Let’s talk about Let’s talk about
RAW MATERIALS
Europe looks to circular economy
DIGITALISATION
The advent of smart laundry
INDUSTRIAL LAUNDRY
The steps of laundry process
TEXTILES
Washing table linen correctly
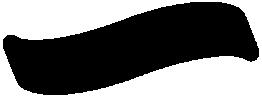
Follow
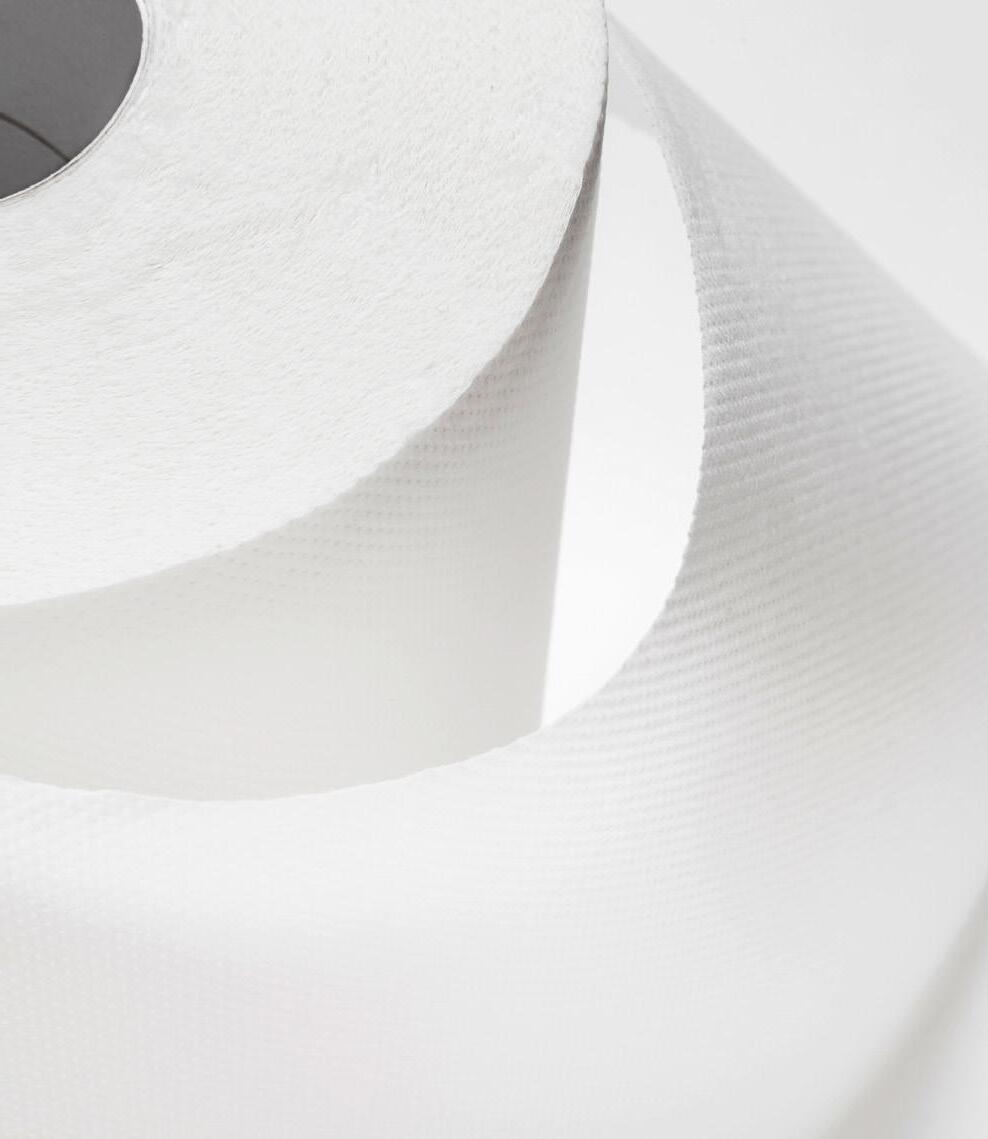

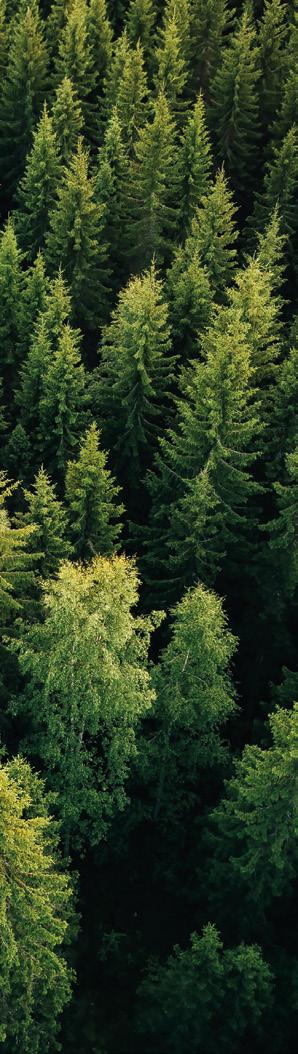
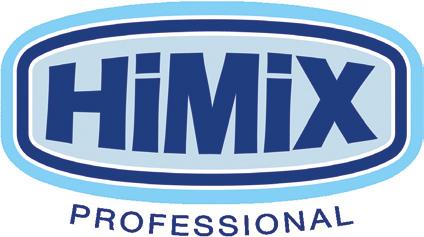
Europe looks to circular economy
DIGITALISATION
The advent of smart laundry
INDUSTRIAL LAUNDRY
The steps of laundry process
TEXTILES
Washing table linen correctly
Follow
The HiMiX Professional line ensures high performance, respect for surfaces and the environment, and guarantees the safety of customers and workers. Compliant with HACCP control plans, it ensures the highest standards of cleanliness and hygiene.
FOR OVER 60 YEARS, HIGH-QUALITY, EFFICIENT, AND RELIABLE PROFESSIONAL FORMULATIONS
For more information, visit our website
www.dimensionepulito.it
Monthly magazine pubished by
Quine Srl
Via G. Spadolini, 7 - 20141 Milano
www.quine.it | info@quine.it | Ph. +39 02 864105
Editor-In-Chief
Giorgio Albonetti
Editorial director
Ornella Zanetti | ornella.zanetti@quine.it
Technical director
Maurizio Pedrini
Editorial coordination
Chiara Scelsi - c.scelsi@lswr.it | Ph. +39 349 0099322
Editors Loredana Vitulano - l.vitulano@lswr.it Ph. +39 342 6618995
Cristina Cardinali - c.cardinali@lswr.it Ph.+39 347 4238879
Simone Ciapparelli - s.ciapparelli@lswr.it Ph. +39 344 0571950
Technical scientific consultants for the section
Environmental hygiene Chiara Dassi - Graziano Dassi
Circulations and subscription service
Ornella Foletti - o.foletti@lswr.it | Ph. +39 342 7968897
COVER
Operating on the national and international market for over 30 years, ICA is a paper converting company specialized in Away-from-Home products. ICA is committed to constantly expanding its wide range of products in a perspective of constant innovation and focus on the environment to offer products that are more and more performing, hygienic and sustainable.
Andrea Anelli, Michael A. Berry, Cristina Cardinali, Simone Ciapparelli, Francesca De Vecchi, Francesca Leoni, Niccolò Luongo, Marco Monti, Maurizio Pedrini, Francesco Pirovano, Michele Ruzza, Giacomo Torrenzi, Loredana Vitulano
Sales manager Costantino Cialfi
Advertising and development Filippo Viola - f.viola@lswr.it Edoardo Rossi - e.rossi@lswr.it
Elena Brusadelli - e.brusadelli@lswr.it
Graphic design Paolo Marchetti - KF Ivest Sagl
Production manager
Antonio Iovene - a.iovene@lswr.it | Ph. +39 349 1811231
Printing New Press Edizioni srl - Lomazzo (CO)
Prices and subscriptions
• Annual subscription: 49 euro
• Subscription outside Italy: 160 euro
• Back copies: 17 euro
• Cost of a copy: 1.30 euro abbonamenti.quine@lswr.it | Ph. +39 02 864105 www.quine.it
www.dimensionepulito.it
Responsibility
Dimensione Pulito is a Monthly Recorded Periodic: Authorization of the Court of Milan No. 598 of 9.11.92 Quine is registered in the Operators Register of Communication n. 12191 of 29/10/2005. The publication or reprint of articles and images must be authorized in writing by the publisher. The articles published on Dimensione Pulito are under the responsibility of the authors. Published manuscripts and drawings will not be returned. INFORMATION PURSUANT TO GDPR 2016/679 Pursuant to art. 13 European Regulation for the Protection of Personal Data 679/2016 below GDPR, the data of all readers will be processed both manually and with IT tools and will be used for sending this and other publications and information and promotional material. The methods of treatment will comply with the provisions of art. 5-6-7 of the GDPR. Data may be disclosed to subjects with whom Quine Srl maintains contractual relationships necessary for sending copies of the magazine. The data controller is Quine Srl, Via G. Spadolini 7 - 20141 Milan, to which the reader can turn to request the update, integration, cancellation e any other operation referred to in articles 15-21 of the GDPR.
© Quine srl - Milan
12 16 22 26 30
Raw materials: Europe looks to circular economy
Maurizio Pedrini
Risk assessment for enzymecontaining products
edited by Simone Ciapparelli
Trends and opportunities in the laundry sector
edited by Simone Ciapparelli
The advent of smart laundries
edited by Cristina Cardinali
The steps of the laundry process edited by Simone Ciapparelli
i
for a perfect aesthetic alignment with the trolleys of the Falpi Hotel line
Correct washing of table linen
Francesca Leoni
Carpet in the modern indoor environment
Michael A. Berry
MACHINES
Road sweeper: instructions for use
Maurizio Pedrini
Emphasize professionalism and experience for the brand
Niccolò Luongo
Reduction, reuse and recycling: the future of EU packaging
Francesca De Vecchi
Safeguarding the competitiveness of EU industry trends
edited by Cristina Cardinali
Paper industry in Europe
edited by Giacomo Torrenzi
Depuration of industrial wastewater
Giacomo Torrenzi
MARKETING
If you have more brains, then use it!
Fabrizio Pirovano and Marco Monti
ON THE MARKET TODAY
Technologies, research and development: the new products in the world of cleaning
Loredana Vitulano
Sustainable methodologies in the containment of commodity pests
Michele Ruzza and Andrea Anelli
As shown by the data in the report World Employment and Social Outlook: Trends 2024, although the economy slowed down, global growth in 2023 slightly exceeded expectations, and labor markets demonstrated unexpected strength. Fueled by robust job growth, both the unemployment rate and the jobs gap have fallen below levels seen before the pandemic. In 2023, the global unemployment rate stood at 5.1 percent, representing a slight improvement compared to 2022. Even with decreasing unemployment rates and favorable employment growth, real wages fell in most G20 nations, as salary increases did not keep up with inflation. Worries about labor and skill shortages continue to be a top priority for policymakers, particularly in advanced and certain emerging economies. Although overall labor force participation rates have rebounded quickly, sectors reliant on essential workers are struggling to attract individuals to meet the increasing demand.
The European Commission released its second status report on the Digital Decade, which reports on progress toward the goals set out in the EU's policy agenda for the Digital Decade to 2030. The report serves as an important warning that the region risks falling behind in digital transformation compared to its global rivals. For the first time, individual member states were analyzed, revealing that their overall performance falls far short of the EU's ambitions. The report raises concerns about the EU's performance in its digital transformation and urges member states to make greater efforts to achieve its goals.
The critical issues highlighted by the report, stemming mainly from a lack
of sufficient progress toward the targets set and significant disparities among member states, are analyzed in clusters, defined according to their contribution to: competitive, sovereign and resilient EU; protecting and empowering people; leveraging digital transformation for smart greening; harmonize digital policies and spending.
The EU has not yet achieved full convergence on most of the goals and targets, and the pace of progress on some of them is slower than expected especially in the areas of skills, high-quality connectivity, adoption of artificial intelligence (AI), and data analytics by companies, semiconductors, and startup ecosystems. In addition, it
points out that since the digital transaction has not yet been completed, the full potential of the Digital Single Market has yet to be tapped.
Growth and investment in infrastructure in China has increased demand for professional cleaning, disinfection and hygiene products and services, allowing this market to grow exponentially in recent years. According to Interclean, this rise can be attributed to several factors, aside from economic growth.One aspect is the focus on innovation: China is focusing on the development of cutting-edge technologies like AI-powered cleaning robots and eco-friendly solutions, definitively distancing himself from copycat products. Another aspect is the focus on sustainability: consumers in China are increasingly demanding eco-friendly products and services. This trend is driving innovation in biodegradable cleaning agents, recycled materials for cleaning tools, and energy-efficient equipment.
This growing market is basically shaped by: the rise of AI, that China is
increasingly integrating into the cleaning sector; the rising demand of high-quality, branded cleaning agents, detergents, and disinfectants alongside eco-friendly options; a growing
environmental awareness, that is leading China to be at the forefront in the development of the biodegradable detergents, recycled tools, and energy-saving equipment.
The 2024 edition of the European Cleaning & Hygiene Awards concluded on the night of 3 October with the crowning of the 11 winners (one for each category) which gave the major contribution to the professional cleaning sector over the past 12-months. The 2024 winners are:
• Best Use of Smart Solutions by a Service Provider - JPC by Samsic
• Investment in Training - CleanEvent
• Start-Up Business of the Year - Cliezen
• Excellence in Client-Contractor Partnerships - Derrycourt Cleaning Specialists at the National Rehabilita-
tion University Hospital
• Sustainability - Best Practice (Manufacturing) - Satino, a WEPA Professional brand
• Sustainability - Best Practice (Service Provider) - Principle Cleaning Services
• Commitment to Diversity in the Workforce - Breedweer Facilitaire Diensten
• Best Initiative Raising the Profile of the Cleaning Sector - Markas
• Technological Innovation of the Year - Nexaro for the NR1500
• Leader of the Year - Diane van Dijk, CSU
• Rising Star of the Year - Kelsey Hargreaves, The British Institute of Cleaning Science (BICSc)
Efficient, resistant, ergonomic and functional: this is Igeax’s Industrial line, designed to be excellent and made in Italy with a focus on sustainable materials.
A complete range that meets the specific needs of industrial cleaning, which by definition is more frequent and intense than domestic cleaning as it has to deal with high traffic areas where dirt accumulates quickly. The unique line also features high resistance to wear and tear making the
equipment suitable for industrial use. Besides, it protects the operator’s health by reducing effort and minimising the risk of work-related illness.
The special range includes all must-have products for cleaning in commercial and industrial environments, made with premium raw materials that guarantee high performance for frequent use: brushes, tube
brushes, cobweb brushes, brooms, dustpans, squeegees, handles and scrapers, without forgetting tools wall bars, Display units and Shadow board for the efficient organisation of working tools. Quality, ergonomics and durability are the distinctive features that characterise the Industrial line, making the whole range up to the task. Besides, the exclusive line is distinguished by certain peculiarities that make it unique.
First, Igeax products are the only ones with a universal connection for maximum compatibility , adapting perfectly to a wide range of tools. With a fixing ring designed for handles with a diameter of 21 to 25 mm, the Igeax’s universal connection ensures superior resistance and safety.
Lastly, the Industrial line features bristles with two different hardnesses to meet every cleaning need . Not only does the double bristle add a
touch of style to the products, but it also maximises their efficiency, making them suitable for a wide variety of operations. Dense punching, perfect cut, optimal inclination and greater contact surface further maximise the performance of Igeax bristles ensuring complete, effective and rapid cleaning
Plastic pollution has become a global problem, causing damage to our oceans, wildlife and ecosystems. Igeax strongly believes in action and positive impact; for this reason, the company uses recycled polypropylene and PET for the production of industrial brooms and brushes, reducing its dependency on virgin plastic and contributing to the circular economy
Moreover, the use of recycled materials reduces its carbon footprint, contributing to a greener and more sustainable future. Igeax’s commitment to sustainability does not compromise the exceptional quality of its products. The Italian company adopts rigorous testing processes and quality control measures to ensure that all its products meet the highest standards.
A level of precision greater than ever before
Countless dense and fine bristles Perfect cut for maximum precision
Designed to ensure even food distribution and complete dirt removal from the tightest spaces
Ergonomic handgrip with anti-drip hole
The strategic goal is to reduce dependence on third countries, particularly for raw materials deemed strategic. The EU intends to invest primarily in research and development, with a vision of sustainable extraction in its own countries, maximizing the recovery of valuable materials from waste
Maurizio Pedrini journalist and technical director of Dimensione Pulito
The European Council has made an important decision, full of repercussions for the future of the continent. Indeed, the highest institution that sets the European Union's overall policy priorities and directions has adopted the European Regulation on Critical Raw Materials, as demand for rare earths is expected to increase exponentially in the coming years. Critical raw materials are items of great economic importance to the EU, with a high risk of supply disruption due to concentration of sources and lack of viable and affordable substitutes. The regulation has some clear objectives: to increase and diversify the EU's supply of critical raw materials; to strengthen circularity, including recycling; and to support research and innovation in resource efficiency and substitutes development. The new rules will also strengthen Europe's strategic autonomy.
