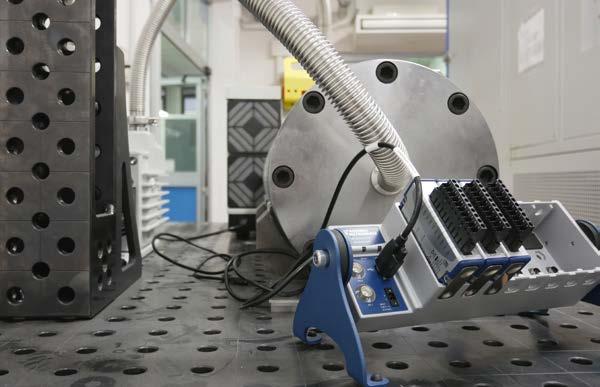
6 minute read
Nuovi controlli al servizio della
TEC EUROLAB
NUOVI CONTROLLI AL SERVIZIO DELLA FILIERA DELL’ADDITIVE MANUFACTURING
AD OGGI, NON È PIÙ POSSIBILE ANNOVERARE LE TECNOLOGIE DI PRODUZIONE ADDITIVA TRA LE TECNOLOGIE DI PRODUZIONE EMERGENTI. QUALSIASI SETTORE INDUSTRIALE È ORMAI COINVOLTO, CON DIFFERENTI VELOCITÀ, GRADI DI ADOZIONE E MODALITÀ PRODUTTIVE. SE SI PRENDE IN CONSIDERAZIONE L’INTERA CATENA DEL VALORE DELLA PRODUZIONE ADDITIVA, SONO EVIDENTI GLI SFORZI CHE SI STANNO COMPIENDO PER AMPLIARE LA GAMMA DI MATERIALI DISPONIBILI, PER RENDERE PIÙ EFFICIENTI E PRODUTTIVE LE TECNOLOGIE E PER FAR SÌ CHE I METODI DI SIMULAZIONE DIVENTINO SEMPRE PIÙ RAPIDI ED AFFIDABILI
DDiversamente, tutto ciò che riguarda la fase di controllo e convalida del processo di fabbricazione additiva e dei componenti realizzati è spesso, ancora legato a metodi di test e analisi concepiti e sviluppati contestualmente alle tecnologie di produzione tradizionali. La produzione tramite additive manufacturing richiede di ripensare anche le modalità e le tecnologie di controllo.
TEC Eurolab, grazie all’esperienza consolidata, alla sinergia con cui operano i diversi reparti e alla dotazione di strumentazione d’avanguardia, fornisce informazioni specifiche, esegue test conformi agli standard, accompagna il cliente nella valutazione dei risultati delle analisi e suggerisce eventuali miglioramenti da apportare al progetto o alle impostazioni dei processi di produzione additiva. Il supporto alle aziende inizia già in fase di pre-analisi, quando il progetto è avviato insieme al cliente, per proseguire nelle fasi di test e successivamente, con l’analisi dei risultati delle prove. Di seguito vengono esplorati due aspetti legati al controllo dei componenti prodotti in additive partendo da approcci radicalmente differenti: da un lato, il Centro Prove Funzionali opera per strutturare test ambientali-funzionali dedicati alla verifica pre-produzione di parti, dall’altro TEC Eurolab sta lavorando per rendere più efficiente il metodo di controllo tomografico con l’impiego dell’Intelligenza Artificiale.
Studio di metodologie per la verifica della funzionalità di parti prodotte in additive manufacturing.
La produzione additiva è in grado di realizzare componenti potenzialmente molto complessi.
A seguito del processo di stampa, una volta ultimate le operazioni di rimozione della polvere di stampa interna al componente, questo deve sottostare ad una serie di verifiche funzionali con l’intento di valutare se risulta in grado di soddisfare i requisiti definiti in fase di progetto.
Le prove che vengono solitamente richieste al Centro di Validazione TEC Eurolab sono:
• prove di pressurizzazione, sia statica sia dinamica, con l’intento di verificare la tenuta pneumatica o idraulica del componente (test di scoppio), oppure di sollecitare ciclicamente il componente, in pressione e temperatura per simulare le condizioni che verranno incontrate in esercizio.
A seconda della dimensione e del settore industriale, le pressioni e temperature possono variare da pochi decimi di bar e poche decine di gradi °C per prove in ambito biomedicale, fino a centinaia di bar e gradi per prove in olio, in uso principalmente nell’automotive e nell’aerospace.
• Prove di flussaggio, sia in olio sia in aria; in questo caso si procede alla selezione del miglior set-up sperimentale, solitamente costituito da pompe, camere climatiche dedicate, raccordi, valvole e sensoristica, in grado di campionare le grandezze fisiche (pressione, temperatura, umidità relativa, portata volumetrica o massica). • Prove di carico meccanico statico e dinamico con acquisizione delle deformazioni; si procede allo studio ed alla realizzazione di un idoneo test rig, ad azionamento pneumatico o idraulico, in grado di applicare un carico meccanico sulla parte. Mediante l’applicazione di estensimetri e sensori a contatto, diventa possibile monitorare in real time l’andamento della deformazione sul materiale. Le informazioni acquisite possono diventare dati di input per successive simulazioni e supportare il progettista durante le iterazioni di design del componente.
