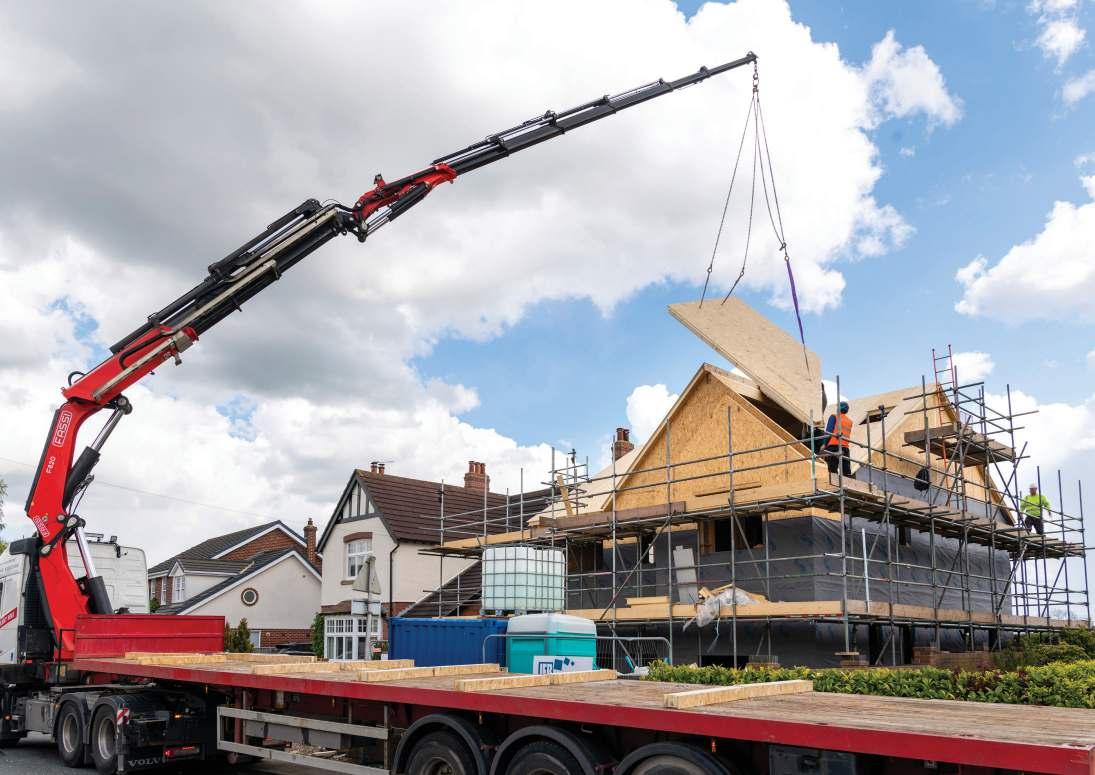
8 minute read
An introduction to building with structural insulated panels
An introduction to Building with SIPs
WHAT ARE THEY?
Better known as SIPs, structural insulated panels are a preengineered building system, which was developed in America in the 1930s and first introduced to the UK in the 70s. The panels are made up of two parallel faces – usually oriented strand board (OSB) – sandwiching a rigid core of expanded polystyrene or injected urethane. These are the most common in the UK but other variations of facing materials and cores exist. The stressed skin panel makes it exceptionally strong, and high levels of insulation can be achieved in thinner wall thicknesses than other forms of construction.
SIPs provide a fast, efficient way of building walls, requiring less timber with fewer studs compared with a timber frame. They have very good thermal performance and form a strong, lightweight structure which is fast to erect, thanks to the large components. They cost slightly more than conventional timber frame with insulated walls and uninsulated roof trusses, but the faster build speed, reduced waste, lower labour costs and less need for on-site machinery can offset the extra expense. Energy-saving benefits should also be considered.
SIPS
Manufactured off site, SIPs can be used in a wide range of applications, and are quick and easy to erect, usually with a crane.
