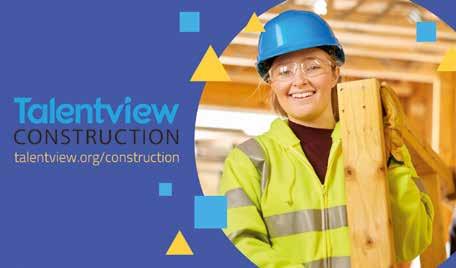
9 minute read
Spotlight on New Talent
Can offsite construction help to tackle skills shortages? Chris Jarman, Director of the Construction Talent Retention Scheme and Talentview Construction, offers some compelling reasons how it can.
In the face of crippling skills shortages which are now impacting on housing completion rates and the levels of activity onsite, unsurprisingly a lot of scrutiny is now turning onto the efficiency and productivity opportunities presented by offsite construction.
Construction is a varied sector, employing about three million people and offering multiple career paths. Even without the growth of ‘green jobs’, it is estimated by the CITB that the industry needs to recruit more than 217,000 new workers between now and 2025 to support its current activity, including the development of exciting new careers in digitalisation and sustainability. This demand is only likely to accelerate, as the latest figures from the Office of National Statistics indicate an estimated 500,000 UK-born workers are likely to leave the sector in the next 10 years as they come to retirement age.
Clearly, we are not going to have the labour options we’ve enjoyed in the past. And as everyone knows, necessity is the mother of invention. We will have no choice but to look again at the way we build. But could the shift to offsite help provide a solution to the skills shortages? Unfortunately, it’s not that simple. In the first place, we need to attract new entrants into the industry and ensure they’re coming in with the right mix of both construction and manufacturing skills and experience.
1
Research that we carried out this autumn found that, despite record numbers of job vacancies, young people are finding it harder than ever to identify the right roles for their abilities and interests. We questioned almost 2,000 young workers and found that only 14% are very confident of finding suitable career opportunities this year, and nearly half believe it’s now harder to find jobs compared to pre-pandemic. When added to the figures above highlighting the looming skills challenges facing the construction sector, it’s clear that something needs to change. The talent is out there, but not enough people are considering construction as a serious career choice. Part of the problem is that, whether the sector likes to admit it or not, we have not done enough to promote the attractions of the sector. We are not the only industry with a skills shortage, and we are up against many other sectors in the war for talent.
However, shifting to offsite could help to tackle part of the issue. As we know, the sector requires more digitally and manufacturing based skillsets compared to traditional methods, which in turn means employers can potentially recruit from a much larger pool of talent than they have had access to in the past.
Many of the roles that the offsite sector is seeking now will be in even greater demand in the future as more employers identify the need for wider technological and manufacturing competencies. It’s highly likely that we’ll see steadily rising demand for continuous improvement leads, agile developers and specialists in areas like 3D printing, automation, LEAN and Six Sigma, along with a broader requirement for world-class manufacturing talent. In BIM alone, Go Construct predict there will be over 200,000 new jobs created within the next five years. Without attracting people from other sectors or encouraging more young people into construction, many firms will struggle to remain productive.
Moving towards more modern methods of construction may help to widen the pool of talent, but employers must also focus on promoting the array of opportunities that are on offer more effectively. If these roles are made more visible, it’s likely that a wider range of young people will at least consider construction as their industry of choice. Solving other issues, like boosting the
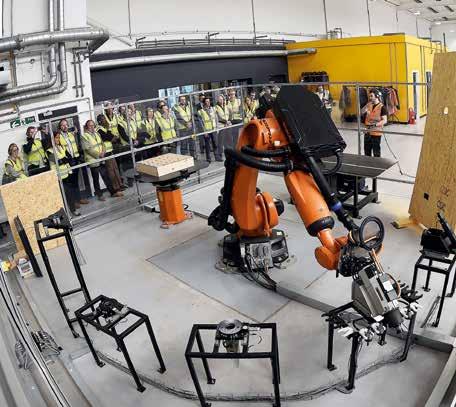
digital supply chain and modernising training programmes, will also help to close the skills gap. But essentially, construction needs to find a way to attract the right talent. Harnessing the potential that offsite holds is at least a step in the right direction.
