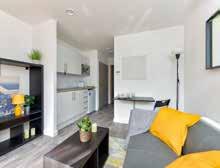
15 minute read
The Adaptable Interim Housing Solution
VOLUMETRIC™ has been working with many sectors to address accommodation needs. From safe and secure living for homeless people to onsite accommodation for keyworkers – MODULHAUS™ can be configured to meet various requirements.
1
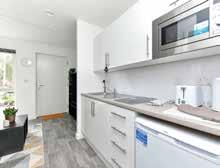
With the financial effects of COVID-19 continuing to pile pressure on those most vulnerable in our communities, and the strain on our healthcare services still evident, concerning figures regarding the UK housing crisis demonstrate why the provision of quality, temporary homes remain a top priority. Designed by VOLUMETRIC™ a specialist manufacturer of rapid build solutions, MODULHAUS™ utilises modern methods of construction to achieve outstanding functional performance and energy efficiency – exceeding Future Homes Standards and delivering net zero accommodation.
Onsite Keyworker Accommodation
Despite the disruption to the economy by the pandemic between 2020 and 2021 UK housing prices increased by 8.5%. This coupled with rising rental and energy costs means that for many keyworkers owning or renting a home is extremely challenging. Recent industry analysis published in ‘The Guardian’ showed that keyworkers on the frontline of the COVID-19 pandemic would not be able to afford to buy, “the average priced home in 98% of Great Britain.”
Not only does this mean home affordability is way beyond the means of many, but research from Citizens Advice shows that fuel poverty is also a major issue with 21% of keyworkers falling behind on their bills and one in five people considered vulnerable in arrears. One of the biggest obstacles currently facing the NHS as outlined in their long-term plan is the gap in workforce numbers as recruitment and retention decreases. Based on current trends, the total shortfall of healthcare staff by 2030 could reach 250,000. Much of this can be attributed to a lack of accommodation in areas of greatest need.
MODULHAUS™ homes offer a viable and cost-effective option for NHS estate managers. Built for adaptability with a 60-year design life, MODULHAUS™ has numerous options for configuration and fit out – making it a highly adaptable asset which can maximise the potential of unused estate space including over car parks. Stackable, interlocking units can create secure onsite keyworker accommodation.
Modular Homeless Solution
housing relies heavily on costly temporary and hostel accommodation, creating a system whereby longterm housing issues remain unaddressed. Leaving many trapped in a cyclic system of permanent instability, limiting the possibility for rehabilitation, employment, and reintegration. Adaptable, interim housing must be the answer. For those affected by homelessness, MODULHAUS™ promotes a pathway back to independence. The solution offers greater dignity whilst relieving the burden on Local Authorities and Councils of ongoing expenses associated with traditional temporary accommodation.
2
MODULHAUS™ is super energy efficient, costing circa £5 per week to run – meeting the guidelines outlined by the Future Homes Standard and negating fuel poverty. Addressing the need for efficiency, MODULHAUS™ homes feature low-energy lighting, as well as fixtures designed to minimise water and energy wastage. LABC Assured with a 60-year BOPAS Certified design-life, MODULHAUS™ homes are future-proofed for Building Regulation changes.
Arriving 100% complete ready for simple site connection and commissioning – design features include ergonomic internal fully fitted living space with furnishings, bedrooms, shower-rooms and kitchens complete with white goods – modules are provided on a turnkey basis, fully equipped for immediate occupation. While these benefits have already provided much-needed relief for those experiencing homelessness, MODULHAUS™ homes also have the efficiency, practicality, and adaptability to give a unique opportunity for investment in keyworker housing.
For more information visit:
www.volumetric.co.uk
Images:
01-02. MODULHAUS™ homes are adaptable for a range of ownerships and locations
MAXIMISING OFFSITE INDUSTRY EXPOSURE
Following the unprecedented success of the 2021 event, the Offsite Construction Awards returns later this year and will take place at Offsite Expo 2022 – the UK’s largest offsite technology event in the construction calendar.
Taking centre stage at Offsite Expo on the evening of 20 September 2022, the Offsite Awards will be a major coming together of the industry where over 500 guests will gather to celebrate ground-breaking achievements and the pioneers who are developing radical new offsite technologies, innovative product developments and landmark projects using factory-based methods.