APPLICATION
SIPs can be used as the inner skin of a cavity wall, as a self-supporting single-skin structural wall, in place of timber frame or blocks, and as a pre-insulated roofing structure. They can be used in walls and roofs, creating ecologically friendly and energy-efficient buildings.
Suitable for new builds and home extensions, SIPs are commonly used for garden buildings and garages, as well as making ideal infill panels for other structures, such as oak, steel or concrete frames.
They are perfectly suited for roofs for new builds, extensions and renovations. The panels arrive pre-cut, with insulation already fitted, and span from wall to ridge beam – usually unsuppor ted. This means that the roof space can be left completely open to be used as fur ther accommo dation, storage or as a vaulted ceiling.
SIPs are very flexible and can be used with any external cladding, including brick, render, weatherboarding and aluminium. They can also be roofed with slates, tiles or metal coverings. Internally, the panels may be simply finished with plasterboard and a skim coating (with service cavities where needed) so wet trades
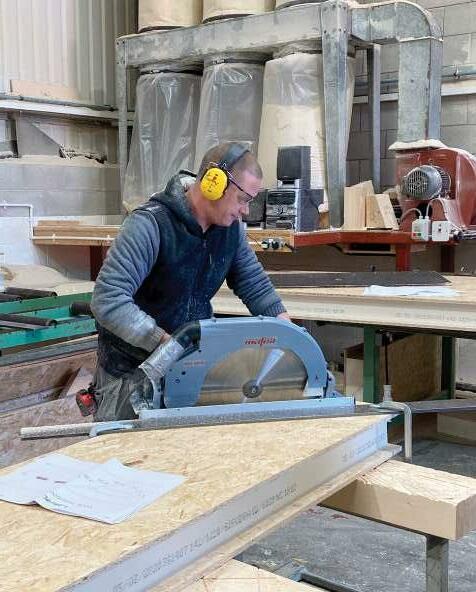
are kept to a minimum and build times reduced.
A SIPs house is very airtight so it won't require much in the way of heating due to the energy efficiency of the building. SIPs are particularly suited for air source heat pump installations, and mechanical ventilation is strongly recommended.
THE PROCESS
House designs can usually be modified to suit a SIPs system. It is sensible to choose a designer who has worked with SIPs and understands the structural implications of a panel system, or use a package company.
Manufactured off site as blank 1.2m-wide panels, with various standardised height options, SIPs panels are cut to size and the openings formed. Designing a house using standard SIPs sizes – usually 1.2m by 2.7m – will be the most cost-effective way to use the system. Utilising a 1.2m grid will reduce the number of cut panels and limit waste, as well as minimise the cost for a fabricator to cut panels to fit.
SIPs can also include service ducting, which makes wiring easy but means that the electrical layout will need to be planned at an early stage. Alternatively, services can be run through internal partition walls, with wiring passing through the cavity between the panel and internal plasterboard, or through a double layer of plasterboard. Including a service zone means that you can decide on the services distribution at a later stage.
Manufactured in the factory the panels will be delivered on site where they can be erected – often by the same company. Some SIPs companies offer a full-build package while others rely on the selfbuilder or project manager to take responsibility for the foundations and fitting-out stages.
Be sure to follow the manufacturer’s recommendations for sealing joints properly. Edge openings, such as window reveals, are lined with inset timber to allow frames to be easily fitted, and floors may be sandwiched between upper and lower walls or attached with joist hangers.
Most foundations are suitable, but the slab should be accurate and leveI, within tolerance, and onsite access should be available for a suitable crane or telescopic handler if required. Panels are joined together, and window and doors are installed on site.
Lightweight wall cladding like cedar, render, rainscreen and brick slips will require additional support to form ventilation spaces, while finishes such as brickwork and stone will typically require foundations to carry the increased weights.
