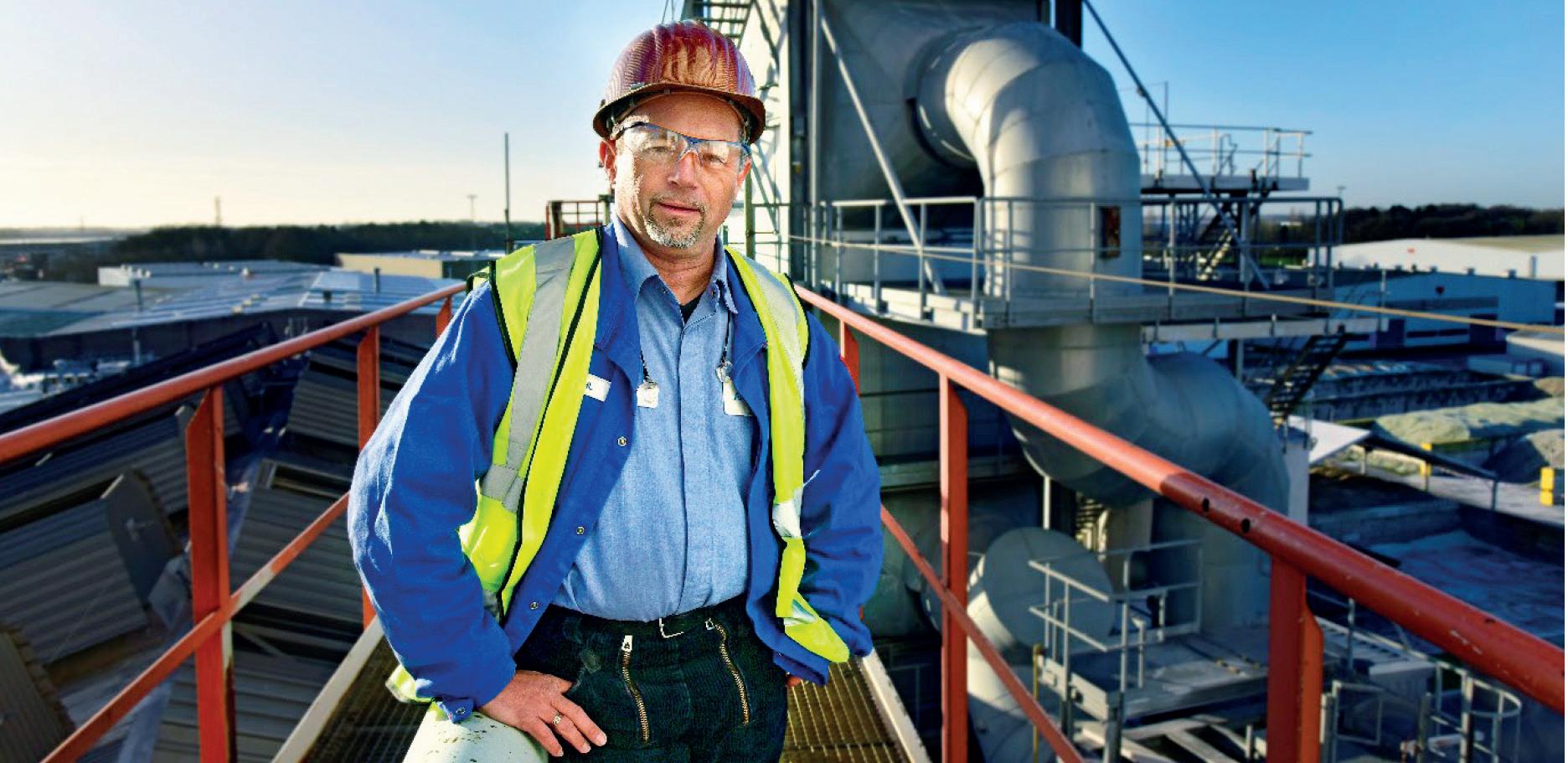
8 minute read
Decarbonisation: Ardagh
While work continues to develop breakthrough decarbonisation technologies in container glass manufacturing, Sven-Roger Kahl, Manager of Furnace Operations and Innovations at Ardagh Glass Packaging discusses alternative routes to reduce CO2.
