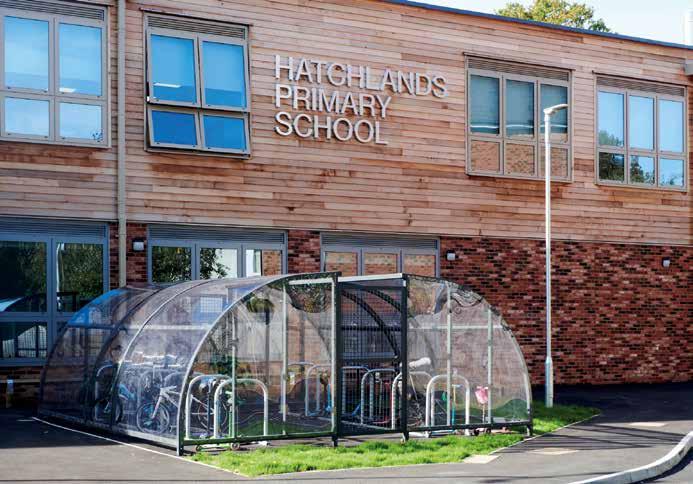
51 minute read
Industry News
Elliott Completes New Best-Value Primary School in 32 Weeks
Development of a new school in Redhill, Surrey, has been completed in just 32 weeks thanks to the speed and versatility of the Elliott permanent modular building system.
Built to provide additional school places because of new residential developments and increasing birth rates in the area, the BREEAM Very Good-rated Hatchlands Primary School has been developed as part of Department for Education’s (DfE) Modular-A Primary School framework. Elliott was awarded the project because it demonstrated excellent value for money and was able to provide a full turnkey solution. The modular manufacturer worked closely with award-winning designers DLA Architecture to create a contemporary high-performance building sympathetic to its environment.
Located adjacent to a Conservation Area on what was once a challenging urban brownfield site, offsite construction of the school used the Elliott Ibex permanent modular building system. Modules were delivered with a high Pre-Manufactured Value and ready for final finishing on site. This reduced the construction schedule by around 50% compared to a traditional on-site build. Elliott routinely achieves MPV’s of over 80% using its offsite construction solutions. The Ibex system is fully building regulations compliant with passive ventilation and has a minimum 60-year design life. Hatchlands Primary School features a contemporary style aesthetic achieved using brick, cedar cladding, purple panelling to complement the school’s branding, render and significant glazed elements to create light-filled teaching spaces.
A large span sports hall uses the Elliott Hybrid system, providing the school with a valuable space that is now used for assemblies, sports and performances. The system allows incorporation of large open atriums and increased ceiling heights and can be fully integrated with the modules to provide greater design scope.
The school was also built to high sustainability standards and achieves a BREEAM Very Good rating. This means it is within the top 25% of buildings in terms of sustainability, aligning with the goals of Reigate and Banstead Borough Council. A suspended concrete floor helps to minimise transmittance of noise, meeting minimum standards set out in The Building Bulletin 93 (BB 93) ‘Acoustic Design of Schools: A Design Guide’. The completed school is indistinguishable to a traditional on-site build yet delivers all the benefits of offsite construction; a shorter 32 week build schedule, less site traffic, more consistent build quality, a reduction of on-site waste and future reconfigurability and recyclability.
Graham Stevenson, Construction Manager at Elliott, said: “Completing Hatchlands Primary School in just 32 weeks is testament to the dedication of all project partners and benefits of our offsite systems. The new school is an important and exciting development for the community and we hope that it will inspire some of the pupils to take up a career in construction.”
Moira Anderson, Headteacher at Hatchlands Primary School, commented: “What a fabulous new school we now have. The children were really excited about moving into their new classrooms and it is certainly very different to the temporary teaching areas we have been using. We were all really impressed with the professionalism and considerate approach of the Elliott team.”
Elliott and its affiliated UK companies have a new face, new name and have united under the common brand name of Algeco. For more on this see p26.
Source: www.elliott uk.com
Sajid Javid Opens Latest MTX Project
The Secretary of State for Health and Social Care, the Rt Hon Sajid Javid MP, officially opened the latest project to be completed by offsite building specialist, MTX, at Leighton Hospital in Crewe.
The 4200sq m two-storey development provided the Mid Cheshire Trust with an A&E department extension that offers a larger, better, and safer environment for patients and staff, whilst helping to combat the extended waiting lists that the NHS is currently facing due to the pandemic.
The development is comprised of ground floor treatment rooms including, rapid assessment bays, isolation and resus bays, a bereavement suite, x-ray facilities, as well as a dedicated paediatric unit and mental health assessment rooms. On the first-floor level, a large number of offices and staff areas have been created. The extension was delivered following the Trust successfully securing Government funding last year.
Steven Hartley, Project Director from MTX heading up the Leighton Hospital works, said: “Efficiency has never been more important in the healthcare industry, especially during these unprecedented times. The project we delivered for Leighton Hospital will allow the Trust to provide greater clinical effectiveness for both patients and staff. “The new department sees the relocation of the ambulatory care services into the new increased capacity facility, in essence, creating an urgent care village which not only reduces patient assessment times, but supports a more cohesive working and overall improved patient experience.’ We’re incredibly proud that the Secretary of State was able to make the visit to open the newly completed project at Leighton Hospital.”
James Sumner, Chief Executive of the Mid Cheshire Trust, added: “We were delighted to welcome the Secretary of State to Leighton, at a time when we are investing in enhanced hospital services for our local community. The purpose-built A&E ensures a bigger, better, and safer environment for both patients
Source: www.mtxcontracts.co.uk

Rollalong Appoints New Manufacturing Director
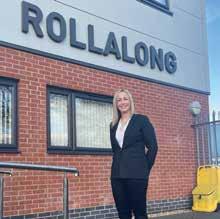
Modular manufacturer Rollalong has appointed a new Manufacturing Director, whose varied career has spanned several sectors, from confectionery to marine machining. Michelle Davies joins the senior team at the largest permanent offsite manufacturer in the south of England, bringing with her years of expertise in various manufacturing management roles. and staff. A&E attendance has increased across the country in recent years, so this provides an excellent opportunity to meet the needs of our growing population of 300,000.”
Dr David Matthews, Clinical Director of Emergency Care, concluded: “The NHS has been tested to the maximum by a combination of higher patient attendances, the Coronavirus pandemic and the annual winter pressures. This facility is really exciting for the Trust – it has been carefully designed to allow for the clear separation of children and adults in a modern, welcoming environment that will greatly improve the patient experience.”
“I joined Rollalong because I saw an opportunity to challenge my skill sets in business management and work with a team that is dedicated to their industry,” said Michelle. “Rollalong is a successful company employing skilled local people. The team has been great in welcoming me and helping me understand all things modular.”
Michelle has several aims and objectives to achieve in her new role, such as improving production processes and flows to achieve target hours, costs and client requirements, maintaining strong communications between production and the rest of the business, and reviewing opportunities to automate, all while continuing to manufacture a high-quality product.
However, Michelle has not always worked in the modular or construction industries; in fact, her first role was in confectionery. “My career began working up from the shop floor in the confectionery industry all the way up to Production Manager,” said Michelle. “From there I became a Production Manager building caravans for the leisure industry and then transferred to General Manager in metal fabrication and machining for the marine and architectural sectors. I am well respected within the marine industry, having worked closely with production builders and class surveyors. “I’ve learned valuable transferable skills throughout my career such as management of people and process control, both of which I’m excited to bring to the table at Rollalong. Engineering is also the base skill for this product which I have experience in, and over the next couple of years I’ll be expanding my knowledge on modular builds. I’m thrilled to be working at Rollalong, it’s been a steep learning curve since my appointment, and I have loved every second. There’s always an exciting new project to work on while using R&D to improve our work along the way.”
