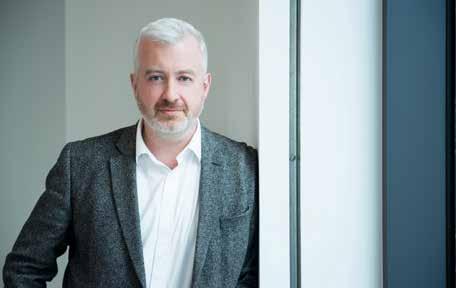
16 minute read
Placemaking with Purpose
How can offsite methods create green jobs in order to help meet sustainability targets and improve the built environment? Rory O’Hagan, Director at Assael Architecture, explains what can be done to help in the race to net zero.
1
Building energy-efficient homes and retrofitting existing housing stock is a vital puzzle piece in improving the built environment's impact on carbon emissions and reaching a net zero future. Offsite manufacturing is a key part of this, and the latest figures from the Green Jobs Task Force are
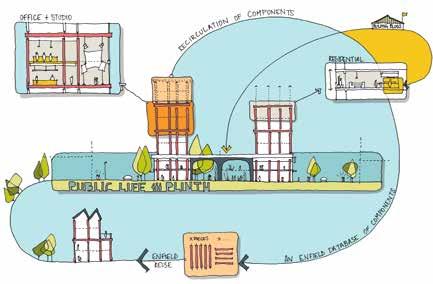
2
a stark reminder that not enough is being done to support this part of the housing and construction sector. To significantly reduce the impact of buildings and ‘build back better', the government must place more emphasis on, and invest in, green jobs. According to a recent report from the Green Jobs Taskforce, every UK job has the potential to be ‘green’. The Government’s vision is an investment drive in skills that will see an industrial revolution carried by low carbon, reducing our dependence on unsustainable practices. This transition to make sustainable skills ‘second nature’ is no more urgent than in the built environment sector, which contributes up to 40% of the country’s total carbon footprint. Green jobs in architecture, development and construction are as necessary as they are transformative. The Office for Budgetary Responsibility (OBR) has forecasted that retrofitting existing stock could cost as much as £400billion, identifying a critical ‘skills gap’ which will need to be filled to meet legislated targets. The Future Homes Standard, too, sets expectations on the carbon neutrality of new homes, which will only intensify over time.
While the transition may seem daunting, much of the infrastructure we need to lower emissions is already in place. Through tried and tested modern methods of construction (MMC) such as offsite modular housing and timber frame construction, the property industry has a real opportunity to make a difference and meet this target in the race to net zero in 2050. Innovation also serves to promote ‘green’ skills as the bi-product of more environmentally sustainable and progressive approaches to traditional housebuilding methods, accelerating that change. In practice, the adoption of sustainable methods starts with a fresh perspective. If the UK is to truly become net zero by 2050, we can no longer afford to look at sustainability as a tick box exercise. As architects, we must rise to the challenge of designing sustainable buildings on a holistic
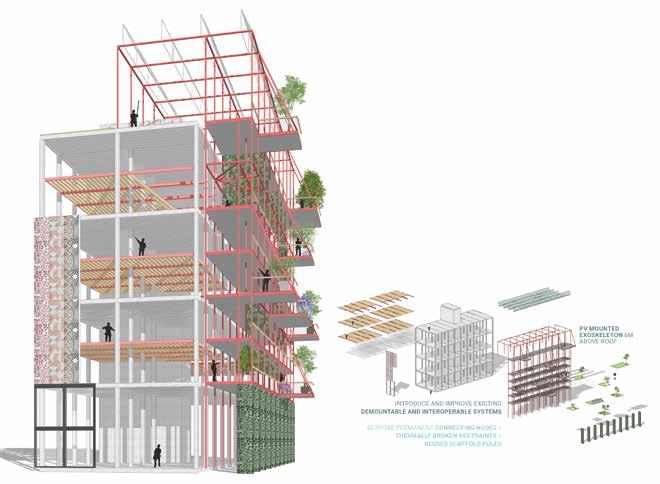
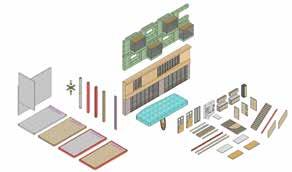
3
4
cradle-to-grave system, putting whole life carbon into the picture, enabling us to begin from day one and see it carried right through to completion.
