
13 minute read
Guide to oak frame construction
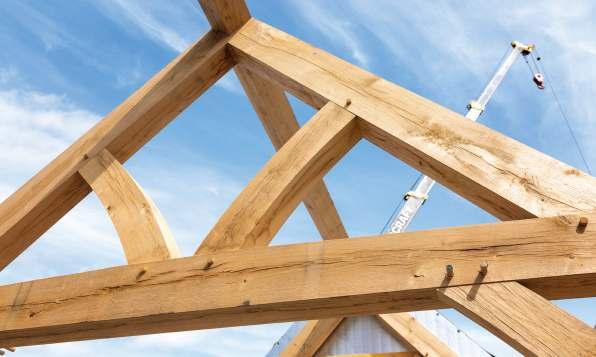
A guide to Oak f rame constr uct ion
The time-honoured tradition of oak-frame construction has never really gone out of fashion and is as popular as ever with selfbuilders, thanks to recent energy performance innovations. Period halftimbered black and white houses have long been admired for their beauty and structural integrity, having survived for centuries, with some dating back to mediaeval times.
Building a new oak-framed house offers the perfect compromise – the chance to combine modern building materials with the instant appeal of exposed beams and timbers. Modern technology allows designers to utilise the beauty, strength and integrity of the frame to its full effect, creating open-plan living spaces without the need for internal structural walls.
Oak is a slow-growing wood with a tight grain which makes it durable, strong and a natural insulator. In a fire, a protective layer of charcoal forms around the outside of a beam, delaying damage to the core, and most oak frames are sturdy enough to withstand the ravages of
OAK FRAMES
Often lasting more than 200 years, oak is a perfect building material: sustainable, durable and a natural insulator. a tornado. A lifespan of at least 200 years is achievable for a well-designed oak frame and, even then, there is the chance to continue the tradition of reusing the timber for other purposes when a house has had its day. Ultimately, oak will biodegrade when eventually redundant, making it the perfect natural building material.
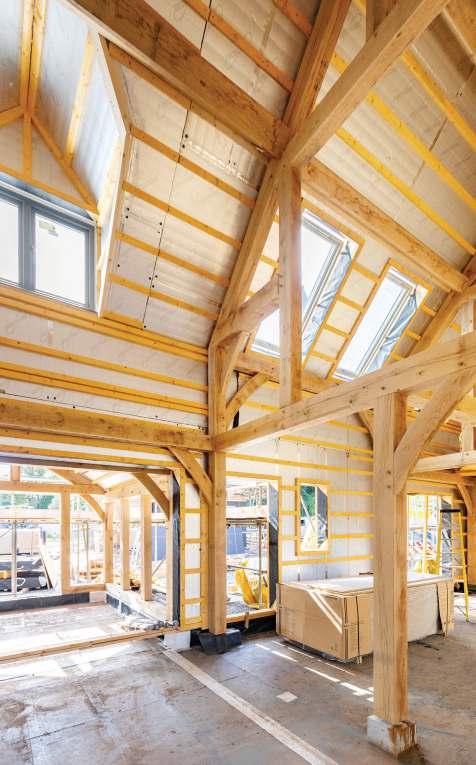
MODERN TECHNOLOGIES
While the design and carpentry of oak frames were already highly developed by the mediaeval period, modern technologies such as insulation, glazing and frame infill techniques now far outperform their historic counterparts. Oak’s versatility can be exploited in great open-plan spaces, soaring vaulted ceilings, galleries and atriums, adding to the sense of drama.
If choosing to build in oak it is important to use an architect who is familiar with the method, or at least to consult an oak-frame specialist early on. Traditional oakframe homes are created around a series of rectangles (bays), which make up the base structure (box frame). A good designer will help you to recognise how to make the most of your structure, the best orientation and the size of the bays and spans. They will also work out the loads, as well as the scale and proportion of the rooms. The design will also be affected by roof pitches – between 42.5 and 52.5 degrees – with the most common being 45 degrees.
