
7 minute read
MPA 42, la produzione additiva come servizio
All’applicazione della polvere segue la rifinitura
HERMLE
CON IL NUOVO CENTRO DI LAVORAZIONE MPA 42 INSTALLATO PRESSO GLI STABILIMENTI HERMLE MASCHINENBAU, NELLA PRODUZIONE ADDITIVA, HERMLE SI PONE COME UN FORNITORE DI SERVIZI
IIl nuovo centro di lavorazione MPA 42 è potente e preciso, ma non è in vendita. L’azienda è focalizzata sulla ricerca di base e sviluppo di nuove tecnologie nel campo della produzione generativa. Conosce le esigenze dei costruttori di stampi, tempi di ciclo brevi e alta qualità dei componenti e, grazie alla sua pluriennale esperienza, è in grado di soddisfarle. Con la nuova generazione di macchine, il processo di fabbricazione generativa guadagna sensibilmente in precisione e velocità. L’amministratore delegato della Hermle Maschinenbau GmbH (HMG) di Ottobrunn, Rudolf Derntl, ci spiega le peculiarità tecnologiche della macchina. . L’abbreviazione “MPA” ne svela il funzionamento: si tratta di un processo di applicazione della polvere metallica che Hermle ha portato alla maturità del mercato circa sette anni fa. “Ciò che il nuovo MPA 42 della Hermle raggiunge ha del paradossale: invece che in versione ridotta, i pezzi grezzi lasciano la zona di lavoro con una massa significativamente maggiore”, afferma.
Additiva con ultrasuoni
Il nuovo MPA 42 si trova presso la Hermle Maschinenbau GmbH (HMG) di Ottobrunn, filiale interamente controllata dalla Maschinenfabrik Berthold Hermle AG che opera dal suo avamposto bavarese dal 2009 e negli anni si è evoluta fino a diventare un fornitore di servizi per la produzione additiva. Focus dell’azienda, la ricerca di base e sviluppo di nuove tecnologie nel campo della produzione additiva. Da alcuni anni, la filiale offre anche ampie capacità di produzione che le consentono di produrre componenti di grandi volumi nel processo brevettato del MPA esclusivamente per i clienti Hermle. Aprendo le porte della cabina insonorizzata del MPA 42, si scopre un centro di lavorazione a 5 assi del tipo C 42 U, pesantemente modificato. Accanto al mandrino, un ugello sporge nella zona di lavoro, mentre manca un’unità di spruzzo per il lubrorefrigerante. “L’ugello di de Laval permette di accelerare la polvere e la spara diritta sul pezzo grezzo di metallo bloccato”, spiega Derntl. Il vapore surriscaldato e l’azoto svolgono un ruolo altrettanto importante quanto la geometria dell’ugello nel far sì che la polvere raggiunga una velocità supersonica e aderisca in seguito a deformazione nel momento dell’impatto. Un generatore di vapore e cinque alimentatori di polvere si trovano nella parte posteriore dell’impianto. Tutti i materiali di applicazione e i pezzi grezzi hanno la stessa duttilità: “Molti metalli funzionano, perché l’applicazione si basa sulla deformazione plastica. Di conseguenza, anche la superficie dei semilavorati deve essere duttile”, aggiunge l’amministratore delegato. Oltre agli acciai da lavoro a caldo e a freddo con un alto contenuto di carbonio, comunemente usati nella costruzione di utensili, si usano anche rame e Ampcoloy. di materiali di acciaio e rame ha quindi un netto vantaggio, dato che il rame dissipa il calore molto più velocemente degli acciai per utensili lavorati: “Con la produzione additiva, introduciamo il rame in quei punti dell’utensile che non hanno spazio per i canali di raffreddamento. Durante lo stampaggio a iniezione, il nucleo di rame dissipa il calore nel canale di raffreddamento appena vicino, molto più velocemente dell’acciaio. L’utente si ritrova così a risparmiare secondi preziosi nel tempo di raffreddamento e migliora la qualità della superficie delle parti in plastica”, sostiene Derntl.
