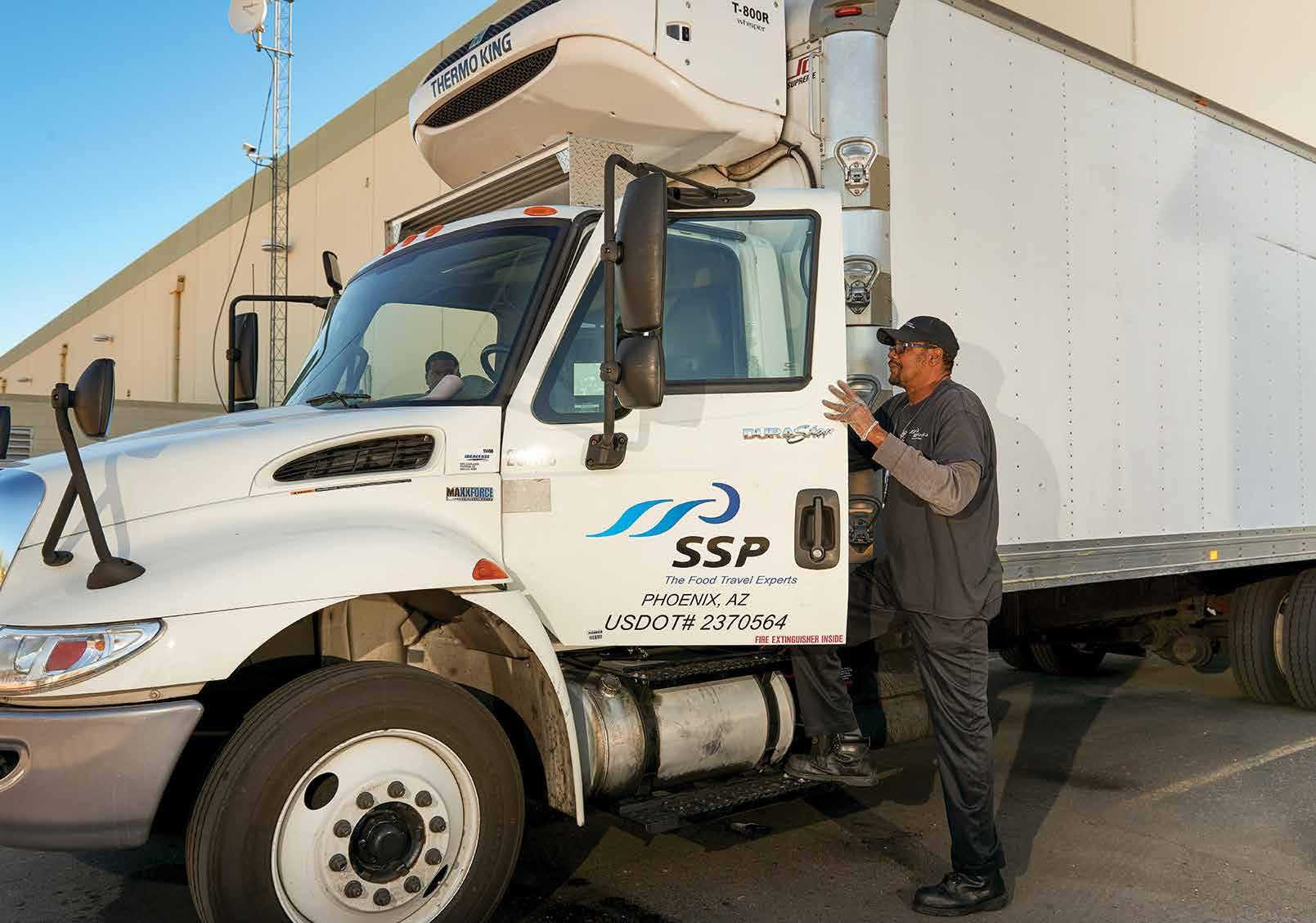
9 minute read
Chain, Chain, Chain
SUPPLY CHAIN STRUGGLES
Shortages And Delays Are Keeping Concessionaires On Their Toes
Advertisement
BY SALLY KRAL
The supply chain affects just about every aspect of our everyday lives. When all is going well and the supply chain is running as intended, it’s not something we even notice. That has changed dramatically since the COVID-19 pandemic hit.
