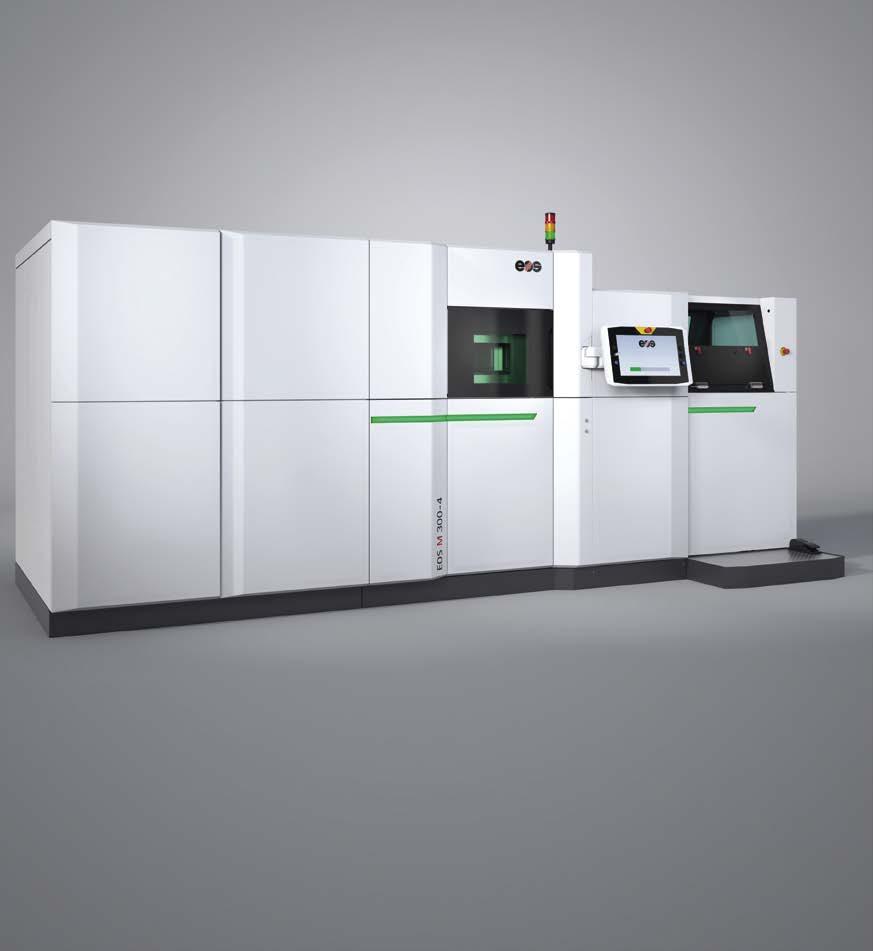
8 minute read
GKN Additive e EOS
UNA PRODUZIONE ADDITIVA PIÙ SNELLA, CON AUTOMAZIONE, INTEGRAZIONE DEI DATI E INDUSTRIALIZZAZIONE DEL PROCESSO DI FUSIONE LASER A LETTO DI POLVERE, GRAZIE ALLA PIATTAFORMA EOS M 300-4
GKN ADDITIVE ED EOS
COMBINANO DIGITALIZZAZIONE, AUTOMAZIONE E PROCESSO L-PBF
AAl giorno d’oggi, la digitalizzazione è alla base della trasformazione di tutti i processi produttivi. Tuttavia sono ancora pochi gli esempi di processi di industrializzazione che comportino l’applicazione della digitalizzazione alla produzione additiva. Grazie alla partnership tra GKN Additive ed EOS, la combinazione tra automazione e l’integrazione dei dati ha portato ad una comprensione più profonda del processo, rendendo per la prima volta possibile una produzione additiva più snella. GKN Additive, utilizzando il sistema EOS M 300-4 e incorporando la capacità del sistema multi-laser, sta dimostrando come la digitalizzazione del processo di produzione renda possibile un’industrializzazione più completa e quali siano i vantaggi. In pratica, GKN Additive ed EOS collaborano per trasformare la produzione 3D del metallo (Metal AM) in produzione digitale. La sfida è aprire la strada della produzione additiva in metallo di serie per applicazioni automobilistiche.
