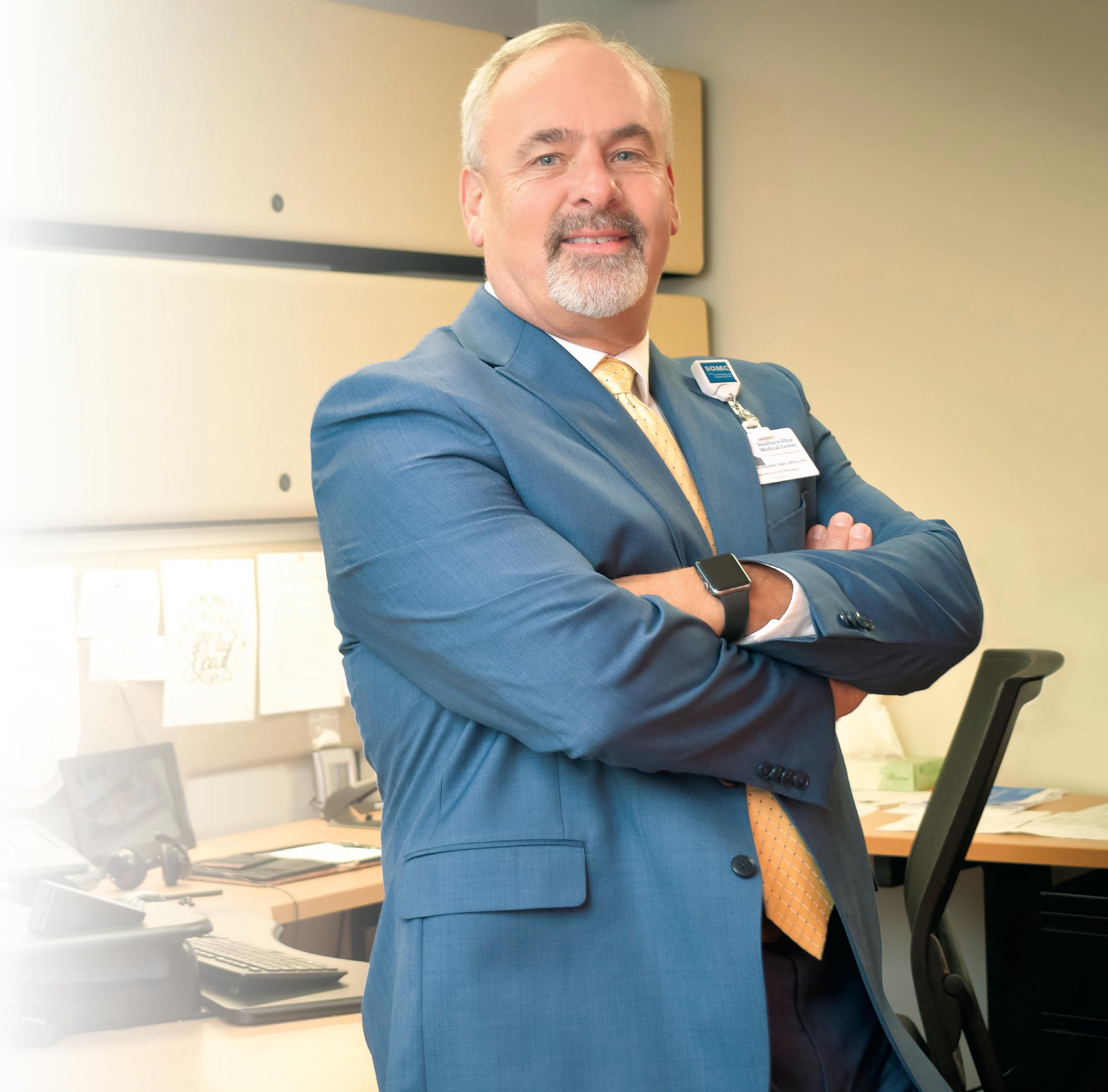
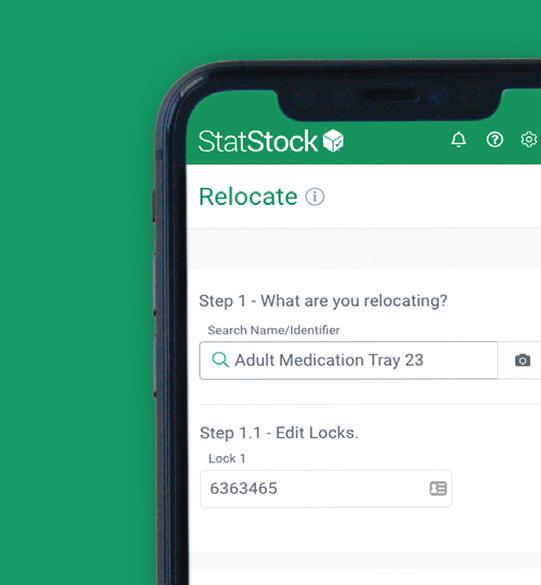
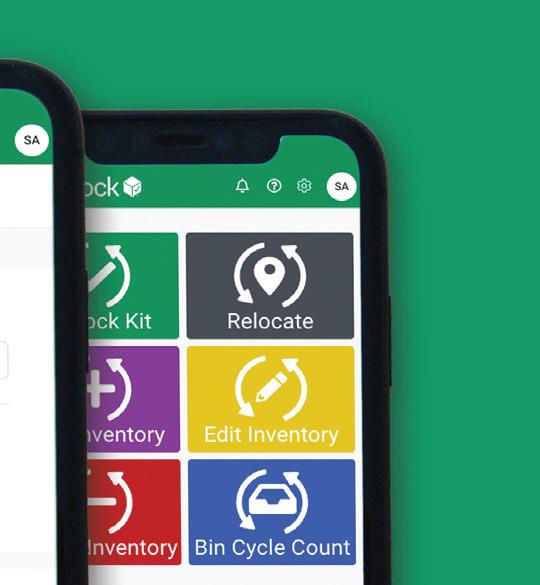

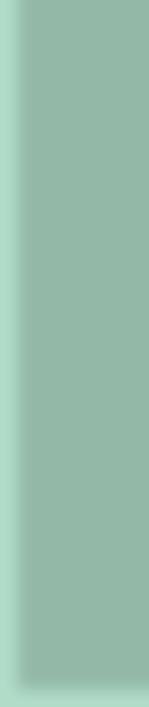
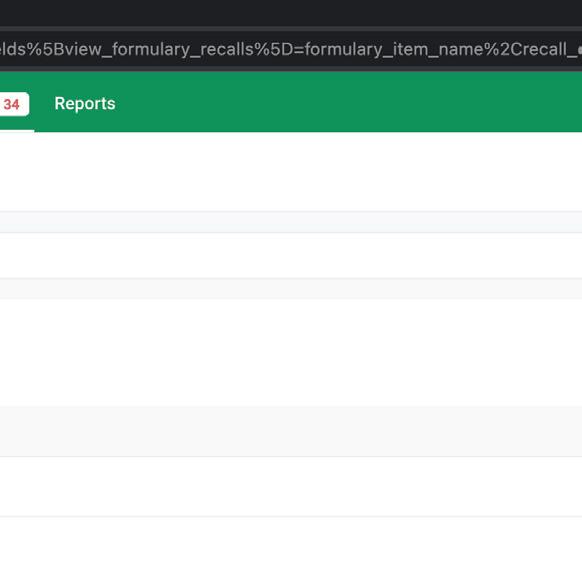
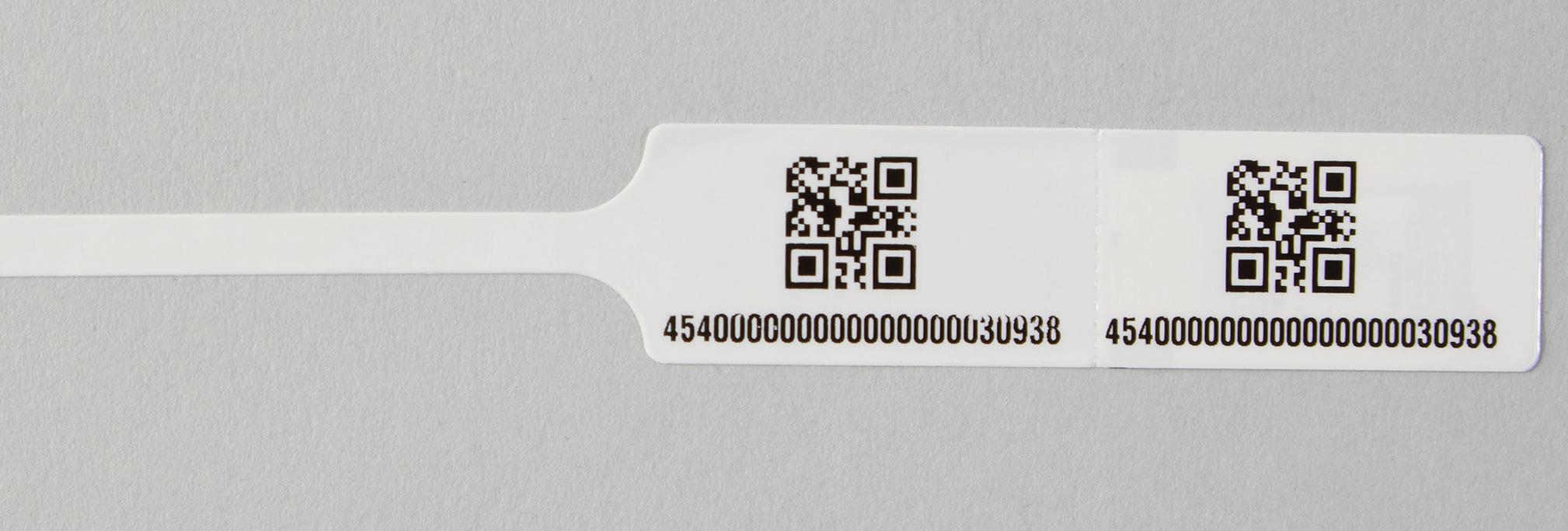
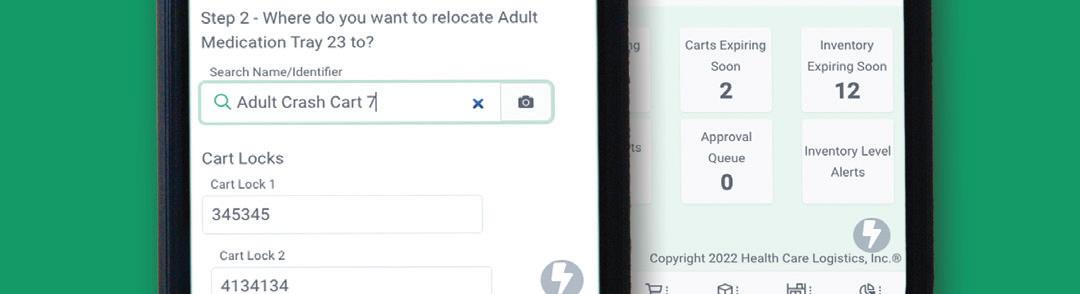




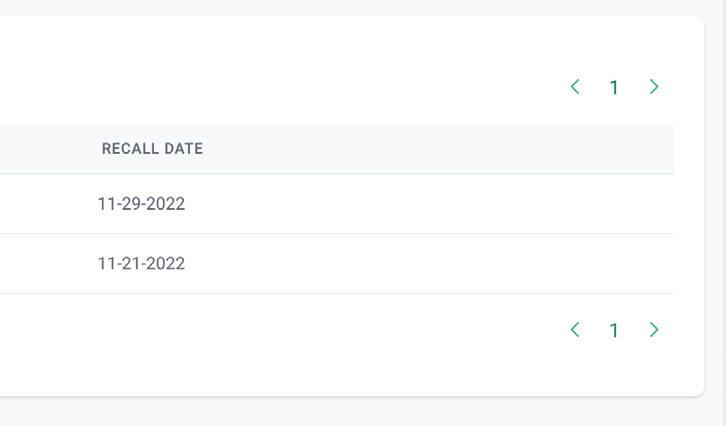
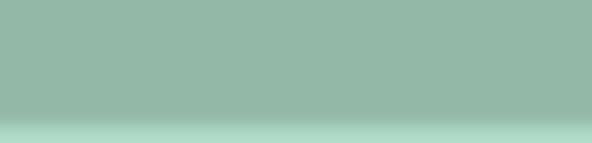

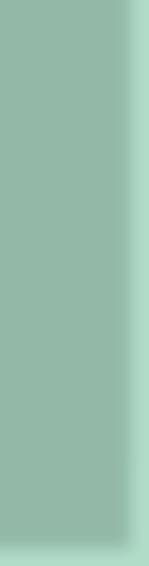
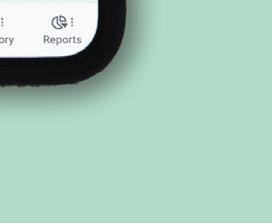
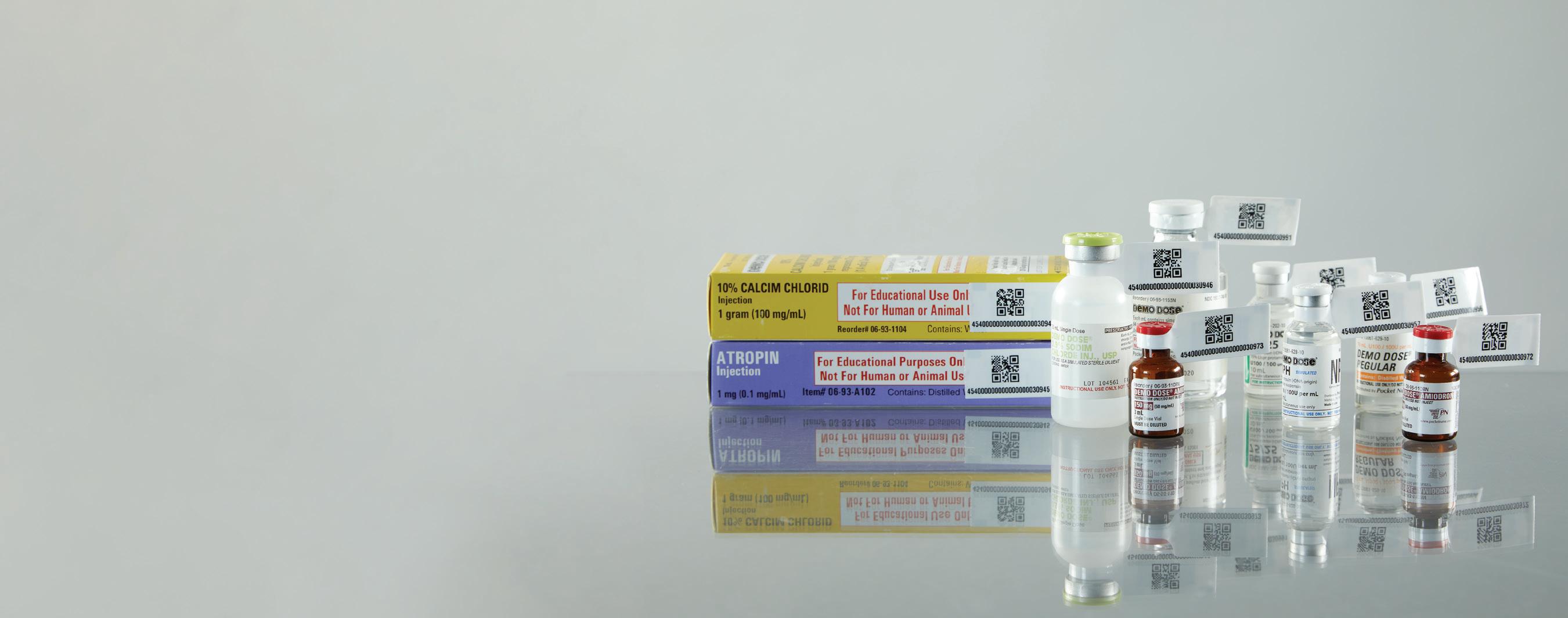
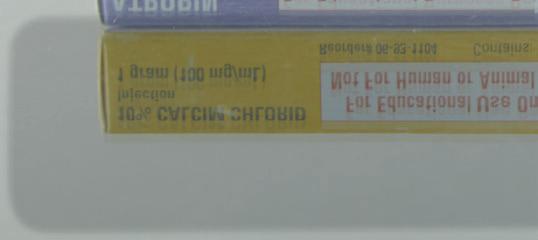
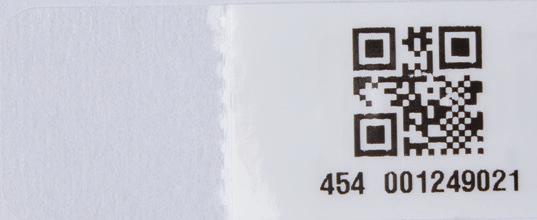
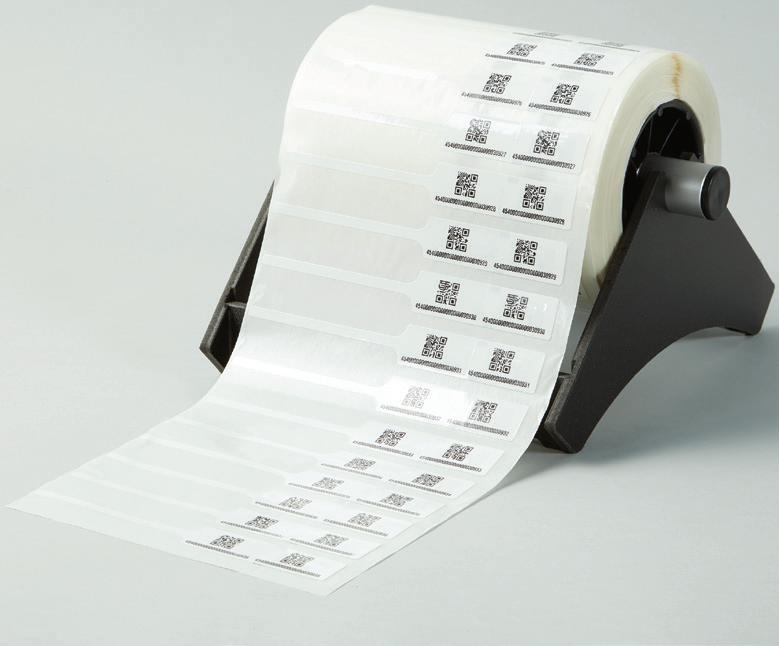

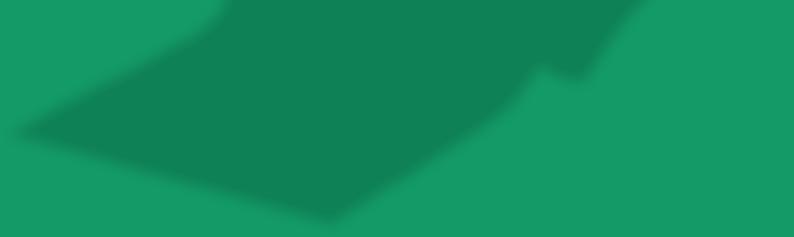
*Product shown with optional/custom features
Containment Primary Engineering Control (C-PEC)
Protection: Product, Personnel, & Environmental
Containment Primary Engineering Control (C-PEC)
Optimized for Sterile Hazardous Drug Compounding Systems
Telescoping or Mechanical Auto-Rising Base Stand Options
Optional IV Bar with 3 Height Locations and 6 SST Hooks
Interior Duplex Outlets and Cord Pass-Through Port
Custom Back-Wall Viewing Window for PC Monitor
Up to 12 inch (305 mm) Access Opening
LabGard ES NU-813 Series
Optimized for Non-Sterile Hazardous Drug Compounding
Telescoping or Mechanical Auto-Rising Base Stand Options
Optional Ergonomic Mount for PC Monitor, Keyboard, and Mouse
Double Exhaust Filter with Bag-In/Bag-Out Options
Polycarbonate Viewing Window and Sidewalls
Sidewall Waste Pass-Through Ports
Protection: Personnel & Environmental
*Product shown with optional features
In the ever-evolving world of hospital and health system pharmacies, staying at the forefront of technology, services, and products isn’t just about keeping pace — it’s about ensuring your patients receive the highest quality care and that your operations run smoothly and effectively. This Winter issue of 20Ways is here to support you in that journey, highlighting the latest advancements in clean technology, supply chain innovations, and customized service solutions that truly address the unique needs of your pharmacy.
Inside, you’ll find valuable insights into navigating the Drug Supply Chain Security Act (DSCSA) and understanding the vital role centralized medication access teams play in hospital settings, two areas shaping the future of pharmacy operations. And, of course, this issue would not be complete without twenty impactful product and service profiles designed to support your goals — whether it’s improving patient compliance, streamlining workflows, or strengthening your pharmacy’s financial performance.
Thank you for your unwavering dedication to advancing patient outcomes. We hope this issue brings you practical tools, fresh perspectives, and, most importantly, inspiration to help your pharmacy continue to thrive.
Greg Cianfarani, RPh Founder & CEO
CEO & FOUNDER
Gregory Cianfarani, RPh
DESIGN & PRODUCTION
Design & Layout: Lora Bourque
Multimedia: Eric Simmons
MARKETING & OPERATIONS
Director of Marketing & Operations, Samantha Roy
Marketing & Operations Coordinator, Amanda D’Amico Credit Analyst & Bookkeeper, Kristin Fennessey
SALES & BUSINESS DEVELOPMENT
EVP, Sales & Marketing, Mike Rahme
VP of Strategic Accounts, Chris Kolkhorst
Executive Sales Director, Shaun Russell Account Executive, Savannah DaSilva Account Executive, Jeff Rackliff
PHARMACY MARKET INTELLIGENCE
Marketing Manager, Alexa DiLuca
Pharmacy Market Analyst, Lexi Cianfarani Pharmacy Market Analyst, Michael McEwen
EDITORIAL ADVISORY BOARD
