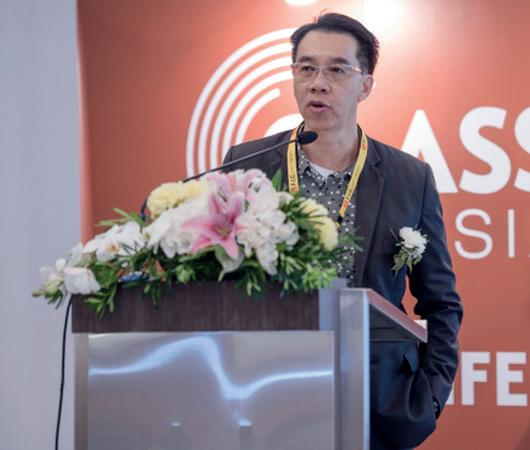
4 minute read
Case Study: Siam Glass and Tiama
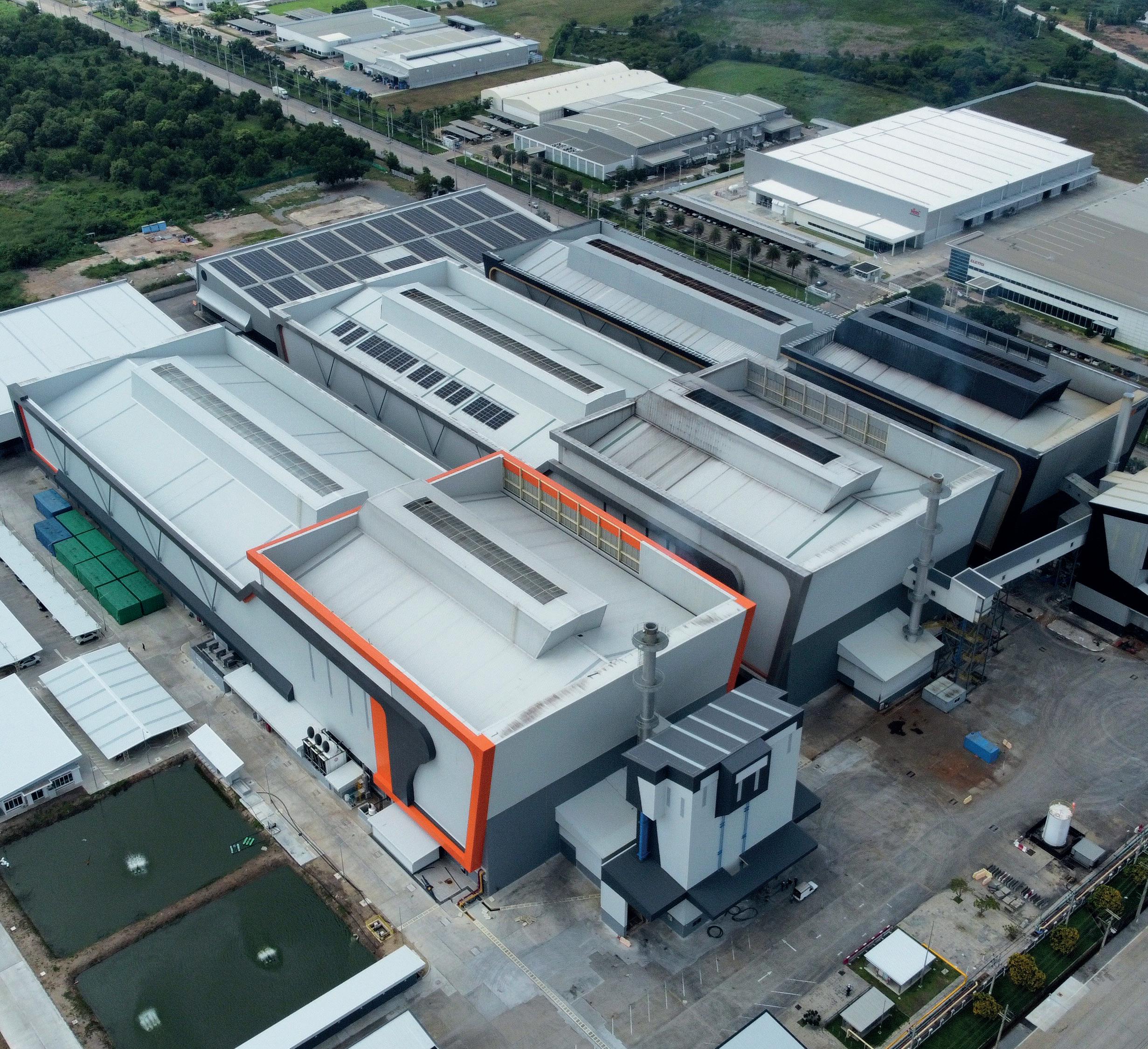
Siam Glass gives its feedback on working with Tiama
Viwat Supatham is the Head of Glass Operations at Siam Glass Industry*, and is also responsible for Myanmar Golden Eagle (MGE) in Myanmar. With 25 years of experience in the glass industry, he has been working with Siam Glass for 12 years. He discusses Siam Glass and its relationship with its long-term partner, Tiama.
