Timetable
by rail engineers for rail engineers JUL-AUG 2022 ISSUE 197 www.railengineer.co.uk
TIMETABLING
planning is an art that must cater for a variety of factors and stakeholders. HS2: GOING GREEN HS2 is meeting its net-zero targets by investing in green plant and equipment. THE ELIZABETH LINE’S PLATFORM SCREEN DOORS The Elizabeth lines PSDs are a marvel, but each represents a potential single point failure. FEATURESFOCUS STOCKROLLING DEPOTS& EQUIPMENT&PLANT&STATIONS TECHNOLOGIESPASSENGER transformationWELSHRAIL AT THE HEART OF EVERY RAILWAY

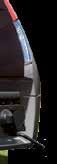
www.railtex.co.uk Exhibit at Railtex 2023, the UK’s number one rail event and benefit from three days of uninterrupted business. The exhibition profile includes: Organiser: Rolling RailwayStockCivil Engineering Track Design, Supply & Construction Track & Infrastructure Maintenance Safety & Security Systems Electrical Products & Equipment Station Equipment & Passenger Technology Information Technology 9 – 11 MAY 2023 | NEC, Birmingham SHOWCASE YOUR PRODUCTS AND SERVICES TO A SPECIALISED AUDIENCE BOOK YOUR STAND NOW PLAY A KEY ROLE IN THE RAIL INDUSTRY OF TOMORROW

76|
HS2: going green Rail Engineer examines how HS2 is meeting its net-zero targets by investing in green plant and equipment.
| Issue 197 | Jul-Aug 2022
FFU goes large Sekisui’s FFU sleepers have set the standard for synthetic railway sleepers on bridges across Europe.
InnoTrans is back! After a four-year wait, leading rail industry exhibition InnoTrans will open in Berlin on 20 September.
Rolling stock wheelsets
The IMechE’s Railway Division This latest feature in our series on professional engineering institutions focuses on the Railway Division of the IMechE.
30|
Another year, another Railway Challenge Competitors gathered at the Stapleford Miniature Railway for the 10th annual Railway Challenge, sponsored by the IMechE’s Railway Division. Update from the Adhesion Research Group
Reconnecting Levenmouth David Shirres reports on the reopening of the branch line to Leven, which will economically transform the area.
The CoventryVLR vehicle
26|
The IMechE holds regular wheelset seminars to share developments and issues. Rail Engineer reports on the latest presentations.
Railway Plant Services in Northern Ireland Companies tendering for contracts in Northern Ireland should not hesitate in contacting Railway Plant Services for their on-track plant requirements.
92|
94|
110|106|86|
98|
91| Electro-Wind: transforming rail projects In 2016, Electro-Wind was approached to work as Devontech’s main transformer supplier for the Feltham and Wokingham re-signalling project.
Vehicle-Track Interface Update 2022 Malcolm Dobell reports on an industry update from the RSSB-sponsored Vehicle/Track System Interface Committee.
The Elizabeth line’s platform screen doors
Welsh rail transformation By 2025, TfW will have delivered its commitment to provide an improved, greener train service for future generations. Train depot technology Maintenance depots are an essential and critical supporting element of every railway, as Paul Darlington reports.
3
Digital engineering in the real world Clive Kessell attended a recent IET and Siemens Mobility seminar covering digital systems on the modern railway. Timetabling – at the heart of every railway Timetable planning isn’t easy and must cater for a variety of factors and stakeholders, as well as customers.
Siemens Mobility – delivering improvedperformance Siemens Mobility has played a key role in delivering crucial systems for the Elizabeth line on behalf of Crossrail Ltd.
80|70|
IRSE Technical Tour Dublin Train protection and level crossing control in Ireland were discussed at the IRSE’s technical weekend held in May. Rail Engineer
Rolling stock: made in Newport, Wales Rail Engineer toured CAF’s UK assembly plant built on part of the former steelworks in Llanwern, South Wales.
50|44|
The ADHERE seminar covered the subject of adhesion, which has concerned railway engineers since the earliest days of rail transport.
38| David Shirres considers this lightweight vehicle and reports on the recent VLR conference held in Dudley, West Midlands.
44 94 CONTENTS 60 19|12| 66|60|54|
The Elizabeth lines PSDs each which represent a potential single point failure. Malcolm Dobell investigates.
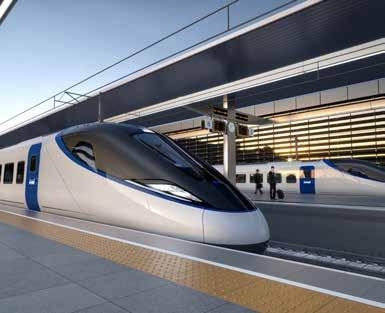
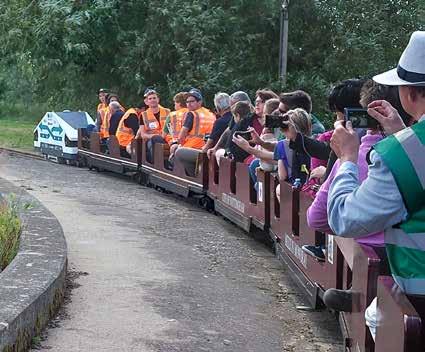

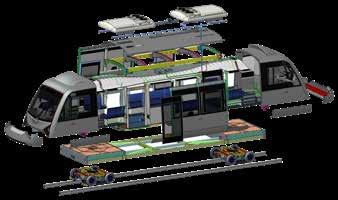
EDITORIAL EDITORIAL Engineering the whole
Rail Engineer | Issue 197 | Jul-Aug 2022
The Great British Railways Transition Team (GBRTT) is currently developing a Whole Industry Strategic Plan (WISP) that is shaped by the objectives of: i) meeting customer’s needs; ii) delivering financial sustainability: iii) contributing to long-term economic growth; iv) levelling up and connectivity; and v) delivering environmental sustainability. To do so, in December, it launched a call for evidence on how these objectives could be achieved and recently published a 90-page summary of responses from 307 organisations. These covered a wide range of issues, yet there was little mention of engineering despite the Williams Shapps report noting that “within today’s structure, no organisation has the financial, technical and operational authority to oversee the design, investment and management of major changes to infrastructure and on-train systems. There was a section on electrification which noted multiple respondents considered that an extensive rolling programme is required although some felt that, due to its high cost, only high priority routes should be electrified. There was no mention of the financial and operational benefits of electrification, including higher capacity freight trains, that the IMechE, ICE and PWI all mentioned in their responses. The Williams Shapps report also noted that electrification “has a clear record of attracting new passenger and freightPerhapscustomers.”thelackof engineering focus is due to responses being structured around the five strategic objectives. Laudable though these are, they all require an effective engineering strategy. Hence, it would be more meaningful to consider how the railway needs to be engineered to deliver GBR’s objectives. We would suggest that this is: A safe, efficient railway with the lowest possible emissions, that has sufficient capacity, reliability, and performance to deliver the timetable as well as satisfying current, and attracting new, passenger and freight customers.
GBR needs an engineering strategy that addresses each aspect of this objective. This requires a whole system approach which provides compatible infrastructure and rolling stock to deliver the timetable.
Paul Darlington tells us of his IRSE visit to Dublin where he learnt how Irish Rail (Iarnród Éireann (IÉ)) is investing in trains, infrastructure, and stations. He also found out why ETCS Level 1 train protection is being installed and visited the construction site of the new National Train Control Centre in Dublin. Interestingly, this will not control level crossings for which IÉ have dedicated control centres at Athlone and Mallow. system
The importance of a whole system approach is illustrated by the recent orders for around 7,000 new trains over a four-year period costing about £10 billion. This was yet another example of railway boom-and-bust procurement which resulted in additional costs and around 2,000 serviceable vehicles being scrapped − some being surplus electric trains due to cancelled electrification schemes. It is not unreasonable to conclude that a billion pounds or so was wasted as a result.
In this issue we explain how this whole system approach is being implemented in Wales, Scotland, and Ireland. We explain how Transport for Wales (TfW) is transforming its railway and, in particular, the South Wales Metro which carries 56% of its rail services. This will see a metro-style frequency from the introduction of new trains and an innovative partial electrification programme with an optimum mix of battery and electric traction. We also report on the many TfW trains being built at the CAF plant in Wales.Theproject to re-open the Levenmouth branch in Scotland will bring huge benefits for the local community. This is being electrified as it is rebuilt despite continuous OLE from Edinburgh being many years away. Thus, the first electric services from Levenmouth will use battery EMUs. However, unlike the Welsh Valley lines, this partial electrification is a transitional solution as these lines will eventually require full electrification for freight and fast passenger trains.
4
Though sometimes taken for granted, the timetable’s importance is shown by our feature on timetabling.
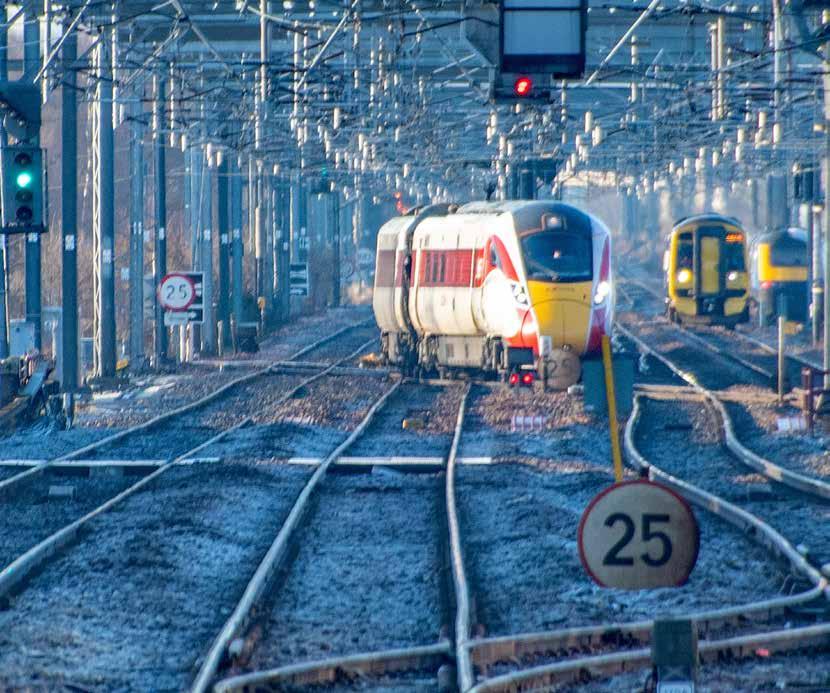
Editor David Shirres david.shirres@railengineer.co.uk Production Editor Matt Atkins matt@rail-media.com Production and design Adam O’Connor adam@rail-media.com Engineering writers stuart.marsh@railengineer.co.ukpeter.stanton@railengineer.co.ukpaul.darlington@railengineer.co.ukmark.phillips@railengineer.co.ukmalcolm.dobell@railengineer.co.ukgraeme.bickerdike@railengineer.co.ukdavid.fenner@railengineer.co.ukcollin.carr@railengineer.co.ukclive.kessell@railengineer.co.ukbob.wright@railengineer.co.uk Advertising Asif Ahmed asif@rail-media.com Chris Davies chris@rail-media.com Craig Smith craig@rail-media.com Rail Engineer Rail Media House, Samson Road, Coalville Leicestershire, LE67 3FP, UK. Switchboard: 01530 816 444 Website: www.railengineer.co.uk Rail Engineer Videos http://rail.media/REYouTube Editorial copy to Email: news@rail-media.com Free controlled circulation Email: subscribe@rail-media.com The small print Rail Engineer is published by RailStaff Publications Limited and printed by PCP Ltd. © All rights reserved. No part of this magazine may be reproduced in any form without the prior written permission of the copyright owners. Part of: ® www.rail-media.com THE TEAM SHIRRESDAVIDRAILENGINEER EDITOR In each of these cases, the railway administration has a clear whole system vision of how their railway needs to be engineered to meet future requirements. This has been derived from the engineering and operational realities of which there is little mention in GBRTT’s call for evidence report. From an engineering perspective, it is therefore difficult to see how the not-insignificant-cost of producing and analysing its 307 responses can be justified. Whilst consultation is clearly required, if GBR is to be a low-cost railway, excessive analysis such as that involved with the GRIP process needs to beTheavoided.importance of whole system engineering is further illustrated by our features on train wheels, the Vehicle/ Track System Interface Committee, and the Adhesion Research Group. Malcolm Dobell’s feature on the Elizabeth line’s platform screen doors also explains how they interact with trains and signalling. We also explain how depot infrastructure needs to be fit for new trains. Away from the main line, a great example of whole system engineering is Coventry’s Very Light Rail (VLR) initiative. This will see a lightweight vehicle running on a lightweight trackform that does not require utility diversions, and which has real potential to make light rail affordable for towns and small cities. The need for digital technologies is mentioned many times in the GBRTT report. Clive Kessell’s feature on digital engineering considers how these are being used in the real world. This includes how projects can benefit from treating data and information as digital assets as part of the outcome-based Project 13 approach used by East West Rail and the Levenmouth project.Thisyear saw the 10th IMechE Railway Challenge competition which is an excellent practical learning opportunity for young railway engineers. We report on this event and how it is one of the ways in which the IMechE’s Railway Division, and its predecessor, the ILocoE, has been supporting the rail industry since 1911.
Finally, Matt Atkins reports how, after four years, the world’s biggest technology trade fair will be back in Berlin in September. Rail Engineer will be there and looks forward to reporting from the show.
5 Rail Engineer | Issue 197 | Jul-Aug 2022
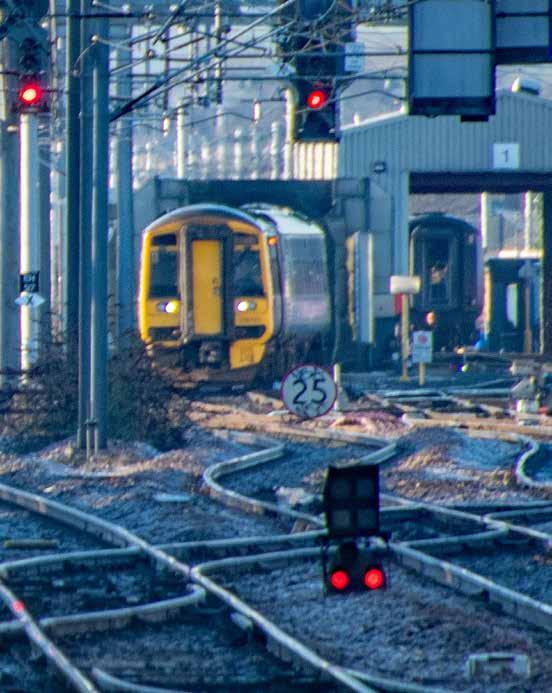

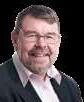

» Accelerated and improved technology deployment: “a raft of labour and life-saving technology that have been stuck in ‘trade union consultation’ for over two years”.
» Multi-skilling: investing in knowledge and skills so employees are better equipped to fix common faults themselves.
» Quicker fault fixes by employing multi-disciplined response teams and the greater use of remote condition monitoring to flag issues to control rooms before equipment fails.
DOBELLMALCOLM NOTICES6 Rail Engineer | Issue 197 | Jul-Aug 2022
Network Rail’s use of technology compares well with the other organisations but to take full advantage of technology deployment, Network Rail needs to have more flexible and responsive working practices.
Network Rail wants to be able to change practices so that a) the right maintenance is carried out at the right time and b) the right number of staff with the right skills are deployed at the right time.
On 28 July Network Rail announced it had started the legal consultation process with its trade unions on the maintenance reforms required to modernise and improve productivity and efficiency aimed at improving safety for both employees and passengers, boosting train service performance, and saving money. The objective stated was to “run the railway more efficiently and put the industry on a firm financial footing for the future”.
» Use of technology to inform maintenance requirements.
The announcement added that the proposed changes would make Network Rail’s maintenance activity much more efficient and would help it to catch up with wider norms in comparable industries, highlighted in the recent Nichols report. But what did the Nichols report actually say?
» Multifunctional teams: using mixed-skill teams so that, for example, three mixed-skilled specialists might be sent in one van to fix a fault rather than two specialist teams in two vans.
» Individual rostering: sending the right number or people to fix a fault rather than teams of a fixed size.
Network Rail's proposed maintenance reforms
Network Rail said that the proposed reforms would likely lead to a smaller maintenance workforce, reducing it from around 10,000 to around 8,000, but that it expected to be able to implement the change through voluntary severance, retraining, and redeployment.
Network Rail asked Nichols – a respected management consultancy, expert in advising on business change initiatives – to carry out a short, independent, comparative study to look at the extent to which the working practices being considered are used in other industries with similar characteristics to Network Rail. Specifically, those with safety critical assets, linear in nature, and subject to external safety regulation, i.e., rail, aviation, roads, and utilities. Based on interviews with these organisations, Nichols’s high-level findings were as follows:
The proposed reforms in Network Rail’s maintenance organisation are intended to deliver:
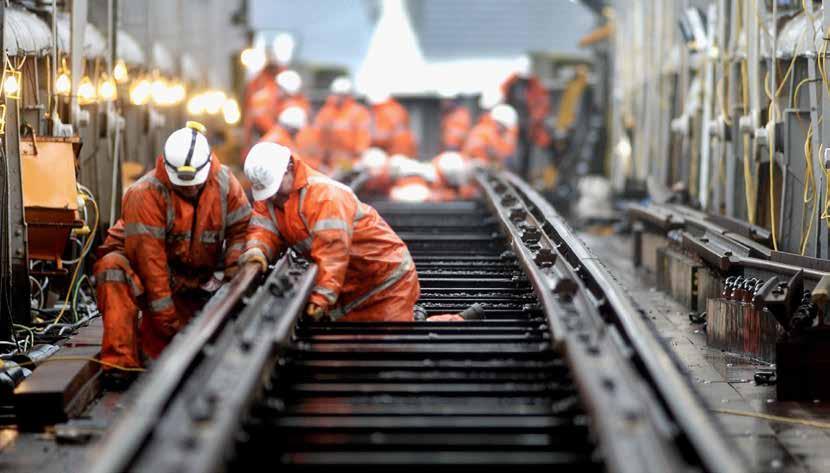
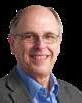

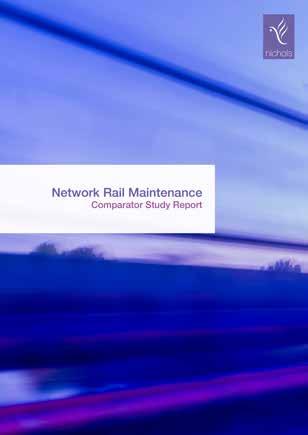
7NOTICES Rail Engineer | Issue 197 | Jul-Aug 2022
» Individuals with broader skills. Frontline operatives in Network Rail are managed in discipline-based teams and operate independently of each other. This contrasts with other organisations where entry-level maintenance practitioners were expected to be able to cover a wide range of tasks.
» Maintenance practices. Moving to more condition and/or risk-based maintenance is consistent with the other organisations. Network Rail review their standards every five years or when there is an event that prompts a change. Network Rail also encourages suppliers and stakeholders to challenge standards and propose changes. Others tend to review their standards more frequently, although the volume and complexity of Network Rail’s standards catalogue was noted.
» Independent rostering. Current Network Rail practice appears to be less flexible than most interviewees who roster staff individually, have a shorter roster cycle managed centrally, and did not report issues with deploying staff when needed.
» Multifunctional teams. Network Rail practice is to have individual teams by discipline. Nichols heard that multi-disciplinary teams who can cover the great majority of most maintenance needs was a very common model with other organisations that appears to be more efficient.
The biggest section in the report concerned night-time and rostering arrangements, highlighting that rostering and maintenance planning are closely linked, night-time maintenance is the norm in similar industries, and that multi-functional teams with multi-skilled personnel able to work across geographical boundaries is usual in other organisations.NetworkRail’s latest pay offer to the RMT comprises a basic cost of living increase and a productivity related increase. Although Rail Engineer would not wish to comment on the cost of living increase, the Nichols report shows that there is scope for significant productivity improvements. The full report can be found at working-practicesof-restrictive-and-inflexible-report-finds-network-rail-guilty-news/new-independent-networkrailmediacentre.co.uk/https://www.

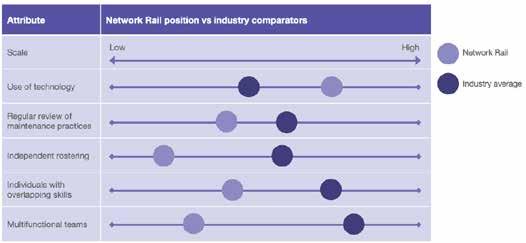
SHIRRESDAVID NOTICES8 Rail Engineer | Issue 197 | Jul-Aug 2022
»
»
»
This year the Institution of Engineering and Technology (IET) published its ‘Guide to Earthing and Bonding for AC Electrified Railways’ and used it as a basis for its recent two-day technical seminar on this subject. During the seminar, Earthing and Bonding (E&B) was referred to as a dark art. This was perhaps not surprising as integrating the earthing of an AC electrified railway with various other railway electrical systems, and lineside and station assets, is a complex subject requiring specialist knowledge.
»
»
Yet rail engineers of all disciplines should at least have an awareness of this topic as their assets might suffer from large traction fault currents due to insulation breakdown or breakage of live conductors.
The seminar covered the following sections of the IET’s Earthing and Bonding guide: AC traction electrification distribution system Protection against electric shock Mass of earth as part of the traction return system Traction return requirements and circuit configuration Electrification system assets excluding the traction return Lightning protection for railway structures Assets not forming part of the electric traction system Earthing and bonding at AC/DC interfaces
»
»
»
The dark art of earthing and bonding
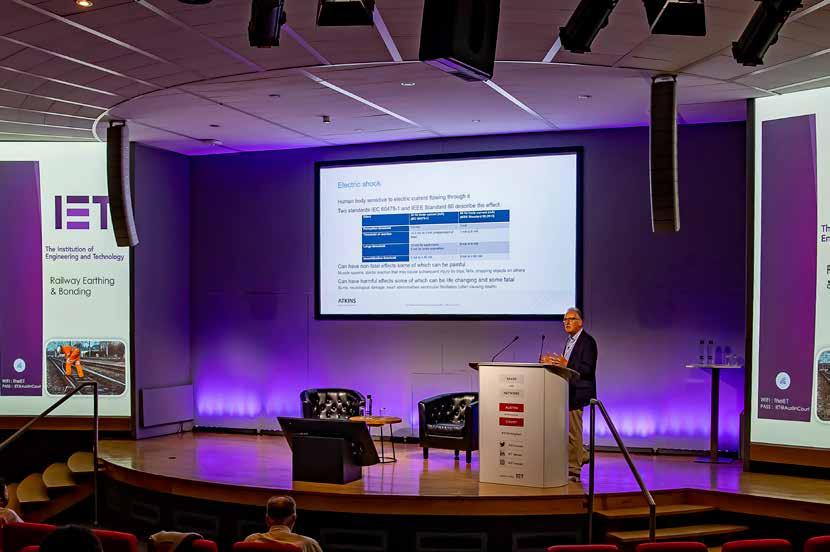
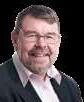

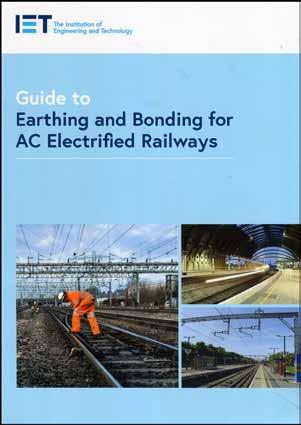
An RMT report has revealed that the government’s switch to management-fee based contracts guarantee around £124 million each year for train operating companies, restoring profits for the year to £600 million across the industry for 2020-21, with every owning group improving its position during the pandemic year.
The entire transport system is under threat from years of profiteering, job cuts, pay freezes and attacks on terms and conditions. Rail workers have had enough!
Britain’s Largest Specialist Transport Union Protecting our members’ interests is our priority Join us today rmt.org.uk FREEPHONE 0800 376 3706 RMTunion Jointhefightback...JOINRMT
STOP STARTtheprofiteeringinvestinginrail D EFEND Rail
All this is being paid for by slashing jobs, cutting services, closing ticket offices and suppressing the wages of transport workers.
Network Rail has also been told by the government to make £billions of cuts.
The ‘Fat Cats’ have lobbied for these changes because of the failures of franchising and they are now reassuring their investors that there will be regular dividends from their rail operations.
Related to lightning protection is the development of surge arresters which can reduce bridge reconstructions required by electrification schemes by reducing bridge OLE clearances. They do so by preventing OLE over voltages from lightning strikes with the use of metal oxide semiconductors. These nonlinear resistors act as insulators at normal voltage but once a 75kV threshold is reached becomes a conductor. Such surge arrestors have trip counters to count the number of over voltage events. Whilst they offer the potential to significantly reduce electrification costs, the associated lower wire height and reduced clearance has long term maintenance implications which are still being evaluated.
NOTICES10 Rail Engineer | Issue 197 | Jul-Aug 2022
The IET is to be commended for its guide and its associated seminar. The guide is available from the IET’s online shop.
Lightning
Elizabeth line
The session on lightning protection covered both protection of AC OLE systems and other railway electrical systems from lightning strikes. The unpredictability of such strikes was illustrated by a speaker from the Hong Kong MTR (Mass Transit Railway) who described how MTR was surprised to find a signalling relay room had been badly damaged by a lightning strike. This was unexpected as the relay room was in a tunnel, 2.5 kilometres from the tunnel portal, and a hundred metres below the lightning strike.
Whitechapel earth mat installation.
The Elizabeth line presented a particularly complex E&B challenge, not least because it was building a 25 kV AC railway through London Underground (LU)’s third rail system. The initial modelling identified a hundred locations where LU was vulnerable from stray 25kV currents and a further 650 earthing and bonding hazards. This modelling had to be done at the start of the project as station earth matts were one of the first things to be built. As part of the assurance regime, the evidence needed to close out E&B hazards also had to be defined at the start of the project so that this could be specified in the design and built contracts.
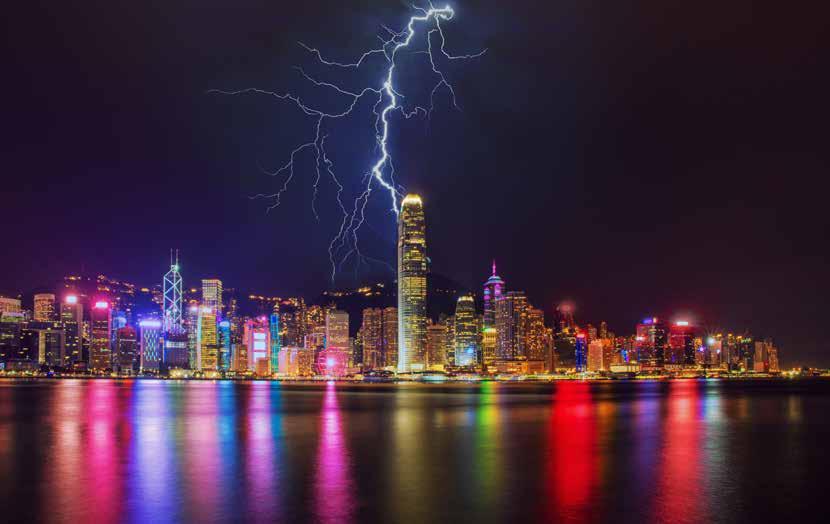
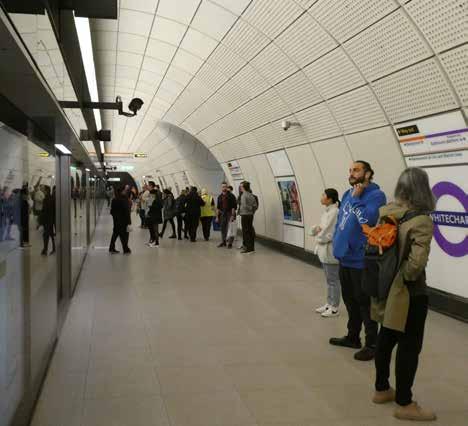
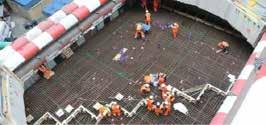
With over 45 years’ experience, Siderise passive fire and acoustic insulation systems provide high-performance solutions for the rail industry without compromise. Coaches built incorporating our rigorously tested thermo-acoustic insulation, benefit from improved sound absorption, reduced sound transmission and improved reaction-to-fire performance to EN45545-2. The result, all-round comfort and peace of mind – from roof, to floor, to walls.
• Exceptional thermal and acoustic performance
ON THE RIGHT TRACK FOR ACOUSTIC, THERMAL AND PASSIVE FIRE PERFORMANCE
• Thermo-acoustic insulation rail products are independently tested for fire, smoke and toxicity performance (to EN45545-2)
• In-house acoustic engineers to assist with product selection
• Wide range of products including vibration damping materials Get on the right track at siderise.com
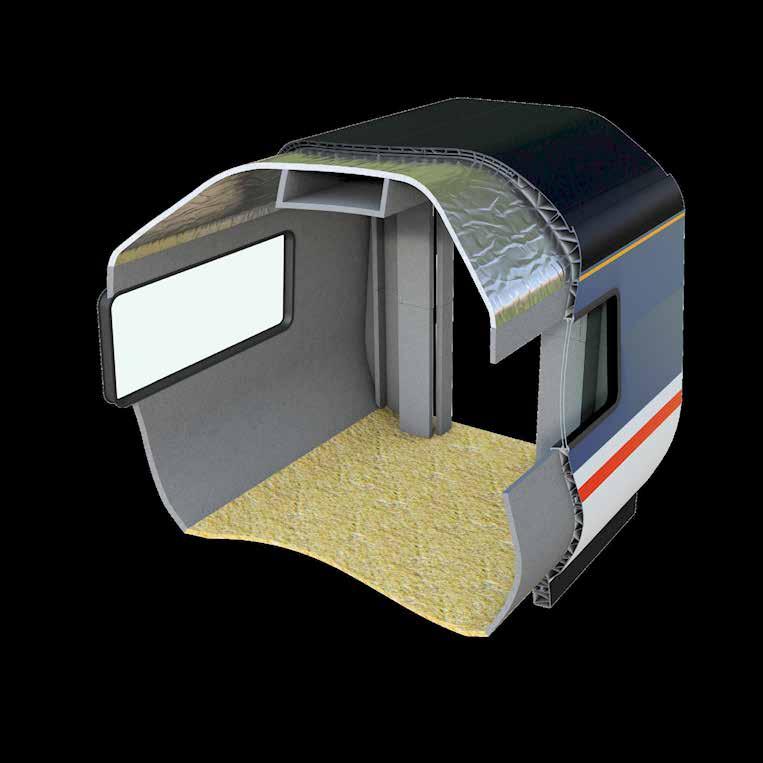
Three Metros
Transport for Wales (TfW) is developing plans for the following Metros: Swansea Bay and West Wales, North Wales, and South Wales. The Swansea Bay and West Wales Metro proposals
transformation SHIRRESDAVID WELSH RAIL
ALL IMAGES: TRANSPORT FOR WALES Transport for Wales rail services. 12 Rail Engineer | Issue 197 | Jul-Aug 2022 ROLLING STOCK & DEPOTS
T he Well-Being of Future Generations (Wales) Act 2015 aims to improve the social, economic, environmental, and cultural well-being of the people of Wales by giving public bodies a duty to set appropriate objectives and act in accordance with sustainable development principles. These include long-term thinking and a collaborative, more joined up approach. A Future Generations Commissioner provides the required support and monitors compliance with these objectives which are supported by various strategies including one for a low carbon Wales, a sustainability plan, and the Welsh transport strategy.
These documents all stress the need for modal shift from car dependency to sustainable forms of transport. The most effective way of reducing transport CO2 emissions in the near-term is replacing car journeys with those on the public transport and active travel. However, this requires both infrastructure and behavioural change measures. To provide a more desirable alternative to the car, the image and the reality of public transport needs to be transformed with a metro-style frequency and better-connected integrated services. Planning Policy Wales also sets out a sustainable transport hierarchy for planning to prevent car-dependent developments.
The Welsh transport strategy sets a target of increasing journeys made by public transport, walking, and cycling from the current 32% to 45% by 2040. Its sustainable transport hierarchy promotes active and public transport over private cars. This includes the provision of coherent ‘Metro’ networks of low-carbon buses integrated with transformed rail services.
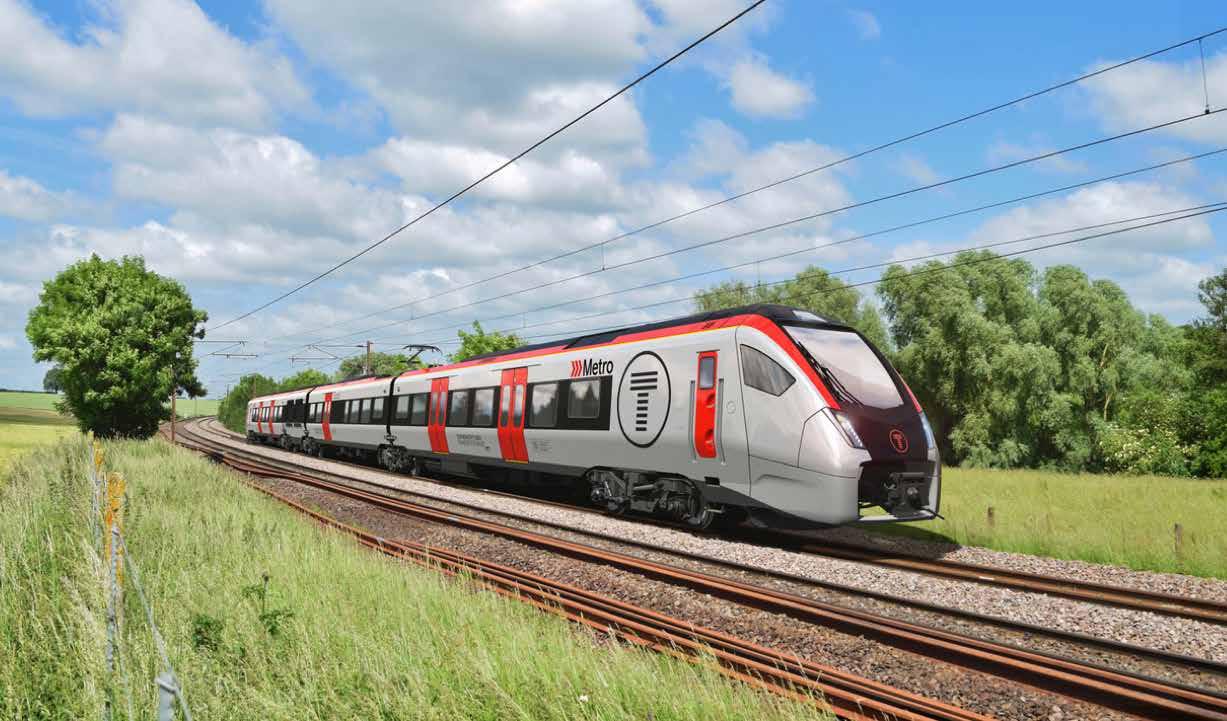
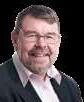

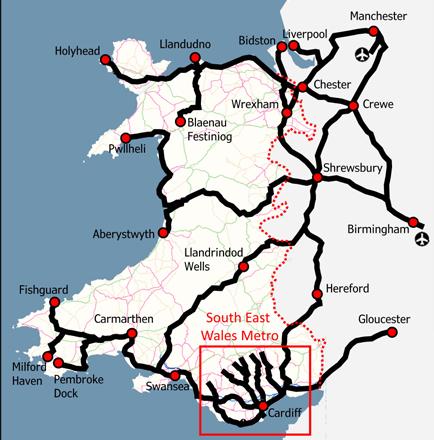
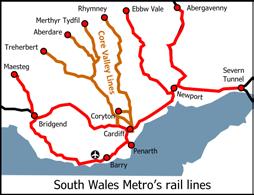

The previous Welsh rail franchise had services that were fragmented, underfunded, and overcrowded. In 2021, its newest trains were 20 years old, and the average age of its fleet was 30 years, compared with the national average of 17 years. Though TfW had ambitious plans, immediate action was needed. In 2019, two sets of Mark II coaches hauled by Class 37 locomotives were introduced on Rhymney services. TfW was also able to provide longer, more frequent trains by the acquisition of: 18 single-car Class 153 units; twelve Class 170 units (eight x three-car and four x two-car); eight four-car Class 769 units; and three x four-car sets of ex-LNER Mark 4 coaches with driving van trailers (DVT) hauled by Class 67 locomotives. The Class 153 fleet units currently operate on the Heart of Wales Line, routes in North and West Wales, and the Core Valley Lines to Rhymney, Coryton, the City Line and Cardiff Bay. A further four units have been purchased Class 769 at Cardiff
TfW also proposes to upgrade the North Wales and South Wales main lines and to improve connectivity, support rural communities, and promote tourism on other Welsh rail corridors. It aims to integrate the rail network with bus services and active travel to deliver seamless “end to end” journeys.
Immediate action
include increased services and other proposals currently under development including a West Wales Parkway, other possible new stations, and lineThere-openings.NorthWales
Metro saw a new service between Chester and Liverpool over the re-opened Hatton curve in 2019 and will see enhanced Borderlands services integrated with Merseyrail services with additional and upgraded stations and possible line re-openings. As described later, work on the South Wales Metro is well advanced.
DrivingCentral.Van Trailer heads a set of Mark 4 coaches of a Holyhead to Cardiff service.
Yet, how can such commitments be delivered when, unlike in Scotland, transport is not a devolved matter in Wales? The answer is that, in 2018, the UK Government agreed that the Welsh Ministers Government can manage the new Wales and Borders rail franchise. This enabled it to start the transformation of its rail services. Hence, shortly after this agreement its arm’s length body, Transport for Wales (TfW), awarded this franchise to a joint venture of Keolis and Amey. It was estimated to be worth £5 billion over the next 15 years including £800 million for new trains and the delivery of the next phase of the South Wales Metro project. In 2018, the Welsh Government also announced £738 million funding for the next phase of this Metro which includes electrification of the valley lines. This funding package includes £164 million from the European Union and £125 million from the UK Government. In March 2020, Wales also took direct control of the Core Valley Lines (CVL) which, although they account for only 15% of Welsh train miles, carry 56% of all Wales and Borders passenger services. These are the lines to Cardiff Bay, Aberdare, Coryton, Merthyr Tydfil, Rhymney, Treherbert, and Radyr, but exclude Cardiff Central and the Great Western Main Line. When TfW took over their ownership from Network Rail, £900 million was transferred from the UK Government to the Welsh Government for their operation, maintenance, and renewal.
13 Rail Engineer | Issue 197 | Jul-Aug 2022 ROLLING STOCK & DEPOTS
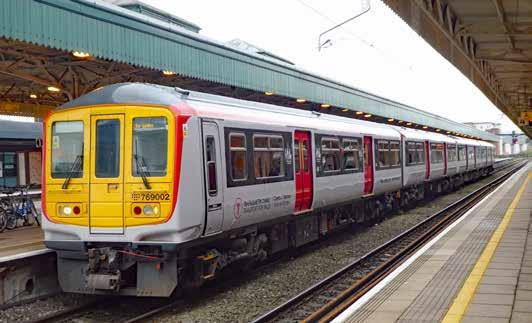
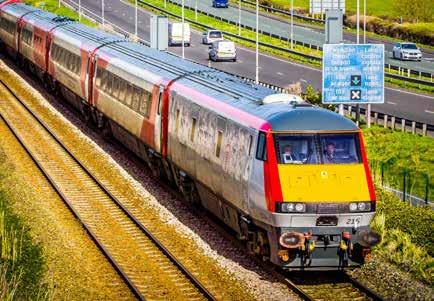
As well as acquiring extra trains, a £40 million fleet refurbishment programme has just been completed. This provides the Class 153, Class 158, and Class 175 fleets with USB and electric charging points, re-covered seats, new carpets, and new interior fittings, rebranding them with TfW’s grey and red livery. Work on the 26-vehicle Class 153 fleet was done at Chrysalis Rail’s Landore works.
In 2018, KeolisAmey announced its first rolling stock deal 15 days after being awarded its franchise. This was for five three-car Class 230 battery diesel hybrid trains produced by Vivarail as described in issue 186 (Sept-Oct 2020). These use GPS systems to cut out the engines in stations and environmentally sensitive areas and are to be introduced on the WrexhamBidston, Conwy Valley, and Chester-Crewe routes.Unfortunately, due to technical issues, specification changes and Covid-related driver training delays, these trains have been significantly delayed. In April, a battery related thermal incident led to a modification being devised which is now being fitted to the fleet. TfW now aims to bring these trains into service by December 2022. The next order immediately followed the Class 230 order. This was for 77 x 100mph Class 197 DMUs (diesel multiple units). Twenty-six of these are three-car units, of which 14 have First class seating, and 51 are two-car units, of which 21 Newly refurbished Class 153 unit. CAF Class 197 unit at Blaenau Ffestiniog.
The Mark 4 coach sets operate the three eachway weekday Holyhead to Cardiff services. TfW has also acquired five further Mark 4 coaches for use on Manchester to Swansea services and lengthening of all rake to five passenger vehicles plus a DVT. Bringing these into service requires modifications for Class 67 operation, fitting selective door operation, gauge clearance, and the development of stabling and depot strategies.
outright by TfW and are awaiting work to reconfigure them to provide enhanced cycle storage on the Heart of Wales Line.
The Class 158 work was done at Arriva TrainCare’s facility in Crewe and included reliability improvements to electrical, heating, and wheel slide protection systems. This 24-train fleet operates the Mid Wales Cambrian Line and services in North Wales. Alstom’s Technology Centre in Widnes refurbished the 27 x Class 175 units which operate long-distance services throughout the Wales and Borders network.
New trains
The Maesteg, Cheltenham, and Ebbw Vales routes saw the introduction of Class 170 units. Class 769 FLEX units have also operated services to Rhymney and Penarth services since late 2020. These initially suffered engine cooling problems and are entirely operated in diesel mode with their pantographs removed. The reliability of this fleet is now much enhanced, though still needs to be improved.
14 Rail Engineer | Issue 197 | Jul-Aug 2022 ROLLING STOCK & DEPOTS
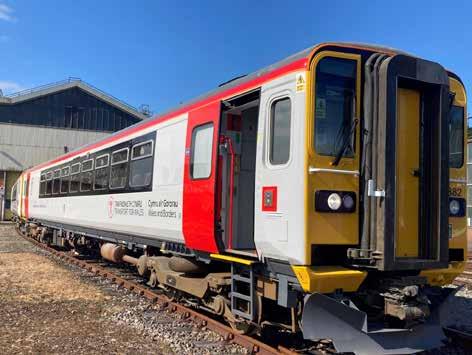
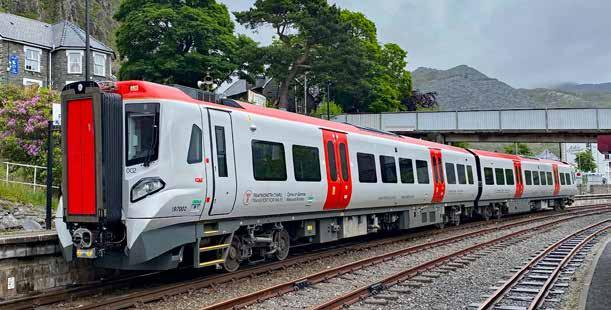
have ETCS for use on Cambrian coast services. These are being built at the CAF plant in Newport and so met KeolisAmey’s commitment to ensure at least half the new fleet is assembled inThisWales.order required these units to be in service by September 2022, except for seven two-car units to be delivered in September 2024. They will generally operate long distance services. However, a recent press release specified that they run on the route that was to have been operated by the Class 230s. The next order, in August 2018, was for three types of Stadler trains for the South Wales Metro. These are:
» Seven x three-car and 17 x four-car 75mph Class 756 FLIRT Tri-mode units which can be powered from 25kV OLE or by their centre power car which has three battery rafts and one diesel engine. These will run on electric/ battery power on the Rhymney/Coryton lines and on battery/diesel power on Penarth/ Barry/Bridgend services. These have large batteries for longer range but require more time to recharge. If required, they can operate in multiple with Class 231 units. The first Class 756 is expected to be delivered in November.
» 36 x three-car 60mph Class 398 Citylink Tram Trains. Apart from their higher floors, these are like the Class 399 units operating on the Sheffield Supertram network. They are powered by 25kV OLE or batteries and are designed for frequent short unpowered sections. They will run on the Treherbert, Aberdare, and Merthyr Tydfil lines. The intention is that the Metro will be expanded for these trains to run on-street for which the immediate priority is the Cardiff Bay area.
15 Rail Engineer | Issue 197 | Jul-Aug 2022 ROLLING STOCK & DEPOTS
Infrastructure work In June 2019, KeolisAmey awarded early contractor involvement contracts to Balfour Beatty, for track, power, and fibre packages, Alun Griffiths for civil works, and Siemens Mobility for signals and telecoms.
The South Wales Metro Infrastructure Hub at Treforest was opened in January 2020. This is a material distribution centre for the project and will evolve into a maintenance depot. It is also home to the Craidd (Welsh for core) Alliance which comprises of Balfour Beatty, Siemens Mobility, Alun Griffiths, TfW and Amey. In November 2021, the Craidd Alliance became the world’s first rail alliance to receive certification to the ISO44001 Collaborative Business Relationship Management Systems standard. Stadler Class 231 FLIRT unit at Cardiff Canton. Newly arrived Stadler Class 399 Tram Train.
The Class 398 units are capable of line-ofsight running and have passive provision for 750V DC opportunity charging. The first unit is now being tested at the Rail Innovation & Development Centre in Melton. All these Stadler units have sliding steps and floors that conform to the standard 915mm platform height above rail level. This, together with a programme of CVL platform adjustments, offers level boarding.
» Eleven x four-car 90mph Class 231 FLIRT DMUs which are powered by four Deutz 480kw V8 engines that meet stage V emission limits. These are in a seven-metre-long diesel power car in the centre of the train. They will operate services from Cardiff to Ebbw Vale, Cheltenham and Maesteg. The first unit was delivered in December 2021.
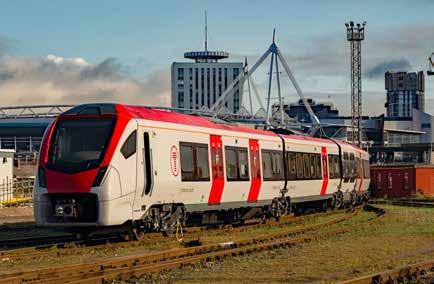
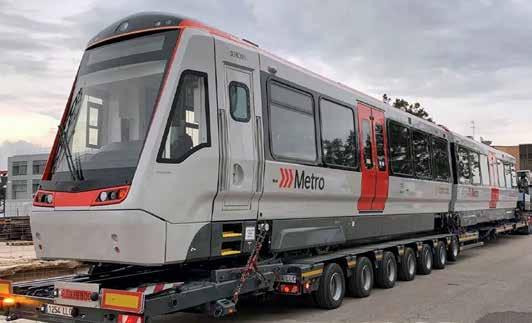
The CVL infrastructure work involves 45 projects with a total of 47,000 programmed tasks with 1,500 design integration milestones. Intermittent electrification
The CVL electrification is the UK’s first large scale use of intermittent electrification which is possible as there is no requirement for electrically hauled freight trains. This approach has permanently earthed sections (PES) and catenary free sections (CFS) of OLE.
With a PES there is no break in the contact wire and so no requirement to lower the train’s pantograph. These are used when OLE can be run under a bridge but there is insufficient clearance for it to be energised at 25kV. Immediately before a PES, a beacon opens the train’s 25kV vacuum circuit breaker (VCB) for it to coast without power under the earthed OLE. After the PES, the VCB closes once the train detects live OLE for more than two seconds. CFS are used where there are complex areas or tunnels that would be particularly expensive to electrify or at bridges with no clearance for the wire itself. At least 13 seconds running time before the CFS, a beacon lowers the train’s pantograph. The OLE terminates at least 10 seconds before the obstruction. At this point the wire height is over 6.3 metres which is above the pantograph’s maximum reach. Thus, if the beacon failed to lower the pantograph, at this point it will rise to its maximum height and the pantograph auto drop-down valve will operate to lower the pantograph before it hits the obstruction. Immediately after the train is back under OLE, a beacon raises the pantograph.170singletrack kilometres (stk) of the CVL is being electrified. This requires about 3,000 masts. Its 30 CFS and 60 PES respectively save 81 and 24 stk of electrification which includes complex locations such as Caerphilly tunnel, and Cardiff Central and Queen Street stations. This results in a capital cost saving of about £150 million but increases the cost of trains, with each of the 54 CVL hybrid trains having a battery costing around £100,000 each that must be changed every seven to 10 years. Also, a good few tonnes extra battery weight adds to energy consumption and running costs. of Power Substation
Station work includes platform adjustments for level boarding at 110 stations, upgrading facilities at 68 stations, 12 new station footbridges, eight extended and eight new platforms which includes an additional platform at the single-track Cardiff Bay station. Two new stations are also to be built at Gabalfa and Butetown.
Installation
As mentioned in issue 195 (Mar-Apr 2022), signalling and telecoms work includes 50 new signals, over 300 axle counter sections, 98 signalling location cases and a new 10Gbit telecoms network. This infrastructure work started in July 2020 and so was subject to Covid precautions. Since then, there have been a series of blockades, most when rail traffic was minimal due to the Covid emergency. These recouped Covid programme delays and maximised economies of scale with, for example, four kilometres of rerailing done in one three-week blockade.
The track work includes six new loops, four loop extensions, 30 kilometres of line speed improvements at 37 sites and 20 track lowers to provide OLE clearance as well as the remodelling Cardiff Queen Street junction with 17 new point ends. Civil engineering work includes reconstructing two overbridges and 52 bridges requiring parapet works.
Traction
at Radyr. Rail Engineer | Issue 197 | Jul-Aug 2022 16 ROLLING STOCK & DEPOTS
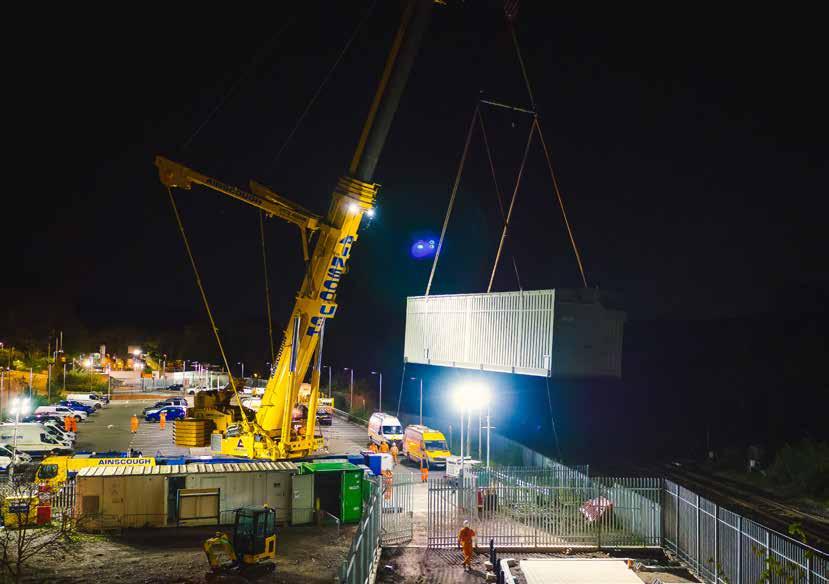
Making best used of this constrained site is helped by the ability of these tram trains to operate on 22-metre radius curves. This £140 million facility will be the base for 400 train crew and 54 staff at its electrical and signalling control centres which will take over control of CVL signalling from the Welsh ROC. The depot will have three 100-metre maintenance pit roads, one with retractable OLE. For overnight charging, its 10 stabling sidings will be the only electrified external lines in the depot as depot train movements are battery powered. The depot will have a vehicle washer and wheel lathe. Its track layout requires 32 point ends. Access to the depot is from a tight curve in an as-yet-to be built tunnel under the Ffordd Bleddyn Bridge. Depot signalling uses a lowcost, programmable logic controller depot signalling system, developed by Sella Controls andDemolitionHima. of the former industrial site started in July 2019. Construction work began on site in August 2021 with the erection of the depot steelwork starting in January 2022.
Taffs Well depot Whilst the new Class 231 and 756 trains will be maintained at an upgraded Cardiff Canton depot, the Class 398 tram trains require a new depot which is being built at Taffs Well. A control centre is also to be provided. These are being built on the 10-acre site of the Forgemaster engineering plant site which closed in the 1980s.
Taffs Well depot site at end
BleddynentrancetodepotturnoutsRecently2021.installedtoTaffsWellinMay2022priorconstructionofdepottunnelatFforddBridge.
TfW considers that its intermittent electrification, which requires battery power needed for 40% of the network, is the most efficient balance between infrastructure investment and train operations, as detailed power and battery performance modelling has been done to achieve the optimum balance of vehicle performance and battery life against infrastructure capital costs. Thus, this whole-system engineering approach minimises whole-life costs. Similarly, an integrated approach is needed to manage infrastructure, rolling stock, and operations assurance and approvals required for entry into service.
Rail Engineer | Issue 197 | Jul-Aug 2022 17ROLLING STOCK & DEPOTS
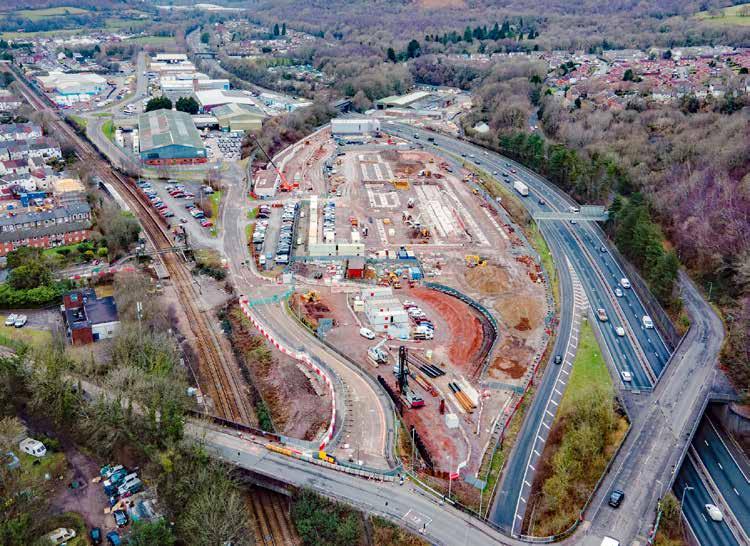
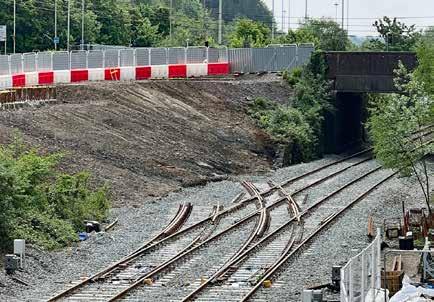
» May 2024 – providing an hourly all stations service between Aberystwyth and Shrewsbury.
In addition, in 2023, five-car Class 197 trains will run alongside five-coach Mark 4 sets between Manchester and South Wales. These units will also operate alongside Class 230 units to provide a two trains per hour (tph) service between Wrexham and Bidston although a date for this has yet to be announced.
Planned energisation dates for CVL electrification are: March 2023 - Merthyr Tydfil and Aberdare; July 2023 – Treherbert; and September 2024 – Rhymney. By 2025, Stadler trains will be operating on all CVL services to double the frequency of the current timetable. By then, there will be around 30% more weekday services, and 95% of journeys on Welsh railways will be on new trains. Electrified CVL lines and new hybrid trains will also have reduced CO2 emissions across the rail network byIn25%.thisway, in less than 10 years, TfW will have delivered its commitment to provide a significantly improved, greener train service for future generations. England and Wales, 1160901, and Scotland, SC047016.
Artist's impression of completed Taffs Well depot. All about people people working in public transport...people like you! Health, welfare and financial help in times of need, hardship and distress. £1.25 a week covers you, your live-in partner and dependent children. 0300 333 2000 | help@tbf.org.uk | www.tbf.org.uk Transport Benevolent Fund CIO, known as TBF, is a registered charity in
less20pthanaday 18 Rail Engineer | Issue 197 | Jul-Aug 2022 ROLLING STOCK & DEPOTS
It is now four years since the Wales and Borders train franchise was awarded to KeolisAmey. Since then, many of the new trains ordered have been built and infrastructure work is well Someadvanced.oftheoriginal target dates have had to be revised with Covid causing supply chain disruption and difficulties training new train crews. Despite this, commitments announced in 2018 are set to be delivered in the next two or three years.
» December 2022 – making Cardiff to Cheltenham an hourly service and providing an additional service per day on the Heart of Wales Line between Swansea and Shrewsbury.
Delivering the future
» December 2023 – providing a new hourly service between Liverpool to Llandudno and extending the current Manchester Airport to Llandudno service to Bangor.
With testing and training of Class 197 units well underway, it was recently announced that these units will be launched on North Wales routes in autumn. They will then be progressively introduced on Cambrian, Cheltenham, and Pembrokeshire services. They will also operate Ebbw Vale services until sufficient Class 231 FLIRT units are available.
In September 2021, TfW announced revised service introduction dates as follows:
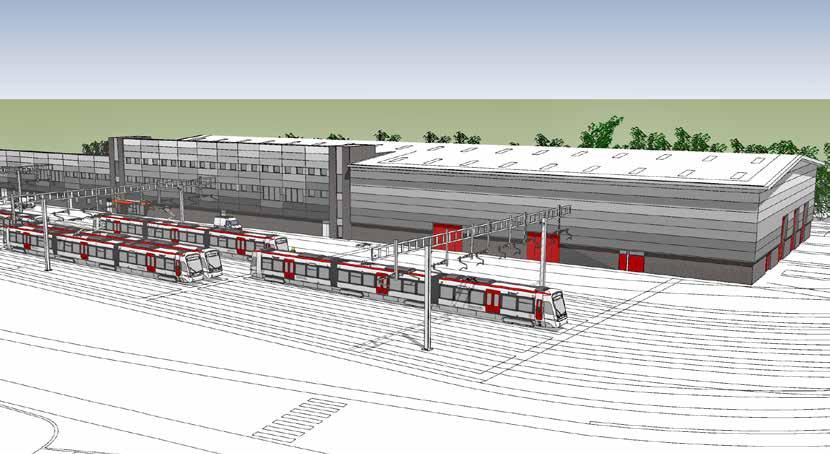
T o ensure trains are safely and efficiently maintained and stabled, an essential and critical element of every railway is a maintenance depot. Rolling stock is as reliable as ever, but it is also more sophisticated as ever and, like all engineering products, trains need facilities for servicing, inspection, overhaul, maintenance and major repairs/upgrades, and cleaning.
DARLINGTONPAUL TECHNOLOGY 19 Rail Engineer | Issue 197 | Jul-Aug 2022 ROLLING STOCK & DEPOTS
Another requirement is a reliable electrical supply and communication links, and good security is essential as there are a lot of very expensive trains and equipment held in a small area.
TRAIN DEPOT
The elements that need supporting include water supply; communications bus; electrical supply, including –traction, lighting, and on train power; heavy maintenance and wheel profiling; and signalling and telecoms, such as radio and automatic train warning and protection systems. No two depots are the same, and the facilities provided will be determined by the rolling stock serviced by the depot. However, depots can be provided with some or all the following facilities: stabling areas; workshops; wash plant; specialist equipment and plant; test track; test facilities for signalling telecoms and traction power; operations and depot control centre; administrative buildings; train lifting facilities; under-floor wheel lathe; and logistics and storage. Unsurprisingly, depots may also need room to expand if required. Depots are mainly located in historic locations but, ideally, they need to be sited with good rail and road access to enable easy transfer of trains to and from their service start and end points, and to ensure good access for maintenance and logistics support – including heavy equipment and routine and specialist support staff.
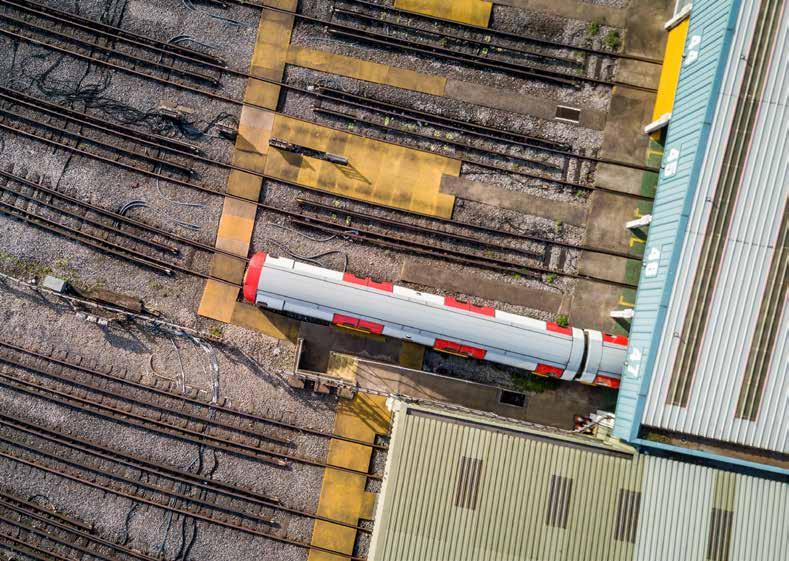
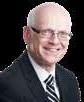

