




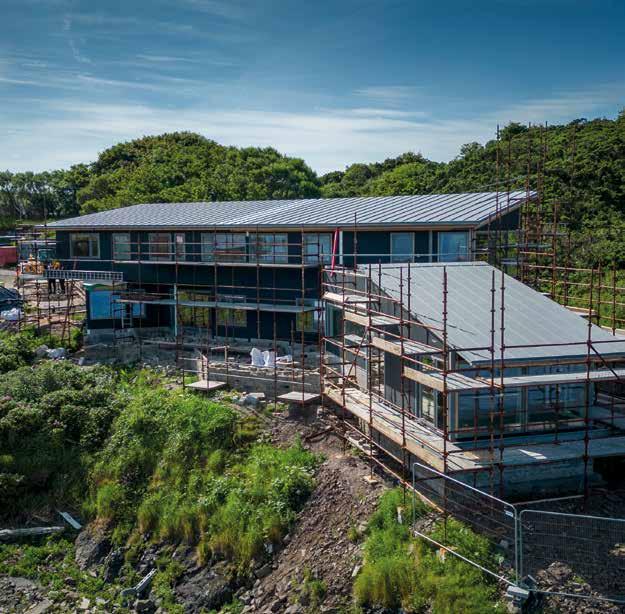



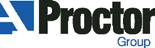


FRONT COVER: VOLUMETRICTM
FRONT COVER: VOLUMETRICTM
PRINTED ON: FSC Mix paper by Buxton Press
PUBLISHER: Volumetric Magazine is produced by Radar Communications: ©Radar Communications Ltd.
Radar Communications Ltd, 101 Longden Road, Shrewsbury, Shropshire, SY3 9PS
T: 01743 290001 www.radar-communications.co.uk
SUBSCRIBE TO RECEIVE: www.volumetricmagazine.co.uk
ADVERTISING ENQUIRIES PLEASE
CONTACT:
Julie Williams // T: 01743 290001
E: julie.williams@radar-communications.co.uk
SEND US YOUR NEWS: T: 01743 290001 E: info@radar-communications.co.uk
DISCLAIMER: The content of Volumetric Magazine does not necessarily reflect the views of the editor or publishers and are the views of its contributors and advertisers. The digital edition may include hyperlinks to third-party content, advertising, or websites, provided for the sake of convenience and interest. The publishers accept no legal responsibility for loss arising from information in this publication and do not endorse any advertising or products available from external sources. The publisher does not accept any liability of any loss arising from the late appearance or non-publication of any advertisement. Content including images and illustrations supplied by third parties are accepted in good faith and the publishers expect third parties to have obtained appropriate permissions, consents, licences or otherwise. The publisher does not accept any liability or any loss arising in the absence of these permissions for material used in both physical and digital editions. No part of this publication may be reproduced or stored in a retrieval system without the written consent of the publishers. All rights reserved.
Following the launch of the latest addition to its portfolio – FAMILYHAUS™ – VOLUMETRIC™ now offers a long-term, sustainable housing solution that could provide a lifeline to vulnerable families and recognises the demand for high-quality interim homes.
News and project developments from the volumetric modular and wider construction sector that you may have missed including: Algeco, BoKlok, Connect Modular, Reds10, McAvoy and more.
ilke Homes is the Yorkshire-based company that has become a flagship name in the delivery of a new generation of energy efficient, low carbon, newbuild modular homes. We caught up with R&D Director Nigel Banks to talk about the latest developments.
Richard Hipkiss, Development Director of the Modular and Portable Building Association (MPBA) considers the significant role volumetric modular can play in achieving new building regulations and carbon neutrality. 26
Lewisham Exchange has been a hugely positive project showcasing offsite construction and brick slip cladding technology. 28
Volumetric modular provider Algeco was part of the team that recently completed the UK’s first net zero restaurant for McDonalds at Market Drayton, Shropshire.
The latest addition to the Tekla Structures constructible modelling software was on show recently at Offsite Expo, with a new Volumetric Modular Tool helping streamline the detailing process.
A newbuild 48-bed critical care building delivered to the prestigious John Radcliffe Hospital in Oxford, saw a range of facilities delivered including five storeys of bespoke volumetric modular accommodation.
Offsite Expo 2022 was a resounding success with the UK’s most important offsite construction event once again proving to be a central hub to network, do business and learn about volumetric modular technology.
A new Modular Research Centre in the Czech Republic is showcasing an innovative use of modular structures by altering conventional building systems and pushing the boundaries of standard modular architecture.
Out of recessions come game-changing offerings, says Andrew Shepherd, Managing Director, at tech-driven modular manufacturer TopHat.
Following the launch of the latest addition to its portfolio – FAMILYHAUS™ – VOLUMETRIC™ now offers a long-term, sustainable housing solution that could provide a lifeline to vulnerable families and recognises the demand for high-quality interim homes.
As a specialist manufacturer of modular housing solutions, VOLUMETRIC™ has seen incredible success over the past couple of years. The award-winning company has seen its innovative MODULHAUS™ range go from strength to strength, delivering modular homes to projects across the UK.
VOLUMETRIC™ developed its range to help mitigate growing pressures on the UK social housing market. Utilising expert offsite knowledge, the VOLUMETRIC™ team has garnered significant industry recognition for their high-quality, fully-fitted modular homes designed to meet rapidly changing accommodation needs.
The VOLUMETRIC™ single-occupancy unit, SOLOHAUS™, achieved high acclaim, winning the coveted Winner of Winners prize at the 2021 Offsite Awards. Further success followed with a win for their double-occupancy offering, DUOHAUS™, in the Product
1
Innovation category at the 2022 Offsite Awards, whilst being a finalist in several other industry Awards. This year, the company expanded its manufacturing facilities and storage capacity allowing for speedy and efficient delivery of homes from stock at short notice.
The company, working with local authorities, charities, and councils across the country to combat the growing housing crisis, has already installed over 200 fully-fitted homes to areas of high need. Having designed a proven solution to meet the rising numbers of single people suffering homelessness in the UK and a costeffective accommodation solution for keyworkers, VOLUMETRIC™ now offers a high-quality, energy-efficient solution to the latest housing crisis to sweep the UK.
Figures shown in the English Housing Survey: a segmentation analysis of private renters, a yearly report
collated by the government, evidence that rising living costs are putting vulnerable families in the private renting market at high risk of eviction. Increased rent prices and the removal of protections put into place during COVID-19 have seen a 39% increase in bailiff evictions between April and June this year. According to the survey, those classified as ‘struggling families’ represent the highest proportion of households (with dependent children) who will likely need to move from private rental to social housing. This will put further demands on limited social housing stock and increase the already surging waiting lists, placing increased pressure on local authorities, particularly in areas already suffering from housing shortages.
‘Struggling families’ make up approximately 473,000 UK households, with those figures likely to grow. Reported to be most likely to experience overcrowding, the survey also states that 43% of these families live in homes deemed unfit for purposes that fail to meet the Decent Homes Standard. Major problems reported included issues with dampness, mould, and condensation. As more families become at risk of being forced out of the private rental market, local authorities need a fast and reliable long-term solution to what will undoubtedly mean more strain on the already over-subscribed UK social housing stock.
Welcome to FAMILYHAUS™ Following the launch of the FAMILYHAUS™ model at Offsite Expo2022, Victoria Moore, VOLUMETRIC™ business development manager, said: “It has been fantastic to see the range developing over the past 12 months. We have already proven the success of our single and duo-occupancy homes, and it feels like
now is the time to look at the housing needs of vulnerable families. We have designed FAMILYHAUS™ to exceed performance requirements, offering high-quality, energy-efficient homes in areas where a rapid solution is needed for those at risk.
“The positive reactions to our launch have been great and speaking to people about the benefits FAMILYHAUS™ provides gives us an opportunity to show the difference these homes can make. We are now looking forward to working with local authorities and registered providers to deliver our FAMILYHAUS™ units across the UK.”
Designed to accommodate two adults and two children, FAMILYHAUS™ comes fully furnished with quality interior fittings and energy-efficient white goods. BOPAS-certified, futureproof for Building Regulation changes, and LABC Assured, with a 60-year
design life, the model exceeds the Future Homes Standards, offering assured quality throughout its lifetime. VOLUMETRIC™ offer fast and reliable delivery and installation, utilising their advanced production facility to manufacture offsite. Provided on a turnkey basis, all VOLUMETRIC™ modular homes can be configured to provide mixed scheme occupancy on the basis that all modules in the range are fully interoperable. Ongoing maintenance is straightforward and hassle-free, with a simple to use Operation and Maintenance Manual provided with each module, along with a Home User Guide. The system sits on six low-impact foundation pads to minimise groundwork and requires only electric, water, and waste connections.
VOLUMETRIC™ has developed a highly-focused energy-efficiency strategy for all modular homes in the range, including FAMILYHAUS™,
which offers exceptional heat, thermal, and acoustic performance. All modules are delivered to the site in one load, minimising site traffic.
To optimise energy efficiency, VOLUMETRIC™ also supply and fit purpose-built energy centres. An innovative solution to energy supply, each centre can meet the requirements of up to six FAMILYHAUS™ homes. Once installed, the energy centre uses intelligent technology to digitally connect to each home, allowing for instant management of energy requirements, hot water, and heating, all minimised by exceptional module fabric energy efficiency performance in terms of airtightness and thermal performance. Modules have mains connection, and energy generated via optional solar panels during the day by the energy centre can be stored in battery cells until required. Surplus energy can be sold back into the grid, carbon offsetting and creating net zero living.
Secure, robust, and cost-effective, FAMILYHAUS™ represents an opportunity to provide comfortable, safe homes for families facing uncertain futures. The expert team at VOLUMETRIC™ continues to innovate and develop by creating modular solutions to meet current housing needs and offer long-term permanent or relocatable solutions to meet future demands.
For information on FAMILYHAUS™ or to request a brochure visit: www.volumetric.co.uk
Images: 01-03. FAMILYHAUS™ solves many problems surrounding the poor quality and lack of accommodation for struggling families
Legal & General Modular Homes (LGMH) have been selected as preferred developer for the major Wolverhampton residential Canalside South scheme.
housing across the West Midlands, having signed a £4billion partnership agreement earlier this year with West Midlands Combined Authority (WMCA).”
LGMH has been selected by the City of Wolverhampton Council as its preferred developer from a strong field of contenders for one of the largest city centre residential development opportunities in the Midlands.
The Council has now entered into an exclusivity agreement with LGMH, to build around 400 new homes, subject to planning approval, at Wolverhampton’s Canalside South – a former industrial site benefiting from frontage onto the Wyrley & Essington Canal and the Wolverhampton Branch of the Birmingham Main Line Canal.
Precision-engineered in LGMH’s modular factory in Leeds, every modular home will include an air source heat pump, PV panels and electric vehicle charging point as standard – all supporting the city’s climate change commitment to be net carbon neutral by 2041. In the current cost of living crisis, a LGMH home will have a major impact on individuals energy bills as the homes are 60% more efficient to run for the homeowner than a Building Regulation compliant newbuild home and the apartments are up to 30% cheaper to heat and run than the average apartment.
The 17-acre waterfront development opportunity sits on the eastern edge of the city centre and is made up of
the Canal & River Trust-owned former Crane Foundry site, and the Council’s former British Steel site and its land off Qualcast Road – all brought together under a collaboration agreement designed to ensure a comprehensive development takes place.
The company has committed to delivering significant social and economic benefits in accordance with the Wolverhampton Charter. This includes delivering local labour and supply chain opportunities, enhancing skills and employability, creating apprenticeships, promoting cohesion and activities within the community, and supporting health and wellbeing.
Rosie Toogood, CEO of LGMH said: “I am delighted that LGMH has been selected as preferred developer by the City of Wolverhampton Council to deliver this major residential development. In the face of a chronic housing shortage, steep energy bill increases, and a looming climate crisis deadline our mission is to reduce costs to consumers and the environment by producing the best quality homes in the most efficient way possible. The City of Wolverhampton shares this ambition and together we are excited to deliver a first-class community for Wolverhampton and the West Midlands. This latest development further demonstrates its commitment to delivering regeneration and
1City of Wolverhampton Council Deputy Leader and Cabinet Member for City Economy, Councillor Stephen Simkins, added: “Legal & General has a strong background in the property sector, investing in urban regeneration, financing affordable housing and building modular homes. We have now secured a prestigious developer with the expertise to deliver this large and exciting opportunity at Canalside South and, through our Canalside Delivery Partnership with the Canal & River Trust, we are determined to realise the scheme’s full potential. Strong partnership working is delivering £4.4billion of investment across Wolverhamptonand by pooling our resources with the Canal & River Trust we believe we can bring about a nationally significant development alongside one of the most historic stretches of canal in the country.”
Canalside South is located minutes away from the city centre and the award-winning £150million transport Interchange, providing easy access to the tram, road, rail and canal network. The overall vision for the Canalside masterplan is the delivery of around 1,000 homes to meet both the city and wider region’s housing needs, with sustainability and placemaking at its heart.
For more information visit: Images: 01. LGMH will play a part in revitalising Wolverhampton with low carbon volumetric modular homes
www.legalandgeneral.com/modular-homes/
Offsite manufacturing specialist, McAvoy Group has marked its 50th year in business with a continued return to sustainable profitability, according to its latest set of consolidated group accounts.
The Lisburn-based company has reported a rise in turnover to £71.5million for the 13-month period to 31 May 2022, compared to £23.8million for the six-month period ending April 2021. Meanwhile, the company generated an EBITDA of £6.2million for the same period, compared to £2.4million for the period ending April 2021. The company strengthened its balance sheet on 31 May 2022 with net debt of 0.8 x EBITDA and equity of £4.9million.
McAvoy Group’s continued return to sustainable profitability and underlying business growth has included several key project successes including the world’s first International Baccalaureate special free school for children with autism at Cavendish, a Low Carbon Pathfinder School for the Department for Education at Redhill and the securing of a significant ten-year rental contract at University Hospitals Birmingham NHS Foundation Trust.
During the most recent financial period, McAvoy Group announced a significant multi-million expansion
programme that included the launch of a new SmartSpace semi-permanent modular fleet that will ensure McAvoy has one of the newest modular fleets in the UK and Ireland. The investment will more than double the capacity of the company’s semi-permanent fleet for rental and will include the creation of approximately 50 new jobs over the next three years.
CEO, Ron Clarke said: “The group is experiencing robust and continued interest in its proposition, supported by favourable structural tailwinds and the Board, with the continued support of our shareholders, has embarked upon a strategic growth plan which includes the creation of a modern and highly flexible rental fleet. Designed and built to enhance energy and fire protection standards, SmartSpace provides our customers with sustainable space solutions which will allow significant scope for future value creation. Whilst recognising that the trading environment will remain challenged by ongoing geopolitical tensions and inflationary cost pressures, we continue to see strong
underlying demand for the company’s sustainable building solutions.”
McAvoy is one of the UK and Ireland’s market leaders in the precision manufacture and delivery of high-quality permanent and semi-permanent modular buildings. Its adaptable and sustainable space solutions are sought after in sectors including health, education, commercial and infrastructure. Innovation continues to be a central part of the company’s activities with several ongoing R&D projects following its involvement in Seismic I and Seismic II which developed a new componentised, platform-based approach to manufacturing and construction, which can be adopted by multiple manufacturers.
For more information visit: www.mcavoygroup.com
Images:
01. Ron Clarke, CEO, McAvoy Group
02. Cavendish School, Redhill, a Low Carbon Pathfinder School
Leading modular housing company ilke Homes has begun on-site to deliver 221 affordable modular homes in Southend-on-Sea, Essex on behalf of The Guinness Partnership.
Of the 221 new homes being delivered, 54 are specified to be zero-carbon – meaning they will generate their own source of energy, helping to drastically reduce emissions produced by utilities such as electricity and heating. The development is owned by The Guinness Partnership, a registered provider and shareholder in ilke Homes, and is being delivered with support from Homes England. ilke Homes is scaling up its operations and delivering over 10,000 sustainable homes over the next five years.
ilke Homes, a company that has grown its pipeline to 3,500 homes, secured the site in March 2021 and successfully secured detailed planning in September 2021 under its ‘turnkey’ offering, by which it acquires land, gains planning permissions, develops the sites and delivers the factory-built homes. The announcement marks the company’s continued expansion into the South East region, where it is already committed to delivering in excess of 1,200 homes across five sites.
It follows news that ilke Homes, in partnership with Octopus Energy and Gresham House, are rolling out the
UK’s first homes to guarantee residents zero energy bills. The three pioneering British tech firms have launched the partnership on a site in Stanford-leHope, Essex where ilke Homes is delivering the UK’s largest zero-carbon housing development.
Precision-engineering techniques mean that ilke Homes will be able to deliver the scheme's factory-built homes in half the time of traditional methods. By manufacturing offsite, the homes delivered will be of the highest quality as ilke Homes is able to benchmark standards at numerous stages of the build cycle. By harnessing artificial intelligence, robotics, and digital design, the modular housing company is capable of creating homes that are incredibly well insulated, meaning less heat escapes, consequently reducing bills.
Matt Suggitt, Development Director South East at ilke Homes, said: “We are incredibly pleased to be delivering yet another affordable and sustainable housing scheme in the South East, bringing our pipeline to over 1,000 homes across five sites in the region. We look forward to delivering this
scheme for The Guinness Partnership, in order to provide a truly sustainable and well-designed community with much-needed, high-quality housing in Southend. By providing ZERO carbon homes, employing the use of lowcarbon technologies, ilke Homes is actively helping Southend-on-Sea City Council, who have declared a climate emergency, reduce carbon emissions associated with the construction and operation of new-build homes.”
Jon Milburn, Group Development Director at The Guinness Partnership, added: “Guinness is pleased to be working with ilke Homes on this, the second scheme under our partnership, which will deliver much needed affordable homes for local residents.”
Work is already underway on-site, with completion expected in Autumn 2024.
For more information visit: www.ilkehomes.co.uk
Images: 01. The Guinness Partnership and Ilke Homes will bring pioneering, sustainable and affordable modular housing to Southend-on-Sea
Work has completed on Abbey Farm Educate Together Primary School in North Swindon, with the school delivered by offsite construction specialist Reds10.
recycled materials, GIFA floorboards with 50% recycled content and timber cladding, which is inherently lower in embodied carbon. Using ThriveTM, its SMART building technology, Reds10 is able to analyse energy usage and production, generating accurate data to ensure that the building is operated at maximum energy efficiency going forward.
Reds10 was appointed by the Department for Education (DfE) as principal contractor to design and build the school, which is part of the DfE’s four-year £3billion Offsite Schools Framework and will be run by the Educate Together Academy Trust. The Offsite Schools Framework was established in 2020 as part of the Government’s drive for greater adoption of MMC to modernise the industry and increase efficiencies, cost savings and innovation within capital building programmes.
The construction of Abbey Farm ET Primary School began in May 2021, and the new building has opened its doors in September 2022, catering to 460 pupils from the local community. Located off Lady Lane, the school is set on a 4.6-acre site and is part of a wider residential-led mixed-use development by Redrow. One of the stand-out achievements of the project is that the building was designed as net zero carbon in operation ahead of the DfE’s sustainability Output Specification (S21) official launch. S21 was introduced under the new
construction framework in November 2021, calling for all new school buildings in England to reach net zero operational carbon.
MMC directly benefits the delivery of school construction projects, through reduced embodied carbon, quicker delivery programmes and less trades on site, which minimises disruption. Reds10 completed the majority of the school building offsite in its factory. In fact, the project achieved 87% pre-manufactured value (PMV), which is 2% higher than their commitment on the framework, alongside minimal waste using MMC with 90% diverted to landfill, and over 100% reduction in carbon emissions under Part L2A building regulation standards for energy efficiency.
The building, which is net zero carbon in design, includes enhanced sustainability features such as air source heat pumps and photovoltaics, both mechanical and natural ventilation to maintain excellent internal air quality, aluminium door and window frames made from
1Nikki Buglass, Trust Development and Marketing Manager at Educate Together Academy Trust said: “Abbey Farm ET Primary School has been in the pipeline for several years and it’s amazing to see this wonderful space about to open its doors to pupils. Reds10 have been instrumental in making this happen and their commitment to it has been incredible. In comparison to projects I am running in tandem, the modular nature of the build has reduced disruption to delivery, with regards to materials and labour shortages and time lost to inclement weather. The quality of the build is fantastic, with several of my subcontractors and the Fire Safety Officer, commenting on the excellent standard of work. What struck me the most was their process – it seems like yesterday that the site was just a field and now here we are with a finished building. The pace has been simply breath-taking.”
