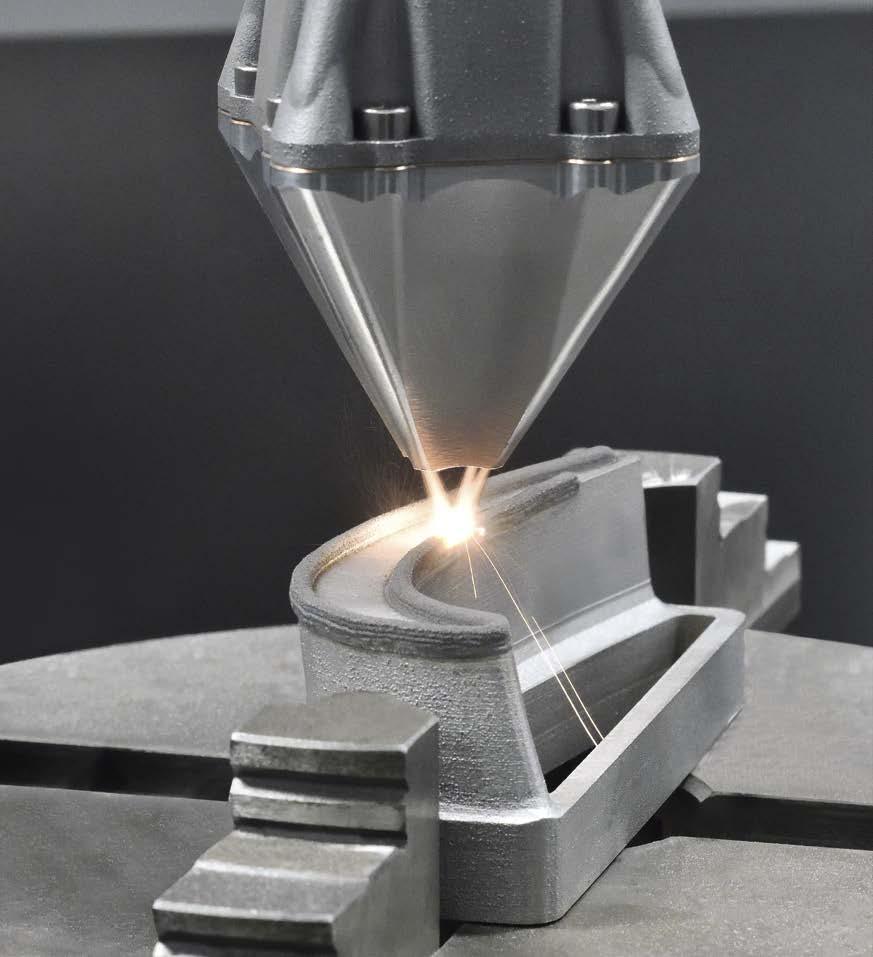
7 minute read
Good to grow
IL MOTTO DI PRIMA ADDITIVE PER UNA CRESCITA INTELLIGENTE E SOSTENIBILE
L’L’additive manufacturing del metallo offre infinite possibilità alle aziende. Spesso, però, per affrontare sfide impegnative, come l’implementazione di una nuova tecnologia all’interno del proprio contesto produttivo, ciò di cui gli imprenditori hanno bisogno è il giusto compagno di squadra con cui vincere questa sfida. “Sin dalla fondazione di Prima Additive, la Business Unit nata nel 2018 all’interno del gruppo Prima Industrie, il nostro obiettivo è sempre stato quello di ridurre le barriere all’ingresso di questa tecnologia, riducendone i costi, aumentandone l’efficienza e fornendo una serie di servizi ai clienti per consentire loro di sfruttare appieno tutti i benefici dell’additive applicati al proprio contesto produttivo”, dichiara Paolo Calefati, Vice President Innovation and Additive Manufacturing Business Development presso Prima Industrie. “Grazie alla nostra esperienza di oltre 40 anni nei sistemi laser per il material processing e all’expertise dei nostri ingegneri applicativi, possiamo realmente essere al fianco dei nostri clienti e guidarli lungo tutto il processo di adozione della stampa 3D del metallo. Siamo sempre trasparenti con tutti coloro che vogliono avvicinarsi a questa tecnologia, aiutando l’utente finale a capire come passare dalle tecnologie tradizionali all’additive, individuare le modalità più efficienti per produrre i propri componenti e capire ogni segreto della tecnologia per poterla sfruttare al meglio. In poche parole, aiutiamo gli imprenditori a tradurre la loro immaginazione in un nuovo business sempre più efficiente”, aggiunge.