I protagonisti
GKN Additive è un produttore digitale di parti e materiali AM in metallo per prototipi, serie di medio e alto volume e aftermarket, con una particolare propensione nello sviluppo di nuove tecnologie per renderle accessibili al mercato più facilmente e più rapidamente. GKN Additive è supportata dal know-how di GKN Powder Metallurgy, leader nei settori della produzione di polveri e della lavorazione dei metalli, e da una rete ingegneristica di oltre 6000 collaboratori in 29 sedi. EOS, leader mondiale nella tecnologia e nella qualità nella produzione additiva (AM) di fascia alta, unisce l’efficienza della produzione ad alta qualità con la sua innovazione pionieristica ed un insieme di pratiche sostenibili, alimentate dalla sua rete di macchine a valore digitale basate su una piattaforma e su un portafoglio olistico di servizi, materiali e processi. Attraverso la propria tecnologia di stampa industriale 3D, EOS fornisce soluzioni per una fabbricazione responsabile ai produttori di tutto il mondo. Sistemi, materiali e parametri di processo sono armonizzati in modo intelligente per garantire un’elevata qualità dei pezzi affidabile.
I due leader tecnologici hanno concordato una collaborazione, rivolta principalmente al mercato automobilistico, che integra le eccellenti posizioni di entrambe le aziende nei rispettivi mercati, per aprire la strada alla stampa 3D industriale business-to-business.
La collaborazione tra GKN ed EOS, in forza del proprio know-how ed esperienza e dell’impronta globale di entrambi i partner, offrirà alle aziende la possibilità di sfruttare appieno le potenzialità rivoluzionarie offerte da Metal AM. Questo approccio, già pienamente integrato in quello della fabbrica digitale di GKN, costituirà il prossimo grande passo verso il futuro della produzione in serie Metal
M 300-4 in produzione
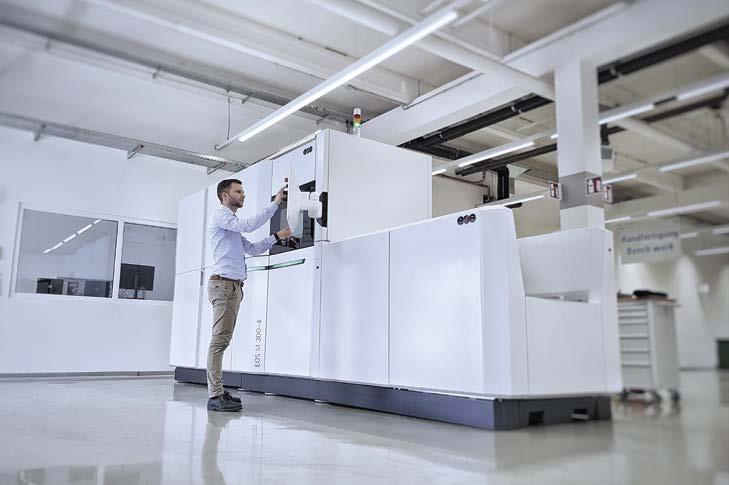
AM per applicazioni automobilistiche. Il Metal AM ha un enorme potenziale nel plasmare il futuro della produzione industriale e dei suoi prodotti, elevandolo a un nuovo livello. EOS e GKN affronteranno insieme questa sfida. “Vogliamo garantire che sempre più aziende riconoscano e utilizzino il potenziale di questa tecnologia innovativa. Allo stesso tempo, vogliamo ampliare notevolmente le aree di applicazione con nuovi materiali testandoli e infine utilizzandoli nella produzione in serie”, afferma Peter Oberparleiter, CEO di GKN Powder Metallurgy. Mentre Hans J. Langer, fondatore e CEO di EOS, dichiara: “La collaborazione tra GKN ed EOS è un altro passo importante verso l’integrazione della stampa 3D industriale nelle linee di produzione esistenti e future e per sfruttare i vantaggi della tecnologia AM per la produzione in serie. Con GKN abbiamo il partner giusto che offre un alto grado di esperienza con la sua presenza globale e la sua produzione ad alte prestazioni per l’industria automobilistica”.
La sfida
Nell’ambito del progetto di finanziamento IDAM, GKN Additive, grazie al proprio parco macchine, tra cui la fusione a letto di polvere laser (L-PBF), la fusione a getto multiplo e i sistemi di getto di legante metallico, ha contribuito alla creazione di una lista esigente di criteri per la selezione di un sistema di produzione L-PBF, focalizzando la propria scelta nel sistema multi-laser ad alte prestazioni EOS M 300-4.