If the architecture and construction sectors are going to decarbonise and bolster the creation of ‘green’ jobs, then the Government must also emphasise investment in MMC and sustainable practice within the associated real estate sector. Expediting our transition to a low carbon economy relies on this enduring support, shedding the reluctance across the industry to embrace the methods already available to meet our carbon neutral commitments.
Increasing the uptake of existing methods with proven results and making them better is an intuitive solution to the pressing requirements of climate change. It’s not advocating for a complete departure to what we see as common practice, and it is in this emerging corner of cutting-edge innovation that ‘green’ skills are already born. Modular construction is a near perfect solution to achieve net zero, with both embodied and operational carbon lessened, and the ability to produce buildings in half the time of traditional construction. Having the ability to manage the materials from its creation to the destination of end use is a transformative way of building with a responsible conscious. This will also have a positive knock-on effect for developers and investors who will be able understand the origins of the products used in specific assets. Modular manufacturing in the UK still carries some negative connotations as many architects are afraid of the concept, feeling as though it infringes on their creativity. There is a false sentiment that ‘modular’ means restrictive, standardised design – the new Lego block-by-block communities of tomorrow. The reality couldn’t be any different: factory built homes can offer desirable versatility, supported by a suite of common components, and are designed through a vigorous process that drills down into the detail early on to achieve optimised housing solutions.
An excellent example of innovation using MMC to produce resilient and contextually sensitive designs is Assael’s work at Meridian Water, a new masterplanned development in north London. As part of the masterplan, after winning Meridian Water’s Placemaking with Purpose Competition in 2020, Assael is creating a flexible and sustainable construction system designed for disassembly and reassembly, allowing reconfiguration and optionality that seeks to extend building longevity. With the key system components of the superstructure already established, architects and designers can focus more on aesthetics and the creation of unique building identities.
By taking advantage of technology and saying goodbye to outdated building methods, we have a great opportunity on our hands and one that I would encourage architects to embrace. From a financial, sustainable and environmental perspective, if we can meet the pledge towards contributing to the Green Jobs Taskforce for the housing sector, then it’s certainly worth investing in.
For more information visit:
www.assael.co.uk
Images:
01. Rory O’Hagan, Director, Assael Architecture 02-04. Meridian Water RightSizer concept – a flexible and sustainable construction system designed for disassembly and reassembly
WHAT A DIFFERENCE A YEAR MAKES AS M-AR TREBLES TURNOVER
It’s been an exceptional year for the construction industry as a whole but for off-site contractor, M-AR, it’s been exceptional for all the right reasons – with record-breaking sales and turnover reported. And now the company has its sights set on breaking even more records this year and beyond.
2
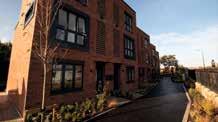
The Hull-based off-site contractor, which is still privately owned today, was founded in 2007 and has gone from strength to strength ever since. It primarily operates across the residential sector, both private and social housing, as well as education and the commercial sectors.
M-AR: the 2020 results are in
Following a period of unprecedented growth, M-AR has reported an increase in turnover of more than 300 per cent up on the previous year. This makes the year ending March 2021 truly exceptional – especially in the face of industry-wide challenges posed by the Covid-19 pandemic and subsequent national lockdowns.
M-AR has reported annual turnover in excess of £20 million for 2020/2021 and, with a clear strategy is on track to increase turnover by a further 50% in 2021/2022. Moreover, the company’s profitability also increased significantly, making it M-AR’s most successful year to date and the sign of things to come as it makes a name for itself as a trusted offsite contractor.
