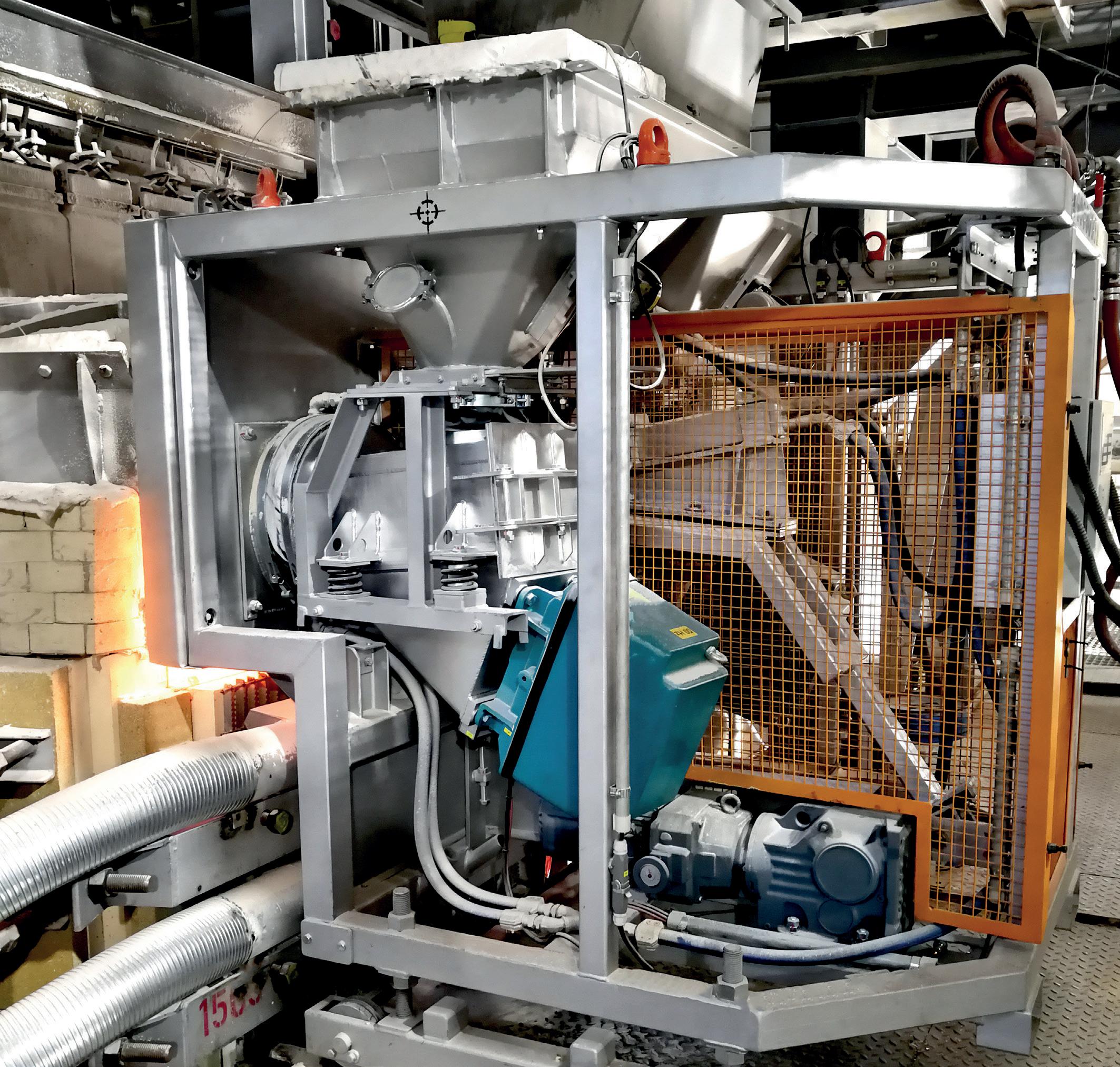
5 minute read
Batch plant: EME
� Fig 1. EME Batch Charger.
Batch handling possibilities to minimise segregation
Sebastian Woltz* discusses how a well-mixed, homogenous batch can help achieve high quality final glass products.
