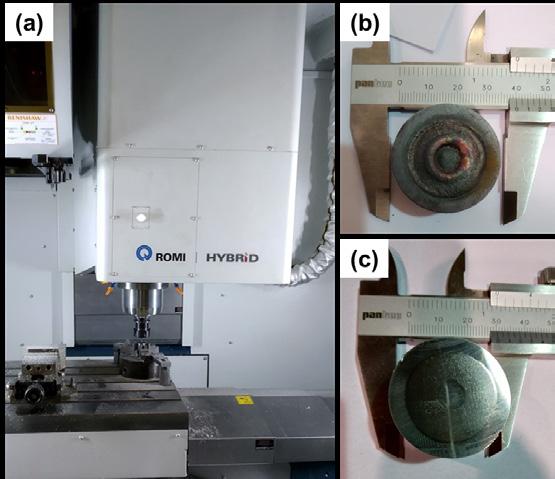
16 minute read
PROCESSOS
O CAM NÃO É MAIS SOMENTE UM CAM
POR SKA
Advertisement
Como assim “o CAM não é mais somente um CAM”? Muitas vezes, classificamos o CAM apenas como uma ferramenta de apoio para os programadores ou operadores de máquina criarem as programações de suas peças. Com geometrias cada vez mais complexas e máquinas e dispositivos seguindo a mesma complexidade, o uso de uma ferramenta assim é indispensável para alcançarmos o máximo de possibilidades e eficiência do setor.
E SE O CAM PUDESSE AUXILIAR NÃO SÓ O SETOR DE PROGRAMAÇÃO DE FORMA DIRETA, MAS SIM TODA A EMPRESA? Podemos começar falando sobre o processo de atualizações de projetos dentro da engenharia. Como essa informação de uma nova revisão chega ao programador/operador?
Com a utilização do CAM, assim que o modelo é atualizado ou alterado, uma mensagem é gerada dentro da tela do software para informar o usuário. O programa, de forma simples e nativa, pode recalcular seus percursos de acordo com a nova geometria e, assim, gerar um novo código atualizado e homologado para esta nova revisão sem a interferência de nenhum outro sistema periférico.
O que temos aqui nada mais é do que um dos pilares da indústria 4.0: a integração entre sistemas, que acabará diminuindo os ruídos de comunicação e consequentemente o refugo de peças produzidas fora de revisão.
COMO SE PREPARAR PARA A PRODUÇÃO Continuando no processo de integração e compartilhamento de informações, cada vez mais uma máquina CNC precisa estar preparada para executar a sua função principal, que é produzir. Mas de que forma estamos preparando o nosso setor para liberar a máquina para esta função? Que tipo de documentação estamos criando? Como estamos compartilhando e para quem?
Com a geração das folhas de processos, podemos adicionar todos os dados de ferramentas, presets, dispositivos, particularidades e qualquer outro tipo de informação pertinente ao processo em uma página da intranet de simples compartilhamento. Assim, os setores responsáveis pela preparação do ferramental podem preparar tudo o que for necessário para a troca rápida em máquina.
Como qualquer computador que estiver conectado à rede da empresa pode ter acesso ao visualizador, podemos disponibilizar também ao operador da máquina as mesmas informações para que o próprio try-out seja mais ágil em sua validação. Com a validação virtual no software de simulação 3D, preparação das ferramentas de forma externa à máquina e informações de como cada processo será executado, a segurança na execução é aumentada de forma significativa deixando a máquina parada o menor tempo possível.
PLANEJAMENTO É A CHAVE E como falamos novamente de outros setores, por que não compartilhar com o PCP o tempo de usinagem de um item para que todo o dia/semana/ mês da máquina possa ser planejado e sequenciado?
Com ferramentas como o SYNECO Planning, o programador e o operador podem ter em suas mãos a sequência das atividades, garantindo não somente os objetivos em relação aos prazos, mas também que todos os pré-requisitos necessários às execuções estejam disponíveis. Novamente, estamos falando de sistemas de integração e agora também, adicionamos mais um dos pilares da indústria 4.0: o big data.
