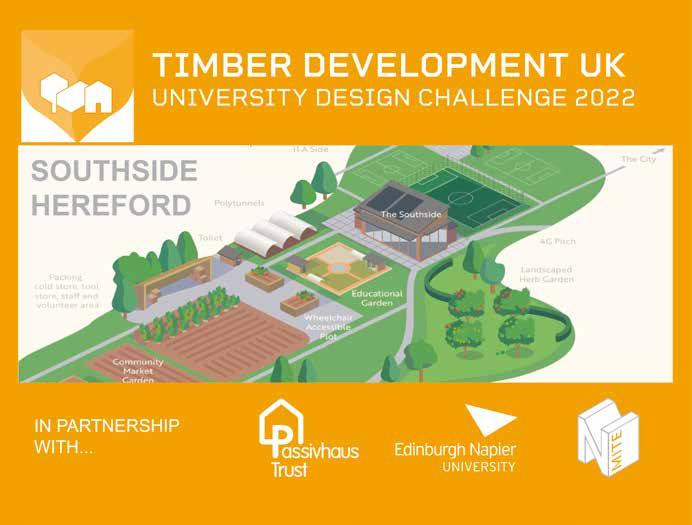
52 minute read
Industry News
Timber Competition for Hereford Net Zero Community Centre
Timber Development UK (TDUK) is partnering with New Model Institute of Technology and Engineering (NMITE), Edinburgh Napier University (ENU) and the Passivhaus Trust, to challenge built environment students, as well as recent graduates, to form multidisciplinary teams to create a ‘net-zero community centre’ based on timber and timber-hybrid systems.
Students from all built environment courses at UK universities, from first to final year, along with 2021 graduates are invited to enter the competition which launched on the 30 November at the Building Centre, London and online. The 2022 challenge – is to design an exemplary community building that produces more energy than it consumes, at Southside in Hereford.
Teams must produce designs that sites the community centre within the local context and landscape integrating the clients’ and communities’ interests. The detailed designs must be ‘net zero’, creatively employing sustainable building materials and construction methods, and be energy and resource efficient, focusing on the health and well-being of people, the community, and our planet. Tabitha Binding, TDUK, University Engagement Programme Manager, said: “Built environment professionals must prepare for a net zero future, and this must start in the classroom if we are to reach our climate goals. Our curriculum must be strengthened to meet the climate challenge by raising climate literacy. For our future architects, engineers, cost consultants, and landscape architects, this means improving their knowledge and capability of working with low-carbon materials such as timber – and being able to use it wisely and well.”
Professor Robert Hairstans, CATT Director, NMITE, added: “The objective is to inspire a generation of built environment professional to think differently about construction delivery towards more sustainable forms using timber rather than the traditional carbon intensive materials of steel and concrete. This challenge will exemplify this approach and create value return for the stakeholder partners of the Southside Hereford Project.”
TDUK is also bringing clarity to how to account for embodied carbon in timber construction with a newly released technical paper. ‘Assessing the carbonrelated impacts and benefits of timber in construction products and buildings’ explains how to account for carbon in timber buildings and Environmental Product Declarations (EPDs) by rigorously applying the latest British / European Standards. This will prove useful for building designers, clients, and contractors when assessing the embodied carbon associated with buildings and other structures, as well as product manufacturers and suppliers in demonstrating the carbon impact of their products.
Charlie Law, Sustainability Director at TDUK said: “Across the built environment professions there is rising wave of awareness that if we are to build to net-zero carbon we need to tackle how we account for embodied carbon. This paper seeks to help unify how we account for embodied carbon within timber buildings and structures so we can better understand, measure, and address these emissions in order to reduce their environmental impact.”
Source: www.ttf.co.uk
Major Offsite Move for Veteran Families
Riverside Scotland has handed over the first homes at the nation’s largest affordable modular housing development with four homes being allocated to military veteran households. The ground-breaking £9.8million project is being delivered by Riverside Scotland and Connect Modular, part of The Wee House Group and will provide 63 much needed affordable homes in Dundonald, South Ayrshire.
Riverside Scotland has made a strong commitment to providing homes for veterans at risk of homelessness at its two newest social housing developments by allocating more than 10% of new homes to support veteran households. At Dundonald 13% (8) of the homes are being allocated specifically to veteran households.
Heather Anderson, Head of Service Delivery at Riverside Scotland developed the Agreement with Lindsay Kirkwood, Clinical Psychologist for Veterans First Point. Heather commented: “Riverside Scotland recognises the housing and wider needs of many veteran households, and the difficulty many experience in accessing suitable accommodation and support upon discharge from the Forces, and beyond.”
The homes were handed over to residents on 25 November and will specifically address the housing needs of households who are at risk of homelessness upon discharge from the forces, or who require dedicated support to assist with resettlement. All properties on the development are built to Housing for Varying Needs Standards, to ensure that they remain flexible and adaptable to meet the changing needs of households over time. This level of provision exceeds the level of capacity provided for veterans in most other housing developments, relative to the size of the build.
Dundonald is the first modular project within the Riverside Group and the Riverside Scotland is proud to be flying the flag to make its housing more sustainable and energy efficient.

Source: www.riversidescotland.org.uk
McAvoy Group Appoints New CEO
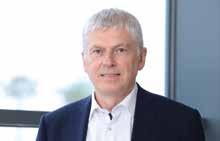
The McAvoy Group has announced the appointment of Ron Clarke as Chief Executive Officer following the retirement of Mark Lowry, who will remain with the business as Non-Executive Director.
Ron Clarke was appointed COO in March 2021 following senior roles with construction leader Graham, where he played a key role in the growth of the business nationally. Mark Lowry joined McAvoy in March 2019, shortly before funds advised by Blantyre Capital became the new majority owner. He has since steered the business through a challenging period and spearheaded its return to profitability. For this development, homes are built in Connect Modular’s manufacturing facility in Cumnock, Ayrshire. Jennifer Higgins, Managing Director at Connect Modular, said: “It’s a momentous occasion handing over the keys for the first five houses in our development with Riverside Scotland, the largest affordable modular housing development in Scotland. Handing over at this time proves the speed and efficiency with which the project is moving, thanks to modular build. A great achievement for all involved, and we look forward to continuing the delivery and handover of these homes in the coming weeks and months.”
The offsite leader reported positive financial results for the six months to 30 April 2021, with a 30% year-on-year increase in revenue. The business has secured all its budget revenues for 2022, with significant progress made in securing forecast revenues for 2023.
McAvoy has continued to perform well throughout 2021, with a strong forward order book supported by an expanding pipeline. It recently secured a series of new DfE education projects totalling £39million, including one of the UK’s very first low carbon school buildings. Existing projects have remained on track, with the Timebridge Centre in Croydon, The Deepings School in Peterborough and Antrim Area Hospital’s new Urgent Care Centre all successfully completed.
Ron Clarke commented: “Mark has played a pivotal role over the past two years in leading an ambitious growth strategy and, together with our very talented and experienced management team, I am looking forward to taking the business into the next phase of its development. We continue to make significant investments in growing the company, including the expansion of our hire fleet.”
Mark Lowry said: “Despite the challenges facing the construction industry during the last 18 months McAvoy has performed well, supported by Blantyre who have stewarded the business through a steep transition period. I’m pleased to be handing the reins to Ron, who benefits from a huge amount of experience in the construction industry, and I’ve no doubt he will be an excellent leader as McAvoy continues to evolve, focusing on long-term sustainability and resilience, underpinned by an effective ESG strategy.”
