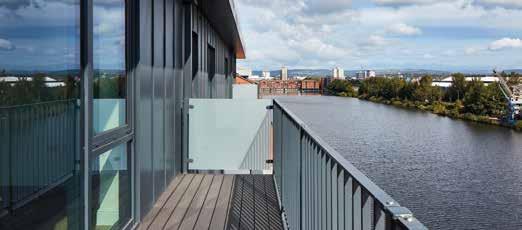
11 minute read
Pushing the Limits
CASE STUDY
Schooner Wharf is a mixed tenure housing scheme commissioned by Cardiff Community Housing Association that adopted passive solar design principles and is built to high environmental performance standards using the MetFrame system.
In response to affordable housing priority needs, Austin-Smith:Lord were commissioned by Cardiff Community Housing Association to design a newbuild mixed tenure housing development in a prominent waterside location in Cardiff Bay. The houses and townhouses are contemporary in design and utilise a combination of traditional and contemporary materials. This creates a development that has a readily identifiable and fresh, modern character whilst also providing the sense of solidity and reassurance that comes from the recognisable layout and scale.
The apartment block is constructed using light gauge steel offsite manufacture whilst the houses utilise timber frame kits. The Metsec loadbearing walls consist of 100mm wide vertical C section studs at max 600mm centres. Metsec components are rolled from pre-galvanised steel. All sections are cut to length and have holes punched to allow bolted connections. Walls are detailed in panels typically up to eight metres long by one storey tall that are pre-assembled offsite by Atkin Trade Specialists. The external face of the MetFrame external panels is clad with a 12mm cement particle board over which the external insulation
1
is installed. Structural steelwork is integrated into the MetFrame system where required.
Cantilever balconies and projecting bays are constructed from a hot rolled steel frame with galvanised finish and thermally broken from the MetFrame structure. These are installed when their supporting external walls are installed. The balconies are designed to allow a lightweight floor to be installed by others. Stairs are offsite assembled/fully welded units with in-situ concrete filled steel treads. They are fitted as each storey of MetFrame is installed. Lift shafts are included in the MetFrame. They have horizontal Metstrut channels bolted into the two side walls of the shafts for the lift manufacturer to fix to. Roof systems use Metsec joists typically 200mm deep at 600mm centres. This project follows on from a previous six-storey apartment block, delivered by the same contractor and design team, which was completed eight weeks ahead of programme by using the same MetFrame system. Lessons learnt from the previous project including a knowledge transfer partnership (KTP) with Cardiff Met University led to improved thermal performance of construction interfaces. The findings of this KTP led to better interface details for Schooner Wharf which in turn led to enhanced thermal efficiency and performance. The design adopted passive solar design principles and is built to high environmental performance standards which will reduce in-use costs. Fuel poverty is addressed through a highly efficient building fabric and energy strategy including use of renewables.
2
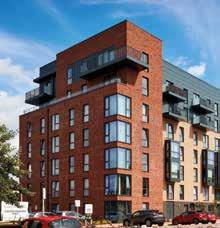
MetFrame was chosen as part of the wider environmental benefits it provides in addition to its cost and speed benefits. The offsite construction and detailed co-ordination prior to fabrication meant there was effectively zero waste and a low carbon footprint for the structural frame.
The speed of erection led to cost savings and allowed other trades to commence work simultaneously. An average of five Atkin Trade operatives was required on site taking just 21 weeks to install the structure of the seven-storey apartment block. Given the site was constricted between a quiet residential development and offices, the speed of construction and offsite construction minimised noise, disturbance and disruption to the local community.
Offsite construction generates up to 90% less waste than site-based building methods and achieves up to 90% fewer vehicle movements on site, compared to a traditional construction project – reducing noise, dust, congestion and carbon emissions. This project pushed the limits of the MetFrame system and required thinking outside the box to overcome the technical challenges of the design.
For more information visit: www.austinsmithlord.com
Images:
01-02. The apartment block is constructed using a well-understood offsite light gauge steel system. Courtesy Austin-Smith:Lord/Metsec
OFFSITE &
LEAN TECHNOLOGY
Offsite construction can become the ‘new normal’ says Stewart Dalgarno, Advanced Industrialised Methods for the Construction of Homes (AIMCH) Project Director and Director of Product Development at Stewart Milne Group.
The global pandemic will have a wide-reaching impact on us all. It is difficult to see how any industry sector will come through this unscathed and without re-examining how to do things differently. What will be important is that we emerge stronger and more resilient, and open to new innovative ways of working.