Então, podemos afirmar que um software de CAM não é somente um software de CAM para gerar caminho de ferramenta. Ele é sim uma ferramenta para auxiliar toda a empresa com informações, dados e recursos para melhorar a produtividade do chão de fábrica e de qualquer outro setor em que ele possa ser integrado.
Em seus mais de 30 anos de história, muito mais do que softwares, a SKA sempre se propôs a entregar soluções e, assim, conquistou mais de 5.000 clientes em todo o país. A Indústria 4.0 já é realidade, mudou a forma de pensar das engenharias e manufaturas, e impacta empresas e processos. A SKA acompanha estas mudanças e traz um novo olhar sobre a engenharia, promovendo uma forma contemporânea de conceber produtos, de organizar processos, de evoluir etapas. Na manufatura, concebe novas formas de utilizar recursos, otimizando tempo, custos, espaço, tornando a cadeia mais sustentável e preparada para o próximo passo. Mais do que oferecer softwares líderes de mercado e desenvolver soluções personalizadas, a SKA se propõe a agregar soluções, promover o desenvolvimento, construir relações para juntos caminharmos rumo a nova era da indústria brasileira. ska.com.br
AVALIAÇÃO DE VIABILIDADE DO PROCESSO DE MANUFATURA ADITIVA HÍBRIDA (MÉTODOS ADITIVO E SUBTRATIVO) PARA O REPARO DE FERRAMENTAS
POR VÁGNER BRAGA - DIEGO TOLOTTI DE ALMEIDA - ANGÉLICA P. DE OLIVEIRA JEAN F. DA SILVA - CAROLINA A. C. DE SOUZA - MILTON S. F. DE LIMA
AManufatura Aditiva (MA) representa a quebra de um paradigma de desenvolvimento e fabricação de produtos na indústria global. Devido a agilidade, precisão e eficiência econômica na customização de peças em comparação com outros métodos de fabricação, há um eminente interesse em aplicações inseridas no contexto das indústrias aeroespacial, de energia, biomédica, automotiva e na reparação de danos em moldes e matrizes.
Os processos de reparo convencionais nas indústrias metalmecânica apresentam limitações consideráveis, sobretudo no que diz respeito ao acabamento do reparo, custo e tempo de processo. Em alguns casos, todo o ciclo de reparo é tão longo e caro que as peças danificadas são simplesmente descartadas. Portanto, métodos de reparo eficientes são extremamente importantes, visando a introdução de uma técnica de reconstrução rápida, ambientalmente correta e de baixo custo.
Por sua vez, a manufatura aditiva fornece a adição controlada de material em camadas a um determinado substrato a partir de um projeto e seleção de materiais no desenvolvimento de um componente por meio de um modelo geométrico computacional 3D. A técnica de deposição de metal a laser (Laser Metal Deposition - LMD), utilizada no presente estudo, é extremamente eficiente em termos de reparo de moldes e matrizes, ou mesmo quando novas peças precisam ser acopladas a peças danificadas.
Paralelamente, o pó metálico de H13 atomizado usado em uma ampla gama de processos envolvendo manufatura aditiva deve ser testado e avaliado antes de ser utilizado em um processo de fabricação. Portanto, foram estudados a microestrutura e aspectos termodinâmicos da interface deposição-substrato.
MATERIAIS E MÉTODOS
Aquisição do Material
Foi utilizado um pó metálico de aço H13 atomizado a gás fornecido pela LPW Technology Inc, cujo foi depositado sobre uma barra arredondada com 30 mm de diâmetro de aço H13, utilizada como substrato conforme é mostrado na Figura 1. As composições químicas do pó e do substrato são apresentadas na Tabela 1. Uma extremidade da barra foi cortada com 10 mm de altura e usinada circularmente com uma ranhura de 5,0 mm de largura e 2,0 mm de profundidade. O processo de usinagem foi realizado com velocidade de 100 m/min, taxa de corte circular de 0,1 mm/passo e taxa de corte em profundidade de 0,5 mm/passo. A escolha do formato do canal (Figura 2) é baseada no desafio
Figura 1: Processo de usinagem das barras de H13 para posterior deposição do pó metálico atomizado e fresamento da camada em excesso. (a) Usinagem da cavidade para deposição; (b) Pó metálico de H13 atomizado depositado na cavidade; (c) fresamento do excesso de pó depositado na superfície do substrato.
de controlar o superaquecimento do pino central e do anel externo em geometria delicada na parte superior da ferramenta.
