
4 minute read
Creating a Pathway for Offsite
John Miles, Technical Manager at Assent Building Control believes it’s time for Building Control to back offsite construction.
During my sixteen years working in building control, I’ve had enough time to see the sector evolve many of its practices and processes in a range of ways. However, the sector seems a step behind when it comes to accommodating offsite construction.
It is clear that offsite construction is shaping the future for much of the built environment. In recent years we have seen government initiatives such as the DfE offsite framework, as well as pressure from the Housing, Communities and Local Government Committee for ministers to centre offsite at the core of its ambitious housing targets, making it clear that leading forces are understanding the benefits of speed, sustainability and precision that modern methods of construction have to offer.
Realising the benefits of offsite construction
Building control needs to catch up. Not only to enable the offsite construction sector to thrive to its fullest potential but also because so many of the advantages that offsite construction brings to the table directly compliment the work that we do as Approved Inspectors (AI’s).
The nature of working from a factory means that offsite manufacturers rely heavily on both consistency and precision – both aspects that the inspection process benefits from. Offsite manufacturers will often use the same team for almost all builds, giving AI’s the opportunity to create longstanding relationships and therefore allowing us to fully understand the systems and processes, before building an approval procedure around them. And because of the emphasis on precision, AI’s need to be involved from the beginning of the design process. This offers a huge advantage, as it means we are able to have a full understanding of the project, from start to finish and it provides an audit trail that isn’t possible with traditional builds. Assessing and enforcing energy efficiency and carbon levels of a building is a vital part of the inspection process. When it comes to offsite buildings, the designs that I see time and again always exceed the minimum requirements for thermal efficiency. This assurance and quality control makes the process considerably easier, as we’re not having to request alterations later down the line. The same goes for safety – the offsite process offers considerably more control, making it easier to ensure fire safety measures from the factory, ready for when the structure is transported to site.
Changing approaches to the inspection process
The issue in all of this, is that current building regulations are generally written for traditional builds and for years, offsite has had to work around with this. That’s not to say that there is no relevance to offsite construction
1
within the current regulations because there is, but the way that Building Control approaches these regulations needs to be revisited.
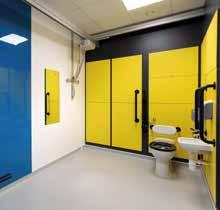
Unlike traditional builds, regulations around fire resistance, acoustics and energy efficiency are all dealt with from within a factory, so by the foundation stage, all of these checks have already been completed. It is crucial therefore, for comprehensive inspections to be carried out at the factory stage, as the structure is already assembled by the time it gets to site, so if something is missed by that point it’s too late. And while site inspections are still a part of the process, AI’s must take careful consideration during factory audits and carry out QA checks during the manufacturing stages in order to fully interrogate the building. These audits provide a holistic view of the build – during just one visit AI’s can see the building frame of one unit, at the same time as seeing another that is ready to be delivered to site. This means changing focus to frontload input at the design stages as early as the original proposal which can take up to five meetings before even reaching the manufacturing stage.

Building skills with offsite construction
As with every sector of the built environment, skills will play a big in Building Control’s adoption of offsite construction. This needs to come as part of the overall rallying cry for new talent as well as being a focus of development for the existing Building Control workforce. There is so much potential for knowledge sharing between the two industries and it’s up to Building Control to ensure we are listening and learning in order to nurture skills and specialisms to deliver the highest quality buildings.

AI’s should be accumulating knowledge from each offsite project that they work on and funnelling it to the manufacturer. As an understanding of the systems and processes grows, AI’s are able to advise more holistically on schemes. The challenge with offsite is the need to understand its methodology and how it all comes together. Once this is established, AI’s have the opportunity to improve the service and focus more tentatively on what is needed.
While offsite continues to calve out its place within the built environment, there is a need for Building Control to create more dynamic approach that allow freedom in the design process and ultimately improve it. The approach to the current inspection process is rigid and linear, responding to the needs of traditional methods of construction. And while offsite is still a relatively small section of the construction industry, the accelerated growth that it’s seen over the past 12-18 months strongly indicates the upward trajectory where it’s heading.
3 2
4
For more information visit:
www.assentbc.co.uk
Images:
01-04. Assent recently worked with Portakabin, to deliver a new primary school under the DfE MMC1 framework in Somerset. Courtesy Portakabin