
8 minute read
Furnaces: Glass Service Using AI for furnace imaging
Using artificial intelligence with near infra-red furnace imaging
Erik Muijsenberg* and Robert Bodi** discuss the rise of artificial intelligence and how modern technologies can improve the glass manufacturing process
Fig1. Furnace images by a near infrared camera and temperature trend lines.
Furnace modeling
Most leading engineering firms and glass producers around the world are already using furnace modeling, also known as Computation Fluid Dynamics (CFD), such as the GS Glass Furnace Model (GS GFM) software package. While in 1990 it was a discussion about the accuracy of modeling, today it is considered reliable and useful. It is now state-of-the-art and is used for almost every furnace design or rebuild.
The GS Expert System III (ESIII) is a model-based predictive furnace and forehearth control system, that has evolved beyond CFD. People were initially sceptical to believe it was possible to control a furnace with Model Based Predictive Control (MPC) but today there are more than 300 furnaces globally with MPC installed, with many of these glass furnaces in operation also on forehearths.
Since 2010, there has been tremendous interest in Industry 4.0, as the glass industry has become aware that industrial producers (including glassmakers) are instigating new standards like furnace cameras and batch convection movement monitoring within the furnace. The question has become: What is happening now? What will come after this evolution of MPC?
Industry 4.0 captures many aspects of the automation of the manufacturing process, including robots, the Internet of Things, simulations of the process, cyber security, system integration, cloud computing, 3D, big data and augmented reality.
When looking at a modern glass production line today, viewing a typical end-fired furnace, a regenerator, melter and a forehearth deliver the glass to the forming machines, many of the processes are already automated within different areas.
On the melting side, PID DCS control has had limited success previously, because of slow furnace reactions. Therefore, GS began by applying modelbased predictive control strategies, because PID control by an operator for 24 hours non-stop was limiting, along with slow temperature reaction times of the furnace and a very large dead time for the responses.
With MPC and its dynamic matrix algorithms, it is possible to capture process behaviours with such models and equations and improve furnace operation. For MPC models and the dynamic base of its algorithms, the process can be driven for optimum quality with the lowest emissions, lowest operational costs and with minimal assistance, even sometimes without the operator. That is why GS has integrated the furnace camera into the ESIII concept.
Furnace camera uses
The main motivation for GS A.SENS furnace camera was to start monitoring the batch blanket to relieve the operator
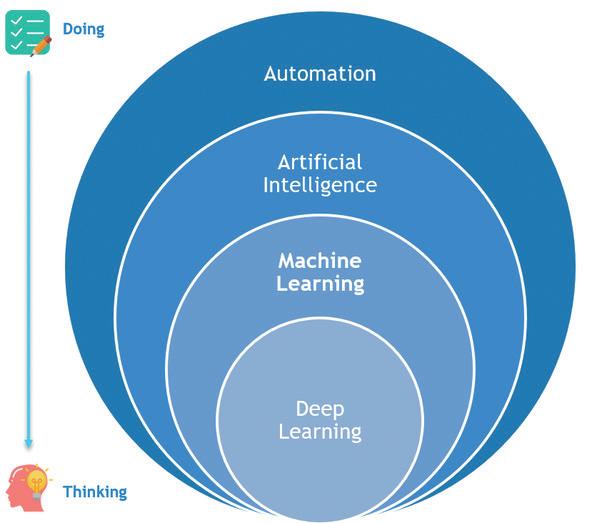
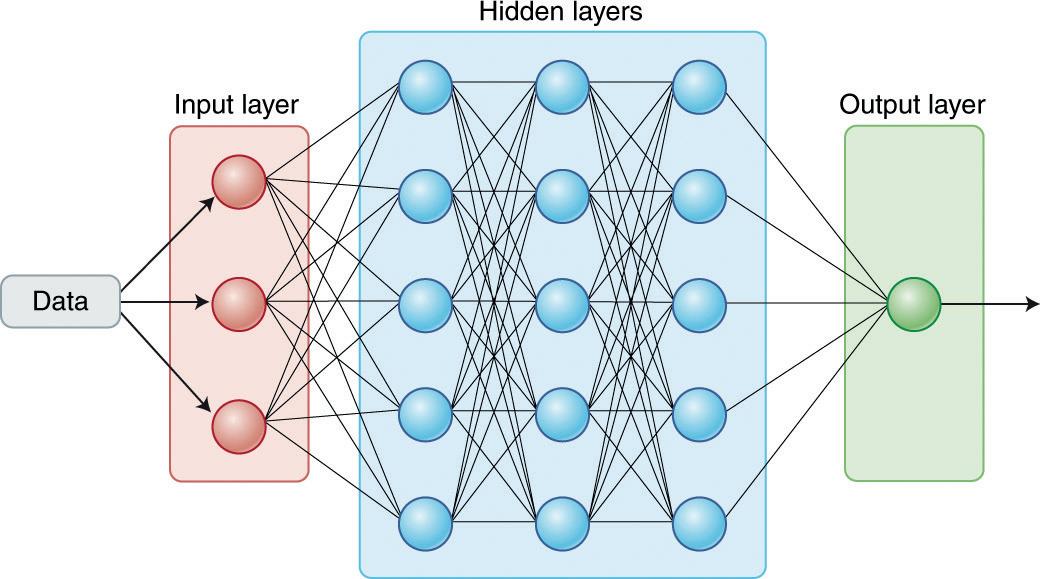
� Fig 2. Automation, artificial intelligence, machine learning and deep learning. � Fig 3. Neural networks.