Rollalong’s Managing Director Steve Chivers commented: “We are delighted to welcome Michelle who brings a wealth of knowledge and experience to the team. We have a strong pipeline of work, and we are committed to delivering a quality product for all of our valued clients. Michelle has joined us to ensure that Rollalong’s manufacturing capabilities meet the strategic needs of the business over the next few years, delivering efficiency improvements and digital solutions to create a solid foundation for the manufacturing team to grow and sustain itself in alignment with the positive growth curve of the company.”
Source: www.rollalong.co.uk
Seismic Unveil New Platform-based Approach Precast Foundation System Welcomed to NHBC Accepts
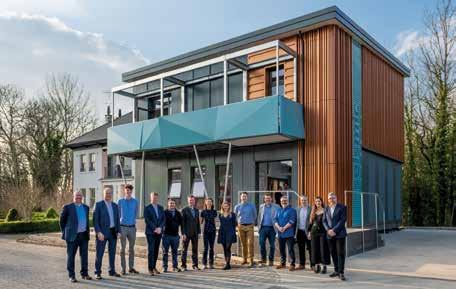
The Seismic demonstrator is the culmination of a four-year project developed by a consortium comprising consultancy blacc, offsite manufacturers Elliott Group and the McAvoy, Tata Steel, the Manufacturing Technology Centre (MTC), the National Composite Centre (NCC) and Specific (part of Swansea University).
Designed in line with the government’s Construction 2025 targets, it exceeds them in every way, delivering a building that is 75% faster to complete, 70% lower in carbon impact and 47% better value than traditional construction. One of the unique aspects of the project is the combination of three manufacturers working independently on the same building. The demonstrator shows this to good effect incorporating systems from McAvoy, Elliott Group and Tata Steel.
Richard Crosby, Director at blacc, said: “Seismic was developed to help drive a shift towards modern methods of construction (MMC) in the industry. What the consortium has achieved demonstrates the value of a standardised, platform-based approach to construction. It is faster at every stage, from design through to manufacturing, assembly and fitout, and offers better quality and value, alongside a dramatically lower carbon impact. Seismic sets the template for a platform-based approach to construction and proves that it can be done now. This offers a huge opportunity for unlocking development, providing a solution for a range of sectors, including education, healthcare, workplace, leisure and residential.”
Seismic has been worked on in two stages. Phase one was developed in response to work with the Department for Education (DfE) to improve the delivery of schools. It focused on the design of a standardised, lightweight steel frame and connector and was completed in 2020. Because of its success, a second stage was commissioned. The objective was to design and construct core components that would work with the frame system, including wall, floor, ceiling and roof cassettes, offering an ‘all-in-one’ solution for clients.
Sam Stacey, Challenge Director for Transforming Construction, said: “Most modular construction relies on bespoke systems created by individual manufacturers. A lack of standardisation means that different systems are incompatible, which adds risk for clients, especially once they take on responsibility for the building’s operation and maintenance. What Seismic shows is that if everyone works to one system it is possible to deliver buildings much more effectively, whether compared with existing modular techniques or traditional construction.”
The National Composites Centre (NCC) was appointed to analyse and recommend the best materials to be used for the platform. It also developed a window shroud which was used within the demonstrator building. This supported a wider package of work led by Specific, part of Swansea University, to assess the carbon impacts of Seismic. This looked at the whole process including design, materials, manufacturing, component performance and logistics.
The analysis showed that a standard Seismic module comprises 581.3 kgCO2e per sq m, well below Construction 2025’s target of 1,300 kgCO2e per sq m. And, because Seismic can be reused, either by relocating modules to other sites or by refurbishing individual components and cassettes, it adds a 234 kgCO2e per sq m clawback. This brings Seismic well beyond even the lowest stretch targets being discussed in construction today.
People can visit the demonstrator building at BRE Watford until the end of the year. To find out more visit: www.seismicgroup.co
NHBC has announced that Roger Bullivant’s RBeam precast concrete foundation system has been officially welcomed to NHBC Accepts. NHBC Accepts is an all-inclusive, end-to-end service that helps to build confidence in innovative construction and enables innovative products to be fast-tracked for NHBC warranty.

As part of the new service, detailed and robust technical reviews of design, manufacture, and construction result in the provision of a certified usage license for a bespoke NHBC Accepts logo and website listing. NHBC’s Innovation Manager, Richard Lankshear, said: “Following a thorough approval process we are delighted to welcome Roger Bullivant Limited to NHBC Accepts.
“An NHBC Accepts certificate is a way of demonstrating that innovative products or systems have already been reviewed thus reducing the risk of delays on site. NHBC Accepts will play a critical role in ensuring developers, manufacturers, lenders, and consumers have faith and confidence in the quality of new homes built with innovative forms of construction.”
The RBeam is a factory-produced reinforced precast concrete foundation system for low-rise developments. The system is used with a range of piled foundation techniques catering to many different soil types and ground conditions including clay heave situations.
Richard Taylor, Bullivant’s Foundation Systems Director, added: “This approval brings customer confidence and improved productivity on site. We also recognise it as an important achievement in the progression of offsite manufacture in the residential market.”
Bullivant’s Foundation Systems Technical Manager Nigel Rake also said: “Roger Bullivant Limited has been designing, manufacturing, and installing precast foundations for many years. The RBeam system is a category 3 pre-manufactured component under the government’s MMC definition framework and we are very pleased that this has been given a seal of approval for NHBC Accepts. This will provide further assurance in our RBeam system to all our customers and the wider industry.”
Basildon Rough Sleepers Get Modular Home
A former adult learning facility will be converted into 10 homes for rough sleepers, with a further six selfcontained SoloHaus offsite homes installed on-site. The Hill Group has gifted the modular homes, and this generous donation, together with the conversion, will result in 60% of Basildon’s homeless being able to live in safe, secure homes and no longer living on the streets.
Planning permission was granted by Basildon Council’s Planning Committee for the former ITEC site in Burnt Mills Road, Basildon. The new development will act as follow-on accommodation specifically for Basildon residents who have found themselves experiencing periods of homelessness. Residents will live in the homes for a maximum of three years, and some will stay for a minimum of six months on an assured shorthold tenancy.
The scheme, which will have office space for support workers, council staff and supporting agencies, has been funded through the Rough Sleeping Accommodation Program (RSAP) from the DLUHC (Department for Levelling Up, Housing & Communities). The six modular units, known as SoloHaus, have been gifted by The Hill Group as part of their commitment to providing 200 homes over the next five years. They will provide safe, comfortable, sustainable homes for single people experiencing periods of homelessness. The 10 one-bedroom homes inside the building will be managed by the housing association, Peabody South East, in partnership with Basildon Council.
Andy Hill, Chief Executive, The Hill Group, said: “We are delighted to be working with Basildon Council on this scheme which once complete will change peoples’ lives for the better. It is excellent news that planning has now been approved, and we are looking forward to working with all of the teams to deliver SoloHaus in Essex.”
Chairman of the Housing and Estate Renewal Committee Councillor Andrew Schrader said: “The scheme aims to provide our residents affected by homelessness with a home. Receiving support, vocational training and the skills required to be able to move on and sustain their own tenancy, they will get the opportunity to turn their lives around.”