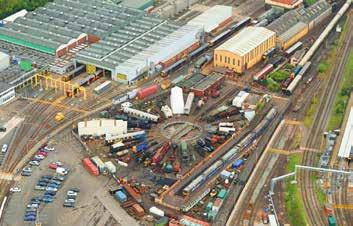
Depot facilities and technology will need to be able to maintain the fleet of trains and support any outof-course activities, including potential fleet modifications.
20 Rail Engineer | Issue 197 | Jul-Aug 2022 ROLLING STOCK & DEPOTS
NPB and POSG also believe that depots are not seen as part of the national network, which has led to a reduced focus on implementing good health and safety on Britain’s railways. Depots are busy areas, and the internal layout needs to be such that the maintenance, inspection, servicing, and cleaning requirements can be undertaken in as safe and efficient a manner as possible.
Depot capacity will depend on the number and type of trains, berths and equipment, the progression of vehicles through the depot, and the sequence of work and vehicle downtimes, along with the team structure and working methods. Poor depot design, equipment, and management is likely to negatively impact the quality of investigations, result in deferred work, and increase the risk of not meeting availability targets with serviceable vehicles.
Each depot will need to determine the planned number of trains that are to be stabled and maintained, but this should be below the maximum number to allow for unplanned interventions.
Depots should be operated within the competency of the depot staff to perform work safely and to enable and sustain long-term reliable growth. Deferred work trends should be monitored to check if there are enough competent frontline maintenance staff. Detailed logistic planning of the trains/ unit throughput of the depot will be needed to ensure good capacity, and efficient and good product quality.
The plan should also take into
For existing depots, the service specification and the physical constraints of the depot need to be balanced to deliver an optimised operation so that the risk to safety, performance, and capability is acceptable. When planning any new depot facilities, the train layout configuration should be optimised, from the receipt of trains to delivery back to the network for service operation. Depot equipment and logistics should be optimised to provide timely procurement and provision of key items to exploit innovation and creative new ways of working where appropriate, so that maintenance downtime is minimised, availability is maximised, and risk of inservice failures is reduced.
The ability to complete work and deliver trains for service should be measured, and trends analysed to understand the need and opportunities for further changes. Trains are becoming more reliable, but with more complex and specialised equipment, so logistical planning also needs to assess and employ specialised and original manufacturerequipmentresources when appropriate. Arrangement should be made for call out contracts with agreed rapid response times for key assets, including arrangements for rerailing vehicles within the depot. Planning and maintenance
Improvements required The Network Performance Board (NPB) and Passenger Operators’ Safety Group (POSG) have identified that improvements are needed in train depot service delivery and safety. An increase in late starts and wrong formations has caused depot delays to increase by 86% since 2014, and there have also been three train depot fatalities in the last seven years.
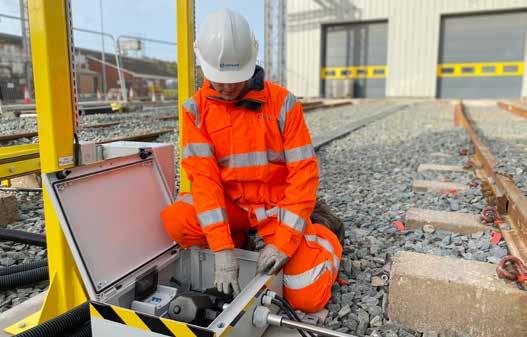
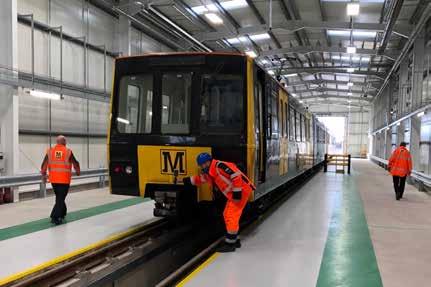
• Depot Protection Systems (DPS) • Depot Control Systems (DCS) • Combined DPS/DCS • Locally Operated Points Systems (LOPS) • SIL 2 Rated Systems as Standard Rail Depot Safety Experts Protect your Sta and Equipment +44 (0)1621 743 743 info@ www.FirstClass-Safety-Control.co.ukrstclass-safety-control.co.uk www.rail-media.com Subscribe to our free publications at www.railsubs.com 21 Rail Engineer | Issue 197 | Jul-Aug 2022 ROLLING STOCK & DEPOTS

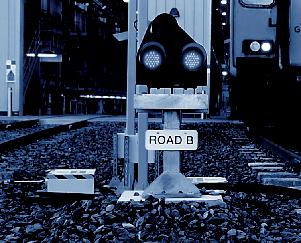


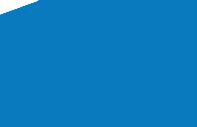
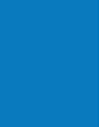
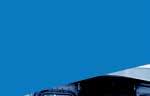


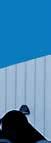

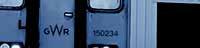
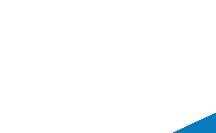

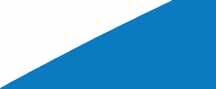
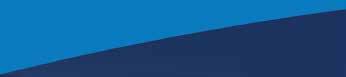

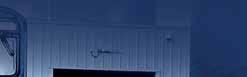
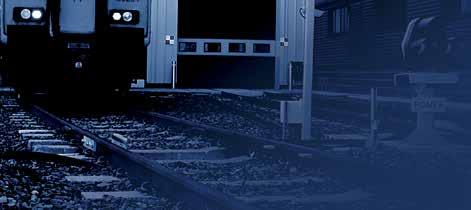
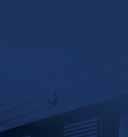

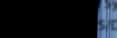
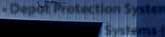



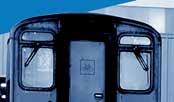


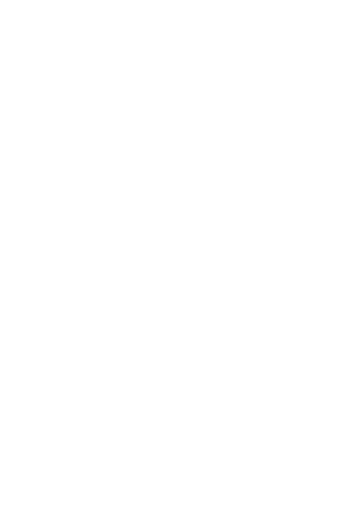










It will also need to take into account the formation lengths of trains, the siding lengths, and reception roads to determine the total depot capacity. Infrastructure and plant are vital for the safe and efficient management of any depot. Track and plant such as lifting equipment, washer and fuel points should be maintained to the required specification. Some depot infrastructure and plant may be considered ‘golden assets’ as they may be vital to service delivery, and maintenance plans should be enhanced accordingly. Depot plant will have specific environmental risks such as fuel spillage which should also be part of the maintenance and management plans. Those engaged in working at depots should be involved in the planning and assessment of work required, and in the assessment and control of risks to ensure depot operation is as safe as possible. It is very often the case that those doing the actual work may know the most efficient and safest way to carry the work out, although this also needs to benefit from independent assessment from third parties.
Health and safety
account how many trains can be accepted, what the headways are between trains, and how many trains can exit the depot.
There should be safe segregation of people and moving trains during all activities, including the use of authorised safe walking routes. A train depot should be a secure and safe place of work, and hazards should be identified and removed, or the risks reduced and controlled so far as is reasonably practicable.
The reduction and control of risks should be done by the design of operational and engineering controls, and not just rely on training, information, and behavioural controls.Procedures and systems should be updated following accidents and incidents, both in the depot and industry, and make use of the Safety Management Information System (SMIS). Incident alerts should be promptly issued after any incident to share learning points and to prevent emergencyreoccurrence.Abusinesscontinuity/planshould be in place to cover degraded situations and emergencies as part of the depot Quality Management System. Emergency services should be consulted when the plan is drafted and this should consider emergency/ degraded situations based on losses of vital infrastructure, such as points failures, derailments, electrical supply, communication links, and felling point issues. Independent audits of depots also provide the opportunity to improve plans and processes. The need for close proximity (or contact) with live 25kV AC and 600/750 V DC electrical supplies should be designed out, or robust mitigation measures should be put in place and subject to regular review. Systems are available which prevent access to live third rails or overhead lines by using guarded access and interlocked gates, which can only be opened with a key that is released from a control panel when the high voltage supplies are isolated. A sequence of unlocking and removing keys ensures access to areas is only permitted when the electrical hazards are safely isolated and earthed.
22 Rail Engineer | Issue 197 | Jul-Aug 2022 ROLLING STOCK & DEPOTS
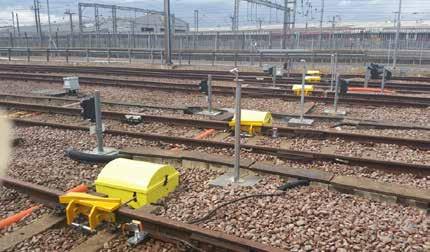
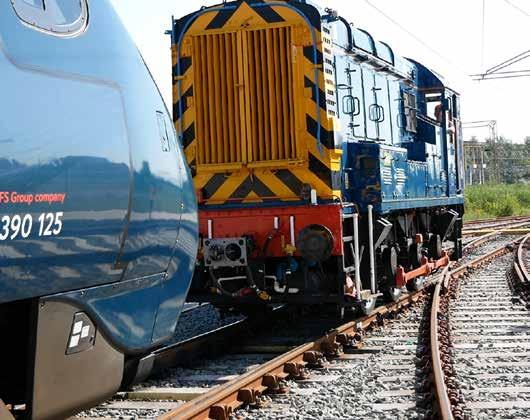
LIFE IS PRICELESS. Renowned as the global market leading depot protection system, the SMART DPPS™ delivers physical protection from vehicle movements to rail depot staff whilst providing visual and audible warnings. The Smart DPPS™: • Protects staff and equipment • Ensures safe and controlled movement of rail vehicles into and out of the depot • Allows train maintenance operations to be conducted without endangering the safety of staff or damaging infrastructure It is: • Fully configurable, flexible and functional • Proven in use and installed globally • Capable of interfacing with third party equipment including signalling systems. • Adaptable to the safe requirements of the depot SMART DEPOT PERSONNEL PROTECTION SYSTEM (DPPS™) www.zonegreen.co.uk Tel: +44 (0)114 230 0822 info@zonegreen.co.uk zonegreen safe working solutions
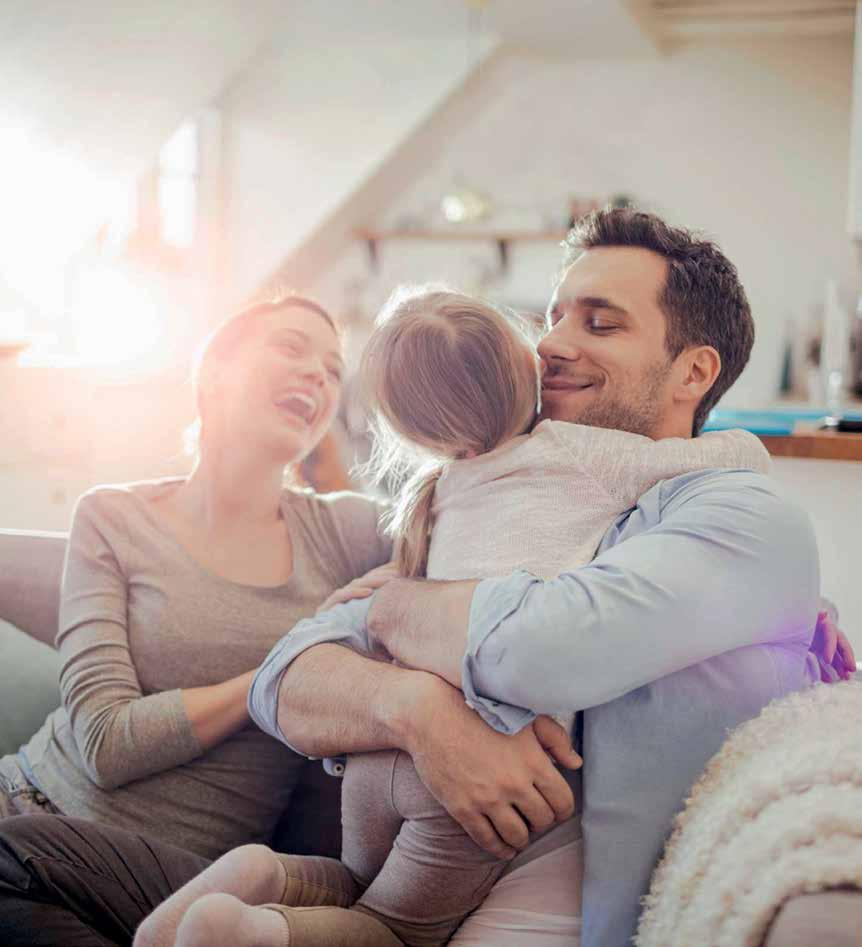
Depot safety arrangements should be set out in guidance that is easily understood and is commensurate with the level of risk. Safety representatives within the depot should be involved in developing safety guidance, risk assessments, briefings, and safety notices. Risk assessments should be carried out to identify hazards and to either prevent or mitigate risk.
Train movements
The type of signalling for the control of train movements internally within a depot, or even if all the available connections need to be signalled to the same standard, may vary and will be dependent on the complexity
Some depots, or the buildings within them, are used to maintain electric locomotives and units despite there being no overhead wires present. The absence of wires is a cost saving to both the installation and maintenance of the site as well as a having a safety benefit. Diesel or battery powered trains are used to move the electric trains. Depot security Depot security should be managed and maintained to lessen the risk of trespass, theft, and assaults on staff, and to mitigate criminal activities. This should involve a risk assessment to understand the strategic importance of the depot and risks such as terrorism, high-risk items that could be subject to criminal activity and stabled trains that could be subject to graffiti or arson if the depot location is overly isolated.
Trains should always be driven from the end that is first going to traverse walking routes. Reversing a train over a walking route should only be done in exceptional circumstances, with the walking route closed for staff use. The coupling of multiple units or coaching stock should, if possible, not have to include crossing a walking route to make the coupling. If a train movement is to cross a walking route, then the driver should sound the horn or use an alternative means of warning staff.Visitors should always be accompanied when at the depot, issued with appropriate personal protective equipment, be given a safety briefing to identify any hazards they may come across, and be made to agree and provide risk control measures. Contractors should be made aware of the boundaries of their work. Depot staff should be made aware of the work being carried out by contractors and briefed on any changes to the depot’s safety arrangements.
24 Rail Engineer | Issue 197 | Jul-Aug 2022 ROLLING STOCK & DEPOTS
Security for depots should be provided in layers of defence including, for example, security fences, CCTV, and alarm systems.Everyone should be encouraged to report instances of trespass and ask for confirmation of identity of anyone not recognised or expected to be at the depot. Tools, equipment, and machinery should always be left securely when not in use.
Wearing uniform, high visibility clothing, and other supplied personal protective equipment, with company identification, makes it easier to recognise authorised staff, but clothing with company identification should also be strictly secured and controlled to prevent misuse.
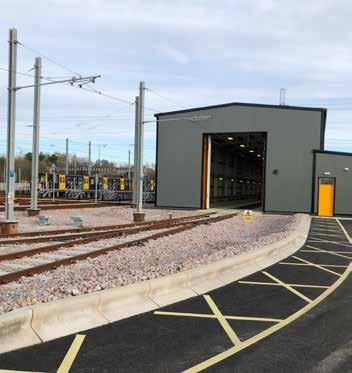
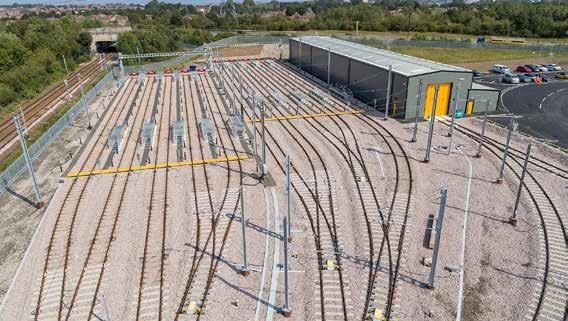
of operation, the volume of train movements in the depot, and system integration with the main railway signalling system.
25 Rail Engineer | Issue 197 | Jul-Aug 2022 ROLLING STOCK & DEPOTS
The systems feature cost effective control technology from other industries, such as intelligent systems with technology such as Radio Frequency Identification (RFID) tags for access control, SCADA operating systems, flexible local control, and de-railers allowing protection to be easily provided when people are working nearby. The systems also provide many other features which are more suited to depots rather than main line signalling.
SIL level 4 driverless Automatic Train Operation (ATO), without any staff on board, is referred to as Unattended Train Operation (UTO). UTO can range from the operation of trains in passenger service with no attendant on board, typically found on metros, or could be used for empty train movements in an automated depot.
Safety Integrity Level Safety Integrity Level (SIL) is an indicator of the relative risk-reduction provided by a safety function in a device. A SIL number between 1 and 4 (1 being the lowest level of safety protection and 4 the highest) is used to describe the degree of safety reliability protection. SIL can be assigned to virtually any function presenting a safety risk. Typical examples of SIL functions for rail are: SIL 1 light metro train speed monitoring and display, SIL 2 depot protection and depot control systems, SIL 4 interlocking of main line points and signals. The requirements for a given SIL are not consistent among all the functional safety standards across different industries, which does cause some confusion. Some asset owners and project managers may be tempted to specify a high SIL simply for availability reasons, and SIL is sometimes mistakenly used to imply that a product has better quality and higher reliability, but this is not always theAncase.item is highly available if it does not fail very often and when it does fail can be quickly returned to service. A system is considered to be safe if it is reliably performing its safety function. However, the system may fail much more frequently in ways that are considered not to be dangerous (fail safe). Therefore, a safety system may be less reliable overall than a non-safety system performing a similar function. Whole life costs will increase to achieve higher SIL levels. This is because designing, testing and maintaining systems to meet high levels of safety integrity is complicated, time-consuming, and expensive. In some cases, it can also lead to lower levels of overall system performance reliability. Specialised SIL systems Main line signalling will typically be designed to the high SIL level 4 but, for depots, such systems may not be able to provide the operational flexibility required for slow speed train movements. So specialised depot SIL level 2 control systems are now available as cost-effective alternatives to expensive, inflexible SIL level 4 control systems. These use clever, inexpensive route indicators, points machines, train detection methods, and SIL level 2 rated PLC hardware/software, to suit depots where safety and flexibility is key for depot train movements.
The method of voice communication between depot and signallers must also be suitable for both safe normal and disrupted operations and ease of dispatch of rolling stock from the depot. Britain’s railways remain the safest in Europe, but with lots of slow-moving trains, high voltage equipment and machinery, maintenance depots are potentially risky locations. Therefore, it is important that every opportunity is taken to provide the right cost-effective technology to keep people safe; and to ensure that trains are safely and efficiently stabled, maintained and upgraded.
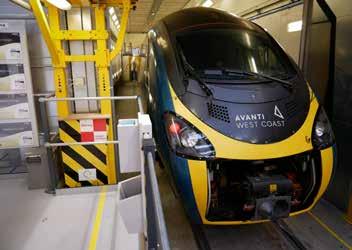
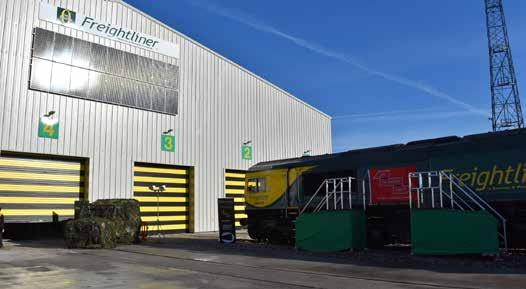
The project approximatelycost£30 million and the footprint of the buildings covers an area of 1,400 m2, with capacity to extend onsite as CAF owns 46,000 m2. By 2020, there were over 200 employees on site and CAF expects that to complete the current order book, up to 300 staff will be necessary. Construction of the factory started in 2017, with production of rolling stock starting in 2018. The site was officially opened by the Prince of Wales in February 2020.
The tour
On arrival at the site, a number of painted car body shells were observed at the west end of the factory awaiting their turn for assembly. The tour commenced in the stores, MADE IN NEWPORT, WALES
26 Rail Engineer | Issue 197 | Jul-Aug 2022 ROLLING STOCK & DEPOTS
Rolling stock:
Painted shell in Zone 1. Zone 2: installation of wiring harnesses. DOBELLMALCOLM
Spanish company Construcciones y Auxiliar de Ferrocarriles (CAF) has opened a factory at the Celtic Business Park in Newport, Wales. Previously, your writer has had the privilege of touring CAF’s facilities in Zaragoza and Besain, and on a recent study tour there was an opportunity to visit the Newport facility.
When CAF was looking for a possible site to assemble trains in the UK, it explored over 100 locations before settling on a part of the former steelworks in Llanwern, South Wales. It is located alongside sidings which follow the main line between Newport and Bristol Parkway, and the site has three main, but integrated buildings: a threeroad assembly plant; a five-road test shed; and a stores building. The east end of the site has a traverser to allow vehicles to be moved from road to road, and a water test facility. The plant will shortly be connected to the siding, but all completed vehicles to date have been delivered by road.
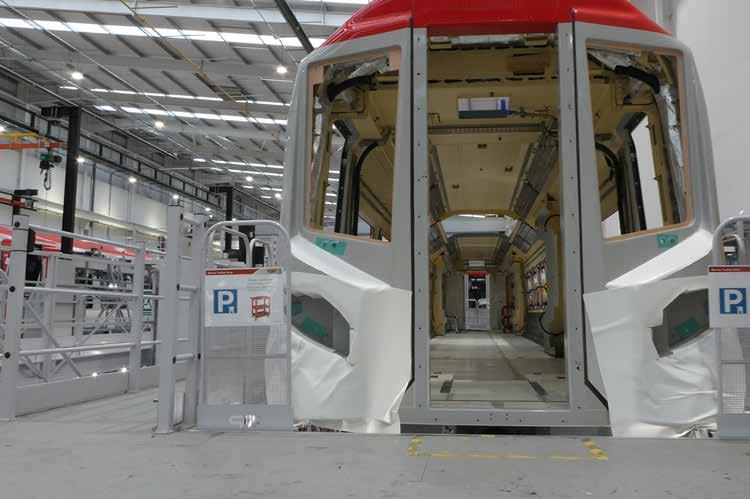
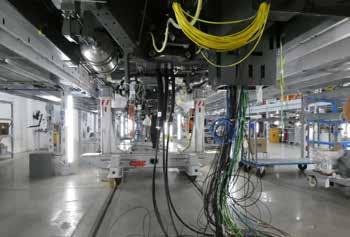
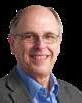


An overriding reaction is that “surely, trains don’t need that many wires?”, but remember that they require electrical sockets to every seat, air conditioning, electrically operated doors, passenger information systems, lighting, seat reservations, WiFi, and many more systems that demand electricity. Trains have moved on from the simple 42way cable down the trains. When the painted shells enter the first of five zones in the workshop, the production team start with marking out for the floor fittings. Here, they use templates reminiscent of a giant plywood jigsaw puzzle, where each piece has cut-outs forming masks for the painted location marks to position the internal floor supports − simple, accurate and reproducible. The supports were fitted next, followed by the carpeted floor. This stage included the start of fitting heat/sound insulation and fitting window frames, the latter involving generous use of Sika adhesive/filler products; cue for much humour about whether manufacturers would cope without Sika products. On the underframe some of the basic mounts for equipment were fitted – many threaded fasteners captive in the C-section solebar tracks.
Zone five was where the interior was completed with the installation of seats and tables, passenger information systems, cab and non-cab end gangways as appropriate, and headlights. Finally, the vehicle was united with its bogies and all connections − electrical, pneumatic, and cardan shaft –were made.
27 Rail Engineer | Issue 197 | Jul-Aug 2022 ROLLING STOCK & DEPOTS
The second zone involved fitting the electrical harnesses, making sure that all the wires were fed though to the correct parts of the vehicle, and installation of equipotential bonding cables (making sure all parts of the vehicle were earthed). Although some connectors were pre-fitted, most were fitted after the looms had been installed on the vehicle. The door mechanisms and doors were fitted at this stage, and carefully aligned so that they opened, closed, and plugged smoothly. The CAF guides reassured the group that, on test, little readjustment is necessary even
Zone three involved fitting the saloon and cab HVAC systems, internal ducting, internal final finishes, and the partition wall between the cab and the saloon. In zone four, the vehicle gained its diesel engine/ gearbox raft whilst, inside, the internal cladding, final surfaces, draft screens, door pillars, and final trims were completed. Windows were also fitted in the driver’s cab. Completion and testing
though significant extra mass is added to the vehicle at later production stages, potentially, altering its shape slightly. Also fitted was the window glass, front end obstacle deflector, autocouplers and toilets. The group was able to examine the underframes at this stage. There was an opportunity to see the installation of the diesel engine heat detection and fire extinguisher system, and the substantial C-section tracks in the aluminium extrusions which are used to support underframe mounted equipment.
Aerial view of CAF Llanwern plant with main production areas labelled.
Sub assembly starts here, and our group saw a pneumatic frame being assembled and the area where the hot water saloon heating modules are assembled and leak tested. Then, up to a mezzanine where the electrical wiring looms were assembled into bundles ready to be fed into the vehicles.
where the sheer range of brought-in items was observed.
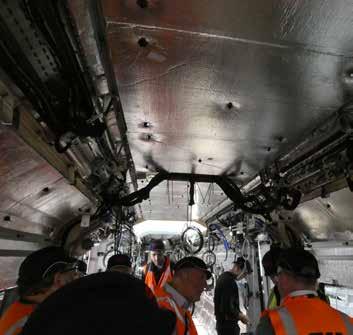

The introduction of class 197 units onto the Cambrian line means that they need to be equipped with ETCS. This ETCS Table 2: Equipment fitted by car type.
28 Rail Engineer | Issue 197 | Jul-Aug 2022 ROLLING STOCK & DEPOTS
Table 1: class 197 composition and car types.
The completed vehicle was towed out of the shed using a small rail-mounted, batterypowered shunting vehicle and onto the traverser where it was moved to the water test building to search for leaks. From there, it was on to one of the test roads. Here, computer aided equipment was used to test the integrity of the wiring looms, including insulation integrity, before coupling into a unit for functional tests to prove all the equipment. The test shop included diesel engine exhaust extraction. After cleaning, the units are uncoupled and prepared for delivery to a site near the customer for dynamic commissioning.
Current production At the time of the visit in early May 2022, production of 180 class 197 diesel multiple unit vehicles for Transport for Wales (TfW) was in full swing. These might possibly be the last diesel-only passenger trains built for UK rail, given the decarbonisation imperative. They are based on the CAF Civity platform which, in DMU form, has also included Northern’s class 195 (149 cars), and West Midland Railways’ class 196 (80 cars). Classes 196 and 197 feature unit end gangways. There will be four configurations of class 197, as shown in Table 1. All cars have a gangway at each end and the gangway at cab ends permits circulation between units when running in multiple. Each car has a 375kW MTU power-pack driving both axles of one bogie. The other bogie is unpowered. Bogies are inside frame type with coil spring primary and air bag secondary suspension, wheel cheek disc brakes, yaw dampers and anti-roll bars. The main equipment on each car is shown in Table 2. Transport for Wales has specified that catering trolley service and a catering area is provided on each DMSL car containing a cold cabinet, a freshwater tank, water heater, dry food store (e.g., crisps and biscuits), and trolley storage.
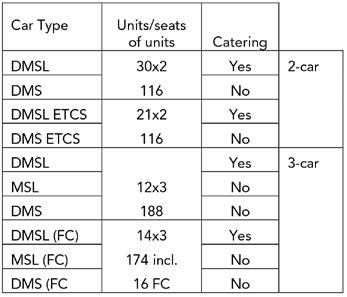
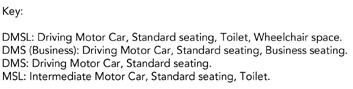

The current crashworthiness standard effectively requires the driver to be further away from the windscreen and the gangway is somewhat longer than the older trains. Both factors result in the driver’s forward view being narrower. This means that trains must stop further away from signals, and in critical locations modifications to the infrastructure might be necessary. For example, at short platforms where the signal is at the platform end, the back of the train might not be completely in the platform requiring ASDO, the platform might need to be lengthened or the signal might have to be moved.
With thanks to the management of CAF Newport for hosting the visit during an organised Institution of Mechanical Engineers’ tour and to CAF’s Graham Taylor for his assistance with this article. Photos courtesy of CAF/ Graham Taylor. Class 197 ETCS block diagram.
Conclusion The class 197 trains made in Wales are a significant part of TfW’s ambitious plan to deliver integrated transport for the country as described elsewhere in this issue. As of early May 2022, 30 units had been completed, with eight units undergoing fault-free running and crew training, and two units having the new yaw damper brackets validated (Issue 195, March/April 2022). Rail Engineer is sure that these trains will be welcomed by customers when they start entering service from Chester, expected in Autumn 2022.
via ethernet: » A European Vital Computer including a Juridical Recording Unit » Human Machine Interface (driver’s touch screen panel including speedometer) » Balise readers » TPWS sub system » Tachometers » Doppler radar speed measurement » GSM-R data radio Unit end gangways
various
TfW is familiar with cab end gangways (class 150, 153, 158), but there are new challenges for the class 197, in common with all other suppliers’ modern unit end gangway designs.
will be the CAF AURIGA on board system compliant with the latest ETCS specification. this to be used, the infrastructure on the Cambrian line needed to be upgraded to baseline 2.3.0d which was commissioned on 15 May 2022 at a cost of £3 million. ETCS to the train is complex and the basic architecture is shown in the adjacent diagram showing the items of equipment required in each cab connected
For
Finally, there are other issues affecting the interface between the class 197 units and the infrastructure caused by the desire for cab end gangways.
Fitting
29 Rail Engineer | Issue 197 | Jul-Aug 2022 ROLLING STOCK & DEPOTS
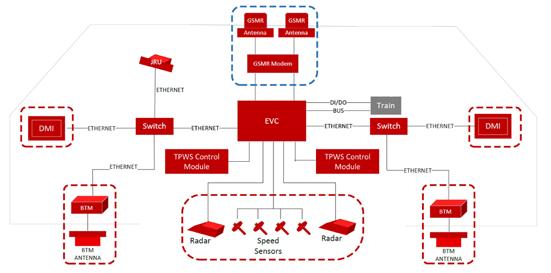
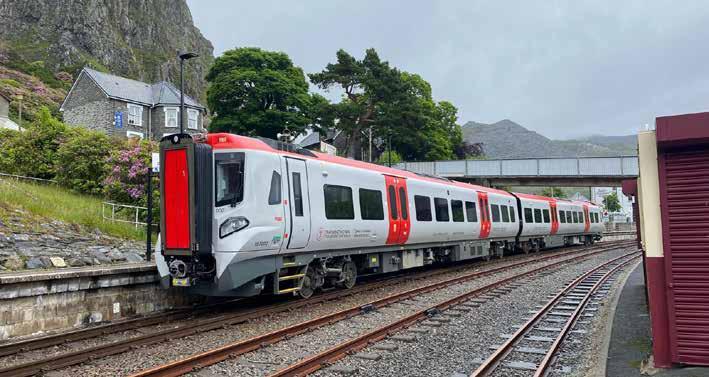
The keynote speaker, Bridget Eickhoff, principal infrastructure engineer at RSSB, has had a long career in vehicle dynamics. She highlighted the challenges still facing wheelsets some 200 years after the principle of coned wheels fixed to an axle was first proposed by George Stephenson. As well as the single point failure risk mentioned above, they operate in an extremely harsh environment (accelerations >80 g are often measured) and they represent a large proportion of fleet maintenance cost. Each area of the industry (tram/light rail, passenger, freight, high speed, etc.) has its own issues and challenges. Finally, as heavy consumable items there is an environmental challenge with the embedded carbon in the steel. Wheelsets support the vehicle mass, steer the vehicle along the track, roll with minimum resistance, transmit all braking and traction forces, and support brake discs and transmission components without wearing out rails unnecessarily. They do all this through a contact patch that is approximately the area of a five pence coin. Bridget said that the contact pressures are extremely high and much higher than any other rolling contact application.
DOBELLMALCOLM W
STOCKROLLING WHEELSETS Rail Engineer | Issue 197 | Jul-Aug 2022 30 ROLLING STOCK & DEPOTS
heelsets come in all types and sizes − large, small, solid; with tyres and without; powered, trailer; inside bearings, outside bearings; and sometimes as individual wheels. Wheels are the heaviest and probably the most expensive consumable parts on trains, and they are safety critical parts; although there are many wheelsets on a train, each is a single point failure risk, and wheels/axles rarely fail safe. Degradation can happen through wear, but serious flat spots or cracks leading to fractures can, and do, lead to derailment.
The railway industry rightly focusses on continuously improving wheelset safety and management. Its work is led by the RSSB sponsored Wheelset Management Group (see panel). For many years the Institution of Mechanical Engineers (IMechE) has held wheelset seminars to share developments and issues. The most recent event was held at the Institution’s Westminster HQ in April 2022. This article reports on a selection of the presentations.
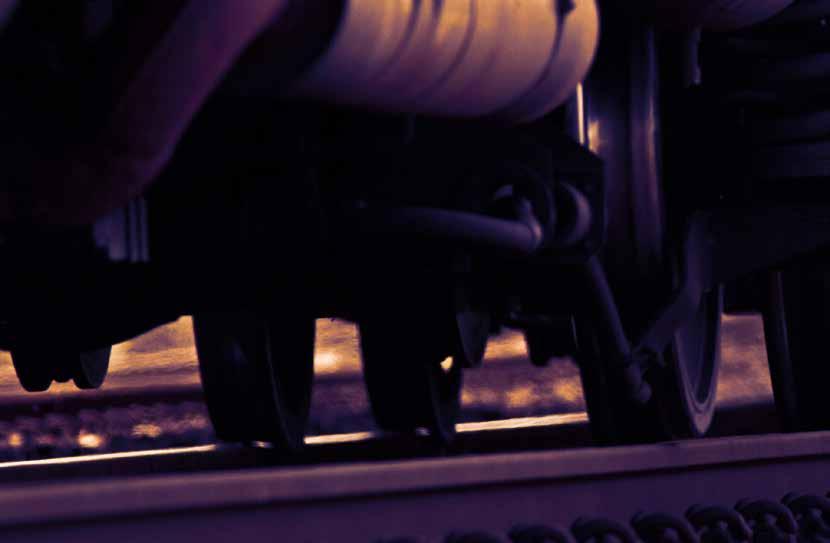
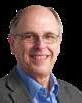

Axle Bearing ParametersWheelset
Wheelset (blue) and other bogie component (turquoise) opportunities.monitoring
Rail Engineer | Issue 197 | Jul-Aug 2022 31ROLLING STOCK & DEPOTS
Remote monitoring Using the principle of what gets measured can be managed, there were two presentations about wheelset measurement. Dr Martin Rosenberger, head of vehicle dynamics, acoustics and analytics at Siemens Mobility, Austria, talked about digitisation in wheelset maintenance. He said that his objective was to move from corrective and preventive maintenance towards condition-based and predictive maintenance operations, with the aim of delivering better availability, reduced life cycle cost, improved safety, longer life span of components, and reduced environmental impact.Wheelset maintenance tasks include inspection, reprofiling, and exchange. The adjacent diagram highlights the wheelset parameters (in turquoise) and other influencing components (in blue). The objective of inspection (data acquisition) is to indicate the health status of the various components, and their remaining useful life both of which are used to plan workshop activity. The digitisation process is aimed at automating all these tasks. Martin highlighted three levels: Acquisition level – including wayside vehicle measurement systems, on board diagnostics and wheel lathe measurements; Execution level including – a computerised maintenance management system and management dashboards; and finally Strategic level - digital twin; and the core element for a digital system, an Internet of Things platform connecting all different levels andWaysidetools. systems can measure most wheelset parameters: profile, diameter, flange height and thickness, back-to-back, and tread defects, including flats, spalling, radial runout. These devices are often located on the entry/exit of depots.
Typical wayside wheelset monitoring system.
WheelBrakeGearMotorBoxDiscsOut-Of-RoundnessWheelProfileParametersWheel RCF Wheel Diameter Wheel Flats
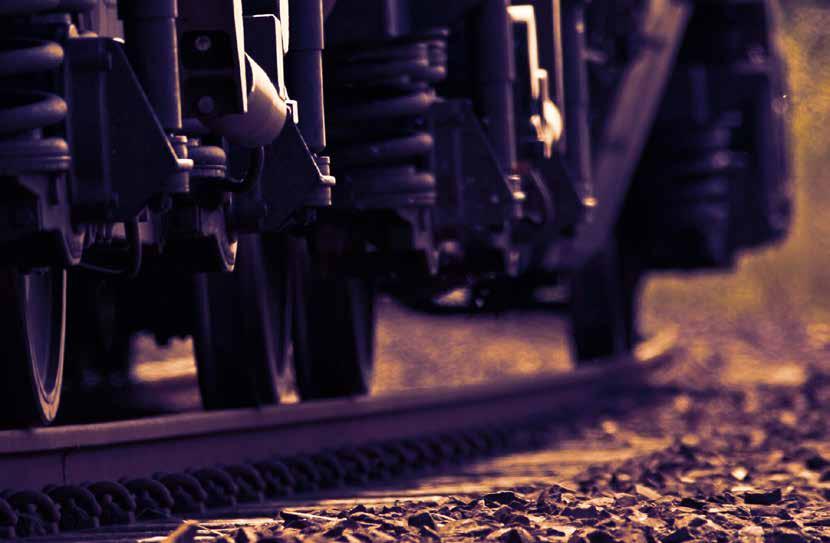
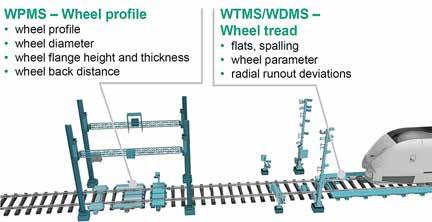
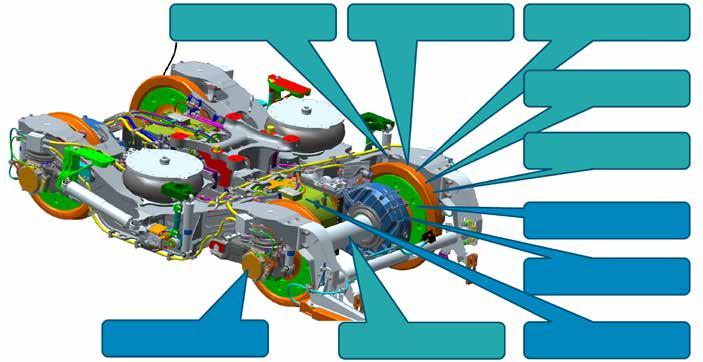