As the housebuilding industry begins to return to work, sites re-open, and companies re-examine their business strategies and models, it will become even more important to embrace new technologies and processes to ensure the restart and future development of the sector is done in a way that it can thrive long term.
With most construction sites having been on pause, efficient delivery will be vital as the industry restarts and
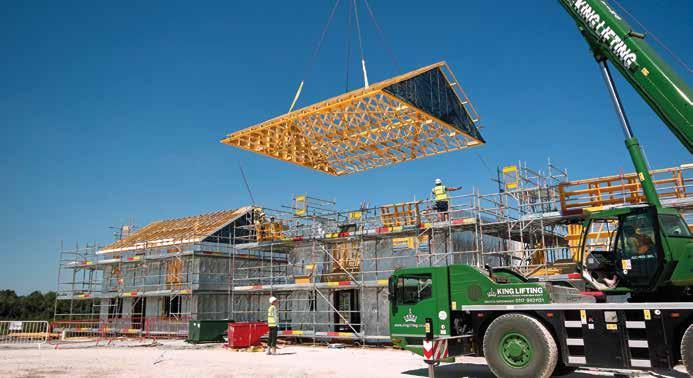
grows. Particularly as the demand for more high quality, cost-effective housing, that can be quickly and efficiently built, has never been more acute and will only build going forward.
During this global health crisis, our homes have provided a safe haven, a place to work and for many, a place of education. The need to deliver more homes, quickly and cost effectively will be essential in tackling the growing UK housing crisis, but it is vital that we are not simply back building, but instead building better homes. Key to this will be to embrace modern methods of construction (MMC), such as panelised offsite construction systems and lean construction, in a more integrated way capitalising on digital technologies and advanced manufacturing.
1
The Advanced Industrialised Methods for the Construction of Homes (AIMCH) project started 18 months ago to trial solutions that could help to tackle the UK housing crisis by mainstreaming the use of these methods and lean technologies. At that time, the consortium set out to transform how the construction industry builds homes to meet current and future demands. Today we are almost halfway through the three-year project, and more than ever, we are convinced that modern methods of construction, such as offsite panelised systems and digital working, offer unrivalled benefits, especially as we find our way through and out of this current crisis.
The fast delivery of much-needed housing is critical. However as the industry reopens, construction sites
2
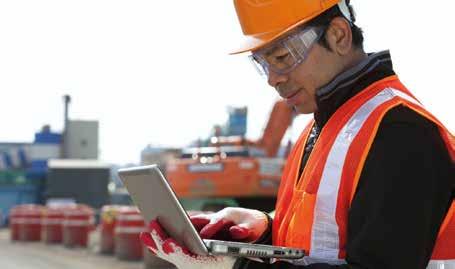
face operational restrictions. With less labour resource onsite, the potential reduction in the supply of materials, coupled with the physical challenges of getting them onsite, and maintaining social distancing safety measures, it will be some time before productivity is at the level is was pre-lockdown, never mind the level it needs to be at to tackle the growing UK housing crisis.
Offsite panelised construction offers a way forward and a viable solution, which is less labour intensive, with fewer personnel on site, unlike traditional building methods.
As part of the AIMCH project preCOVID-19, partners have been undertaking productivity measurement studies, using time and motion and more innovative blue-tooth enabled tracking of operatives to monitor site efficiency or traditional and a variety of offsite systems. This technology has potential to monitor safe social distancing, providing useful data on
3
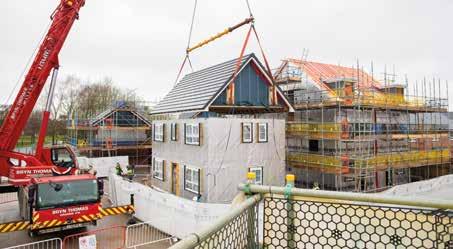
worker compliance social distancing and site operating guidelines.
Bringing panelised offsite systems on to sites can also aid a quicker and more efficient delivery of homes. AIMCH has been assessing the benefits of standardisation. Through research studies, the partners are now developing a suite of standardised product families, that can be configured and used within future housing pattern books. Providing a digitally enabled, efficient and costeffective home designs that can be built fast to higher quality standards with less labour input. Homes can be externally finished using conventional materials, to provide robust, durable and beautiful homes, to suit any planning or aesthetic requirement.
Offsite panelised building systems, helps business recover through securing a more integrated and robust supply chain, by adopting a manufacturing led approach, which can be scaled up quickly to meet demand. The AIMCH project has utilised automotive learning from around the world, to develop advanced manufacturing approaches, such as simulation, to build a model of the ‘future offsite factory’ where digital technology and automation, such as robotics, drives productivity lowering production costs and increasing capacity. The mathematical model and simulation program under development, will enable robust assessment and validation of future MMC investments, which will be crucial as the industry, housebuilders and businesses reset, recover and re-plan the future, during these uncertain economic times post-COVID-19.
