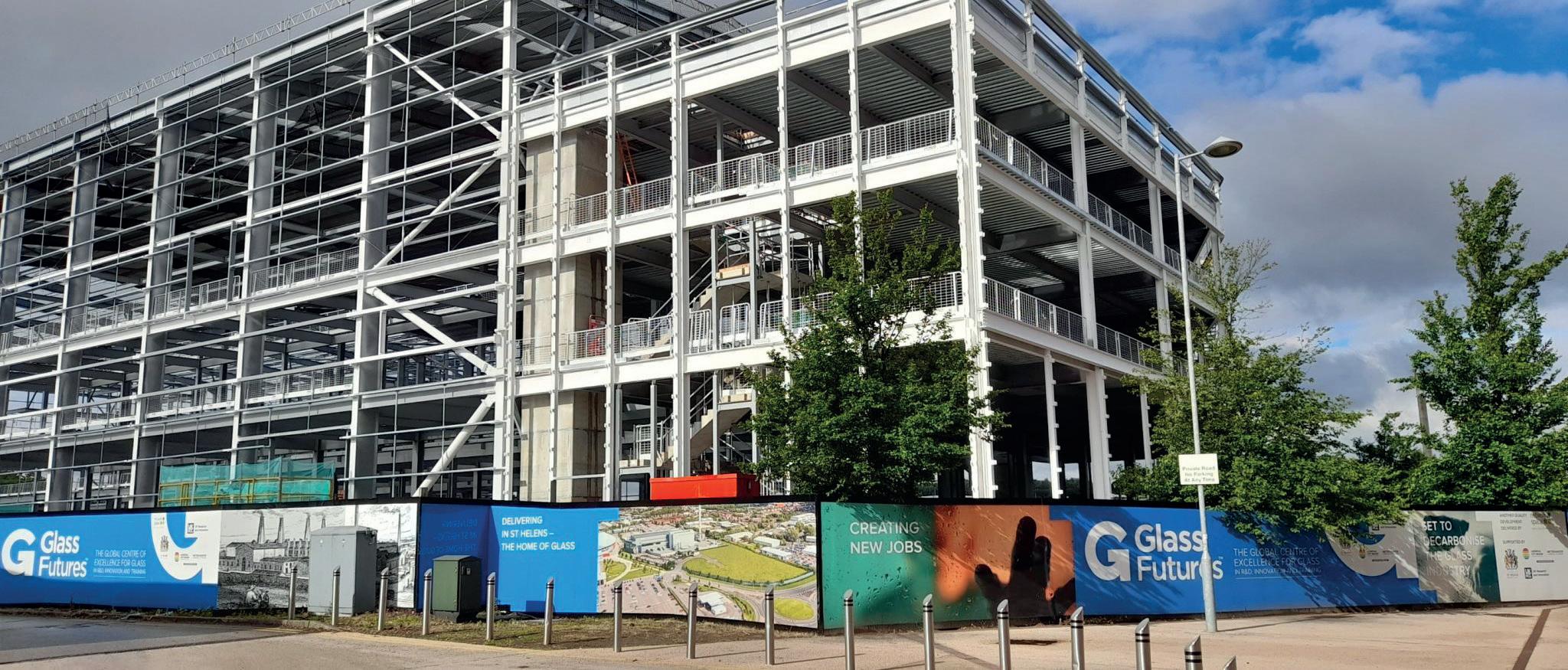
11 minute read
Furnace Solutions review
Decarbonisation the focus at Furnace Solutions
More than 100 glass industry professionals attended Furnace Solutions earlier this month. It was the first time the event had been held in person in three years and for many it was a chance to catch up at long last. Greg Morris was in attendance.
Glass industry solutions to tackle the climate crisis were among the main topics at the Furnace Solutions conference this month.
More than 100 people were in attendance as the annual glass manufacturing conference organised by the Society of Glass Technology (SGT) took place in person for the first time in three years.
It was held at a new venue, the Totally Wicked Stadium in St Helens, UK, next door to the Glass Futures research and development construction site (pictured top).
Attendees among the 107 audience included glass manufacturers, technology suppliers as well as academia. Among the attendees were O-I, Saint-Gobain, Guardian and Ardagh and as well as suppliers such as Fives, Land Ametek, PSR, Sefpro, Zippe and Hotwork International. Visitors came from USA, Italy, France, Germany and Poland as well as the UK.
The two-day conference included 14 presentations from companies such as NSG group, Glass Technology Services, Simpson Combustion, CelSian, DSF and Emisshield.