32 Rail Engineer | Issue 197 | Jul-Aug 2022 ROLLING STOCK & DEPOTS
A new decision tool for condition-based maintenance of wheelsets was demonstrated by Steven Cervello, innovation and design manager for Lucchini RS, Italy. Axle non-destructive testing is often mandated at fixed intervals of either time or distance, but the actual loads experienced by wheelsets vary by route. A straight, flat route will tend to have lower loads than routes with significant curves and/ or gradients.
Steven demonstrated that on a mountainous route there were significantly more stress cycles in the medium-high range than for the same train running on a flat coastal route, influencing the optimal inspection interval. He also showed that the information combined with GPS signals allows engineers to identify locations where loads were higher than usual (often associated with switches and crossings) and to monitor them to detect potential track deterioration over time. Once the impact on the axles is understood, engineers are able to identify the appropriate NDT intervals for that fleet, something that can be kept under review as service patterns change over time.
On board systems typically use accelerometers and speed sensors to identify wheel flats, out of roundness, wheel diameter, wheel profile parameters, and axle, gearbox, and motor bearing issues. If these sensors are connected to the train’s computer systems with Wi-Fi/4G communications data and/or alerts may be sent continuously.FortheInternet of Things data platform, Martin stressed the importance of an “open ecosystem” to allow data from a variety of sources and in a variety of formats to be integrated to enable “advanced analytics and decision making”. He said that this information would be input into the maintenance logistics planning and management system with the automatic generation of work orders. Martin also demonstrated sample health status screens from Siemens Railigent® software. His final slide highlighted this system already in use in Siemens depots, for the 115 class 700 Thameslink trains.
Smartset comprises three main components: strain gauges to measure bending and torsion stress in the axle; a telemetry module to send the signals by Wi-Fi to a carbody mounted data unit; and an electro-magnetic inductive power supply to provide energy to the electronics (for freight vehicles with no built in power supply, an axle end generator may be fitted). The data allows engineers to carry out stress frequency analysis.
Wheelset load monitoring
Steven introduced Smartset®, an instrumented wheelset that collects loads which are used to calculate crack propagation rates and hence estimate appropriate NDT intervals.
Steven said that the system should be fitted to both trailer and motor wheelsets. In response to questions, he said that generally only one of each is required to be fitted on a given fleet/route as the objective is to characterise the route, rather than continuously monitor every wheelset.
Sample Siemens Railigent® screen telemetrystrain-instrumentedLucchinicomponenthighlightingcondition.Smartset®wheelsetdetail(right)showinggaugesandWi-Fimodule.
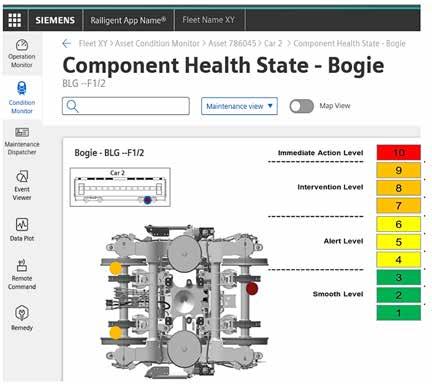
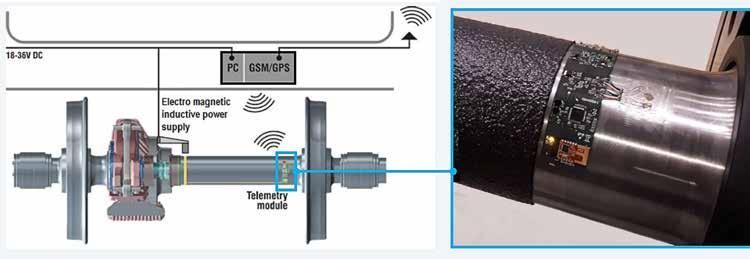
Platform, Depot & Trackside GRP Access Solutions GRP Walkways GRP Hand Railing GRP Catch Pit Covers GRP Embankment Stairs GRP Access Equipment GRP Maintenance Platforms GRP Roof, Track & Cess Walkways GRP Vehicular & Pedestrian Trench Covers GRP Platform Gates, Steps, Ramps & Fencing for the RAIL INDUSTRY Step on Safety www.steponsafety.co.uk01206396446 GRPLOW-MAINTENANCELONG-LASTING,THEALTERNATIVETOSTEEL
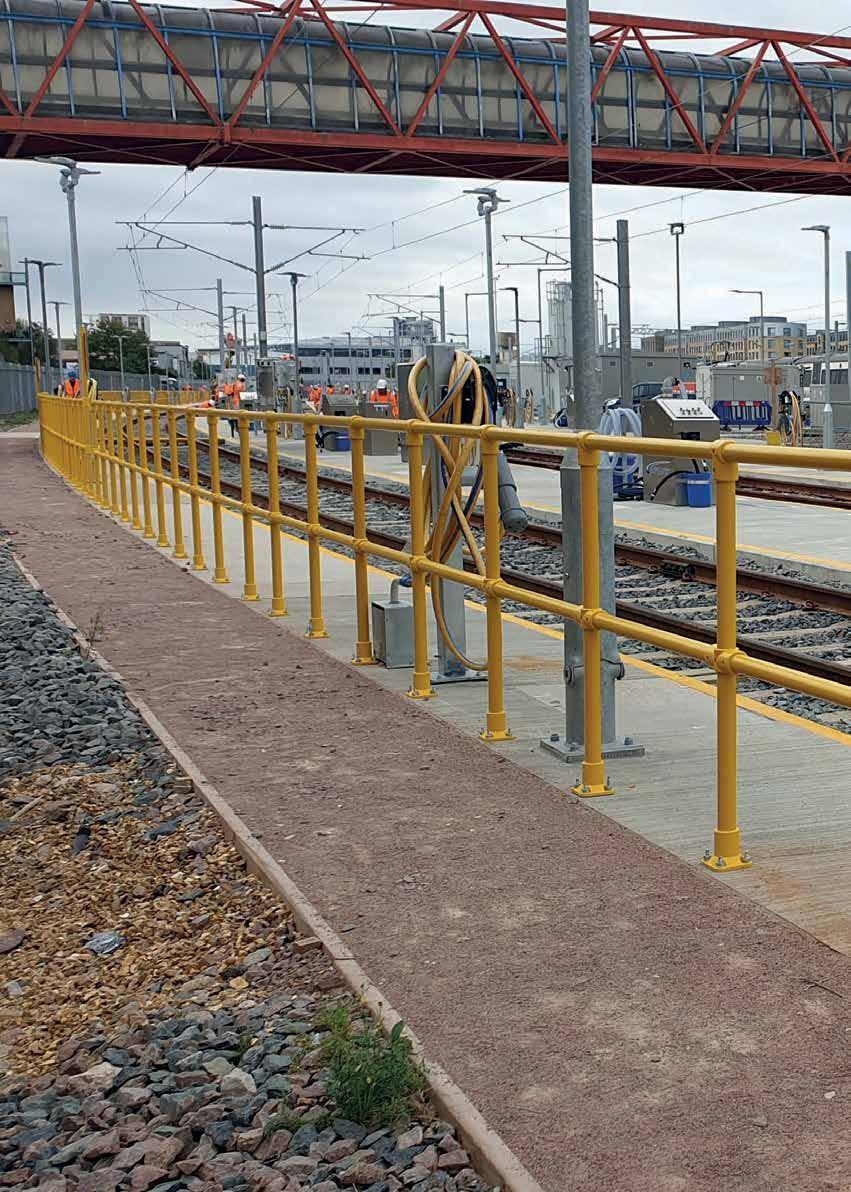

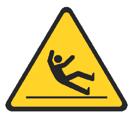
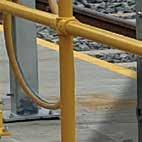

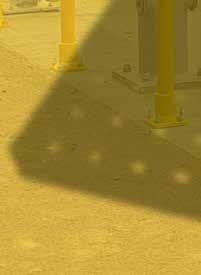

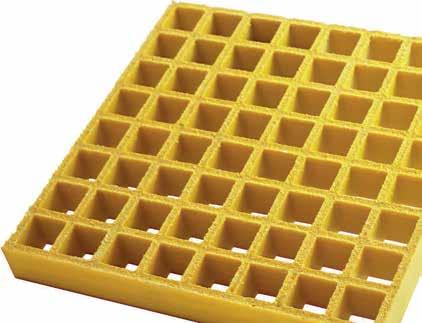

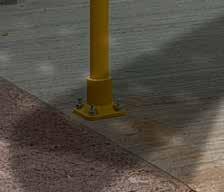

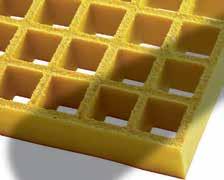


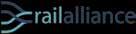
brakes, installed hollow axles, used smaller 720mm diameter wheels, fitted lightweight axial-flux automotive motors on a suspension mount, and added carbon fibre drive shafts and aluminium brackets. The unsprung mass of the freight wheelset (1086kg) was reduced to 967kg in this version, including the gearbox. Overall, the fully motorised bogie still weighs less than the original freight bogie by some 140kg. No brakes? Don’t worry! There are no brakes on the wheelsets, as the RVLR uses its traction motors to brake the vehicle to stationary, and the brake disc adjacent to the motor is a parking (and emergency) brake, spring applied and electrically released. This approach saves considerably on weight and maintenance. Adrian added that magnetic track brakes could be added for routes which operate by line of sight. Adrian addressed the track-wear impact of smaller wheels compared to a class 153 vehicle. This is approximately the same capacity as the RVLR, weighs 55% more, and has 840mm diameter wheels. RVLR has a lower wheel load to diameter ratio and the peak stress on the wheel is some 27% lower than that of the class 153. Adrian said that RVLR has delivered “best in class” low weight, meaning low wheel loads for reduced wear – despite the smaller diameter –and low track cost, ideal for restoration and line reopening.
Liebherr Controlled Active (LiCAS), a smart axle steering solution for existing rail bogies was presented by Rob Wheeler, director sales and customer Service UK & Scandinavia, and Ivo Kovacic, systems engineer for hydraulic applications, both from Liebherr-Transportation Systems. The principle of this system is that diagonally opposite wheel bearings are moved LN25 motor bogie under prototype RVLR vehicle. (Below) Components of the RVLR drive train. Emergency/parkingbrakeactuator noseAluminiummount motor Compositedriveshaft Semi-suspendedgearbox
To use the Wabtec LN25 bogie, TDI needed to make a number of changes which included reducing the wheel size to reduce the height, developing a drive train, and having the masses and fixings approved by Wabtec. Wabtec was also asked to configure the suspension for optimum comfort. To reduce the bogie mass, TDI removed the standard freight
Wheelsets for Very Light Rail (VLR) Adrian Howson, chief technical officer at Transport Design International (TDI), described the Revolution VLR vehicle which was covered in issue 193 (November/December 2021), before focussing on the bogie and wheelset design. The aim of the RVLR design was to be light weight so that the cost of the track and other infrastructure, as well as the propulsion energy, might be reduced. When the prototype vehicle was commissioned, Adrian’s team thought “where can we get two bogies for our prototype?” Having considered bogies from scrap Manchester trams which were “too challenging to clean up and adapt”, TDI’s research identified that freight bogies were often made in small numbers and could be motorised. The DB Axiom (part of Wabtec) LN25 bogie was selected. Adrian said: “In hindsight we chose well for our principal application – a rugged proven bogie, perfect for sub-optimal track on restored lines – and we are now getting enquiries for the powered bogie for many other applications such as electric freight”.
Steering bogies – extending wheel life
(Right) Revolution VLR (Right)Prototype.Modified
permanentWater-cooledmagnet
34 Rail Engineer | Issue 197 | Jul-Aug 2022 ROLLING STOCK & DEPOTS
suspensionSecondary motorCompliantmounting


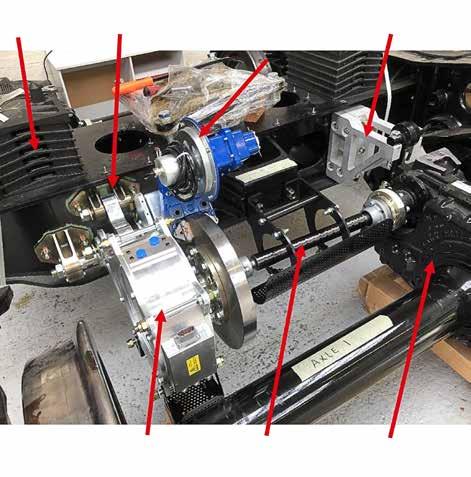
Supporting a sustainable railway is a key priority for Wabtec UK. Through our refurbishment, overhaul, upgrade and maintenance services, we are committed to reuse and recycle as much material as is possible. Sustainable rail is in our DNA REUSED RECYCLED WASTE >18,700TONNES >3,700TONNES TONNES<66 83.2% 16.5% 0.3% Note: Top 14 UK projects by volume in 2020
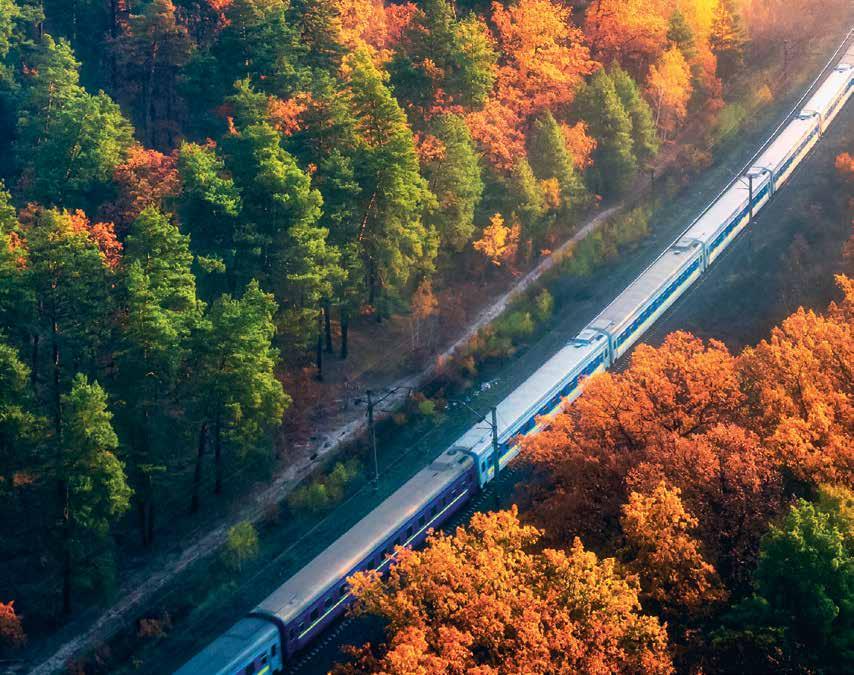
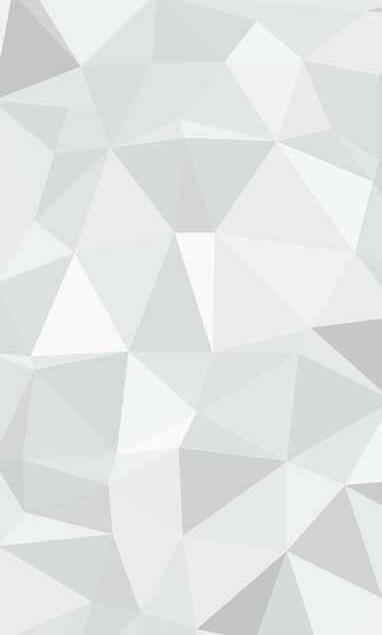
Lucchini are focussing on reducing the energy needed and hence the carbon emissions at every other stage of the production process. Eighty-eight percent of the energy was used in steel making (59%) and machining (29%). Machining is also, of course, powered by electricity with the opportunity to use renewable sources.
Examining axles using ultrasonic non-destructive examination (NDE), looking for defects that could lead to a crack or a fracture, is part of the in-service maintenance regime for most axles in the UK. Given the improvements in the steel making processes, product quality assessment measures, and the use of modern-day robust design philosophies, confirmed indications from these
Axle non-destructive examination
All this is part of Lucchini’s GREEN ID; a methodology to report the greenhouse gas emissions associated with the product’s lifecycle (cradle to grave – or cradle to cradle to emphasis recycling) in accordance with ISO 14067 Carbon footprint of products – Requirements and guidelines for quantification. Lucchini divided the entire process into three main steps: Upstream (raw material, packaging, transport); Core (manufacturing, maintenance, waste, transport to customer); and Downstream (Periodic maintenance, product end of life). Steven added that the customer can receive a kind of identity card, where the total carbon footprint associated to the entire life of the products is expressed in kilograms CO2 eq.
The final big opportunity is in the hands of users. Steven showed a graph showing the average life of a wheel made from Lucchini’s SuperLos steel. This showed an approximately 90 % improvement compared with standard steel, which might roughly halve the number of wheels required during a train’s life.
The actuators were fitted to a BT10 bogie on a withdrawn mk3 carriage and tests were performed on the Weardale Railway in County Durham. Eighty-one test runs with different control settings were carried out including 10 combinations of control settings with five steering factors and five failure modes: passive mode, curve detection, actuator position detection, leakage, and fault control. The failure modes were tested to ensure there was no risk of derailment even with adverse actuator positions. The track included: high track and curvature irregularities, variation of rail head geometry, low adhesion (high humidity, rainfall), and cant excess (low speed).
The final presentation of the day, ‘Towards the Obsolescence of In-Service Ultrasonic Axle Testing’, was given by Roger Deuce, principal specialist & technical manager, wheelsets, at Alstom.
36 Rail Engineer | Issue 197 | Jul-Aug 2022 ROLLING STOCK & DEPOTS
towards or away from the bogie transom under hydraulic power in response to a carbody/bogie rotation sensor. The principal aim was to develop an actuator that could be retrofitted to bogies with radial arm primary suspension in place of the radial arm
The tests were carried out successfully. LiCAS worked as expected. A significant reduction of angle of attack and T-gamma was demonstrated. The tests also validated the simulations and a significant reduction of track access charges was forecast. Finally, the LiCAS system was able to be classified as fail-safe for the BT10 bogie.
Sustainability A new topic at the IMechE Wheelset seminar was a presentation about the sustainability of wheelset manufacture. There is a great deal of embedded carbon in wheelsets and a modern train is likely to use at least four sets of wheels and several brake discs during its life. The presentation ‘Energy Impact of Wheelset Component Manufacture’ had been prepared by Moira Trimarco, CSR Manager, Lucchini RS and was delivered by Steven Cervello. Lucchini is a global company with over 2000 employees, an annual turnover of over €400 million, and nearly 800 clients in 45 countries. Railway production includes circa 250,000 wheels, 40,000 axles, and 12,000 completed wheelsets per annum. Steel is eminently recyclable, but unlike with inkjet printer cartridges, it is impractical to include a pre-paid envelope to return scrap wheels! Although some scrap wheels do get recycled by Lucchini, the overwhelming majority of raw material used is
delivers longitudinal movement of +/-15 mm and lateral movement of +/- 5 mm. The maximum longitudinal force is +/- 45 kN. Simulations have demonstrated improvements in each of the following parameters: angle of attack, T-gamma, track shifting force, rolling resistance, the lateral force of the wheel flange on the rail (Y), and the ratio of this to the vertical wheel load (Q) known as Y/Q. The steering was able to work down to a radius of 200 metres and a 30% to 50% reduction in wheel maintenance cost was forecast.
other scrap steel. Steven emphasised The Lucchini way: Reduce, Re-use, Recycle. Reduce raw material, energy and waste; Re-use scrap and water; and Recycle machining scrap, scrap wheels, and axles.Steel production is energy intensive and Lucchini generates 0.76 tonnes of CO2 eq per tonne of steel produced. That said, this value is much better than is usual in the steel sector (up to 1.9-2.0 tonnes of CO2 eq per tonne of steel). Most importantly, Lucchini invested in electric arc furnaces which already have the potential to use electricity from renewable sources (currently 40%). This has allowed Lucchini to reduce its emissions by over 3,800 tonnes of CO2 eq emissions during the past 2 years.
Thebush.actuator
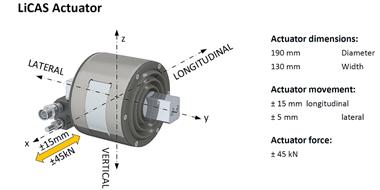

It is more challenging to justify extensions if solid axles are retained, but a similar assessment process can be used. However, there are now modern computer-aided ultrasonic inspection processes available using phased array scanning which can provide new opportunities for solid axles.
Roger described the process by which the technical expert might assess the maintenance regime required, including load/stress levels in the axle, the ability of the inspection method to detect cracks, the allowable size of crack to ensure no failure before the next inspection and the risk of false alarms. Justifying extensions of time are somewhat easier with hollow axles as the entire outer surface can be examined using ultrasonic probes running along the entire inner surface of the axle bore, therefore enabling a higher detection sensitivity due to the reduced scanning distance.
WHEELSET MANAGEMENT GROUP (WMG) Lucchini's Italian factory.
Roger concluded by showing a photograph of a series of axles intended for Alstom FLEXX Eco bogies destined for use under Alstom’s Aventra EMUs by the use of hollow axles and by designing the axle with reduced working stresses Alstom has been successful in achieving a key industry goal of no longer requiring in-service ultrasonic inspection.
37 Rail Engineer | Issue 197 | Jul-Aug 2022 ROLLING STOCK & DEPOTS
in-service axle inspections have become rare. Comments from the floor suggested that the main reason for scrapping axles was actually as a result of defects in wheelsets caused by fitting or removing wheels.
» Axle. » Monobloc wheel. » Wheel centre, tyre, and retaining ring.
WMG is a subgroup to the Vehicle / Track System Interface Committee (V/T SIC). Its purpose is to provide an industry forum for wheelset management issues including safety performance, standards (new, current and legacy for design, manufacture and maintenance etc.), the supply chain, maintenance best practice, and applicable research. The scope includes the following wheelset components:
The current EN15313:2016 and RIS-2766-RST (2017) standards clearly require the definition of an NDE regime (e.g., MPI or ultrasonic inspection). This must include, where appropriate, the required activities at overhaul as well as in-service between two overhauls. As a minimum, the regime must be verified to ensure that, if a defect in the axle is just below the detectable size, then it will not grow to failure before the subsequent inspection.
» Axle bearings. » Brake disc. » Transmission or final drive, including suspension tubes.
Other techniques available include redesigning the axle to reduce working stresses, as well as potential material techniques such as induction hardening, cold rolling, and, as Roger said, “avoiding exotic material grades”.
Roger recollected the origins of many of today’s NDE requirements citing a Railway Inspectorate report into a derailment caused by a broken axle on a 1949 Shenfield Type electric multiple unit on 13 December 1963. The report recommended that “no axle should be tested less frequently than once in every 18 months”. A later accident caused by a broken axle on a freight wagon on 8 March 1996 at Rickerscote recommended, amongst other things: improved axle surface preparation; better protective coatings and coating maintenance; a review of NDE frequencies and methods; consideration of theoretical predictions of crack propagation; consideration of the use of MPI in addition to ultrasonic inspection; and a review of overseas experience with NDE techniques and axle coatings. These two reports, together with the learning from two other significant events in Germany (2002 and 2008) and one in Italy (2009), have significantly influenced many of today’s axle NDE standards.
Once again, this seminar demonstrated that there is a lot of innovation under way to improve safety, and performance whilst reducing cost.
» Axle box / radial arm. Wheelsets for Alstom FLEXX Eco Aventra Bogies.
Thanks to John Reddyhoff, who led the organising committee and to the presenters for their help in preparing this article. All photographs and illustrations courtesy of the presenters/their companies.
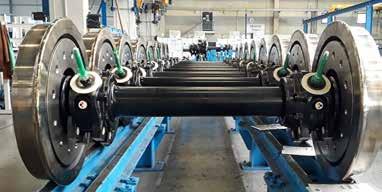
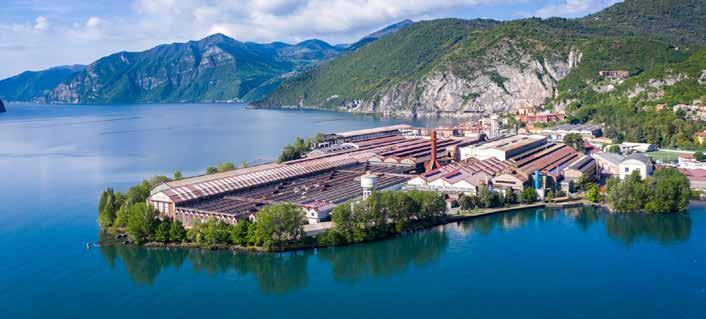
Affordable light rail – part two Coventry VLR vehicle under VLRNIC’s fast VLRcharger.conference.
In our last issue, we described the novel trackform that enables Coventry City Council to install a Very Light Rail (VLR) system at a cost of £10 million per kilometre, around a quarter of the cost of a conventional tram, largely because it can generally be installed without the need to divert utilities. In this issue we consider the lightweight vehicle that makes this low-cost track possible and report on the recent VLR conference held in Dudley, West Midlands. The event was organised by the Black Country Innovative Manufacturing Organisation (BCIMO) and took place adjacent to the VLR National Innovation Centre (VLRNIC). The Black Country was once the centre of the industrial revolution. In 1868, an American visitor described it as “black by day and red by night, it cannot be matched for vast and varied production by any other space of equal radius on the surface of the globe.” However, in recent years the Black Country’s economic growth and wealth has declined. BCIMO was founded in 2020 to reverse this decline. It was set up to oversee the build, launch and operation of the VLRNIC, and to support local businesses to develop new products and services and innovate by, for example, providing 12 hours of free support to help prepare an innovation plan, connect with potential partners, and access funding.RailEngineer visited the VLRNIC when it was under construction as described in issue 191 (Jul-Aug 2021). Funding totalling £32 million has been provided by Midlands Engine, Dudley Metropolitan Borough Council, the European Union’s Regional Development Fund, Black Country and Coventry and Warwickshire Local Enterprise Partnership, and Coventry City Council.
SHIRRESDAVID
Rail Engineer | Issue 197 | Jul-Aug 2022 38 ROLLING STOCK & DEPOTS
The Coventry VLR vehicle
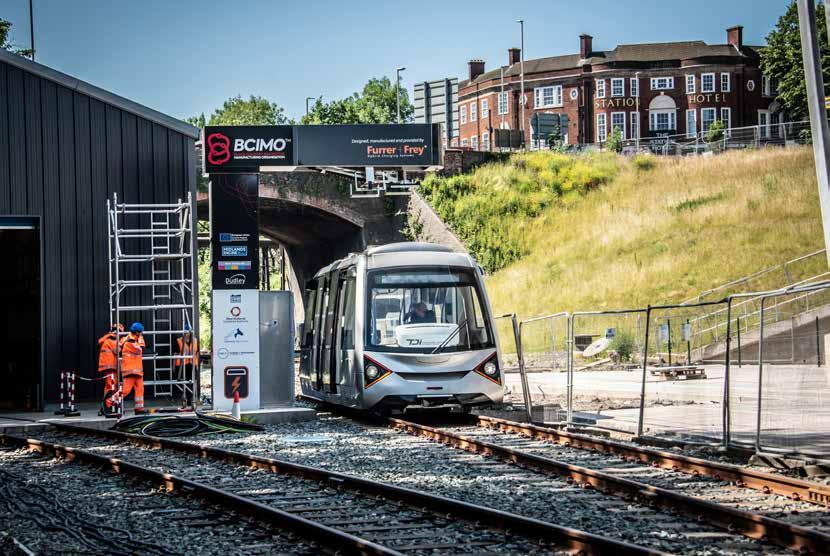
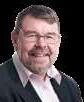

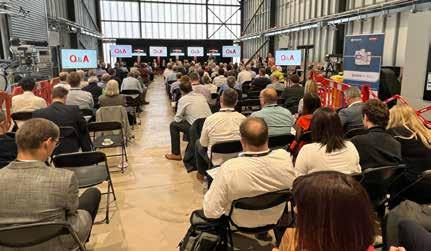
It includes 2km of new ‘100mph’ standard track of which 870 metres is in a tunnel; a 15-metre radius track loop for VLR trials; a 300kW fast charger manufactured by Furrer+Frey; a 60-metre x 20-metre triple-height engineering hall with overhead gantry crane; and research laboratories and conference facilities. It also offers accommodation for SMEs and start-up business.Thecentre is now complete and is being used to evaluate the prototype Coventry VLR vehicle.
VLR national innovation centre.
39 Rail Engineer | Issue 197 | Jul-Aug 2022 ROLLING STOCK & DEPOTS
Why Coventry?
At the conference, Coventry City Council’s director of transportation and highways, Colin Knight, and senior rail programme manager, Nicola Small explained why Coventry was pioneering VLR and how the programme had developed.Colinacknowledged that it was both unusual and challenging for local government to be leading an R&D project such as its VLR system. He advised that when the Council considered how best to connect the city to HS2’s interchange station nine miles away, a bus connection was not felt to be suitable. However, it was doubtful that there was a business case for an expensive tram line and that something more affordable was needed.
Hence in 2016, the Council asked the Coventry-based WMG at the University of Warwick if they could apply their lightweighting technology to create a lightweight tram car and, if so, whether it would be possible to develop a lightweight track that would not require utility diversions. The answer to both these questions was yes. As elsewhere, Coventry faces the challenges of decarbonising transport, improving air quality, and providing connectivity for its expanding developments. With very light rail offering the solution to these issues, and, with lots of great innovators in the West Midlands, this proposal attracted the support of local politicians. Thus, the Coventry VLR project was born. Nicola was asked what advantages Coventry VLR offers over electric buses. She advised that electric buses are very much part of the solution with Coventry set to become the UK’s first all- electric bus city by 2025. Yet the aim is for an integrated transport network of which VLR would provide the backbone. She also advised that the permanency of rail infrastructure attracts more development as it gives developers greater confidence. A rail solution, with only longitudinal movement, is also easier to adapt to autonomous working.
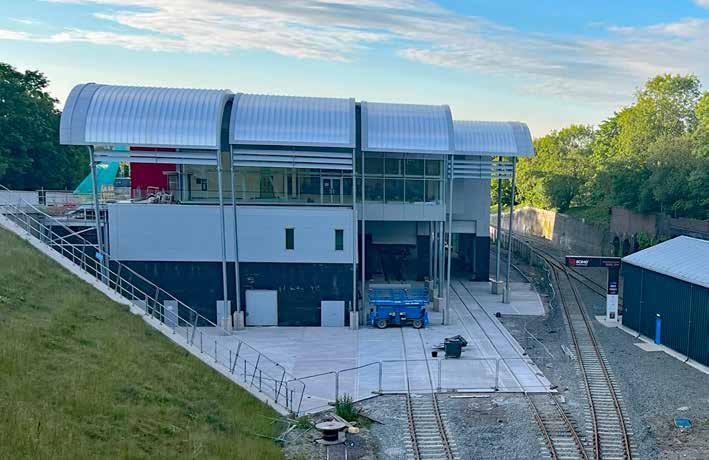
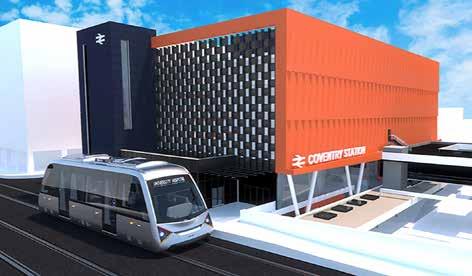
Three types of VLR BCIMO’s Chief Executive, Dr Nick Mallinson, reflected how Britain’s railways went through their biggest period of innovation and growth between the 1840s and 1890s. Yet by the 1960s they had fallen into significant decline due to mass motorisation. In recent years it has been recognised that due to climate change, air quality, and congestion, there needs to be a shift from cars to public transport. The permanency of rail tracks also encourages clustering of housing, businesses, and leisure facilities along urban routes, whilst improved transport links in rural areas help boost productivity and level up disparities. However, such situations do not necessarily generate high passenger numbers so the challenge is for such rail routes to be financially sustainable.
40 Rail Engineer | Issue 197 | Jul-Aug 2022 ROLLING STOCK & DEPOTS
As a result, VLR vehicles weigh no more than a tonne per linear metre. Hence, whilst a heavy rail vehicle typically weighs 44 tonnes and can Coventry’s VLR.
Nick pointed out that recent developments in technology such as lightweighting, batteries, fast charging, 5G, digital manufacturing, and autonomous operation have made a new mode of affordable rail-based transport possible in the form of VLR which “does what it says on the tin.”
She advised that there was a “phenomenal interest” in the project from other local authorities including West Yorkshire Combined Authority, Cambridgeshire and Peterborough Combined Authority, West of England Combined Authority, Oxfordshire, Derby, and Stoke which is progressing an urban Coventry VLR feasibility study. She felt “it was really exciting to work with other Councils on something that is innovative and game changing in the way we encourage people to use public transport.”Colinadvises that the aim is to have a 1.6km demonstration VLR line between the railway and bus stations operational in 2024. Coventry’s eventual VLR network is planned to have four loops, the first is planned to open in 2026/27 to connect Walsgrave Hospital to the city centre.
A developer’s perspective Master developers Urban&Civic buy large areas of land to establish high-quality settlements. They then obtain planning permission, provide the required roads, services, schools and community facilities, and market parcels of land to housebuilders. Its managing director, Robin Butler, provided the VLR conference with an insight into his business and the issues associated with rail connectivity.
The company currently has six large developments. In total these will have 35,500 homes, 53km of roads, 10 million square feet of employment space, 2,000 acres of open space and 19 primary and 5 secondary schools.
Financing such developments is a risky business. They typically require £350 million spent over a 25-year period. This generally includes £85 million on schools, £170 million on roads, utilities, parks etc., and £5 million on bus improvements. Typically, about £50 million is spent in the first seven years before any income is received. Developers have gone bust when this period without income was longer than expected.
None of these developments are rail connected. Robin emphasised that this was not for the want of trying. Indeed, he has 40 years’ experience of trying to provide developments with rail provision with little success and much frustration.Asanexample, a station on the East Coast Main Line for the Alconbury Weald development is in Cambridgeshire County Council’s long term transport strategy and had planning permission following initial discussions in 2009. However, railway enhancements to make this viable were cancelled by the Department for Transport (DfT) inRobin2017.advised that developers much prefer developments with rail connections as they make houses sell better. Over the past five years, house prices within 2km of a railway station in Southeast England have typically grown between 40% and 50%, compared with an average 20% increase in the region. There is also less financial risk from rail-connected developments which are less likely to have an extended period without income. Robin was also convinced that house building would be massively accelerated if government accelerated railHedelivery.advised that his company’s developments are all bus connected for which the required facilities are less than 2% of the total development’s cost. As developers would gladly pay more for affordable rail provision, he considered that there is a strong financial case for VLR in new developments.
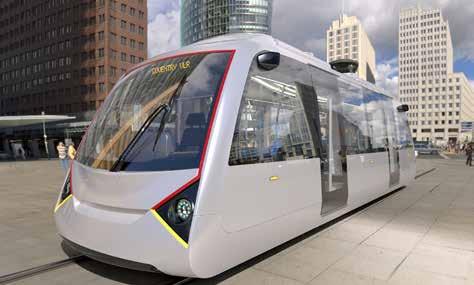
carry 100 passengers, a similarly loaded 11-tonne Coventry VLR vehicle carries 50 passengers. This lower weight reduces infrastructure costs which is a key area for driving down railway costs.
3. Autonomous personal rapid transit (PRT) pods offering last-mile on-demand nonstop travel on a segregated track such as those operating from Heathrow’s terminal 5.
2. Large towns and small cities, such as Coventry, for which there is no business case for a conventional tram system.
41 Rail Engineer | Issue 197 | Jul-Aug 2022 ROLLING STOCK & DEPOTS
There are three potential opportunities for VLR
VLR’s evolution Martin Pemberton founded Transport Design International (TDI) in 1987 to support international rail projects. He explained to the conference how the VLR vehicle concept had evolved. This started in 1995 when Brighton Council engaged TDI to consider how the Volk’s electric railway could be linked to the town centre. This led to the realisation that there was a massive gap in the market between conventional light rail systems and buses. Hence, Martin felt that a lighter vehicle was required, guided either by rails or electronically for rubber tyred vehicles.
To demonstrate this concept, TDI produced a
factoryworkersspeedpassengerincludingdiesel18-metre-longpassengerconsultancyberesultedkm/hr.anduptheinitsstationstriallocationswascarrytyred1.75-metre-wideprototyperubber-minitramwhichcould30passengers.Thisdemonstratedatvariousincludingasix-weekbetweenBradford’stwoin2005.In2008,TDIdesignedandbuiltfirsttrainfora30-inchrailwayOmanthattakesvisitorstoAlHootacave.Thisscaledthestructureoftheminitramhadamaximumspeedof16ItwasTDI’sfirstVLRtrain.AnenquiryfromTurkeyin2012inwhatTDIbelievetothefirsttimeaUKdesignhasproducedatrain.Thiswasanstandardgaugehybridvehiclewhich,standees,carried120andhadamaximumof65km/hr.ItferriedfromKonyacitytoaonabranchlineseven
miles away. Using the experience of the Al Hoota train, this vehicle was designed, built, and brought into service within 18 months. It was built by specialist vehicle manufacturers Severn Lamb and tested at Long Marston. This Konya vehicle was the forerunner of the Revolution VLR vehicle. In 2016, it won TDI and Severn Lamb the 2016 Global Light Rail Award for ‘Outstanding Engineering Achievement’ as it is 40% lighter and 50% cheaper than a comparable conventional vehicle. This accolade was helpful in persuading RSSB and others that TDI should be awarded £3 million funding in 2016 to lead the development of RVLR for rural rail services. Key to the further evolution of VLR is autonomy. Martin advised that TDI gained experience of this when, in 2015, they became a delivery partner for the familysized Vectus vehicles being Revolution VLR. Award winning Konya lightweight train.
1.operation:Revolution VLR (RVLR) has been developed to reduce the cost of re-opening closed lines or take advantage of little used freight lines as reported in issue 193 (NovDec 2021).


» Transcal for metal fabrication works, seating, and interior fittings.
» AP Racing, manufacturers of clutch and braking systems
» Cable manufacturer Phoenix Dynamics » Quantum seating » Venture Engineering
(Above) Coventry
» Datum composite products
side (Inset)view.Coventry VLR cross section. 42 Rail Engineer | Issue 197 | Jul-Aug 2022 ROLLING STOCK & DEPOTS
produced for Korean SkyCube PRT project and for which TDI developed special miniature bogies to drive the vehicles around sharp curves. The lightweight carbon fibre Vectus vehicles operated on interconnecting guideways to short headways of as little as two seconds. They take passengers directly to their destinations without stopping at intermediate stations and are controlled to Safety Integrity Level 3 by purpose built electronic control units. The 5km SkyCube network opened in 2014 and has 40 vehicles which gives it a capacity of 1,300 passengers an hour. It is currently the world’s largest PRT system.Martin advised that TDI was glad to receive enquiries from WMG and Coventry about adapting RVLR for use in the city. However, he felt that the Vectus PRT vehicle provided a better platform for urban use, especially as its small bogie could be developed to go round 15-metre radius curves without wheel squeal. However, the Vectus vehicle is powered by third rail, so it needed to be adapted to accommodate the lithium titanate battery used on the RVLR vehicle. Hence, the Coventry VLR is a hybrid of Revolution and Vectus technology.Following these discussions, in June 2018 WMG awarded TDI the contract to design and build Coventry’s VLR vehicle. Local manufacturing centres Having designed the Coventry VLR vehicle, and with the benefit of its previous experience in light weighting, in Autumn 2020 TDI started phase one of its build to assemble the VLR outer body panels. For this initial build phase, the Coventry-based NP Aerospace, which normally specialises in building military vehicles, was appointed as assembly contractor under TDI’s management.Phasetwoof the build was carried out at TDI’s facility in the Long Marston Rail Innovation Centre. This started in March 2021 and took 10 months. It involved completion of the mechanical elements, installation of electrical and electronic systems, and software integration.Aftercompletion of the build, TDI undertook four months of mechanical, electrical, electronic, and systems testing at Long Marston. In May 2022, the vehicle was moved to the VLRNIC for further site tests prior to being handed over to Coventry City Council this summer.Thesuppliers involved included: » Tikab & Arogus which supplied the bogies
» Echandia, who generally supply batteries for marine Afterapplicationstrialling the Local Manufacturing Centre (LMC) concept for the initial build phase of the CVLR programme in Coventry, TDI’s intent is that future VLR vehicles will be built in a similar way at local pop-up facilities. Its aim is that 70% of suppliers will be sourced within 50km of the LMC, helping to upskill the local workforce and promoting economic sustainability in the region. In this way, manufacturing VLR vehicles will support local businesses close to their point of use. VLR
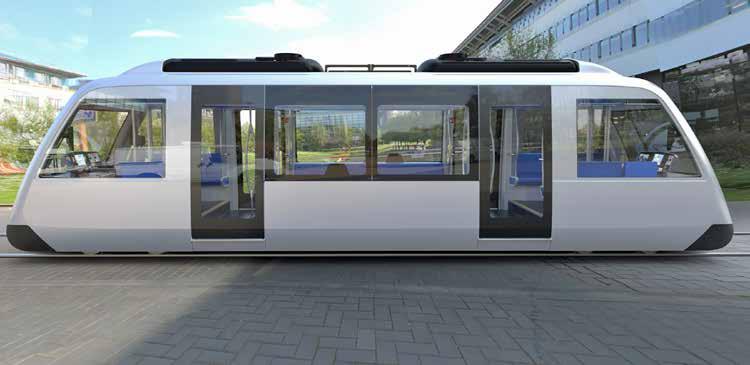

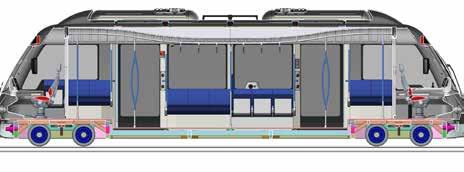
Driverless vehicles also offer a greater load factor by enabling a more cost-effective deployment of additional vehicles at peak times. With advances in autonomous systems, the idea of a remote operator controlling multiple vehicles and intervening when alerted to problem situations seems feasible. No doubt the VLRNIC will be actively involved in the development of this concept.
A tonne per metre Unladen, Coventry’s 11-metre VLR vehicle weighs 11,000 kilogrammes and so meets the aspiration of a lightweight vehicle weighing a tonne per metre. The vehicle is 3.17 metres high, 2.65 metres wide and can carry 70 passengers with 20 seated. When fully loaded its weight is 16 tonnes, resulting in a maximum four-tonne axle weight.Theprototype vehicle has a maximum speed of 70 km/h and can tackle a 5% gradient. All axles are driven and it can run on 15-metre radius curves. It has a 750V 54kWh Lithium Titanate battery which has a particularly safe battery chemistry and is packaged underfloor with the control electronics. Its range between charges is of the order of 20km, though this varies considerably according to temperature, load, and other factors. The battery can be charged overnight from a 20kW supply and, during the day, receive 3.5-minute rapid charges from a 200kW supply, as well as being charged from the regenerative braking. It is made from steel, aluminium, and composites, with a carbon/polyethylene bumper and carbon/Kevlar cab ends. The exterior bodywork is lightweight carbon composite panels. Poly-carbonate windows meet the requirements of the post-Croydon accident recommendations and are 44% lighter than glass. Its design allows for future autonomous driving.Witha typical four-minute headway between vehicles carrying 50 passengers, the Coventry VLR system has a capacity of 750 people per hour. It should, however, be noted that, although VLR is a much more affordable system, it offers less capacity that a conventional tram. Edinburgh trams, for example, carry 250 people and have a capacity of 2,142 people per hour at seven-minute headways.
Coventry’s VLR changes this dynamic as it offers an affordable solution that gives towns and small cities the chance to benefit from urban light rail. It could also result in a new industry with significant export prospects. With such huge opportunities Rail Engineer looks forward to reporting further VLR developments.
The interest generated by this new system was evident by the large number present at the VLR conference, where many saw VLR as an affordable way of attracting people from their cars onto public transport. But if there is to be serious investment in VLR, it needs to be clear beyond doubt that VLR offers an affordable workable solution. In this respect, Dudley’s VLRNIC has an important role in helping demonstrate both the viability of the VLR vehicle and its trackform, and that it can be provided at the anticipated cost. If VLR is to significantly increase the number of UK light rail systems, its capital and operating costs must be low enough to give it a strong business case. However, with a driver needed for each 60-person vehicle, compared with one for each 250-person conventional tram, autonomous operation is likely to be required if VLR systems are to become widely affordable.
43 Rail Engineer | Issue 197 | Jul-Aug 2022 ROLLING STOCK & DEPOTS
Coventry VLR exploded view.
This method of production can also be relatively easily scaled up should there be a large take-up of VLR systems after the first scheme in Coventry. This would suit regional requirements in the UK and can be used for the international market too.
After Manchester reintroduced its trams in 1992, six other large conurbations followed suit. As a result, UK light rail now carries 300 million passenger journeys per year with proven economic benefits. Yet those outside large cities are denied these benefits as, for them, conventional light rail is simply unaffordable.
Looking to the future Heavy rail has taken many decades to evolve into an efficient transport system. In contrast, the whole system approach used to transportationproducedandVLRthedevelopCoventryvehicletrackhasanewsystem in less than 10 years.
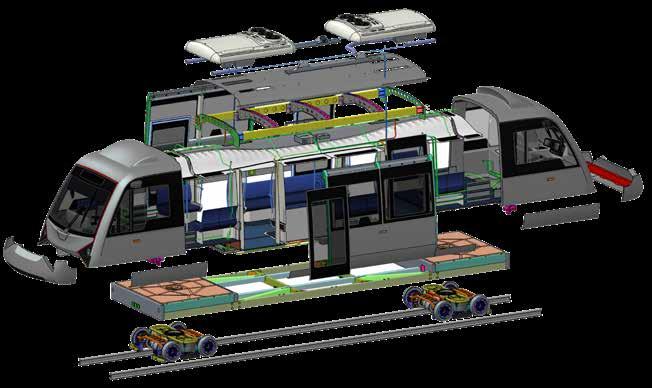
The Stapleford Miniature Railway is a private 10 ¼ inch gauge (1/5th scale) railway, owned by the family of the 4th Lord Gretton, and operated for charitable purposes by the Friends of Stapleford Miniature Railway (FSMR). The Railway Challenge has exclusive use of the site where many of the contestants camp for the duration of the competition. The last team to arrive was the team from Poland who had suffered a puncture during transit through the Netherlands which resulted in a hospital visit for one of their number. That didn’t dim their enthusiasm, however.
All photographs courtesy of the IMechE, and the IMechE volunteers.
Between 24 and 26 June, seven teams of apprentices, undergraduates, and graduates gathered at the Stapleford Miniature Railway just outside Melton Mowbray for the 10th on-site Railway Challenge, sponsored by the Institution of Mechanical Engineers (IMechE) Railway Division. The event started in 2012, but was held online in 2020, due to the coronavirus pandemic.
The competitors are required to build a locomotive to haul two of FSMR’s carriages (circa 1.2 tonnes) around the approximately two-mile circuit while undertaking a number of challenges. They also have paper-based and presentation challenges to complete. All the challenges relate to real life situations that contestants might encounter if working on a full-scale locomotive and, while the nature of the challenges has changed little over the years, teams still find them rather tricky.
Since 2012, the locomotive designs have changed. In the first competition, all bar one of the teams developed locomotives powered by petrol generators while the University of Birmingham developed a hydrogen fuel cell locomotive. In 2022 only one entry was powered by a petrol engine − the rest were powered by a variety of types of battery. In a previous competition, the team from Aachen in Germany also offered a hydrogen locomotive (pictured below), although this demonstrated that hydrogen powered locomotives depend on the whole hydrogen supply chain; transporting the locomotive from Germany was straightforward, transporting hydrogen was not!
DOBELLMALCOLM RailwayCHALLENGE Another year, another 44 Rail Engineer | Issue 197 | Jul-Aug 2022 ROLLING STOCK & DEPOTS
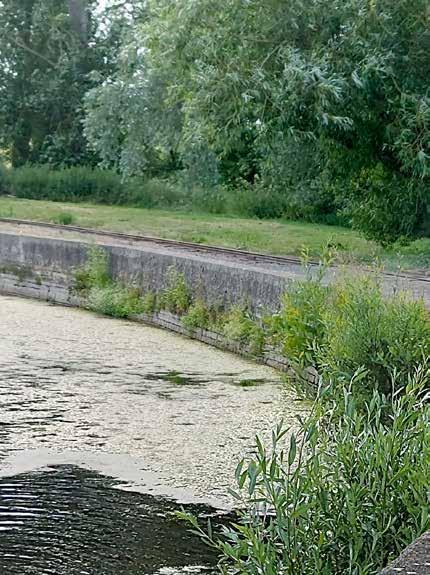
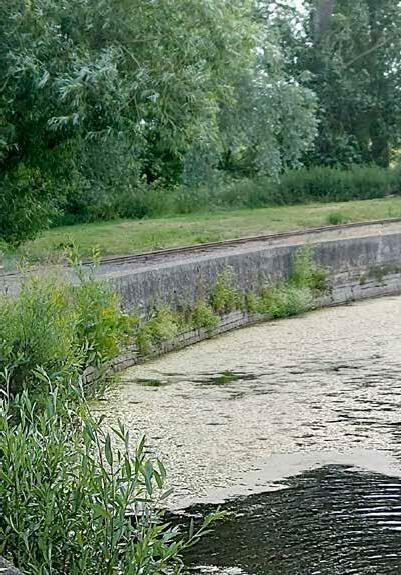
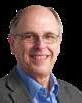

