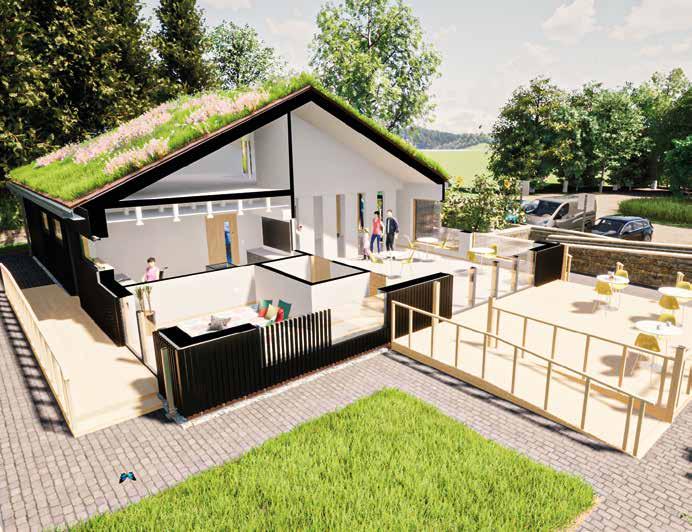
44 minute read
Industry News
Offsite Ready Challenge Delivers New Visitor Hub
Students from Edinburgh Napier University and the City of Glasgow College have linked up to design a new visitor hub for Beecraigs Country Park, Linlithgow. Two teams from the Scottish institutions were tasked with creating an ecologically sustainable, environmentally friendly and inclusive focal point to the vibrant country park.
The aim was to layout a proposed building that could be constructed and deconstructed away from the intended site and was part of the ‘Are you Offsite Ready? Online design challenge’ sponsored by Stora Enso.
‘Team 2’ won the first prize, designing a hub which would cater for cyclists, with open and accessible areas. ‘Team 1’ delivered their presentation on a centre which would withstand the elements, including a mezzanine complemented by the carefully considered path of the sun.
The challenge was originally conceptualised by Edinburgh Napier lecturer Dr Mila Duncheva and research assistant for the Centre for Offsite Construction and Innovative Structures, Louise
Rogers, with Catriona Jordan, from City of Glasgow College, as a way of giving students an opportunity to gain some industry experience out with the university curriculum and in lieu of the international internships usually available to students from Edinburgh Napier’s School of Engineering & the Built Environment.
Rory Doak, Business Development Manager at Stora Enso UK & Ireland said: “Stora Enso were thrilled to support a student-led design project, showcasing the abilities of students to adapt to new working conditions and produce manufacturable, sustainable and inclusive designs. I hope that we will see more competitions emerge, like this, that equip students with strong fundamental knowledge of BIM, inclusivity, and sustainable construction with timber. I am sure these principles will be key industry drivers in the future, and these students will continue to champion these design principles as they build their careers.”
Dr Mila Duncheva added: “This challenge was designed to develop students’ transferable skills including teamworking, problem solving, working to tight deadlines and collaborative digital workflows using building information modelling (BIM). I was astounded by both teams’ intricate technical solutions and striking visual presentations and am delighted we provided a positive experience for them during the worst of the pandemic.”
The project spanned 12 weeks and presented challenges for the students as they learned to work together remotely, whilst figuring out how to get the best from their designs and cater for the park’s one million yearly visitors. The Offsite Ready challenge teams collaborated with West Lothian Council to provide accurate geographical plans of the proposed sites and engineering consultant firm SWECO, who did an analysis of the project’s factors.
This challenge was part of the wider Offsite Ready project funded by the Construction Industry Training Board (CITB) and led by the Construction Scotland Innovation Centre (CSIC) in collaboration with Edinburgh Napier University, City of Glasgow College, Construction Wales Innovation Centre, Ministry of Building Innovation and Education and Class of Your Own.
New FR OSB Product Launched
Fast-growing modular construction business Integra Buildings has announced plans for a major expansion of its Yorkshire base. Integra is in the final stages of acquiring six acres of land next to its site in Paull, East Yorkshire, and has submitted plans to East Riding of Yorkshire Council to incorporate this area into its operations. The development of the land will increase the Integra site footprint to over 14 acres and create room to meet the award-winning company’s current and future needs. The expansion will create 20 new jobs and is key to the Integra management team’s ambitions to double revenues to £60million within three years. The land has been earmarked for a new production facility as well as storage, loading and dispatch areas. Pending planning permission, Integra intends to begin work integrating the land into its site in six months. Managing Director Gary Parker said: “We need more room to deliver our current projects, service our very healthy order book and continue our growth. We’re already bursting at the seams much of the time. It’s also absolutely essential to maintain operations on a single site, for operational efficiency and to maintain our competitiveness. The expansion of our current site, MEDITE SMARTPLY has launched SMARTPLY MAX FR B into the market. SMARTPLY MAX FR B brings an increased reaction to fire rating, up from Euroclass C offered by the current SMARTPLY MAX FR product and is the first Euroclass B board manufactured in the UK and Ireland to feature wood flakes treated with flame retardant solution before pressing. SMARTPLY MAX FR B replaces SMARTPLY MAX FR, building on the success of its reputation as one of the go-to boards for applications where strength, moisture resistance and flame retardance are paramount.

“We are extremely excited to introduce SMARTPLY MAX FR B to the marketplace, expanding our extensive SMARTPLY OSB range,” says Richard Allen, Sales Director at MEDITE SMARTPLY. “In SMARTPLY MAX FR B, customers can expect all the fantastic benefits of a SMARTPLY OSB board, with the addition of ZeroIgnition® solution, a water-based and environmentally friendly flame retardant which is added during panel production, before the wood flakes are pressed.
“This ensures that SMARTPLY MAX FR B’s flame retardance is integral and maintains its structural integrity, unlike many post-treated alternatives. Customers can rest assured that this boards flame retardance will hold to Euroclass B standard, even when cut to size, which makes it different to other FR boards out there. where we have already invested millions in facilities, is the perfect solution. This is great news for our employees and our supply chain, the vast majority of which is within East Yorkshire, as well as creating 20 new skilled and semi-skilled production jobs for local people. This is a landmark moment in the development of the company and we’re very excited by the opportunity to move to the next level.” The expansion will mark the latest chapter in Integra’s remarkable growth, which has accelerated following the consolidation of operations at the Paull site. Integra has invested more than £3million transforming its “At MEDITE SMARTPLY, we want to support a safer, wider future for timber buildings, that will enable the wider construction industry to work more sustainably and more efficiently, truly building for the future. This has been one of our main motivations in developing SMARTPLY MAX FR B.”
Manufactured using advanced resin technology that results in a high performance, no added formaldehyde panel, SMARTPLY MAX FR B can help specifying architects, contractors and fabricators contribute to the creation of safer, healthier environments. This includes not only the built environments actively created but the natural environments left behind:
SMARTPLY MAX FR B is sustainably produced using timber from sustainably managed Irish forests. SMARTPLY MAX FR B meets with the requirements of European Standards EN 300 and EN 13986, while also complying with the European reaction to fire class B-s2,d0 and Bfl-s1. The panel also complies with the FR/FR Build performance requirements in accordance with Structural Timber Association’s Design Guide to Separating Distances During Construction for timber frame buildings above 600m² total floor area. Boards can be manufactured in largescale formats of up to 2.8m wide by 7.5m long, making it ideal for offsite manufacturing, alongside traditional building.