from this difficult task. But apart from monitoring the batch blanket, the operator also typically takes some optical temperature readings to make sure the thermocouple readings are reliable and refractory is not overheated. This led to the idea to develop a furnace camera that can also capture the furnace temperatures, which resulted in the near infra-red (NIR) camera solution. But the NIR cameras available from the market had low pixel resolution. The lower pixel resolution may have been sufficient for temperature readings but it is insufficient to detect the smaller batch islands that float on the glass surface.
The next step is how to decide if the camera actually sees batch, foam or glass surface and how to avoid a dust particle on the camera lens not being identified as batch. For this requirement, GS in cooperation with A.SENS had to develop an artificial intelligence algorithm that uses deep neural networks to learn from many glass furnace images what is what. The AI solution with the GS NIR camera detects flames but also decides what is flame, refractory and other objects that are commonly seen in glass melting furnaces.
The AI software also makes temperature readings that can be used by the MPC control more reliable. When the temperature is influenced by other parameters, the AI software can use this to correct the virtual TC reading given to the MPC or DCS.
Such NIR cameras can give valuable visual information, as well as data that can be used in the control algorithm (Fig 1)
AI and neural network definitions
So what are artificial intelligence (AI) and neural networks, how do they work and how can they help in the glass industry?
Automation is the basis of this consideration. Most people are used to DCS control and MPC control. Automation is the creation of technology and its application, in order to control and monitor the production process. It performs tasks that were previously performed by humans. AI is a field where regular control techniques cannot resolve irregular issues that are inefficient. AI then enables the computer to mimic human intelligence using neural network decision trees and machine learning to solve a problem. Machine learning is simply a subset of the AI, using sufficient data subsets to train the neural network.
Deep learning may be referred to as something magic but it is simply a multilayered deep neural network that handles vast amounts of information. Actually, it is used daily when searching something on Google. Google suggests an answer what is actually being searched for, or Netflix suggests movies, because they are learning from a person’s previous behaviour. This is already AI.
Referring to fig 2, the relationships between the various entities can be seen. Automation (A) is the creation of technologies and its application, to control and monitor a production process. It performs tasks that were previously performed by humans. Artificial intelligence (AI) is the field where regular control techniques fail or are inefficient. AI enables computers to mimic human intelligence using neural network decision trees. Machine learning (ML) is a subset of AI using sufficient data to train a neural network.
Deep learning (DL) trains multi-layered deep neural networks with vast amounts of data.
What is a neural network? It was probably given this name because some parts function similarly to neurons in the human body. A set of data needs first to be analysed, and after it is analysed, the result is the outer layer which is its meaning.
First, this data has been created in the inner layer of the analysis, formalised and then put it into the neural network. This neural network is taught to fill certain highs and constants inside different neurons, to learn (with lots of data on the entrance side) to predict what comes out as the output and to recognise it automatically. The key factor is these neurons are not fully understood, although it is not necessary to understand them. They are simply filled out by giving sufficient data and sufficient output for the neurons that are going to be filled with the mechanism that they recognise best.
Fig 3 shows the input of data, the analyses of the data and the output of the process.
Machine learning is nothing more than training a neural network with many inputs and outputs, until all these neurons (at least one hidden layer) has learned enough to predict what is happening. Deep learning means there is a neural network with more than one hidden layer. This is quite common, especially for more complex tasks that need more than one layer.
To illustrate these concepts, an imaging technique is presented that is used with the GS NIR furnace camera. By ‘training’ the camera software as to what kind of images it is seeing, after some time the camera is able to detect what is the batch, the flame, the glass surface, the refractory and the camera build-up. Where, for example, there is camera buildup covering a thermocouple, it can no longer be used reliably.
� Fig 4. Furnace image from a camera with neural network analysis results
Furthermore, input data of this thermocouple should not be applied to deep learning. Deep learning is also able to detect the flame independently from the batch and determine if the flame is up or down, as well as providing information or an alarm that the furnace needs attention. With neural network technology, it is possible to obtain much more information from these images and process them into control and decision making, as opposed to what it is possible to learn with furnace temperatures only.