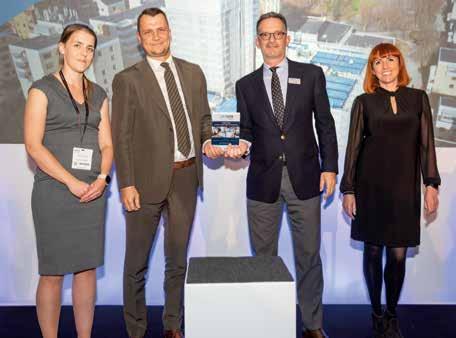
Winner of International Offsite Project - Forta Pro
Entries in to the 2021 Offsite Awards were record breaking with over 200 entries and the profile and coverage gained by all the finalists and winners has helped to propel the sector to another level. This event is the ideal opportunity for construction professional to maximise industry exposure by demonstrating what separates them from their competitors. So, if you are proud of your exceptional team, project development or product innovation, there are just five questions to answer to grasp the opportunity to take centre stage at the 2022 Offsite Construction Awards.
Being shortlisted for the Awards will earn the recognition within the offsite community and the wider construction industry – opening doors to securing new business development opportunities.
The deadline for submissions is 27 May 2022 with the winners being announced on 20 September 2022 at Offsite Expo 2022.
Many of the sponsorship packages have already been snapped up by savvy companies wanting to take advantage of the opportunity to promote their company and maximise industry exposure.
For more information on how to get involved in the Offsite Construction Awards, please contact Rhian Morris on rhian.morris@radar-communications.co.uk
FULL LIST OF OFFSITE CONSTRUCTION AWARDS CATEGORIES FOR 2022 INCLUDE:
BEST USE OF BEST USE OF TIMBER TECHNOLOGYSTEEL TECHNOLOGY
BEST USE OFBEST USE OF VOLUMETRIC HYBRID TECHNOLOGYTECHNOLOGY
BEST USE OF CONCRETE TECHNOLOGY BEST USE OF MEP & POD TECHNOLOGY
EDUCATION PROJECT OF THE YEAR
PRODUCT HEALTHCARE PROJECT INNOVATION AWARD OF THE YEAR
BEST USE OF COMMERCIAL PROJECTRETAIL/LEISURE PROJECT INFRASTRUCTURE
CONCRETE OF THE YEAR OF THE YEAR PROJECT OF THE YEAR
TECHNOLOGY BEST USE OF TIMBER TECHNOLOGY BEST USE OF STEEL TECHNOLOGY BEST USE OF HYBRID TECHNOLOGY BEST USE OF VOLUMETRIC TECHNOLOGY BEST USE OF MEP & POD TECHNOLOGY PRODUCT INNOVATION OF THE YEAR COMMERCIAL PROJECT OF THE YEAR RETAIL/LEISURE PROJECT OF THE YEAR EDUCATION PROJECT OF THE YEAR HEALTHCARE PROJECT OF THE YEAR INFRASTRUCTURE PROJECT OF THE YEAR
2020 2022
20.09.22 CBS ARENA - COVENTRY
Co-located with FFSITE EXP
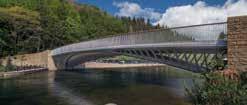
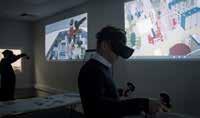

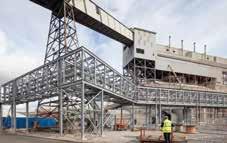
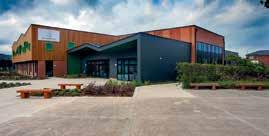
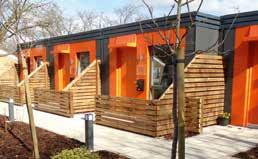
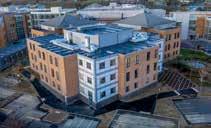

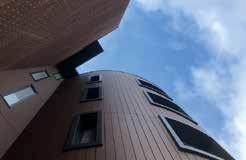
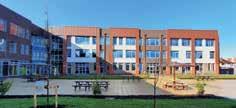
Celebrate the best in precision building design and delivery at the Offsite Construction Awards. The Awards will reward outstanding examples of prefabrication and factory-based methods, products, systems and disciplines that increasingly strive to develop a sustainable, streamlined and cost-effective way to deliver a better built environment.
All 25 categories are free to enter, and the submission deadline is 27.05.2022 – simply visit www.offsiteawards.co.uk to start your submission today.
SOCIAL HOUSING OFFSITE PIONEER PROJECT OF THE YEAROF THE YEAR PRIVATE HOUSING PROJECT OF THE YEAR PRIVATE HOUSING INSTALLER OF THE YEAR INTERNATIONAL OFFSITE PROJECT OF THE YEAR PROJECT/CONSTRUCTION MANAGER OF THE YEAR
PROJECT
OF THE YEAR SOCIAL HOUSING PROJECT OF THE YEAR OFFSITE PIONEER OF THE YEAR INTERNATIONAL PROJECT OF THE YEAR PROJECT OR CONSTRUCTION MANAGER OF THE YEAR INSTALLER OF THE YEAR
ENGINEER ENGINEER OF THE YEAR OF THE YEAR ARCHITECT ARCHITECT OF THE YEAR OF THE YEAR CONTRACTOR CONTRACTOR OF THE YEAR OF THE YEAR BIM/DIGITAL CONSTRUCTION AWARD
CLIENT HEALTH & OF THE YEAR SAFETY AWARD
BIM/DIGITAL BUILDING PERFORMANCE PIONEER AWARD
CONSTRUCTION
AWARD
CLIENT OF HEALTH & THE YEAR SAFETY AWARD
BUILDING PERFORMANCE PIONEER
RECYCLE AND REUSE
Sustainable sourcing is essential at every level, and alongside energy efficiency policies and new regulations, pressure remains on the construction sector to continue to improve its building methods and product choices.
1
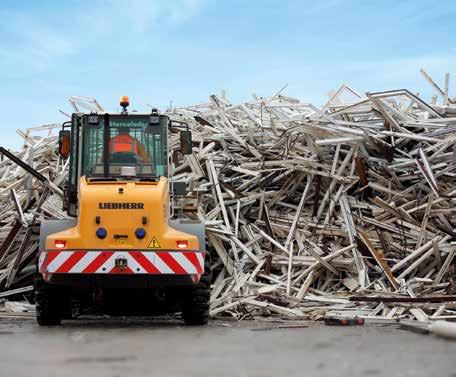
2022 sees changes to Part L of the Building Regulations come into force in June, and any new homes will have to produce 31% lower carbon emissions. This is ahead of the introduction of the Future Homes Standard in three years’ time.
PVC-U is already playing its part and for offsite construction, there are plenty of benefits to consider. Set against other potential product choices such as aluminium or timber composite, not only are there lightweight PVC-U options, making it ideal for offsite installation, but it also offers longterm durability and high performance. Plus, attractive aesthetics to support design visions, it is also cost effective and, through important initiatives such as Eurocell’s visionary and industry leading recycling processes, provides a truly sustainable product answer. Combined with effective glazing solutions, buildings can be better insulated and use less energy with PVC-U’s ability to offer a lower U-value for lower cost. The option to achieve excellent thermal performance results through a cost-efficient product choice without compromise, is a reason why PVC-U solutions that contain high levels of recycled content, are becoming a sustainable product choice for many.
Eurocell has been committed to recycling for over 20 years. Eurocell’s nationwide recycling service called Eurocell-Recycle meets two primary objectives: it prevents plastic window and door frame waste being sent to landfill and enables Eurocell to recycle end of life waste into new PVC-U extrusions. Two waste plastic recycling plants at Ilkeston and Selby are at the heart of the Eurocell-Recycle service. Using a ‘closed loop’ recycling system that deals with both post-consumer and post-industrial plastic window and door frame waste, the plants are now responsible for processing over 40,000 tonnes of plastic waste per year, a figure that has been steadily rising as demand for recycled product solutions has escalated in recent years.