Joe Shepherd, Education Sector Lead of Reds10, added: “As Abbey Farm Educate Together Primary School welcomes pupils for the new school year from September, it is an exciting milestone for us, being our first school to be completed for the Department of Education’s Offsite Schools Framework. It shows that successful delivery of sustainable school buildings at pace and to budget is possible, through harnessing the power of MMC. As project lead, we were able to collaborate closely with
the DfE, local authorities, stakeholders and the design team to bring to the fore the full potential of what MMC can offer to deliver a modern, sustainable and nurturing learning environment for pupils to enjoy for many years to come. Abbey Farm ET Primary School sets a new standard of performance for school buildings and we are proud of our central role in delivering the next generation of offsite schools.”
Pushing the architectural boundaries, Reds10 is challenging the ‘one size fits all’ perception of modular construction and instead creating amazing buildings with high architectural integrity in partnership with architectural practices. Its projects range from permanent to temporary developments in the education, healthcare, residential, defence and leisure sectors, all delivered from Reds10’s own manufacturing facility in East Yorkshire.
Claire Wakelin, Head of Education at HLM Architects, which designed the new school building, said: “We’re very proud to have been the lead
designer for this fantastic new school. The school engagement process took place during the 2020 lockdown but, using our digital tools and consultation experience, we were able to quickly form close working relationships with the DfE and Trust teams. Our strategic design approach was centred on the creation of a high-quality, safe and secure environment for pupils, maximising the opportunity for learning and socialising. Biodiversity
was also a major inspiration, resulting in an environment that seamlessly integrates into the surrounding landscape.”
For more information visit: www.reds10.com
Images: 01-02. The Abbey Farm Educate Together Primary School project achieved 87% pre-manufactured value
Our AluSpace Interior Screening System is designed to divide or delineate both residential and commercial spaces, while at the same time providing an effective acoustic barrier.
Choose from hinged single, double doors, pivot or sliding doors to accompany our stylish fixed glazed screen. This flexible and versatile system provides almost limitless design options whilst requiring minimal maintenance. AluSpace will provide many years of assured, reliable and robust performance.
For more information visit smartsystems.co.uk/aluspace
E sales@smartsystems.co.uk
Beattie Passive recently won two prestigious industry awards in as many weeks and continues its fast recruitment drive.
enough renewable energy to power the buildings throughout the entire year. As a result, these homes don’t just use less energy – they create their own.
The Norwich-based Passivhaus specialist was recognised at the Inside Housing Development Awards for the affordable social housing scheme it delivered in Llangan, Wales, with Flying Factory partner, Canna Developments, for Newydd Housing Association. Named Cwrt Canna, the judging panel were impressed by the social value inherent in the development, which included a prisoner rehabilitation scheme, training and apprenticeships.
Built by Newydd Housing Association in partnership with The Vale of Glamorgan Council, the 13 ultra-low energy, low carbon homes at Cwrt Canna have all been constructed to Passivhaus standard, which can reduce heating bills by up to 90% (with an attendant decrease in carbon emissions). As fuel costs soar and climate concerns intensify, many social housing providers are embracing Passivhaus as a preventative measure to stop their tenants falling into fuel poverty, while at the same time ensuring they meet their environmental obligations.
Beattie Passive was also named ‘Building Performance Pioneer of the Year’ at the 2022 Offsite Awards for its work with Cardiff Council to provide 48 ‘Passivhaus Plus’ certified properties for homeless families in the city. The volumetric modular homes were all built at Beattie Passive’s offsite factory, near Norwich City’s stadium at Carrow Road, before being transported to site and craned into position. The site is named HAFAN, a Welsh translation of ‘haven’, because it provides accommodation for families that have experienced homelessness in Cardiff. The homes are now occupied and Cardiff Council is providing full wraparound support services for residents. With this scheme, the Council is providing an exceptionally high standard of accommodation that will, in turn, result in a higher quality of life with better outcomes.
The net zero-rated development has been built to the ‘Passivhaus Plus’ standard, which, by definition, must not only dramatically reduce energy consumption, but also generate
Commenting on the award wins, Nathan Beattie, Commercial Operations at Beattie Passive, said: “We’re absolutely delighted to be recognised for our work with Cardiff Council and Newydd Housing Association. These schemes pushed the boundaries in terms of sustainability and social value. It was a privilege to be involved and we’re extremely proud. We would like to take this opportunity to thank everyone who worked with us to deliver these pioneering Passivhaus projects – it was a real team effort. And extra special thanks to our forward-thinking clients who have embraced the Passivhaus standard and are passing the benefits on to their residents.”
1Continuing its recruitment drive, Beattie have appointed Trevor Barnett, previously of Chesterfield Borough Council, as Sales Manager for the north of the UK and has been tasked with driving sales in the region, particularly among social housing providers.
Trevor said: “I’m passionate about finding solutions to the UK’s housing crisis, particularly in relation to social housing, and that has been the main focus of my professional studies over the course of my career. I want to be a trusted Passivhaus provider and I’ll be working with honesty, passion and integrity to add value and exceed the expectations of my clients. I’m really excited to have joined Beattie Passive and I’m looking forward to contributing towards the growth and expansion of the company and making a real difference to communities.”
In addition to announcing three new appointments on the sales side of the business, Beattie Passive has also
strengthened its senior executive and marketing teams in recent months. Modular industry veteran Jack Randall stepped into the newly created role of Chief Commercial Officer in May, and Drew Barker was hired to head up the marketing department in March.
Commenting on the new appointments, Ron Beattie, Founder and Managing Director added: “It’s
our mission to increase awareness of the benefits of Passivhaus and make it more accessible to more people, from self-builders right through to social housing providers. We’ve been committed to Passivhaus from the start because the energy efficiency and environmental benefits are so compelling. Passivhaus can cut the nation’s energy bills, put an end to fuel poverty, improve our energy security,
and pave the way to net zero. With all these advantages, why would anyone choose to build any other way?”
For more information visit: www.beattiepassive.com
Images:
01. Low carbon homes at Cwrt Canna have all been constructed to Passivhaus standard, which can reduce heating bills by up to 90%
02. HAFAN at Ferry Road, Cardiff
Across Europe and worldwide, BeA’s fastening technology, tools and consumables are the trusted choice for some of the biggest and best known names in offsite timber and light gauge steel frame manufacturing.
Reliable products, competitive prices and the kind of service and delivery you can depend on from BeA.
01482 889 911 sales@uk.bea-group.com www.bea-group.uk
Connect Modular are bringing much needed housing to the market with several successes that have seen them appointed on the H2 New Build Housing Construction Framework by the Scottish Procurement Alliance (SPA).
produce a modular building, whilst construction waste is considerably reduced through stringent factory recycling and the proper storage and protection of materials.
The four-year public-sector framework replaces the previous H1 framework and is worth £500million. Developed by public sector construction framework provider LHC, the SPA website states that the framework has been designed to ‘provide an efficient, value for money procurement route for local authorities, social landlords and other public sector bodies for the development of new build housing projects and associated works.’
Of the twenty contractors listed on the H2 Framework, Connect Modular is the only modular construction company to be appointed, with Managing Director Jennifer Higgins saying: “This is the first time Connect Modular has been named on this prestigious framework and we are delighted. Having the endorsement of the Scottish Procurement Alliance and LHC is hugely important and will make it easier for clients to work with us.
Connect Modular was recently appointed by North Ayrshire Council to deliver six new amenity bungalows
at Afton Court, Stevenston. The development, which is supported by a Scottish Government grant, will see construction of two one-bedroom and four two-bedroom affordable homes in the heart of the Ayrshire town.
This is the second time North Ayrshire has partnered with Connect Modular to deliver new affordable housing using the innovative modular construction method. In 2019, Connect Modular constructed 31 modular affordable homes for North Ayrshire Council on Ardrossan Road, Seamill. Jennifer Higgins adds: “We are delighted to work again with North Ayrshire Council, this time to deliver greener standard amenity bungalows in Stevenston. As demonstrated at our Seamill development, our modular approach to building will minimise disruption to neighbouring residents and businesses.”
All bungalows in this new development will be constructed inside Connect Modular’s Ayrshirebased manufacturing facility with kitchens, bathrooms, plumbing and electrics all pre-fitted. The houses will then be split into modules, transported to site and craned into position for the final 10% of building work to be completed. In comparison to an equivalent, traditionally built project, up to 67% less energy is required to
Tenants of the new housing development in Stevenston should benefit from huge savings in their energy bills thanks to the bungalows’ ultra-insulated building envelope and the installation of air source heat pumps and photovoltaic (PV) panels. Work is expected to commence on site at Afton Court in winter 2022, with completion targeted for spring/ summer 2023.
Councillor Scott Davidson, Cabinet Member for Place at North Ayrshire Council, said: “We are excited to see the development of these new homes which are built in a cuttingedge and environmentally conscious manner. The new properties are a great example of the innovative thinking which is allowing us to build homes across North Ayrshire to meet the needs of our tenants and to help regenerate town centres and communities.
“We received tremendous feedback from the new homes in Seamill which were built using modular construction and I’m sure the development at Afton Court which will be just as popular. We have one of the most ambitious housebuilding programmes in the country and the new homes at Afton Court will contribute to our commitment to build 1,625 homes in every part of North Ayrshire by 2027.”
For more information visit: www.theweehousecompany.co.uk
Images:
01. Homes at Seamill constructed using volumetric modular technology
02. North Ayrshire Council staff during a recent visit to the Connect Modular Factory
SO Modular’s Operations Director, Charlotte Hale, has been named as winner of the Women in Construction category at this year’s Swansea Bay Business Awards.
The award was presented to Hale at the prestigious annual awards ceremony, held at the Brangwyn Hall in Swansea on 15 September 2022. The Swansea Bay Business Awards cover the Swansea Bay City Region, incorporating the local authority areas of Swansea, Neath Port Talbot, Carmarthenshire, and Pembrokeshire. They celebrate the achievements of the talented and successful individuals, companies and entrepreneurs that work across the region.
Charlotte Hale is the Operations Director of Neath-based SO Modular, a rapidly expanding timber frame manufacturer. The firm designs and manufactures innovative timber frame components for national homebuilders, contractors and housing associations across the UK.
The award, sponsored by Pennant Homes, recognises Hale’s excellence in leadership and management, and highlights her as an exemplar and champion for encouraging more women to pursue a career in what has previously been perceived as a maledominated industry.
Charlotte Hale (pictured), winner of the Women in Construction award, said: “This is a great personal honour for me and, I believe, a recognition of the superb work the whole team at SO Modular are currently doing. The finalists in all the categories were of an exceptional standard, and so I feel I am in very special company to be chosen as the winner of the Women in Construction award. Construction is an industry that has long been perceived as a male-dominated field of work. So, it is very heartening to hear the
stories of the other inspirational female finalists in the category, and the great work they are doing in the construction sector – an industry that is open to all as a potentially fulfilling and rewarding career.”