Critical raw materials
Raw materials are defined as metals, minerals and natural materials that, as we all know, are integral and indispensable parts of our daily lives. Among them, those that are of particular economic importance and have a high supply risk are called “critical raw materials.” These are essential elements for the functioning and integrity of various industrial ecosystems. The EU Commission has identified 34 critical raw materials that fall squarely within a number of areas considered particularly strategic to the functioning and integrity of a wide range of industrial ecosystems. Some areas are of extraordinary strategic relevance to the EU's renewable energy, space and defense objectives. From the 34 critical raw materials thus identified, a specific list of so-called strategic raw materials was subsequently drawn up, for which exponential growth in terms of supply is assumed in the coming years because, being the result of complex production, they are exposed to a higher
risk of supply and access problems. By now, as we all know, critical raw materials - also called rare earths - are used just about everywhere. In fact, without them, many of the tools and technologies critical to everyday life could not function, as they are found in many everyday devices.
Smartphones, a mine of precious metals
Think, just to give one example, of smartphones, which - in addition to being devices that are now indispensable in our lives - also store memories, photographs, contracts, notes and other precious material that is almost indispensable to our daily lives. Many people do not know, however, that they also represent a kind of mine of precious metals: rare earths, precisely. According to the American Chemical Society, a single iPhone contains 16 out of 17 rare earths, but together they do not exceed 1 percent of the weight of the device. Rare Earth Elements (REEs) are, for example, scandium, lanthanum, cerium, praseodymium, neodymium, promethium, samarium, europium, gadolinium, terbium, dysprosium, holmium, erbium, thulium, ytterbium, and lutetium. Complex names for metals that are probably unknown to most, but because of their effective performance they are used in a variety of areas: from the electronics and technology industries to aeronaut-
ics and the military. Although little known, rare earths enable the production and operation of objects that are part of everyday life and also play a key role in green technologies.
These increasingly valuable critical raw materials are in the vast majority obtained outside the EU. The European Union is well aware that it is, unfortunately, not self-sufficient, but - finally - for some years now it has been firmly on the path to diversify its supply as much as possible: a path made all the more urgent and indispensable by the geopolitical upheavals that are sweeping through the West, the whole world and Europe in particular. At present, the picture is still highly problematic. The EU is heavily dependent on China for magnesium (98.9% of imports in 2023) and gallium (79.2%), Turkey for borates (76.0%), and Brazil for niobium (86.6%). An increasing weight of Russia for rare earths and gallium imports also emerges between 2022 and 2023 (30.1% and 12.5% in 2023, respectively, percentages rising to 62.2% and 23.9% in the first two months of 2024). In addition, the EU does not exceed the 7% share of global production in any of the 34 critical raw materials, thus denoting a strong vulnerability at the beginning of the supply chain, which only partially improves going downstream in the production process.
From the JRC assessments, five technologies in particular show strong vulnerability throughout the supply chain: batteries; photovoltaic panels; data storage and servers; smartphones, tablets and laptops; and drones. Looking at the most recent critical commodity prices, two trends emerge: in the long term, a marked increase in prices compared to the pre-Covid period; in the short term, a more heterogeneous picture, where some prices stabilize while others (such as copper) continue their growth.
But from the decidedly worrying analysis of the situation, let us see how in concrete terms the EU is acting to try to reverse the trend. Precisely in order to reduce dependence on third countries for access to rare raw materials, the EU has set important goals for 2030. One of these, diversification of EU imports to reduce stra-
tegic dependencies: at least 10% of the EU's annual consumption will have to come from extraction within the EU. There will also be a focus on domestic recycling: at least 25% of the EU's annual consumption will have to come from it. To this end, the EU will intensify trade measures, including: the establishment of a club for critical raw materials that brings together all countries ready to strengthen global supply chains; strengthening the World Trade Organization; expanding its network of investment facilitation agreements and free trade agreements; and increased focus on enforcement to combat unfair trade agreements. The European Union intends to invest primarily in research and development, with a vision of sustainable extraction in its own countries, maximizing the recovery of valuable materials from waste. One way to reduce, at least partially, de -
pendence on the complex dynamics of global markets for critical raw materials lies in enhancing its own “urban reserve” of technological waste. According to a recent ERION report, the proper and complete management, geared toward recycling instead of disposal, of post-consumer WEEE electrical and electronic equipment can become a real “mine” in the logic of the transition to the circular economy. According to data in the report, while more than 900,000 tons per year of electrical and electronic equipment is placed on the market, just over 350,000 tons per year of WEEE is collected separately, or 40 percent, compared to a European target of 65 percent. Of these, 89 percent go to recycling. With the right investments and policy choices, there could be many more recycled materials, reducing our consumption of primary materials.
Royal 15 is the compact walk-behind scrubber dryer ideal for cleaning small and medium-sized surfaces such as stores, laboratories, offices and restaurants and which, thanks to its 15-liter capacity and 385 mm cleaning width, guarantees an output of up to 1.540 m2/h.
The meticulously thought-out design is tailored to make this machine extremely compact and easy to handle, while at the same time providing top-notch professional performance to ensure excellent cleaning results, even in the tightest spaces.
This scrubber dryer is the ideal machine for working on all types of floors, even the most difficult ones (such as concrete, bolted, non-slip surfaces), ensuring excellent cleaning results.
Due to their versatility and positive benefits, enzymes are more frequently incorporated into professional cleaning products. But like all cleaning products, also those containing enzymes must undergo a safety risk assessment to ensure that they are safe to use by the end users
edited by Simone Ciapparelli
For many years, enzymes have been used safely in professional products for bulk laundering of fabrics and clothing from the manufacturing, healthcare, and service industries.
Enzymes have also been used in a variety of professional products such as surface cleaners.
Enzymes can contribute to the sustainability and environmental safety profile of formulations that use them. Enzymes do this through reducing the temperature at which the product needs to be used, replacing the function of harsher ingredients, being fully and quickly biodegradable, and virtually non toxic to people1, flora, and fauna.
Nevertheless, despite their low order of toxicity, exposure by inhalation may lead to the development of occu-
A.I.S.E. represents the detergents & maintenance products industry in Europe. Based in Brussels, A.I.S.E. has been the voice of the industry to EU regulators since 1952. Membership consists of 29 national associations across Europe, 19 corporate members and 23 value chain partners. Through this extensive network, A.I.S.E. represents over 900 companies supplying household and professional cleaning products and services across Europe.
pational allergy2. To have the potential to cause respiratory sensitisation, the enzyme must become airborne as a dust particle or mist droplet. Moreover, the concentrations required to cause respiratory sensitisation are extremely low. This means that not only do enzymes as raw materials present a risk, but also the finished products that contain them may present a risk. However, only a minor fraction of those individuals exposed to sufficiently high doses of airborne enzyme will at some point be at risk for developing a sensitisation towards the specific enzyme. Professional cleaning products are used across a wide variety of different scenarios, but broadly can fit into one of three classes:
X used in a fully closed system (e.g. in Cleaning in place or in a closed machine such as an industrial dishwasher/washing machine);
X used in a partially closed system or process (e.g. in Cleaning out of places, manually dosed into a closed system, cleaning of equipment items by manual immersion in a closed container);
X used in the open for cleaning of surfaces and/or equipment, (e.g. food preparation surfaces, floors and walls, sanitary equipment).
Each scenario imparts a different level of risk for the end user, and that information allows product development and design to reflect the risk in each scenario. The higher level of containment and control for the end use application, the lower the risk of exposure. Likewise, the elimination and/or minimisation of inhalable dust or aerosol through product design will also reduce the risk of exposure. Combining containment, exposure control and safe product design is the obvious target to achieve.
Of the three main scenarios, the use of enzyme products for open cleaning of surfaces carries the highest risk of exposure and therefore these products require very careful design and
use instruction. Training is also an important part of the safety management program for use of any professional cleaning product regardless of the formulation. But for enzyme-containing products, very specific training is required. In all scenarios, the risk from residual product contamination on surfaces, including the one coming from the enzymes used in the product, must also be considered. Residual enzymes on surfaces may become airborne from subsequent process steps or conditions resulting in uncontrolled exposure.
Since there is little difference in how consumer and professional products are manufactured and packed, it can be inferred that the experiences, mistakes, best practices, and historical data from detergent manufacturing are entirely relevant. However, as previously stated, the end use can be different. This makes the need for exposure data or benchmarks for every type of application extremely important, if not critical, for the completion of an effective end user risk assessment. The document developed by A.I.S.E. Guidance for the Risk Assessment of Enzyme-Containing Products for Professional Cleaning, on which this article is based, aims to inform and guide companies developing and marketing professional cleaning products containing enzymes to ensure, through the process of risk assessment, the design of professional products are safe for the intended application, and safe for the end users and others in the vicinity of their use.
Prior to introducing an enzyme-containing cleaning product onto the market, a risk assessment is conducted to ensure the safe use by the professional. Enzymes have a very good safety profile but, as with many other proteins, they can act as respiratory sensitizers and so may lead to allergy symptoms. This potential risk is the primary focus
for risk assessments for enzymes and must be managed carefully.
Risk assessment can be divided into four areas:
X hazard identification;
X dose-response or benchmark identification;
X exposure assessment;
X risk characterization.
Hazard identification
This is the characterization of the fundamental physical, chemical and biological effects of a material. The toxicology of enzymes poses no significant hazard. Acute and sub-chronic toxicity is not of concern for industrial enzymes. Enzymes have a low order of toxicity. In the context of this article, the safety concern being addressed is a potential induction of respiratory allergies.
Skin and eye irritation may be an issue in case of long-term exposure to high concentrations of an enzyme from the class of proteases. This hazard is not
related to enzymes outside the class of proteases, and it is not discussed in this guideline.
Dose-response or benchmark identification
Generally, in this step of the risk assessment process, the relationship between the level of exposure and the specific biological effect is characterized. However, since the dose-response relationship for enzyme allergy is not fully understood and there are gaps in our understanding of the relationship between exposure, sensitisation and symptoms, benchmarks are generally used to support decisions in enzyme risk assessments. Such benchmarks are based on studies in which measured or estimated exposure levels are associated with a demonstrated specific biological effect (such as whether an allergen-specific antibody is produced) in those exposed. A clear benefit of this strategy is that it can be based entirely on human data.
In EU countries, there is a requirement by the REACH legislation to define a Derived No Effect Level (DNEL) for registered substances. Where a DNEL cannot be established, e.g. for sensitizing substances like enzymes, then a Derived Minimal Effect Level (DMEL) is recommended. For enzymes, a DMEL has been established by thorough retrospective review of occupational and consumer experience4. The DMEL for occupational exposure has been set as 60 ng/m3 thereby following the Threshold Limit Value (TLV) set for Subtilisin by the American Conference of Governmental Industrial Hygienists (ACGIH) in 1971. For consumer exposure, the DMEL is 15 ng/m3. Professional uses should apply one of these DMELs depending on the character of the use. If the professional receives training in the safe handling of an enzyme containing product and have access to personal protective equipment like correct respiratory protection equipment, then the DMEL of
60 ng/ m3 may apply. For other professional users, the DMEL of 15 ng/m3 should apply.
It establishes the amount of airborne enzyme to which the user may be exposed during intended use or foreseeable unintended use. This value is then compared to the benchmark exposure (in most cases the DMEL) in order to make risk decisions. Measuring, or even estimating, exposure to enzymes is not necessarily a simple process. However, the determination of exposure values is needed for carrying out these risk assessments. In the absence of good quality exposure data, reasonable worstcase assumptions and uncertainty factors are employed, which lead to an overestimation of exposure levels and thereby limit unnecessarily the amount and type of enzyme that can be used in a professional cleaning product. It is therefore important that the exposure assessment be conducted thoroughly, in order to enable the optimum use of enzymes in the products. The most important step of an exposure assessment is trying to define the factors that may influence the exposure.
It is the examination of the relationship between human exposure (calculated or measured) and the inherent toxicity of a substance, in order that the likely incidence and severity of any effect can be assessed. This step is important because it integrates information regarding the hazard identification and exposure assessment associated with use and foreseeable unintended use of a product. It should be recognized that risk assessment is a continuously evolving discipline. The quality and reliability of a risk assessment is dependent on and is only as good as the data used to conduct the assessment. Uncertainties exist in dose-response relationships, exposure data and estimates from exposure models.
Assumptions and estimations need to be stated clearly as they can affect the reliability and quality of the risk assessment. It is important to consider these points when evaluating information from the risk assessment in determining whether the risk is considered acceptable.
The objectives of the risk management process are to determine the significance of risks to human health to ensure that the product use remains within the acceptable risk levels, and to communicate risks, or lack thereof, to appropriate audiences, in an effective manner.
In general terms, the risk control step of the risk management process should strive to reduce the risk by limiting airborne exposure to enzymes included in the product formulation. Risk reduction options may include product modification, only allowing certain uses or a decision not to market the enzyme containing product. Modification options may include changing the matrix or delivery system of the enzyme containing product, reducing the enzyme concentration in the product, substituting other ingredients that may be affecting the potency of the enzyme, or a combination of these approaches.
An integral part of the risk management process is to communicate enzyme product benefits, as well as potential risks, to appropriate audiences in an effective way. There are important audiences to target in designing a risk communication program:
X users of the company’s products;
X employers of professional users, e.g. cleaning companies;
X persons responsible for worker safety in the companies employing professional users;
X other stakeholders, such as the general public, governmental and non-gov-
ernmental organizations, or industry partners.
Product labels are the primary means of communication with consumers and professionals. For enzyme-containing products, as with all consumer products, labels are a mechanism for communicating composition of the product, first aid information, appropriate warning statements, and use and handling guidelines with detailed examples of correct use and concrete recommendations to steer towards proper use. For professionals, SDSs are available but these are often only suitable, i.e. understandable, for people with the proper training to interpret the SDSs. Hence, it is important for products used by professionals in small companies to provide all significant information in the same way as for consumers.
Notes
1 Basketter et al, Enzymes in cleaning products: An overview of toxicological properties and risk assessment/management, Regulatory Toxicology and Pharmacology 64 (2012) 117–123.
2 Basketter et al, Managing the Risk of Occupational Allergy in the Enzyme Detergent Industry, Journal of Occupational and Environmental Hygiene, 12: 431–437 (2015)
4 D.A. Basketter, C. Broekhuizen, M. Fieldsend, S. Kirkwood, R. Mascarenhas, K. Maurer, C. Pedersen, C. Rodriguez, H.-E. Schiff; Defining occupational and consumer exposure limits for enzyme protein respiratory allergens under REACH; Toxicology 268 (2010) 165–170
Source: A.I.S.E., Guidance for the Risk Assessment of Enzyme-Containing Products for Professional Cleaning (June 2024)
Christeyns presents its new Professional Hygiene product portfolio, designed to meet the needs of hygiene professionals worldwide. This innovative portfolio is divided into four macro ranges, each designed to offer specific solutions for each area of application: laundry, kitchen floors and interiors. For all the following ranges there are environmentally friendly alternatives belonging to the Green’r line, ECOLABEL branded products.
To meet the needs of the customers, laundry specialists have developed the CARETEX line, which includes products for non-delicate and delicate fabrics.
For those using ozone generators, offer the RAPID-O line, with compatible products that ensure deep and environmentally friendly cleaning.
With CARETEX, Christeyns guarantees impeccable results for every type of fabric.
The RELAVIT range is designed to help kitchen professionals maintain impeccable hygiene in the kitchen environment. The RELAVIT range includes periodic cleaners, degreasers, descaling agents, disinfectants and specific products in different packages, concentrations and forms, such as solids and sprays. These products ensure perfect cleaning results, leaving the kitchen spotless and safe.
Christeyns helps hygiene professionals select the right products for the maintenance and treatment of different types of floors, especially with the FLOORIT product range. FLOORIT products are designed for daily maintenance and also include
specialised products, all available in different fragrances and ecological variants. The range includes waxes, wax removers and degreasers, ensuring radiantly clean and well cared-for floors.
The LUFRA range comprises a wide selection of interior cleaning products, including cleaners for various surfaces and bathroom-specific purposes. Standard cleaners are available in both concentrated and ready-to-use formulas, accompanied by degreasers, descaling agents and polishes.
LUFRA offers specific solutions for glass and metal surfaces, ensuring excellent results for interior cleaning and maintenance.