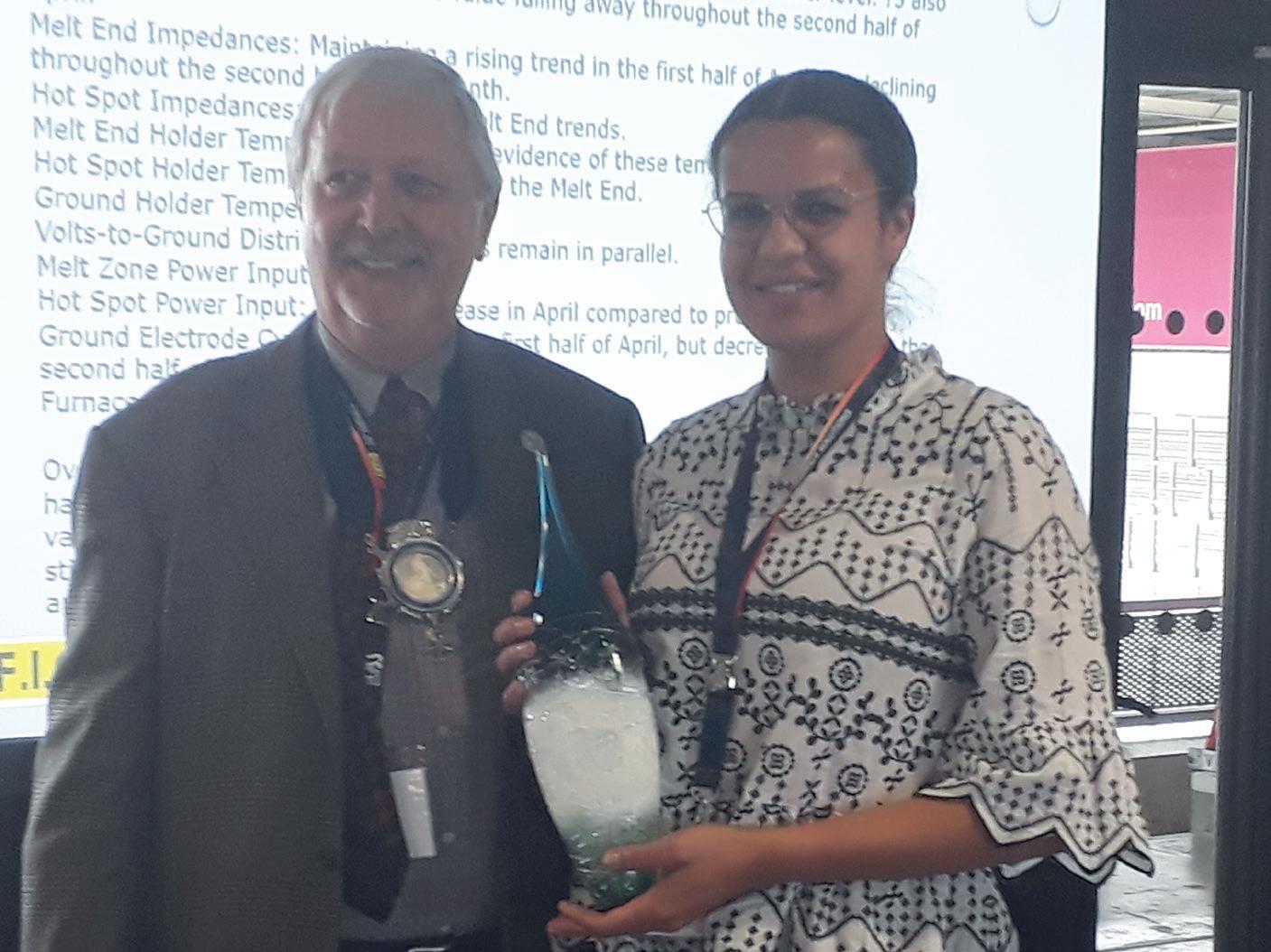


Above Martyn Marshall of Glass Technology Services (GTS) discussed Alternative Raw Materials from Waste and Decarbonisation. � Wayne Bridger of BOC.�
� FIC’s Christoph Jatwauk, Chris Windle of DSF Refractories who discussed Hy-ghly durable refractories for hybrid glass melters and Kelvin McAlister of Emisshield.

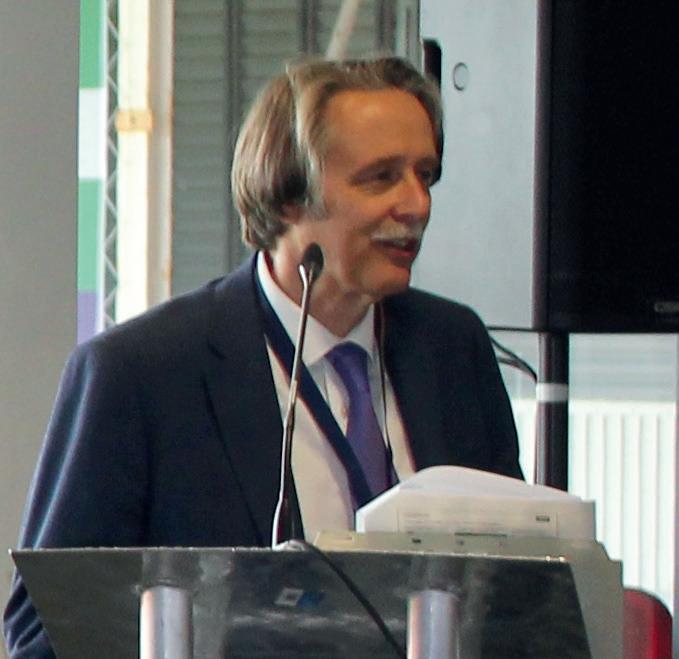
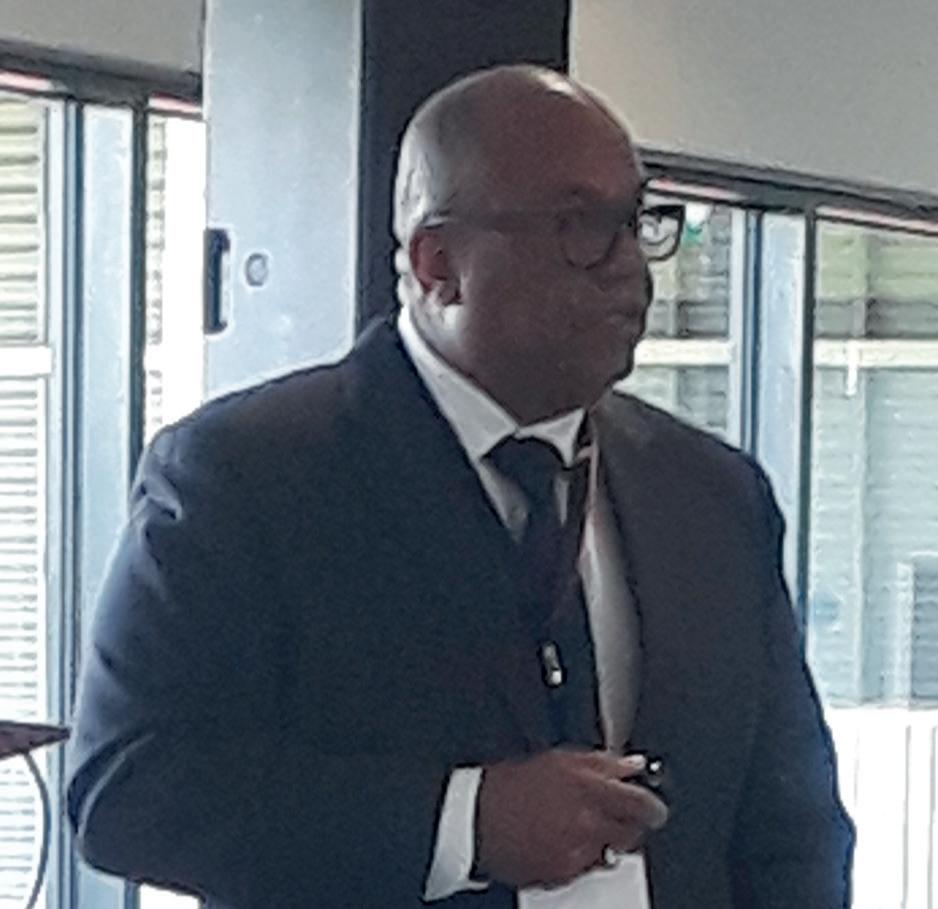
BEST PAPER
Every year, the Michael Garvey award is given for best conference paper and this year Encirc’s Batch and Furnace Supervisor, Lara Edison won for a paper discussing recent biofuel firing trials at Encirc (pictured first page and right).
Ms Edison provided a presentation which discussed a successful threeweek trial at the company’s Derrylin, Northern Ireland site.
Gas was switched with biofuels made from animal fat in a project organised in conjunction with UK research and development group Glass Futures.
The trial helped reduce the CO2 emission of each glass container by 89% compared to the average container produced at the Derrylin plant in 2020.
SGT president Stuart Hakes said Ms Edison’s paper just edged the other presentations.
“She a confident young woman, who knows her stuff and who delivered her paper very well. We had some strong papers from Andy Keeley at NSG and Wayne Bridger at BOC who ran her close but she just pipped them.
“There is an older generation of glass industry professionals who are in the process of handing over the baton and when you see people like Lara you realise that the future looks good for the industry.”