The growth in the business was accompanied by the announcement of additional senior management hires and promotions, with Martin Daly joining as Chief Financial Officer and the promotion of Stephen Clayton to Preconstruction Director. The company’s Modular Hire and Sales division has also been boosted with Glen Busby’s promotion to divisional director.
Johann Scheid at Blantyre Capital, added: “The McAvoy Group has performed well throughout a tremendously challenging period for the construction industry - with continued, strategic investments to support growth and a commitment to continue leading innovation within the offsite and MMC field, the business will continue to extend its market share across key sectors.”
Source: www.mcavoygroup.com
Offsite & Digital Tools Key to Future Construction CO2 Consuming Concrete Tested at Warwick University
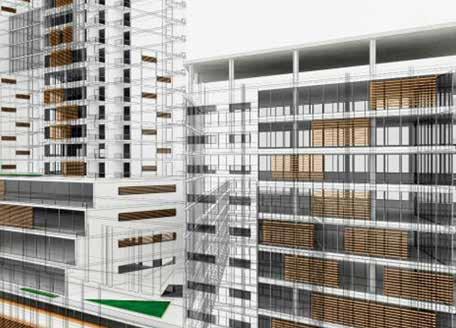
NBS, the platform for connected construction information, has revealed its eleventh annual survey, now the Digital Construction Survey, previously the NBS BIM Survey. With over nine hundred respondents, this year’s report provides a more comprehensive picture of the sector’s digital transformation, along with BIM adoption levels, and day-to-day usage of technology.
With approaching three-quarters (71%) of respondents now using BIM, it’s fair to consider this approach is now embedded across the sector, with adoption levels consistent for the past couple of years. The construction industry is now on board with technology and confident that it will help solve the challenges facing the sector, as demonstrated by eight in ten stating that digital technologies deliver a better-built environment, with three quarters (75%) saying that tech offers sustainability benefits.
The forthcoming Building Safety Bill has forced safety to the forefront of the construction industry, and regulation requires a digital “golden thread” of information. The golden thread covers information and documents as well as information management processes, all stored as structured digital information. While eight in ten (78%) respondents say they need to be working digitally and 70% say they need to have adopted BIM to make the golden thread a reality, only half (51%) are clear how they will do this. The golden thread process is made much easier with the data available through a digital twin. In addition, having a digital twin enables access to all the essential information in one place and allows for constant monitoring and maintenance of the asset.
While three quarters (74%) of respondents believe that digital technology is helping create a safer built environment, digital twin adoption is still relatively slow, with only 16% having worked on a project that used a digital twin in the past year.
In the past twelve months, half the survey's respondents have worked on an offsite project, a clear sign that a move to MMC is taking place, yet this figure shows there's still work to be done if the government is going to embrace MMC on the scale it intends. The Digital Construction Survey asked respondents to rank how various essential technologies or ways of working will transform the sector for the better over the next five years. The top five are as follows, 1 BIM, 2 Cloud computing, 3 Offsite construction, 4 Digital Twins, 5 AR/VR mixed reality.
Commenting on the survey’s results, David Bain, NBS’ Research Manager, said: “The adoption of new, digital technologies and ways of working should help to improve outcomes, so it is encouraging that 80% of built environment professionals agree that they are helping to create better buildings and places. Also, 75% say these innovations positively impact environmental sustainability, and 74% see them making a safer built environment. The industry also recognises the key role digital and BIM will play in realising the golden thread of information.”
Over 900 construction professionals took part in this year’s Survey, which included views from architects/ engineers and other consultants (66%), contractors (13%), clients (9%), and suppliers (9%) in the UK and beyond.
The full report can be downloaded at: www.thenbs.com/digital-constructionreport-2021
Technology developed by Concrete4Change (C4C) that can make concrete a carbon sink rather than carbon producer will be trialled and tested by researchers from the University of Warwick. C4C are on a mission is to enable the concrete industry to transition from CO2 emitters to CO2 sinks, by developing a technology capable of removing significant amounts of CO2 from the atmosphere and absorbing it into concrete.
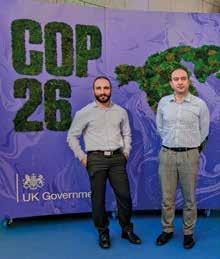
The sequestration of CO2 results in the strength enhancement of concrete; therefore, reducing the amount of cement required to produce equivalentstrength concrete. Both CO2 sequestration and cement reduction can contribute to the reduction of concrete’s CO2 footprint. This technology has the potential to mitigate 2 billion tonnes of CO2e emissions, the equivalent of 4% of global CO2e emissions.
The School of Engineering and High Value Manufacturing Catapult at the University of Warwick will undertake essential testing for the company with the help of funding through Innovate UK and the DI4M programme. Dr Reyes Garcia from the School of Engineering said: “As the world strives to reach zero-carbon goals, the construction industry and we civil engineers have a huge role to play to make concrete more sustainable. The cement we use to produce concrete contributes massively to CO2 emissions, and therefore we need to take drastic action now if the construction sector is to achieve its CO2 reduction goals.”
C4C has also been selected by British Precast as one of the top three most innovative companies and as one of the top five companies for Knowledge Transfer Network Transforming Foundation Industries. Pictured: left to right, CTO Dr Michael Wise and Dr Sid Pourfalah, Founder and CEO of Concrete4Change at COP26.
Hill Group Seeking Sustainable Change
Hill Group has committed to achieving net-zero carbon in its Scope 1 and 2 business operations by 2030 and net zero operational carbon in the homes they build by 2030, twenty years ahead of the UK’s broad 2050 net-zero carbon target.
Additionally, Hill has committed to achieving biodiversity net gain on all its future land-led developments. Hill has already modelled a range of house types and apartment layouts to interrogate CO2 reduction performance standards required for delivering future homes. This will see the phasing out of fossil fuels, with electricity becoming the primary low-carbon energy source powering air source heat pumps. Photovoltaics and battery storage are likely to be part of the optimal solution too.
Hill's solutions will include improved building fabric performance, reduced embodied carbon of materials, increased offsite manufacture, increased airtightness, better thermal bridging and supply chain deliverability. In addition, increased reliance on electricity as the primary energy source, and increased need for electricity for car charging points, is already causing Hill to look at grid capacity and planning additional sub-stations into development layouts. Brendan Ritchie, Head of Sustainability at Hill Group, said: “We are always keen to be at the forefront of any industry changes, and we already have live projects at design and early construction stage featuring a range of house and apartment types which will meet the expected Future Homes Standard and deliver ‘net-zero ready’ homes several years ahead of the anticipated regulatory timescale.
“But our solutions must ensure that homes remain affordable to run. We must avoid fuel poverty as an unintended consequence of the drive towards zero carbon homes. We have lots to do to be Future Homes and zero-carbon ready as a sector. However, at Hill, we are confident that our pioneering approach alongside the national background of continual de-carbonisation of the electricity grid will help us find optimal solutions".
Two of Hill's most recent developments, Knights Park and Agar Grove, have raised the bar in terms of placing emphasis on sustainable living and placemaking. The homes at Agar Grove are certified to a gold Passivhaus standard, and the overall development is the largest Passivhaus regeneration development in the UK.

