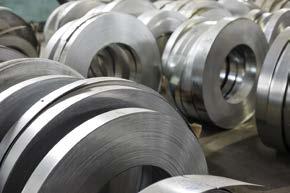
8 minute read
Un coraggio all’avanguardia
FOCUS ON
MITSUBISHI MATERIALS
La serie iMX: un innovativo sistema di fissaggio prodotto con una cura artigianale
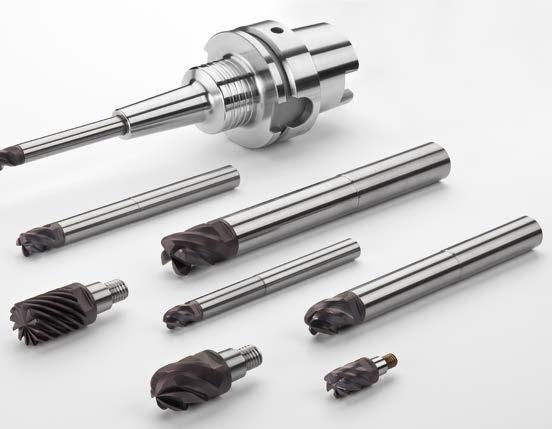

Un coraggio ALL’AVANGUARDIA
APPOSITAMENTE PROGETTATA DA MITSUBISHI MATERIALS PER SODDISFARE LA CRESCENTE DOMANDA DI VERSATILITÀ DA PARTE DEI CLIENTI, LA SERIE IMX È UN SISTEMA RIVOLUZIONARIO DI FRESE CHE COMBINA I VANTAGGI DEL METALLO DURO INTEGRALE E QUELLI DELLE FRESE CON INSERTI INTERCAMBIABILI. È COSÌ POSSIBILE OTTENERE GRANDI VANTAGGI IN TERMINI DI PERFORMANCE OLTRE AD UN RISPARMIO ECCEZIONALE, IN PARTICOLARE IN APPLICAZIONI CON SBALZI ELEVATI. IL COSTO DELLE FRESE IN METALLO DURO MOLTO LUNGHE È INFATTI RESO VANO DALL’USO DELLE TESTINE INTERCAMBIABILI. OLTRE A PERMETTERE LA RIDUZIONE DELLE GIACENZE DI MAGAZZINO, L’INTERCAMBIABILITÀ COMPORTA ANCHE UNA RIDUZIONE DEI TEMPI DI SOSTITUZIONE DELLA PARTE TAGLIENTE, DAL MOMENTO CHE LA TESTINA PUÒ ESSERE FACILMENTE SOSTITUITA ANZICHÉ ESSERE SMONTATA DA UN MANDRINO OPPURE DAL PORTAUTENSILI A CALETTAMENTO COME ACCADE PER LE FRESE INTEGRALI
Gli utensili con una testina in metallo duro che si innesta su di uno stelo in metallo duro sono solitamente costruiti con una parte dello stelo composta da metallo duro saldobrasata su uno stelo di acciaio. Tale metodo presenta un punto debole nella giunzione rispetto ad uno stelo in metallo duro integrale. Caratteristica peculiare della iMX è il doppio contatto tra testina in metallo duro e stelo, che garantisce sicurezza e rigidità quasi paragonabili a quelle di una fresa integrale. Ciò è possibile poiché il cono posteriore e le superfici di bloccaggio frontale della testina e dello stelo sono entrambi in metallo duro e solo la parte filettata è in acciaio. I vantaggi di questo metodo di bloccaggio, preciso e sicuro rispetto al convenzionale metodo acciaio su metallo duro, sono maggiore efficienza, grazie alla possibilità di poter adottare parametri di taglio più elevati, precisione migliorata, e, fattore principale, un’affidabilità eccellente. Gli ingegneri Mitsubishi Materials hanno ritenuto che la giunzione a doppio contatto fra le parti in metallo duro fosse un elemento essenziale per garantire questi benefici: la sua realizzazione ha richiesto tuttavia una tecnologia completamente nuova. Queste le parole di uno dei tecnici che hanno preso parte al processo di ideazione e sviluppo di questa innovativa serie: “L’idea alla base dello sviluppo iniziale era unire i vantaggi di frese integrali e frese a testina intercambiabili, per soddisfare in maniera ancora migliore le esigenze del cliente” spiega Takayuki Azegami. “Il meccanismo di fissaggio originale sosteneva la testina soltanto grazie al contatto con la superficie conica, soluzione che non garantiva la resistenza e la rigidità necessarie. In seguito a un lungo processo per tentativi, siamo giunti alla conclusione che utilizzando un doppio contatto delle parti di metallo duro per il meccanismo di fissaggio si sarebbero migliorate notevolmente le prestazioni.” Scoprendo che i filetti della vite in metallo duro tendevano a rompersi durante il serraggio, era chiaro che sarebbe stato necessario sviluppare una tecnologia che permettesse di inserire viti in acciaio nel metallo duro: il doppio contatto applicato alla serie iMX è stato ottenuto agevolando le proprietà di deformazione elastica delle parti coniche per creare un solido contatto tra la superficie anteriore della testina e lo stelo. Tuttavia, sebbene sia durissimo, il metallo duro è al contempo anche fragile, possedendo una capacità di deformazione elastica estremamente ridotta; esiste dunque un’elevata possibilità che lo stelo possa rompersi quando la testina viene serrata. Per risolvere questo problema il team Mitsubishi Materials ha utilizzato un metallo duro con un grado di durezza maggiore. Durante la realizzazione di un prototipo dello stelo, la sua superficie anteriore è stata rettificata gradualmente con