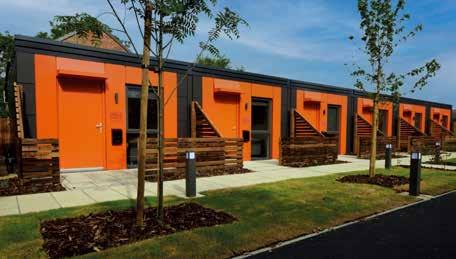
Source: www.solohaus.co.uk
Donaldson Timber Systems Rebrands from SMTS Dudleys Delivers Sweet Project
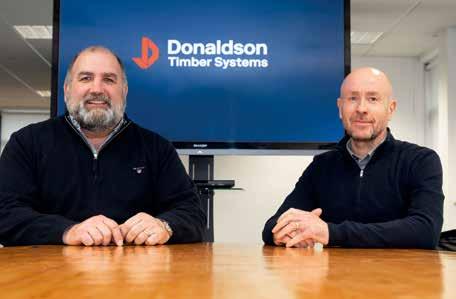
The UK’s leading timber frame manufacturer has a new identity. Following its acquisition in 2021, Donaldson Timber Systems (DTS) is the new brand of the business formerly known as Stewart Milne Timber Systems (SMTS).
Established in 1975 as the timber frame arm of the Stewart Milne Group, Donaldson Timber Systems is a pioneer in timber frame technology and manufacturing, operating throughout the UK from three manufacturing plants in Aberdeen, Witney and Falkirk. Since its acquisition in December 2021, all staff and operations have moved over to the Donaldson Group, with Managing Director, Rod Allan and the former SMTS Board of Directors continuing to drive the business.
Alex Goodfellow, formerly Stewart Milne Group Managing Director – Strategic Development, has a new role in the Donaldson Group, as CEO of Donaldson Off-site. Comprising Donaldson Timber Engineering, Donaldson Timber Systems, and Rowan Manufacturing, this new division services the UK housebuilding and construction markets with an unparalleled breadth and depth of products and services.
Donaldson Timber Systems prides itself on being highly sustainable, innovative and efficient. With unrivalled experience and knowledge in timber, DTS has an established history of bringing new commercial and operational innovations to the market. One example is the Sigma II closed panel system offering nearpassivhaus standards of insulation and sustainability. The system is being widely used with housing developers, particularly with those interested in whole life costs and fabric performance, contributing positively to fuel poverty challenges.
The Donaldson Group has over 160 years of expertise in timber importing and distribution, as well as decades of experience in timber engineering and merchanting. The acquisition strategically and operationally complements the Donaldson Group portfolio and marks the Group’s entry into the timber frame market.
Rod Allan, Managing Director, Donaldson Timber Systems said: “The rebrand to Donaldson Timber Systems is a major milestone in our company history. While the business is moving forward with the same people and operations as before, incorporating the Donaldson name highlights the step-change in our approach. We’re very proud to have joined this longstanding family business, with both timber and people at its heart. The quality of our products and service remains unchanged, but we have many exciting plans and we’re confident that this new venture will prove of great benefit for our customers.”
Andrew Donaldson, CEO of the Donaldson Group added: “It’s been a fantastic few months integrating the new members of the team into the Donaldson Group, and the response from all involved has been hugely positive. This change of name fully aligns the business with the Group and has included a full rebrand including new logo, new branding and new website.
“Now the rebrand exercise is well underway, we’re looking forward to seeing Donaldson Timber Systems develop and grow, building on the excellent foundations that were created in its almost 50 years of operation.”
Currently led by the sixth generation of Donaldson, the Donaldson Group comprises 11 specialist timber and building product businesses, operating throughout the UK from 45 locations employing over 1,500 people.
Pictured: Rod Allan (Managing Director) and Mike Perry (Business Development Director), Donaldson Timber Systems.
Source: www.donaldsontimbersystems.com
Structural and Civil engineering consultancy, Dudleys has completed works on a major new £34million, light gauge steel frame (LGSF) residential development on Sweet Street in Leeds city centre for its client Oakapple Group.
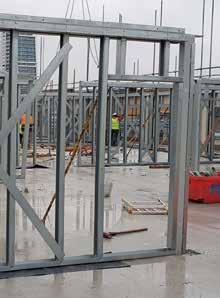
Pin Yard is a 12-storey build to rent (BTR) scheme of 216 units comprising a mix of studios, one, two, and three-bedroom apartments. The building incorporates a resident’s gym, lounge, co-working spaces, a basement car park and private gardens. It is located on a former warehouse site, adjacent to the Headquarters of Jet 2 in the burgeoning South Bank area of Leeds. Oakapple Group speculatively purchased the site, gained planning consent in 2019, and secured forward funding from Grainger plc, the UK’s largest listed private landlord. The scheme is now handed over to Grainger to operate rentals within its BTR portfolio.
Paul Brownlow, Director at Dudleys said: “We are delighted to complete this significant scheme on behalf of Oakapple Group. As a local consultancy, we are very familiar with the regional landscape and built environment to be able to provide strategic and practical guidance throughout the build programme. The project was not without its challenges due to the tight site constrained by two main roads as well as delays caused by the pandemic. We have worked closely with the delivery team to complete a scheme of exacting standards, using advanced techniques, that we are very proud of.”
Phil Taylor, Chairman of Oakapple Group, added: “It’s certainly not been easy for the team, but despite everything we have all had to face over the last 12 months we continue to work together as a team. We are delighted the project completed successfully in January 2022 and we will definitely look to negotiate further projects with Dudleys.”
A Member Of:

Offsite Alliance
James Latham Officially Launches Carbon Calculator
James Latham Ltd (Lathams), one of the UK’s leading distributors of timber, panels and decorative surfaces, officially launched its powerful new specification tool, the Carbon Calculator at Futurebuild 2022.
Developed in partnership with the University of Bangor the Lathams Carbon Calculator has been designed to help architects and designers better understand the sustainability of the materials they specify. Trialled amongst Lathams’ customers over the past three months, it is already assisting them in selecting the most suitable, sustainable option to meet their respective project requirements. It is also giving specifiers essential assurance that the information they receive relating to a product’s carbon credentials is complete and accurate, from sourcing the raw materials to selection and delivery.
The Carbon Calculator is a back-end tool, designed to achieve transparency and give specifiers confidence when selecting for sustainability. Built using official, publicly available data and manufacturer product information, the Carbon Calculator collates and aggregates the environmental impact of a chosen material, according to three criteria: Carbon Footprint, Embodied Carbon and Data Confidence.
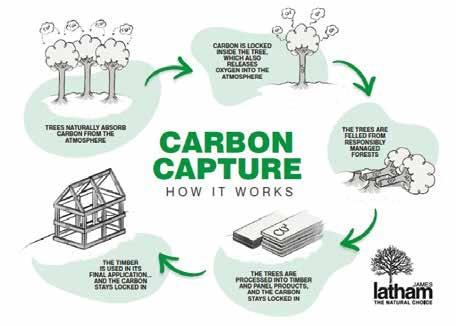
Once evaluated, the product receives a confidence rating from 1-4 (one being the best). The lower the score, the higher the availability and quality of data points reviewed (e.g. published EPDs). The final rating, including carbon data, is then added to quotations, invoices, delivery notes, and other key documentation, delivering a tangible, codified proof point. This ensures a robust audit trail for the product, providing valuable information for future carbon reporting and responding to sustainability briefs.
It is important to caveat, even the lowest-rated materials still meet stringent supply requirements, such as mandatory sourcing from sustainably managed forests. Essentially, the Carbon Calculator’s rating is intended to highlight the quality and range of available product information, certification and documentation, informing the specifier if data is based on an estimate or actual performance.