Amanda Binkley, PharmD, BCIDP, AAHIVP Clinical Pharmacy Specialist Infectious Diseases Penn Presbyterian Medical Center
Miriam Cho, PharmD President & Chief Pharmacy Officer MacRx
Lindsey Dymowski Constantino
President & Cofounder
Centennial Pharmacy Services & LTC@Home Pharmacy Network
Mark Garofoli, PharmD, MBA, BCGP, CPE, CTTS Director of Experiential Learning and Clinical Assistant Professor West Virginia University of Pharmacy
Sebastian Hamilton, BSP, RPh, MBA, PharmD, ACE Chief Pharmacy Officer, Operations and Community/ Ambulatory Partnerships, 340B ACE Boston Medical Center
Brian Musiak, PharmD, MBA, CPEL System Director of Pharmacy Care New England
Abby Roth
Owner/Microbiologist
Pure Microbiology
FOLLOW US
LinkedIn @RXinsider Facebook /RXinsiderB2BSolutions X @RXinsider
Instagram @rxinsider
Pinterest /RXinsider
Vimeo /rxinsider
Propofol Injectable Emulsion, USP supplied by Samson Medical Technologies, under the Avet label, is the smart choice for your pharmacy service, offering you the same formulation as Diprivan® , free of benzyl alcohol, sulfites, and latex, with the easy ordering and excellent service that you have come to expect from the providers of SmartPak® .
SmartPak® provides a revolutionary delivery system for these essential drugs, offering faster, easier preparation more economically. It’s also safer. The SmartPak bag system is a convenient alternative to using multiple glass vials. No glass means no breakage during handling. SmartPak saves time and labor with less waste. SmartPak — the smart choice for your pharmacy service.
This important product now in the exclusive delivery system.
important product now in the exclusive delivery system. provides a
This important product now in the exclusive delivery system.
SmartPak® provides a revolutionary delivery system for these essential drugs, offering faster, easier preparation more economically. It’s also safer. The SmartPak bag system is a convenient alternative to using multiple glass vials. No glass means no breakage during handling. SmartPak saves time and labor with less waste. SmartPak — the smart choice for your pharmacy service.
delivery system for this essential drug, offering faster, easier more economically. It’s also safer. The SmartPak bag system is a convenient using multiple glass vials. No glass means no breakage during handling. SmartPak labor with less waste. SmartPak — the smart choice for your pharmacy service
SmartPak® provides a revolutionary delivery system for this essential drug, offering faster, easier preparation more economically. It’s also safer. The SmartPak bag system is a convenient alternative to using multiple glass vials. No glass means no breakage during handling. SmartPak saves time and labor with less waste. SmartPak — the smart choice for your pharmacy service
66288-1100-11100
SmartPak® provides a revolutionary delivery system for this essential drug, offering faster, easier preparation more economically. It’s also safer. The SmartPak bag system is a convenient alternative to using multiple glass vials. No glass means no breakage during handling. SmartPak saves time and labor with less waste. SmartPak — the smart choice for your pharmacy service
SmartPak® provides a revolutionary delivery system for these essential drugs, offering faster, easier preparation more economically. It’s also safer. The SmartPak bag system is a convenient alternative to using multiple glass vials. No glass means no breakage during handling. SmartPak saves time and labor with less waste. SmartPak — the smart choice for your pharmacy service.