Soluzioni tecnologiche sempre più innovative
Se dal punto di vista dei servizi di supporto all’applicazione, Prima Additive ha già raggiunto ottimi livelli di maturità, continua l’impegno dell’azienda per rendere l’additive una tecnologia sempre più competitiva grazie allo sviluppo di soluzioni sempre più innovative, in grado di migliorare l’efficienza del processo. “Siamo sempre alla ricerca di nuove soluzioni per ottenere di più dalle tecnologie additive”, dichiara Calefati. “Così, nel corso dell’ultimo anno, abbiamo presentato diverse novità dal punto di vista del prodotto: su tutte ne citiamo due, una per la tecnologia Powder Bed Fusion, l’altra per la tecnologia Direct Energy Deposition”. Nell’ambito della tecnologia Powder Bed Fusion, funzionale alla realizzazione di componenti dalle geometrie complesse, uno dei campi in maggior evoluzione al momento è rappresentato dallo sviluppo di nuovi materiali processabili. “Negli ultimi tempi – osserva Calefati - abbiamo registrato una crescente domanda del mercato di applicazioni in rame, oro o altre leghe altamente riflettenti e dotate di elevata conduttività termica ed elettrica. In particolare, la domanda sta aumentando soprattutto nei settori dei motori elettrici, degli scambiatori di calore, dell’elettronica, dell’aerospace e della gioielleria. Lavorare queste leghe con laser infrarossi presenta problematiche legate ad un basso assorbimento, che porta a scarsa efficienza e performance instabili. Per questo, grazie alla nostra esperienza nei sistemi laser, abbiamo lavorato sull’implementazione del laser verde, che presenta una lunghezza d’onda più adatta a lavorare materiali altamente riflettenti”. Nello specifico, le due soluzioni sviluppate dall’azienda sono basate sulla piattaforma 150, dotata di un volume di costruzione cilindrico con una base di 150 mm di diametro per un’altezza di 160 mm. Due le soluzioni dotate di laser verde presentate nel corso di quest’anno: la Print Green 150 a laser singolo e la Print Genius 150 Double Wavelength, che invece presenta due laser, uno verde e uno infrarosso, che possono lavorare alternativamente sulla stessa area a seconda delle necessità. “In aggiunta alla configurazione laser, entrambe le soluzioni presentano le altre innovazioni disponibili sui nostri sistemi, su tutte: il riscaldamento della piattaforma fino a 300° C, che avviene sia dall’alto che dal basso, e il sistema ottico con Beam Expander, che consente di adattare in tempo reale la dimensione dello spot laser”, spiega Calefati.
Ottimizzazione e controllo dei processi dei sistemi di produzione additiva
Un importante vantaggio in termini di efficienza di stampa a parità di qualità della Print Genius 150, il sistema di produzione additiva di Prima Additive con tecnologia Powder Bed Fusion caratterizzato da due laser che lavorano sulla stessa area, deriva anche dalla collaborazione di Prima Additive con Materialise, leader globale nelle soluzioni di stampa 3D, per l’ottimizzazione
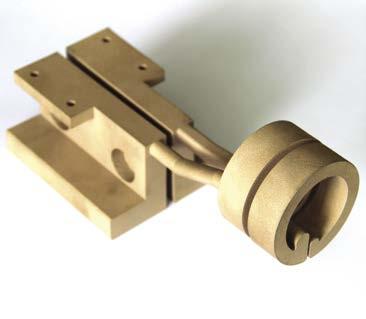
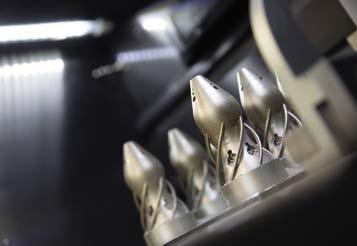
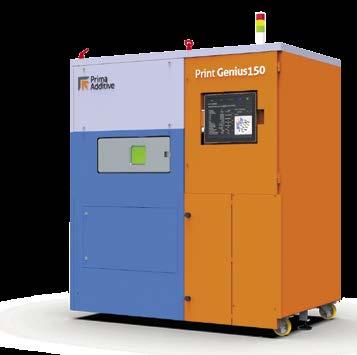
dei sistemi di produzione additiva del metallo. Prima Additive ha integrato su questa macchina il controllo hardware MCP (Materialise Control Platform) di Materialise per ottenere funzioni di controllo in tempo reale e una combinazione ottimizzata con sistemi esterni di assistenza al processo, come i sistemi di monitoraggio e controllo. Un importante risultato dell’integrazione tra i sistemi di Prima Additive e Materialise è lo sviluppo di un algoritmo di “Laser Workload Balancing” che permette di sfruttare al massimo e in modo bilanciato i due laser, ottimizzando il loro carico di lavoro. Grazie a questo algoritmo i due laser sono in grado di lavorare in ogni strato per lo stesso periodo di tempo, distribuendo automaticamente il lavoro in modo omogeneo ed eliminando i momenti in cui solo uno dei due laser è in funzione, massimizzando il beneficio di avere due laser sulla stessa macchina.