Il nuovo sistema AM doveva raggiungere l’alto livello di qualità delle parti, ma doveva anche garantire un processo di stampa 3D industriale molto stabile, basato sulla polvere.
Tuttavia, ciò che era più essenziale, era fornire interfacce digitali standardizzate (per esempio OPC UA) al fine di facilitare la perfetta integrazione nei processi digitali, dal monitoraggio, alla manutenzione predittiva e ai controlli automatici. Il modulo per l’introduzione della polvere metallica (il dispenser) dovrebbe garantire la flessibilità dei materiali utilizzati in modo da poter utilizzare sia materiali in polvere atomizzati a gas che ad acqua.
Per raggiungere l’industrializzazione con l’alta produttività del sistema desiderata, era consigliabile l’uso di un sistema multi-laser ad alte prestazioni, che l’EOS M 300-4 offre. Un’altra ragione nella scelta dell’EOS M 300-4 è stata la sua funzione a tutto campo: ognuno dei quattro laser è in grado di eseguire un’esposizione sovrapposta alla piattaforma (“full-field overlap”). Dato che il sistema di produzione modulare assicurava un’interfaccia fisica insieme alle interfacce digitali richieste, è stata una scelta chiara per GKN.
“Le caratteristiche riproducibili dei pezzi e un ambiente di processo affidabile sono i vantaggi principali del sistema multi-laser EOS M 300-4. Finora abbiamo stampato con successo 120 build jobs nel primo anno. Le prestazioni della macchina e il suo concetto modulare giocano un ruolo chiave per la nostra strategia di industrializzazione”, afferma Sebastian Blümer, Technology Manager Laser AM, GKN Additive.
La soluzione
Uno scenario così complesso e di vasta portata significa più di un’integrazione di “una sola” nuova macchina di produzione in un processo di produzione in corso. GKN ha iniziato con test intensivi del sistema: indagine sulla qualità dei componenti, analisi delle strategie multi-laser e valutazione intensiva del processo complessivo. Sono state studiate anche le strategie che permettono di utilizzare nel modo più efficace i quattro laser - bilanciamento del carico, swimlane o quadranti.
Fin dall’inizio è stata analizzata criticamente la capacità del processo di produzione dell’L-PBF, per quanto riguarda la densità, le proprietà meccaniche e le superfici. A questo proposito, GKN si è concentrata sullo sviluppo di un materiale proprietario: l’acciaio a bassa lega a doppia fase (DPLA). La stretta collaborazione con EOS e Additive Minds ha accelerato i primi passi nella qualificazione del materiale DPLA. Sulla base dei risultati degli studi sul laser singolo, GKN è stata in grado di far avanzare rapidamente la capacità del materiale DPLA sul sistema EOS M 300-4 e alla fine ha avuto successo.
Oltre allo sviluppo dei parametri di processo, al fine di monitorare costantemente le prestazioni del sistema, i dati di processo dell’EOS M 300-4 vengono monitorati e valutati utilizzando il software interno di GKN (compresi i sistemi di Business Intelligence). “La fornitura di un’interfaccia OPC UA garantisce un flusso continuo di dati che ci supporta nella nostra valutazione tecnica del processo
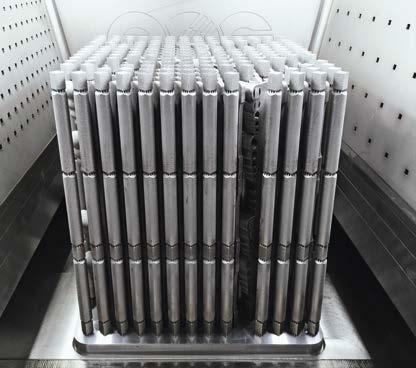
A marzo 2019, un consorzio di 12 partner provenienti dai settori della produzione additiva, automobilistico, della ricerca e industriale ha lanciato il progetto IDAM (Industrialization and Digitalization of Additive Manufacturing). Fondamentalmente, il progetto affronta i limiti della fusione a letto di polvere laser (LPBF) AM, compresa la mancanza di automazione e gli elevati costi associati, che ostacolano l’adozione della tecnologia per la produzione industriale in serie in settori come quello automobilistico. Nell’ultimo anno, i partner del consorzio IDAM hanno compiuto progressi nella creazione delle linee pilota AM digitalizzate affrontando una serie di argomenti, tra cui le fasi di pre-stampa, stampa e poststampa. Tra le questioni più critiche affrontate in questa fase del progetto, c’è la creazione di un’architettura digitale, inclusi standard digitali e una panoramica connessa all’IoT della catena di processo AM. Un’architettura digitale che copra l’intero processo AM è fondamentale per garantire la comunicazione tra i moduli della catena di processo AM e ottenere l’affidabilità richiesta per la produzione in serie. Uno dei maggiori ostacoli nell’adattare l’architettura digitale è la creazione di una soluzione completa per vari sistemi LPBF che variano tutti nelle loro interfacce alla catena di processo. La diversa natura dei sistemi LPBF sul mercato rende difficile implementare un’interfaccia affidabile e flessibile.
