
9 minute read
Ottimizzazione del trasporto dal magazzino alla produzione
Con i robot mobili autonomi è possibile realizzare flussi automatizzati anche laddove non è finora mai stata presa in considerazione l’idea di poterlo fare
Ottimizzazione del trasporto
dal magazzino alla produzione
La movimentazione industriale dei materiali destinati alle linee di assemblaggio è un compito “time consumer” che non aggiunge alcun valore. I robot mobili autonomi (AMR) rappresentano la soluzione più semplice, efficiente e conveniente per automatizzare il trasporto interno dei materiali in quasi tutte le situazioni
di Davide Boaglio
Negli stabilimenti produttivi, semilavorati, assemblati e altri materiali di consumo sono, in molti casi, trasportati manualmente su lunghe distanze: dal magazzino alle linee produttive. Queste operazioni possono essere svolte facilmente dagli AMR in modo sicuro ed efficiente, ottenendo un risparmio di tempo significativo, che i lavoratori possono spendere in attività a maggior valore per l’azienda. Nell’intento di ottimizzare la logistica, molte aziende hanno predisposto magazzini intermedi nella linea di produzione. Questa è una soluzione che, però, occupa spazio prezioso nello “shop floor” e che nel contempo diminuisce la flessibilità del layout produttivo. Va considerato, inoltre, che i siti di produzione sono tipicamente ambienti dinamici e altamente popolati: l’uso di carrelli elevatori con equipaggio, così come i transpallet manuali o elettrici, possono creare situazioni di pericolo per i lavoratori in transito lungo i percorsi di trasporto e di stoccaggio. Gli AMR, al contrario, si muovono in modo sicuro ed efficiente anche negli ambienti produttivi più trafficati, fermandosi automaticamente per evitare collisioni e manovrando intorno a persone o altri ostacoli. Senza alcun bisogno di strutture fisse, gli AMR possono essere facilmente riprogrammati nei nuovi layout di produzione o linee di assemblaggio, e le missioni dei robot possono adattarsi a qualsiasi requisito di consegna. Oltretutto, il software dell’AMR può essere integrato con i sistemi MES, ERP o WMS utilizzati dall’azienda, in modo da ottenere consegne autonome dei materiali lungo le linee e soddisfare processi lean e just in time, eliminando così la necessità di stoccaggio all’interno della produzione.
Le applicazioni per l’automazione delle linee di magazzino e assemblaggio
I flussi di lavoro possono risultare assai differenti a seconda della tipologia di industria e dei relativi settori, tuttavia la flessibilità e l’adattabilità dei robot AMR di MiR possono essere personalizzate per adempiere tutte le esigenze aziendali. Questi robot mobili hanno un’interfaccia aperta, che offre la possibilità di abbinare moduli top customizzati per diverse applicazioni. Di seguito vengono descritte tutte le applicazioni tipiche che diverse aziende hanno sperimentato, riuscendo con successo a ottimizzare i trasporti interni.
Scaffalature
Le unità a scaffale sono un modo semplice e molto apprezzato per automatizzare il trasporto dal magazzino alle aree di montaggio. La struttura dello scaffale può assumere vari aspetti, in funzione del materiale che dovrà contenere. Ad esempio, nel caso di minuteria
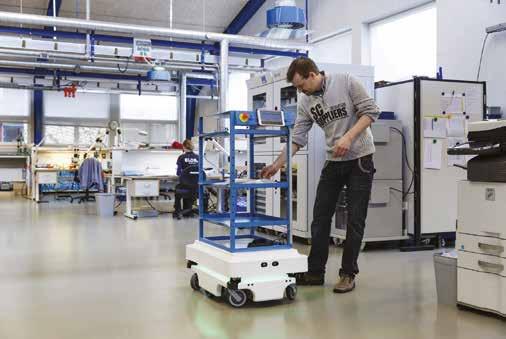
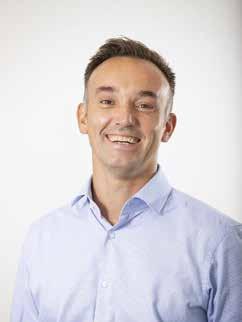
come viti o particolari di piccole dimensioni, lo scaffale potrà essere munito di sportelli (anche ad apertura comandata) in modo che l’operatore possa prelevare rapidamente i particolari destinati al montaggio. Nel caso di semilavorati di dimensioni più grandi, è possibile studiare in modo opportuno la parte superiore dello scaffale per alloggiare senza problemi quantità di pezzi tali da aumentare la portata e consegnare un maggior numero di pezzi in un singolo viaggio. La struttura della scaffalatura può essere installata sulla parte superiore del robot per essere subito pronta all’uso. Gli scaffali statici, pertanto, sono per lo più utilizzati in soluzioni semi automatizzate, dove l’operatore richiama l’AMR tramite l’interfaccia presente sul tablet, posiziona il materiale assemblato negli spazi ricavati sullo scaffale e lo invia a destinazione con un solo click. Esistono numerosi casi d’uso per quanto riguarda gli scaffali statici: cassetti apribili, scomparti dedicati, così come alloggiamenti più capienti per semilavorati più grossi. A seconda dell’esigenza di trasporto, le soluzioni possono essere tantissime, e ognuna si può adattare perfettamente agli AMR MiR. Inoltre i robot sono in grado di gestire l’apertura/chiusura degli scomparti, evitando la perdita di materiale lungo il percorso. Quella degli scaffali statici rappresenta la soluzione più semplice e immediata per il trasporto di particolari.
