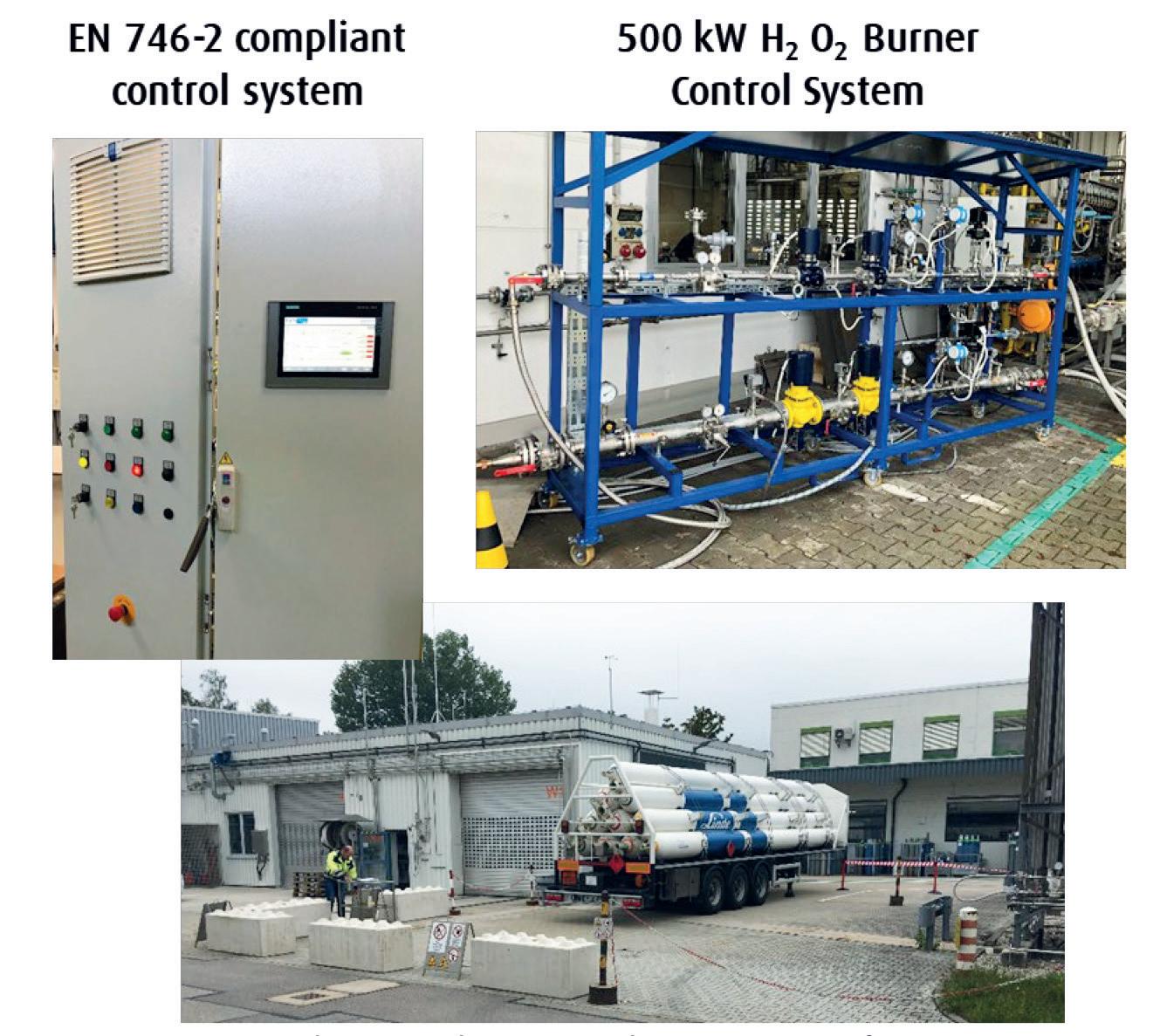
7 minute read
Decarbonisation: Linde
Oxy-Fuel burner testing with Hydrogen and Ethanol
Martin Adendorff*, Robert L. Bell** and Shrikar Chakravarti*** discuss Linde’s efforts to optimise its burner portfolio for use with hydrogen and other green fuels in the glassmaking process.
Due to the increased emphasis on sustainability, glass companies are looking for ways to substantially reduce CO2 emissions from their operations, especially from the melting process.
One approach is through use of low carbon fuels, examples of which include renewable hydrogen, biofuels, biogas, biomass-derived syngas, and renewable ammonia.