Through industrialising housing, embracing modern methods of construction, the AIMCH solution will help attract new talent with digital, logistics, engineering, design, robotics and project management skills, making the sector more appealing to a wider employee pool. With more automation in a factory setting, digital working, integrated supply chains, lean construction assembly and with staff collaborating with onsite teams, the greater efficiencies achieved will support the construction of the additional 120,000 homes needed each year to address the UK housing shortage. That’s a challenge that the housebuilding sector simply can’t meet using traditional construction methods alone.
Offering integrated supply chain solutions, increased efficiencies, greater collaboration, increased productivity and commercially competitive mainstream offsite panelised construction methods, the AIMCH project has a significant role to play in the post-COVID recovery, with offsite construction becoming the ‘new normal’ in the sector.
For more information visit:
www.aimch.co.uk
Images:
01-03. Developers and clients need to embrace more advanced methods of construction such as panelised offsite construction systems and lean construction and capitalise on digital technologies
KEEP CARBON CLEVER
Wood for Good has played a huge role in promoting timber to the wider built environment for many years now. Campaign Manager, Sarah Virgo spoke to us about the plans ahead including the new Wood CO 2 ts less campaign.
Not everyone realises the full extent of wood’s benefits and that is what I have set out to address as the new Wood for Good Campaign Manager. We need to collaborate as an industry and communicate the benefits of building with wood to the construction industry and beyond.
I was prepared for a challenge when I took on the role six months ago, but along with the rest of the world, I was not prepared for a global pandemic. However, lockdown has not stopped me from setting out what I want to achieve, and I have been overwhelmed by the positivity, passion and dedication within the industry and its desire to provide solutions that work. Despite not being able to attend industry events and meet with those pushing for change, we have bonded over virtual meetings and established what we need to do to drive the agenda forward.
Climate change has been a part of my life for as long as I can remember and my interest in sustainability and nature runs deep. It is what made me seek out a career in marketing and communications for the third sector and how I became a member of the 2050 Climate Group in Scotland. I hope to use these connections to increase exposure for the timber
1
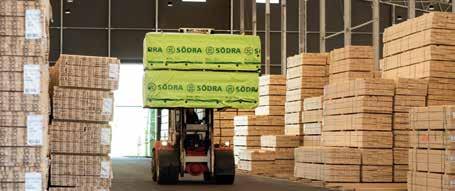
industry and inform those responsible for the design and construction of buildings about the benefits wood products can bring.
The timber industry is perfectly placed to take centre stage in discussions around how we can work towards zero carbon. It is not the only solution to climate change, but it is the best natural solution available to us, critical to building a circular economy. In addition to capturing carbon, we can’t ignore the inherent beauty of wood’s aesthetics, its flexibility and adaptability as a material, and its contribution to health and wellbeing as a product.
Wood for Good’s supporters have continued to share this message throughout the pandemic, despite the challenges they have faced. However, lockdown, if anything, has made our message stronger, highlighting the urgency and importance of combating climate change. We must embrace a green recovery and we will continue to do so through the Wood CO 2 ts less campaign.
Launched in the middle of July, Wood CO 2 ts less is an industry-wide campaign developed by Wood for Good, Swedish Wood, Confor, the Timber Trade Federation (TTF) and the Structural Timber Association (STA). We began with a generic launch of the message to engage the timber industry and influencers within the construction and sustainability sectors. Now, we are widening the campaign’s message to focus on the construction industry and policymakers.
The campaign has been a great success so far. In addition to backing from the main supporters, the timber industry is pledging its allegiance to the campaign. Södra, Vastern Timber, James Latham, James Jones, BSW and Scottish Forestry have all shown their support and through the campaign’s visibility, we have also seen new supporters join Wood for Good.
Planning for the future feels complicated right now. The pandemic’s long-term effects on industry, society and the environment will impact us for years to come. Yet, with the announcement that we have plunged into another recession, now is not the time to stand still.
Despite some positive reports on the reduction of CO 2 emissions while the world was on lockdown, they are on the rise again and will continue to plague us if we do not act. We must continue campaigning for wood as a natural solution to achieving net zero into 2021 and encourage those in the entire supply chain to help communicate this message. Together we will see the wood for the trees.
For more information visit:
www.woodforgood.com/CO2
Images:
01. Wood has a huge role to play in sustainable construction and low carbon buildings.
Courtesy Södra Wood