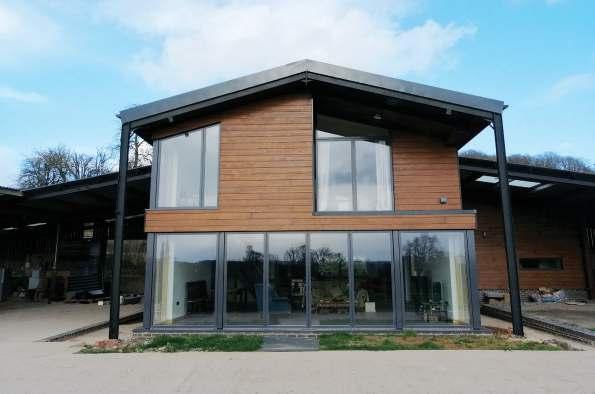
4 minute read
Meeting the challenge
When farmer Nigel Box approached Frame Technologies to convert his barn into a family home, the Herefordshire company was ready to take on the challenge.
rame Technologies used an energy-
Fefficient timber system to convert a steel-framed agricultural barn and concrete yard into a sensitively integrated residential dwelling. Nestled in an eightacre field for grazing livestock, the stunning new three-bedroom family home is idyllically located in beautiful Herefordshire countryside.

Planning permission for the barn conversion was approved under Permitted Development Part Q. Frame Technologies has created a modern structure that blends into its agricultural setting.
With any barn conversion, there are specific challenges to consider as working around an existing structure can be tricky, especially as they are not originally intended for human habitation. Most farm buildings are not insulated either, so significant work needs to be done to upgrade their thermal performance.
On the plus side, these structures can offer unique features, such as double-height internal spaces, beautiful open-plan living, and fantastic rural locations, which make them so aesthetically pleasing.
With the Leadon Dale project, farmer Nigel Box used the barn for winter housing of his beef cattle and hay storage. Initially Nigel was concerned because it looked unlikely that he would get planning permission for an on-site residence. However, under Permitted Development Part Q for change of use of an existing agricultural building to a residential dwelling, planning permission was granted.
Adopting a fabric-first approach to ensure optimum energy efficiency, Frame Technologies created a unique timber solution to the planning requirements which stipulated that the existing steel framework had to remain in situ and the building could not be enlarged.
Using integrated architectural drawings along with Nigel's additional design requests, Frame Technologies has created a structure that blends into its natural surroundings and retains its agricultural heritage, thanks to an innovative timber system and cement timber-effect external cladding.
Careful consideration had to be given to the home entrance to take into account the daily farming and agricultural activities. The new timber dwelling incorporates undercover car parking for protected access to the dwelling, as well as a downstairs shower room at the immediate entrance.

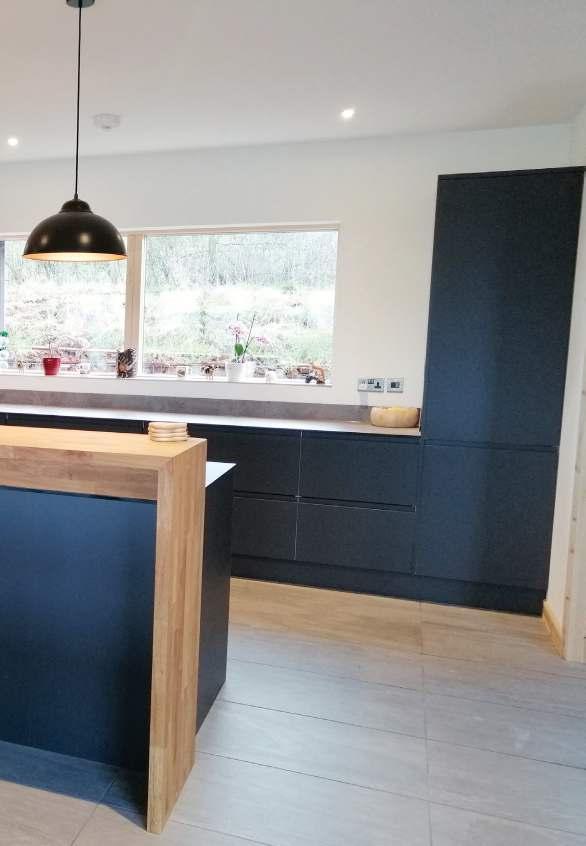
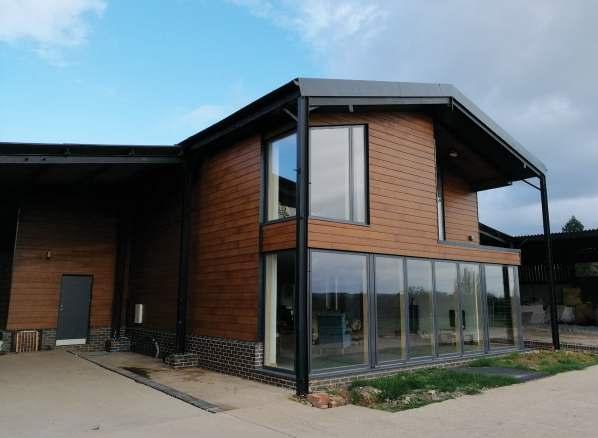
THE INTERIORS The new home has a distinctly modern look and offers year-round comfortable temperatures, thanks to the airtight structure, high levels of insulation and solar gain from south-facing glazing.
THE BUILD The original steel frame has been retained, with Frame Technologies' Tech Vantage System used to provide an insulated airtight shell.

To improve storage, two custom loft spaces have been built into the roof voids to the left and right of the main living area.
The barn was built using Frame Technologies’ unique Tech Vantage System, consisting of a 140mm panel with glass mineral wool insulation that is tightly packed between a sheathing board and a wood fibre board. Inside the panel, a 25mm service batten is nailed to the OSB. Based on a breathable wall principle, the system uses natural insulation to deliver a wall U-value of 0.14 W/m2K. The system’s excellent thermal properties work well with the impressive solar gain from extensive south-facing glazing.
To reduce cold bridging, the wall is sheathed in 20mm wood fibre board, which is fixed to a 140mm timber stud with full-fill insulation. A 9mm OSB is fitted internally with site-fitted PIR insulation, with tapered joints, a 25mm x 50mm service batten and 15mm plasterboard. The floors use 254mm top-hung metal web joists, instead of traditional ring beams, to reduce shrinkage and improve thermal performance through the floor zone.
Optimal airtightness has been achieved through a timber system that includes membranes and tapes for sealing joints or apertures around building services; airtightness detailing in critical areas such as intermediate floor-to-external-wall panels; battens to form service zones and reduce the need for penetration through the barriers; and OSB sheathing on internal faces of external walls that were then taped.
Following a site measure and survey, it became apparent that the original slanted steel framework of the barn was twisted. Working with Frame Technologies, Nigel uprighted the building based on structural details. The next challenge was to erect the wall panels and integrate the existing steel trusses of the old building with the roof zone of the new frame. This was achieved using an engineered rafter, sheathing and roof sheets that matched the existing design.
The structure was made weathertight within days, and with project planning, efficiency was maximised, on-site risks were minimised and internal works could run parallel to external finishes. Not only is the timber system environmentally friendly, recyclable and waste efficient, it is also lightweight, requiring only simple cost-effective foundations.

“When we were obtaining quotat ions for the t imber frame, most companies we approached were put off by the requirement for the steel-framed building to remain in sit u. In contrast, Frame Technologies welcomed the challenge.” Nigel Box, owner