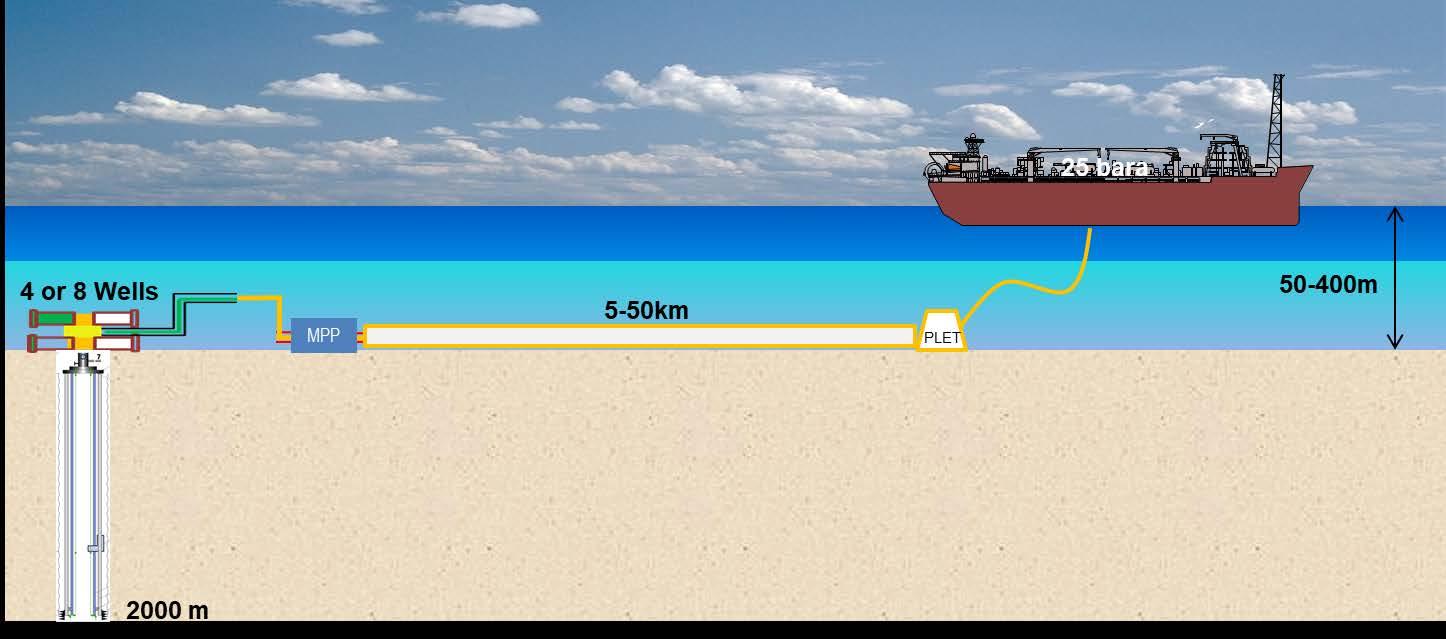
31 minute read
Reducing CO2 Emissions Through the Selection of an Energy Efficient Artificial Lift Method
Reducing CO2 Emissions Through the Selection of an Energy Efficient Artificial Lift Method Hongkun Dong, Per Bloch Helmers, and Øyvind Reimers, OneSubsea Ltd, a Schlumberger Company
Introduction
The United Nations has adopted a set of sustainable development goals (SDGs) for attainment by 2030. Agencies such as IPIECA have outlined how oil and gas industry contributes to SDGs /2/, one of the big contributions is in energy efficiency, which is related to power consumption as well as gas flaring. The IEA estimated that 46% percent of CO2 emission savings would come from end-use efficiency compared with 17% from renewable energy /3/. In recent years, CO2 emission in the oil and gas industry has gained more attention on a global basis because of climate change. The industry focus is shifting toward more environmentally friendly alternatives to reduce the overall CO2 impact. This change is also driven by new legislation that regulates CO2 emissions, both nationally and internationally. Norwegian Statistics has published a report detailing CO2 emissions from the Norwegian oil and gas industry /4/. The report is based on historical data on production levels, emission data, physical data, and commercial data from 41 fields on the Norwegian Continental Shelf from 1997 to 2013. One of the findings was that gas production is less emission intensive compared with oil production. Further, oil production is increasingly emission intensive as the reservoir pressure declines and water cut increases as the field matures. This implies that the heavier the fluid is, the more energy demanding it is to produce. Artificial lift is often applied to enable production at an economically attractive level. For an offshore asset, this typically implies use of gas lift, electric submersible pumps (ESPs), seabed pumps, or a combination of gas lift and seabed pumps. In this study, carbon emissions for a field requiring artificial lift is evaluated based on either gas lift or subsea pump system. The results are compared, and correlations are highlighted. To evaluate this, a purpose-made simulation
Norwegian Statistics has published a report detailing CO2 emissions from the Norwegian oil and gas industry /4/. The report is based on historical data on production levels, emission data, physical data, and commercial data from 41 fields on the Norwegian Continental Shelf from 1997 to 2013. One of the findings was that gas production is less emission intensive compared with oil production. Further, oil production is increasingly emission intensive as the reservoir pressure declines and water cut increases as the field matures. This implies that the heavier the fluid is, the more energy demanding it is to produce. Artificial lift is often applied to enable production at an economically attractive level. For an offshore asset, this typically implies use of gas lift, electric submersible pumps (ESPs), seabed pumps, or a combination of gas lift and seabed pumps. model is built to represent a typical production system. This generic model will not be specific In this study, carbon emissions for a field requiring artificial lift is to any fields or reservoirs but will hold enough evaluated based on either gas lift information to evaluate the relative differences between the different cases. Sensitivities have been performed on tieback distances, number or subsea pump system. The results are compared, and correlations are highlighted. To evaluate this, a purpose-made simulation model is built to represent a typical production system. This generic model will not be specific to any fields or reservoirs but of wells, water cut, and water depth to obtain will hold enough information to evaluate the relative differences between the different cases. a comprehensive overview for the comparison.Sensitivities have been performed on tieback distances, number of wells, water cut, and water depth to obtain a comprehensive overview for the comparison. System and technology description
Gas Lift System
Gas lift is the most commonly used artificial lift SYSTEM AND TECHNOLOGY DESCRIPTION technology for offshore wells and is often the base case for most reservoir engineers early in Gas Lift System a field’s development. A simplified schematic of a production system with downhole gas lift is shown in Fig. 1. Gas lift may be injected Gas lift is into the well stream either downhole or at a the most commonly used artificial lift technology for offshore wells and is often the base case for most reservoir engineers early in a field’s riser-base location. The former is considered in development. A simplified schematic of a production system with downhole gas lift is shown in Fig. 1. this report. Gas lift may be injected into the well stream either downhole or at a riser-base location. The former is considered in this report.