Commenting on the launch of the Carbon Calculator, Ewa Bazydlo, Environmental Manager at Lathams, said: “We feel that this is the latest milestone in an exciting journey towards low-carbon specification across the entire building, construction and design community. By providing a methodology through which the value of sustainability information and certification can be holistically appreciated, we’re increasing confidence amongst architects and designers that they are making the greenest choice possible, in line with the requirements of their project brief. Working closely with academic institutions, market leading suppliers, designers and developers we’ve created a backend tool which adds tangible value to the material selection process.”
Source: www.lathamtimber.co.uk/about-us/ carbon-calculator
TopHat Appoints Former FTSE 100 HR Director to Spearhead Growth
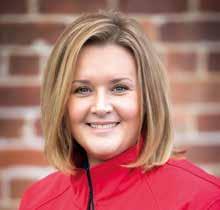
TopHat, the Goldman Sachs-backed modular housebuilder, has hired Lucy Weaver, formerly of FTSE100 firm Halma Plc and Unipart Rail (a division of the Unipart Group), as Group HR Director. Prior to her role at Halma Plc, Weaver worked at Unipart Rail. She was responsible for managing 900 employees across 14 sites across the UK. Weaver has 18 years of experience in manufacturing and logistics, meaning she is well placed to help TopHat reach its growth ambitions.
Weaver will lead the HR agenda for TopHat with a strong focus on recruiting and growing talent and capability as the company looks to increase its current capacity to deliver up to 3,500 factory-built houses and apartments a year by 2025. As part of the recruitment drive, Weaver is set to focus heavily on ensuring that the company hires people from demographics that are currently underrepresented in the construction industry.
Lucy Weaver, Group HR Director at TopHat, said: “It brings me great pleasure to have joined TopHat during such an exciting period for the business. I’ve been incredibly impressed with what TopHat has achieved in such a short amount of time. The company is continuing to deliver high-quality, highly efficient homes across the country and I look forward to supporting the growth of TopHat over the coming years.” According to the Construction Industry Training Board, the sector will need over 216,000 new workers by 2025 to meet growing demand. To help tackle this problem, TopHat will offer a range of opportunities and shift patterns for new joiners from all socio-economic backgrounds – including part time and flexible roles. Internal learning platforms to enable skills development across a range of construction and manufacturing profiles - including lean, digital, engineering and construction – will also be developed. Women still make up only 11% of the UK’s construction workforce. By 2023, TopHat aims for women to account for 40% of its workforce, making it the top-rated construction firm for gender balance.
Jordan Rosenhaus, Chief Executive at TopHat, added: “Lucy’s appointment comes at a time when we’re really accelerating the growth of the business as we continue to increase our pipeline of developments across the UK. As we look to progress with a longterm strategic vision of growth, TopHat will benefit from Lucy’s industry and commercial experience that will help us to continue revolutionising housing delivery across the UK.”
Bellsmyre Regeneration Sees First Tenants
The major regeneration scheme at Bellsmyre, Dumbarton is taking shape with four families moving into their new homes and the council giving the green light for the next phase of the major scheme, partfunded by the Scottish Government, to improve the housing provision in the area.
The first tenants have been handed keys to their new homes at Muir Road, for Caledonia Housing Association. A further 62 homes will be completed by May this year providing much needed, high quality and affordable housing for the area. The brownfield site along Muir Road is the first phase of Caledonia Housing Association’s regeneration for Bellsmyre. The new development is designed by ECD Architects and constructed by CCG (Scotland). The new homes constructed at Muir Road will be a mix of houses and flats with one, two and three bedrooms to cater for a wide range of families and individuals. There will be a further 40 two and three-bedroom houses, and 22 one and two-bedroom flats.
Construction at Muir Road used modular offsite building methods allowing for enhanced levels of performance and quality for the newbuild construction. It also limits the need for heavy machinery on site and reduces work force traffic resulting in less disruption for tenants moving in and for the community nearby. All the homes at Muir Road are finished in a grey multi-tone textured brick, with contemporary grey window frames. When complete Muir Road development will include areas of open space with a dedicated area with children’s natural play equipment, benches and landscaping.
Andrew Kilpatrick, Director of Assets, said: “Creating new homes at Muir Road is a real milestone and we will be handing over keys for the much-needed affordable housing, from now until the development is completed in the early Summer. Many of the new tenants moving in have been in alternative decant accommodation for two years, whilst they waited for the development to be completed. We are so pleased we can now welcome them to a high-quality new home.”
Dilveer Kaur Hoonjan, the lead Project Architect, ECD Architects, commented: “It’s great to see tenants now moving into their homes at Muir Road. We are delighted to receive planning approval with the positive feedback we have received from the community and West Dunbartonshire Council for this project for Caledonia Housing Association. We look forward to seeing the project progress over the coming months.”
The planning permission approval is to build a further 140 new homes and improve community amenities in Bellsmyre, Dumbarton. The ambitious plans for the £40million regeneration including new homes to replace many of the original tenements. Complete, the development is set to be one of the most energyefficient of its kind in West Dunbartonshire with varying standards of build, including operational net zero carbon and the Passivhaus standard.
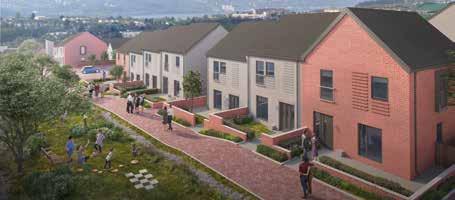
Source: www.c-c-g.co.uk
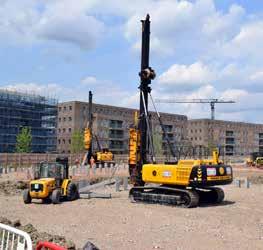
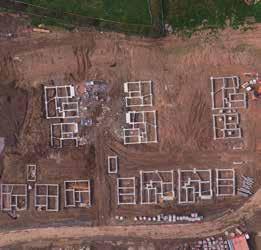
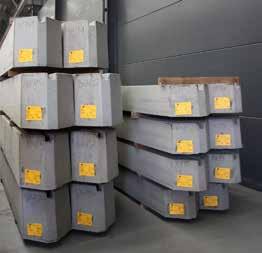

OFFSITE MANUFACTURED FOUNDATIONS:
DESIGNED
MANUFACTURED
INSTALLED
www.roger-bullivant.co.uk 0845 838 1801 info@roger-bullivant.co.uk
Housing Pattern Books Will Transform Affordable Homes Delivery
Advanced Industrialised Methods for the Construction of Homes (AIMCH), the three-year project to support the sector to tackle the UK housing crisis, has arrived at an answer to the UK’s chronic housing shortage. Following 18 months of intense collaboration and research, AIMCH partners Stewart Milne Group (SMG) and L&Q have developed housing blueprints for developers, housing associations and SMEs to bring affordable homes to market quickly and cost effectively.
The affordable housing pattern books, featuring 24 designs, have been created to facilitate the construction of cottage flats, bungalows, semidetached and terraced houses, all of which offer the flexibility to meet planners needs, and to fit in with local character. Designs from the pattern book can also be pieced together to accommodate a range of elevations and streetscapes.
A central element of the type approved housing collections is their use of closed panel MMC timber technology, optimised to meet 55% PMV (Premanufactured Value), a requirement of Homes England grant funding. Their 0.20 U-Value provides a fit-and-forget, fabric first approach to energy efficient building envelope, set to comply with new June 2022 Part L building regulations.
In creating the pattern books, the developers have leveraged learnings from Design for Manufacture and Assembly (DFMA), Design Standardisation and Product Families (Kit of Parts) and BIM (3D modelling) outputs. AIMCH developers plan to exploit the standard house type pattern books on their own sites, or through strategic partnerships with other developers and clients.