TÉCNICA LASER METAL DEPOSITION (LMD) Tanto a usinagem quanto a deposição de material foram executados na ROMI 4X D800 Hybrid Machine. A instalação híbrida combina a capacidade subtrativa de uma máquina CNC de 4 eixos com um cabeçote LMD para operações aditivas. O cabeçote Ambit® Hybrid AM é conectado a um laser de fibra (Yb) com as características fornecidas na Tabela 2. As condições reais de processamento LMD são apresentadas na Tabela 3. Os parâmetros representativos do processo LMD consistem na espessura da camada, velocidade de varredura, potência do laser, estratégia de varredura e espaço entre as varreduras do laser.
ANÁLISE DA MICROESTRUTURA Inicialmente foi realizada a avaliação da distribuição de tamanho de partícula do pó metálico H13. O software ImageJ foi utilizado para realizar 109 medições de diâmetros de partícula de forma aleatória a partir de imagens geradas pelo microscópio eletrônico de varredura (MEV).
As seções transversais das amostras processadas com LMD foram polidas mecanicamente seguido de ataque químico com Nital 3% (ácido nítrico 3% em etanol 97%) para revelar a microestrutura. As imagens de microscopia óptica (MO) foram obtidas por meio de um equipamento Zeiss Imager2M. Já as imagens de microscopia eletrônica de varredura foram adquiridas com o auxílio de um microscópio eletrônico de varredura (MEV) JSM-6380LV.
RESULTADOS E DISCUSSÕES
Caracterização do pó metálico de aço H13
A Fig. 3 apresenta a imagem gerada via microscopia eletrônica de varredura do pó de aço H13, bem como a
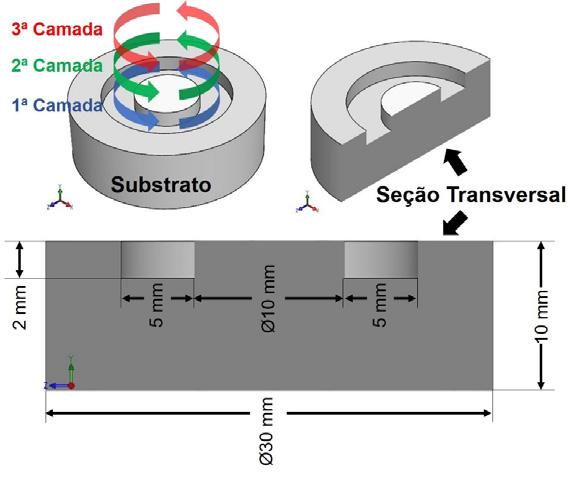
Figura 2: Esquema representativo do substrato de aço H13 com suas respectivas dimensões.
Pó metálico H13 atomizado a gás
C Mn Si V Mo Cr Fe
0.32 - 0.45 0.20 - 0.50 0.80 - 1.20 0.80 - 1.20 1.10 - 1.75 4.75 - 5.50 Bal.
Substrato: Bloco de aço H13
C Mn Si V Mo Cr Fe
0.4 0.35 1.00 0.90 1.50 5.20 Bal.
Tabela 1: Composição química (wt%) do pó metálico e do substrato.
Cabeçote laser Potência Máxima (kW)
Yb: Fiber (λ = 1070 nm) 1.5 kW Distância entre bocal e ponto focal (mm) 10 mm Diâmetro focal (mm) 2 mm
Tabela 2: Características do feixe de laser.