To further substantiate the sustainability credentials of PVC-U product solutions, the Faculty of Science and Engineering at Manchester Metropolitan University recently reviewed an array of data sets and modelling emanating from peer-reviewed publications. This has established a lifecycle assessment of the use of recycled PVC-U window frames within Eurocell’s manufacturing operations.
For example, a typical semi-detached house comprising seven windows and a pair of French doors will see an average weight of post-consumer PVC-U within the eight products plus cavity closure of 122kg. Therefore, a development constructing on average 2500 units of semi-detached houses will save around 627 tonnes of carbon dioxide equivalent per year by specifying recycled Eurocell windows and cavity closures over a competitor who is using full virgin PVC-U windows.
For more information visit:
www.eurocell.co.uk
Images:
01. Two waste plastic recycling plants at Ilkeston and Selby are at the heart of the Eurocell-
Recycle service
TOOLS TO TACKLE THE CLIMATE CRISIS
Progress in reducing embodied carbon requires new tools and a shared language. Timber Development UK Sustainability Director, Charlie Law outlines what these should be.
The construction and built environment sector are responsible for nearly 40% of global carbon emissions, of which a significant percentage comes from the extraction, processing and energy intensive manufacturing of building products – known as embodied carbon. After many years of efforts across the industry, embodied carbon as an issue is finally emerging into the mainstream.
We see this in the debate of how we should handle our existing buildings, with the carbon cost of the proposed demolition of M&S on London’s Oxford Street grabbing national headlines, in local planning policy, with the London Plan including a requirement for whole-life carbon assessments, and in the Houses of Parliament where the ‘Part Z’ for embodied carbon recently came forward.
While excellent progress is being made, there remain outstanding challenges. For the timber industry this is seen in the debate on how to measure the impact of carbon sequestered by wood products. With the many differing opinions, it has sometimes been difficult to fully communicate the benefits which timber and timber building systems bring to reducing embodied carbon.
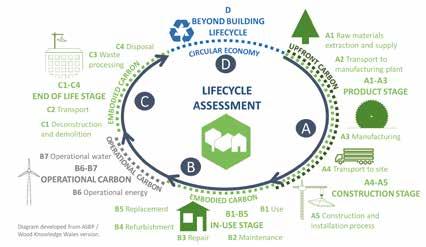
1
In our new technical paper ‘Assessing the carbon-related impacts and benefits of timber in construction products and buildings’ we set out to solve this problem by communicating a clear process for accounting for carbon in timber buildings and Environmental Product Declarations (EPDs) in accordance with the latest European Standards (EN 15978 and EN 15804+A2) and RICS Professional Statement on Whole Life Carbon Assessment in the built environment. As with any other core part of a business, from finance to operations, ‘if you can’t measure, it you can’t improve it’. To ensure the rigorous application of these standards to an industry leading level we worked with an independent party, Jane Anderson of ConstructionLCA, a world-renowned expert on embodied carbon, lifecycle assessments and EPDs for many different materials within the construction sector, to develop this technical paper.
To fully understand the carbon impact of construction requires a whole life carbon assessment. Within this assessment it has not always been simple to quantify what the impact of the biogenic carbon, which is sequestered by timber, is on the overall carbon footprint of a construction project. There needs to be a clear understanding of the construction product all the way from the forest – where our paper starts by looking at the forest ecosystem as a carbon sink – through to its end of life when it might be recycled into another product, converted into bioenergy, or otherwise released into the atmosphere, as well as all points in between.
Where timber is sourced from a sustainably managed forest then the sequestered biogenic carbon stored within the product can be considered as part of an assessment. On average, a balance of 568 million tonnes of CO2 has been added to the forestry carbon sink in Europe annually over the last ten years. The amount of carbon stored in harvested wood products, including timber used for building, is estimated to increase by 40 million tonnes of CO2 each year.
One of the reasons this technical paper has become possible is from the creation of Timber Development UK, formed from the merger between the Timber Trade Federation (TTF) and Timber Research and Development Association (TRADA). This paper will be the first of many as we set out to use our position in the timber industry to build a roadmap, along with the tools, training, guidance, and auditing to support the sustainable timber supply chain to become a net zero carbon industry.