Il processo di produzione additiva a deposizione diretta di energia (Direct Energy Deposition) utilizza energia termica focalizzata, generata da una sorgente laser, per fondere polvere metallica irrorata nel punto focale del raggio laser. In questo modo il laser fonde la polvere depositata sul componente. “Per quanto riguarda questa tecnologia – aggiunge Calefati - abbiamo sviluppato e brevettato un’innovativa testa laser chiamata “REAL_DED”, acronimo che sta per REal-time Adaptive Laserbeam for Direct Energy Deposition. La tecnologia DED consente di depositare materiale là dove serve, consentendo così non solo la realizzazione di parti da zero, ma anche riparazioni o funzionalizzazioni di componenti esistenti. La testa REAL_DED consente di aumentare le prestazioni e l’efficienza del processo di deposizione e permette all’operatore di adattare in tempo reale le dimensioni dello spot del fascio laser durante il processo senza dover modificare alcun componente meccanico o configurazione ottica della macchina”. La tecnologia alla base della testa REAL_ DED permette di ingrandire il diametro dello spot del raggio laser almeno fino a 2 volte rispetto alla dimensione originale data dalla configurazione della fibra di erogazione della macchina. “La testa – precisa Calefati - è stata interamente progettata da Prima Additive, con il supporto di altre due business unit del gruppo Prima Industrie, Prima Electro e Convergent Photonics, ed è realizzata anch’essa in additive con la tecnologia Powder Bed Fusion delle nostre macchine. Siamo convinti che con il nostro background ingegneristico e meccatronico riusciremo ad accelerare lo sviluppo tecnologico portando sul mercato soluzioni sempre più performanti”.
I vantaggi “green” dell’AM
Nel settore aerospaziale e automotive è sempre più diffusa la tendenza a produrre componenti altamente funzionalizzati e alleggeriti. In questi casi la stampa 3D si presta a valorizzare i materiali in termini di forme e geometrie. La logica di sviluppo di Prima Additive, basata su principi di riparazione, funzionalizzazione e alleggerimento, sposa i principi dell’economia sostenibile. “La sostenibilità e la circular economy non riguardano solo l’etica dell’innovazione, ma anche la competitività, che può risparmiare e rendere più profittevole il suo business”, afferma Calefati. Sono tre le ragioni che rendono l’additive una soluzione sostenibile. Innanzitutto, la stampa 3D utilizza solo il materiale necessario, a differenza dei metodi tradizionali basati sull’asportazione di materiale da un blocco pieno. Inoltre, la produzione on demand consente di evitare l’onere di gestire grandi stock di prodotti o pezzi di ricambio, riducendo così spazi e costi di magazzino. Infine, grazie all’additive è anche possibile riparare componenti ad alto valore aggiunto, estendendo il loro ciclo di vita. Le soluzioni di Prima Additive dotate di tecnologia Direct Energy Deposition, infatti, consentono di riparare parti in metallo, ma anche di rivestirle di altro metallo o di aggiungere parti customizzate su pezzi già esistenti. In questo modo, anziché creare nuovi componenti è possibile riparare e riutilizzare potenzialmente all’infinito componenti ad alto valore aggiunto, rendendo la produzione più “green” e sostenibile e, soprattutto, risparmiando tempo e risorse. Anche la tecnologia di additive manufacturing Powder Bed Fusion è green, poiché il processo di fusione della polvere strato su strato, consente di utilizzare solo il materiale necessario per produrre l’oggetto. La polvere di metallo utilizzata nel processo di produzione e non fusa può essere riciclata ed utilizzata successivamente. In questo modo si riducono drasticamente gli scarti di lavorazione, che sono invece un elemento decisamente ingombrante nel caso delle tecnologie di asportazione truciolo. Le infinite possibilità offerte dall’additive manufacturing consentono di realizzare qualunque pezzo che possa stare all’interno dell’area di lavoro della macchina. In questo modo è possibile produrre parti che prima venivano realizzate da fornitori diversi, ridurre il numero di assemblaggi necessari consolidando più parti in una, oppure realizzare pezzi contoterzi per settori molto diversi tra loro. Infine, l’additive manufacturing rivoluziona la supply chain: è possibile produrre pezzi on demand, evitando di avere grandi stock di parti di ricambio in magazzino e producendo solo ciò che serve quando serve, evitando lunghe attese e trasporti.