In particular, hydrogen is considered as the fuel of the future to eliminate CO2 emissions from combustion of hydrocarbon fuels. The first large scale demonstration of 100% hydrogen firing in a glass furnace was conducted recently at Pilkington UK’s St Helens facility, as part of the HyNet Industrial Fuel Switching project.1
However, long term adoption of H2 as a fuel in glass melting operation will require: 1. Modification of burner and fuel piping systems. 2. Understanding impact of higher water vapor concentration in furnace atmosphere on glass chemistry and refractory life. 3. Cost-effective generation and supply of clean H2.
This paper focuses on efforts at Linde’s combustion laboratories to optimise the Optifire burner portfolio for use with green fuels, e.g. H2, H2-NG blends, bioethanol.
H2-based combustion systems
Since 2018, Linde has been investigating the use of hydrogen fired oxyfuel burner systems for multiple industries including steel, glass and non-ferrous metals at their combustion technology centres in Sweden, Germany, and USA.
Fig 1 highlights some of the upgrades at the combustion lab in Germany, which includes: 1. New transportable 500 kW EN 746-2 (similar to NFPA 86) compliant hydrogen oxygen control system with a fail-safe PLC, Land NDIR furnace camera. 2. New flue gas analysers. 3. Trailer based hydrogen supply system, comprising of a high-pressure reduction station, supply piping and end use low pressure reduction stations to two locations at the combustion laboratory. 4. Relining the combustion furnace with a 1600°C fibre refractory material to allow faster heat-up and more comprehensive testing at high furnace temperatures, similar to those in commercial glass furnaces.
� Fig 1. Upgrading Combustion Lab in Germany for H2 testing
Current tests are focused on understanding the impact of using NG, H2 and H2-NG blends with multiple burner types on various physical flame parameters and emissions. Fig 2 is an example of a burner trial (firing rate of 400 kW) for a specific glass customer.
The combustion laboratory in the US has also been upgraded to facilitate testing with H2 and H2-NG blends. Fig 3 illustrates open air trials with the Optifire COROX-R burner, which has been especially optimised for speciality glass/ borosilicate furnaces.
Linde has designed the Optifire XD burner to mitigate condensate buildup
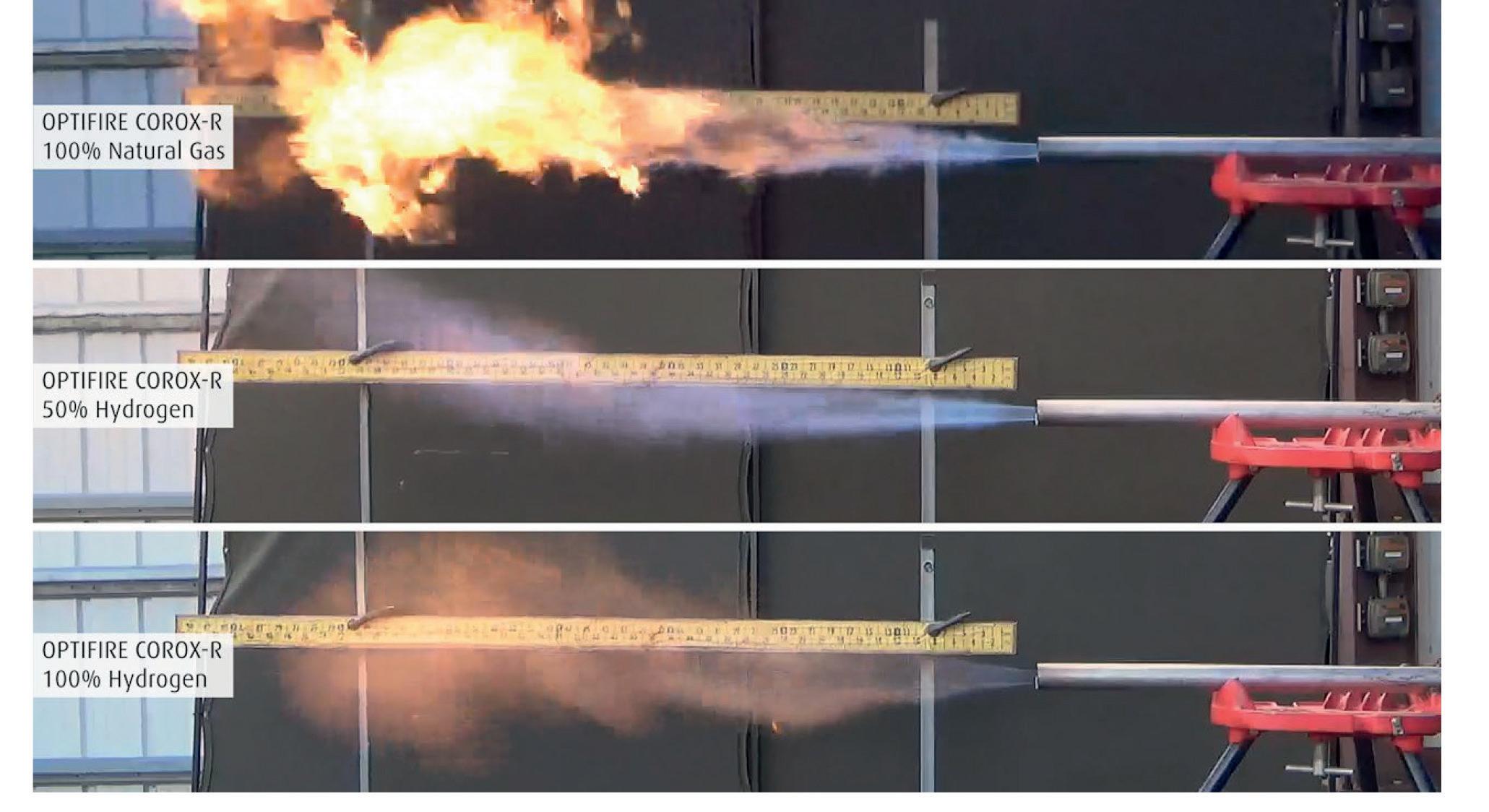
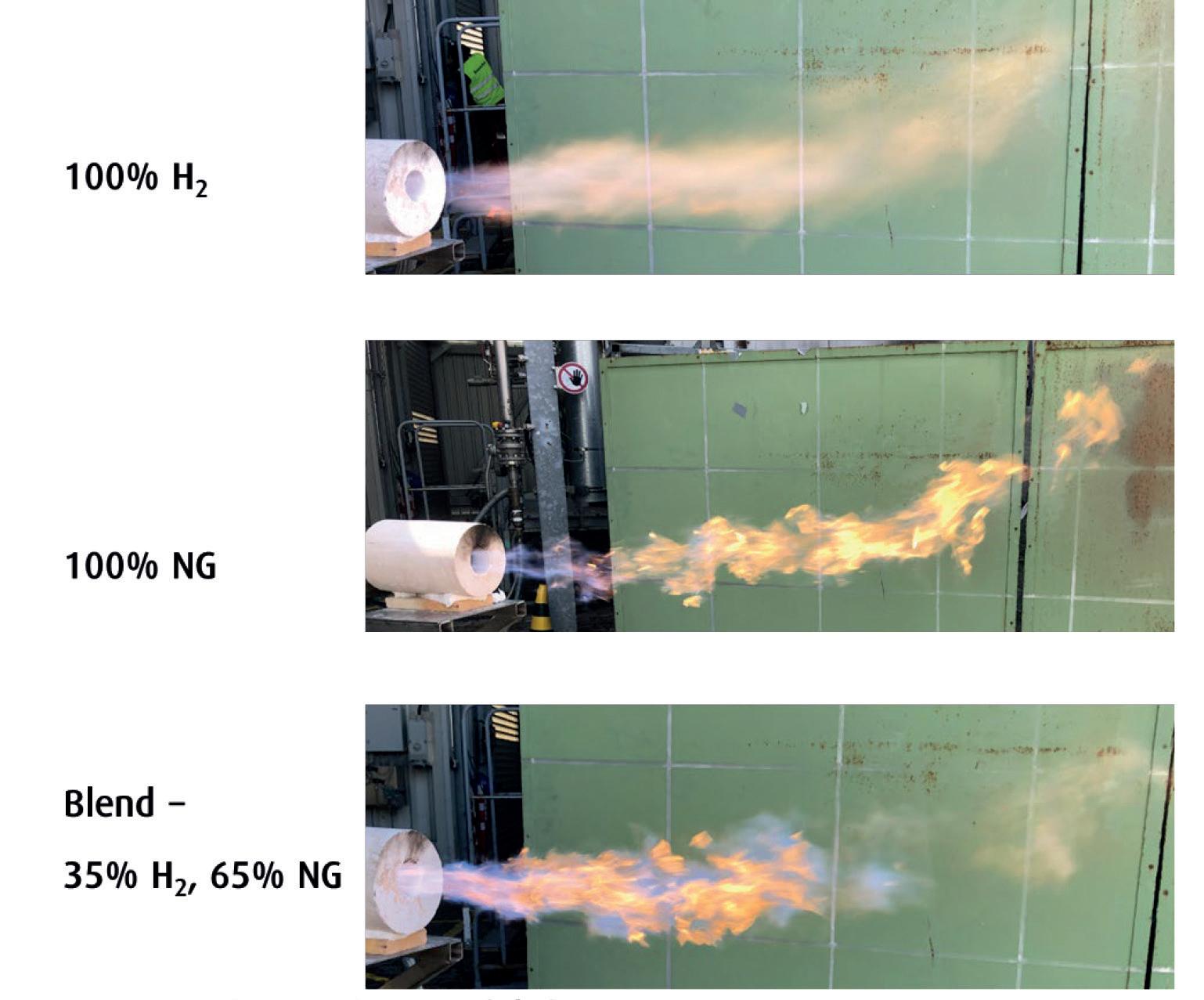
� Fig 2. Performing burner trials for customers.