The Michael Garvey Award is presented each year to the winner of the best paper and is sponsored by Guardian Industries. Recent winners have included Glass Futures Rob Ireson in 2021, Sisecam’s Burcin Gul in 2019 and Giorgio Minestrini of Stara Glass in 2018.
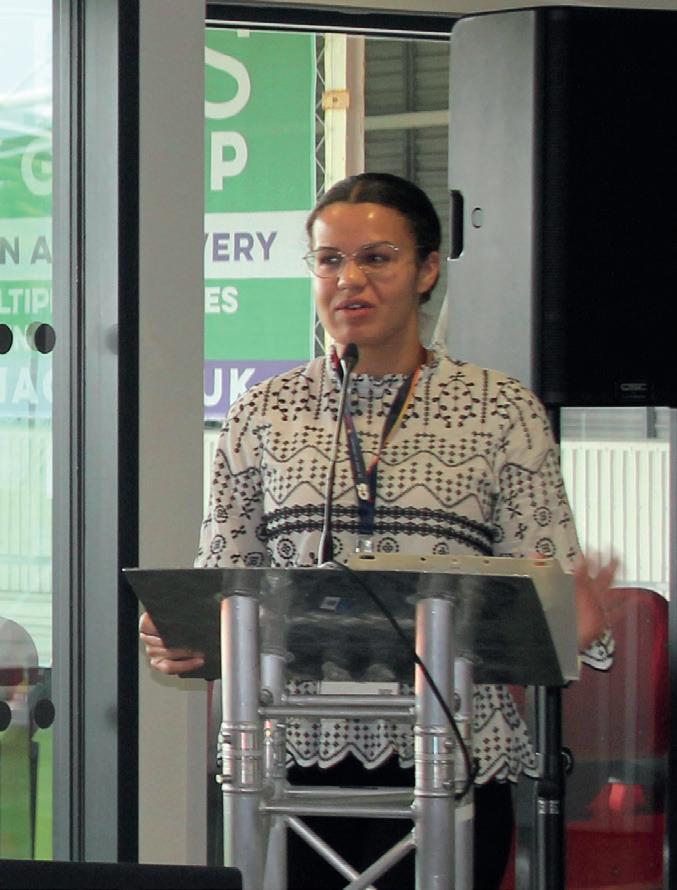
Continued>>
DAY TWO FOCUSES ON ELECTRIC
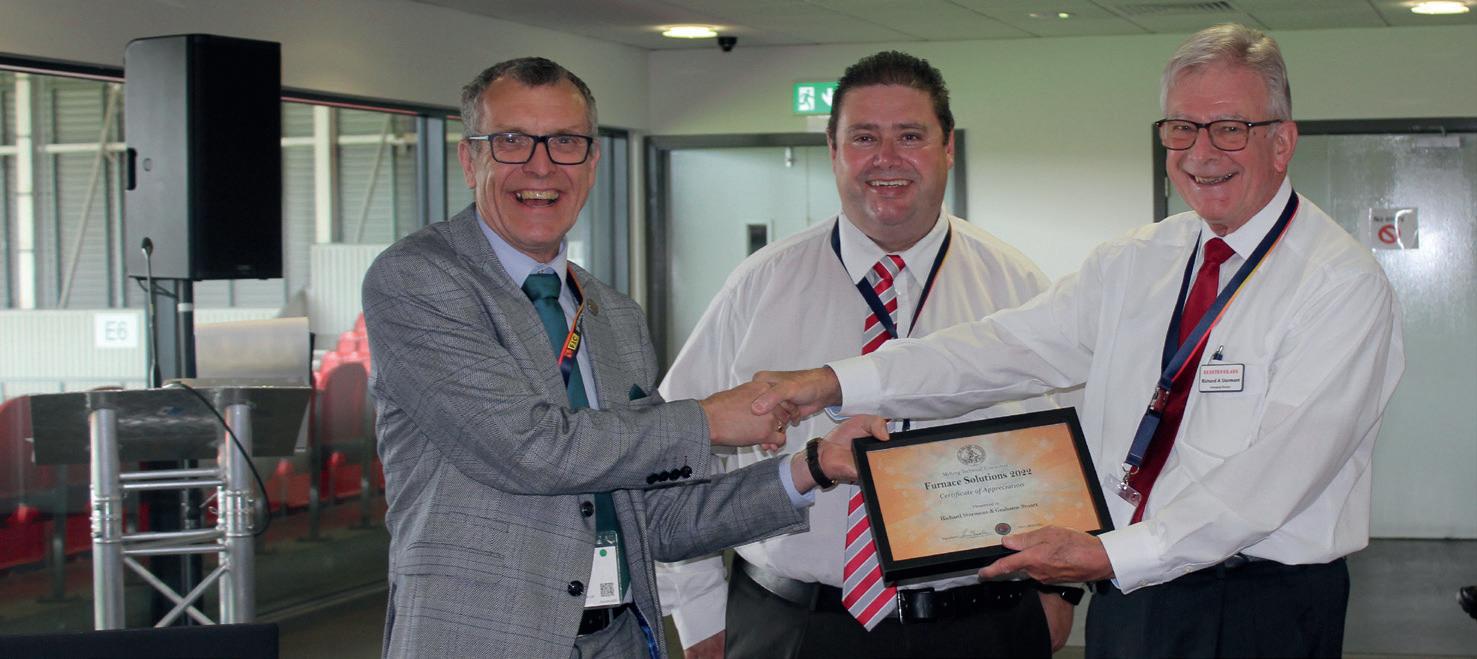
The SGT’s Nigel Longshaw with Grahame Stuart and Richard Stormont of Electroglass.�
Earlier on day two, delegates had heard from Electroglass, Encirc, DSF, CelSian, British Glass and FIC UK.
In the presentation titled: ‘Are we nearly there yet?’ Electroglass’ Richard Stormont focused on electric furnaces, while later in the presentation colleague and Grahame Stuart discussed forehearths.
Mr Stormont said approximately 85% of global glass production is still reliant on fuel-fired furnaces. There is a high degree of losses from these type of furnaces - the losses are typically greater than the net melting energy. Inroads had been made to improve furnace performance, with oxy fuel firing but these are hot top furnaces. Hydrogen is a recent focus but will require investment.
In Mr Stormont’s words if a glass manufacturer is to be totally renewable, the way forward is to use electric melting. He felt though there was no single path for the industry to take – option one was to continue in the current direction with improved energy efficiency measures to reduce emissions and increase furnace life. This direction is still reliant on fossil fuels though.
Option two is to focus on renewable sources such as high efficiency electric melting. The technology already exists and eliminates combustion gases completely.
One established option is the use of electric boosting using electrodes which can boost output by up to 50%. A 50% increase in output by boosting means 33% of furnace output is produced electrically.
In the second half of the presentation, Mr Stuart said not to forget about forehearths. They can bring typical operating energy cost savings of between 60-90% and their homogeneity index is higher than a gas fired equivalent.
The company does a lot of work converting gas heated to all electric forehearths. He provided examples of three projects of various-sized forehearths, one of which lead to an 88% reduction in losses – the equivalent of £744, 000 saving a year.
“This was just one forehearth, imagine what you could do if you had five,” he said.
With the price of gas becoming more expensive, he said the future of electricity is looking bright.
In a presentation titled Hy-ghly durable refractories for hybrid glass melters, DSF’s Chris Windle, said despite three decades of global climate initiatives there are still plans to build more coal-fired power stations.
This was marked in the recent COP26 meeting where, after tense negotiations, China and India agreed to phase down rather than phase out, their use of coal.
Approximately a third of global electricity is generated from coal-fired power stations, contributing about 30% of CO2 emissions. There are currently 8200 coal fired power stations in the world - the majority in China and India. Surprisingly Germany has 63 such stations, while 34 countries are planning to build more coal fired plants.