Sistema di carrelli
Si tratta di un’applicazione in cui il robot viene dotato di un modulo superiore che preleva, trasporta e consegna carrelli. L’AMR può trasportare il carrello, ad esempio carico di semilavorati, dal magazzino alla produzione, dove può depositarlo interamente continuando poi il suo percorso. In questo modo il robot, una volta scaricato il carrello pieno, può andare a raccoglierne uno vuoto riportandolo al magazzino, come anche prelevarne uno nuovo contenente altri particolari destinati a un’altra linea di montaggio. Il sistema di carrelli ha la stessa flessibilità di personalizzazione della scaffalatura, ma con il grande vantaggio che con un solo AMR si possono spostare un gran numero di carrelli. Ciò è possibile grazie al fatto che l’AMR monta un sollevatore ed è libero di manovrare. Un caso specifico dimostra come il sistema di carrelli sia stato interpretato in modo particolare: quello di un’azienda che ha dotato due robot MiR di un sistema di carrelli che sono stati trasformati in un vero e proprio banco di lavoro mobile. Il funzionamento ottenuto è molto semplice: i semilavorati
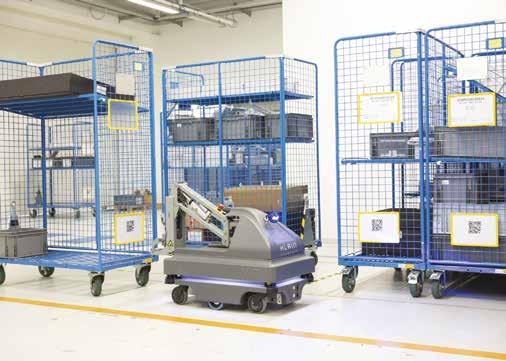
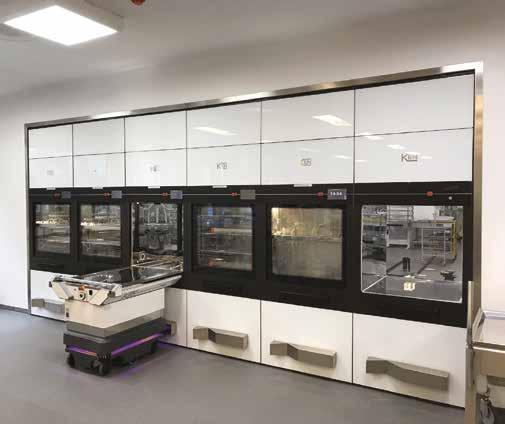
vengono caricati sul carrello e trasportati dal primo AMR fino al punto di montaggio, dove successivamente, ad assemblaggio terminato, vengono depositati i prodotti finiti. Il secondo AMR preleva il carrello con i prodotti finiti e lo trasporta fino all’area di confezionamento. I due robot in questo modo, diventano parte integrante della linea produttiva e i lavoratori vengono liberati dai compiti di trasporto. Restando in tema di carrelli, è necessario menzionare anche i ganci da traino che permettono di incrementare la portata dei robot. Il recente lancio del MiR Hook 250, amplia ulteriormente le possibilità di movimentazione delle merci, poiché è un modulo superiore che provvede ad agganciare un carrello in completa autonomia, ma è anche in grado di mettere l’AMR nelle condizioni di trainare un treno di carrelli. Questa applicazione permette di elevare la quantità di materiale trasportato laddove non è necessario avere particolari tipologie di carrello. La caratteristica di riuscire a trasportare due o più carrelli genera valore destinato ai processi logistici interni dove i materiali transitano attraverso stazioni intermedie e la quantità di merce richiesta è maggiore e deve essere disponibile in tempi ristretti.