and refractory port fouling.2 This burner has been successfully commercialised for environments with high levels of volatiles, e.g. insulation fibre glass furnaces, burner ports close to the batch blanket in container glass furnaces. An extensive trial with 100% H2, 100% NG and a range of H2-NG blends with the Optifire XD burner is shown in Fig 4.
The hydrogen flame is less luminous vs the NG flame in all open-air burner trials. This can be expected to be the case when the burners are fired within the glass furnace as well. H2 has a wider flammability range and a higher adiabatic flame temperature as compared to methane. No adverse impact on the radiation heat transfer is expected since the water vapor concentration of combustion gases will be close to 100%. This would enhance the gas emissivity of oxy-hydrogen flames and combustion gases. The conversion of the existing natural gas firing system to hydrogen firing will require fuel piping and burner modifications, but no fundamental heat transfer issues are expected with a proper oxy-hydrogen burner design.
One of the challenging aspects with oxy-hydrogen firing is high water vapor content in the flue gas, ~90% in relatively airtight furnaces. The long-term impact on refractory and glass chemistry is yet to be characterised. The high propensity of water condensation needs to be accounted for in the design of the flue gas system. It is also important to ensure that the combustion system is operated in an optimal mode – neither too much excess oxidant nor too much unburnt fuel. This can be typically monitored by measuring the flue gas composition. The high water vapor content of the flue gas also makes the sample drying and preparation using existing Peltier based dryers, prior to analysing the composition of the flue gases, a significant challenge. High performance sample dryers capable of removing around 1 litre of water from a 2 Nm3 flue gas sample, or wet based flue gas analysers are required.
Linde is also participating in multiple European based R&D partnerships and development projects. These include: � Hydrogen combustion in industrial heating processes (DNV led TKI project3 with 39 industrial participants from glass, steel, oil, industrial gas and ceramic industries). � CFD modeling of heat transfer from hydrogen-rich flames.4 � Influence of hydrogen rich combustion on foaming.4
Linde has also secured funding from the Bavarian Ministry for Economic Affairs, Regional Development and Energy, as part of the HYDROUS development project, towards the research and development of oxyfuel burner technologies fired with green hydrogen for high temperature industrial processes.
Other Low Carbon / Renewable Fuels
Aside from H2, several other low carbon fuels, e.g. biomass, biogas, biomass derived syngas, bio-ethanol, can be considered for use as fuel in glass furnaces5 - 6. Ethanol has an established supply infrastructure in some geographies. At the request of a glass customer, outdoor burner trials were conducted with ethanol at the US Combustion Lab. The tests were conducted over a range for firing rates 200 – 800 kW with both NG and ethanol. O2, air and NG were tested for use as the atomising gas in the case of ethanol combustion. The side-byside comparison in Fig 5 indicates that flame shapes are comparable in both cases; confirming the readiness of burner technology for use with liquid fuels such as ethanol.
Summary
Low carbon fuels such as hydrogen will be critical to glass companies achieving carbon neutrality in the long term. To prepare for this scenario, Linde is investing in multiple areas related to H2 – both supply systems7 and oxy-fuel burners. Recent open air trials for several burners from the Optifire portfolio indicate a high level of readiness for deployment in glass furnaces fired with green fuels like hydrogen and ethanol. �
References
1. HyNet Industrial Fuel Switching project, August 2021, https://hynet.co.uk/ 2. G. Kulkarni, U. Iyoha, S. Chakravarti,
� Fig 3. 800 kW trials with OPTIFIRE COROX-R at the US Combustion Lab.

� Fig 4. Trials with OPTIFIRE XD burners at the US Combustion Lab.