Integra Buildings Announce Major Expansion Plans
Source: https://bit.ly/3cC9RXF
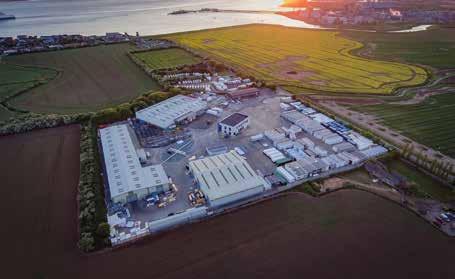
operations at Paull, including a state-of-the-art office building, which was self-built on-site using cuttingedge modular construction techniques and serves as a showcase for the quality of facilities the business creates for clients.
Integra’s turnover has grown significantly in recent years with revenues rising from £18.6million in 2016, before the investments at the Paull site, to a projected £30million-plus in the current year.
Source: www.integrabuildings.co.uk
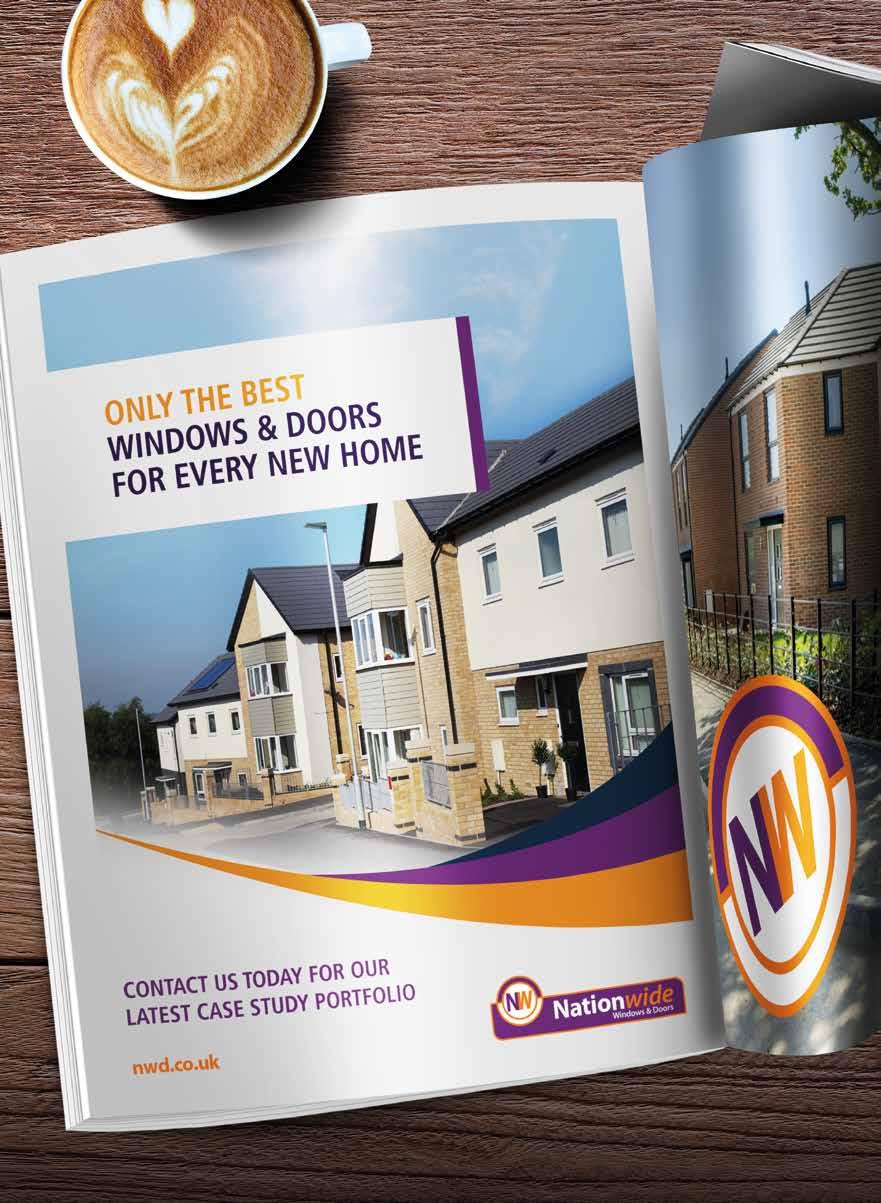
CSIC Wants You to Change the World
Construction Scotland Innovation Centre (CSIC) has called on students with a passion for innovation and disruption to help lead the charge for change in the construction sector.
CSIC is looking to galvanise forward-thinking attitudes by launching its Built Environment Innovation MSc Fund 2020-21, calling on prospective students who want to play a part in tackling climate change, to take the lead on significant technical advancements in the construction world and to be involved in finding that one simple creative idea that can completely transform the way the sector operates.
From the rise of 3D printing, allowing companies to print out entire buildings, to virtual reality software being used in the planning stages of construction, the opportunities for creative and disruptive thinking students are endless and successful innovation enables businesses to punch above their weight.
The grant will encourage new talent into Scotland’s construction landscape and to apply, CSIC is asking that students have an interest in bringing a creative thinking solution to the built environment sector and that they can support and work on a research project during their programme of study that can be applied directly to the industry.
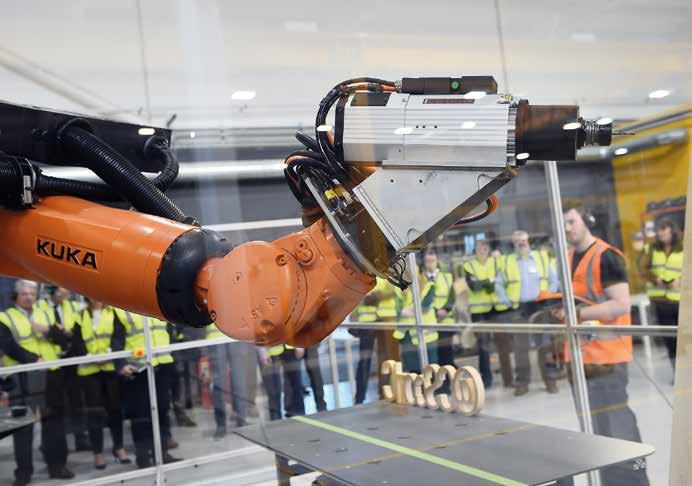
“Some of the most important solutions and innovative ideas come from those on the ground,” said Stephen Good, Chief Executive at CSIC. “Creating this opportunity for the future innovators of the construction world to develop their ideas is key to changing the sector. This is an exciting opportunity for students to be part of real transformational change together with industry, helping to set a new direction post lockdown as we build back better to create a built environment that works effectively for people, business and our economy.
“Construction and the built environment are changing, and the skills needed are wide ranging, including digital, climate change logistics, engineering, design and robotics. The demand for skilled professionals in the industry sector remains high and the opportunities are countless. The MSc funding offers people a real opportunity to create a career that positively impacts everyone through the physical spaces we inhabit.”
Dale Johnstone, who benefited from CSIC’s MSc grant in 2016/17, said: “I would encourage anyone interested in developing their skills and prospects of a career in the built environment sector to apply for the MSc Grant on offer from CSIC. The access to industry experts within the sector was incredible. I was partnered with the Scottish Borders Council as part of their Engineering and Design department and after the programme secured a full-time role at the Council. This new role allowed me to be a part of several civil engineering projects across the Borders, from the design stage right up to construction. I take great pride in being able to provide projects which have significant benefits to the local community and which continue to improve and shape the world we live in.”
There are up to 20 places, each with £6,530 funding available, to help support candidates who are looking to carve a career and look to change the future of the built environment sector. Students can apply with an industry partner already in mind or CSIC can help find a partner from the wide network of contacts the Innovation Centre already has. During the programme, students will work closely with their chosen industry partner and have access to a number of skilled mentors, workshops and the chance to connect with experts across the sector.
Source: www.cs-ic.org
£16m Whitehaven Academy Win for Wates
Wates Construction has been awarded a £16million contract to build the new state-of-the-art Whitehaven Academy School, its second educational facility in the area after completing Campus Whitehaven last year.
The development will replace the existing Whitehaven Academy School, which will be demolished to make way for a new three-storey education facility and sports hall, together with associated parking and landscaping. The main school building will contain a mixture of general teaching spaces for 900 pupils aged 11-16, with a focus on specialist teaching spaces for subjects as science, PE, design and technology. It has also been designed with flexibility and future expansion in mind, with plans to accommodate a 150-pupil sixth form centre in the next five years.
Wates is carefully phasing the works and strictly adhering to social distancing guidelines to help minimise any disruption and protect workers and pupils at the school. Government mandated BIM 4D modelling will also be used to foster greater collaborative planning, design co-ordination, and clash detection. Work started on site in late June, with handover of the new school set to take place in early 2022. It will be delivered in partnership with supply chain partners SES Engineering Services, Cubby Construction and Elland Structures. Dave Saville, Business Unit Director for Wates Construction in the North West, said: “We’re looking forward to delivering another outstanding educational facility to the people of Whitehaven, after completing Campus Whitehaven last year. After years of collaboration, we fully share the Department of Education and Cumbria Education Trust’s vision for what schools could and should be like – world-class educational spaces and facilities that inspire both pupils and teachers, promoting the learning process at every stage and future-proofed for the next generation.
“As with any live school construction site, there will always be challenges when it comes to building close by to current school buildings. However, by making use of our offsite facilities and with decades of experience in the education sector, we have the skillset and capability to minimise disruption to the school – which was crucial to us gaining a place on the framework.”
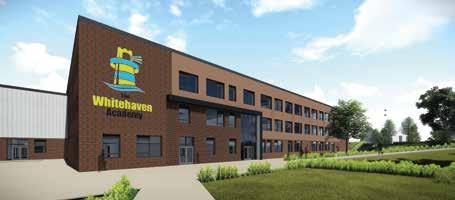
Nick Polmear, Operations Director at Cumbria Education Trust, added: “It’s time to replace the Whitehaven school buildings, with a new, modern design that is fitfor-purpose, provides the best learning environment for students, and can be adapted to accommodate further expansion in time.”
The Whitehaven Academy School has been procured by the Department for Education via its Construction Framework, further bolstering Wates’ already expansive education portfolio in the North West, with the firm also delivering Maghull High School and the Star Academies Eden schools in Blackburn and Manchester. The project is the latest for Wates Construction in the North West, with the team currently delivering St. Helens Fire Station, Sands Leisure Centre in Carlisle, and a new leisure hub in Widnes.
Source: www.wates.co.uk
Inspiring solutions for creative minds
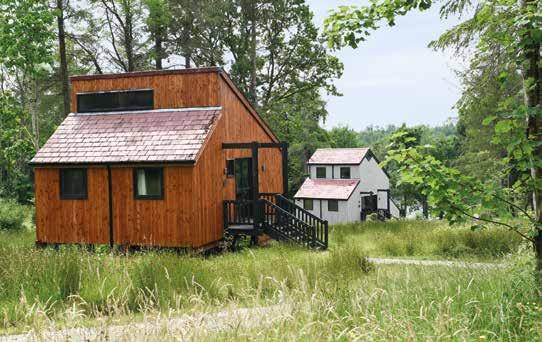
Whatever your project, we have the architectural aluminium solutions to meet your design vision. For over 40 years we’ve worked alongside some of the UK’s leading architects and contractors, providing support throughout the design and construction process. These stunning log cabins situated in the Each cabin was manufactured off-site in Killykeen Forest Park in County Cavan, Ireland several sections, before being shipped to the feature the slim lines of our elegant Alitherm park where the pre-built units were joined Heritage window and French door systems. together on-site.
Arnolds Way, Yatton, Bristol North Somerset, BS49 4QN United Kingdom
E sales@smartsystems.co.uk T +44 (0)1934 876 100 F +44 (0)1934 835 169 W smartsystems.co.uk
Darwin Group Reaches Completion of STEM Modular Build LSFA Announces the Appointment of Inaugural Chair
Modular construction specialists, Darwin Group has delivered a new multi-use block for Gretton School in Cambridge. The brand-new STEM block will provide the school with two science labs, a design and technology workshop, art studio and associated services. Part of the Cavendish Education Group, Gretton is an independent specialist school in Girton for students aged 5 to 19 years old – offering a safe and secure learning environment for all.
By utilising Darwin’s modern approach to design and turnkey solutions, the block was completed in three and a half months and arrived on-site with fully-fitted science labs, gas facilities, prep-room and desk space providing a functional space for experiential and theory lessons. After receiving expensive designs from other companies, the school began to consider that it’s grand vision may have to be compromised. Darwin Group, in conjunction with LXA Projects Ltd, were able to streamline the process and provide a more cost-effective solution for the school thanks to its skilled in-house team of education construction experts.
Specially designed using modular methods, the block has been built with the future in mind with high-quality materials. As it was constructed offsite at Darwin Group’s Shrewsbury-based facility, disturbance to the rest of the school was kept to a minimum.
Charles Pierce, Managing Director at Darwin Group, said: “As a proud British company we are thrilled to be able to offer an innovative solution that has bought this project to fruition. Our modern techniques and unique
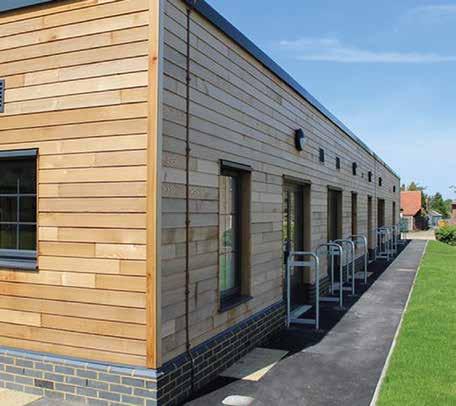
turnkey service allows us to redefine what is realistically achievable within tight timescales and limited budgets making us the perfect fit for projects of this nature.”
Ian Thorsteinsson, Principle at Gretton School, added: “Our smart new block is a fantastic addition to our school. Darwin Group were true professionals and considered the needs of our staff and students at every stage of the project, from start to finish. It was a great relief that the majority of the construction work could be completed offsite without disturbing the school and we were amazed at how fast it was assembled.
“Many of our students get lots of enjoyment from the creativity that science, technology and art provide so I think this space is going to become their favourite place to work. We aim to make our students school life structured, fun and enjoyable and the new teaching environment will allow us to enhance their learning whilst providing the secure space that they need to grow. We can’t wait to show our students when we welcome them back in September.”
Richard Parton, Director of LXA Projects Ltd (Project Managers, Quantity Surveyors and Interior Designers), added: “It was a pleasure to deliver this new academic facility in conjunction with Darwin Group. The team were flexible and responsive throughout the project and the end product is a fantastic new addition to Gretton School.’’
Source: www.darwingroupltd.co.uk
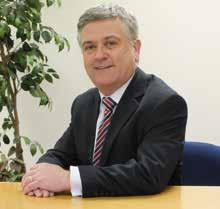
Mike Fairey has been unanimously voted in as the Association’s new Chair. Mike is Joint Director and Owner of Salvesen Insulated Frames Ltd and back in 2010 with his partner Tom Salvesen, bought the assets of Fusion Building Systems with the objective of firmly establishing the business as a UK leader in the offsite manufacturing of light steel frame super-structures.