“I think most people right now can relate to the situation of going to the store and they’re either out of the products you need or they’re not in the right size or your preferred brand,” says Patrick Murray, executive vice president of SSP America. “Right before Thanksgiving, my wife sent me to the grocery store for sage and rosemary and neither was on the shelf.”
Murray points out that there’s a lot behind those herbs, from the farm where they’re grown to the packaging facility to the distributor to the produce company which ultimately gets them to stores and restaurants. “Every one of those businesses requires
MAIN CAUSES:
Many cite the labor shortage as the main cause of the current supply chain disruptions happening all around the world, though the spike in product demand has contributed as well.
BEST PRACTICES:
Swift adaptation has been the key to navigating supply chain issues. Sourcing substitutions for out-of-stock product, building up inventory and enhancing internal forecasting efforts are just some of the ways that concessionaires are remaining agile, flexible and creative in the face of these disruptions.
HARDEST HIT ITEMS:
Concessionaires are facing shortages of all types of products, including proteins like chicken wings and ground beef; packaging and disposable products; foodservice equipment; and construction materials like concrete, steel, copper and PVC products.
DOMESTIC VS. IMPORTED GOODS:
Imported furniture, fixtures and equipment are typically more affordable for concessionaires to source, but with shipping issues and port delays causing much longer lead times for these items, some businesses are transitioning to domestic goods, which are often costlier but are more readily available.
TECH SOLUTIONS:
The supply chain is currently reliant on many human-centered processes and stands to benefit from more automation and tech solutions, especially in the face of the current labor shortage.
human beings, and every one of those businesses is severely challenged right now,” he says. “So, it’s really affecting every component of our lives.”
Indeed, from an individual not being able to find the herbs they’re looking for while grocery shopping to a multinational chain like Wingstop not being able to procure chicken wings and instead pivoting to selling chicken thighs, supply chain challenges are showing up everywhere. That includes airports.
“These issues are like nothing we’ve seen before,” says Claude Guillaume, senior vice president of restaurant operations for Paradies Lagardère. “It has impacted an extremely high percentage of our items or needs in both our retail and dining operations over the course of the past year. Like many retailers and restaurateurs, our airport operations have dealt with delayed shipments, unavailable products, cancelled orders and so many other challenges.”
And like many things right now, the future of the supply chain remains unknown. “Something like this just cuts so deep,” Murray says. “It has reverberations in the business that are going to take us quite a bit of time to work out.”
Root Causes And Main Effects
For SSP America, basic food items like hamburger buns, hamburgers, French fries and chips, as well as packaging materials for these items, are some of the hardest hit by delays. “Every one of those things is experiencing some element of a breakdown right now,” Murray says.
He notes that the biggest challenge the company has faced has been over the past several months, as New York, Chicago, San Francisco and Seattle have all had major disruptions in their distribution centers. “Seattle recently went 13 days without a delivery – our business in Seattle generally takes two tractor-trailers a day to our remote commissary,” Murray says. “So, we were literally sending out our trucks to go shopping at Costco and Sam’s Club, and if need be, the smaller grocery stores, just to have products to be able to sell in the airport. And, of course, they’re not the right products, they’re not sized correctly. If the recipe on the wall for a cook says these French fries get cooked for 30 minutes but the ones we bought at Costco are actually thicker, that presents a problem.”
Murray points to the labor shortage as the biggest cause of the supply chain breakdown. “You have fewer people working in every capacity; it’s almost like the economy tapped the brakes and everybody just slowed down,” he says. “And somehow we’ve got to grease the skids and get us back up and going again because we’re just not quite there yet.”
Regina Chin, vice president of supply chain and quality assurance for HMSHost, notes that the three components of supply chain issues are product availability, transportation of product and labor – and that, indeed, labor is the main sticking point right now. “The labor shortage coupled with the spike in product demand has created this situation,” she says.
She adds that for HMSHost, bottled beverages, disposables and proteins have been the most impacted. “Suppliers are having a hard time getting raw materials to produce PET plastic bottles. Likewise, there’s a short supply of raw materials for disposables and an increase in demand, making it difficult to procure cups and containers. We’ve also seen an increase in prices and a lack of availability of many proteins because there is little to no automation in meat processing. The labor shortage has had an immediate and damaging effect on item availability for products like chicken wings and ground beef.”