It is worth noting just how flexible the design services offered by oak frame companies can be. Many selfbuilders assume that they will have to build one of the standard house types shown in their brochures but these tend to be a sales aid designed for guidance rather than an indication
PRINCIPAL RAFTER
QUEEN POSTS WIND BRACE RIDGE
COLLAR WAISTED KING POST STRUT
GIRDING RAIL
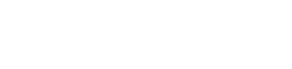
SOLEPLATE GLAZING STUD TIE BEAM CHAMBER BEAM
BRACE
of the available options. Many standard designs can be adapted to create individual houses, and in-house designers and architects can produce bespoke plans and elevations, including detailed drawings for Building Regulations.
It is possible to build a very contemporary home around an oak frame, and if a structural engineer specifies additional steelwork to reinforce the building this can be concealed within an oak beam. Alternatively, traditional frames are based upon the design and style of the vernacular oak frames found in English towns and villages. There is no county in England without examples of oak framing and this can be extremely useful in persuading local authorities to grant planning permission.
A popular option is the barn-style oak frame, which combines the contemporary and the vernacular. The essential difference is that the beams are not generally exposed externally. These buildings invariably have a more openplan feel, with fully vaulted roofs, and the heavy oak frames are well suited to accommodating large areas of glazing.
Some package companies will undertake everything from gaining planning permission and erecting the frame to organising subcontractors and completing the entire project on your behalf. Others will simply design, supply and erect the oak frame, leaving the selfbuilder responsible for organising everything else.
FRAMING
Some oak-framing companies continue traditional framing techniques, passed down through generations, with hand tools still very much in evidence. Others favour fast, computer-controlled cutting machines.
The oak is used soon after it is felled so that the green timber is easy to cut and work into the desired shapes. Green, unseasoned oak is traditionally assembled with classic wooden pegged mortise and tenon joints, and the timber continues to contract – tightening the joints to give a uniquely strong structure which will last for centuries.
Most companies make up the entire frame at their framing yards prior to dismantling it ready to be delivered and re-erected on site. The finished building will also need to incorporate modern materials such as air barriers in order to meet Building Regulations.
It is important to find out the lead (waiting) time
for an oak frame because these can vary enormously depending on how busy the suppliers are, frame This is a estimating stage set of drawings for discussion only.size, design complexity and other issues.
PURLIN CONSTRUCTION
SLING
WALL PLATE
JOWL/BAY POST
DIAGRAM
- - - DRAWINGS PRODUCED BY
T.J. Crump Oakwrights Ltd
The Lakes, Swainshill,
Hereford, HR4 7PU +44 (0)1432 353353 enquiries@oakwrights.co.uk © This drawing, its contents, and all information contained therein is protected by Copyright. It may be used once only for its intended purpose under a contract with T.J. Crump Oakwrights Ltd, but not for any other use or purpose. This drawing is for Planning purposes and does not constitute a construction issue drawing. All setting out dimensions and levels are indicative and are subject to detailed site survey and site conditions. The Client and their agent are responsible for ensuring that Building Control and construction drawings are carried out following Planning approval. Scaling from this drawing is for Local Planning Authority information only. CLIENT
Mr& Mrs XXX SITE ADDRESS
XXXXX PROJECT
New Dwelling DEPARTMENT
ESTIMATING DRAWING FRAME ELEMENTS SCALE N/A DATE DRAWN DATE ISSUED
XXXXXXXX XXXXXXXX DRAWN CHECKED XXX XXX DRG. NO. REV. 190XXX -01
Like all timber-frame construction, the foundations must be accurately completed before the frame can be delivered, so ensure you leave plenty of time for unforeseen problems at this stage. Oak frames need a level surface, and poorly built foundations are a frequent problem for all types of timber frame, so it pays to employ experienced groundworkers. Make sure that site access will not be a problem for a crane, which may be required to lift the huge trusses and cross sections from the lorry. Erecting the frame will then usually take between a few days and several weeks to complete by a specialist team. Once the frame has been built the timber stud infill panels and insulation can be fixed in place, and the shell clad with materials such as brick, stone, weatherboarding or render. Structural insulated panels (SIPs) are a modern alternative to a timber stud wall, manufactured in a controlled environment and shipped to site ready for erection. They consist of an inner insulating core of expanded polystyrene The main (EPS) sandwiched between two outer skins of oriented strand components of board (OSB), and provide excellent thermal efficiency.an oak frame. Whether renovating or building from scratch, it PICTURE is recommended that traditional materials are used OPPOSITE such as lime mortars and plasters, which allow for Oakwrights' minor building movement. Hydraulic lime mortars are show home particularly useful in timber-frame buildings because outside their excellent vapour exchange properties minimise rot Hereford and damp while providing good weather resistance.where potential It is possible to build externally exposed oak frames clients can that meet and exceed Building Regulations. Additionally, stay overnight encapsulation systems have been developed which to experience completely insulate the frame externally, minimising the what it’s like to cold bridging effect of the timbers and providing a draught-live in an oakframe home. free environment. Several oak-framing companies have developed their own prefabricated encapsulation systems and most well-made, exposed oak frames – with the proper detailing – perform exceptionally well on airtightness tests. Oak, unlike many other timbers, does not require preservative because the wood is naturally resistant to insects and weathering, although the frame can become marked from the natural tannin in the wood. These marks and other stains from the building process can be removed by sanding or using oxalic acid once the frame has been built.
