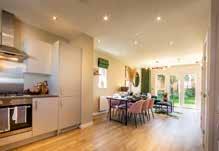
12 minute read
A Shift in Housing Supply
Ilke Homes has raised £60million to scale-up its operations and deliver an ambitious five-year plan that could put them on course to become a top ten housebuilder within the next five years by delivering 10,000 factory-built homes.
1
The £60million is split between £30million debt from government agency Homes England and £30million of equity from multiple new investors. The Guinness Partnership, one of the UK’s largest providers of affordable housing and a customer of ilke Homes, is one of the new equity investors.
The housing association has signed two deals with ilke Homes in the last year, for sites that will deliver 250 factory-built homes. Tech-focused family office Middleton Enterprises and private equity firm Sun Capital have also taken equity stakes. TDR Capital has also injected further equity.
Stephen Robertson, Founding Partner at TDR Capital, said: “Precisionengineering housing will be a critical solution to greening cities and with housing needs continuing to significantly outstrip supply, we are also confident that this sector is immensely scalable.”
The £30million of debt comes via a facility from Homes England’s Home Building Fund. The Government’s housing agency invested an initial £30million into ilke Homes back in 2019, which marked the first time the agency had ever directly invested to boost an offsite manufacturer’s production capacity, with the latest round demonstrating that ministers remain prepared to take genuinely innovative steps to intervene in the
housing crisis by creating meaningful supply-side incentives to increase house building capacity.
Harry Swales, Chief Investment Officer at Homes England, said: “Manufacturers like ilke Homes are vital if developers are to build new sustainable homes at the pace and scale the country needs. This debt facility from the Home Building Fund shows our commitment in increasing productivity and efficiency in construction to meet government’s housing delivery ambitions.”
The new funding will be transformational for ilke Homes, allowing the company to invest heavily in automating more of its manufacturing processes to drive efficiencies, secure more sites and expand its ‘package deal’ strategy, which offers full development service of site, infrastructure and homes in a rapidly growing market. Both housing associations and build-torent operators are looking to scale up delivery of homes over the next few years, and the potential to deliver modern homes quickly and sustainably is an attractive proposition.
Stephen Stone, a board member of ilke Homes who floated FTSE 250 housebuilder Crest Nicholson in 2013 while CEO, said: “This announcement proves that there is a shared ambition among the public and private sectors to find innovative solutions to structural issues that have dogged the construction and housebuilding industries for decades. This new funding will help us create hundreds more highly-skilled, green jobs for an economy that is gearing up for a Green Industrial Revolution.”
The monies will also be used to scale-up production and accelerate capacity to deliver up to eight homes a day, up from two today – all helping to bring down manufacturing costs in the process. The homes delivered are also highly energy-efficient, with the company, as part of its ilke ZERO offering which was launched this year, able to deliver thousands of zero-carbon homes a year for a mix of institutional investors, private developers, housing associations and councils.
Catriona Simons, Group Chief Executive at The Guinness Partnership, adds: “Our investment in like Homes demonstrates our continued commitment to delivering high-quality, energy-efficient homes as quickly as possible, to those who need them most. Having partnered with the company on two sites already, we have seen first-hand the benefits ilke Homes’ method of delivery affords – which will help ensure we can continue to play an important and active role to address the housing crisis.”
Speaking about the investment plans, Government MMC Champion Mark Farmer said: “True zero-carbon homes just cannot be delivered at scale through using traditional construction methods and our constrained skills base, we therefore need to move quickly to less resource intensive and higher performing pre-manufactured solutions. However, alongside government support, the private sector increasingly needs to recognise the investment case for change and that is why this announcement as a truly joint public and private financing package for a key market disruptor is so welcome.”
For more information visit:
www.ilkehomes.co.uk
Images:
01. The homes being delivered by offsite methods are of huge sustainability, quality and customer appeal
A DIFFERENT KIND OF LIVING
'House by Urban Splash’ has created its first Row House homes – a new typology designed by architect shedkm – and builds upon the hugely successful Mansion and Town House concepts.
The designs for the first Row House homes were unveiled at the start of the year with the offsite prototype developed in the ‘House by Urban Splash’ factory in Alfreton, East Midlands, before being delivered to the East Float area of the Northbank neighbourhood – a community that is being developed in partnership with Peel L&P at Wirral Waters in Merseyside.
