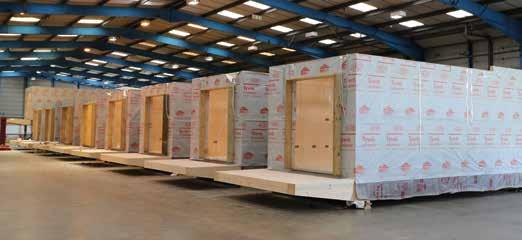
12 minute read
A Sign of the Times
CASE STUDY
The Hope Rise housing project in Bristol will see ZED Pods provide a revolutionary cost-effective, eco-friendly and affordable housing solution using timber volumetric offsite manufacturing technology.
In collaboration with Bristol City Council and Bristol Housing Festival (BHF) the project is designed to be the first 100% affordable and lowcarbon housing development aimed at creating a mixed tenure affordable housing scheme over the Chalks Road car park, adjacent to St. George Park, Bristol. It is a pioneering environmental and socially-focused development which will deliver much needed social housing for young people in need of affordable housing.
The project site is currently used as a car park which serves St George’s Park and the nearby retail area. The proposed development seeks to retain the site’s existing use as a car park in conjunction with a residential use comprising 11 duplex apartments. The homes have been optimised for energy efficiency and lowest possible energy costs, with PV panels to generate electricity in the day, quiet running heat pumps for low energy heating, controlled ventilation which recovers usable heat from inside the building whilst bringing in fresh air, triple glazing, LED lighting and energyefficient appliances. The apartments have been made from cross laminated timber (CLT) panels. The building fabric is further optimised
1
using offsite fabrication with superinsulated walls and roofs to achieve high level of airtightness (1.3 ach at 50 pascals), heat recovery ventilation, high standards of draught proofing, and low heat loss – circa 90% improvement over building regulations. The scheme aims to improve the fabric efficiency of the building beyond the 97% fabric energy improvements in the Standard Assessment Procedure (SAP). This development is capable of offsetting all regulated energy demands and the A-rated Preliminary Energy Assessment (PEA) shows that negative carbon emissions are possible across the site. Airtightness membrane in between CLT panels and insulation ensures that the airtightness layer will be untouched for the life of the building.
The client agreed on timeframe and budget with a ‘not to exceed’ price point. Because units are prefabricated in a factory, construction time is shorter without affecting the building safety and durability of the apartments. By monitoring and using regular supply chain products, the cost of production was optimised whilst minimising construction risks.
This project was deemed as a Bristol MMC pilot project with the opportunity of scaling up and replicating the scheme to other sites. ZED Pods was chosen by the council based on superior energy performance measures and help them achieve ultra-low carbon and ultra-low energy consumption – a complete sustainable development. Over the lifetime of the project the scheme is expected to have no net carbon footprint and
2
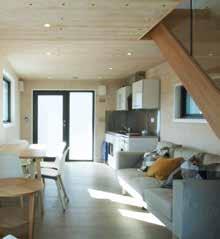
could offset both the carbon footprint of the original construction, plus the annual maintenance and annual energy needed to run the homes.
There is minimised concrete and aggregate use by using screw pile foundations. Wet trades are minimised to save energy and water. Gas is eliminated from the scheme and buildings are all electric. The scheme is air quality neutral with reduced impacts on local air pollution, noise and dust levels. The scheme creates living spaces above large carpark in urban centre, with easy access to local amenities and public transport networks. It is a direct and innovative response to the challenge of a sustainable transport future
Using timber as a structural component also gives flexibility to adapt for individual designs and offers end users an open plan to use with solid floors, walls and ceilings to amend internal layouts as required - e.g. hoists can be installed in ceilings for disabled users. This innovative development will rethink existing land use in central locations, demonstrating new thinking to help solve housing crisis whilst providing beautiful, low carbon housing and is the UK’s first CLT residential development to be built above a carpark.
For more information visit: www.zedpods.com
Images:
01-02. The timber homes will be a trailblazer for affordable low carbon living. Courtesy ZED Pods
ELIMINATING
INEFFICIENCY
Ron Lang, Impact Director for Value at the Construction Innovation Hub, illustrates why value-based decision-making will accelerate the shift towards adopting an offsite methodology.
Whether you work in offsite or the more traditional side of the industry, 2020 has been momentous for all of us in construction. The lockdown, which at times felt endless, saw a whopping 60% of building activity grind to a screeching halt, leaving our sector staring at the greatest period of uncertainty in its very long history. Even as I write this, we are once again faced with another period of uncertainty which is bound to leave many of us feeling just as concerned as we did back in March.