Christeyns’ new portfolio represents a major step forward in the modernisation of the chemical industry, offering innovative, efficient and environmentally friendly solutions for Professional Hygiene. Stay tuned for further updates and details on the official launch.
The industry is moving toward increasing use of new technologies and strategies aimed at energy efficiency and environmental sustainability, including addressing energy and gas costs
edited by Simone Ciapparelli
The business of industrial laundries, including rental, covers the following products: flat linen (tablecloths, sheets, pillowcases, towels); work clothes and PPE; mattresses and pillows; carpets; sterile operating room sets.
In relation to the characteristics of the service provided and the target end market, the sector can be divided into three segments: Public and Private Healthcare, Hotel and Catering, and Community and Industry.
There is a high level of competition in the sector due to the presence of numerous players, especially in the Hotel and Catering area and in the Sanitation segment of the Healthcare area. Competition is basically based on price, except in some areas (sterilization activities, integrated services for Healthcare and PPE), where the quality of the service provided is much more relevant. Differentiation in the sector is rath-
er low, due to the rather basic needs of most of the market, however, some areas require special skills, certifications and periodic investments by sup -
pliers, in order to adapt technological resources and personnel to customer needs. The sector is coming out of a particularly challenging three-year
period, which saw the succession of several exogenous events (pandemic, Russia-Ukraine conflict) capable of affecting its performance both in terms of revenues and margins (see box). Strengths of the sector include an efficient and flexible organizational structure; the ability to preside over tenders; a balanced price/quality ratio; quality of service delivery, particularly in the health care sector.
The great focus on public health and welfare, indirectly amplified by the pandemic, has led to an even greater emphasis on ensuring sanitation, sanitization, and cleanliness, and represents an opportunity for the sector in the medium term as well. It must also be kept in mind that the sterilization segment still has wide margins for de-
velopment, and its evolution is closely related to possible outsourcing choices by healthcare facilities. There is also an increasing use of Reusable Technical Fabric products, replacing disposable ones, which may therefore lead to an increase in demand for laundry services.
In the restaurant industry, on the other hand, there is an increase in the use of disposable table linens, which could lead to a decline in demand in that sector.
Technological innovation and digitalization are central to the industry to simplify the organization of work, ensure process control, streamline operations and rationalize costs, reducing waste. Technological development affects all areas of the business and includes the adoption of advanced
management control systems, data analysis, and process automation (see article on page 26). More structured operators use platforms that manage all processes, from rental contracts, to organizing material pickup and delivery, to warehouse management, including general and analytical accounting and business intelligence. System certifications are increasingly common in the industry; most major operators are environmentally certified to ISO 14000 and some hold Emas registration. Process and product certifications are also widespread, for example, the RABC (Risk Analysis Biocontamination Control system) certification, which covers the entire process, from the collection of soiled items to their delivery to the customer. The goal is to make green not the individual product, but the entire produc-
tion process, thanks in part to technological innovation, which makes it possible to use less and less water, detergents and energy, limit waste and the use of resources, while ensuring quality of the result and greater durability of the fabrics.
Over the past few years, the topic of sustainability has become increasingly important to industry players, not only because of its ethical aspects, but also because of its impact on the efficiency and profitability of companies. In the industrial laundry sector, the implementation of sustainable practices concerns:
X water management, which involves rationalizing water withdrawals and optimizing its consumption and recovery. At the same time, the risk of water pollution is kept under control with modern sewage treatment plants and containment basins to eliminate the risk of soil contamination;
X the use of eco-friendly processes and products, such as detergents, and optimizing the use of chemicals, with the replacement of packaging and plastic collection bags with recycled and/or reusable materials;
X proper management of reusable textiles, seeking to lengthen the life cycle of products, and the spread of TTR
(Technical Reusable Fabrics), replacing TNT (Nonwoven Fabric) disposables. TTR allows significant waste reduction and can be sterilized through steam autoclaves, unlike disposable products, the sterilization of which involves the
use of chemicals, in addition to the fact that they produce a large amount of waste that is difficult to dispose of.
Source: Cerved Marketing Intelligence, Lavanderie industriali (August 2023)
Although industrial laundries do not fall under the definition of an “energy-intensive enterprise,” it is easy to see how energy aspects play a crucial role in running a business that involves washing and drying hundreds of tons of laundry each day. Over the past three years, the incidence of energy and gas costs for laundries has increased almost fivefold. According to data from the International Energy Agency (IEA), gas has gone from costing about Euro 20/MWh in May 2020 to
more than Euro 70 in the same month of 2021, with subsequent spikes taking it to Euro 343/MWh due to the war. Thus, it can be argued that the war has aggravated an already worrisome situation. Washing is one of the sectors most affected by the energy crisis, partly because a characteristic feature of the industry is the difficulty in passing on these price increases to customers, immediately translating into heavy budget losses for businesses. These difficulties have
led operators to implement energysaving strategies such as flexible use of processing temperatures and working hours and investments in extraordinary maintenance to reduce heat losses in the washing process.
Companies' investment projects aimed at implementing higherperformance production equipment capable of reducing processing temperatures and times for the same amount of linen processed have also continued.
Less working time, less effort required
More control over wash cycles, more efficiency in your business
designing your clean www.imesa.it
A
edited by Cristina Cardinali
When we talk about a smart industrial laundry, we are referring not to a technological upgrade for its own sake, but to a true technological conglomerate, integrated into an ecosystem, where every element, from smart IoT sensors to data management systems, from predictive analytics software to user interfaces, works in synergy to improve efficiency, reduce costs and increase sustainability.
Let's take an example for clarity and think about the benefits that can be derived from advanced sensors that can monitor various parameters such as temperature, humidity and levels of soaps and detergents, water quantity and quality, to optimize internal transportation routes and warehouse management by sending real-time data to a centralized management system. Here, in this “central brain,” AI algorithms and Machine Learning models analyze collected data to make accurate predictions about operation and maintenance needs in order to optimize resource use and even adapt processes in real time to unforeseen
circumstances.
Added to this is the strategic use of data analytics, which can provide valuable insights into customer behavior, market trends, and operational performance, assisting management in choosing which strategic plans to un-
dertake and the timeframes needed to align goals.
THE ROLE OF AI
One of the most revolutionary and important contributions of AI in the context of industrial laundries
Below is some useful information on how to calculate the amount of laundry to be washed based on weight and washing time, and how to calculate energy consumption.
The following can be kept in mind when calculating the amount of laundry for a utility:
- A 3-4 star hotel room produces about three to four kilograms of laundry with each change.
- As for catering, the amount of table cloth per cover can be calculated as 0.3 kg per person.
is in predictive maintenance. Traditionally, maintenance of industrial equipment has always been carried out following fixed schedules or in response to failures generated on the spot. The application of models borrowed from AI, however, allows for a much more proactive approach; by examining historical data and “real time” numerical values, it is possible to predict, with accuracy, when a piece of machinery may fail or otherwise require technical intervention, thereby avoiding production line stoppages.
If we have seen so far the importance of digital transformation and the growing expectations of the industrial laundry sector, it is equally important to understand how, in practice, it is possible to map out a roadmap for transformation, that careful planning to determine exactly what technology implementation to address and how to ensure that the goals are effectively achieved. Let's look, then, at how to map out a roadmap for digital transformation broken down into three ba-
To make calculations easier, always consider that a wash cycle takes at least 60 minutes.
To evaluate energy consumption as an indication, it is advisable to keep in mind that:
- To get an idea of water consumption, keep in mind that each kilogram of laundry needs 3 to 4 liters of water in each washing step.
-Each kilogram of wool needs 7 to 8 liters of water in each washing step.
-Each kg of washed laundry corresponds to the consumption of 1
kg/h steam or 0.75 Kw/h electric.
-Each kg of laundry dried corresponds to the consumption of 1.5 kg/h steam or 1.1 Kw/h electric.
If you have the potential in electric kw multiplying by 1.36 will give the equal consumption in kg/h steam. If you have the gas consumption expressed in kw multiplying by 862 you will get the Kg/cal of potential. If you have the potential in kg/cal divided by 600 you get the Kg/h steam.
sic phases: planning, implementation and monitoring.
The planning phase
The first step in any planning process is to conduct a thorough analysis of the business environment, which involves assessing internal competencies, existing infrastructure and market positioning. By examining these aspects, it is indeed very likely to be able to trace the critical areas that need technological innovation. It is therefore necessary to define objectives that must be specific, measurable, achievable, relevant and timed, linked to business drivers for profitability, improved operational efficiency or expansion into new markets.
implementation phase
Once the planning phase is completed, the next step is the implementation of the most appropriate technologies. Choosing the right technology stack is vital and must be aligned not only with business goals but also with the skills of the staff. Whether cloud-based solutions for data processing or AI platforms for
advanced analytics, the choice must be made with an eye toward scalability and compatibility with existing assets.
Important is that the team can also come “aligned” with the technology used, including through targeted training and appropriate training to make the transformation natural and effective.
The monitoring phase
It is not enough to implement new solutions and hope they work: it is critical to have clear and measurable metrics and KPIs in place to assess the effectiveness of initiatives. This goes beyond simple ROI analysis; it extends to more sophisticated metrics such as Time to Return on Investment (TROI), Customer Lifetime Value (CLV) or Net Promoter Score (NPS). But in an ever-evolving industry, such as precisely the technology sector, it is also crucial to monitor a “feedback loop” of continuous updating: the roadmap for transformation can never be a linear path defined once and for all, but a continuous cycle of improvement and adaptation.
Technological progress has revolutionized the industry in many ways. The industrial laundry industry is no exception. Automation, data analytics, and recycling systems are some of the numerous innovative technologies that can help industrial laundries boost efficiency and cut costs.
Predictive Maintenance Software utilizes data analysis and machine learning algorithms to anticipate when machinery is expected to fail, enabling industrial laundries to plan upkeep in advance of any malfunctions. This results in less downtime, prolongs the lifespan of equipment, and lowers maintenance expenses.
Industrial laundries can remotely control their operations using machine management systems from any location with internet access. This technology has the potential to enhance productivity, lower expenses, and enhance scheduling and resource allocation flexibility.
Robotic arms are employed in these systems to organize and transport laundry items during the washing and drying stages. This technology has the potential to greatly lower labor expenses and enhance processing speed, resulting in increased efficiency and savings. Automated sorting systems can additionally decrease the likelihood of harm to employees and enhance general
Water recycling systems collect and process used wash water from laundry, enabling its reuse for washing or other potential uses. This could greatly decrease the use of freshwater and the release of wastewater, ultimately resulting in better environmental sustainability and lower water expenses.
RFID technology utilizes radio waves to monitor items as they progress through the laundry process. An RFID system designed for industrial laundries can enhance inventory control, minimize losses, and enhance customer service. RFID technology has the potential to enhance workflows and decrease processing times, resulting in increased efficiency and cost savings.
To sum up, industrial laundries can greatly profit from adopting modern technologies like water recycling systems, predictive maintenance software, cloud-based management systems, RFID, and automated sorting systems. Industrial laundries can enhance sustainability, reduce costs, and increase efficiency by utilizing these technologies, all the while delivering excellent services to their customers.
https://www.wientjens.com/blogs/5-innovativetechnologies-for-industrial-laundries-to-boost-efficiencyand-cut-costs
Industrial laundries perform a service that is fundamental to the normal operation of the health and tourism sectors and of public benefit to the entire community through the provision, sanitization and sterilization of textile devices, work clothes, PPE, linens, surgical instruments
edited by Simone Ciapparelli
The first activity consists of the collection of soiled linen carried out at the customer's premises; this work step can also be contracted by the laundry to outside firms. The material to be picked up is already placed by the staff of the client company in closed bags, which are of different colors depending on the textile product contained and the adopted coding of the laundry. The bags are then loaded onto vehicles and transferred to the washing and sanitizing plant. After transport, the items are stored in a special unloading area until they are moved to the washing department, which is done, either manually, by means of closet or roll type trolleys, or automatically, by means of conveyor belts that are generally overhead.
This activity consists of sorting incoming linen, dividing it into: flat material (e.g., sheets, tablecloths, napkins); made-up material (e.g., suits, gowns, aprons). More and more laundries, particularly those whose customers are health care companies, are performing this operation downstream of the washing process. In this way, both the biological risk from possible operator contact with infected substances and the risk of abrasions and wounds due to the presence of foreign objects among the linen are reduced. Operators open the bags and drop the material onto a scale belt through which it is moved to the washing department when the predetermined weight-threshold is reached. Even where the presence of overhead lines to transport the material does not require direct operator intervention, the department is still manned. Traceability of items is ensured by making use of the reading of radio transmitter tags attached to each item (transponder-chips), which are read by low-frequency radio wave antennas. In other cases, the operation is carried out before washing, thanks to the use
of pit counters; the linen is manually selected and sorted by the operator according to the type of textile and the degree of soiling. In addition, the items are coded within the company's information system to ensure maximum traceability and optimize process flows, before being transferred to the washing department, inside appropriate bags, usually by means of an overhead handling and storage system that feeds the washing lines.
Washing is generally carried out by means of a continuous batch washer automatically powered by an overhead track conveyor system, on which the bags with the linen to be sanitized move, and by movable arms, while for garments with special characteristics washer-extractors are sometimes used. Detergents used are mostly water-based such as anionic, cationic and nonionic surfactants and fabric softener. Lines are generally dedicated to the treatment of a particular type of laundry. The wash centrifuge is a washing machine with a rotating drum, sup -
plied by cold water or heated by steam depending on the characteristics of the textile to be treated, and is generally used for washing delicate garments, with special specifications, or for stubborn dirt. The continuous washer, on the other hand, is an actual washing tunnel consisting of several “chambers” (from 6 to 24), through which the laundry is moved. During the process, the operator/trainer supervises the dosages, checking the correct concentration of the aqueous bath, and replacing the detergents when finished. In addition to the detergents listed above, the operation also involves the use of other chemical agents such as stain removers, acidifiers, and bleaches. The choice of washing method and mix of detergents and chemicals depends on the types of fabrics to be treated and the dirt to be removed. At the end of the washing phase, for linens destined for health care facilities, bleaching, acidification, and finally hydro extraction operations follow. Linen processed in the washer-continuum is pressed and scarfed, unlike linen from the washer-center, which is
Before shipment, the linen packed is counted again by transponder-chips to ensure that the flow of material incoming is the same as the outgoing
centrifuged. Pressing is generally done by means of a special press equipped with oil- or air-operated pistons. At the end of the process, the linen is advanced to the dryers for drying, by means of a shuttle or conveyor belt.
After washing, the linen is partially dried by means of dryers, of which there are two different types:
- steam: it is powered by 10 bar and 180 °C steam and is equipped with a rotating basket with closing doors, a first
chimney for air intake and a second chimney for expelling the water vapor produced during drying;
- gas-fired: operates similarly to the steam dryer, but is heated by means of a gas burner. It is equipped with a gas leak detector and solenoid valve, which cuts off the power supply in case of leakage.
The linen is then moved to the ironing department either by overhead conveyance or through metal cages equipped with wheels and an adjustable table top or by using specific trolleys, pushed manually by operators.
For flat material, the ironing department consists of three pieces of equipment for each ironing line: introducer,
ironer and folding machine. The introducer automatically feeds the ironer, inside which the drying process of the textile is completed, resulting at the same time ironed. In addition to advancing the linen, the mechanical action of the roller also makes it possible to eliminate any creases present on the textile. The linen is then run over a metal basin heated by steam or thermal oil to a temperature of 180 °C, where the ironing of the garments is completed. The high temperature of the basin is a further guarantee of the sanitization of the textile. At the exit of the ironer, a belt system transports the linen to the folding machine, which automatically folds and stacks the sanitized textiles, which are ejected from the machine when a predetermined
number of processed pieces has been reached. The resulting blocks of linen are finally advanced by conveyor belts to the bagging machines and then to the shipping department.
In the case of packaged linen, the operator picks up one garment at a time, visually inspects it to examine its integrity, and arranges it on hangers that, depending on the type of ironing, automatically direct the garments to the ironing tunnel or to special dummies. In the former case, the garments, still hanging on the hangers, are completely dried by means of hot air and steam jets at a temperature of 170 °C, which allows, at the same time, industrial ironing. In some cases, ironing can also be done or completed manually, using traditional ironing boards. Once the process is completed, the linen is folded (in some cases also manually) and bundled, either in an automated manner with the help of special robots, or manually, and from there it is sent to the mending department, or to the warehouse for replacement (in case of non-repairable damage). Mending is carried out with ordinary sewing machines.
After the sanitization treatment, the shipping department receives the material and makes up the rolls with the packed linen, on which labels prepared by the shipping department are affixed. The material is packed with heat-shrinkable polyethylene film to prevent contamination or damage during transport. The rolls are then placed in dedicated aisles within the shipping area, where drivers pick them up and load them into vans for delivery to customers. Before shipment, the packed linen is again counted by means of the same system used during sorting (transponder-chips) to ensure that the incoming flow of material is the same as the outgoing flow.
