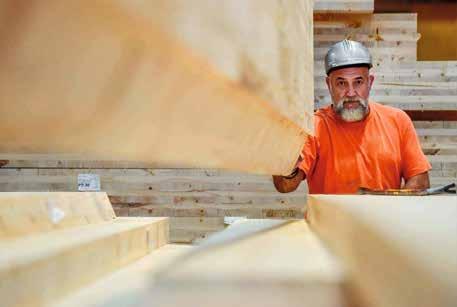
12 minute read
Mass Timber Insurance: a stock take
Joe Giddings, Projects & Campaigns Director at the Alliance for Sustainable Building Products (ASBP) new Timber Accelerator Hub, explains how some of the complexities surrounding timber and insurance can be addressed.
Despite its many well-known advantages in terms of carbon, waste, speed and quality of construction, mass timber faces multiple challenges that are preventing it being adopted as the primary structural material for most medium and high-rise commercial and residential developments.
Unfavorable changes to regulation have combined with high costs or lack of availability of insurance. With widely held doubts and misconceptions around fire performance persisting amongst insurers, many developers are reluctantly reverting back to concrete or steel – so what’s the solution?
The Timber Accelerator Hub (TAH) was launched earlier this year by the Alliance for Sustainable Building Products (ASBP), in partnership with the Laudes Foundation, to help develop solutions to these complex challenges alongside timber industry partners including Swedish Wood & Timber Development UK. The TAH’s steering group brings together expertise from insurance, fire engineering, cost consultancy and sustainability, and couples this with timber industry knowledge. This collaborative approach is the starting point to developing initiatives to not only increase the uptake of mass timber but do this in a way that helps improve building safety and durability.
I was brought in as Projects and Campaigns Director for the TAH in April, drawing upon my experience from establishing another collaborative network, the Architects Climate Action Network (ACAN). Since April we’ve been building connections and developing a number of working groups in order to scope out the issue from different perspectives. We’ve been speaking to developers, brokers, insurers and architects amongst others to understand exactly what the problems are and to begin to address them. Insurance providers’ reluctance to provide cover rests upon the relative lack of data in terms of premiums and claims specific to mass timber buildings. Data from the 1,000 or so mass timber buildings that have been completed in the UK exists in silos within different insurance companies, with no obvious solution as to how to pool this. One broker pointed out that: “insurers’ data is their intellectual property – their datasets are what gives them the edge over competitors”. Set this against the backdrop of a ‘hardening’ insurance market in recent years, where the cost and availability of insurance has been increasing across the board, and construction materials such as CLT, DLT, glulam and LVL begin to look unattractive for insurance providers, leading to huge hikes in premiums or cover being removed completely over a certain threshold, as the risk appetite of insurers decreases.
Chase Underwriting International have responded to this situation with the announcement of a UK Mass Timber Construction Insurance Facility, which will fill the gap in the UK construction insurance market with a viable policy that matches the needs of developers wanting to utilise mass timber products in their projects. Through the facility, commercial projects between £10-60million in value can be covered, supported by multiple insurers each taking on just a small slice of the risk, with Chase Underwriting managing that spread of risk.
Chase’s facility is a smart solution that patches over part of the problem, and we encourage interested clients, developers and contractors to get in touch to learn more. Construction insurance is however only half the picture. Beyond this, a further challenge awaits the UK property insurance market. Amongst property
1
2

STRUCTURAL TIMBER: FOCUSING ON THE FACTS
The Time for Timber campaign has released a white paper that aims to help insurance companies understand the vital role they play in supporting the construction industry to achieve net zero status by 2050.
Founded with the ambition of challenging misconceptions in the insurance and financial sectors about structural timber, the Time for Timber campaign seeks to highlight the material’s numerous sustainable benefits and underlines the need to increase its use if we are to stand any chance of preventing the environmental crisis that we face today.
Recently, there has been an increasing reluctance to back timber projects by some insurers – yet, as the long-term impacts of climate change become more widely felt, insurers are increasingly realising the value in supporting such low carbon construction methods. Unfortunately, some uncertainties still remain – and the white paper is an attempt to address this balance by providing a credible source of factual information and research. Reiterating the environmental, economic, health and wellbeing benefits that structural timber has to offer, the white paper also expresses a real desire to work with the UK’s insurance sector to further its understanding, using international examples to demonstrate that timber is a widely recognised and viable structural material.