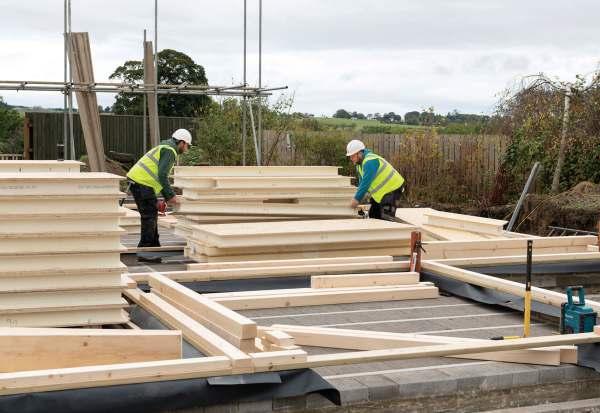
PICTURES
SIPs are made in the factory and are relatively easy to handle on site. They can be put in place quickly to achieve a weathertight shell and achieve unrivalled levels of airtightness and insulation.
THE BENEFITS
l SIPs offer high levels of insulation, structural strength, and airtightness, with thinner wall sections. They can also increase the available roof space, thanks to their truss-free construction, enabling rooms to be created in the roof. . l By combining the stages of conventional timber-frame construction – framing, sheathing and insulation – into a single unit, a structure can be erected quickly and with less specialised labour. A crew of two, with no special equipment, can easily install smaller panels, while larger panels may be erected with the use of a crane. l SIPs are relatively lightweight, at around 25kg/ sqm, and may only require a reduced foundation specification. The shell of a typical house can be erected within a matter of days. l SIPs don’t require particulary good site conditions (except for wind) and the speed of erection can offer savings on skip hire, scaffolding and finance costs. l The size of the panels makes them less likely to be stolen from site than more conventional building materials. l The panels are exceptionally strong, and high levels of insulation can be achieved in thinner walls than other forms of construction. In timber-framed buildings the spacing of vertical timber wall studs is usually at 600mm centres, whereas with SIPs panels these are usually 1,200mm, depending on point loads. SIPs use insulated splines to provide a continuation of the insulation core. Choosing deeper panels will increase energy efficiency, 2 and U-values as low as 0.10W/m K can be achieved. l SIPs are ideal for meeting the stringent energy-efficiency requirements of Passivhaus construction. A Passivhaus build is airtight and has high levels of insulation, with little need for home heating and cooling. l Radiators, kitchen cabinets, light fittings and other fixtures can be easily attached to the continuous OSB surface, with little or no additional support required. l The OSB and insulation core are resistant to attack by mould and microbes and have no food value to vermin. l The jointing techniques in SIPs buildings mean that sound transmittance between rooms is reduced.
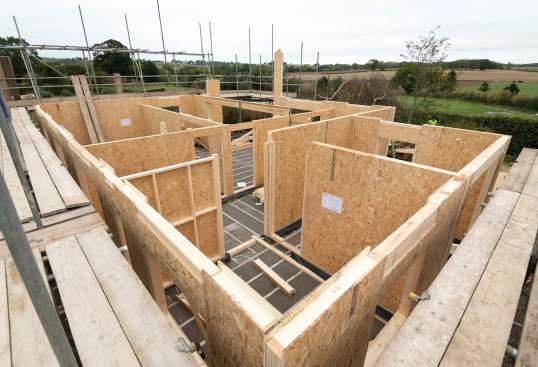
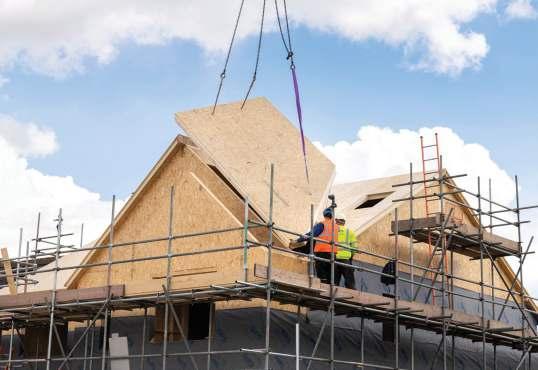
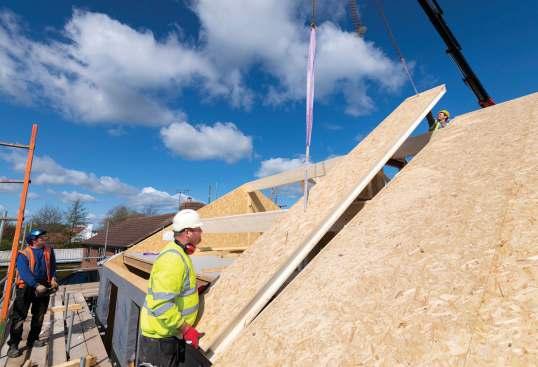
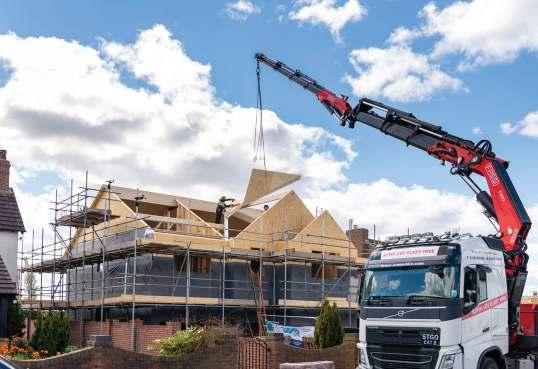
6 top SIPs tips
Building your own home can be a daunting prospect but to get you started and help you along the way, here are a few pointers from SIPs expert Ian Clay to make sure your self-build experience is a good one.