Source: www.hill.co.uk
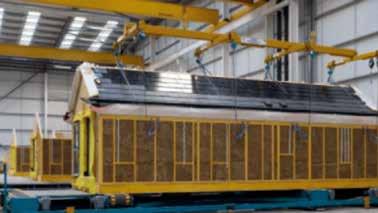
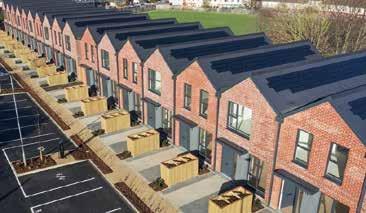
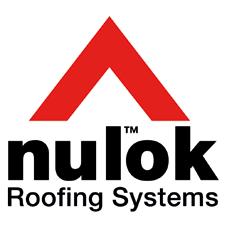
YOUR OFFSITE SLATE & SOLAR ROOFING PARTNER
Fully recyclable Install fully offsite 30-year warranty Light-weight Low maintenance Solar ready
Call: 0330 123 4440 Email: matthew@nulokroofing.com Visit: www.nulokroofing.com/uk/modular
New Modular Trade Body Formed Wernick Acquires AVDanzer
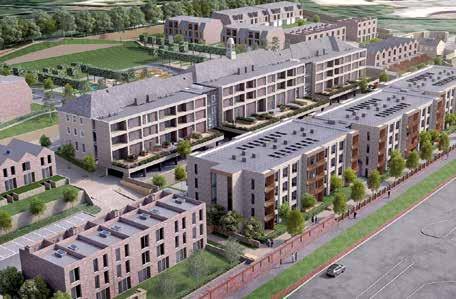
Make UK has launched a new trade body Make Modular, bringing together leading modular housing manufacturers with a plan to solve the country’s housing crisis by delivering 75,000 affordable highquality homes before the end of the decade.
The UK housing market is at a tipping point where it could transform into the most advanced housing manufacturing market in the world in under a decade delivering more than 75,000 new homes via modular techniques. Make Modular members’ factories can produce a new home every 2 hours. These homes are near defect free with 97% less embodied carbon than traditional builds. Make Modular members have already invested more than £500 million in new factories, cutting edge processes, and state of the art technology.
The UK construction sector will have lost at least 25% of its workforce by between 2016-25. There is a major risk that by the next election construction has become the new haulage with economic competitiveness undermined by an ageing workforce leaving the industry.
More than 2,000 new jobs have been created by Make Modular members in the last three years. By moving people offsite and into clean, safe, modern working conditions volumetric can rebuild the construction workforce bringing up to 50,000 new younger people into the workforce.
Uniquely in the construction sector, modular housing provides the opportunity to construct offsite and in regions where labour is available. Homes are then transported to the areas where demand for new homes is the highest. Current factories driving the start of the modular revolution are already located in the Midlands and the North of the country, providing highly skilled and sought-after careers using the latest digital and automated technologies with innovative design bringing about the highest environmental credentials. Stephen Phipson, CEO of Make UK said: “Imaginative and speedy solutions are required to tackle Britain’s housing crisis and modular housing could certainly play a significant part in helping local authorities deliver the challenging home building targets set for them by Government. But to make real significant progress, modular housing needs to have equal access to land for construction with many sites still favouring traditional modes of construction. Modular also needs to have the weight of Government procurement behind it using a joined-up approach including education, defence and housing to build much needed scale the UK’s modular industry.”
Modular housing manufacturers are also keen to accelerate the development of building regulations to match a new, more ambitious new normal when it comes to quality and energy across construction as a whole, driving forward the world’s biggest challenge of climate change.
Dave Sheridan, Chair of Make UK Modular added: “Modular housing has grown rapidly in the last few years. The establishment of our own trade body is the crucial next step in this process. As a natural partner to Government to solve the housing crisis, deliver the levelling up agenda, and combat climate change Make Modular will accelerate and advance the MMC agenda through one strong voice rather than a series of disparate ones.’
Members include: TopHat, Urban Splash, Ilke Homes, Laing O’Rourke and Legal and General Modular with backing from Goldman Sachs, Laing O’Rourke, Legal & General, Sekisui House and TDR Capital, with support also provided by Homes England.
Source: www.makeuk.org
The new acquisition means that Wernick will add additional manufacturing capabilities and increase their fleet with more than 2,000 cabins and modular bays.
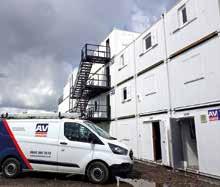
AVDanzer, also known as Danzer, is a Manchesterbased firm that supplies high-quality modular buildings for sale or for hire. The business has a long history of catering to some of the UK’s major infrastructure and development projects including the London Power Tunnels Project and the nuclear power station at Hinkley Point in Somerset. In addition, they are widely known to cater to a range of sectors and can provide schools, hospitals, offices, laboratories, sports facilities and more.
Following the acquisition, Danzer will continue to operate as usual from its sites in Manchester and Langley Mill. The manufacturing of anti-vandal steel that is currently based at Langley Mill will continue trading as AVDanzer. Meanwhile, the Brentwood depot will merge and become a part of Wernick’s depots in Essex and Kent.
Wernick’s Group Chairman, David Wernick, said: “We have strong admiration for Danzer’s manufacturing capability and products, and after initial discussion it quickly became apparent that both family-owned businesses share the same values of excellent customer service, outstanding product quality, focus on safety, and keeping things simple. We are delighted to welcome the Danzer team to the family and look forward to sharing ideas and growing the business further.”
Director at AVDanzer, Dan Holloway, added: “We pride ourselves on being agile and innovative to adapt to new market conditions; the COVID pandemic has really driven the demand for high-quality innovative accommodation and offices and our team has kept us at the forefront of developments in our sector. We are pleased to join forces with a business with a similar history and ethos. With the combination of Wernick and our team of experts, we are confident that this transaction will boost our capabilities to offer even more flexible solutions to both new and longstanding clients.”
Source: www.wernick.co.uk
CALA Group Boost Net Zero & MMC Ambitions
CALA Group has made two key senior appointments as its Sustainability Strategy, launched earlier this year, continues to build momentum.
Kathryn Dapré has taken up the role of Head of Sustainability, with Robin Dodyk joining as Head of Modern Methods of Construction (MMC). They will help drive its commitment to be operational net zero carbon by 2030, as well as reaching net zero greenhouse gas emissions, in line with the Scottish Government’s 2045 target and ahead of UK Government’s 2050 target. These goals reflect owner Legal & General’s pledge to make all its new housing stock operational net zero carbon enabled from 2030, as part of its wider commitment to set science-based targets and align with the UN Paris Agreement and global efforts to achieve net zero carbon emissions by 2050.
Kathryn will direct CALA's roadmap of research, innovations and targets across key areas contributing to reducing its environmental impact, working closely with regional teams to empower its colleagues to play their own part in carbon reduction.
With 28 years of experience across a wide spectrum of sustainability and climate change focused roles, Kathryn joins CALA from NHS Scotland, where as Head of Energy and Sustainability, she was instrumental in developing and implementing national sustainability policies and strategies. including the development of the NHS Scotland Climate Change and Sustainability Strategy.
Having spent more than 44 years in the construction sector, including over 20 years with Oregon Timber Frame in Selkirk. Robin Dodyk will guide the business in adopting greener housing, leading on MMC research, trials and implementation, as well as associated training and development for the wider team. He will initially spearhead a major initiative to roll-out timber frame across CALA’s entire range of homes, ensuring efficiencies in the 40% of homes which already use timber frame as well as establishing and executing a strategy to efficiently introduce it to the rest of the business. Robin said: “Within the construction industry, our route to reducing carbon will involve a lot of change and innovative thinking if we’re to achieve our sustainability goals. It’s an exciting time to join the CALA team when our environmental impact is at the forefront of the agenda. With timber frame offering up to a 20% reduction in embodied carbon over similar size traditional building methods, our plans to switch to this new approach is a huge focus. We will also explore other elements of MMC and wider innovations in construction to help achieve our net zero ambitions.”
