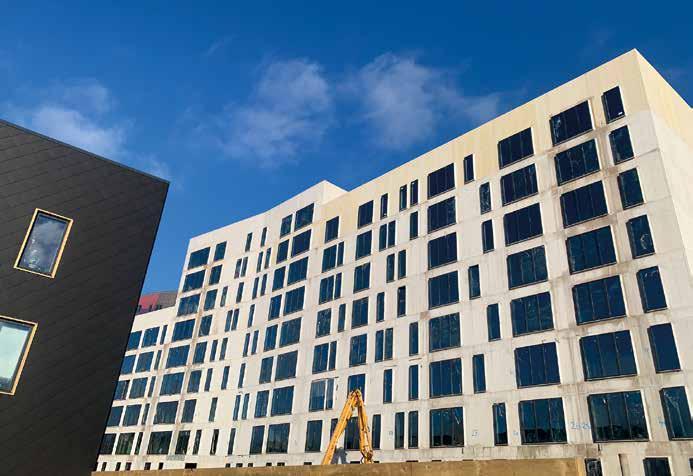
11 minute read
Bringing Accuracy to Offsite
Offsite construction provides many benefits and at its core is the need for accuracy. Nick Milestone, Operations Director at Sigmat explains why Building Information Modelling (BIM) is a perfect partner for factory-based design.
The clash detection capabilities, enhanced level of detail and greater visualisation that the 3D digital environment offers, all provides the assurance that if it fits in the model then you know it will fit on-site. While this assurance is of course valuable on any construction project, it’s perhaps especially critical when it comes to offsite – given that one of its primary advantages is for on-site assembly to be both quick and efficient. If components don’t fit together correctly, then that level of efficiency will fall dramatically. Essentially, it’s the idea of a digital rehearsal. You get to construct it twice: once in the digital environment and once on-site. From accuracy at the detailing phase through to on-site coordination, Tekla software comes into play at every stage and feeds into our Virtual Design and Construction (VDC) processes.
Taking this theme of accuracy further, Sigmat recently worked closely with Trimble to embed Sig-Deck (own decking profile product) into the Tekla BIM library in Tekla Structural Designer. Having access to this product-specific content will in turn lead to enhanced
1
levels of accuracy, as well as aiding engineers from a design calculation point of view.
Another benefit of BIM for offsite is the data integration that it enables. All the constructible data is present and co-ordinated throughout the entire process, ensuring that the high levels of accuracy are maintained from the detailing stage through to factory fabrication and beyond.
When it comes to fabrication, we’re able to upload the CNC files from the Tekla Structures model directly
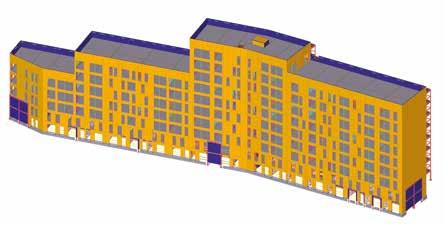

into the factory and use this data to programme our machinery. When processing stud and track profiles, for example, the machines will use the model data to correctly profile it, cut it to specification, drill the holes, etc. Fully automated, this enables our steel frame fabrications to be carried out to extremely high levels of accuracy – to within 2mm.
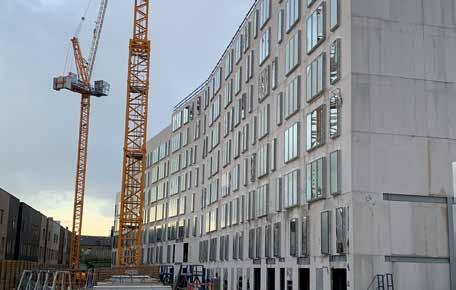
As well as offering a connected data journey, the Tekla modelling software is also designed to work with a variety of construction materials, including steel, concrete and timber.
At Sigmat, we work with both hotrolled and cold-formed steel. As such, it’s important that our chosen modelling software can keep up and allows us to detail and consider all materials within the one model environment. As well as saving time and improving productivity levels when it comes to the detailing process – avoiding the need to swap between multiple software interfaces or deal with several file types – this is another factor that contributes to high levels of accuracy.
Sustainability is a key consideration for us all. Thanks to our BIM workflows and the accuracy that this 3D modelling enables, it means that we can achieve zero waste. With correct material quantities ordered, thanks to the automatic quantity take-offs – no rework required due to detailing or fabrication errors and integrated data.
In addition to the Tekla structural modelling software, we have recently incorporated Trimble Connect – Trimble’s cloud-based collaboration platform – into its business. Used throughout the company, both internally and externally, Trimble Connect is facilitating effective communication and coordination.
As well as using the Trimble Connect platform to share files and models internally within Sigmat project teams, we’re also able to better communicate with the client and other key project stakeholders. Everyone is a part of the same project. While collaboration is important on any construction project, it’s perhaps especially critical when it comes to offsite, volumetric and modular. For example, our pre-panelised frames will often require close co-ordination with M&E contractors, ensuring that we are all aware of what the other party is doing.