For more information visit: www.somodular.co.uk
The National Fire Chiefs Council (NFCC) have released a ‘Position Statement’ on Modern Methods of Construction (MMC) calling on the government to tighten rules for the testing of offsite systems including volumetric modular methods.
improved building standards and fire safety. The statement outlines: “Whilst we hold concerns and support proper scrutiny of all building and construction that use MMC, we hold particular concern around the following methods, particularly when in use for high-rise buildings, buildings that are housing vulnerable people, and buildings with a ‘stay put’ or an evacuation with designed delay: 3D Modular (Volumetric) constructionCategory 1 of the MMC Definitions Framework (3D primary structural systems) and the use of engineered mass timber products e.g. CLT and glulam.
The Position Statement says that while the NFCC understands that the Government is very supportive of MMC and see MMC as central to the delivery of ambitious housing targets and the Affordable Homes Programme, significant cultural change in the system must take place to improve competency levels across the sector and ensure that MMC is promoted and used in a manner which provides safe buildings for all.
Gavin Tomlinson, NFCC Protection and Business Safety Scrutiny Committee Chair said: “NFCC is concerned that MMC buildings are being designed, approved and built despite a lack of understanding about their performance. Given the current regulatory system has already been described and accepted by Government as ‘not fit for purpose’ even for traditional construction techniques, this adds additional uncertainty in the built environment.”
Mark Hardingham, Chair of the NFCC added: “It is vitally important to make sure that products and technologies are safe for use, including their likely performance in a fire, before they are used in the built environment. Not only is this important for safety but it also helps to protect leaseholders from unnecessary costs that can arise when buildings need remediation, or interim measures, including things like waking watches.”
NFCC support reducing the environmental impact of construction wherever possible and recognise the role that MMC can play in achieving this. However, this must not be at the expense of safety.
The Position Statement asks for a range of measures to ensure that new construction products and technologies do not contribute to the risk of fire and that there should not be a conflict between sustainability,
1Amongst the many recommendations is a key aim that government should ensure that structural and fire engineers are included on its MMC taskforce announced in March 2021 and that the remit of the group is widened to focus on safety and promoting better understanding of the performance of MMC.
Ben Brook, NFCC lead on Climate Change said: “We are understandably seeing a focus on sustainable building approaches and materials, including the use of timber and living walls. While these may present useful solutions to help reduce the carbon footprint of buildings, they should also be supported by evidence and testing to demonstrate their longterm suitability and safety to provide reassurance for the lifetime of the building.”
You can download the Position Statement from: www.nationalfirechiefs.org.uk
Images:
01. Mark Hardingham, Chair, National Fire Chiefs Council (NFCC)
Emma joins after 12 years at Stubbings Property Marketing consultancy, which has also been BoKlok’s trusted advisor since 2019. Prior to this, Emma successfully ran her own development company and has a breadth of experience and knowledge in residential housing development and land planning.
Graeme Culliton, BoKlok UK Managing Director and Country Manager said: “Emma has first-hand knowledge of our customers and how they perceive our offering, her experience brings another dimension to our business, and we now welcome her to the BoKlok family to lead our sales, marketing, customer care and satisfaction teams. She has been instrumental in tailoring the BoKlok brand to the UK residential home
market and building our sales and customer care approach.”
Emma replaces Jerrie Kristiansson who for the last four years has been responsible for establishing BoKlok’s marketing, sales, and customer processes in the UK. Jerrie has been with BoKlok Group for over 10 years and will continue to work within the company as senior advisor and resource for business-critical initiatives across the international markets.
BoKlok is a residential housing concept providing sustainable homes and communities 'for the many people'. The concept is developed and jointly owned by Skanska and IKEA. BoKlok homes are built primarily from timber, using an innovative, industrialised and efficient process minimising the
environmental and climate impact and are committed to becoming net zero carbon throughout the BoKlok value chain by 2030. BoKlok currently has three home development sites in Bristol, Worthing and Littlehampton.
For more information visit: www.boklok.co.uk
Images: 01.
Award-winning housebuilder The Hill Group has gifted six SOLOHAUSTM homes to the Salvation Army, to help tackle homelessness in Basildon, Essex, as part of their Foundation 200 initiative.
Earlier in August, the keys for eight SOLOHAUSTM units were handed over to Dacorum Borough Council, the first council in Hertfordshire to make use of these purpose-built modular homes as follow-on accommodation for people who have previously experienced homelessness in the local area.
Designed to provide follow-on temporary accommodation for people who have experienced homelessness, the purpose-built modular homes were handed over on 28 September at an event attended by Basildon Council leaders and senior representatives from The Hill Group, The Salvation Army and Citizens UK.
The specially designed modular homes were provided through Hill’s philanthropic initiative Foundation 200, a £15million pledge to manufacture and donate 200 modular homes by 2025 to charities tackling homelessness. The temporary homes, which arrive fully furnished, are designed to Future Homes Standards, exceeding building regulations for energy efficiency and sound insulation.
Andy Hill, Group Chief Executive at The Hill Group, comments: “We are delighted to gift these six purposebuilt modular homes to the Salvation Army, supporting their efforts in helping vulnerable people in Basildon turn their lives around. Our SOLOHAUSTM technology is making a tangible difference to the lives of many people dealing with homelessness, and we are confident that these homes will help people get back on their feet in secure, modern comfortable accommodation.”
Once installed, the SOLOHAUSTM homes will be managed by The Salvation Army. The Salvation Army has a presence in 650 communities and accommodates a nightly average of four thousand people who were formally homeless, while Citizens UK provides vital support at night shelters and food banks in local communities and neighbourhoods.
Major Howard Russell, Divisional Commander of the East of England Division, The Salvation Army added: "Having safe independent accommodation is a vital part of transitioning back to a more stable living arrangement for those who have experienced homelessness. SOLOHAUSTM empowers people with that vital step in getting their lives back on track and we are confident that these units will make a huge difference to people in the Basildon area.”
Councillor Andrew Schrader, Chairman of Basildon Council’s Housing and Estate Renewal Committee, said: “This is a brilliant project that will transform the lives of Basildon’s residents in need. Thank you to all the partners who have worked so well together to make the opening of the first part of the scheme a reality.”
Management of the homes will be undertaken through a partnership arrangement led by the Council with DENS, a local charity with a proven track record of supporting Dacorum residents to realise their aspirations for housing, skills development, employment and education. The residents and homes at Hampton Close in Hemel Hempstead will be supported by DENS, the homeless charity for people in Dacorum. DENS do much more than just providing a roof and a bed for people in need, aiming to be the first port of call for people in Dacorum who are facing homelessness, poverty and social exclusion.
Wendy Lewington, CEO at DENS said: “These smart, modular homes will enable us to support even more people facing homelessness in Dacorum. DENS staff will be providing tailored advice and training to the residents so they can develop the skills, confidence and resilience to help rebuild their lives and take the next step into independent living”.
SOLOHAUSTM units are manufactured in the West Midlands by Hill Group’s manufacturing partner Volumetric Modular prior to being delivered and installed on site. So far around 150 SOLOHAUSTM homes have been handed over to local authorities in the fight against homelessness.
For more information visit: www.solohaus.co.uk
A planned modular housing development has received the Modern Methods of Construction (MMC) award in the South West’s Constructing Excellence Awards, while being shortlisted for further national accolades.
Tom Northway, Chairman of ZED PODS, added: “A great recognition for this fantastic modular development. We had over 400 visitors to our demonstration home in Cullompton last year, by taking on board their comments and feedback we designed this award-winning scheme. This will be ZED PODS’ first project in the district and is a brilliant example of how working with the local community, council officers and consultants we can deliver much needed affordable homes.”
Built in partnership with innovative, modular house builder ZED PODS Ltd, the zero-carbon development is set to be installed on the St Andrew’s Estate in Cullompton. The scheme is set to be delivered on council-owned sites, which were previously occupied by garages and car parking, by the end of this financial year.
Along with the award-winning homes at St Andrew’s, a similar scheme is also being built in Shapland Place, Tiverton. Both developments are set to be carbon-neutral, making this one of the first social housing projects of this type within the district and continuing the Councils ambition towards being carbon zero by 2030. The planned housing development in Cullompton took home the Modern Methods of Construction (MMC) award at a ceremony on 8 September and was shortlisted in three categories, they were: Innovation Award, Residential property of the year and Net Zero Award.
The awards were run by Constructing Excellence South West which forms part of the Constructing Excellence Regional Partnership (CERP) and exists to improve industry performance in order to produce a better built environment. The zerocarbon social homes project has also received national recognition by being shortlisted in the Inside Housing Development Awards: Best partnership (up to 100 homes) and Best affordable housing development (less than £5m).
Cllr Stuart Penny, Cabinet Member for Housing and Property Services, said: “Being able to transform our council-owned sites into affordable, low carbon homes that help towards our climate agenda is a huge boost for the area. The innovative plans which have now been approved will prove valuable for residents looking to live and work within two of our major towns.”
1The site in Cullompton looks to provide three one-bedroom and three two-bedroom homes, each with their own car parking spaces. A mural on the building has also been set out in the plans which will seek design ideas from the local community. An additional eight ZED POD homes and 37 parking spaces are planned for development in Tiverton only a few 100m from the River Exe and town centre. The proposals include a mixture of housing types, including four one-bedroom, three twobedroom and one three-bed homes.
Both sites will be completed with triple glazing and solar panels, have their own private communal green space as well as separate storage for residents’ bins and bicycles – with plans for new homes to be built on land currently occupied by garages and car parking.
For more information visit: www.zedpods.com/mid-devon-standrews-estate
Images: 01. The modular development is a further success for the ZED PODS approach
A high degree of prefabrication plays an increasingly important role in construction with ITW Construction Products Offsite’s Toolmatic range leading the way.
Our German engineered innovative Toolmatic range of tools brings major benefits in reliability, durability, high speed and long service intervals. Toolmatic tools are designed specifically for automation with only one air feed and one power line to attach. This simplifies attachment and eliminates the mess of wires required for modified hand tools.
These tools are reliable due to the high precision hand-built assembly in Germany. Here is how Toolmatic solutions can add value to your production line:
Toolmatic tools are designed specifically for automation simplifying attachment and eliminating mess of wires needed for modified hand tools.
Toolmatic automated tools help deliver a perfectly balanced solution geared to the precise requirements of each production line activity ensuring consistent spacings, accuracy of position and depth of required fixing.
All mechanical characteristics are designed to extend service intervals to minimise downtime and keep you running.