Kris Irwin, vice president of design and construction at Delaware North, notes that the products that have been the hardest for the company to come by have been foodservice equipment, which often has shortages of certain parts, as well as construction materials like concrete, steel, copper and PVC products. “And then there are the shipping issues, whether from delayed off-loading at ports or not having enough drivers once product is ready to ship.”
Aaron Bonham, chief merchandising officer for Paradies Lagardère, notes that two areas that have been particularly difficult for the company are imported products and items from larger domestic manufacturers where there’s competition with big box retail. “From actually finding items to order to having those delivered in a timely fashion, almost each day presents its own trials,” he says.
Best Practices And Possible Solutions
Andrew Weddig, executive director of the Airport Restaurant & Retail Association (ARRA), notes that adapting quickly to new circumstances has been key to concessionaire survival. “Since supply chain challenges are generally one-of-a-kind and unforeseen, responses are necessarily reactive,” he says. “Honing one’s ability to adapt – that is, to be agile, flexible and creative – is really the only tactic there is.”
Indeed, navigating the supply chain over the last year or so has been an ad hoc experience, Murray says. “We’re trying to learn from everything that has happened in the past and assume that it will happen again so we can predict the best-case scenarios to solve those things.”
He adds that at SSP America’s large operations around the country where storage is available, they’ve been stocking up as much as possible on frozen and non-perishable goods. “But there are still places where that’s not so easy, where there’s not enough to buy. So even if you want to stock up on them, you can’t.”
Irwin says that some tactics Delaware North has taken from the start include constantly leveraging the company’s relationships with vendors to mitigate shortages and delays, plus locking in purchase orders early to alleviate inflationrelated cost increases.
HMSHost, too, has been working closely with vendors to stay up to date on product and labor shortages so the company can adapt accordingly. “We moved quickly with
Left: Similar to “street” operators, airport concessionaires are facing significant supply challenges that are exacerbated by labor shortages.
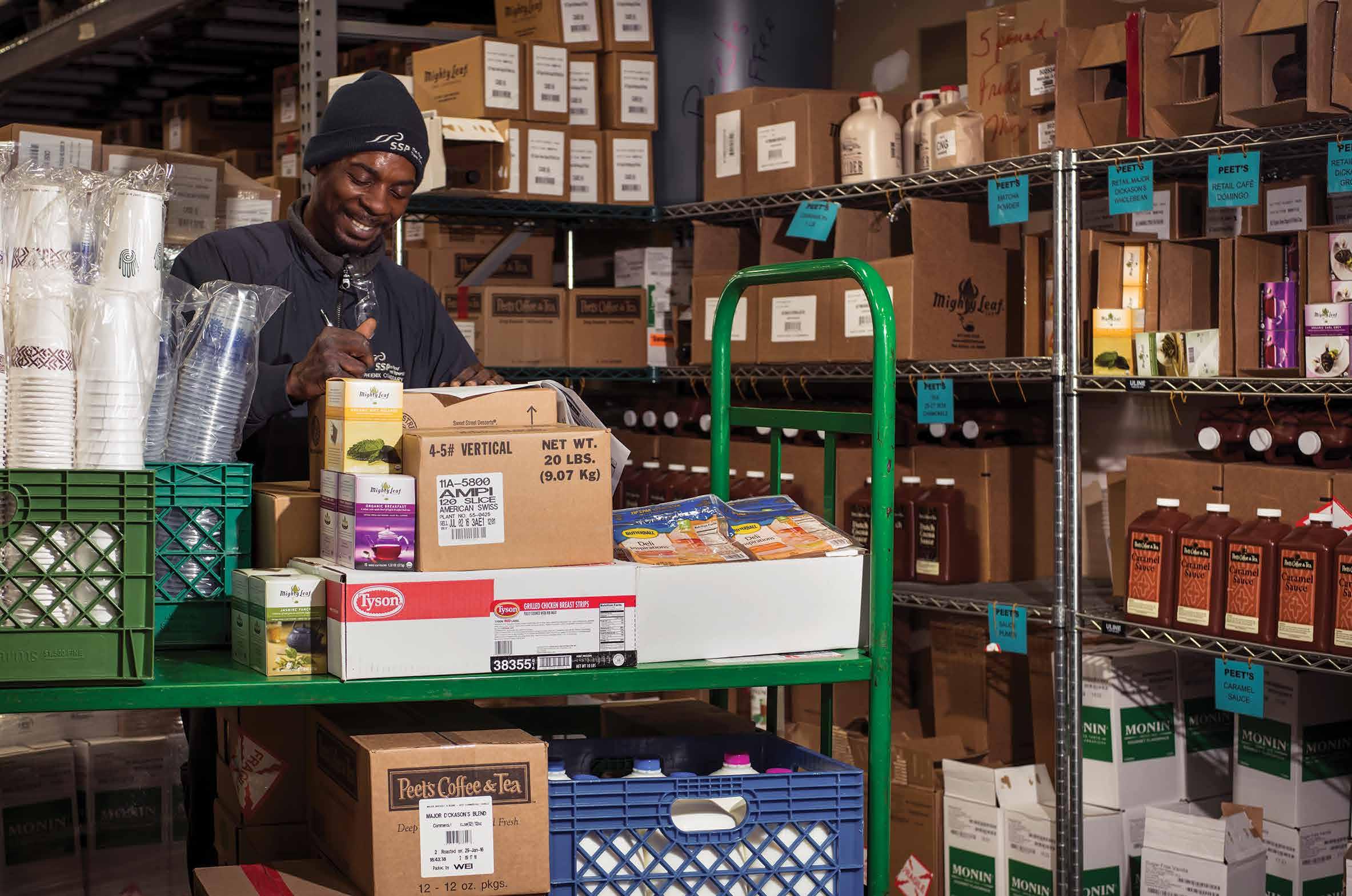
our vendors to identify substitute products and find new vendors that offer similar products and are less impacted by supply chain shortages,” Chin says. “We’ve also been working with our current suppliers to provide modifications to contracts that allow us to purchase competitor products due to their shortages.”
Chin adds that she’s seeing manufacturers actively working on reducing lead times by locally sourcing raw material and analyzing opportunities to bring overseas production to the U.S. to mitigate long lead times and the growing concern of freight increases.