Laundries also perform other clean-
ing, washing and sterilization activities, including:
X Sterilization activities of the operating textile: Linen sterilization activities are carried out in a special central plant, located in a purpose-built room within the industrial laundry, equipped with microclimatic conditions to comply with the provisions of medical device legislation. Material entering the central unit is visually inspected for abrasions, holes or cotton dust, then sorted. The items are then washed and dried by means of a washer-extractor. This is followed by the composition of the kit, its packaging, and the sterilization phase. The latter takes place inside an autoclave by means of steam. The sterilized kit is therefore stored inside a dedicated sterile area, where it remains waiting until delivery to the customer, which is done by means of specific closed trolleys capable of preserving the material from external contamination, guaranteeing its sterile condition. The entire process is mapped at all stages to ensure maximum traceability of each individual component.
X Surgical instrument sterilization ac-
tivities: In addition to the sanitization and sterilization of drapery destined for operating rooms, another activity of industrial laundries related to the surgical field is the decontamination of surgical irons. Kits containing instrumentation from operating theaters are received by the laundry and, after an initial sorting phase performed manually, the irons are decontaminated using special chemicals diluted with water. Washing can be done manually (by contact or immersion) or automatically by means of the use of an iron washer, the operation of which is similar to that of a conventional dishwasher suitably modified. In the latter case, chemical dosages are handled automatically by the machine. Once the process is over, the instrumentation is allowed to dry and the kits are reassembled, which are, then, sterilized using the same procedure adopted for the drapery, that is, through the use of an autoclave. Return to the customer is also done in the same manner as described for surgical textile kits.
Source: Inail, Analisi dei rischi lavorativi nelle lavanderie industriali (2022)
The best way to prevent the spread of germs and bacteria during meals is to use tablecloths and napkins that have undergone a correct washing process
Francesca Leoni
The World Health Organization, in its operational considerations for the management of the Covid-19 virus for the tourist accommodation sector in addition to providing recommendations for the various activities carried out within the hotel, also intervenes in relation to proper management practice and sanitation with regard to catering. Catering, like the hospitality part, holds the characteristic of having a high degree of social gathering i.e., a large number of guests who not only interact with each other but also interact with the restaurant staff, with a high probability of contact.
They therefore need specific attention: - the guest accommodation system; - the management of services (food, drink, organization of the activity);
- sanitation of rooms and surfaces, especially tables; - interactions between guests and the facility and interactions with the environment.
Hygiene practices
Regarding sanitation aspects, WHO provides specific ways of handling dishes, cutlery and table linen. Among other things, since the transmissibility of the virus occurs by air via droplets produced by coughing or sneezing, which can settle and persist even on inanimate surfaces, or by contact with contaminated hands, it is urged to sanitize even items that have not been used directly by the customer. The attention in the restaurant to the hygienic aspect, especially to the work and support surfaces for dishes - cut-
lery, plates, glasses, etc. - and for hand hygiene turns out to be fundamental since the consumption of food and beverages inevitably involves direct contact of potentially contaminated objects or hands with the mucous membranes of the oral cavity, which represent one of the gateways for the entry of the virus.
That said, the issue of table hygiene and cleanliness deserves a closer look, not only in what has been a particular highlight, but as a constant and inescapable element of food risk control. It plays a central role in this context that table linens are properly sanitized and treated by specialized companies that also provide the customer with certifications about the mode of treatment dedicated to the linen before it is delivered.
The starting point is to be able to ensure that guests who enter the restaurant for the tasting of food prepared by the kitchen have a dining room with a high degree of hygiene, as well as the desired comfort and elegance, the result of a serious and constant practice of sanitization previously studied, then implemented and documented. In this way, the guest will feel that he or she is in a hygienically welcoming environment and can comprehensively appreciate his or her experience through all the senses such as sight, touch, smell and finally taste.
Good sanitation practice starts from the premise that it is necessary to clean and sanitize the room and table at every customer change. To do this, it is necessary that the room environment, including the furniture, service accessories and the table, are subject to prior sanitization by an operator properly and adequately trained on hygiene; a serious method for sanitization cannot disregard the use of materials and
manual actions for cleaning, for cleansing with the help of cleaning products and disinfectant agents, which, only if preceded by the previous actions, with adequate contact time, guarantee the basic sanitization of the room.
It is therefore evident that the operations of sanitizing the hall will have influence on the operational timelines and especially if they occur during the service they may also have repercussions on the decorum and customer service.
Considering the above for the dining room, it is now important to highlight the need for the table to be covered with a reusable fabric with a level of sanitization guaranteed by specialized laundries and certified according to a specific standards, which guarantee control over the biocontamination of textiles through a Risk Analysis Biocontamination Control system.
Elegant tablecloths and napkins made of reusable natural fabric thus offer the convenience of being easily replaceable at the end of each service. After all, it is improper to even imagine the use of disposable items of uncertified origin and significant environmental impact.
In this way, the room operator, through a fast and safe procedure will be able to change in the presence of other customers only the tablecloths, thus offering the next customer maximum hygienic safety.
To set the table, the worker, after removing the used tablecloths, simply puts on gloves and opens the package with the linen and picks up the needed item. Folding allows tablecloths and tablecloth covers to be set using only the fingertips of the thumb and forefinger. The used table linens will be placed in closed containers (bags or sacks in carts) by handling and shaking them
as little as possible in the environment before placing them in the container; the linens will then be picked up by the rental and sanitization company's driver (the truck is sanitized each time it is loaded) who will deliver them to a special area of the company, separate from the clean linen department. In contrast, the choice to use tables without table linens could create strong problems regarding good table sanitization practice because at the time of table rearrangement, the surface will have to be compulsorily washed in the presence of customers and presumably quickly through the use of cloths and products that have a high disinfectant content. This is therefore a highly inadvisable practice since in order to truly sanitize hard surfaces these must be cleaned by cleansing and sanitizing, but if this is done during service the risk is to negatively affect room service and induce out of haste a rushed sanitization to the detriment of the next customer.
The Standard in question is an essential prerequisite for ensuring the catering and hospitality establishments, but also the health sector, the supply of linen that is qualitatively and hygien-
ically safe from the point of view of controlling its biocontamination.
In other words, in order to prevent the spread of diseases transmissible by pathogens, the industrial process of sanitizing textiles - in addition to sensory cleanliness and comfortmust guarantee their hygienic quality and safety, achieved precisely through the technical standard “UNI EN 14065:2016 and the Assosistema Guidelines” based on a RABC (Risk Analysis Biocontamination Control) system.
In this sense, UNI EN 14065 guarantees the implementation of a business management system that ensures treated textiles have the appropriate microbiological quality according to their specific use (healthcare, tourism, catering, industry).
Microbiological analysis covers all stages of the process to which treated textiles are subjected in a laundry industry, from receipt of soiled linen to delivery to the customer, through: sorting, grading, washing, hydro extraction, drying, finishing, folding, packaging and transport.
It should be emphasized that the UNI EN 14065 standard dwells not only on the importance of sanitizing and decontaminating textile devices, but also on the need to protect them from po -
Different types of products are included within the heading “table linen”. Let's see which are the main ones. Tablecloths. The name “tablecloth” refers to the larger fabric that adorns a restaurant table. The tablecloth is an essential element of the most classic or elegant restaurants, although the trend in more modern restaurants is to adopt other solutions, such as American placemats. The size of a restaurant tablecloth can range from 130 to 160 cm.
Slipcovers. These are smaller
tablecloths, between 100 and 120 cm, that are placed above the tablecloths. The tablecover protects the tablecloth underneath and is changed with each change of guest at the table.
Napkins. They are the essential complement to tablecloths. They are made of different fabrics, but cotton is usually the favorite because it is pleasant to the mouth. They have a size of 40x40 or 50x50 cm.
American placemats Increasingly popular, American placemats are very
tential re-contamination through risk analysis and prevention measures implemented over the entire production cycle, up to the moment the products are returned for reuse.
The industrial process includes a thermal component, as washing is carried out at predefined temperatures suitable for sanitization and the subsequent drying/ironing phase reaches high temperatures. Then there is the mechanical action, the time factor, and the chemical treatment part, which takes place through the use of cleaning products and disinfecting agents with bactericidal, virucidal and fungicidal capabilities that guarantee perfect sanitation and safe use. The RABC System also includes actions to monitor and sanitize surfaces, machinery, means of transport and operators.
The UNI EN 14065 standard ensures a proper analysis of biocontamination risks that examines, for each stage of the textile treatment process, what the potential microbiological risk may be, its potential cause, the control method implemented as well as the identification of the intervention measures put in place in order to restore the conformity of the process in case of detection of any deviations and anomalies.
convenient for a restaurant to use because their maintenance is quick and easy. Their use is constantly increasing. They are about 40/50x30 cm in size.
Runners. Runners are a less bulky version of a tablecloth that only covers the place of two diners positioned next to each other, leaving the sides of the table visible and uncovered. This is a very useful solution when you have a nice table and do not want to cover it completely.
Carpet in the modern indoor environment poses no risk to public health, as long as it is properly maintained and cleaned
Michael A. Berry PhD
Arobust assessment of carpet is fundamental to any objective judgment related to carpet and human exposure indoors. A responsible decision with regard to carpet in sensitive environments, such as schools and health care facilities, should be based on factual, documented evidence. Therefore, it is intended that this body of information be considered in the process of establishing public and industry policies with regard to carpet, carpet buying decisions, and responsible communication with consumers, public administrators, and the technical community. A panel of ten academic and industry researchers and technical specialists met at the University of North Carolina at Chapel Hill to critically examine peer-reviewed or otherwise credible science with regard to the positive or
negative attributes of carpet in the modern indoor environment. The review was organized to assess environmental benefits of carpet, as well as negative perceptions and environmental concerns. The primary objective of the expert review was to examine key studies that address carpet as a major contributor to indoor environmental quality and as a possible source of adverse human response. Regarding the latter, the panel was asked to closely examine any relevant scienti fic data related to toxic substances and allergens commonly found, or alleged to be, in and over carpet and related non-carpet surfaces. The panel was also asked to evaluate maintenance and management practices related to long-term carpet performance and health protection. Hundreds of studies were examined in the course of this review.
This article is reprinted with permission from issue 1, volume 5, of the Cleaning Science Quarterly, the official peer-review journal of the Cleaning Industry Research Institute (CIRI)
The review examined the scienti fic literature at large, but mainly focused on information found throughout the peer-reviewed technical literature, National Health Sciences Libraries, EPA’s research information database, and previous reviews and conferences conducted by recognized experts. In advance of the meeting, each expert prepared a review paper for his or her specialty area. In the exchange, new sources of information were identi fied, points of view surfaced, and important issues were highlighted.
A comprehensive review of the literature supports the contention that carpet is a significant positive contributor to the quality of life indoors. The purpose of every indoor environment is to provide for security, comfort, social interaction and productivity. A
healthy indoor environment is one that achieves these four purposes and radiates a “sense of well-being” to inhabitants. An elevated sense of “well-being” is the basis for the human condition we call “healthy.” Reviewers, working independently, noted how carpet contributes to these “healthy design” factors: usable space that promotes social interaction and productivity; safety as in the prevention of slips and falls; aesthetics; physical comfort and ergonomics; lighting to include the management of glare or light reflectance; acoustics and the management of noise; climate control in keeping the surrounding space warm, cool, and dry; and cost-effective maintenance with minimal environmental impact.
• Carpet is a product designed specifically to enhance the quality of life indoors. From an environmental science
perspective, the desirable aspects of carpet are based on the fact that carpet is an energy absorber with a strong tendency to adsorb matter. Because of these properties, carpet is acknowledged in many health-related documents as having desirable attributes for sensitive environments.
• As with any high-volume-use indoor product, when carpet is reasonably maintained, it poses no adverse exposures or health effects. When installed and maintained as intended, carpet is not a risk to public health. When examined in proportion to its use, carpet is associated with minimal complaints, consumer dissatisfaction or concern. Research going back over 40 years consistently shows that carpet is a preferred and widely used floor covering associated with long-term consumer satisfaction. In the United
States alone, there are approximately 150 billion square feet of carpet currently installed in over 100 million buildings. A large proportion of the developed world's population is exposed to carpet, and so it is remarkable and significant that this review found no epidemiological or toxicological studies presenting clear or direct evidence that exposure to carpet in any environment causes an adverse human health response. Furthermore, where controlled studies have been conducted in relation to carpet chemical emissions and animal and human response, no adverse response was found to have occurred.
• Carpet does not emit concentrations of VOCs that present a real risk. Carpet entraps particulates and removes them from the indoor environment. When weighing the different factors in
making a flooring selection, health effects, if considered at all with regard to carpet, should be considered in a positive rather than negative context.
• The most controversial aspect of the impact of carpeting on air quality is the perception of indoor air quality in buildings containing carpeting. Only recently have scientists attempted to quantify this effect of carpeting, despite the fact that odor perception studies have been undertaken, primarily in occupational settings, for over 30 years. In the current review of the literature, the “perception” of the quality of air indoors may be the parameter most closely associated with non-quantified or non-quantifiable health effects including sick building syndrome and multiple chemical sensitivity.
• The review indicated that there are a vast number of studies that describe, measure, and address particles, dusts,
allergens, and other contaminants of all types in carpet and other indoor surfaces. In these studies, no source and exposure relationships were established between contaminant accumulations in carpet and airborne concentrations of particles and dusts. This is consistent with the lack of finding a direct link between carpet and human health effects. This is a fundamental risk assessment finding that has significant non-exposure implications. Human response cannot occur unless there is exposure and sufficient dose delivered to the human receptor.
• Wet, dirty carpet will support microbial growth. However, less is known by way of the literature about human exposure and response to this microbial growth - other than symptoms tend to diminish with drying and cleaning of these spaces. Studies of damp or water-damaged environ-
ments tend not to consider or sort out the specific roles of the various building materials.
• Recommendations to remove carpet to reduce or prevent allergic responses have not been based on studies showing a relation of carpet to allergic reaction. This review failed to find any study or benefit analysis of carpet removal from sensitive environments. If carpet alone was removed from environments for the purpose of preventing or reducing allergic response, there is no evidence in the literature that allergic conditions or response improved. A recent allergy conference held at the Royal Society of Edinburgh supports the above finding: “In the past 10 years there has been a generalized trend for the removal of carpet in home and public places. This has been widely recommended and has occurred despite the absence
of studies demonstrating beneficial effects of isolated removal. Indeed, in Sweden between 1973 and 1990 there has been a 3-fold increase in asthma and allergy despite an 80% decline in carpeting and substitution and laminate flooring.” (Devereux, 2003, pg 402).
X In sensitive environments like hospitals that have been studied for nearly 40 years in relation to carpet, there is no indication that carpets contribute to the spread of disease. A recent CDC expert workgroup concluded: “Broad recommendations against the use of carpets in immuno-compromised patient care areas have been removed from this Guideline, since there is no epidemiological evidence to show that carpets influence the nosocomial rate
in hospitals.”
X Little published research is available on the presence of microorganisms in carpet. Although some studies have compared the presence of microorganisms in rooms with carpet and those in rooms without carpet, much of the reported research provides information on air quality. Most carpet today that is used in commercial settings is produced from synthetic materials including nylon, polypropylene, polyester and SBR, which do not inherently provide the nutrients required to support microorganism growth. In addition, these products have low moisture regain, and therefore, excess moisture is not present in the components of modern-day soft floor coverings.
X The interaction of carpet types
with vacuum cleaners and dust loading suggests that systems understand the impact of carpet and carpet cleaning activities on the quality of indoor environments. These studies point to the fact that there are scientific principles behind effective carpet cleaning and that carpet cleaning is an integral part of the overall environmental strategy necessary to keep indoor environments (environments where people spend the vast majority of their time) inviting, comfortable, productive and safe. An effective cleaning program must emphasize (tested) technology directed at maximum extraction, minimum residue, safety, and ease of use; a cost-effective cleaning strategy plan and schedule; training and recognition of cleaning technicians; and periodic
inspection, assessment and management review of cleaning programs.
X Every high-use building requires cleaning as intense and frequent as any high-use office complex. With regards to the proper maintenance of floor surfaces, Building Owners and Managers Association (BOMA) published statistics showing that cleaning cost is reduced in relation to carpet environments. BOMA estimated maintenance in carpet environments to cost $0.64 per square foot of flooring as compared to $1.24 per square foot for VCT. An independent cost analysis done as part of this assessment came to same general conclusion ($1.38 per square foot for VCT and $0.83 per square foot in a 12-month school year operation.) In addition, there are a number of hidden costs and environmental lifecycle considerations including water use, chem-
ical use, residue disposal, and storage and labor stress, which are all considerably higher for hard floor maintenance than for carpet maintenance.