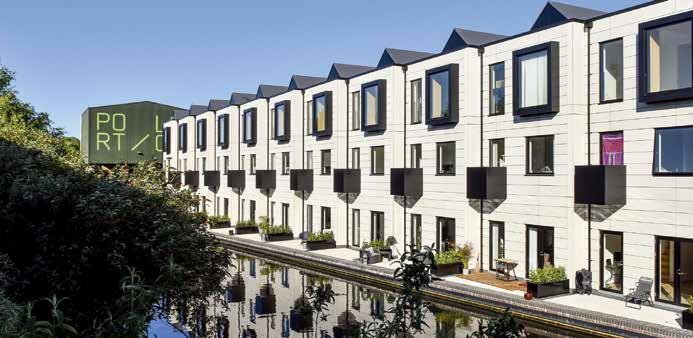
Chris Shaw, Delivery Director at ‘House by Urban Splash’ explains: “Row House is the third residential typology in our award-winning portfolio and comes from our experience in recent years in using MMC to create hundreds of sustainable, brilliantly-designed homes across the country. To date, we have completed our three storey Town House homes and Mansion House apartments in places like Manchester, Birmingham, Salford and North Shields – it’s a pleasure to now bring more of our pioneering architecture to a new area of the country.” Hazel Rounding of Liverpool-based shedkm – designers of the Town House and Mansion House products – adds: “Row House is a pioneering new design for homeowners, featuring our most innovative thinking around modular layouts, with efficient internal space and open-up features that offer additional outdoor living space – a concept that will suit the needs of modern buyers spending more time at home. We are delighted to see them become a reality at the Wirral.”
The first three storey Town House homes have also been delivered to Wirral Waters, with all of the homes occupying a waterfront position overlooking East Float Dock, a stone’s throw from the River Mersey. Richard Mawdsley, Director of Development for Peel L&P’s Wirral Waters, said: “The arrival of these first homes at East Float is yet another significant example of progress at Wirral Waters. Together with the other developments along Northbank, we are creating a new mixed, sustainable neighbourhood – a
1
community for all. These innovative homes will sit alongside new public realm, including pocket parks and dockside walkways, helping to support healthier communities with a focus on fresh air and active travel.”
Town Mansion & Row House Success
‘House by Urban Splash’ is an innovative concept delivering radical new products to the UK housing market. Using offsite manufacture and customisation, House enables customers to design their own homes, selecting from a variety of options to tailor homes to suit their lifestyle. The last year has seen the completion of sites at Port Loop and Piercy Street, with others progressing in Birmingham, Manchester, Wirral, and Cambridgeshire.
Building on the success of the volumetric Mansion and Town House product – now in production for five years, and recently launched in improved Mark 3 guise – the House core range has expanded to
encompass a variety of new homes designed by shedkm. As a sister to Town House, Row House uses the same modular technology, but repackaged in a smaller, simpler and more affordable format, allowing higher densities.

At Port Loop, Birmingham, houses are arranged in terraces enclosing a shared garden square. This provides a generous communal amenity space of much greater size and quality than individual private gardens would allow and has been instrumental in fostering a sense of community among residents. Customer choice was again a key part of the brief, but the emphasis was on allowing customers to choose any size of home on any plot. The new Row House homes will form the third phase of regeneration at Port Loop and will stand adjacent to another phase of Town House homes – 105 of which have already been created at the waterside site close to Birmingham city centre. Chris continues: “In two short years, Port Loop has completely transformed. What was once a disused, rundown former industrial patch of land, has fast become a vibrant, award-winning place in which hundreds of people now live, work and play.

“We continue to evolve our product portfolio, introducing new homes to the market to help more people across the country live in brilliantlydesigned houses and communities. After the success of our Town House family homes, and our Mansion House apartments – the first of which have sold out in Manchester – we have created Row House for customers who want something different again. We look forward to seeing it become a reality at both Port Loop and Wirral Waters.”
2
3
For more information visit:
www.shedkm.co.uk www.housebyurbansplash.co.uk
Images:
01-02. Homes at Port Loop 03. One of the first Row House homes being craned in by the River Mersey at Wirral Waters 04. Northstowe is fast developing with modular housing
NORTHSTOWE – THE MODULAR NEIGHBOURHOOD
Progressing its new development at Inholm at Northstowe, Cambridgeshire, ‘House by Urban Splash’ delivered 43 homes in 43 days. “This is a wonderful day,” said Eva Hogan, Sales Manager at Inholm. “We’re so excited to complete on this area of Inholm. We’ve created the homes using modern methods of construction (MMC) – meaning they’ve come to life quicker and more efficiently than traditional build. The MMC process is slick, with a precision manufacturing approach that means the homes are created to a high design specification. Now all the homes are in-situ, it’s rewarding to see how we’ve rapidly transformed this site into a brand-new neighbourhood. “This is a futureproofed new take on suburbia which is proving extremely popular. It’s not about cul-de-sacs, or places that accommodate cars over people: our blueprint is an alternative which promotes great design and healthy living for the future of all residents. As the world has changed so much over the past 18 months, we’re creating a neighbourhood which accommodates work and play – in an environment created to enjoy life.”
4

OFFSITE CONSTRUCTION – SHOWCASING THE LATEST INNOVATIONS
Futurebuild – the built environment event that’s championed sustainable construction for the past 16 years – will return to the ExCeL London from March 1–3, 2022, with an Offsite Section giving visitors the opportunity to meet with leading offsite construction professionals.