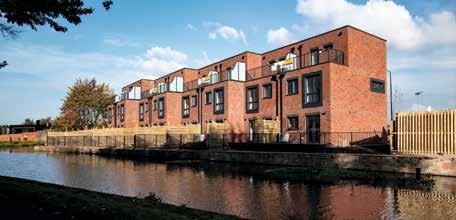
1
What’s the secret to M-AR’s success?
M-AR works in partnership with customers and supply chain partners to find the right solution for each project brief, using its expertise to tackle any challenge to create and deliver schemes without compromise. The company primarily focuses on volumetric schemes but has the ability to provide alternative construction solutions, making its offering truly unique.
M-AR also owes its success to its continued commitment to selfinvestment in all areas of the business with the latest period of growth fuelled by large-scale company-wide investment. M-AR was early to the housing market and is now part of the Buildoffsite Property Assurance scheme (BOPAS) and has invested significantly in its technology to allow it to increase its offering within the housing market.
In the last year the company has appointed 35 new members of staff, moved to a brand-new dedicated 100,000 sq. ft. manufacturing facility and invested over £2m in new machinery and equipment. This ongoing investment will continue to reduce the cost base for its customers and lay the foundations for M-AR’s ambitious five-year growth plans, allowing it to increase the volume of projects it can deliver sustainably and without impacting on quality or customer service.
What’s next for M-AR?
Ryan Geldard, Operations Director at M-AR commented: “We’re delighted that our novel approach is working well for our customers, and that is reflected in our financial results and forward order book. We’re entirely focussed on creating better project outcomes and lowering costs for our customers through our holistic assessments of their needs and by aligning our people and technology, merging the gaps between traditional contracting and manufacturing.
“Our management team is committed to making M-AR a happy and healthy place to work and also supporting our peers in industry to drive better collaboration. We’re first in line on many great initiatives that are breaking the mould of how high quality housing is delivered.”
For more information visit:
www.m-ar.co.uk
Images:
01-02. Modular construction is going to play a vital role in the UK’s ‘Build Back Better’ drive thanks to its speed and efficiency.
EJOT LAUNCHES NEXT GENERATION RANGE
Fastening technology specialist EJOT has upgraded its range of ETA-approved through-bolts with the launch of its new BA Plus range of Option 1 anchors, suitable for both cracked and non-cracked concrete applications.
1
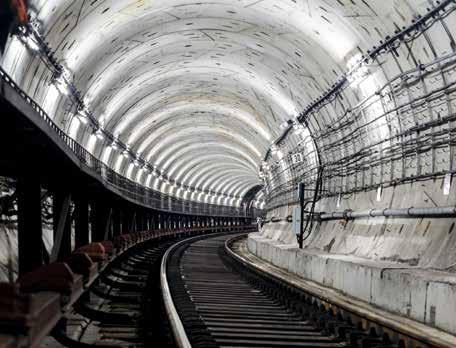
The EJOT BA Plus range is a new generation of higher performing through-bolts. This builds on the strengths of its established BA range to deliver additional performance benefits and new application potential. And, in addition to concrete, these torque-controlled expansion anchors are also suitable for installation in other hard base materials including natural stone.
The innovative design of BA Plus allows the required installation torque to be achieved with 30-50% fewer revolutions than previously, and new M8 and M10 through-bolts can now be used for anchoring in to concrete which is up to 20mm thinner. The risk of on-site errors is also further minimised with a setting depth clearly marked to the thread and anchor length letter coding marked on every bolt head. The BA Plus range provides throughbolts for all the most typical cracked and non-cracked concrete applications ≥ C20/25 up to the seismic Option 1 performance. Backed with the independent assurance of European Technical Assessments (ETAs), the range offers a dependable solution for numerous applications including steel structures, column base plates, heavy duty racking, cable racks, handrails and facades.