X The review established that clean carpet poses no risk to public health. The amount of matter in any environmental compartment, such as dust in carpet, is referred to as “loading.” Field data suggests that carpet with a loading of less that 1 gm/m 2 is for all practical purposes “sanitary.” However, carpet with loading greater than 2 gm/m2 is more likely to release matter to the surrounding environment, elevating exposure and risk. Kinetic modeling suggests that IAQ is most influenced by ventilation and cleaning practices. Models and first-order relationships suggest that carpet has the physical potential to negatively influence IAQ when carpet is heavily loaded with
matter. Tracking, not air deposition, is the primary means of loading carpet. Heavily loaded carpet has the potential to influence IAQ more than other elevated surfaces indoors because of the large amount of matter carpet is capable of holding, a small portion of which is eventually transferred to air. Modeling suggest that so long as that matter deposited in carpet is not excessive or is managed, through walkoff mats, vacuuming, and extraction carpet cleaning, IAQ is not adversely affected.
Devereux, Graham, et al. “The increase in allergic disease: environment and susceptibility.” Proceedings of a Symposium held at the Royal Society of Edinburg, 4th June 2002. Clinical Experimental Allergy 2003: 394-406, 2002.
Some advice for making the best use of these machines and the latest innovations in sweeper’s engineering
Maurizio Pedrini
Road sweepers, versatile, easy to handle, increasingly sustainable from an environmental point of view: let's get to know them better, also taking care of their maintenance and looking towards the present and the immediate future, which sees manufacturers particularly committed to facing the challenges of saving energy and water, in the name of maximum environmental sustainability. We can divide the macro sector of street sweepers into two large families: standard sweepers, in which the brush pushes the waste towards the appropriate container; suction sweepers, or vacuum sweepers, in which the brush pushes the waste which is then sucked up.
Electric or with a combustion engine: how to choose?
Walk-behind and ride-on sweepers can be equipped with a battery-powered electric motor or a combustion engine. The electric models, being powered by a battery, have a reduced autonomy, which varies depending on the battery. When choosing the machine, this characteristic of electric models must be taken into proper consideration because the sweeper must be able to clean a given surface with a single charging cycle. Conversely, combustion engines guarantee greater autonomy but since they produce exhaust gasses they are used exclusively in sweepers used for cleaning operations to be carried out in outdoor environments. When choosing which sweeper to buy, you will first need to take into consideration the type of surface to be cleaned and its specific characteristics. For an optimal choice of the best machine to use in cleaning operations, two particularly important parameters must be taken into account: X the working width, which generally depends on the size of the machine and corresponds to the width that the machine cleans as it advances; X the hourly yield in square meters,
which depends on the relationship between working width and speed of advancement and which corresponds to the area that the machine can theoretically sweep in one hour.
The hourly output, together with the autonomy of the machine, will in turn allow you to determine the area that the sweeper is able to clean with a single charging cycle as well as the time necessary to carry out the operation. Another parameter to take into account is the type of engine, which can be electric or combustion. The use of combustion engines is reserved for outdoor cleaning operations, due to potentially harmful emissions.
Any sweeper can function more or less correctly based on a fundamental factor: correct maintenance, which must be carried out with the utmost care after each use. Like all other cleaning machines, sweepers also require essential maintenance to be carried out after each use. Periodically the filter needs to be cleaned and a quick visual check of the brushes is necessary. Daily maintenance of the sweeper is also important, perhaps by checking the manual provided by the manufacturer to better understand, in detail, the methods of operations to be carried out. Periodic maintenance of the machine is also highly recommended, having an authorized technician carry out a check at least once a year or after two hundred and fifty hours of operation. All with two fundamental objectives: improving performance and maximizing the life and use of the sweeper. The role of the technician is fundamental, in fact he will be able to best advise on various issues, for example on the importance of using original spare parts to replace the sweeper's consumables. The latter, in fact, integrate best with the sweeper, meeting the minimum quality standards and satisfying all the
European regulations regarding safety and the environment.
A few simple precautions can prove to be truly invaluable in avoiding the onset of problems when using the sweeper: first of all, do not work in outdoor environments where there are residues such as ropes, strings, nylon packaging large enough to wrap the central brush, causing it to progressively stop. You must always remember to vacuum when working on damp surfaces, so as not to damage the filter. Faced with the most frequent problems, a series of questions must be asked. For example: if the sweeper does not work and does not turn on, if the sweeper is battery-powered, it is necessary to check that the battery connector is connected to the sweeper system, also making sure that the batteries are charged. However, if the sweeper is powered by a motor, you must check that the starting battery is charged and connected to the machine's system. It is also essential to check that there is fuel in the engine tank or in the cylinder, based on the type of fuel supply of the machine. It doesn't hurt to check the fuel filters either, making sure they are not clogged.
Another useful suggestion concerns a possible scenario: inadequate working autonomy of the machine. As we well know, sweepers are chosen precisely because they allow large spaces to be cleaned very quickly. Therefore, if the autonomy of a battery-powered sweeper is very low, the causes of the problem must be promptly identified by carrying out the following steps:
X check that the charge level is sufficient;
X check that the batteries are also connected correctly and that the battery connector is connected to the electrical system connector;
X make sure that the battery poles and
terminals are not oxidized or dirty. If this is the case, it is best to contact a technician;
X always check the condition of the batteries, remembering that the older the batteries, the less they hold a charge.
Some simple tips to keep in mind in case the sweeper does not clean well are:
X check the adjustment of the central brush;
X check the state of wear of the brushes: if they are too worn, the cleaning performance of the sweeper is progressively reduced and, in the most serious cases, they can ruin the floor;
X check that the type of brush is suitable for the type of flooring and the dirt to be cleaned. In fact, there are special brushes with soft, or medium, hard, mixed bristles and with steel wires for more resistant dirt. The thicker bristles are more resistant and therefore should be used on surfaces with solid or heavy dirt (gravel, cans, etc.). On surfaces with light dirt or dust it is better to use softer bristles;
X check the condition of the filter which, if clogged, must be cleaned. However, if the sweeper is equipped with an electric filter shaker, it is necessary to check its correct functioning;
X check the collection box. If it is full, it must be emptied promptly.
A machine at the service of safety
We can legitimately say, without fear of contradiction, that the street sweeper performs multiple and important tasks to protect our safety. We mention just a few of the most important ones: it removes dirt avoiding slipping, allows better visibility of horizontal signs, reduces the sources of pollution present in the air (vehicle dust, rubber dust, tar, etc.) destined to end up in our lungs or wastewater. In short, cleaning and sanitizing floors with professional equipment, which filters the air sucked in before releasing it back into
the environment, improves the quality of the air we breathe. The sweeper also has the ability to remove loose, non-adherent dirt (stones, small solid debris, leaves and more or less fine dust), thanks to the mechanical action of the brushes, without the use of liquid detergent solutions.
cleaning and innovation 4.0
Today, more than ever, manufacturers of street sweepers are called upon to face great challenges regarding the equipment of the machines, starting with the use of intelligent systems that allow remote interaction in a bidirectional manner with the vehicle used in cleaning operations. Programs which, by exploiting geolocation and artificial intelligence, allow you to control the machine at any time, being informed directly by it about its state of health, the presence of any anomalies and therefore managing to intervene promptly with remote assistance, avoiding machine downtime or costly maintenance interventions. In the process of digitizing information, the new applications allow the use of automotive tools which, by saving energy and optimizing intervention times for scheduled or accidental maintenance, definitely aim at optimal use of the sweeper. Manufacturers are also committed to speeding up extraction
activities and ergonomics, to ensure less fatigue for the operator, without neglecting the effectiveness of the results. But it is on the dust filtration front, guaranteeing the total reduction of PM10 and other microparticles present in the air that many producers are working. Currently, these sophisticated control systems enable, especially the most powerful and robust machines with man on board, to reduce water consumption to the bare minimum - by resorting to recycling - or completely eliminate - by operating dry.
Without forgetting the creation of applications that have the task of measuring the data relating to CO2 production in real time, thus allowing us to intervene with actions aimed at their reduction. And finally, precisely in this regard, how can we not talk about HEPA filters, that is, that particular high-efficiency filtration system, now universally adopted by manufacturers also for street sweepers, recognized as a standard by the European Union which today allows an extraordinary filtration efficiency, capable of capturing microparticles up to 0.3 microns thick. Here are some of the many reasons why, ultimately, it is right to recognize the street sweeper's leading role in the context of mechanized cleaning, in the ambitious goal of creating a better future for our planet.
In the competitive world of professional cleaning, choosing the right machines can make the difference between a mediocre service and an exceptional one. not only to ensure superior performance but also to optimise management and reduce operational costs.
nowned for their robustness and reliability. Each sweeper
is equipped with design features that make them easy to manage and maintain, minimising post-sale issues. This not only improves the satisfaction of the end customer but also allows dealers to focus on growing their business rather than on technical problems.
Thanks to the quality of the materials and precision engineering, MP-HT sweepers are built to last. This represents a significant advantage for rental companies
as well, which can benefit from robust machines that reinforce customer confidence in the service offered.
With MP-HT, dealers find a partner offering not only high-quality products but also continuous innovation. The acronym E4H, present in the new sweepers, is the manifesto of a new design approach where technology generates solutions that simplify work and improve operator well-being.
Dulevo is a leader in street, industrial and commercial sweepers, thanks to a range of machines designed to meet any need. Robust, easy to use and maintain, Dulevo sweepers are ideal for the harshest environments, guaranteeing high performance and a positive impact on the environment, thanks to their durability and repairability.
Dulevo sweepers are capable of tackling the most demanding jobs thanks to powerful motors and advanced sweeping systems. These features allow them to pick up even the heaviest
and bulkiest debris, ensuring deep and fast cleaning, even on large surfaces or in particularly heavy-duty industrial settings. Durable materials and the ability to operate in tough conditions make Dulevo sweepers ideal for the most extreme environments. At the same time, the high filtration capacity provided by bag filters allows them to retain even the finest dust and minimize particulate matter released into the air.
Dulevo sweepers are designed to be intuitive and easy to use. Ergonomic controls
allow operators to get the most out of them with minimal training. Maintenance is also simple with easy access to key components, which reduces downtime and operating costs. This aspect makes the sweepers not only cost-effective but also sustainable, as it optimizes the use of resources and reduces the interventions needed. In fact, Dulevo sweepers are built to last, with durable materials that ensure their long operating life even in harsh conditions. This feature not only reduces operating costs but also limits the need for new production, reducing environmental impact. The repairability of the machines allows targeted and rapid in-
terventions, avoiding total replacement and extending the product life cycle, in line with circular economy principles.
The legendary Dulevo 120 is an example of ruggedness and reliability that lasts. On the market for more than 40 years, this model continues to be in demand because of its long-lasting and easyto-repair features. The Dulevo 120 represents a perfect blend of tradition and innovation, updated to meet modern needs but maintaining the same build quality that has made it a classic.
In addition to classic models, Dulevo is constantly working to innovate the cleaning market. With Kronos, the new industrial sweeper concept, Dulevo outlines its future in the industry with a focus on sustainability, efficiency and cutting-edge technology. Equipped with advanced features such as an ergonomic cockpit, a high-tech dashboard and the possibility of autonomous driving, Kronos represents the perfect synthesis of operational efficiency and environmental friendliness.
In an industry as competitive as cleaning, standing out from the competition is not always easy. Often, price becomes the sole consideration for customers, neglecting a far more important factor: professionalism and experience
Niccolò Luongo Marketing specialist
Professionalism and experience are two intangibles that represent the true added value of a cleaning company and are the key to retaining customers and winning new ones. In this article, we will look
at how to emphasize professionalism and experience in your brand, stressing the importance of communication, training, certifications, and a team of qualified employees. In addition, we will provide some tips to improve your
brand positioning in the market. Communication is the first tool a business uses to connect with the public. For this reason, it is essential to use professional and confident language that conveys competence and reliability. This means using precise and concise vocabulary, avoiding ambiguous or slang terms that could confuse the customer. In addition, it is important to adopt a courteous and respectful tone of voice, demonstrating attention to the client's needs and placing oneself in a position of active listening.
Professionalism manifests itself in every aspect of a cleaning company's work, from the first contact with the client to the delivery of the finished service. Investing in professionalism and experience means making a for-
ward-looking choice that brings added value to the cleaning company. A solid and recognizable brand allows you to retain customers, win new contracts and establish yourself as an industry leader. In an ever-changing market, professionalism and experience are the key to success and lasting growth. A professional enterprise is distinguished by:
- Expertise: in-depth knowledge of cleaning techniques and products used to ensure flawless and safe service.
- Reliability: punctuality in service execution, adherence to agreed timelines, and ability to handle unforeseen events.
- Efficiency: optimization of time and resources to ensure prompt and quality service.
- Courtesy: positive and proactive attitude toward customers, ensuring a pleasant and reassuring experience.
Experience is an invaluable asset that only time can build. An experienced cleaning company has accumulated a wealth of knowledge and expertise that enables it to meet any kind of challenge, ensuring excellent results in any situation. It results in:
- problem solving skills: Rapid and effective identification of problems and implementation of appropriate solutions.
- Flexibility: adaptability to different needs and contexts, ensuring personalized service for each client.
- Industry knowledge: keeping up to date with the latest innovations and trends in the cleaning industry to provide state-of-the-art service.
In order to offer high quality service, it is essential to invest in the ongoing training of the staff. A company that places training at the center of its development demonstrates a concrete commitment to professionalism and excellence. Moreover, certifications are a tangible
guarantee of the company's professionalism, demonstrating adherence to rigorous and nationally and internationally recognized quality standards. This kind of recognition increases the company's credibility in the eyes of clients, who can thus rely with confidence on impeccable and safe service. But the most valuable resource is qualified employees. The staff represents the soul of a cleaning company. For this reason, it is essential to invest in the selection and development of its employees, creating a positive and motivating work environment. Hiring qualified and trained staff means not only ensuring high quality service, but also creating a cohesive and close-knit team capable of efficiently and professionally meeting any challenge. Competent professionals who possess the knowledge and skills necessary to do their jobs flawlessly. Motivated people, passionate about their work and eager to provide excellent service. Collaborative professionals, able to work in synergy to achieve common goals.
To emphasize the professionalism and expertise of one's cleaning company brand, it is essential to implement a 360-degree communication strategy that includes:
- A professional website, offering a clear presentation of the company, services offered and company values.
- An active social media presence to interact with customers, promote their businesses, and build a strong online reputation.
- Targeted marketing campaigns to reach the target audience and communicate the company's strengths.
- Participation in trade fairs and industry events to make themselves known and make contacts with potential customers and partners.
In conclusion, emphasizing professionalism and experience is an ongoing process that requires commitment, dedication, and focused investment. However, the end result is more than rewarding: a solid brand that is recognized and appreciated for its excellence in the cleaning industry. Professionalism is reflected in every aspect of a business, from communication to customer service. Continuing education is an essential investment in a company's future. A team of qualified employees is the strength of one's brand. A targeted marketing strategy allows you to reach new customers and increase the visibility of your brand. If you focus on these key points you will be well on your way to building a successful brand in the cleaning industry.
As part of the European Green Deal and the new action plan for the circular economy, one of the most important games is being played on reducing the environmental impacts of packaging. Regulatory interventions are and will all be oriented to reduce the amount of packaging and materials used, with the goal of ensuring that all packaging is reusable or recyclable
in an
economically
feasible
manner by 2030
Francesca De Vecchi food technologist
The Green deal is the European strategy to drastically reduce emissions so that Europe will be the first climate-neutral continent by 2050, with at least 55 percent fewer greenhouse gas emissions by 2030 than 1990 levels. In 2050, therefore, no more net greenhouse gas emissions are to be generated and economic growth is to be decoupled from resource use. Interventions will affect both productive sectors and the actions of individual citizens, who, after all, are demonstrating that they are particularly sensitive to the issue of sustainability. One of the most important games is now being played on reducing the en-
vironmental impacts of packaging. The new rules, approved on April 24, on packaging and packaging waste take action on a strategic and vital sector, from an economic point of view. In 2018 in the EU, packaging generated a turnover of 355 billion euros. A significant turnover but also a steadily increasing source of waste, with the EU total rising from 66 million tons in 2009 to 84 million tons in 2021 (EU source). Each European generated 188.7 kg of packaging waste in 2021, a figure that without further measures could rise to 209 kg in 2030 (chart 1). A trend that needs to be stopped and if possible reversed. In terms of envi-
ronmental impact, in fact, regulatory interventions are and will all be geared toward reducing the amount of packaging and materials used. In fact, as part of the European Green Deal and the new Circular Economy Action Plan, in November 2022 the European Commission unveiled a revision of the Plastic Packaging Waste Reduction (PPWD) Directive, with the goal of ensuring that all packaging is reusable or recyclable in an economically feasible manner by 2030, strengthening its requirements, including recycled material content. Europe claims to be acting proactively not only in the interest of citizens but also driven and supported by the
real interest citizens show in the issue, about which, however, they have, according to recent research, approximate knowledge.