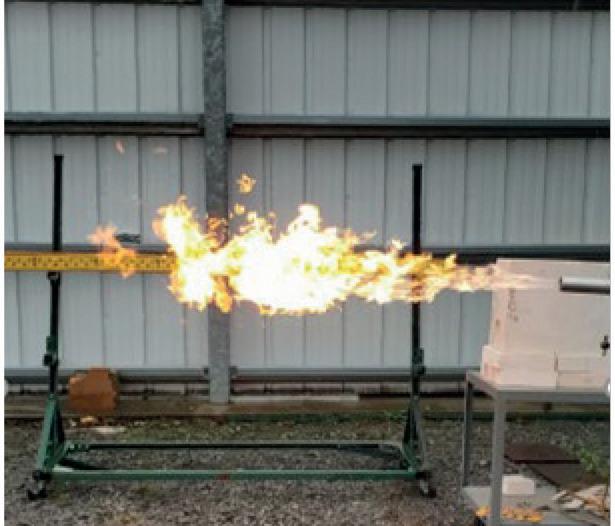
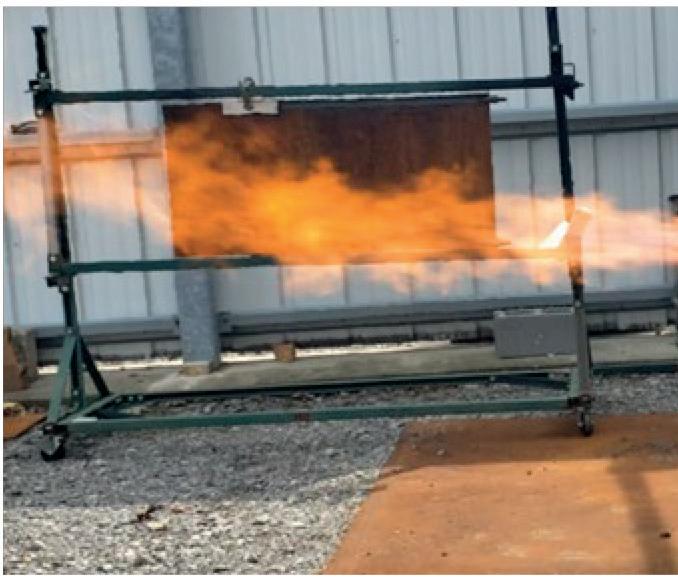
� Fig 5. Left - Oxy NG (400 kW); Right - Oxy Ethanol atomised with O2 (400 kW). P. Diggins, A. Francis, and G. J. Panuccio, “Staged Oxy-Fuel Wide Flame Burners to Mitigate Refractory Port Fouling and Foaming in Glass Furnaces”, 79th Conference on Glass Problems, Columbus, OH, October 2018. 3. https://www.dnv.com/news/dnv-gllaunches-hydrogen-industry-consortiumto-reduce-carbon-emissions-frommanufacturing-181919 4. https://www.glasstrend.nl/projects/ 5. H. Kobayashi and S. Chakravarti, “OxyFuel Combustion toward CO2 Neutral Glass Production”, Glass Trend Seminar, April 2018. 6. S. Chakravarti, “Low Carbon Fuels for Glass Furnaces”, Sustainability in Glass Manufacturing, GMIC Symposium, October 2019, Columbus, OH. 7. S. Chakravarti and M. M. Shah, “Preparing for Sustainable Glass Production – Technical and Economic Investigation of Hydrogen Supply for Glass Melting”, Webinar by Glass International, June 2021.