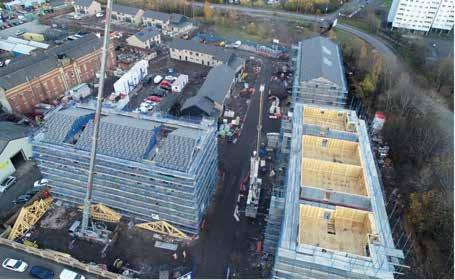
Source: www.cala.co.uk
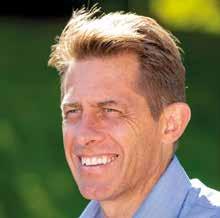
Ibstock has revealed plans for a £50million capital investment in a new West Yorkshire factory and is aiming to build the UK’s first automated brick slip systems factory in Nostell. The planned investment is set to provide capacity for up to 60 million brick slips per annum. An initial investment of around £38million, providing capacity to produce 30 million brick slips, will be spread evenly across 2022 and 2023, with the factory commissioning in late 2023. The second phase of investment is expected to be made shortly after as additional capacity is required.
The factory will be constructed within the existing footprint of the group's Nostell facility, which operated as a brick factory until its closure in 2020. The planning application process has begun, and construction on-site is expected to start during the first quarter of 2022. The facility is the launch project for Ibstock Futures – a new business unit established to capture growth opportunities in new, fast growth sectors of the UK construction market.
As demand grows for façade products and solutions for both newbuild and re-cladding products, Ibstock Futures will develop new products suitable for a wide range of residential, commercial and mixed-use applications. Ibstock Futures enables the Group to develop a stronger presence in the fast-growing offsite and modular construction markets. “The launch of Ibstock Futures is an important strategic development for the Group,” says Joe Hudson, Ibstock plc’s Chief Executive Officer (pictured). “Our new business unit will directly address a number of exciting growth markets that complement our existing offer for conventional building methods as the focus on sustainability and the industrialisation of construction processes gathers pace.
“The initial £50million investment in brick slip manufacturing capacity at Nostell, West Yorkshire, will be a first for the UK and will enable us to take a leadership position in this fast-growing market. Crucially, it will also be a beacon of manufacturing excellence and sustainability – we are all very excited at the prospect of producing a net zero brick slip. We have made ambitious commitments on our Sustainability Roadmap to 2025 – and this announcement underpins our ambitions. The Nostell plant is the first of a pipeline of growth initiatives we have in development for Ibstock Futures and we are excited about the potential this new business has to accelerate growth in the years ahead.”
Source: www.ibstockbrick.co.uk
MMC Trials Held Across 105-house Development
The latest scheme of a 1,000-home major housing contract is being built using a mix of modern methods of construction (MMC) supplied by Roofspace Solutions and flooring by Nuspan. Together, the two solutions will help to speed up overall delivery of the phase compared to traditional methods. Lovell, the leading partnerships housing expert, is delivering a major housing project on behalf of the Borough Council of King’s Lynn and West Norfolk. The current construction phase began in October 2020 at the Nar Ouse Regeneration Area (NORA), which encompasses plans for 105 two- and three-bedroom properties for affordable rent, private rent shared ownership and market sale.
Lovell began the initial phases of the development with traditional methodologies, such as masonry superstructures, before opting to trial an offsite approach for the current phase. This includes installation of 24 i-House™️ units from Roofspace Solutions, which speed up construction to watertight stage by 35-40%, building from the slab up to the roof trusses within five days on an average three-bedroom house. These will be combined with 105 of Nuspan’s precast insulated floors, a system that offers a reduction in labour of up to 83% and no onsite waste. The system is also five times quicker to install than traditional block and brick floor foundations – when calculating the time taken to obtain a structural floor, from golden brick to superstructure (approximately one plot a day for block and beam vs six plots a day for Nuspan).
Lovell chose to trial these MMC products due to the higher standards of design quality provided, alongside the sustainability benefits and reduction in waste typically associated with MMC. What’s more, any success achieved in the project could act as a blueprint for widespread rollout of MMC across future Lovell developments.
Michael Saunders, Operations Manager at Lovell, said: “This project demonstrates that more exacting standards are achievable with offsite construction methods. The approach also helps us to combat current industry challenges such as strain on the supply chain and skills shortages. Success in this trial will mean that Lovell and our client will be able to make more informed decisions about MMC investment on our future developments.” Graeme Reed, i-House Operations Director, said: “Roofspace Solutions and Nuspan are greater than the sum of our parts. Individually, we create products and solutions that address a need in the construction market and help to speed up housebuilding. Together, those benefits are multiplied, allowing the contractors and developers to reap the associated benefits such as cost savings, increased safety and a significant reduction in construction time.”
Helen Wildin, Sales and Marketing Manager at Nuspan, added: “This collaboration demonstrates what can be achieved when the industry works together. It also highlights the potential of using MMC to speed up construction – sustainably – on the scale we need to meet the huge demand for housing.”

Vertex BD It’s All About BIM
Vertex BDSource: www.roofspacesolutions.co.uk/i-House www.nuspan.co.uk
It’s All About BIM
Vertex BD Vertex BD Sales Architectural Design
Marketing Framing
One BIM software platform to drive your entire building project from start to finish
• Architectural Design • Automated Steel and Timber framing • CNC data for CFS, Timber and HRS
• Precise project documentation Project Archive
• One software, one model
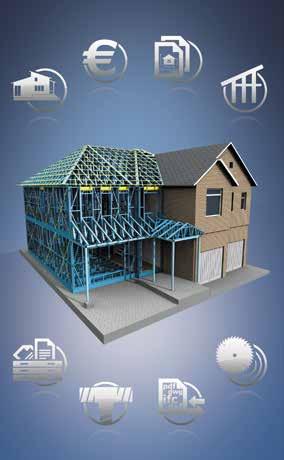
IFC Collaboration File Format Conversions Production Automation
Increase Productivity, Improve Quality, Minimise costs
Contact our Harrogate based team today to learn how we can help you with your next project.
Marketing Sales Architectural Design
Framing
Project Archive
IFC Collaboration File Format Conversions Production Automation
Present Made Deliver on Eddington Masterplan
Present Made, the UK’s first purpose-built and designed single-family rental housing platform, has been appointed by the University of Cambridge to develop sustainable smart homes as part of its ambitious 150-hectare Eddington masterplan.
Under plans submitted to Cambridge City Council, Present Made will develop and operate close to 370 rental homes – including the UK’s first family houses to be designed and built exclusively for rent – as part of a new neighbourhood that will promote healthy and sustainable living. The £160million scheme, and the broader Present Made concept, has been curated by award-winning Jo Cowen Architects. Residents will further benefit from Present Made’s corporate focus on sustainability, with the company targeting a net zero carbon operational model as part of a wider ESG-driven strategy.
The homes at Eddington will be highly energy efficient thanks to a combination of smart technology and offsite construction, with the houses precision engineered in a factory environment in a process that is less wasteful, disruptive and time consuming compared to traditional construction techniques. Richard Jackson, co-founder of Apache Capital and CEO at Present Made said: “It is a privilege to be working alongside the University of Cambridge in delivering the UK’s first family homes to be specifically designed and built for rent. This would not have been possible had it not been for the strategic concept, design and development by Jo Cowen Architects, which was central to the University of Cambridge's decision to select Present Made.