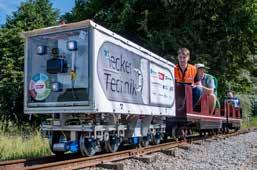
A team effort The competition depends on the cooperation of three groups. First, the FSMR team led by Richard Colby, are in charge of all activity on the site they manage, and akin to the main line safety regime, they are the duty holder. Second, the excellent team of Lucy Killington, Natalie Bradshaw, and Kirsty Joyce from the IMechE staff, who organised the facilities and equipment needed. Third and finally, the IMechE volunteers, including eight past Railway Division Chairs, and who were split into three groups − operational interface with the railway led by RSSB’s Bridget Eickhoff, scrutineering that the teams’ locomotives are safe to run led by TfL’s Tim Poole, and the judges that assess the performance of the locomotives
in the various challenges led by Transport Scotland’s Bill Reeve. Many of the judges, your writer included, are not getting any younger, so it was great this year to welcome two new trainee judges − Trans Pennine Express’s Alice Callaghan (a former competitor) and Scotrail’s Blair Hutchinson. Safety is, of course a key requirement, starting with delivery. Each team is required
45 Rail Engineer | Issue 197 | Jul-Aug 2022 ROLLING STOCK & DEPOTS
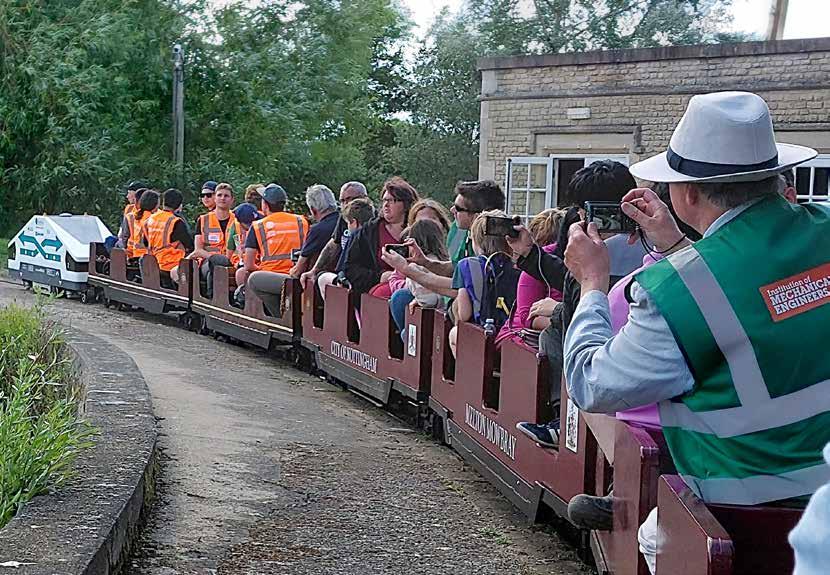
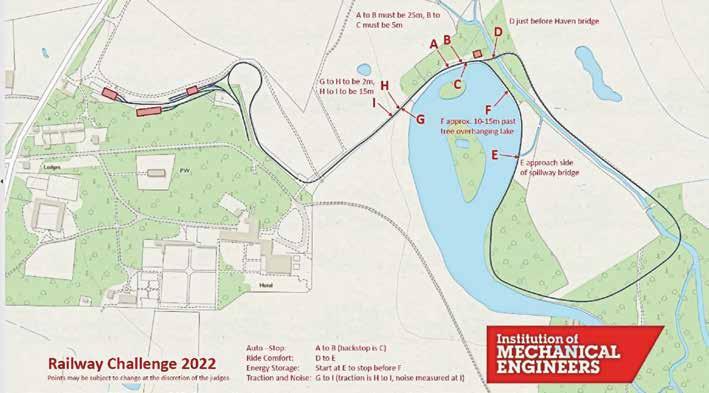
46
to provide a loading/unloading plan/risk assessment with unloading observed by an IMechE engineer. These locomotives weigh between 0.5 to 1 tonne and one would not want one to land on someone’s foot. Sometimes a little (or a lot) of reassembly is required. Unloading happens on the Thursday, unless delayed by punctures!Alltheteams are required to demonstrate, in a video, their commissioning and reliability proving runs prior to arrival at Stapleford. This year only three teams – Aachen, TfL, and Sheffield submitted videos. It is no accident that two of these three teams gained the maximum reliability score during the competition as they had already proven their reliability. Unfortunately, Sheffield’s innovative two module locomotive was subject to modification after its reliability runs which led to some electrical damage − another issue that full size rail vehicle engineers face. Sadly, this issue affected the teams progress throughout the weekend.Network Rail and Alstom’s locomotives looked more or less complete quite early on, but both Huddersfield and Poznan had some considerable reconstruction to do. Close inspection Friday’s first task is scrutineering. Tim Poole and his colleagues assess that the asbuilt design complies with the requirements. Is it in gauge? Will the locomotive stop on demand? If the emergency brake is tripped, what happens when it releases − does the service brake remain applied? Is the horn loud enough? Are there clear instructions for the driver? They also keep a handy watering can to check watertightness.Thisisthefirst time that volunteers and judges see the various ideas the teams have incorporated. Your writer is deputy head judge and judges the design competition where the locomotive design is explained, but even with this prior knowledge it is still exciting. For your writer, the quality of Poznan’s welded bogie frames, the cleverness of Aachen’s steering bogies, and TfL’s innovative approach to delivering a graduated electrically released spring brake system were particularly noteworthy. In a later tour with Bill Reeve, we were particularly impressed by the Alstom team’s pull-out battery trays made of composite material. This contributed to their success in the refuelling challenge. After static scrutineering, each team’s locomotive is coupled to two FSMR wagons and the train, under the control of an FSMR guard, sets off to run round the line for dynamic scrutineering which includes a brake test. Many of the locomotives use chains to drive the wheelsets and this is usually where chain alignment or tension problems are experienced.
Engineer | Issue 197 | Jul-Aug 2022 ROLLING STOCK & DEPOTS
Technical University of Poznan, Poland (Poznan). Network Rail and Colas (Network Rail). Rail
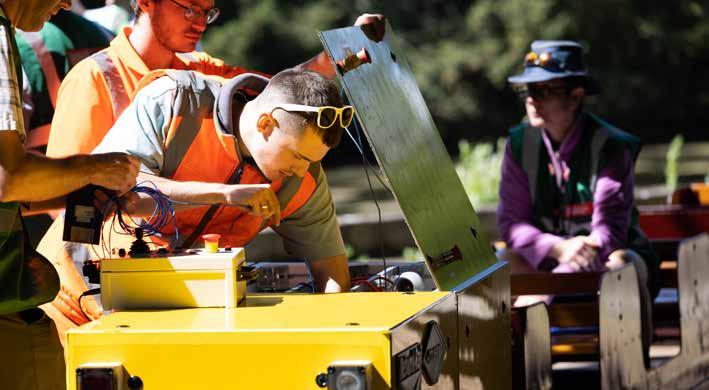
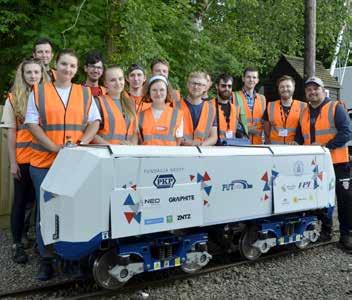
The challenge begins Once a locomotive has passed scrutineering, teams are given time slots to go out and practice the various challenges. Even if they have tested them on another 10 ¼ inch line, the particular, characteristics at Stapleford might alter calibration. For example, the auto-stop challenge might have been tested on straight flat track, but at Stapleford it is on a slight down gradient on a slight right hand curve.
The Aachen team, who used GPS for position sensing carried out their calibration run and achieved a creditable result of 1.2 metres short of the stop point. However, after calibration, their competition result at 1.7 metres short was, sadly, worse. This is another area where engineers working on full size ATO railways take many attempts to achieve reliable accurate stops.BySaturday, Alstom were still struggling as their locomotive’s motors seemed to be fighting each other. They eventually realised that sending speed signals to the motors was leading to instability. Sending torque commands would have been better but would not have been an easy fix so they resolved the issue by running with fewer motors connected.
The maintainability challenge starts on Friday afternoon and involves safely removing and refitting a wheelset in the shortest time. TfL, the winning team, managed to lift the locomotive, disconnect the wheelset, roll it clear, and reassemble in just under four minutes. All seven teams managed to complete this challenge, but the team that struggled most took nearly 30 minutes.
Changing batteries is therefore accepted as a refuelling method and the winner, Alstom/ University of Derby, managed to change their four lead acid batteries in just under one minute − less than half the time it took Huddersfield to refill their petrol tank from a jerry can.
Alstom(TfL). and University of Derby (Alstom).
While all this is going on, Poznan were still building and Sheffield were hopeful. But the Huddersfield team discovered a serious fault with their petrol generator and despite a visit to the University for spares, they were unable to rectify the situation.
On Sunday morning, only the Aachen, TfL, Network Rail, and Alstom teams were ready to run, but it was hoped that Poznan and Sheffield might be able to demonstrate their locomotives after the competition was concluded. The FSMR team run passenger trains between the Transport for London
47 Rail Engineer | Issue 197 | Jul-Aug 2022 ROLLING STOCK & DEPOTS
Next was the refuelling challenge in which teams had to refuel safely in the shortest time. The specification had always set a maximum refuelling time of two minutes. The organisers had thought this would be ample time for refilling a petrol tank from a jerry can (cold engine, electrics off), but recognised that recharging batteries would take much longer than two minutes even if FSMR had somehow acquired a bank of Tesla super chargers.
The final day
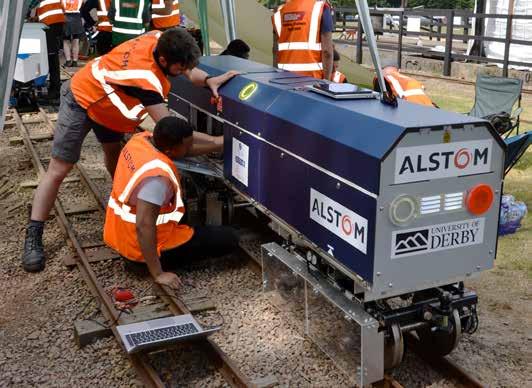
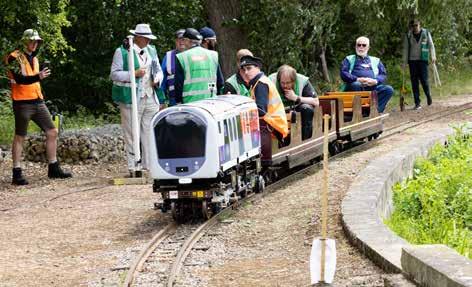
Prizes awarded That concluded the track challenges. These results are made known to the visitors and teams, but not the scores nor the results of the paper/presentation challenges. This means that after judges’ deliberations to make sure that any rule infringements are properly dealt with, the prize-giving ceremony is a genuine surprise to everyone except the judges. Many of the early awards (design, business case, innovation) went to TfL, but the overall winner was the team from Aachen with a score of 1660 points, 211 points clear of runner up TfL, with Alstom/University of Derby in a very close run third place. Prizes were awarded by representatives of the event’s sponsors: Network Rail, Young Rail Professionals, RSSB, and Angel Trains. The design challenge was presented by James Rollin and Lucy Marsh who also sponsor the event in memory of their University of Sheffield (Sheffield).
48 Rail Engineer | Issue 197 | Jul-Aug 2022 ROLLING STOCK & DEPOTS
competition entries, this year hauled by an Atlantic (4-4-0) steam locomotive named John H Gretton. This is followed by a competition entry (competitor’s loco and two wagons) and a petrol-powered locomotive in the pattern of a BR Warship class, known as “the diesel”. Aachen were first to carry out their tests. Their ride quality, based on EN 12299:2009 ‘Railway applications – Ride comfort for passengers –Measurement and evaluation’ (section 6.7.2 – Mean Comfort Standard Method), was a winning 3.18, and distance travelled using only the energy recovered during a service brake stop from 15 km/h was a record breaking 116 metres. The traction challenge involved timing the locomotive between two points 15 metres apart on the 1 in 80 up gradient, delivering a joint winning time of 5.94 seconds and the noise level at the end of the traction test was 91.9 dB (corrected speed). The other teams delivered the following results:Alstom delivered a winning auto stop result of 0.16 metres short of the stop mark, a ride quality of 8.08, a traction challenge time of 7.73 seconds and noise level of 92.5 dB. They were unable to collect any energy for the energy recovery challenge.
University of (Huddersfield).Huddersfield
Network Rail’s auto-stop system was not working and, sadly, the locomotive unexpectedly came to the end of its battery range during the ride challenge and had to be assisted back to the station by the diesel.
TfL’s auto stop sensor failed to trigger the control system, despite it working on test, and although they travelled some distance on the energy recovery challenge, they were unable to demonstrate that they had only used the energy recovered in a single brake application leading to no result being recorded, although a feature of the scoring system is that one third of the points are awarded for genuinely attempting a challenge. They delivered a ride quality of 3.32, just behind Aachen, traction time equal to Aachen’s result, and noise level slightly better at 89.5dB.
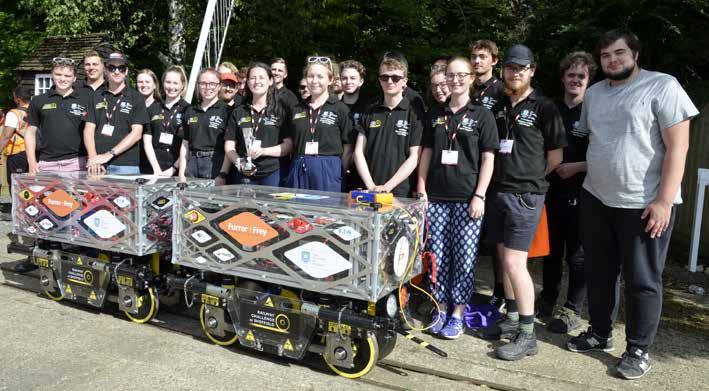
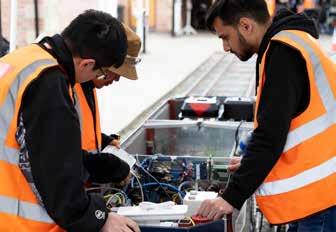
table.ChallengesGermanyReuschlingLokomotivenfabrikWestfaelischeGmbH&Co,(Aachen).andresults
FH Aachen University of Applied Sciences and the
father David Rollin, a founder and first managing director of Interfleet Technology (now SNC Lavalin) whose graduate trainees won the first Railway Challenge. Their sponsorship this year included donations from founder members of Interfleet collected at their 25th anniversary dinner. After the awards, the Aachen team demonstrated their winning locomotive hauling a full nine-car passenger train around the circuit. This is some five times the mass of the specified load and is the first time this demanding, unspecified challenge has been completed without damage to the locomotive. Its performance was amazing given the small size of the lithium titanate oxide batteries demonstrated in the refuelling challenge. Simon Iwnicki who thought up this challenge in 2010 and has chaired the organising group ever since summed up the event: “Thanks to everyone for supporting what was a truly excellent 2022 Railway Challenge. There was a real buzz all weekend and I know that all the teams got a huge amount out of it (even those who struggled most). It was fantastic to see Poznan run round successfully at the end. Overall, I think it was a really great event and I'm already looking forward to 2023! Well done everyone.” For 2023, it is hoped that a turntable might be completed near the station which will allow more competitors than the current maximum of 12. So, dear readers, please encourage more participants to enter. Former participants and newcomers would all be very welcome.
49 Rail Engineer | Issue 197 | Jul-Aug 2022 ROLLING STOCK & DEPOTS
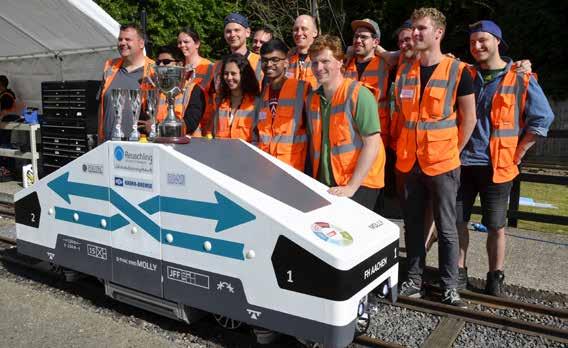
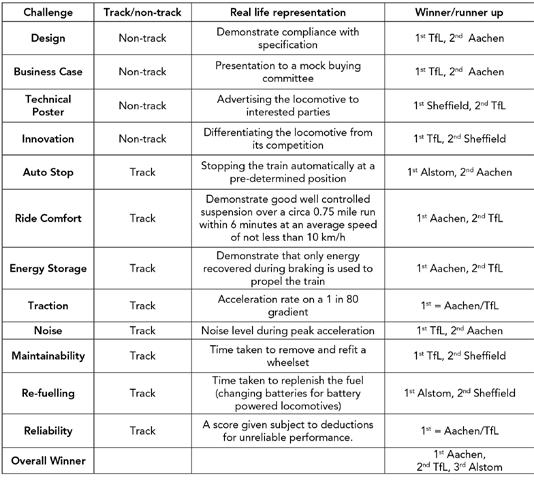
Update from theADHESION RESEARCH GROUPARGMission. RSSBOVENDEN/NEILIMAGE: DOBELLMALCOLM 50 Rail Engineer | Issue 197 | Jul-Aug 2022 ROLLING STOCK & DEPOTS
Driver confidence Much to his surprise, Steve said, given the number of train/freight/ on-track machine (OTM) operating companies in the UK, they examined 91 company driving policies and associated documents. They also carried out 39 interviews with drivers, driver instructors
The driver makes key decisions which depend on the technology and information at his or her disposal. Has the railhead been treated, has a warning been given, what type of brakes are fitted, and are there effective sanders fitted? Moreover, the characteristics of the particular class of train need to be taken into account and these sometimes change over time. Putting this another way, quoting from part of the final report: “It is important to note that there are limits to what train drivers can achieve when low adhesion is an issue. Drivers attempt to overcome challenges posed by the infrastructure and environment, whilst providing a safe and reliable service to passengers - getting this right often involves split-second and instinctive decisions. Far from drivers being a cause of adhesion incidents and operational delay, drivers enable safe and effective operations under difficult environmental conditions and when other control measures cannot overcome the“Improvementsproblem. to railhead condition, whether that be achieved by enhanced sanding, cleaning or other approaches that enable better acceleration and braking, will help realisation of all goals (safety, performance, comfort, and damage). Such improvements will also make it easier for the driver as there will be less demand on them to ‘weigh-up’ low adhesion risk.”
Heart of the system Steve Roberts from S and L Roberts (Railway Consulting) Ltd had, with Richard Roels (RJ Roels Ltd) and Gary Stewart, studied the development of policies for consistent approaches to low-adhesion traction and braking (RSSB Research Project T1221). The objective was to provide the UK rail industry with guidance on low adhesion driving policies, to enable consistent and effective traction, and braking under low adhesion conditions, facilitating improved, safe performance. The project also evaluated the intended and actual use of existing in-cab low adhesion warning lights, to propose the ideal driver and vehicle response, to help inform driving policies.
Part two of this feature covering the RSSB-sponsored 2022 VehicleTrack System Interface Committee and ADHERE seminar, looks at the challenging subject of adhesion, something that has worried railway engineers since the very earliest days of powered rail transport.
Rail Engineer has reported extensively about the Adhesion Research Group’s (ARG) work aiming to improve the safety and performance of the railway in low adhesion conditions. The seriousness of this work was brought into sharp focus in autumn 2021 when two trains collided at Salisbury on 31 October 2021 after one train failed to stop short of a signal at danger because of extremely low adhesion.Thehybrid meeting in York had updates on driver behaviour, managing train sanders, using train and other data to forecast adhesion issues, and some fundamental research on sand-like substances that might better activate low voltage track circuits.
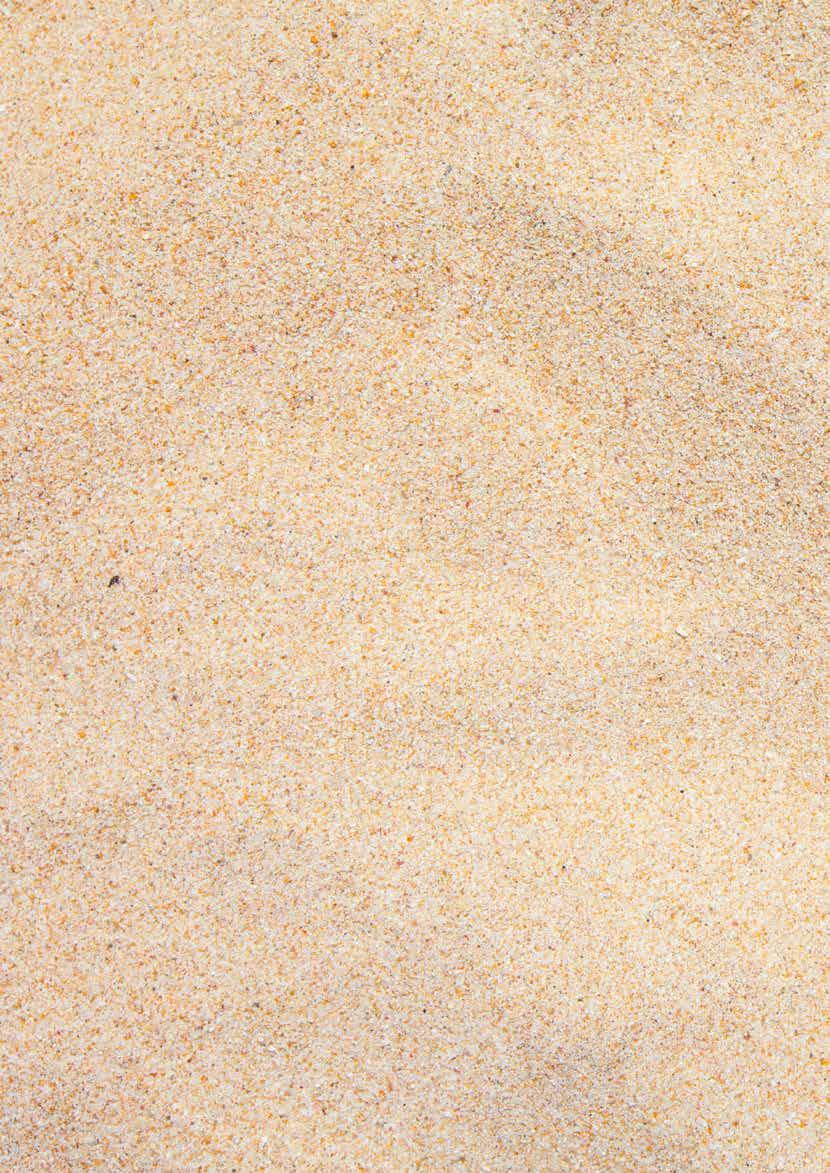
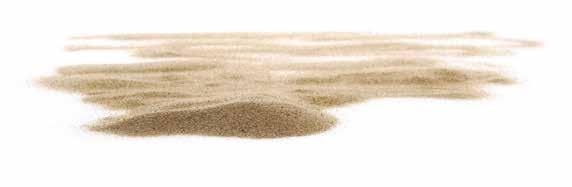
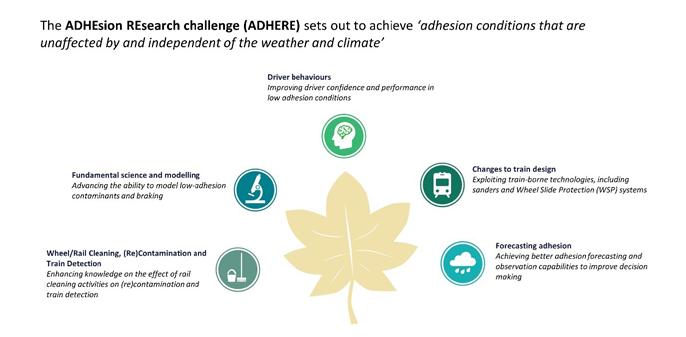
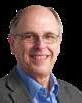

» Chiltern and Great Western Railway have designed their sanding systems so that they work in brake step 1 as the wheelslide protection systems are not considered to be working properly without sanding.
» For cascaded stock, low adhesion tends not to figure much in the management of change documentation.
“How much earlier, how much lighter?”, Steve wondered. He highlighted the plight of on-track machine (OTM) operators as they often drive vehicles with few, if any adhesion aids and limited knowledge of where poor adhesion might be an issue. It was not surprising, therefore, that the driving policy report for OTMs was the biggest. The project has delivered policy guidance documents for freight, passenger, OTM operations and for the in cab low adhesion warning light, together with several case studies and an overall report. All this material is available from the RSSB Research Catalogue websites. Steve concluded with an observation from one of the case studies concerning RSSB’s recent report showing that a disproportionate number of SPADs took place on empty coaching stock at low speed in the autumn. Musing aloud he wondered why sanding is cut out below 10 mph when emergency braking is applied?
» sand quality (is it the right grade and dry?)
ROBERTSSTEVEIMAGE: ROBERTSSTEVEIMAGE: 51 Rail Engineer | Issue 197 | Jul-Aug 2022 ROLLING STOCK & DEPOTS
» storage (keeping sand dry is critical), hopper filling (many ways to get this wrong; access; obstructions, keeping the sand dry, etc, so this could benefit from a human factors review)
» Remarks in policy documents terms such as ‘brake earlier/brake lighter’ were undefined and not always reflective of rolling stock capabilities.
Sanding has featured frequently in Rail Engineer over the last five years, most recently in issue 190 (Jul-Auge 2021) discussing the performance of Double Variable Rate Sanders (DVRS) on two class 323 units and the business case for fitting to the entire fleet (now approved).
Factors contributing the driving goals on low adhesion.
Liam Purcell from Ricardo and Andrew Lightoller from DB ESG recapitulated the benefits before moving on to describe the Sander Maintenance Good Practice Guide aimed at preventing empty sand hoppers, incorrect sand flow rate from the system, and/or the nozzles not pointing at the wheel-rail ‘nip’. The good practice guide covers all aspects including:
and senior managers, examined the braking and adhesion systems fitted to GB rolling stock; and hosted two workshops to address challenges which were attended by 16 railway undertakings.Stevementioned some things that were learned during the study including:
» Many operators require extra brake tests in the autumn, but the nature of the tests varied from ‘drop speed by 10mph’ to ‘slow down almost to a stop’.
Sanding good practice
» daily check (your writer has observed the neat piles of sand around the stabling positions of Croydon trams at Therapia Lane depot)
» periodic check (measured and recorded sand flow, nozzle direction)
» pre-autumn checks (since sanders are typically little-used for the rest of the year). Pre autumn checks should include cleaning, checks on hopper seals and breather as well as checking for dry oil free compressed air (once again to make sure the sand stays dry).
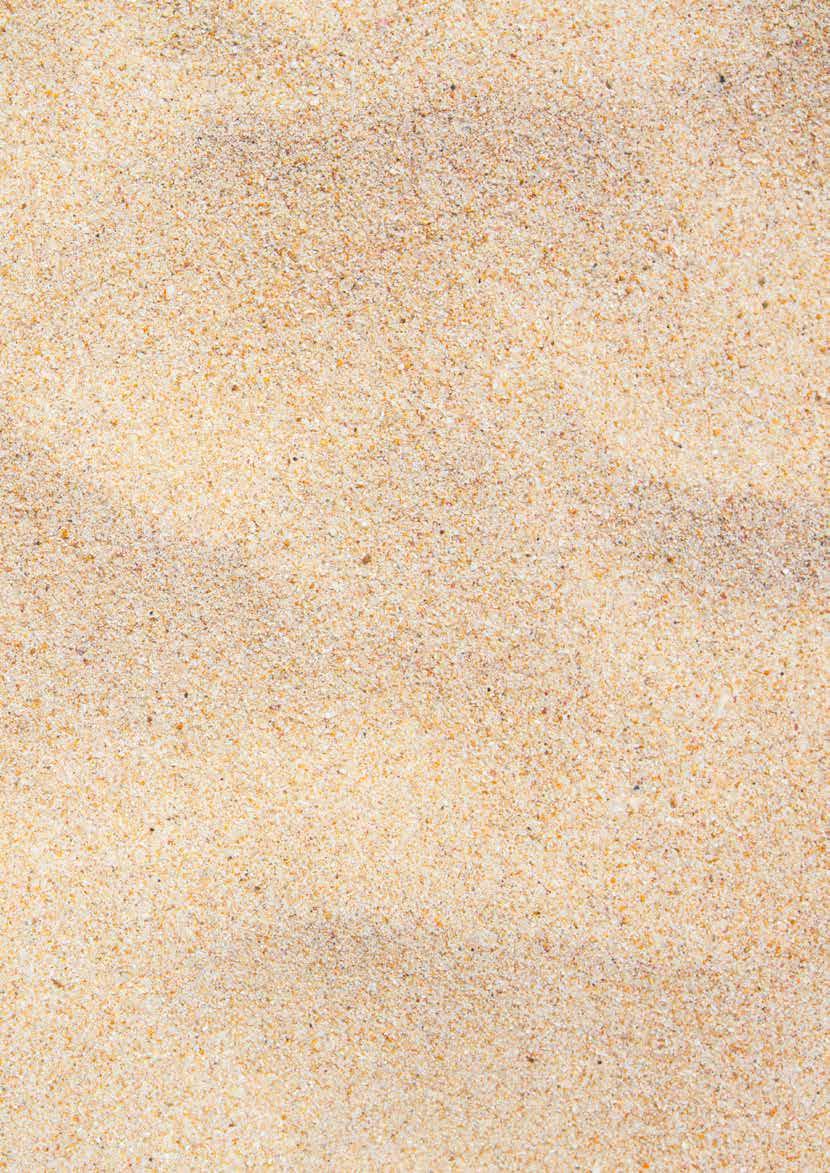
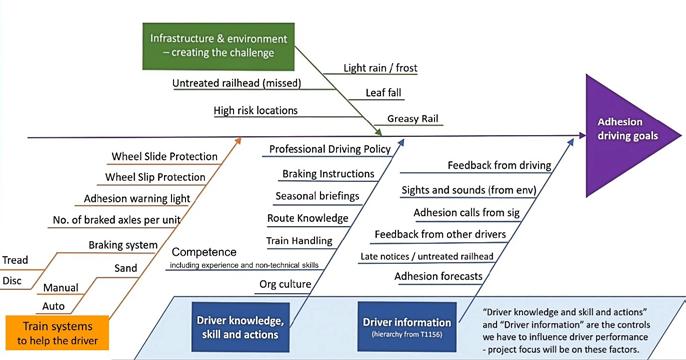
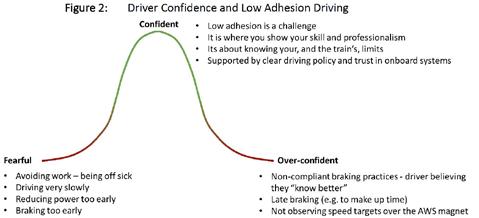
RICARDOPURCELL/LIAMIMAGE:
RICARDOPURCELL/LIAMIMAGE: 52 Rail Engineer | Issue 197 | Jul-Aug 2022 ROLLING STOCK & DEPOTS
SKIPPERWILLLEWIS/ROGERIMAGE: Field test.
» Quantity of dispensed adhesion enhancing material might be increased to improve performance in contaminated areas without risk of poor track circuit performance.
» The use of ‘enhanced sand’ for leading sanders at the front of a train might obviate the need for a lowspeed sander cut off which could help with the final braking action that in turn could reduce low adhesion related platform overruns.
Will said that the next steps will include further field testing to ensure acceptable adhesion levels, testing in real world operations to ensure compatibility with sanders, further study of conductive performance characteristics and, of course, investigation of economic benefits.
Data to insights Targeted adhesion management using on-train data was the final presentation of the day, from Stephanie Klecha, head of digital services at Porterbrook Leasing. Her role within Porterbrook was to maximise the value of data recorded
Sheffield’s Professor Roger Lewis and Dr Will Skipper described their work to characterise how the composition of enhanced adhesion materials affects track circuit performance. Note the term ‘enhanced adhesion materials’ rather than sand. Questions about whether this was sand mixed with some conductive material were not answered in the interests of commercial confidentiality.
Properties of Sand
GB sand and two of the new materials were tested, with a third subjected to some of the tests. The results showed that two of the new materials were consistently delivering much better train detection compared with GB sand.
Seven different particle types, including standard sand used in today’s sanders (GB sand) were characterised in the laboratory for mechanical properties: size distribution, shape distribution, density, flowability, direct shear test and breakage index. The laboratory tests also covered testing for adhesion and conductivity on a simulated 0.5V dc track circuit in the presence of clean wet and dry conditions, and with wet and dry leaf film. All seven products produced acceptable adhesion performance – typically three to four times better than the unsanded performance with leaves. For electrical resistance, some of the newly developed products produced lower resistance values than GB sand, with none producing a higher resistance. Some of the new products showed a lower flow rate than GB sand (possibly undesirable) and some showed a narrower spread from the nozzle (possibly desirable).
These results open the possibility for a number of additional benefits of sander use:
The project demonstrated that the new products reduced the likelihood of isolation occurring in both laboratory and field testing compared to GB sand, and in the lab tests, none of the products created low adhesion conditions and they all had a mitigating effect against leaf contamination.
» On routes with low voltage DC track circuits that are compromised by leaf fall.contamination, regular use of ‘enhanced sand’ could tactically help reduce track circuit failures until the track circuit replacement work happens.
Keeping with the topic of sand, signal engineers have long been concerned that sand will affect track circuits’ ability to detect trains. Neil Ovenden, chair of the ARG said that the only confirmed instances of this had been with the one-shot sanders used for a while when braking sanders were in their infancy, but the risk remains and the Universities of Sheffield and Newcastle were commissioned to investigate.
Tests were also carried out on a real railway with a class 20 locomotive on a 0.5V dc track circuit. A number of different application rates were simulated by hand applying sand on the rail head over 20 metres of track and two passes were made over the material.
Liam and Andrew concluded that the guide is available on the RSSB Research Catalogue websites.
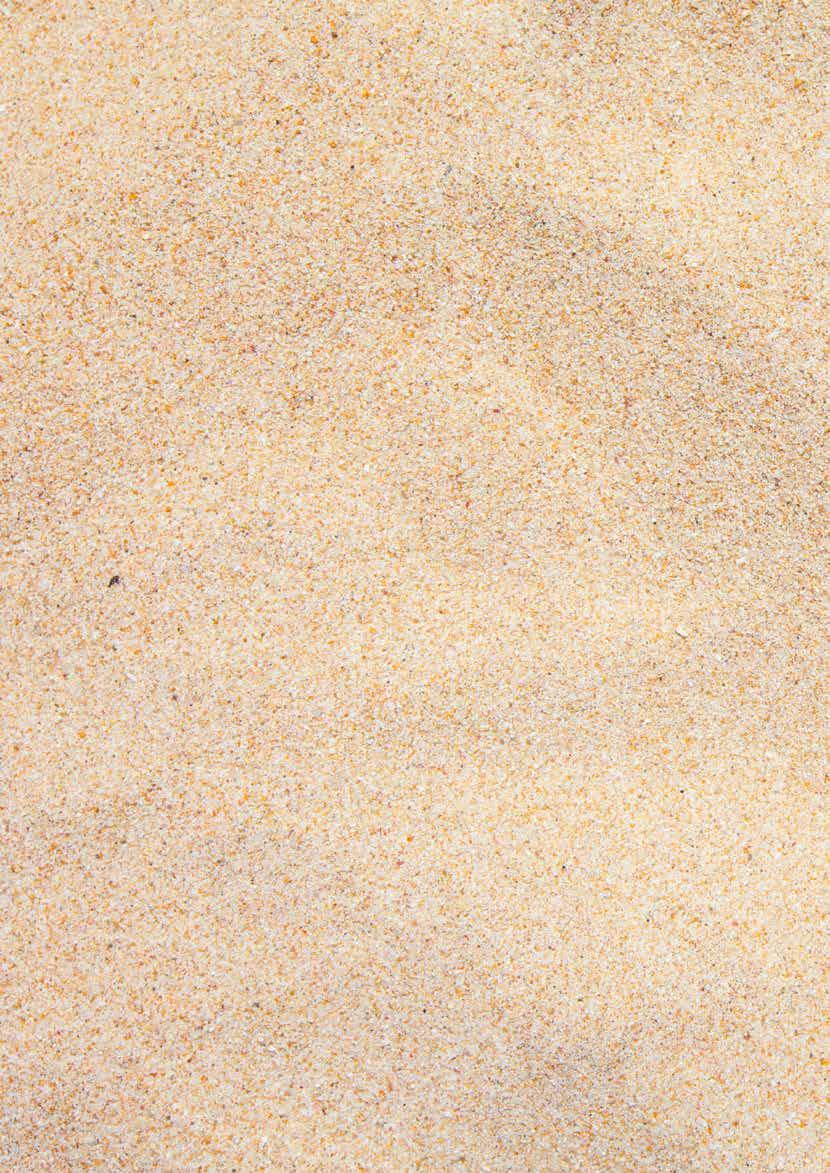


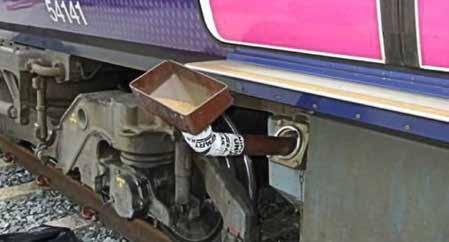
SKIPPERWILLLEWIS/ROGERIMAGE: 53 Rail Engineer | Issue 197 | Jul-Aug 2022 ROLLING STOCK & DEPOTS
The plan also includes collaboration with other projects and suppliers to access additional datasets including: alternative rail head treatment technologies (e.g. PlasmaTrack); alternative adhesion measurement systems (e.g. tribometer rail head friction measurement); DVRS roll out including tracking where sand is applied; exploring links with weather forecasters on adhesion forecasting models; and exploring links with vegetation mapping from FFCCTV datasets. An ambitious plan indeed.
Porterbrook is also supporting the supply chain to develop a visualisation that adhesion controllers might buy into. Initially, the system was using an OTDR feed which frequently downloaded data, but since mid-2021 this is now a live feed to accompany a GPS feed, giving 10-metre accuracy on the correct running line. A significant part of the project was to develop the commercial aspects of reliably delivering and integrating data from a variety of different sources, including the GTR operated trains from Porterbrook and other leaseholders, the Meteorological Office, and NR.
KLECHA/PORTERBROOKSTEPHANIEIMAGE: SKIPPERWILLLEWIS/ROGERIMAGE: Field test schedule. Field test
Network controllers and infrastructure managers are not forgotten, with the work to make available information about adhesion risk areas which might lead to more intelligent scheduling of railhead treatment trains. Thanks to the presenters for their assistance in producing this article and to Ben Altman from RSSB.
Conclusion It is good to see steady progress towards the roll out of DVRS combined with appropriate guidance for drivers to make best use of it. Work on what might loosely be described as ‘conducting sand’ opens the way for an even higher volume to be used if conditions make it necessary.
Map of braking zones: green indicated braking without WSP and red with WSP. Wide area view and magnification showing Clapham Junction, Brighton fast and slow lines with up and down lines shown separately. results.
on trains, to enable all reliability, engineering, and maintenance planning to be underpinned by data analytics and to unlock the value of the 90%+ unused data across the industry. For adhesion management/forecasting, Porterbrook has, since 2019, been working with Network Rail (NR) and Govia Thameslink Railway (GTR) on a project that uses GPS and on train data recorder (OTDR) data to map and trend adhesion issues (i.e., WSP/ sander activity). This is linked to tracking the daily rail head treatment trains to assess whether the water jetting/sandite application is making a difference.
The plan for 2022 and onwards includes expansion beyond GTR; encouraging OEMs, TOCs, supply chain, and ROSCOs to share their equivalent data; trialling NR’s ‘data marketplace’ as the end point for the data and the subsequent source for visualisations; collaborating with RSSB and RDG on data specifications and sharing data across the industry.
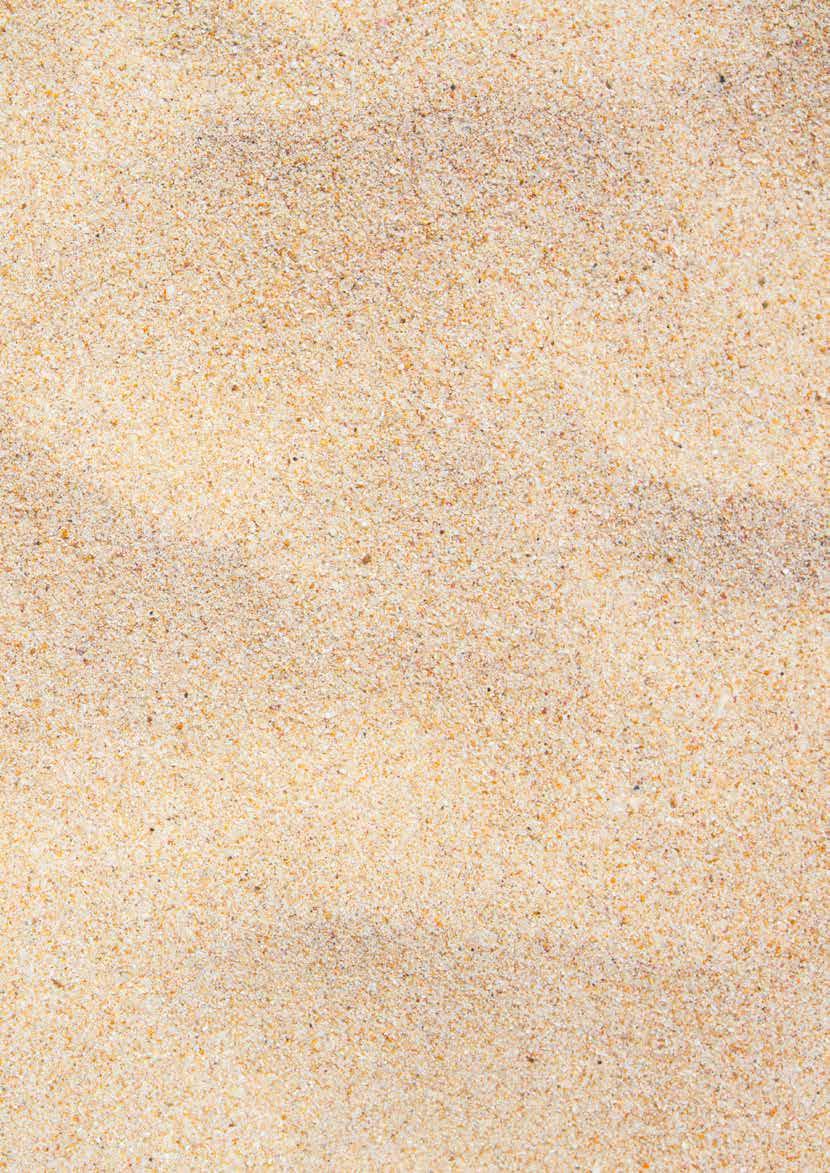
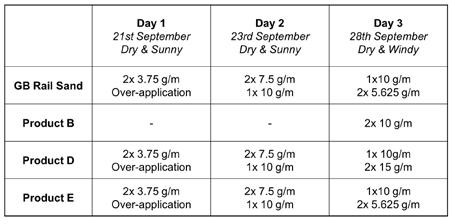
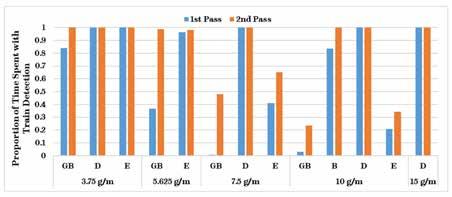
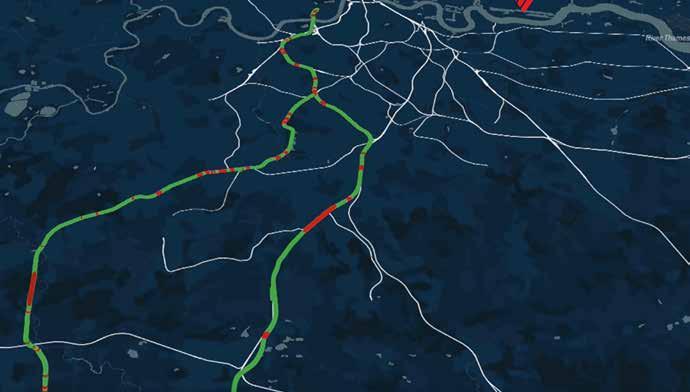
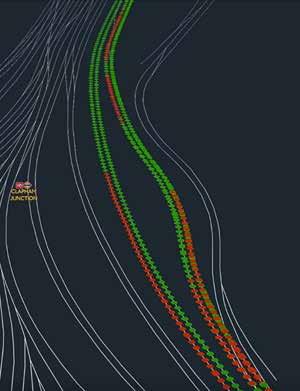
Rail management A fixture at the event is Brian Whitney, Network Rail’s expert for track and S&C. He appears to have infinite capacity to frighten the audience with his images of broken or damaged track, while reassuring them with the learning that gets fed back to asset management teams.There is approximately 30,000km of track (60,000km of rail) in the UK and currently
The current organisations leading this work are the RSSBsponsored Vehicle/Track System Interface Committee chaired by Gareth Evans, Network Rail Technical Head of Track, and its sub-group the Adhesion Research Group chaired by Neil Ovenden Head of Engineering, Rail Delivery Group. Each year they present updates to the industry at an event organised and hosted by RSSB. On this occasion a faceto-face event was held in the York National Railway Museum with an on-line feed. This article covers track-train interaction. Adhesion will be covered later in this issue.
In 1808, Richard Trevithick demonstrated his pioneering steam locomotive on a circle of track in Bloomsbury, London. It is thought that the high loads from the serrated wheels he used with the aim of improving adhesion, caused rail breaks, leading to derailments. For more than 200 years railway engineers have had to deal with rail breaks and poor adhesion. Over that time great strides have been made in understanding the issues at the wheel rail interface.
54 Rail Engineer | Issue 197 | Jul-Aug 2022 ROLLING STOCK & DEPOTS
DOBELLMALCOLM
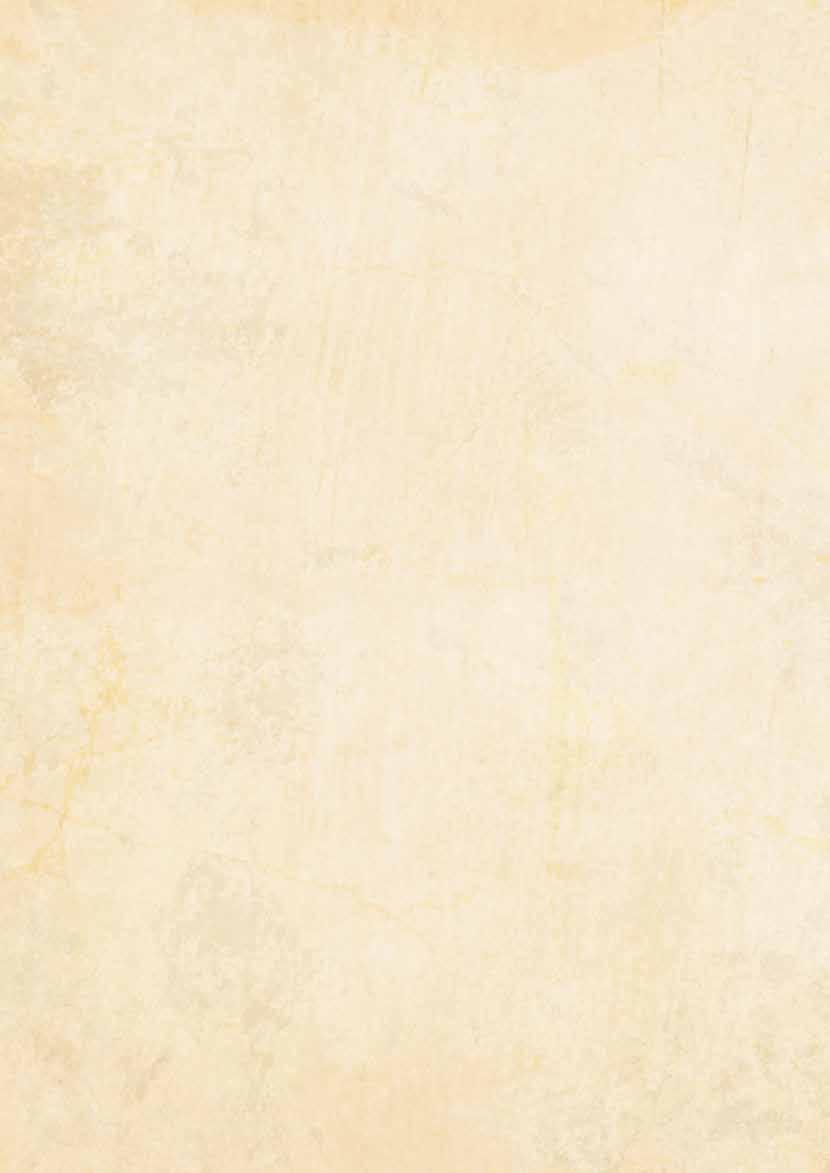
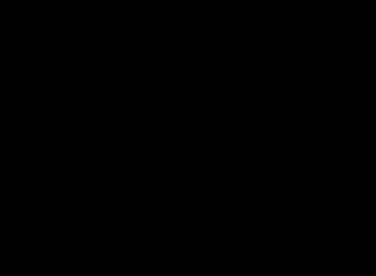
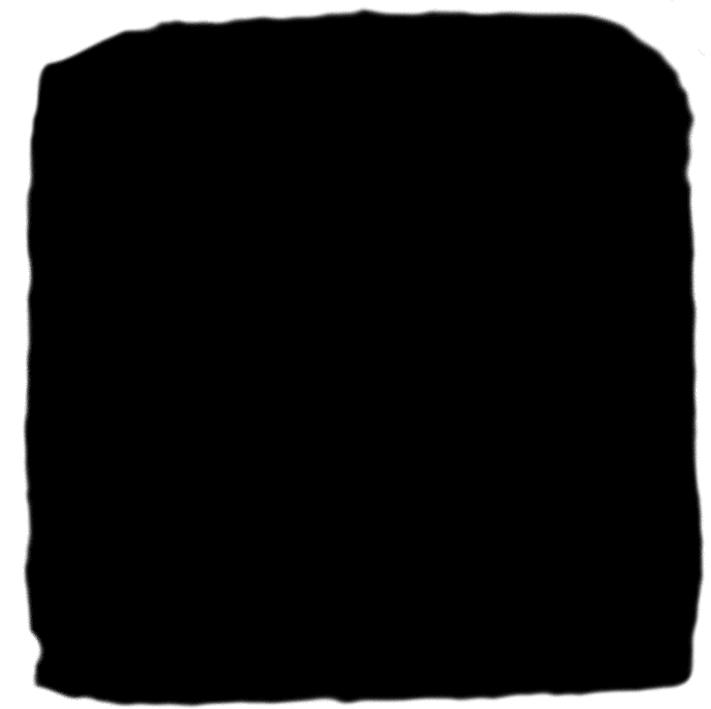
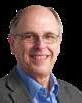


there are circa 80 to 90 breaks per year, down from approximately 10 times that number before the year 2000. It was the Hatfield train crash in 2000 that shone a very bright light on rail breaks and the attention paid to this subject since then has been instrumental in delivering the improvement although Brian cautioned that the number has been in the 80-100 range for the last five years, with no sign of further improvement.
55 Rail Engineer | Issue 197 | Jul-Aug 2022 ROLLING STOCK & DEPOTS
Rail breaks by type. Coloured circles grouped by type.
There are some 30,000 rail defects reported per year, over half of which are caused by surface defects arising from the fingernail sized contact between wheel and rail. All must be dealt with in accordance with timescales prescribed in standards, sometimes accompanied by a speed limit.
Part of the improvement stems from the attention paid to managing rolling contact fatigue and the grinding programme that restores a crack free rail head. However, there is also rigorous management process of testing, monitoring, and action to eliminate defects before they become fractures.
The top two causes, representing over 25% of all breaks, were rail foot corrosion and breaks in tri-metallic welds – used where a stainless steel insert is used in the weld between rail and cast crossings.
Broken rails 2020-2021.
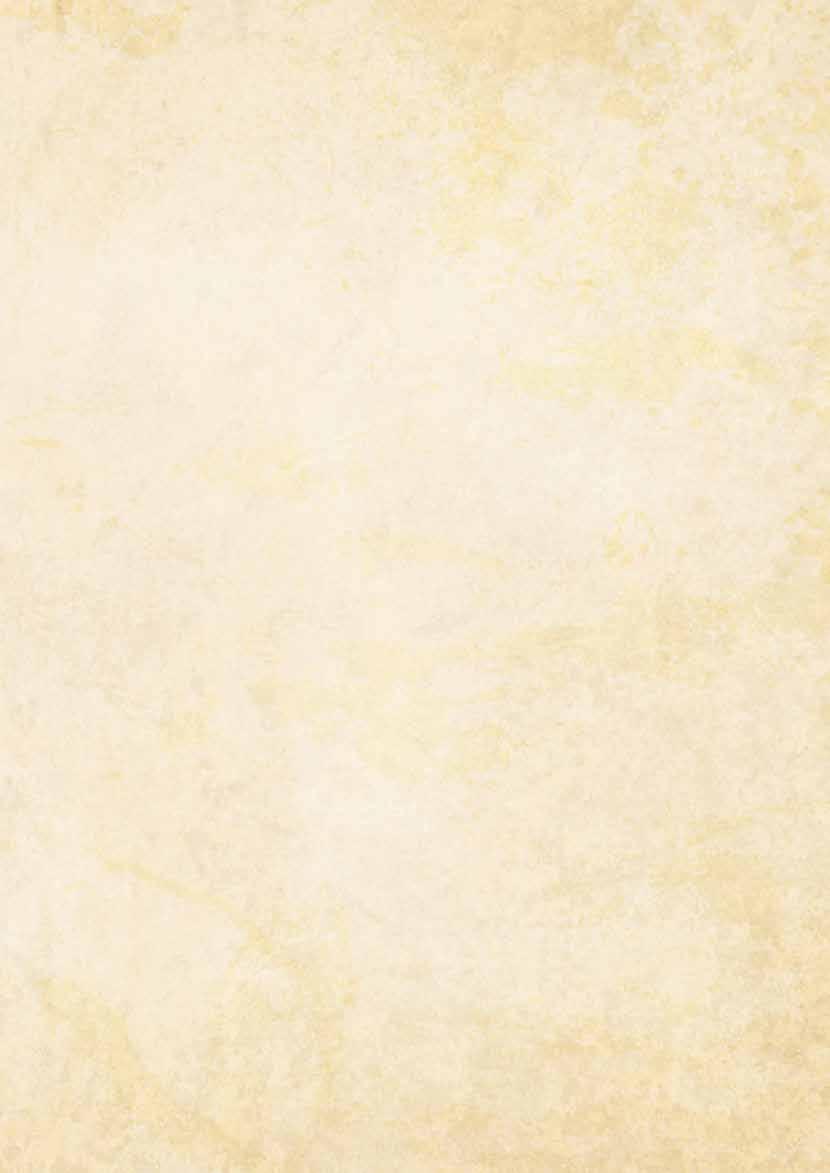
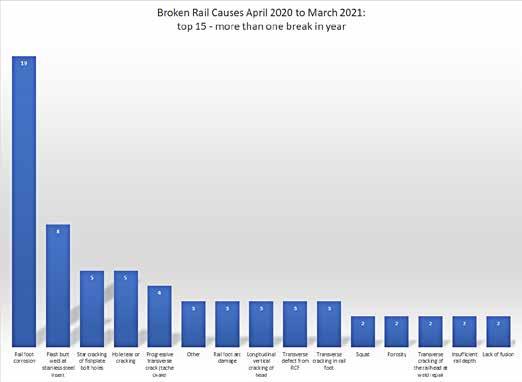
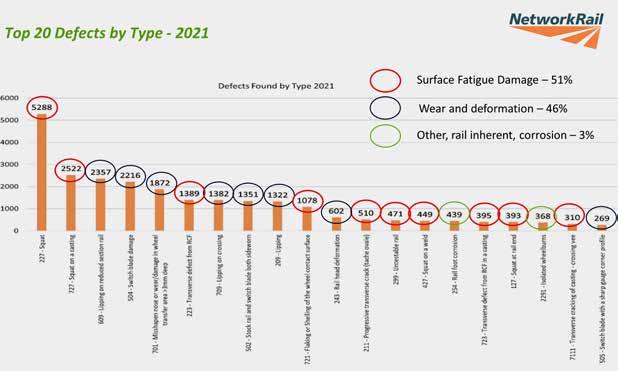
Network Rail needs to consider the potential of replacing rail in at-risk locations before a physical defect is detected through routine inspection but where the fatigue life of the rail foot is shortened due to local conditions.
1 1 2 3 56 Rail Engineer | Issue 197 | Jul-Aug 2022 ROLLING STOCK & DEPOTS
Brian also reflected that although rail foot corrosion/ cracks represent just under 1.5% of the defects, it is also the cause of more than 25% of all the rail breaks. He said that rail foot cracks are the hardest to detect and had been looking at whether the conditions for rail foot fractures could be forecast.
Brian added that this area had discoloured ballast partly because of paint markings highlighting cables routed under the ballast, and partly from the localised attrition under increased dynamic loads, indicating that this small area had not been tamped.Indiscussion, Brian agreed that a way of managing defect precursors might be for areas, not able to be tamped or otherwise having discoloured ballast or slight dips, to be given expert attention from track maintainers, perhaps using stone blowing.
Double rail break Sandy SandyNorth.
Dealing with rail defects costs more than £150 million per year, and part of Brian’s remit is to find ways of detecting defects so they can be dealt with during routine maintenance rather than having any form of emergency work carried out. He illustrated this with an incident where both rails broke almost next to each other at Sandy North. The track had been laid in 1988 vintage CEN 56 section rail, supported on F27 concrete sleepers. Both had broken from small foot cracks which, under tension from a slight dip angle of 10 to 15 milliradians had fatigued and then fractured. It was discovered that one rail had fractured some time before the other and the fault was only detected when the second rail fractured, which interrupted the signalling.
Using data
North broken rails: 1, broken ends in situ; 2, discoloured ballast from FFCCTV; 3, foot defects (defects together with the rail dip initiated the fractures.
Detecting defects
On the theme of recognising defect precursors, Brian reported that, as an organisation, Network Rail is data rich but information poor, and he spends a great deal of time exploring how better to understand the local condition(s) of the track asset. He seeks to use data from different sources to focus on potential risk sites which will require improved information systems and accurate alignment of different data sets to enable easyBriancorrelation.wantstofind ways of turning this data into algorithms that can do the same job automatically, in order to understand areas at higher risk of failure. For example, this could lead to better management of support conditions particularly at transitions/wet beds/voiding. This might, he said, lead to enhanced minimum actions for locations identified as higher risk where rail replacement may be required before a failure occurs.
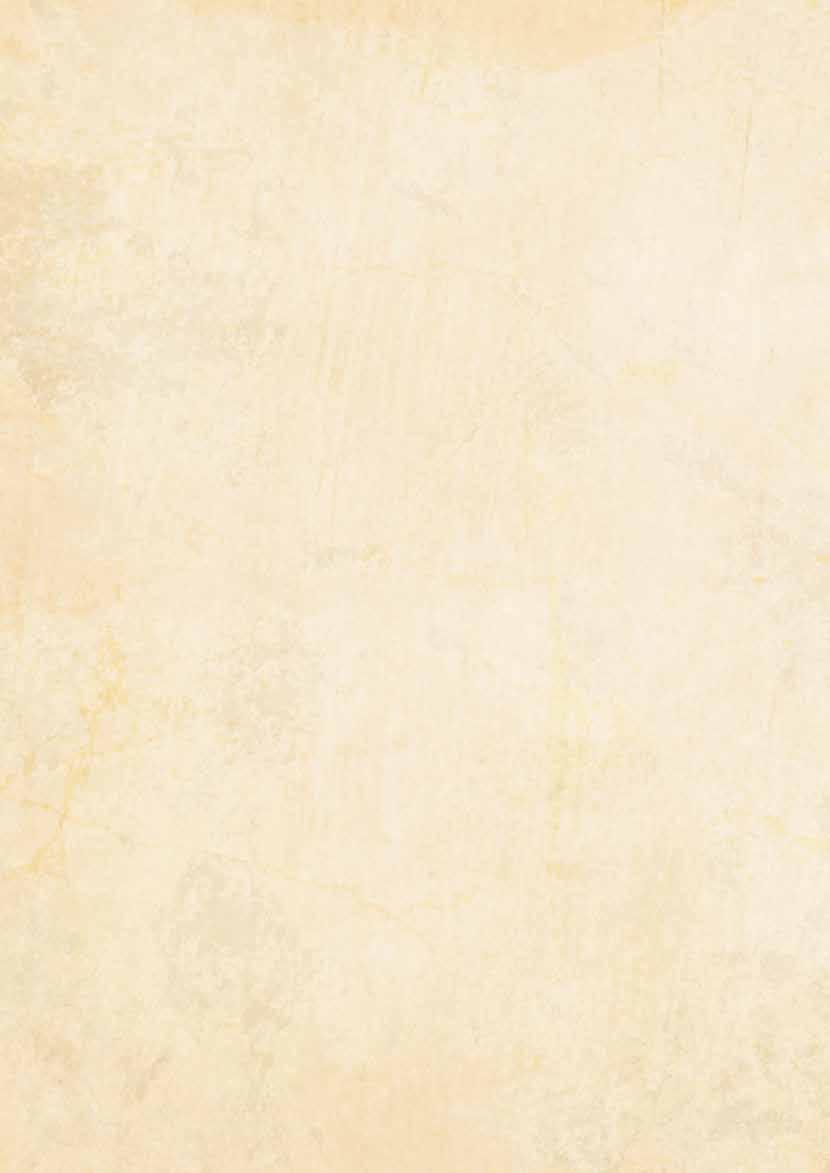
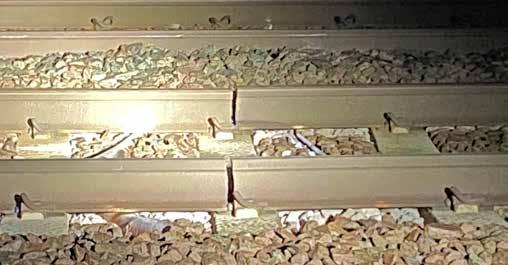
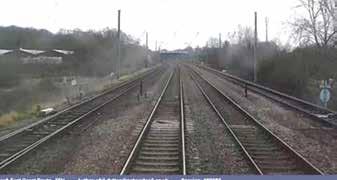
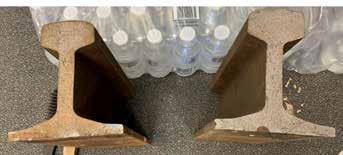
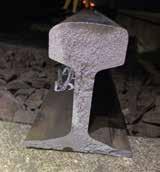