Sep. M
Production Flowline, increased frictional losses
Gas Lift Flowline & Riser, frictional losses
Sep. VSD
Production Flowline, reduced in-situ gas volume
Power Cable, voltage drop
Fig. 2: Multiphase boosting system sketch.
The main purpose of gas lift is to lighten the weight of the hydrostatic column between the reservoir and topside facility. Produced gas is recompressed topside and fed down a gas lift riser and through a gas lift flowline and into the subsurface infrastructure. The gas is mixed with the well fluids in the well, resulting in lower fluid density, lower backpressure for the wells, and higher production rates. Because the gas will continue expanding as the pressure decreases toward topside, there is an optimal gas lift rate where any further increase in gas lift rate will lead to a choking effect in the flowline. Hence, the amount of gas lift needs to be balanced between the added production due to reduced hydrostatic height and the added frictional losses from the added gas volumes. Topside gas compression is the main energy consumer and contributor to CO2 emissions related to gas lift.
Multiphase Boosting System
Fig. 2: Multiphase boosting system sketch.A simplified schematic for a production system with subsea multiphase boosting system is ilThe power to the pump is supplied from a topside drive system and down through a power umbilical. lustrated in Fig. 2. The pump is normally inThe main loss of energy for this system will be in the electrical system.stalled in by-pass to the flowline downstream of the wellhead trees and manifolds, enabling boosting of multiple wells through a single DESCRIPTION OF MODELING AND METHODOLOGYpump system. The lifting energy is added directly into the produced fluids by reducing the wellhead pressure and boosting it to the The energy efficiency study is developed to enable comparing topside separator. The compressed gas at the energy consumption and CO2 emission at a high level. A generic field model is used to analyze the energy consumption using pump discharge also reduces the friction losses different improved oil recovery (IOR) technologies in gas lift and multin the flowline. Generally, more power trans- iphase boosting. A hydraulic simulator is used as the engine to calculate pressure drops and system deliverability. ferred to the fluids through the pump will lead A simple general subsea system is established (Fig. 3), and the following parameters are assumed for the reservoir, well, and flowline conditions. to a higher production. As the inlet pressure approaches very low pressures, the expansion effect becomes significant, thus reducing the benefits of reducing the pump inlet pressure further. The power to the pump is supplied from a topside drive system and down through a power umbilical. The main loss of energy for this system will be in the electrical system.
Description of modeling and methodology
The energy efficiency study is developed to enable comparing energy consumption and CO2 emission at a high level. A generic field model is used to analyze the energy consumption using different improved oil recovery (IOR) technologies in gas lift and multiphase boosting. A hydraulic simulator is used as the engine to calculate pressure drops and system deliverability. A simple general subsea system is established (Fig. 3), and the following parameters are assumed for the reservoir, well, and flowline conditions. Because the oil production system can vary significantly from field to field, the generic model looked at key system parameters in the typical oil and gas system to reflect the trends
Schlumberger-Private
Fig. 3: System diagram.
for different production systems. The cases in Tab. 1 have been combined and analyzed.
In addition to the production system, the flowing and reservoir conditions may also impact on the thermal hydraulic performance and therefore the energy efficiency for the lifting methods. The flowing and reservoir condition in the generic model is configured as in Tab. 2.
The energy consumption for the gas lift compression work is calculated by using a simplistic approach assuming the isentropic process and a fixed discharge gauge pressure of 250 bar. The power consumption for any interstage cooling and pressure losses in the gas lift compression system is not included.
Tab. 1: Case Matrix
Parameter
Cases Tieback distance, km 5, 20, 30, 40, and 50 GOR, Sm3/Sm3 50, 100, and 150 Number of wells 4 and 8 Water cut, % 10, 20, 40, 60, 80, and 90 Water depth, m 50, 100, 400, 600, 1,000, and 2000 Separator pressure (absolute), bara 5, 10, 15, 20, and 25
Parameter In addition to the production system, the flowing and reservoir conditions may also impact on the Tab. 1: Case Matrix thermal hydraulic performance and therefore the energy efficiency for the lifting methods. The flowing and reservoir condition in the generic model is configured as in Tab. 2.