As part of the Sorg Group, EME is committed to delivering a perfect batch. It includes providing glass manufacturers with raw material intake and storage, equipment for dosing, batch weighing and mixing, and technologies for delivering the mixed batch to the furnace.
The synergy between EME and Nikolaus Sorg reaches its peak in the batch charging process. EME has one of the widest varieties of batch charging systems worldwide, thanks to Sorg’s combination of a batch plant expert and a furnace specialist in one single group.
Our batch charging solutions and technologies result from the combination of the know-how of both companies. This combined knowledge focuses on batch charging technologies and batch and cullet preheating systems. The two companies work together to offer and sell systems for glass manufacturers all over the world.
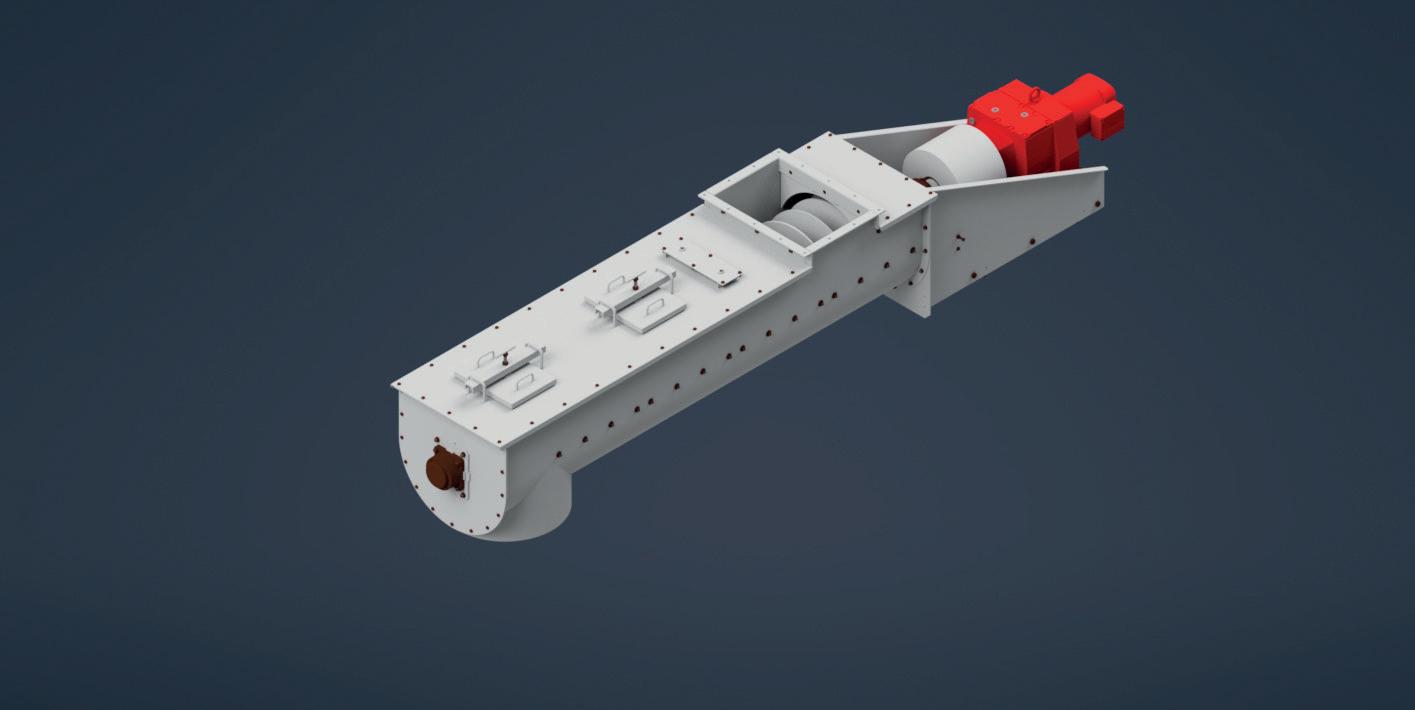
De-mixing and segregation
Charging the furnace with a well-mixed, homogenous batch to achieve highquality final glass products is essential. The main goal is to minimise the demixing and segregation of free-flowing particles. The characteristics that influence segregation are nominal grain size, grain size distribution, particle shape and specific gravity. The forces from demixing in streams of flowing solids result from the free-flowing action of individual particles during mechanical movements.
