrogen. The signal was then fed into the control systems to adjust the fuel being fired on each of the ports within the furnace.
Overall, the full furnace trial proved that the plant could cope successfully with a hydrogen/natural gas blend. Mr Keeley said that the trials ‘gave confidence’ that NSG could convert its furnace to fire hydrogen when it becomes available in large quantities.
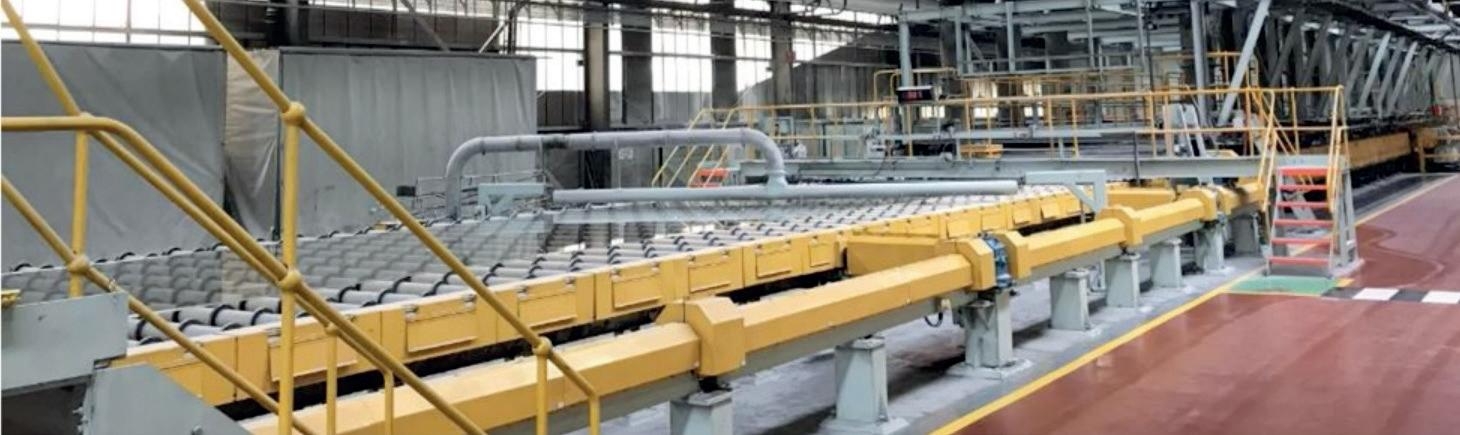
� Fig 3. NSG discussed the outcome of hydrogen firing trials at Pilkington’s Greengate furnace in St Helens, UK.
Continued>>
Air Products is blazing a new trail for oxy-fuel burner technology . . .
Boost your performance and productivity for better glass with the Cleanfire® HRx ™ burner!
Upgrading your oxy-fuel burners, adding burners to boost production, or converting your air-fuel furnace to oxy-fuel? The patent pending Cleanfire HRx burner offers you expanded functionality and flexibility with unmatched performance. It can deliver: •Increased flame radiation for high fuel efficiency •Ultra-low NOx emissions •Foam reduction capability for higher-quality glass •Enhanced productivity •Optional remote performance monitoring feature •Integrated high efficiency oxygen supply system This burner is the latest innovation in the long line of industry-leading Cleanfire® burners for the glass industry, which are now able to utilize hydrogen as a fuel, for a lower carbon footprint. To learn more or to schedule a demonstration in our state-of-the-art lab, call 800-654-4567 (code 10868) or visit airproducts.com/HRx.