From there, a constant challenge facing employers has been identifying young people seeking a career in the sector. But this is where platforms like Talentview Construction (TVC) step in. TVC is a new, free-to-use governmentbacked initiative designed to make it easier for those searching for a career in construction and the built environment to join the sector and take advantage of the wide array of opportunities, from practical jobs through to digital and project management roles.
Mark Reynolds, Group CEO of Mace Group and the Construction Leadership Council’s lead on skills, says: “More than ever, the industry needs a strong pipeline of talent. Talentview Construction is a window on the industry for all those wishing to enter construction as new entrants and career changers. We must make it easier for people to join our sector to support growth and to improve our levels of diversity – but to do so everyone needs to do more to recruit openly and make flexible opportunities accessible through schemes like this.
“This is exactly what so many businesses have been crying out for, helping them tackle skills shortages and gear up for future growth. Initiatives such as Talentview Construction – part of the Construction Talent Retention Scheme – have the potential to dramatically improve our industry, but we all need to get behind it if it is to be a success.” It’s clear that the construction industry needs to source talent, not just for now, but also for the future shift to more offsite model adoption. Interestingly, data from the Construction Talent Acquisition Forum, a group of the UK’s leading construction employers, found that almost every organisation surveyed was facing the same shared challenges, whether that was sourcing experienced talent, or attracting new
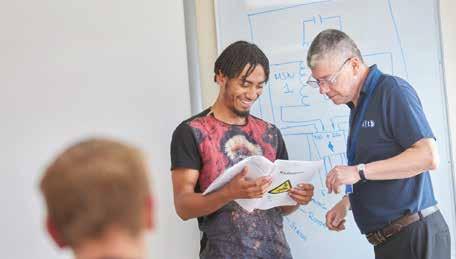
TALENTVIEW CONSTRUCTION
Talentview is the newest offering from the Construction Talent Retention Scheme (CTRS) which was established by the Department for Business, Energy and Industrial Strategy (BEIS) and the Construction Leadership Council last summer. Together with complementary sites like CITB’s Go Construct, TVC and CTRS help to create a ‘one stop shop’ sector talent hub for the attraction, development and retention of people and skills within construction and the built environment, as part of the Government’s broader support to business on skills.
2
3
people to the industry. Equally, that suggests that working together and collectively supporting talent initiatives could benefit the entire construction sector.
For more information visit:
www.talentview.org/construction www.trs-system.co.uk/construction
Images:
01. Talentview was launched in September 2021 02. Robotics and digital design is transforming construction. Courtesy Construction Scotland
Innovation Centre 03. More concentration on offsite manufacture and cutting-edge technology skills will help draw in a younger and more diverse pool of talent
CASE STUDY PRECISION PROCESSING FOR CLARIDGE’S HOTEL
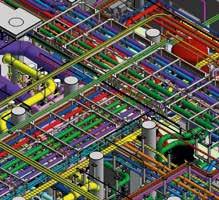
Recent work on London’s prestigious Claridge’s Hotel, saw MEP specialist Kane invest in the Holobuilder digital platform to add to its existing digital expertise and make smooth progress on a complicated scheme.
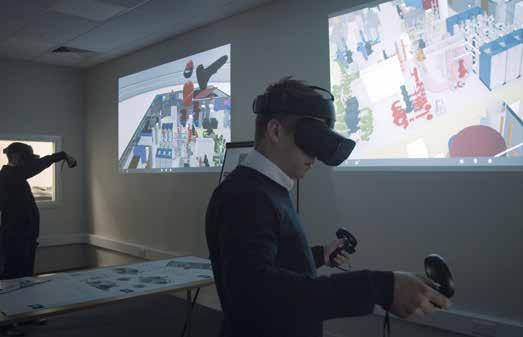
An iconic building in the heart of Mayfair, Claridge’s Hotel has undergone a colossal extension, with five floors underground. Appointed by the Maybourne Group, Kane designed, prefabricated and installed the £12million Energy Centre successfully, exceeding client expectations. The scope of works encompassed a Basement Energy Centre and Basement Works. The project ‘mega basement’ comprised of combined heat and power systems, gas fired boilers, chillers and plate heat exchangers.