“Present Made homes will sit in master-planned, landscape-led communities that have been designed around people not cars, to promote active, healthy and sustainable lifestyles. Harnessing the power of institutional capital, Present Made will own, develop and operate beautiful, sustainable homes for the long term. Our aim is to create a new way of living, providing aspirational yet attainable housing set within living streets and active communities that are integrated with their surroundings.” Jo Cowen, CEO of Jo Cowen Architects, added: “Present Made at Eddington will be characterised by a high-quality of architecture and a highly-liveable public realm, with the idea of time well-spent being central to the concept. We have designed a sustainable neighbourhood focused around people, not cars, which aims to connect an intergenerational community with one another and improve the quality of everyday lives through high quality homes and streets. The scheme will deploy modern methods of construction through bespoke design, integrating new technologies with a holistic vision to deliver a development and amenity spaces that promote sustainable living, wellness, human connection, personal growth, and common unity.”
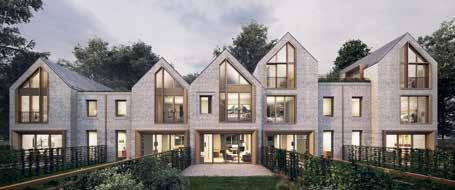
Source: www.apachecapital.co.uk
Homes England Launch New Delivery System
Housebuilders of all sizes will find it easier than ever to access Homes England land, with the launch of the new Delivery Partner Dynamic Purchasing System (DPS). This new system replaces the Delivery Partner Panel 3 (DPP3), transforming the way Homes England procures housebuilders and disposes of land.
Switching to a dynamic purchasing system means that housebuilders can now apply to join the agency’s list of preferred developers at any time, rather than having to wait until the list is renewed once every four years. This is the biggest DPS of its kind, and, valued at £20billion, is Homes England’s largest procurement exercise to date.
Stephen Kinsella, Chief Land and Development Officer at Homes England, said: “This marks a significant step forward in the way we work with developers to build homes. The flexibility of the DPS means that housebuilders can apply to join when it suits them, or when they see a relevant site on our Land Hub. We’ve also simplified the application process, so whether you’re a large, nationwide housebuilder, or a small local developer, it will be easier for you to access land you want to build on. We encourage all housebuilders interested in working with us to monitor our recently updated Land Hub and apply to join the DPS when they see a site of interest.”
Local authorities and housing associations can also rely on the DPS as a procurement-compliant solution for finding housebuilders, making it easier for them to build homes on the land they own. Initial applications opened earlier this year, and 66 housebuilders have now been appointed to the DPS, of which 24 are SMEs.
Housing Minster Christopher Pincher said the flexibility of the DPS will offer SMEs and new entrants, commenting: “This Government is making great progress in building new homes and we are keen to continue delivering the homes this country needs, he said. “We welcome this change which will support SMEs while providing more opportunities for home ownership to hard-working people across the country.”
Applications to join are now open on an ongoing basis, and housebuilders are encouraged to apply as and when they see sites of interest on Homes England’s Land Hub, the agency’s interactive tool used to advertise sites it is bringing to market.
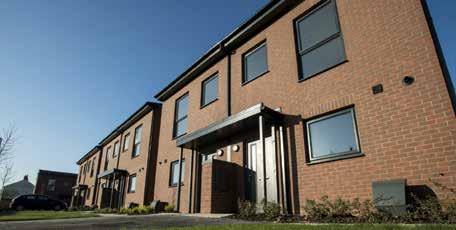
Information on how to apply to join the DPS can be found on the Government website at: https://bit.ly/3CQEjci
Stora Enso Launches UK Low-Carbon Industrial Buildings Solutions
Stora Enso has launched a suite of tools to support developers of the UK’s industrial buildings to create more attractive, productive and sustainable buildings, with spans ranging from 12 to 36m, from small workshops to large retail sheds and warehouses.
Stora Enso’s timber industrial buildings allow developers to cut embodied emissions by up to 30% while also benefiting from highly modular and flexible designs. Crucially, the new design tools incorporate a high degree of pre-fabrication, allowing for accelerated construction timelines, and can be configured for easy disassembly and reassembly as needs change. With available UK warehouse space estimated at less than 50million sq ft with the potential to run out within a year, thanks to the pandemic and rise in online shopping, timber industrial buildings offer a way for developers to rapidly respond to market dynamics while also improving sustainability performance.
Sebastián Hernandez, R&D Manager for Building Concepts at Stora Enso comments: “Industrial buildings are at the nexus of a number of megatrends in the UK. On the one hand, we have the moral and policy imperative to decarbonise our building stock; on the other, we have the planned renaissance of British manufacturing and shift to online shopping increasing demand for these types of structures.
“Not only can wooden industrial buildings enable companies to respond to these trends, but by moving away from monotone grey sheet metal and concrete, they can allow us to create better working environments for UK employees and improve the increase the quality of retail and industrial parks up and down the country.”
To support adoption of engineered timber for industrial buildings, Stora Enso has created a source hub for architects and developers that includes fully interactive 3D models and technical specifications of eight different base types for different industrial buildings. These are pre-optimized for the most standard and common industrial buildings we see in the market and can used as a basis for designing bespoke concepts.
The industrial concept is the latest in a series of building concepts designed to support the construction industry in adopting mass engineered timber to improve sustainability and building performance.
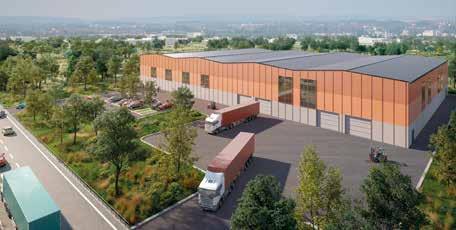
Source: www.storaenso.com
New Group Structure for Excel
Having invested in re-branding its business in 2019, specialist offsite building solutions provider, Excel, has created a new, dynamic group operating structure. Introduced to define and add greater clarity to its comprehensive solution provision and product offering, Excel Group now incorporates three separate and autonomous operating divisions – Excel Structures, Excel Facades and Excel Off-Site.
Group Managing Director, Jason Pritchard said: “The expanding, multidimensional nature of the business made the decision to create a Group operating structure an obvious one. We occupy a unique position in the sustainable off-site building sector in our capacity to offer a range of different building systems, not just one. Such a proven and all-inclusive business model has proven hugely successful, and with the new structure in place we are looking to further elevate our standing within the off-site construction sector, which continues to gain momentum here in the UK.”
Excel Structures adopts responsibility for delivering a range of offsite building systems – SIPS, Light Gauge Steel Frame, pre-insulated timber frame and cross laminated timber (CLT). In terms of project flexibility, Excel Structures’ involvement can extend from designing, supplying and installing a structural build system, through to a complete weather tight and insulated structure. Excel Off-Site will support a move into the arena of main contractor, where full project build and co-ordination will become the order of the day.
“Setting up a main contractor division has been something that has always been on the sidelines,” add Jason. “However, we feel the time is now right to expand our capabilities even further. We already have established proven, sustainable and scalable relationships with not only our specialist supply partners, but also a growing team of architects, consultants and sub-contractors, so full project delivery of offsite schemes is something that we are extremely excited about. Indeed, by creating a platform where we can manage the complete build process, we will ensure that the benefits of utilising an off-site building system are maximised project by project.”
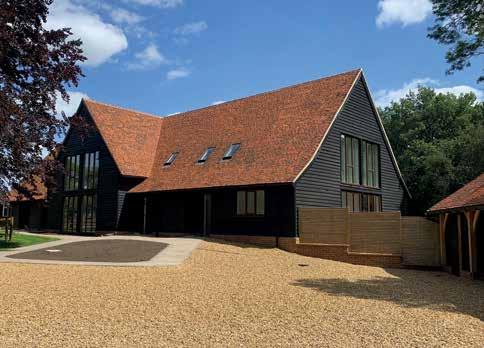
Source: www.excelgroup.uk
Salford University Announces Partners for Global Net Zero Facility
Salford University’s Energy House Laboratories has announced its first collaborative project partners ahead of the launch of its multi-million-pound Energy House 2.0 research facility in 2022.