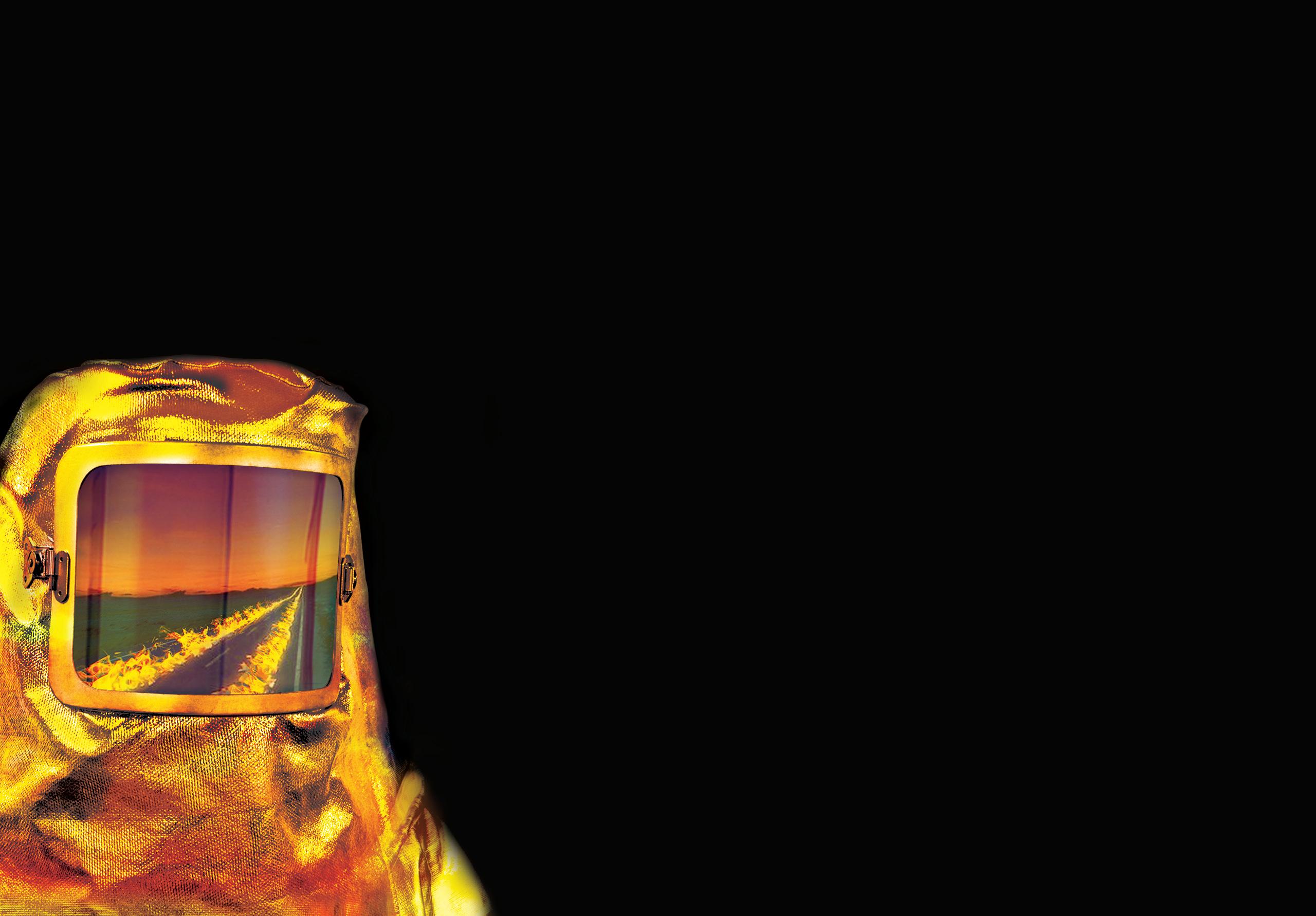
© Air Products and Chemicals, Inc., 2021
tell me more
airproducts.com/HRx
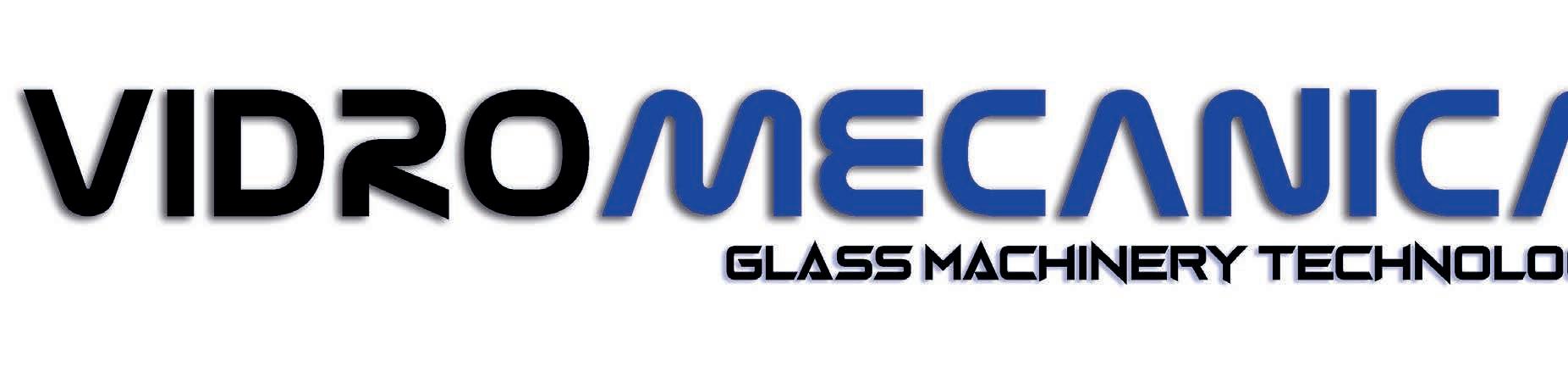
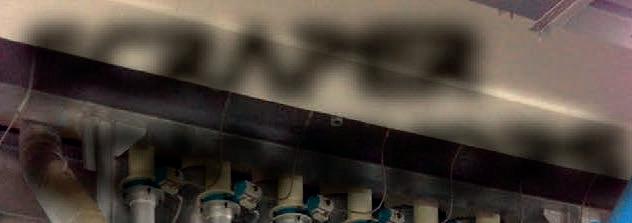
Automatic Chutes SCRAPER CONVEYORS
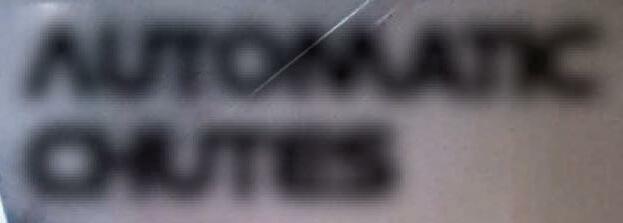
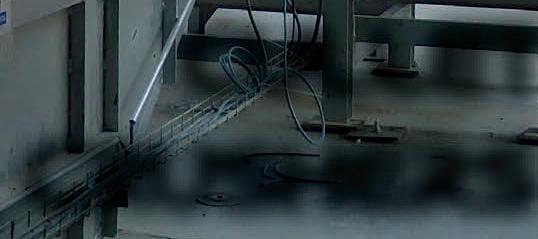
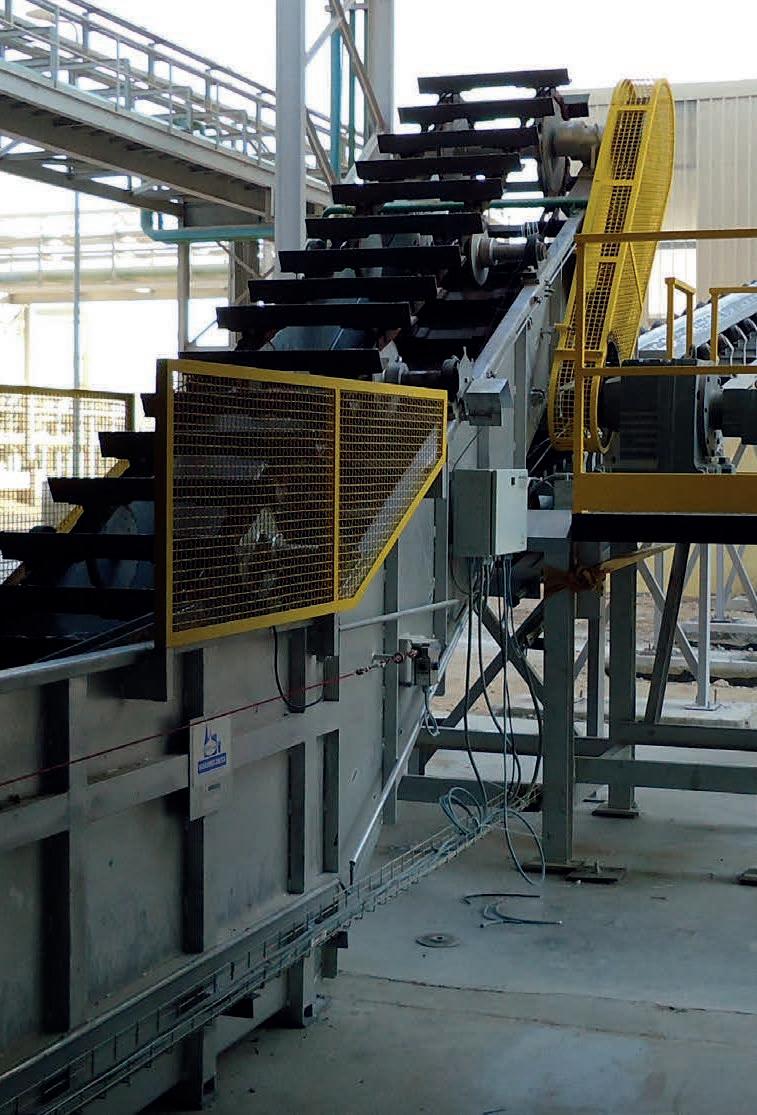
CULLET CRUSHERS
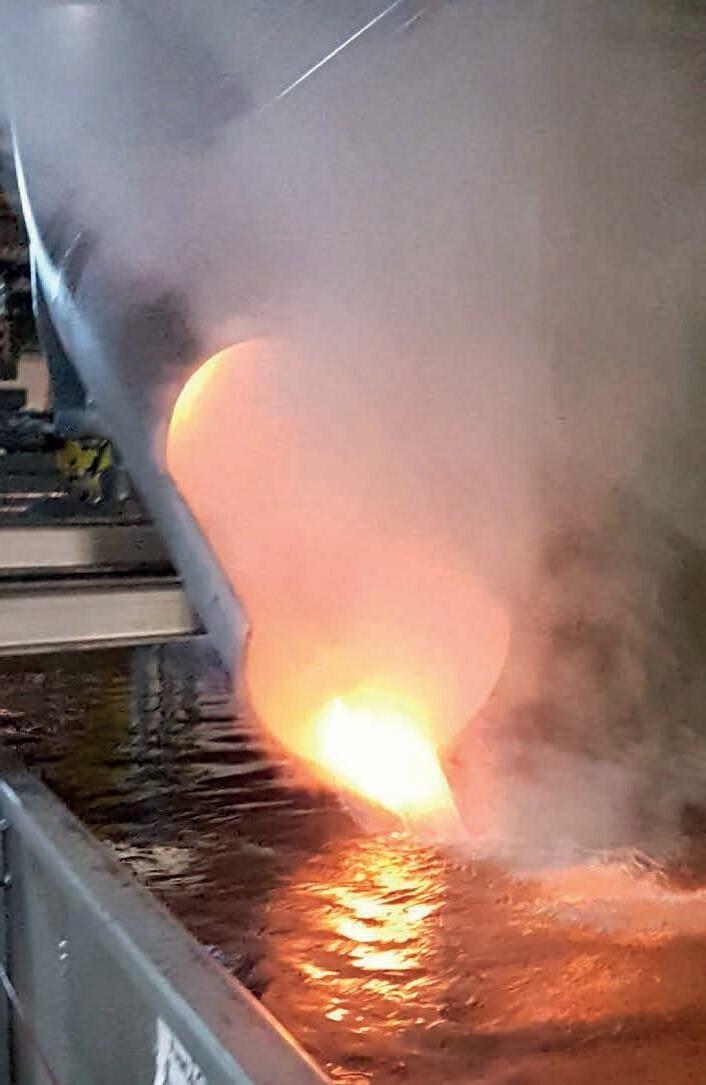

FINANCING SUSTAINABILITY - IFC
Li Tu, Senior Investment Officer, and Marek Stec, Senior Industry Advisor, from the International Finance Corporation (IFC)3 highlighted the company’s approach to financing sustainability in the glass industry.
Ms Tu and Mr Stec discussed IFC’s Climate Change Action Plan, implemented in April 2021, and its sustainability objectives for the glass industry. They also highlighted IFC’s mission to reduce poverty by supporting development in emerging areas.
IFC is a member of the World Bank Group (WBG), with offices in nearly 100 countries around the globe. Ms Tu described the company as an institution that provides advisory services and technical support as well as financial aid; IFC has invested more than $321 billion since the company’s founding in 1956.
The company largely focuses on developing countries, maximising the amount of finance available in the areas that need it the most, as well as creating new markets and expanding weaker ones. IFC also offers equity, trade and commodity finance, donors and loans; its 3.8 credit rating provides competitive loan rates within the market.
The company’s manufacturing portfolio is categorised into three main areas: chemicals and fertilisers, construction material and energy efficient machinery. Glass falls into the second largest category of construction material.