CLEAN TECHNOLOGY, SUPPLIES, SERVICES
Clean technology, supplies, and services industry expert Q&A, Market’s Leaders Buyer’s Guide, and more. page 46
THE VALUE OF A CENTRALIZED MEDICATION ACCESS TEAM
Discover the benefits of Centralized Medication Access (CMA), which simplifies specialty medication processes, enabling clinical teams to focus on patient care. page 28
FROM BOTTLENECKS TO BREAKTHROUGHS; LEVERAGING TECHNOLOGY TO OPTIMIZE PHARMACY WORKFLOWS
Exploring the impact of network platforms and digitalization on the end-to-end healthcare supply chain. page 92
HOW STANDARDIZATION LED TO CONSISTENCY, VISIBILITY, AND LESS RISK
Helmer Scientific — Improving Your Cold Storage Through Standardization page 22
SOUTHERN OHIO MEDICAL CENTER
PUTS PATIENTS FIRST WITH INNOVATIVE SPECIALTY PHARMACY SERVICES
CPS — The Mission: Making a Difference page 36
DBA KCCARE HEALTH CENTER
TRANSFORMS PATIENT CARE FOR THE UNDERSERVED COMMUNITIES
Elevating Patient Health With ScriptPro’s Pharmacy Solutions page 56
GROWING A SUCCESSFUL COMPOUNDING
PHARMACY: THE CRITICAL ROLE OF ENVIRONMENTAL MONITORING
Rees Scientific and Olive Tree Compounding Pharmacy page 84
USP <800> RESOURCES
Leading pharmacy suppliers of USP <800> compliant solutions. page 14
TRADE SHOW & MEETING EVENT CALENDAR
Detailing key industry events throughout the year. page 74
PHARMACY CASE STUDIES
Discover the stories, research, and reports from real pharmacies. page 68
Gowning Service to Help Keep Your Controlled Environment Ready for the Workday®
PROTECT YOUR PEOPLE. PROTECT YOUR PROCESS.
When you need Cleanroom garments — and the peace of mind that comes with them — Cintas delivers. With strategic ISO 5 Cleanrooms across the U.S., we support a diverse range of industries.
COVERALLS
Get the right coverall for your specific controlled environment needs.
FROCKS, ESD LAB COATS & SPECIALTY GARMENTS
Many options to keep your employees in the cleanroom Ready™ .
BOOTS AND SHOE COVERS
The right footwear for your controlled environment.
GOGGLES
Protective eyewear for your team. Gamma sterilization compatible.
Innovative cleaning solutions at your fingertips.
WIPES
Cleanroom cleaning wipes delivered with your gowning.
VERITY SOLUTIONS — THE FUTURE OF HIGH-PERFORMING HEALTHCARE IS HERE
We serve all healthcare facilities and 340 covered entities by combining innovative technology and best-in-class partnership to optimize pharmacy supply chain outcomes for better financial results and patient care. page 19
RXCARBON® POLY STERILE AND NON-STERILE CHEMO MAT FROM RXCARBON, LLC. — INCREASE SAFETY, LOWER COST
Why are RxCarbon® Poly Chemo Mats the color gray? RxCarbon Poly Mats have two layers of RP718 activated carbon which makes our patented mats appear gray. RP718 activated carbon sequesters oncology and hazardous drugs, mitigating exposure risks to both practitioners and our environment. page 21
COREPOINT ® SCIENTIFIC — MAKE EVERY DROP COUNT WITH LIFESAVING COLD STORAGE
Precision cooling for life-saving storage. Corepoint Scientific’s line of blood bank refrigerators and plasma freezers ensure consistent temperatures, regulatory compliance, and reliable performance — protecting the integrity of critical blood and plasma supplies. page 27
SWISSLOG HEALTHCARE — OPTIMIZED PHARMACY WORKFLOWS FROM INVENTORY MANAGEMENT TO CSC
Deliver exceptional patient care with innovations from the core of the central pharmacy to enhance performance workflow efficiency, improve accuracy, and increase safety. page 33
NOVUM IQ INFUSION PLATFORM FROM BAXTER IS A PUMP PLATFORM LIKE NO OTHER
At every step, the Novum IQ Infusion Platform with Dose IQ Safety Software helps you build and deploy one of the safest and most effective drug libraries possible for large volume, syringe, and enteral infusions. page 35
KWIKDOSE ORAL DISPENSERS FROM MEDSAFETY SOLUTIONS, LLC
KwikDose oral dispensers accurately deliver small volumes of oral liquid medication. Enlarged numbers and easy-to-read marking lines allow for quick and accurate volume identification, even with dark liquids. The unique tip prevents wrong-route administration. page 41
STERI-TAMP ® TAMPER-EVIDENT STERILE SEALS BY ALLIED PHARMACY PRODUCTS, INC.
The only single-use, tamper-evident seal that provides and maintains a 100% sterile barrier. page 43
HCL ® ’S EXCLUSIVE OFFERINGS GIVE PHARMACIES MORE UNIT DOSE PACKAGING POWER
Improve confidence in the quality of tablet repackaging and unit dose batching from start to finish. page 53
VISANTE – HIGH-PERFORMING PHARMACY SOLUTIONS FOR HOSPITALS AND HEALTH SYSTEMS
Our mission is to transform healthcare through pharmacy. We help hospitals and health systems optimize pharmacy operations, improve financial performance, and deliver better patient care. page 55
Q.I. MEDICAL, INC.™ YOUR PARTNER IN USP <797> PHARMACY COMPLIANCE
Providing quality assurance products to hospitals and pharmacies practicing sterile compounding, with a singular focus on pharmacy compliance. Our long-standing regional distribution partners are able to provide exceptional in-person service and training. page 61
Gowning Service to Help Keep Your Controlled Environment Ready for the Workday®
PROTECT YOUR PEOPLE. PROTECT YOUR PROCESS.
When you need Cleanroom garments — and the peace of mind that comes with them — Cintas delivers. With strategic ISO 5 Cleanrooms across the U.S., we support a diverse range of industries.
COVERALLS
Get the right coverall for your specific controlled environment needs.
FROCKS, ESD LAB COATS & SPECIALTY GARMENTS
Many options to keep your employees in the cleanroom Ready™
BOOTS AND SHOE COVERS
The right footwear for your controlled environment.
GOGGLES
Protective eyewear for your team. Gamma sterilization compatible.
Innovative cleaning solutions at your fingertips.
Cleanroom cleaning wipes delivered with your gowning.
AMERICAN HEALTH PACKAGING (AHP) IS A LEADING MANUFACTURER OF SERIALIZED, BARCODED UNIT-DOSE PRODUCTS
With a responsive line of barcoded unit-dose oral solutions, a growing liquid unit-dose offering, as well as individually wrapped inhalants, AHP continues to deliver on it’s commitment to supporting pharmacy efficiency. page 63
MEDI-DOSE, INC./EPS, INC. DELIVERS BAR CODING, PACKAGING, AND LABELING PHARMACY SOLUTIONS
Improve your Solid Oral Unit Dose needs with our comprehensive Bar Coding, Packaging, and Labeling Solutions — designed by healthcare professionals, for healthcare professionals. page 67
REDUCE THEFT AND MISUSE OF CONTROLLED SUBSTANCES IN YOUR ORGANIZATION WITH PROTENUS DRUG DIVERSION SURVEILLANCE
Utilize artificial intelligence and advanced analytics to audit 100% of medication use transactions — reducing the risk to your workforce, organization, and most importantly, your patients. page 71
ISO-MED — YOUR ASSURANCE FOR TOP-QUALITY PRODUCTS
As a leading provider of pharmacy cleanroom supplies, ISO-MED is dedicated to offering an unparalleled selection of specialized medical, compounding, and cleanroom supplies. We understand the importance of meeting the requirements of USP, accreditation organizations, State BoPs, and the FDA. page 73
NUVEM’S HOLISTIC SOLUTION DELIVERS 100% PATIENT SCRIPT VISIBILITY
Empowering covered entities to successfully manage all their patient scripts with one holistic pharmacy solution, positively impacting patient health and financial outcomes. page 81
MEDIZAP — TERMINAL STERILIZER BY E-BEAM | X-RAY IRRADIATION BUILT FOR COMPOUNDING
Combining expertise and advanced tech, we elevate sterile compounding for 503A and 503B pharmacies. Our solutions enhance safety and effectiveness in custom sterile drugs, addressing FDA shortages for hospitals and patients. page 83
ARL BIO PHARMA — THREE STERILITY TESTING OPTIONS, ONE STANDARD OF EXCELLENCE
Get sterility test results in as little as four hours with rapid test methods. page 89
TRUDELIVERY ® — READY-TO-USE (RTU) PRODUCTS BY ENDO
The TruDelivery® RTU portfolio helps meet the real-world challenges of hospital pharmacies — and is always ready when you are. It’s about time. page 91
SO-LOW ENVIRONMENTAL — YOUR TRUSTED COLD STORAGE MANUFACTURER
For over 65 years, So-Low has been manufacturing ULT freezers and medical-grade refrigeration equipment. Our goal is to provide the highest quality cold storage equipment with a personalized customer service experience. page 95
SIMPLIFI+ ® PHARMACY COMPLIANCE AND SENTRI7 ® CLINICAL SURVEILLANCE — WOLTERS KLUWER
Simplifi+® and Sentri7® applications on one powerful SoleSource® platform help to standardize clinical, pharmacy, and compliance programs. Customers access evidenced-based content, tailored workflows, and robust analytics to improve patient care, quality, and safety. page 97
20Ways MISSION
To educate pharmacy management on products and services that serve to improve patient care or improve a pharmacy’s financial bottom line, while distilling and presenting this relevant information via 20 product profiles.
VIEW 20Ways ONLINE
RXinsider.com/20Ways
GENERAL SUBSCRIPTION INQUIRIES
RXinsider LTD c/o 20Ways
1300 Division Road, Suite 103 West Warwick, RI 02893
General Information: 20Ways@RXinsider.com
20Ways is an official publication of RXinsider.
NOTICE OF POLICY
20Ways is published quarterly by RXinsider LTD, 1300 Division Road, Suite 103, West Warwick, RI 02893. Postmaster: Send address changes to 20Ways/RXinsider, 1300 Division Road, Suite 103, West Warwick, RI 02893. Notification of address change must be made six weeks in advance, including old and new address with zip code.
Editorial — views expressed in articles or profiles in the 20Ways are those of the author(s) and do not necessarily reflect the policies and opinions of RXinsider, our editorial board(s), our advisory board(s), or staff. Advertising – products, services, and educational institutions advertised in 20Ways do not imply endorsement by RXinsider.
Copyright © 2024 RXinsider LTD. All rights reserved. Reproduction without permission is prohibited.
With increasing drug shortages and supply chain disruptions, access to quality medicine is more important than ever.
Leiters Health is an FDA-registered 503B outsourcing provider of high-quality compounded sterile preparations and pharmacy services including:
Pre-filled syringes and IV bags; pre-labeled and ready to administer. ON-Q* Pain Relief System Pharmacy Fill Service. Opioid-free surgical pain services medications.
Ophthalmic medications including FDAcompliant repackaged Avastin
Contact us to learn how we can support your hospital pharmacy and your patients.
Leiters.com | 800.292.6772 | info@leiters.com
48”W x 25-1/2”D x 40”H x 84”H
36”W x 25-1/2”D x 40”H x 84”H
24”W x 25-1/2”D x 40”H x 84”H
48”W x 25-1/2”D x 40”H x 54”H
36”W x 25-1/2”D x 40”H x 54”H
24”W x 25-1/2”D x 40”H x 54”H
48”W x 32-3/4”D x 34”H 36”W x 32-3/4”D x 34”H
x 32-3/4”D x 34”H
The workstations can be prewired or supplied with a blank quad and data box for easy wiring. As your needs change, so can your design!
Non-electrical ships in 7-10 business days after payment. Pre-wired takes a few weeks.
All include Slate Grey laminate tops, Designer White décor panels, and RX White metal components.
www.RXinsider.com/USP800
We serve all healthcare facilities and 340 covered entities by combining innovative technology and best-in-class partnership to optimize pharmacy supply chain outcomes for better financial results and patient care.
CEO: George Puckett
Founded: 2015
Employees: 160
Toll-Free Phone: (800) 581-1378
Phone: (425) 947-1922
Address: 12131 113th Avenue NE, #200 Kirkland, WA 98034
Website: www.verity340b.com
Verity Solutions has been the leader in 340B program administration and now offers pharmacy supply chain optimization solutions for all healthcare entities. Recognized as Best in KLAS: 340B Management Systems for six years, and in the 2024 KLAS Emerging Solutions Top 20 Report, we are on a mission to create pharmacy excellence through predictable automation and outstanding support so that every customer can maximize their savings. We partner with integrated healthcare systems, acute-care hospitals, community health centers, federally qualified health centers, pharmacies, and 340B-eligible covered entities throughout the U.S. who rely on Verity software and services to successfully manage their pharmacy purchasing and 340B program.
Our powerful cloud-based software platform provides comprehensive 340B program management solutions, including split billing, contract pharmacy, and specialty contract pharmacy. Plus, a contract pharmacy gateway solution called VHUB®
Our pharmacy purchase optimization products offer real-time, intelligent solutions that automatically verify contract pricing and select the best priced NDC available for your complete order. We enable pharmacy buyers to dramatically decrease drug spend and save time while maintaining supply.
Our depth of in-house technical and software development resources and our highly skilled account management team are closely aligned to swiftly adapt as changes arise. We offer:
• Agile Software Platform: Built and deployed with security, performance, scalability, and agility as primary goals.
The Verity 340B platform is HITRUST® certified, demonstrating robust HIPAA compliance.
• Intuitive Application: Designed with our users in mind, we maintain ongoing feedback and collaboration with our clients. This collaboration steers our continual software and services development.