Potência (W) 800 W
Velocidade do feixe laser (mm/min) 350 mm/min Velocidade de alimentação (g/min) 8 g/min Gás de proteção Argônio (99.995% Ar) Fluxo de gás do bico (l/min) 4 l/min
Fluxo de gás de proteção (l/min) 8 l/min
Carrier gas flow (l/min) 4 l/min
Espaçamento entre as linhas (mm) 0.65 (2/3 da largura do cordão) Número de camadas 3
Tabela 3: Parâmetros de processo LMD.
distribuição e a média de tamanho de partícula.
A morfologia das partículas é típica do pó H13, apresentando formas esféricas ou quase esféricas com superfícies relativamente lisas, embora algumas partículas se pronunciem na forma de “satélite,”oblongas arredondadas” e “semelhantes a pera”. As partículas mais grossas tendem a ter formas ovais, enquanto as mais finas são mais esféricas.
A forma refinada e esférica das partículas de pó pode melhorar a densidade do depósito e, consequentementre, favorecer a distribuição uniforme do material entre as camadas, otimizando as características mecânicas do componente.
A morfologia “tipo pera” mostrada na Fig. 3 (a), ocorre quando um pó esférico fino se integra a um pó mais grosso e ocorre um estreitamento entre eles, formando um estrangulamento. A morfologia “oblonga arredondada”, também apresentada na Fig. 3 (a), é caracterizada por um tamanho de partícula grosseiro.
A última morfologia mostrada é a “satélite”, que é a forma de partícula típica no processamento de pó metálico. Em geral, diferentes morfologias de partículas podem impactar na sinergia entre o feixe de laser e as partículas em “vôo”, promovendo diversos fenômenos, o que torna ainda mais necessário a identificação das formas de pronunciamento dessas partículas. Conforme mostrado na Fig. 3 (b), a curva de distribuição normal apresenta maior frequência em torno de 68 µm (diâmetro de partícula) a partir de um total de 109 medições.
ANÁLISE DA MICROESTRUTURA DO PÓ DE AÇO H13 DEPOSITADO VIA LMD A Fig. 4 apresenta imagens de microscopia óptica da seção transversal da amostra. A Fig. 4 (a) mostra o esquema da região onde as imagens foram obtidas. Na Fig. 4 (b) é possível visualizar as diferentes regiões: zona de pó de H13 depositado, zona parcialmente fundida (partially melted zone - PMZ), zona afetada pelo calor (heat affected zone - HAZ) e o substrato H13. A partir da Fig. 4 (c-d), é possível ver claramente as marcas das camadas de deposição e dos limites da poça de fusão (melt pool boundaries - MPB), que têm cerca de 1 mm de profundidade. As regiões PMZ e HAZ possuem cerca de 0,1 e 0,5 mm de profundidade, respectivamente.
Na Fig. 4 é evidente que as camadas fundidas do depósito preencheram a ranhura, porém não mantiveram sua forma retangular original (Fig. 2). Uma parte do substrato foi fundida durante a MA, particularmente aquela próxima à superfície, ocorrendo o processo de fundição entre as partículas de pó do substrato. Comparando a Fig. 4 (c) com a Fig. 2, pode-se observar algum excesso de material no topo da ferramenta, embora a profundidade de deposição seja apenas a profundidade da ranhura. O preenchimento adequado da ranhura foi garantido pela baixa diluição na parte inferior do canal e sobra de material no topo, pronto para o processo usinagem.
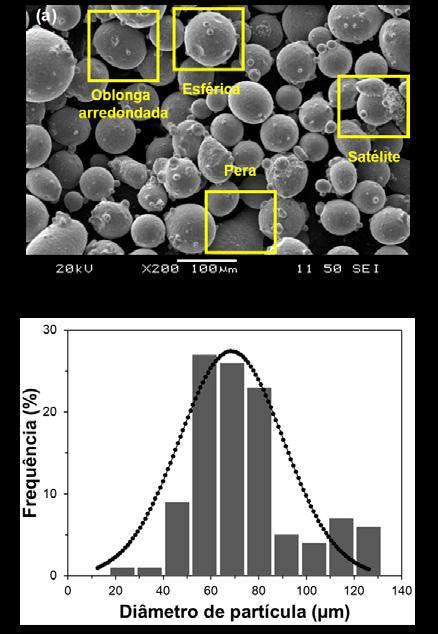
Figura 3: Características do pó metálico de H13: (a) Morfologia do pó; (b) Frequência de distribuição. Figura 4: Micrografias da seção transversal da amostra. (a) Esquema; (b) Visão geral; (c) Magnificação de 50x; (d) MPB, PMZ e HAZ.