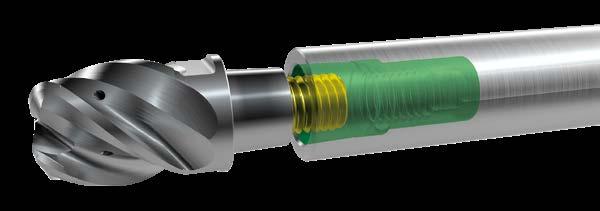
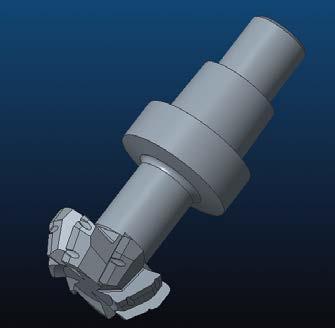
incrementi di 1 μm per trovare la tolleranza perfetta. Dopo la finitura dello stelo è stato condotto un esperimento di fissaggio, che ha confermato che la deformazione elastica permetteva al diametro esterno dello stelo di aumentare di pochi μm nello stato di doppio contatto. La produzione in massa del meccanismo di fissaggio con doppio contatto ha richiesto lo sviluppo di una nuova tecnologia che permettesse di impostare le rigorose tolleranze dimensionali necessarie, aspetto che allora era ritenuto impossibile da realizzare su larga scala. “È stato un processo per tentativi,” conclude Azegami, “Abbiamo selezionato diversi materiali per le parti in acciaio e metallo duro, e abbiamo condotto numerosi test sulle giunzioni e sulla trazione su centinaia di unità prima di riuscire a ottenere la resistenza richiesta. È stata una bellissima sensazione quando l’operatore addetto ai test ha finalmente approvato le prestazioni del prodotto”.
Qualità Made in Japan, fantasia Made in Italy
La vasta gamma di testine intercambiabili della serie iMX assicura maggiori prestazioni su un’ampia varietà di applicazioni: dalla lavorazione di leghe di titanio e resistenti al calore (HRSA), alla fresatura ad alta prestazione di acciai inossidabili, acciai al carbonio, acciai legati e acciai temprati. Questa versatilità è resa possibile non solo dal sistema di bloccaggio resistente e affidabile, ma anche dal grado di metallo duro rivestito Smart Miracle EP7020. Lo strato di metallo duro ad elevata tenacità e resistenza possiede un innovativo rivestimento (Al, Cr)N Smart Miracle, che può garantire una resistenza all’usura significativamente incrementata rispetto ai rivestimenti convenzionali. La superficie del rivestimento è inoltre sottoposta a un trattamento di lucidatura, che comporta migliorie delle superfici lavorate riducendo la resistenza al taglio e migliorando l’evacuazione dei trucioli. Questo rivestimento di nuova generazione garantisce prestazioni e vita utensile ottimali, specialmente quando si lavorano acciai inossidabili e altri materiali difficili da tagliare. La versatilità dell’iMX, originata con lo sviluppo nei sofisticati centri R&D nipponici, trova vasta applicazione
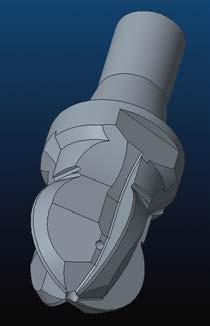
anche nel mondo dell’utensile speciale “Made in Italy”. Giancarlo Dossena, Manager del Dipartimento di Project Engineering di MMC Italia, afferma: “Siamo da sempre impegnati nello studio e sviluppo di utensili dedicati alle esigenze del cliente. Per definire strategie mirate all’ottimizzazione delle tempistiche, sia in fase di richiesta di offerta che di produzione, il nostro team di esperti è in costante collaborazione con lo stabilimento produttivo Mitsubishi Materials sito a Valencia, Spagna.” A suo parere, l’utilizzo del metallo duro originale Mitsubishi e le relative tecnologie produttive sviluppate dalla casa madre giapponese sono l’elemento chiave su cui puntare per fornire al cliente lo standard qualitativo che il mercato si aspetta da un leader di settore quale Mitsubishi Materials. Il controllo finale da parte del team dell’Inspection Department presso la sede milanese garantisce infine il rispetto delle procedure qualitative interne proprie di MMC. Grazie alla varietà di applicazioni delle testine intercambiabili, la serie iMX è diventata standard di lavorazione in pressochè tutti i settori industriali serviti