• Responsive Support: Designated account managers provide focused support, training, audit readiness, and regular business reviews to maximize your 340B program success and help you maintain compliance.
We continually invest in our technology and people to ensure success for our clients. With increasing pharmacy costs and complexity, it is more important than ever to have the right solutions — and the right partner.
n Highlights
• Industry-leading core functionality of our platform with optional, patent-pending add-on modules to enhance all aspects of 340B operations in challenging and unique environments.
• Access to your own unique program test environment — before and after implementation. Test environment runs continually in parallel to your live system.
• Easy and exportable reporting functionality, including detailed data for manufacturer audits, HRSA audits, and UDS reporting.
• Multiple vendor support with controlled substances ordering system (CSOS) — efficiently place orders with both EDI (electronic data interchange) and non-EDI vendors.
• Two-week sprint release cycles ensure timely software updates driven by customer feedback, regulatory changes, and user needs.
• Verity Care Card Program — directly pass 340B savings to uninsured and underinsured patients.
• Referral capture opt-in functionality to compliantly add meaningful savings lift to your 340B program.
• Responsive customer service provided by our in-house staff — 80% of our customer support cases are resolved within two hours; 95% resolved within 24 hours.
Specifications:
• Validated Sterile, Gamma Irradiated
• 600 ml spill capacity
AT $.71/PAD
• RxCarbon Poly protects surfaces during transport, storage, compounding, and infusions.
• Virtually eliminates cross-contamination of liquid hazardous drugs
• Meets ISO 9073-10 and BS EN 13795 standards for low lint and low particulate matter
RxCarbon® Poly Protects:
Employees, patients, and environment by deactivating and absorbing HD/Oncology liquids during:
• Administration, Infusion, Spills, Transporting , and Compounding
Unlike White or Blue Mats, our Gray Mats, with TWO layers of RP718 Activated Carbon, Sequesters Hazardous Drugs The Next Generation Surface Protection & Wipe With Hazardous Drug (HD) Deactivation
Place RxCarbon Poly on the surface. Hazardous Drugs are adsorbed/absorbed preventing surface contamination.
Hazardous drugs are prevented from being released into the environment and contaminating our water. Easy
Responsible
Protect healthcare workers, patients and the public from hazardous oncology liquids.
President & CEO: Gregg Short
Founded: 2003
Employees: <20
Toll-Free Phone: (866) 436-9264
Phone: (760) 930-9101
Why are RxCarbon® Poly Chemo Mats the color gray? RxCarbon Poly Mats have two layers of RP718 activated carbon which makes our patented mats appear gray. RP718 activated carbon sequesters oncology and hazardous drugs, mitigating exposure risks to both practitioners and our environment.
Address: 6054 Corte del Cedro Carlsbad, CA 92011
Website: www.rxcarbon.com
RxCarbon®, LLC was founded in 2019, and our pads are protected by U.S. Patent #11,344,933. RxCarbon is the only absorbent pad that sequesters liquid controlled and hazardous drugs with two layers of RP718 activated carbon. We started out looking for a way to eliminate illegal diversion of narcotics. RxCarbon® Pad was developed for existing RCRA and Sharps waste containers to help address illegal diversion from waste containers. Our pads can easily be placed inside waste containers by end users or waste container manufacturers as a replacement of the current absorbent pads.
After designing the pad, we recognized a need to address USP 797 and USP 800 standards and decided to add an impermeable backing to the pad, creating RxCarbon® Poly. Practitioners handling hazardous drugs during compounding, infusions, transporting, or as a clean-up wipe can use RxCarbon Poly.
RxCarbon® Poly Chemo Mat product line comes in sterile and non-sterile versions, is 11x17" lying flat, and can be used as a clean-up wipe. Each mat has an absorption capacity of 600 mL. Our sterile version is validated sterile and gamma irradiated. We designed RxCarbon Poly to provide surface protection during compounding, infusions, transporting, and as clean-up wipes. Practitioners handling hazardous drugs risk occupational exposure. RxCarbon absorbent pads sequester liquid hazardous drugs and reduce continued exposure and cross-contamination. RxCarbon Poly Mats meet ISO 9073-10 and BS EN 13795 standards for low lint. RxCarbon provides increased safety and lower cost when comparing other blue chemo mats.
“As studies have repeatedly shown, hazardous drugs often migrate past compounding hoods and work surfaces as far as counters, doorknobs, and elevator buttons. The new RxCarbon pads and wipes are a major leap forward in providing a simple, cost-effective method for greatly reducing contamination by these pharmaceuticals that are life-saving when administered appropriately but potentially harmful when present consistently in the work environment. I have personally witnessed the absorption capacity of the pads which is also a benefit in the case of spills or a leaking IV set. I highly recommend them for both hazardous drug compounding areas and hazardous drug administration settings. Using the RxCarbon® wipes routinely during compounding and adding them to all HD spill kits is the next step in reducing routine contamination and protecting employees and patients.”
— Charlotte A. Smith, R. Ph., M.S., President, GreatWorks LLC
• HCP — Hospital Pharmacy Conference
• ASHP
GPO Affiliations
• Premier, Inc.
Ordering Information
For more information or a quote, email info@rxcarbon.com or call (866) 436-9264.
RxCarbon® Poly Sterile (RXCp1117PS-(1)cs): Case quantity 300, individually bagged, master bag of 25, 12 master bags in case.
MSRP $362.50
RxCarbon® Poly-Sterile (RXCp1117PS-(5)cs): Case quantity 300, five pack, master bag of 25, 12 master bags in case.
MSRP $324.00
RxCarbon® Poly Non-Sterile (RXCp1117P-(10)cs): Case quantity 300, 10 pack, master bag of 50, six master bags in case.
MSRP $212.50
“Since switching, we have not experienced temperature excursions, and the units maintain their setpoint.”
The hospital facility is the flagship location of a widely-recognized integrated, not-forprofit healthcare system. This location boasts yearly net patient revenues of over $2B and over 38,000 annual discharges.
As the main campus of a leading health system in medical research and patient care, the organization’s core values of innovation, excellence both for patients and staff, and stewardship of resources demanded this problem be addressed. Every temperature excursion was an opportunity for a drug to lose safety or viability, causing danger to patients and financial loss to the hospital.
With over 1,000 staffed beds and several outpatient facilities to support, the pharmacy manager at this nationally-recognized research hospital was looking to streamline oversight of the eighty-five pieces of cold storage equipment responsible for storing and distributing life-saving vaccines and medications across her facility.
Her existing cold storage fleet included a collection of mismatched units from various vendors that required a staggering 1,000 manual log recordings per week. Recognizing the value of consistent monitoring and the immense burden of weekly manual temperature logs, the pharmacy director installed a remote-monitoring system to track cold storage performance in real time.
Not long after the installation of the new monitoring equipment, performance issues began to surface in the cold storage fleet. The facility was experiencing temperature excursions in some of their refrigerators multiple times per day. The pharmacy team spent weeks “chasing their tails” adjusting and readjusting units that had fallen out of acceptable temperature range.
“These units are reliable and consistent, which is a huge relief for me and my team, as the previous units were a big point of stress and difficult to manage.”
The problem of temperature-controlled transportation and storage is not new in the medical industry, however in recent years, particularly with the advent of biologic medications, the medical cold chain has become a critical and central component in the healthcare industry with manufacturers and health systems spending millions of dollars each year to produce, transport, and store temperature sensitive medications, vaccines, and other necessary patient care material.
Improper temperature storage can have potentially dangerous health risks to patients. Improper storage can reduce the effectiveness of vaccines, medications, and diagnostic tools. Exposure to improper storage can render some vaccines inert and can lead to a false sense of security with patients believing that they are protected from certain ailments, when they are not. Improper storage can also reduce the potency of medications, resulting in poor patient outcomes, and reagents and samples stored at improper temperatures can create testing inaccuracies that can lead to misdiagnosis.
Surprisingly, until recently, regulations on refrigerators for use in healthcare settings were relatively lax. Many patient care settings relied on food-grade refrigerators to store medications. However, recognizing the potential risk to patients, the CDC released the Vaccine Handling Toolkit with recommendations that vaccines be stored in purpose-built units both to protect temperature sensitive materials and to reduce the burden on staff for manual monitoring and adjustment.
Constant monitoring and adjustment of eighty-five refrigerators and freezers, many of which were non-medical-grade units, spread across the central pharmacy and throughout the nursing floors was an unsustainable arrangement for this respected hospital.
Every minute spent outside of proper storage temperature, hospital resources and patient health were at risk, and the overloaded staff struggled to keep up with the necessary adjustments each time a unit fell out of the acceptable temperature range. It was clear that standardizing to medical-grade cold-storage would be imperative for this health system to maintain their commitment to delivering the best outcomes for patients and the best experiences for staff.
While standardization required significant upfront investment, the benefits were clear.
• Reduced clinical staff-hours spent adjusting out-of-range units
• Reduced biomedical staff-hours spent repairing low-quality units
• Reduced risk of material and reputation loss to the hospital
• Reduced health risk to the patient
“Switching to Helmer refrigerators has been a night and day difference.”
“Having the peace of mind is priceless.”
Given these benefits, the pharmacy manager decided to swap out all eighty-five of her cold storage units in favor of medical-grade, NSF/ANSI 456 certified GX Solutions cold storage units from Helmer Scientific.
After replacing her eighty-five mismatched units with GX solutions refrigerators, the pharmacy manager had this to say:
“Since switching, we have not experienced temperature excursions, and the units maintain their setpoint. They are reliable and consistent, which is a huge relief for me and my team, as the previous units were a big point of stress and difficult to manage.”
In addition to peace of mind and reduced staff burden, the hospital has experienced several unexpected benefits from standardizing.
• Reduction in noise output – At roughly the noise output of a quiet library, Helmer GX solutions reduce distractions and improve experience on patient floors.
• Efficiency from standardization – Staff need only learn the systems once and can successfully operate any cold storage unit in the hospital.
• Reduced down-time – As a bulwark for reliability in the medical-grade refrigeration industry, Helmer’s GX Solutions are designed and tested to perform under extreme conditions, providing performance and reliability for the long-term.
• Repair and maintenance efficiencies – Since all eighty-five units are Helmer units, the biomedical staff requires technical knowledge for fewer units, allowing for easier and faster repairs, more efficient preventative maintenance, and the ability to carry replacement parts on-hand.
When asked about the investment to standardize to Helmer GX Solutions cold storage units, the pharmacy manager replied, “Switching to Helmer refrigerators has been a night and day difference.”
The standardization process was so successful that the health system has now added Helmer cold storage units as a standard part of the blueprint for any facility expansion or renovation.
Medical-grade cold storage is imperative for hospitals and health systems that value patient outcomes. Trends in diagnostics and medicine demand higher volume and higher levels of precision for temperature sensitive materials. The increased demand for cold storage will add operational complexity for both clinical staff and biomedical teams. Investing in reliable cold storage across the care setting can reduce complexity by creating uniform processes for staff operators, reducing technical knowledge burden on biomedical teams, streamlining parts ordering and, as the pharmacy manager put it, “having the peace of mind is priceless”.
Consistency, visibility, and less risk for sensitive pharmaceuticals, vaccines, and biologics
UPGRADE TO STATE-OF-THE-ART BLOOD BANK REFRIGERATORS AND FREEZERS
Maximize blood banking efficiency with our advanced cold storage solutions, featuring generous storage capacity, precise temperature control, and an optional chart recorder for continuous monitoring. These units create the ideal conditions for preserving life-saving inventory, ensuring reliability when every drop counts.
Industry Compliant
Class II Medical Device
21CFR Part 820 Compliant
• AABB’s StandardsCompliant Product
• EPA SNAP Compliant
ETL and cETL Listed
Units include stainless steel sliding drawers with a 400+ blood bag capacity for single door units and an 800+ bag capacity for double door units.
Our models are equipped with advanced temperature monitoring systems and a full array of alarms.
Efficient Cooling
Designed with natural, hydrocarbon refrigerants and variable speed compressors, resulting in minimal noise levels and reduced operational costs.
Preserving Life, Ensuring Safety Blood Bank Refrigerators and Plasma Freezers
President: Laura Steiner
Founded: 1994
Employees: 150+
Toll-Free Phone: (800) 648-4041
Phone: (843) 821-8010
Precision cooling for life-saving storage. Corepoint Scientific’s line of blood bank refrigerators and plasma freezers ensure consistent temperatures, regulatory compliance, and reliable performance — protecting the integrity of critical blood and plasma supplies.
Address: 125 Varnfield Drive Summerville, SC 29483
Website: corepointscientific.com
Corepoint® Scientific, a Horizon Scientific Inc. brand, provides a full range of temperature-controlled equipment to our customers across healthcare, laboratory and clinical research, pharmaceutical, and industrial segments. Our extensive portfolio of quality products ranges from small capacity countertop refrigerators and freezers to special purpose, application-specific models such as blood bank and plasma storage. Ensuring customer requirements are met, all products are designed in a variety of configurations, from general purpose cold storage to medical and pharmaceutical storage with stringent temperature performance requirements. With over 25 years of experience, Corepoint® Scientific excels at quickly developing customer solutions at competitive price points while providing industry-leading service levels. Our advantage includes a comprehensive array of products and services to meet your temperature-controlled storage needs, an industry leading warranty, a dedicated support team, and many models are available from in-stock inventory and are ready to ship.
