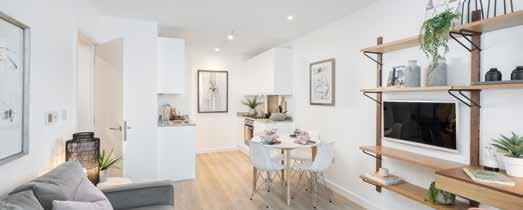
9 minute read
Building Homes: Building Efficiency
CASE STUDY
Bollo Lane is a landmark mixeduse development in Ealing, comprising 112 homes, two communal roof terraces and flexible office space that benefited from a volumetric modular solution.
Built on a challenging site previously occupied by a redundant warehouse and bound on three sides by railway lines, the difficult site context and the quality and time benefits led Pocket Living to utilise modular construction to deliver the development. This increased the speed of delivery, allowing first time buyers to move into their homes more quickly. This development was completed in 21 months from site clearance to handover.
Bollo Lane comprises 112 homes, of which 84 are sold at a 20% discount to the local market to first time buyers who live or work in Ealing. The discounted Pocket homes are 100% owned by the purchaser and remain affordable in perpetuity. The Vision Modular System was chosen as the preferred approach for Bollo Lane, enabling Pocket Living to overcome the site’s challenges and save five months on typical construction.
500 volumetric 3D structural modules were manufactured on a controlled assembly line in a factory in Bedford for this development. The automated production lines, manned by skilled operatives, transferred the modules through the manufacturing process. The Vision Modular System extended from manufacturing to delivery of the modules to site, where the process
1
continued with the module installation, followed by final connections and commissioning being carried out under strictly monitored procedures by Vision site-based personnel.
Pocket homes are well suited to modular construction as they are a standard layout. Each one-bedroom Pocket home is ergonomically designed withing two modules: the kitchen/living space make up one module and the bathroom and bedroom the other. High ceilings and large windows make for light-filled spaces that offer views and bring the outside in, and there is plentiful builtin storage. This development shows the flexibility of modular construction methodology as it also provides one, two and three-bedroom Pocket Edition homes with balconies.
The use of volumetric technology at Bollo Lane has improved building efficiencies, optimising what part of the build is constructed traditionally (substructure and cores) and what is delivered as modular construction. By reducing the number of apartment typologies and completing a minimum of 80% of the apartment fit-out offsite, Pocket Living significantly reduced the complexity in the build whilst enhancing construction precision, simplifying procurement of goods and materials and improving the design of the homes through consistency and quality of workmanship in the modular element of the build. Consistency in build quality and process is due to factory processes, as it is easier to spot trends in products used if one is found to be performing well or not performing. There is easier assessment for maintenance, so if an item is
2
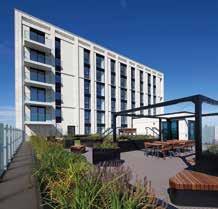
failing, it is easy to isolate and remedy. Finally, logs of the factory process are significantly better than the on-site build process.
Completing much of the apartment fitout within the modular factory helped reduce both material waste and carbon emissions, contributing greatly to the build achieving a BREEAM Very Good certification. The ecological aspect of the site has been addressed by introducing green spaces in the form of planting beds on the two communal roof terraces provided. The drainage strategy was carefully designed to reduce and delay the discharge of rainfall to public sewers to minimise the risk of localised flooring and environmental damage. The majority of materials used in the building also hold a third-party verified responsible sourcing certificate to help reduce carbon emissions. Additionally, all homes are supplied with the latest technology: smart meters, remote control of heating and lighting through smart phone and a special secure parcel drop off storage system within the communal areas.
Bollo Lane illustrates why modular construction has won the support of both government and industry, showing high-quality, energy efficient homes can be built quickly and why modular techniques will play an increasingly important role in delivering more housing.