*Senior Technology Expert, **Senior Research Engineer, ***Business Development, Linde Inc, Danbury, CT, USA, www.linde.com
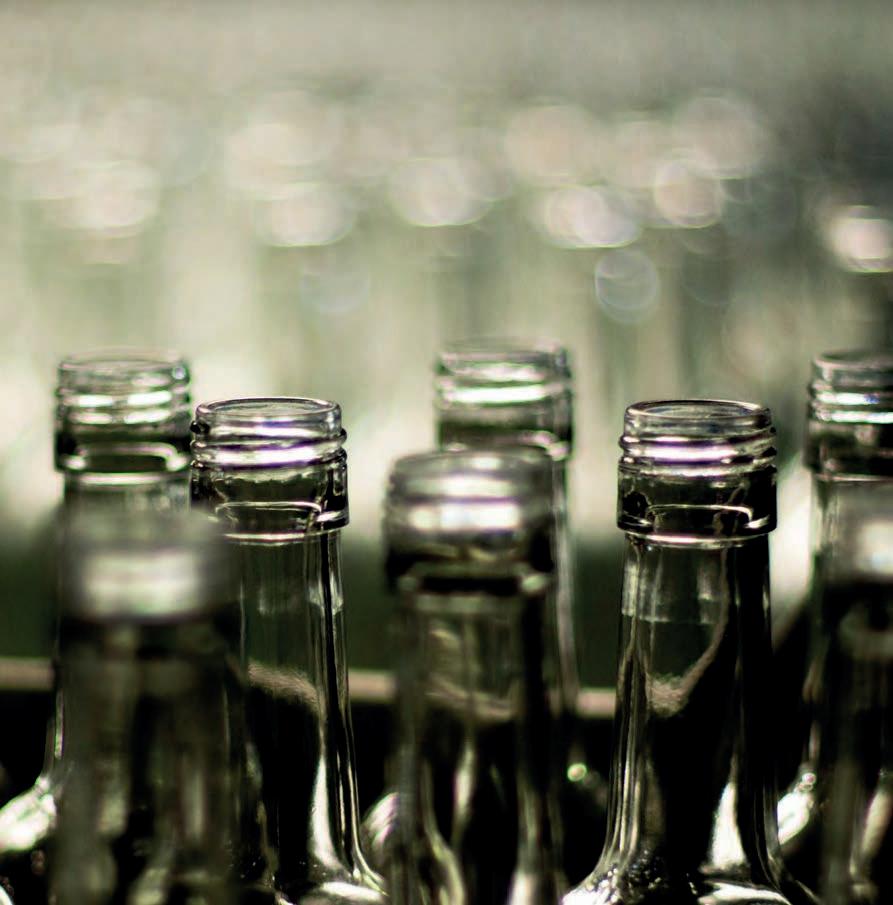
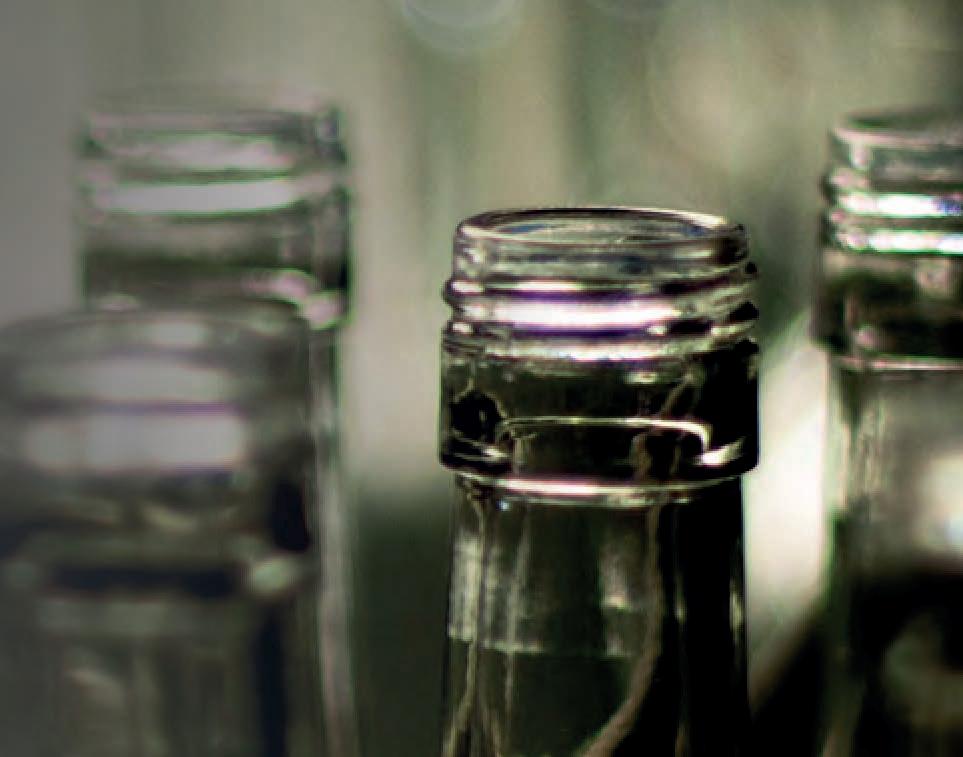