You can download ‘Assessing the carbon-related impacts and benefits of timber in construction products and buildings’ for free at: www.ttf.co.uk/ download/tduk-technical-paper
Images:
01. Lifecycle assessment graphic explaining the areas of embodied carbon
CASE STUDY MAKEOVER FOR HISTORIC PUB

De Matos Ryan architects have transformed the Grade II listed Alice Hawthorn pub and restaurant using homegrown timber and sustainable design.
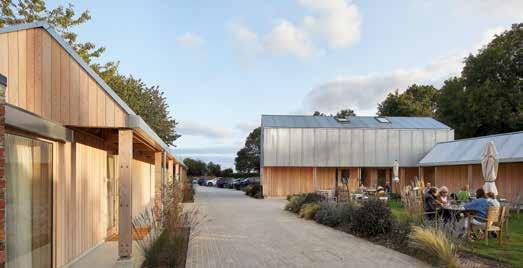
Named after a famous 19th Century racehorse, The Alice Hawthorn is the village of Nun Monkton’s last remaining pub. Close, collaborative consultations with Harrogate Borough Council and the local community informed the project’s design. After several years of neglect, it was important to save the pub from extinction.
The scheme includes twelve en-suite guest bedrooms, four on the first floor of the pub and eight around a new courtyard, which extends the village green into the pub’s rear garden. The homegrown Douglas fir framed buildings use authentic agricultural building materials, such as galvanised corrugated steel roofing and larch cladding, to create the sense that the animals have only recently moved out. A simple and honest construction typology ensures that the project looks like the way it was built.
The new timber frame buildings include the sheds, field barn, stables and tack room. Double member ‘cloister’ columns engage stainless steel feet sitting on cast concrete upstands. Adjacent to the front gate, the Sheds is a single-storey infill building between existing brick outbuildings with two staff bedrooms and a bathroom. It is clad in larch with a
1
pan-tile roof to match the outbuildings. The Field Barn is a south facing, twostorey structure with four guestrooms. The lower level is clad in larch while the upper level is sinusoidal galvanised steel. There are no windows to the north and west to prevent overlooking and light pollution to the neighbours.
The Tack Room, a single-storey structure with a wheelchair accessible guestroom, sits adjacent to the west boundary and the Field Barn. It also provides shelter to the outdoor kitchen, pizza oven and pub garden bar. Adjacent to the east boundary, the Stables is a single-storey extension structure with three guest rooms. Both the Stables and the Tack Room are clad in larch with a sinusoidal galvanised steel roof and back wall.
Internally, in contrast to traditional pub interiors, the newbuild elements have no plaster and are lined with larch boarding and poplar plywood. Subtle distinctions between the timber species are blurred by a tinted treatment. The only internal wall decorations are lino cut prints created by village primary school children, who have a vegetable patch at the rear of the garth.
Sustainability is at the heart of the project’s design. A ground source heat pump provides heating and hot water, supplied by bore holes and supported with high levels of non-combustible mineral wool insulation and airtightness to a standard higher than current Part L2A building regulations. The timber frame buildings are naturally ventilated through use of high-level clerestory windows and rooflights on actuators.
2
Solar gain is reduced by roof overhangs, which offer shading. LED and low energy lighting, as well as low volume water appliances, have been fitted throughout. The sustainable drainage system includes permeable paving and surface water attenuation tanks concealed below the pub garden. A challenge was to develop a one-hour fire resisting timber frame wall within 1m of the site boundaries. This was resolved by employing a fire resisting sheathing internally, thus avoiding carbon heavy blockwork.
On completion, the newbuild scored an EPC ‘A’ rating. Biodiversity has been improved on-site through extensive planting and habitat creation. The new courtyard is bounded by borders planted with native species, which also help screen the adjacent bedrooms. An orchard at the back of the site, which would have been typical of these plots in medieval times, is being re-established with fruit trees and will ultimately supply the pub’s kitchen.
For more information visit: www.dematosryan.co.uk
Images:
01-02. The new development has been transformed with timber into an EPC ‘A’ Rated sustainable eating experience. Courtesy Hufton + Crow