Stewart Dalgarno, Director of Innovation and Sustainability at Stewart Milne Group, and AIMCH Project Director said: “Typically, in the affordable homes sector, design and housing procurement are done on an isolated project-by-project basis, which potentially leads to higher costs, inefficiencies and variability in quality. Because of this, AIMCH sees enormous potential for accelerated use of pattern books in the sector. Furthermore, through endorsement from regulators, funders, and insurers, AIMCH believes that housing pattern books and standardised products will become commonplace in the affordable housing sector.”
Wayne Hill, Production Strategy Director at L&Q added: “L&Q is proud to be leading the way in the adoption of offsite technologies in the affordable housing sector. These developed approaches offer a clear way for housebuilders, housing associations and local authorities to adopt MMC methods, and the efficiencies which come with them, to build homes for those who need them the most.”
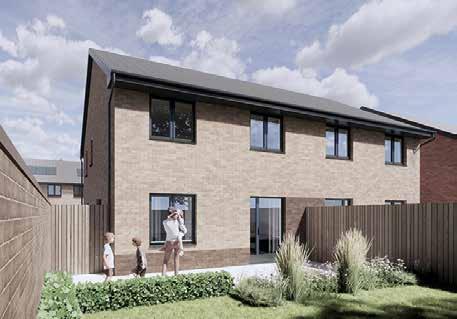
Source: www.aimch.co.uk
Top Five Housebuilder Bellway Goes Modular
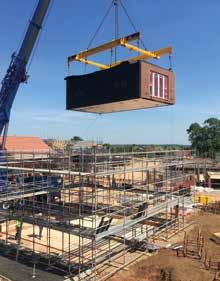
Leading modular housing company ilke Homes has been selected by top five housebuilder Bellway to deliver the FTSE 250 company’s first modular homes. The partnership will see ilke Homes deliver 40 factory-built homes on a site in Milton Keynes. Branded Tattenhoe Park, the wider scheme will comprise 160 homes built from steel and timber framed homes as part of a pilot project being led by Homes England.
Homes England’s pilot projects are delivering 1,800 homes across the country as part of a study into the benefits of MMC. These include improved quality and energy efficiency, and a reduction in construction waste. A recent report from the House of Lords’ Built Environment Committee suggested factorybuilt housing will be instrumental in speeding up development across the UK.
It is the first time ilke Homes and Bellway have partnered to deliver homes in the UK, with the modular housing pioneer already having signed several other deals with some of the country’s biggest house builders. ilke Homes will be delivering a mix of two, three and four-bedroom homes for Bellway, for both affordable and open market tenures. Tom Heathcote, Executive Director of Development at ilke Homes, said: “Proof of both concept and delivery means that ilke Homes has become a partner of choice for the UK’s biggest house builders. It’s great to partner with Bellway Homes at Tattenhoe Park, a truly innovative, Homes England-backed scheme that is aiming to demonstrate the benefits of MMC by collecting granular data on the performance of our own precision-engineered homes.”
Paul Smits, Managing Director at Bellway Northern Home Counties, added: “Bellway is pleased to confirm this partnership with ilke Homes to deliver our first modular homes at Tattenhoe Park. We have developed our plans with ilke’s input throughout, and their expertise has accelerated our learning around their products and processes. Now contracts are signed, we look forward to seeing these new homes being manufactured by ilke Homes and preparing to install the units at Tattenhoe Park.” Bellway is due to start work on site in March, with ilke Homes expected to deliver the first homes in August.
Source: www.bellway.co.uk www.ilkehomes.co.uk
Surrey Low Carbon School Celebrates Modular Milestone
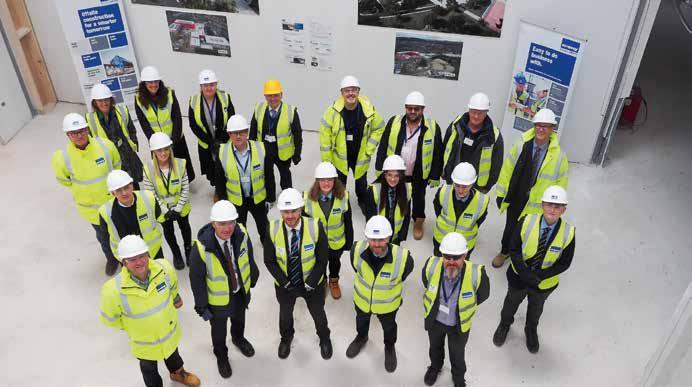
A significant milestone in one of the DfE's ‘Low Carbon Pathfinder' projects has been reached with an end-of-module-installation ceremony taking place at Merstham Park School, near Reigate in Surrey.
The ceremony was attended by representatives from DfE – including Paul Mustow, Divisional Director for DfE – GLF Schools and the project’s principal contractor, McAvoy. With final fit-out and site works now underway, the multi-million-pound school that will provide learning space for around 900 pupils is scheduled for final handover in time for the new academic year in September. The new two and threestorey building will replace the school’s temporary facilities that have been in use since the school's opening in 2018 and will provide pupils with highquality classrooms, play space, a dance studio, an all-weather sports pitch, and a sports’ hall.
The ‘Low Carbon Pathfinder' school for pupils aged 11-16 seeks to minimise energy usage by implementing the ‘Be Lean, Be Clean, Be Green' energy hierarchy which focuses on reducing the demand for energy at source through passive measures before considering efficient systems and renewable technology. The building will run mainly on electricity and will feature roof-mounted solar panels. The biophilic design approach encourages pupils and staff to engage with nature, trees will be positioned around sun boundaries to create an inviting environment and assist with cooling.
All the school accommodation, apart from a new sports hall, has been manufactured in a factorycontrolled environment at McAvoy's state of the art facilities. Over the course of six weeks McAvoy's expert team craned 178 modules into place. Its onsite team will now carry out final ground works and fit-out in advance of official handover later in the year.
McAvoy's Contracts Director, Martin O'Neill said the adoption of offsite construction, as opposed to more traditional build methods, had major advantages for the DfE, school and its local community. “In this instance, by choosing an offsite solution the Department was able to commit to delivering a high quality, low carbon school within a much shorter time frame than would have been the case otherwise. In addition, with much of the school structure being manufactured offsite, both the schools' pupils who are studying in temporary accommodation and the local community will be exposed to significantly less site traffic movements and disruption. We are delighted with the progress so far and we are looking forward to seeing the pupils being able to enjoy their new school having been in fully temporary accommodation for more than two years."
Ron Clarke, Chief Executive Officer at McAvoy, said: “This will be an exceptional school building that will meet extremely high environmental standards. We are honoured to have been selected by DfE to drive forward its commitment to low carbon schools within the context of this Pathfinder Project.”
Allan Thomson, Project Director at DfE added: “I am delighted that we have reached this significant milestone. It is testament to the hard work and collaborative approach adopted by everyone involved, from the DfE project team and our technical advisors (MACE) to the McAvoy team and of course the GLF Trust who will be the ultimate end-user of what will be a wonderful teaching and learning environment that will benefit not only the staff and pupils but also the wider community for years to come."
Jon Chaloner, CEO of GLF Schools is delighted that the new building has been built to high environmental standards championing the DfE's long-term commitment to low carbon schools, saying: “It has been a pleasure to watch the build grow and develop and the highlight has been to finally tour the site and understand how it will look this summer when it's finished. With its state-of-the-art facilities, this new build will create wonderful opportunities for our students at Merstham Park and our other local GLF schools, Lime Tree and Merstham Primary who will be able to share, along with the wider community.”