The cost of managing and rectifying track defects is one of the factors included in the rail industry’s Vehicle Track Interaction Strategic Model (VTISM) which is used by asset managers and others to understand things such as likely track degradation rates, impact of different types of rolling stock and likely budget requirements.
Despite the gloom, Brian was pleased with the progress that has been made in the overall culture of the industry, recognising that track does not look after itself. “Neglect it at your peril”, he said, “track very rarely fails safe.”
Professor William Powrie of the University of Southampton introduced Modelling the Impact of Heavy Axle Weight (HAW) on Infrastructure. HAW vehicles (defined here as an axle weight of 22.8 to 25.4 tonnes) can cause disproportionate damage to the infrastructure.
Track modelling
Andy Rhodes from Serco Rail Technical Services described further enhancements to the model both to keep it compatible with computer hardware/software and to include updated knowledge and cost values. Infrastructure VTISM allows track engineers to investigate the impact of heavy vehicles on the track and infrastructure engineers aspire to have a similar tool focussed on the assets under the track.
This project has scoped a methodology for developing, populating, and validating a model to understand and quantify the incremental effects of HAW on rail infrastructure. This, together with possible mitigations and associated costs, would enable an estimate of the impact of HAW. Infrastructure covered: geotechnics
althoughhasofthumbbridges,behaviourwithdifferentreliabilitydegradationtoimpactsdegradationconsideredtrack).timbersfeaturesandsoil,bridges,embankments,(earthworks,andcuttings);substructure(naturalsubgrade,andsub-ballast);limitingtracksystem(e.g.)longitudinalanddirectlyfastenedTheprimaryimpactwasassetrate.Secondarywerecostimplicationsmitigateestimatedandsafety/risksassociatedwithoptions.Williamillustratedtheworkadescriptionoftheofmasonryarchwheretheruleofthattheworkingload50%ofthecollapseloadbeenconfirmedbytesting,thereisalwayssome Another example of unexpected failure - of a steel bridge: Stewarton 27 January 2009. 57 Rail Engineer | Issue 197 | Jul-Aug 2022 ROLLING STOCK & DEPOTS
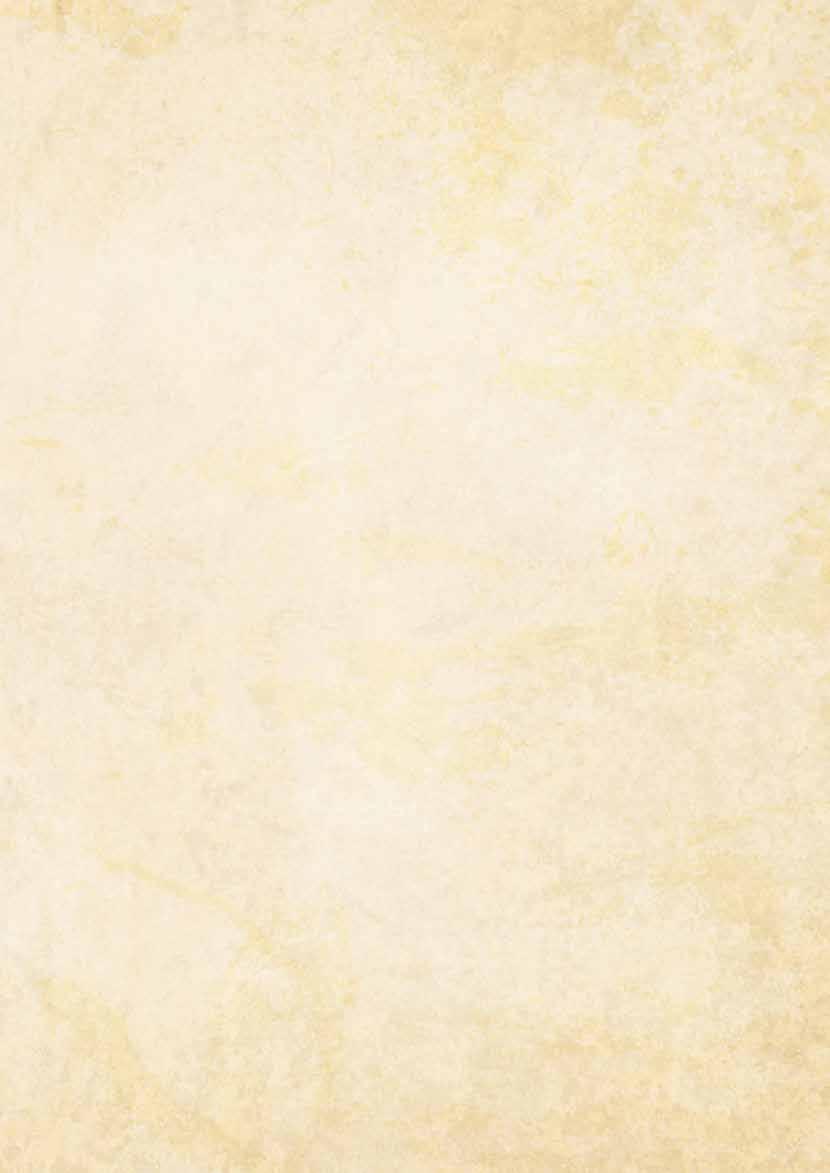
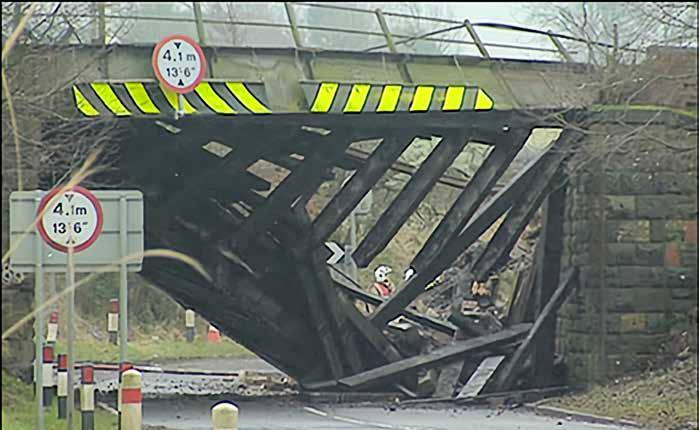
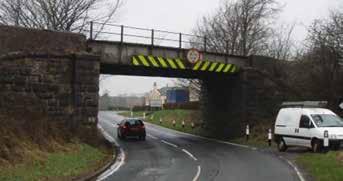
Lateral loading – best practice Adam Bevan, Professor of Railway Systems Engineering at University of Huddersfield reported on a project to review lateral track loading requirements, as the current practice for specifying loading for track design is inconsistent. He said that although loading standards are typically based on known satisfactory performance of existing track systems, there are variations in how these loads are interpreted and whether they are being over or under specified.Adamoutlined a whole range of current standards where the limiting lateral forces are significantly different with the largest force specified being twice the smallest in some cases. A large number of dynamic simulations have been undertaken to quantify the multitude of lateral loads for a wide range of vehicle types and operating conditions.Interactions of asset types.
| Issue 197 | Jul-Aug 2022 ROLLING STOCK & DEPOTS
uncertainty around the original construction and current condition.Theproject has collated the current understanding of the condition of various asset types in a hazard assessment and identified work required to populate the proposed model. It has also shown how the various asset types interact. In both cases, considerable additional understanding and/ or knowledge is required to fully populate the proposed model.
Findings to date. Rail Engineer
58
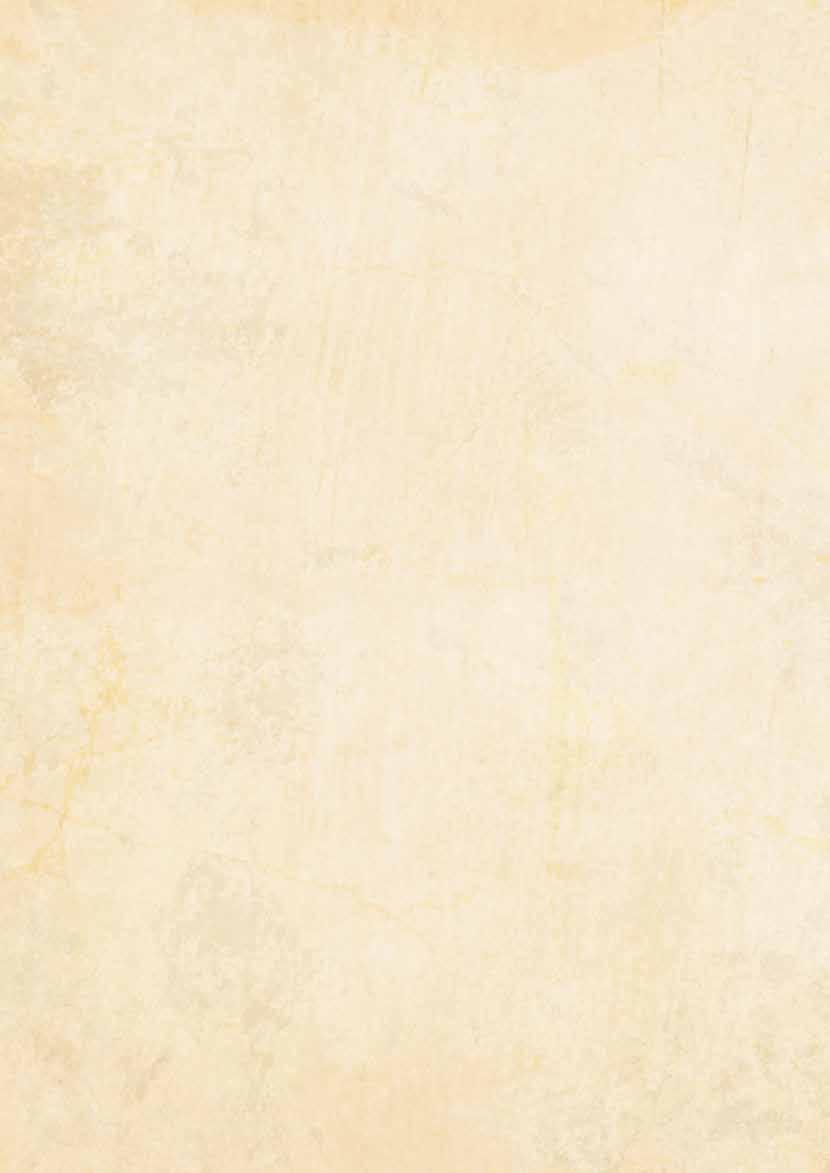
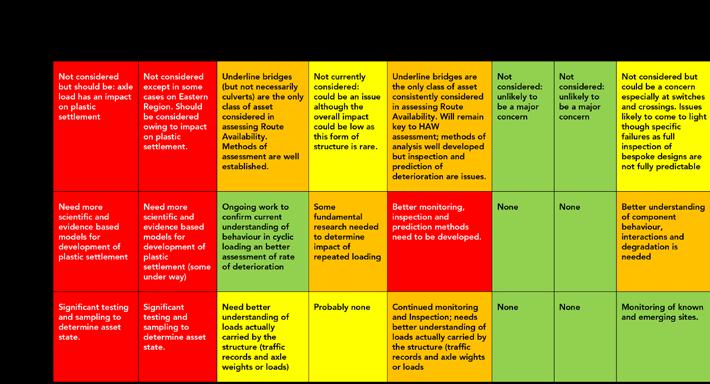

¬ Technology: solar-powered LED ¬ Temperature range: -20°C (- 4°F)
(185°F) ¬ Output at full power: up to 240 hours without additional solar radiation ¬ Service life: more than 8 years ¬ Colours: yellow, red, white, green, blue (two colours per cover possible) ¬ LED configuration: one-sided and two-sided reflectors ¬ Charging time: approx. 3 hours on a sunny day STRAIL (UK) Ltd. - Richard Whatley | Tannery Lane // Send / Woking // GU23 7EF // Great Britain Phone +44 (14 83) 22 20 90 // info@strail.com | www.strail.com pedeSOLAR - INCREASED SAFETY. pedeSOLAR > finding your way at night and in www.strail.comfog! 59 Rail Engineer | Issue 197 | Jul-Aug 2022 ROLLING STOCK & DEPOTS
When is a wheel flange too thick?
Outputs have, not unexpectedly, shown the key influence parameters such as axle load, curve radius, and cant deficiency, but have also shown that typically the lateral force is not an average across the two axles of a bogie; generally there is a higher force from one of the axles. The next stage is to develop a framework for lateral loading.
Julian Stow and Jordan Brant, both from University of Huddersfield, reported on their work ‘Investigating the need for a maximum flange width limit’. Group Standard GMRT2466 sets out the requirements for the control of geometry of wheels including maximum new and worn flange width (at a specified height above the wheel tread) and maximum new and worn flange height. There is currently no limit on the maximum worn flange width, although flange width can increase where tread wear dominates, something increasingly common on modern passenger vehicles with good steering characteristics.
Thanks to the presenters for their assistance in producing this article and to Ben Altman from RSSB. Illustrations courtesy of the presenters. to 85°C
There is a requirement in the Rolling Stock National Technical Specification Notice for flange width not to exceed 33mm but measured at a height of 10mm, not the UK practice of 13mm (dimension A in the diagram). The work included a survey of different wheel profiles to assess the scale of the issue, followed by an assessment of the potential hazards using various simulation and modelling methods. These highlighted that the key reason for specifying a maximum flange width was to ensure that good guidance and protection is maintained at crossing noses. The study has recommended limits which will be considered by RSSB for future inclusion in the standard. This was a lively event and even the online audience could tell that people were pleased once again to be able to meet face-to-face.
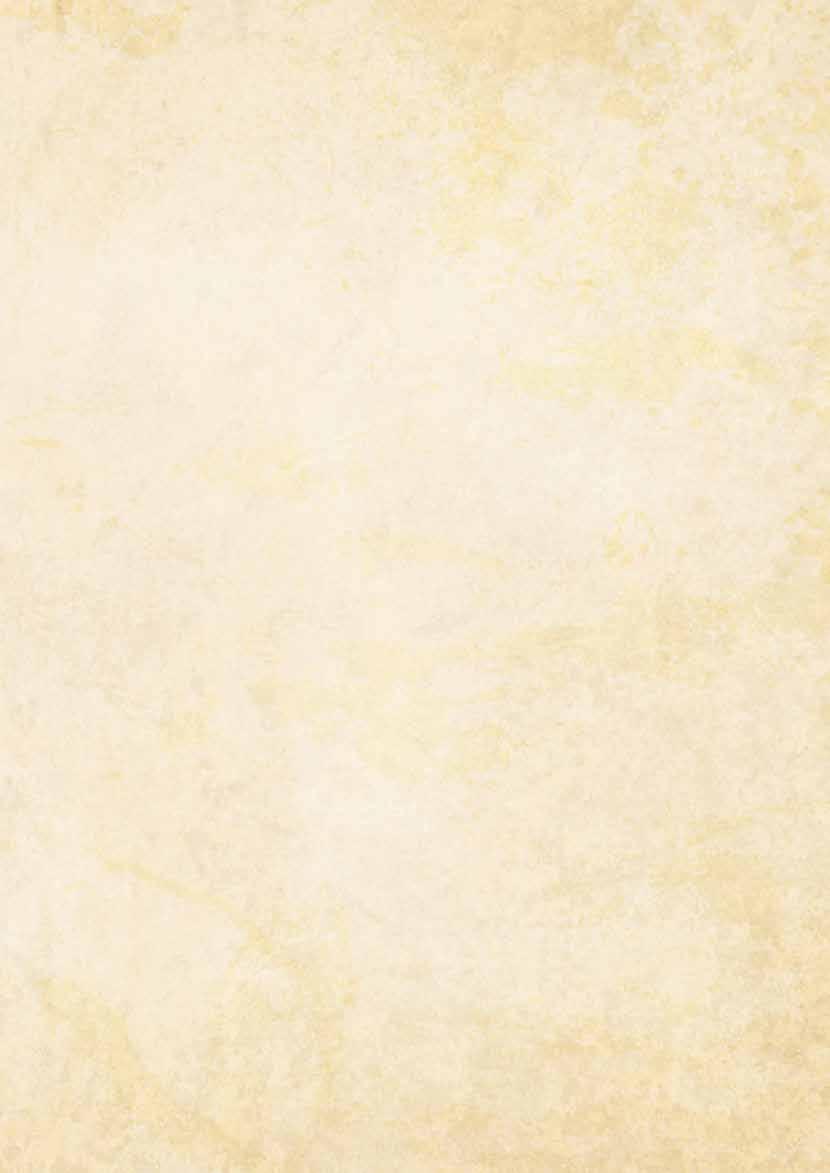
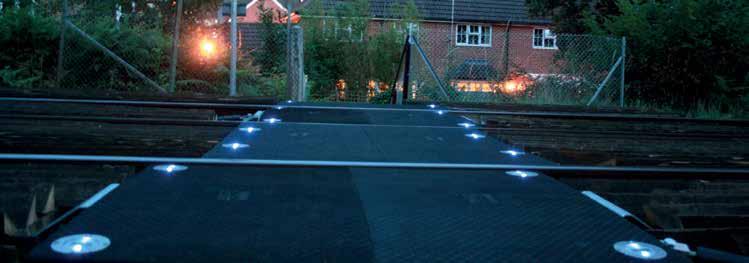
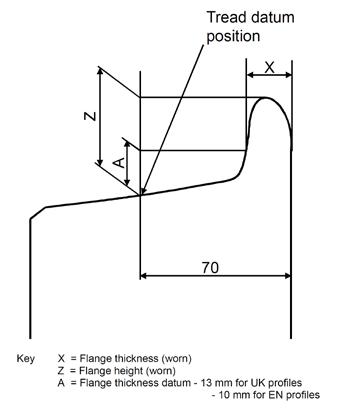
(Below left) Rail mounted PSD manipulator with three axis longitudinal,movement:lateraland tilt. (Below right) Rail mounted manipulator manoeuvring PSD module tilted to clear beam. BREMSEKNORRPHOTO:BREMSEKNORRPHOTO: 60 Rail Engineer | Issue 197 | Jul-Aug 2022 STATIONS & PASSENGER TECHNOLOGIES
Much has been written about the engineering marvel that is the Elizabeth line, which opened on 24 May 2022. There have been many articles, conferences, and TV documentaries chronicling its construction, and a two-part programme on BBC 2 in June focused on systems integration. This is something that is usually not visible, but the implications of not integrating properly is a railway that doesn’t work. When chairman of British Railways in the 1980s, the late Sir Peter Parker observed that railways tend to fall flat on their interfaces. With the advent of computers and telecoms systems, that has never been truer.
The Elizabeth line’s
The original concept for Crossrail was 10car trains of 20-metre-long cars. In the end, Bombardier won the contract with 9-car trains of just under 23 metre-long cars. Clearly, this matters for the PSD design as the train and platform doors must align perfectly, leading to the original PSD design concept being amended. PSD design has evolved and become quite standardised since they were first adopted on the Singapore metro in the late 1980s. Clearly, heights/widths and spacings must be decided and site-specific issues such as wind loadings must be agreed. Then, thoughts turned to authorisation for use. Compliance and authorisation
Take the Elizabeth line’s Platform Screen Doors (PSDs) which were specified for its eight underground stations. This amounts to 432 pairs of doors which seems a lot, although compared with the 3,780 pairs of sliding plug doors on the trains it is quite a modest number. However, each PSD represents a potential single point failure. We’ll come back to this.
platform screen doors
The casual reader might assume that the Elizabeth line’s PSDs would be just another version of those fitted to the Jubilee line which, coincidentally, also has eight underground stations so equipped, albeit with 476 door pairs. But the environment on the Elizabeth line is quite different. Three significant differences are that: i) compared with the Jubilee line, the Elizabeth line screens are floor to ceiling, so the latter have to withstand pressure pulses not present on the former; ii) Elizabeth line systems have to provide access for maintenance whilst protecting the maintainer from the 25 kV overhead rail; and iii) Elizabeth line systems enable a selective door function, that allows for PSDs not to open if the adjacent train door is locked and vice-versa. Both lines’ platform door systems were manufactured and installed by Knorr-Bremse Rail Systems (UK) Ltd, and KnorrBremse Group's IFE division manufactured and supplied the class 345 train door systems.
The Elizabeth line was subject to the Interoperability Requirements of the Railways and other transport systems regulations, as well as the common safety method (CSM) on risk evaluation and assessment. As far as your writer is aware, this was the first time PSDs had to be authorised under these regulations. The
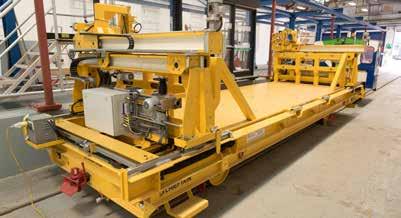
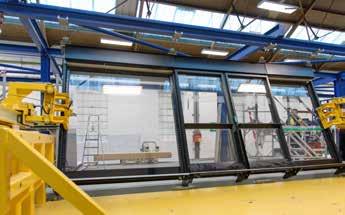
(Below left) Palettes of PSD modules ready for loading onto the manipulator (Belowwagons.right) Fixed screens installed: note space above for services and passenger information screens.
It was not feasible to transport the preglazed door and screen modules from surface to platform as the logistics for the deep stations would have been impossible. Instead, base plates on the platforms were carefully installed in exactly the right places, and the pre-built modules were delivered on works trains which were equipped with special manipulators to slide the modules precisely onto the baseplates once the train has been positioned approximately in the right place longitudinally.Notonlydid these manipulators have to move the door modules horizontally and longitudinally, they also had to be able to be tilted to clear pre-installed vertical and horizontal beams. Once the doors and screens were in place, other disciplines filled the
DOBELLMALCOLMPHOTO: 61 Rail Engineer | Issue 197 | Jul-Aug 2022 STATIONS & PASSENGER TECHNOLOGIES
Challenging installation
DOBELLMALCOLM
Technical Specifications for Interoperability were silent on PSDs. For demonstration that risks had been properly evaluated and assessed, the choices were demonstrating compliance with Codes of Practice (e.g., Euronorms), comparing against Reference Systems, or carrying out Explicit Risk Estimation (a.k.a., QRA). At the time there were no codes of practice or relevant reference systems, and explicit risk estimation is an exhaustive and exhausting process. It was hoped that an international committee would develop a Euronorm in time. In the event, it was not until 2021 that Euronorm EN17168 ‘Railway applications. Platform barrier systems’ was published so, apart from some sub-systems which were already approved, much explicit risk estimation was undertaken.
FOLEYFRANKPHOTO:
BREMSEKNORRPHOTO:
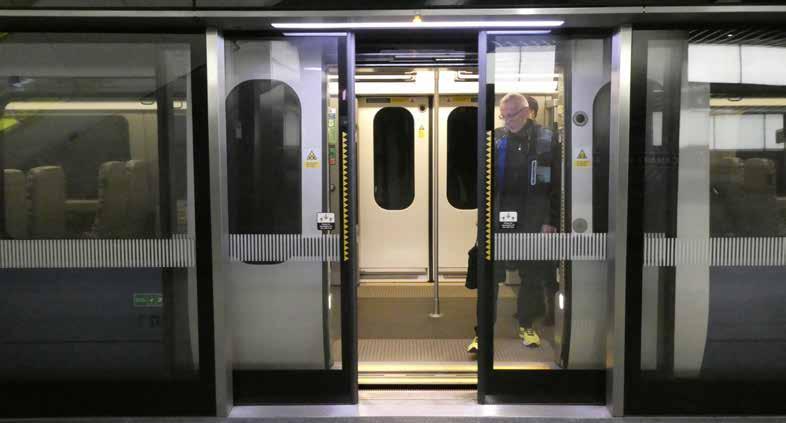
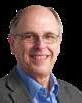

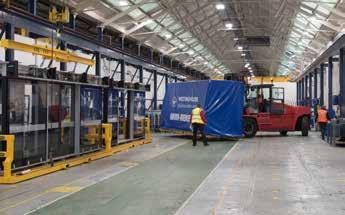
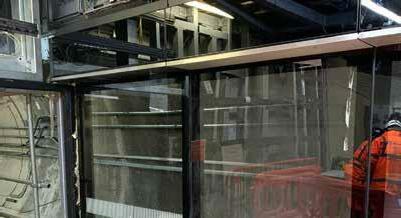
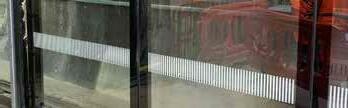
Frank Foley, lead PSD engineer for Crossrail at the time said: “The design, installation, testing and integration of the Elizabeth line Platform Screen Doors has been a great challenge – much more so than is obvious for a system that ‘just opens and closes the doors’. Practical and logistical constraints around physical access, coordination and safety on site have on occasion caused excitement; technical and integration issues have taken many people and many hours of testing, careful analysis, consultation, innovation and collaboration between teams.”Agood place to admire the installation is on the eastbound platform at Tottenham Court Road where the flat glass doors and screens follow the gentle curve – the only curved platform on the new build sections of the Elizabeth line. System controls Clearly the PSDs must be perfectly synchronised with the train doors. This involves interfaces with the signalling system, the SCADA system, and, of course, the power supply. Station staff and control room staff need to know about any failures. If a PSD on the Jubilee line fails it can be locked closed, and the service continues even though the train door adjacent to the failed will open and close as usual. There is no equivalent on the trains; if a train door fails, then the train is taken out of service.
The additional feature is that locked-out train or platform doors are synchronised with the adjacent door; be it train or platform. If a train door is locked out, during the transit from one station to the next, the TCMS via the OBCU, and wayside signalling, sends this information to the next station’s PSD controller so that the PSD adjacent to the locked-out train door remains closed. as illustrated in the photo on page 64. So far, so good. This is a useful system but no substitute for reliability as locked-out doors tend to increase dwell times.
There is also, currently an integration issue in the overall PSDSignalling-Train system when there are two trains in transit between stations at the same time, something that will happen frequently when the service ramps up to 24 trains per hour. The following illustrates the issue:Ifthe first train has some defective doors, the TCMS, via the signalling system, tells PSDs and the appropriate PSDs stay closed. This is still held in PSD system memory and when the second train is approaching, the PSD controller, again via the signalling system, tells the second train’s TCMS that some PSDs are isolated. This TCMS then inhibits the corresponding train doors. The trouble is that the second train’s TCMS has got in first and told the PSD controller that all the train doors are healthy. This means that when the second train stops, all the PSDs open but the inhibited train doors stay closed. This is termed the ‘door inhibit carry-over’ issue and, fortunately, the remedy is a straightforward change to the software within the overall PSDSignalling-Train system. Another feature of the system is that this process only works once the failure has been identified and the appropriate door has been locked Court Road Eastbound platform.
Tottenham
DOBELLMALCOLMPHOTO: 62 Rail Engineer | Issue 197 | Jul-Aug 2022 STATIONS & PASSENGER TECHNOLOGIES
space between the top of the door modules and the tunnel roof including other services such as lighting and passenger information screens.
On the Elizabeth line there is a new feature that makes the control system more sophisticated. Firstly, as is usual main line practice, individual train doors can be locked out of use, and this information is reported to the train’s control system - TCMS. Each PSD can be locked out of use too and its status is reported back to the PSD controller. In normal operation, the train brakes to a stand automatically. When the signalling system registers that it has stopped in the correct position, it issues permission for the doors on the correct side of the train to be released. When the ATO or the train driver signals to open the doors, the train’s TCMS issues an instruction to open the train doors and, simultaneously, a signal goes from the TCMS to the Siemens Trainguard MT On Board Control Unit (OBCU) which is transmitted to the wayside signalling system and on to the correct station PSD controller which instructs the PSDs to open. It takes longer to write about this than for the instruction to be carried out, as the train and platform doors open or close more or less in sync.
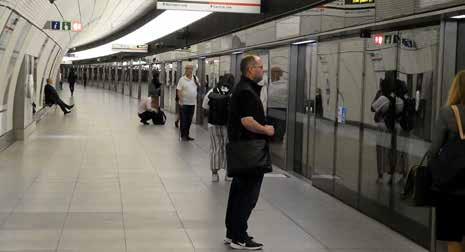
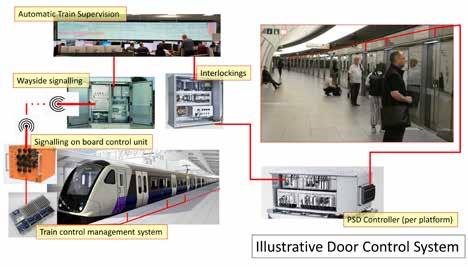
www.railsta awards.com THE RAILSTAFF AWARDS 2022 MORE THAN AN AWARD NOMINATE TODAY! Apprentice of the Year Award for Charity Covid HeroDigitalCovidIndividualOutstandingAwardHeroes-OutstandingTeamAwardCustomerServiceAwardDepotStaAwardRailway(S&T)PersonorTeamAwardGraduateorNewcomerAward Health & Wellbeing Award HR, Diversity & Inclusion Person or Team Award Learning & RailCommunicationsLifetimeAwardDevelopmentAchievementAwardMarketing&TeamAwardCivils/InfrastructureTeamAward Rail Engineer of the Year Rail Manager of the Year Rail Person of the Year Rail ProjectAwardManager Rail Team of the Year Safety Person or Team SamaritansAwardLifesaverAwardStationStaAward THE NEC, BIRMINGHAM // 24TH NOVEMBER 2022 Let’s recognise those who are outstanding, those that go above and beyond, those who are special. They need to know just how much they are appreciated.
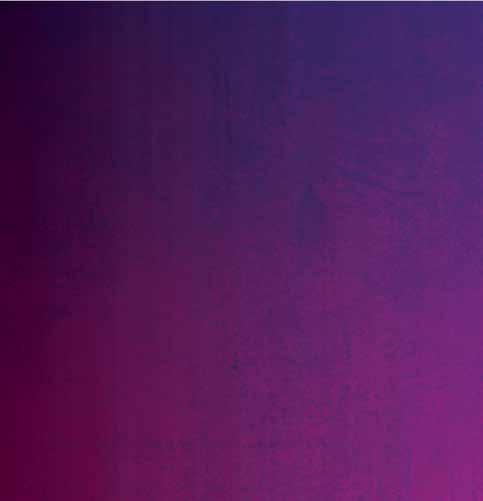

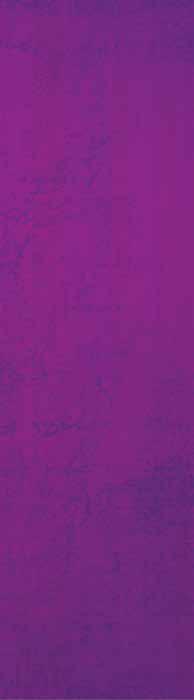
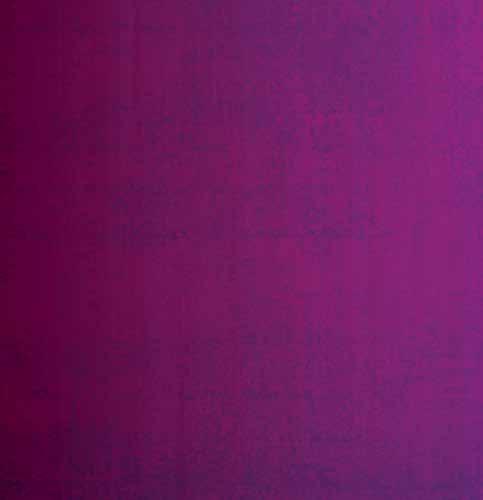
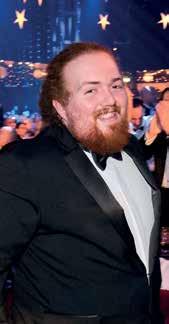
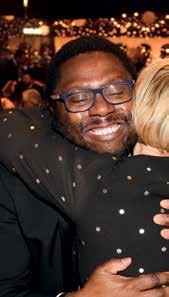
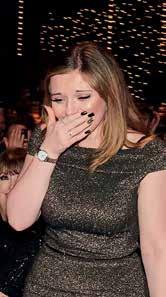

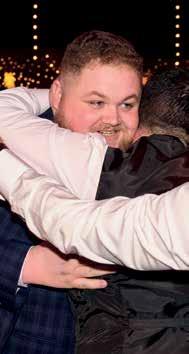


























Frank Foley concluded: “There will always be things that could have been done better or could be improved in retrospect. But all the teams and individuals involved in delivering the system can be truly proud of their contribution. We hope that our friends and colleagues now operating and maintaining the system are as proud of it as we are.”Stuart Mills, director of infrastructure for the Elizabeth line, who in a former role was responsible for the Jubilee line PSDs, is very pleased. Imagine this type of analysis for the 3780 sliding plug doors on the class 345 trains, a big opportunity!
CYSTEMSBARBER/CPCALEXIMAGE: DOBELLMALCOLMPHOTO: 64 Rail Engineer | Issue 197 | Jul-Aug 2022 STATIONS & PASSENGER TECHNOLOGIES
Solution in the data
out of use. Where it doesn’t work is if the PSD fails to a) open or b) close properly. In the case of a), the train door will still open and, in the case of b), the train cannot depart until someone has attended, encouraged the PSD to close, and has locked it out of use.
The systems integration team working on Crossrail, from consultants WSP and CPC systems, has been working on a data to information system for the PSDs. By design, PSD controllers and the SCADA system collect closing times and interlock alarms for all 27 PSDs on each platform face and this can be aggregated across the whole suite of 432 door pairs.
Having identified doors that might be getting to the edge of tolerance for reliable operation, the software alerts the issue to Knorr-Bremse and then maintainers are deployed to visit, and feedback what they find so that the software algorithms may be improved. Already some service-affecting failures have been prevented. As the software is optimised, one day the system might automatically issue work orders.
The software looks for trends. SCADA provides individual door alarms, but using lower-level trending of close times, the whole platform interlock signal is used. This always gives the slowest door to close but, at that stage, which of the 27 might not be known. If one close cycle is particularly bad (for example, if there is extra pressure in the tunnel from a nearby train) then SCADA alarms will highlight that door.
Thanks to Frank Foley formerly of Crossrail, and colleagues in CPC Systems for their assistance in producing this article.
Luke Church and Alex Barber from CPC Systems built an application that analyses this data, which is currently nearly 77,000 open/ close cycles per day but will more than double when 24 trains per hour services are introduced and Bond Street station opens.AlexBarber said “the data set required to monitor the PSDs was already present in existing signalling logs. The challenge was in shaping the data into useful information then making that insight integral to maintenance operations.”
Tottenham Court Road Westbound platform illustrating locked out PSD caused by trapped discarded plastic. Process diagram for door performance analysis.
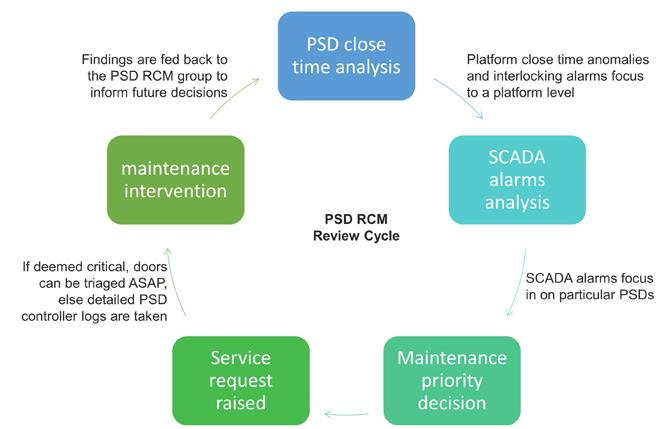
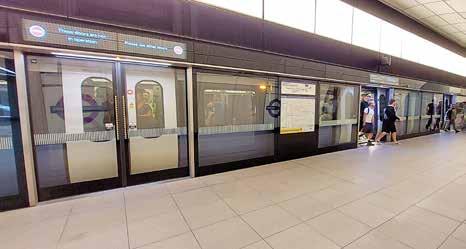
Merson Group provides technical rail sign design consultancy and the highest quality product, Transforming rail passenger journeys With over 850 signs manufactured and installed by Merson Group for the MTR Crossrail Elizabeth Line, including wayfinding and platform signs as well as illuminated totems and digital signs, our unrivalled rail signage expertise is ready to deliver for your next project. Speak to our rail signage experts and discover how Merson Group can work with you. Call: 01355 243 021 or Email: enquiries@mersongroup.com www.mersongroup.com

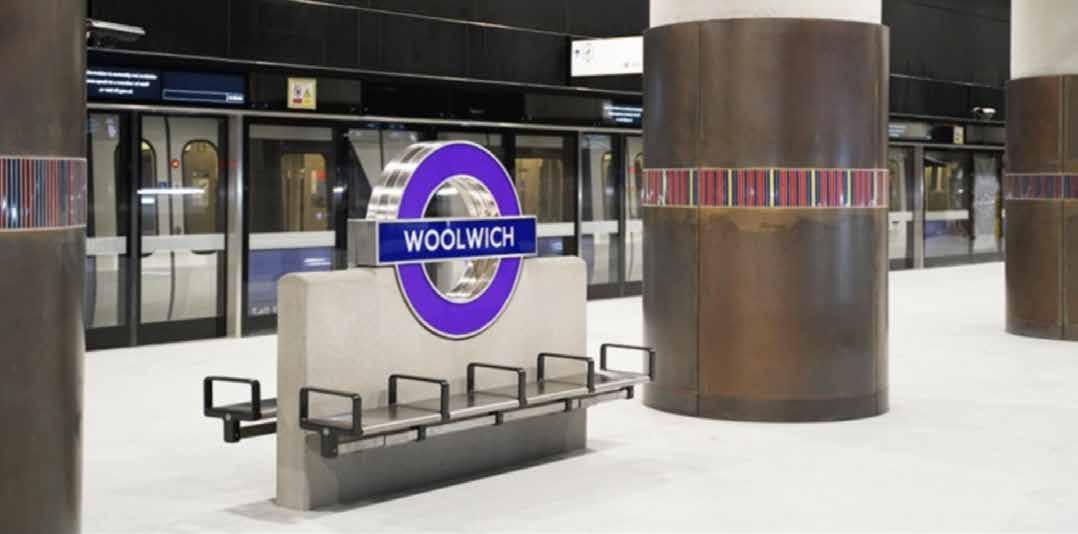
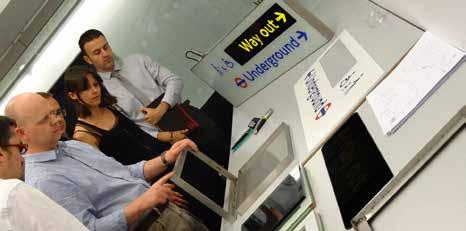

The new Elizabeth line opened to passengers on 24 May 2022, the culmination of a 13-year programme which has seen the construction of ten new stations and 42 kilometres of new tunnels through Central London. Transforming travel across London and the South East by dramatically improving transport links, cutting journey times and providing additional capacity, the line is initially operating as three separate railways, with services from Reading, Heathrow, and Shenfield connecting with the central section later this year.
Siemens Mobility has played a key role in delivering both the central section signalling and control system and the communication and station and central management systems for the new line on behalf of Crossrail Ltd. The company worked under two separate contracts, the first of which covered the design, manufacture, installation, and testing of the communicationsbased train control (CBTC) signalling and control system for the central section of the line. The CBTC system enables high-frequency and automated train operation, with much of the work under this contract carried out at the company’s engineering and manufacturing facility in Chippenham. In addition, Siemens Mobility in the UK led the design and installation of a host of systems that touch virtually every part of the railway. At its heart is the Siemens Mobility Digital Station Manager (DSM) system which features a fully integrated SCADA (Supervisory Control and Data Acquisition), and monitors and controls 21 subsystems, such as CCTV and platform screen doors. This covers safety systems and 40 equipment interfaces, such as lifts and escalators, across the entire central section including the Station Management
MobilityDELIVERING IMPROVED PERFORMANCE Rail Engineer | Issue 197 | Jul-Aug 2022 66 STATIONS & PASSENGER TECHNOLOGIES
Siemens
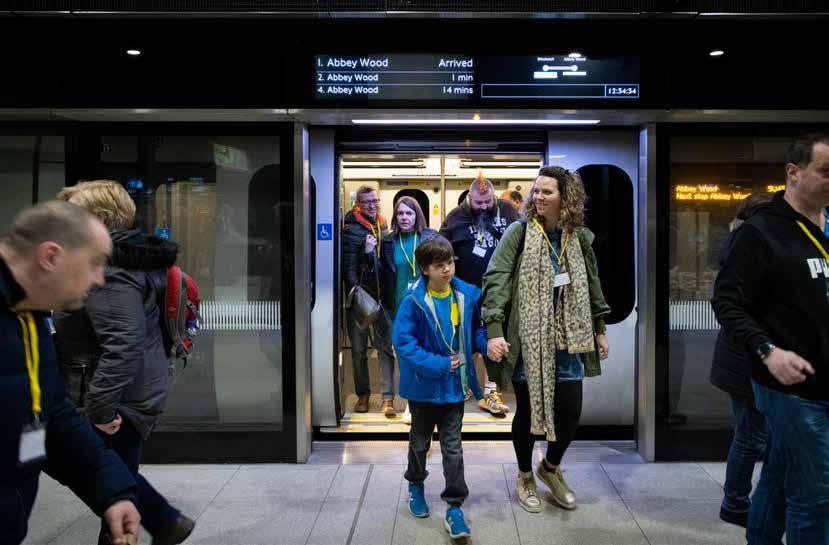
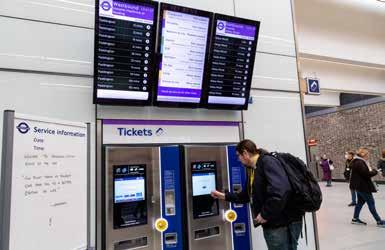
In addition, the Elizabeth line data and optical fibre networks, GSM-R, airwave and London Fire Brigade radio systems, and the DSM system are all carried through this network. The SCADA system also provides centralised control and monitoring of the traction power, overhead line equipment, high voltage power and platform screen doors. By pulling all the information into one place, the operator is able to manage the station network incredibly effectively, from the RCC. From this central location, they can identify and respond to emergencies, for example train or personnel incidents and alarms, and answer calls from help points, using the SCADA data and information to ensure the railway’s performance is Tooptimised.takeasimple example, when a passenger presses the help point to get some information, a telephone rings on the operator’s desk together with an indication appearing on their DSM screen showing that a phone call is being made and where it’s coming from. Once the operator answers the call, the station CCTV camera which points at the help point, starts recording and the image is played to the operator on a different screen. The operator can also easily navigate to the station layout map where the help point is located and provide further directions and information as requested. The system undertakes these integrated actions which simply triggered by the call being answered. Maintenance made easy For the maintainers, all the required health information from different systems and devices, regardless of their communication methods, are displayed within easy reach on a dedicated workstation within the RCC. This enables the maintainer to identify the exact device that has a fault, the type of fault, and send a maintenance ticket to the relevant team.
System. The information collected by the DSM is then presented to operators in the Route Control Centre (RCC) at Romford to monitor activity, offering unparalleled performance data.
Rail Engineer | Issue 197 | Jul-Aug 2022 67STATIONS & PASSENGER TECHNOLOGIES
Control and monitoring A fibre optic data network provides the backbone to the DSM, connecting some 60,000 communication and control assets, each with individual inputs and outputs. These devices range from simple circuit breakers to enormous tunnel fans and include CCTV, driver-only operation, public address/voice alarm (PA/VA) and customer information and telephony systems.
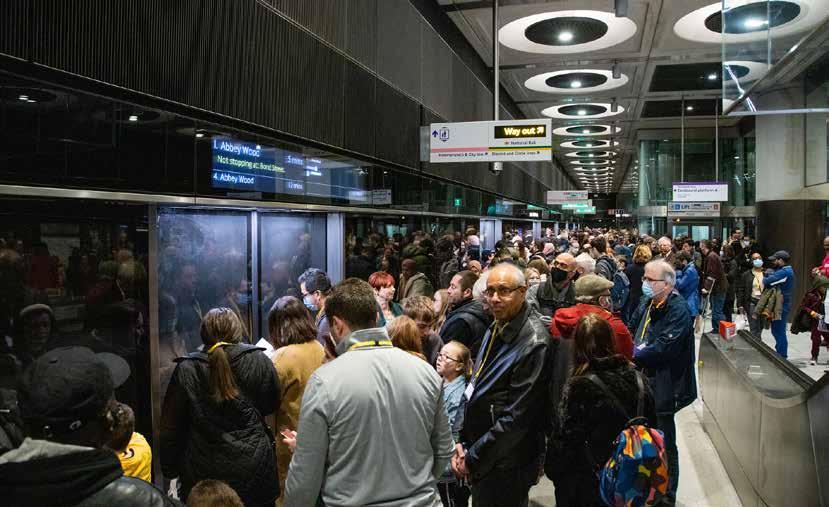
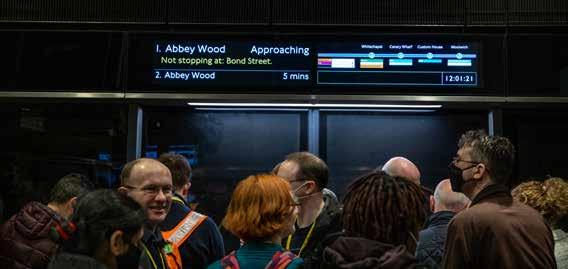
The PA speakers also represent a step change in technology, with acoustic engineers determining the optimum placement, and the speakers automatically adjusting depending on the ambient noise.
While the Elizabeth line is now open to passengers, Siemens Mobility’s work on a programme to provide station information and security systems (SISS) for the seven London Managed Stations is just beginning. Covering Blackfriars, Cannon Street, City Thameslink, Charing Cross, Guildford, Victoria, and Waterloo, the programme will set the template for a new approach in the provision of a SISS that is scalable and deployable for use in any sized station.Having delivered GRIP Stages 1 to 4, Siemens Mobility is now the principal contractor responsible for delivering Stages 5 to 8, with its teams now approaching the end of the detailed design phase. Work on site is scheduled to begin in September 2022, with a detailed programme being designed to keep passenger disruption to an absolute minimum. This will see assets migrated from the existing life-expired equipment to the modern replacement, with all seven stations being worked on at the same time. At the heart of the SISS will be the station data network, which will host Siemens Mobility’s DSM and customer information systems, together with PA/VA and CCTV systems. Although this is essentially an asset renewal scheme, much of the new equipment will bring significant benefits to operators and passengers. For example, the new customer information display screens at Blackfriars and City Thameslink will see the old LCD screens replaced with new TFT (thin-film transistor) technology. Similarly, at Charing Cross, LED panels will be replaced with RGB screens, bringing more flexibility for the operator and more clarity for the passenger, along with a reduced whole-life operational cost benefit. Improved performance The latest generation CCTV cameras will also be installed, with more than 700 new cameras to be deployed across five of the seven stations. The new cameras feature AI technology so, for instance, if a child is lost, the CCTV recordings can be scanned to find images of a child in a red top and blue jeans. The technology can also measure crowd density, a particularly helpful feature in the event of disruption, to manage overcrowding or to keep passenger numbers at a set level to maintain safe operations.
Across the Elizabeth line, London stations programme, and projects worldwide, DSM is delivering improved performance for passengers and operators alike, supporting improved, faster journeys, more efficient station operations, and increased capacity.
Before the Elizabeth line entered service, all operators were fully trained, with user manuals and floor walkers helping to make sure any issues were resolved quickly. Siemens Mobility is also providing maintenance support for the DSM system, 24 hours a day, 365 days a year. London managed stations
Rail Engineer | Issue 197 | Jul-Aug 2022 68 STATIONS & PASSENGER TECHNOLOGIES
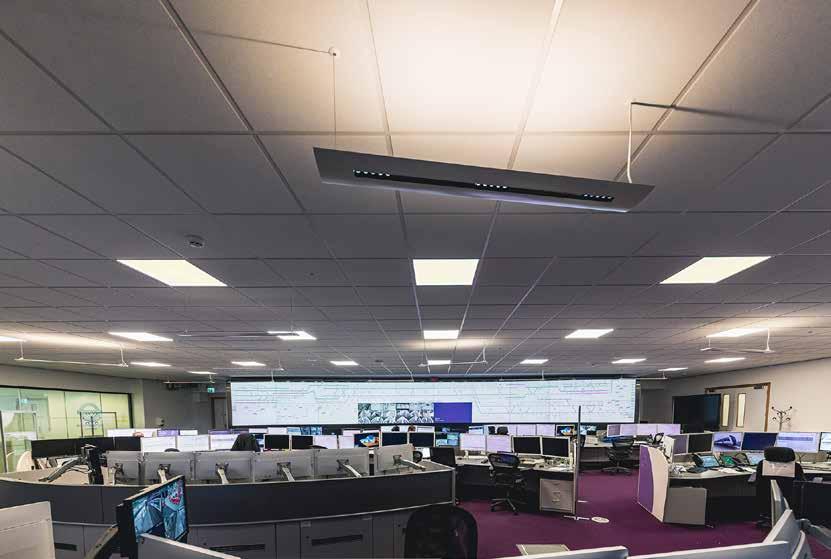
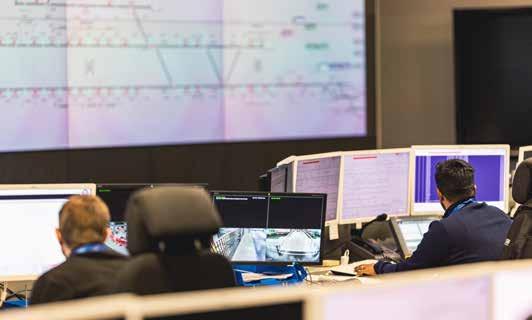
Anderton has an unrivalled reputation for manufacturing market-leading rail and structural precast concrete products. From troughing to signal bases, cable theft deterrents to ballast and king boards, Anderton has the solution. Along with our bespoke concrete offering, we’re the go-to provider of quality concrete products for the rail industry. Call 0333 234 3434 or visit www.andertonconcrete.co.uk £All inmanufacturedproductstheUK Full range of cost solutionseffectiveavailable
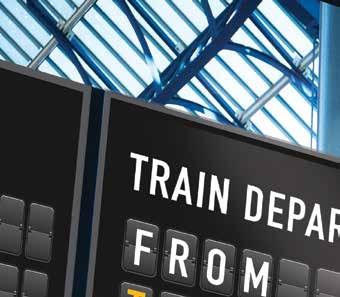