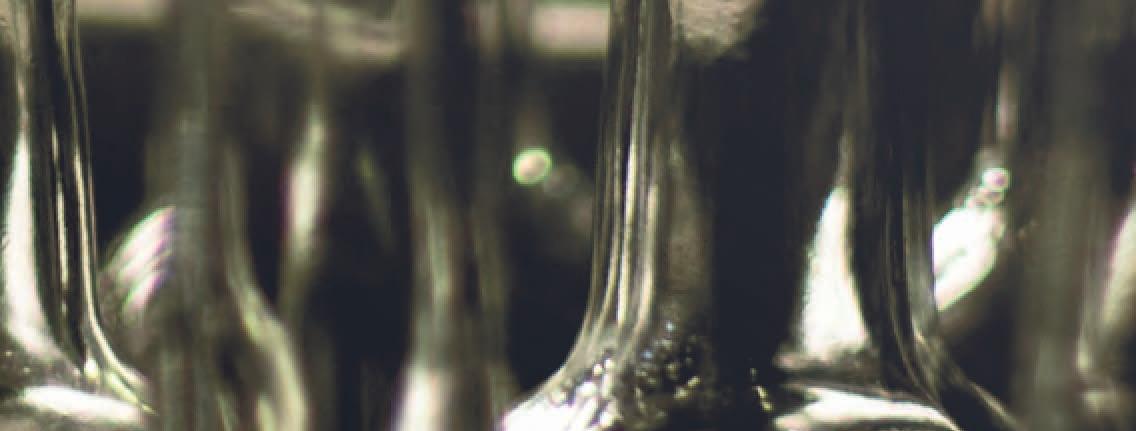


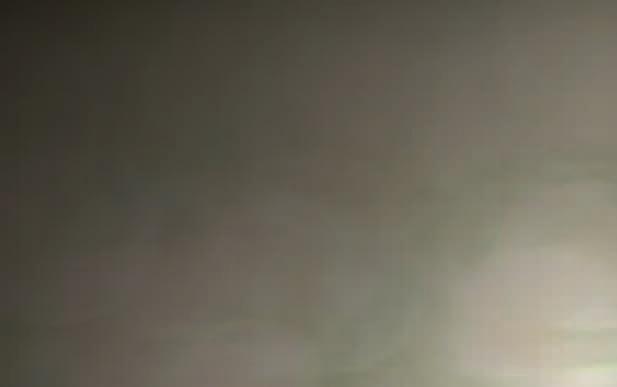

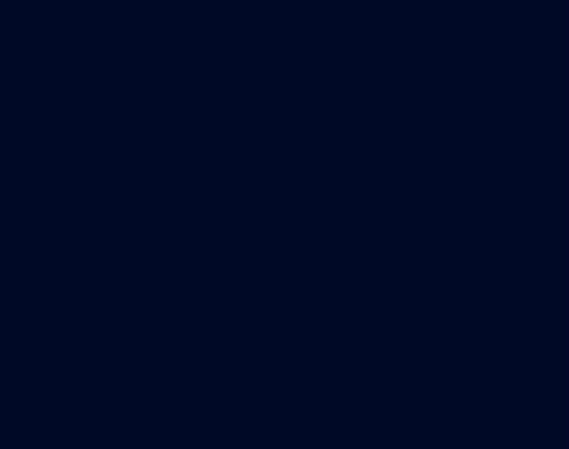

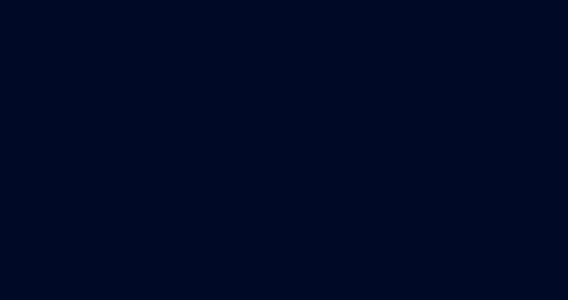
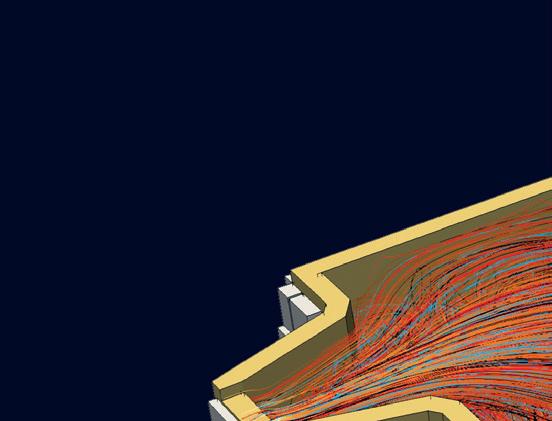
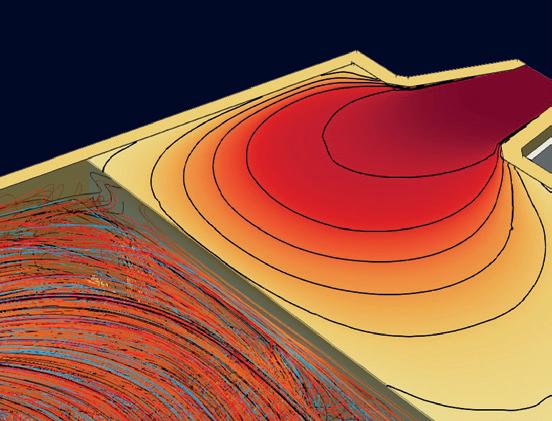