� AGP’s Sven-Roger Kahl, Manager of Furnace Operations and Innovations.
Container glass manufacturing is an energy-intensive process that currently uses fossil fuel as its main energy source. For a sustainable future, the industry must develop breakthrough and alternative technologies to address carbon emissions – the only downside to the packaging material beloved of the food and beverage industry. Reducing the industry’s carbon emissions to net zero by 2050 is the goal and, unsurprisingly, there are several ways to get there.
Presenting to the industry at Glass Trend in December 2021, Sven-Roger Kahl, discussed how alternative technologies can reduce the carbon footprint of the container glass industry.
He explained how AGP has proven that carbon savings can be achieved through using more recycled cullet, alternative recycled raw materials, batch pre-heating and cullet drying, and talks about the challenges of each different route.
Each of these methods impacts energy consumption, which in turn impacts the CO2 footprint. Where alternative recycled raw materials do not directly reduce the carbon footprint they always contribute to the circular economy.
Recycled cullet
Using high quality recycled glass cullet to make new glass containers requires less energy in the furnace. Every 10% of cullet used in place of raw materials reduces energy consumption by 2.53% and reduces the use of primary raw materials. Plus, the more cullet re-used in the furnace means less goes to landfill.
The challenges around using more cullet are quality, availability and price.
In terms of quality, any organic contamination within the cullet can cause discolouration and blistering in the glass. Contamination such as CSP (ceramic, stone, porcelain) can lead to inclusions in the final product, and any metal contamination can shorten the lifetime of furnaces.
Ardagh has been working with cullet suppliers for many years to agree higher cullet quality standards across the industry. Its Cullet Task Force, formed in 2009, has led to a change from a local to a centralised cullet process across all of Ardagh’s 20 European plants.
An approved cullet specification and cullet quality monitoring system have been instrumental in ensuring consistency and reliability of cullet quality, while an internal cullet database enables live trend monitoring of cullet quality on factors such as pollution and colour.
Most aspects of this specification are summarised in the German Industry Standard T120 issued by BV Glas.
AGP uses up to 90% recycled cullet in its European furnaces, but availability is a challenge. The Close the Glass Loop multistakeholder platform created by FEVE, the European container glass federation, has set out to achieve a post-consumer glass container collection target of 90% in Europe by 2030, and to ensure that this is recycled into the container glass bottleto-bottle production loop.
This will be achieved through close cooperation between the whole glass packaging value chain, sharing best practices on innovative and tailored collection models, high quality sorting and recycling, and consumer communication campaigns.
Data recently released by the Close the Glass Loop platform confirms that glass collection and recycling in Europe increased in 2019 to reach an average rate of 78%, representing a growth of 2% compared to the previous year’s performance and an all-time record high.
See the latest glass recycling map and discover more on closetheglassloop.eu
The fluctuating price of recycled cullet also impacts the amount that can be used; adding more cullet to the batch recipe must still be financially sustainable.
Alternative recycled raw materials
Most raw materials are carbonates: soda ash, limestone and dolomite, which all release CO2 during the melting process when making new glass containers.
However, there are alternative raw materials from waste streams that are carbon neutral, or are circular materials, and AGP has proven they can be used effectively in place of specific raw materials in the furnace: � Slags from blast furnaces can be used to produce all glass colours, replacing up to 20% of sand weight. Aluminium and steel smelting slags show similar potential based on theoretical calculations but are not yet used in industry. � Fly ashes: Sodium Carbonate can be used to produce flint and amber glass colours, replacing up to 30% of soda ash. � Water treatment waste: Calcium carbonate, Sodium sulphate and Iron (hydr)oxide can be used to produce flint and emerald glass colours, replacing up to 80% of limestone.
The impact of using these alternative raw materials can be substantial.