I cinque assi del centro di lavorazione permettono pressoché qualsiasi orientamento del getto di polvere rispetto al componente, garantendo così la massima libertà di progettazione.
I canali di raffreddamento possono quindi essere realizzati direttamente sulle superfici curve di un pezzo grezzo. In questo modo, anche gli stampi a iniezione più grandi possono essere raffreddati vicino ai loro contorni senza dover costruire additivamente l’intero componente. L’unico limite è la zona di lavoro del C 42 U. “In funzione della geometria, il limite dimensionale per il processo additivo è di 600 millimetri ciascuno, in lunghezza e larghezza. Di norma, però, i componenti sono più piccoli”, spiega Derntl. La macchina risulta anche particolarmente utile nella produzione di componenti cilindrici o conici come le boccole di precamera raffreddate. Applicando il materiale mentre il componente è in rotazione, le tasche e i canali sono riempiti in modo efficiente e racchiusi dall’acciaio per utensili.
Oltre a conseguire un raffreddamento efficiente, il processo di MPA offre altre interessanti possibilità di applicazione. Molti materiali sono compattati dall’applicazione in modo tale che le superfici dei componenti possano essere lucidate a specchio senza problemi. La HMG soddisfa così anche le esigenze più elevate
Il MPA 42 unisce la costruzione additiva del materiale con la lavorazione di alta precisione I vantaggi del processo di MPA
Per la progettazione di stampi a iniezione, la combinazione
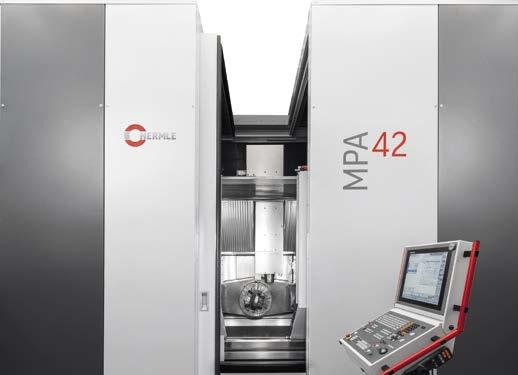
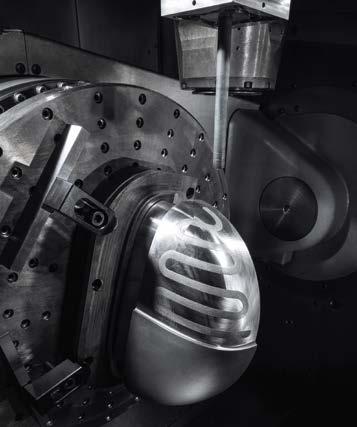
Dopo che i canali di raffreddamento sono stati riempiti con una polvere metallica solubile in acqua, si passa all’applicazione della polvere metallica
per gli stampi a iniezione.
Il processo di MPA può anche essere utilizzato per incorporare elementi funzionali come fili termici o sensori per il monitoraggio della temperatura della cavità in acciaio o rame e quindi integrarli nell’utensile, l’ideale per il controllo vario-termico della temperatura. Ma le possibilità della tecnologia MPA soddisfano anche al di là dello stampaggio a iniezione. “Nel caso di un ugello per colla dotato di elementi riscaldanti integrati, ad esempio, gli adesivi mantengono la temperatura di lavorazione ideale su tutta la larghezza dell’ugello. Il sensore nello strumento permette un controllo reale”, chiarisce Rudolf Derntl.