If no policies were implemented to limit emissions and emissions carry on at their current rate then global temperatures will rise by 4.1C by the year 2100. Most of the earth would be an arid desert, marked with huge thunderstorms in the tropical regions.
“It is an uncomfortable imperative – we need to decarbonise,” said Mr Windle.
In the glass industry there is light at the end of the tunnel, with the increased use of electric melting, use of biofuels and the increased number of hydrogen-focused projects taking place.
In its bid to decarbonise Mr Windle forecast the industry to adopt the use of biofuels as an immediate step, with hybrid furnaces in the interim, with the final step all-electric melting – provided the electricity comes from renewable sources.
He then discussed the various refractories which are available to use with hybrid melters.
Concluding his presentation he said: “I think the industry will get there, we will decarbonise. It’s a big challenge but if we get behind it, we will achieve it. I’d like to think that delegates at Furnace Solutions in the year 2100 will look back and recognise the huge challenge we faced, but that we overcame the challenge and became a decarbonised industry.”
In the final presentation of the conference, Stuart Hakes of FIC UK discussed critical points in how to maintain an electric furnace.
“Know your furnace!” He said. It is the most important asset in a glass company and is the most worthwhile item of equipment in a glass plant.
“People may be sitting in the control room but they have not got a blind idea of what is going on. There may be cameras inside the furnace but what about regenerators bottoms and top, and flames from the port?”
He suggested furnace controllers should visit the plant at night in order to walk around the furnace in the dark to see the regenerator bottoms and spot any inconsistencies.
Health and safety reasons mean it is rare for operators to look underneath the furnace today.
“That is a massive potential problem by not going underneath the furnace to look for wear.”
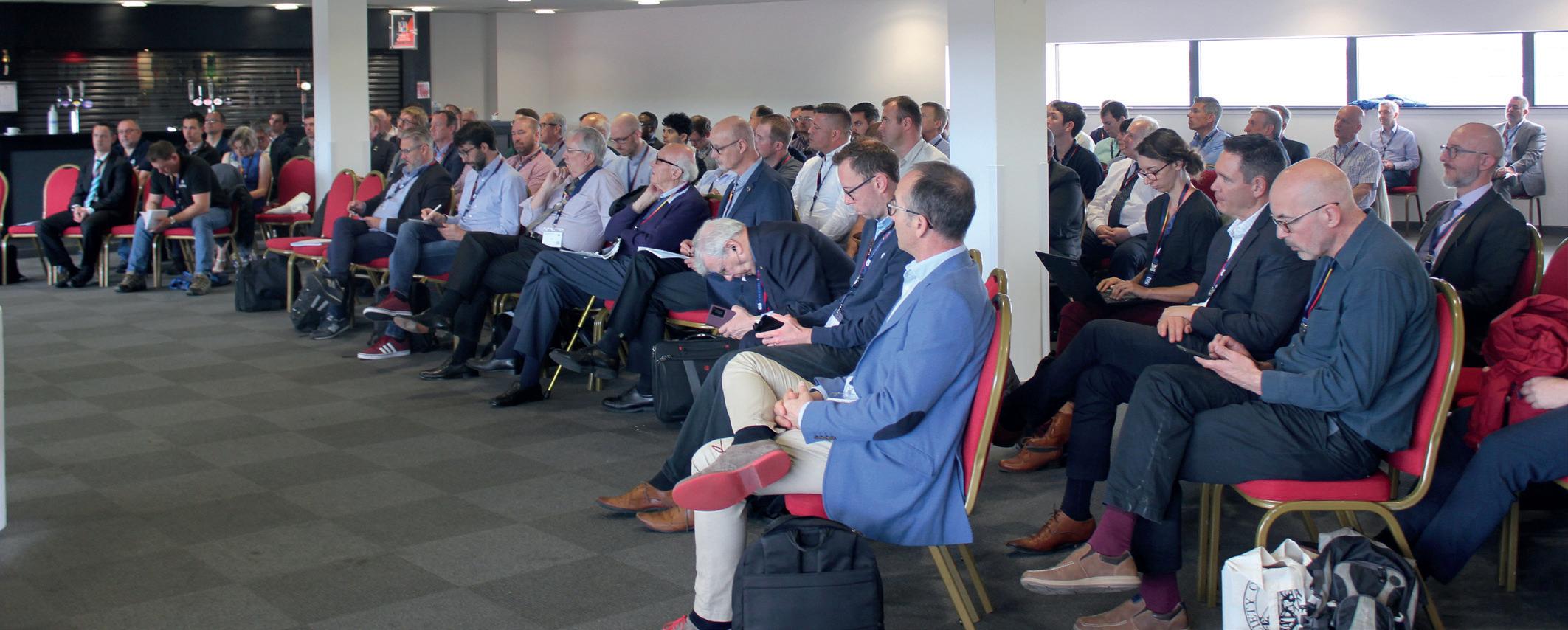
HYDROGEN THE FOCUS ON THE OPENING DAY
Speakers in the opening morning session highlighted the potential benefits of both hydrogen and biofuels as a solution for the industry to reduce its CO2 emissions.
Andy Keeley, of NSG Group, discussed the recent hydrogen trials which had taken place at the company’s Greengate, St Helens facility while Wayne Bridger, of BOC, highlighted the group’s involvement in the trials.
Mr Bridger discussed the use of hydrogen in the glass process and suggested that, while it has tremendous potential, it may be more than 10 years before adequate infrastructure is in place for it to be used on an industrial scale.