Toolmatic pistons are PTFE/copper alloy sealed requiring no lubrication and ensuring clean operation eliminating maintenance downtime, reducing wear and tear and avoiding damage. The tools re-cycle exhaust air to cool the bumper. This enables quicker fastening rates.
Toolmatic tools are ‘ready to mount’ with appropriate fixing brackets. No unnecessary time or cost is wasted. ITW Construction Products Offsite forge partnerships together with automated line manufacturers and timber framers.
Since Toolmatics tools are designed for automation, there is minimal risk for injuries, resulting in an overall safer work environment. The tools work incredibly efficiently and lower the
noise level significantly compared to manual production which is an added benefit in creating a healthier and safer work environment for employees.
Designed for offsite customers with influence from leading manufacturers coupled with ITW’s knowledge and flexible solutions, Toolmatic tools are made to meet the needs of timber frame manufacturers and many other offsite systems. Experience next level quality, productivity and service with ITW Construction Products Offsite.
You can find out more information on ITW Construction Products Offsite’s Toolmatic brand by emailing: orders@itwcp.com
Images: 01-04. Toolmatic tools offer a massive range of options to improve production line processes
The award-winning Gang-Nail Truss Frame system offers true design flexibility. Gang-Nail Truss Frame gains its structural strength and superior resistance to wind loading from the design and use of Gang-Nail nail plates for the joints of the timbers. This means less requirement for steel goal posts and the elimination of sheathing, which allows for more freedom in house design, such as open plan living and larger apertures.
Using Gang-Nail Truss Frame in conjunction with new panel design tool iPanel, and STITCHER®, the Gang-Nail Software Suite helps panel designers save up to 75% of their input time.
Q: Since launching in 2018 ilke Homes has become a leader in offsite housebuilding and achieved huge success in a very short space of time – to what do you attribute this spectacular growth?
Nigel Banks (NB): By creating a suite of high-quality house types, we have been able to cast our net wide when it comes to partners. Since being founded five years ago, we have worked closely with institutional investors, private developers, councils and housing associations to engineer solutions to some of the industry’s most fundamental problems – like quickly increasing output while simultaneously reducing the emissions associated with the development process. Thanks to our pioneering lowcarbon solutions to house building, ilke Homes has already secured a pipeline that exceeds 3,500 homes, putting us well on course to become a top ten housebuilder within the next five years.
Q: The offsite construction sector has boomed over the last 3-4 years with many new entrants to the market plus recent business casualties as well –what is ilke Homes bringing to a busy offsite sector?
NB: Launched in 2020, our turnkey offering means we can take care of the whole development process – from acquiring sites and securing planning, through to development and housing delivery – on behalf of clients. Our land team, comprising FTSE 250 talent, has helped build our land-led pipeline, and secured some of the sector’s biggest deals to date – including one where ilke Homes was chosen by FTSE 100 firm Boots to deliver a 622-home scheme at the pharma giant’s former HQ in Nottingham.
Q: Factory-design and volumetric modular systems are one of many options available to unlock ‘net zero’ housing and reduce the construction sector’s carbon footprint – how is ilke Homes delivering its ilke ZERO brand
with sustainability, affordability and net zero targets in mind?
NB: Last year we announced our ilke ZERO commitment, which is rolling out ZERO carbon homes with ZERO bills guaranteed for residents. Delivered in partnership with renewable energy provider Octopus Energy, investor Gresham House and their shared ownership residential platform SO RESI, the first ZERO bills homes are being delivered in Stanford-le-Hope, Essex and represent the future of UK housing.
On top of the standard efficiency gains associated with factory-built homes – better insulation, with airtight precision-engineering and low thermal bridging – the ZERO bills homes also feature solar photovoltaics, air-source heat pumps (ASHP) and battery storage technology that combine to generate more energy that a home consumes. This, teamed with a bespoke energy tariff provided by Octopus Energy, will see residents
ilke Homes is the Yorkshire-based company that has become a flagship name in the delivery of a new generation of energy efficient, low carbon, newbuild modular homes. We caught up with R&D Director Nigel Banks to talk about the latest developments.
potentially save thousands of pounds on their annual energy bills as the energy price cap continues to eye-watering highs. With the UK’s housing stock – the oldest in Europe –accounting for 20% of Britain’s carbon emissions, and the cost-of-living crisis beginning to bite, the ZERO bills offering sets a precedent for UK housing which all housebuilders and providers should seek to emulate.
Q: Improving productivity is a common concern across the construction sector – and the UK generally – but how can factory-based manufacture and specifically ilke Homes’ volumetric modular systems improve productivity levels?
NB: The UK has a backlog of around four million homes, while the methods used to construct newbuild housing have remained largely unchanged for the last 100 years. These problems are compounded by the fact that traditional construction has a rapidly accelerating retirement rate. According to the Construction Products Association (CPA), the age demographic of construction workers across the industry is massively skewed towards those aged between 50 and 56, meaning that the sector is expected to lose about a quarter of its workforce within 10 to 15 years, regardless of the impact of the pandemic.
Because ilke Homes is more akin to a manufacturing business, rather than construction, we can draw from different talent pools – spanning digital design, advanced robotics etc. Meanwhile our ilke Academy is committed to training up the next generation of house builders at our factory in North Yorkshire. The techniques we deploy across our production lines mean we are able to create six homes a day, a feat of engineering. Also, with 90% of the build stage taking place inside a dry, factory-controlled environment, our construction programmes are not exposed to the elements that tend to slow down progress such as adverse weather conditions.
Q: The use of technology and digital tools within factory environments is central to offsite manufacture with additional rollout of toolkits, platform approaches, repeatable components and harmonised design – how is ilke Homes developing this Industry 4.0 approach?
NB: Building a modular home is fundamentally different to constructing one in the traditional way. The level of complexity and accuracy required alongside rigorous quality control requires a particular approach. Every dimension, tolerance, and offset needs to be precise and fully co-ordinated meaning significant information is required to articulate each module in fine detail.
Before the development of ilkeX, a collaboration with matterlab to improve the efficiencies of our manufacturing techniques, the process of taking the early designs and creating the fabrication and assembly content took a team of eight people within ilke Homes a period of three months to produce. This included 4,000 drawings required to manufacture a home using multiple design tools, while also relying on an interoperability workflow between software that simply doesn’t exist to the level ilke Homes require.
On top of this considerable amount of work, the introduction of robotics and machinery on the factory floor left little room for error and manual intervention. As ilke Homes strive to create the best homes available in the UK and with a new product line, the goal was to automate the production of all information relating to linings, fixings, framing, all openings in steel, plasterboard, sheathing board etc, then co-ordinate within a 2mm tolerance to allow for a full product range refresh in a single phase rather than one at a time.
When matterlab and ilke Homes began to work together in 2020, they challenged themselves with finding a solution to the problem above by leveraging technology and automation to massively accelerate product revision cycle time, reduce errors, enable full virtual prototyping, integrate BOM and ERP, and digitally transform the end-to-end process. In June of 2021, a year after beginning this collaboration, modules designed and documented entirely from the software were built on the factory floor with precision-engineering and automated manufacturing. This introduced huge financial savings throughout ilke Homes and reduced errors in the overall process, reducing downtime on the factory floor which can cost upwards of £50k/day.
For more information visit: www.ilkehomes.co.uk
Images: 01. Nigel Banks, R&D Director, ilke Homes
ilke Homes expertise draws from different talent pools – spanning digital design, advanced robotics and cutting edge modular design
Developers face significant changes with major steps taking place in the government’s drive to become carbon neutral. Richard Hipkiss, Development Director of the Modular and Portable Building Association (MPBA) considers the significant role volumetric modular can play in achieving new building regulations.
1.4 for windows and rooflights and 1.4 for doors. In non-domestic builds there is a lowered U-value of 0.26 for walls and the majority of windows and curtain walling must achieve 1.6 W/m2
Since the government amended the Climate Change Act in 2019 to commit the UK to achieving net zero carbon emissions by 2050, the construction industry has been confronted with the need to decarbonise. According to the World Green Building Council, construction and buildings in use are responsible for 39% of all carbon emissions in the world. This is broken down into two elements with 11% being linked to the manufacture of materials and construction processes known as embodied carbon emissions and 28% associated with operational emissions caused by heating, cooling and lighting systems when a building is in use.
Paving the road to net zero targets and the nationwide commitment to create a cleaner and greener built environment, the new updates to Part L building regulations will have a big impact on the construction industry. The new regulations came into place in England on 15 June in the biggest change to building regulations since 2006, while Scotland can expect to see similar changes implemented later this year.
There are now higher performance targets and CO2 emissions are reduced by 31% for dwellings and 27% for other buildings and a new emphasis has been placed on low carbon heating systems. Part L sets out the rules that homebuilders must abide
by, while also setting out guidelines for the efficient use of fuel and power in new buildings, outlining what materials can be used and the correct procedures.
Homebuilders will face a range of changes, including how a property is insulated, as well as in relation to heat pumps and solar panels. The regulation changes also apply to non-domestic developments.
The changes continue to broadly follow a ‘fabric first’ approach, requiring lower U-values than previous versions of the regulations, whilst also incorporating renewable technology. In all new domestic builds, the new U-value for walls will be 0.18 W/m2,
1As an industry association it is our mission to demonstrate how the route to 2050 could follow a number of different paths. We intend to achieve this by extolling the virtues of volumetric manufactured buildings as well as removing the complexity surrounding so called modern methods of construction by diluting the myths and embracing reality.
Volumetric modular buildings are less susceptible to poorly specified manufacturers’ products as time can be taken upfront to validate the correct specification of materials. Designs are digitally constructed and virtually tested before they move onto the manufacturing phase. This process eliminates waste and achieves highly accurate and airtight building envelopes designed and built to
higher sustainability standards. This allows clients to have confidence in the quality and performance that they can expect from their new building.
Unlike factory manufactured buildings, there is significant evidence that traditional construction methods do not produce buildings that perform as well as design expectations and there is a void between anticipated and actual in-use performance. Findings from studies such as PROBE (Post Occupancy Review of Buildings and their Engineering) reveal that actual energy consumption in traditionally conceived buildings is often as much as twice of that predicted in the design.
Not only is the actual construction of the building ‘greener’ but volumetric manufactured buildings are also more energy efficient – reducing primary energy requirements and in-use operational emissions during the lifetime of the building.
At the core of the manufacturing of volumetric modular buildings is Design for Manufacture and Assembly (DfMA) protocols and Building Information Modelling (BIM) technology which empowers the optimal configuration of volumetric modular solutions by digitally connecting multi-discipline teams from the beginning of the concept design right through to the development process and beyond.