Since its introduction at the Focus on Framing conference in June 2019, the Light Steel Frame Association (LSFA) has grown in stature and numbers – now including some of the most prominent names operating in the sector. As the construction industry looks to raise the bar to meet building regulations banning the use of combustible materials on and within external walls of specific residential sectors above 18m – the light steel frame industry has witnessed unprecedented demand for non-combustible panelised and volumetric modular systems.
Mike’s engineering career began in the early 1980s when he completed a five-year engineering apprenticeship in prototype automotive design and testing. Later in his career as an informed and respected member of the light steel frame industry, Mike was appointed to the Board of The Housing Forum in 2016 to provide insight and become the voice of offsite construction. He now uses his extensive expertise to champion offsite construction methods, helping to educate and transform approaches for housebuilding in the UK.
Mike Fairey said of his appointment: “It is a real opportunity to chair such a forward-thinking group of construction professionals. My primary objective is to agree formal collaborations with other key industry associations and bodies such as The Housing Forum. We are galvanising the sector as we’re on the cusp of a major opportunity which has been driven by building regulations and the potential to further reduce the restriction of non-combustible materials in external walls to 11m. The sustainability and longevity benefits combined with the fire resistant properties mean that light steel framing systems are a vital offsite technology that can be used in so many building types and applications.”
Source: www.lsf-association.co.uk
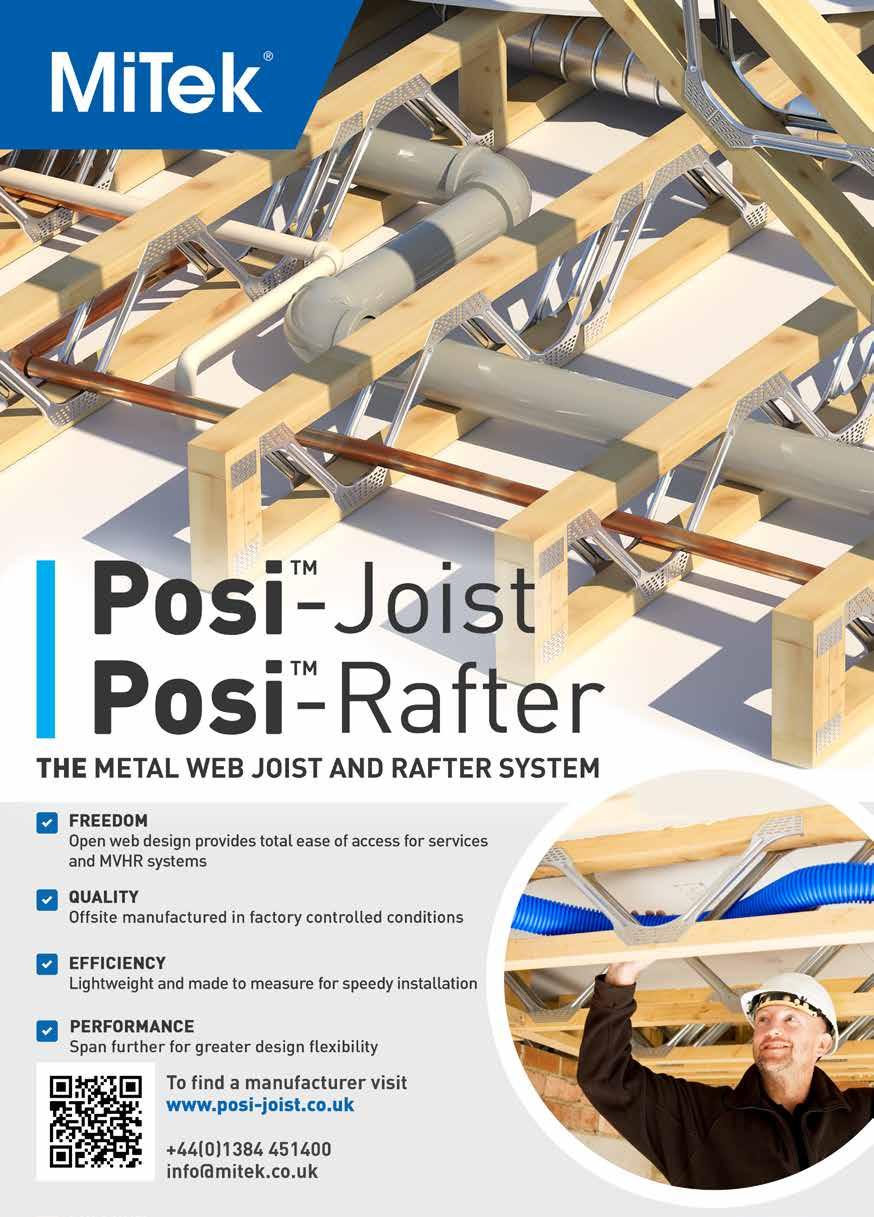
Seismic II Takes MMC Schools to the Next Level
A £6million project to transform the way schools and healthcare facilities are built has been granted £2.9million of funding to showcase the future of modern methods of construction (MMC) in the UK.
The consortium-led Seismic II project is working on the future of construction. Among a range of outcomes, the UK Research and Innovation (UKRI) funded project via the Industrial Strategy Challenge Fund, will create a set of standardised reconfigurable components, working closely with the Construction Innovation Hub to align platform interface standards. These components will reduce waste, cost and carbon dioxide emissions while increasing speed of delivery.
The consortium is conscious of the need to align and harmonise its work with the outputs of the Construction Innovation Hub and will be working with them throughout to ensure maximum impact. Government procurement is already set to shift from traditional construction methods to MMC. Seismic II will show how this shift can happen while meeting the government’s own ‘Construction 2025’ vision of lower costs and emissions, faster delivery and an increase in exports from the industry.
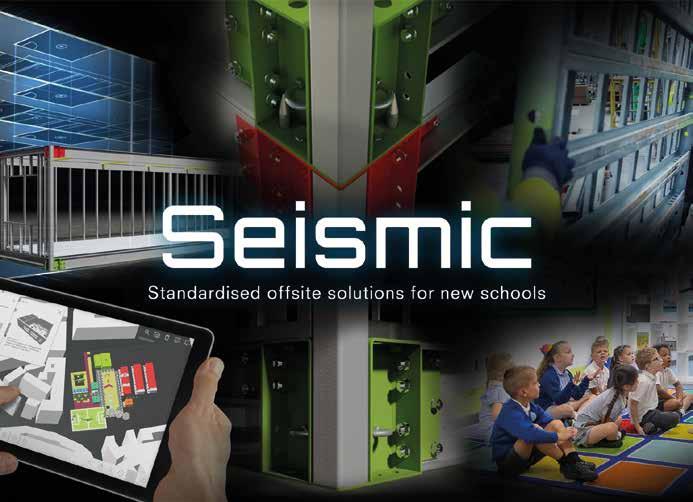
Seismic II builds on the success of the Seismic I project, which showed how a standardised light steel frame could change the way new schools were designed and constructed. With the new award from the Industrial Strategy Challenge Fund, the system will encompass the production of wall, floor, ceiling and roof components that are all completely interoperable with the standardised light steel frame.
“The Seismic system is already proving the benefits of offsite construction in the schools sector and our componentised offsite schools solution has saved the country tens of millions,” said Richard Crosby, Director, blacc Ltd. “Unsurprisingly, we are gaining interest from many other sectors too, including housing and healthcare. With this additional investment we’re through to a whole new level of productivity, efficiency and materials innovation.”