da Mitsubishi, e come già accennato è particolarmente indicata nella lavorazione di materiali tipo “superleghe” e nel settore automotive. Per approfondire le innovative soluzioni elaborate a partire da questa famiglia di frese, il sig. Dossena illustra due progetti recentemente realizzati dal team di Project Engineering italiano: “Uno dei progetti più interessanti che abbiamo sviluppato riguarda l’ideazione di una fresa sagomata per lavorazione cave sagomate su acciaio 18NiCrMo7 HRc 34. Con lo scopo di ridurre l’innesco di vibrazioni è stato utilizzato un adattatore cilindrico in metallo duro, portando così alla sostituzione di un vecchio progetto in HSS con il quale il cliente stava lavorando da anni. La lavorazione è avvenuta in ciclo quadro, con asportazione di sovrametallo di circa 1.5 mm.” Nonostante la lavorazione sia stata eseguita su macchine utensili “datate” e con scarsa rigidità, con parametri di lavoro non ottimali per il metallo duro, l’utilizzo delle testine iMX speciali ha prodotto benefici tali in termini di produttività e di risparmio economico, per cui, dopo la prima serie di campionatura limitata ad un solo profilo, il cliente ha completamente rinnovato il parco frese speciali, composto da quattro tipologie di profili. A seguire, anche un’azienda partner del cliente citato ha provveduto a sua volta alla sostituzione di tutte le frese speciali saldobrasate per una lavorazione simile. La seconda sfida affrontata dal team italiano ha riguardato la realizzazione di una fresa speciale sferica, impiegata nella semi-finitura e finitura alloggiamento sfere su acciaio 42CrMnMo7 bonificato. Questa lavorazione ha previsto l’utilizzo di un mandrino a calettamento termico HSK50 con prolunga standard iMX in acciaio, con doppia passata di finitura (la seconda a vuoto). Il risultato è stato un notevole incremento della vita utensile grazie alla riduzione delle vibrazioni, ed una riduzione del numero di utensili utilizzati determinato dall’incremento della vita del filo tagliente. Conclude il sig. Dossena: “Il metallo duro originale Mitsubishi, le moderne ed innovative tecnologie di ricopertura PVD e di superfinitura della superfice di taglio, unite alla elevata capacità produttiva delle macchine affilatrici a disposizione, fanno delle testine iMX speciali il prodotto ideale ogni qualvolta si richieda estrema precisione e tempi ridotti di setup, oltre ad una qualità pari al prodotto standard.”
Uno sviluppo continuo
La serie è stata recentemente estesa con l’aggiunta di due nuove geometrie di testina semisferica e di due nuovi gradi di metallo duro, EP8110 ed EP8120. Questi nuovi gradi, appositamente concepiti per applicazioni su acciaio temprato, dispongono di un nuovo rivestimento multistrato che vanta una superiore adesione al substrato. In questo modo si ottiene la migliore resistenza all’usura necessaria per la lavorazione dei materiali più duri. Le due nuove geometrie iMXB3FV e iMX-B2S completano la serie
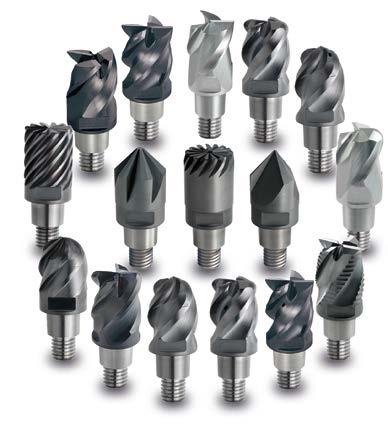
con testine semisferiche rispettivamente a 3 e 2 taglienti. La tipologia a 3 taglienti sfrutta una geometria sferica con elica a forte torsione, resistente alla scheggiatura, e un bloccaggio sulla parte conica posteriore che la rende idonea a lavorazioni stabili anche in applicazioni di spallamento profonde. La testina a 2 taglienti presenta invece una geometria sferica con un basso angolo di elica, che la rende perfetta per la finitura di acciai temprati fino a 65 HRC. Mitsubishi Materials si pone l’obiettivo di continuare a sviluppare tecnologie di fabbricazione di precisione per soddisfare le necessità dei clienti con prodotti di alta tecnologia. Oltre a garantire una riduzione dei costi di lavorazione e di magazzino, l’utilizzo degli utensili prodotti dagli artigiani nipponici assicura ai clienti affidabilità, efficienza ed alta precisione.