Mr Stec said that IFC was aware of the growth within the glass industry, and emphasised the increasing demand for glass products in several sectors including flat glass, beverages and electronic goods.
Sustainability
One of IFC’s main goals is sustainability. The company focuses on development impact and climate change as well as promoting environmental, social and corporate governance standards. This includes advice on how to improve issues such as energy efficiency.
The WBG plans to invest $200 billion over the next five years in climate related financing. Ms Tu said that, for IFC, this would be reflected in two commitments. The first being that, by July 1st 2023, 85% of IFC’s operations will align with the objectives of the Paris Agreement, such as limiting global warming to 1.5°C. This number will increase to 100% by July 1st 2025.
The second commitment is that at least 35% of WBG’s financing will have climate co-benefits over the next five years. In manufacturing, IFC will support proven abatement measures and innovative new technologies.
To achieve these objectives, IFC has collaboratively developed a strategy to assess the Paris Agreement alignment, which is currently being tested and refined. According to the methodology, projects must pass both a mitigation assessment and an adaptation and climate resilience assessment.
Mr Stec defined mitigation as the influence of industry towards the climate, and adaptation as the influence of climate towards the industry. He said both of these forces could be balanced and assessed.
Green loan
IFC’s ‘Green Loan’ is specifically for projects that are climate-related (migration or adaptation). The Green Loan Principles have four core components: 1. Use of proceeds must be destined exclusively for eligible green projects. 2. Must undergo a strict process for project evaluation and selection. 3. Processes must be managed to ensure that they will be allocated to eligible green projects. 4. Processes and the impact of eligible green projects must be reported.
Ms Tu said that companies eligible for the Green Loan can use the IFC and WGB name to promote their image in the market, and will have access to a ‘green channel’ within the IFC, resulting in a quicker processing time.
Ms Tu also outlined a set of criteria for eligibility, and said that if a glass company addressed any of the sustainable practices listed, then it could apply for a Green Loan. Practices included: having a heat recovery system, exploring carbon capture and storage, having good energy efficiency and using renewable energy.
After applying, in-house industry specialists and experts from IFC’s climate team join other assessors to decide whether the company can grant the loan.
Glass objectives
Over the years, the glass industry has implemented a variety of methods to reduce its carbon impact, such as developing carbon capture technology and increasing the percentage of cullet usage. However, Mr Stec said that it was still difficult to find a method that was ‘economically feasible’ on a large scale, and that a solution for decarbonisation would require some time.
The company has the following sustainability objectives for glass: � Ensure efficient energy consumption in the production processes (supporting clients in glass recycling). � Reduce the amount of GHG emissions � Increase the cullet usage in production � Have innovation in products that contribute towards sustainability
IFC has worked with two major glass manufacturers, Kioo and NSG. Kioo is the largest glass container manufacturer in East Africa, and the only such producer in Tanzania, whilst NSG has operations in over 20 countries.
IFC increased the production capacity of Kioo by approx. 35% and implemented several sustainable practices, such as energy-efficient retrofits and increased cullet use. Similarly, at NSG, the company enhanced productivity through new R&D investments. Clean technologies and ‘green’ glass products (triple glazed glass) were also introduced.
Additionally, IFC has recently released a report entitled ‘Strengthening Sustainability in the Glass Industry’. Ms Tu said this report outlined the company’s view on the industry and its approach to support sustainable development within it.
Continued>>
CARBON NEUTRALITY - STEKLARNA HRASTNIK
Tilen Sever, Research Scientist at Steklarna Hrastnik4, spoke about the company’s four-phased project for carbon neutral glass production.
Mr Sever discussed how hydrogen could significantly reduce the company’s scope emissions and enable it to reach carbon neutrality.
Steklarna Hrastnik has 160 years of experience developing and manufacturing engineered glass products in partnership with other brands. The company produces approx. 280 tons of glass daily, has nearly 600 employees and exports its products to around 55 countries worldwide.
The company’s range of products includes premium and ‘super-premium’ glass containers, primarily dedicated to the spirits, perfumery and cosmetics market. Its main focus for glass making is innovative and sustainable solutions.
Mr Sever said: “Reaching climate neutrality by 2050 is one of the biggest challenges for the industry today. Meaning that the glass industry will have to decarbonise completely over the next 30 years.”