“There is a weight of expectation on hydrogen in the future, there is almost a utopian vision of it. But there is nothing built yet, it is a long horizon and we have problems today.”
He suggested a bridging period in the intervening years where glass industry fuel efficiency could be derived from oxy fuel combustion.
His talk was followed by Rob Ireson of Glass Futures who highlighted the potential and challenges of biofuels in the glass production process.
While Glass Futures and container glass manufacturer Encirc have held successful trials using biofuel in the industrial process, there remain concerns over the seasonal availability of some bio-fuels as well competition with other sectors for their availability.
His presentation also outlined how Glass Futures has evolved from an ingenious concept into a team of more than 30 staff, soon to be based at a new 30 tonne/day glass manufacturing pilot facility in St Helens, working alongside a global membership from across the glass industry and academia.
Ernesto Cattaneo, of Stara Glass, discussed the LIFE SUGAR Project and the architecture of a furnace heat recovery system including a steam reformer. The companies involved in the project are: Stara Glass; Johnson Matthey of Reading, England; KT Kinetics Technology of Rome, Italy; Italian research organisation Stazione Sperimentale del Vetro (SSV) of Venice, Italy; and the University of Genoa.
Regenerative glass furnaces are some of the most efficient devices invented. Yet, they still waste about 30% of the fuel energy by expelling hot waste gas.
The LIFE SUGAR Project aims to save such residual heat by utilising it to power a steam reforming reaction and converting a part of the natural gas into hydrogen, to be burned in the furnace.
The reforming unit will be integrated in the particular heat exchange configuration of the Stara Glass Centauro system.
The final goal is to design a furnace with an about 15% lower consumption than a modern regenerative furnace. The project includes the realisation and testing of a lab section (mock-up), the realisation and testing of an industrial section (pilot), 1:5 scaled compared to the final technology, and the final design and commercialisation of the full scaled technology.
Continued>>
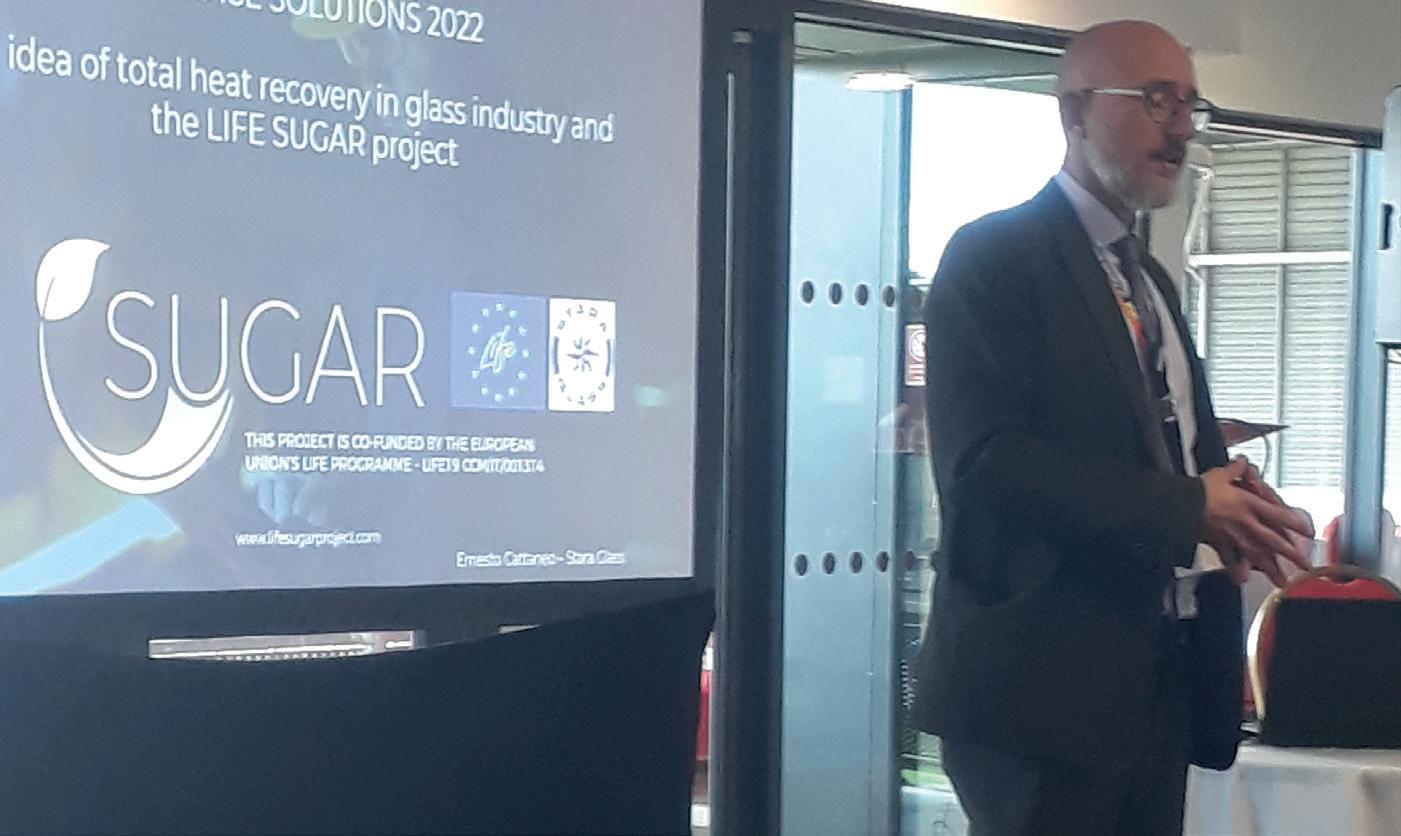
Ernesto Cattaneo of Stara Glass spoke about the LIFE SUGAR project.�
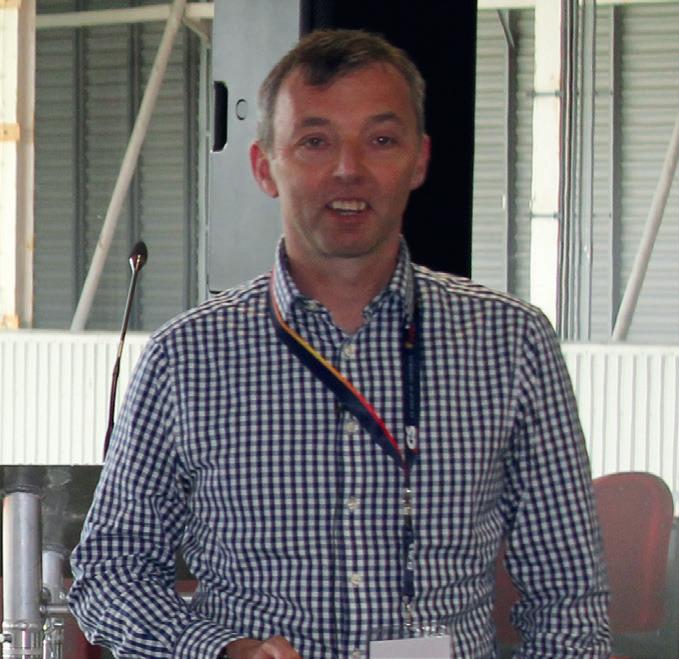
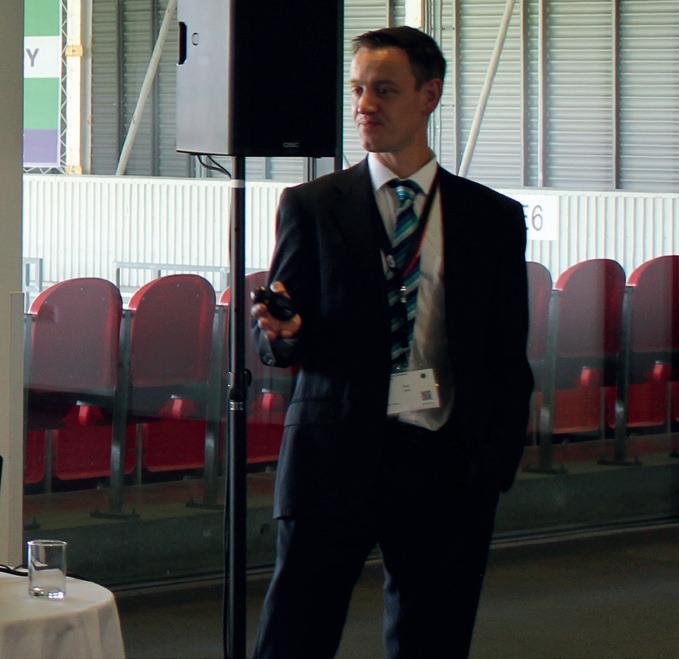
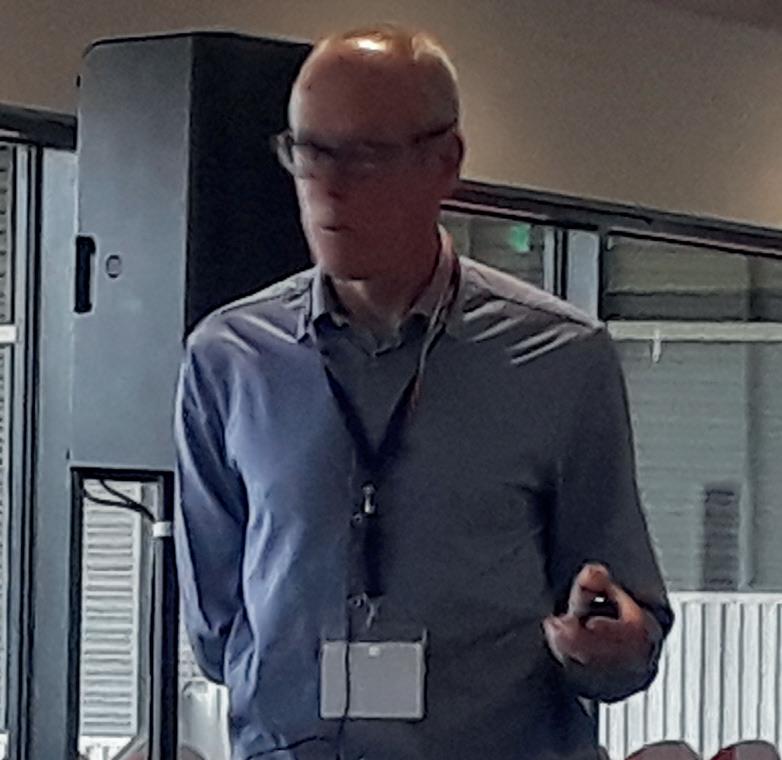
� British Glass’ Mark Pudner, Rob Ireson of Glass Futures and Andy Keeley of NSG. Mr Keeley opened the conference with a paper about hydrogen trials at NSG.