Fig 4 shows a template for a furnace operation, including identification of batch islands, the flame, glass surface, refractory and even build up around the camera.
During the next step and after the batch is identified, it can be seen that the camera is typically looking at an angle into the furnace. After the batch coverage is calculated, the image is then transferred into a horizontal picture looking from a bird’s eye view (Fig 5).
The image is digitally analysed as the yellow area on the section there and this would then enable the user to calculate the square meters of the batch in the various positions.
For some furnaces, stability is very important and for others, it is less of an issue. The batch monitoring system allows the user to monitor the batch location, coverage and movement, enabling any corrective actions to be made and to automatically alarm if necessary.
In summary, the NIR AI furnace camera developed by GS in co-operation with A.SENS is a perfect combination with the ESIII expert system solution. Benefits include more stable automatic furnace control and glass production, increased glass quality and energy saving, plus CO2 and NOx emissions reduction.
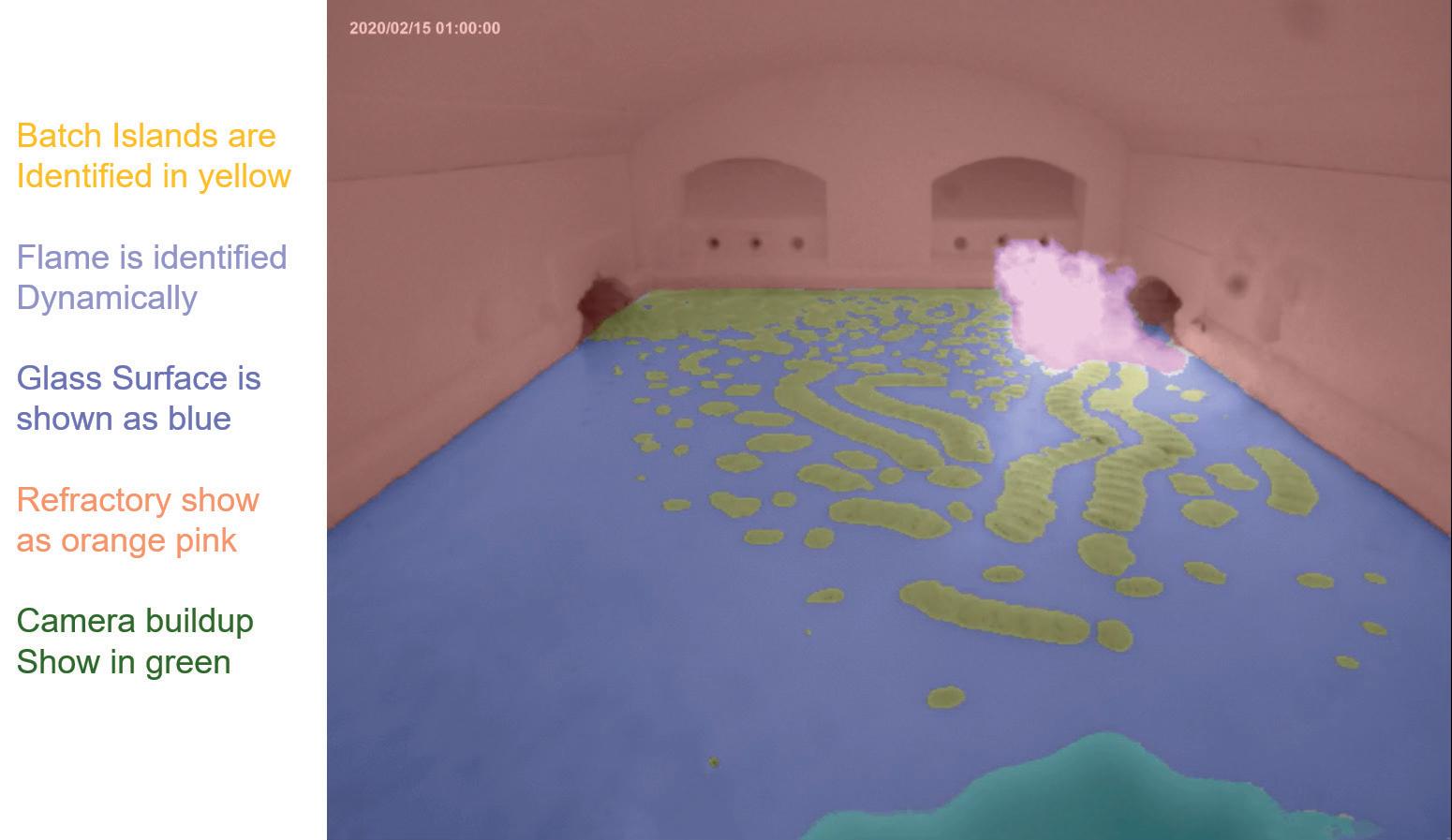
About the company
Glass Service is headquartered in the Czech Republic and develops technology to optimise glass melting, performing defect analyses, 3D furnace simulations, MPC and bench marking of large furnaces. Furthermore, GS supplies the necessary hardware.