At the moment, we’re working towards BIM Level 2+ and ISO19650. A key part of this is working with our clients within a federated environment. With the one-model approach, we stand to achieve greater levels of clash detection, a seamless design process and improved collaboration and coordination. It’s clear that BIM has been a really big part of offsite, developing alongside the sector as it has grown in popularity and strength. The changes seen within construction, offsite and BIM technology in the last 25 years has been extraordinary and the next 25 years promises to be just as instrumental.
Personally, as we move forwards, I can see the industry shifting towards a more iterative, predictive and intelligent form of modelling, using data from past projects and designs to inform and influence the new. Also, an emphasis on standardised platform design. Currently, we engineer and design every building and structure on an individual, one-off basis, rather than using a standardised platform as a base. Doing so could help to boost Offsite’s efficiency and productivity benefits even further.
2
4 3
For more information visit:
www.tekla.com/uk
Images:
01-04. Modelling software creates a connected data journey and is designed to work with a variety of construction materials, including steel, concrete and timber
MOVING HEALTHCARE WHERE NEEDED
The design team that developed the temporary NHS Nightingale Emergency Hospitals at the height of the COVID-19 pandemic in April 2020, oversaw the completion of the first of 40 community NHS diagnostic centres opening in England.
1
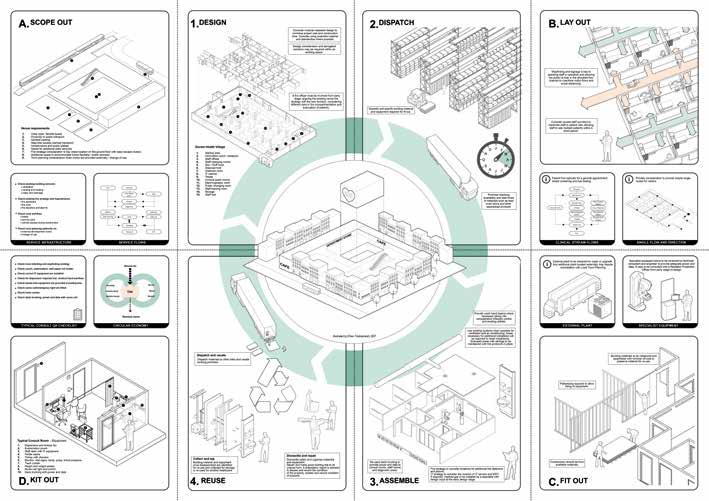
To reduce the current pressures on the NHS, interdisciplinary design consultancy, BDP and its construction and facilities management partner, CFES have been working with University Hospitals Dorset NHS Foundation Trust to open a new centre for breast screening and diagnostics in Beales department store in Poole. Situated in the Dolphin shopping centre, it will also offer testing and assessments for orthopaedics, ophthalmology and dermatology diagnoses. In a highly sustainable and efficient move, the BDP team has reclaimed and reused materials from the demounted Nightingale Hospitals across the UK to build a one-stop-shop for much needed and overdue checks, scans and tests in the community.
Paul Johnson, Architect Director at BDP, who also led the design of the Nightingale Hospital in London’s ExCel centre, explains: “This project is the first of its kind in the country. Not only does it support a circular economy by reusing the materials from the emergency COVID-19 hospitals in an existing building, it is also built on the same collaborative and sustainable methods of design and construction.
“NHS waiting lists are at an all-time high and through good design, based on imaginative adaptation of space and recycling of equipment, we are creating real solutions to the problem. As a collaborative, interdisciplinary team, we are thinking bigger about the issues faced by today’s society. This new centre will help bring true health benefits to the community,
1
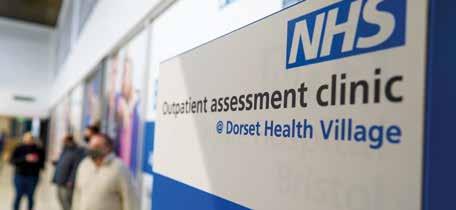
reduce pressure on our NHS and give a welcome boost to the retail sector. We are very proud to be a part of such an impactful and important initiative and hope to deliver this flexible and repeatable solution for another 39 diagnostic centres in original, underutilised spaces across the country.”
The new centres will benefit millions of people by providing earlier diagnostics and more convenient and accessible treatment in communities across the country. The design also contributes to the NHS’s net zero ambitions by providing multiple tests at one visit, reducing the number of patient journeys and helping to cut carbon emissions and air pollution.
Ashleigh Boreham, Deputy Director of Design and Transformation at Dorset Clinical Commissioning Group, said: “The pandemic has affected the way NHS trusts deliver services. Unfortunately, this meant many outpatients appointments had to be cancelled to reduce the spread of infection with the rise in number of patients with COVID-19. We have reached a critical point where we have to manage the backlog and protect the NHS, which has led us to the opening of this centre. I’m so pleased at the speed we have mobilised this solution but not at all surprised.
“This team deserves a lot of credit. Adapting and repurposing unused retail space is going on elsewhere in the country but to work within this existing centre and create something built simply for the outpatients, for diagnostics and assessment, is quite different – it’s a first.”