Along with improving the offsite production processes for projects using MMC, Seismic II will also look at the whole life performance of the buildings produced that way. The government’s industrial strategy aims to reduce the construction costs and whole life costs of buildings by a third, while seeing those same buildings delivered in half the time and with a 50% reduction in carbon emissions from the sector. Graeme Jeremy, Head of Construction & Infrastructure, NCC said: “Using advanced materials in construction is still relatively novel, and through the Seismic II project, we’ll be investigating areas where composites can add the most value to modular buildings, taking advantage of the increasing uptake in manufacturing.”
Originally intended for school construction, Seismic II has drawn interest from the healthcare, commercial and residential sectors. The completed demonstrator building will be a template for high performance buildings of all types, delivered using high quality, reliable, standardised components.
Phil Clements, UK Technical Director at Tata Steel added: “This project will allow thousands of children to have access to education in buildings which have been designed using the latest technology, constructed offsite to lower emissions and can be repurposed and recycled.”
Source: www.blacc.co
Manufacturers Urged to Digitise Product Data to Reduce Risk
A new initiative aims to get manufacturers in the construction industry to take ownership of their product information. The project is producing a Plain Language Guide for manufacturers setting out why digital product data is important and how manufacturers can benefit by taking simple low-cost steps. The project is supported by the Institution of Engineering and Technology, Construction Products Europe and the UK BIM Alliance.
“Structured product data has many benefits”, says Paul Surin of IBM, a member of the project editorial team. “By structuring data and taking advantage of the new standards, manufacturers can start treating their information as an asset, monetise their data, save considerably on marketing costs and reduce risk.”
The risks to manufacturers of analogue methods of handling data are considerable, Patricia Massey of Electrium explains: “The Grenfell tragedy has showed our industry that knowing where your products are is essential to public safety, but it also protects manufacturers. The new Building Safety Bill requires building owners to certify their buildings are safe, and that requires knowing what is in them. We are also seeing increasing instances of construction companies being prosecuted for product related failure. “Manufacturers will need to conform to the market need for standardised, traceable product information soon, if only to protect their business interests. New international standards published this year make it possible for information to be provided in a standardised, interoperable way, and the project team believe that a simple process will allow manufacturers to make their products traceable and protect against fraud and incompatible product substitution.”
Christophe Sykes of Construction Products Europe (CPE) said: “One of the characteristics of the European industry is that we have the Construction Products Regulation (CPR). It lays down harmonised rules for the Single Market of construction products in the EU. The Regulation offers a common technical language, allowing the assessment of the performance of

construction products, and ensuring the delivery of reliable technical data to the market. More recently, our Smart CE marking initiative allows this regulated data to be delivered in a harmonised digital format. We welcome this initiative to help manufacturers understand how digitisation can help compliance.”
Blane Judd, Chair of IET Built Environment Panel, added: “One of the goals of the IET’s Built Environment Panel is to support the digitalisation of the built environment sector. This still has a long way to go and a better understanding and management of product data will make a significant contribution to this journey. Delivering built as designed buildings which will perform better and are safer can be a reality.”
Source: https://bit.ly/2E9g7cG

Rollalong and Magna Housing Agree New Modular Contract
Two Dorset businesses have strengthened their relationship by agreeing a contract to manufacture 50 more sustainable modular homes for communities in the South West. Rollalong the largest permanent offsite manufacturer in the south of England, will manufacture the homes offsite at its factory in Wimborne for Dorchester-based Magna Housing before installing them on several sites across Dorset and Somerset.
The new contract marks the start of a decade in which Magna will invest £400million into new and existing homes across Dorset and Somerset. Fortyfive homes have already been manufactured and earmarked for sites across Dorset. The Magna homes range by Rollalong are built offsite in a factorycontrolled setting.
Rollalong has over 50 years of experience in the rapid and risk-free delivery of quality, bespoke and modular buildings for all market sectors. “This is tremendously exciting and we’re delighted to continue working with Magna Housing,” said Steve Chivers, Managing Director of Rollalong. “Our ongoing collaboration will ensure that high-quality, precisionengineered homes continue to be manufactured in the local area by local people.”
Saxon Reach Gets Offsite Boost
L&Q is delivering 225 new homes at Saxon Reach in Milton Keynes using offsite manufactured timber frame. All properties at Saxon Reach – ranging from onebedroom apartments to five-bedroom homes – are being constructed with Stewart Milne Timber Systems (SMTS), promising a more energy efficient build and significantly lower running costs for new residents. Setting the benchmark for future homes, Saxon Reach’s timber frame properties form part of L&Q’s New-Build Homes: Quality Standard promise, a commitment to delivering premium fixtures, fittings and appliances as standard at no additional cost to the buyer. All apartments at Saxon Reach come with private outdoor space. Debi Lama, National Account Manager at Stewart Milne Timber Systems, said: “Our ambitious partnership with L&Q is not only reducing build costs for the Housing Association, meaning that the charitable organisation has more money to re-invest back into existing communities and other new homes, but is also delivering the highest standard of construction for buyers. We believe that L&Q are setting the standard for housebuilding in the UK and look forward to seeing happy new residents on site at Saxon Reach.” Magna Housing owns 9,000 properties and has a workforce of about 450 people aiming to build over 500 more homes over the next three years. They are in discussion with other clients in the region to open up the long-term supply of homes built offsite to complement existing capabilities in on-site delivery
Paul Read, Head of Development and Sales at Magna Housing, added: “This is great news for both our organisations, which have been working together very successfully for the past 18 months. Magna’s partnership with Rollalong and its continued Saxon Reach is part of the wider Glebe Farm development area, a growing new residential quarter for Milton Keynes, which will meet the demands of the budding town. Glebe Farm will deliver new retail and commercial facilities, a doctor’s surgery and sports and leisure facilities, as well as an extension of the Milton Keynes Redway system – a 200 mile network of shared use paths for cyclists and pedestrians. The site will also be home to a new school – welcoming children from primary age up to the end of secondary school. Christine Osborne, Sales and Customer Services Director (Counties) at L&Q, added: “We are proud to

commitment are securing jobs in the local area, generating social returns for the local economy and building a sustainable future in the South West.”
Rollalong has a factory capacity of 2,000 homes per annum and is well placed to support central Government and play its part in solving the current housing crisis. The new homes will be manufactured from the newly designed 2020/21 range and have been designed to fully comply with the Higher Fabric First approach in the Future Homes Standard.
Source: www.rollalong.co.uk
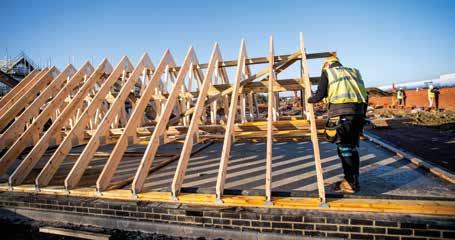
be partnering with SMTS to deliver innovative new homes for our buyers in Milton Keynes. As well as significantly reducing household bills, offsite timber solutions are vital in addressing housing shortfalls in the area – allowing us to deliver homes up to 30% quicker, particularly important in an area like Milton Keynes that has seen significant population and employment growth over recent years. We are pleased to be offering local residents the opportunity to purchase a high quality new homes in this thriving new district, paving the way for future newbuilds in the area.”
Source: http://bit.ly/SaxonReachTimberFrame
McAvoy Tops Out in Croydon
With construction nearing completion at the new Timebridge Community Centre in New Addington, a topping out ceremony was held by The McAvoy Group and their client Croydon Borough Council to mark the milestone recently.