Siam Glass is an affiliate company under the Osotspa Public Company, a Thai-based beverages specialist. Osotspa focuses on functional drinks and personal care products.
It has existed for more than 130 years, which makes it one of the oldest companies in Thailand.
Siam Glass has three main sites: Siam Glass Osotspa, Siam Glass Ayutthaya (pictured above, Furnace 1, 2 and 3) and Siam Glass Samutprakarn.
It is currently listed on the Stock Exchange Thailand (SET).
The main challenges it faces are raw material costs, production flexibility
�The Tiama Smart Factory.
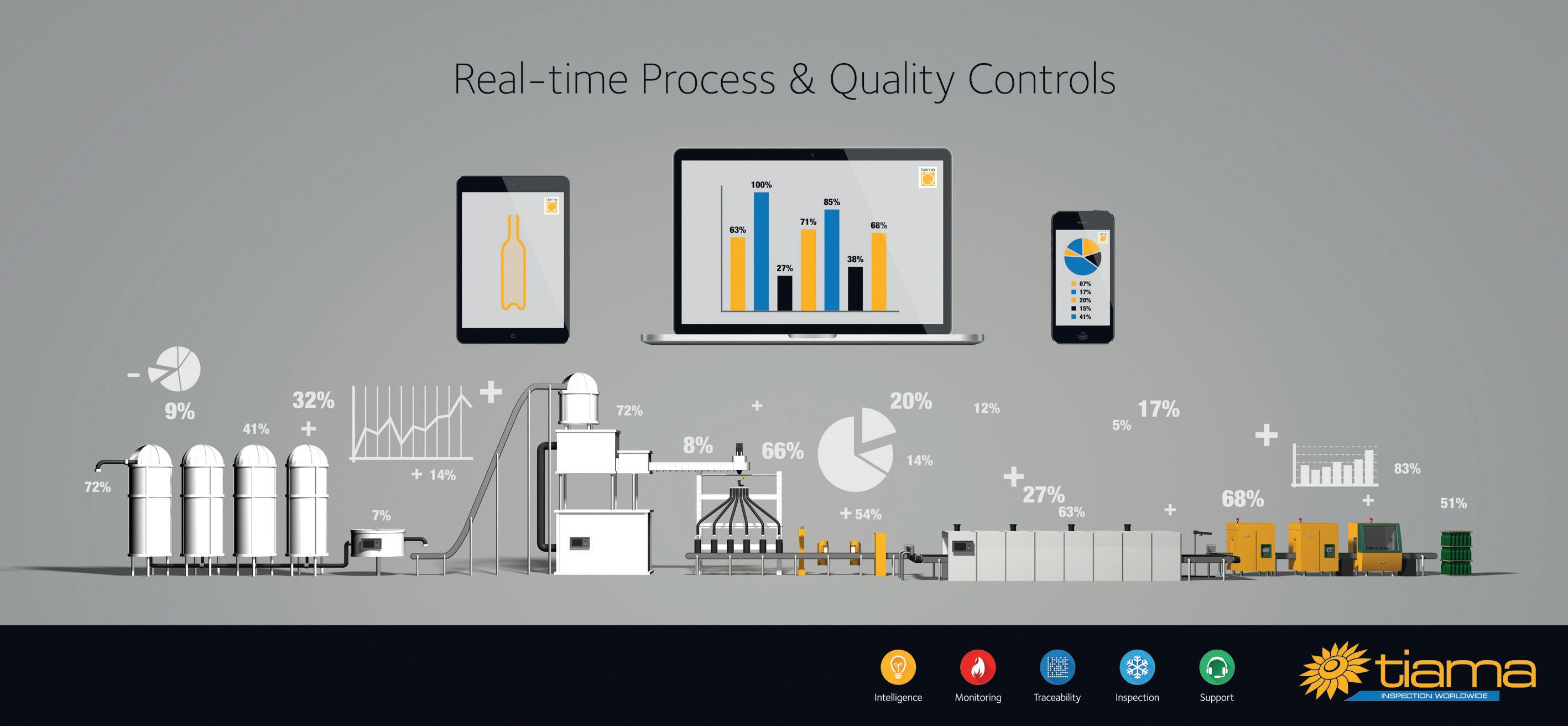
(job changes) and product developments brought by a larger variety of demands and customers.