DfMA means buildings are conceived for manufacture within a factory environment. BIM facilitates early design detail and three-dimensional design information, minimising the risk of errors by eliminating the timeconsuming process of translating engineers’ information into material requirements and assembly drawings.
The benefits of volumetric manufactured buildings begin in the factory, continue on to the construction site and last through the lifetime of the building. The volumetric modular
The MPBA plays a key role in the connecting of sectors in the modular and portable building industry. The association collaborates with specialist technical advisors to enhance innovation in the design and manufacture of volumetric modular buildings. These can be designed and manufactured from timber or steel in any size and shape to meet individual client needs while ensuring full compliance with building regulations. To discover how volumetric modular technology can benefit construction projects visit: www.mpba.biz
way limits the amount of concrete in the ground and eco-friendly materials are often specified and each individual component can be selected specifically for its performance characteristics, tailoring every inch of a volumetric modular build.
As the construction sector develops and adapts to meet changing government strategies to reduce carbon emissions, I firmly believe the upward trajectory of volumetric modular buildings will continue to meet new building regulations and we need to act now to help mitigate the impact of climate change for future generations to come.
Images: 01-06. Volumetric modular buildings can be designed, digitally constructed and virtually tested before they move onto the manufacturing phase.
Lewisham Exchange has been a hugely positive project showcasing offsite construction and brick slip cladding technology.
unison, chasing the finished pods up the building.
Offsite construction not only ensured time saving benefits compared to more traditional methods of concrete or steel frame, but also quality of product with each one being manufactured in optimal facility conditions for consistency of quality. Furthermore, sustainability efforts were achieved through the reduction in transportation movements to and from site meaning less trucks needing to complete journeys for the finalised modular pods.
The construction site has changed dramatically over the years, with safety, sustainability, efficiency, and legislation all driving factors that have led to product innovation and materials used, affecting how construction methods are approached. But now, developers and contractors are looking at other means to make gains. Most notably, the construction process and method itself. As such, offsite construction has increased in popularity thanks to its various benefits from a cost, time and waste saving perspective, and efficiency of construction, storage, and labour.
For Lewisham Exchange, offsite construction was primarily chosen due to the time saving properties and cost benefits provided. However, the development did not concede on design or aesthetics, instead, improving on these key aspects contrary to what might be expected from a modular constructed, offsite build. The development stands more than 100m in height at its highest peak, making it the tallest modular student accommodation building in Europe. It is built from 3D volumetric
structural modules, which were completed offsite by specialists Vison Modular.
The twin-tower block structure consists of 35 and 20 storeys and accommodates more than 750 student apartments and around 70 affordable homes. Meanwhile, its commercial properties at the foot of the structure achieved an ‘Excellent’ BREEAM rating, putting them in the top 10% of buildings from a performance perspective.
Constructed by Tide Construction using 3D volumetric modules enabled on-site construction to be streamlined and contributed to the impressive 35-week completion of the brick slip cladding installation by Century Facades Ltd, who also carried out the window installation offsite. The modular build saw the housing ‘pods’ manufactured in optimal facility conditions, including windows, which were then delivered to site where they were erected around the building’s lift cores. Then, once ten or so stories were complete, the external envelope’s Mechslip cladding was constructed in
1Mechslip was chosen for its exceptional A1-rated fire accreditation and innovative natural brick cladding aesthetics. These benefits overcome difficulties with competitor products that in the past have either not been fire accredited or from an aesthetics perspective, look unnatural with clay extrusions which can’t compete with Ibstock’s eye-catching, real cut bricks. Importantly, the development also breaks the narrative surrounding modular structure builds and their limited design availabilities that come with the technique. Lewisham Exchange showcases incredible architectural and aesthetically pleasing detail thanks to the Mechslip cladding technology.
The Lewisham Exchange development is an example of how innovative technologies such as Mechslip can combine with the increasingly popular offsite construction processes to make real-world gains on sustainability, time, and cost efforts across a modern new build – all without compromising on aesthetics and quality.
For more information visit: www.mechslip.co.uk
Images:
01. The twin-tower block structure consists of 35 and 20 storeys and accommodates more than 750 student apartments and around 70 affordable homes
Vertex BD is Building Information Modelling (BIM) software which is your complete source of information for prefabrication and modular projects.
design phase, whilst giving its users the flexibility to build the way they need.
Vertex BD specialises in cold-formed steel and timber framing and we aim to offer our clients all the benefits from Vertex BD whilst fitting in with how they are currently operating. Design time can be vastly reduced, accuracy increased, and costly errors avoided. Vertex BD uses digital automation to seamlessly translate information about a project across all disciplines within a project, so all the plans, schedules, material reports, shop drawings, and manufacturing data can be automatically generated and saved within the BIM model.
have to sacrifice control over your construction specifications to take advantage of automated tools. The result is uncompromised speed, accuracy, and control.
Import existing 2D drawings and 3D models from other CAD systems and export your plans and models for collaboration. Vertex BD supports over 20 file formats used in construction projects, such as IFC, PDF, 3D PDF, DWG, DXF, IGES, STL, and many more. Vertex is compatible with over 30 different CNC Manufacturers for steel and wood.
For more information visit: www.vertexcad.com
Efficiencies in the manufacturing process need to be matched by efficiencies in the design process, this is where Vertex BD comes in. Vertex BD uses a high level of automation to rapidly reduce the time spent in the
Minimise queries from your on-site and manufacturing teams by generating clear, concise and understandable documents with Vertex BD. You don’t
Images: 01-02. Vertex BD uses digital automation to seamlessly translate information about a project across all disciplines within a project
Volumetric modular provider Algeco was part of the team that recently completed the UK’s first net zero restaurant for McDonalds at Market Drayton, Shropshire.
The construction industry by nature is a heavy consumer of natural resources, and construction activities are directly responsible for around 10% of all UK emissions. What’s more, between 20% and 40% of the UK’s total carbon footprint comes from our built environment, with estimates differing depending on whether or not they include the energy used within buildings. Clearly, the industry has work to do to improve its green credentials and contribute to the UK’s drive towards net zero.
Algeco, manufacturer and supplier of flexible, modular buildings for over 50 years is part of the innovative approach to carbon reeduction. All of the company’s building components are designed and fabricated offsite, before being transported to the construction site for assembly. This approach has
numerous benefits over traditional methods, offering a faster, greener way to deliver high quality new buildings, and maximising efficiencies at every level. The modules are fully recyclable and reusable, making them a much more environmentally friendly than traditionally constructed buildings. Green options such as solar panels and smart energy management solutions can be specified and included as part of the build.
UK’s First Net Zero Restaurant McDonald’s in Market Drayton, Shropshire, is a wind turbine and solar panel-powered restaurant which will produce as much energy as it uses over the course of a year. It has been verified as net zero using the UK Green Building Council's (UKGBC) net zero carbon buildings framework.
From the project outset, McDonald’s made it clear that its requirements included achieving a net zero build with minimal impact on the environment. Algeco’s innovative, turnkey solution included a kitchen, dining area, servery, toilets, offices and storage, as well as a car park and an external landscaped area. The building itself was 80% completed in the company’s factory in East Yorkshire before being transported to site, minimising waste and maximising quality control, efficiency and speed of construction.
The modules are constructed using a steel-framed system, a 100% recyclable material sourced from a UK supplier with certified Environmental Policy Declarations. The lightweight nature of the steel frame modules reduced the
need for carbon intensive foundations. These were done at the same time as the modules were manufactured which reduced the overall build time by around half compared to an on-site build. Once on-site, the modules were connected to services and underwent a final fit-out, ready for handover. The project comprised a number of small, incremental improvements which combined to make a huge difference in overall energy performance and environmental impact. For example, the building utilises responsibly sourced and recycled materials throughout.
Other sustainable features include sheep's wool insulation instead of fibreglass: cladding, ceiling, floor and wall tiles made from recycled plastic; a rainwater harvesting system; wind turbine electricity generation and photovoltaic car park lighting complete with battery backup. The kitchen incorporates a heat exchange that feeds into the dining area.
All the Algeco offsite modules are designed to have a service life of at least 60 years, and the restaurant itself has been designed to allow for relocation, reconfiguration or recycling, depending on McDonald’s future requirements. Graham Stevenson, Construction Manager at Algeco, said: “This is a landmark project for McDonald’s, Algeco and the building industry as a whole. Achieving a net zero carbon build confirms that the ambitious targets set for the built environment are achievable using our modular and offsite solutions.”
McDonald's spokeswoman Beth Hart added: “We've already started to
roll out some of these innovations to other restaurants, but what is exciting about Market Drayton is the fact it will act as a blueprint for our future new builds. We believe that our food needs to be served in restaurants that are sustainable for the future. Market Drayton is a big step towards making that a reality.”
In the coming years, the UK construction industry will play a critical role in transitioning to a low carbon economy. The McDonald’s net zero build is an incredible example of what can be achieved, and the Algeco approach at Market Drayton opens up the possibility of a more sustainable solution for leisure and retail businesses as they look for ways of meeting their new zero commitments. For McDonald’s, Market Drayton sets out a route for all their restaurants being net zero in use by 2030. By opening the UK’s first net-zero carbon
restaurant, McDonald’s has introduced cutting-edge innovations, the most successful of which will be rolled out in McDonald’s restaurants nationwide.
For more information on McDonald’s Market Drayton carbon net-zero build visit: www.algeco.co.uk/news/algecoserves-carbon-net-zero-buildmcdonalds www.algeco.co.uk/permanent
Images: 01-02. McDonald’s Market Drayton has been designed to act as a blueprint for future sites
03: (L-R) Gareth Hudson, McDonald's Director of Development, Matt Winfield, McDonald's franchisee and Beth Hart, McDonald's Vice President Supply Chain and Brand Trust at the Market Drayton launch
04: The modules are created at the Carnaby factory and deliver many project and green benefits
The latest addition to the Tekla Structures constructible modelling software was on show recently at Offsite Expo, with a new Volumetric Modular Tool helping streamline the detailing process.
Offsite is a growing sector of the construction industry, helping structures to be built faster, greener and more efficiently. Building Information Modelling (BIM) can be a key part of this modern construction revolution, with the use of BIM software helping offsite manufacturers to visualise and model a building before construction has even started. With this comes the ability to anticipate design clashes and remedy them before a project reaches site, improving accuracy levels, saving time and therefore costs, as well as reducing waste material. In this regard, BIM and Offsite are great partners. Using a BIM workflow can help to enhance all the values and benefits of Offsite Construction, helping to provide higher quality outcomes.