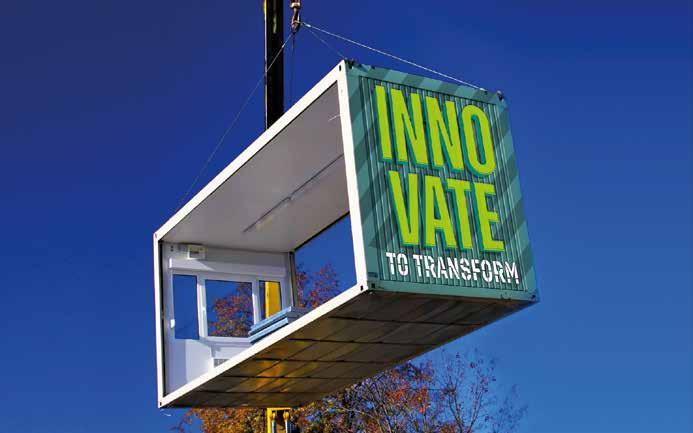
As longstanding partners and publishers of Offsite Magazine and Offsite Hub and organisers of Offsite Expo and Offsite Awards — the Explore Offsite team will partner with Futurebuild to give visitors a comprehensive and contemporary perspective of this rapidly evolving sector. Other leading partners, such as the trade association for UK precast concrete manufacturers and members of the supply chain, MPA British Precast, the Structural Timbers Association (STA) and the Light Steel Frame Association (LSFA) will also explore the use of offsite technology to effectively construct a better and more sustainable environment.
“Futurebuild champions a sustainable built environment by cultivating cross sector collaboration and working with experts in their field, such as Cogent Consulting and Explore Offsite,” explained Martin Hurn event director at Futurebuild. “Offsite construction will be a key player in reducing emissions, delivering more sustainable structures and helping us to reach net zero goals. This partnership will enable us to accelerate change, giving visitors the opportunity to interact with these game-changing technologies and processes.”
Futurebuild 2022’s accompanying world-class knowledge programme will feature leading UK and international offsite manufacturers and thought leaders from all aspects of the offsite arena. Attendees can see presentations from a range
Mark Farmer
Chair, AIMCH stakeholder group, Advanced Industrialised Methods for the Construction of Homes (AIMCH) Richard Hipkiss
Development Director, Modular and Portable Building Association Jenny Burridge
Head of Structural Engineering, The Concrete Centre Stewart Dalgarno
Project Director, AIMCH and Director of Product Development, Stewart Milne Group Andy King
Group Technical Director, Wernick Buildings and Technical Committee, Chair, Modular and Portable Building Association
of suppliers specialising in broad spectrum of panelised, volumetric modular, pod and prefabricated mechanical, electrical and plumbing solutions. The Offsite Seminar Sessions will explore the use of offsite technology to effectively construct a better, sustainable environment. The presentations will also show how the industry can respond to unprecedented demand through greater investment in lean manufacturing systems.
“We often find that built environment professionals know what to do to reduce emissions, they now need to know how to do it and how to do it at scale,” adds Martin Hurn. “By featuring speakers who are pioneers in sustainability, visitors have the opportunity to learn from practical examples and case studies that they can use to create their own action plans.”
Leading partner, Advanced Industrialised Methods for the Construction of Homes (AIMCH), will present at the offsite stage about the key outcomes from its three-year project. Mark Farmer, Chair of AIMCH will discuss how AIMCH is transforming how we build homes and share its outcomes and learnings to educate the industry. AIMCH focuses on how prototyping, future factory planning, technology and standardisation can help tackle industry challenges, such as skills shortages, an ageing workforce and low affordability.
Visitors can also attend a talk on volumetric modular buildings from the Modular and Portable Building Association (MPBA), which explores how a confused construction chain could be slowing construction progress. By removing the complexity of modern construction methods, industry consultants can accurately report on the embodied carbon figures that are relevant to each business and compare these against more traditional construction methods. Richard Hipkiss, Development Director at MPBA, will consider if volumetric modular buildings can deliver a net zero future for construction. His colleague, Andy King, Chair at MPBA, will discuss a manufacturer’s perspective on the volumetric building sector and how carbon can be embodied to improve net zero practices.
BRE will speak about the importance of volumetric module accurate testing. Without supporting evidence, structural tests on a single building section or in a test laboratory cannot predict structural behaviours of a fullscale building. Right now, it is not clear whether significant changes can occur between the testing techniques and reality if results are too conservative or not conservative enough. The seminar will discuss in an open forum the state-of-the-art knowledge about the similarities and differences between a module’s structural static and dynamic behaviours and buildings constructed using combinations of linked modules.
Taking place from March 1 – 3 2022, Futurebuild will connect specifiers, decision makers and disruptors with major brands and start-ups, attracting over 20,000 senior professionals from across the built environment. As the home of innovation, the event is the perfect opportunity for the industry to meet and collaborate, to achieve the transformational change needed if the built environment is going to reach net zero.
To discover more about the Offsite Section in partnership with Cogent Consulting and Explore Offsite, visit: www.futurebuild.co.uk/offsite/
PARTNERS: