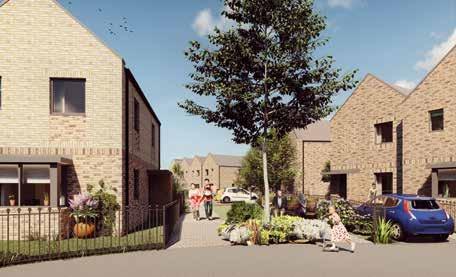
48 minute read
Industry News
Castleoak and Pobl Bring Low-carbon Homes to Newport
Wales-based organisations, Pobl and Castleoak are partnering to bring sustainable homes supported by Welsh Government funding. The timber frames for the homes will be prefabricated at Castleoak’s offsite manufacturing facility in Ebbw Vale before being assembled on-site.
Alway in Newport will gain 39 low-carbon affordable homes as Castleoak and Pobl partner on a project at the former site of the Ladyhill Day Centre and Seven Stiles pub. Castleoak specialises in later living and social housing, has partnered with Pobl, a not-for-profit housing organisation, to bring 20 two-bedroom and 19 three-bedroom homes to the one-hectare site. The project is partly funded by the Welsh Government’s £155million Innovative Housing Programme, which seeks to use offsite construction to bring low-carbon affordable homes to Wales.
The frames of the homes will be made at Castleoak’s offsite manufacturing facility in Ebbw Vale, including pre-fitted windows and insulation, and adapted to house specialist mechanical and electric solutions and smart water cylinders, aiming to maximise energy efficiency. The homes will also have roof solar panels and storage batteries, further minimising the homes’ lifetime carbon footprint and energy costs. Once created, they will be assembled at the site by Castleoak’s construction team.
Andrew Duggan, Managing Director of Offsite Manufacturing at Castleoak said: “Our homes can help us live happier and more fulfilling lives. Increasingly that means buildings which can give us good conscience and reduce the pull on our pursestrings through lower energy costs. That’s what we’re going to bring to Alway. It’s fantastic to be working with Pobl to bring truly low-carbon, affordable homes to people in Newport, not just through the fabric of the buildings, but also through innovative energy solutions which will help to keep costs low for future residents.” Gavin Howells, Senior Project Manager at Pobl Group added: “Pobl has a growing reputation for delivering forward thinking housing solutions, and we are excited to be working with Castleoak on this project that will deliver much needed affordable and truly sustainable homes for Newport. We’re grateful for the support of the Welsh Government & Newport City Council on this project and we share their ambitions to create high quality places to live – and we look forward to working with the Alway community on this new venture.”
Source: www.castleoak.co.uk
Former Crest Nicholson Boss Joins ilke Homes
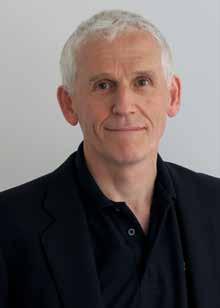
The former boss of one of the country’s largest listed housebuilders has been appointed as Chief Financial Officer at ilke Homes.
Former Crest Nicholson Chief Executive, Patrick Bergin is joining the modular housebuilder following three years of rapid growth, in which it has grown its order book to over £200million – putting it on par with some of the UK’s largest developers. Bergin, who joins with 15 years’ of experience in housebuilding, rose through the ranks at Crest Nicholson where he held numerous senior roles, including the company’s Chief Operating Officer from 2016 to 2018.
In his role as Chief Financial Officer at the FTSE250 housebuilder between 2011 and 2016, Bergin was instrumental in Crest Nicholson’s successful initial public offering in 2013. Bergin successfully grew revenue by 90% in the three years that followed the company’s stock market launch. Bergin, backed by his years of experience at a volume housebuilder and in public markets, has been brought in to contribute to the strategic management of the business as it enters this period of rapid growth and ensure that management processes and controls are appropriate for the enlarged operation. Bergin’s appointment comes at a time when an increasing number of investors, developers, housing associations and councils are turning to offsite manufacturing to deliver greener homes at pace. Changing building regulations, a worsening housing crisis and pressure from policymakers to reduce emissions produced by the UK’s housing stock, mean many in the housebuilding industry are being forced to innovate at a pace they are incapable of.
Patrick Bergin said: “To successfully transition to a net zero economy by 2050, there requires a significant step change in the way the UK builds homes. Regulatory pressures, challenges to traditional models of delivery and the urgent need to decarbonise housing mean that there has never been a more crucial time for UK house building to innovate and adopt more modern methods of construction. Following several years of intense research and development, I believe ilke Homes’ lowcarbon, energy-efficient solution to housing makes the company a firm market-leader. I expect the company’s strong growth trajectory to be maintained in the years to come as more investors look to go green quickly.”
Source: www.ilkehomes.co.uk
Construction Groups Unite to Hit Net Zero Targets
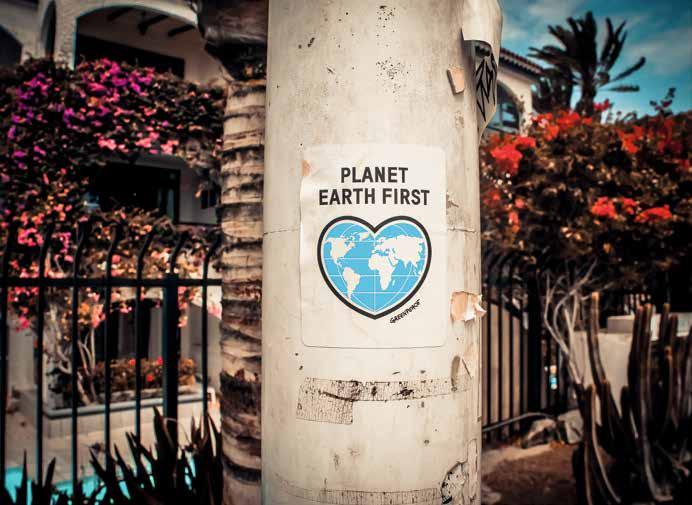
The Royal Institution of Chartered Surveyors (RICS), working as part of an international coalition of built environment professional groups seeking to drive the industry in measuring carbon has jointly published for consultation the world’s first international standard for reporting carbon emissions across all areas of construction.
The consultation will seek input from industry on how to make sure carbon emissions factor directly into the extensive decision making that goes behind planning construction projects. This is to be followed shortly, by new RICS guidance for professionals on how to assess ‘embodied carbon’.
With construction contributing around 40% of the world’s carbon emissions, it’s crucial for the built environment to move towards more sustainable practices if communities are to realise their net-zero ambitions in time for 2050.
Under development by RICS in partnership with Building Research Establishment (BRE), Chartered Institute of Building (CIOB), Chartered Institution of Building Services Engineers (CIBSE), The Environment Agency, UK Green Building Council (UKGBC), Institution of Civil Engineers (ICE), Institution of Structural Engineers (IStructE), Royal Institute of British Architects (RIBA) and The Carbon Trust, the new built environment carbon emissions database will allow professionals to log construction projects – whether that’s new homes, offices, or infrastructure – when ready later this year.
The database will give an indication of how much carbon has been emitted during the manufacturing and construction process (the upfront 'embodied carbon’), along with future maintenance, energy use and demolition, and enable designers to identify and avoid carbon-intensive products in favour of more sustainable materials that will help the UK get to net-zero by 2050.
Commenting on the database James Fiske, Director of RICS’ Building Cost Information Service, said: “It’s not every day that an entire industry comes together in agreement over climate change. The new database – coupled with the ICMS consultation - are real examples of the construction sector uniting in its mission to tackle carbon emissions and meet its commitment to net zero.” Following the consultation, the final ICMS standards are expected to be published in November 2021 followed by updated RICS guidance on carbon assessment – which sets out a universal methodology for calculating carbon emissions. This will form a toolkit to enable decision makers to minimise the carbon footprint of all construction projects.
Alan Muse, Head of Construction Standards at RICS and ICMS lead, added: “This update to ICMS and subsequent RICS standards which our professionals follow when completing any construction project will see the construction sector making a large and measurable impact when it comes to leading from the front and combatting climate change. Supported by the latest tech, such as the built environment carbon database, these new standards provide a professional toolkit to measure and consistently report on carbon and influence the most basic design and construction decisions.”
Source: www.rics.org
Senior Politicians View HMflex at Wernick Factory
Wernick Buildings’ factory in Port Talbot welcomed local senior politicians to receive a demonstration of its latest modular building system – HMflex. The four-bed hospital ward allows visitors to experience the same high-quality environment that healthcare professionals and patients will experience.
Visitors included Stephen Kinnock, Member of Parliament for Aberavon, Edward Latham, Leader of Neath Port Talbot Council, Julie Davies, Business Development Coordinator at Neath Port Talbot County Borough Council, Andrew Collins, Regeneration & Economic Development Manager at Neath Port Talbot County Borough Council and Susanne Renkes, Caseworker for Stephen Kinnock MP.
Commenting on the unit, Aberavon MP, Stephen Kinnock, said: “I was honoured to be able to see first-hand the incredible hi-tech work of one of Port Talbot’s major employers. It is fantastic that our constituency is home to such well-established firms leading the way on the national stage. I was also thrilled to hear about Wernick’s plans for expansion and long-term career opportunities companies like theirs are providing for the people of our community.” The HMflex building system is specifically designed with the healthcare sector in mind, providing ward and clinical spaces via standardised layouts. The new system adopts a fast-paced, quality solution to fit the needs and requirements of the sector as the system is designed to deliver a fully fitted HBN and HTM compliant four-bed ward in just two units. This means that a four-bed ward can be delivered, installed and ready for fit-out in as little as 24 hours.
Carl Curtis, Operations Manager at Wernick Buildings, commented: “From compliancy to speed, HMflex is specifically designed with the needs and requirements of the healthcare sector in mind. The demonstration ward presents and emphasises the benefits modular construction can offer the NHS and other healthcare providers.”
Following the closure of the demonstration ward, the units will be transported to Queen Alexandra Hospital in Portsmouth where they will complete a new 78 ward building. Wernick Group also recently announced a new Chief Executive with the appointment of Jonathan Wernick. From Yard Operative to Chief Executive, Jonathan has worked his way through many roles within the Wernick Group. He replaces Simon Doran following Simon’s retirement on 30 June.
Jonathan believes that it is the people that make his job enjoyable: “We have the privilege of employing the best people in our sector who bring with them an abundance of skills, experience, and more importantly, personality to make every day a pleasure. It’s exciting to be the fourth generation of the family to be leading the company and I look forward to the challenge of continuing its success.”
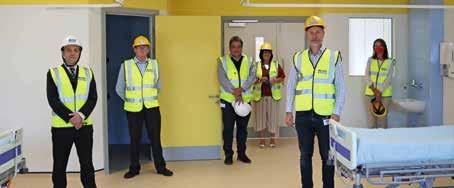
Source: www.wernick.co.uk
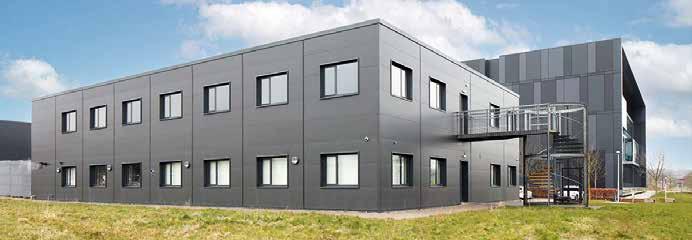
Thurston Group Lands Place on NHS Framework
Yorkshire-based modular and portable building manufacturer, Thurston Group, is pleased to announce that it has secured a place on the £1.6billion NHS Shared Business Services Framework. The business has secured its position across four core lots for ‘Building Purchase’ covering healthcare, education, residential and bespoke buildings up to the value of £25million+ per scheme. Set to run from July 18th for an initial two years, the framework has an expected spend of £180million per annum for the lots secured. Securing a place on the four framework lots through a competitive tendering process will further support Thurston’s ever-growing Projects division, whilst underpinning the growth strategy set out by its shareholders and executive leadership team.
The purpose of the framework aims to complement the speed of modular and offsite construction by providing an equally quick, easy and compliant procurement route for a range of NHS and public sector clients across the education, healthcare and residential sectors. The framework contracts cover health and corporate services including IT, legal, estates & facilities and business services.
From consultancy and design to finance and build, Thurston’s offers turnkey building solutions for every sector. With Three factories across Yorkshire, Thurston’s has the capacity to deliver over 5000 units per year. Managing Director, Matthew Goff, was delighted after landing a place on the framework, saying: “A huge well done to the business development team for securing our place on the framework. This is a fantastic achievement by the team and accelerates our position ‘to be the provider of choice’.”
United Welsh Group Developing Timber Frame Factory
With over £2million of investment from Welsh Government’s Innovative Housing Programme, the factory will be delivered by Celtic Offsite, a new social enterprise within the Caerphilly-based United Welsh Group.
The factory, which is due to open this autumn, will manufacture high quality, sustainable timber frame structures complete with factory-fitted insulation and windows to build up to 250 low carbon homes per annum. Using over 28,000sq ft of manufacturing facilities, Celtic Offsite will provide affordable housing for contractors and developers using a Welsh supply chain, including Welsh timber and local partners. There will also be a training suite on-site to provide skills development and apprenticeships for green construction jobs, training the next generation of workers to deliver more energy efficient homes.
Richard Mann, Deputy Chief Executive and Director of Operations for United Welsh Group said: “The Welsh Government Innovative Housing Programme funding has been vital in enabling us to develop the new Celtic Offsite factory in Caerphilly. The factory will create community benefits at every stage of production, designed on the principles of developing the foundational economy and doing better by working together.
“It will support the United Welsh Group, Local Authorities and other partners to realise our shared ambitions of achieving net zero carbon through the provision of new energy efficient homes, while supporting Welsh business growth and tackling fuel poverty. The factory opening will also create up to 28 new jobs, with investment planned for green construction training opportunities for local people year on year. All profits from the enterprise will be reinvested into our social purpose of providing more affordable homes and community services, including our decarbonisation programme to become carbon neutral by 2035.”
The Celtic Offsite factory will be located at Pontygwindy Industrial Estate near Caerphilly town centre. The project is a positive step in Welsh Government’s commitment to build more high quality homes in factories here in Wales. Julie James, the Welsh Government’s Minister for Climate Change, added: “This is a very exciting project that we are very proud to have been able to support. We have already started work on implementing our manifesto commitment to develop a timber industrial strategy and create a stronger wood economy for Wales. 80% of the timber used in the UK is imported, and only 4% of the 1.5 million tonnes of harvested timber is processed to be used as construction-grade timber in Wales. There’s a real opportunity for timber processors and manufacturers in Wales to contribute to this wood economy, creating new jobs in rural Wales as well as building an innovative supply chain for high value added, longer life uses.”
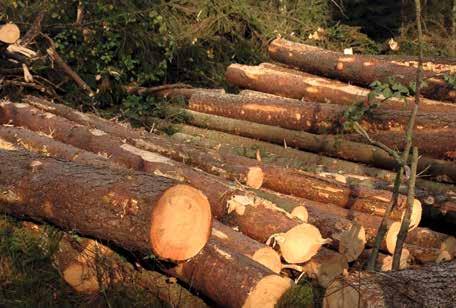
Source: www.unitedwelsh.com
AIMCH Calls for Game-Changing Housing Solutions
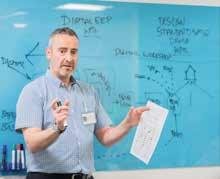
Advanced Industrialised Methods for the Construction of Homes (AIMCH) is inviting suppliers to enter the sandpit challenge to showcase their innovative products or services, demonstrating how they can deliver industrialised offsite solutions required to meet current and future housebuilding demands. The three-year AIMCH project, whose goal is to support the sector to tackle the UK housing crisis by building new homes quicker, more efficiently and to a higher standard, is encouraging innovation and collaboration from across all parts of the industry. There are three challenge areas for suppliers to submit their technically and commercially promising products and systems – advanced MMC solutions, with a particular focus on scaffoldless erect: standardised solutions, including modular stairs, bathroom pods, and preformed windows and doors: zero carbon solutions, with a particular interest in heat pumps, underfloor heating, convection heaters, battery storage, and lower lambda mineral wool.
Successful partners could see their products and services trialled on live housing projects, with successful methods subsequently being commercialised and brought to market in volume.
Daniel Shea, AIMCH Partner and Technical Innovation Co-ordinator, Barratt Developments Plc, said: “What we are looking for from the sandpit challenge is for suppliers to bring forward truly innovative and unique near to market solutions that have the potential to be scalable. Already we have witnessed the success of new product and system trials during the first two years of the AMICH project and we know that there are many more companies out there who are innovating and can play their part in helping to transform the sector. We need to find more sustainable ways of building quality new homes and achieving a net zero carbon built environment, and we need gamechangers who can support this transformation.”
The AIMCH project aims to develop know how that supports the key sector stakeholders deliver 120,000 homes for the same or less cost than traditional methods, built 30% quicker and has the potential to impact on 35,000 homes being delivered by AIMCH partners across the UK each year. Successful applicants will be invited to participate in a workshop hosted by one of three AIMCH partners, L&Q, Stewart Milne Group or Barratt Developments Plc.
Innovators who can play their part in delivering the project aims are encouraged to submit their proposals by completing the application form on the AIMCH website at: www.aimch.co.uk/news/aimch-suppliersandpit-challenge
Vision for ‘Deploying Modular Housing’
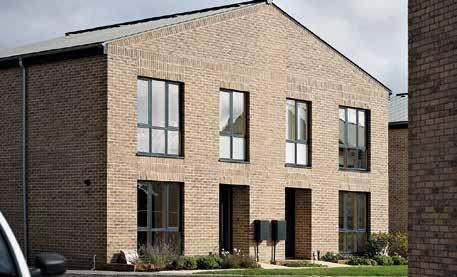
A new report has called on the government and housebuilders to come together and pave the way to create more UK homes using modular construction. The ‘Deploying Modular Housing in the UK’ report is the work of affordable homes-led placemaker Places for People and the University of Cambridge’s Centre for Housing and Planning Research. Together, they have outlined a joint vision for viably accelerating the use of modular construction in the UK market.
Among the recommendations within the report are calls for government support – both financially through grants and subsidies for developers using modular technologies, and through planning policy incentives. It also calls for industry standards and warranties akin to traditional builds, something the authors say will ‘provide certainty and confidence’ not only for housebuilders, but for end users and for traditional lenders who are sometimes cautious of loaning on modular homes.
The answer, the report says, lies in systematic data capture and evidence collection by housebuilders to create a strong evidence base of the benefits of offsite housing construction and MMC – something which would help to combat customers’ mistrust, overcome risk aversion, and boost confidence among lenders.
Scott Black, Group Executive Director of Development at Places for People, explained: “There are so many potential benefits to creating homes using modular technologies, but there are a host of current barriers and constraints that need addressing. Issues such as regulatory and approval barriers, skills shortages in the factories and a lack of cross-sector support are hindering the growth of modular construction – slowing down the take up.
“As an industry, we have the vision and the capabilities, but we need to pull together to address the barriers outlined in this report, and pave the way for a sustainable, modular future, one underpinned by an adequately skilled workforce who can drive the technology forward – helping establish it as a credible building practice for future consumers.”
The report also addresses the skills shortage in the UK sector, with traditional and modular building skills varying greatly. Gemma Burgess, Director of the Cambridge Centre for Housing and Planning Research at The University of Cambridge, co-authored the piece and added: “Another important factor is the need for investment in the development of a different set of skills than those used on traditional sites. This can be achieved by equipping the industry’s labour force with the necessary tools – including digital literacy and the use of new software and knowledge in offsite manufacture. This will all go hand in hand with retraining schemes and education programmes in collaboration with national and local government, education providers, industry bodies and the housebuilding industry.”
The report also proposes the idea of ‘innovation champions’ among housebuilders and developers – individuals and companies who actively use modular and offsite approaches and MMC, in order to boost their efforts and promote the benefits of innovation. Other recommendations include proposals for the standardisation of materials, and having a ‘kit of parts’ to be used across the industry by different manufacturers – something which Scott Black again says will come through collaboration: “The more we share, the more we will learn. There do however need to be initiatives to promote this within the housebuilding industry – the Building Better group (NHF 2020) for example. Such plans would provide structures for effective communication, synthesise learning, and help to build networks and collaboration opportunities.”
The report ‘Deploying Modular Housing in the UK’ can be downloaded and read at: https://placesforpeople.co.uk/news/ publications
DC Timber Systems Receives STA Assure Silver Status

DC Timber Systems, timber frame kit specialists, a division of The JR Group, has been acknowledged with a silver status accreditation by the Structural Timber Association (STA), through its STA Assure scheme. This marks the first award to collected by the Ayrshire-based firm.
The STA Assure membership and quality standards scheme, is designed to benefit both customers and members alike, promoting the differing specialisms and quality standards held by STA members. This is the first accreditation assigned to DC Timber from the STA since its creation in 2020. Based in Dundonald in Ayrshire it specialises in the design, manufacture and erection of structural and full timber frame kits throughout Scotland and the UK.
Ian Samson, Managing Director of DC Timber Systems, said: “We are delighted to be awarded silver status from the STA, and it reflects the hard work of the team in-house in delivering quality procedures, management systems and product performance as well as external accreditations held by STA members, offering clients complete transparency. As a relatively new business, we are thrilled to further demonstrate our exceptionally high standards to the market and offer complete reassurance for our customers.”
The JR Group, including DC Timber Systems, employs around 200 staff and was founded in Govan in 1995. It started as a scaffolding business and is now one of the largest building and construction firms in Scotland. The business operates throughout Scotland and Northern England working on behalf of a number of the UK’s leading housebuilders, registered social landlords and private clients.
Source: www.thejrgroup.co.uk
Wolverhampton Set to Accelerate Sustainable Industries
Wolverhampton has become the first English city to sign the European Circular Cities Declaration – a major environmental agreement designed to accelerate the adoption of circular economies across the continent. The certification of Wolverhampton as a Europe-leading centre of green growth is spearheaded by the city’s expertise in sustainable and offsite construction.
Part of the University of Wolverhampton, its Springfield Campus will be Europe’s largest specialist academic centre for architecture and built environment, offering world-class teaching, research and training in modern methods of construction (MMC) and revolutionary remediation techniques to unlock brownfield development. Firmly establishing the city’s offsite expertise is the arrival of a new £17.5million National Brownfield Institute (NBI), created to help the construction industry unlock disused land for greener, safer and cheaper building projects.
Cllr Ian Brookfield, Leader of City of Wolverhampton Council and Portfolio Holder for Economy and Innovation at the West Midlands Combined Authority (WMCA) said: “Our city is at the helm of the sustainable revolution in construction, with the National Brownfield institute (NBI) and best-in-class research from the University of Wolverhampton putting us on the map as a unique centre of excellence for environmental development and regeneration. These strengths form a critical lever for enhancing our economy post-pandemic, opening up opportunities to unlock new investments, create jobs and boost skills training for local people in a sector that is becoming increasingly vital to achieving a Green Industrial Revolution.”
The city is also driving forward the UK Government’s agenda to expedite the delivery of homes built using offsite, as the formal base for the Ministry of Housing, Communities and Local Government’s new MMC Taskforce. This follows the Department’s earlier decision in February 2021 to house a second ministerial headquarters in Wolverhampton, in acknowledgement of the Black Country’s rising influence in sustainable housebuilding.
Andy Street, Mayor of the West Midlands, said: “We are already taking bold strides here in the West Midlands to protect our environment and provide the good ‘green jobs’ of the future. Just as we were the home of the industrial revolution in the past, this commitment by Wolverhampton City Council helps demonstrate we’re now the home of the ‘green’ industrial revolution of the future. It means using modern methods of construction which are friendlier on the environment, while providing new highly skilled, well paid job opportunities. It means taking advantage of new digital technologies, and training local people with the skills we’ll need to seize these opportunities. And it means helping people access new job opportunities through improved public transport connectivity, helping increase the size of our economy, whilst reducing carbon emissions and our impact on air quality.”
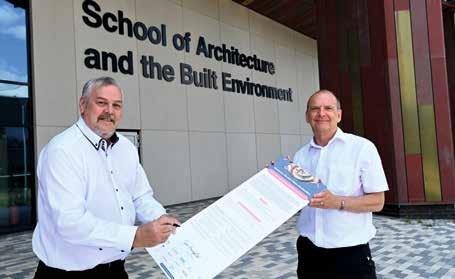
Source: www.wmgrowth.com
NHBC Accepts Celebrates First Year in Operation
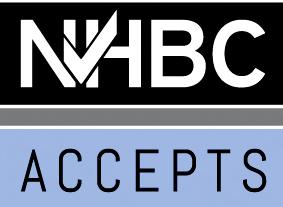
The UK’s leading warranty and insurance provider for newbuild homes marked the first anniversary of its service for innovative products and systems – NHBC Accepts. Launched in July 2020, the service has now accepted a range of products and systems, which over the course of the year have helped in the delivery of more than 5,000 innovative high quality new homes across the UK. NHBC Accepts – endorsed by the Government’s Modern Methods of Construction (MMC) Champion, Mark Farmer and recognised by Homes England and UK Finance – enables quicker assessment of a home for warranty and reduces the risk to the builder of delays in their project. Any product or system with the NHBC Accepts logo will have been rigorously assessed to ensure it can meet NHBC’s robust standards, giving confidence to developers, investors, lenders and homeowners.
NHBC Innovation Manager Richard Lankshear said: “We know from feedback that once a product or system is given the NHBC Accepts green light that this creates confidence in quality, long-term durability and traceability. We actively assess construction quality both on-site and offsite to verify that each product is suitable and acceptable to meet the standards set to obtain our ten-year NHBC Buildmark warranty.
“With the demands on the industry to increase the volume of new homes and the simultaneous challenges around materials and skills, we are at a critical stage in the development of MMC. We are proud to be using our scale, expertise and knowledge of house building to work with manufacturers to provide the confidence that innovative products and systems can meet and sometimes exceed the same high standards of quality and durability as traditionally-built homes.”
Once accepted, NHBC’s Innovation team continue to review quality through factory and site inspections and seek feedback from those working with the product on-site. This knowledge is shared with the system owners to help continually improve their product. Ultraframe’s panelised roof and gable wall system was one of the products added to the NHBC Accepts portal earlier this year.
The firm’s Design and Development Director Andrew Thomson, explained: For us, an NHBC Accepts certificate demonstrates that our product has been thoroughly reviewed by the team, in turn giving confidence to prospective buyers.”
Source: www.nhbc.co.uk
Premier Modular Awarded HS2 Contracts
Premier Modular has been awarded multi-millionpound contracts to provide project offices and welfare facilities for 15 sites that form part of the first phase of HS2 – the high-speed rail line. Awarded by Skanska Costain STRABAG Joint Venture (SCS JV), the contracts are for sites along the final 26.4km of HS2 to the southern terminus at London Euston.
Premier is delivering more than 15,000sq m of buildings made up of over 500 modules configured to SCS’s precise requirements and specification. The facilities will accommodate open plan offices, meeting rooms, break-out spaces, showers, drying room, toilets, first aid room, and canteen. Each building is being installed complete with lighting, air conditioning, fire and security alarms, toilets, partitions, and doors.
The buildings will be in use for at least five years and have a number of sustainability features to minimise impact on the environment, including rainwater harvesting to provide water for site operations such as dust suppression, low energy lighting, PIR lighting sensors, low water consumption showers, dual flush toilets, and effluent tanks to minimise discharge into local drainage systems.
Some of the sites are in close proximity to existing railway lines requiring liaison with teams at Network Rail and careful logistical planning particularly for the building installation phases. Commenting on the contract awards, John Harrison, Section Lead Construction Manager at SCS JV, said: “Premier has developed the most cost-effective building solutions that met our requirements and budget. Their team has been very flexible, adapting the designs to our changing needs, and with a strong emphasis on customer care.”
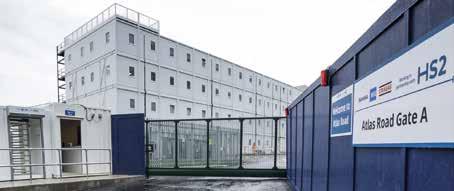
David Harris, Managing Director of Premier Modular added: “We are delighted to be contributing to this important infrastructure project. As a Yorkshire business we know just how critical HS2 is to rail projects in the North and how it will help to rebalance the UK economy. Our aim is to provide the best quality office and welfare facilities in the construction sector. We were able to offer building solutions to SCS to suit a wide range of sites, in compliance with Building Regulations Part L and to stringent fire ratings because the facilities will be in use for at least five years.
“On each project we are working to short programmes and on some highly constrained sites near to live railway lines. We have invested £12million in our hire fleet in the last 12 months and have expanded our workforce with an additional 100 people in the same period to meet the rising demand for our building services. The scale of the HS2 projects for Premier is a significant factor in that investment.”
HS2 is designed to be the new high-speed railway linking up London, the Midlands, the North and Scotland, serving over 25 stations, including eight of Britain’s 10 largest cities, and connecting around 30 million people.
Courtesy: Absolute Photography
www.premiermodular.co.uk
As the united voice representing the sector, the
Modular and Portable Building Association (MPBA)
offers valuable industry insight, guidance and ongoing research to significantly improve the volumetric modular building process. mpba
modular & portable building association
benefits of membership
Raising Industry Profile Through Strategic Marketing Quality Training and Knowledge Transfer Access to Learning Hub FREE Health & Safety Guidance and Support FREE Technical Advice FREE Employment and Law Services FREE Industry and Legislative Updates


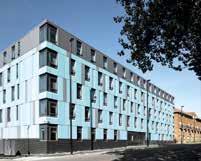
for more information:
call: 0870 241 7687 email: mpba@mpba.biz visit: www.mpba.biz
Canvas and Beyond Housing Create Eco-friendly Modular Development
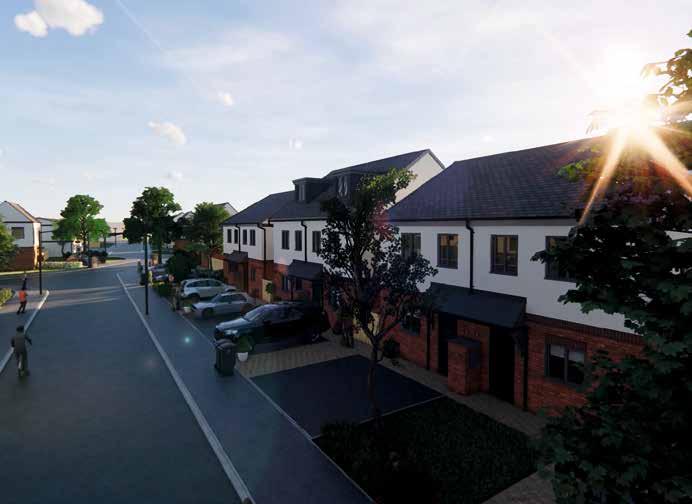
Beyond Housing is investing £19.5million into a new housing development of 117 family-ready and ecofriendly homes in Stockton-on-Tees. Beyond Housing, in partnership with Canvas Homes, is constructing 51 homes for affordable rent, 34 for shared ownership and 32 for rent to buy on the Princeton Drive development site, which will become the largest modular housing scheme in the North of England.
Situated on a large brownfield site between Durham University’s Queen’s Campus and the Tees Barrage, Princeton Gardens will offer fantastic waterside views of the River Tees and Stockton’s iconic Infinity Bridge. The newbuilds will include two, three and fourbedroom homes with each floor precision-engineered offsite under controlled factory conditions and then transported and craned into position.
Canvas’ modular homes use high quality materials with high thermal performance that exceed regulatory requirements. By constructing the homes offsite, Canvas is able to reduce energy use, materials, waste, noise pollution and disruption, making it an environmentally friendly and efficient way to build homes. Harrogate-based Canvas Homes is pushing the envelope to reduce waste as part of this development by using recycled steel piles from de-commissioned North Sea oil platforms and by pioneering precast foundations which are also made offsite. Situated on a large brownfield site between Durham University’s Queen’s Campus and the Tees Barrage, Princeton Gardens will offer fantastic waterside views of the River Tees and Stockton’s iconic Infinity Bridge.
Frances Barlow, Development Manager at Beyond Housing, said: “We are committed to building quality homes in desirable neighbourhoods and we are sure that these new family homes in Stockton will be highly sought-after additions to the area. We are pleased to be working with Canvas Homes to deliver these eco-friendly modular homes, and as they are largely constructed offsite, we can minimise site disruption and reduce waste while keeping a focus on sustainability.”
James Mottram, CEO of Canvas Homes, said: “We are proud to be working with Beyond Housing and Homes England to bring forward the 117 high-quality, eco-friendly homes in Stockton as part of the largest modular housing scheme in the North of England. This partnership creates an opportunity to deliver a true mix of tenure on sites, enabling the people of Stockton to live in a high-quality home through rent to buy, shared ownership or affordable rent.
“The development of Princeton Gardens is a hugely important milestone for Canvas Homes ahead of the launch of our new BTR REIT which will create a portfolio of accessible high-quality family homes to rent across the UK, which will significantly increase affordability and consumer choice. We passionately believe this new development of high-quality homes will complement the exceptional regeneration work being delivered in Stockton town centre.”
Ian Hall, Senior Development Manager at Homes England, said: “As the Government’s housing accelerator we are excited to work with Canvas Homes and Beyond Housing to unlock a site where they are bringing forward the largest modular housing scheme in the north. We’re passionate supporters of MMC and the sustainability benefits that they bring. As such we’re excited to see Canvas Homes’ plans to go the extra mile and bring these high-quality, eco-friendly homes come to life.”
Source: www.beyondhousing.co.uk www.canvashomes.uk/teesbarrage
Leeds Hospitals Look to DfMA
The latest concept designs for two new state-ofthe-art hospitals in Leeds – inspired by the Yorkshire landscape – have been unveiled. The event took place on the site of Leeds General Infirmary, parts of which are being demolished to make way for the two new hospitals – one for children and one for adults.
Interdisciplinary practice, BDP, has been appointed by Leeds Teaching Hospitals NHS Trust (LTHT) to lead the architectural design of its Hospitals of the Future programme, part of its long-term vision to transform healthcare facilities for patients and staff in Leeds and the wider region. The future-proofed plan uses BDP’s knowledge in designing clinical and patient pathflows, using digital design and offsite construction including significant integration of Design for Manufacture and Assembly (DfMA) techniques. This will create an innovative and flexible hospital that meets the demands of modern clinical requirements and future medical developments.
Andrew Smith, head of healthcare at BDP, said: “By applying our experience in designing the best healthcare facilities around the globe we are delivering a healthy and thoughtful hospital design for Leeds that looks to the future of best practice and innovation.
BDP has proposed a hospital structure that is shaped like the contours of the Yorkshire fells and dales, with a large island garden and play deck at its centre. Outdoor space and play areas were some of the facilities that children and young patients suggested in a design competition, held last year, which have inspired the architects with their latest concept.
The development of a new adults’ hospital, along with a new home for Leeds Children’s Hospital, is set to be one of the most significant healthcare projects in the UK. Julian Hartley, Chief Executive of Leeds Teaching Hospitals NHS Trust, said: “The building of our two new hospitals is the most important development in Leeds city centre for a generation. And, in terms of hospitalbased healthcare, it’s the most important development in the city centre since 1868, when Leeds General Infirmary was first built. Dame Linda Pollard, Chair of Leeds Teaching Hospitals NHS Trust, added: “Digital technology and worldleading innovative techniques will be central to the services provided in the new hospitals whilst the old hospital estate will be redeveloped as part of the City’s Innovation District, bringing about direct and wider economic benefits of up to £11.2billion in net present value terms and more than 3,000 jobs. This redevelopment of the old LGI site will also help us to preserve some beautiful buildings with significant history to their former glory.”
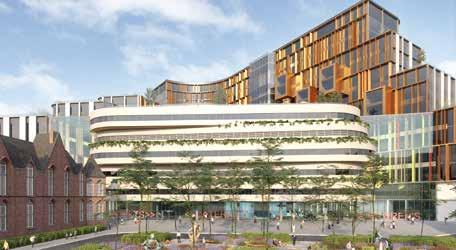
Source: www.bdp.com
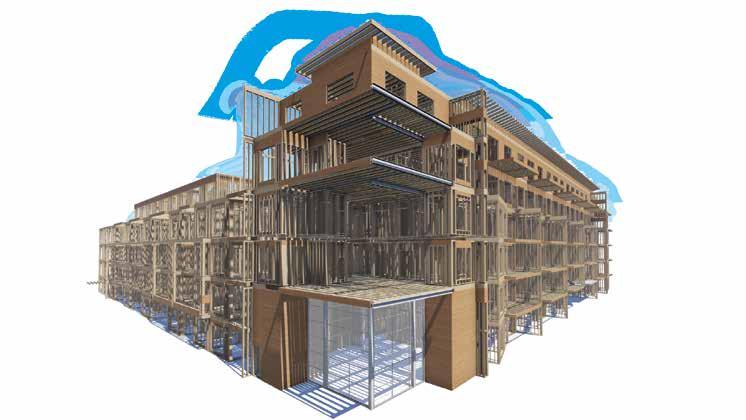

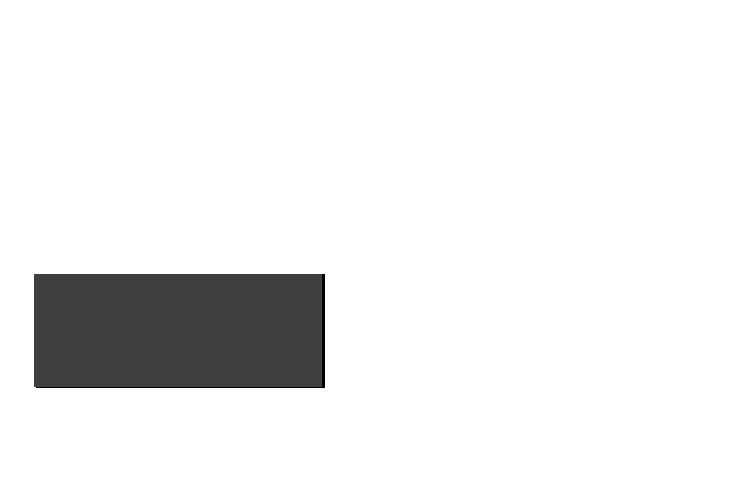
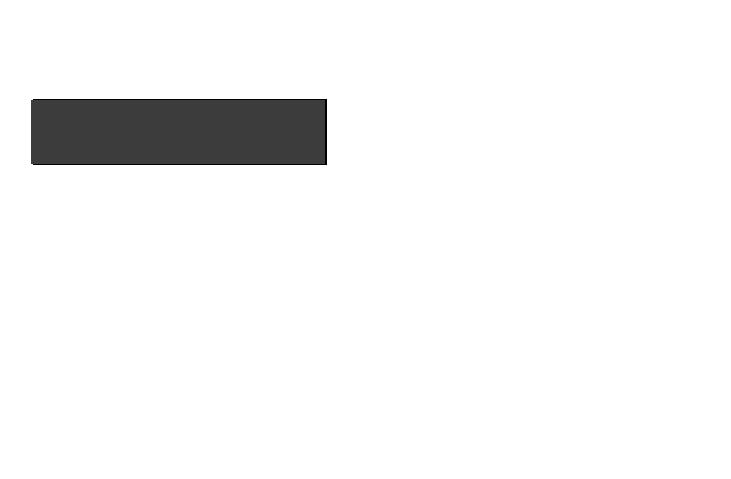
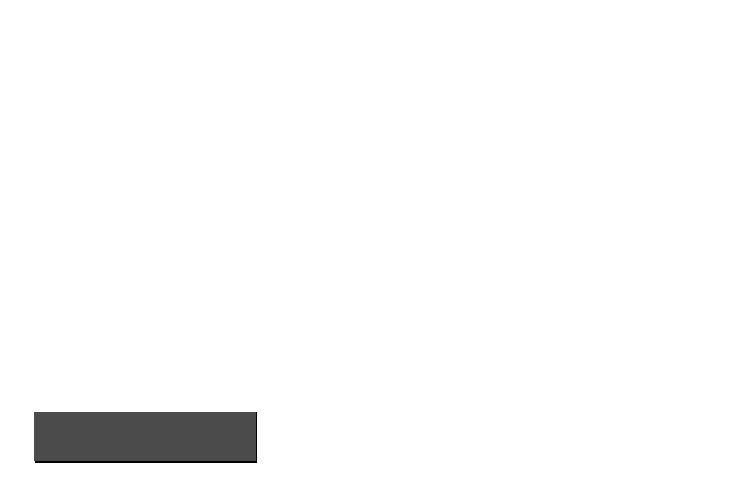


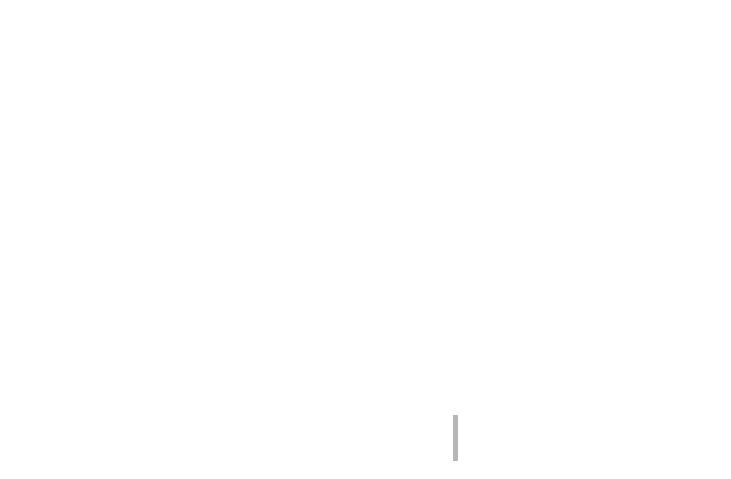
Major Investment Boosts SO Modular Production Capacity by 700% CITB Welcomes New Chief Executive
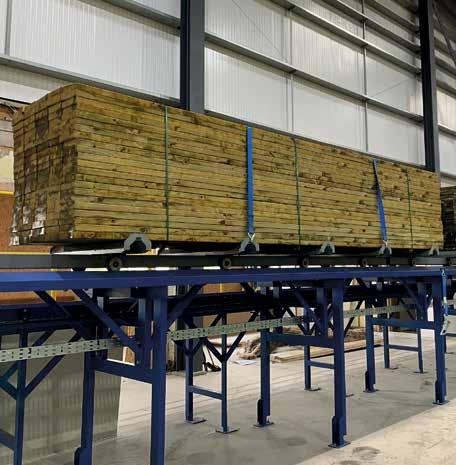
SO Modular, the timber frame construction specialist, has increased its production capacity by 700% thanks to a significant six-figure investment in new machinery at its new 350,000sq ft timber and modular manufacturing facility in Neath, South Wales.
The development of the facility began in April 2020 and is set for an official launch at the end of summer 2021. Once completed, with all the new machinery installed and running, the site will immediately be able to expand from its current production capacity of 500 homes per year to 3,500 homes per year on a single shift. The timber and modular manufacturing facility will also be a zero-carbon, sustainable site, creating a number of skilled employment opportunities in the local area.
SO Modular has been able to fund the purchase of its new machinery through an Innovative Housing Programme (IHP) loan with Tai Tarian – one of the largest social landlords in Wales. The new machinery is considerably more efficient – both in terms of speed and energy usage – than that currently being employed by the company. It will also produce less waste and will contribute towards the company sustainably manufacturing low carbon homes. The new machinery includes a treatment tank, production lines, a biomass boiler, a Hundegger TURBO-Drive II Saw, a vertical saw and a factory blow insulation machine. The Hundegger TURBO-Drive II Saw will speed up timber processes, increase accuracy and reduce waste with the use of computer software technology. The saw’s optimisation software means that any offcuts it produces are automatically cut into smaller standardised pieces, which can then be used as other functional aspects of modular joist and cassette manufacture. The new treatment tank will allow high- and low-pressure treatments, meaning SO Modular will be able to treat not only standard timber but also timbers that require a higher level of treatment such as sole plates. This makes it far more cost effective than imported pre-treated timber, helping the company to achieve its affordable homes target.
Charlotte Hale, Operations Director at SO Modular, said: “We’re very excited to announce the purchasing and acquirement of new machinery, with the help of the IHP Tai Tarian loan. These new, efficient machines will go a long will in aiding us to establish a state-of-the-art, sustainable manufacturing facility in Wales. Furthermore, this acquirement will allow us to create new jobs in the area and provide even more affordable, low carbon homes to help the UK meet zero-carbon targets, protect the environment and address the country’s need for affordable housing.”
Source: www.somodular.co.uk
Tim Balcon is the new Chief Executive of the CITB – a former apprentice who brings a strong track record in skills, training and organisational development. Tim has led professional and membership bodies, the most notable being as Chief Executive at the Institute of Environmental Management and Assessment, where he transformed its vision and performance, leading to year-on-year growth.
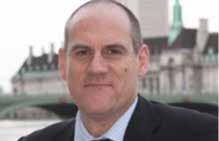
“As a former apprentice I know how much having the right skills at a young age can transform your whole career and support your employer,” said Tim Balcon. “That’s why I’m so passionate about skills and am thrilled to be joining the team at CITB to help many more people join the construction sector and to have long and fulfilling careers within it.”
Tim’s knowledge of education and skills was reflected in his previous appointment to the board of Ofqual at a time of major education reform, and prior to this he was also a member of the UK Vocational Qualifications Reform Board. Tim started his CEO journey back in 1999 as CEO of The Gas and Water National Training Organisation, leading a fledgling organisation from £400k turnover to over £7m in three years. He started out from a mining town in South Yorkshire as an apprentice service engineer with British Gas in the early 1980s, where he spent his early career.
Peter Lauener, CITB Chair, said: “I’d like to welcome Tim to CITB, an outstanding candidate for the post of CEO. He brings considerable experience in skills and training and strong leadership qualities. This is a crucial time for construction skills across Britain, and the Board is looking forward to working with him to drive forward our strategy to meet the skills needs of employers.”
Mark Reynolds, CEO of Mace Group and co-lead of the Construction Leadership Council skills workstream, added: “I am looking forward to working closely with Tim as we address the huge skills challenges we face in construction. Tim’s journey from apprentice to Chief Executive is one that will resonate with the industry and will inspire others to follow in his footsteps.”
Tim takes over from outgoing CITB Chief Executive Sarah Beale, who will relinquish her post at the end of September 2021.
MEDITE SMARTPLY Playing Key Role at COP26
MEDITE SMARTPLY will play a crucial role in the construction of the COP26 House, a zero carbon, timber frame building built by Beyond Zero Homes. The project will showcase low carbon, circular solutions in building and living during the 2021 UN Climate Change Conference in Glasgow this October.
Chris King, Managing Director at MEDITE SMARTPLY said: “We are delighted to be part of this project that will help demonstrate the boundless opportunities for sustainable timber based solutions in construction. Actions speak louder than words, and this building encapsulates MEDITE SMARTPLY’s commitment to building a more sustainable future. The products and systems for fighting the climate emergency are already available. We in the construction industry have not only the opportunity but the responsibility to put theories into action and show the world how we can build and live sustainably, using timber and ecologically responsible solutions.”
The members of Beyond Zero Homes are united by a common goal that goes beyond zero carbon: to demonstrate how beautiful, affordable, healthy homes can be developed with minimal impact on the environment, throughout their lifecycle. The one-bedroom house will be built on a 10m x 5m footprint. It has been specifically designed to use homegrown C16 Spruce to avoid the need for imported timber, and the construction is based on a 1.2m grid to be easily panelised and prefabricated. These elements lend themselves perfectly to the specification of SMARTPLY OSB, sustainably produced in Ireland and already stored across the UK. As part of the Coillte Group, the company prides itself on its sustainable supply chain and manufacturing processes, meaning the company’s products are as environmentally conscious in their make up as they are in their application.
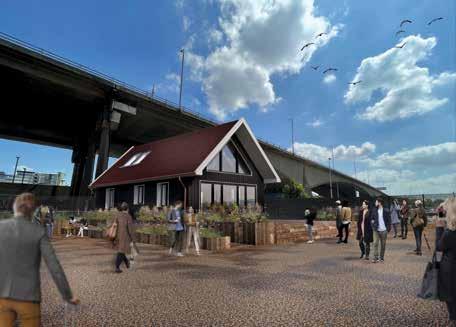
The build is due to commence soon. Find out more and follow its progress at: beyondzerohomes.co.uk/cop26-house/
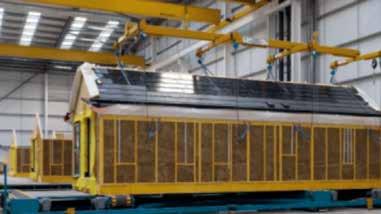
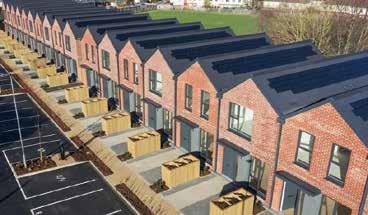
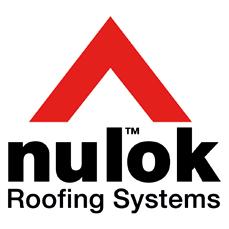
YOUR OFFSITE SLATE & SOLAR ROOFING PARTNER
Fully recyclable Install fully offsite 30-year warranty Light-weight Low maintenance Solar ready
Airspace Developers Launch New Association
Kier Appointed to Build New £43m Surgical Centre
Four of the UK’s leading airspace developers recently joined forces to launch the Association of Rooftop and Airspace Development (ARAD) to champion the sector and act as a unified voice for developers and associated stakeholders involved in the development of airspace.
The independent, non-profit organisation will promote learning, innovation and development of good practice, while lobbying for its members’ interests and helping to unlock much needed housing at both a local and national level. The founding partners are Apex Airspace, Click Above, Fruition Properties and Upspace. Collectively, they have secured and developed numerous airspace homes and have been directly involved with the 2020 Permitted Development for Upwards Extensions, helping to lay the foundations for future growth and innovation.
Airspace and rooftop development refers to the ability to build on top of existing buildings, whether residential, commercial or industrial, to deliver new homes by typically adding one or two storeys. It is particularly effective in densely populated areas and is a sustainable way to meet increasing demand for housing while preserving existing architecture, aligned to ever evolving innovations and offsite construction. This means that such developments can now be
Kier has been appointed by NHS Golden Jubilee to deliver a new £43million surgical centre at its hospital in Clydebank. This latest award follows Kier’s successful completion of the eye centre for the hospital and is part of the hospital’s expansion programme. Cabinet Secretary for Health and Social Care, Humza Yousaf visited the hospital to officially mark the start of this new project.
Procured through Frameworks Scotland 2, the surgical centre will provide a range of first-class facilities, including theatre suites, a surgical admissions and recovery unit (SARU), a surgical administration space, central sterilising and processing department facilities, endoscopy unit, orthopaedic amenities, outpatient and pre-operative spaces, as well as staff wellbeing spaces. When complete, this building will support the hospital to provide over 9,400 new outpatient consultations, more than 4,400 pre-operative assessments and over 13,900 other procedures.
Kier will utilise modern methods of construction (MMC) throughout the build, including a hybrid produced with greater ease, precision and efficiency. A spokesperson for ARAD, said: “Airspace is part of the future of housing – it has vast potential across London and the UK to help unlock much needed homes in a non-invasive way. ARAD aims to bring together organisations who want to and have the expertise to work in airspace - whether investors, architects, developers, local authorities or consultants - to learn from each other and champion airspace so that rooftop development can flourish while maintaining high standards for the betterment of all stakeholders.
“Rooftop development is not the same as ground-up development. In order to effectively deliver homes or office space, there are many more pitfalls to overcome, including the legal aspects, fire safety considerations, and resident engagement through to the actual build itself. ARAD will act as a forum to help
precast concrete frame, the envelope of the building being precast with windows and brickwork completed offsite. The project is due to be complete by June 2023 and as part of Kier’s commitment to leaving a lasting legacy in the areas in which it builds, at least 65% of its supply chain will come from a 30-mile radius of the hospital. Kier will also provide a range of opportunities to the local community including at least ten apprenticeships, work placements, job opportunities and career talks at schools.
Phil McDowell, Regional Director at Kier Regional Building North & Scotland, said: “Following on from our recent success with NHS Golden Jubilee delivering its new eye centre, we are proud to have been given the opportunity to continue to deliver for patients and the local community with this prestigious ensure the sector is better understood and that there is a clear Code of Conduct to ensure that the sector can grow in a professional manner.”
Over the last ten years London has delivered an average of 28,000 new homes per year and between 2018-2019, this figure reached 36,000 – only 55% of the 66,000 needed. Research conducted by global property consultancy Knight Frank has found that as many as 41,000 new dwellings could be built in central London using rooftop development space alone, providing a clear part of the solution to alleviating the housing shortage.
Pictured: ARAD founders, left to right - Laith Mubarak (Director, Click Above), Andrew Powell (FD, Apex Airspace), Mani Khiroya (CEO, Fruition Properties), Richard Taube (MD, Upspace)
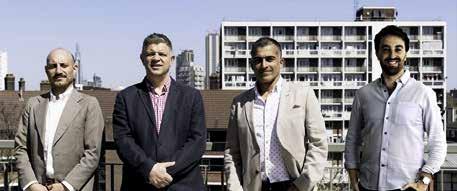
Source: www.arad.uk
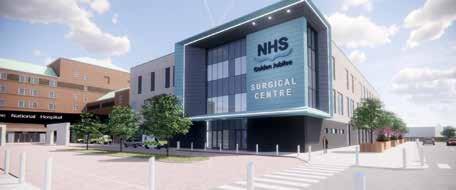
scheme. We have extensive experience delivering healthcare schemes and we will utilise our skill and technical excellence to deliver a first-class facility for the hospital and people of West Scotland.”
Chief Executive of NHS Golden Jubilee, Jann Gardner, added: “We recently marked the completion of Phase 1 of our expansion with the opening of our new, state-of-the-art, eye centre: the first of the National Treatment Centres. This started treating patients in November 2020 and this year is estimated to carry out over 12,000 cataract procedures. We now look forward to benefiting patients across Scotland with our new surgical centre.”
Source: www.kier.co.uk
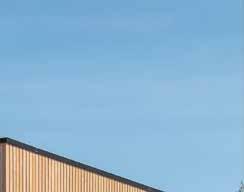
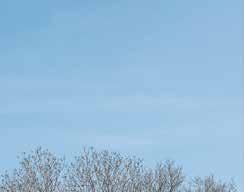
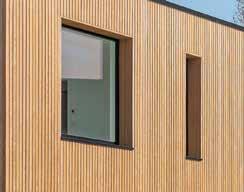
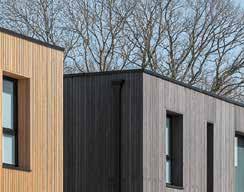
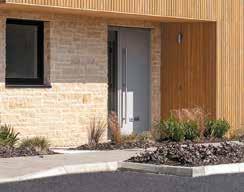
Windows – Doors
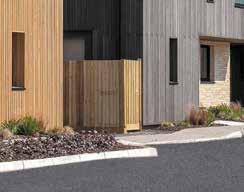

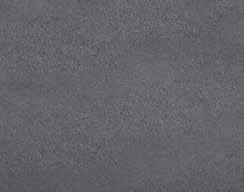

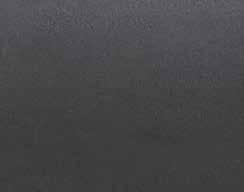

BUILD BACK BETTER & SMARTER
Wates Construction Group recently appointed Inna Lim as its new Strategy and Integration Director. We caught up with her to find out more about emerging technologies, innovation and championing more offsite manufacture.