Sistemi Karakuri
Questa soluzione è particolarmente indicata per le produzioni lean che, come caratteristica principale, hanno la completa automazione. Sono oramai molte le aziende che hanno integrato questo sistema direttamente sopra gli AMR. Il sistema Karakuri è una soluzione semplice, formata da rulliere che sfruttano la forza di gravità in combinazione a collegamenti meccanici e cinematismi dedicati: la gravità permette infatti al rack installato sull’AMR di scaricare e caricare le merci sul robot. Con questo sistema il robot è in grado di operare in perfetta autonomia, andando a interagire con la parte fissa, generando un flusso di merci che non richiede più l’intervento umano. Con il sistema Karakuri si può automatizzare completamente il processo di carico e scarico su di una linea di assemblaggio, garantendo la massima efficienza. Nel caso di un robot mobile integrato nel sistema ERP, è possibile eliminare l’intervento umano, poiché il robot viene richiamato in modo automatico collegandosi al sistema Karakuri fisso, caricando e scaricando in modo autonomo. Inoltre, e ciò non è da sottovalutare, con questo sistema i consumi energetici per la movimentazione sono pressoché nulli. Sugli aspetti energetici sono oramai molte le aziende attente e che hanno iniziato a mettere in pratica politiche sostenibili e dal basso impatto ambientale.
Nastri trasportatori
Gli AMR che sono muniti di una rulliera diventano un collegamento adattabile tra nastri trasportatori fissi, generando l’elemento di continuità nello spostamento delle merci. Questo tipo d’impostazione può sovente far parte di una soluzione completamente automatizzata, dove l’AMR è incaricato al trasferimento dei semilavorati dal magazzino alla produzione o tra le linee di assemblaggio. Con un AMR dotato di rulliera, il processo logistico del nastro trasportatore viene reso molto più agile e semplificato grazie al fatto che non è più necessario avere nastri trasportatori fissi. L’AMR potrà coprire agevolmente le distanze, diventando una sorta di navetta che andrà a collegare più punti di prelievo e consegna con la possibilità di cambiare percorso. Affidandosi, invece, ai nastri trasportatori fissi, la necessità di spostare il percorso di un nastro, richiederebbe molto ma molto più tempo. Occorre considerare, infine, che il robot riesce perfettamente a interagire con i nastri, arrivando a prelevare o consegnare il materiale senza intoppi, aumentando in modo significativo le possibilità di itinerario delle merci.
Sollevatori di pallet
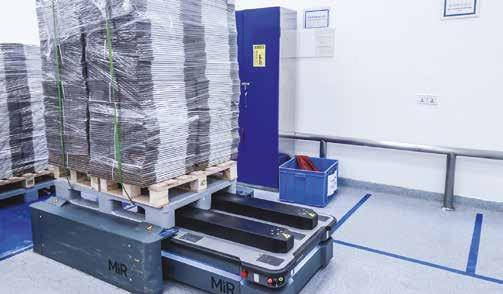
Quando è richiesto lo spostamento di materiali dalle grandi dimensioni, da un magazzino alla produzione, i sollevatori per carichi pesanti possono occuparsi della movimentazione dei pallet
Massima sicurezza
Attualmente la tendenza è quella di lasciare i carrelli elevatori lontani dalle aree produttive della fabbrica per garantire agli operatori un maggior livello di sicurezza. I robot AMR sono l’unica alternativa efficiente e sicura perché progettati per viaggiare evitando ostacoli e persone. In MiR la sicurezza è sempre stata al primo posto, e l’obiettivo di ridurre a zero gli incidenti influisce positivamente sulla produttività e sull’ambiente lavorativo. Riguardo agli ultimi due arrivati in casa MiR, il 600 e il 1350, rappresentano un ulteriore passo avanti per l’efficienza dell’intralogistica non soltanto per le capacità di portata, ma anche per una protezione elevata e vanno così ad arricchire una gamma già estesa di AMR adatti a diversi impieghi, grazie alla loro semplicità di utilizzo e flessibilità. Il MiR600 e il MiR1350 sono AMR dotati di grado di protezione IP52 che consente di resistere a polveri e liquidi. Questa caratteristica rappresenta una novità rispetto al resto della famiglia MiR. Massimizzare l’efficienza delle operazioni logistiche mantenendo un altissimo livello di sicurezza è il nuovo obiettivo che MiR ha raggiunto con il recente lancio dei due AMR.
zione dei pallet. Con i moduli sollevatori e i rack personalizzati, gli AMR MiR possono prelevare dal magazzino, trasportare e consegnare i pallet in modo autonomo, garantendo una movimentazione efficiente. Recentemente è stato aumentato il range di portata con due nuovi AMR, il MiR600 e il MiR1350: con quest’ultimo ora è possibile movimentare pallet di oltre una tonnellata.