The benefits of offsite construction are widely known and proclaimed, from faster build times, improved accuracy and quality, and reduced waste – the latter point being key when considering the efforts to reduce carbon emissions.
When it comes to delivering on the offsite vision, employing Building Information Modelling (BIM) solutions can be a big help. Indeed, in many ways the benefits of BIM align perfectly with the offsite goals, contributing to a more streamlined and efficient construction sequence and workflow. BIM and offsite truly are the perfect partners.
With this in mind, it could be said that BIM software providers have
a big responsibility in providing offsite contractors, suppliers and manufacturers with the tools that they need. Digital technology is an area that is in constant development, with new features and tools arriving on the market as the construction industry itself develops and progresses.
Developed on the back of the SEISMIC project, the new Volumetric Modular Tool was launched in the 2022 version of Tekla Structures. Designed specifically for the offsite market, the tool enables users to construct 3D models of container-sized modular units far quicker and easier, with automation at the tool’s core. A basic unit can be created in just a couple of clicks, saving valuable time and making the BIM workflow even more
efficient and effective. The tool also offers a clear assembly hierarchy, automatically creating and organising assemblies, sub-assemblies and parts ready for production.
Taking the time-saving benefits even further, the Tool’s parametric capabilities mean that the change management process is far easier to manage and coordinate. For example, if you make a change to one assembly it will automatically make the same change to all connected parts. Likewise, if you put in door or window openings, the Tool will automatically configure the surrounding steelwork to account for the design change.
Craig Johnson, Business Development Manager for Trimble’s Detailing and Manufacturing segment, said:
“Our aim is to make sure the offsite industry, in particular, is aware of the fact that the design and planning of all building elements can be kept within the one 3D model, making sure all information and data are consistent, amalgamated and easily accessible. This is so important for an industry where time and accuracy are crucial for the success of any project.”
The Volumetric Module Tool is now available to download at: www.warehouse.tekla.com
Images: 01-03. The Volumetric Modular Tool will bring an additional way for building designers to collaborate on volumetric construction and maximise quality and productivity
The UK BIM Alliance, the independent, not-for-profit organisation established in 2016 to champion implementation of building information modelling (BIM) in the UK is rebranding as ‘nima’.
The name, also the Greek word for ‘thread’, is not an abbreviation. It has been selected to help give the volunteer-led organisation an identity, sense of purpose and a set of behaviours that are better aligned with current and anticipated future UK thinking about digital working in the built and managed environment.
Explaining the change, announced at UK Construction Week, Birmingham in October, Dr Anne Kemp OBE, Chair of nima, said: “The UK has been hugely influential in the international adoption of BIM adoption since the launch of the UK government’s drive for change in 2011. Setting a ‘BIM Mandate’ in April 2016 did much to stimulate people, process and technology change and to help build a standards-driven movement. And since 2016, the Alliance has also helped maintain momentum, by, for example, supporting development of the UK BIM Framework.
“However, the debate has started to shift. It is no longer just about BIM – often seen as a technological change – but about wider industry information management challenges, including building safety, climate change, and delivering value across the life cycle of our built and managed assets.”
The organisation has been debating its identity and purpose since the publication of the international ISO 19650 standards in January 2019, mindful that industry discussions were also embracing emerging concepts such as digital twins. BIM was becoming ‘business as usual’ for significant parts of the construction sector. However, it was often misconstrued as a 3D design technology rather than a process supporting purposeful use of information across the whole landscape of the built environment, from the inception stages of projects, through construction, and – most importantly – then to support efficient operation, maintenance and use of assets through to their end of life. Continuing, Anne explains:
“Our new name, nima, reflects evolution of our industry and our organisation. We are keeping an international perspective, continuing to support digital transformation across the sector, and aiming in our behaviours to be as inclusive as possible. We are not the ‘BIM police’ – we are a self-help community that anyone can tap into if they want to improve their information management.”
As part of the rebranding process, the nima name is supported by a new logo, a refreshed strategy has been developed, and the organisation’s website and social media channels are being updated.
Existing content (including the UK BIM Framework guidance – endorsed in the government’s 2021 information management mandate), local and sectoral group resources, and relationships with industry organisations (including UK government, professional and trade association affiliates, technology providers, and buildingSMART International) will be maintained and expanded.
Nima will also continue to support clients and industry practitioners with case studies, plain language guides, national and local events, and exemplar information management implementation projects.
For more information visit: www.wearenima.im
Leading modular housing company ilke Homes has reduced factory overheads and boosted output following the introduction of a bespoke solution from lifting specialists Totalkare.
Totalkare solved this with the provision of two sets of six T8DC cable-free mobile column lifts, complete with rubber in-fill plates. This enables the unit to be lifted so a flat bed transport can reverse underneath before the unit can be lowered and secured in place.
by a Totalkare service plan which includes two service engineer visits per year plus Reports of Thorough Examination.
ilke Homes manufacture up to 2,000 steel framed homes a year from its 250,000sq ft factory in Knaresborough, North Yorkshire. Modules are precision-engineered along production lines and then loaded onto lorries for despatch across the UK. Previously, the loading operation was conducted by crane – a painstaking process adding significant time to the process.
1Flexible & Cost Effective Totalkare’s T8DC mobile column lift can lift 7,500kg per column and can be used in sets of four, six or eight depending on the lifting requirement. Highly manoeuvrable, they can be put aside when not in use, making them a flexible, cost-effective solution for any workshop.
Following their successful introduction, ilke Homes has invested in an additional two sets of six T8DC mobile column lifts, taking the total number at the factory to 24. Each set is supported
“Using the Totalkare lifts in our production facility has increased the speed in which completed units are despatched to site, while also saving the considerable cost of crane hire,” said Rachel Beech, Supply Chain Director for ilke Homes. “Doubling the number of lifts on site allows us to replicate these efficiencies as we optimise our production processes.”
For more information visit: www.totalkare.co.uk
Images: 01. The safe and efficient lifting of modules is of paramount importance in the factory
A newbuild 48-bed critical care building delivered to the prestigious John Radcliffe Hospital in Oxford, saw a range of facilities delivered including five storeys of bespoke volumetric modular accommodation.
Healthcare construction specialists MTX have provided Oxford University Hospitals NHS Foundation Trust with a 5,450sq m new critical care building, achieving a pre-manufactured value (PMV) of 54%. The new five-storey facility, now called Oxford Critical Care (OCC), was part of a regional approach for managing critical care demand and activity throughout the COVID-19 pandemic, in addition to supporting and alleviating future seasonal and epidemic pressures for the Trust and its one million annual users.
Situated directly next to the hospital’s existing Trauma Department, the OCC connects directly into one of the main live corridors at ground floor level, proving a seamless flow between departments housing theatres and imaging and diagnostics facilities.
Through offsite construction, MTX were also able to minimise disruption to the Trauma Department and allow for uninterrupted staff and patient access.
The use of volumetric modular construction, MEP services, virtual prototyping and speedy onsite installation minimised disruption to the Trauma Department and enabled uninterrupted staff and patient access 24/7. MTX’s platform approach, incorporating multiple MMC disciplines, quickly delivered this high-quality new hospital facility cost effectively, within budget and openly on time. MTX bespoke solutions are specifically created for medical and healthcare use, with advanced super-efficient mechanical heating and ventilation systems, which
optimise clean air flow and meet clinical needs, in addition to reducing energy consumption and protecting the estates power capacity, all whilst minimising the carbon footprint.
The new OCC comprises 3no 16 bed wards across the ground floor, first floor and second floor, with dedicated plant room and non-clinical accommodation (seminar rooms, offices and spacious staff rooms) across the remaining 2 floors. The top floor dedicated staff area, boasts enviable 360-degree views of the Oxfordshire countryside, providing staff with a beautiful and calming training environment.
Careful planning and logistics allowed the team to work out of hours to install and commission 148 modules to be
safely and efficiently craned into place in just five days by the experienced on-site team. Through continuous and close communication with the client, the team were able to work meticulously and successfully deliver the project in the shortest possible programme as well as continuity of intensive patient care.
Significant logistical challenges included tight site constraints, maintaining access to the Trauma Building and main hospital, creating the foundations and installing the piling on a pronounced slope, and obtaining the Execution Grade 3 steelwork. MTX also had to address the exacting ventilation requirements of a critical care building, divert the water and gas services, create the new sub-station and associated electrical infrastructure, and subsequently ensure vehicular access, including for cranes of different sizes.
Through excellent collaboration and teamwork between the key project partners – the Trust’s clinical, estates, and projects personnel, architects IBI Group, consulting engineers DSSR and Hoare Lee, civil engineers Rossi Long and structural engineers Alan Wood, the scheme progressed smoothly.
Lyn Bennett, Matron
for the new building said: “This is a fantastic new building which has been constructed to a limited budget. We have been able to incorporate advanced 21st century designs that, from experience, will enable the clinical team to provide efficient and excellent clinical care for patients while working in a modern, bright, natural daylit and person-centred environment. The design of the new critical care building has attracted considerable external interest, including from NHSE/NHSI and believe it will prove to be a landmark building.”
A combination of an extremely rapid design and planning process and strenuous on-site 14-hour working days, saw it take just 15 months to get the prestigious project from initial design to successful handover. This critical care building with such complex services requirements, would have taken up to three years to complete if traditional construction methods were used.
For more information visit: www.mtxcontracts.co.uk
Images: 01-04. MTX won Healthcare Project of the Year at the Offsite Awards 2022 for its work at John Radcliffe Hospital
Premier Modular was appointed as the principal contractor for the 62-bed, priority assessment unit at St Peter’s Hospital in Chertsey, supported by delivery partner Claritas. Faced with increasing patient numbers and tight deadlines, the Trust needed the new building to support increased demand, especially during the busy winter period. St Peter’s chose to fasttrack the building project by using offsite construction, which reduced the overall programme time by nine months.
Designed by BDP and delivery architects P+HS, the new space purposefully reflects the existing environment, while matching the hospital’s modern needs, ensuring seamless integration. The new facility was linked to the emergency department with 62 patient bays, alongside nurse stations, staff rooms, seminar rooms, laundry and clean utilities and kitchenettes for staff. The new unit provides updated technology, with datacomms, security systems, CCTV and nurse call systems, which are all fully integrated with the main hospital.
“This project shows how striking and unique architectural design, that is also in keeping with its surroundings, can
be successfully married with efficient delivery via offsite construction, bringing many benefits including speed and quality,” said Akshay Khera, Architecture Director, BDP.