In this large category, food packaging serves special functions: it protects against mechanical damage, light or water vapor, thus maintaining food safety and food quality throughout the supply chain. However, the material, shape and design can vary greatly, which therefore also differentiates the environmental impact of each packaging.
A 2021 study (S. Otto et. al) published in the Journal of Cleaner Production pointed out that consumers tended to judge packaging material by circular economy criteria, by more or less natural appearance, and by design. While consumers' knowledge of paper/ cardboard and metal impacts was in line with available scientific data, the impacts of plastic packaging tended to be underestimated, and those of glass and biodegradable plastics greatly overestimated. European consumers' evaluations and scientific life-cycle as-
sessments actually differed, especially when going into the details of concepts such as recyclability, biodegradability, and rate of packaging reuse, resulting in purchasing behavior, for environmental impact purposes, that was far less sustainable than was desirable. Despite the lack of scientific knowledge of the phenomenon, it should be noted how much attention to the topic has grown year by year, as noted by several analyses. The FMCG Packaging Observatory, curated by Nomisma and presented during Cibus 2024 (Parma, May 7-10), highlighted how citizens are particularly interested in the sustainability of food packaging, especially when the issue crosses with that of health and nutrition (see box).
“All industry sectors, EU countries and consumers must play their part in the fight against over-packaging,” said Frédérique Ries (Renew, BE Ries), the rapporteur of the new European Packaging and Packaging Waste Regulation
(PPWP) voted on April 24, which aims to combat ever-increasing packaging waste, harmonize internal market rules and promote the circular economy.
“For the first time in an environmental law, the EU is setting targets to reduce packaging, regardless of the material used,” Ries said. The text, accepted by the EU Parliament with 476 votes in favor, 129 against and 24 abstentions, will enter into force following Council ratification. Long debated, it is the result of many adjustments, which had to take into account different demands and interests, with one of the sectors concerned, the plastics industry, ultimately only partially satisfied.
“The new rules promote innovation and provide exemptions for micro-businesses; the ban on the use of non-degradable chemicals (so-called forever chemicals, ed.) in food packaging is a major victory for the health of European consumers.”
As also written in the conclusions of the Future of Europe Conference with the adoption of this legislation, the
intent of the Parliament is to meet the expectations of citizens to build a circular economy, avoid waste, phase out unsustainable packaging, and address the use of single-use plastic packaging.
The main points of the Regulations
The legislature pointed in the direction of a net reduction in packaging; from a safety perspective, it set a limit on PFAS (perfluoroalkyl and polyfluoroalkyl contaminants) content in food-contact packaging (MOCA); set targets for reuse of certain types of packaging-including the use of customer-brought packaging for takeaway; introduced a recyclability requirement for all packaging (with some exceptions); and some minimum recycled content targets.
Reducing production and limit some types of packaging
Under the rules provisionally agreed with the Council, packaging reduc-
tion targets aim for 5 percent by 2030, 10 percent by 2035, and 15 percent by 2040; EU countries will have to reduce, in particular, the amount of plastic packaging waste. To decrease unneeded packaging, a maximum empty space ratio of 50 percent for mixed, transport, and e-commerce packaging is envisaged. Manufacturers and importers will also have to ensure that the weight and volume of packaging is kept to a minimum.
Certain types of single-use plastic packaging will be banned starting on January 1st 2030. These include those for fresh unprocessed fruits and vegetables, packaging for food and beverages filled and consumed in bars and restaurants, single servings (e.g., condiments, sauces, cream, sugar), packaging for toiletries, and very light plastic bags (below 15 microns).
Reuse and refill for consumers
Specific reuse targets (40 percent by 2030 and 70 percent by 2040) are set for alcoholic and non-alcoholic bever-
age packaging (with the exception of milk, wine, flavored wine, and spirits whose reuse target in 2030 is set at 10 percent and 40 percent in 2040), transport and sales packaging, and multiple packaging. Five-year exemptions are provided but only under certain conditions.
End distributors of take-out food and beverages will have to offer consumers the option of bringing their own container. They will also be required to commit to offering 10 percent of products in a reusable packaging format by 2030. Excluded from these reuse targets is flexible packaging in contact with food, feed and food ingredients.
Recyclability and improved waste collection and recycling
Under the new standards, all packaging (except light wood, cork, fabric, rubber, ceramic, porcelain and wax) will have to be recyclable according to strict criteria. There are also minimum recycled content targets for plastic packaging and minimum recycling targets by weight for packaging waste.
By 2029, 90 percent of single-use plastic and metal beverage containers (up to three liters) will have to be collected separately (through deposit-return systems - DRS - or other solutions that ensure the collection target is met).
Packaging design and reuse of recycled
By 2030, recyclable packaging must be specifically designed to be sent for recycling, sorted according to pathways that do not impair the recyclability of other waste, and so that secondary raw materials obtained from the recycling process can be used instead of primary raw materials.
From 2030, plastic packaging must contain a minimum amount of recyclables calculated by weight. In the intentions of the European institutions, it should help “set standards concerning the entire life cycle
of packaging that contribute to the efficient functioning of the internal market, harmonizing national regulations while preventing and reducing the negative effects of packaging and
packaging waste on the environment and human health. By establishing measures in line with the waste hierarchy, it should contribute to the transition to a circular economy.” It cer-
tainly has the potential to reshape the entire packaging industry over the next 20 years, shifting balances between packaging materials and their respective supply chains.
EU packaging waste generated, recovered and recycled, 2010-2021 (kg/ per capita) (Eurostat, 2023)
According to the survey of the FMCG Packaging Observatory, curated by Nomisma, 88 percent of the surveyed sample, Nomisma says, have adopted savings strategies to counter rising food and beverage prices; in Italy, country surveyed by this study, purchasing choices are being made with an eye to moderation, given the general rise in food prices, but with an eye to sustainability.
“Sustainability,” comments Emanuele Di Faustino, Head of Industry, Retail & Services at Nomisma, ”remains at the center of everyday actions: for 62% it is in fact a fundamental element to be evaluated in purchasing choices, while for almost 1 consumer out of 3 it directly affects spending behavior. In this scenario, packaging undoubtedly plays a leading role: for 2 out of 3 consumers, packaging in fact plays a decisive role in their food
and beverage purchasing choices, while for 1 out of 2 it represents a crucial aspect in helping to make a food product more environmentally friendly. And in fact, the features most sought after by consumers who want sustainable packaging are: no over-pack, fully recyclable and biodegradable packaging.”
But what does sustainable packaging look like for consumers? What characteristics does it need to have? For almost half of the respondents (45%), excess in packaging is a negative feature. This is followed by the recyclability of the packaging (43%). 38% like compostable/biodegradable packaging or packaging with recycled material (35%). Plasticfree packaging is preferred by 29% of the sample while interest emerges in packaging that may be
reusable several times or produced with responsible use of resources. Packaging, therefore, can also communicate values. In foods with a strong nutritional added value-healthy foods, i.e., those foods and beverages to which consumers recognize beneficial effects on a person's health and physical and mental well-being, vegan and vegetarian foods or fortified foods, or free-from foods - the packaging features capable of capturing consumers' attention concern for a good part the environmental sustainability of the packaging and the materials from which it is made (together, of course, with the presence of certifications attesting to the 100% plant-based origin of the ingredients, nutritional information, and the presence of images that recall the veg world).
Paper and paperboard sector suffers from falling demand in Europe, reduced inventories and high production costs
edited by Cristina Cardinali
Suffering from an unfavorable macroeconomic environment, paper and pulp production in Europe declined in 2023. This is due to several external factors combined: an unfavorable economic environment, reduced inventories, and still high energy costs, as shown by preliminary Cepi data.
As medium-term global economic trends impacted demand for paper and paperboard and exacerbated the reduction in inventories, consumption fell by 15.3 percent in 2023, and in turn, production in the paper and paperboard sector suffered a second consecutive year of contraction, falling by 12.8 percent. After a 2022 marked by skyrocketing energy prices, the decline in production in 2023 continues to be more pronounced even than during the Covid-19 crisis period (-4.7 percent in 2020).
These global trends have been exacerbated by comparatively high costs
in Europe for production inputs, particularly energy, the cost of which continues to be unsustainably high. This is illustrated by the fact that domestic paper and paperboard production in Europe has contracted more than in many other regions of the world, where declines have ranged from -2% to -10%.
But, in a globalized context of low demand, both imports and exports have declined equally, and the European pulp and paper trade balance remains far and away positive, since by this yardstick it is one of the EU's leading manufacturing sectors.
Traditionally the industry's growth engine, the production of paper and paperboard packaging in Europe also continued its downward trend. The segment suffered from a slowdown in retail and e-commerce figures, having returned from pandemic levels. This in turn had an impact on the consumption of paper for recycling (-7.3 percent), as paper-based packaging in
Europe is predominantly made of recycled material.
Much more stable appeared to be sanitary and household paper compared to the other segments, with a moderate decline at -3.7 percent. These are still benefiting from favorable social trends in hygiene products, with the “household” markets, including tissues and toilet paper, performing better than the “away-from-home” markets, which are more affected by inflation and stagnant private consumption. Finally, pulp production in Europe also declined less rapidly than overall paper production, by 7.5 percent. The decrease in production of this “processed wood,” which is the primary raw material for paper and paperboard production, can be attributed to a large number of closures of graphic paper mills that also produced pulp. Pulp production for the market grew by 4.8 percent in 2023 as capacities went to full capacity and benefited from strong demand from China.
The European association representing the paper industry (Cepi) is a nonprofit organization. Cepi is led by Director General Jori Ringman with a staff of 21, based in Brussels. It has four standing committees, which adopt long-term strategic perspectives on issues affecting the industry. These are
At its last meeting before the European elections, the European Competitiveness Council presented what could be seen as guidelines for the future Commission on how to prevent Europe from falling into an industrial crisis. Safeguard the competitiveness of EU industry while staying on track to achieve the goal of zero net emissions.
The plan includes support for industries that have already taken the path of increasing circularity, embraced the bioeconomy, and decoupled growth from resource use.
The document sets out the vision of a competitive European industry serv-
the Environment and Safety, Climate Change and Energy, Forestry and Recycling committees.
The Association Directors Group (ADG) is the senior advisory group to the Director General of Cepi and is composed of the Directors General of the National Associations.
Cepi is managed by a 33-person Board, and is composed of representatives of the National Associations and the CEOs. The Council is currently chaired by Marco Eikelenboom, CEO of Sappi
ing a green, digital and resilient economy. To meet Europe's climate goals without compromising the industrial backbone of its economy, the Council insists on the need to “create favorable conditions for demand for sustainable products, [...] and circular products and materials,” a central demand of Europe's forest-based industries, often competing with a heavily subsidized fossil-based sector. The Council lists the bioeconomy as a priority and asks the Commission to update the European plan to the strategy in this area by the end of 2025.
Managing resources so that they can be constantly renewed is also central
Europe. It approves Cepi's policies, strategies, and goals, as well as the business plan and budget proposed by the Board.
The Steering Committee, consisting of two ADG members and four board members, provides a formal link between the committees and the board, guiding policy areas.
The CEO of Cepi ensures that Cepi's actions conform to the decisions of the Board and that policies are consistent among the committees.
to the EU forestry plan as a business model for the sector. The bio-based circular industries demonstrated a high level of resilience during the Covid crisis, with the advantage of being able to rely on local resources. For the pulp and paper industry, which together with the forestry sector have already called for European legislation to take into account the environmental and social aspects and benefits of renewable resources, the next five years could be a positive turning point, a recognition of their potentially transformative role within the broader European industrial sector.
The pulp and paper manufacturing industry requires significant energy and raw materials, accompanied by substantial capital expenditures and lengthy investment periods. However, it boasts a strong history of resource efficiency and innovation
Leveraging its expertise in wood fiber, the pulp and paper industry is leading the way in the creation of both innovative and traditional products. It stands as a trailblazer in transforming the EU's lowcarbon bioeconomy into a tangible industrial reality. Pulp and paper industry is relevant in many ways: in Europe, it employs around 647,000 workers in 21,000 companies. Due to enhanced process efficiency, the industry has achieved greater energy self-sufficiency and reduced CO2 intensity by producing over fifty percent of its primary energy
from biomass. In fact, the advanced expertise, coupled with ongoing research and innovation, enables these industries to leverage new business models, create cuttingedge products and technologies, and advance towards a low-carbon bioeconomy.
Main challenges for the sector Energy prices: the advanced expertise, coupled with ongoing research and innovation, enables these industries to leverage new business models, create cuttingedge products and technologies, and advance towards a low-carbon bioeconomy.
Raw material supply: the demand for domestic wood supplies within the EU is growing among end-users, including bioenergy companies. To align wood supply with demand, it's essential to sustainably increase wood mobilization and explore
edited by Giacomo Torrenzi
innovative methods to enhance the added value of raw materials through the cascading use of wood. Recycling: the paper recycling rate in Europe is nearing its peak. Enhancements in separate collection systems and advancements in sorting and recycling technologies could further improve the quality and accessibility of secondary raw materials. However, the supply might face challenges due to the rising volume of recovered paper exports to countries outside the EU. Lower consumption: the consumption of graphic paper in Europe continues to decline as a result of digitalization. However, this trend is offset by an increase in the demand for packaging and hygiene papers. Additionally, the development of innovative biobased products presents significant opportunities for the industry. Trade barriers: the sector is expanding its export share beyond the EU; however, tariff barriers and protectionist subsidies for competing products result in an uneven competitive landscape. Additionally, taxes and export duties levied by non-EU countries on wood exports are a cause for concern. For instance, fiber as a raw material constitutes the largest portion of production costs, making its availability at reasonable prices vital for the sector's success.
Source: https://single-marketeconomy.ec.europa.eu/sectors/ raw-materials/related-industries/ forest-based-industries/pulp-andpaper-industry_en
For 14 years EcoNatural has been synonymous with sustainable innovation. A project born from advanced technology that transforms what is no longer needed into a resource, recycling all the components of beverage cartons thanks to a production process that is unique in the sector. Beverage cartons are an essential part of our daily lives. They are composed of cellulose fibres, polyethylene and aluminium and, if correctly sorted, can be recycled through a specific process.
Thanks to Lucart’s unique technology, the cellulose fibres are used to produce Fiberpack®, the raw material from which a complete range of toilet paper, towels, handkerchiefs, napkins and reels from the EcoNatural range is made.
The compound of polyethylene and aluminium, on the other hand, is used to produce Al.Pe®, which in turn is used to manufacture the dispensers, making it the only system able to offer a complete paper and dispenser solution made entirely from recycled food cartons.
EcoNatural products can also be proudly recognised as circular, sustainable and environmentally friendly thanks to their multiple certifications: all products in the range are EU Ecolabel certified, FSC® Recycled and, all products
manufactured at the Laval-sur-Vologne site are also Cradle to Cradle® certified. In addition, all EcoNatural toilet paper and towels, produced at the Laval-sur-Vologne and Diecimo plants, have obtained Product Climate Neutrality in accordance with the PAS 2060 standard , which means that all greenhouse gas emissions generated during the product’s life cycle over a given period have been reduced and offset to zero.
But Lucart’s journey towards concrete and complete sustainability is not limited to the product itself: where possible, standard packaging has also been replaced with recycled and compostable paper or recycled plastic packaging.
EcoNatural is the hygiene solution of the future, giving your customers the quality, and the planet the respect they deserve, that guarantees a tangible and measurable ecological solution: if we consider the tonnes of Fiberpack® paper produced, Lucart has contributed to the recovery of over 10.7 billion 1litre beverage cartons since 2013, avoiding the use of more than 4.6 million trees, for a surface equivalent to 15,800 football pitches and avoided CO2 emissions emitted into the atmosphere exceeding 281,300t, equal to the emissions of 2,165,749 journeys by car from Paris to Frankfurt am Main.
In 2024 Lucart Professional continues the innovation path and presents EcoNatural FLOW, the new unique range of dispensers in the EcoNatural line, made from beverage cartons, featuring a new exclusive and patented design with sinuous and elegant lines.
The range includes dispensers for auto-cut towels, for centre-feed toilet paper, for folded towels, for jumbo toilet paper, for bulk pack toilet paper and for refill soap, all available in black and white finish. All FLOW dispensers are fully recyclable and certified ReMade in Italy and TÜV OK Recyled. These certifications attest the traceability of production, starting from the verification of the source of input raw materials, to the finished product, representing a tool for transparency and simplification for Green Public Procurement and the private market.