Cases Tieback distance, km 5, 20, 30, 40, and 50 GOR, Sm3/Sm3 50, 100, and 150 Number of wells 4 and 8 Water cut, % 10, 20, 40, 60, 80, and 90 Water depth, m 50, 100, 400, 600, 1,000, and 2000 Separator pressure (absolute), bara 5, 10, 15, 20, and 25
In addition to the production system, the flowing and reservoir conditions may also impact on the thermal hydraulic performance and therefore the energy efficiency for the lifting methods. The flowing and reservoir condition in the generic model is configured as in Tab. 2.
Tab. 2: Network Model Inputs
Fluid
GOR, Sm3/Sm3 Reservoir Tab. 2: Network Model Inputs Well Flowline
50 Depth, m 2,000 Tubing ID, in 5 ½ Inner Diameter, in 4 W: 12
Fluid Reservoir Well Flowline8 W: 14
Water cut, % GOR, 10–Sm3/Sm390 50 Pressure Depth, m 2,000 Tubing ID, in 5 ½ Inner Diameter, in 4 W: 12 (absolute), bara 8 W: 14
200 Casing ID, in 9 5/8 Temperature (ambient), degC 4
Water cut, % 10–90 Pressure (absolute), bara
Oil, gAPI 30 Temperature, 200 Casing ID, in 9 5/8 Temperature degC (ambient), degC
RESULTS AND DISCUSSION 100 Gas lift depth, m 1500 U value, W/m2K 1.5 4
Oil, gAPI 30 Temperature, degC Schlumberger-Private
100 Gas lift depth, m 1500 U value, W/m2K 1.5
Gas specific gravity, 0.64 Liquid PI, m3/d/bar 30 Gas lift rate per well, m3/d 2,000–200,000 Water depth, m 50–1,000
Water specific gravity. 1.02 Tieback distance, km 5–50
Schlumberger-Private
Gas specific gravity, 0.64 Liquid PI, m3/d/bar 30 Gas lift rate per well, m3/d 2,000–200,000 Water depth, m 50–1,000
Water specific gravity. 1.02 Tieback distance, km
5–50 consumption for the gas lift compression work is calculated by using a simplistic Tab. 2: Network Model Inputs approach assuming the isentropic process and a fixed discharge gauge pressure of 250 bar. The power consumption for any interstage cooling and pressure losses in the gas lift compression system ��������ℎ���������������������������������������������������������������������������������������������������������������� =��������(ℎ2 −ℎ1) /5/ = gas flow rate enthalpy per unit mass for an isentropic path = inlet enthalpy per unit mass. The gas lift used is assumed to have a molecular weight of 28 g/mol and specific heat ratio of 1.3. The approximation of (ℎ2 −ℎ1), assuming the isentropic head, is calculated as � The gas lift used is assumed to have a molecular weight of 28 g/mol and specific heat ratio (ℎ2 −ℎ1)= of 1.3. The approximation of (h2 − h1), assuming the isentropic head, is calculated as
��������1���������������� (��������− �������� 1)(���������������� ��������2 ��������1
The energy consumption for the gas lift compression work is calculated by using a simplistic approach assuming the isentropic process and a fixed discharge gauge pressure of 250 bar. The power consumption for any interstage cooling and pressure losses in the gas lift compression system is not included. ��������ℎ���������������������������������������������������������������������������������������������������������������� =��������(ℎ2 −ℎ1) /5/ m = gas flow rate h2 = outlet enthalpy per unit mass for an isentropic path h1 = inlet enthalpy per unit mass. The gas lift used is assumed to have a molecular weight of 28 g/mol and specific heat ratio of 1.3. The approximation of (ℎ2 −ℎ1), assuming the isentropic head, is calculated as ��������−1 �������� −1] /5/ (ℎ2 −ℎ1)=
1 = suction temperature = compressibility factor = Gas law constant = ratios of specific heats = gas molecular weight 1 = suction pressure 2 = discharge pressure consumption for the multiphase pump system work is calculated by a flow simulator’s generic multiphase booster model, and a fixed percentage (30%) is added to account for losses in the electrical system between the topside variable speed drive and the pump shaft (typical losses are in the range of 20%–30%). The boundary conditions for the power system is the grid interfacing the compressor or pump drive topside. The energy consumption for the multiphase pump system work is calculated by a flow simulator’s generic multiphase booster model, and a fixed percentage (30%) is added to account for losses in the electrical system between the
The energy consumption for the gas lift compression work is calculated by using a simplistic approach assuming the isentropic process and a fixed discharge gauge pressure of 250 bar. The power consumption for any interstage cooling and pressure losses in the gas lift compression system is not included. The energy consumption for the gas lift compression work is calculated by using a simplistic approach assuming the isentropic process and a fixed discharge gauge pressure of 250 bar. The power consumption for any interstage cooling and pressure losses in the gas lift compression system is not included. ��������ℎ���������������������������������������������������������������������������������������������������������������� =��������(ℎ2 −ℎ1) /5/ m = gas flow rate h2 = outlet enthalpy per unit mass for an isentropic path h1 = inlet enthalpy per unit mass.
The gas lift used is assumed to have a molecular weight of 28 g/mol and specific heat ratio of 1.3.