For example, by using Calumite (blast furnace slags) in place of the standard batch, process CO2 is reduced from 46.8
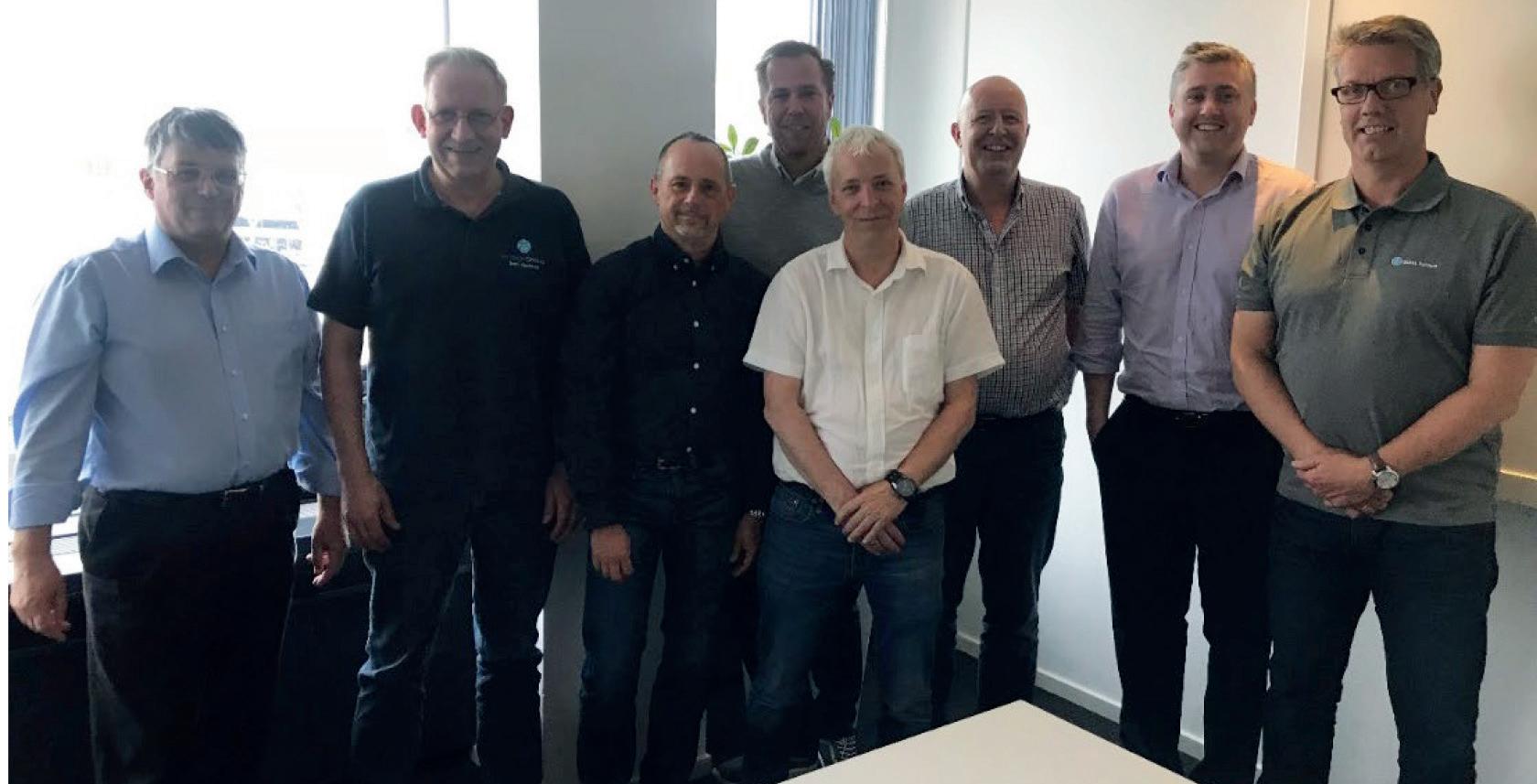
The Cullet Team at AGP, working on improvements in recycled cullet strategy.�
Close the Glass Loop Case Study: Zero Waste Leeds
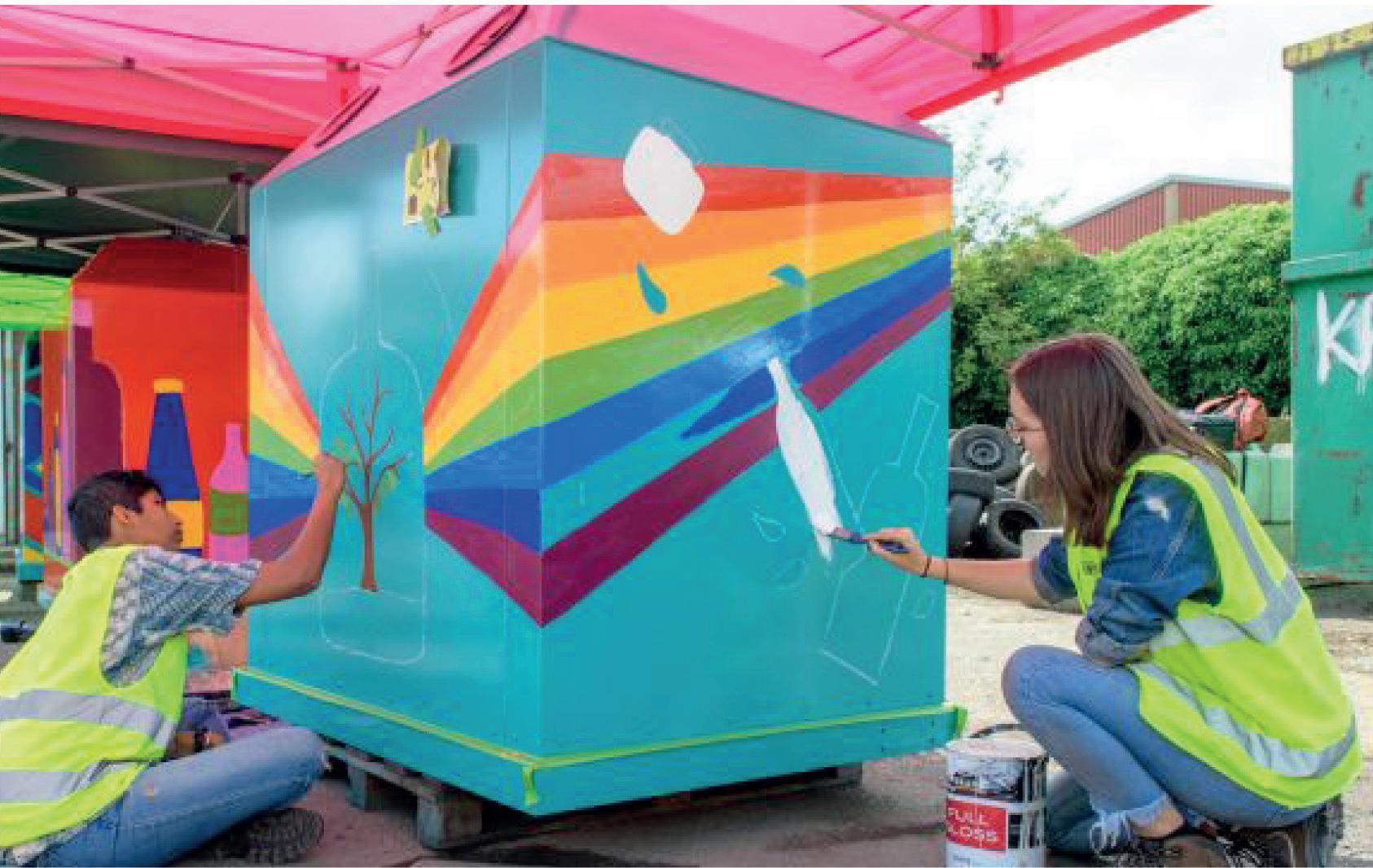
In summer 2021, AGP supported a local social enterprise: ‘Zero Waste Leeds’ to encourage the people of the City of Leeds in Yorkshire, UK, to keep recycling glass. This campaign involved a 12 week-long communication and community engagement campaign and included the installation of three new glass recycling banks around the city. Local children created colourful designs for each new glass bank, to make recycling a more fun and enjoyable experience. The campaign showed residents where to recycle their glass with an interactive map and explained how it is recycled within Yorkshire in a true circular economy, saving both natural resources and CO2. The outcome was in impressive 43% increase in glass collected from the new banks across the three sites, compared with the same period in the base year of 2019.
kg per ton of glass, to 37.6kg per ton of glass. This reduces process emissions from the batch by 20% and overall CO2 emissions by 4%.