Finding the right balance between domestic furniture, fixtures and equipment and imported ones has been another strategy of Delaware North. “We’ve had to consider the tradeoff between sourcing domestic or North American products, which typically cost more but are available sooner, versus imported products, which are often cheaper but with longer lead times due to shipping issues and port delays,” says Gonzalo Checa, the company’s vice president of category management.
Paradies Lagardère’s Bonham notes that transitioning from import to domestic supply sources to cut down on delivery distances is one of four key initiatives in the company’s multi-pronged approach to mitigating supply chain issues. “Switching to domestic products where possible has been mostly relevant for our retail operations, but in our dining operations we’ve re-engineered menus to provide offerings from a list of items more readily available,” he says. “Additionally, we’ve expanded our grab-and-go programs, which was a category that was on a strong growth track even prior to the pandemic.”
The other initiatives in Paradies Lagardère’s approach include finding comparable products to substitute for items that are unavailable; committing to an even greater level of anticipation of needs through trends and sales reporting; and building inventory levels in the company’s airport locations to the best of their ability. “The earlier-than-normal orders and a strong on-site inventory base alleviates the pressure from slower delivery schedules or supplies that are completely out of stock at times,” Bonham says. “In general, extreme flexibility has been key to our efforts.”
Bonham adds that as a “side solution” to supply chain woes, the company has expanded their service levels in stores and restaurants with contactless order and payment options. “From our Scan, Pay & Go and self-checkout kiosks in our retail stores to mobile order and pay options on the Grab app in our restaurants, we’re helping travelers navigate their transactions
Above: With product shortages rampant, many concessionaires are stocking up as much as possible on frozen and non-perishable goods.
more easily, which adds value to the customer interaction and helps relieve a perception of product shortages.”
Chin believes that the supply chain is too reliant on many human-centered processes and needs automation technology. “COVID-19 outbreaks in plants continue to shut down operations for days, making it impossible to break the cycle of issues,” she says. “Still, our hope is that these issues improve each quarter and things are normalized by the first quarter of 2023.”
Paradies Lagardère’s Guillaume, too, hopes and expects supply chain issues to subside over time. “However, there’s such a domino effect in the supply chain process that a full ‘return’ will take some time,” he says. “Like when facing most challenges, we’ll continue to adapt so we can keep a normal cadence of operations, but we’ll also use the situation as a learning opportunity to discover previously unrecognized advantages that may evolve into more permanent efforts rather than temporary fixes.”