The approximation of (ℎ2 −ℎ1), assuming the isentropic head, is calculated as (ℎ2 −ℎ1)= ( ��������1���������������� ��������−1 �������� )(���������������� [�������� �������� 2 1 ���������− �������� 1� −1] /5/ T1 = suction temperature Z = compressibility factor
R = Gas law constant � k = ratios of specific heats MW = gas molecular weight P1 = suction pressure P2 = discharge pressure
The energy consumption for the multiphase pump system work is calculated by a flow simulator’s generic multiphase booster model, and a fixed percentage (30%) is added to account for losses in the electrical system between the topside variable speed drive and the pump shaft (typical losses are in the range of 20%–30%). The boundary conditions for the power system is the grid interfacing the compressor or pump drive topside.
consumption for the gas lift compression work is calculated by using a simplistic approach assuming the isentropic process and a fixed discharge gauge pressure of 250 bar. The power consumption for any interstage cooling and pressure losses in the gas lift compression system ��������ℎ���������������������������������������������������������������������������������������������������������������� =��������(ℎ2 −ℎ1) /5/ per unit mass for an isentropic path = inlet enthalpy per unit mass. ssumed to have a molecular weight of 28 g/mol and specific heat ratio of 1.3. (ℎ2 −ℎ1), assuming the isentropic head, is calculated as (ℎ2 −ℎ1)= ��������1���������������� ��������−1 �������� )(���������������� [�������� �������� 2 1 ���������− �������� 1� −1] /5/ T1 = suction temperature Z = compressibility factor R ( = Gas law constant k = ratios of specific heats MW = gas molecular weight P1 = suction pressure P2 = discharge pressure The energy consumption for the multiphase pump system work is calculated by a flow simulator’s generic multiphase booster model, and a fixed percentage (30%) is added to account for losses in the electrical system between the topside variable speed drive and the pump shaft (typical losses are in the range of 20%–30%). The boundary conditions for the power system is the grid interfacing the compressor or pump drive topside.
consumption for the gas lift compression work is calculated by using a simplistic approach assuming the isentropic process and a fixed discharge gauge pressure of 250 bar. The power consumption for any interstage cooling and pressure losses in the gas lift compression system ��������ℎ���������������������������������������������������������������������������������������������������������������� =��������(ℎ2 −ℎ1) /5/ per unit mass for an isentropic path = inlet enthalpy per unit mass. [ (The gas lift used is assumed to have a ��������1���������������� ��������−1 �������� )(���������������� [��������2 ��������1 ���������−1 �������� � −1] /5/ molecular weight of 28 g/mol and specific heat ratio of 1.3. The approximation of (ℎ2 −ℎ1), assuming the isentropic head, is calculated as 1 = suction temperature = compressibility factor (ℎ2 −ℎ1)= = ratios of specific heats = gas molecular weight 2 = discharge pressure consumption for the multiphase pump system work is calculated by a flow simulator’s generic multiphase booster model, and a fixed percentage (30%) is added to account for losses in the electrical system between the topside variable speed drive and the pump shaft (typical losses %–30%). The boundary conditions for the power system is the grid interfacing the compressor or pump drive topside.
��������1���������������� ��������−1 �������� )(���������������� [�������� �������� 2 1
The energy consumption for the gas lift compression work is calculated by using a simplistic approach assuming the isentropic process and a fixed discharge gauge pressure of 250 bar. The power consumption for any interstage cooling and pressure losses in the gas lift compression system is not included. ��������ℎ���������������������������������������������������������������������������������������������������������������� =��������(ℎ2 −ℎ1) /5/ m = gas flow rate h2 = outlet enthalpy per unit mass for an isentropic path h1 � = inlet enthalpy per unit mass. The gas lift used is assumed to have a ( molecular weight of 28 g/mol and specific heat ratio of 1.3. The approximation of (ℎ2 −ℎ1), assuming the isentropic head, is calculated as ��������− �������� 1�(−ℎ2 1] /5/−ℎ1)=
1 = suction temperature = compressibility factor = Gas law constant = ratios of specific heats = gas molecular weight 1 = suction pressure 2 = discharge pressure consumption for the multiphase pump system work is calculated by a flow simulator’s generic multiphase booster model, and a fixed percentage (30%) is added to account for losses in the electrical system between the topside variable speed drive and the pump shaft (typical losses are in the range of 20%–30%). The boundary conditions for the power system is the grid interfacing the compressor or pump drive topside.
��������1���������������� (��������− �������� 1)(����������������
��������2���������− �������� 1� −1] /5/ ��������1
T1 = suction temperature Z = compressibility factor R = Gas law constant k = ratios of specific heats MW = gas molecular weight P1 = suction pressure P2 = discharge pressure The energy consumption for the multiphase pump system work is calculated by a flow simulator’s generic multiphase booster model, and a fixed percentage (30%) is added to account for losses in the electrical system between the topside variable speed drive and the pump shaft (typical losses are in the range of 20%–30%). The boundary conditions for the power system is the grid interfacing the compressor or pump drive topside.
The energy consumption to boost production for both gas lift and multiphase pumping (MPP) is shown in Fig. 4. When using the lifting energy to increase production, the power consumption increases from both gas lift and MPP. The gas lift, in a red curve, has an optimal gas lift rate from which further increasing the gas lift rate is a waste of energy because of the choking effect. For MPP, in the blue curve, the flow rate increases will also become flat because of the expansion effect when lowering the suction pressure toward atmospheric pressure.
Fig. 4: Example of power consumption comparison with gas lift and MPP.