The offsite solution was engineered to fit seamlessly into the existing hospital, maintaining flows between the existing facilities and the new unit, with continuous level floors throughout. Externally, the assessment unit is finished with vertical rainscreen cladding in grey and brickwork to complement adjacent buildings.
Andrew Grimes, Assistant Director of Property and Capital Development added: “This project responds to the urgent national need to increase capacity in emergency care. Offsite construction allows us to add space on our hospital campus more quickly. We estimate Premier reduced time on site by around six months and the overall programme by nine months. Less time on site also means less disruption to patient care, which is always a priority for hospital building projects.
“Premier had the capabilities to meet the technical constraints of this site and the brief very well, particularly to provide seamless connections at two levels to maintain patient flows
and allow us to move beds easily between this building and the existing facilities. Premier was also the only offsite specialist who was able to meet our module height requirement without the addition of ramps. And the lightweight nature of steel-framed modular construction minimised groundworks which had time and cost savings. Premier demonstrated the flexibility and design capabilities to engineer a bespoke solution for this challenging site, with all the speed and value benefits of offsite construction.”
1To support the Trust’s sustainability targets, the building envelope has been designed to be thermally efficient to reduce running costs and carbon emissions. It incorporates technology, such as solar control glass, integral brise soleil sun shading and a building energy management system (BeMS) to optimise energy usage.
“This scheme was ideally suited to offsite construction,” said Dan Allison, Divisional Director, Premier Modular. “It allowed the Trust to meet an urgent need to expand capacity for emergency care and the development of a very constrained site. The new building has been constructed in a courtyard and close to the emergency department, which required careful logistical planning from our project team. We maximised construction and fitout work offsite to radically reduce disruption to patient care and were only on site for around six months to produce a facility for the trust.”
For more information visit: www.premiermodular.co.uk
Images:
01. The new unit shows how modular construction can offer a striking and unique architectural design
The 2022 show was a resounding success with the UK’s most important offsite construction event once again proving to be a central hub to network, do business and learn about the many ways offsite technology is changing the built environment.
some quality time with some key people within the industry. Fantastic and I’m sure we will be back.”
This year Offsite Expo hit a record attendance, with 3,462 delegates visiting 130+ exhibition stands and feature builds promoting the various offsite systems, technologies, and services with many attending the seminars and masterclasses that were equipped with 100+ industry expert speakers.
“Offsite Expo has been a really good show this year,” said Adam Salt, Business Development Manager –A Proctor Group. “We’ve had lots of quality relevant people come to our stand. It’s been one of the best shows we have attended… it’s all been business and we have enjoyed it very much.”
Offsite Expo was developed as a platform for endless networking and creating new business opportunities. At the heart of the event, the Offsite Connect Buyers and Specifiers Forum, sponsored by Kiss House and James Latham, was open exclusively to exhibitors, and proved to be a hive of activity. With 80+ buyers and specifiers registering to participate, including main contractors such as Galliford Try, Morgan Sindall and Willmott Dixon.
Paul Cashman, Business Development Manager for British Offsite added: “This is our second year at Offsite Expo and we got such a good response from last year, we definitely wanted to return this year. The sort of clients we are meeting at Offsite Expo are from all over Europe – we’ve met developers, architects, designers, students and housing associations, so it’s been very, very good for our exposure to the offsite world.”
Whether a new product launch, or an association update, Offsite Expo brought the picture-perfect target audience together under one roof. Getting to grips with the latest international offsite methods and smart digital technologies was high on the agenda – the extensive range of CPD Accredited Offsite Masterclass and seminar content provided a dynamic and interactive experience, focusing on a variety of offsite construction technologies.
Simon Boyles, Commercial Director from Fusion Steel Framing said: “The one-to-ones at the Offsite Connect Buyers and Specifiers Forum have proven really useful, it’s great to have
Taking centre stage at Offsite Expo on the evening of 20 September, the Offsite Awards also saw over 400 guests gathered to celebrate the many ground-breaking achievements and pioneers who are developing radical new offsite technologies, innovative product developments and landmark projects.
“Enquiry levels and quality levels have been very, very impressive,” said Nick Whelan, Commercial Director from Kingspan. “From us it’s a good investment, and we’ve rebooked again for next year’s Offsite Expo. The show itself is very intimate and extremely focused on what we do as a business and that’s what we need. Very happy, thank you.”
Offsite Expo will take place again at the Coventry Building Society Arena on 19 & 20 September 2023 and will include the Offsite Awards 2023. Presenting a compelling proposition, Offsite Expo will feature a combination of advanced manufacturing approaches and smart digital construction technologies. With innovative displays, live demonstrations, and pioneering speakers – the event will play host to leading experts, offsite manufacturers and component suppliers.
For more information visit: www.offsite-expo.co.uk
A new Modular Research Centre in the Czech Republic is showcasing an innovative use of modular structures by altering conventional building systems and pushing the boundaries of standard modular architecture.
Following their first collaboration in 2007, CHYBIK + KRISTOF and KOMA Modular recently announced the completion of the striking new Modular Research Centre (MRC). The latest in a series of collaborations, the 170sq m building is situated at the edge of the KOMA complex and carefully integrates the factory into its surrounding environment while creating a large semi-public social gathering square.
The new research centre is also serving as a think-tank presenting new concepts and possibilities behind
modular construction. Set to become an innovation hub for the factory complex to develop and explore new building methods with modules, the research centre forms an adaptable system that can meet multipurpose needs. Acting as an ‘idea generator’, the building is an important meeting place for all professionals to create innovative and special products, becoming a default gathering and evolution centre for all those interested in the future of modular construction.
Created as a prototype for a new and adaptable modular system, the MRC
underlines the studio’s dedication to expanding the limitations of modular architecture and engaging in supporting local communities. Putting the focus on crafting new shapes offering unrestrained modularity and showcasing an innovative system of multifunctional modular shapes, the studio is expanding on the typical rectangular construction.
Bypassing the restriction of the use of right-angled units placed side by side, the MRC varies from a standard model in the basic re-imagination of the use of modular structures.
Containing three main module elements, the floor, the container and the roof units, the space creates a new unique system – spatial units containing the facilities are levelled onto the planar flooring modules, which are anchored to the foundation, functioning as columns. Placed in between the containers and the roof, vast window surfaces draw in an abundance of light, keeping the workplace open and connected to the exterior space.
The juxtaposition of the main modules and glass surfaces forms
an all-inclusive spacious open area dedicated to horizontal and vertical working spaces. The area itself is entirely flexible, avoiding negative aspects of large open space offices, and can be readjusted to meet the specific needs of any project, forming multiple adaptable and individual workstations.
Building materials further aid in reflecting and understanding the innovative modular concept of the research centre, with its perforated surface and visible details used to the
maximum extent in their natural form.
As a material that KOMA manufactures and uses daily, aluminium was a clear choice for the complex, and was felt aided the understanding of modular build principles easily.
For more information visit: www.koma-modular.cz/en/
Images: 01-07. The new Modular Research Centre is playing with the traditional layout of volumetric modular design and is hoping to stimulate new ways of designing and building
Out of recessions come game-changing offerings, says Andrew Shepherd, Managing Director, at tech-driven modular manufacturer TopHat.
Such price rises have and will continue to make certain projects unviable, especially for the ones being carried out by smaller firms who often lack the scale to hedge.
These problems are compounded by the fact that, according to industry figures, five million tonnes of construction waste still find its way to landfill every year, meaning, as an industry, we are not using what we have efficiently. Real estate has done relatively well from 10 years of loose monetary policy and lowish taxes. But this year marked the end of a decade of cheap debt. This has huge implications across the built environment as many projects rely on some sort of leveraging to fund schemes.
Rishi Sunak took up his new role as prime minister with a monstrous in-tray. Rocketing inflation, and the consequential interest rate rises to tame it, along with the cost-of-living crisis and its implications, including for housing affordability, will be jostling for attention from the new administration along with other domestic and international challenges. And there is no doubt that these factors are, and will for some time, have a profound effect on the economy, not least construction and housebuilding. It is a daunting moment, but in the face of hardship, innovation can sometimes flourish.
Despite a strong initial recovery from COVID-19, construction firms, and more specifically housebuilders, continue to grapple with major supply chain issues. A shortage of materials such as timber, plaster and steel have seen prices rise by 24.1% year-on-year according to government figures.
Interest rate increases heightens the sensitivity of ‘time’ when considering capitalised interest, meaning speed becomes more important than ever. The same can be said for investors looking to access revenue streams at the earliest possible time. By manufacturing offsite, TopHat can typically cut construction programmes in half thanks to high levels of repeatability and most of the build stage taking place in a factorycontrolled environment.
This makes the corporate case for offsite, but what role does the sector play in helping consumers face the ever-growing macro headwinds face on? Targeted government support will go some way in shielding UK households from the worst of the energy crisis, but when it comes to an abrupt end in six months, up to 11 million households could be plunged into fuel poverty. That’s according to the End Fuel Poverty Coalition who has described the outlook as “frankly terrifying.”
Throw into the mixer rising mortgage repayments and the picture looks even more bleak. Britain’s ageing housing stock – one of the oldest in Europe –has left residents heavily exposed to rapid rises in wholesale gas prices. With over 20 million homes across the UK requiring some sort of retrofitting to make them compliant to new energy standards due to be introduced in 2030, it’s important that the homes we deliver today do not continue to kick the net zero can down the road.
Due to the high levels of insulation, and sustainable technologies like air source heat pumps (ASHP) and solar panels, TopHat homes are fully future-proofed and have the potential to be zero carbon homes. These technologies are already gas-free, instead running on electricity, so as the grid moves towards decarbonisation, TopHat’s homes become lower carbon over time.
This future-proofing means the average energy consumption of a TopHat home is 30% lower than a traditionally built home across its lifetime. Moreover, the infrastructure of a TopHat home means it has the potential to be fully sustainable, producing its own electricity, and therefore not requiring power from elsewhere, resulting in zero bills in the long-term. Offsite’s meteoric rise will not be slowed down by the impending recession, in fact it will act as a catalyst for growth as institutional investors, developers, housing associations and councils yearn for cost, time and quality efficiencies.
For more information visit: www.tophat.io
Images: 01. Andrew Shepherd, Managing Director, TopHat
In partnership with Volumetric Modular Magazine and The Modular and Portable Building Association, this TWO-DAY CONFERENCE and EXHIBITION presents a prime business opportunity to gain insight and network with those who are shaping the future of the volumetric modular industry as it focuses on the latest developments, innovations, and investments in the volumetric modular offsite sector.
2021 Offsite Awards Winner for ‘International Project of the Year’ Image courtesy of FortaPRO