Subsidiary GS companies are FlammaTec for burners, FIC (UK) Ltd for electric melting and super boosting in hybrid melters and A.SENS for AI software with near infra-red (NIR) furnace imaging. The combination of AI NIR cameras connected to MPC is bringing Industry 4.0 and Big Data connected to the Internet of Things. �
*Vice President, **General Manager, Glass Service, Vsetin, Czech Republic email: info@gsl.cz, www.gsl.cz
� Fig 5. Batch coverage as converted into a bird’s eye view.
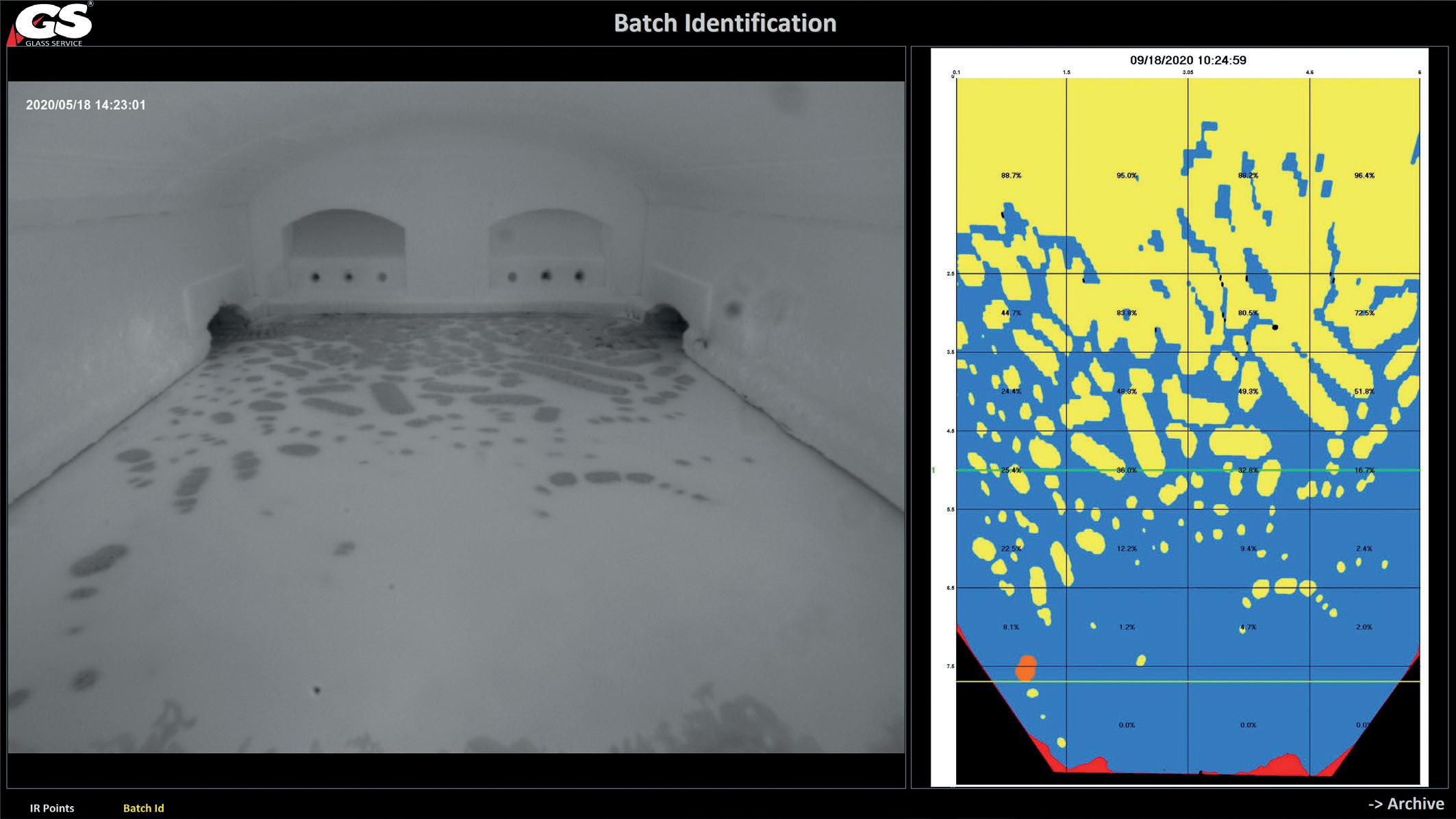