Intelligenza Artificiale al servizio del più grande centro di Tomografia italiano
La scansione per mezzo della tomografia industriale computerizzata permette di ottenere informazioni dettagliate sull’eventuale presenza di difettosità e geometrie interne, con la ricostruzione del modello 3D, l’estrazione dello stesso modello e il confronto dimensionale.
Uno degli aspetti critici dell’analisi dei difetti è che può necessitare di un team di tecnici la cui attività principale è visionare migliaia e migliaia di immagini, alla ricerca delle anomalie presenti all’interno del componente virtualizzato tramite tomografia.
La tomografia industriale è la tecnica diagnostica non distruttiva ideale per potere mappare completamente gli eventuali difetti presenti nel componente. Con particolare riferimento ai componenti prodotti in AM, le eventuali indicazioni presenti possono essere molteplici, spesso in posizioni difficilmente identificabili con altre metodologie diagnostiche e la cui valutazione tecnica può risultare spesso complicata.
L’intelligenza artificiale viene in aiuto proprio in questi casi, nei quali un computer può svolgere più efficientemente un lavoro ripetitivo rendendolo oggettivo.
L’intelligenza artificiale
L’Intelligenza Artificiale può essere definita come un insieme di tecniche che permettono di risolvere problemi o di svolgere compiti e attività tipiche della mente e delle capacità umane. In informatica è la disciplina che si occupa di realizzare macchine in grado di prendere decisioni autonomamente sulla base di un problema circoscritto, imparando autonomamente dai dati forniti tramite tecniche di deep learning e machine learning.
L’obiettivo del progetto è quello di sviluppare una piattaforma di Intelligenza Artificiale per l’analisi automatica delle immagini rilevate dalla tomografia industriale computerizzata allo scopo di identificare i difetti di fabbricazione su un componente. Per fare ciò è stato progettato e realizzato un software dedicato, che riceve in ingresso le immagini rilevate dalla tomografia industriale. La AI opportunamente addestrata processa in automatico le immagini e genera un report con indicate una serie di
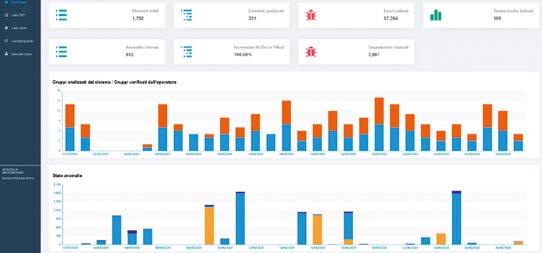
Tool di training
informazioni statistiche tra cui le immagini che presentano anomalie. L’operatore attraverso una dashboard di controllo (raggiungibile via browser) avrà la possibilità di visualizzare il report prodotto per ogni singolo oggetto analizzato.
I risultati
Dopo un lavoro di raffinamento del modello di deep learning è stata raggiunta una precisione nell’identificare e dettagliare le anomalie ad un livello di accuratezza superiore al 95% con punte del 99%.
L’operatore attraverso il software fornito ha la possibilità di validare le anomalie identificate dall’Intelligenza Artificiale o inserirne di nuove. Queste anomalie vengono elaborate in automatico dal sistema che periodicamente effettua un re-training per il miglioramento continuo delle performance.
Le anomalie vengono identificate in qualunque posizione e in qualunque dimensione o forma. È stato raggiunto l’obiettivo primario di allineare il modello al know-how dell’operatore e ora, grazie alle dinamiche del deep learning, il modello identifica anomalie non conosciute in precedenza e fa predizioni su anomalie oggettivando il controllo che non è più basato sul giudizio dell’operatore ma su un algoritmo.
Il modello ha quindi acquisito una percezione del problema dell’individuazione delle anomalie molto vicina a quella di un operatore con esperienza e riesce ad affiancare con successo il lavoro di analisi del tecnico specializzato riducendo i tempi di analisi.
La breve panoramica riportata mostra solo alcuni dei servizi offerti per la caratterizzazione globale di un componente realizzato in additive presso i laboratori e i centri di testing di TEC Eurolab.
Futuri sviluppi si concentreranno sempre più sull’implementazione di tecniche per la failure predicition del componente, permettendo di raccogliere sin dai primi test svolti, informazioni utili per svolgere modifiche progettuali e re-design. Le tecniche diagnostiche dovranno interfacciarsi non solo con il controllo qualità in produzione, ma anche con i reparti di R&D ed ingegneria, integrando sempre più il controllo predittivo sin dalle fasi di progettazione della parte.