It faces the disrupted market and the logistics challenges around the world by adjusting its production in all the plants; the key is achieving faster job changes, lighter bottles, higher productivity costs reduction and lower energy consumption.
Siam Glass and Tiama in 2022
Mr Viwat Supatham (pictured overleaf, inset) did not hesitate to place Tiama at the top of his supplier list. ‘’Tiama makes up 95% of the inspection equipment present in our production plants’’.
With eight furnaces and 25 production lines in total, Siam Glass has used Tiama (and previously SGCC) for more than 30 years, even before he joined the company.
Some of Tiama’s oldest machines were overhauled and/or upgraded and are still being used today.
The more recent plants use Tiama’s latest technology e.g., MULTI4, MCAL4, ATLAS, TIAMA IQ scan (MES).
Mr Supatham likes the machines because they are “user friendly, very efficient, and adapted to modern industry with low maintenance”. He also highlighted the reliability and the skills of Tiama’s local service team.
Most Siam Glass’ furnaces started up in the last two to three years are equipped with the latest Tiama solutions at the cold end with no presence of manual inspection.
All inspections are done with automatic equipment and Tiama’s own HD camera systems.
Mr Supatham explained that the quality of the Tiama equipment and services has been improving for the last 20 years.
Thanks to a strong partnership with the French company, Siam Glass can “continuously gain experience while saving costs on all the spare parts which are centralised and exchanged among the plants.”
Tiama is not only a cold end solutions provider with vision and carousel machines, but also supplies hot end inspection systems, laboratory equipment, traceability systems (engraving solution and readers), data solutions and many services.
This diversity is a strength that “none of the other suppliers can match”. Mr Supatham also insisted that Tiama keeps developing new equipment and services that responds to Siam Glass’s needs.
Data
Mr Supatham considers data as essential in the glass industry. The production lines need to be flexible and respond to customer demands quickly.
Data needs to be easy and ready to be used at all times. Siam Glass uses Power BI in addition to Tiama MES to collect and process data.
This naturally helps improve its pack to melt every day. Tiama solutions automate the production as much as possible, which is why Tiama became vital to its Industry 4.0 strategy.
In 2022, Mr Supatham plans on having the Tiama IQ scan in all the glass manufacturing lines.
Tiama also wanted to have his opinion on other solutions that are penetrating the glass world, such as the Tiama HOT systems and he explained from the time they started using hot end inspection systems at Siam Glass, the equipment has proven to be very beneficial, not only to their quality, but also to their efficiency at the hot end, which has contributed to improving the plants’ performances.
When questioned about the gap between the quality standards in Europe and Asia, he said: “There is no difference between them. I would say the control is even tighter in our plants.”
He also specified that Siam Glass exports its bottles to the USA where high standards are expected, and it also uses Tiama systems to inspect those products and to ensure the best quality.
When asked what he believes is missing from the glass inspection market, Mr Supatham answered by explaining that the Thai market needs a closed loop information system feedback on the hot end, which is the missing step to achieve the full automation of the entire production line.
This is where Tiama’s latest collaboration comes in, the recently launched Glassform AI platform, available via https://www.glassform.ai/ �
Tiama, Vourles, France www.tiama.com
*Siam Glass, Bang Kapi, Bangkok, Thailand http://www.siamglass.com/
Glassform.AI, Rovereto, Italy www.glassform.ai