Andrew Orriss, Chief Operating Officer at the Structural Timber Association (STA), says: “While we still feel that the Government’s net zero targets are achievable, we are rapidly running out of time. We have spoken to many insurance companies and there is a genuine interest in supporting timber projects, but the lack of clear and reliable information is hampering this effort. The hope is that this white paper will help us to engage with insurance companies, so that we can close the gap between misinformation and the facts before it is too late.”
For more information and to download the white paper visit: www.cutt.ly/timefortimber_whitepaper
insurers there is clearly a need for an increase in understanding regarding the performance of mass timber structures when exposed to fire and water during their lifetimes, as well as a need to pool any existing claims data on the UK’s existing mass timber buildings. Together with Dominic Lion, a broker at AJG, we’re convening a forum to communicate the latest in fire engineering, testing and best practice to a large group of the UK’s leading property insurers, to assuage doubts, provide reassurance, and address concerns. We have a number of sessions planned for the coming months which we hope will begin to turn the tide in property insurance for mass timber buildings.
Ideas abound for longer term systemic solutions: from the achievable aim of mass timber specific regulation to more imaginative solutions such as a structural timber ‘captive’ insurer (an association of large developers providing coverage for themselves to allow for greater flexibility) and even a Government-backed reinsurer. We’ll be looking to other countries such as France, Austria and Canada to understand how policy instruments can support the adoption of mass timber, and we’re closely watching the development of innovative concepts such as Waugh Thistleton’s ‘new model home’.
There’s a lot of work being undertaken right now by proponents of mass timber in the UK to demonstrate its safety, sustainability, quality and performance. Our role at the TAH is to bring this together to unlock the use of mass timber in construction. If you’d like to contribute your thoughts, we’d be delighted to hear from you.
You can contact Joe Giddings at: joe@asbp.org.uk
For more information on Chase Underwriting International’s UK Mass Timber Construction Insurance Facility contact Philip Callow at Philip.Callow@chaseunderwriting.co.uk or Brad Green at Brad.Green@chaseunderwriting.co.uk www.asbp.org.uk
Images:
01-02. Timber’s role in construction is constantly under scrutiny. Courtesy Urban Splash Maccreanor Lavington
CASE STUDY CLT FOR CYBER QUARTER

2
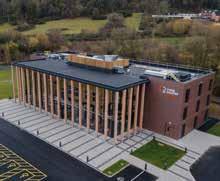
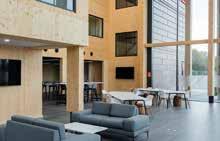
Cross laminated timber (CLT) is at the heart of the Cyber Quarter – a newbuild multi-purpose centre of excellence in the field of cyber security and a flagship scheme for the University of Wolverhampton.
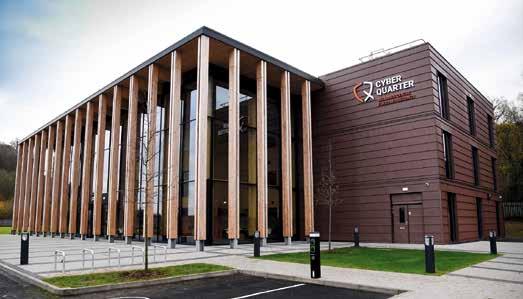
The newbuild CLT frame centre provides facilities for research and development across three cyber laboratories as part of the Wolverhampton Cyber Research Institute and provides tenanted office space for up to twenty cyber companies. A full height glass atrium acts as a dual break-out space and function hall, alongside the main threestorey building that houses business suites, innovation rooms, IT workshops and a ‘Cyber Range’ – a cutting edge facility to defend against the global rise of hacking.
The superstructure mainly comprises CLT wall and floor panels, as well as glulam columns and beams. The ground floor provides the principal training spaces for the facility. Each wing is an open area to facilitate break-out meetings. The upper floors are restricted access and contain most of the tenant units, giving them greater security, away from the open areas on the ground floor. The first floor comprises the cyber tenant units with enlarged corridors to provide break-out seating areas. The third floor houses the cyber range, a facility that generates real-time hacking scenarios.
1
The 2000sq m building, with the main building comprising three storeys, was constructed using CLT floor and wall panels and glulam elements, to create a highly sustainable and functional superstructure solution and produce a stunning natural aesthetic.