McAvoy Group is also finalising installation work at Porton Science Park where a new two-storey, 3,716sqm building will provide SME research companies, including ‘start ups’, with opportunities for collaborative working, utilising a mixture of serviced labs, office facilities, conference and meeting rooms. The new facility will sit adjacent to Porton Down – home to Public Health England and the Ministry of Defence Science and Technology Laboratory. The building is scheduled to be ready for use in Summer 2022.
Source: www.mcavoygroup.com
Final Modules for King’s College Hospital
Premier Modular, has installed the final modules for a new 3,450sq m outpatient services building at King’s College Hospital in London, achieving a major milestone in the build programme. The £21million contract is Premier’s largest single offsite healthcare project in its 65-year history, which is being delivered with its construction partner Claritas.
133 steel-framed modules weighing up to 11.5 tonnes each have now been installed using a 500-tonne crane in a complex operation. This involved careful logistics planning to maintain access through the hospital campus at all times, and to co-ordinate cranage to avoid any disruption to the helipad and air ambulance helicopters. The site is highly constrained with roads to three sides and is immediately adjacent to another hospital building.
When finished later this year, the building will provide 48 consulting rooms and eight procedure rooms for a range of outpatient services, including dermatology, rheumatology, neurosciences, as well as other aspects of surgery and therapy. Commenting on the completion of the building installation phase, Jon Wardle, Chief Executive of Claritas, said: “The whole project team, the Trust and our delivery partners have done a tremendous job of installing this large-scale building on an incredibly constrained site at the heart of this major hospital. Everyone involved worked hard to ensure the installation phase was completed as smoothly as possible.”
All the modules have now been installed and connected. Stage two of the construction programme will involve final fitting out and completion of the external façade, including a feature entrance with double height glazing to provide high levels of natural light for the reception and waiting area. The project was procured through the Crown Commercial Service framework and is designed by P+HS Architects. The M&E specialists are TClarke.
Dan Allison, Divisional Director at Premier Modular, said: “When you have a hospital site as restricted as this one, it is easy to see how offsite construction really comes into its own. We are reducing the amount of plant, materials, and vehicle movements to site by moving as much work offsite as we can. And by constructing the building structure in the factory while the foundations were progressed on site, these new hospital facilities will be brought into use at an earlier stage, to the benefit of patient care.”
Bespoke building solutions can be developed for highly constrained hospital sites and are manufactured with zero waste to landfill. Existing facilities can also be expanded easily, safely and cost effectively, both vertically and horizontally.
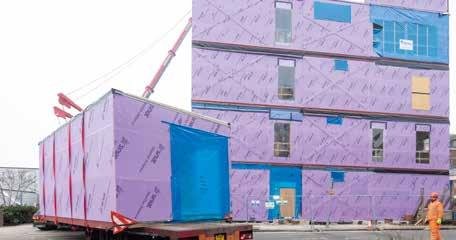
Source: www.premiermodular.co.uk
Setting the standards for offsite fastening
BeA your partner for offsite timber and light gauge steel frame construction
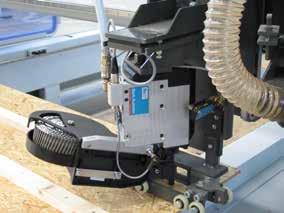
Across Europe and worldwide, BeA’s fastening technology, tools and consumables are the trusted choice for some of the biggest and best known names in offsite timber and light gauge steel frame manufacturing. BeA manufacture an extensive range of market leading choice of fasteners, nails, staples and tools. We offer customers: • An unrivalled range of manual, semi-automatic and fully automated fastening solutions. • Using industry leading quality controls, BeA meet or exceed standards such as Eurocode 5.
Reliable products, competitive prices and the kind of service and delivery you can depend on from BeA.
01482 889 911 sales@uk.bea-group.com visit our website www.bea-group.uk
Trimble Announces Latest Version of Tekla® BIM Software
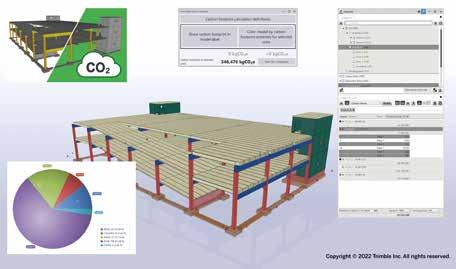
Tekla's latest software automates workflows and ensures communication between project participants at all stages. Tekla Structures and Tekla Structural Designer, which are based on Trimble's workflow streamlining technologies, now offer a dynamic embodied-carbon calculation function for design and drill-down processes using the Embodied Carbon Calculator. This visual and dynamic calculation tool allows users to assess the environmental impact of their design decisions directly quickly and accurately in Tekla software.
Design engineers can use the calculator to compare different design options and their associated carbon loads. Environmental professionals on project teams can also use the specially designed OneClick LCA carbon dioxide emission calculator integrated into the Tekla system to produce environmental product declarations (EPDs). Combining ordered Tekla software data with One Click LCA data and the extensive EPD database allows you to calculate the embodied carbon emissions for the materials used in production, down to each nut, bolt and rebar throughout the entire lifecycle.
The 2022 version of Tekla Structures improves the entire workflow – from design to production – with built-in intelligent functions for creating production drawings, and reduces the time spent creating and editing drawings. To produce concrete parts, the new Tekla Structures system offers reinforcing assemblies. The new feature, used primarily in Manufacturing and Assembly Technology (DfMA), strengthens Tekla's portfolio of tools for automated element manufacturing. Another new feature in Tekla Structures 2022 is the advanced Embodied Carbon Calculator, which allows Tekla Structures users to perform dynamic calculations and visualize the CO2 implications of design decisions.
The Embodied Carbon Calculator, which was already introduced in Tekla Structural Designer in 2021, now offers improved viewing, reporting and sharing of carbon emissions. Using Tekla Structural Designer, design engineers can calculate the embodied carbon in various versions at the design stage, optimising materials for designing structures with low carbon emissions. Information is easily transferred from the software by exporting reports, charts and data.
To improve the interconnection of design and detail processes, Tekla Tedds 2022 software makes it easy to share design information and documentation through the Trimble Connect™ collaboration platform. The latest version also includes new calculations and updates to existing ones for faster and more reliable design of structural elements.
The Tekla PowerFab 2022 steel fabrication management software suite solves common engineering problems, with improved management of layout and materials for joining and splitting elements. Thanks to simplified system implementation, new customers can seamlessly migrate from their current production management information system (MIS) on Tekla PowerFab. This helps to avoid tedious manual work and allows you to confidently use the new system, since data from past projects is automatically saved as needed. The software also improves monitoring and control thanks to the new delivery calendar in the Tekla PowerFab Go web application.
Michael Evans, Senior Commercial Director of the Trimble Group, said: "Tekla software continues to change the way we work in the construction industry. Our solutions organise information about construction and facilitate access to such information for all project participants, which allows us to optimise the cost of materials and the use of human resources. Thanks to continuous improvements and the high intellectual capabilities of the software, as well as the implementation of solutions for the sustainable development of the construction industry, we occupy a leading position in the supply of BIM technology platforms in the modern market.”
Source: www.tekla.com/2022
HE Simm Group Create Pinnacle Offsite

The HE Simm Group – one of the UK’s leading engineering and services businesses – has invested £1million in a new-state-of-the-art 21,000sq ft facility, to build on its ever-expanding order book for MEP prefabricated solutions.