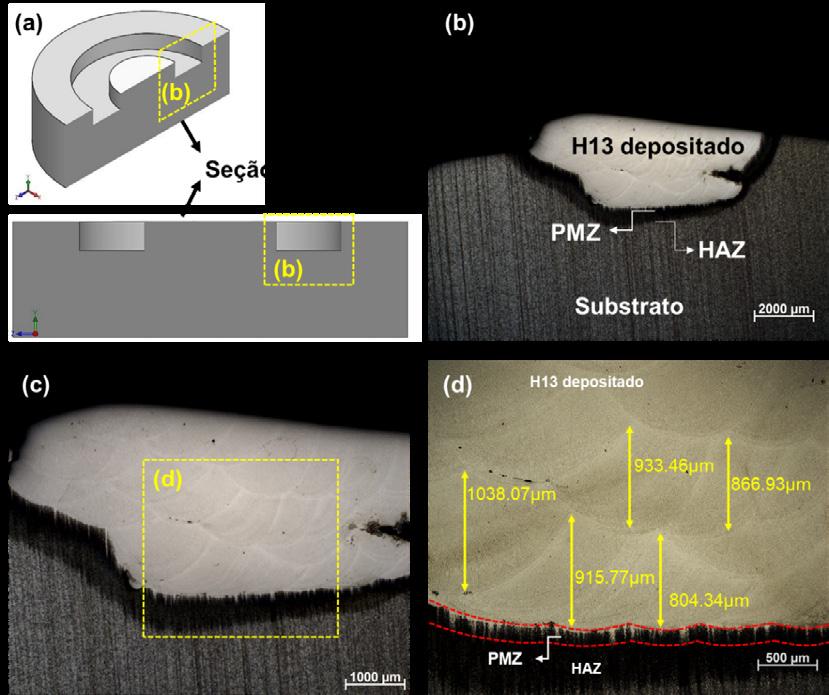
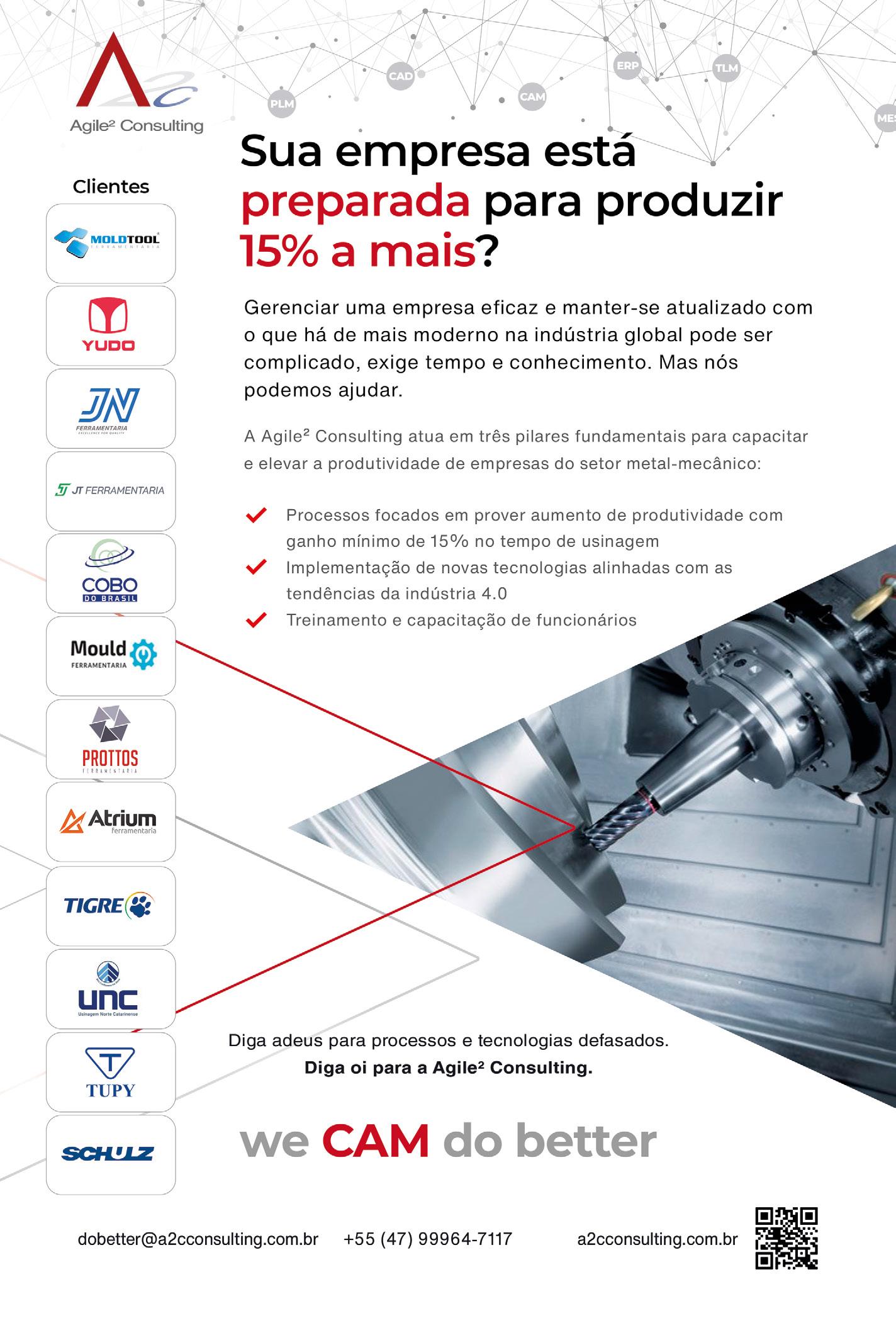
A Fig. 5 mostra a microestrutura da seção transversal da matriz de aço H13 após o processo de deposição ser efetuado. A estrutura celular do pó de H13 com grão quase equiaxiais solidificados durante o processo de atomização de gás pode ser vista claramente, bem como grãos grosseiros e colunares formados pelos efeitos de aquecimento e resfriamento. Conforme mostrado, o material consiste em muitos grãos com geometria quase equiaxial e textura quase aleatória, juntamente com uma disposição homogênea de precipitados na matriz. A estrutura colunar é encontrada próxima à região inferior da zona fundida a laser, uma vez que a solidificação geralmente começa com o crescimento epitaxial da matriz.
As transformações de fase e o pronunciamento de carbonetos ocorrem na zona de transição entre PMZ e o substrato, limite da poça de fusão, como mostrado na Fig. 5 (d). Adicionalmente, a Fig. 5 (a-b) mostra a morfologia de solidificação do pó de H13 depositado, que apresenta uma morfologia dendrítica celular. Esta morfologia inclui grãos colunar e equiaxial dependendo da região do material resolifificado. A geometria das células de solidificação, sejam equiaxiais ou colunares, também é influenciada pelo ponto de vista do ângulo de corte, onde as seções perpendiculares e paralelas à direção da sobreposição das camadas possuem formas equiaxiais e alongadas na micrografia do aço processao a laser, correspondentemente.
Sugere-se que o processo de solidificação do H13 ocorre de duas formas: como austenita primária ou como ferrita. Se a fase primária for ferrita, uma transformação em austenita ocorrerá durante o resfriamento e provavelmente haverá uma redução significativa de tensões . Por outro lado, se a solidificação ocorrer como austenita primária, não haveria qualquer alívio de tensão em teoria. Porém, quando a austenita é encontrada em baixas temperaturas, seja austenita formada de ferrita ou austenita primária, ela se torna martensita no aço H13 por causa de sua alta temperabilidade, conforme mostrado na Fig. 5 (b).
