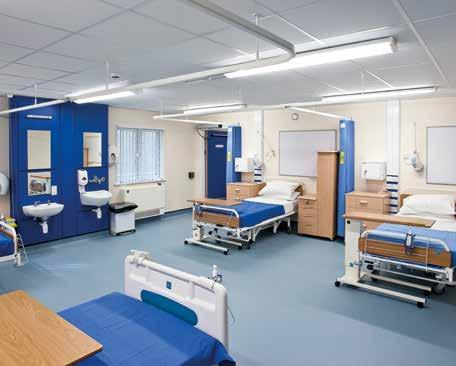
5 minute read
Modular Offsite a green construction option
With world leaders recently meeting at COP26 to formulate plans to tackle climate change, Rollalong’s Managing Director Steve Chivers, says offsite construction should be considered as part of the solution to this global issue.
It’s clear now that we are approaching the point of no return when it comes to reversing the damaging effects of our CO2 emissions on our environment. The construction industry has to step up and play its part. According to the Technology Strategy Board the construction, operation and maintenance of the built environment accounts for 45% of total UK carbon emissions (27% from domestic buildings and 18% from non-domestic buildings).
To reduce this negative impact, we must find new, greener ways of constructing buildings and we have to design buildings with a low or zero carbon footprint. This means adapting from the bricks and mortar, ground up approach which the industry has adhered to for centuries and adopting modern methods of construction (MMC) instead. We adopt three key steps to deliver clients’ key targets in relation to sustainability. Where clients set building design aims to exceed current zero carbon building standards, the following areas are considered. Firstly, the fabric first approach with all our buildings – the highly insulated walls, floors, roof, the highperformance windows and doors, and the airtightness of the building fabric mean that all Rollalong buildings exceed current Building Regulations as standard.
1
Next is energy efficiency. The use of mechanical ventilation heat recovery systems (MVHR), wastewater heat recovery systems (WWHR), LED lighting and efficient water fittings further lower emissions in all our buildings. We then introduce renewable energy technologies: we start by replacing the fossil fuel gas boiler with highly efficient air source heat pumps to provide space heating and hot water. Heat pumps require just a third of the energy of conventional heating systems, and they use electricity to compress the energy in the outside air to warm our buildings. Finally, our buildings can be fitted with solar photovoltaic (PV) panels to generate their own electricity to offset energy use to net zero carbon targets and beyond.
The embodied carbon in modular buildings is lower than that of traditionally constructed schemes. We are targeting a 75% reduction in the whole-life carbon emissions of its buildings by 2030. Because buildings created in a factory setting are manufactured to precise requirements, MMC can reduce waste on-site by up to 90% compared to traditional construction, and much of this waste can then be recycled rather than sent to landfill. At least 95% of our waste is recycled.
Our building projects also have a smaller impact on the local environment on site. Using MMC, buildings are manufactured in highly controlled conditions in a factory. Offsite methods generate significantly less noise and less dust on-site. Modular construction also reduces vehicle movements to and from the construction site, so the toxic fumes and carbon emissions are reduced too. A building site using offsite modular methods reduces vehicle movements to and from the site by up to 90%, so heavy traffic created by large, dirty trucks can be avoided, and disruption to local residents is kept to a minimum.
What’s more, it’s considerably faster to build a modular building than it is to build from the ground up using bricks
2
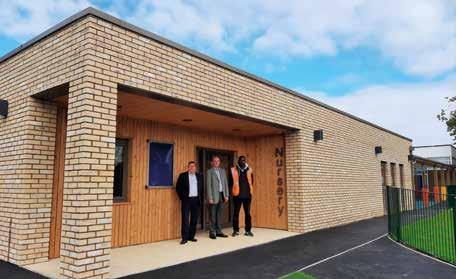
and mortar – up to 50% faster. As our buildings take less time to manufacture and install, we use less energy. We watched COP26 with interest and we look forward to further announcements of UK Government support for MMC as a construction method which can help the UK to achieve its net zero target by 2050.
For more information visit:
www.rollalong.co.uk
Images:
01-02. Modular manufacture are at the forefront of newbuild education and healthcare buildings with reliable quality and delivery timescales
“The role that modular construction can play in reducing operational carbon centres on the better build quality derived from manufacturing practices in a controlled environment, says Antonio Lopez of Stelling Properties. “The quality assured factorycontrolled production and installation processes provide a greater certainty regarding the thermal performance of the unit due to the integrity of insulation and low air leakage.
Indeed, volumetric buildings have been achieving airtightness levels of <5m3/m2/hour against the traditional building targets of 10.
“The role volumetric construction plays in reducing embedded carbon might not be immediately obvious, however it can contribute significantly to the less carbon being used in the construction process. Let’s first look at the operatives employed in the construction process, the average daily commute for workers in the UK is a round trip of 23 miles per day, based on this the vast majority of the operatives will live within 10-12 miles of the factory unit, which in conjunction with car share schemes, the use of public transport and for the fit and energetic cycling to work, there is a reduction in the carbon created by transporting staff to different site locations.
“Good design is a key factor in the success of modular construction, at the design stage material wastage can be engineered out of the construction process due to the certainty over the tolerances within the modules, materials can either be ordered cut to size directly from the manufacturer alternatively standard size products like plaster board are optimised to reduce the material wastage, this helps significantly in reducing the reported 100 million tons a year of waste the UK construction industry creates and importantly eliminates the carbon used in producing the wasted materials.
Within the controlled environment of the factory, it is easier to ensure that any waste materials are where possible recycled, as it becomes a part of the standardised manufacturing process.
“The materials used in the construction, will still need to be delivered to site, however with modular construction, there is one delivery point for multiple sites, meaning greater efficiency in delivery logistics, with materials for use on several sites being delivered to one facility reducing frequent multiple site deliveries.
Unlike most construction sites, factories can provide safe, secure, dry, and environmentally controlled warehousing for materials, allowing for the efficient delivery of materials, further reducing supply chain mileage by reducing the number of deliveries. Modular construction offers several benefits over traditional construction and should be considered as an integral element in making the construction industry more sustainable, and better placed to deliver the net zero buildings and homes of the future.
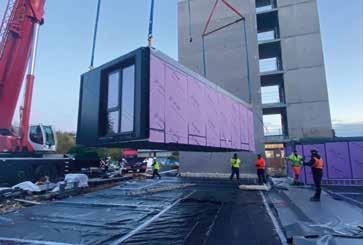