To be known in the marketplace as Pinnacle Offsite, the business, which is being led by Ernie Price, a prefabrication specialist with over 20 years’ experience, has been launched off the back of continued and sustained demand for prefabricated solutions from its UK-wide customers. The facility, based in Walsall in the West Midlands is already working on the production of prefabricated solutions for customers the length and breadth of the country. Solutions include the manufacturing of packaged plant rooms, plant skid modules, MEP lateral and riser modules and prefabricated utility cupboards.
Commenting on the news, Gareth Simm, HE Simm Group’s CEO, said: “This is a major milestone for us. As we have grown, we have seen a distinct rise in demand from our customer base for prefabricated solutions. Our investment in the facility and in the Pinnacle Offsite business overall proves our commitment to this offering, which will enhance what we can provide as a leading MEP player. Ernie is a specialist in this field, and we have no doubt that he will make a real success of it. He will work closely with Greg Simm and Marcus Wallis – Managing Directors of our Engineering business in the North and South respectively, to make sure that our bids always comprise, wherever possible, a prefabricated solution.”
Greg Simm, the Executive member of the Group responsible for Pinnacle Offsite, added: “This really is very exciting. We’re delighted with the investment we’ve made, with the facility that’s already up and running, and with the team we have in place. We’re looking forward to becoming well known in the marketplace for our innovation in this area and to growing it over the coming years.”
Timber Development UK Release 2022 Market Statement
Willmott Dixon Look to Offsite in Northminster
Following an extraordinary year for the timber industry, Timber Development UK (TDUK) has released a market statement to provide greater clarity on the current supply and demand situation. The market statement provides a detailed analysis of the past year, looking at the import and price statistics of 2021, as well as how recent events will impact inflationary trends in 2022.
One key takeaway from the statement is that the timber supply chain is resilient with 2021 proving to be a record year for imports despite significant disruptions to the market. Import volumes in 2021 reached nearly 11.7 million m3 – a 15% increase on 2020. This is the largest volume of imports seen in the UK since 2008, reflecting strong demand for timber products.
With another year of significant disruption highly likely due to the invasion of Ukraine and economic sanctions against Russia and Belarus, communication across the supply chain will remain vital. The report considers how the invasion will influence supply, demand and price, and recent market trends, with consideration given to construction forecasts for 2022.
Nick Boulton, Timber Development UK head of technical and trade policy, said: “This market statement provides clarity on what was a truly remarkable year for our industry, as well as what we can expect in 2022.
A landmark £65million high-quality housing and commercial space complex, which is being delivered by national contractor Willmott Dixon on behalf of Peterborough Investment Partnership (PIP), has officially started on-site with a ground-breaking ceremony attended by city leaders.
The new Northminster development will boast 315 units consisting of one, two and three-bedroom apartments, and 37 townhouses. The two ground floor units present leisure and hospitality commercial space opportunities, and residents will also benefit from improved public space at nearby Laxton Square.
Using innovative construction methods to build better, greener and smarter, Willmott Dixon plans to make efficiency savings through pre-manufactured value, which it forecasts will contribute to 63% of the project value. Offsite elements will include a light gauge steel frame, brick slips and the use of bathroom pods, which will help to ensure quality, programme certainty and come with environmental benefits. Reflecting on 2021, for the first time in my memory we saw timber nearly cleared off the shelves of all merchants.
“I would like to say that we are moving back towards normality in 2022, however, the supply situation remains particularly tricky given continuing labour shortages and high fuel costs. Recent weeks have also seen the awful illegal invasion of Ukraine by Russia which is likely to exacerbate existing supply and price pressures. Yet against this backdrop, timber will continue to play a pivotal role in 2022 as the UK looks to build back better, safer, and greener while achieving net-zero targets. As the only mainstream low carbon construction product, timber will be central in our bid to reduce construction emissions.”
Due to be finished in August 2024, the development, which is, in part, being funded by a £14million grant from Cambridgeshire and Peterborough Combined Authority, will provide much needed high-quality and affordable housing. All homes will be let at discounted rents, set at or below 80% of the normal market rate.
David McCallion, Director at Willmott Dixon, said: “We are proud to be delivering this fantastic ten-storey flagship Northminster development in collaboration with PIP, providing affordable housing stock and valuable commercial spaces to further attract investment into the area. This is such an important regeneration project for Northminster and we are looking forward to working alongside our delivery partners to revitalise the area for residents and the wider community.” All readers should note that both PEFC and FSC have reclassified goods from Russia and Belarus as ‘conflict timber’. Any goods which had due diligence applied AFTER 2 March 2022 should be considered ‘conflict timber’ and ineligible for PEFC certification and trade. For FSC any goods which were shipped and placed on the market AFTER 8 April 2022 should be considered ‘conflict timber’ and ineligible for FSC certification and trade.
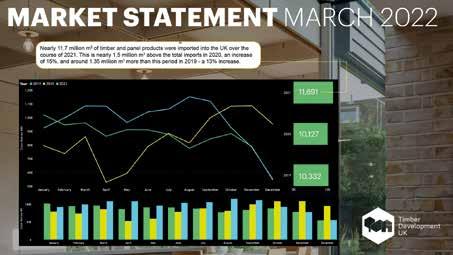
Source: www.ttf.co.uk www.pefc.org www.fsc.org
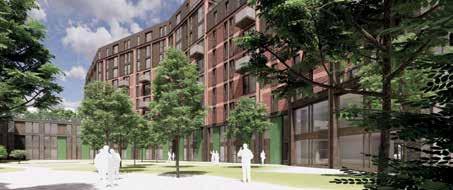
Peter Hiller, Board Member at Peterborough Investment Partnership, added: “This is an exciting day for the city and the beginning of a new era for Northminster. When finished, residents will be able to look out from beautiful apartments and see the spires of Peterborough City Cathedral on their doorstep. They’ll be a short walk from our train station, with great links to the north and south, and an even shorter walk to the excellent bars, shops and restaurants in the city centre.” Willmott Dixon is working alongside project architect Corstorphine & Wright – a partnership that has been successful on several projects across the UK.
Source: www.willmottdixon.co.uk
DESIGNING IN CHANGE
Late last year, the Construction Innovation Hub’s Platform Programme published the findings from a series of workshops and development activity. Trudi Sully, Impact Director at the Hub outlines what to expect, with the first draft of the Product Platform Rulebook soon to be published.
1
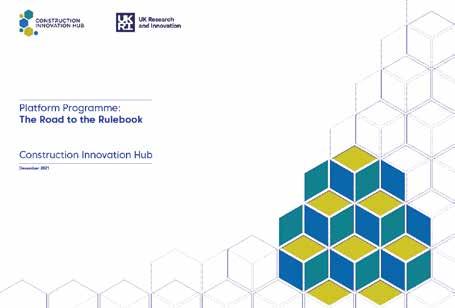
At the end of last year, the Construction Innovation Hub’s Platform Programme published ‘The Road to the Rulebook’. Summarising feedback received via extensive stakeholder consultation, this document provided
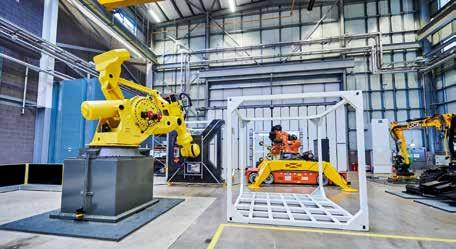
2
both an introduction to the concept of platform-based approaches in construction as well outlining a framework, guiding readers as to how to develop and deploy product platforms to meet an aggregated demand. The creation and release of this ‘Product Platform Development Framework’ is one of several key steps guiding the industry to develop and apply product platforms in the manner driven by government, through policy such as the Construction Playbook and Transforming Infrastructure Performance Roadmap to 2030.