However, for optimal production using gas lift, the MPP can achieve the same production with much lower energy consumption. It means that more energy-efficient production is possible, if only to [ achieve the same production target. The MPP could have higher production in comparison because it may produce a much higher differential pressure in the system. This paper discusses the IOR difference but only in terms of energy efficiency and potential energy savings. topside variable speed drive and the pump shaft (typical losses are in the range of 20%–To evaluate the energy savings potential when comparing MPP and g has been defined as below. as lift, an energy saving ratio 30%). The boundary conditions for the power system is the grid interfacing the compressor or pump drive topside. ������������������������������������������������_ ����������������������������������������������������������������������������������������(%)=
Results and discussion
The energy consumption to boost production for both gas lift and multiphase pumping (MPP) is shown in Fig. 4. When using the lifting energy to increase production, the power consumption increases from both gas lift and MPP. The gas lift, in a red curve, has an optimal gas lift rate from which further increasing the gas lift rate is a waste of energy because of the choking effect. For MPP, in the blue curve,
10000 8000 Liquid Flow Rate 4000 6000 2000 0
0 1000 2000 3000 4000
Power Consumption, KW
������������������������������������������������������������������������������������������������ An example of energy savings ratio is demonstrated in Fig. 4; for the same flow rates, it is possible reduce the power consumption from 2.6 kW to 0.6 kW and save 77%. As previously mentioned, the potential energy savings can be impacted by the actual production and system configuration, such as the tieback distance, water depth, reservoir depth, or reservoir conditions such as pressure and GOR. To investigate energy savings potential with regards to different parameters, simulations were performed with the simulation matrix. As an example, for a four-well system, the energy saving map with respect to tieback distance and water depth can be seen in Fig. 5. Gas Lift MPP Fig. 4: Example of power consumption comparison with gas lift and MPP. the flow rate increases will also become flat because of the expansion effect when lowering the suction pressure toward atmospheric pressure. However, for optimal production using gas lift, the MPP can achieve the same production with much lower energy consumption. It means that more energy-efficient production is possible, if only to achieve the same production target. The MPP could have higher production in comparison because it may produce a much higher differential pressure in the system. This paper discusses the IOR difference but only in terms of energy efficiency and potential energy savings.
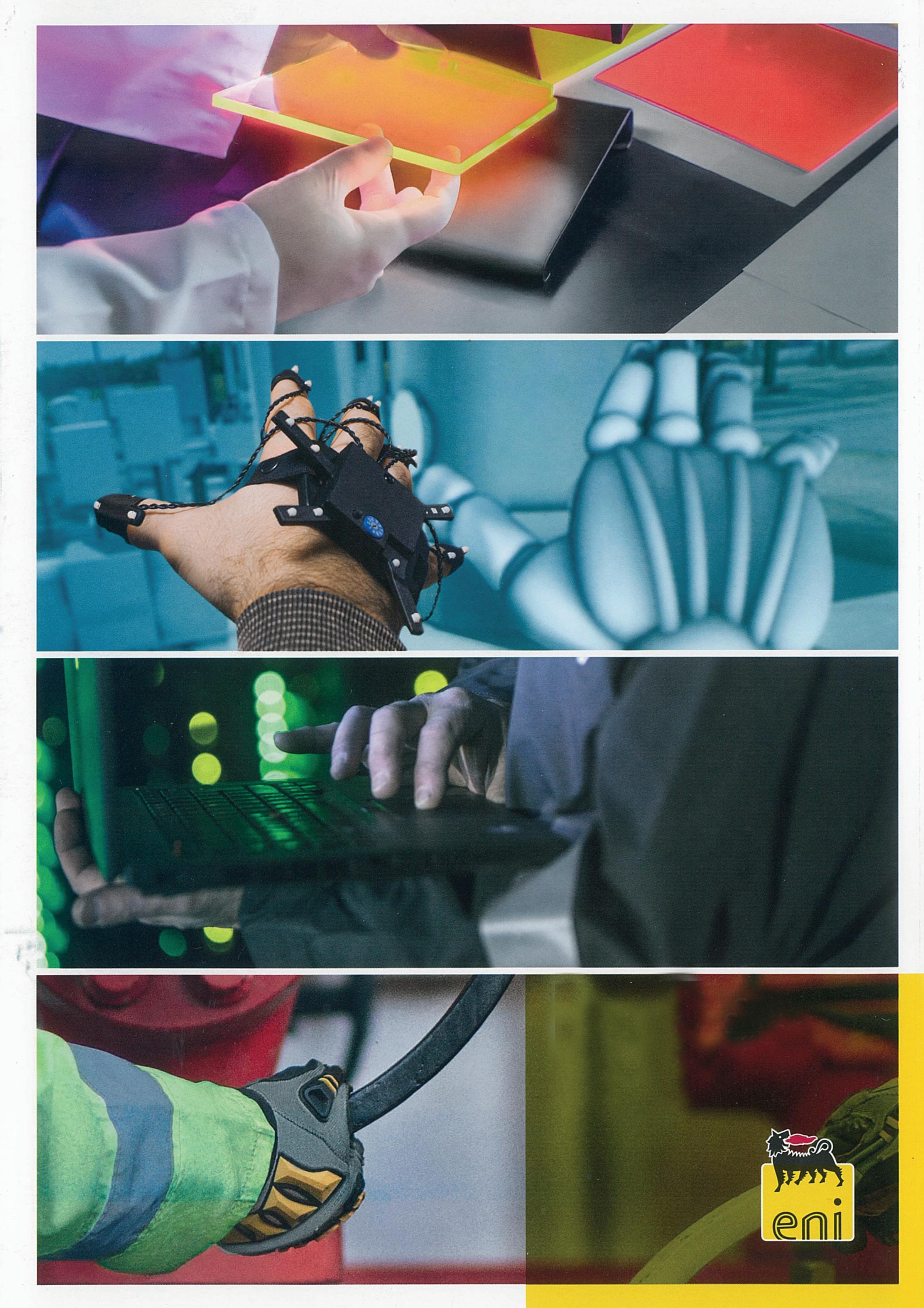
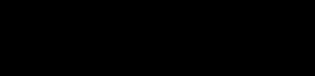

However, for optimal production using gas lift, the MPP can achieve the same production with much Example of power consumption comparison with gas lift and MPP. lower energy consumption. It means that more energy-efficient production is possible, if only to achieve the same production target. The MPP could have higher production in comparison because it may produce a much higher differential pressure in the system. This paper production using gas lift, the MPP can achieve the same production with much discusses the IOR difference but only in terms of energy efficiency and potential. It means that more energy-efficient production is possible, energy savings. if only to achieve the same production target. The MPP could have higher production in comparison because To evaluate the energy savings potential when comparing MPP and gas lift, an energy saving ratio has been defined as To evaluate the energy savings potential when comparing MPP and gas lift, an energy saving ratio has been defined as below. it may produce a much higher differential pressure in the system. This paper discusses the IOR energy efficiency and potential energy savings. potential when comparing MPP and gas lift, an energy saving ratio An example of energy savings ratio is demonstrated in Fig. 4; for the same flow rates, it is possible reduce the power consumption from 2.6 kW to 0.6 kW and save 77%. As previously mentioned, the potential energy savings can be impacted by the actual production and system configuration, such as the tieback distance, water depth, reservoir depth, or reservoir conditions such as pressure and GOR. To investigate energy savings potential with regards to different parameters, simulations were performed with the simulation matrix. As an example, for a four-well system, the energy saving map with respect to tieback distance and water depth can be seen in Fig. 5. The energy savings potential increases with water depth and tieback distance. Up to 80% energy savings can be achieved. The energy savings map can be changed with other factors, such as water cuts, reservoir conditions, and arrival conditions at the separator. The following sections discuss the impact of other factors.