La forza della HMG sta nel sapere dove hanno senso le combinazioni di materiali, qual è il modo migliore di disporre i canali di raffreddamento e gli elementi funzionali e nella capacità di costruire utensili per stampi in un unico pezzo. “Non vendiamo macchine, vendiamo know-how”, spiega l’amministratore delegato. Il team di Ottobrunn consiglia i progettisti di stampi a iniezione, adotta i modelli 3D e ottimizza le parti stampate a iniezione prodotte successivamente con questo utensile per mezzo di un canale di raffreddamento, un elemento funzionale o una combinazione multimateriale. “Il punto è avere tempi di ciclo ridotti e qualità più elevate dei componenti che sono altrimenti difficili da ottenere con altre tecnologie”, fa notare Derntl.
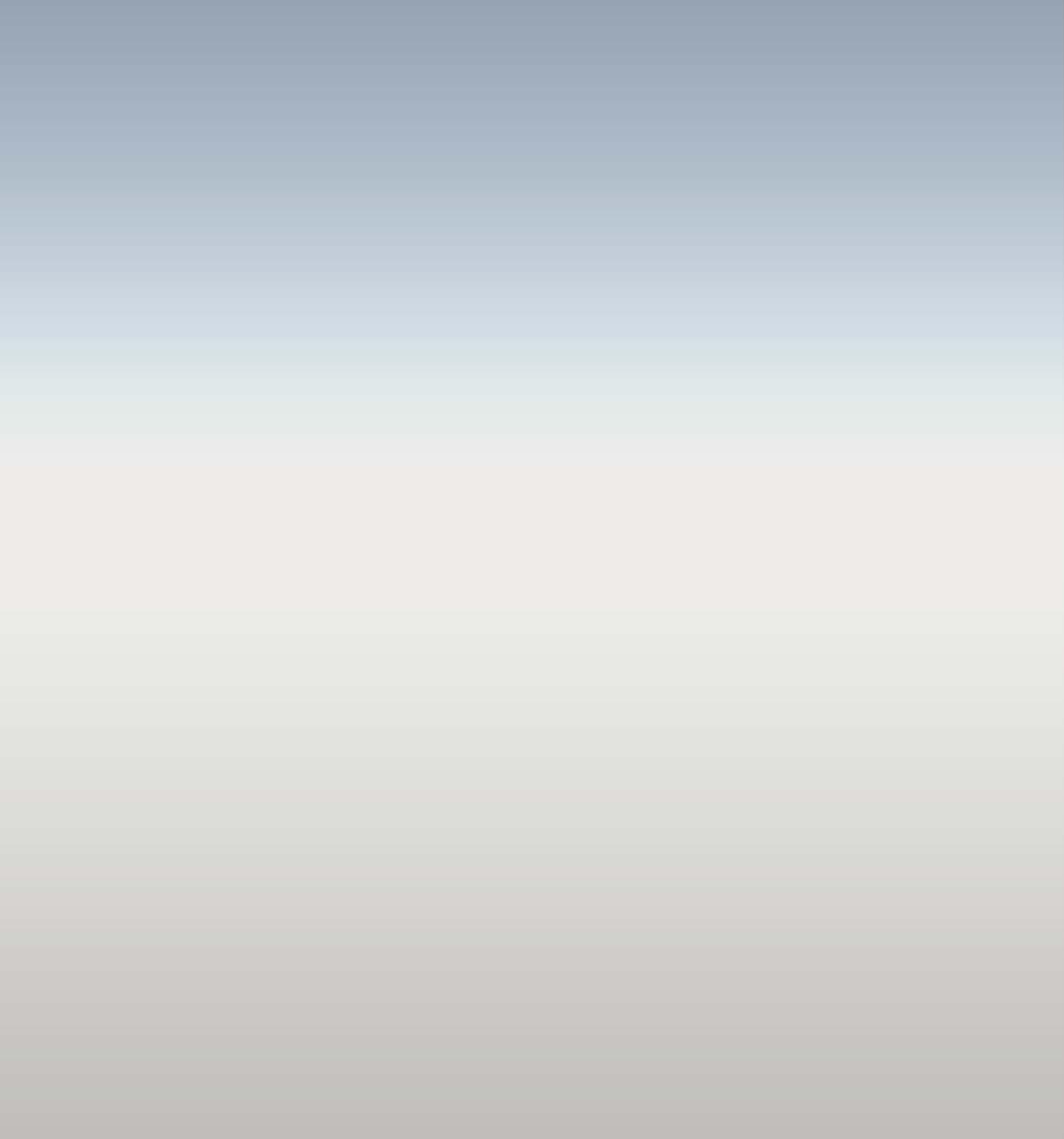
Un software ad hoc per l’applicazione e l’asportazione di materiale
Gli ingegneri applicativi usano il proprio software CAM per generare il codice per l’unità di comando. Ciò include non solo i movimenti del percorso, ma anche le quantità di polvere, le temperature specifiche e l’alternanza tra accumulo di materiale e fresatura. “Poiché nessun produttore CAD/CAM poteva mappare lo speciale processo alternato - fresatura, applicazione, fresatura - abbiamo scritto il software da soli. Questo significa che possiamo anche rispondere alle richieste speciali dei clienti in qualsiasi momento”, aggiunge l’amministratore delegato. Gli esperti sono praticamente seduti porta a porta. Una volta completato il lavoro preliminare, il cliente invia il suo pezzo grezzo alla HMG. “Il 95% delle volte, costruiamo su un prodotto semilavorato che il cliente può predisporre da solo sulla sua macchina fresatrice”, spiega il consulente dei clienti Oliver Müller. Così il componente arriva a Ottobrunn già con canali di raffreddamento fresati o tasche per l’applicazione del rame. Qui, il team HMG controlla la precisione dimensionale del pezzo grezzo e guarda se le specifiche di progettazione sono state soddisfatte. “Per esempio, non ci devono essere smussi sulle tasche. Abbiamo bisogno di bordi affilati per l’applicazione della polvere”, spiega Müller.