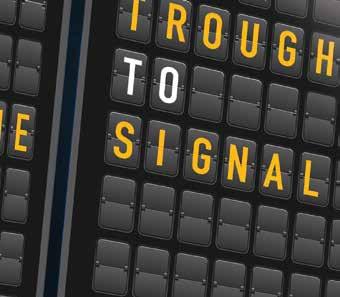
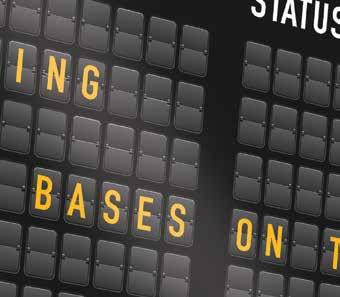

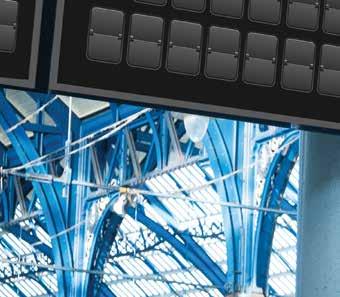
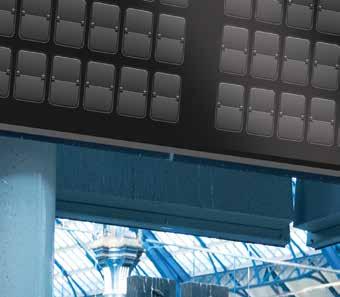

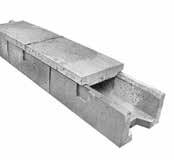


























The seminar’s chair, Rob Morris, who has been an engineer for all of his career and is currently the managing director for Rail Infrastructure at Siemens Mobility, offered a definition as ‘the ability to test and analyse systems in laboratory conditions’. As a broad statement, this seemed a good start, but adding to this the ability to see what would happen if changes are made and the concept of digital twins (of which more later) are certainly a bonus.
Digital’ is still the buzz word for the modernising of railways as indeed it is for many other industries. Yet, with all that is written about digital systems, what does it actually mean in practice? Many people would struggle to provide a fully understandable answer. A recent online seminar organised jointly by the IET and Siemens Mobility examined the issues and produced some surprising answers.
» East West Rail from Oxford to Cambridge, which will be part of developing the UK equivalent of Silicon Valley.
» The Levenmouth line in Scotland, to regenerate an area with high unemployment levels and little opportunities for work.
KESSELLCLIVE ‘ FEATURE70 Rail Engineer | Issue 197 | Jul-Aug 2022
The opportunity for simulating services, passenger behaviour, journey planning and suchlike are definite benefits. A recurrent theme of the seminar was that digital systems provide a much better platform for collaboration between partners and improved sharing of ideas. This is much more difficult to grasp as is the concept that digital systems should make things less expensive.So,what is the experience of people and organisations who have implemented digital systems? Some quite different thoughts and opinions emerged. An industry transformation? Getting people to work differently, especially engineers, is a major challenge. To help this, Melissa Zanocco OBE, the head of programmes at the Infrastructure Client Group, explained the vision that had emerged in April 2021. In this, the focus shifts from creating built environments to understanding the outcomes enabled by them. Two examples of rail projects which are in line with this thinking are:
IN THE REAL WORLD
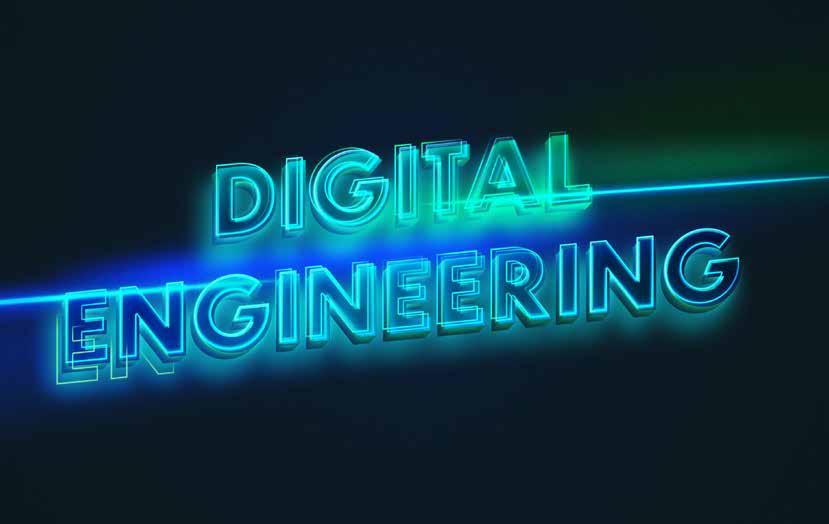
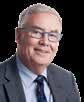

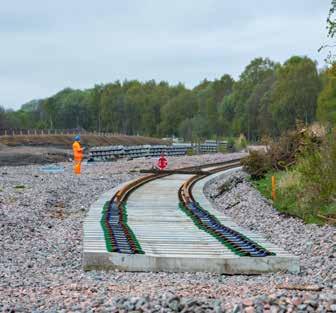
The Crossrail experience
The built systems provide the ability to offer up better services and improved integration, but the digital technology needs to be applied wisely to achieve the desired outcome. The route to be followed is Policy Strategy Action Vision. This is somewhat different to what many people would expect, in that it is the vision that delivers the end result.
One might reflect on all of this with the various methods that have been tried in the past – hub and spoke contracts; lead/main contractor in charge of sub-contractors; professional consultants in charge of contract teams; client control of a works programme. Pre-tender meetings often resulted in stony silences with the prospective contractors wary of giving away any perceived company advantages, technology developments, or even admissions of weakness. There is no doubt that change is necessary as engineering costs remain too high. A new mindset will however be required from many of the participating organisations.
The Elizabeth Line opened in a blaze of glory but, behind the publicity front, there remain some significant challenges still to come. In an excellent and honest appraisal of the project, Mark Wild, the former CEO of Crossrail, gave an insight into how digitalisation had impacted on the project and not always for the better. In terms of statistics, Crossrail is twice the size and twice the speed of traditional tube lines and can be likened to the German S Bahn and the Paris RER networks. The 30-metre depth of tunnelling proved to be very difficult as did some of the station construction integration to other underground lines. Critical to the seamless travel envisaged is the signalling (perhaps better Rail Engineer
The old method of progressing projects has always been: Consultant Client Contract Contractors. However, the new method being put forward is Owner Advisors Integrators Suppliers. This implies a whole new approach to procurement where sharing of technical and engineering knowledge will be required from the outset. In other words, transactional business models will be replaced by collaborative ones. Network Rail is reported to be using this methodology on the Trans Pennine upgrade.
» Need for Investment – 75% do not understand the need.
» Decision making – 86% are not equipped to make the right decisions.
| Issue 197 | Jul-AugFEATURE2022 71
Both of these projects are being delivered in accordance with the Project 13 delivery model which is an industry-led initiative to upgrade performance and focuses on achieving better outcomes for both people and the environment.
Project 13 aims to improve these weaknesses. Some of the changes needed will not sit comfortably with those who are used to the traditional way of doing business.
» Resilient organisation – 85% of industry does not possess this.
A cross-government change programme is in place with input from government departments, industry, and academia. From this has been created the Infrastructure Client Group that has many constituents including Network Rail, Transport for London, East – West Rail, and others, including non-rail industries. Drilling down further is the Digital Transformation Task Force (DTTG) with the three focuses of Strategy, Benchmarking, and Share / Adoption. In each of these, the use of existing expertise on Building Information Modelling (BIM) and Digital Twins techniques, will be a major element. Analysing the present understanding within industry of where the weaknesses are revealed considerable ignorance in many disciplines:
» Skills shortage – 53% do not understand the skills gap.
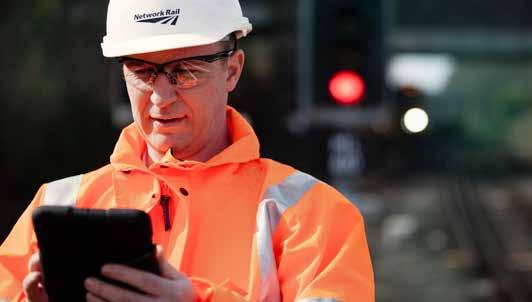
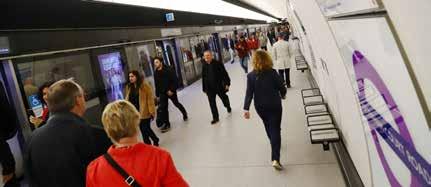
To give a scale of the data consumption, the SCADA system has around 60,000 inputs and outputs, monitoring all infrastructure conditions: power, ventilation, platform screen doors, fire protection, and many others. The line has a state-of-the-art customer information system, but this too has to interface to the other information systems at the five underground interchanges which in turn have had to be modified to provide Elizabeth Line information. All of this is a digital minefield, and it was the realisation of this back in 2018 that caused the project to be delayed another four years. Mark had to grapple with the problems of digital engineering when appointed to the job. He gave three key lessons that others should take note of for similar size major projects.
Starting again with what the operator actually needed should have been the concept. The technologists got carried away with offering things that were not necessary.
Modelling and simulation
Rail Engineer | Issue 197 | Jul-Aug 2022 FEATURE72
described as control and command) with a CBTC system in the centre section from Paddington to Abbey Wood, interfacing to ETCS out from Paddington to Heathrow and Reading, and to TPWS / AWS on the Great Eastern line out to Shenfield. These latter connections have still to happen but are programmed for later this year.
Third, be mindful of the need to produce value. Too many ‘gizmos’ were put forward that created bespoke engineering and would add little value. The aim must be to produce much more modularity so that standardised deliverables can be adopted at every possible location.Whenquestioned about the three signalling systems, Siemens commented that, with hindsight, using ETCS with ATO similar to that deployed on Thameslink would have been a better solution. However, at the time the decisions were being made, the ETCS ATO package was undeveloped and there was considerable doubt as to whether the system would have been able to offer the train throughput required. It remains to be seen how reliable the resulting interfaces will perform in everyday service.
First, adopt a concept of the minimum viable project. Crossrail had over specified requirements in that it had wanted everything to be available on day one. This overwhelmed the project and gradually a re-specifying of the digital requirements to a minimum level provided a realistic way forward Second, beware of promising outcomes for the operator. This caused over complexity in the rule book that no-one really understood.
An interesting presentation from Andy Woods of Siemens and Mick Vere of Graffica gave insight into the simulation being produced for the ETCS programme. Inputs to the modelling include train speeds, headways, braking distances, speed restrictions, and journey times,


| Issue 197 | Jul-AugFEATURE2022 73
attempts to create a digital representation of how a system will work but the development of modelling concepts is an ongoing exercise. For rail, it is all about taking the track and rolling stock components and interfacing these to the command-and-control system, viz the signalling. Managing functional complexity is part of the challenge and leads to the creation of what is called an ‘Abstract Architecture Layer’. Bringing all this together should lead to optimising the original design, which Graffica is working on with Siemens for the ECML project. Much is made nowadays of Digital Twins, the process by which modelling takes place on two separate digital platforms, with new ideas being developed on one platform and fed back into the other to see whether it will produce the expected benefits for the project. This is a continuing process and can extend forward even after the system has been commissioned when often a debugging exercise is needed when systems don’t perform as anticipated.
Rail Engineer
The ECML digital experience Reference to this project has already been made for which Siemens Mobility has the task of designing and supplying. An article on the ETCS provision was produced for Rail Engineer in Issue 189 (March/April 2021), following a discussion with the Network Rail programme manager. This suggested an eight to nine year timescale to complete and remove traditional lineside signals on the section from Kings Cross to Stoke Tunnel just south of Grantham. The project has progressed since then and Steph Neath, the BIM manager at Siemens Mobility explained some of the work being carried out to simplify the tasks that have to be undertaken.
all used to produce a model of how a route such as the East Coast Main Line (ECML) would function. It was admitted that ETCS on its own cannot deliver an optimum performance, as the impact of other trains on the route is not within the ETCS function. The addition of Traffic Management Systems (TMS) must be part of the overallDigitalsimulation.engineering

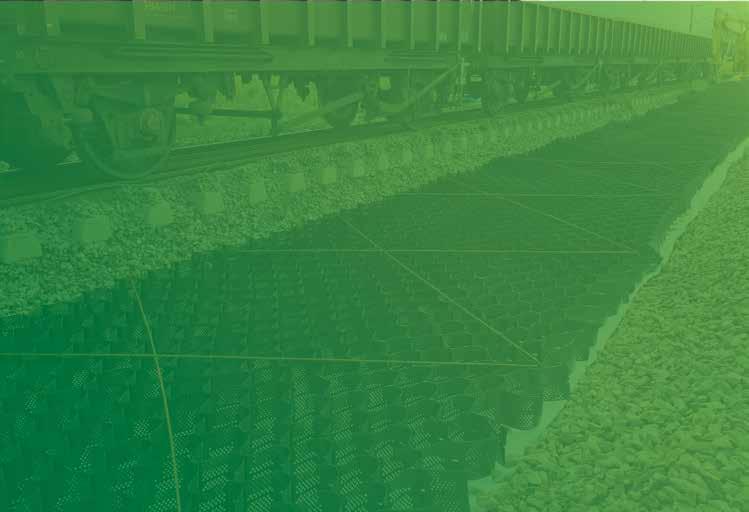
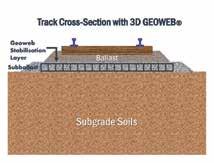
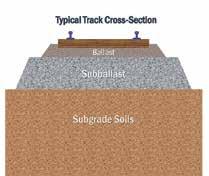

Rail Engineer | Issue 197 | Jul-Aug 2022 FEATURE74
Digital engineering services aim to unlock the value from the masses of centrally managed data that is being accumulated and to make this available on desktop or mobile devices for engineers doing the design and implementing equipment on site. The use of digital twins has been mentioned but this facility is being used in three different ways. Firstly, a project twin to create and model the asset; secondly, a connected twin to monitor asset operation and maintenance; and thirdly, a prospective twin to consider the eventual replacement or renewal of assets.Minimisation of site visits by undertaking digital survey work with the results directly transferred to the signalling design data is one benefit. Another is to produce 3D designs which lead to digital equipment sighting being used for digital rehearsals and works planning, and finally delivery and handover to the implementation teams including RAM assessments. Once commissioned, the data assembled will be used for real-time updates and assessments that can be given to passengers when disruptions or line possessions occur. The development of digital techniques is ongoing and will go hand-in-hand with the ECML project. However, a digital railway between Kings Cross and Grantham with no lineside signals is not expected until 2029, some seven years from now.
Final thoughts Whilst this online seminar gave real indications as to how digital technology can make projects easier to progress, the stated benefits of lowering costs and shortening timescales have still to be realised. Rail projects in general, and signalling projects in particular, seem to be taking much longer to fulfil than in times past. Little doubt that nowadays this is due in part to the myriad of regulations requiring certification and safety assessments to be in place. Can digital techniques assist with all this procedural overhead?Thedeclared intention of having ETCS fitted to all the UK main rail routes looks as far away as ever, with the risk that skilled staff will reach retirement age before many of these projects have even started. A rolling programme with a guaranteed continuity of work would seem to be called for, such that hard won digital expertise can be used to maximum benefit. What is also clear is that ETCS in itself will not produce the operational reliability that a digital railway needs. The whereabouts and timekeeping of trains is a vital ingredient and thus systems such as TMS and Connected Driver Advisory Systems (C-DAS) have all got to be integrated at the design and implementation stage, regardless of who is supplying the different piece parts. A question asked was whether, when using digital twins, people need railway knowledge or software expertise. The answer is both, and the lessons from Crossrail should be heeded by all.
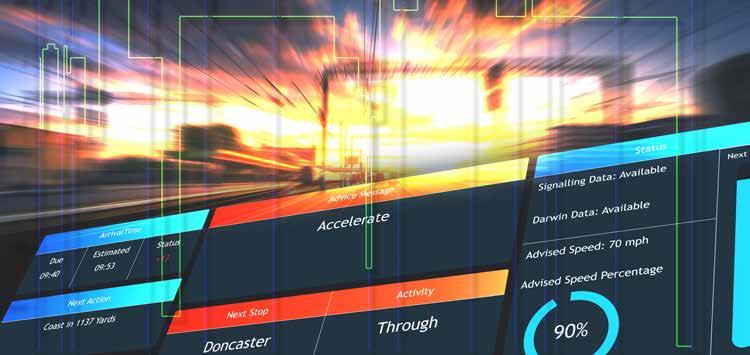

Quality precast concreteForformanufacturers...concreteagreatrangeandevengreatervaluemoreinformationonElitequalityproductsphone01952588885orbrowsewww.eliteprecast.co.ukElitePrecastConcreteareoneoftheUK’sleadingprecastconcretemanufacturerscombiningthehighestlevelsofcustomerservicewithalwaysbeingthebestvalueoption.Ourfocusisondrivingdownthecostbaseandthenpassingthesesavingsontoourcustomers.Thisenablesustoprovideconstantandpredictablepricestructureswhichinturnunderpinourethosofdevelopingcustomerrelationshipsoverthelongterm.Everyproductwemakeiscastfromthesamepremiumquality,highstrength(50N/mm2)concrete.Wewerealsothefirstandbyfarthelargestmanufacturerofinterlockingblocksforvarioustemporaryworks;firebreaks;retaining,blastandpushwallsandalso,byofferingthreeblocktypes,youcanbecertainthatwehavethesolutionyouarelookingfor.
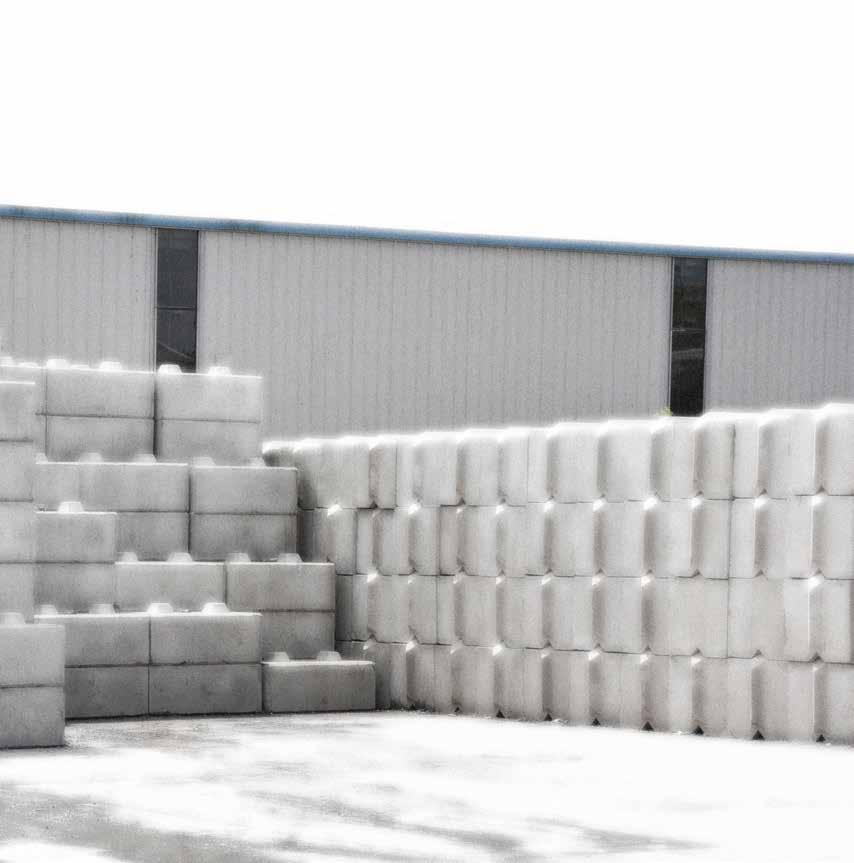

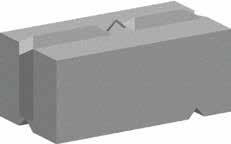
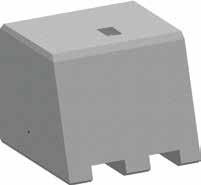
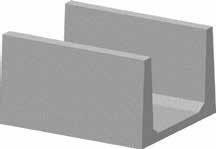
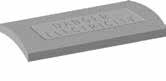
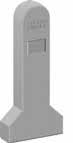

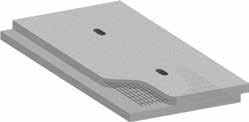
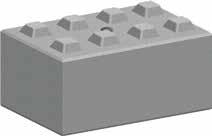
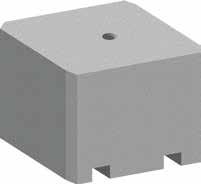

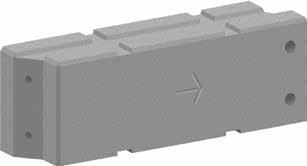








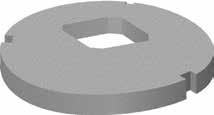









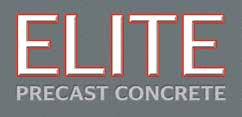
» Corrosion protection after 30 years.
The two-track bridge was built between 1911 and 1913 to cross the Kiel Canal and has a total length of 2,486 metres. Sekisui Chemical GmbH, based in Düsseldorf, received the order to process and deliver 8,600 bridge sleepers made of FFU synthetic wood. The sleepers are 260cm long, 24cm wide, and vary in height between 24cm and 28cm. A particular requirement of the cross sleepers is the deflection of railway loads via an offset of up to 50cm between the rail and the steel bridge longitudinal beam. Furthermore, the continuously welded track does not have any expansion joints. Track renewal on the bridge is scheduled to start in 2023. This is not the first time that DB AG has selected FFU sleepers for use on a rail bridge. In 2017, it built the Haus-KnippBridge which crosses the Rhine at Baerl, near Duisberg. With a total length of 767 metres, 1,624 FFU sleepers of various dimensions were installed on one track. In 2020-2021 DB AG also installed FFU railway sleepers on the Herrenkrug Bridge which spans the Elbe in spansinstalledof2,400Magdeburg-Herrenkrug.sleeperswithdimensionsw/h/l=24/22/260cmwereonthebridge,which680metres.
» Steel construction after 50 years.
Benefits for bridges
FFU synthetic wood can be used on railway bridges in exactly the same way as conventional, natural wood timbers. However, the use of FFU comes with additional engineering and environmental benefits.Oneproperty, which prompted Vienna’s public transport authority, Wiener Linien, to become an early adopter of FFU synthetic wood, is its maintenanceextendedintervals which include:
» Rail renewal after 30 years.
» Renewal of FFU bridge timbers after 50 years.
In 2022, Deutsche Bahn AG (DB AG) selected Fibrereinforced foamed urethane (FFU) synthetic sleeper technology for a track renewal on the Rendsburg High Bridge in Germany’s northern state of Schleswig-Holstein.
FEATURE76 Rail Engineer | Issue 197 | Jul-Aug 2022

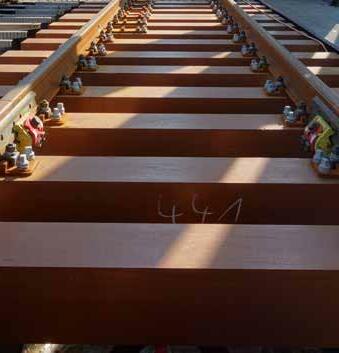
Shapes and sizes Germany’s Federal Railways Office and Switzerland’s Federal Transport Office granted approval for the use of flat FFU sleepers in 2017 and 2019 respectively. In close cooperation with employees of Deutsche Bahn, it was discovered that there are always pressure points requiring very cost-intensive maintenance. This is especially so where the construction height of the ballast under the conventional sleepers is too low, or where the engineering structure above or below the track restricts the railway’s headroom.In2012,Germany’s Bochum-Gelsenkirchen, Straßenbahn AG (Bogestra) built a set of points with 10cm high synthetic wood sleepers on a ballast bed. Sleepers with a constructive height of 12cm are being used on a Deutsche Bahn track in the Hanover area that carries 100,000 tonnes a day. The Rhaetian Railway in Switzerland has been fitting 12cm high sleepers to bridge structures sinceSince2014.2008, Wiener Linien has been regularly installing FFU sleepers with a construction height of 10cm with direct fixing, for example, on the track of the Route 31 tram on the Floridsdorfer bridge. A total of 1,600m of track was laid using this technology.
As a large part of the Vienna underground network is equipped with polyurethane sleepers dating from the 1970s and 1980s, and which have now reached their life expectancy, a long-term programme is currently in place to exchange these sleepers for FFU synthetic wood sleepers, both on solid trackway or on heavy and light mass-spring systems in tunnel locations.
Longitudinal beams in railway bridges are regularly used in the UK and Ireland. The dimensions of these longitudinal FFU beams were up to 16,000cm length, 700cm width, and 510cmBi-blockheight.sleepers with this technology have also been created and installed. The first solid track tunnel project was equipped with this as long ago as 1980.
FFU goes large
FEATURE 77 Rail Engineer | Issue 197 | Jul-Aug 2022
These specifications mean that railway operators need only implement long track closures once every 50 years, reducing significant disruption to railway operations.

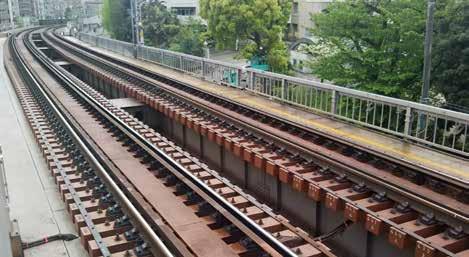
Safety on the tracks
On the Deutsche Bahn network, the life cycle cost analysis (LCC) of rail bridges is largely concerned with bridge timbers fastened directly to exposed steel bridge beams.
» For long (remaining) lifetimes of the bridge, there is a high potential saving from using FFU sleepers.
The results of these economic efficiency calculations can be summarised as follows:
FFU synthetic wood sleepers have been successfully used in continuous operation on rail networks for over 41 years. Its patented manufacturing technique guarantees the highest level of safety and reliability in daily use on railway tracks. In many countries across the world, FFU synthetic wood has set the standard for synthetic railway sleepers on bridges and S&C.
FEATURE78 Rail Engineer | Issue 197 | Jul-Aug 2022
The base scenario shows a cost saving for FFU sleepers if the remaining lifetime of the bridge exceeds the lifetime of the wooden sleepers. The return on investment of the FFU sleepers is about double that of the wooden sleepers. In other words, even if wooden sleepers are only be replaced once, FFU sleepers are the more economical option. The lifetime of wooden bridge timbers will be considerably reduced now that bans have been enforced on the use of certain impregnation materials.
For example, on 31 July 2021, a 2013 EU-wide creosote ban, came into force. Research into the reduced lifetime of wooden sleepers − LCC Bridge Sleepers - Economic Assessment of FFU Bridge Sleepers in Sweden (2019) − shows that the return on investment for FFU sleepers is about three times as high as that for wooden sleepers.
» If the (remaining) life expectancy of the bridge beams exceeds that of the wooden sleeper by even one year, then it is economically expedient to use FFU sleepers.
Experience with a wide variety of synthetic sleepers has shown that the various technologies differ considerably in terms of quality, technical characteristics, and behaviour of the materials used. For this reason, by classifying the materials into types, specialists from rail networks in many countries have presented these differences in a manner that is practical for the ISO Standard 12856-1:2014 for synthetic sleepers.Asthose responsible for the rail networks are aware, these differences are evident when it comes to procurement and, much more importantly, when it comes to the safety of daily rail operations, technical longevity, reliability, therefore, the availability of the track systems.
Life cycle cost analysis
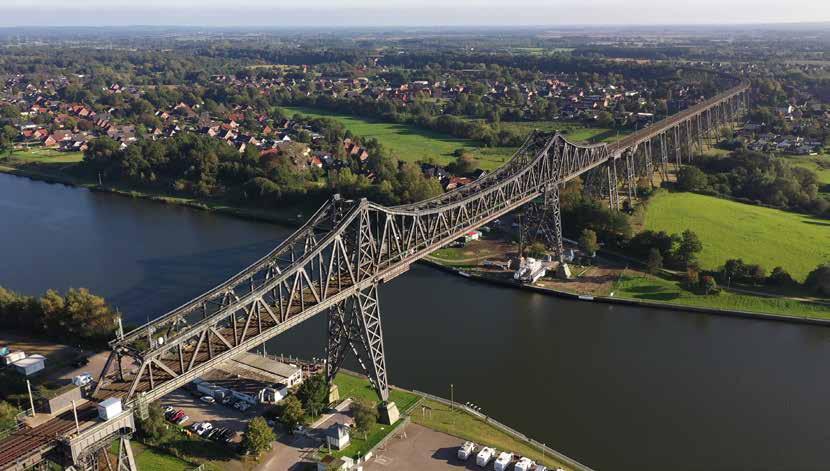
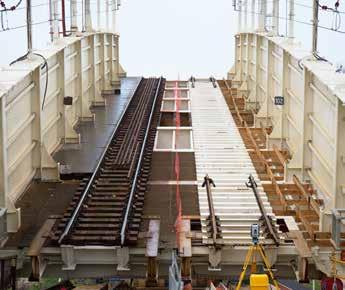
Since 1985 we have installed more than 1,550 km of track 1.7 billion load tonnes | equivalent of 50 years use Application: Ballast, Slab Track, Steel Construction and Direct Fastening Can carry Axle loads of up to 65 tons Use on High Speed Rail up to 300 km/h Maintains long term track geometry Contact with ballast similar to timber sleepers Workable properties like timber sleepers ofStatethe Art RAILWAY TECHNOLOGY SEKISUI CHEMICAL GmbH Patrick Childs | T: E-Mail:+44-(0)796-6598055childs@sekisui.dewww.sekisui-rail.com INNOTRANS 20.9 – 23.9.2022 Hall 25, Stand 110 SleeperSynthetic Simply working & sustainable
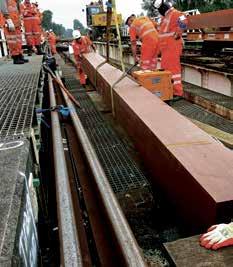
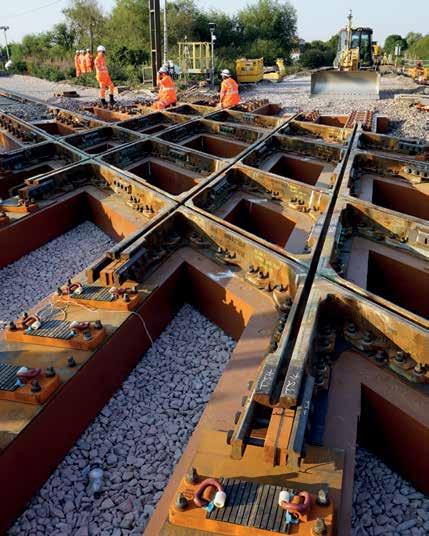

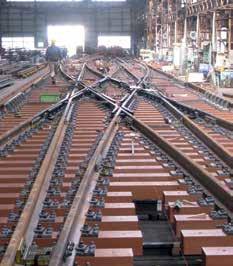

Timetable planning is not easy. It has to cater for a variety of factors and has to be an acceptable compromise for the many stakeholders and customers of the railway. The factors involved in timetable planning include speed limits, which vary across the network depending on points and bends in the track, and with only one train occupying a given section of track at any time. Signalling infrastructure varies across the network and what is a safe distance between trains at one part of the route can differ at another part.
Arailway is very much a system of systems, with track, structures, earthworks, telecoms, signalling, electrical power, and rolling stock all having vital roles to ensure an effective service is provided for all customers. Good people are obviously at the heart of the railway, but a vital system is an effective timetable.
There has to be a minimum time gap between trains using the same platform at a station, which can vary depending on the type of train and how busy the trains are in terms of passengers leaving and joining the train. Stopping, non-stopping, and freight trains all travel at different speeds, so a mix of these trains on the same route affects the number of trains that can use the route. Electric, diesel, (and steam), passenger, and freight trains all have different performance characteristics and changing the type of train will affect the timetable.
Keeping moving Trains run more efficiently and use less energy when they keep moving, so we don’t want trains on more than one route arriving at a junction at the same time. Trains can’t be scheduled to run too closely together, because flexibility is needed if there is an incident in order to get trains back on time. Trains need to be taken out of the network for maintenance and re fuelling, so at the end of a timetable path they ideally need to be near to a maintenance depot.
DARLINGTONPAUL
TIMETABLING at the heart of every railway
FEATURE80 Rail Engineer | Issue 197 | Jul-Aug 2022
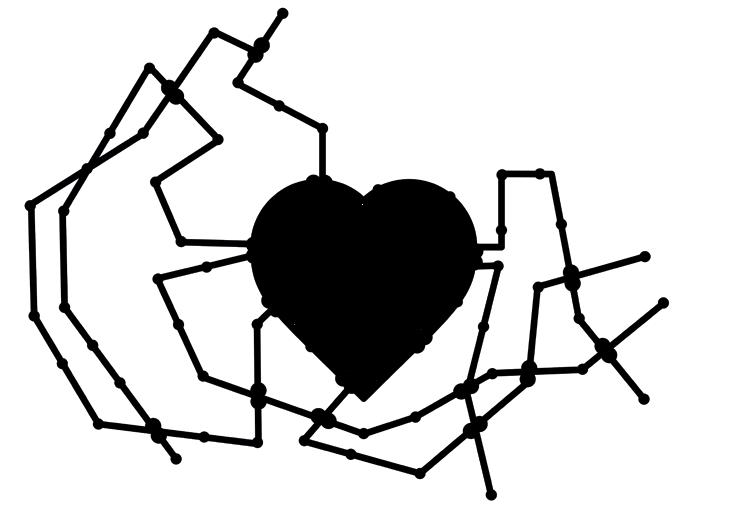

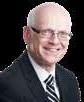

The risks first emerged in delays to the planning and delivery of the North West Electrification Programme, combined with late changes to the scope of the Thameslink Programme, compressing the time available to develop the timetable and then further compressing the time left available for train operating companies to prepare for the implementation of new services.
FEATURE 81 Rail Engineer | Issue 197 | Jul-Aug 2022
the changes were intended to deliver around 70% of the capacity benefits of the Thameslink Programme, and to facilitate ‘tube-like’ service frequencies, with trains every two or three minutes. The scale of investment and complexity of introducing new services meant that the change planned for May 2018 was unprecedented in scale. It would have complex effects across multiple franchises and very large portions of the national rail network. It involved 42,300 individual changes, affecting 46% of all passenger services and the timetable change of May 2018 was around four times the scale of a typical six-monthly timetable change. The inquiry found that different projects and processes were inter-dependent, which meant that risks and delays arising in one area were quickly passed to others.
May 2018 In the autumn of 2017, as the North West electrification schemes fell behind schedule, a high-risk decision was taken to catch up the work over Christmas 2017 and, around the same time, a decision was taken to re-plan the introduction of the new Thameslink services. The Christmas works were not completed, and the re-planning of the Thameslink services proved to be more complex than expected. The timetable process began to fail because the volume of changes required was too great and late in the timetable development programme to be reasonably manageable. The scale and impact of the problems came to a head with the introduction of the May 2018 timetable. In the following ‘Failing to plan is the same as planning to fail, this commonly used expression is no better expressed in the rail timetable plan. The timetable is the glue which holds the structure of train operations together. If the running time data is incorrect or the train planning margins are not calculated accurately then the plan starts to fall apart. Several big lessons have been learnt in recent years on how a timetable should be planned accurately and use of technology is becoming a much bigger tool in the development of an accurate timetable plan.’
Time for project work to increase capacity, and routine maintenance to keep the network running reliably, also needs to be planned in. Customers want to avoid changing trains and to get to their destination quickly and reliably, so there has to be a compromise of stopping and nonstopping trains on any route. To some, a timetable may appear to be just a list of times at different locations or lines on a graph. But these are people and goods, and represent the value of rail to society. The timetable is the product and promise that rail delivers to its customers, and the sum of the whole railway system distilled into times and locations. It is also the result of a set of operator and stakeholder requirements taking into account what the network system is capable of delivering. It’s what train performance is measured against, which is important to engaging with and providing customer satisfaction and attracting more customers.Thetimetable is also a tool, with evidence benefits, disbenefits, and trade-offs, and is formed from meaningful discussions with funders and stakeholders. It’s the reason many investment projects are funded and delivered to provide an enhanced reliable product, or a new high-performance product for customers. Timetable and performance modelling is key to understanding, quantifying, evidencing, and assuring that the benefits for customers of any project are delivered.
The risk of change A new timetable is a change, and any change is a risk. If not implemented correctly and not taking into account all the factors involved, a timetable change can be a major issue. This was the case in May 2018, when a new timetable was introduced for large parts of the rail network. This caused major disruption to services for customers, especially in the North of England and in the South East. The subsequent inquiry found that there were systemic weaknesses in the planning and delivery of the new timetable.
Andy Pepworth, Capacity Planning Manager, D2 Rail
The May 2018 timetable followed major investment in large infrastructure projects and delivery of new rolling stock to introduce thousands of new services. In the North of England, brand new trains, including more than 500 new carriages, with room for 40,000 extra passengers and more than 2,800 extra services a week were planned. In London and the South,
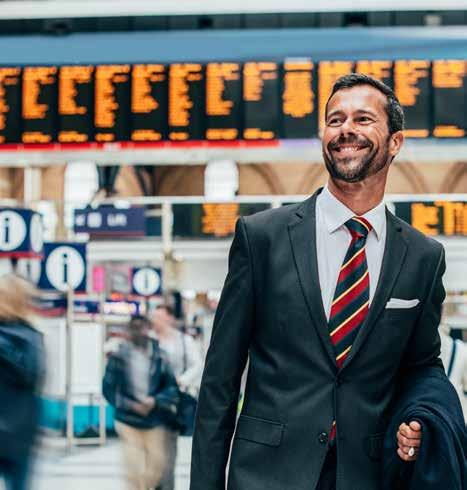
Enhancements
weeks, Govia Thameslink Railway (GTR) the operator covering much of London and the South, failed to run about 470 (12%) of its planned daily services.
Signalling, line speeds, type of train, train length, and stopping patterns all form the foundation of the timetable, which also has to take into account the Sectional Running Times (SRT), the time taken for a particular train to traverse a network link. The headway is the minimum time interval between two successive train schedules at a specific timing point on the same line in the same direction. A junction margin is the minimum permissible time interval between two trains that are performing conflicting moves at a timing point. Both the headway and junction margin have to be such that the second train on the route can also meet its SRT. To make things even more complicated; operator service requirements, passenger dwell times, train crew rules, train loop lengths, platform lengths, turnaround times, engineering allowances, and train gauge all have to be carefully considered and taken into account when developing a new timetable.
FEATURE82 Rail Engineer | Issue 197 | Jul-Aug 2022
Douglas explained that the timetable is the core product rail provides to its customers and the quality of the timetable will be one of the reasons customers choose rail over other modes of transport.
Much has been learned and put in place to improve timetable planning as a result of the May 2018 timetable “fiasco” − as Sir Peter Hendy has described it − including the proposed creation of Great British Railways. However, with new managers joining the industry all the time and new innovative and creative processes being introduced (which are vital for the future of the industry) it is important that the lessons learned from the May 2018 timetable incident are not forgotten.
The inquiry found that failures to identify these risks and properly manage them were attributable to Network Rail, train operators, the Department for Transport (DfT), and the Office of Rail and Road (ORR). It found Network Rail was in the best position to understand and manage the risks, but did not take sufficient action. Neither train operator Northern or GTR were properly aware of or prepared for the problems in delivering the timetable.
Timetable foundation Douglas Rarity, programme manager strategy and investment, Network Rail recently gave a presentation to the IRSE in Scotland called ‘Timetable Led Project Development and Benefits Realisation’.
For any track or signalling project enhancement, the timetable is the output, benefit point, and ultimate product. The enhancement should ideally be planned when it is necessary to renew track, signalling (and traction current supply if applicable) due to asset condition. The development of the enhancement should start with the timetable output, which must remain a constant thread and a benefit checker throughout the project lifecycle. If it is not necessary to renew the track and signalling then a timetable solution by changing some of the other factors involved with the timetable should be first evaluated.Enhancements can also be made to rolling stock, such as the increase in top speed from 100mph to 110mph on the Siemens Desiro EMUs running out of Euston which allowed an additional path in the timetable on the fast lines. Electrification also offers significant benefits by, for example, providing more powerful electric trains which reduce the performance differential between passenger and freight services. In Scotland, a key justification for electrifying the line to Stirling was to avoid Stirlingbound diesel trains delaying electric Edinburgh to Glasgow trains. Multiple timetable scenarios based on a train service requirement which isn’t possible with the current infrastructure, rolling stock, or both, should be evaluated. These scenarios can then be used to deliver the train service requirement resiliently, which is important. This can then be used to quantify and demonstrate the benefits to customers, in terms of journey times and number of trains paths, and to facilitate working with customers to identify ‘tradeoffs’ early in the development.
Arriva Rail North, which operated rail services across the whole of the north of England, failed to run approximately 310 (11%) of its planned 2,810 services per weekday.
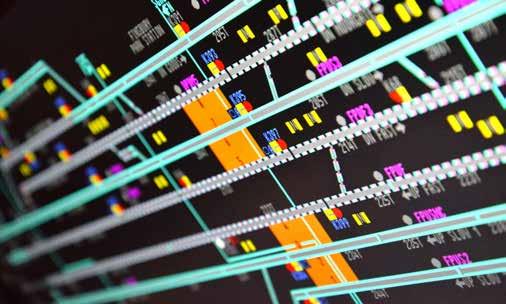

• Interactive graphs, timetables and diagrams • Digital train requirementservicechecking • Conflict detection
Timetable led development case study In conjunction with Project Acceleration in a Controlled Environment (PACE), good timetable development allows the initial work to be delivered quickly in order to inform infrastructure requirements before design work commences. It also prevents multiple infrastructure interventions from being superfluously designed, and enables an assurance process to check the various enhancement work types will work together as a system to deliver the outputs and benefits of an overall enhancement project.
against train
Douglas explained a case study for timetable and infrastructure developments for the Aberdeen to Central Belt in Scotland. The challenge was to reduce inter-city express journey times from Aberdeen to/from Edinburgh by 20 minutes, Glasgow by nine minutes, and Dundee by three minutes, together with additional stopping passenger train and freight trains, and with improved connectivity for customers at stations between Dundee and Aberdeen.
ATTUneSystemistransforming
The results of the timetable modelling were the identification of a number of proposed signalling enhancements,
Working collaboratively with all the operators concerned, four timetables were created to identify where timetables worked and didn’t work, along with identifying the evidence why they didn’t meet the service specification, and to identify the required performance resilience enhancements. This took into account the journey opportunities per hour, connection times, freight paths per hour including the length of freight trains, and journey times.
The UK’s Leading Timetabling and Diagramming
Wide industry compatibility with open data support for PIF, CIF, SPG and Diagram Exchange timetable import and export.
• Fully integrated timing and vehicle diagramming • Validate
This also allows output-based decisions to be made on the engineering interventions to take forward, in conjunction with market data to determine the appropriate level of enhancement.
Service interaction and connections at Dundee to take into account stopping and non-stopping trains was another challenge; together with trains terminating and starting their journeys at the station.
Instantaneous timetable validation against train service requirements enables reliable fulfilment of stakeholder needs.
the design and delivery of timetables, both in the UK and around the world. By detecting conflicts and validating services against planning rules it is helping train operators deliver a better, more reliable product for customers. schedules planning rules between services
Talk to our team to arrange a demonstration or a free trial.
FEATURE 83 Rail Engineer | Issue 197 | Jul-Aug 2022
Automatic conflict detection based on trains routed through a digital network model, capable of checking 100,000+ trains as you make changes in real-time.
Holistic, integrated timetabling thanks to an automatic daily import and validation of every train operating across the UK rail network. Easy-to-use drag-and-drop vehicle diagramming which automatically updates when your timetable changes, delivering huge planning e ciencies.
Evidencing the reason why asset enhancements are required, where and how they will work together, and exploring the options between different timetables to reach the best engineering solution that can be implemented. It may also be that a case can be made to demonstrate an engineering enhancement is not required, by challenging perceptions and assumptions to ensure the best value and maximum benefit is delivered, by identifying when and where something is needed.
bellvedi.com info@bellvedi.com
Average journey times of 62mph for passenger trains compared to 39mph for freight trains presented an overtaking challenge and a requirement to ensure adequate passing loops were provided.
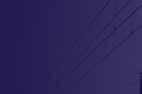
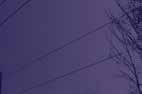

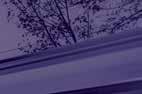


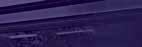
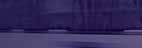

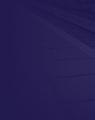

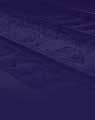
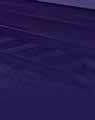
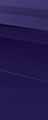



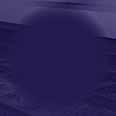

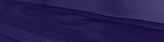
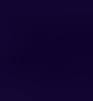
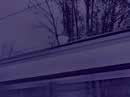

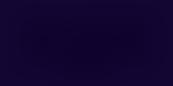


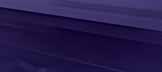





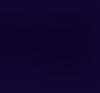
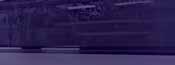


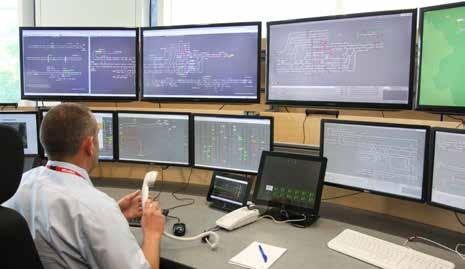
An important long-term strategic priority is the transition to the target end state − an integrated set of compatible planning applications and processes (the integrated system).Implementation will require significant effort and commitment by the whole industry. Change cannot be delivered without ongoing collaboration and transparent cooperation, and an industry timetable portfolio board has been established to provide pan-industry leadership of this major change.
The amount of changes now being made as a result of investment in infrastructure, rolling stock, and new services can create challenges, as was the case highlighted by the disruption in May 2018.
The industry has responded to the Covid-19 pandemic by making four major timetable changes, re-planned the December 2020 timetable, and seen a significant increase in short term/weekly timetable changes, using the existing technology. However, more integrated and intelligent technology will support the industry to quickly and accurately deliver significant timetable changes, as well as help to manage risks that may arise during theSeveralprocess.new strategic priorities have been identified, including the utilisation of current technologies through to introducing automated conflict detection functionality.
Rail Engineer would like to thank Douglas Rarity for his help and assistance with this article.
Completion of the early development timetable-led accelerated internal development for the project has been much faster than historic norms (circa 15 months against historic norms of up to 48 months) and the cost of work done to date is less than 2% of anticipated final cost against a benchmark of 10%. The project has also been part of a whole line of route approach, considering the way to minimise disruption to passengers and freight. This has generated efficiencies from shared survey work and creates a major opportunity for potential scope and delivery efficiencies from incremental benefits, shared resources, and minimised disruptive access.Next steps for the project will be to work collaboratively with ScotRail to better understand the effect of the proposed loops and to look at an all-day 2026 timetable with LNER services and current freight as well as passenger services in the Central Belt. The Scottish government has set a target to decarbonise domestic passenger rail services by 2035 and the Aberdeen to Central Route by 2030. The modelling only considered a diesel railway, so both a diesel and fully-electrified timetable will be evaluated to compare infrastructure requirements and service provision.Scottishgovernment policy is to also encourage more freight off the road and on to the railway, lowering carbon emissions, driving economic growth and easing congestion. The 2026 enhancement will deliver additional opportunities for freight services to run, but the planned 2026 enhancement must also enable the likely growth in the freight market and the impact of any subsequent electrification of the line.
The project outputs and costs also need to be proportionate to reflect changes to passenger behaviours and levels of demand post Covid-19, whilst meeting political priorities and anticipating future recovery.
FEATURE84 Rail Engineer | Issue 197 | Jul-Aug 2022
Industry Timetable Technical Strategy
Unintegrated timetable technology that requires high levels of manual intervention is still widely used. Although there has been progress in technology, the developments have not been coordinated across the industry as part of an integrated system. This means timetable production is often slow and published timetables contain conflicts that can affect train performance.
freight loops, and other infrastructure enhancements, including additional platforms, bi-directional signalling and a junction reconfiguration at Aberdeen, freight gauging, and some platform extensions at other stations. This resulted in a plan to improve journey times to/from Aberdeen, with potential additional benefits to customers north of Aberdeen; improve connectivity for North East passengers with barriers of through travel on the corridor removed; additional passenger services providing additional travel options and flexibility for customers; additional freight services with the potential for the South Aberdeen Harbour development; and improve through service provision with additional pathing at Aberdeen for through services, together with new station provision south of Aberdeen. The modelling also provided input into Nestrans. This is the Transport Partnership for Aberdeen City and Shire, the purpose of which is to develop and deliver a long-term regional transport strategy and take forward strategic transport improvements in the area.
The Industry Timetable Technical Strategy sets out how the industry will get more out of new technology to produce timetables.
Benefits to date and next steps


Operational Planning – Strategic Planning – Project Design Support – Performance Analysis www.d2rail.co.uk Planning your vision, delivering your promise D2 Rail provides timetable, operational, and capacity planning consultancy to support the development of projects and operational strategies. • Timetable Development • Strategic Planning • Operational Modelling • Performance Analysis • Signal Design Support • Rail Operations Advice • Feasibility Studies • Automated Schedule 4 Cost EstimatesWhether it is timetable development, performance modelling, signal design support, or expert operational advice, D2 Rail offers a unique blend of experience and bespoke software solutions. D2 Rail is working on some of the largest rail projects in the UK and internationally, supporting the design development process along with operators and infrastructure providers. Call 0161 258 7534 or email info@d2rail.co.uk to find out more. D2 RAIL | 1 RIDGEFIELD, 16 – 18 KING STREET, MANCHESTER, M2 6AG Capacity Planning - Strategic Planning - Project Design Support - Performance Analysis
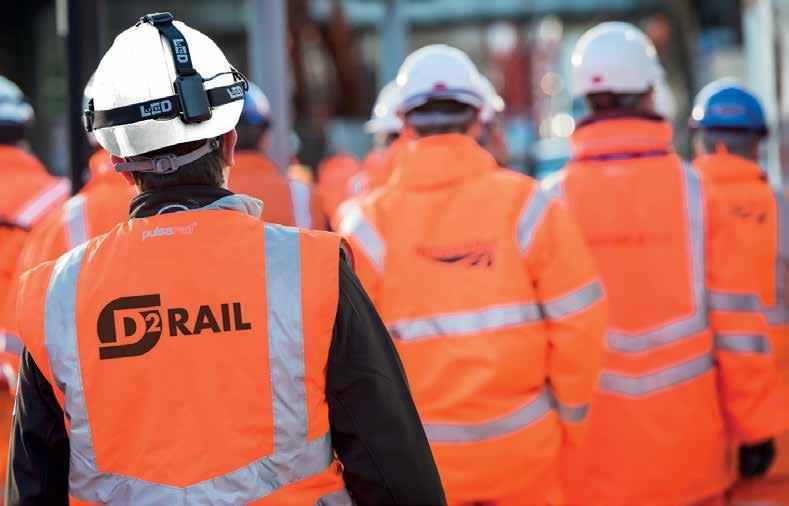
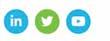
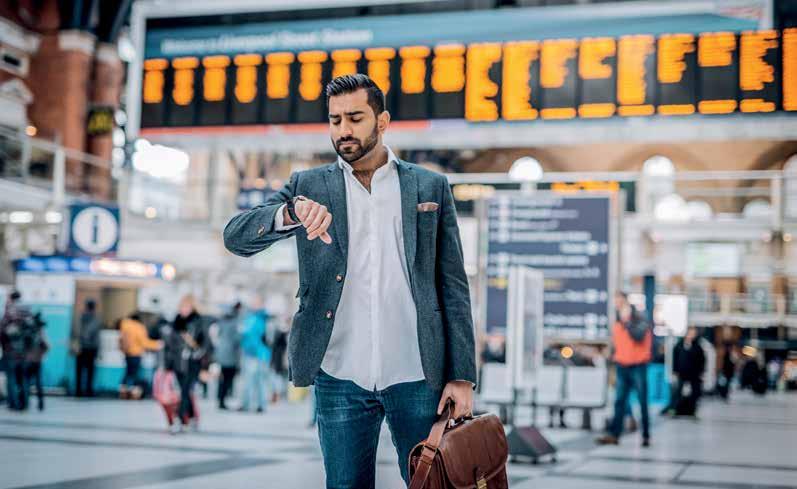
FEATURE86 Rail Engineer | Issue 197 | Jul-Aug 2022
There were presentations during the weekend to explain the IÉ plan for rail, the history of train protection in Ireland, the IÉ European Train Control System (ETCS), L1 Automatic Train Protection (ATP) programme, and the Indra Rail Traffic Management System (TMS). The Irish Section of the IRSE promotes signalling development, education, and knowledge across the various railway sectors of both Northern Ireland and Eire.
T rain protection and level crossing control in Ireland were two of the topics covered in the Institution of Railway Signal Engineers (IRSE) technical weekend held in Dublin in May. Both train protection and level crossings are two of the most important functions provided by the signal engineer. The technical weekend also included a visit to the new National Train Control Centre (NTCC) of Irish Rail Iarnród Éireann IÉ which is under construction at Heuston, Dublin, as well as a level crossing control centre at Athlone. The event drew attendees from the UK, Eire, Netherlands, France, Spain, Italy, and South Africa.
DARLINGTONPAUL
IÉ is building for the future to maximise the role of Ireland’s rail services to meet the growing transport needs of the country. Supported by the National Transport Authority and funded under Project Ireland 2040, a plan to invest in trains, infrastructure, stations, and customer service are part of the National Development Plan 2018-2027. Investment will also support the national Climate Action Plan and includes 790 new train carriages to cater for growingHeuston in Dublin.
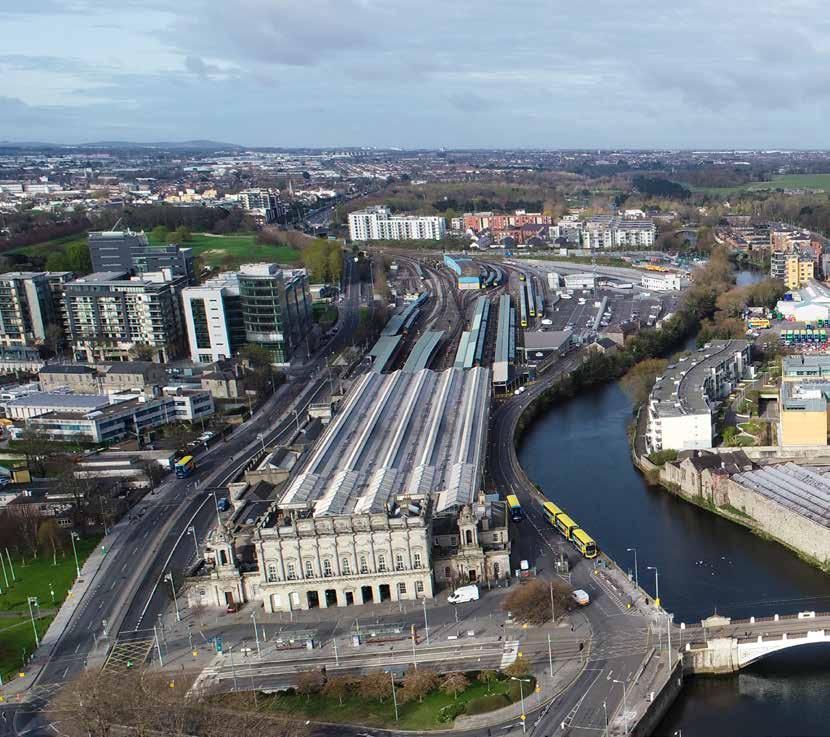
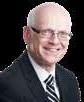

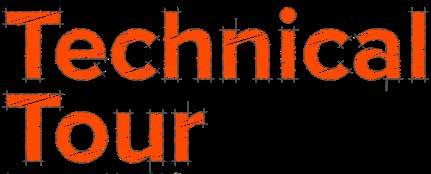
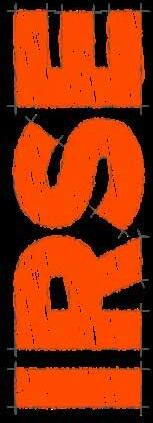

FEATURE 87 Rail Engineer | Issue 197 | Jul-Aug 2022
Istvan demonstratingDarazsi the Irish Rail train protection system.
CAWS repeats the line side colour light signal aspects on an Aspect Display Unit (ADU) inside the driver's cab. The ADU continuously displays the aspect that was shown by the previous signal until updated about 350 metres before the next signal. The ADU then displays the aspect shown by that signal. A change of ADU display to a less restrictive signal is called an ‘upgrade’, while a change to a more restrictive signal (single yellow to red) is called a ‘downgrade’. Any change of ADU display is accompanied by an audible indication. A momentary audible ‘warble’ sound indicates an upgrade. A downgrade is accompanied by a continuous audible tone and the illumination of the Acknowledge Switch that must be pressed by the driver within seven seconds to prevent an automatic brake application occurring for one minute.
Train drivers must be provided with clear signal indications so there is no confusion and limited risk of reading the wrong signal. The two main errors a driver can make are failure to control the speed of their train correctly and failure to stop at a signal. It is these functions which a train protection system must address.Trainprotection can consist of warning systems and full train protection systems. A warning system will normally be associated with the location at which braking should commence, and a protection system will aim to stop the train at or soon after the end of movement authority.
demand, with up to 600 electric or battery electric carriages; investment in track, signalling and level crossings to increase frequency and improve journey times; and new stations and upgraded existing stations including improved accessibility and car park facilities.
In Britain, Automatic Warning System (AWS) is a warning system that provides the train driver with an audible warning and visual reminder that they are approaching a caution or stop signal, a reduction in permissible speed, or entering a temporary / emergency speed restriction. Train Protection & Warning System (TPWS), as it names suggests, is the basic train protection system used throughout the British passenger main-line railway network and in Victoria, Australia.
Train protection
TPWS in Britain was developed from AWS after a decision in 1994 that the installation of a full ATP system was not practicable. Unlike ATP, TPWS will not prevent a Signal Passed at Danger (SPAD) but it does mitigate the consequences of a SPAD, by reducing the speed of a train or stopping it before a conflict point.InIreland, a coded track circuit carrier-based ATP and Continuous Automatic Warning System (CAWS) cab signalling system has been used since the early 1980s. This was based on historic North American technology supplied by Union Switch & Signal based in Pittsburgh, Pennsylvania. The system was provided as part of the electrification and driver only operation of the DART (Dublin Area Rapid Transit) network. There was a need to provide rear end train protection via ATP as there would be no guard to protect a failed train.
The problem was that, as well as the new DART driver only electric trains, there were also legacy diesel trains from other parts of Ireland running on the same routes as the DART ATP fitted trains. At the time, these diesel trains could not easily be provided with ATP, as the trains all had different braking curves. Some clever engineering was deployed to provide the diesel trains with a warning system with signal aspects in the cab via the same coded track circuit system. This was called Continuous Automatic Warning System (CAWS).
Since the ATP and CAWS are dependent on track circuits, axle counters cannot be used for train detection, and CAWS does not act in the event of a SPAD if the red aspect has been acknowledged by the driver. It is also a 40-year-old system and the technological and regulatory environment has changed significantly since its introduction. In addition to the difficulties of maintaining the
An ageing system
Train protection system cab display unit.
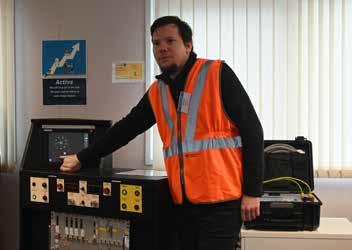
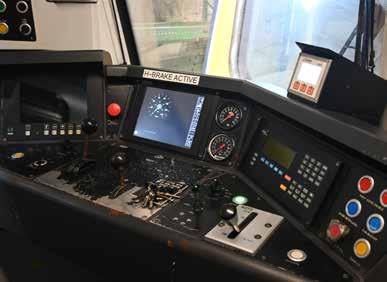
ageing system, the technology did not deliver several features of modern ATP systems, such as automatic train stop, train-regulated line speed, and compliance with speed restrictions.IÉlookedat options to replace their coded track circuit carrier-based ATP and CAWS. They initially decided against ETCS, as it was still relatively new and IÉ didn’t have a need for high-speed rail like other railways. So, it decided to develop Iarnród Éireann Hybrid System (IÉHS). The concept of IÉHS was that it would be a balise based system (similar to ETCS), providing modern full ATP features and designed to work as an ‘add on’ to the existing ATP and CAWS, with track circuit code being used to provide continuous infill where code was unavailable – approximately 50% of the network. However, during the development of the project, problems were discovered with the old-coded track circuit technology and electromagnetic interference (EMI) − unwanted noise − from things like farmers’ electric fences, rebar (reinforcing bar) in concrete sleepers, and even magnetic ‘puddles’ from rails that had been handled with magnetic grabs. ETCS had by this time become more mature, with several railways successfully deploying systems, and new trains were on order for Ireland that could be provided with ETCS. GSM-R, which provides the communication to the train rather than coded track circuits, was also now available. So, it was decided to deliver ETCS Level 1 Train Protection System (TPS) to provide train stop and overspeed supervision (permanent and temporary speed restrictions), as well as protection against SPADs and buffer stop collisions. Supplied by Alstom, the first stage of ETCS implementation will be on the Dublin Connolly based lines between Dundalk in the north and Greystones in the south. Covering a distance of approximately 125km, this initial phase will involve about 400 signals and include the only routes in Ireland currently electrified. This will involve manufacture and installation of about 180 location cases, 1,350 balises, and 50km of cable containment housing some 135km of cables. Ultimately, the rollout will include most of the existing operational network, some 450-route km of multiple track and 1,100 route km of single track, involving more than 1,600 signals and 5,000 balises.TheETCS trackside subsystem will be overlaid on existing signalling system consisting of 11 SSIs, four centralised relay interlockings, and relay-based auto signals with TPS location cases next to the existing signals.
A contract has been awarded to Indra to develop an advanced rail TMS to control the majority of the IÉ network.
Indra, based in Spain, is one of the leading companies in traffic management, with projects in countries including the United States, Australia, the Netherlands, Lithuania, Saudi Arabia, Turkey, Mexico, Colombia, Malaysia, and India. Indra will design and install an automated integrated control system, which will enable management tasks to be centralised, providing efficiency while improving passenger service, incident resolution procedures and maintenance. The scope of the Indra TMS includes the design, supply, installation, and commissioning of fully integrated and control equipment, as well as its maintenance for 15 years, with the possibility of extending it to 20 years. It also includes training facilities, such as a signalling simulator, as well as providing a backup control centre.TheTMS system is based on the Indra Mova Traffic line of solutions. The new control centre at Heuston will have the capacity to control the majority of signalling systems on the network to manage in the order of 600 passenger trains and 10 freight trains per day operating on the 2,400 km rail network. An automatic router, networkcommunications,management,a control panel and remote monitoring will be part of the TMS. Train IRSE visitors in the Athlone Level Crossing Control Centre. Athlone station.
Indra traffic management system
FEATURE88 Rail Engineer | Issue 197 | Jul-Aug 2022
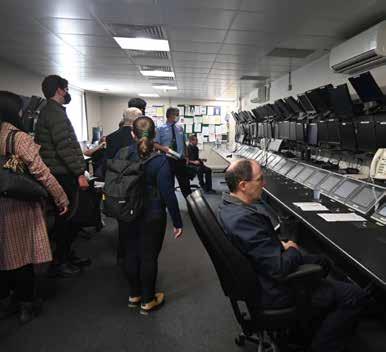
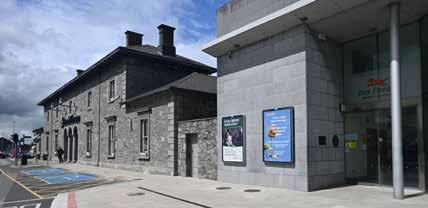
After visiting a valeting complex to inspect a train, the group travelled by train to see the Athlone Level Crossing Control Centre (AE LCCC).
Around the world, accident statistics demonstrate that level crossings are high risk sites for all railways and they also contribute to many near-miss events. There are many types of technology available to signal and telecoms engineers to provide the right combination of equipment for level crossings to be safe, effective, and affordable. Convenience to the level crossing user is also an important factor in any system selection.IÉhascreated level crossing control centres at Athlone and Mallow which can each remotely National Train Control Centre (NTCC) when
Indra has been working in Ireland for more than 15 years in the transportation market, with projects such as the Dublin Port Tunnel and many of the toll roads around the country.
FEATURE 89 Rail Engineer | Issue 197 | Jul-Aug 2022
Heustoncomplete.National Train Control Centre under construction.
Level crossings
The system already controls more than 3,000km of high-speed rail in Spain, 500km of the Mecca-Medina highspeed railway, almost 2,000 km of the Turkish high-speed network, and other networks of different characteristics in countries such as Lithuania, Malaysia, Colombia, Morocco andIndraSpain.says its Mova Traffic rail traffic management solution will incorporate digital big data, artificial intelligence and IoT technology. It will make it possible to “adapt transportation to actual demand, improve the passenger experience, facilitate maintenance, and more intelligent, safe, sustainable, efficient, collaborative and open mobility”.
On the Saturday, a visit took place to the impressive new NTCC at Heuston in Dublin, which will replace the existing Central Traffic Control Centre at Connolly station as it is at full capacity and is reaching its end-of-life. The NTCC building is still under construction, but once completed it will be IÉ’s centre for the management and regulation of train movements on the network. In addition, the NTCC will house other co-located control centres, specifically a control room and a regional traffic management control centre for An Garda Síochána, Ireland’s national police and security service. The NTCC will also provide real-time customer information at stations on the IÉ website and social media platforms. The existing Connolly control centre will be used as a backup centre to the NTCC. The top floor of the new building will be for An Garda Síochána, which will be the first to move into the building at the end of the year.
Control centres
circulation will be optimised, reducing potential conflicts and errors by providing operators with a single interface and making information easily accessible to all stakeholders. Access to the railway for maintenance work and incident control will also improve, enabling fast and efficient resolutions.
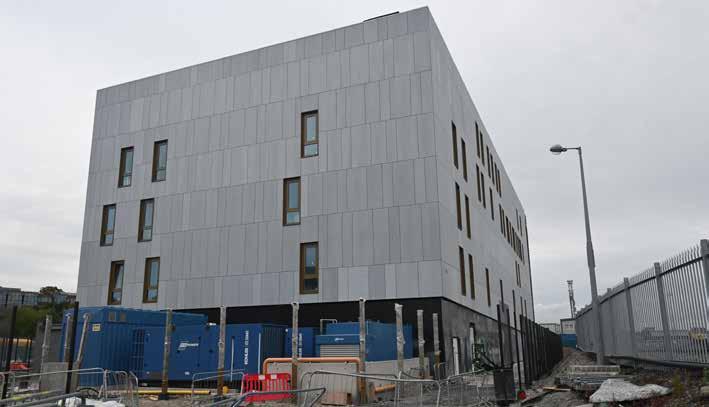

After returning to Dublin the technical weekend was followed by a two-hour show including an interactive and memorable concert of authentic Irish music performed by impressive local musicians and troupe of Irish dancers. The IRSE and Irish Section are very grateful for the financial support received from RIVVAL, Alstom, and Indra for the event, and 'benefit in kind' support from Iarnród Éireann Irish Rail, Transdev, Dublin tram operator Luas, and Purcell Construction.
FEATURE90 Rail Engineer | Issue 197 | Jul-Aug 2022
There are six central PLCs in Athlone which communicate over the fibre transmission system to an individual PLC located at each crossing. A central PLC has the capacity to communicate with up to 16 level crossings, thus giving AE LCCC the total capacity of 96 crossings.
control up to 96 crossings via CCTV. The control centres run on Industrial PLC’s that are SIL4 certified. The control centres communicate and control each individual level crossing over the IÉ internal fibre optic network. On the journey to Athlone the train passed through three level crossings which are controlled from Athlone: Meelegans, Ashfield, and Bunnavalley.
The AE LCCC was previously a goods shed and a Guinness store and was established in 2007 with, at first, eight level crossings. Each crossing was upgraded from either a mechanical gated crossing or automatic half barrier to four full barriers. Once this was completed, the crossings were switched to remote working and controlled from Athlone via CCTV and PLCs.
Currently, AE LCCC controls 85 crossings spanning across four lines: Galway Line – 14 crossings; Mayo Line – 39 crossings; Sligo Line –14 crossings; and Waterford Line – 18 crossings. The centre is currently staffed by 26 crossing keepers, with a minimum of four working together on any day shift, plus a supervisor.
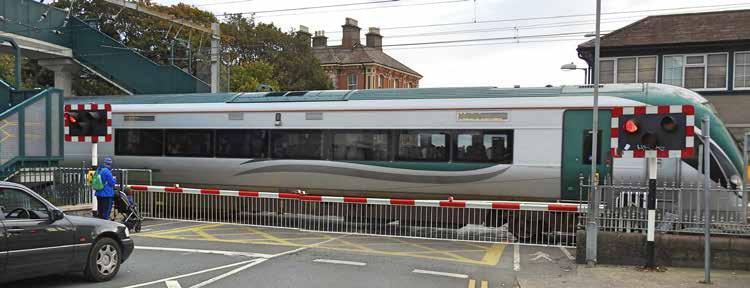

For over 35 years, Electro-Wind engineers have been designing and manufacturing single and three-phase transformer products for customers across the globe. With a well-established reputation, the company has fulfilled many contracts for companies including Alstom, Tata, Corus, Mitsubishi, Siemens, and Toyota. In early 2016, Electro-Wind was approached by Devontech to work as its main transformer supplier to design, build, and obtain approval for a range of PSP transformers for the Feltham and Wokingham re-signalling project. Between them, the Feltham Area Signalling Centre and Wokingham Signal Box cover 80 miles of railway and 500 separate pieces of signalling equipment on key areas of the South Western Railway (SWR). Dating back to 1974, the existing equipment, which includes signals and track circuits, is becoming increasingly difficult to maintain. Electro-Wind, Devontech, and Atkins global have been working on the project which is part of Network Rail’s commitment to transform the entire UK network through the deployment of digital signalling and train control
Electro-Wind: RAILTRANSFORMINGPROJECTS FEATURE 91 Rail Engineer | Issue 197 | Jul-Aug 2022
The project is currently running on schedule, with final commissioning for the project into service in April 2024.
The company also provides a rapid response repair service, from new enclosures to complete rewinds, and can offer a 24-hour service when needed. For further information, get in touch using the details below:
Electro-Wind’s expertise and capabilities in the coil winding industry allow it to manufacture any bespoke transformer from 10VA up to 2MVA, in addition to AC reactors, DC rectifiers and chokes, with a comprehensive range of associated products including site electrical accessories on offer.
Technology.Todate,Electro-Wind has manufactured 57 transformers for the project ranging from 5kVA up to 60kVA. The transformers have been 400V/650V signalling transformers on which Devontech and Electro-Wind worked closely together to get PADS approval for the Network Rail Infrastructure. The project, which began in December 2015, is due for completion in March 2023. There have been five phases: phase one, in the Strawberry Hill area, was completed in Easter 2021; phase two, Virginia Water and Ascot, was completed in Easter 2022; phases three and four, in the Windsor, Staines, Feltham and Kew Bridge areas, are expected to be completed in August 2023.
Devontech Tel: 01626 contactus@devontech.co.ukwww.devontech.co.uk 333886 Electro-Wind Tel: 01782 776 sales@Electro-wind.co.ukwww.Electro-wind.co.uk321
Finally, phase five, in the Wokingham area, is expected to be complete in February 2024.

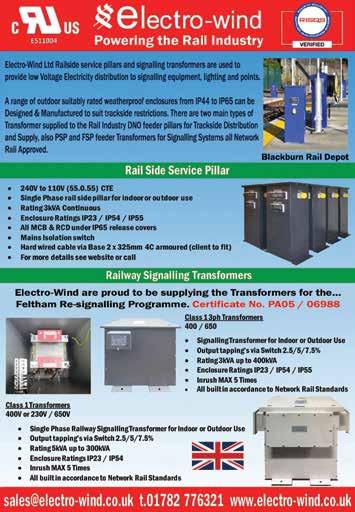
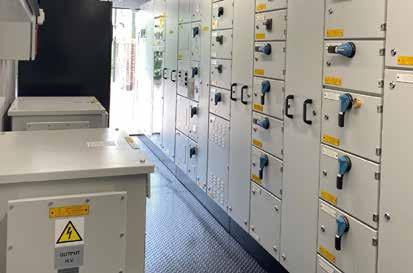
In 2008
Railway Plant Servicesin Northern Ireland
FEENEYCHRIS
tenderingwhoCompaniesmaybefor contracts in Northern Ireland, should not hesitate to contact Railway Plant Services for their on-track plant requirements. A family run company with competitive rates, dedicated to providing a quality service.
FEGANKIERAN
Rail Engineer | Issue 197 | Jul-Aug 2022 92 PLANT & EQUIPMENT
Kieran Fegan and Chris Feeney spotted a gap in the market for a Plant and Labour supplier for railway infrastructure in Northern Ireland, at that point Railway Plant Services Ltd was founded. Prior to this, both directors worked for a decade in the railway industry in England and Ireland. Together they share a wealth of experience and knowledge from working in these regions. The company began its life with a fleet of two machines and a few attachments. Over the next few years the fleet increased as the company grew. In 2018, Railway Plant Services moved away from labour supply and concentrated business operations on the hire of RRV’s and operators. New RRV MEWPs were added to the fleet, diversifying its services. Another addition to the fleet was its RRV Land Rover. Fast forward to the present, the company now boasts a fleet of over 30 RRV machines, a large fleet of rail trailers, and much more specialised rail equipment such as Tin Bin vacuum systems. The large fleet of RRV’s and Service Vehicles is expertly maintained by the company’s in-house team of specialised technicians. Railway Plant Services ensures its RRV fleet and drivers are fully compliant to railway standards and the latest editions to the fleet are two new RRV Komatsu 160’s. The company also provides low loader transport service and Hiab services.
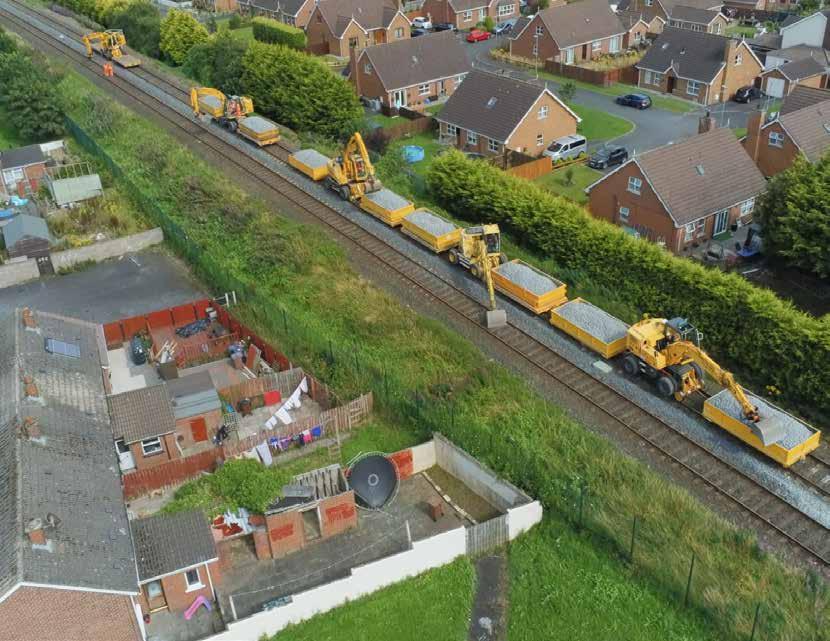
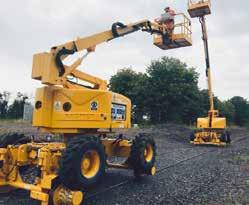

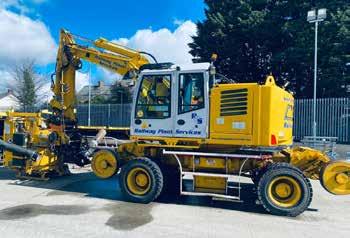

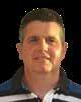


Railway Plant Services Ltd, 19 Drumaran Rd, Gilford, Craigavon, BT63 6DB DEDICATED TOSERVICEQUALITY On-track plant specialist in northern ireland With a fleet of over 30 RRV machines, a large fleet of rail trailers and many more specialised rail equipment to o er such as the Tin Bin vacuum system, Railway Plant Services Ltd are the company for your on-track plant requirements in Northern Ireland. for more information, please visit www.railwayplantservices.com contactus@railwayplantservices.com 028 3883 0787 Chris 07702714947Feeney Kieran 07980004176Fegan

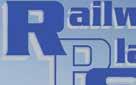
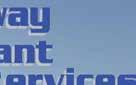

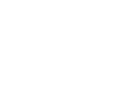


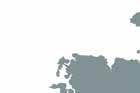
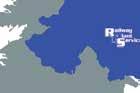
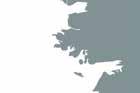
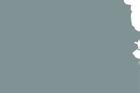
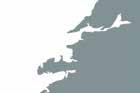
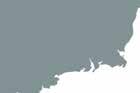
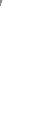

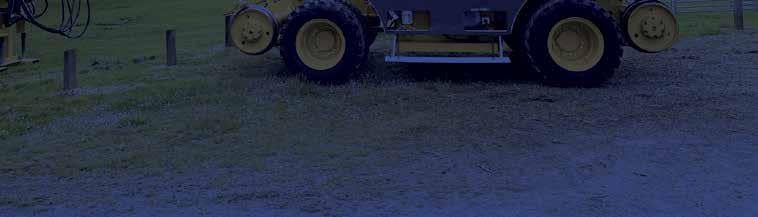
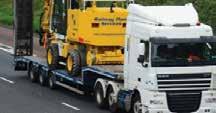
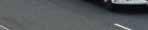
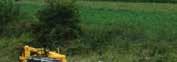
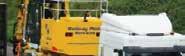
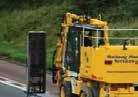
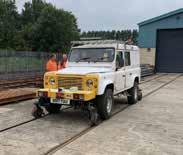





Zero emissions Liebherr electric crane at HS2's Old Oak Common site.
Aiming to achieve net zero carbon from 2035, and with a target of achieving diesel-free construction sites by 2029, HS2 is collaborating with the industry and its supply chain to accelerate innovation in low carbon technologies, such as fully electric machinery, alternative fuels, and renewable energy solutions.
Low carbon cranes Back in February, HS2 announced a step forward in its move towards this goal when it announced the arrival of three fully electric crawler cranes at its sites in London. This followed the UK’s first trial of an electric crawler crane at HS2’s Curzon Street Station site in Birmingham in 2021. With only five of these 100% emissions-free, giant Liebherr cranes in the world, three are currently in use by HS2, helping to cut carbon, improve air quality and reduce noise, and make sites cleaner and safer for site workers and local communities.Expanded– a Laing O’Rourke specialist business working for Balfour Beatty, VINCI SYSTRA joint venture (BBVS) – took two of the giant battery-powered electric crawler cranes onto HS2’s Old Oak Common Station site in West London. The Liebherr LR1250E, a 250-tonne lattice jib crawler crane, and the 160-tonne Liebherr LR1160E both operate emission-free and are being used to construct the 850-metre-long Old Oak Common Station box which will house six high-speed rail platforms. The third crane – a 160 tonne Liebherr LR1160E, was delivered to HS2’s Canterbury Road vent shaft site managed by Skanska Costain STRABAG joint venture (SCS JV).At the time of their arrival, HS2 Minister, Andrew Stephenson said: “Having the UK’s first fully electric crawler cranes begin work on HS2 is
HS2’s Net Zero Carbon Plan, published in January, set out how the project will achieve new carbon reduction milestones, support the decarbonisation of the UK construction sector, and reduce the carbon footprint of its programme. As Europe’s largest infrastructure project, HS2 says it is “acutely aware” of its responsibilities and is “committed to playing our part in the collective endeavour to combat the climate emergency.”
HS2: GOING GREEN Rail Engineer | Issue 197 | Jul-Aug 2022 94 PLANT & EQUIPMENT
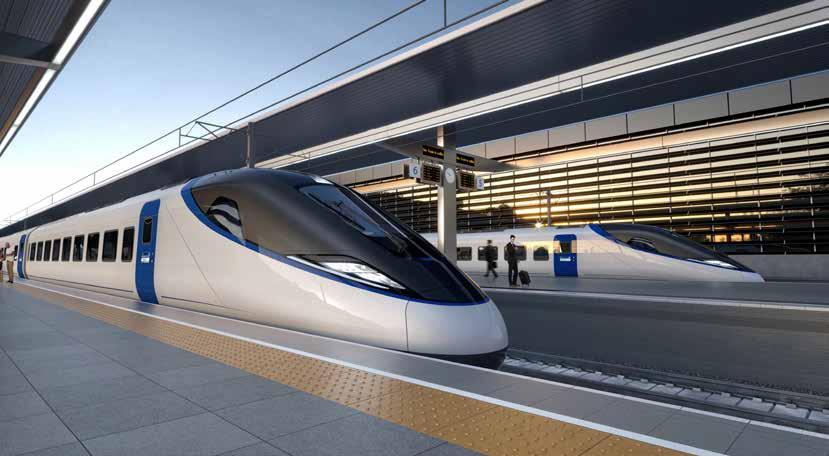
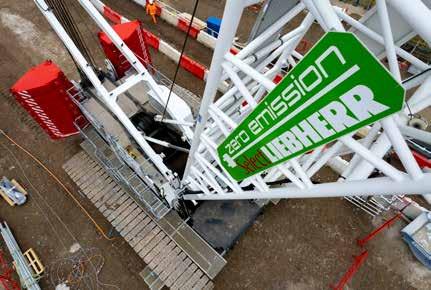
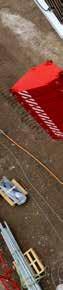
Other sites are set to follow suit, with innovations including retrofit technologies and solar power helping to cut carbon across the whole of the route.
the latest step in making these commitments a reality and aligning the country’s biggest infrastructure project with the Government’s ambitions for a greener transport.”
Diesel-free construction In a further positive step, in May, the Canterbury Road vent shaft site was named HS2’s first diesel-free site. Along with the LR1160E crane, SCS JV has introduced a range of diesel-free technologies and greener equipment to the site from biofuels (hydrogenated vegetable oil) to power plant and machinery; an electric compressor; and access to mains power on a 100% renewable energy tariff.
Cleaner, quieter drilling rigs To help meet HS2 carboncutting targets, Balfour Beatty VINCI Joint Venture (BBV), is currently trialling the world’s first all-electric, high-capacity drilling rig on a construction site inTheWarwickshire.100tonne BAUER eBG33 drilling rig creates an overall reduction of 1292kg CO2 per day compared to a traditionally powered rig and also reduces noise by 50%. In terms of performance, the rig is able to carry out exactly the same tasks as its traditional counterpart.
The new BAUER eBG33 piling rig cuts 1,200kg of CO2 per day and reduces noise by 50%.
Rail Engineer | Issue 197 | Jul-Aug 2022 95PLANT & EQUIPMENT
Andrea Davidson, HS2’s air quality manager said: “We are proud to be working with our supply chain and leading manufacturers to drive a step change in the UK construction industry, demonstrating the viability and benefits of emissions-free heavy electric plant.“Being at the forefront of a ground-breaking trial like this is another step on our journey to achieving our target of all diesel-free construction sites by 2029, and net zero carbon from 2035 - helping HS2 to become the most sustainable infrastructure project ever delivered.”TheBAUER eBG33 replaces the diesel engine drive with a powerful electric drive. The environmental benefits include reduced exhaust and noise emissions; high energy efficiency due to modern threephase asynchronous motor; and flexibility through an integrated frequency converter. BAUER are also trialling different E-connection concepts and an innovative concept for set-up operation via an autonomous secondary drive which is independent of the power supply.“We’re thrilled to be leading the industry with this electric rig,” said Tim Laemmle from HS2 Minister Andrew Stephenson and SCS Electric Crane Operator Leon Sobers.
Andrew commented:Stephenson“This,the first of many diesel-free sites, is another example of how the country’s biggest infrastructure project not only delivers on its commitment to be Net Zero from 2035, but is a pioneer in leading the whole industry to cleaner, greener construction.”
The new machine is being used by BBV’s deep foundations contractor SB3 (a Joint Venture between Bachy Soletanche & Balfour Beatty Ground Engineering), and works alongside a dieselpowered rig to construct large diameter piles, with the aim of demonstrating that heavy, electric-powered construction plant can perform the same tasks as traditional machines.




» Non-Road Mobile Machinery retrofit solutions, which add pollution control equipment onto older vehicles as an alternative to replacing the machine or the engine, reducing emissions.
The GeoPura hydrogen power units on HS2 site.
BAUER Maschinen GmbH, the rig’s developers and manufacturers. “It is great to be working with HS2, BBV and SB3, as the first UK specialist contractor to demonstrate the capabilities of the product. We’re fully committed to bringing foundationequipmentemission-freetothedeepsector.There is a strong desire to promote our new electrified equipment as a genuine, reliable alternative to fossil fuel driven machinery.” Hydrogen powered The generation of power on site is another hurdle to clear in the drive for lowcarbon construction sites. In July an HS2 site in London held successful trials for two zero-emissions hydrogen fuel cell-based electricity generators – cutting carbon and improving air quality for workers and the localThecommunity.twoGeoPura 250kVA hydrogen power units (HPUs) were trialled in2021 at HS2’s Victoria Road Crossover Box in Ealing, as a direct replacement for diesel generators to power machinery on the site. Tested and commissioned by HS2’s mains work civils contractor Skanska Costain STRABAG (SCS JV), the trials showed that the products are capable of producing the required energy to power equipment required for site operations.
» ‘EcoNet’ developed by Invisible Systems, Balfour Beatty and Sunbelt which controls and reduces energy output from key appliances, reducing power demand by 30%.
» Clean Air Gas Engines funded through Innovate UK and led by OakTec, which replaces diesel power with ultra-low (bio-LPG) emission engines in Advante Welfare units and standalone units.
» CESAR constructionenginetowhichComplianceEmissionsVerification,isaresilientsystemshowtheEUStageemissionclassofallplant.
» Proactive dust management solutions to reduce impacts associated with on-site activities.
» Fully Electric Renewable Energy using solar and wind to power noise and air quality monitors, site security cameras and site briefing areas and solar pods powering sites by combining solar PV, battery storage and a back-up generator. Embracing cleaner technology and shifting away from outdated machinery is crucial if industry of all sectors, is to meet climate change targets. HS2 looks to be committed to tackling emissions across its project, from construction to final operation.
The trial, supported by HS2’s innovation programme, has already gained industry recognition, picking up the ‘Best Use of Technology Award’ at this year’s Construction News Awards. Innovation all around Along with the innovations we’ve covered, many more are being rolled out on HS2 sites along its route. These include:
“This is another example of how HS2 is driving change in the industry by trialling alternative fuel innovations,” said Andrea Davidson. “With no harmful pollutants, the technology brings major air quality benefits to the workforce and local communities around construction sites, something which is vitally important to HS2 across the whole project.”
The hydrogen power units provide 100% renewable and emission free power derived from a hydrogen fuel cell, with power capabilities ranging from 20kW through to 2MW. They use 100% green hydrogen produced from renewable energy, and data from the trial showed that running the units for 400 hours eliminated around 51 tonnes of carbon compared to using standard diesel generators.Theyarealso quieter than standard diesel generators and the only emission is water which is so clean it’s drinkable. A hydrogen tube trailer and hydrogen cannisters were used to fuel the generator.
Rail Engineer | Issue 197 | Jul-Aug 2022 96 PLANT & EQUIPMENT
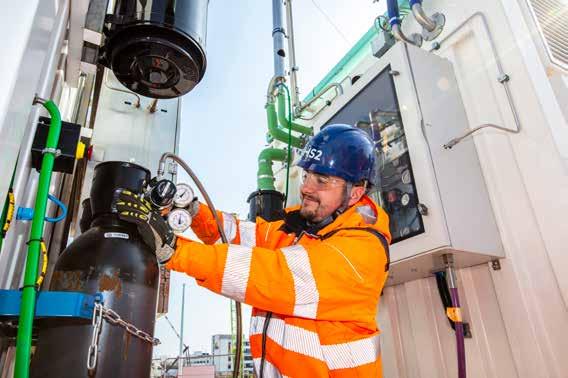

Scan this // Watch // TRS CEO Paul Bateman talking about HVO at Rail Live 2021 total rail sustainable Total Rail Solutions ditches diesel and switches to a cleaner , greener fuel for a more sustainable rail network . • Alternative HVO fuel from Crown Oil to be supplied in all plant • Further improving the environmental impact on the rail network We are one of the first hirers in rail to make this change and are committed to protecting all our futures. Visit totalrailsolutions.co.uk or call 01962 711642 to find out more
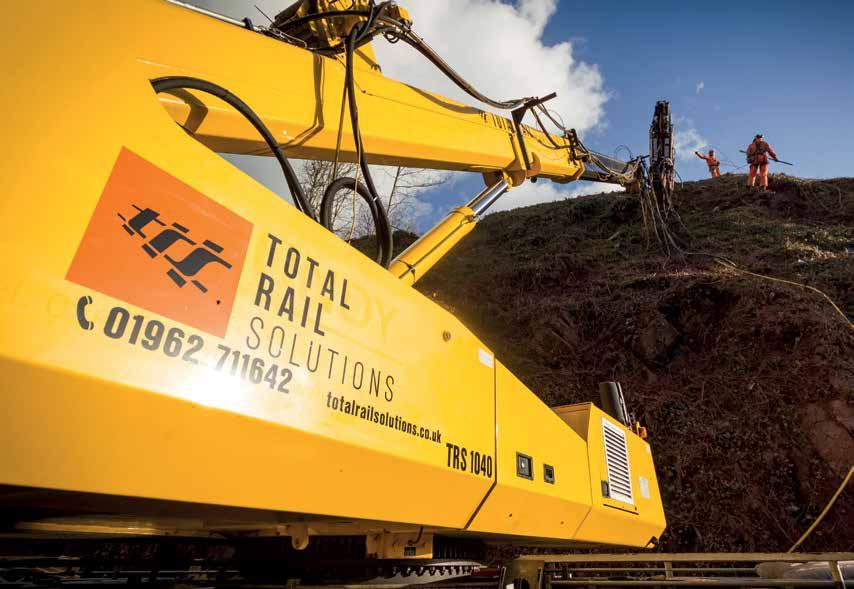
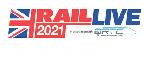

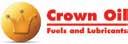
With some justification, the Levenmouth Rail Campaign (LMRC) has for some time argued that there is a strong case to re-open the six-mile branch line to Leven. This was originally part of the line around the coast of Fife’s East Neuk to St Andrews. Following the Beeching Report, this was closed in 1965 although its Leven branch remained open. Nevertheless, British Rail closed the branch to passenger traffic in 1969. It then remained open to freight traffic which ceased about 20 years ago. The line is still owned by Network Rail which is not required to maintain it as it is out of use under Short Term Network Change (STNC) provisions. Hence, the infrastructure remained in place, albeit neglected and heavily overgrown.TheLevenmouth area includes the communities of Buckhaven, Methil, and Leven which have relatively high levels of unemployment following the closure of coal mines and heavy industry.
Though ‘Reversing Beeching’ is a popular aspiration, the question of whether a line should have been closed is quite different from whether it should now be reopened. Providing new rail infrastructure is an expensive business and can only be justified if it offers significant benefits.
With a population catchment of almost 50,000 people, Levenmouth is the largest settlement in Scotland without a rail link. It also has Diageo’s bottling plant and grain distillery − Europe’s largest − which offers significant rail freight potential. A re-opened Leven branch would therefore serve a sizeable settlement and bring an economic transformation to the area. It would also be relatively cheap to re-open as the base infrastructure is in place and there is no requirement for parliamentary powers or significant land purchase. Since its formation in 2014, LMRC had been campaigning to get these arguments accepted. Its case was acknowledged at a Scottish Parliamentary debate in 2017 when Transport Scotland, was instructed to undertake a Levenmouth Sustainable Transport study. Of the various transport options considered, this study concluded that a 30-minute train service from Cameron Bridge and Leven stations “emerged as the highest overall value for money option.”
In August 2019, Scottish Cabinet Secretary for Transport, Michael Matheson, announced the go-ahead for design work to support the reopening of the branch. Delivering the benefits To maximise the economic and social opportunities presented by the new Leven rail link, the re-opening project is working closely with the Leven Programme Partnership and the Levenmouth Reconnected Programme.TheLevenProgramme is Scotland’s first sustainable growth agreement. This is a partnership of different organisations working across a river catchment to improve the natural environment, support active travel, and create a hub for tourism, business, and
Reconnecting LEVENMOUTH (Inset) Thornton North Junction from Leven branch in 2017. (Below) Track laid to junction. SHIRRESDAVID FEATURE98 Rail Engineer | Issue 197 | Jul-Aug 2022
Although it is only 37 miles from Edinburgh by road, public transport from the area to the city can take almost two hours.