A key part of Croydon Borough Council’s extensive regeneration programme for New Addington the new two-storey purpose built centre combines the Fieldway Family Centre, the Timebridge Community Centre and includes a food bank, the Learning Tree nursery and a youth centre. There are also several flexible spaces to hire, including a multi-purpose hall, two studio spaces, conference and meeting rooms and social space.
The event was held with safe distancing measures being followed by all attendees. Guests included Croydon’s Madam Mayor, Maddie Henson, local ward councillors and representatives of local community groups. Gavin Ward, Project Manager at The McAvoy Group, said: “By incorporating the most advanced offsite construction techniques, we have been able to turn this project around in under a year, despite COVIDrelated delays – it’s a high-quality, intuitively designed building and I’ve no doubt it will continue adding huge value to the local community for many years to come.”
Fusion Celebrates 20 years in Offsite
Fusion Building Systems is celebrating 20 years of offsite construction excellence, building more light steel frame superstructures over the past two decades than probably any other supplier. Fusion was founded in Ireland in 2000 when a construction entrepreneur wanted to find a way of delivering high quality housing at speed, with less reliance on labour and the weather. In 2010, the Company was acquired by Salvesen Insulated Frames Ltd, relocated to Northampton and since then, has retained its position at the forefront of the offsite construction sector. Over the past two decades Fusion has designed, engineered, manufactured and built light steel frame superstructures for more than 25 schools, 2,000 care home beds, 3,000 residential housing units, 4,000 apartments and 12,000 student beds. Its client portfolio has also grown exponentially, and its offsite excellence has been recognised by such prestigious award programmes as Construction News and the Offsite Construction Awards. Now as the construction industry begins to embrace a digital future and the more widespread adoption of MMC and design for manufacturing principles, Fusion continues to drive change. Its Directors are proud to sit Cllr Simon Hall, Cabinet Member for Finance and Resources, Councillor for New Addington North Ward addressed the attendees saying: “The new centre will provide much needed enhanced facilities enabling local groups to continue with their excellent work in serving the local community. This new community centre follows on from the completion of the all new leisure centre on central parade. The Council has also commenced with works on the Timebridge fields for an all new SEN school which will be completed in Sept 2021.” on the boards and steering committees for a number of influential Government and industry bodies. Fusion Director Mike Fairey, said: “I’m proud of our legacy in the offsite sector. We’ve built numerous structures across many sectors and continue to use the knowledge we’ve gained to improve our products and processes. We’ve seen a lot of change over the past 20 years, though it’s probably only since around 2015 that we’ve seen offsite methods of construction really begin to push towards centre stage for the construction industry as a whole.” Fusion’s work over the past 20 years has included urban regeneration projects, historical renovations, off-the-shelf school construction system and product focused ‘brand’ solutions for some of the UK’s largest contractors and developers. Most recently, Fusion has completed a 2,000 bed student accommodation
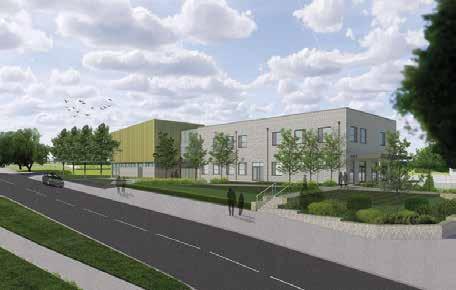
The McAvoy Group has also announced that it is to close its factory in Co Tyrone and centralise all operations in Lisburn. The 91,350sq ft headquarters near Coalisland is up for sale for £2.5million. McAvoy Managing Director Mark Lowry described the sale as: “The final part of a post-COVID restructuring strategy to ensure that the business is in the best possible shape for the future.”
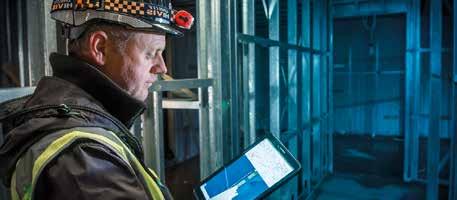
Source: www.mcavoygroup.com
project for Balfour Beatty at The University of Sussex believed to be one of the largest light steel frame projects undertaken.
“This is an extremely exciting time to be in the offsite sector, adds Mike. “We’re now talking about the role technology has to play as part of the ‘Golden Thread’ for MMC, and the prospect of shifting the construction industry’s mindset from a project-led approach to one which is centred on the product. These are changes I think we’ll be seeing accelerate over the next five years, paving the way for our next 20 years in the industry.”
Source: www.fusionbuild.com
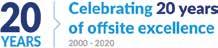
Housing First for Bristol
A UK first took place in a car park in Bristol recently as 11 innovative zero carbon ZED Pods apartments were craned into place. The development, designed by award-winning modular housing company ZED Pods will see the one and two bedroom apartments built on a podium above the car park in Chalks Road, St George.
This ground-breaking development is being delivered in partnership with Bristol City Council, Bristol Housing Festival, YMCA and Bristol and Bath Regional Capital. The factory-built modular units can be erected within days and are designed to be zero carbon, energy neutral and have the lowest possible running costs. Each unit is precision-made in a factory environment to high environmental standards and comes with full BOPAS (Build Off-site Property Assurance Scheme) accreditation.
Because the development takes advantage of the air rights above a council-owned car park, the land cost has been removed thus making the development extremely affordable. This is also the first 100% socially rented development of its kind in the country. This environmental and socially-focused development will deliver necessary council housing in St George for young people in need of affordable housing and those at risk of housing crisis, including NHS workers. ZED Pods Operations Director Dr Rehan Khodabuccus said: “We wanted to address key worker and affordable housing issues without compromising on our values of sustainability and quality. We are very pleased that Bristol City Council has had the foresight to partner with us direct and are so enthusiastic about the potential for more developments like this.”
Marvin Rees, Mayor of Bristol, added: “I am really pleased to see this development come to fruition. It’s an exciting and yet practical approach to addressing some of the housing challenges we have in the city and I hope we can see more of these sort of projects delivered in the near future. We have to be thinking creatively about how we best use the space we have in the city and not keep pushing people further and further out because they can’t afford city house prices.”
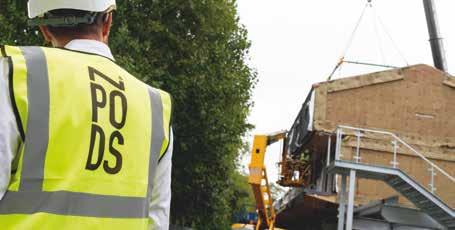
Jez Sweetland, Bristol Housing Festival Project Director, said: “This was one of the projects that came about as a result of our five year Bristol Housing Festival that started in 2018 which is all about trying out new ideas and re-imagining better ways to live in our cities. Our aim has always been to deliver tangible projects and so I am thrilled that the ZED Pods project is now actually a reality and that there are other projects in the pipeline.”
You can read more about this project on p48 of this issue.
Source: www.zedpods.com www.bristolhousingfestival.org.uk
STRIKINGLY VERSATILE

With the Gebrik cladding system, you are assured of a simpler, faster brick façade that performs precisely as it should. Tried, tested and simple to install, our solutions provide you with the freedom to create strikingly versatile buildings.