Il ruolo del calore
Prima che il processo inizi, il componente entra nella stazione di riscaldamento e viene portato a circa 300 gradi Celsius. Anche se il materiale non è saldato, il processo non sarà completo senza intervenire sulla temperatura: poichè sia il supporto, che la polvere metallica devono essere riscaldati per una migliore duttilità. L’energia per l’accelerazione della polvere viene dal vapore acqueo. Quando entrambi i componenti passano attraverso l’ugello, la polvere raggiunge la necessaria velocità supersonica. Per garantire che la temperatura rimanga costante durante la lavorazione, il MPA 42 riscalda il componente fino a quando l’ultimo truciolo viene rimosso. “In questo modo impediamo i gradienti di temperatura che stanno a indicare tensioni, crepe o distorsioni”, chiarisce Rudolf Derntl.
Nel processo di produzione, il materiale viene alternativamente applicato e lavorato. Dopo l’applicazione della polvere, i dettagli come le costole sottili, vengono fresati nel nuovo materiale, i canali di raffreddamento vengono riempiti con un materiale metallico solubile in acqua e chiusi di nuovo con uno strato di acciaio mediante applicazione del MPA. “Possiamo poi risciacquare il materiale di riempimento in un bagno d’acqua per ottenere le cavità desiderate”, spiega Müller. Con il getto di polvere si raggiungono tassi di accumulo da 200 a 400 centimetri cubici all’ora; con il rame, sono possibili quasi 1.000 centimetri cubici.
“Con la nuova macchina siamo al passo con i tempi e portiamo la nostra tecnologia MPA a un nuovo livello di prestazioni. È il cuore della nostra offerta di servizi”, sottolinea l’amministratore delegato, per il quale è importante mappare tutti i processi all’interno dell’azienda, quali consulenza, ottimizzazione e i test di fattibilità fino ai test dei materiali e al controllo finale della qualità. «Ciò ci rende agili e protegge il nostro know-how e quello dei nostri clienti».