Blood bank refrigerators and plasma freezers are essential components in the safe and effective management of blood products. Designed to maintain precise temperature controls, these specialized storage units protect the integrity and viability of blood and plasma. With advanced cooling technology, they provide a stable environment that prevents spoilage and ensures that blood products remain usable for transfusions and other medical procedures. Units feature easy-to-read temperature displays, alarms for temperature deviations, and reliable backup systems, guaranteeing that your critical supplies are always protected.
At Corepoint® Scientific, we prioritize compliance with industry regulations to ensure the highest standards of safety and quality for our blood bank refrigerators and plasma freezers. Our products meet the stringent requirements set forth by the AABB (American Association of Blood Banks), which mandates rigorous quality assurance processes and performance standards for blood storage. Additionally, all of our units are designed to comply with FDA regulations, guaranteeing that they meet the necessary criteria for safe and effective use in medical facilities. By choosing our certified storage solutions, you can be confident that your blood products are stored in environments that adhere to the most respected industry standards.
Each unit in our lineup is engineered for dependable, long-lasting performance with energy-efficient designs and intuitive features. Corepoint® Scientific refrigerators and freezers are ideal for blood banks, hospitals, and research laboratories, delivering unmatched reliability to ensure that critical supplies are consistently preserved and readily accessible.
• Precise temperature control technology ensures consistent maintenance of temperature ranges for storing blood products.
• AABB and FDA Compliance: Meets stringent AABB standards for safety and quality of blood-based products, while adhering to FDA regulations for Class II Medical Devices.
• Stainless steel sliding drawers optimize storage space and provide easy access to products.
• Units include a 400+ blood bag capacity for single door units and an 800+ bag capacity for double door units.
• Designed with natural hydrocarbon refrigerants and variable speed compressors, resulting in minimal noise levels and reduced operational costs.
• Real-Time Temperature Monitoring: Equipped with digital displays and alarms for immediate alerts on temperature deviations.
• User-Friendly Interface: Easy-to-navigate controls and displays for convenient operation.
Centralized medication access (CMA) is revolutionizing the patient journey to specialty care. We consistently see the challenges that arise from the lack of medication access and believe that a centralized medication access team is the solution. It allows the clinical team to concentrate on what matters most: direct patient care. At the same time, it makes the process of obtaining specialty medications for patients much more straightforward.
Contributors:
Angie Amado, PharmD, CSP, Senior Director at Visante
Amy O’Kroley, CPhT, PACS, Specialty Pharmacy Service Manager at Visante
The Challenges: What Happens When CMA Isn’t in the Picture?
CMA is a network where a pharmacy-driven medication access team manages all aspects of medication authorization and distribution. This ensures streamlined processes and improved access and affordability for patients.
Unfortunately, a CMA team is the missing piece in many struggling healthcare systems. To put it simply, medication access is absolutely necessary to achieve the best possible patient and healthcare outcomes.
n Increased Administrative Burden
One of the primary challenges for organizations lacking a CMA model is the increased administrative burden on providers and their staff. They are required to manage time-consuming tasks such as writing appeal letters and navigating insurance coverages, which detracts from their ability to focus on direct patient care. This administrative overload is not only a source of frustration but also a major contributor to provider and staff burnout.
n Inefficiencies in Operations
Without CMA, healthcare operations become less efficient. The absence of streamlined processes means that more time and effort are needed from healthcare providers and clinical staff to manage medication-related tasks. This hampers overall workflow and productivity.
Poor management of medication access often results in financial inefficiencies and reduced financial performance, which can further stress already limited healthcare resources.
n Delayed Treatment
Patients are directly affected by the lack of CMA through delays in receiving their medications. Slower authorization processes can impede access to necessary treatments.
Additionally, this often leads to missed opportunities for financial assistance, resulting in higher out-of-pocket costs for patients. This financial burden can be particularly challenging for patients with chronic conditions who require ongoing medication.
n Patient Stress and Confusion
The complexities of authorization and financial assistance processes without a centralized medication access team can also cause significant stress and confusion for patients. Navigating these complexities can be overwhelming, especially for those who are already dealing with serious health issues.
In fact, without streamlined access and comprehensive financial support, patients are less likely to adhere to their prescribed treatments. Lower medication adherence leads to poorer health outcomes and difficulties in managing chronic conditions.
n Logistical Challenges
Logistical challenges arise as patients may face hassles in obtaining specialty medications. They often have to rely on specialty mailorder pharmacies or navigate complex insurance directives, which can be cumbersome and inefficient for both patients and providers.
From writing appeal letters to navigating insurance coverage, providers and their staff are often required to take on tasks that distract from patient care. A centralized medication model offers several benefits:
• Reduced Administrative Burden: Centralized services take over administrative tasks like handling prior authorizations, managing insurance claims, and coordinating with pharmacies, allowing providers to focus on direct patient care. Studies indicate that up to 75% of healthcare providers believe that centralized systems, like electronic health records (EHRs), enable them to deliver better patient care.
• Enhanced Operational Efficiency: Streamlined processes reduce the time and effort required from healthcare providers, improving overall workflow. Implementing CMA can lead to increased patient throughput and reduced medication errors.
• Improved Financial Performance: Better management of medication access leads to improved financial outcomes
for healthcare facilities. Efficient patient access systems ensure accurate and timely capture of patient information, avoiding claim denials, underpayments, and delays in revenue collection.
• Better Clinical Outcomes: Hospitals with CMA have reported improvements in patient compliance with prescribed medications, resulting in better management of chronic diseases and reduced hospital readmissions.
From skyrocketing medication prices to treatment delays, patients often face significant challenges with the medication access process. CMA offers several benefits for patients, including:
• Timely Medication Access: Centralized services expedite the authorization process, ensuring patients receive their medications faster. This leads to improved treatment outcomes as patients can start their therapies promptly.
• Financial Assistance: CMA connects patients with comprehensive financial support, including copay assistance and drug assistance programs.
This reduces the financial burden on patients, making essential medications more affordable.
• Reduced Stress: By handling the complexities of authorization and financial assistance, CMA simplifies the process of receiving medications. Additionally, clear communication and streamlined procedures help reduce patient anxiety and confusion.
• Improved Health: With reduced financial and administrative barriers, patients are more likely to adhere to their prescribed treatments. This is crucial for achieving better health outcomes and managing chronic conditions effectively.
CMA: Your Comprehensive Solution
Centralized medication access is essential for the modern healthcare system; it solves many logistical challenges, boosts efficiency, and provides patients with peace of mind.
What's more, some covered entities generate as much as 600% in
In short, your patients benefit -and so does your health system.
Turn to dedicated mentorship and accredited in-house continuous education (CE) for ongoing training
Rely on CPS’ network of pharmacy experts for regulatory compliance, clinical, financial, and operational support whenever you need it
Thrive
Work for an organization where you can advance your career trajectory and move up into new roles over time
Nationwide Opportunities:
Corporate Office
Hospital Pharmacy
Health-System Specialty Pharmacy
Part- & Full-Time Positions:
Director of Pharmacy
Staff Pharmacist
Pharmacy Technician
Great Benefits*
Competitive Salary
Medical, Dental, & Vision Insurance
Generous PTO Package
401k Match Program
* Full-time positions only
SCAN TO SEE CURRENT JOB LISTINGS ABOUT CPS FOR
Founded over 50 years ago, CPS Solutions, LLC (“CPS”) is one of the nation’s leading providers of pharmacy and hospital services, employing over 2,500 pharmacy and healthcare professionals and servicing over 800 healthcare facilities nationwide. CPS helps its clients develop and accelerate their own specialty pharmacy services and enables its clients to optimize the efficiency and cost savings of traditional inpatient pharmacy services. CPS’ offerings include specialty pharmacy management, inpatient pharmacy management, pharmacy consulting, 340B program consulting, telepharmacy, supply chain, rehabilitation, and technology solutions.
President & CEO: Cory Kwarta
Founded: 1915
Employees: 500-1000
Toll-Free Phone: (800) 396-9666
Deliver exceptional patient care with innovations from the core of the central pharmacy to enhance performance workflow efficiency, improve accuracy, and increase safety.
Address: 11080 Circle Point Road #500 Westminster, CO 80020
Website: www.swisslog-healthcare.com
Headquartered in Westminster, CO, Swisslog Healthcare has been delivering best-in-class automation solutions and services for more than 100 years. At Swisslog Healthcare, we lead change for better care. Our focus is on improving workflows and reducing the time clinicians spend doing repetitive tasks — enabling more time for patient care. Discover how our pharmacy automation solutions can boost efficiency, improve care, and reduce costs at www.swisslog-healthcare.com.
Hospitals today are held to increasingly higher accountability for the overall patient experience. The timely dispense and delivery of correct medications are critical to improving patient outcomes and fostering a positive experience. Whether on a large scale or small, the right automation can enhance patient safety, decrease medication waste and drug shortages, reduce costs, and enable staff to spend more time focusing on clinical activities. Swisslog Healthcare enables forwardthinking health systems to create a connected medication ecosystem.
n BoxPicker® Automated Pharmacy Storage System provides pharmacies with secure, high-density, modular storage of medications, controlling access, improving pharmacy workflows, and expediting the picking process. The modular design of the BoxPicker enables hospitals to tailor the system to their exact needs. The ability to add multiple operator stations allows for simultaneous operations, significantly increasing efficiency as one technician can stock medications while another can complete dispensing activities. Automated medication storage and retrieval not only eliminates picking errors and increases safety at dispense, but also creates, a more efficient pharmacy workflow. Designed to eliminate the need for static shelving, BoxPicker allows pharmacy staff to focus on clinical tasks and spend less time locating, picking, and verifying medications.
n PillPick® Automated Packaging and Dispensing System is a completely automated solution that decreases human touches in packaging, storing, dispensing, and returning unit-dose medications. The patented PickRing® delivers patient-specific medication on a single ring ready for administration, reducing the opportunity for missed medications
and speeding up administration time. With the ultimate automated pharmacy system for patient safety and operational efficiency, nurses can spend more time delivering high-quality care.
n Consolidated Service Centers (CSCs) or Integrated Service Centers (ISCs) enable forward-thinking organization to combat challenges presented by an increasingly complex supply chain by centralizing supply chain and pharmacy operations off-site. Partnering with Swisslog Healthcare for CSC implementations helps healthcare organizations actualize their CSC goals and maximize benefits from streamlined pharmacy operations. Effective CSCs automate manual processes and standardize workflows, improving operations system wide.
n AutoPack™ Automated Oral Solid Packager is an oral solid packager that integrates easily with pharmacy operations to provide fully automated, patient specific, unit-dose or multi-dose oral solid medication packaging, ensuring that 100% of medications are scan-ready at the bedside.
n ezCUT Automated Tablet Cutter might be compact in size, but offers unparalleled optimization. Tablets of varying sizes (round and oblong) are flawlessly halved, and damaged or irregular tablets are automatically discarded — ensuring the accuracy of every dose. Manually cutting tablets is time-consuming and strenuous, but automating the process with ezCUT saves time and energy, allowing pharmacy staff to focus on high-value clinical tasks. ezCUT can be used as a standalone solution or complementary to either the PillPick® or AutoPack™
n AutoCarousel® Semi-Automated Pharmacy Storage System, together with medication management software, transforms medication management by reducing labor, drug waste, missing medications, and picking mistakes.
AutoCarousel is accurate and reliable, and the vertical design ensures maximal storage in a compact footprint. In addition, AutoCarousel helps pharmacies ensure medication safety with password-protected access and barcode scanning during the stocking and dispensing processes to track the chain of custody and manage all items comprehensively.
n Delivery Manager is a sophisticated application that enables your hospital to achieve a complete chain of custody, ensuring compliance, control, and, most importantly, patient safety. The Delivery Manager application reports carrier locations, identifies the sender and receiver, and enables visibility into carrier contents. Adding the Delivery Manager application to your TransLogic pneumatic tube system technology helps department leaders in your facility gain ultimate visibility into what is being delivered throughout the hospital. When Delivery Manager is combined with RFID, WhoTube® and timely software updates from TransLogic, your facility achieves a complete chain-of-custody. Implementing intelligent tracking with Delivery Manager provides a single point of control, accountability, and traceability throughout the entire delivery process — from your tube system to your manual transport.
According to ISMP guidance for Optimizing Safe Implementation and Use of Smart Infusion Pumps, the goal for drug library compliance should be 95% or greater. Even a single percentage point increase in drug library compliance can significantly reduce the number of unprotected infusions.2 Baxter infusion platforms with Dose IQ Safety Software deliver 97% compliance within one month of implementation.1
AVAILABLE IN THE NOVUM IQ INFUSION PLATFORM. POWERED BY
President & CEO: Jose Almeida
Founded: 1931
Employees: 50,000 globally
Stock Symbol: BAX
Toll-Free Phone: (800) 422-9837
Phone: (224) 948-1812
Address: One Baxter Parkway Deerfield, IL 60015
At every step, the Novum IQ Infusion Platform with Dose IQ Safety Software helps you build and deploy one of the safest and most effective drug libraries possible for large volume, syringe, and enteral infusions.