For more information visit: www.pocketliving.com
Images:
01-02. Pocket homes are well suited to modular construction as they are a standard layout. Courtesy Pocket Living
20.10.20 ONLINE EVENT
Brought to you by Volumetric Homes Group (VHG), the Modular and Portable Building Association (MPBA); MODULAR MATTERS ONLINE CONFERENCE & EXHIBITION demonstrates the application of volumetric modular technology across a range of housing projects including; student accommodation, private residential and affordable housing.
In recent years, the need for faster, leaner, and smarter construction has become essential to meet the rapidly growing demand for affordable housing as a result of Britain's housing crisis.
Volumetric modular construction has been placed at the forefront of offsite techniques due to its remarkable impact on reducing costs whilst increasing quality and safety. In addition to this, advanced modular techniques reduce build times by an astonishing 50-60%.
Whilst historically offsite construction has been considered a novelty, as we enter a time where rapid, reliable, and high performing building solutions are required, could this be the beginning of a more modern method of construction?
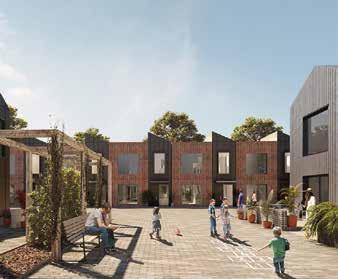

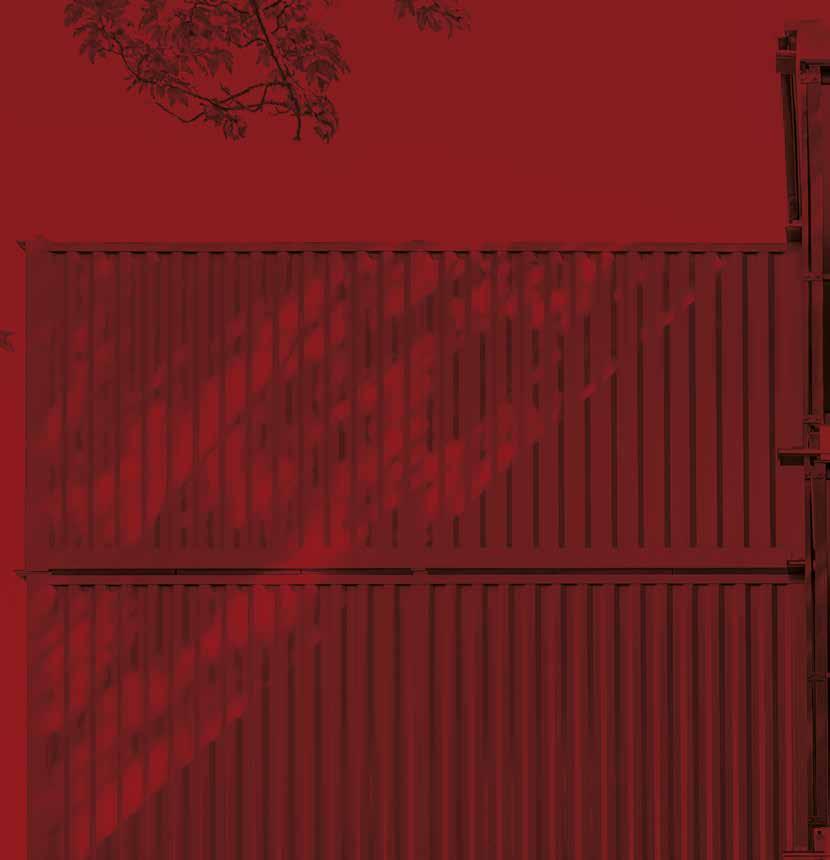
Modular Matters demonstrates how to tackle industry challenges through a range of project case studies, innovative architecture and building design, IT and software development, as well as presenting what the future of manufacturing may look like with presentations from a collection of the UK's leading offsite manufacturers.
Brought to you by
For more information on our MODULAR MATTERS speakers, visit: www.modularmatters.co.uk
MODULAR MATTERS is aimed at attracting construction clients, construction professionals, architects, surveyors, engineers, contractors, facilities managers, building product manufacturers and suppliers.