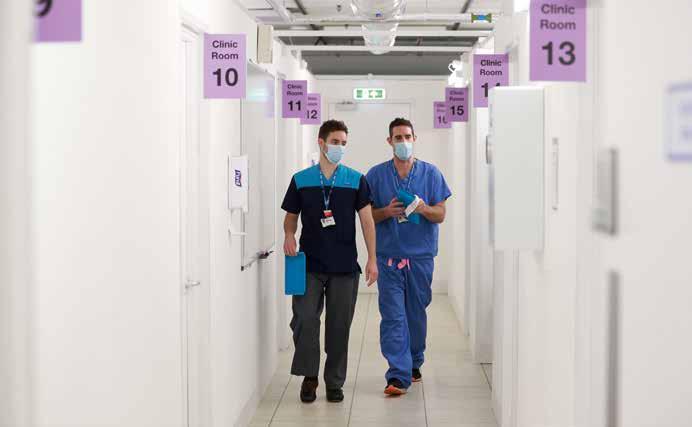
Rob Doubtfire, Managing Director at CFES, added: “Working within established relationships in proactive design and build project delivery has delivered real benefits for the NHS for the first of this kind of Community Diagnostic Centre. The use and re-use of materials from Nightingale stock
2
3
requires quick and close engagement from all partners and once again we are pleased to have been a part of this with the NHS and BDP.” The community diagnostic village in Poole is now open for patients referred for assessments from local GPs.
For more information visit:
www.bdp.com
Images:
01. Dorset Health Village diagnostic design instruction manual showing circular offsite thinking. Courtesy BDP 02-03. The use of efficient demountable healthcare buildings could only have been achieved with offsite manufacture. Courtesy University Hospitals Dorset NHS Foundation Trust.
WORKING AT CHANGE
There is a real need for skilled workers in both the construction and manufacturing sectors, but as Ron Clarke, CEO of the McAvoy Group argues, offsite manufacturing may provide many answers.
A recent report issued by the Construction Industry Training Board (CITB) and Experian that covers the period 2021-2025 highlighted the need for an extra 217,000 workers in the construction sector. This equates to 43,000 workers per year over the next five years. Furthermore, in his 2016 Review of the UK Construction Labour model, Mark Farmer identified the real ticking time bomb as being that of the industry’s workforce, size and demographic. It was noted at the time that, based purely on the existing workforce age and current levels of new entrant attraction, there could be a 20-25% decline in the available labour force within a decade.
Additionally, referring to the 2015 Arcadis paper ‘People and Money’, Mark Farmer highlighted the need to recruit 700,000 people in the construction sector to replace both those retiring and those lost through natural leakage to other industries. It is clear then that the demand for extra workers will not be met through new industry entrants. Hence, it should be considered – how do we attract more people to the industry to address this deficit? I would argue that offsite manufacturing (OSM) can be part of the solution.
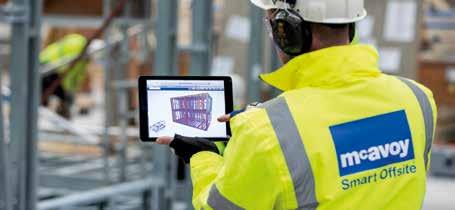
1
Other industries may not experience the same growth trajectory as construction – therefore, this presents a clear opportunity to attract people into the construction sector. OSM is ideally placed to attract people, given its emphasis on creating buildings in a factory setting. For instance, the transition from one manufacturing industry to another, such as modular construction, is likely to be less challenging for workers than if they were to transfer from a manufacturing environment to a construction site environment.
OSM also offers a much more attractive work environment than the traditional construction setting, where all works are carried out on-site and factors such as weather conditions make it considerably more difficult to deliver projects with time and cost certainty. Shift patterns can also be introduced much more easily in a factory environment, which can allow flexible response to demand. A manufacturing-led approach leads to a less itinerant workforce too, as the focus is on one location. Breaking down the manufacturing process into component parts also alleviates need for wide skillsets and training can be given more easily to upskill the labour force. All this means that OSM is much less exposed to high labour costs, particularly in periods of high demand. It is a well-rehearsed fact that productivity in the construction sector is extremely poor when assessed against other industries. Manufacturing-led industries tend to perform much better when automation and technology play a significant part in productivity improvement. During periods of high demand for labour, productivity tends to reduce due to less productive workers entering the industry which negatively impacts overall productivity. This is due to labour being the dominant determinant of overall unit productivity. In other industries, where automation is more prevalent, productivity is more uniform. A manufacturing environment proves less susceptible to productivity volatility.
With its appeal to a wider spectrum of workforce, OSM has a huge opportunity to develop and reduce the overall demand and reliance on a decreasing trade-based skills pool. Workers can be trained to the appropriate skill level needed, providing a much greater pool to recruit from. OSM is also better placed to invest in apprenticeships via structured training schemes. Apprentices will be employed at the same location throughout their apprenticeship, which provides a stable learning platform for new recruits. With a consistent flow of work through the factory, offsite can and will play a major part in addressing current and future skills shortages.
For more information visit:
www.mcavoygroup.com
Images:
01. Workers can be trained to the appropriate skill level needed and provide a much greater pool to recruit from across the offsite sector