To find out more, visit our website www.aquariancladding.co.uk 0044 (0)808 223 9080 info@aquariancladding.co.uk @aquarian_cladd
Timber Boost for Maidenhead Office Park
Hutchison Kivotos Architects recently completed a two-storey cross laminated timber (CLT) and glulam office extension at No. 2 Maidenhead Office Park. The extension connects the two existing wings of a 38,000sq ft office building by creating a welcoming, contemporary ‘heart space’ opening out to a generous landscaped courtyard. The new building was designed, supplied and installed by mass timber and hybrid specialist G-frame Structures with the two-storey block formed of PEFC-certified HEXAPLI CLT with glulam columns and beams from French supplier Piveteaubois.
“It was important to create a building that would provide a differentiating factor for our client in the highly competitive commercial lettings market,” says James Johnson, Director at Hutchison Kivotos. “Prior to COVID-19 there was a strong market at Maidenhead Office Park and creating a unique, contemporary and flexible office space was vital to meet the growing demand – particularly from young, tech and start-up companies. We felt that a contemporary timber structure would achieve this.”
It sits on a simple, four-sided ‘doughnut’ shaped plan with accommodation housed in a three-sided horseshoe shaped section. The original layout of the building was awkward, requiring people wanting to cross from east to west wing to pass through the reception area: the new structure squares this off, linking the two original wings of the building and improving the connection to the courtyard. Internally, the CLT and glulam have been left exposed providing a complement to the original office space and resulting in a light-filled, calm atmosphere. The use of timber also helped to overcome the constraints of building within an internal courtyard, allowing prefabricated elements to be lifted into the middle of the ‘doughnut’ using a mobile crane placed at the front of the building.
“It’s really good to see the growing awareness in the commercial lettings sector of the benefits of building with wood,” said Lee Murphy, Managing Director at A new report has been published – jointly authored by Cast CEO, Mark Farmer and HTA Architects partner, Mike De’Ath. Both are long-term industry colleagues and passionate advocates of modernising homebuilding through use of offsite construction including modular techniques. The new report sets out a bold ambition to seize on the opportunities presented by COVID-19 recovery planning to accelerate the role modular homebuilding plays in the future as part of a much more strategic approach to nurturing and mainstreaming the manufactured housing market. The vision in the report sets out the potential to create a sector capable of delivering 75,000 newbuild homes every year within a decade through a series of interlinked, long-term interventions by Government and its agencies coordinating demand stimulation alongside responsible capacity building. At its heart is the call for more tenure diversity to allow deeper market absorption combined with a new modular homebuilding national integration platform capable of aggregating and co-ordinating the market at scale such that clients and manufacturers can combine and collaborate in one place in a move towards more unified design and technical standards, quicker and larger data and evidence collection and the building of confidence in underwriting markets.
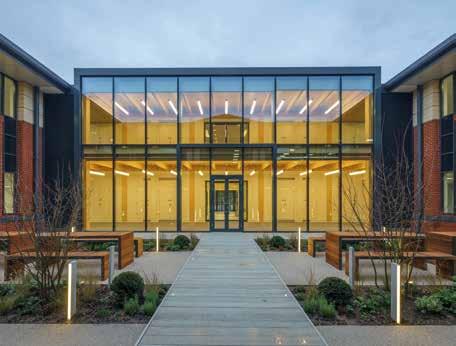
G-frame Structures. “For developers of commercial portfolios, it is a savvy investment to transform an average office building of standard décor into a desirable and healthy workspace by the addition of a mass timber extension. No. 2 is now an environment to which incoming tenants are likely to respond well and settle in for a long time in the certain knowledge that the building meets their social distancing needs and is adaptable and future-proofed.”
New Report Urges Modular Acceleration
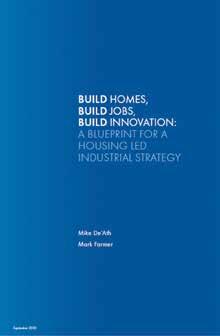
Source: www.g-frame.co.uk
The report says: “In writing this paper we have sought to place modular housing delivery at the heart of the Government’s post-pandemic industrial strategy and hopefully influence building blocks that might be laid in the Spending Review, due to be announced in the Autumn. Our asks, derived from our experience as practitioners as well as from research with consultees, are rooted in greater collaboration to re-shape the market to face the challenges ahead. We need a plan that joins up Government and its agencies with housing procurers and deliverers at an unprecedented scale. A strategy that also calls for targeted Government subsidy, investment, land release, planning reform and tenure diversification. This will promote the manufacture of great housing to meet both latent current and future demand whilst creating new jobs and building a green recovery.
“Much of the great work we have discovered in our research is fuelled by local or business level ambition with similar thinking replicated throughout the country. Some are more advanced than others, many have not yet commenced, however the need for homes has never been greater. We call on those with this ambition to embrace modular and wider MMC delivery, to share and support each other and collaborate to come together at an unprecedented scale."
You can download or read ‘Build Homes, Build Jobs, Build Innovation’ at: https://bit.ly/3iY0iVo
PM Visits Hereford MTX Fast-track Ward Project
After declaring the UK government’s intention to deliver ‘Project Speed’, including a £3billion capital investment into the NHS, healthcare construction company MTX, welcomed the Prime Minister to their latest £12million, 72-bed, fast-track ward project at Hereford County Hospital.
The Prime Minister visited the construction site in August keen to see for himself near completed ward project, that aims to deliver the NHS a total of 72 extra beds across three state-of-the-art wards – all in just 11 months. All part of the government initiative to ‘to build better, to build greener, to build faster’ the new ward extension is being delivered using MTX’s fast-track construction methods that reduce the build time by up to 50%. Talking on the PM’s twitter feed whilst on -site, Boris described the project as: “The beginnings of a new series of wards for Hereford County Hospital… The first of the 20 new hospital upgrades that this government has embarked on… The beginning of a record programme of investment in our NHS.”
David Hartley, Managing Director of MTX said: “The site team were excited to welcome the PM to our latest project and talk him through the clear benefits
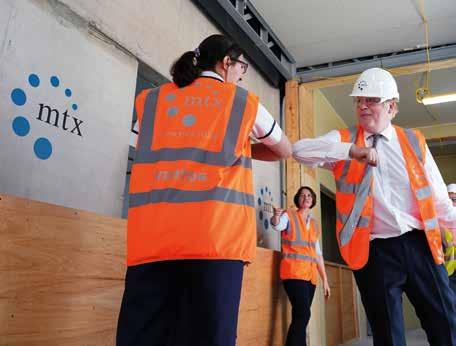
of these rapid construction methods. For this project, the building is largely built offsite in a factory, then transported and craned into position. This not only means we can deliver buildings much faster, but we can produce 60% less waste, ensure safer construction sites and all to the same standard and quality as a traditionally built hospital.” With the Government’s ‘Project Speed’ well underway and described as:
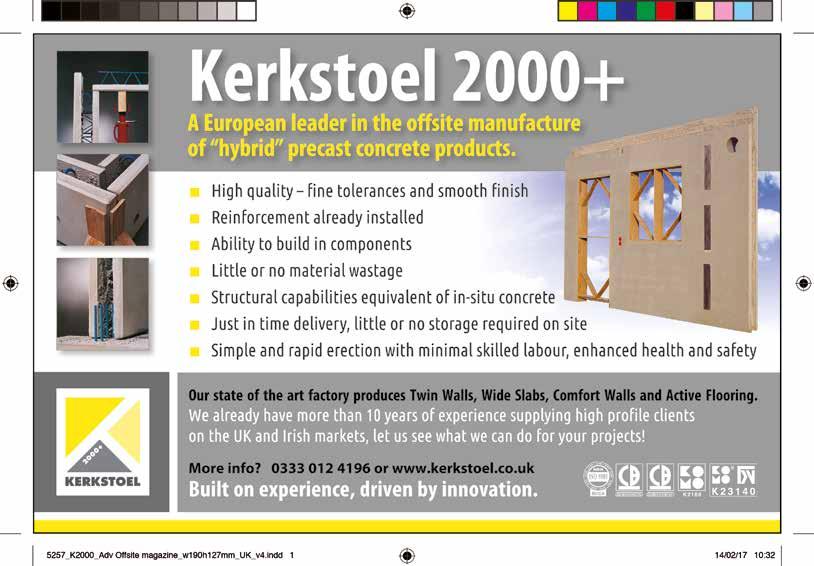
“the most radical reforms of our planning system since the end of the second world war,” there is also attempts to offset the economic impact of the Coronavirus pandemic with the MTX offsite method of construction leading the way on delivering Boris’s promises.