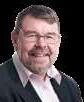

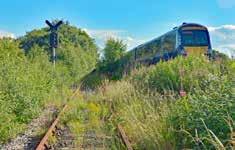
Martin explained how, in December, the local population were asked for their view on the sites of the new stations as well as active travel links and integration with other transport modes. Due to the Covid situation these events were held online with anyone interested able to book 15-minute video calls with the team. The project website also provided an opportunity for onlineFollowingsubmissions.thisconsultation, the locations of the stations were finalised.
The re-opening project By January, the scope of the project had been defined as: “An affordable, reliable double track railway between Thornton North Junction and Methil Docks and two stations at Leven and Cameron Bridge. Future proofed for electrification with the possibility of freight and heritage connections to an agreed baseline cost, Levenmouth aims to increase capacity on the line to two passenger services an hour and the possibility of two freight trains a day by 2024. The journey time between Leven and Edinburgh is not to be greater than 70 and 75 minutes depending on the route
Network Rail’s senior project sponsor Martin McKinlay explains that a large part of his role is to work with these initiatives and other stakeholders to ensure that the new railway will provide the greatest benefit to the community, particularly in respect of active travel opportunities. In this way he feels that Network Rail’s project team is doing much more than providing a railway as the key requirement is to make sure that it can provide the best benefit to the community.
One stakeholder challenge is the need to close established walking and cycling routes along and across the disused line. The strategy is a soft closure of these routes which will not be closed until they have to be. In the meantime, notices advise of the need to be aware of increased risk from work activities. Some of these paths will be replaced by new active travel routes. However, some routes across the line will be closed as the new line will have no level crossings.
» Six switch and crossing units.
» Route wide track formation work and earthworks.
» Railway systems: signalling
(IECC FEATURE 99 Rail Engineer | Issue 197 | Jul-Aug 2022
Leven station is to be the most southerly option next to the bus station and leisure centre. Cameron Bridge station is the most easterly option with access off a busy main road. There is little scope for consultation on station designs as these are being built to a basic template. However, Martin advises that at Leven there are opportunities to provide facilities nearby by, for example, funding to facilitate retail opportunities. This location is also the subject of a placemaking study to create a quality public realm around the station and towards the town centre.
Detailedtaken.”design established that delivering this scope required: » 9.3 kilometres of electrified double track railway of which the first kilometre from Thornton North Junction is single track, a total of 19 single track kilometres. Due to its curves, the linespeed between the junction and Cameron Bridge will be 45mph.
» Underbridges: five repaired and redecked; two demolished.
industry. Its partners include the Scottish Environmental Protection Agency (SEPA), Scottish Natural Heritage, Sustrans, Fife Council, and Scottish Enterprise. The programme includes a connectivity project to develop a series of paths in the area between Cameron Bridge and Leven and is supported by Transport Scotland’s Places for Everyone Levenmouthprogramme.Reconnected is a £10 million fund managed by Fife Council to maximise opportunities presented by the new line by awarding grants to projects which, for example, generate employment or provide community serves.
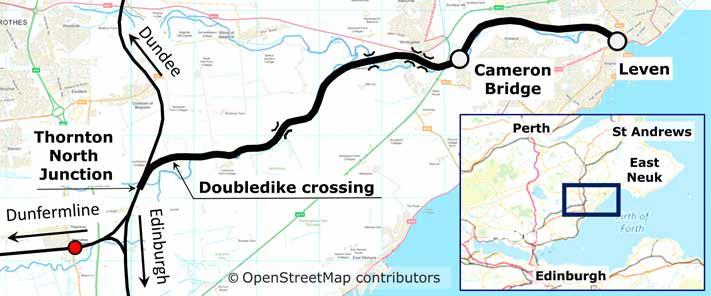

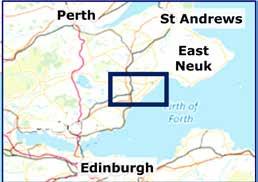
Since then, it has been confirmed that the project will also renew the 75-year-old Bawbee Road bridge in Leven at a cost of £8 million. The bridge crosses the site of the new station and is used by 18,000 vehicles each day. It currently has an 18-tonne weight restriction as a result of chlorine contamination and corrosion. Due to the interface between this work and the rail project, it was agreed that the bridge renewal is best done as part of the rail project.
The project is one of a small number of Network Rail projects being delivered in accordance with the Project 13 delivery model. This is an initiative led by the Institution of Civil Engineers which is based on a partnership enterprise model rather than traditional Trackbed at bridge 2 before devegetation work.
FEATURE100 Rail Engineer | Issue 197 | Jul-Aug 2022
In January, the Scottish Government confirmed that £117 million was to be invested in the Levenmouth railway and that it will open in spring 2024.
workstation upgrades, interlocking and axle counters, telecoms including one GSMR mast and E&P.
The work requires the provision of a temporary road which includes a temporary bridge over the River Leven. This will be in use from August for the 12 months required for the bridge renewal.
Project 13
» A station at Cameron Bridge with two x 140-metre-long platforms, lifts, footbridge and a 300-space car park and bus stop.
» Six overbridge electrification parapet extensions.
The Levenmouth project includes electrification as it is clearly less expensive to electrify a line as it is built. This is part of a programme to remove diesel trains from Fife passenger services. Whilst Scotland’s Rail Services Decarbonisation Action plan has a longterm plan for full electrification, to replace diesel trains as soon as possible, the Fife lines will initially be partly electrified and operated by Battery EMUs for which procurement is already underway. In addition to the Levenmouth branch, this requires a programme of 104 single track kilometres (stk) of electrification which is planned for completion in December 2025.
» A terminating station at Leven with a single island platform 200-metres long and a 90-space car park. The long platform provides an opportunity for stabling and charter operation.
Electrifying Fife
In June, work started the first part of this programme to electrify the line between Haymarket and Dalmeny, immediately south of the Forth Bridge. This will see 25 stk electrified by December 2024 at a cost of £55 million, with a feeder station to be provided at Thornton North Junction. From there, other lines will be electrified to Kirkcaldy, Lochgelly, and Ladybank as part of this programme. In view of the above, after the new Levenmouth lines opens it will be about two years before it can be operated by electric trains. As a result, it is possible that the line might be wired as part of the later Fife electrification works given the security issues associated with delay in energising the Levenmouth branch.
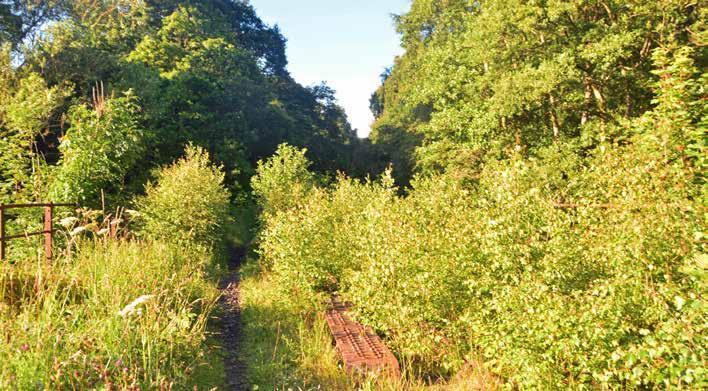
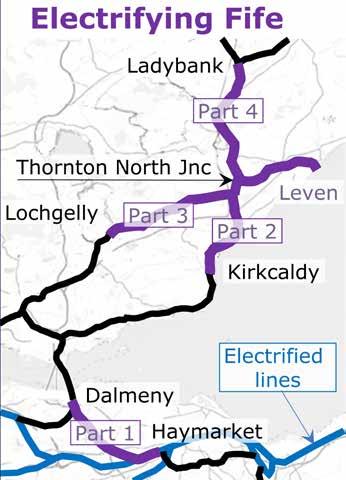
.
Modern Railways EXPO is supported by key industry players including Network Rail and the Rail Forum Engage with these organisations at the show discover how your organisation can contribute towards the future of Britain’s railways:Engage with representatives from a range of Network Rail departments, including seminars, panel discussions and the chance to explore some of the new technology being introduced onto the network. Engage with Rail Forum members and join the trade body for a seminar programme aimed at supporting companies in the supply chain.
Showcasing the future of Britain’s railway EXPLORE THE INDUSTRY Modern Railways EXPO will be laid out in dedicated zones based on industry areas, giving you an overall perspective of the latest developments and technologies on show as companies look to the future of Britain’s railways. • Freight • Industry and Regulatory Bodies • Infrastructure and On Track Plant Suppliers • Professional Advice, Consultancy and Services • Rail Recruitment • Rail Vehicle Enhancements • Rolling Stock Manufacture, Supply & Delivery • Signalling and Telecommunications Want to join them? Then get in touch today by e-mailing david.lane@keypublishing.com or call 07795 031051 include:Zones To nd out more please visit us at... COLLEAGUESMEETwww.modernrailways.com/expoWITHDISCUSSTHEKEYISSUESENGAGEWITHKEYORGANISATIONS
to
325/22 NOWREGISTERfor our excitingnew show!
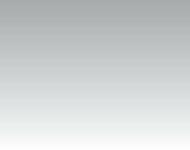
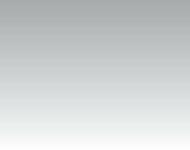
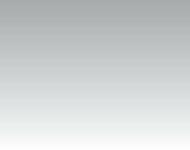
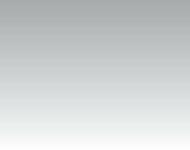


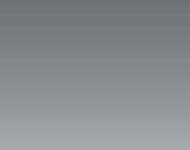
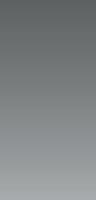
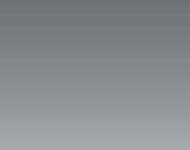
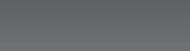
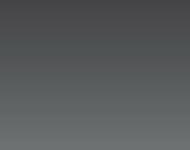
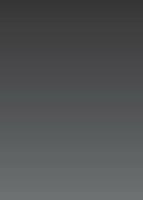
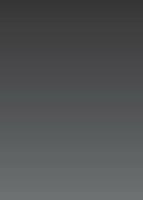
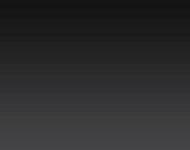
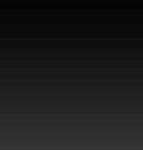
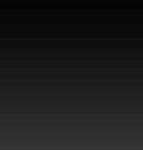
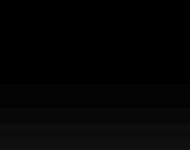
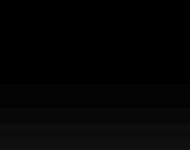
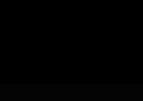
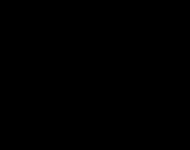
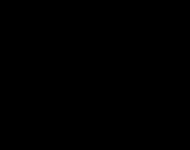

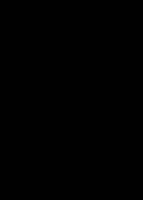







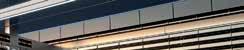
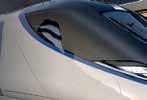
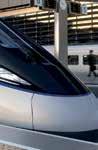
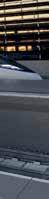
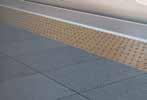
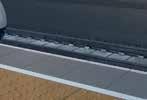



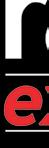
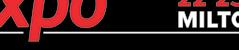
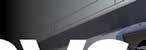
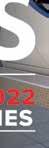

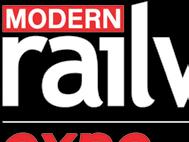
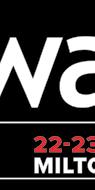
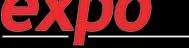
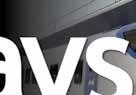
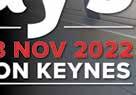


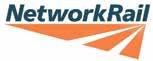
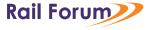
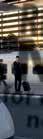




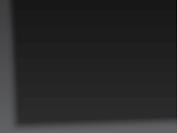
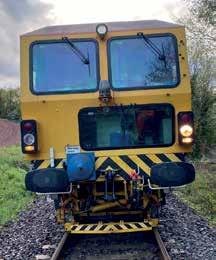
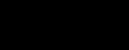
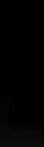

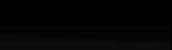

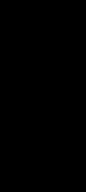

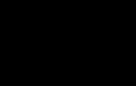



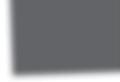

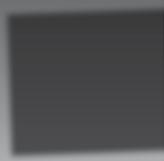
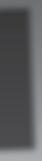

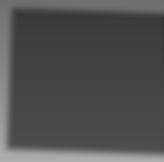

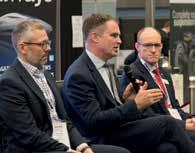
» Governance – owners establish rules and processes to guide their interactions with suppliers.
» Organisation – owners engage the right suppliers at the right time and integrate them into the team.
» Digital transformation – develop new business models to take advantage of new technology.
The intention is to provide a greater focus on infrastructure project outcomes rather than deliverables. The deliverables are defined by the previously mentioned project scope whereas outcomes are driven by adding value. A key outcome is making “Levenmouth a better place to live, work and play.” As an example, 14 mentors from the project’s eight partners have engaged with 250 young people in a STEM (Science, Technology, Engineering and Maths) initiative. For the Levenmouth project, the enterprise partners are Transport Scotland as investor, Network Rail as owner, and AmcoGriffen, Atkins, Babcock, BAM, Siemens, SPL, Story, QTS, Rail Safety Accreditation Scheme (RSAS) as suppliers. Atkins is the designer and BAM is the principal contractor.Theproject is supported by a steering group of representatives from Network Rail, the framework contractors, and the designer. Its role is to provide strategic leadership and ensure the project is delivered in accordance with Project 13 principles. There are also six integrators who are key individuals from different enterprise partners and are accountable for project delivery. These are: design and engineering assurance – Atkins; planning and control – SPL; operation and construction – Network Rail; project management – BAM; commercial –Babcock and safe delivery – Story.
On site Work to re-open the Levenmouth branch started with devegetation work late in 2020 which was followed by the start of site investigation work early in 2021. In July, work started to remove the old disused track and other redundant infrastructure. This track was all reused, recycled, or repurposed on the project with much donated to heritage railways in Scotland. During a weekend disruptive possession in March, work was undertaken at Thornton North Junction. This is a single lead junction which required heavy maintenance and did not need to be remodelled. Though technically operational, this junction last saw regular use between 2012 and 2015 when new sidings were provided near Doubledikes level crossing, one kilometre from the junction, to load coal from a nearby opencast mine. March also saw the first mile of track from the junction being laid and the establishment of the first construction compounds.
» Integration – owners must develop culture, practices, and systems appropriate to the programme.
transaction arrangements between infrastructure owners and suppliers. The model has the following five key features:
» Capable owners who must have the capability to define outcomes, articulate technical requirements, manage stakeholders, put infrastructure into operation and work collaboratively with whole team.
Old track removed which will be reused.
FEATURE102 Rail Engineer | Issue 197 | Jul-Aug 2022
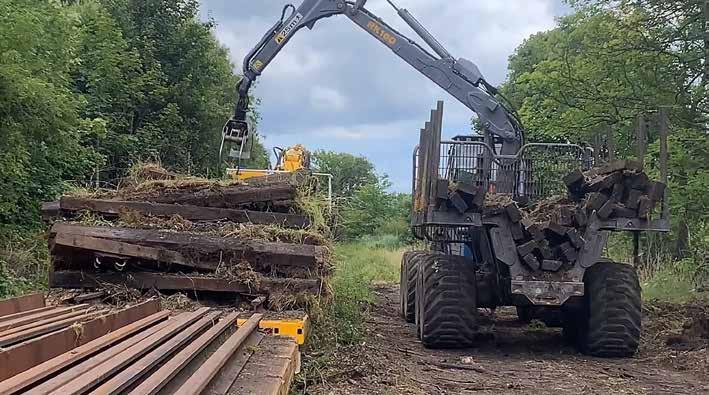
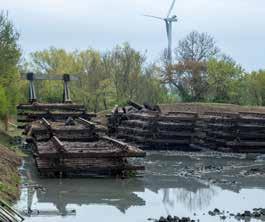
Visit www.rssb.co.uk/training for more information, or email training@rssb.co.uk if you’d like RSSB to deliver any of our non-technical skills course as a bespoke training remotely or at a location of your choice.
www.rssb.co.uk/training Scan Me
Are you one of the 2000 people who have benefited from a RSSB training course?
The railway relies on high-calibre, competent professionals. As the UK’s independent organisation that works for a better, safer railway, we offer a range of training courses to help with the professional development of rail employees and make a positive impact on your business.

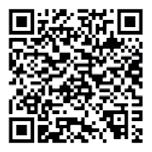
In May, I was glad of the opportunity for a site visit to see the work done and understand the challenges of the work to re-open the line. My visit was hosted by the project’s operation and construction integrator, Joe Mulvenna and senior communications manager, Owen Campbell, both of Network Rail. Whilst walking alongside the newly laid track, Joe explains that, in May 2021 Thornton Yard took delivery of the 16,000 sleepers needed for the project and became a virtual quarry for the 80,000 tonnes of ballast that the project will require. 13,500 tonnes of which was used for the initial track laying. Our walk takes us across Doubledikes level crossing. A sign at the crossing advises that work is now underway to create the Levenmouth rail link. Although an established walking and cycling route, it is a private crossing and is not one of Fife’s adopted core paths. As there are to be no level crossings on the line, this route will be closed unless additional funding can be found for a bridge.Joealso explains the environmental challenges. For much of its route, the line follows the sometimes-steep valley of the River Leven which it crosses four times. Although there are no major environmental issues, the local ecology, in particular otters, badgers, and bats must be protected. Invasive species including Hogweed and Himalayan Balsam are also a problem. The project has established environmental buffers zones within which no work can take place unless authorised by an Environmental Clerk of Works. The original line was a twotrack railway. Although it has no major earthworks, there are some steep slopes such as those above the track in the river valley near Tullybrek. Construction of earthworks to current standards at such locations requires the purchase of some parcels of land. We then visit the station sites at Leven and Cameron Bridge. At Leven, the old line continued over a bridge over the River Leven to Methil docks which was once the largest coal exporting port in Scotland. Although there are no plans to extend the line, the station design allows for this eventuality. Whilst standing under the Bawbee bridge at the new station site, it is clear why the bridge works need to be completed before the new line opens. Owen explains how the new station is to be an integral part of the town centre offering an improved public realm and potential for new facilities.Thenew Cameron Bridge station is off the busy A915 road which runs through Fife’s East Neuk to St Andrews. Hence the station is likely to be a rail head for the area and so has a 300-space car park with land available for its expansion, if necessary. Active travel options to the station from the north and from the distillery site to the south are currently being developed. This includes the use of one of Fife’s adopted core paths which crosses the railway at Duniface and so will require a bridge if it is to be Althoughmaintained.thelocation of the station was subject to public consultation, another factor of the line - for now.
End
FEATURE104 Rail Engineer | Issue 197 | Jul-Aug 2022
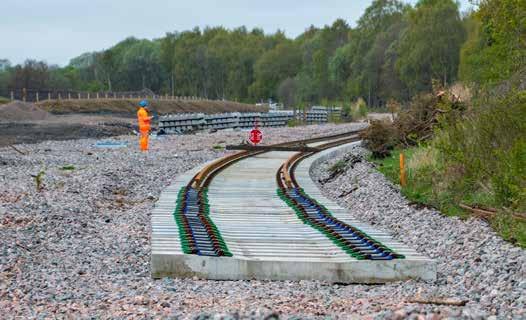
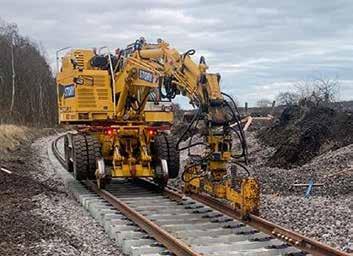
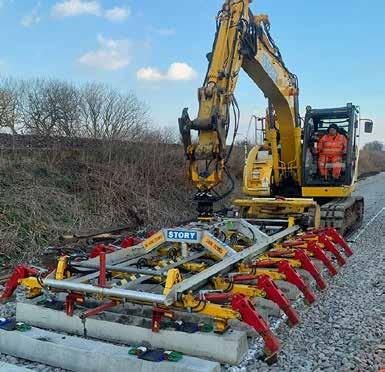
The final part of my visit is to see the work on a river underbridge which is one of five that needs repairs. Joe advises that the bridges are generally in good condition. They all need grit-blasting back to bare metal, recoated with a special paint system and new timber decks installed. This work requires the bridges to be fully encapsulated.
Engineer | Issue 197 | Jul-AugFEATURE2022 105
The Project 13 approach should build on this support to ensure that the new railway will provide the greatest benefit to the community with initiatives such as its STEM engagement.
A much-needed railway With much work already done, it is clear that the new railway is coming. This will become even more evident when track laying starts in October.Everyone we spoke to about this project advised that, in their experience, it is rare for everyone affected by a railway project to positively want it to happen. Hence the project has total support from the community.
As an example of the benefits offered by the new railway, Fife Council anticipate that it will generate investment equivalent to its £117 million construction cost. Although such benefits were clear to those who have campaigned for the re-opening for many years, it takes time to justify and approve the large cost of re-opening a railway. The railway will open during the tenth anniversary year of the LMRC campaign group. When the line does reopen, it seems certain that it will achieve its outcome of making “Levenmouth a better place to live, work and play.” Rail Engineer will return to Levenmouth to report on the progress with this new railway.
Rail
Bridge 2 before work starts and whilst encapsulated in May 2022. was the nearby Diageo distillery which is a lower tier COMAH (Control of Major Accident Hazards) site. As a result, the station had to be a minimum distance from this site.
Between Cameron Bridge and Leven is the Fife Heritage Railway’s premises at Kirkland. Part of this is being rented to the project for its main site offices. However, this did not stop the railway holding its annual Leven Car Rally there, for which Network Rail sponsored the overall winner’s prize. A connection is to be provided at Kirkland to provide passive provision for heritage and freight use. However, it seems that the line’s greatest potential for freight will not be realised as Diageo have indicated that it wishes to use Thornton Yard for its rail freight.



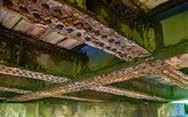
In a reflection of changing attitudes of the time, in 1918 a woman spoke at an IMechE meeting for the first time on ‘The employment of women in munition factories’. The Institution saw its first female member in 1924. ILocoE
Attracting the next Technicalgeneration.lecture at Birdcage Walk under George watchfulStephenson’seye.
FEATURE106 Rail Engineer | Issue 197 | Jul-Aug 2022
By the late nineteenth century there were around 1,200 mechanics’ institutes set up by public subscription and local benefactors. These provided classrooms and libraries to educate the working man to tend, repair and improve the complex machinery that
The following year this led to the formation of the UK’s second engineering institution, the IMechE, and the appointment of George Stevenson as its first president. In 1877, the IMechE moved from Birmingham to London, where it had built its current headquarters at Birdcage Walk, which opened in 1899. In 1909, the IMechE founded its first international branch in Kolkata, India, though UK local branches were not formed until 1920. In 1930, King George V signed the Institution’s Royal Charter allowing members to refer to themselves as Chartered Mechanical Engineers.
The IMechE’s Railway Division SHIRRESDAVID
This latest feature in our series on railway-related professional engineering institutions considers the Railway Division of the Institution of Mechanical Engineers (IMechE). Currently, there are 37 institutions licensed by the Engineering Council to register professional engineers. The Institution of Civil Engineers was the first, founded in 1818 with the aim of “directing the great sources of power in nature for the use and convenience of man.” In an age when everything was moved by muscle power, engineering was primarily concerned with the builtWithenvironment.therapiddevelopment of steam power, in 1846 a meeting was held in Birmingham to consider the formation of an institution made up of mechanics and engineers engaged in “Manufactories, Railways and other establishments”. The aim was to discuss and exchange ideas to improve knowledge across the various “branches of Mechanical Science”; and to give an “impulse to inventions likely to be useful to the world”.

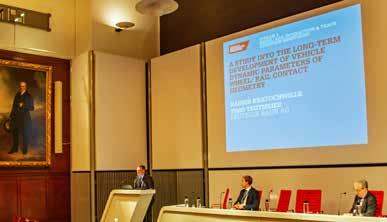
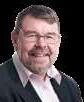

Six of ascompanies,manufacturinglocomotivefrompresidentstheclosereflectionpresidents,asalsoOliverStanier,Gresley,includingpresidents,ILocoE’stheNigelWilliamandBulleid,servedIMechEaofthelinkswithIMechE.OtherwereBritain’ssuchtheVulcanFoundry, Beyer Peacock, Hunslet, English Electric, and the North British Locomotive Company.TheILocoE responded to the many organisational, industrial, and technical changes faced by Britain’s railways. In 1948, nationalisation brought about common locomotive maintenance practices. This followed President Lt-Col Harold Rudgard’s address “Organising & Carrying Out of Examinations at Running Sheds in Relationship to Locomotive Performance and Availability”, which had outlined LMS practice which was soon adopted throughout British Railways. The 1950s onwards were a challenging time, with diesel and electric motive power replacing steam and the introduction of specialised rolling stock. The ILocoE provided support as its engineers adapted to these changes and, in 1957, widened its scope to include carriage and wagon engineering.Britain’sonce strong locomotive manufacturing industry had provided the ILocoE with a great deal of support. However, with its decline in the 1960s it became clear that the ILocoE could not continue as an independent body and so, in 1969, it became a new division of the IMechE. Programme for the ILocoE’s visit to the Brush Loughborough works in 1965 shows Class 47 locomotives under construction, the swansong of British manufacturing.locomotive Rail Engineer
1938 visit Scotland.to
| Issue 197 | Jul-AugFEATURE2022 107
Membership and activities rapidly expanded with the first regional centres being established in Leeds (1918), Manchester (1919), and Glasgow (1920). Presentation and discussion of papers at each of these centres was an important activity. From 1915 the papers were published in the ILocoE’s journal, which reported the discussions verbatim. By 1921, its membership numbered 1120 and the ILocoE had created a library. From the start, it ran a full programme of UK and overseas visits and social events, such as the annual luncheon. The ILocoE had a particular interest in overseas practice and developed international connections. Indeed, the first paper presented to it on 27 May 1911 was about French locomotive practice. Later that year there were visits to Belgium, Austria, and Germany. In 1920, the first overseas centre was established in Buenos Aires. Around this time ILocoE representatives were appointed in India, Nigeria, South Africa, and China. An important forum The ILocoE provided an important forum between Britain’s manufacturing industry and the engineers running its railways. Presidential addresses showing the value of this forum included those by Richard Maunsell (1916) and William Stanier (1938) who both highlighted maintenance problems from poor design. Maunsell’s strong views are reflected in his paper’s conclusion: “the engineer instinctively looks for the prominence of details which he knows should be accessible and he rightly regards as a monstrosity a machine which is lacking in this respect.”Meetings with railway infrastructure engineers date back to the first joint meeting with the Permanent Way Institution in 1928, when Harold Holcroft presented his paper “Some points of common interest in Rolling Stock & Permanent Way”. In 1949 the first meeting with the Institution of Railway Signal Engineers was held when author Oswald S Nock, presented his paper “The relationship between Signalling and Brake Power in the Handling of Modern Traffic”.
drove the industrial revolution. These institutes supported self-improvement groups, including those formed at major railway centres.
In 1909, the Stephenson Locomotive Society was formed to cater for railway institutes. However, some felt that the society did not adequately address technical issues and led a breakaway group to form a new society in 1911, the Institution of Locomotive Engineers. Its principal objective was “The advancement of the science and practice of Locomotive Engineering by enquiry, experiment or other means; the diffusion of knowledge regarding Locomotive Engineering by means of lectures, publications, exchange of information and otherwise; the improvement of the status of the Locomotive Engineer.”
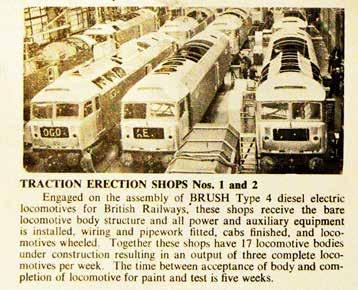
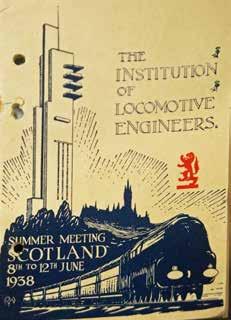
The Division also continued to present pertinent papers. With the new motorway network, railway engineers developed the Inter City 125 to combat increased competition from the car. The spirit of this time was exemplified by Bruce Sephton’s 1986 Chairman’s address entitled “Railways Do or Die?”. Today, the Railway Division has a membership of around 5,000 and runs an extensive programme of lectures and seminars at its HQ and seven Regional Centres (Midlands, Milton Keynes, North East, North West, Scottish, South East, and South West). It also has a young members section which runs a presentation competition for developing professionals, with a prize awarded for the best paper.
The Railway Division was formed around the time of the inauguration of the Britain’s first AC electrified inter-city services on the West Coast Main Line. With increasing electrification since then and, in recent years, the introduction of digital signalling, it is no longer appropriate to consider trains in isolation as the ILocoE generally did. With increased focus on whole system engineering, the Division’s focus reaches far beyond rolling stock and so considers issues associated with electrification and signalling. In this way, members of the Division are associated with all aspects of railway engineering and, generally, are no longer solely concerned with mechanical engineering. In 2012, the Division started to run its Railway Challenge. This was inspired by the Formula Student Challenge run by the IMechE’s Automobile Division. The challenge requires teams to design and build a 10 ¼ inch Inter City 125 on its farewell tour from Edinburgh Waverley in December 2019 after 40 year’s
Today’s Railway Division
Challenge.attentionLocomotiveservice.receivingattheRailway FEATURE108 Rail Engineer | Issue 197 | Jul-Aug 2022
The IMechE’s Railway Division continued the traditions of the ILocoE with a thriving programme of technical presentations, its annual luncheon, and technical tours abroad. With the globalisation of the rail industry, it arranged visits well beyond Europe to Singapore, Malaysia, USA, Japan, and China. These tours offer the opportunity to learn from foreign practice and had a mix of senior engineers and young engineers who would also learn from each other.
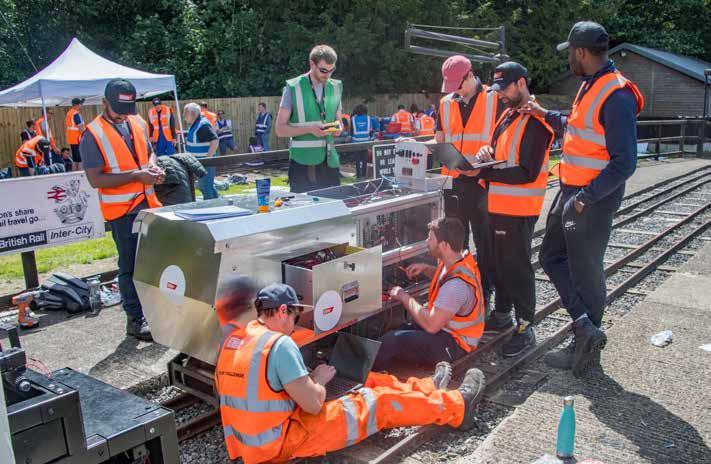
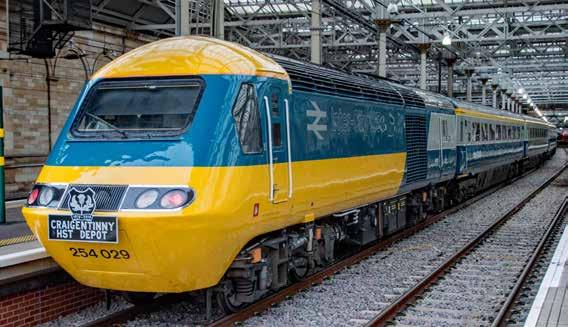
Two of its past chairs − Tony Roche and Carolyn Griffiths − have also become IMechE presidents. In this and other ways, the IMechE’s Railway Division is continuing the traditions which were started over a hundred years ago to promote railway engineering excellence as well as attracting and supporting the next generation of railway engineers.
Continuing traditions
gauge miniature locomotive. These are then put through a series of trials at the Stapleford Miniature Railway near Melton Mowbray which include traction, ride comfort and energy storage recovery during braking. The teams are also marked on the design of the locomotive and their business case presentation. In this way, these young engineers face many real-world operational, design, and project management problems. To date, 70 teams have participated in the 10 challenges that have taken place in late June. This has provided around 500 young engineers with a great opportunity to gain experience of technical and organisational skills such as project management and team working in a tight time frame.
2022 Annual technical tour participants at CAF’s Newport plant. www.railuk.com happens.
Over 15,000 rail articles. Rail Engineer | Issue 197 | Jul-AugFEATURE2022 109
The IMechE’s Journal of Rail and Rapid Transit attracts research papers from around the world and complements more general presentations at Railway Division meetings. During the Covid pandemic these were held online with the result that recordings of these events are available online in the Railway section of the IMechE’s Webinar Hub. The Division continues to act as a learned society promoting best practice in railway engineering, including new rolling stock, international standards, and research and development. Its programme encourages the development of today’s engineers, as does its annual technical tour and prizes awarded for papers and innovations. The Division’s popularity is such that its annual luncheon is held in London’s only hotel that can provide for over a thousand attendees.
Latest rail video. Daily email update. UK rail news as it
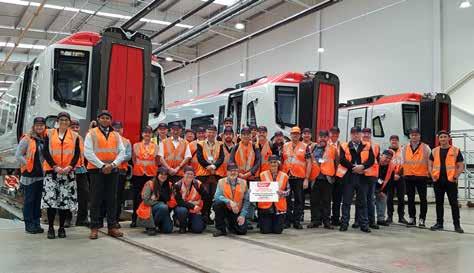
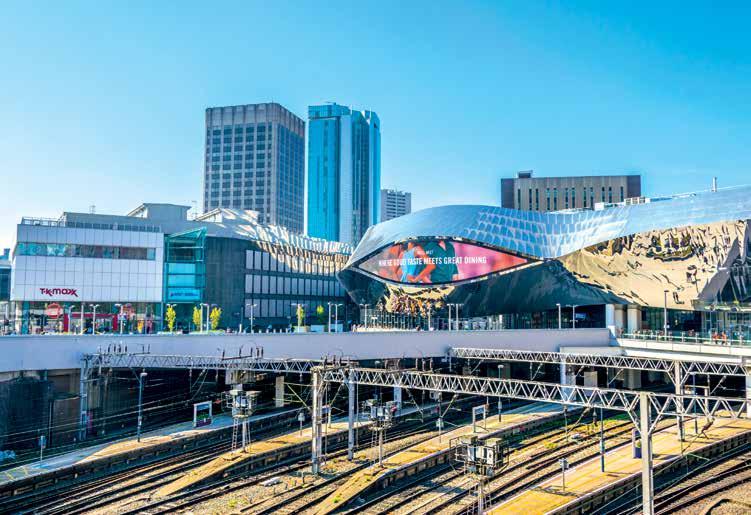
In 2020, the exhibition became one of the many casualties of the covid outbreak and was initially pushed back to April 2021. However, as the pandemic dragged on it was again postponed, this time for a further 18 months down the line. Thankfully, it will now go ahead in a world where the threat of covid and its accompanying restrictions are muchInnoTransreduced.2022 will be a bumper event. In 2018, the exhibition attracted 3,062 exhibitors from 61 countries, presenting their latest innovations to 153,421 trade visitors. Bookings for floor space at this year’s exhibition surpassed 2018 totals over 12 months ago, and 98% of the display area was booked up by the start of 2022 – an impressive feat given that 10,000m2 of space has been added to the exhibition grounds since the last show.
The exhibition − one of the leading items in the transport technology calendar – runs for three days till 23 September and is set to be a huge occasion.
INNOTRANS110 Rail Engineer | Issue 197 | Jul-Aug 2022
InnoTrans is back!
After a four-year wait, InnoTrans is back and will open at Berlin’s ExpoCentre City on 20 September.
The theme of this year’s event is ‘The future of mobility in times of climate change’, a particularly pertinent topic after Europe’s record-breaking heatwaves have caused havoc for the continent’s transport systems.
Future of mobility
As always, the exhibition will open with a panel discussion featuring high-profile politicians and industry players, and invitations have been extended to more than 1,000 senior national and international figures. Federal Minister for Digital and Transport Dr. Volker Wissing will welcome the international visitors to this year’s event and European Commissioner for Transport, Adina Vălean, is also expected to attend.
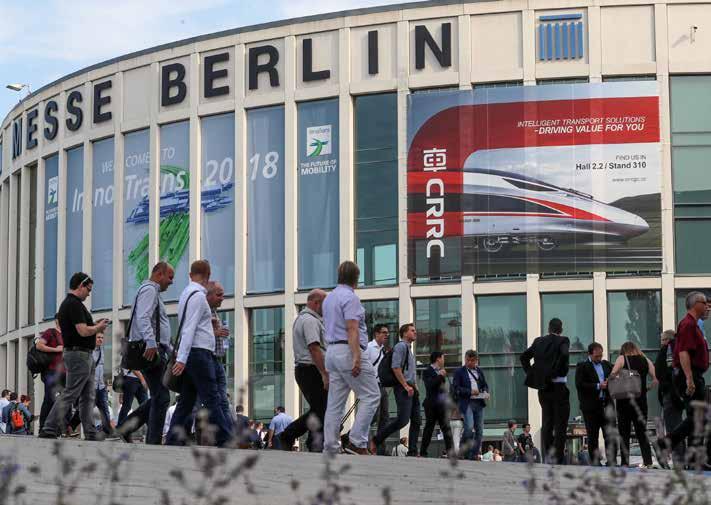
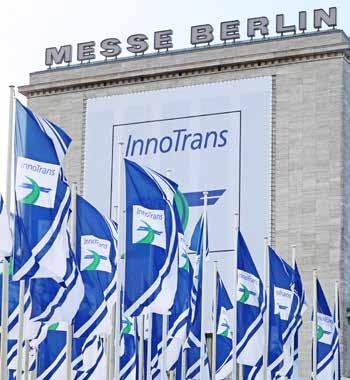
–
Eurailpress
RecruitingLAB |
More information at innotrans.de/en/campus Apply now Pick up a job! Career Boost only on 21 September, 2:00 p.m. Talent Stage
Ready for a career in the mobility industry?
Associations from across the globe will represent the industries of their respective countries, including Swissrail (Switzerland), MAFEX (Spain), JORSA (Japan), ARIA (South Africa), CAMET (China), CRIDA (Taiwan), KORSIA (Korea) and ALAF (Argentina). Taking part for the first time will be the International Monorail Association, an association dedicated to promoting the monorail sector worldwide.
The outdoor display is the highlight of the show. Vehicles will be presented on tracks located directly adjacent to the exhibition halls. From high-speed trains to hybrid locomotives; road-rail vehicles to trams – this is where manufacturers present their new products to the trade public. This year, exhibitors will show over 100 vehicles, all pushing the envelope of rail innovation.
| Jobwall | Career Tours | Reduced student tickets INNOTRANS 111 Rail Engineer | Issue 197 | Jul-Aug 2022
Furthermore, a combined stand featuring Zeleros Hyperloop and Hardt Hyperloop will present the latest developments in ultra-fast overland hyperloop transport systems for passengers and freight.
–
Currently, the following industry figures are also scheduled to attend: Dr. Richard Lutz, CEO of Deutsche Bahn AG; Peter Spuhler, CEO of Stadler Rail; Henri Poupart-Lafarge, president of Alstom Transport S.A.; and Michael Peter, CEO of Siemens Mobility GmbH.
Exhibition space InnoTrans extends across the grounds of ExpoCentre City, occupying forty-two halls and an outdoor display space – a total area of 200,000 m². To ensure that exhibitors and visitors are able to keep their bearings, the exhibition is divided into five segments: Railway Technology; Railway Infrastructure; Public Transport; Interiors; and Tunnel Construction.
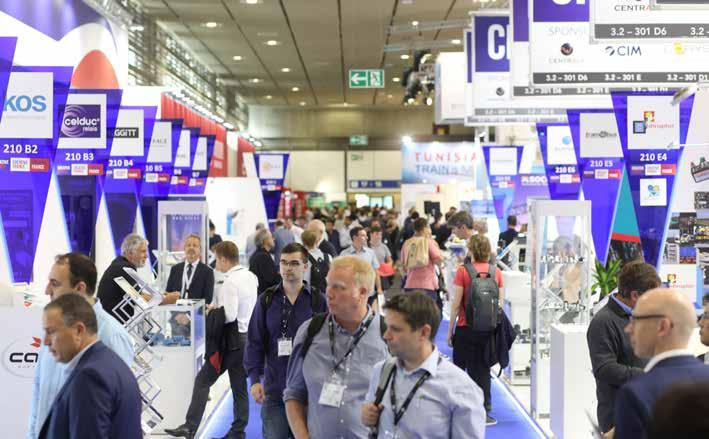
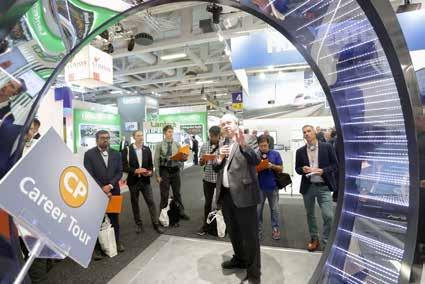
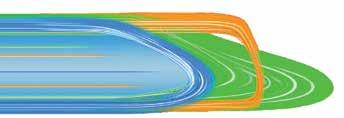

New for 2022, the Mobility+ Corner in Hall 7.1c will feature lectures on the future of multimodal transport, include smart charging infrastructures, digital passenger data surveys and the future of public transport.
» Public transport and interiors
» Railway infrastructure and tunnel construction Looking forward Bringing together visitors and exhibitors from around the globe, the size and scope of InnoTrans cements is reputation as one of the most important events on the rail industry’s exhibition calendar. Showcasing the latest innovations from industry’s top names, along with its smallest players and all those in between, the event provides a snapshot of current thinking and technological progress. As a key forum for networking and discussion, InnoTrans will explore the most prominent challenges facing the transport sector and encourage dialogue to provide solutions.InnoTrans 2022 takes place from 20-23 September. For further information and to purchase tickets, visit www. innotrans.com.
Siemens Mobility and Deutsche Bahn are presenting the H2goesRail project and the Mireo Plus H, a new generation of fuel cell-powered trains. Stadler is taking part with seven vehicles this year and Tatravagónka, a goods wagon manufacturer from Slovakia, is planning to make a big appearance with six vehicles supplementing its hall stand.
INNOTRANS112 Rail Engineer | Issue 197 | Jul-Aug 2022
» Railway technology (energy and electrical engineering)
» Railway technology
» Railway technology (drive and bogies)
Mirko Ross, cybersecurity expert and CEO of asvin GmbH, will hold a lecture on the security challenges of intermodal mobility. Visitors to the trade fair can also try out some of the solutions on their way to the exhibition grounds or in Berlin’s city centre. Innovation tours To complement this packed itinerary, visitors can also experience the latest rail breakthroughs at first hand on one of the exhibition’s World Innovation Tours. Senior company representatives will be on hand to welcome participants to their stands, where they can discover everything about their latest innovations. There is, of course, also the opportunity to ask questions.Tourswill run several times a day, lasting around 90 minutes taking in 10 stops. Visitors will be provided with headsets for translation. The tours will be broken down into area of interest which will include:
Trade visitors can also look forward to presentations from Alstom, Siemens, Vossloh, Plasser & Theurer and many other major exhibitors.
Conference corner Innotrans has hosted the Conference Corner since 2016. This event, which features lectures and conferences organised by travel organisations and companies, takes place from the final day of the exhibitions, onwards. This year, the Hyperloop Conference will take centre stage. As the first international conference on high-speed transportation worldwide, it will feature a wide range of formats and topics surrounding ultra-highspeed transportation. The event will include keynote speeches, panel discussions, masterclasses, and Q&A forums focusing on the challenges that the hyperloop eco-system poses for mass transit, and the challenges for goods transport.

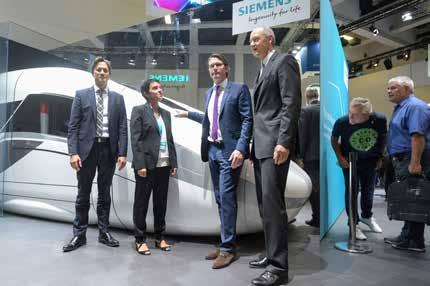
way People visit: www.RailwayPeople.com / email: rp@rail-media.com / telephone: 01530 816 450 job board in the UK. How can it help me? With the top career opportunities updated daily, your next move is a fingertip away. What should I do? Visit RailwayPeople.com today to find your next role and become an essential part of the UK’s rail industry to help the nation build back better. 01483 361 061 | info@advance trs comA D V A N C E T R S C O M D E S I G N V E R I F I E R S L E A D P R O J E C T M A N A G E R S ALSTOM AND ADVANCE TRS RECRUITING IN THE RAIL INFRASTRUCTURE SECTOR ACROSS THE UK Q U A N T I T Y S U R V E Y O R S Advance TRS are currently recruiting on behalf of Alstom for projects across the UK with key areas of focus in York, Derby, Birmingham, London and Bristol If you are looking for your next opportunity and are interested in working on major rail infrastructure upgrades for Alstom with the latest technologies contact our team today DERBY BRISTOL BIRMINGHAM YORK HATFIELD CAREERS 113 Rail Engineer | Issue 197 | Jul-Aug 2022
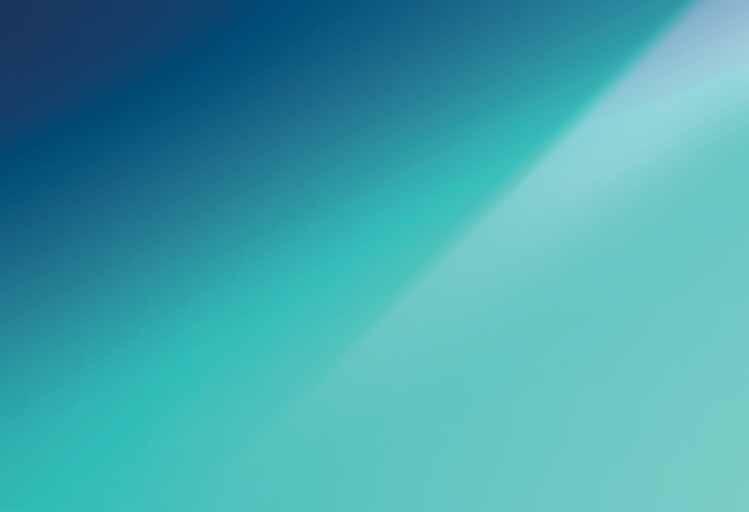

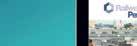


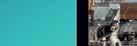
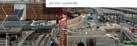

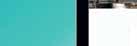
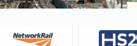
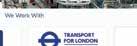
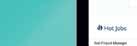
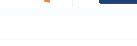

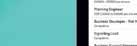
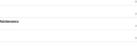
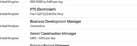


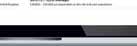
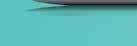

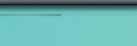
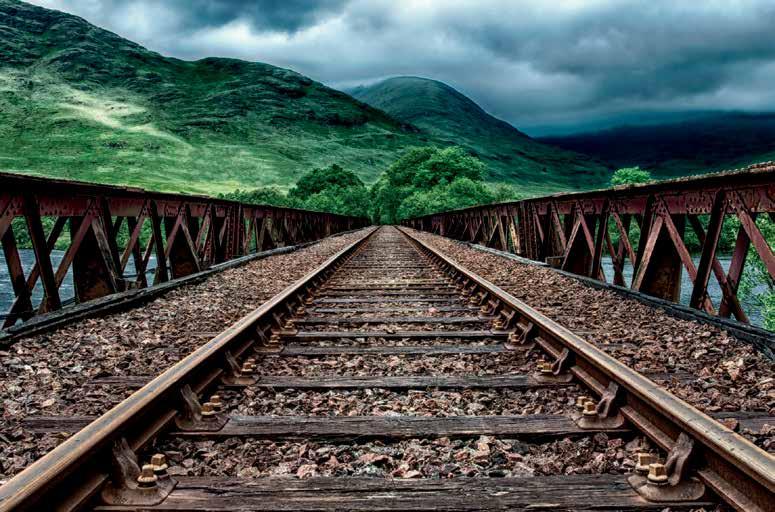
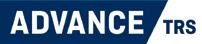
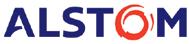
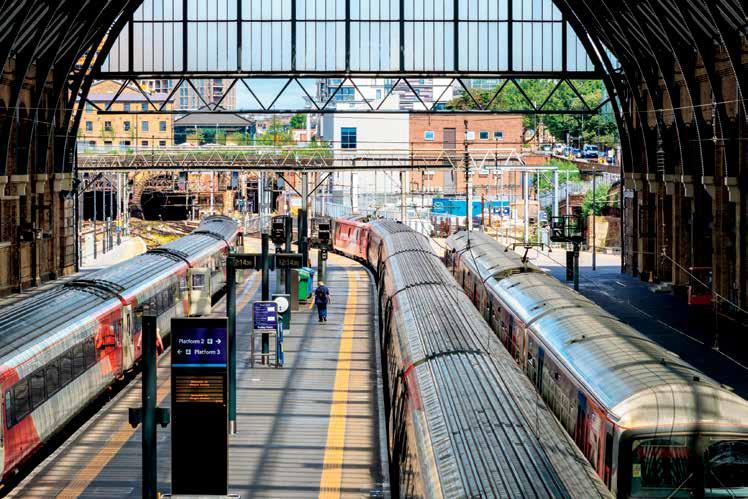
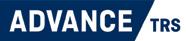
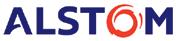
NSAR AssessorsTrainersApproved/ Nationwide OpportunitiesCareer Due to exciting growth and further expansion, Intertrain, part of
We offer full-time, permanent contracts. You will receive a competitive salary, life assurance cover, company car, and corporate bonus. You will also benefit from the additional leave during Christmas shutdown.
Intertrain, part of City & Guilds was established in 1997 and is the UK’s largest commercial railway infrastructure training provider, with training centres across the country. As part of your role, you will assess the learner’s progress and maintain accurate records of the assessments of learning carried out, the learner’s journey, achievements, and feedback.
currently have several permanent vacancies for qualified NSAR
We are opening new training centres nationally and we are keen to hear from you!
We are looking for professional, committed, and passionate NSAR Approved Trainers / Assessors with solid occupational experience to join our team.
If you are interested in joining our expanding professional team, please apply by email with your CV: careers@cityandguilds.com or to apply online please visit: www.intertrain-careers.co.uk
Some of our industry leading training centres are based in Doncaster, Warrington, Portsmouth, Bristol, Birmingham, Crayford and London. City & Guilds Approved
Trainers / Assessors. We hiring!are
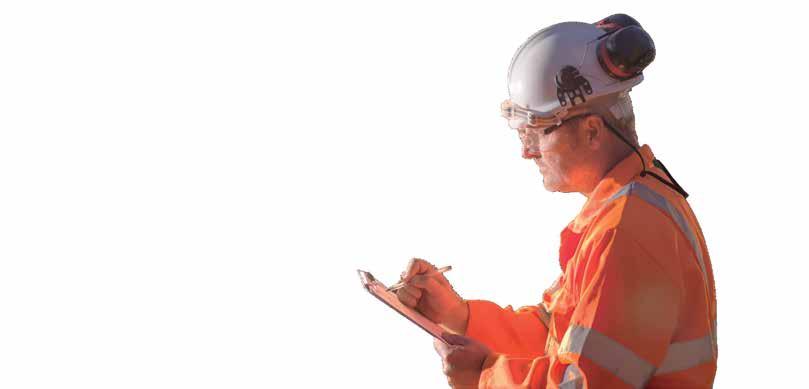
www.colasrail.co.uk Joining Colas Rail UK provides the opportunity to not only establish yourself within one of the biggest contractors in the rail industry, but also the springboard to take your career to new heights. We’re always looking for passionate people to join our business and with several bases across the UK, there are plenty of opportunities to join our Railway family. We offer an attractive salary and benefits with a culture of can do, empowerment and flexibility, to allow you to make a real difference. We would like to hear from people who would like to work in the rail industry. Please register your interest by sending your CV to recruitment@colasrail.com and we will provide you with further information. Training will be provided to successful candidates. » FITTER OPERATORS UK MOBILE » MAINTAINER / OPERATOR UK MOBILE » MULTI SKILLED DRIVER CONDUCTOR UK MOBILE » TECHNICAL SUPPORT ENGINEER UK MOBILE » HEALTH & SAFETY ADVISOR RUGBY » SAFE WORK PACK ADMINISTRATOR RUGBY » STORES OPERATIVE RUGBY » STORES BUYER RUGBY We are constantly looking for new talent to strengthen the Colas Rail UK team. Our people are our strength, and everyone working for Colas Rail UK plays a vital part in the company’s success. DRIVEN CHANGEBY Join Our Rail Grinding Team Career Opportunities Include: CARE | SHARE | DARE
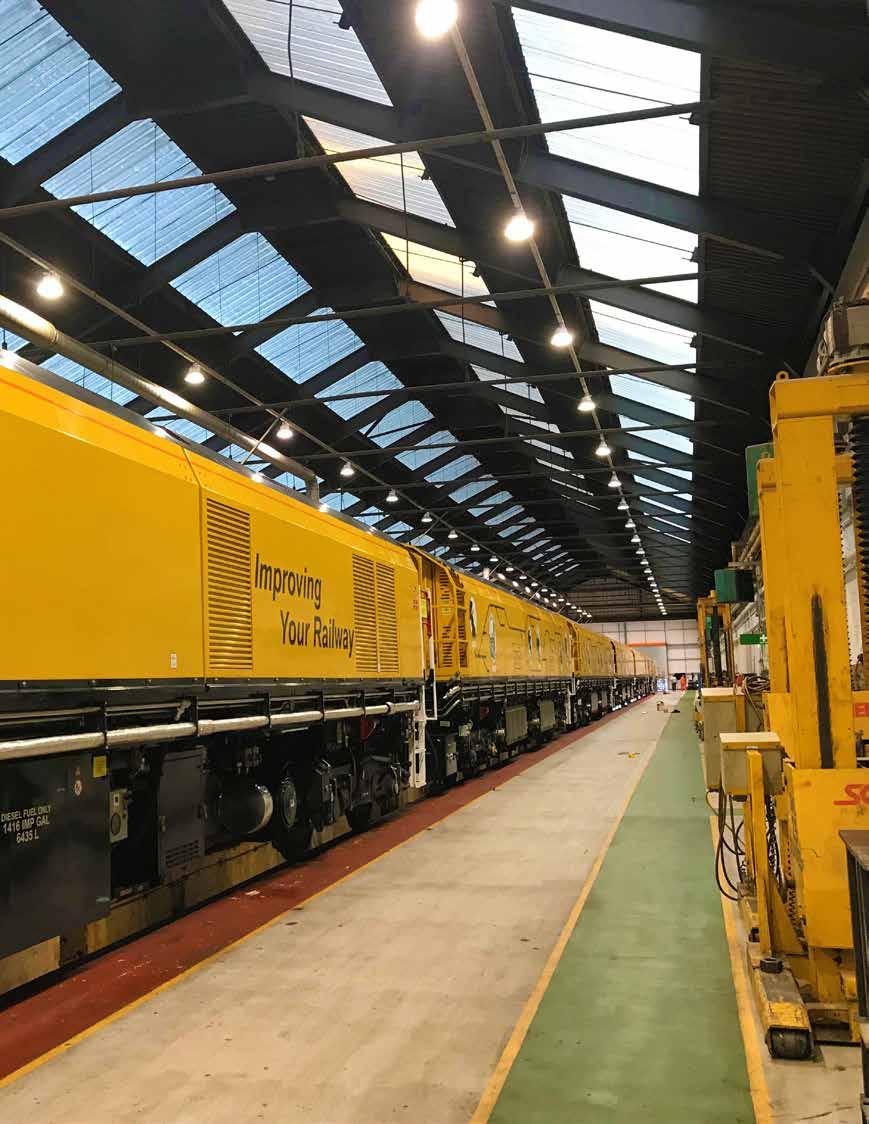
People for Infrastructure Call now 0845 543 5953 info@mcginley.co.uk Scan tme o lview ive roles. McGinley hires workers or finds permanent employees for companies in the infrastructure sector of the construction industry, building and managing workforces all over the UK Whether you are looking for a job or a supply chain partner, we have the knowledge and expertise to help you succeed As true infrastructure experts we have over 40 years ' experience and an unparalleled network. This combined with a large number of accreditations, memberships and awards give you the confidence you need to engage with us. • PTS & safety critical contingent labour • Signalling & telecoms • Overhead line electrification • Track welding • Minor works packages • Flexi-jobs apprenticeships WE ARE RECRUITING

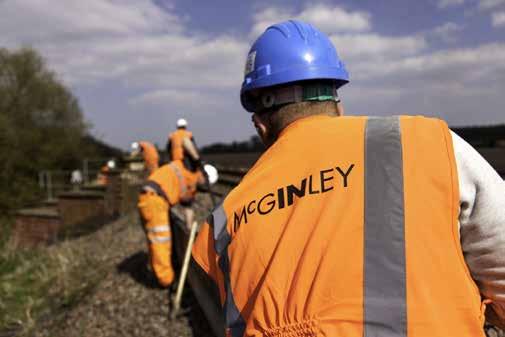