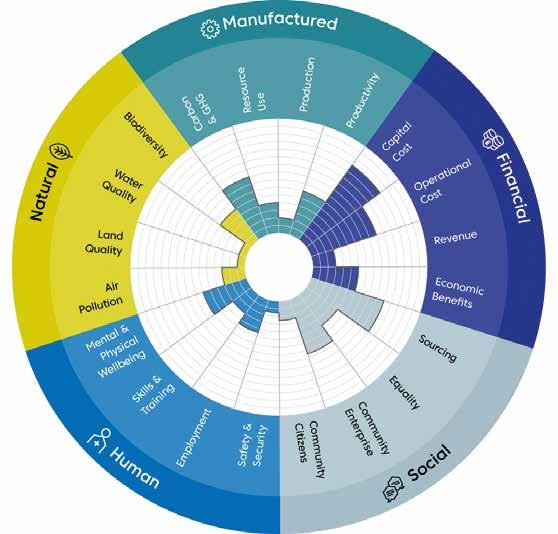
Despite the bleakness that has characterised much of 2020, something else has been happening this year which has given me a genuine sense of optimism. My role as the Hub’s Value Impact Director gives me a unique and privileged insight into what construction professionals in all corners of the sector are thinking and feeling. COVID-19 is naturally preying on everyone’s minds – not least with the recent rise in infection rates – but what is also unmistakably clear from the conversations I’ve been having, is a
1
growing consensus that construction’s future needs to look very different.
Building Momentum for Change
While the momentum for change in construction has been growing steadily for some time, what has become more noticeable in recent months, is the growing sense of urgency. Those long lockdown months have undoubtedly provided us all with a rare opportunity to pause and reflect on what kind of future we want for our sector. In truth, we’ve all recognised for some time that
the wasteful, unproductive, inefficient practices which have long been the modus operandi of our sector need to give way to new and better ways of doing things.
With a comprehensive Roadmap to Recovery now in place and supportive measures provided by Government, we have a unique opportunity to come together as never before and ensure that the slow march towards a transformed sector becomes a full-on charge. The stimulus for this will be getting to grips with value. Value is one of those deceptively simple concepts which is in fact frustratingly nebulous and difficult to define. All too often, value is seen through the narrow prism of pounds and pence. But if we are serious about accelerating that charge towards new and better ways of doing things, then we really need to get to grips with value in broader terms. We must agree on a consistent approach to defining, articulating and measuring value in the context of what we deliver and how we deliver it. Only then, can we consistently drive positive social, environmental and economic outcomes.
Laying the Groundwork
This may seem at first like a tall order, not least in the present climate we face, but the good news is that the groundwork is already proceeding apace. In recent months, I’ve had the privilege to work together with some of the best and brightest minds across construction, leveraging the networks of the likes of CLC, ACE, Constructing Excellence, CECA, UKGBC, Social Value UK, CIOB, RIBA and RICS (to name just a few) to develop the ‘Value Toolkit’. The Toolkit will help clients and project teams embed valuebased decision making throughout
2
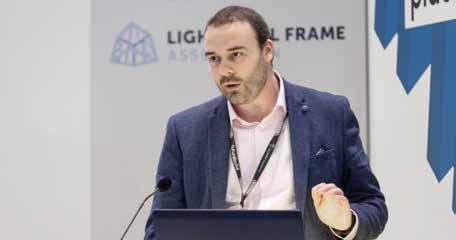
the investment lifecycle from business case through to procurement and delivery and operation improving overall sector performance in line with key policy objectives such as driving modern methods of construction (MMC), delivering social impact and accelerating the path towards net zero.
Grasping the Opportunity: the critical role of offsite
Value-based decision-making is particularly crucial for the offsite sector. By embedding this new model at scale, it will be far easier to demonstrate clearly and systematically that offsite construction and the emerging platform approach can deliver the social and environmental outcomes we are striving for as a sector and as a nation.
To give an example, by setting clearly understood, value-based expectations right at the outset of a build project, the offsite market would have a far greater opportunity to demonstrate close alignment with those key drivers. If value-based decision-making were to become the new modus operandi, then it would become increasingly difficult to justify why MMC such as offsite, were not being embedded right from the outset, rather than part-way through a project as happens all too often at the moment. For the offsite sector therefore, being at the forefront of the movement for valuebased decision-making is very much a ‘win-win’.