MAINTENANCE
Untreated oak weathers to a silver-grey colour externally, while remaining deep golden inside. As the oak seasons it hardens to a nail-bending density, so carpenters tend to work the wood while it is fresh and unseasoned. Oak is described as ‘green’ when it has been felled only a couple of years and the timber still has a high water content and is not dry in the middle.
It then takes between five and 10 years for an oak beam to dry out completely and season, and this process often results in shrinkage and movement – a factor which can alarm homeowners. As the oak dries and shrinks, the process creates minor splits or ‘shakes’, which are all part of the building’s charm but can cause a few creaks and groans to emanate from the timbers. Oak can be exposed externally without any need for artificial coatings and is extremely resistant to insect attack. For wood to rot there
must be a serious damp problem, as moisture passes through wood unless covered in materials such as cement render.
COSTS
Oak framing is often seen as an expensive building option, with oak costing at least one-third more than other timbers. In general, though, oak construction will only increase the overall cost by between five and 10 per cent and the simpler the design, the less expensive the frame. Resale values are high and there are ways to reduce costs and ensure that you get maximum value from the exposed frame without breaking the bank.
One option is to combine this form of building with a less expensive alternative, such as blockwork and areas of softwood framing. By building just one section of a house using an oak frame you can benefit from all the advantages of the wood in prominent areas like vaulted hallways and sitting rooms. Known as ‘hybrid’, this method is ideal for those on a more limited budget who wish to feature some oak within their home.
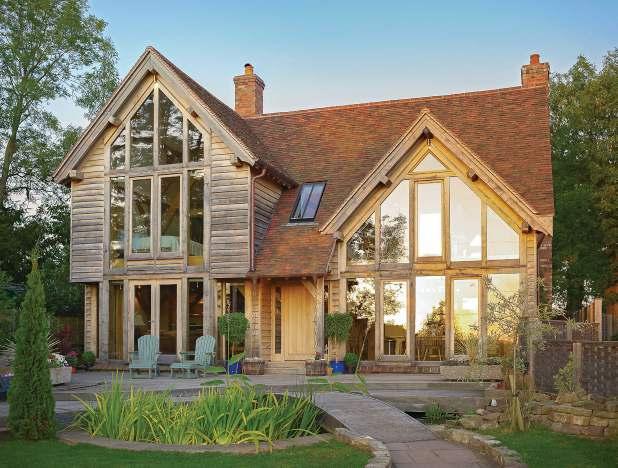
8top T IPS
By Helen Needham RIBA ARB Architect, head of architecture at Oakwrights 1. MAKE A WISH LIST Refine your ‘wish list’ of spaces – in words, or even your own sketches – what are the essential components of your brief? This will be room uses; number of bedrooms etc, and may also extend to what you have always desired from your oak-framed home, such as wanting a galleried landing, a picture window, a wow staircase that is framed by the oak, or something designed around pieces of furniture or paintings you own. Whether big or small, your wishes matter and drive the project – this is your opportunity to create your bespoke dream home.