Segregation mainly occurs during shipment, storage and transport, but it can be avoided using, for example, a mass flow silo design.
The most critical step regarding demixing starts when the ready mixed batch is transported to the furnaces. The batch quality mainly depends on handling the batch during transport and storage. There is always a balance between flow behaviour, homogeneity and consistency, since batch consistency and flow behaviour are always in conflict (Fig. 1).
Wetting of batch in the mixer
De-mixing and segregation must be reduced. It can be done by suppressing the free-flowing characteristics of the raw material particles. A common form of suppression, broadly used in the industry, is creating a thin film covering the raw material particle. The process must use sufficient water to allow a soda ash chemical reaction, resulting in hydrate formations such as deca-, hepta- or monohydrates. The batch’s temperature determines which hydrate will form. The soda ash particles need to be fully hydrated before the wetting of all particles occurs.
Alternatively, batch wetting with caustic soda solution results in a simplified wetting system. In this case, the soda ash will not hydrate, staying in anhydrous form. However, this might not be the best cost-effective answer since caustic solutions usually are more expensive than sodium. Therefore, this technique is dependent on ideal marketing conditions.
Wetting makes the batch tacky to impede its typical free-flowing properties. But these conditions complicate the handling of the batch during subsequent conveying and storage. Agglomeration of wetted batch may occur, making it more difficult to avoid and minimise spillage at, e.g., the scraper devices of the belt conveyors. It also makes it harder for the batch to flow uniformly out of the furnace silos.
The critical parameters to minimise the clogging of batch are storage time (the batch components must have enough time to interact with each other), temperature, moisture content and lack of movement in the silo.
In case of problems, operators can resort to reasonable filling strategies, excellent silo geometry, and discharge aids like vibrating bottom discharge or knockers. Additionally, a high cullet proportion minimises the agglomeration tendency.
Agglomeration in the silo can, in principle, be avoided by making sure that the batch temperature will never drop below 35,4°C, preventing the absorption of large quantities of water by the formation of compounds Na2CO3-7H2O and Na2CO2-10H2O.
Nevertheless, wetting the batch does not eliminate size segregation in raw material handling and storage. Even a chemically uniform batch may vary considerably in size sometimes.
Besides segregation reduction, wetting the batch also reduces dusting emissions during transport and in the furnace. A decrease in the rate of regenerator plugging and particulate stack emissions is also achievable but requires a limitation on the amount of water used.
The evaporation of batch water in the glass furnace requires additional energy and should be minimised.
� Fig 2. EME Wetting screw.
Wetting screw
Especially in countries with high temperatures or long batch transport routes, additional wetting by wetting screws are in practice. Thus, before introducing the batch into the furnace, additional mixing and adjusting of the required moisture content, adaptable to the current outside conditions, must be completed.
The wetting screw system is installed between the batch furnace silo and the batch charger, exactly where the synergy between EME and Sorg is at its best. The transfer and dosing of the right amount of batch into the wetting screw can be done directly by controlling the vibratory bottom of the batch silo or by an additional screw feeder or vibratory chute that doses the right amount of material in the wetting screw.
The wetting screw conveys the batch to the batch charger by mixing and moistening the batch. Water is introduced into the screw through several spraying nozzles where water is put in, and the batch is moistened uniformly (Fig. 2).
Summary
The glass industry’s batch de-mixing and segregation problems are well-known and extensively studied. Nevertheless, customers must have a plan of action that considers the need for dust and spillage reduction in the batch house and the increasing demand for batch quality. These measures require an exceptional experience and should be agreed upon during the planning and execution of new systems. EME has the technical knowledge and expertise that a successful glassmaking plant needs, from batch wetting after the mixing process to the input of the batch in the furnace. The partnership with Sorg enhances its natural capability. Together, the companies deliver the best solutions for batch plants combined with Sorg’s renowned furnaces.
*Sales Director, EME, Germany www.eme.de
References
Engineered Materials Handbook Volume 4: Ceramics and Glasses