1: Do your product research
You may have already decided to build with SIPs but remember, not all SIPs systems are the same.
There are plenty of systems on the market, so make sure you understand the composition of SIPs and the benefits the different options offer.
Look at thermal qualities, the jointing system - which is key to creating an airtight envelope – certifications and fire performance, strength and stability. Consider a recognised brand such as the Kingspan TEK Building System for all-round quality. 2: Weigh up the long-term benefits
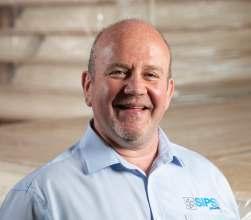
Budget is key with any self build and it’s easy to lose sight of the long-term benefits of SIPs. Consider the speed of construction and short build programme, reduced on-site labour and plant costs, the additional floor space, ie a habitable roof space, and the increased value it brings. Look at the lifetime cost savings of a thermally efficient SIPs home and, most of all, take comfort from living in a sustainable home that you’ve built yourself. 3: Find a credible supplier
Just like the variety of SIPs systems available, there are many suppliers offering different levels of service and product.
Your supplier should demonstrate unrivalled knowledge of their product, offer a comprehensive package of design, supply, installation by certified fitters, and be members of the Structural Timber Association (STA). Ensure they are transparent in their costings and capabilities. 4: See if you can arrange a factory visit
After you’ve made your shortlist of suppliers, visit their factories and meet the teams.
You will quickly get a feel for the organisation and see how your new home will be designed and fabricated.
Also, ask to see examples of previous work and speak to past clients about their experience with the company. 5: Be ambitious with your design
There are no limitations to SIPs designs and homes don’t have to be boxy and boring. If you, your architect or SIPs designer has vision then almost any thing is possible.
Consider adding value to your project with a ‘room in the roof ’ or double your room height by leaving the roof space open to the apex. 6: Plan upfront
It’s important to work with your provider on some upfront thinking.
This will ensure that window and door openings are suitably positioned, MVHR duct location is identified to enable correct alignment of floor joists, and any other technical complexities are identified early on.
It’s a lot of work upfront but it will ensure value engineering, precise fabrication and save time, hassle and possibly additional costs later on. Ian Clay is managing director of SIPS@Clays: clays.com