By using aluminium and steel slagbased batch in place of the standard batch, process CO2 is theoretically reduced from 27.8 kg per ton of glass, to 7.7kg per ton of glass. This potentially reduces process emissions from the batch by 70% and overall CO2 emissions by 10%.
There are challenges when using waste stream materials which require the knowledge of experienced glass technologists: � chemical composition and stability
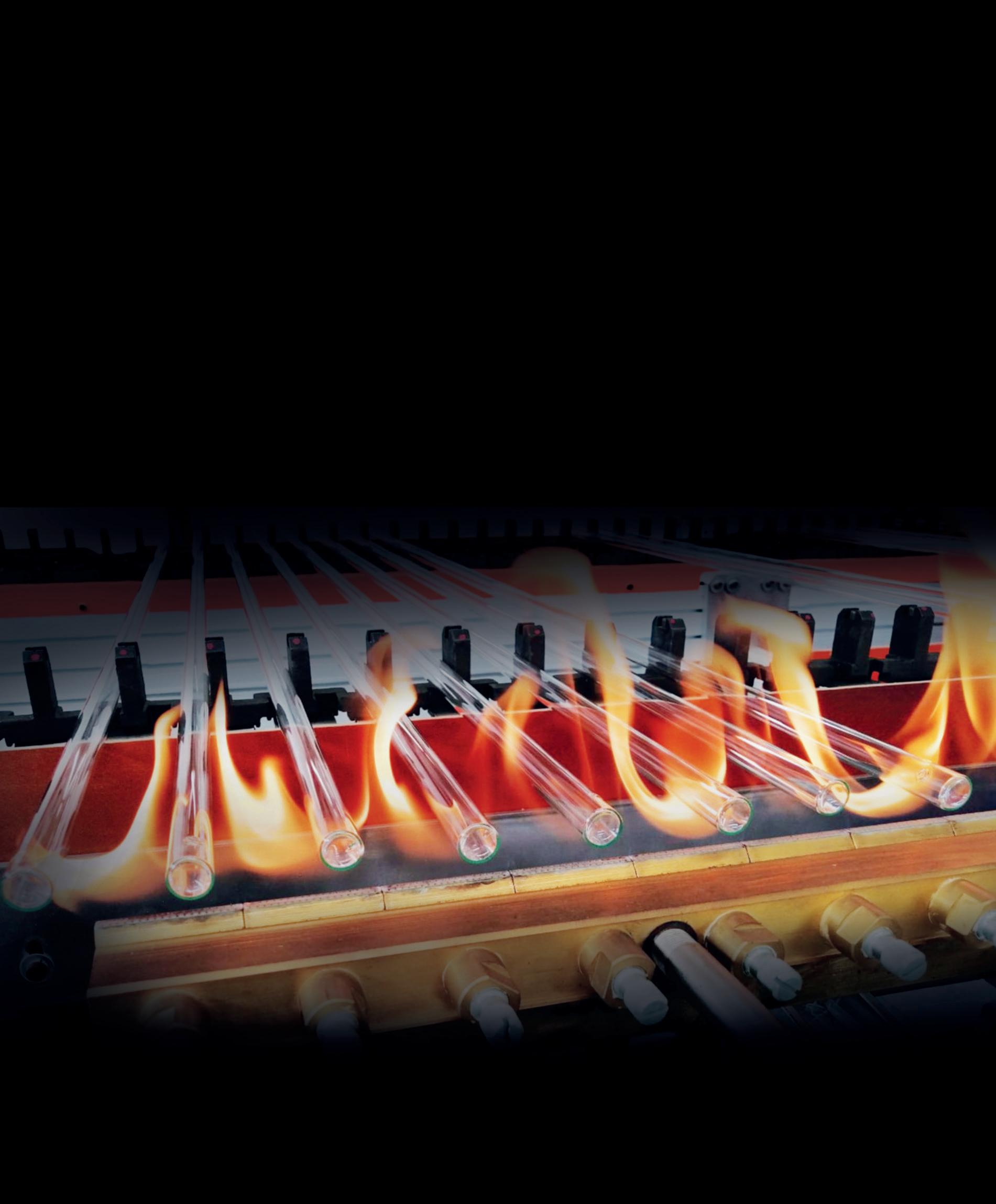
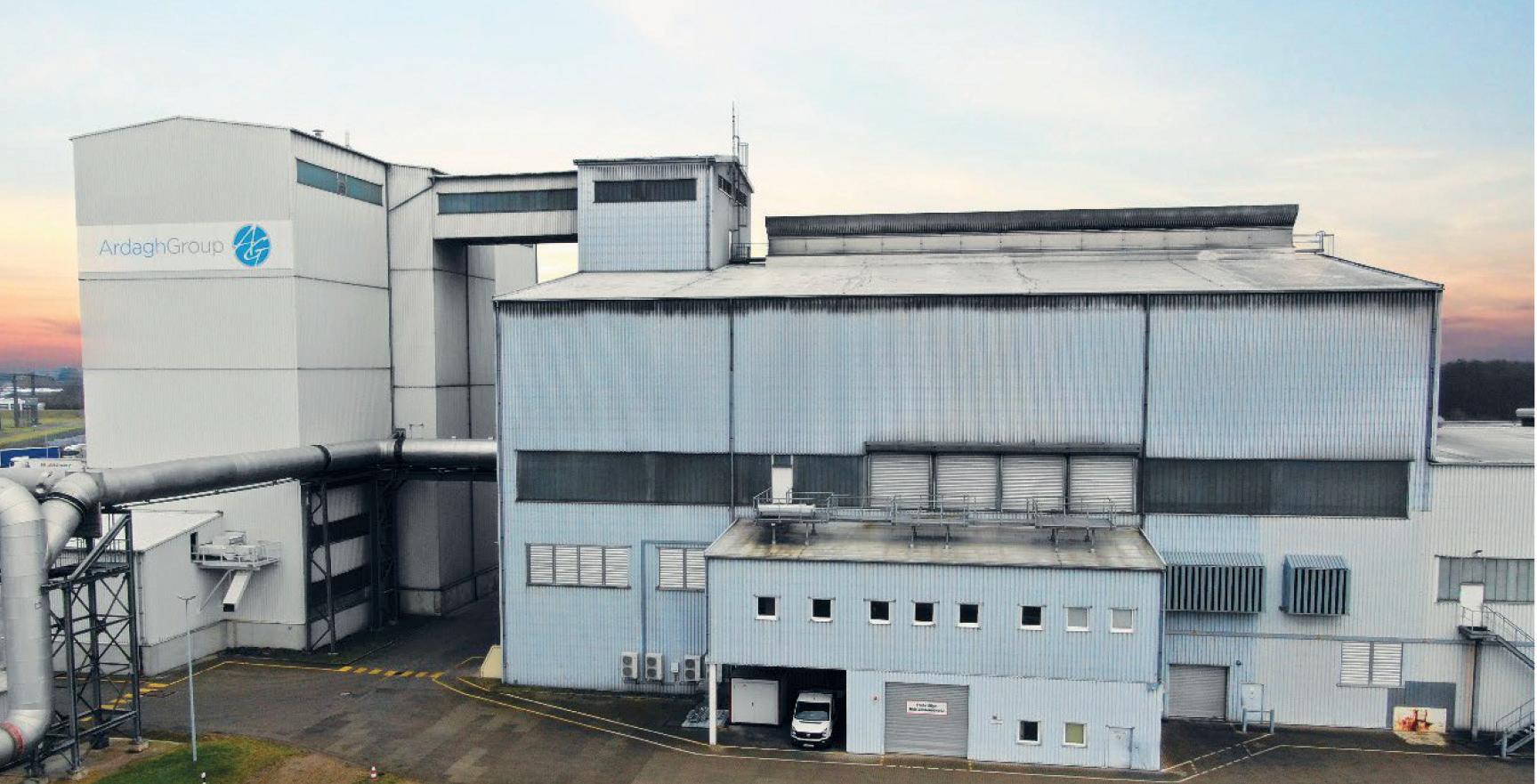
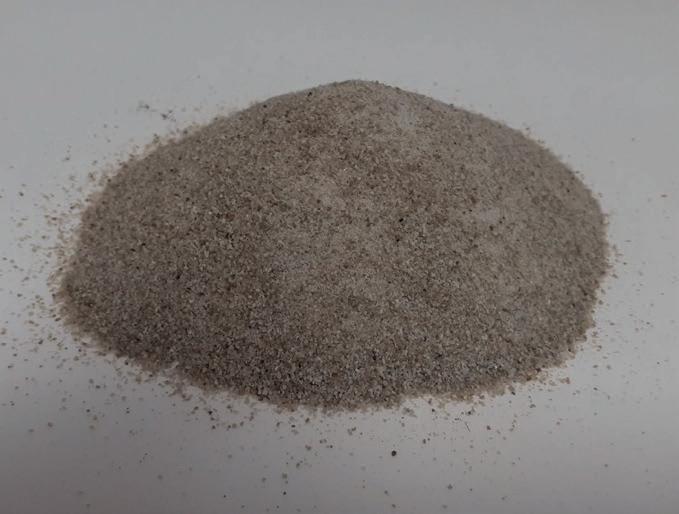
� Calumite can be used to produce all glass colours and can replace up to 20% of sand weight in the batch.
� contamination by heavy metals and volatile elements (chlorine and fluorine) � grain size distribution (some are very fine) � unexpected chemical reactions from waste materials and stability of supply.
The glass technologist must work together with the waste material producer, to decide which fraction can be used in glass melting and what additional processing steps may be necessary to make the waste material fit for glass melting.
Traditionally the glass industry has been hesitant to use alternative raw materials due to concerns over the resulting bottle quality, but AGP has proven that if your alternative materials are high quality, the end result is as good as using traditional raw materials.
Batch and cullet pre-heating
AGP first installed a batch pre-heater at its Nienburg plant in Germany in 1987 and thanks to their multiple benefits, has increased that to six installations with a seventh currently in construction. The pre-heater heats the batch and cullet, which means less energy is required to melt materials in the furnace.
Our example shows the difference in conditions in the furnace, with and without a pre-heater. The blue line indicates the amount of batch ingredients yet to be melted thanks to the difference in temperature. In terms of performance, pre-heating: � reduces flue gas volume and CO2 by 15% � increases the melting capacity by 10% � reduces energy costs by 15% � there is little maintenance required and as the pre-heater installed in 1987 is still in operation, its lifetime is at least 34 years.
The challenges of using pre-heaters are: � the CAPEX required - payback is between three and seven years � the installation requires space, which can sometimes require a complete footprint reconfiguration � companies require knowhow, from design through to operation, to achieve the optimum benefits.