Holobuilder provides access to 360-degree progress photos which are organised by location and time, enabling a walkthrough of each project remotely as if you were there. From the outset, the team scanned a one-toone digital copy of the background building before commencing design works. This allowed the team to measure the exact position of column walls within millimetre accuracy, allowing a precise background model to be built. The design team used Revit fabrication to design the pipework, fixtures, fittings, steel support framework models, pump skids and heavy plant. Authored in Revit, Kane’s in-house team designed the layout of all services at high and low level using its co-location virtual reality bespoke rooms.
Collaboration between the design, prefabrication, and operations teams was undertaken to analyse the model using Navisworks, to detect internal clashes within the structure at the design stage and ensure zero co-ordination issues throughout the installation process. Autodesk Navisworks allowed the team to analyse and sequence the works. This was critical as the project was very constrained for space, using a single small entry point for all pipework which was lowered five levels below ground.
1
The co-ordination of the setting out points, the technology to geolocate thousands of specific points within the structure for fixtures and fittings, such as steelwork supports, hanging points and ductwork, each with unique reference points, ensured a seamless on-site installation. Kane’s in-house prefabrication facilities enabled early on-site construction, increased the speed of installation, lowered manpower in the confined space and
2
reduced the requirement for hot works by 80%. All its prefabrication works went through a rigorous quality control procedure which was pre-tested before delivered to site. As part of its BIM protocol, Kane provided COBie compliant families, cross referencing BIM Level 2 designs for manufacturing and used its in-house bespoke Procurement App enabling digital ‘take off’s’ which was meant a streamlined ordering process.