Utilising the inherent airtightness of CLT frames and employing a ‘fabric first’ approach resulted in a high energy efficiency and a reduction in operational energy requirements, leading to a subsequent reduction in future operational carbon emissions to complement the low embodied carbon contained within the building itself. The Cyber Quarter achieved a rating of BREEAM ‘Very Good’ and an EPC ‘A’ rating, highlighting the long-term benefits of a ‘fabric first’ approach in both an environmental and commercial sense. The final structural form’s use of CLT panels and glulam meant that the structure stored 30 tonnes of carbon dioxide equivalent (CO2e) through carbon sequestration when constructed. An equivalent steel or concrete building would have emitted 563 tonnes of CO2e, showcasing the tangible environmental impact that sustainable design can achieve when implemented. The prefabricated nature of the CLT panels ensured that on-site construction waste was kept to a minimum. The CLT panels were manufactured offsite using computeraided manufacturing. Builders work holes were also preformed offsite, which required early stage coordination and clash detection across the multidisciplinary team to ensure a co-ordinated design and a smooth construction and installation process. The lightweight nature of CLT and glulam compared to traditional steel or concrete buildings meant that a relatively thin ground-bearing raft foundation could be used to support the structure. Using a smaller volume of materials in the foundations led to material cost savings and embodied carbon reductions when compared to a more traditional superstructure frame option.
3
4
For more information visit: www.cundall.com
Images:
01-04. The use of CLT panels and glulam meant that the structure stored 30 tonnes of carbon dioxide equivalent (CO2e) through carbon sequestration when constructed. Courtesy Cundall
CASE STUDY FORGED FOR THE FUTURE
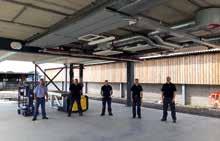
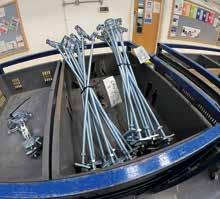
Paul Aulton, Regional Director of Engineering at NG Bailey, explains how offsite manufacturing is transforming the construction industry and resulting in substantial environmental benefits.

Although NG Bailey has been pioneering offsite construction since the late 1990s, adoption of these techniques has been the exception rather than the norm. But a new focus on increasing efficiency in construction means that is changing. With its many benefits including improved environmental performance, increased programme certainty and reduction in safety risks, the adoption of offsite techniques is set to grow.
Traditionally, most buildings in the UK are procured individually, designed conventionally, and constructed on-site, using traditional skills and materials. But the new Construction Sector Deal, published in 2018 through the UK Research & Innovation’s Transforming Construction Challenge programme, aims to create a more sustainable and productive sector. Additionally, the government-funded Construction Innovation Hub is also playing a key role in transforming the UK construction industry by targeting a built environment with better whole life performance.
As an advocate for modern methods of construction (MMC), it made perfect sense for the company to become a partner in the Platform Design Programme – the largest ever Government-backed research and development programme in the industry. By working alongside partners from the Construction Innovation Hub and the Manufacturing Hub, we are volunteering time and expertise to support the development of solutions aimed at transforming the construction industry.
NG Bailey is supporting the construction of The Forge using offsite methods. The Forge is an innovative office development for Landsec, based in Southwark, London. After securing the tender for the project in December 2019, we were chosen to work with multi-disciplinary design consultants, Bryden Wood Technology, to develop, manufacture and install a mechanical and electrical (M&E) kit of parts.
1
The development is the world’s first large scale office building to be designed and constructed using a ‘kit of parts’ led solution, built on a platform design for manufacturing and assembly structural frame. Landsec has ambitious targets for The Forge – with aims for the construction and operation of the 139,000sq ft development of two nine-storey office buildings to be net zero carbon – a first for the UK, setting the benchmark for future developments.
Offsite manufacturing has many benefits compared to traditional onsite techniques, including saving on build costs, labour costs, time and reducing waste. However, one of the most crucial benefits is the environmental impact. Sustainability and improving the environmental performance of construction is extremely important to us at NG Bailey. By manufacturing offsite, the local impact of a build is improved by greatly reducing noise
2
3
and traffic levels from deliveries and people onsite. By reducing traffic levels, this has a positive effect on the environmental outcomes of a project by minimising deliveries to site, therefore reducing carbon emissions. Naturally, there is less waste as materials can be more accurately calculated for a build.
The approach taken on The Forge will remove around 20,000 operative hours from the project. This in turn will deliver substantial carbon benefits by avoiding 35,600km of vehicle movements, which alone saves six tonnes of carbon from entering the atmosphere. This is the equivalent to the carbon dioxide removal from 276 tree seedlings grown for 10 years. It is clear to see that there is still work to do within the construction and manufacturing sector to ensure offsite becomes the preferred option, but we will continue to champion for this change by consistently looking for new techniques to transform the industry.
For more information visit: www.ngbailey.com
Images:
01-03. The offsite approach taken on The Forge will remove around 20,000 operative hours from the project.