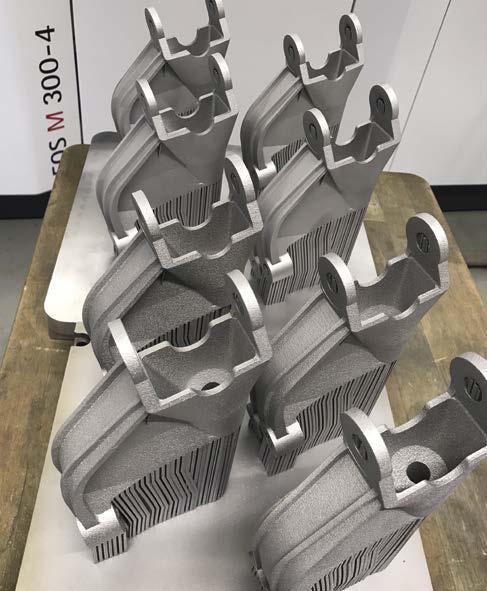
Produttività 3 volte più elevata con il sistema multi-laser
e dell’efficienza del sistema risultante”, afferma Sebastian Blümer, Technology Manager Laser AM, GKN Additive. “La collaborazione con EOS ci ha permesso di ottimizzare ancora di più l’utilizzo delle interfacce fisiche e digitali. Oltre al monitoraggio dei dati, è ora possibile inviare comandi che controllano l’EOS M 300-4, e quindi porre le basi per un sistema automatizzato”.
I risultati
I risultati attuali hanno già dimostrato che GKN ha scelto il giusto approccio e il giusto hardware EOS. Dato che GKN ha in uso anche l’EOS M 290, è stato possibile confrontare entrambi i sistemi per quanto riguarda la qualità e la produttività ottenibili. Come previsto, il sistema multi-laser sfrutta pienamente i suoi vantaggi.
Questa superiorità è stata messa in mostra anche per il “lungo raggio”: GKN ha stabilito un’alta disponibilità, tra l’altro, per quanto riguarda la protezione generica della macchina (selezione del layout del lavoro, basata sui risultati del Joint Working Group (JG 79) - in linea con ISO TC 261). Un lavoro di costruzione di un pezzo è stato stampato in 160 ore con una densità di nidificazione del 35% e, tutti e quattro i laser erano permanentemente attivi. Nel follow-up, l’attenzione è stata posta sul test della robustezza del sistema e sull’analisi delle richieste di qualità dei componenti. Il risultato è stato che il sistema è molto durevole nel funzionamento continuo e produce una qualità elevata e riproducibile dei componenti per un lungo periodo di tempo di costruzione.
“La qualificazione completa del sistema EOS M 300-4 è stata la base per l’automazione della macchina e per l’industrializzazione del processo L-PBF ricercato con il suo utilizzo. L’EOS M 300-4 ha già un hardware proprietario per la gestione automatica dei supporti della piattaforma di costruzione. In questo modo, sfruttiamo tutto il potenziale del sistema per poter servire più rapidamente i progetti di piccoli e grandi volumi in futuro”, riassume Sebastian Blümer. Tutto questo aumenta il numero di applicazioni potenziali, ad esempio geometrie/disegni di lamiera complessi sono ora possibili con questo pacchetto di soluzioni.