Source: www.mtxcontracts.co.uk
OFFSITE FUTURE: DATA & DIGITALISATION
Graham Cleland, Managing Director of Berkeley Modular, sees digitalisation as an enabler to scale and a way to leverage productivity. With the landscape of the UK’s offsite sector becoming increasingly populated over the last few years, what developments should we be looking out for?
Many new entrants – mostly concentrated on residential development – joining a host of longer-established players are embracing business models based on the manufacture of volumetric modular residential product, rather than other forms of offsite solution such as panellised product. The investment profile of these new entrants suggests that the success or otherwise of their business models directly relates to an ability to operate at scale and achieve high levels of productivity.
Digitalisation and the power of datacentricity across the wider construction industry is somewhat misunderstood. Most often, parties tend to think that the creation of 3D models using common software platforms in order that information can be easily shared and the likes of clash detection carried out constitutes all that is required for the building of an information model. Indeed, over the last 10-15 years, new roles such as BIM Manager and BIM Co-ordinator have emerged across the industry which tend to reflect this limited understanding. Yet the creation of a geometric digital twin in a virtual modelling environment does not really constitute the building of an information model that digitally captures both the product and the process needed to be executed to create the physical entity.
The newer entrants to offsite who are focused on the manufacture of volumetric modular product for the residential sector appear to lack understanding of digitalisation and the power of data-centricity. For such manufacturing-based enterprises, it is not to say that their utilisation of sophisticated software to foster collaborative working to help the efficient development of a geometric digital twin is not beneficial, rather that in itself it is not adequate for the purpose of facilitating scalability and high levels of productivity.
The digitalisation (or digital engineering) of product and process implies a more wide ranging set of activities than just the collaborative development of a geometric digital twin. Whether these enterprises have implemented rigid manufacturing workflow to support the production of a limited range of standard product, or a more flexible manufacturing workflow to support production of mass-customised products, a datacentric logic which facilitates control of the value chain and supports data-driven decision making is a pre-requisite to success. Plainly, an expansive notion of digitalisation and the power of data-centricity reflects something more than the simple idea of building information modelling, and whilst not widely appreciated it really does hold the key to an enterprise realising scale and high levels of productivity.
In order to comprehend the power of data-centricity, enterprises must secure a deep understanding of what data it needs and how it must flow to efficiently operate. Most enterprises do not invest the time and effort to secure the necessary insight regarding data creation and flow. Without this understanding, they are unable to determine the nature of the technology platform needed to support the effective digital engineering of product and process. As a result, they typically default to a technology strategy incorporating a set of software packages which cannot be fully integrated, and so
ultimately thwart the enterprise’s ability to exploit the power of data. Furthermore, these enterprises tend to recruit resource into their businesses which reflect the conventional skill sets mentioned earlier, which further limits the enterprise’s potential digital engineering and data-centricity prowess.
Of course, for those construction and offsite enterprises who have made relatively low levels of investment to help harness data, such a technology strategy might not be overly constraining because their direct competition might operate in a similar way realising similar mediocre levels of performance. However, for those newer enterprises that will be manufacturing volumetric modular product for the residential sector and who possess an appetite to operate at scale and leverage productivity, it is likely these will encounter serious challenges and such a technology strategy will ultimately prove to represent a weak link.
The true power of data is still largely unknown. This is not necessarily a criticism, rather just a statement of reality and if something does not appear to be a problem then resource is not usually allocated to resolving it. And yet, for a manufacturing-based enterprise that wants to operate at scale and with high levels of productivity, a data-centric focus is imperative.
Accordingly, whilst there is additional investment involved in acquiring the necessary talent into a business and affording the same the time to evolve the appropriate process logic and identify the associated technology platform to fully secure control of the value chain and facilitate datadriven decision making, the longterm benefits are enormous. This requirement for investment can be perceived as a leap of faith compared to capital expenditure on machinery, because the power of data-centricity is not readily understood, and often technology projects fail to get delivered.
Nonetheless, the infographic opposite contains some examples of the sort of automated data capture / flow that are required in an enterprise that aspires to be a profitable, high-volume manufacturer of volumetric modular product for the residential sector.
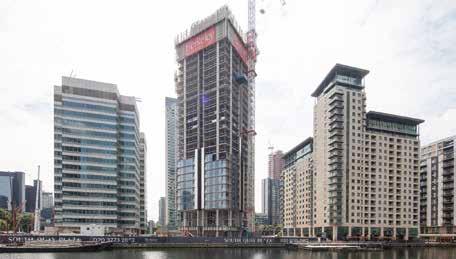
The power of data-centricity can only be realised if an enterprise has a true, granular understanding of what data is important. An enterprise must seek to understand what data it needs and how it must flow to efficiently operate, and crucially how the same should be authored, configured, manipulated and managed. It is only when an enterprise develops a profound insight that it can also start to consider how the authoring, configuring, manipulating and managing of data can be automated. Indeed, for those newer entrants to the offsite sector who want to operate at scale and achieve high levels of productivity, one option often used to compensate for not comprehending the power of datacentricity is to simply employ more resource.
Given the fragmented, skills-scarce climate that such businesses might currently be operating in, this sort of compensatory mechanism ultimately remains a limiting factor to achieving scale and high levels of productivity. The rationale behind this is straightforward enough: the skill sets of many of the sorts of people operating across the construction and offsite sectors are not sufficiently broad to properly understand the full idea that lies behind digitalisation. Whilst some of these enterprises might have a fairly advanced understanding of what to build, they are characteristically lacking in terms of their understanding of how something should be built.
The true power of data-centricity can only be realised if data is discretised, that is the packets of data that are shared between two actors (e.g. from person-to-person, or person-tomachine) only contain information that
2
is relevant to that particular transaction. Any exchange of data which involves surplus, superfluous, imprecise or erroneous information only gives rise to inefficient working because process time is wasted stripping out the unnecessary components of the communication and validating that the remainder is adequate and accurate to facilitate processing.
Furthermore, it is crucial to comprehend the importance of data purity and data integrity, so it is essential to create process logic that affords management and maintenance of data sets to avert risk of data pollution. Where data is discretised, such process logic is easier to identify and implement because the size of data packets can be configured to be easier to handle. So, an offsite providers that can secure control of the value chain and facilitate data-driven decisions is likely to become a sector lead.
To summarise, the value to any enterprise of acquiring a granular understanding of the power of data-centricity, including what data is important and how it must flow, is the essence of digitalisation and it is this knowledge that will enable scale and realisation of high levels of productivity.
For more information visit: www.berkeleygroup.co.uk
Images:
01. The power of data-centricity can only be realised if an enterprise has a true, granular understanding of what data is important 02. Large scale modular developments can be driven to high scales of efficiency through improved data harnessing