Q: As new Strategy and Integration Director at Wates, can you say more about the role and what you want to achieve with it?
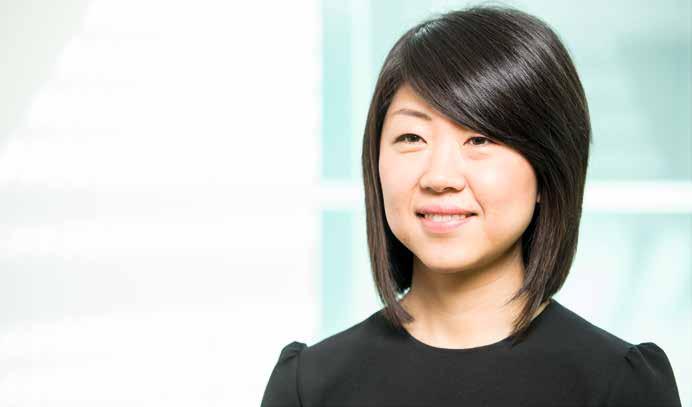
Inna Lim (IL): I am accountable for driving a new integrated business across the Wates Construction Group. This a new role and together with key members from our engineering and specialist businesses – SES Engineering Services, Wates Building Services, Wates Dry Lining Services and Prism Offsite Manufacturing – we aim to create a unique market offering that gives Wates Group a competitive advantage across a number of sectors. Most importantly, I want to help our organisation offer construction and engineering solutions that are built around our customers’ needs. So, starting with the customers and end users in mind and then working backwards to our pre-construction and operational activities.
Q: What are the benefits of integrating the four businesses and what do you hope to achieve?
IL: Ultimately, this is about delivering efficiencies and adding value for our clients and business. But it’s also responding to a range of challenges UK construction companies face today – be it pandemic-related or age-old problems relating to efficiency and quality. Our primary objective here is to share the technical expertise, capabilities and thinking from our four specialist businesses within the Wates Construction Group. Our industry peers continue to approach offsite manufacturing as an isolated concept, but we plan to dominate this space by enhancing our existing offsite facility, Prism, and developing a fully integrated in-house capability of smart offsite solutions. This will provide our customers with rapid and optimum solutions and support during the project’s life cycle.
1
Q: Prism has been hugely successful in delivering prefabricated MEP with a modular approach – will the facility be developed further and is offsite MEP still not fully understood by the wider construction industry?
IL: We’re putting a lot of energy into enhancing the capabilities and capacity of our Prism facility –
particularly around enhancing our offer through a more standardised approach. Currently our solutions are quite bespoke, so we’re heading towards a more ‘kit of parts’ approach, where at a project’s inception our construction partners, both internally and externally, could select a product that could drive the design and architecture of the rest of the building. This would naturally lead to upgrades within the factory in terms of the products we deliver. In terms of whether offsite MEP is fully understood, I’d say most understand its importance but conveying value for money vs a traditional approach can sometimes prove difficult, since the comparison doesn’t happen across the entire value chain of the project delivery.
Q: The use of technology and digital tools within factory environments is central to offsite manufacture – is this the future of offsite’s successful wider adoption and how is the Construction Group and the wider business driving this?
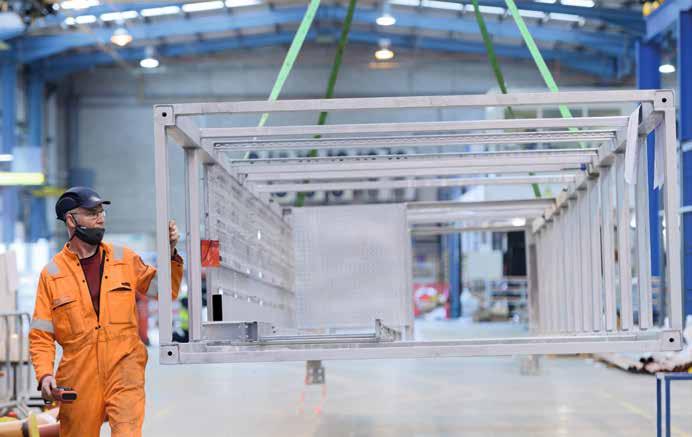
IL: Technology and digital tools are crucial to any industry but for offsite they aren’t central to future adoption. Though very important, the success of offsite depends on industry players – especially our customers’ mandating offsite as the only delivery option for their projects. The construction industry must also understand how to integrate offsite early on, and digital tech will play a massive role in supporting that early engagement. For example, if we had a standardised ‘kit of parts’, we would have digital information held on each of our products. If we were then engaged early, we would be able to freely share that digital information with our construction partners as part of the design process, giving our clients a rich source of project information from day one.
Q: The type of skills required in the modern construction industry is changing rapidly – not least in the use of digital tools (BIM/AI/VR) being more important than ever – is that a fair assessment?
IL: Yes! Certainly, from an offsite, building services and digital perspective. Part of the challenge is that the broad range of skills required are extraordinarily high and hard to come by. You could, for example, have a skilled digital engineer, who knows little about the intricacies of building service installation, and this is where our integrated offer comes back in because we have all those different skill sets within the four businesses. By aligning those capabilities there’s a clear route for those skilled staff members to work together to find the best solution for a job.
2
Q: The construction industry is under huge pressure to reduce energy consumption and change material use to meet the UK’s net zero targets. How will the integrated businesses deliver a more energy-efficient built environment?
IL: An exciting part of the integrated business is the sustainability experts we have on offer – from smart building specialists to environmental engineers and sustainability specialists – who can work together to engineer the most efficient building from a building services perspective. By working alongside our construction colleagues early on, our integrated team can run models and come up with an optimum solution to help support energy efficiency on projects. For example, we might be able to advise on certain tweaks that could benefit the running of a building, such as altering the G-value of its windows, which could
reduce the need for excessive air conditioning and heating systems, which is hugely important from an energy-efficiency standpoint.
Q: The built environment is going through a huge period of change – not least with issues surrounding boosting quality and productivity. What other forces are driving change and what role will the integrated businesses play in solving these issues?

IL: The built environment has been going through a period of change for quite some time now. Issues around quality and productivity were identified as early as 1934 by Alfred Bossom, who said UK construction was a wasteful industry where construction took too long, was too expensive and was not satisfactory for its clients. Wates Construction’s solution to this is to focus on our people, productivity, and partners. We’re 100% dedicated to our people and passionate about helping them grow and advance. We’re currently going through a productivity revolution, looking at our processes and delivery, including – of course – a huge focus on offsite. And, lastly, we always strive to understand exactly what our partners and client base want, working with them to deliver.
Q: In a post-pandemic world encouraged to ‘Build Back Better’ – how do you see the offsite sector contributing over the next 18 months and what technologies and innovation do you see emerging?
IL: There are numerous ways offsite will contribute to ‘Build Back Better’, with technology playing a key role. Post-pandemic, the impacts of supply chain constraints and product supply, for example, will be challenging, but offsite takes away a lot of those risks since we’re not exposed to the same labour and resource constraints as traditional builds. Collaboration will also be critical, and we’ve invested heavily in digital collaboration tools, such as building a 360-degree immersive workspace, for our customers, supply chain partners and internal teams to work together to thoroughly understand a project, from design and efficiency to logistics and engineering. Looking ahead, there’s a whole host of future applications for this tech such as virtual training or creating digital twins of buildings.
3
For more information visit:
www.wates.co.uk
Images:
01. Inna Lim, Strategy and Integration Director, Wates Construction 02-03. The Prism facility has been instrumental in bringing precision offsite methods to the UK built environment