Both the client and AECOM were hugely positive about the relationship development with Kane and the overall project delivery. The client has recognised that the design innovation and offsite prefabrication was key to the success of the project and additionally awarded Kane with an extended Scope of Works that included more hotel central works. Client representative, Mark Allen, from Rainey & Best said: “Kane delivered an outstanding Energy Centre contract at Claridge’s Hotel. Kane provided solutions, through their in-house digital and prefabrication expertise, to overcome the complexities of the constrained site five levels below ground. We were confident that they could deliver this project and they did just that, superbly.”
For more information visit: www.kanegroup.co.uk
Images:
01-02. Digital technology drove the successful delivery of this complex project with plant rooms and services across five levels. Courtesy Kane

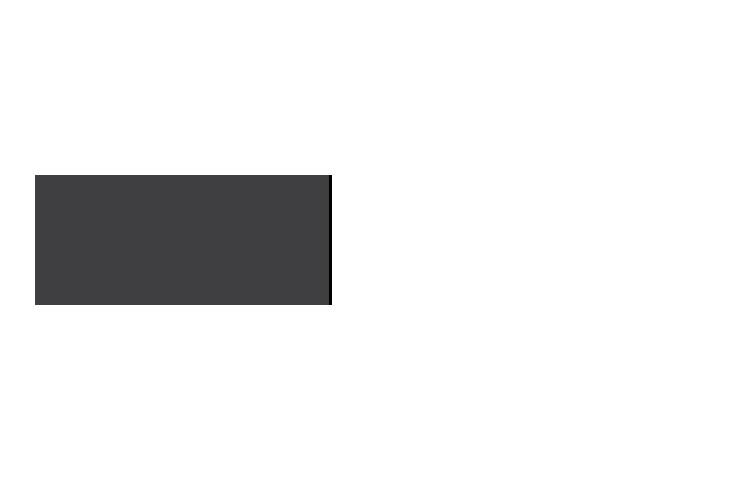
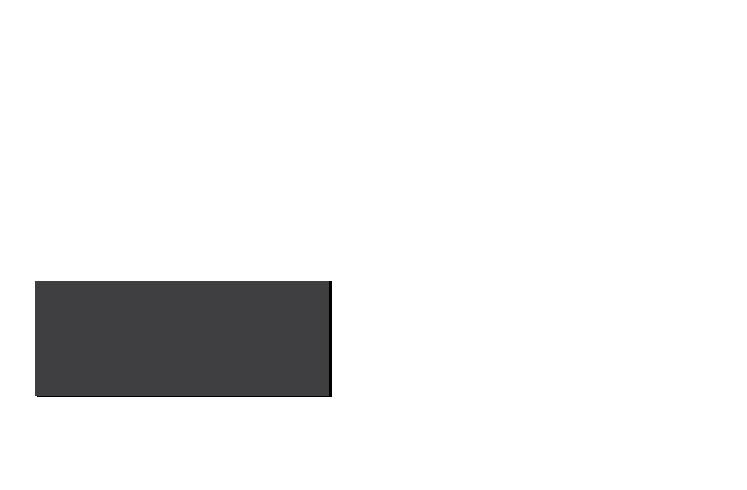
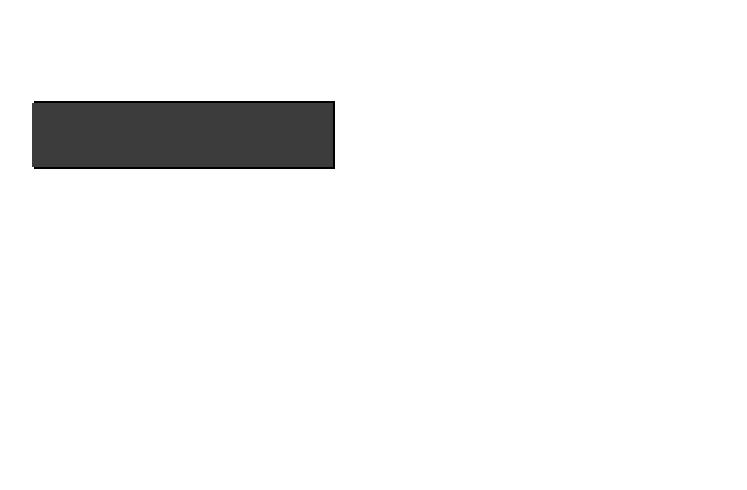
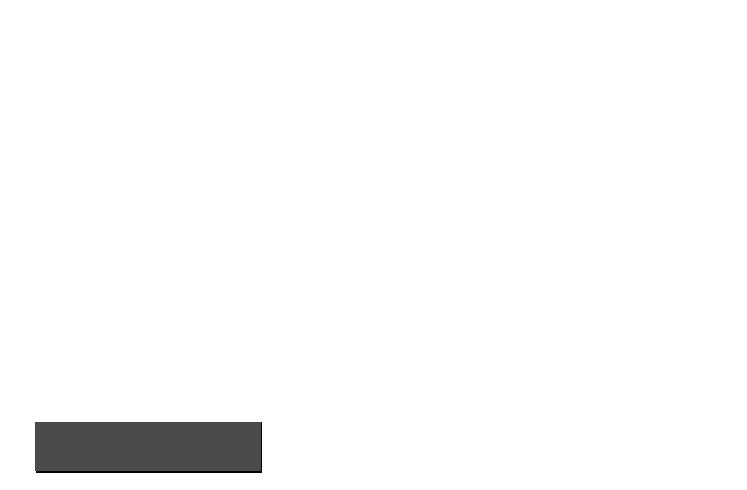
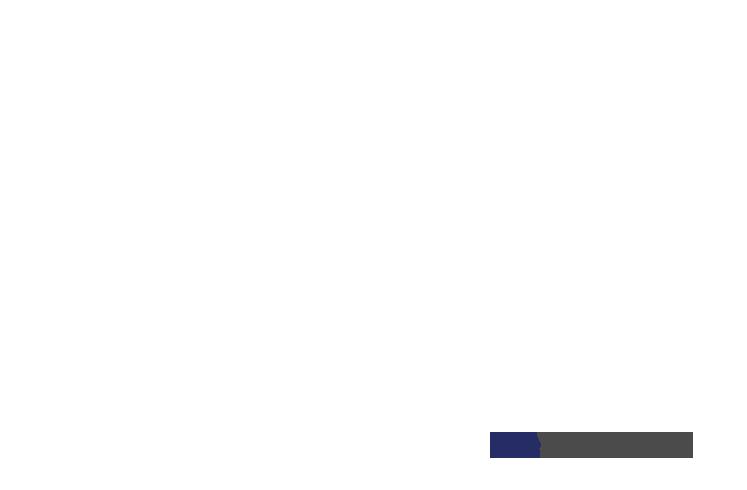
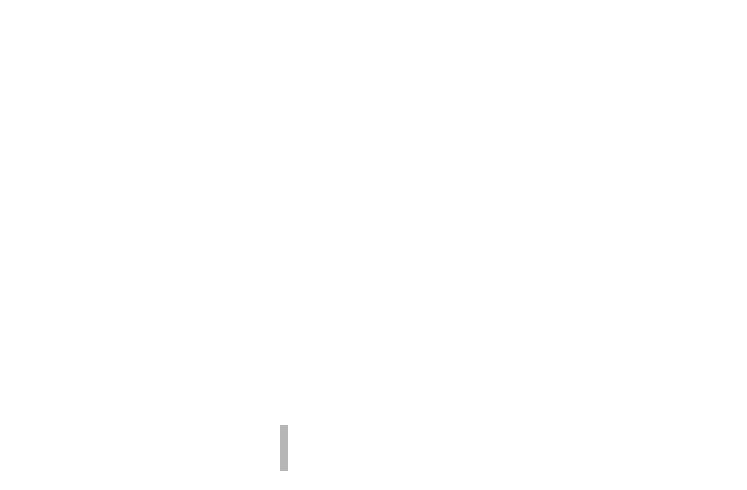
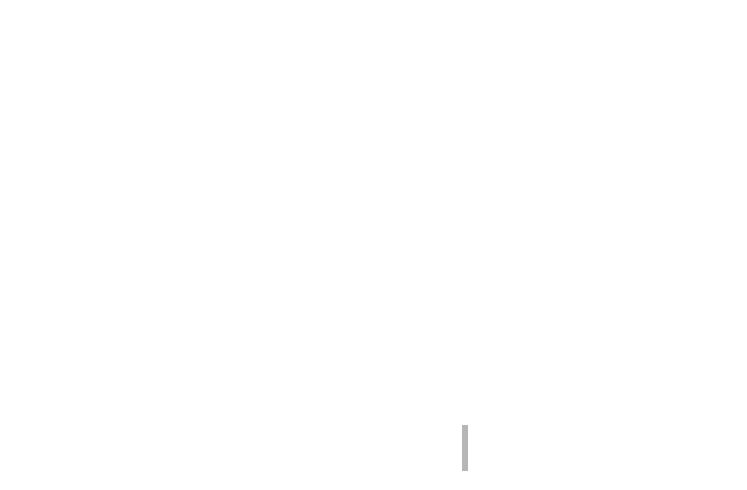
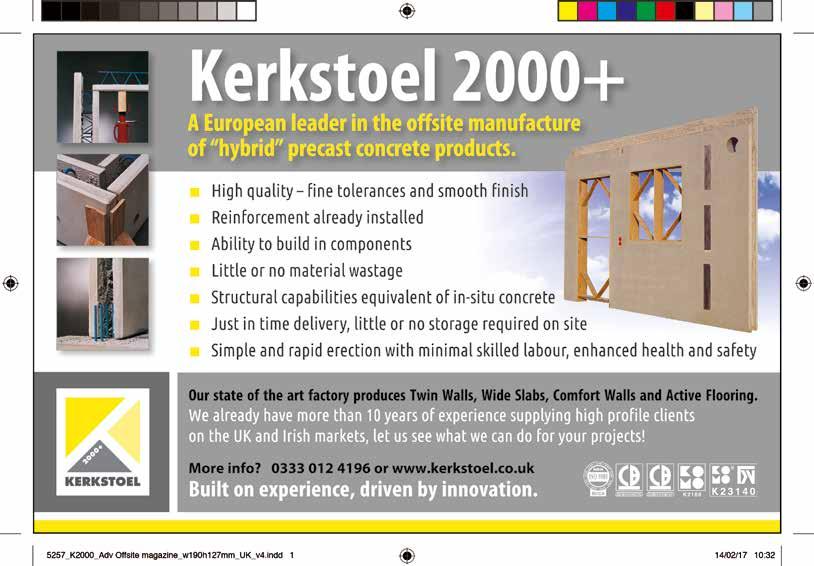