It’s difficult to predict in any meaningful way what the next few months has in store for construction and indeed the country. What we can say however, with a reasonably degree of certainty, is that the demand for housing, schools, hospitals and other vital buildings will only continue to grow. Against this backdrop, we are at a unique crossroads as a sector. We could take the safe route and go back to the way things were, but we all know that’s simply not sustainable. I’m confident – now more than ever – that we will choose the latter and embrace this once in a lifetime opportunity to embed real change. Be in no doubt however, we will not get there without the offsite sector at the forefront of the movement for change.
For more information visit:
www.constructioninnovationhub.org.uk
Images:
01. Value is measured in more than ‘pounds and pence’ 02 Ron Lang, Impact Director for Value,
Construction Innovation Hub
THE COMPLETE TOOLKIT WILL HELP CLIENTS TO:
Establish a balanced value profile for each project or programme, shaped by both strategic policy ambitions (e.g. net zero, MMC) and specific client, local and user needs, with a baseline Investment Value Index, based on established metrics and benchmarks, against which decisions and options can be assessed in the development and procurement phases
Select the best Delivery Model and Commercial Strategy to maximise realisation of value, based on value needs and considering the market context, risk and capability specific to the project
Use a new Procure for Value tool allowing procurement choices to be made on delivery of best whole-life value, not simply cheapest capital cost
Monitor and benchmark value throughout delivery and operational phases to ensure benefits are being delivered, to optimise value throughout operation and to inform future decision-making on similar projects and programmes.
USING CONCRETE
FOR LIFE
Jenny Burridge, Head of Structural Engineering, The Concrete Centre talks us through the use of long-lasting precast concrete as a perfect offsite construction for tall buildings design.
The use of precast concrete elements is a well-established construction method and provides solutions with a great variety of use, location, shape and finish. Taking the concreting work into the factory provides benefits of tight tolerances, excellent finishes not reliant on weather and provides a safer location for most of the work.
The core of a tall building is arguably the most fundamental and important element under consideration during the design process. For most tall structures, the core forms the main backbone of the building and plays a significant role in carrying a large proportion of vertical loading and, frequently, the majority of lateral loading.
Many offsite tall buildings use a slip form core as the stability system as the slip forming can be done before any other superstructure work proceeds and is sometimes started as a top down system where the core is supported by temporary piles while the basement is excavated below. Cores can also be formed from volumetric precast concrete core elements bolted together to form a full core. These are normally half a storey height tall and sized to be able
1

to be transported. These were used on the Kingston University Townhouse project, which is a predominately precast building.
Precast cores can be formed from crosswall elements or from twin wall elements. Crosswall elements are flat panels of precast concrete connected using ties at the corners and joints. Twin wall elements are formed from two skins of precast concrete fixed apart with a latticework of reinforcement. The space between the skins of precast concrete is filled with in situ concrete making a hybrid concrete solution. Ties between the panels of twin wall and connections to the horizontal elements are made using reinforcement through the in-situ section.
Precast concrete has inherent fireresistance characteristics, with the concrete cover providing insulation to the reinforcement. Fire-resistance periods of two hours can be easily achieved, which is the typical requirement for tall buildings. As a non-combustible structural material, concrete does not burn and can be used to meet and exceed stringent requirements for the fire safety of people and property. Another aspect of design that is becoming ever more urgent is sustainability, in particular the embodied carbon in buildings. Tall buildings are inherently higher in embodied carbon per square metre of usable space than low rise buildings whether these are built on-site or offsite. However, this can be offset to a certain extent by the reduction in travel distances for high-density urban spaces. The design of the concrete mix can reduce the embodied carbon of the structure but needs to be considered together with the other aspects of the design. To enable the fast demoulding of precast concrete elements from their formwork, cement replacement rates in precast concrete are typically lower than that of in-situ concrete. However, designers should discuss with their precast manufacturer lower carbon concrete options, accepting that this may slow the production process. Factory casting of elements means they can be lean and material efficient, which will reduce the overall embodied carbon of a precast concrete frame.
Early design and contractor involvement is key to producing safe, durable, resilient tall buildings designed for manufacture and assembly, taking the work into the factory and off the construction site. Only by working together can the optimum solution be reached. Tall buildings are a vital part of our city landscape and should be designed to last many years so that the full benefit can be realised for us and future generations.
The Concrete Centre has hosted a webinar, where members of the Town House, Kingston project team discuss the construction methods used. Watch at: www.concretecentre.com
Images:
01. Kingston University Townhouse.
Courtesy PCE Ltd