Hot on its heels, the Hub are very soon to release the initial draft of the Product Platform Rulebook for consultation. This Rulebook of open access guidance, key processes and approaches, will be the blueprint for developing and implementing product platforms for current and future market players, with built-in mechanisms for continuous improvement and future opportunities for harmonisation and rationalisation as capability and capacity grows. It is intended to address directly:
• Why: Why do we need a platform approach to construction, what outcomes are we trying to drive and how is policy driving the emergence of product platforms?
• What: What are product platforms, what are their defining features and what are the rules that govern whether something can be deemed a product platform?
• How: Guidance on how to develop a product platform, the key decisions that need to be taken and the key outputs required to demonstrate compliance and to support their deployment on construction projects
Most of the Hub team driving the Rulebook development come from organisations in a competitive market, truly demonstrating the power of
collaboration and the commitment of these organisations to work together to overcome common industry challenges for the benefit of all. Furthermore, the Rulebook will be brought to life through relatable and relevant case studies, with contributions from proof of concepts and flagship projects and solutions, such as SEISMIC, Bryden Wood’s Platform II, the Department for Education’s Gen Zero, and ProCure’s Repeatable Rooms.
However, input does not stop there. The early consultations involved 120 different organisations, from government departments, to consultants, contractors, manufacturers and throughout the supply chain. Once the draft is released next month, another round of consultation will be held to enable further refinement and development with the first edition release scheduled for late summer.
There is recognition that the Rulebook will need to remain a live document, sitting with an impartial custodian, that will coordinate ongoing development by industry contributors as more product platforms are developed and deployed.
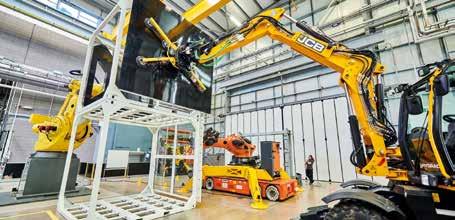
Ultimately the Rulebook is designed to support government departments in implementing policy set out in the Construction Playbook and TIP Roadmap - building a strong aggregated pipeline of programmes on which product platforms can be deployed via a disaggregated supply chain - whilst enabling industry to confidently build their capability and capacity in response to the demand going forward.
We can’t wait to share all the hard work when the first, beta edition of the Rulebook lands and hope this marks the beginning of a live and agile resource which can support the rapid emergence of, and continuous improvement in, construction product platforms for generations to come.
To find out more about the Construction Innovation Hub Platform Programme visit: www.constructioninnovationhub.org. uk/platform-programme/
Images:
01. The Rulebook will help boost the manufacturing process as a central aspect of product specification and reliability 02-03. Factory precision is the future of a more productive construction industry
3
WHAT ARE PRODUCT PLATFORMS?
The term Platform is widely used but consistently includes: • A set of low variety core assets (i.e. components, processes, knowledge, people and relationships) • A complementary set of peripheral components that exhibit high variety • Stable interfaces that act as a bridge between the stable core and variable peripherals. (Source – Network Plus digest)
A Product Platform includes a kit-of-parts, associated production processes, and the knowledge, people and relationships required to deliver all or part of construction projects using a platform approach.
A Platform approach provides the mechanisms to improve productivity whilst ensuring high standards of quality and performance, thus enabling better, faster, greener delivery of our infrastructure needs. The approach encourages innovation and enables market evolution.
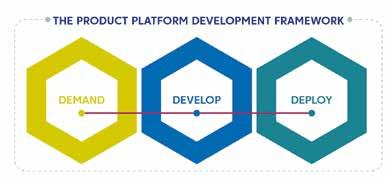
DEMAND DEVELOP DEPLOY
Demand: The use of product platforms requires an aggregated demand, which is supported by harmonisation and rationalisation of design requirements across a range of asset types and client organisations. This is done away from the project environment and needs to provide confidence to the supply chain that the solutions they develop will have a market.
Develop: How to respond to an aggregated market demand through the development of a particular product platform which can be deployed across multiple projects and programmes.
Deploy: Approaches for incorporating one or more product platforms in the delivery of a specific project or programme. Shifting, where possible, from design and construction to configuration and assembly.
NEW BRAND: NEW VISION
Elliott and its affiliated UK companies have a new face, new name and are looking towards an exciting future ahead as they unite under the common brand name of Algeco.
The move creates a single, consistent brand across the UK and Europe, to reflect the Group’s position as a global industry leader. Algeco is a longestablished brand in the European modular services and infrastructure industry, originally formed in 1955 providing a strong basis for the single identity, which will facilitate growth in its brand equity and allow greater synergies to be achieved within the Modulaire group. Customers can expect to see a stronger, combined UK organisation as well as more sharing of innovations and resources within the group, and a unified product range available throughout the UK.
“Algeco, is part of the Modulaire Group, Europe and Asia Pacific’s leading specialist in modular services and infrastructure,” says John Campbell, UK Managing Director, Algeco. “It introduced the first stackable modular accommodation in 1965. Throughout the 70s, 80s, and 90s, the brand developed a stream of further innovations that expanded its high-quality modular accommodation from construction into education, health and commercial sectors.
“We have been planning the rebrand to Algeco for some time and it coincides with sustained growth in our UK businesses. At the same time there is unprecedented change happening in the way that physical spaces are created in a wide range of vertical markets, driven by climate change, safety and growing user expectations. Adopting a single brand in the UK will create a common sense of identity and purpose for the newly combined UK business.
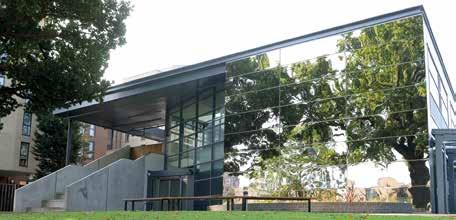
Integrated product ranges within a single, unified brand
“This rebrand is more than a change of identity. Incorporating three separate brands into one UK entity has also meant business integration. A key element involves aligning the product lines and product architecture to further strengthen our overall offering.
“Elliott Group, Carter Accommodation and Procomm Site Services, are well respected businesses in the markets they serve, and all have strong product line brand names that complement our offer. The Elliott Moduflex system is well established in the site accommodation market. Carter is a leading player in the temporary accommodation hire business with a modern and well-invested fleet. It is well known for its Containex product, which offers quality modular site accommodation. Procomm is a large customer of Carter, which provides obvious synergies. The combined UK business will be headquartered in Peterborough, Cambridgeshire with a total of 23 site locations throughout the country servicing its portable, modular building and offsite construction hire and sales activities.”
1
What does the Algeco brand mean to customers?
“The new brand represents our collaborative approach to finding solutions for customers, developing both our products and our people to deliver leading quality service and ensuring the futures of customers, their end users and our organisation are sustainable. The rebrand is a major milestone for the UK business and comes at a time when post-COVID government stimulus programmes, aging building stock and a structural shift towards modular space are driving demand.
“We want to be trusted solutions advisers to the markets we support. By doing that, our goal is to be clear market leader in modular and temporary accommodation. The rebrand will be a journey that opens up opportunities for UK customers as we begin to share ideas and resources. It will see an acceleration of new product development, and we already have some exciting innovations in the pipeline. If you were to summarise the brand it would be that together, we develop sustainable futures.”
A new Algeco website is scheduled to go live at the end of March 2022 when the rebranding process is complete.
For more information visit:
www.modulairegroup.com www.algeco.be/en
Images:
01. Customers can expect to see a stronger, combined organisation and a unified product range available throughout the UK