20-40%
������������������������������������������������������������������������������������������������ 40-60% Energy Savings
An example of energy savings ����������������������������������������������������������������(%)= ratio is demonstrated in Fig. 4; for the same flow rates, it is possible reduce the power consumption from 2.6 kW to 0.6 kW and save 77%. previously mentioned, the potential energy savings can be impacted by the actual production and system configuration, such as the tieback distance, water depth, reservoir depth, or reservoir conditions such as pressure and GOR. To investigate energy savings potential with regards to different parameters, simulations were performed with the simulation matrix. As an example, for a well system, the energy saving map with respect to tieback distance and water depth can be seen in Fig. 5.
ratio is demonstrated in Fig. 4; for the same flow rates, it is possible reduce the power consumption from 2.6 kW to 0.6 kW and save 77%. 60-80% Energy Savings he potential energy savings can be impacted by the actual production and system configuration, such as the tieback distance, water depth, reservoir depth, or reservoir conditions such as pressure and GOR. To investigate energy savings potential with regards to were performed with the simulation matrix. As an example, for a well system, the energy saving map with respect to tieback distance and water depth can be Fig. 5: Energy savings map with respect to water depth and tieback distance.Fig. 5: Energy savings map with respect to water depth and tieback distance. The energy savings potential increases with water depth and tieback distance. Up to 80% energy Schlumberger-Private savings can be achieved. The energy savings map can be changed with other factors, such as water cuts, reservoir conditions, and arrival conditions at the separator. The following sections discuss the impact of other factors.
Schlumberger-Private Sensitivity to Water Cut - 20K TB-WD400m - 4 Wells 100% 90% SENSITIVITIES 80% Water Cut During the life of field, one can expect increasing water cut, which may impact the energy efficiency of the lifting strategy. It is widely believed that gas lift is required for the late life of the field when the 30% 40% 50% 60% 70%Energy savings, % water cut is high, which point20% s to a lower efficiency for gas lift in low water cuts and higher efficiency for gas lift in water cuts10% . 0% The power saving 0 s potential is high at low water cut, and it decreases slightly with higher water cut 10 20 30 40 50 60 70 80 90 100 when the gas lift efficiency increases. At a very high water cut Water Cut, % (>60%), the power savings potential increases because the MPP efficiency would also dramatically increase with higher water cuts and Fig. 6: Sensitivity to water cut. Fig. 6: Sensitivity to water cut.
Sensitivities lower gas-volume fraction (GVF), but the energy savings stay above 50% for all water cuts. Another reason that could contribute to this trend is that the higher mixing viscosity with the increasing water cut increases the power consumption from boosting.
Water Cut
During the life of field, one can expect increasing water cut, which may impact the energy efficiency of the lifting strategy. It is widely believed that gas lift is required for the late life of the field when the water cut is high, which points to a lower efficiency for gas lift in low water cuts and higher efficiency for gas lift in water cuts. The power savings potential is high at low water cut, and it decreases slightly with higher water cut when the gas lift efficiency increases. At a very high water cut (>60%), the power savings potential increases because the MPP efficiency would also dramatically increase with higher water cuts and lower gas-volume fraction (GVF), but the energy savings stay above 50% for all water cuts. Another reason that could contribute to this trend is that the 57
higher mixing viscosity with the increasing water cut increases the power consumption from boosting.