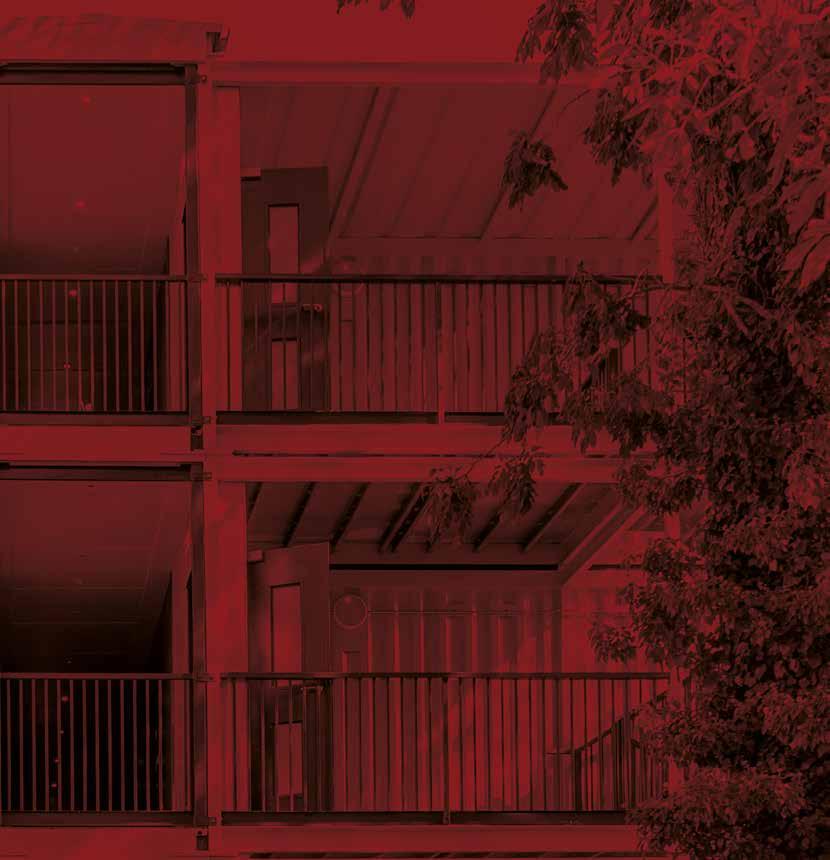
To enhance your presence at MODULAR MATTERS book an online Exhibitor or Sponsor package and receive great benefits.
To learn more about the online Exhibitor & Sponsor opportunities available including the full list of benefits, please do not hesitate to contact the team. EXHIBITOR & SPONSORSHIP OPPORTUNITIES AVAILABLE - CONTACT THE TEAM ON:
01743 290042
julie.williams @radar-communications.co.uk
ADDING LONGEVITY
TO THE SUSTAINABILITY DEBATE
It is a fundamental of good design that buildings and structures should be safe and that measures to enhance their environmental performance should not compromise this essential requirement. Here Steve Thompson, Managing Director for specialist steel framing manufacturer EOS, adds longevity and building performance to the safety versus sustainability debate.
Buildings should not only be inherently safe but should also be constructed to last a long time and therefore be inherently sustainable. Buildings are responsible for almost half of the UK’s carbon emissions and around a third of its landfill waste. This means that the UK’s sustainable development targets cannot be met without a major change to the way in which buildings are designed, constructed and operated.
National targets for carbon emission reductions and the drive for buildings that are ‘low carbon’ in operation present a huge challenge to the construction industry – a challenge which the steel construction sector is playing a major part in overcoming.

Steel can be recycled or reused endlessly without detriment to its properties. This unique characteristic gives steel a high value at all stages of its life cycle. The recovery infrastructure for steel recycling is highly developed and extremely efficient and has been in place for decades. Current recovery rates from demolition sites in the UK are 99% for structural steelwork and 96% for all steel construction products – figures that far exceed those for any other construction material.