Steklarna Hrastnik focuses on sustainability challenges such as renewable energy sources, improving energy efficiency, renewable fuels, electrification and green investments and innovations.
Pilot project
In 2017, Steklarna Hrastnik started a project for an innovative, hydrogenbased solution for glass melting, which would use pure, low-carbon hydrogen gas to reduce carbon emissions per unit of glass produced.
This resulted in the OPERH2 Pilot System (Fig 4 and 5), which introduced a number of new technologies for production. These included: renewable energy sources, the use of solar cells, the production and storage of green hydrogen and the partial addition of hydrogen to natural gas.
The production of renewable energy from solar cells is used to power the system. The electric current then splits water into oxygen and hydrogen, and is later stored in hydrogen vessels. Consequently, the only emission produced in the glass melting process is water rather than CO2.
After investing €1.5 million in development and building the industrial pilot, the system was successfully commissioned in 2020. For small-scale demonstrations, key components of the system included: a photovoltaic (PV) power plant, an electrolyser, hydrogen storage and a glass furnace of 200 kg/day capacity.
One of the main goals was to balance the capacity of the electrolyser with the solar power generation, which was achieved through software. Mr Sever described the energy management system, which was installed through control units at individual production sources:
“The software solution combines, aggravates, predicts and optimises allincluded production sources and flexible loads automatically, or on the request of the user. The solution provides benefits, savings and a lower ecological footprint.”
Messer also helped Steklarna Hrastnik produce a customised burner with hydroflexibility. The system used hydrogen from 0% to 100% with air and oxygen combustion options, and informed the company of the technological limits of using hydrogen for melting.
Mr Sever said: “By implementing the pilot system, we can confirm that a PV plant with an electrolyser and glass furnace is possible, and hydrogen can be used with up to 100% of higher efficiency. The hydrogen is also suitable for oxyfuel as well as regenerative furnace technology.”
Fig 4. OPERH2 Pilot system, an innovative and hydrogen-based solution for glass melting.

Fig 5. Outline of Steklarna Hrastnik’s OPERH2 project.
Scope emissions
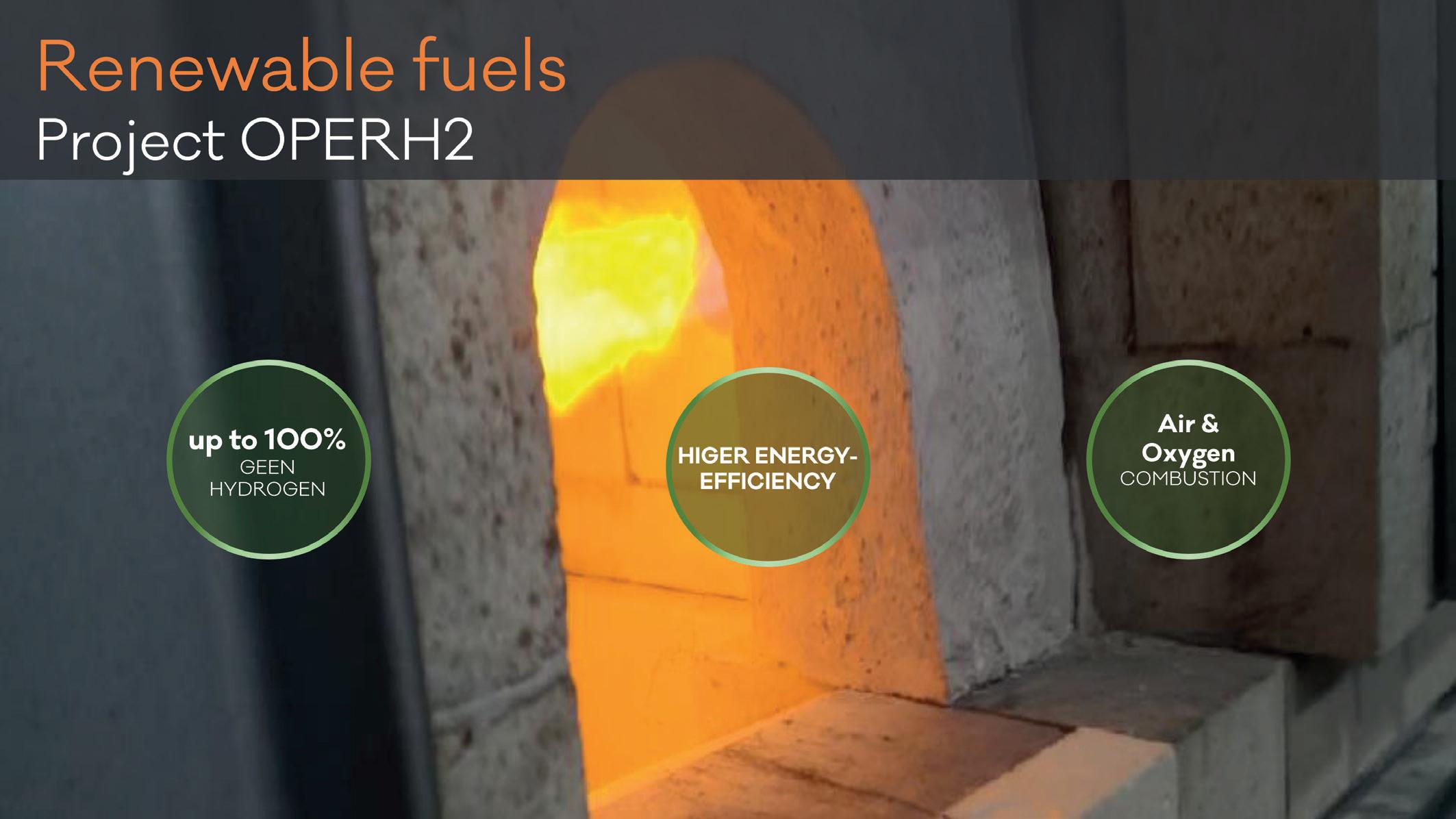
Steklarna Hrastnik demonstrated an almost carbon neutral glass production by using the OPERH2 pilot system, due to a reduction of scope emissions. Mr Sever outlined the company’s scope emissions as follows: Scope 1 emissions are made up of process emissions, fuel emissions and other direct emissions. Scope 2 emissions are purely from electricity, whilst Scope 3 emissions are value chain emissions from the supply of raw materials.