Topside Separator Pressure
As wellhead pressure drops with time because of falling reservoir pressure, increasing water cut, or both, a common way to maintain or increase production is to reduce the first stage separator pressure topside. This will cause a reduced backpressure for the wells, but there are some energy aspects associated with this to be aware of, depending on the artificial lift method selected. Schlumberger-Private For a gas lifted system, lowering the separator pressure will give the following effects:
Topside Separator Pressure As wellhead pressure drops with time • because of The inlet pressure to the gas lift com-falling reservoir pressure, increasing water cut, or pressor is decreased, but the compressor discharge pressure remains as the lift both, a common way to maintain or increase production is to reduce the first stage separator pressure topside. This will cause a reduced backpressure for the wells, but there are some energy aspects associated with this to be aware of, depending on the artificial lift method selected. requirement at the injection point also remains. This leads to an increase in the required compression work. For a gas lifted system, lowering the separator pressure will give the following effects: • Increased friction losses occur in the pro• duction because of the expansion effect from the gas. This effect is bigger when The inlet pressure to the gas lift compressor is decreased, but the compressor discharge pressure remains as the lift requirement at the injection point also remains. This leads to an increase in the required compression work. • Increased friction losses occur lift gas is added compared with mulin the production because of the expansion effect from tiphase boosting, where no gas is added.the gas. This effect is bigger when lift gas is added compared with multiphase boosting, where no gas is added. For a multiphase boosting system, lowering the separator pressure will give the following For a multiphase boosting system, lowering the separator pressure will give the following effects: effects: • • The backpressure will be reduced while The backpressure will be reduced while the pump inlet pressure remains. The the pump inlet pressure remains. The re-required differential pressure for the pump is therefore reduced. • Some frictional losses will occur because of the expansion of the gas but are marginal compared with using gas lift (adding gas volumes). The above effects from lowering the separator pressure will give the following effects on the power requirement:
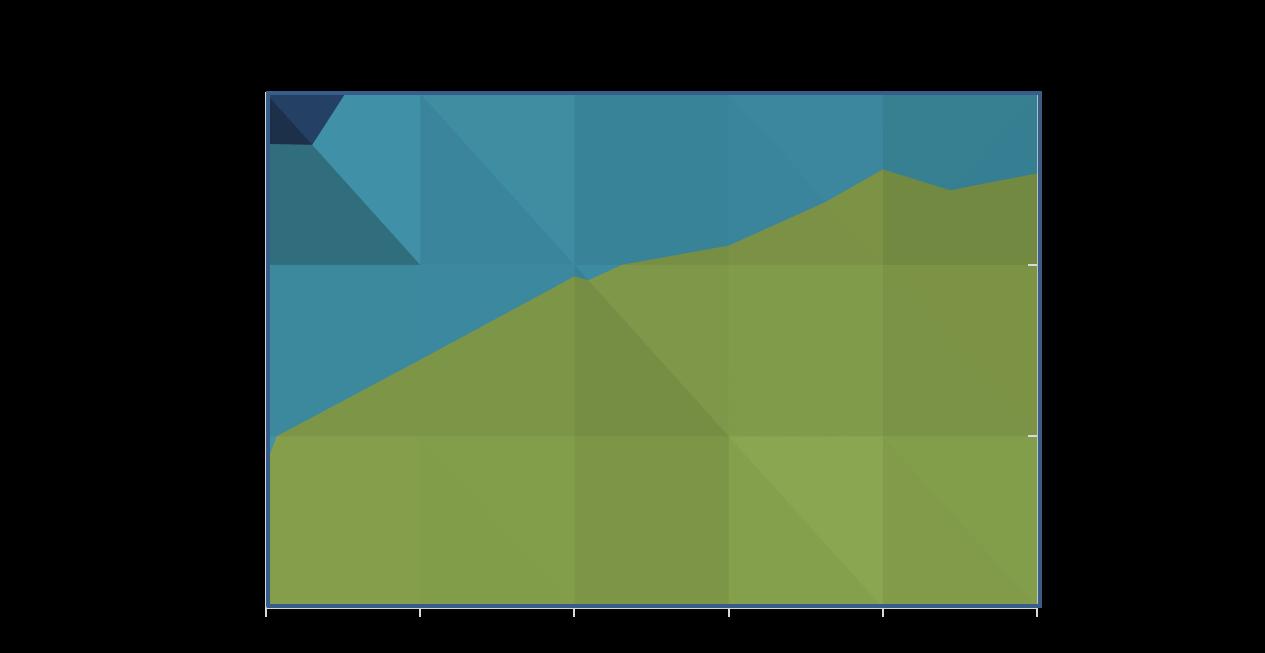
quired differential pressure for the pump is therefore reduced. • Some frictional losses will occur because of the expansion of the gas but are marginal compared with using gas lift (adding gas volumes).
The above effects from lowering the separator pressure will give the following effects on the power requirement: • increase in the power requirement for a gas lifted system • decrease in the power requirement for a multiphase boosting system.
Therefore, more savings can be realized for the system with lower separator pressures (Fig. 7).
Discharge Pressure
Gas lift compressor discharge pressure also has a significant impact on the energy consumption for gas lift systems. The case assumed the constant discharge pressure of 250 bar absolute pressure, but the discharge pressure could vary depending on the injection point, reservoir pressure, and if the compressor was also used for exporting gas. With an increasing discharge pressure, the energy savings potential for using an MPP increases (Fig. 8).
Therefore, more savings can be realized for the system with lower separator pressures (Fig. 7). 90%
20% 80% 10% 70% 30% 40% 50% 60%Energy savings, %0% 0
5 10 15 Separator pressure, bara
20
Fig. 7: Sensitivity to separator pressure.
25 30
20% 10% Discharge Pressure
0% 5 10 15 20 25 300 Gas lift compressor discharge pressure also has a significant impact on the energy consumption for gas lift systems. The case assumed the constant discharge pressure of 250 bar absolute pressure, but the Separator pressure, bara discharge pressure could vary depending on the injection point, reservoir pressure, and if the compressor was also used for exporting gas. With an increasing discharge pressure, the energy Fig. 7: Sensitivity to separator pressure. Fig. 7: Sensitivity to separator pressure.savings potential for using an MPP increases (Fig. 8).