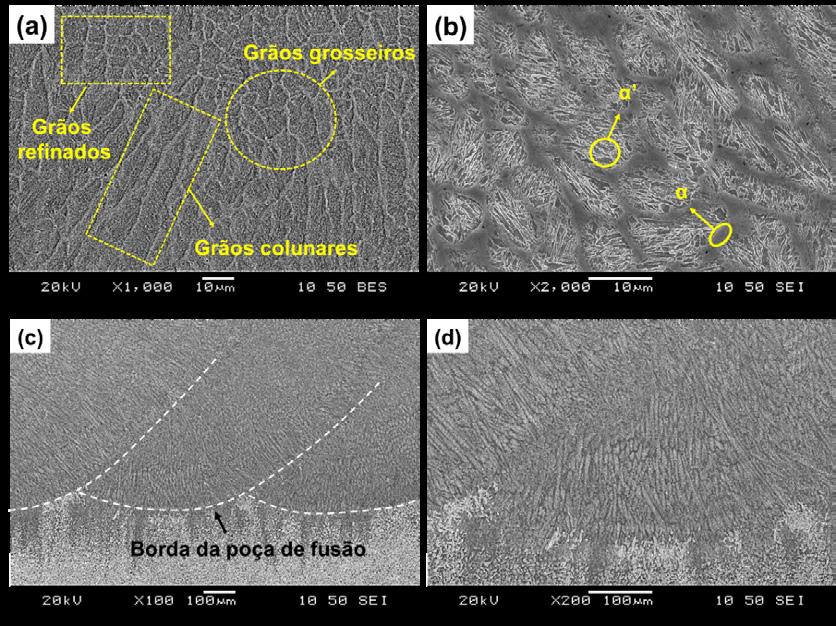
Figura 5: Micrografia eletrônica de varredura do aço H13 processado via LMD: (a) MEVBES da região de deposição; (b) MEV-SEI da região de deposição; (c) Borda da poça de fusão da região depositada; (d) Borda da poça de fusão (magnificação de 200x).
A morfologia da camada depositada com H13 fabricada pelo método LMD é mostrada na Fig. 5 (c-d). As características típicas da fabricação aditiva de metais podem ser observadas onde poças de fusão sobrepostas de formas relativamente semielípticas foram formadas. O desenvolvimento da poça de fusão semi-elíptica é intrínseco à MA usando classificações de ligas ferrosas e não ferrosas devido à origem do processo. As poças de fusão têm 170 a 190 μm de profundidade e aproximadamente 160 a 180 μm de largura. A formação dessas poças de fusão ocorre devido à solidificação de células colunares e equaxiais de diferentes tamanhos.
A Fig. 5 (c) também mostra a forma estimada da poça de fusão (linhas tracejadas). Durante o processo de deposição de metal a laser, a energia do laser é convertida em energia térmica, então o fluxo de calor na poça fundida desempenha um papel razoável na determinação da morfologia e do tamanho da área depositada. À medida que a temperatura da superfície atinge a região de fusão, a convecção térmica é mais evidente na poça de fusão. O fluxo de líquido na poça derretida foi impulsionado principalmente por convecção termocapilar (efeito Marangoni) que depende em certa medida da força de empuxo e principalmente do coeficiente de temperatura da tensão superficial.
O efeito Marangoni provoca a distribuição irregular de elementos, por exemplo, “fluxos circulares”, e gera uma certa mistura nas poças de fusão, bem como a segregação de alguns elementos de liga de aço H13, como Cr e Mo. Este fenômeno também pode auxiliar na diluição dos elementos de liga, levando à distribuição dos elementos de liga do substrato H13 nas poças de fusão. Dessa forma, a formação da PMZ ocorre por meio da liquação dos precipitados do substrato, acompanhada de aumento, dando origem a precipitados maiores próximos da poça de fusão. Os precipitados aglomerados atuam como pontos de nucleação para solidifica-
ção. O fluxo de circulação juntamente com a diluição dos elementos do substrato ocorre apenas na região da primeira camada depositada mais próxima da interface, o que contribui para o padrão de fluxo circular.