Website: baxter.com and novumiq.com
For over 90 years, Baxter has introduced significant medical innovations, including the first commercially produced intravenous (IV) solutions and the first home-based dialysis system as an alternative to hemodialysis in a hospital or clinic. Baxter has been highly innovative in providing healthcare solutions to unmet medical needs through scientific advancement as well as strategic acquisitions and partnerships.
Every day, millions of patients, caregivers, and healthcare providers rely on Baxter’s leading portfolio of diagnostic, critical care, kidney care, nutrition, hospital, and surgical products used across patient homes, hospitals, physician offices, and other sites of care. We’ve been operating at the critical intersection where innovations that save and sustain lives meet the healthcare providers who make it happen. With products, digital health solutions, and therapies available in more than 100 countries, Baxter’s employees worldwide are now building upon the company’s rich heritage of medical breakthroughs to advance the next generation of transformative healthcare innovations. To learn more, visit baxter.com and follow us on X, LinkedIn, and Facebook.
n Novum IQ Infusion Platform — Large Volume and Syringe Pump Models
Benefit from an elevated infusion experience. The Novum IQ Large Volume Pump and the Novum IQ Syringe Pump share advanced technology and enhancements to help protect patients and standardize infusion administration.
• Streamlined workflows and intuitive operation to drive compliance in the use of pump safety software, helping to ensure a safe continuum of care for patients.
• An easy-to-use common interface across large volume and syringe pumps, supported by 350+ hours of human factors testing, helps to simplify pump operation for clinicians and streamline training.
• On-screen barcodes with scan prompts ensure that pumps are correctly identified, helping to provide safety and efficiency during auto-programming and drive auto-programming compliance.
• A visual beacon so clinicians can see from a distance that a pump needs attention.
• A backlit keypad and an ambient light sensor to improve visibility.
• Baxter single set technology accommodates both large volume pump and gravity infusions to deliver efficiency, safety, and savings.
• A broad range of compatible syringes have been qualified for use with the Novum IQ Syringe Pump.
n Dose IQ Safety Software
Rely on Dose IQ Safety Software to help you protect more infusions and reduce the risk of preventable errors. Accurate and up-to-date drug libraries are important to help ensure patient protective measures are maintained throughout infusion therapy, especially for patients receiving critical medications. However, even when drug libraries are used, current implementation practices can limit their effectiveness. At every step, webbased Dose IQ Safety Software helps you build and deploy one of the safest and most effective drug libraries possible. Dose IQ Safety Software offers unique and best practice capabilities.
• Titration error prevention technology allows Novum IQ pumps to intercept dose and rate changes that could be potentially harmful.
• Unique drug-linking feature that provides more library capacity and flexibility with 32 care areas and 10,000+ drug entries across large volume and syringe pumps.
• Comprehensive units of measure, including MillionUnit dosing.
• Color coding for enteral infusions.
• Configurable anesthesia care area settings with optional passcode protection.
• Standardized drug library creation in partnership with First Databank (FDB) and incorporation of its FDB Infusion Knowledge database.
Count on rigorous cybersecurity to provide advanced protection for patients’ infusion data. The Novum IQ Infusion Platform is built to meet stringent cybersecurity protocols.
• UL 2900 certification, which attests to independent cybersecurity testing and assessment for the IQ Enterprise and Dose IQ2.
• Secure remote updates to IQ Enterprise Connectivity Suite on both servers and network.
• Encrypted software and firmware to pumps.
• Collaboration with Health-ISAC and ICS-CERT organizations.
• 95% field serviceability to help get pumps back in use, potentially reducing cost and downtime.
• Modular design with cost-effective field-replaceable units to streamline service and maintenance.
• Remote troubleshooting and diagnostics combined with parts ordering, to help reduce maintenance burden.
The Mission: Making a Difference
Rory Phillips, BSPh, MBA, CPEL, RPh
Director of Pharmacy & Respiratory Services
~ Southern Ohio Medical Center (SOMC)
Founded in 1954, Southern Ohio Medical Center (SOMC) is located in Portsmouth, Ohio. The Main Campus features a 211-bed not-for-profit hospital providing emergency and surgical care to the surrounding community. These services include an inpatient pharmacy and several outpatient clinics offering various healthcare services ranging from oncology and cardiology to rheumatology and primary care, among others. With 60+ offices throughout southern Ohio and northeastern Kentucky, SOMC has 2,600+ full- and part-time staff and 140+ physicians, specialists, and advanced practice providers (APPs).
The health system’s mission is to make a difference in the lives of its patients, employees, and the community. With this mission in mind, Director of Pharmacy & Respiratory Services Rory Phillips, BSPh, MBA, CPEL, RPh, began exploring how to create a specialty pharmacy to better serve SOMC's patients and medical staff members.
Historically, SOMC worked with a mail-order specialty pharmacy to meet patient needs. “The physicians and APPs were happy with the process, but I wanted to deliver a higher level of patient and medical staff satisfaction,” explains Phillips. “I wanted patients and medical staff members to be able to rely on people from here — people who truly understood and cared about the local community ” However, as he began researching who could help him achieve this goal, he found many operated on a call center model. Phillips ultimately chose CPS Solutions, LLC (CPS), one of the nation’s largest pharmacy and hospital service providers, to help build and manage SOMC’s specialty pharmacy.
$2.4M
PATIENT FINANCIAL ASSISTANCE, 2023
92%
TREATMENT ADHERENCE
96%
PATIENT SATISFACTION
100%
MEDICAL STAFF SATISFACTION
“CPS’ patientcentered approach to specialty pharmacy is truly making a difference at SOMC.”
Rory Phillips, BSPh, MBA, CPEL, RPh
Director
of Pharmacy & Respiratory Services
~ Southern Ohio Medical Center (SOMC)
“CPS’ emphasis on local care was a big deciding factor for me,” he says. “But so was their approach. They spent a day and a half with me and others on the leadership team to ensure buy-in and gain a thorough understanding of our health system's operations and priorities.”
SOMC is CPS’ longest-running specialty pharmacy client. With CPS, team members are on site, which means medical staff members and patients talk to their neighbors to help them navigate the complex specialty pharmacy landscape. “As far as patients and medical staff members are concerned, CPS pharmacists and liaisons are SOMC staff,” says Phillips. “This is exactly what I wanted — specialty pharmacy staff building relationships with patients and medical staff members, giving patients familiar people to reach out to for help.”
“[CPS] Pharmacists and liaisons assist physicians and patients in managing all of their prescriptions. It is a holistic approach and includes all of the patient’s medications. The CPS team contacts the patient and manages new and refill prescriptions proactively,” explains Phillips.
In 2023 alone, SOMC provided $2.4M in financial assistance for its patients. “CPS’ patient-centered approach to specialty pharmacy is truly making a difference at SOMC,” says Phillips. Medical staff members and patient satisfaction scores are 100% and 96%, respectively, for 2023. “That, to me, is a clear demonstration of our success,” he adds. “When specialty pharmacy staff can talk to patients or colleagues about their kids, their job, or even the county fair, they put patients at ease and trust pharmacy staff to care for them.”
One of the aspects Phillips appreciates most about CPS is that they are a true teammate for the long run. “Over the years, our goals and priorities have evolved — and CPS has been willing to shift right along with us.”
A significant goal for SOMC is to improve patient care through chronic disease management (CDM). That’s why the health system implemented CPS’ CDM services in all family practice clinics in late 2021. SOMC also worked with CPS to focus on medication adherence, which resulted in patient adherence reaching 92% last year.
Since the third quarter of 2023, CPS has been assisting SOMC with its transition of care processes and the hospitals’ Medicare Star Ratings. The goal is to minimize readmissions, which can improve patient outcomes while also reducing hospital costs incurred for inpatient stays and procedures. Through this process, CPS coordinates prior authorizations for medications given to SOMC patients at the time of discharge and also submits patient medication counseling documentation in a web-based performance
“With CPS’ help, the pharmacy is no longer considered a cost center — it’s a revenuegenerating operation.”
Rory Phillips, BSPh, MBA, CPEL, RPh Director of Pharmacy & Respiratory Services
~ Southern Ohio Medical Center (SOMC)
information tool to give SOMC credit for performing medication therapy management. SOMC’s specialty staff and the CPS team manage all patient medications holistically; they are doing the work. They are now documenting this work to increase Medicare Star Ratings, thereby reducing direct and indirect renumeration (DIR) fees and improving prescription reimbursement. “It’s one more example of how CPS goes the extra mile.”
In just 10 years, SOMC opened six community pharmacies and has secured space for building pharmacies seven and eight. Revenue growth was dramatic in SOMC’s first year of operation — and they have continued to achieve double-digit gains year after year. “With CPS’ help, the pharmacy is no longer considered a cost center — it’s a revenuegenerating operation,” notes Phillips.
Consequently, SOMC’s specialty pharmacy services became a lifeline for the community. As chain pharmacies began closing stores in the area, some patients were faced with the prospect of driving long distances to get their medications. “The addition of the specialty pharmacy has just lowered barriers for patients to access medication,” he says. “Beyond that, it’s enhanced the quality of care SOMC clinics and medical staff members can deliver.”
Phillips and SOMC do not plan to stop there. “Because CPS represents multiple organizations, they can address limited distribution drugs with manufacturers and payer lockouts with health plans better than I can as a stand-alone pharmacy,” explains Phillips. That dedicated support, amongst many other reasons, is why the health system has signed a contract with CPS through 2035.
Operating a successful health system pharmacy is more complex now than ever before.
With 50+ years’ experience in hospital and health system pharmacy, CPS understands what you are facing. Pharmacy leaders across 800+ healthcare organizations rely on our proven expertise, technology, and services to improve patient care and thrive today and in the future.
Our Solutions:
Compliance, Operations, and
Specialty Pharmacy Patient Management Software Telepharmacy
Remote Order Entry 340B Program Compliance and Optimization
KwikDose oral dispensers accurately deliver small volumes of oral liquid medication. Enlarged numbers and easy-to-read marking lines allow for quick and accurate volume identification, even with dark liquids. The unique tip prevents wrong-route administration.
President & CEO: Steve van Engen
Founded: 2016
Phone: (720) 500-2500
Fax: (720) 500-2571
Address: 11233 E. Caley Avenue Suite 300 Centennial, CO 80111
Website: medsafetysolutions.com/kwikdose
Founded in 2016 by industry professionals with decades of collective medical device experience, the MedSafety Solutions team speaks your language and understands your hospital pharmacy’s non-negotiable need for quality, efficiency, and predictability when selecting critical equipment and supplies. Nimble by design and friendly by nature, our team will do whatever is needed to make sure that you are well informed about your IV administration choices and completely satisfied with the products and services you receive. Our goal is to be a trusted partner, and we know that reliability, responsiveness, expertise, and a friendly, human touch are what it takes to earn that trust.
The latest addition to Medsafety Solution’s product family is the KwikDose oral dispenser. The KwikDose oral dispensers offer the same high-quality oral dispensers pharmacies know and trust. The unique tip prevents wrong-route administration. Enlarged numbers and easy-to-read marking lines allow quick and accurate volume identification, even with dark liquids. KwikDose oral dispensers are available in six convenient sizes (0.5, 1, 3, 5, 10, and 20 mL), in both clear and amber. Also available with blue self-righting tip caps.
Product Specifications
• Sizes: 0.5, 1, 3, 5, 10, and 20 mL
• Available in Clear and Amber
• Made in Denmark
TwoFer Huber-Tipped Needles enable vented and non-vented vial additions and withdrawals, effectively performing the functions of two devices. The TwoFer Needle facilitates the movement of liquid drugs from one container to another without the time and expense of changing needles. Color-coded and available in 1.5" and 1.0" lengths, the TwoFer Needle is appropriate for a variety of receptacle sizes and applications.
n Tamper-Resistant Add Port Caps
Tamper-Resistant Add Port Caps are easy-to-use, hinged plastic caps that impede tampering when storing and transporting IV solutions.
n Female Luer Lock Cap
The Female Luer Lock Cap is designed to seal male Luer fittings on devices such as manifolds, stopcocks or IV sets, reducing the risk of touch contamination and medication leakage.
n KwikVial™ Oral Liquid Containers
KwikVial Containers are used for unit-dose packaging, delivery, and administration of oral liquid medications. Versatile and easy to use, they can accommodate a variety of dosage volumes, are sealed for tamper-prevention resistance and detection, and are designed for efficient packaging and administration.
Key Business Partners
KwikDose and our other products are available directly from MedSafety Solutions and from various distribution partners.
Trade Shows/Meetings Attended
Stop by our booth #439 at ASHP Midyear 2024 in New Orleans.
Ordering Information
For more information or to preorder today visit our website medsafetysolutions.com/kwikdose.
• Sterile and Paper Free (USP 797 Compliant).
• Maintains a 100% sterile barrier* with 3X greater adhesion. *Tested in Nelson Labs, Salt Lake City, UT
• Helps prevent contamination of drugs and provides added protection to pharmacists.