EcoNatural is the system to turn something no longer needed into a resource and represents a virtuous system that reduces the burden of waste on the environment and that has allowed Lucart to become a true circular economy benchmark in Europe.
Usually intended for the sanitary, horeca and food industry markets, tissue paper should have certain properties that depend mainly on the type of fibers used and their processing
edited by Giacomo Torrenzi
The technological level of machinery and process used in the production of tissue papers has a great impact on the final quality of the product. There are five main and indispensable properties that a quality tissue paper must possess. Let’s see in detail what they are:
This important property is closely related to absorbency and softness, and is mainly determined by two factors: production technologies and the quality of the fibers used. In order to achieve high bulkiness at the production stage, state-of-the-art technologies can be used, such as the Through-Air Drying, or TAD, process in which the wet-pressing stage is minimized in favor of drying operations that take place in the dry section of the paper machine. In addition to production technology, other determinants of bulkiness are the use of lower pressure in the press nip, less intensive fiber refining, and paper creping. In order to achieve high bulk, it is recommended to prefer high-yield cellulosic pulps that are stiff
and less prone to collapse due to higher lignin content and lower porosity.
This is a fundamental property for any tissue product dedicated to liquid drying. The sheet must therefore possess both a high absorption rate, in order to effectively carry out its drying action, and a high retention capacity, in order to remove as much liquid as possible. Absorbency is given by the type of fiber used, the refining operations, the creping performed, the layers in the final product, and the additives used.
Tissue paper sheet, in its life cycle, is subjected to significant stresses during manufacturing operations, at the stage of converting reels into finished products, and, finally, during consumer use. Hence the need to obtain a sheet with an adequate level of strength, given by the combination of three factors: strength and fiber arrangement in the sheet; level of molecular bonding between the fibers themselves; presence of reinforcing additives.
This is a very important and sought-after requirement for consumers, especially with regard to products dedicated to the hygiene or personal care market. Moreover, the perception of softness depends not only on touch, but also on sound and visual perceptions such as color (the degree of whiteness) and noise upon tearing.
Some tissue products, such as kitchen paper, need to be strong even when wet, and this characteristic depends on the level of molecular bonding between the fibers of which they are composed. In order to maintain the wet strength of these products as much as possible, additives aimed at supplementing or replacing the hydrogen bonding of the fibers can be used. In this way it is possible for tissue paper to retain, when wet, up to 50 percent of its dry strength.
Source: www.acelli.it, 5 proprietà per una carta tissue soffice e voluminosa
ICA’s journey to success has been built one step at a time, starting from a small company, and developing an international attitude.
ICA has been founded in 1983 in a small town around Cuneo, in the north of Italy. Thanks to its vision and desire to pursue new ambitious goals, ICA grew from a small local paper converting factory and started exporting its products in Europe in the Nineties.
Even after consolidating its export network in Europe, the main goal was to keep growing. This is why in 1999 ICA moved its headquarters to Corneliano d’Alba: the larger spaces allowed to
upgrade the equipment and the company purchased a second production line. With new machinery, new opportunities opened in front of an ambitious company eager to improve itself. In the following years ICA worked to expand and consolidate its export network in the world, especially in Oceania where the Stella Products® brand, that was proudly created in Italy 25 years ago, arrives in Brisbane with a dedicated company.
The company is committed to constantly expanding its wide range of products in a perspective of constant innovation and focus on
the environment to offer products that are more and more performing, hygienic, and sustainable. Over the years, ICA has consolidated its production process by focusing on the pursuit of strict quality and sustainable standards. ICA’s desire to minimise its environmental impact, promoting responsible resource consumption and contributing to a better world by promoting the use of renewable sources and the safeguards of forests, led ICA to obtain PEFC and FSC certifications.
ICA presents the compact collection with dispensers: the ideal solution for washrooms where space is limited. ICA 2ply compact towel is soft, absorbent and above all practical with its 5 x 5 cm folds that make it the narrowest in its class. Its dispenser is only 8 cm deep so it is the ideal solution for bathrooms and work areas where space is limited and where the installation of a traditional dispenser would
undermine the functionality and liveability of the environment. The 5-fold design also promotes hygiene by offering a single sheet dispensing, where users only touch the sheet they take. Our two-ply pure pulp compact toilet paper is suitable for demanding high traffic washrooms. Its small core (only 2,5 cm diameter), its compactness and its double-capacity dispenser reduce run-outs and refills.
Industrial wastewater treatment is defined as an effluent that has been contaminated with organic and/or inorganic pollutants. Sewage treatment consists of a succession of several stages during which unwanted substances are removed from the wastewater, concentrating them in the form of sludge
edited by Giacomo Torrenzi
Industrial wastewaters are all those waters whose quality has been impaired by anthropogenic action after their use in industrial activities, thus becoming unfit for their direct use because they are contaminated with various types of organic and inorganic substances that are hazardous to public health and the natural environment. For this reason, they cannot be directly reintroduced into the environment because the final deliveries such as soil, sea, rivers and lakes are unable to receive an amount of pollutants that exceeds their self-purifying capacity without seeing the normal balance of the ecosystem compromised.
Wastewater from buildings or installations in which commercial activities or production of goods are carried out (including those subjected to prior purification treatment), are qualitatively different from domestic wastewater and stormwater runoff, meaning also those that have come into contact with substances or materials, including pollutants, not related to the activities carried out in the establishment; the
characteristics of such wastewater are variable according to the type of industrial activity.
For example, toxicity and significant organic components often characterize wastewater from the chemical industry, while paper industries use a significant amount of water, with often high values in terms of total suspended solids, Biochemical Oxygen Demand (BOD) and Chemical Oxygen Demand (COD).
Sewage treatment plants are facilities through which various water decontamination procedures take place. Wastewater purification takes place through various stages, during which toxic substances are removed from the liquid waste, turning it into sludge. The latter, not yet being completely free of harmful material, in turn undergoes other special treatments. Only at this point can the resulting sludge be disposed of in special landfills, or used in agriculture or taken to composting plants. Wastewater treat-
ment processes include:
X Screening: wastewater screening is one of the preliminary mechanical treatments to which wastewater is subjected at the inlet of treatment plants to remove and reduce suspended and floating materials. Screening is normally the first of these treatments, and its main purpose is to remove coarse bodies and objects. In particular, screening prevents damage to subsequent plant sections, such as pumps used to lift and move liquid, and reduces the accumulation of solids in pipes. The screened material is collected in a dumpster and then sent for final disposal.
X Grit removal: wastewater grit removal is one of the preliminary mechanical treatments to which wastewater is subjected at the inlet of treatment plants to remove and reduce suspended and floating materials. Desanding in particular is the removal of sands and inert solids, normally heavier and coarser than organics.
X Primary sedimentation: it takes place in tanks in which decantation is imple-
mented to separate sedimentable organics, achieving a reduction in BOD of around 30 percent. The tanks are equipped with automatic devices for sludge collection and evacuation.
X Secondary treatment: then the sewage, still turbid due to colloidal and putrescible suspensions undergoes secondary (oxidative or biological) treatment, in which the organics are first oxidized, that is, rendered imputrescible, and then removed. Several techniques are used for biological oxidation: percolating bed plants, consisting of filter beds on which saprophytic bacteria are present that degrade the organic substances present; or activated sludge plants, currently the most widely used technique because of its high efficiency. Activated sludge is a suspension in water of active biomass (saprophytic bacteria, protozoa, amoebae, rotifers and other microorganisms), usually in the form of flocs. In activated sludge biological treatment, a controlled aerobic dynamic system is
realized in the tanks, which reproduces in an artificial environment the same biological mechanisms that occur in nature for the purification of water polluted by biodegradable organic substances. In fact, by mixing a discharge to be purified with activated sludge in which there is a high concentration of preformed aerobic microbes, the same self-purification process occurs as in nature, but with an accelerated rate of reactions and less space occupied.
X Tertiary treatment: is applied to the effluent from secondary treatment, when the final discharge is to undergo further abatement of the pollutant load, which would otherwise be incompatible with the chosen final discharge; tertiary treatments can also be biological; the following are part of this stage: chemical-physical treatments (clariflocculation); mechanical treatments (filtration on activated carbon or on sand filters); biological-natural treatments (phytodepuration, lagooning; biological treatments (nitrifica-
tion, denitrification and defosphation); disinfection treatments. Disinfection is used to break down pathogenic bacteria in the purified effluent and can be accomplished by: chlorination; ozonation; actinization (which takes advantage of the bactericidal action of UV-C rays); and the use of peracetic acid (a powerful biocide that bases its action on altering cellular structures such as enzymes and membranes).
X Treatment of sewage sludge: the primary objective of sludge treatment is to stabilize organic matter so as to minimize the cost of its final disposal without creating problems for the environment. Sludge treatment processes are chemical, biological, and physical/thermal and can be divided into two broad categories: separation processes, which aim to remove part of the liquid fraction from the solid fraction of the sludge; and conversion processes, which aim to change the characteristics of the sludge to facilitate further treatment.
Emotional intelligence can provide a set of skills that can support us in understanding and managing ourselves and others, greatly increasing our interpersonal skills
It has always been thought that talking about intelligence means referring to our rational abilities. It is only in recent years, thanks to the scientific contributions of scholars such as Paul Ekman, or the outreach activities of networks such as Six Seconds and authors such as Daniel Goleman, that the idea that there may be an additional type of intelligence, emotional intelligence, has begun to gain ground.
Let's clear the air of a basic misunderstanding: using emotional intelligence does not mean being nice, kind, or empathetic. It means being able to use an essential part of human nature, namely emotions.
But, exactly what are emotions? Let's clear the air of another possible misunderstanding: emotions are not the little hearts and smiley faces we exchange via WhatsApp. They are much, much more.
We are emotional, thinking machines
Professor Paul Ekman defines an emotion as “a process, a particular kind of automatic evaluation influenced by our personal and evolutionary past, during which we feel that something important to our well-being is happening, while a series of psychological changes and emotional behaviors begin to interact with the situation.”
To better understand what Ekman says, let's take an example. You see a car about to hit you. You feel fear. Emotionally, it has been a process - that is, it has had a beginning and an end of which you are aware (a peculiarity that differentiates it from a state of mind)activated by a stimulus (which Ekman calls a “trigger,”) that has led you to react in order to preserve your safety by moving.
How much did you reflect in order to dodge the car? Simple, you did not reflect, but acted automatically with behavior functional to your survival, enacted through the emotion of fear. Instead, try to think of a case in which, out of fright, you became petrified. Have you ever been faced with danger? What did you think about while doing so? Again, nothing. It is obvious, you simply enacted-as in the first case-an automatic behavior, which for primitive man might have been functional to
defend himself from certain predators who saw only moving prey. Too bad a car is not a predator and doesn't care whether you move or not. Fortunately for you, the driver of the car saw you and, having been frightened in turn, by automatism activated a learned behavior, namely braking. All this always without any activation of our rational part, instinctively guided by emotions. Try now to think of another emotion, anger. When you get angry, your eyebrows lower and come together, your gaze becomes stinging, your lips show tension, your voice becomes more harsh and its volume higher. During the most violent outbursts of anger, you clench your fists and puff up your chest, and the main neurophysiological reaction causes blood flow to go up to your head, causing redness and sensations of heat, and into your arms, which become activated. These automatisms, fine-tuned by our evolution, enabled us to prepare for combat in order to survive. That is to say, you would behave this way if one of your kind wanted to take away the prey you just hunted with your spear in the middle of the forest, before re-entering your cave. Too bad you still behave this way today in many other situations. Do you want an example? How do you react when a supplier on the phone aloofly warns you that he will not deliver the material you have been waiting for so long for an important customer? Or when a smart-faced guy walks past you while you are patiently waiting in line for your turn to come?
Or again when you are self confident and insist on convincing someone, but that someone, in spite of your excellent arguments, will not be convinced? Different situations, different contexts, but - with different intensities depending on the situation - same automatic behavior. With a special feature: try to think of the very case in which you want to convince someone. Can you ever succeed in your intent if you get angry with him? Illogical, isn't it? Yet we do,
and the reason is inherent in the automatic behavior activated by the switch (trigger) that triggers the emotion: in the case of anger it is represented by an obstacle to the achievement of our goal. It applies to a prey in the forest, to a delayed supplier, to a disrespected queue, to someone who will not be persuaded: the emotion that is triggered is always the same and, consequently, the related automatic behavior.
In essence, emotions rule us in the same way they ruled Stone Age man and give rise to automatic behaviors that are functional to safeguard our survival and our essence as social beings. Unfortunately, these automatisms do not always turn out to be the most appropriate way to cope with every situation, because nature's intent was to make us quick to react at the expense of some possible error (the dysfunctional behaviors). The brain, whose main task is to keep us alive, is a complex, energy-intensive system that prefers behavioral shortcuts for the sake of speed of execution: a rational assessment of the situation would in most cases be too slow to execute to protect us from imminent danger. Thus, if the human being is primarily an emotional system, interacting with it means dealing first and foremost with its emotions and, consequently, with our own. So let us return to the initial concept: if, as we said, it does not mean being nice, kind or empathetic, what then is emotional intelligence? To answer this, it may help to start with the definition of intelligence. With a really extreme summary, we can say that intelligence is the ability to understand and process data and, through this, arrive at conclusions and solutions of different types and natures. Permuting the concept, we can then say that emotional intelligence consists of the ability to understand and process data from emotions, our own and others'. Basically, to understand and process the true essence
of what drives people's behavior and to arrive at conclusions and solutions. Is it not enough? In the world of work, emotional intelligence is an extremely important skill, at whatever level you are placed in the corporate organization: from top management to operational type assignments. Emotional intelligence is not a substitute for traditional intelligence, let's be clear. It does not replace specific technical skills, but it can provide a set of skills that, if learned, can support us in understanding and managing ourselves and others, greatly increasing our interpersonal skills.
Achieving success with emotional intelligence
The point of this article is to dissuade those who might be looking for shortcuts and tricks, to keep away those who think things can be reduced to a decalogue of instructions worthyperhaps - of explaining the operation of a household appliance. Not least because of shortcuts and tricks we know of none. In the area of relationships there is no such thing, and stay away from those who induce you to think so. Does anyone think they can learn a sport with a three-minute video course? Or three hours (so much wouldn't change)? Yet the Web is teeming with sports video courses, just as it abounds with gurus who try to reduce the ability to handle human nature to 10 tricks, 5 rules, 3 tips. Of course, ones that “others will never reveal to you.” If you have come this far, it means two things: the topic interests you, you have the perseverance to go deeper. You are on the right track. If we study years to learn how a machine works, let's forget that we can learn in 10 minutes how the most complicated system in the universe, namely the human being, works. We have said it before: emotional intelligence is a skill that will pay you back with highly satisfying results, provided you know it and train it with commitment.
4 CLEANPRO SRL
4cleanpro.com
4CleanPro is a company that has been operating in the market for over twenty years. 4CleanPro products are appreciated mainly for the construction and quality of the components used. The stainless steel frames make production extremely resistant and the structure guarantees professionalism and efficiency as well as quick responses while maintaining collaborative and assistance relationship over time.
MIRA ERGO 40. Lighter to drive
The MIRA ERGO 40 presents itself with a new design. A new handle offers a greater lever arm and makes it lighter to drive. In the lower part there is the 5 liter recovery tank with a quick release for emptying. The filter and float system is the traditional steel mesh cage with balls that plug the suction pipe when the water reaches the maximum level.
TWIST 40. Green and ecological
Taking into account the most recent developments and updates in the technological field and the need to produce increasingly "green and ecological" machines, Twist 40 was born: it cleans and sanitizes 1,200 m2 in 1 hour using only 36 liters of water and consuming only 0.5 kW of energy. Tanks made from 98% recycled plastic and 100% remelted steel from scrap metal.
Loredana Vitulano
falpi.com
Falpi has clear ideas: to bring the dynamism and desire to innovate of a young and motivated team to the world of professional cleaning equipment, always faithful to the quality of “Made in Italy” and environmental sustainability. Falpi products are designed for cleaning companies, hospitals, communities, hotels and are made with recyclable materials.
Fibronette cloths
Falpi's Fibronette cloths have recently obtained the EU Ecolabel certification. This recognition attests the constant commitment at Falpi towards environmental sustainability and confirms that Falpi’s products meet strict ecological criteria throughout their entire lifecycle. The Fibronette cloths, made of high-quality microfiber, are ideal for various sectors, from civil to industrial, offering excellent performance while fully respecting the environment.