CONCLUSÕES Com base nos resultados deste estudo, as seguintes conclusões podem ser consideradas:
1. A caracterização do pó mostrou partículas com tamanho médio de 65 µm, mas algumas outras apresentaram morfologias ligeiramente diferentes. Em geral, foram obtidas partículas esféricas refinadas e grosseiras, e uma distribuição muito homogênea, o que contribui positivamente em termos de qualidade de deposição. 2. Quanto à microestrutura formada a partir do processo, foi possível observar uma matriz α-Fe composta por α’-martensita, o que
é normal quando se trata de um processo de solidificação rápida. 3. O processo de reparo via LMD permitiu o preenchimento da cavidade sem que o substrato apresentasse alterações na microestrutura. A alta precisão do processamento do laser em termos de efeitos causados ao material e a agilidade do processo, são decisivos para que não ocorram danos na parte do substrato mais suscetível ao feixe de laser.
AGRADECIMENTOS Em nome da Bruning Tecnometal, os autores agradecem pela parceria e colaboração técnica, de fundamental importância para o desenvolvimento deste trabalho. Os agradecimentos se estendem à FAPESP (Fundação de Amparo à Pesquisa do Estado de São Paulo) que, através dos processos 2018/23884-5 e 2016/11309-0, viabilizou a concretização do estudo.
Vágner Braga: Engenheiro de Materiais pela Universidade Franciscana - UFN. Mestre em Ciências e Tecnologias Espaciais pelo Instituto Tecnológico de Aeronáutica - ITA. Doutorando do Programa de Pós-Graduação em Ciências e Tecnologias Espaciais – Instituto Tecnológico de Aeronáutica (ITA), com período sanduíche na Ryerson University, Toronto - Ontário (CA). Atualmente ocupa o cargo de Analista Sênior de Pesquisa, Desenvolvimento e Inovação na Bruning Tecnometal Ltda., Panambi/RS. vagner.braga@bruning.com.br
Diego Tolotti de Almeida: Engenheiro Mecânico pela UNIJUI - Universidade Regional do Noroeste do Estado do Rio Grande do Sul, Mestre em Ciência e Tecnologia dos Materiais pela UFRGS. Doutorando do Programa de Pós-Graduação em Engenharia de Minas, Metalurgia e Materiais (PPGE3M/UFRGS). Supervisor de Pesquisa, Desenvolvimento e Inovação na Bruning Tecnometal Ltda., Panambi/RS. diegot@bruning.com.br
Angélica Paola de Oliveira Lopes: Engenheira de Produção pela UNICRUZ - Universidade de Cruz Alta, Mestranda em Engenharia Mecânica na Universidade Federal de Santa Maria (UFSM). Analista de Pesquisa, Desenvolvimento e Inovação na Bruning Tecnometal Ltda., Panambi/RS. angelica@bruning.com.br
Jean Fleck da Silva: Engenheiro Mecânico pela UNIJUI – Universidade Regional do Noroeste do Estado do Rio Grande do Sul. Atua como Analista de Desenvolvimento de Produtos da Bruning Tecnometal Ltda., Panambi/RS. jean. fleck@bruning.com.br
Carolina Alencar Caldeira de Souza: Engenheira Metalúrgica pelo Centro Federal de Educação Tecnológica Celso Suckow da Fonseca - CEFET/RJ. Mestranda do Programa de Pós-Graduação em Ciência dos Materiais - Instituto Militar de Engenharia (IME). Atua como Trainee de Pesquisa, Desenvolvimento e Inovação na Bruning Tecnometal Ltda., Panambi/RS. carolina.caldeira@bruning.com.br
Milton Sergio Fernandes de Lima: Graduado em Física, mestre e doutor em Engenharia Metalúrgica. É pesquisador do Instituto de Estudos Avançados (IEAv), professor do Programa de Pós-Graduação em Ciências e Tecnologias Espaciais do Instituto Tecnológico de Aeronáutica (ITA) e professor do Programa de Pós-Graduação da REDEMAT - Rede Temática em Engenharia de Materiais da Universidade Federal de Ouro Preto (UFOP). msflima@gmail.com