Among the partners included are residential housebuilder Bellway Homes, development partnership, The English Cities Fund (ECF), and a joint venture between construction materials and solutions firm Saint-Gobain and Barratt Developments. Across the studies, the organisations will be supported by leading academics from the University in a bid to tackle some of the built environment’s biggest challenges when the state-of-the-art research and testing facility opens next year.
Building on the success of the Salford Energy House, a two-bedroom terraced house constructed inside an environmentally controllable chamber, Energy House 2.0 will have the capacity to replicate a total of four, fully furnished houses across two environmental chambers which can replicate climatic conditions and environments experienced by 95% of the global population. The £16million research facility, part-funded by the European Regional Development Fund (ERDF), aims to work with businesses and manufacturers in the built environment to support global ambitions to reach
carbon reduction targets by 2050 and deliver net zero future housing.
For more than a decade, the University of Salford’s Energy House Laboratories has been leading the way in low carbon innovation in the home. Professor William Swan, Director of Energy House Laboratories said: “Domestic energy and heating is a major source of carbon emissions and this was a hot topic at the recent COP26 Climate Change conference in Glasgow this month. It has clearly been acknowledged by world leaders that we need to act now to protect our planet.
“Homes and the built environment contribute around 40% of the UK’s total carbon footprint, and the global picture is similar. That’s why we’re so excited to announce new partnerships, which will help our work with key players in the private sector to drive innovation and solutions that address global, domestic energy efficiency challenges – making a world of difference to our future and our planet.”
The unique research facility will allow partners to innovate, test and validate housing design, home heating and approaches to using a variety of energy technologies. Each of the research partners will be building a house in one of the state-of-the-art environmental chambers within the facility and will investigate distinct challenges over an estimated nine months. Energy House Laboratories and the Energy House 2.0 partners are looking to collaborate further with businesses across the UK and globally that may be interested in supporting their studies.
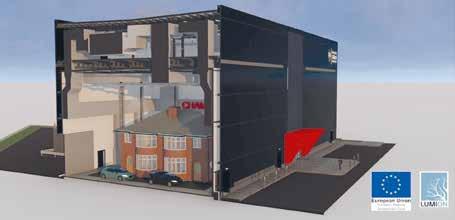
Source: www.energyhouse2.com
Places for People Choose Offsite Options
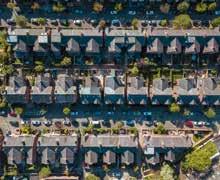
Places for People, one of Britain’s leading placemaking organisations, has announced a pioneering partnership with ilke Homes to deliver hundreds of modular homes in the South East and South West. Following the largest deal yet for Britain’s modular housing sector in 2019, ilke Homes and Places for People have struck a two-development deal which will see the delivery of 472 affordable homes. As part of the agreement and subject to planning permissions, Places for People will purchase two sites: a 307-home development in Burgess Hill, Sussex; and a 165-home development in Exmouth Junction, Exeter. Both developments will provide a range of apartments and two, three and four-bedroom affordable homes, which will be managed by Places for People and available for affordable rent or for sale through shared ownership.
Scott Black, Group Executive Director – Developments, at Places for People, said: “By adopting modern methods of construction (MMC), our partnership with a proven modular business such as ilke Homes allows us to create more affordable, well-designed mixed-tenure communities across the country – speeding up delivery, cutting costs and giving our customers unrivalled choice and quality.
“The partnership is about pioneering a new way of delivering homes through making socially responsible decisions and working with best-in-class partners. Our investment in modular housing across our developments and the proposed acquisition and delivery of Exmouth Junction and Burgess Hill forms an integral part of Places for People’s ambitious growth strategy to deliver high quality affordable homes which meet people’s needs.” The news of the deal, which comes two years after ilke Homes entered a strategic partnership with Places for People, follows last month’s announcement that the modular housing pioneer has been selected by FTSE 100 firm Boots UK to deliver the UK’s largest low-rise modular housing development – a 622-home scheme in Beeston, Nottingham. The deal marked the first time the retailer had released any part of its Nottingham HQ site holdings for housing.
As part of sweeping reforms to the planning system, the Government is encouraging the redevelopment of brownfield sites to bring new investment into areas and increase housing delivery. Places for People is a strategic partner with Homes England.
In 2018, Places for People was one of the first organisations to be awarded a grant from Homes England and will deliver circa 6,000 affordable homes over the next 10 years through this partnership.
Source: www.placesforpeople.co.uk
Premier Modular Achieves BOPAS Accreditation Following Residential Expansion
Premier Modular has achieved BOPAS accreditation for its modular living solutions, following its expansion into the residential sector. Premier has five factories at its production centre in East Yorkshire. It has capacity to produce 100,000sq m of living space per year, with the opportunity to increase output to meet demand.
Commenting on the new accreditation, Jeff Maxted of BOPAS and a Director of BLP Technical Services (UK), said: “It is fantastic to see Premier’s expansion into the residential sector, building on their vast experience in other areas. BOPAS is an independent, standards-led benchmark for modular housing, providing long-term assurance to lenders and valuers that homes built using non-traditional methods of construction offer longevity and reliability.”
Dan Allison, Director of Premier Modular, said: “We are immensely proud to receive this industry accreditation which reinforces our expansion into the residential sector. BOPAS provides our local authority and developer clients as well as funders and mortgage lenders with complete reassurance of best practice and that our modular apartment solutions meet or exceed the required standards.”
“We have ambitious plans to bring innovation and sustainability to the UK housing market. We already have a number of residential projects on-site and nearing completion and are receiving a high level of enquiries for new schemes. We anticipate the demand for offsite construction will continue to increase to help address the housing crisis and the drive for net zero.
“We offer a range of modular solutions for low to mid-rise apartment developments, and the speed of offsite manufacturing will help to reduce housing waiting lists. We have also successfully demonstrated the structural stability of our building system beyond 15 storeys, giving our customers even greater confidence in our design and construction capabilities.
“The residential sector is facing considerable challenges – from the shortage of skilled labour to the need for increased productivity and improved quality in housebuilding to meet the rising demand for new homes. By moving the construction of new apartment schemes offsite and into a more controllable factory environment, we can produce energy-efficient homes with less impact on the environment, to reduced programmes, and significantly enhanced quality.”
Premier has been awarded full BOPAS accreditation for design, manufacturing and construction. A rigorous assessment was carried out by BOPAS, which audited all aspects of Premier’s operations, including quality control systems, health and safety, project management, and interfaces, from design through to offsite manufacture, construction, and handover.
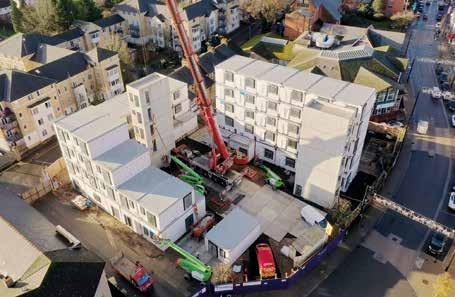
Source: www.premiermodular.co.uk
NG Bailey Engineers Support Expansion at Clydebank’s NHS Golden Jubilee
NG Bailey’s Engineering division has secured a second contract to support the ongoing expansion of NHS Golden Jubilee in Clydebank, Scotland. The £15million contract is the second time the UK’s largest independent engineering and services provider has been appointed by the principal contractor Kier Regional Building Services – Scotland, to support the Hospital’s expansion plan.