• Will not fall off, even in cold storage conditions (down to -20 degrees centigrade).
• Patented dual-layer indicates true tamperevidence, with “OPENED” marking.
National Sales
Manager: Alex Meadow
Phone: (516) 374-8862
The only single-use, tamper-evident seal that provides and maintains a 100% sterile barrier.
Address: 2905 South Congress Avenue, Suite A Delray Beach, FL 33445
Website: steri-tamp.com
Email: info@steri-tamp.com
Established in 2010, Allied Pharmacy Products, Inc. was created from a commitment to enhance the preparation and distribution of intravenous medication within hospital pharmacies and compounding environments. The development of Steri-Tamp® stems from the insights of a pharmacist who recognized the imperative for improved tamper-evident measures and sterility in IV preparation. Throughout our journey, Allied Pharmacy Products, Inc. has remained dedicated to listening and responding to the needs of pharmacists. This ongoing responsiveness has been instrumental in our continuous product line expansion.
The Steri-Tamp® product line features seven cutting-edge tamperevident seals. Our IV bag port seals come in blue, red, and yellow (labeled CHEMO) variants. For vial seals, we offer options in 13 mm (red), 20 mm (silver), and 28 mm (blue). Among these, our belly button bag seals (green) stand out for their ability to adhere to both the ICU medical “belly button” bag port and the top of a 13 mm vial.
Steri-Tamp® has introduced specialized IV bag port seals tailored to meet the labeling requirements of USP 800 and ISMP. These seals offer a streamlined solution for handling paralytic agents and hazardous drugs in a unified workflow.
What sets Steri-Tamp seals apart is their true tamper-evident design. Utilizing dual-layer technology, these seals serve as a clear indicator to hospital staff if a bag or vial has been tampered with or used. Removing the top foil layer reveals an “opened” layer, after which it cannot be reapplied. Thanks to a 3X stronger adhesive, Steri-Tamp ensures a 100% sterile barrier.
In addition to our sterile options, we also offer two non-sterile syringe seals. These seals boast increased tensile strength, making them easy to remove from the liner and apply to a wide range of containers, including syringes, inhalers, EpiPens, insulin pens, and more. Our latest innovation, the Tamper-Clear Syringe Seal®, enables visibility of syringe markings and barcode scanning on syringes, inhalers, insulin pens, and other related items.
n Steri-Tamp® IV Bag Port Seals:
• Deliver a foolproof and potentially life-saving method to ascertain medication dispensing.
• Safeguard the IV admixture bag’s point of entry from contamination and accidental double dosing.
• Securely attach to the port through a simple “twist” mechanism, ensuring an airtight seal.
• The green belly button bag seal is purpose-built for the unique “belly button” port on ICU medical bags and can also be used on 13 mm vial tops.
n Steri-Tamp® Vial Seals:
• Designed to lie flat on the vial top, effectively preventing bacteria from entering the vial, without overlapping the edges.
• Preserve the medication’s integrity.
• Specially sized for 28 mm, 20 mm, and 13 mm vial tops, ensuring the right seal for the corresponding vial size.
n Steri-Tamp® Syringe Seals:
• Offer non-sterile solutions to provide tamper-evidence for syringes and other medical containers.
• The innovative Tamper-Clear Syringe Seal® provides clear visibility to the syringe barrel and facilitates barcode scanning, making it ideal for sealing small oral, pediatric, and NICU syringes.
n Available in rolls of 1,000 seals each.
n All our seals contribute to reducing waste, streamlining workflow, and ultimately saving you time and money.
“Tamper-Clear works great! Helps prevent the caps falling off the syringes.”
— Lead Pharmacy Technician, Colorado Springs, CO
“They’re the best seals we use. It’s a must have!”
— Pharmacy Purchasing Specialist, Orangeburg, SC
“Love the syringe seals. Able to remove them without them breaking beforehand. It really is a higher quality seal!”
–– Pharmacy Tech/Purchasing Lead, Houston, TX
Additional Product Lines
Stay tuned for exciting updates to our products set to launch in 2024!
Trade Shows/Meetings Attended
ASHP Midyear, EAHP, NPPA Conference, and various ASHP state affiliate pharmacy conferences.
Ordering Information
Available through major wholesalers and distributors. Visit our “order info” page at steri-tamp.com to find Steri-Tamp® order numbers for your preferred vendor.
• ULPA filter, creating ISO 3 workzone, cleaner than standard ISO 5
• ECM blower, creating stable airflow at energy-efficient 150 Watts
• Comfortable low noise at 55 dBA, full legroom, dished work tray
• 7” Touchscreen Controller With built-in user guide, and 21 CFR Part 11 compliance
• ULPA filter, creating ISO 3 workzone, cleaner than standard ISO 5
• Comfortable low noise at 58 dBA, dished work tray, builtin armrest
• Lowest height in the market at 55”, suitable for cleanroom
• Two HEPA filter in series, allowing exhaust to room instead of ducting
• Comfortable low noise at 57 dBA and full-width front access opening
• Dished phenolic resin worktop, preventing spill, scratch, and corrosion
• Fully customizable according to your needs Model: LHG-4BS-F9
• High-grade stainless steel 316 construction
• Multi-step stations combining several isolators
• Optional integrated VHP generator and freeze dryer
Q. What are the key differences between pharmacy isolators, cleanrooms, and barrier isolators in terms of functionality and regulatory compliance?
Pharmacy isolators, cleanrooms, and barrier isolators (also known as Restricted Access Barrier Systems or RABS) serve distinct roles in pharmacy operations, each with unique functionalities and regulatory compliance requirements. Both pharmacy isolators and RABS are categorized as Primary Engineering Control (PEC) while cleanrooms can be categorized as Secondary Engineering Control (SEC) where the PEC is housed.
• Pharmacy isolators are designed to provide a controlled environment for aseptic processing and compounding of sterile drugs. They are fully enclosed systems that prevent contamination from external sources. Pharmacy isolators need to be pressure tested according to ISO 14644-7 and ISO 10648-2 with a stringent leak rate. Thanks to this design principle, pharmacy isolators can be equipped with a quantifiable and automated decontamination system, as well as good reliability for toxic containment.
• Barrier isolators, or RABS, also provide a controlled environment and an enclosure with the separative partial barrier, however, as per CETA CAG-002-2006, there is no requirement for the RABS to be pressure tested. RABS will be highly dependent on operator aseptic techniques to reduce the contamination risk and has low capability in toxic containment.
• Cleanrooms are also designed to provide a controlled environment via an open system and will refer to regulatory standards like ISO 14644.
In summary, while pharmacy isolators, cleanrooms, and barrier isolators all aim to ensure safe and effective compounding processes, they differ significantly in functionality and regulatory compliance requirements.
Q. How would a facility determine the appropriate cleanroom classification needed for their specific pharmacy operations?
First, the pharmacy facility will need to define the compounding activities and risk levels. Will it be for non-sterile compounding or sterile compounding? If it is sterile compounding, will it be a sterile hazardous (HD) or non-hazardous (non-HD) compounding? Will the pharmacy operations produce Compounded Sterile Preparations (CSP) Category 1 or Category 2?
The U.S. Pharmacopeia (USP) standards, especially USP <797> and USP <800>, outline cleanroom requirements for sterile compounding (797) and hazardous drug handling (800). Critical areas where sterile compounding occurs, whether it is hazardous or non-hazardous drugs, should maintain an ISO Class 5 classification. This air cleanliness can be achieved with the use of Primary Engineering Control (PEC), which can be either a pharmacy isolator or RABS.
Depending on the product categories based on the risk of microbial contamination and whether the CSPs are HD or
non-HD, the pharmacy facility can consider the following:
• For non-HD CSPs with a beyond-use date of less than 12 hours stored in temperature or less than 24 hours refrigerated, PECs (laminar flow hoods, biosafety cabinet class II, and compounding aseptic isolator/RABS) can be located in an unclassified room or segregated compounding area with no air changes per hour requirement.
• For non-HD CSPs with a beyond-use date of less than 24 hours stored in temperature or more than 24 hours refrigerated, PECs (laminar flow hoods, biosafety cabinet class II, and compounding aseptic isolator/RABS) must be located in a positively pressured ISO Class 7 cleanroom as buffer room with ISO Class 8 cleanroom as ante-room. The ISO Class 7 cleanroom must achieve more than 30 air changes per hour. In special cases with the use of a pharmacy isolator, this PEC can be housed in an ISO Class 8 cleanroom as a buffer room with fewer air changes per hour requirement of 20.
• For HD CSPs with a beyond-use date of less than 12 hours stored in temperature or less than 24 hours refrigerated, PECs (biosafety cabinet class II, and compounding aseptic isolator/RABS) can be located in an externally vented, negatively pressured unclassified room or segregated compounding area with minimum 12 air changes per hour.
• For HD CSPs with a beyond-use date of less than 24 hours stored in temperature or more than 24 hours refrigerated, PECs (biosafety cabinet class II, and compounding aseptic isolator/RABS) must be located in an externally vented, negatively pressured ISO Class 7 cleanroom as buffer room and ISO Class 7 ante-room with minimum 30 air changes per hour.
Due to better sealing, in non-hazardous CSP settings, pharmacy isolators can produce preparations with longer beyond-use dates even when they are placed in less strict cleanrooms.
Q. Can you provide insights into the best practices for maintaining and validating cleanroom environments, including the role of cleaning supplies like wipes and mops? Maintaining and validating cleanroom environments requires rigorous, routine cleaning protocols and specialized supplies to control contamination effectively.
• Daily and shift-based cleaning using lint-free wipes, disposable, non-shedding mops, and pre-saturated disinfectant wipes help ensure consistent disinfection, with rotation between different disinfectants to prevent microbial resistance. A thorough cleaning should consider high-touch surfaces such as work benches, PECs, and door handles. The frequency of this high-risk equipment should be cleaned at least once per shift or daily.
• Environmental monitoring, including particle counting and microbial sampling, verifies air and surface cleanliness against ISO standards.
• Top-to-Bottom, Back-to-Front Technique Implementation where the cleaning starts from the cleanest areas (top) to the least clean (bottom), from the back to front to prevent re-contamination of already-cleaned surfaces.
• Proper entry and exit protocols, including gowning and equipment sterilization, reinforce contamination control.
• The validation of HVAC and HEPA systems, air changes per hour validation, and cleanroom pressure maintenance are critical to meeting cleanroom requirements.
• Clear SOPs and comprehensive documentation of cleaning activities, coupled with regular personnel training and certification, uphold regulatory compliance and ensure the reliability of cleanroom operations.
Q. What are the essential requirements for USP-compliant supplies, and how a facility ensure the facility meets these standards?
Essential requirements for USP-compliant supplies are sterile, nonshedding, and chemically compatible supplies, like lint-free wipes and sterile alcohol, to maintain a classified environment. Facilities should select USP-compliant materials that support the ISO classification of the cleanroom and implement a robust environmental monitoring program to regularly test air, surfaces, and particle levels to meet USP <797> or <800> standards. The facility ensures compliance by establishing comprehensive SOPs for cleaning frequency, procedures, and agent selection, as well as providing staff training in aseptic techniques and gowning.
Q. How does the integration of advanced filtration systems impact the overall performance and safety of pharmacy isolators and cleanrooms?
The integration of advanced filtration systems significantly enhances the performance and safety of pharmacy isolators and cleanrooms by improving air quality and reducing contamination risks. High-efficiency particulate air (HEPA) and ultra-low particulate air (ULPA) filters capture up to 99.9995% of particles at 0.3 microns, including bacteria and other contaminants. The use of an advanced filtration system ensures the cleanroom environment meets stringent ISO classifications and USP standards for sterile compounding.
Advanced filtration also allows for more effective removal of hazardous materials, including cytotoxic particles, which is critical in handling hazardous drugs in compliance with USP <800> guidelines. The use of this filtration system in a pharmacy isolator’s exhaust system will also impact both operator and environmental safety. By maintaining stable airflow patterns and filtration efficiency, these systems help ensure aseptic conditions, reduce the risk of product contamination, and protect both staff and patients from exposure to harmful substances. Regular monitoring, validation, and maintenance of these filters are essential to uphold safety and operational standards, ultimately enhancing the reliability and safety of pharmacy operations.
Q. What training or certifications are recommended for pharmacy staff to effectively use and maintain clean air technology systems?
Pharmacy staff should receive specialized training and certifications to effectively use and maintain clean air technology systems. Recommended areas include aseptic technique training, USP <797>, and <800>
compliance for handling sterile and hazardous drugs. Together, these credentials ensure staff can uphold high standards of cleanliness, safety, and regulatory compliance in pharmacy operations.
Q. What are the cost implications and potential return on investment (ROI) when upgrading to the latest cleanroom technology and fixtures?
Upgrading to the latest cleanroom technology and fixtures involves significant initial costs, including the purchase of advanced equipment, installation, and ongoing maintenance. Training staff on new systems also adds to the investment. However, the potential return on investment (ROI) can be substantial. In general, an ISO Class 8 cleanroom with a pressure-tested pharmacy isolator is typically more cost-effective than an ISO Class 7 cleanroom with RABS.