Zinc plated, hot dip galvanized, and A4 stainless steel through-bolts are available, providing a solution for a wide range of applications including harbours and tunnels where the highest level of resistance to corrosion is required. Their design ensures easy installation, with no risk of damage to the thread when the bolt is hammered into position and an embedded sleeve that expands reliably as the bolt is tightened to the required torque. The M10 and M12 options are available in two different anchorage depths for extra versatility.
Richard Bowhay, Sales Manager for Building Fasteners at EJOT UK says: “BA Plus represents an important enhancement in the performance capabilities of our through-bolts and gives installers a reliable and highly secure anchor solution for every type of concrete application – backed by the third-party assurance of ETA approval. It demonstrates collectively, the objectives of our technical teams worldwide in their capacity to regularly assess if and how we can advance the performance of construction fixings to give architects and building owners total peace of mind, as well as improving efficiency for installers.”
The BA Plus range is complemented by EJOT’s new range of through-bolts for Option 7 non-cracked concrete applications, BA-C NC, which provides a class-leading anchor for many other applications including warehouse racking and stadium seating, backed by the third party assurance of an ETA.
EJOT UK’s team offers a wealth of technical support and specialist guidance to specifiers and installers to ensure they can achieve the right result when anchoring into cracked and noncracked concrete every time.
Full details about the Option 1 BA Plus range and the Option 7 BA-C NC through-bolt are available at: www.ejot.co.uk
Images:
01. EJOT's BA-Plus range covers indoor, outdoor and industrial environments.
SYSTEM ACCEPTANCE FOR INNOVATIVE CONSTRUCTION
The Premier Guarantee system acceptance process has been developed to help manufacturers gain accreditation under our technical requirements, allowing them to be promoted as an accepted system provider.
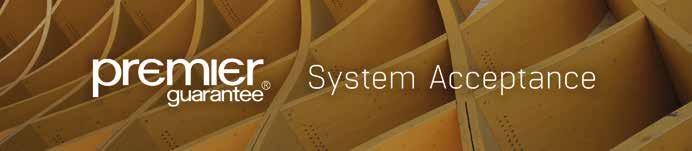
As part of our warranty application process, developers and builders must ensure that the systems they use onsite are accepted by us in line with the requirements of our Technical Manual. System acceptance from Premier Guarantee would:
• Enable your system to be accepted for use by our registered developers and builders throughout the UK • Provide assurance to our clients and lenders that your system performs to a consistent standard and will remain durable in line with our warranty requirements • Provide you with a certificate of acceptance • Include your accepted system on the Premier Guarantee system listing section of our website.
How to get accepted
An initial triage of the design package would be undertaken to ascertain whether the system broadly meets our performance standards. If it does not, we will provide feedback. If the system is considered suitable to proceed as an application, a detailed review of the submitted system/documentation can commence, subject to the fee being paid.
Our internal technical team will undertake a design audit of your system, making sure it meets the requirements of our Technical Manual. The auditors will ask for: • Design details – drawings, plans, sections, elevations and specifications of the construction (including structural and weatherproof elements) • Copies of independent/thirdparty assessment certificates of products and component of the system e.g. BBA, BM TRADA, BRE,
Europe Technical Approval (ETA) or conformity to International,
European and British Standards where applicable • Third-party manufacturers’ warranties.
Meeting and factory inspection
If the design review is successful, a factory inspection will take place. If we are satisfied with your system it will be issued with a provisional acceptance for an initial test site. Our technical auditors will contact you to arrange a meeting and factory inspection. The factory inspection will assess: • Quality control system • Manufacturing/assembly process • Storage of materials and components • Protection of modules during transportation • Method of onsite connection of modules • Manufacturing aligns with the design.
Issue system acceptance
An initial trial site will be assessed, once registered with Premier Guarantee for warranty purposes. The developer will need to demonstrate that the system can be constructed to meet our technical requirements. Once this has been demonstrated, the system will gain a full system acceptance. This will be limited to one year and require annual renewal (due to changes in technical requirements and legislation we have to ensure that the system design intent is maintained and meets current legislation).