2. CHOOSE A STYLE Oak is a really versatile product, bringing quality and character to a new home. The exteriors are extremely adaptable with a variety of materials and proportions – would you like a traditional, country, or contemporary appearance? You may have seen barn, cottage, farmhouse, single-storey, or other styles that catch your eye. Collating examples helps to channel the design and allows your architect to understand your tastes, so keep those magazine cuttings, and create that Pinterest board.
3. SET A BUDGET Do you have a build budget that you need to work to? A design should be tailored to this. Or do you need guidance? Again, options can be given to refine this for you. Indeed, monitoring the build budget throughout the whole process is vital – you want to ensure that what is designed is buildable when you arrive at that exciting stage. Buying a standard design from a range will help you to budget better and save on design fees. A turnkey service will allow a professional project manager to manage your build and your budget. 4. USE A SPECIALIST Working with an oak framing specialist who can guide you through the important planning and technical design steps is essential. They will ensure the layout and design will work well for an oak frame and is buildable. You need to get on well with your design team, to trust that they listen to your wishes, and also to ensure they are professional and experienced, and will support you throughout. Understanding their processes and what they produce is essential – will they be creating 3D software images at the early stages for you to visualise your design? Will they be liaising with oak frame and encapsulation designers at the concept stages? This is all key to ensure the services and expectations of both parties are clear.
5. GET THE PLAN RIGHT The position of the main habitable spaces and stairs is essential, while carefully considering those equally important ‘working’ sides of the house – for ancillary areas such as side entrances, boot rooms, utility etc. Oak may not be necessary for these sides and can be built in structural softwood. As a rule, the clear span between oak posts should be no more than five metres - though with additional posts or steels, larger spans can also be achievable. In open-plan areas, the oak framing works perfectly as it creates zones and visual separation. Vaulted spaces and fully exposed oak framing can make the most of the aesthetic appeal of the oak. We can start to divide and ‘sculpt’ spaces to give a frame the right amount of proportion and balance on the eye within a room. The oak frame designers provide creative ideas using terms such as cruck, arch-braced collar frames, scissor trusses, and dragon ties! 6. SIGNING-OFF STAGES For any build to go well, a good design is paramount. A good design team has the ability to design any style, shape, or size of house. At Oakwrights, once the design is agreed we also handle the planning submission. When planning is approved by the local authority we then start the process with the finite oak framing details with our frame designers to create a buildable and costeffective frame. From the early stage we are considering the next technical design stage – so, for example, the soil pipes are considered alongside the oak frame. It is important that each of these stages is signed off by the client.
7. QUALITY IS KEY Selecting the right manufacturer and product for your build is important. The building fabric is key to the future comfort of your home and will also affect planning and Building Regulations – building to a green agenda will assist with both. Insulation and airtightness are essential parts of the construction, reducing energy consumption and lowering heating costs. A post-and-beamstyle home, ie with the main oak structure on the inside, wrapped with an insulated encapsulation system, will create the most energy-efficient method. Our wraparound encapsulation systems will encase your bespoke frame, using either our Wrightwall (PIR foil-backed and mineral wool insulation) or the Wrightwall Natural (recycled newspaper option). The amount and orientation of glazing also need to be carefully factored in. You may even go on to require Passivhaus levels (we built the first two and only oak-framed Passivhaus buildings in the UK).
8.THE SYSTEM How the frame is produced is also important – ensuring there is precision and quality control in the workshop. Understanding how a building will be constructed can enable you to save time and cost at a later stage. The off-site production of an oak frame can allow you to press on with the enabling works, while the oak frame is being designed and constructed under workshop conditions. The structural oak frame could take as little as a week to erect. With the encapsulation wrapped around it you could have a dry shell within four to six weeks.
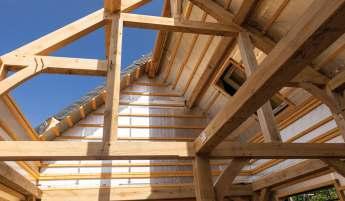