
9 minute read
Can Volumetric Deliver a Net Zero Future?
CAN VOLUMETRIC MANUFACTURED BUILDINGS DELIVER A NET ZERO FUTURE?
Is the road to a net zero future a well mapped out route or is there uncertainty along the way? Richard Hipkiss, Development Director of the Modular and Portable Building Association (MPBA) makes the case for volumetric buildings shaping a more sustainable future.
Since the government amended the Climate Change Act in 2019 to commit the UK to achieving net zero carbon emissions by 2050, the construction industry has been confronted with the need to decarbonise.
According to the World Green Building Council, construction and buildings in use are responsible for 39% of all carbon emissions in the world. This is broken down into two elements with 11% being linked to the manufacture of materials and construction processes known as ‘embodied carbon’ emissions and 28% associated with ‘operational emissions’ caused by heating, cooling and lighting systems when a building is in use.
The challenge is therefore two-fold. Whilst there has been a drive to reduce operational emissions through the implementation of government legislation such as the changes to Part L of Building Regulations to improve the building fabric – little has been done to address the carbon inefficiencies in the construction process. It is now established that volumetric modular approaches are a game changer for the construction industry – reducing build times whilst increasing quality, productivity and safety. But what is not so widely understood is that compared to traditionally built projects it is much easier to control energy use in factory settings than in an open construction site. On average 67% less energy is required to produce a volumetric manufactured building and up to 50% less time is spent onsite, resulting in up to 90% fewer vehicle movements which again reduces carbon emissions.
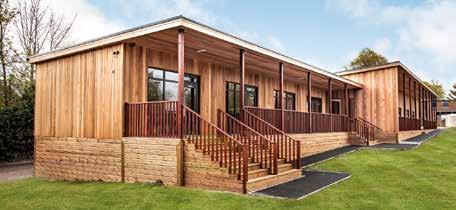
Volumetric manufactured buildings are digitally designed and virtually tested before they move onto the manufacturing phase. This process eliminates waste and achieves highly accurate and airtight building envelopes designed and built to higher sustainability requirements. Unlike factory manufactured buildings, there is significant evidence that traditional construction methods do not produce buildings that perform as well as design expectations and there is a void between anticipated and actual in-use performance. Findings from studies such as PROBE (Post Occupancy Review of Buildings and their Engineering) reveal that actual energy consumption in buildings is often as much as twice of that predicted in the design.
1 2
Not only is the actual construction of the building ‘greener’ but volumetric manufactured buildings are also more energy efficient – reducing primary energy requirements and in-use operational emissions during the lifetime of the building. As the construction sector develops to meet changing government strategies, I firmly believe the upward trajectory of volumetric modular buildings will continue as the benefits begin in the factory, continue to the construction site and last through the lifetime of the building.
For more information visit:
www.mpba.biz
Images:
01-02. All volumetric modular buildings from TG Escapes are net zero in operation. The use of timber and biophilic principles delivers spaces which enhance learning outcomes and support well-being
MODULAR METHODS REALLY DO MATTER
The Modular Matters conference and exhibition returned for its fourth year as a two-day event on 15 & 16 February 2022 at the National Conference Centre (NCC), Birmingham. What went on and what were the key messages?

Modular technology is ever evolving and to help keep pace with this fastmoving sector, the Modular Matters event demonstrated how to tackle industry challenges through a range of project case studies, and expert insight into the future of construction. These events represent a great opportunity to gain industry intelligence and network with those who are at the forefront of the volumetric modular sector.
On day one – Tuesday 15 February – delegates heard in expert detail how volumetric modular technology is being used across a range of vertical construction markets including commercial, education and healthcare. Day two – Wednesday 16 February – focused on housing projects including private residential, build to rent and affordable housing: collectively creating huge interest in offsite technology. Across both days a range of issues were raised and discussed with carbon reduction probably top of the agenda.
Carbon Reduction Must Happen
Peter Rankin, Head of Energy and Environmental Standards (Building Regulations) for the Department for Levelling Up, Housing & Communities, delivered his keynote presentation: “Our journey towards net zero – what it means for the offsite sector” at the start of day one. With building regulations updating in June, he gave an indication on what to expect in the drive to create more energy efficient homes and how the new regulations will help move the country to meet its net zero targets. New regulations will include a 30% carbon reduction for newbuild homes from current standards, with other new buildings, including offices and shops, expected to reduce by 27%.
Following Peter, Richard Hipkiss from the Modular and Portable Building Association (MPBA) highlighted the facts surrounding volumetric design and how a “confused construction supply chain” could be slowing progression, while MPBA and Wernick’s Andy King offered a manufacturers perspective on the complex “lexicon of carbon”, building lifecycles and the pressing needs to act in a more circular fashion – when consultants request embodied carbon figures do they all know what they are asking for? Can volumetric modular be benchmarked for embodied carbon in the same way as traditional building materials?