Once accepted you will receive a system acceptance document, certificate and logo. The assessment process we provide is purely for our warranty purposes and is not a thirdparty approval such as a European Technical Assessment Certificate or a BBA (British Board of Agreement approval) nor is it recognition that it meets the requirements of other structural warranty providers or Building Regulations.
To apply for or enquire about system acceptance, contact our innovations team on 0800 107 8446 or SystemAcceptance@premierguarantee.co.uk.
SIZED FOR PERFECTION
Quality craftsmanship has long been recognised as a hallmark of good building, but in the past it was a slow, painstaking process. Sapphire Balconies have made huge strides in saving time and money on-site.
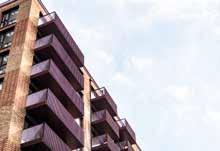
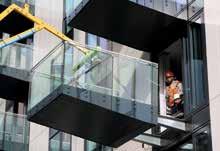
1
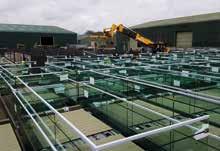
In modern construction, speed is of the essence – but it’s not the only challenge for architects and developers. Using MMC processes, Sapphire Balconies delivers balconies embodying quality craftsmanship and time-saving processes to today’s construction sites.
It’s often said that balconies add visual and lifestyle value to high-rise residential buildings. But because balconies are either built in-situ or bolted on to the main structure – rather than being an integral part of it – they have tended to be at the centre of cost, timing and safety issues on some building sites.
With the high demand for new residential accommodation driving demand for faster building, architects and developers have welcomed the new materials and methods now available for use within modern regulatory standards. However, balconies still challenge designers to reduce installation time and costs – as well as contributing to increased site safety. It would be a tough challenge without Sapphire’s own offsite solution.
Sapphire Balconies is a specialist offsite manufacturer of balcony systems which complement MMC processes on building sites – as well as meeting the aesthetic and economic requirements of architects
2
and developers and providing valuable ‘outdoor’ space for residents. Sapphire’s Glide-On™ Cassette® balconies are delivered fully assembled, including balustrades. They are then simply craned into position and glide on to steel support arms for final attachment. Minimal further finishing is required, making this time-saving installation so fast that it is possible to fit 44 balconies in a single day.
There’s no requirement for on-site storage, which is a great help on inner-city building sites where space is invariably very limited. Sapphire’s balconies are delivered by third party logistics specialists who collect and store balconies in line with site programmes and crane availability. This flexibility gives contractors a faster and more reliable flow than the alternative ‘just in time’ approach. On delivery, the prefinished balconies can go virtually straight from lorry to lift.
Building on specialist factory production lines adds real quality to Sapphire’s craftsmanship. There is a high degree of quality control at each stage of the process, ensuring not only that each balcony is sized for a perfect fit, but also that it provides ample rigidity to overcome any risk of a ‘bouncy balcony’. In fact, building in this way ensure levels of quality that are almost impossible to achieve with on-site construction. The offsite approach also saves money. For example, because the balconies are fixed by installers from inside the building, external scaffolding can be removed prior to balcony installation. In practice, these two processes can even be simultaneous as Sapphire’s Glide-On™ Cassette® balconies can be installed top-down. This is possible with Sapphire’s counterbalanced lifting system, which offsets the crane hook. Sapphire’s offsite process also helps to reduce overall costs through the time and material efficiencies that can be enabled in a dedicated factory environment.
When installing Sapphire’s balconies there is minimal risk of health and safety issues. There are no hot works and installers work from behind a special safety barrier inside the doorway until the balcony is guided on to its arms and bolted into place. The balustrades and decking are factory fitted, so once the balcony is secured, the installers can remove their safety barrier and complete further finishing that may be necessary.
3
For more information visit:
www.sapphire.eu.com/case-studies
Images:
01-03. Sapphire’s Glide-On™ Cassette® balconies are delivered fully assembled and are then simply craned into position and glide on to steel support arms for final attachment.