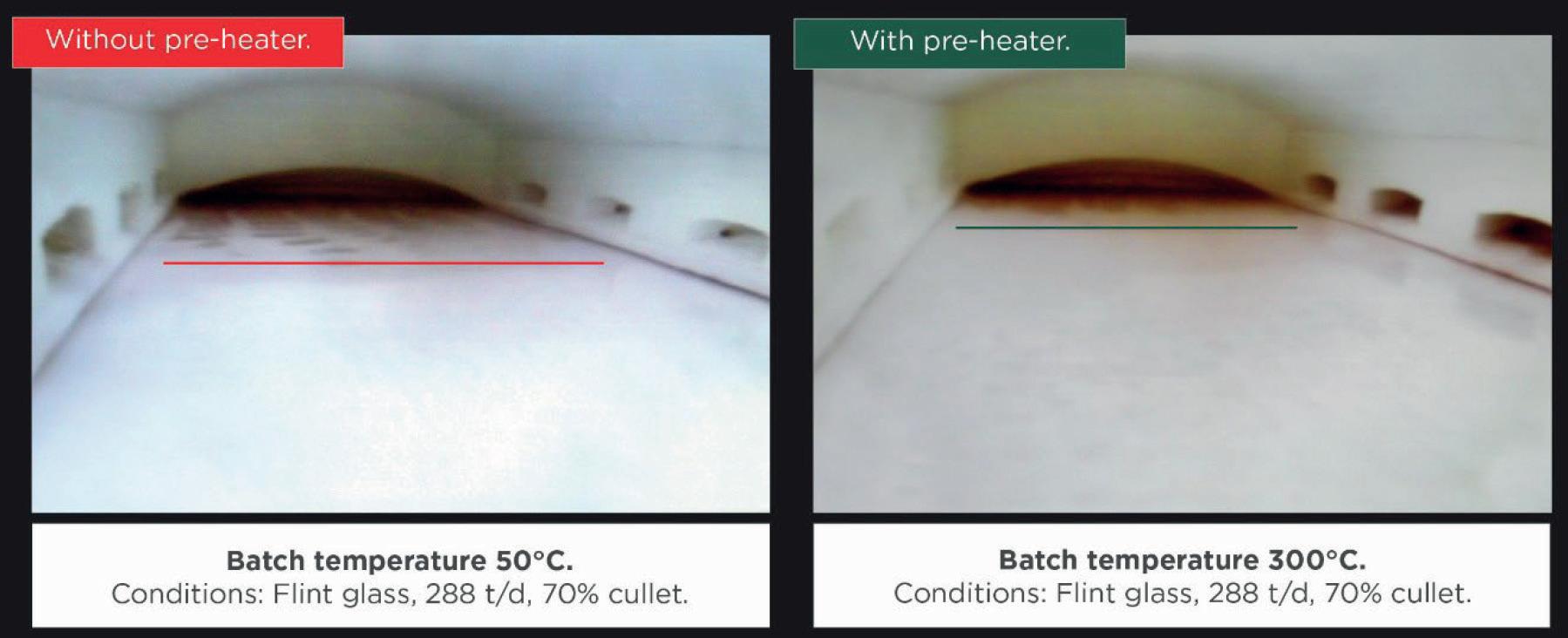
� Difference in conditions in the furnace, without and with a pre-heater. Red and blue lines indicate the batch line in the furnace.
Cullet drying and pre-heating
During winter, snow, water and ice accumulate on cullet in open storage. As water in all its forms causes obstacles in operation and increases energy consumption, it makes sense to dry it out and pre-heat the cullet before it goes into the production process.
The way we do this is to blow warm air from the plant’s production hall into a heat exchanger, which heats up the air further. A second heat exchanger transfers the energy from the hot air to the wet or frozen cullet, which defrosts and dries it, leaving high quality cullet. The system can process 457 tons of wet or frozen cullet per day.
The benefits are: � 190 kW of thermal energy is gained from the heat generated in the production hall � weather-induced operational problems are solved � CO2 is reduced by 334 tons per year due to using residual heat from the production hall instead of using additional energy to dry the cullet in the furnace. This is equivalent to the annual CO2 emissions of 208 cars.
This system is also known as ‘Frozen Cullet’, a program supported by the German Ministry of Environmental Affairs.
The challenges of using the heat exchangers are: � the CAPEX required – payback is between one and three years � the installation requires space � companies require knowhow to realise the full benefits.
To read more about Ardagh Group’s sustainability progress and to read our 2021 Sustainability Report, please visit ardaghgroup.com/pdf/sustainabilityreport-2021. �
Ardagh Glass Packaging, www.ardaghgroup.com
� The AGP facility in Neuenhagen, Germany where a batch pre-heater is installed between the batch plant and the furnace.