Steel’s material properties make it the ultimate sustainable construction material both in terms of its longevity, material properties and enhancing the safety credentials of steel-framed
1
buildings. Its superior strength-toweight ratio means a little steel goes a long way, giving architects complete flexibility to innovate and create new and exciting buildings. Low and zero carbon buildings and buildings with high BREEAM ratings are readily achievable using steel construction.
An excellent example of this is a project EOS were involved in to create a prestigious £25million flagship Travelodge hotel in London that was developed as a declaration of renewed confidence in the brand following substantial investment. The aim was to deliver a fully clad offsite manufactured panelised steel frame system, complete with the sub frame of SFS
2
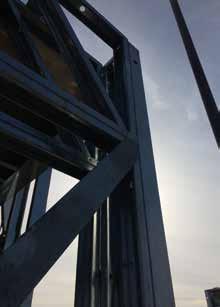
infill panels, pre-fixed to a lightweight innovative stone cladding solution which not only looks outstanding but also achieves a highly energy efficient, non-combustible building envelope. Once delivered, the fully-formed panels were craned in and fixed back to the substrate.
The impressive eight storey, 395- room property is built to BREEAM excellent standards and delivered through innovative engineering combined with technically advanced offsite manufacturing. The greater efficiency and quality associated with sustainability is also helping to make this Travelodge more commercially successful. There is growing evidence that BREEAM Excellent buildings provide increased rates of return for hotel operators. BIM Level 2 technology combined with design for manufacture and assembly protocols reduced errors onsite and snagging – as well as enhancing the energy performance throughout the lifecycle of the building.
When the cost of operating a building for 30 years can be four times greater than that of designing and building it, it is no surprise that those who own and maintain buildings are keen to find in-use savings. Now we have more sophisticated research available, the equation of ‘build them high build them cheap’ – simply does not stack up from an owner operator’s perspective. And this is why steel framing systems are favoured by the build-to-rent, education, healthcare and other public sector buildings.
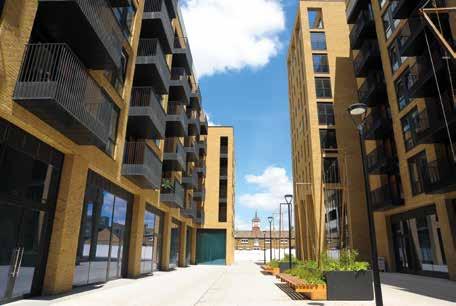
The UK leads the world in steel construction both commercially, technically and in terms of quality. The industry has made dramatic improvements in technology, productivity and efficiency. According to research carried out by independent consultants Construction Markets – steel continues to be overwhelmingly the structural framing material of choice with their survey showing that steel now has a 72.5% share of the multi-storey office market and a 60.9% share in the ‘other multi-storey buildings’ which includes retail, education, leisure and healthcare sectors.
Quality, safety and sustainability are at the very core of our organisation, it is therefore with great pride that I share that EOS has just successfully completed three quality badge audits with 100% success and zero nonconformances. This is an outstanding achievement and testament to the work that went in to ensuring all procedures, records and management systems were in first-class order providing the auditors with all the necessary information to award EOS total compliance with zero non-conformances. We successfully passed the five-day re-certification audit against ISO 9001:2015 quality management systems, ISO14001:2015 environmental management systems and ISO45001:2018 health and safety management with no nonconformance issues or even any opportunities for improvement or areas of concern. I would like to take this opportunity to publicly thank
3
4

my team for their hard work and dedication to achieving the ultimate standard.
Partnerships are central to our business. We have a wealth of experience and our specialist teams strive to support our clients throughout the design and construction phase. EOS has the capability and capacity to meet the exacting demands of the construction industry and guarantee a very competitive price structure with no hidden costs for deflection heads or transport and we can provide a lump sum total cost which will not alter, providing the specification remains unchanged.
For more information visit: www.eosframing.co.uk and to view video case studies including the Travelodge Hotel and client testimonials visit: www.eosframing.co.uk/informationcentre/video-vault
Images:
01-04. Steel's superior strength-to-weight ratio means a little steel goes a long way, giving architects complete flexibility to innovate and create new and exciting buildings