Discharge Pressure Gas lift compressor discharge pressure also has a significant impact on the energy consumption for gas lift systems. The case assumed the constant discharge pressure of 250 bar absolute pressure, but the discharge pressure could vary depending on the injection point, reservoir pressure, and if the compressor was also used for exporting gas. With an increasing discharge pressure, the energy savings potential for using an MPP increases (Fig. 8). 100%
100% 90% 80% Energy savings, % 30% 40% 50% 60% 70% Sensitivity to Discharge Pressure - 20K TB-WD400m - 4 Wells 20% Sensitivity to Discharge Pressure - 20K TB-WD400m - 4 Wells
COMBINED GAS LIFT AND BOOSTING OPERATION COMBINED GAS LIFT AND BOOSTING OPERATION
80% 90% 10%Combined gas lift and boosting In many cases, MPP and gas lift can be combined to maximize lifting efficiency. It is common in some cases that the well does not flow naturally without gas lift or boosting. In a deep well with high In many cases, MPP and gas lift can be combined to maximize lifting efficiency. It is common in some cases that the well does not flow naturally without gas lift or boosting. In a deep well with high 30% 40% 50% 60% 70%Energy savings, % Fig. 8: Sensitivity to compressor discharge pressure. Fig. 8: Sensitivity to compressor discharge pressure. 0% 100 150 200 250 300 350 400 Compressor discharge pressure, bara operation In many cases, MPP and gas lift can be combined to maximize lifting efficiency. It is common in some cases that the well does not flow naturally without gas lift or boosting. In a deep water cuts, the gas lift can be required to reduce the hydrostatic head. In Fig. 9 on the left, the gas lift rate of 100,000 m3/d is used to achieve the bottomhole pressure (BHP) of 120 barg. After the MPP is put into place, a small pressure boosting from the MPP reduces the wellhead pressure (WHP) to 20 barg. If looking at lift gas in well as champagne bubbles in a water cuts, the gas lift can be required to reduce the hydrostatic head. In Fig. 9 on the left, the gas lift rate of 100,000 m3/d is used to achieve the bottomhole pressure (BHP) of 120 barg. After the MPP is put into place, a small pressure boosting from the MPP reduce the wellhead pressure (WHP) to 20 barg. If looking at lift gas in well as champagne bubbles in a 20%well with high water cuts, the gas lift can be glass, with the lower WHP, With the lower WHP, the champagne bubbles get bigger and more gas glass, with the lower WHP, With the lower WHP, the champagne bubbles get bigger and more gas 10%required to reduce the hydrostatic head. comes out of the oil, which reduces the required gas lift rate for the same BHP.comes out of the oil, which reduces the required gas lift rate for the same BHP. In Fig. 9 on the left, the gas lift rate of 100,000 m3/d is used to achieve the bottomhole pressure (BHP) of 120 barg. After the MPP is put into place, a small pressure boosting from the MPP reduces the wellhead pressure (WHP) to 20 barg. If looking at lift gas in well as champagne bubbles in a glass, with the lower WHP, With the lower WHP, the champagne bubbles get bigger and more gas comes out of the oil, which reduces the required gas lift rate for the same BHP. The gas lift efficiency energy can be high at low gas lift rate with the low gas lift rates, as shown in Fig. 10, when combined with a small boosting, the total lifting efficiency is maximized. While it should be recognized that multiphase boosting has significant potential to improve energy efficiency, gas lift can be very beneficial in many cases. From an operational point
0%
100 150 200Schlumberger 250-Private
300 Compressor discharge pressure, bara
350
Fig. 8: Sensitivity to compressor discharge pressure.
Schlumberger-Private
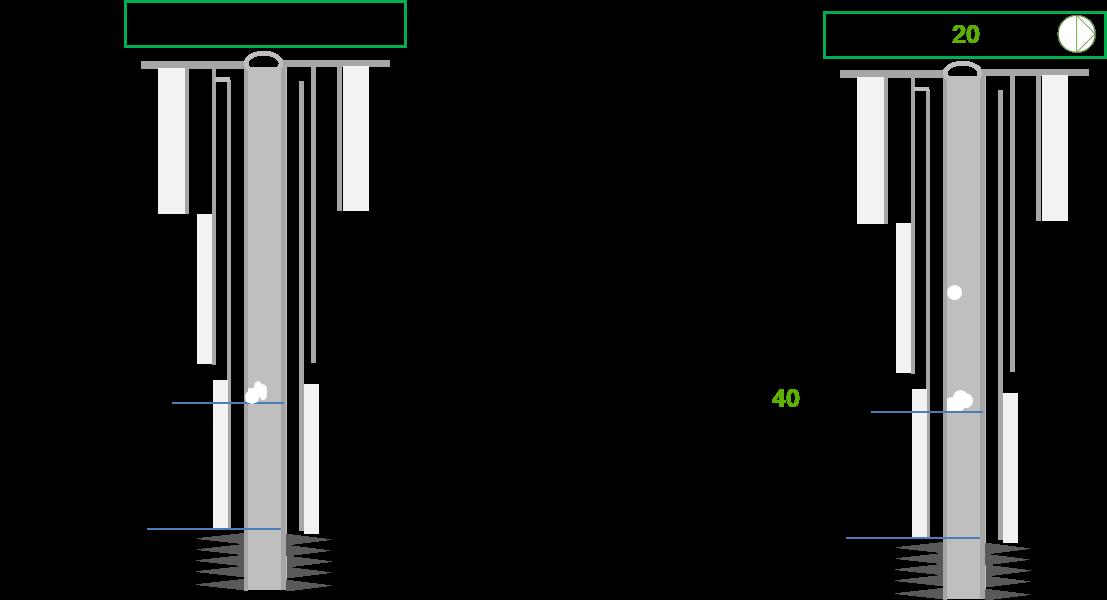