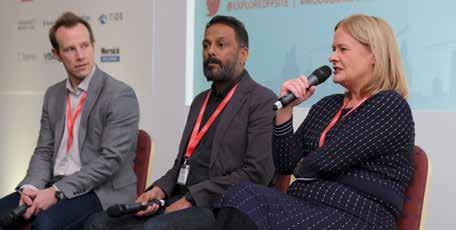
The next session showcased some award-winning projects including Dinton Activity Centre with HLM Architect’s Alex Pullins. Paul Ruddick, Chairman, Reds10 outlined the company’s work on the Imperial War Museums’ new London staff hub. Paul discussed how the project pushed design to a higher level and truly showed the quality that can be achieved when architecture is embedded in the modular construction process from the start.
The afternoon session opened with Scott Tacchi, Head of MMC for the Department for Education who delivered his keynote presentation: “DfE MMC – Following 6 years of MMC School delivery the observations are….” which looked in detail at the DfE’s MMC delivery for its school’s programmes. He also gave some context to the rollout of the MMC1 Framework and offered some observations for the future including DfE ambitions to develop standardised
solutions for secondary and SEN schools and the central hosting of a digital twin with cradle to grave data management.
Delegates then heard several case studies including: ‘The Valentine’ a student accommodation building on Gant’s Hill which was presented by Richard Foxley from HTA Design. Andrew Tindale from Hawkins\ Brown and Simon Elliott from Premier Modular co-presented their collaboration on TEDI-London and Emily King, Divisional Director, Spatial Initiative, discussed New Horizons and Southwest Exeter New School – “two examples of a standardised approach with bespoke outcomes.”
Closing day one, Robert Townsend of Wernick Group looked at how healthcare facilities are benefiting from standardised modular design whilst Dean Hill from Thurston Group delivered a case study on their extension for Tameside General Hospital which was delivered in record time to help fulfil patient numbers during the COVID-19 crisis.
Technology, Design & Delivery
Opening day two, a sold-out audience heard from Giles Carter, CEO of ilke Homes, that have quickly become a core business in the modular homes sector and are committed to delivering net zero targets with the ilke Zero and new Zero Bills homes. “It’s an amazing time to be in modular and in low carbon housing,” said Giles. The Zero Bills home come with a combination of three sustainable technologies – solar panels, new battery design for power efficiency and an air source heat pump – to add to a premium fabric first approach.
Another exciting central player in the modular homes market is ‘tech-driven’ TopHat. CEO Matt Evans explained their vision and how its White Road project is a blueprint for housing, with the modular approach and advanced manufacturing are fundamentally changing the way homes are built. “Everyone working on our homes has a task they can master and get better at,” said Matt. This road to quality, reliability and repeatability will ultimately improve growth and productivity. Victoria Moore, Business Development Manager, Volumetric Modular, offered a different dimension to the housing sector, with its response to the homelessness crisis with MODULHAUS™. Designed and developed by VOLUMETRIC™, Victoria gave an overview of the award-winning concept. In partnership with Hill Group, it is providing turnkey solutions to help house some of the 274,000 homeless people in England alone. Using lean manufacturing and DfMA techniques, it provides a safe place to stay but importantly, it offers a ‘key to the door’. Meaning the chance to ‘own’ an address, open a bank account, find a job and be independent.
Following a social/affordable housing themed morning, the programme then turned to focus on build-to-rent projects including Greenford Quay – the UK’s largest purpose designed rental community. Greystar’s Design Director, Neal Shah outlined how the mixed-use scheme used advanced design to produce repeatable rooms and typologies, and highlighted the collaboration required between client, developer, design team, contractor and manufacturer.
Michael Swiszczowski, Director at Chapman Taylor, explained why modular construction is perfect for build-to-rent by showcasing their collaboration with leading global offsite manufacturer CIMC. Chapman Taylor has designed multi-family apartment layouts for CIMC’s patented modular system, which is capable of quickly and flexibly delivering one, two and three-bedroom apartments in an innovative residential format for the UK market.
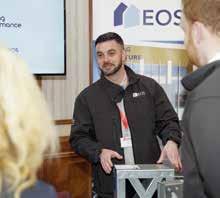
L&G Modular Homes are now delivering several high-specification projects. CEO Rosie Toogood gave the delegates an insight into the modular approach they have taken at Waddington Walk, Bristol, and how the modular scheme is helping Bristol on its journey to be carbon positive by 2030. “I’m convinced that modular will change the housing market,” said Rosie.
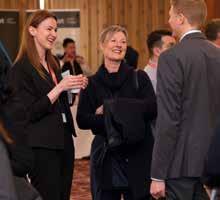
In the final session, Wayne Yeomans from M-AR Offsite looked back at their modular town house project at Wigan Pier, whilst Andy Cornaby, Managing Director of ModPods International, showcased their Broadlands Housing, Webster Court Project. Both explained their approaches to maximising the potential of scaling up projects and increasing system pre-manufactured value (PMV) before they leave the factory.
Graeme Culliton, UK Managing Director for BoKlok – the joint venture between Ikea and Skanska – finished the day by explaining how affordability is central to its homes concept. Its partnership with TopHat producing timber-based, single-family homes can deliver the same kind of stunning results that are a ‘normality’ across Scandinavian markets.
Two full and thought-provoking days put into perspective how the modular construction market continues to mature and is starting to be a part of: “breaking the cycle at getting worse at building and redesigning and unlocking different supply chain habits.” As many of the speakers pointed out, much of what is built traditionally and inefficiently now must be replicated by low carbon, resilient and standardised offsite manufacture.