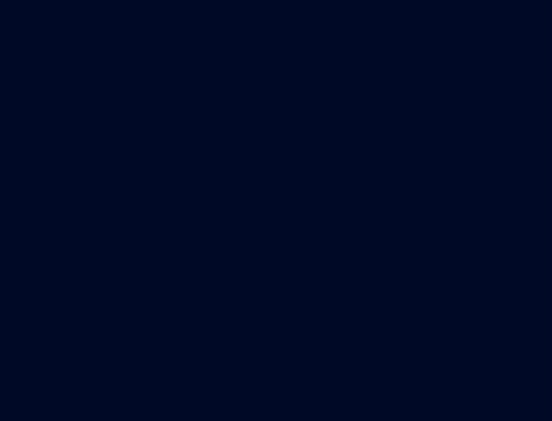

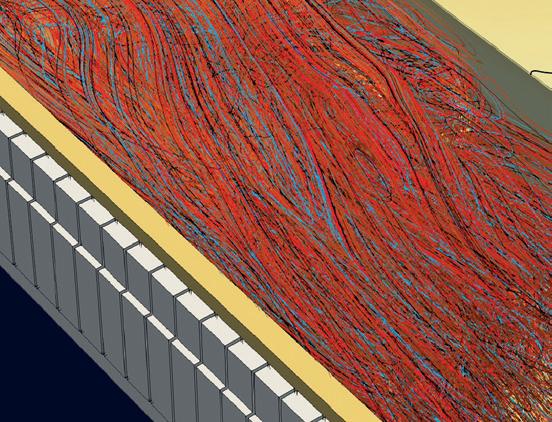
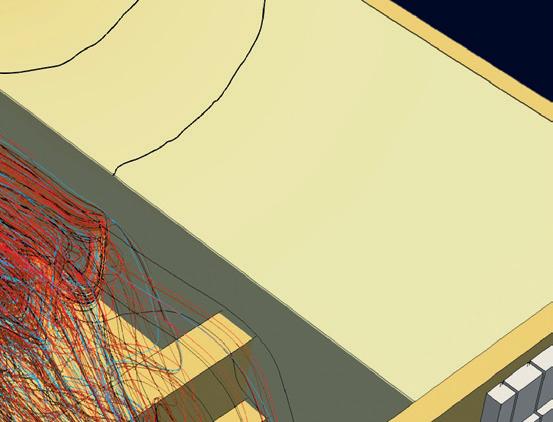
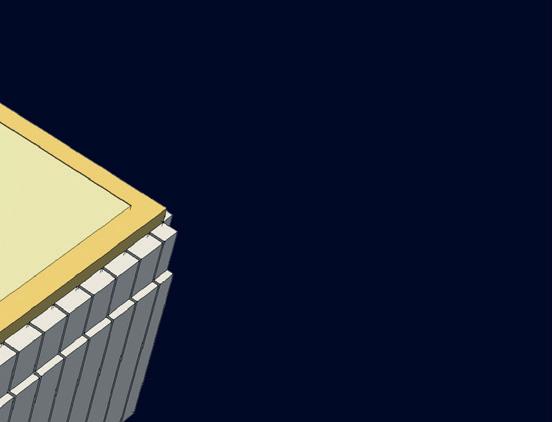

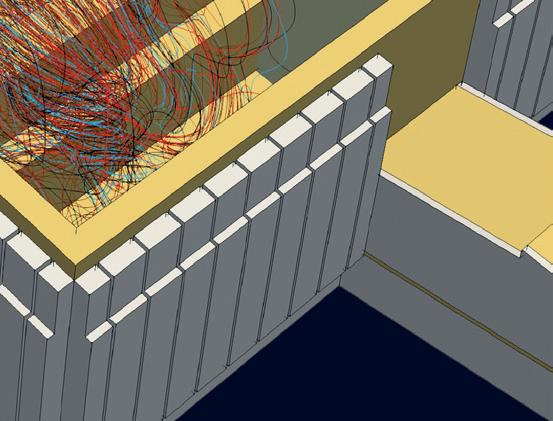