During 2020, the company delivered the mechanical, electrical and plumbing installations (MEP) for phase one of the expansion, a new six-theatre eye centre which began receiving patients in November 2020.
Work on the second phase of the National Treatment Centre is already underway and is expected to be completed by June 2023. This will enable the NHS Golden Jubilee to carry out thousands of additional hip and knee replacements and other orthopaedic procedures annually, as well as significantly expanding diagnostic testing and general surgery. The project is due to be completed in summer 2023.
A team of NG Bailey engineers, including apprentices, will be on-site to support the delivery of the new three-storey development which will include theatre suites, orthopaedic amenities, outpatient and preoperative spaces, a surgical admissions and recovery unit, a central sterilising and processing department and a new endoscopy unit. Offsite construction is being widely used across the project and many of the service installations, including heavy duty service modules, plant room skids and plant room frames are being manufactured at NG Bailey’s specialist Offsite Manufacture facility. The building will also feature a range of energy saving measures including high efficiency heating, cooling and ventilation systems, presence-controlled lighting systems, and a heat recovery system serving the operating theatres.
Patrick Morrison, Healthcare Sector Director at NG Bailey said: “We are delighted to be working with Kier again to deliver this important project which brings further enhancements to patient care in the region. We have extensive experience delivering healthcare projects across the UK, working in live hospital sites where maintaining on-going patient services is vital. We’ve designed our solutions to embrace modern methods of construction as this accelerates the delivery of our programme, reduces the carbon impact of the works and minimises disruption by reducing the number of deliveries required.”
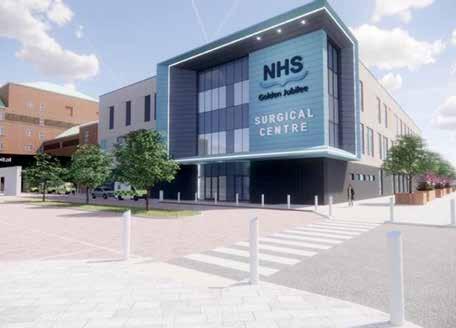
Source: www.ngbailey.com
Sika’s Offsite Division Changes Shape
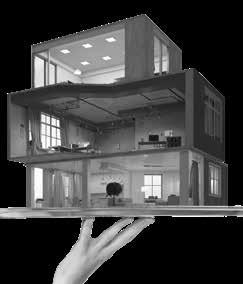
Sika’s modern methods of construction (MMC) Division has extended its team of offsite manufacturing specialists to cover a breadth of skill and expertise. The team works with offsite manufacturing and assembly companies to look at how Sika products can be used as part of the process in this fast-growing sector. At the helm is Simon Griffiths, Head of Sales – Offsite Construction. He will be supported by nine members from across Europe each bringing their own personality and experience to the table.
Speaking of the news, Simon Griffiths, said: “Offsite has grown steadily over the past few years. Its benefits are widely known and understood. We are at a point where we believe that the use of offsite will accelerate to meet the demands of many projects such as HIP. As a business, Sika has many products that can be used in offsite construction, both within production assembly lines and/or application upon delivery to site, for a variety of purposes. To support the development of this important market sector, we have expanded our specialist team of experts.” Sika’s MMC division is utilising global experience to guide offsite manufacturing companies towards unlocking new potentials. The division can offer a customised approach for modular manufacturers, especially where construction solutions need an industrial approach. As part of its commitment to offsite manufacturing across the nation, Sika also recently joined the Offsite Alliance, a membership organisation that increases the uptake and delivery of offsite technologies in the residential sector.
Sika’s decision to be part of the Offsite Alliance signifies the company’s commitment to the offsite manufacturing effort. Through a combination of action and collaboration, Sika will work with fellow like-minded organisations to promote best practice, share innovation and work together to create the high quality, sustainable homes of the future.
“We are delighted to have joined the Offsite Alliance,” added Simon Griffiths. “We see a perfect strategic fit. We have a great team at Sika, who in many cases, are already involved in driving forward industry and association agendas. We see this addition as a natural step forward to working collaboratively with the MMC industry, to raise the profile and standards, and to help deliver the aspirations of the industry.”
Source: www.sika.com
GENERATION NEXT
MOBIE was founded in 2017 by the architect and TV presenter George Clarke and is driving the future of home design. Chief Executive, Mark Southgate, talked to us about how it is radically improving the way we construct – and increasingly manufacture – homes in the UK.
Q: MOBIE has aspirational and ambitious long-term aims – for those unfamiliar, can you say a little about the background to its formation and its team?
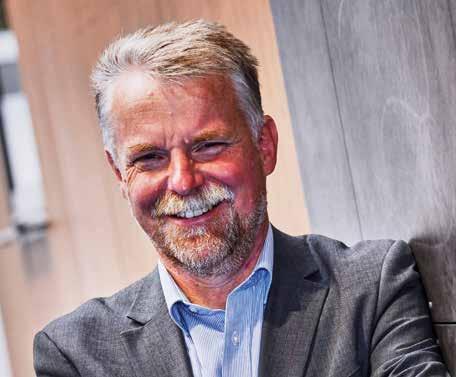
Mark Southgate (MS): The home is the most important piece of architecture in our lives and at the Ministry of Building Innovation and Education (MOBIE), we want to raise design standards, build quality and introduce innovation in homebuilding. To do this we want to inspire the next generation to join the industry and drive the change we need, through a different way of thinking and doing. MOBIE engages with young people from primary school to university through our design challenges and with education partners we have created new courses
1
in home design and manufacture from BTEC to PhD. Through our Homes for the Future Innovation Centre with Northumbria University, we are helping to bring much needed research and development and innovation to the housing sector.
Q: You have created a unique ‘educational pathway’ that will hopefully provide a new generation of professionals working across the built environment – what does this pathway entail?
MS: We believe it is for tomorrow’s generation to define how they want to live. Working with our education partners we have created new modules and courses at BTEC, Nationals Certificate and Diploma, Bachelors, Masters and PhD. They focus on a different approach to home design and manufacture, with topics such as digital design, new technology and materials, new processes and offsite methods, sustainability and alternative energy. We want to attract and nurture a new cohort of designers, makers, developers, planners and surveyors to enter and reshape the housing industry, to help to deliver our most important buildings better, more sustainably and more affordably. We want them to have a broad understanding of the built environment and through the courses discover the right professional discipline for them.
Q: There is a lot of talk of ‘disruption’ across the construction sector, with tech-driven start-ups appearing regularly – does MOBIE see itself as part of this disruptive change to the norm?
MS: Yes, MOBIE sees itself as disruptors, but disruptors for a reason. The way we build homes has hardly changed in the last 100 years. We need to change the way we build houses, so they better meet the needs of their occupiers, and they reduce their impact on the environment. We can do this by adopting more digital approaches and applying manufacturing thinking. We also need to change to attract our future home creators to the industry – we have a big attractiveness problem in the industry with not enough young people wanting to join. But by utilising new approaches and technology this will help make us a more attractive proposition to new entrants, and importantly help retain workers we already have and help them get more from working in the industry.
Q: What feedback have you had from the course options so far and initial intake of students?
MS: We started with the MSc at Teesside University, Advance Home Futures. We have since added a distance learning MSc at the University of Wolverhampton, Offsite Housing Construction, and Bachelors’ at Teesside, Innovative Home Design and Construction, and Birmingham City University, Design for Future Living and are working with more universities to develop new courses. Our first graduates were from the Teesside MSc in 2019, followed by a second cohort in 2020.