Kubi Ecolabel EU
The Kubi trolley certified with the EU Ecolabel by Falpi stands out for its high-quality materials, which ensure durability and long-lasting resistance. This model represents innovation by combining advanced functionality with cuttingedge design. Entirely Made in Italy, the Kubi is distinguished by its design focused on sustainability and environmental respect. Every stage of its production is designed to minimize environmental impact, from the sourcing of raw materials to the final assembly.
ghibliwirbel.com
Ghibli & Wirbel SpA is an Italian worldwide leading manufacturing company specialised in the development and production of professional cleaning machines. All products are developed and produced in their entirety within the manufacturing plant located in Northern Italy and they are all conceived in order to reach the highest quality, technological and design innovations, and reliability.
Green Pro, the complete range of machines made with recycled plastic, grows thanks to a new model. Green Pro Royal 15 BC Lithium is born, the “green” version of Ghibli & Wirbel’s walk-behind scrubber dryer that can guarantee same quality and performance of the standard model: 15-liter capacity, 385 mm cleaning width and productivity up to 1.540 m2/h.
Racer is Ghibli & Wirbel’s compact ride-on scrubber dryer designed for cleaning operations in medium areas. Extremely versatile thanks to its 85 liter capacity, its 65 cm cleaning width and its small dimensions, Racer can easily perform even the most complicated operations where all the ride-on, including the most compact ones, can’t achieve satisfactory cleaning results.
designing your clean
imesa.it
With a rich history spanning over 50 years, lmesa stands as a family-owned business, priding itself on meticulous attention to detail. Nestled near Venice, ltaly, Imesa specializes in the manufacturing of high-quality commercial washing machines, tumble dryers, and ironers. What sets Imesa apart is its commitment to innovation, incorporating Cloud technology into all its products. This cutting-edge feature allows users to effortlessly control and monitor their equipment via their smartphones, exemplifying lmesa’s dedication to convenience and technological advancement in the realm of commercial
PROEasyLine- High spin washing machines 6-8 Kg capacity
Available with 6 and 8 Kg capacity models, 1400 rpm, the line can be with electric heating and with valve or pump drain system. The 304 stainless steel structure makes the line professional and the compact size makes it ideal for small rooms. PROEasyLine is a guarantee of durability. The PROEasyLine is particularly suitable for the professional cleaning sector to which it is aimed with specific cycles for washing mops, fringes and microfibers.
LM 14 – High spin washing machines 14 Kg capacity
IMESA LM14 washing machine offers specific cycles for the treatment of mops, microfibres and cloths, fully customizable through the standard IM11 touch screen. Detergent consumption can be monitored through the IMConnect portal and the IMESA pump dosing system. This function is particularly required by detergent manufacturers and in the case of washing machine rental contracts, as it ensures total remote management of consumption and cycles performed by the washing machine.
lindhaus.it
Lindhaus offers a full range of state-of-the-art cleaning machines designed for efficiency and sustainability. With a global presence in 52 countries, including the supply to major government buildings, Lindhaus consistently sets new benchmarks in the market for a cleaner, greener world. Lindhaus focuses on Italian, Padua-based excellence throughout the product supply chain, from initial concept to construction and assembly. This guarantees excellent machines designed and cheeked down to the smallest detail.
The “LW44-52 Flexy Hybrid” battery-powered scrubber drier has a patented joint that offers two modes of use: with a lockable neck every 15° for maximum operator comfort and zero effort, or free to rotate 360° to easy access under tables and busy areas. There is no limitation on the angle of use as all motors, battery and recovery tank are placed on the base. This gives the possibility to work even with the machine in a horizontal position.
LW38 CC is the ideal machine for washing any type of synthetic rug and carpet. This innovative carpet cleaning system with a powerful mechanical action and great suction which allows to collect more than 90% of the water used for washing. Thanks to its uniformly wet soft roller rotating at 1500 RPM and a front suction nozzle, the LW38 CC deeply washes carpets and rugs, leaving the surfaces almost dry, thus reducing the total drying time.
lucart.com
Lucart Professional is the reference brand for the Away From Home market of Lucart, a multinational Italian industrial group founded in 1953. Lucart Professional is able to bring concrete and tangible sustainability to the Away from Home sector, offering operators in the sector innovative solutions for hygiene away from home, ranging from tissue products to dispensing systems to soaps.
EcoNatural FLOW is the new unique range of dispensers made from polyethylene and aluminium from beverage cartons, featuring a new exclusive and patented design with sinuous and elegant lines. The range includes dispensers for auto-cut towels, centrefeed toilet paper, folded towels, jumbo toilet paper and bulk pack toilet paper, all in black or white finish. All FLOW dispensers are ReMade in Italy certified and are fully recyclable.
The new Identity Soap 900 system from Lucart Professional boasts a complete range of 100% Made in Lucart soaps, designed to meet the different needs of the professional world, thanks to the two fragrances available:
- Frequent Foam, enriched with aloe vera extract and hypoallergenic;
- Classic Foam, enriched with almond oil; The system is completed by a touchless dispenser with a distinctive and timeless design, available in white and black.
PAPERDI SRL
paperdi.it
Since 1989, Paperdì has been operating in the tissue sector of the paper industry producing disposable items for sanitary and food uses. In 2018 the Pietramelara paper mill comes into operation maximizing the total quality of products and implementing the production by pursuing a development model capable of creating economic value while also protecting and safeguarding the environment.
AVAN ECO
V Folded hand-towel Havana is a new Paperdì product of Avan Eco brand. Avan Eco project focuses on sustainability and strengthens territorial networking through the creation of partnerships with local companies, to promote a circular supply chain economy and to produce 100% of recycled raw materials. The hand-towel has a compact packaging, is completely free of plastic (and and has been awarded Ecolabel and FSC sustainability certifications).
From Paperdì's experience, comes the new line of fast dispersion products. Product quality and technological innovation come together in Fast Dissolution: softness and consistency are combined with a fast melt rate in a few seconds, guaranteeing performance and effectiveness. Preventing pipe clogging is a concrete benefit that can decrease inefficiencies and maintenance costs of the systems.
RUBINO CHEM SRL
rubinochem.it
Rubino Chem is an Italian company that designs and manufactures essences, detergents, and disinfectants for professional and domestic use, operating nationally and internationally since 1960. Thanks to its research and development activities, it offers innovative products formulated with high-quality raw materials that meet market needs, with a special focus on the environment.
Degreaser Food
Degreaser Food from the HiMiX Professional line, an ultra-concentrated, highly alkaline degreaser that effortlessly removes animal and vegetable fats, grease, oils, and burnt residues from washable surfaces. Its ready-to-use liquid formula meets HACCP regulations. Ideal in various food processing areas, including hoods, ovens, grills, cooktops, trays, food displays, and more.
Glass + Inox Ultra
Glass + Inox Ultra from the HiMiX Professional line, an ultra-concentrated cleaner for glass, mirrors, steel, and washable surfaces. Its high degreasing power removes grease, limescale, rain spots, soot, fingerprints, dust, and smog, leaving an invisible protective film that delays dirt buildup. Ideal for various surfaces, including windows, glass doors, countertops and more.
From a sustainability perspective, a biological control program was developed within a food company, with excellent results
Michele Ruzza Consultant and Pest Management Advisor
Andrea Anelli Technical advisor
According to the 2020 "Farm to Fork Strategy"1 of the European Commission, in order to guarantee a fair, healthy and environmentally friendly food system, a new strategy is being outlined that is part of the European Green Deal. For food companies, therefore, it is not only necessary to guarantee food safety, but to gradually face the transition to greater sustainability, with the aim of guaranteeing a neutral or positive environmental impact, using the principles of Integrated Pest Management (IPM).
According to the IFS Pest Control Guideline V.22 among the different control methods, before using biocides, the use of biological control is identified, which the same legislation identifies as Biological controls are the use of natu-
ral enemies (predator, parasites, pathogens, and competitors) to control pests and their damage, namely Biological controls are the use of natural enemies to control their damage.
The concept of biological control was developed in Europe and sagaciously summarized in “One hundred years later: the manifesto of biological control”3 of 1989 where it is identified as biological control is a strategy for strengthening the pest control by natural means. Unlike the use of chemicals, it does not simplify, but makes ecosystems more complex and therefore more stable, and does not increase environmental mutagenesis. If it is therefore true that biological
control is an enhancement of natural control and that, unlike chemical control, it does not simplify the concept of pest control, from a sustainability perspective it must present as its main objective the possibility of guaranteeing profit without causing damage to the environment, without compromising the quality of life and future generations, ensuring food safety.
Among the main pests of foodstuffs, we can include the lepidopterans belonging to the Pyralidae family. These pests, in food companies, are subject to monitoring using pheromone traps and when, based on the Risk Analysis, the so-called acceptability threshold is
exceeded, chemical treatments are intervened with the sole purpose of lowering their presence. As can easily be deduced, this control system does not fully satisfy what is stated by Integrated Pest Management (IPM), therefore it is necessary to identify other methods that can keep the possible presence of moths below a risk threshold from a sustainability perspective. On the basis of the above, between 2022 and 2023, a holistic approach was developed between the DAFNAE of the University of Padua, the Bio-Fab of Colkim srl and a food company for the control of moths in the foodstuffs in a food company.
In the first phase (Year 2022) what can be considered the main natural antagonists of moths were identified. Thus, the breeding and development methods of Habrobracon hebetor4, a Braconid hymenopteran which parasitizes the larvae of moths and of Trichogramma evanescens which in-
stead directly parasitizes the eggs of lepidopterans, were developed.
In the second phase (year 2023) the inoculation of useful insects was carried out in two food companies, one specialized in the transformation of almonds and one in the transformation of rice. The aim was to identify the correct methodology to be implemented for biological control, through inoculation of antagonists5 as well as the parasitization effectiveness of natural antagonists against moths6, creating operational protocols.
In one of the two companies, in which it was decided to carry out a biological control of the lepidopterans, during the year 2022, a constant exceeding of the risk thresholds was highlighted which had led to the need for fortnightly treatments with biocidal products.
Once the company to be subjected to biological control was identified, an operational protocol was developed that was necessary for the correct management of the inoculations of moth antagonists.
The first phase, necessary to identify the correct quantity of inoculants, was the study of the moth catches detected in the previous year. The catch values of each individual monitoring station were thus identified and the areas where the catches were higher and the trend of the infestation within the site were highlighted.
In the second phase, the structural, cleaning and infestation (photo 1) criticalities present on the site were evaluated in order to identify the areas subject to inoculation, as well as identifying white areas, where to carry out checks on the effectiveness of the biological treatment implemented.
Once the areas were identified, the intervention plan was developed, in consultation with the food company.
In the third phase, developed over 6 months, the antagonists were inoculated every 15 days, using both Habrobracon hebetor and Trichogramma evanescens. At the same time, weekly monitoring of the pheromone stations was carried out to assess the degree of infestation with the aim of carrying out corrective actions if necessary. During the test period, a greater number of natural antagonists were used for inoculations, which made it possible to identify the correct quantity of parasitoids to be used depending on the size of the company and the degree of infestation present. At the same time, efficacy tests were carried out using Bio-Test.
At the end of the first year of inoculations, it was possible to detect a significant decrease in the capture of weeds (moths) compared to the captures detected in the same period of the previous year, identifying the correct quantity of inoculum to be applied per unit of surface depending on the degree of infestation. In addition to the data highlighted above, it was also possible to identify how in the 2022 season it was necessary to intervene in the structure with 9 adulticide treatments in order to contain the presence of infestation, while with the inoculation of useful insects the number was reduced to two interventions, necessary only in the first phase, i.e. until the correct quantities of useful insects to be inoculated have been defined. Other significant data that emerged were: 42.06% reduction in disinfestation costs incurred by the Food Company, which largely cover the costs necessary for the increase in monitoring and inoculation of useful insects; Decrease in product returns of 0.18%
(Kg returned/Kg produced) compared to the previous year; Absence of beneficial insects in the finished product.
As we mentioned at the beginning, biological control is a strategy to enhance natural control, it fights nature with nature. Unlike chemical control, it does not simplify, but makes ecosystems more complex, therefore more stable, and does not increase environmental mutagenesis, and after more than two years of tests it is evident how the same can be successfully applied even within food companies. The system to be implemented is certainly more complex than adulticidal treatments alone, but it fully falls within the concept of Integrated Pest Management (IPM), with a view to true sustainability of the sector, as it guarantees a profit both for the Pest Control (monitoring and inoculation of beneficial insects) and for Food Companies (decrease in product returns), to which is added a constant and progressive decrease in the use of biocides ensuring food safety and sustainability.
Bibliography
(1) Farm to Fork Strategy – For a fair, healthy and environmentally-friendly food system – European Union, (2020) (2) IFS Pest Control Guideline – Version 2 (September 2022) 2.2 Integrated pest Managent (IPM) – What is it? Pag. 10
(3) Manifesto della lotta biologica stampato nel gennaio 1989, in occasione del centenario di questa disciplina affermatosi come scienza a partire dal 1888/89 - Come Rami della Grande Quercia – 1st edition May 2021 – in.edit edizioni, Via Varignana, 200/O
(4) Master’s Thesis in Science and Technology for the environment and territory Messa a punto di tecniche di allevamento di Habrobracon hebetor (Hymenoptera, Braconidae) e indagini sul comportamento riproduttivo - University of Padua, Department of Agriculture and Veterinary Medicine – October 2022 - Speaker: Prof. Luca Mazzon; Corapporteurs: dott.ssa Ivana Carofano, Dott. Michele Ruzza; Grad student: Samuele Moraro.
(5) Master's Thesis in Science and Technology for the environment and territory Monitoraggio delle infestazioni di tignole delle derrate (Lepidotera, Pyralidae) in uno stabilimento alimentare sottoposto a controllo biologico mediante inoculo di antagonisti - University of Padua, Department of Chemical Sciences (DiSC), Department of Agronomy, Animals, Food, Natural resources and Environment (DAFNAE) – October 2023 - Speaker: Prof. Luca Mazzon; Co-rapporteurs: dott. Samuele Moraro, Dott. Michele Ruzza; Grad student: Andrea Bonadiman
(6) Bachelor's Thesis in Science and Technology for the environment and territory Indagini etologiche ed efficacia di parassitizzazione dii Habrobracon hebetor (Hymenoptera, Braconidae) nei confronti delle tignole delle derrate - University of Padua, Department of Chemical Sciences (DiSC), Department of Agronomy, Animals, Food, Natural resources and Environment (DAFNAE) – December 2023 - Speaker: Prof. Luca Mazzon; Corapporteurs: Dott. Samuele Morao, Dott. Michele Ruzza; Grad student: Andrea Tedesco
The level of comfort in the environments we inhabit every day contributes to our overall well-being and enables us to tackle each moment effectively. Therefore, it is important that the air is pleasant, clean, and free from insects, which are generally very annoying and harmful to people, and consequently to the image and reputation of the places experiencing these issues.
To effectively manage the comfort of everyday environments, within its Hygiene line, Orma offers a unique and innovative solution for controlling, enhancing, and maintaining air hygiene in virtually all types of enclosed spaces. This solution is the Air Control System, an automatic aerosol diffuser that stands out on the market as a revolution in instant air control.
In addition to being an air freshener, it can also act as an immediate and long-lasting insecticide and sanitizer, depending on the type of aerosol canister chosen to insert into it.
Thanks to its compact size, lightness, and practicality, the Air Control System is a non-invasive and convenient system to use. Installed at a height of approximately 2.53 meters in a position that promotes the even distribution of the product dispensed by air currents, it operates on a timed jet with three different intervals to choose from (7.5 - 15 - 30 minutes). If purchased with a light detection photocell, it can also be programmed for day/night/24-hour operation, based on different needs. Furthermore, it stands out for its durability, as a 250 ml canister left in operation for 24 hours a day with a 15-minute interval provides up to 4 weeks of functionality.
Restaurants, bars, hotels, as well as offices, gyms, and public places, with the Air Control System can finally rid themselves of problems caused by insects such as flies and mosquitoes, ensuring customers the highest level of tranquility, serenity, and air hygiene.
With the Air Control System,
you will always have the certainty of obtaining, and thus ensuring, the highest level of comfort because:
• with Air Control S insecticide spray can, it guarantees immediate and high daily efficacy with an immediate knockdown effect on flies, mosquitoes, tiger mosquitoes, moths, and much more.
• with Air Control Sanitizer disinfectant spray can, it ensures constant hygiene thanks to a rapid bactericidal, yeasticidal, and virucidal action, as it is effective against all encapsulated viruses and some non-encapsulated viruses.
• with Air Control Classic/ Plus deodorant spray can, it offers countless fragrances to choose from for maximum well-being and the immediate disappearance of bad odors.
Thanks also to its three dispensing intervals, the Air Control System is the simple and convenient solution to always offer the excellence of air quality in everyday spaces.
PRODUCTS AND SOLUTIONS MADE IN ITALY INSECTICIDES AIR CONTROL S® DISTAIR S® WITH NATURAL PHYRETHRUM
VIRUSES - BACTERIA AND YEASTS TWO TYPE OF CONCENTRATIONS