Neil Simpson, of Simpson combustion, gave a presentation titled: ‘How many m3/hr of gas to produce a Tonne of CO2 - how do you justify the investment to reduce both?’
Starting with gas laws and the basics of combustion, he looked at techniques available today and simple financial models to justify investment in energy reduction and resulting emissions.
From gas supply to stack, it will show how analysers, burners, control logic, training, and everything in between can be justified through CO2 and energy savings in a simple spreadsheet. For simplicity, assuming natural gas is methane, if you save 1Nm3, you save 2kgCO2. Assuming CO2 is €100/Tonne, if you save 1Nm3/h, it saves close to £1500 of CO2 credits a year plus the gas savings.
Afterwards Stuart Hakes, SGT president, thanked Glass Futures and St Helens Council and said the venue was extremely appropriate. He added that
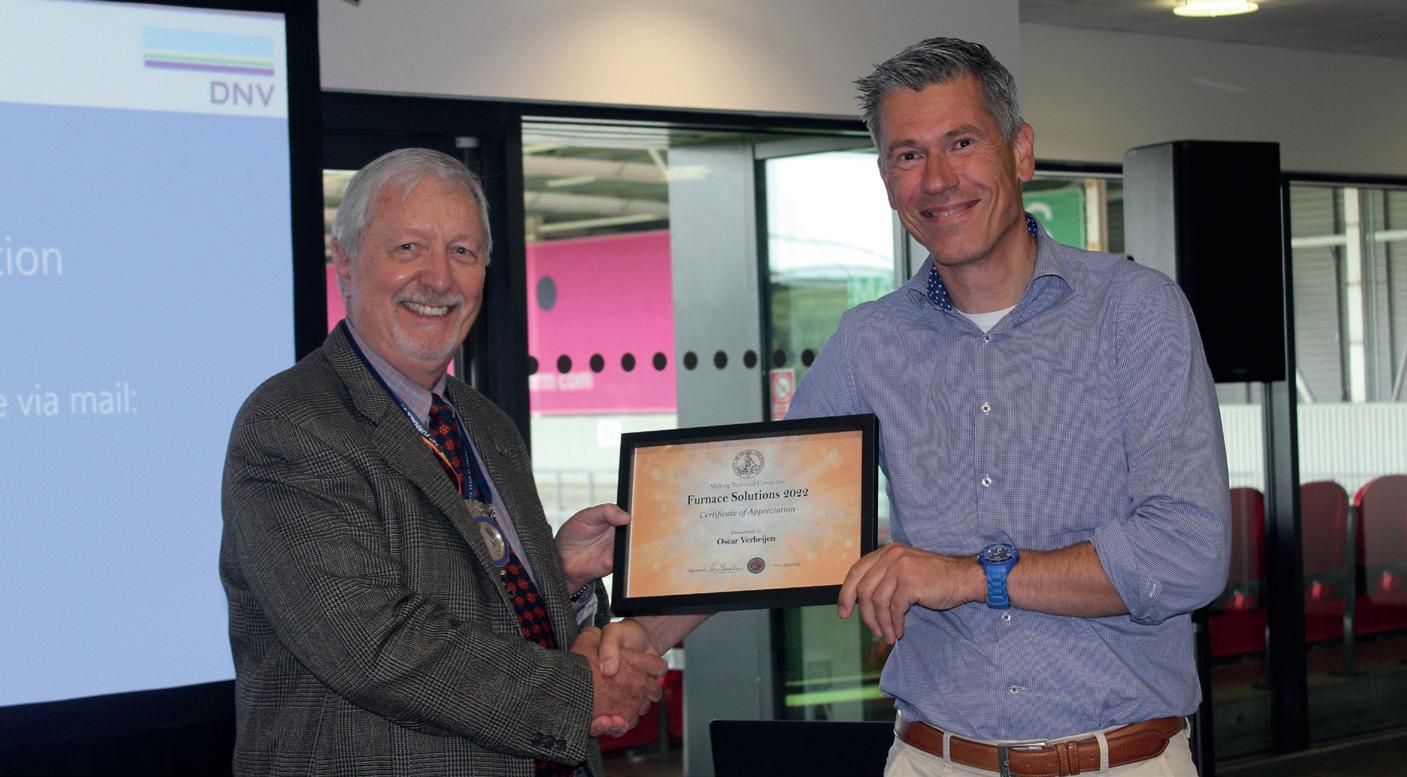
� CelSian’s Oscar Verheijen highlighted Hydrogen Combustion for the Glass Industry in his paper.
Glass Futures will feature strongly in our lives going forward.
“This was the first time we have been together in three years and it gave the opportunity to see old friends and new ones. More importantly it gave us the chance to learn what we need to do for the future. Of all the heavy industries, the glass industry is doing more than anybody else in its decarbonisation efforts.”
Mr Hakes added: “I felt that this year’s event was the best yet. We had a fantastic array of speakers, everybody has commented on the range of subjects covered, and it was held in a wonderful venue.
“It was more of a knowledge conference rather than a commercial one and that is something that the committee has always strived for.”
He thanked the SGT’s Nigel Longshaw, Christine Brown and Lisa Tyers for their tireless work in securing the speakers and for the organisation of the event. �

� Neil Simpson (right) of Simpson Combustion. Society of Glass Technology, Sheffield, UK www.sgt.org
With thanks to the SGT for their assistance in providing images.