We are delighted that many have found employment with housebuilders using modern methods of construction (MMC) and other built environment practices where they can play an active part in shaping and changing the future of the homebuilding industry. That’s what we wanted them to do, and we are pleased they are finding companies and roles where they are being asked to do this. All our graduates and challenge winners become part of the MOBIE community that is shaping the future of the industry.”
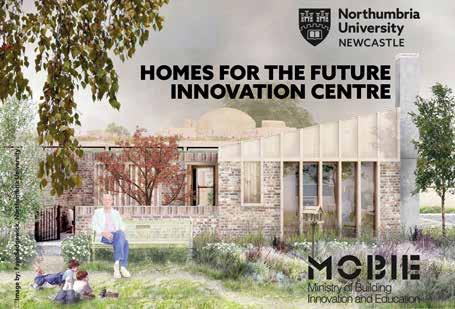
Q: The ‘traditional’ way of housebuilding construction – ostensibly brick and block and site-based operations – is increasingly being seen as outdated, with offsite construction, DfMA and factory-based methods moving ‘manufacturing and construction’ closer together – is that fair to say from your perspective?
MS: Whilst we have seen dramatic technological and productivity changes in other sectors, housebuilding has hardly shifted the dial. Unfortunately, this is reflected in the product – the ‘snagging’ lists of faults for new homes can be enormous. You just do not see that in other manufacturing environments. We need to improve our product, to make our homes more efficient, adaptable and sustainable and to better meet people’s needs. Adopting manufacturing process thinking and techniques can help us improve homes by reducing waste, reducing their environmental and climate impact and improving the build quality of the product. We will still build homes using bricks and mortar, but manufacturing – be it components of homes or whole houses – will continue to grow and become an ever-larger part of the market. Consultancies such as Savills and McKinsey predict that MMC homes could make up 20% of homes built in the UK each year by the end of this decade.
Q: How integral to the future of homebuilding is the understanding and use of digital tools and technology to develop energy efficient new homes and a cleaner industry?
MS: Homebuilding has been slow on the digital uptake, but a revolution is coming. The future of construction is digital, and the approach marries well with MMC. In a manufactured environment, the product delivered should be as per its ‘digital twin’, but on many traditional sites where ‘workarounds’ are necessary we know this is not the case. Digital design can help maximise energy and environmental efficiency and reduce waste.
Where the manufactured house mirrors the digital design, then maintenance and repair become so much easier – this is very attractive to organisations who retain and maintain houses once built, such as Registered Social Landlords. Using digital tools in the design of homes will make the industry more attractive to a new workforce that thinks and operates digitally. It could even help in fields such as planning where you can more easily show affected communities the nature and impact of proposed new development. Frankly, as an industry that produces a 3D product, it amazes me how slow we have been to adopt 3D design representation and techniques – digital capabilities must be a fundamental skill for the future and they a core part of our training.
2
Q: Carbon reduction is now a constant topic of discussion – how can we best marry together the ‘efficient and the ecological’ to secure the 2030 and 2050 net zero targets?
MS: Climate change matters to young people, as they will have to live with the consequences. We see this all the time in their designs for our challenges. They want to live in low, and preferably zero, carbon homes. We need to provide them with those homes, and we need to train them how to create them, so low carbon housing is a key part of MOBIE courses. 40% of our carbon emissions come from the built environment – be it embodied energy in their creation, or operational energy used to heat and run the home. We can already build zero carbon homes, so we need to share the knowledge on how best to do this and adopt it at scale. We will also need to retrofit between 27 and 29 million existing homes in the UK to deliver on our zero carbon commitments. Delivering effective retrofit training is essential. MOBIE is a member of the skills group of the Optimised Retrofit programme in Wales and we are working on how best to create and deliver such training.
3
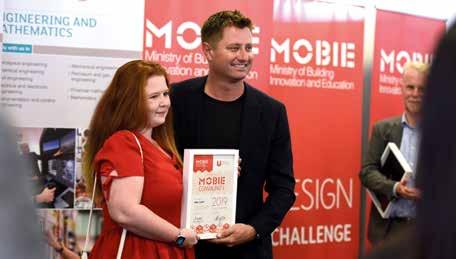
Q: Many industry reviews focus on increasing housing numbers, declining skills, an ageing workforce, low productivity levels and variable quality of finished product – how can MOBIE help?
MS: That is why MOBIE was formed in the first place – we started MOBIE to create a generational shift. MOBIE will help inspire and attract a new generation of talented young people to join the built environment and housebuilding industries to secure their future and drive necessary change. We will train them with the skills they need to improve our product and the industry’s productivity, including though use of digital skills and manufacturing approaches. I chair the Offsite Alliance Skills Group and we are identifying the skills that the MMC sector needs to deliver a higher quality product and how best to deliver them.
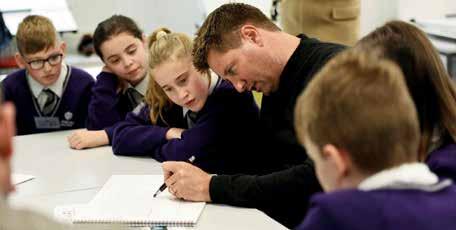
Q: Earlier this year the ‘House iO’ competition asked architectural students from University of West England (UWE) to form teams, to design a prefabricated housing scheme – what kind of schemes were proposed?
4
MS: The competition asked architectural student teams from UWE to design a prefabricated housing scheme to address homelessness in Bristol, using Totally Modular’s House IO system – volumetric modular homes built to near carbon zero standards. The students could choose from three sites allocated for housing in the city. The challenge attracted entries from first year to final year students, who enjoyed tackling a real-life brief and acting as design teams working under pressure to deliver their proposals in under a week. The teams created a range of sensitive, well-researched and well-argued proposals for their sites. The winning entry utilised the layout of their site to create blocks and clusters of modular housing with retained trees and communal spaces that provided both quality shared space and privacy. It was a high-quality housing scheme designed with great thought about the needs of its users.
Q: The Mayor of London is partnering with MOBIE to launch a design challenge for young Londoners this Autumn – what is this all about?
MS: Design Future London is our latest place making and design challenge for 11- to 25-year-old Londoners. It was launched at London Build on 18 November and runs until 6 May 2022. We are asking young Londoners to design an innovative and inspirational green home and urban neighbourhood in the Royal Docks, East London. The home and neighbourhood designs should address four key priorities central to London’s recovery from COVID-19: making places, sustainable transport, building housing, addressing climate change and providing green energy for London. They should meet the changing needs of future generations of Londoners, including promoting wellbeing, quality of life and healthy living.
The challenge is free to enter. We hope that it will inspire a new generation to learn about the built environment and bring learning in subjects like geography, history and design and technology to life. The challenge will also introduce young people to the built environment sector and the variety of jobs – from planning and architecture to engineering and construction – that exist and employ nearly 10% of the UK workforce.
For more information visit:
www.mobie.org.uk
Homes for the Future Innovation Centre
www.northumbria.ac.uk/businessservices/engage-with-us/mobie
Optimised Retrofit
www.optimised-retrofit.wales
Design Future London
www.consult.london.gov.uk/hub-page/ design-future-london
Images:
01. Mark Southgate, Chief Executive, MOBIE 02. The Homes for the Future Innovation Centre will help bring much needed research and development and innovation to the housing sector 03-04. Architect and TV presenter George Clarke was a key founder of MOBIE