The first measure to reduce CO2 was to use 100% of external cullet. This resulted in the complete reduction of process emissions, and a reduction of fuel emissions by 25%. By using external cullet (collected from waste recycled glass) as the only raw material, the Scope 3 emissions were reduced by 84%.
The second measure was to use hydrogen. By using 100% of hydrogen fuel, Steklarna Hrastnik reduced fuel emissions entirely, but Scope 2 emissions increased by 950%. However, by using renewable energy only, the company’s Scope 2 emissions were reduced by 98%.
The last measure was to implement electrification (annealing) as well. With this measure, the company additionally reduced its direct emissions by 70%. Mr Server concluded: “Altogether, we reduced the Scope 1, 2 and 3 emissions by 92%. Which means we almost completely reduced all emissions. However, to go to 100% additional carbon offsets are needed.” He suggested that planting 0.4 trees per tonne of glass could enable the company to reach carbon neutrality.
Phase two
Now the pilot phase is finished, Steklarna Hrastnik is working towards its three phases for large-scale demonstrations, which are: achieving an industrial qualification for the use of hydrogen in glass furnaces (2022), designing and constructing the system (2022-2023) and operating the system (2024-2028).
The large-scale system design is composed from a PEM water electrolyser, which will be used to produce hydrogen from clean electricity. The electrolyser will be included in a mix of grid services to reduce the price of hydrogen production. Mr Sever said that the creation of hydrogen would be compensated with large-scale industrial hydrogen storage with a short, stable carbon-free supply of fuel.
After the hydrogen is produced, it would then be applied to the existing oxyfuel firms, to avoid any damage to the furnace whilst melting, at a capacity of 120 tonnes per day.
Mr Sever said that, on average, hydrogen fuel would replace 50% of primary fuel, resulting in approximately 20-25% lower carbon emissions from fuel. This would save more than 3000 tonnes of CO2 per year.
Steklarna Hrastnik is ambitious to replace a third of its fossil fuel consumption by 2025 using green energy. The company plans to increase its energy efficiency by 10% and decrease its carbon footprint by over 25% - which will decrease by a further 15% (approx.) by 2030.
1. CCEP: https://www.cocacolaep.com/
2. NSG Pilkington: https://www.nsg.com/ 3. IFC: https://www.ifc.org/
4. Steklarna Hrastnik: https://hrastnik1860.com/