For example, given the case of establishing a new facility for non-HD CSPs. The values are estimated and as a rule of thumb. The estimated required buffer room for a single workstation is 120 square feet.
Disclaimer: The pricing estimates provided above are for general guidance only and may vary significantly based on geographic location, specific facility requirements, material choices, and vendor pricing. These figures assume typical costs for cleanroom construction, equipment, maintenance, and compliance but do not account for potential additional expenses, such as custom engineering, utility upgrades, or unique facility needs.
Improved compliance with regulations enhances patient safety and reduces the risk of costly penalties, while modern systems increase operational efficiency and throughput. Upgraded filtration and containment technologies can minimize product waste, leading to higher yields and lower disposal costs. Additionally, energy-efficient equipment can result in long-term savings on utility and maintenance expenses.
Ultimately, while the upfront costs may be high, the long-term benefits such as enhanced competitiveness, improved reliability, and increased profitability make a compelling case for investing in cleanroom and PEC upgrades.
Acute Care Pharmaceuticals (888) 909-7700 pharma-choice.com
AirClean Systems | Mystaire (919) 255-3220 aircleansystems.com mystaire.com
Allied Pharmacy Products (Steri-Tamp) (516) 374-8862 steri-tamp.com
American Analytics (818) 998-5547 americananalytics.com
Azzur Labs, LLC (484) 550-7709 azzur.com/services/ laboratory-services
Berkshire (800) 242-7000 berkshire.com
Blue Thunder Technologies Inc. (860) 321-8323 bluethundertechnologies.com
Carter Health (407) 296-6689 carter-health.com
ChemoGLO, LLC (877) 215-2705 chemoglo.com
CINTAS (888) 834-2883 cintas.com/uniform-workapparel/uniform-rental/ cleanroom.aspx
Cleanetics (412) 405-8692 cleanetics.com
Cleanroom Connection (800) 616-5319 cleanroomsupplies.com
Containment Technologies Group, Inc. (317) 713-8200 mic4.com
Contec, Inc. (864) 503-8333 contechealthcare.com
Dycem Corporation (401) 738-4420 dycemusa.com
Ecolab (866) 781-8787 ecolab.com/solutions/cleaningequipment-for-cleanrooms
Esco (215) 441-9661 escolifesciences.com
FG Clean Wipes (413) 598-8344 fgcleanwipes.com
Germfree (386) 265-4300 germfree.com
Grifols (800) 379-0957 grifolsinclusiv.com/en/home
Health Care Logistics (800) 848-1633 gohcl.com
Infinity Laboratories (303) 730-7330 infinitylaboratories.com
Integrated Medical System, Inc. (800) 755-3800 integratedmedsys.com
International Medical Industries (800) 344-2554 imiweb.com
ISO-MED, Inc. (800) 797-1405 iso-med.com
IsoTech Design (800) 476-2010 isotechdesign.com
Labconco (800) 821-5525 labconco.com/pharmacy
Lakeland (256) 350-3873 cleanroom.lakeland.com
MedSafety Solutions (720) 500-2500 medsafetysolutions.com
MedXL Inc. (514) 695-7474 medxl.com
Modular Cleanrooms, Inc. (800) 496-7666 modularcleanrooms.com
Modular Devices (317) 333-8742 modulardevices.com/cleanrooms
NuAire (763) 553-1270 nuaire.com
Owen Mumford (800) 421-6936 owenmumford.com/us
Parasol Medical (847) 520-3000 parasolmed.com
PCCA (800) 331-2498 pccarx.com
Perfex Corporation (800) 848-8483 perfexonline.com
ProPharma Cleanrooms (469) 283-1190 propharmacleanrooms.com
Prudential Cleanroom Services (800) 767-5536 prudentialuniforms.com/ services/cleanroom
Pure Microbiology (610) 417-4795 puremicrobiology.com
Q.I. Medical Inc (530) 272-8700 qimedical.com
QleanAir Scandinavia (614) 954-1040 qleanair.com/us/ products/cleanrooms
Stratix Labs (612) 416-4388 stratixlabs.com
Teknipure (844) 309-2376 teknipure.com
Texwipe (800) 839-9473 texwipe.com
The Baker Company (800) 992-2537 bakerco.com
Total-Shield PLUS HG (877) 910-4208 totalshieldhg.com
Travis CleanAir (970) 203-0516 traviscleanair.com
TRC Healthcare trchealthcare.com
Veltek Associates, Inc. (610) 644-8335 sterile.com
Vileda (630) 270-1437 ce.vileda-professional.com
Clean technology, supplies, and services are critical components for hospital pharmacy professionals to ensure compliance with sterile compounding standards and safeguard patient safety. These environments, designed with controlled air filtration, temperature, and humidity, are essential for the preparation of medications like IV infusions, chemotherapeutic agents, and other compounded sterile products. Pharmacy directors rely on cleanroom supplies, such as sterile gowns, gloves, masks, and HEPA filters, to maintain the highest standards of cleanliness and reduce contamination risks.
In addition to physical supplies, cleanroom services, such as regular cleaning, certification, and environmental monitoring, are crucial to meeting USP <797> and <800> guidelines. By investing in cleanroom technology and ensuring proper maintenance, hospital pharmacies can achieve operational efficiency, regulatory compliance, and, most importantly, protect patients from preventable infections and contamination.
Whether planning a cleanroom renovation or building a new cleanroom, Modular Devices provides solutions for your short- and long-term cleanroom needs. Our modular prefabricated units deliver standalone, turnkey cleanrooms that only require utility connections upon delivery. Our customizable rigid wall systems can transform your current space or outfit your new build into the safe and efficient workspace you need to support your pharmacy operations. Experience unmatched quality, state-ofthe-art materials, and equipment, with cleanrooms that will exceed your expectations, and USP 797/800!
Lease and Purchase Options Meets and Exceeds USP797 & 800
Large Fleet and Nationwide Coverage Standalone Units Include:
> Hands-free Scrub Sinks
> Hands-free Interlocked Doors
> Continuous Data Logging & Monitoring
> Includes 4' BSC's and 4 LFH's
> Includes Dedicated Refrigerators
> HEPA Filtered Interlocked Passthroughs
> Dedicated Haz & Non-Haz Gowning Rooms
> USP 800 Neg. Pressure Unpack/ Storage Room
> Hands-free Flush Mount Intercoms
> Guaranteed Environmental Control
> Guaranteed Certification
Improve confidence in the quality of tablet repackaging and unit dose batching from start to finish.
President & CEO: Gary Sharpe
Founded: 1978
Employees: 300+
Toll-Free Phone: (800) 848-1633
Phone: (740) 477-3755
Address: P.O. Box 25
Circleville, OH 43113
Website: GoHCL.com
What began in 1978 as a garage-based business at the home of HCL® Owner Gary Sharpe now encompasses five well-equipped facilities in central Ohio and reaches customers around the globe. Employment has grown too, with more than 300 employees now dedicated to the company’s mission of providing unmatched customer service. Sharpe discovered early in his career the need for healthcare products in sizes, quantities, and materials not readily available and was determined to deliver. And has he ever. Today, inventory includes more than 9,000 different products all designed to provide “Special Answers to Special Problems.” Most of these items are maintained locally in more than 320,000 square feet of warehouse space and meet the supply needs of hospitals, pharmacies, chain drug stores, pharmaceuticals, and many other facets of healthcare.
Tablet repackaging and unit dose batching can be complicated and costly. Often, the number of blisters per sheet and labels per sheet don’t match. Or if they do, the labels adhere crooked. Not only do you have to start over, but you must also toss the supplies you already used.
In response to these frustrations, we created the EZ Grid® system to ensure you consistently achieve precise label-to-blister alignment. Sheets for blisters and labels are designed in 5x5 grids so there are no unused pieces and no waste to discard.
Designed around a sturdy aluminum frame with two locator pins, EZ Grid allows you to choose your inserts (pick from round, slot, or square; all are interchangeable), then choose the matching blister and label combination that meets your Class A or Class B package requirements. Blister and label combinations meet USP <671> so you can be confident in the quality of your unit dose package from start to finish.
Further enhance this routine by printing your labels from a desktop printer using our free online service, goHCLabels® Seamlessly integrate these printed labels with packages prepared using your choice of EZ Grid components. Because goHCLabels is web-based, there is no software to install and no valuable information to risk losing with a computer crash. Ready-made templates save time and improve efficiency.
Recognizing the importance of data security and access control, goHCLabels allows pharmacies to define distinct roles and permissions for staff, which ensures only authorized personnel can access or modify critical label information. This feature enhances accountability and minimizes the risk of unauthorized changes, which gives pharmacies greater control.
Our commitment to excellence led us to develop these solutions, which mark a significant milestone for unit dose management. Experience the power of these services together to elevate your everyday pharmacy performance.
Our additional lines include unit dose; storage; IV accessories and injectables; compounding and dispensing; seals; plastic bags; refrigerators, freezers and accessories; temperature monitoring; infection prevention; carts and accessories; pharmacy supplies; crushers, cutters, and organizers; and error prevention.
We offer small package quantities, no order minimums, free samples, and ship most orders on the same day. Our hassle-free return policy allows you to return any product at any time for any reason. Connect with our live chat team from 8 a.m. to 8 p.m. EST Monday through Friday.
CEO: Steve Rough
Founded: 1999
Toll-Free Phone: (866) 388-7583
Our mission is to transform healthcare through pharmacy. We help hospitals and health systems optimize pharmacy operations, improve financial performance, and deliver better patient care.
Address: 101 East 5th Street, #2220 St. Paul, MN 55101
Website: www.visanteinc.com
Visante’s innovative healthcare solutions help health systems improve patient care, operational performance, and financial results. Our approach fully integrates infusion and specialty pharmacy solutions to put the patient first. We maximize client value through deep expertise in highly specialized services including 340B optimization and compliance, medication access services, pharmacy revenue cycle, and pharmacy supply chain optimization.
Visante’s healthcare solution integrates specialty pharmacy and infusion services to offer extraordinary value for our clients. We bring a transformative solution to health systems by delivering an unmatched patient and provider experience and accelerate the system’s ability to achieve its goals and fully leverage its opportunity.
Our innovative, comprehensive approach to specialty pharmacy and infusion services unlocks the value of an integrated program: timely medication access; reduced administrative burden; operational efficiency; improved financial performance; and enhanced clinical outcomes. Visante helps improve the lives of patients while supporting the financial objectives of the health system.
n Specialty Pharmacy
A clearly defined specialty pharmacy strategy helps improve patient care and the bottom line. Developing a specialty pharmacy strategy or expanding your existing services can be a complex process, but our team guides you through each phase and delivers lasting ROI. Our specialty pharmacy solution provides operational assessment and pro forma models; multi-year business and strategic plans; facility design including workflow and automation options; implementation and project management; accreditation support; contract pharmacy strategy; wraparound strategies to include consideration for site of care challenges (infusion); and home infusion and business planning.
n Infusion
A comprehensive home infusion services strategy can help lower total cost of care, maximize patient outcomes and access to quality care, reduce the administrative burden for patients and providers, and optimize organizational financial performance. Visante’s infusion solution provides business planning, design, and implementation of comprehensive infusion
care strategies using our deep and specialized expertise in all aspects of infusion, including home infusion therapy, specialty pharmacy, 340B program management, supply chain strategies, and innovative solutions to drug delivery and therapy administration.
n
Visante’s independent, external audit support provides transparency to your 340B processes, allowing you to recognize compliance gaps while focusing on new opportunities within the program. Our 340B team offers unique expertise in supporting 340B ESP™ data submission and price restoration analysis. Our services include: internal and external audit support, on-site HRSA audit support, and corrective action plan guidance in the event of HRSA audit findings; gap analysis and targeted recommendations, focusing on long-term strategy in the mixed-use and contract pharmacy space to ensure program optimization; program implementation and development of internal oversight structure and maintenance; and split billing RFP guidance, implementation, and program re-designs.
Sustained financial growth is one of the top challenges for even the most successful organizations in the healthcare industry. Effective pharmacy programs can increase revenue by maximizing existing opportunities, creating new programs and services, and reducing costs. Our team of experts are here to help maximize financial performance within your organization through our mastery of both pharmacy and revenue cycle operations. Our consultants bring a wide range of experience to the table to assist each of our clients in a way that best fits them and their financial goals.
Visante’s centralized medication access services help hospitals and health systems overcome operational, financial, and administrative barriers. Our team manages the intricacies of medication insurance authorizations, coordinates financial assistance, and supports streamlined access to treatment. Our team provides support through all sites of care, helping patients navigate the journey of accessing and affording their medications. This approach alleviates the administrative burden from the care team, improving provider and patient satisfaction.
n
Supply chain and utilization management are complex, evolving aspects of a pharmacy enterprise. To find success in these areas, disciplined focus and alignment must be prioritized. Visante’s supply chain experts help hospitals and health systems achieve reliable, safe and efficient drug supply chain performance while also realizing significant financial returns.
Dr. Kamile Johnson, PHARMD Vice President of Pharmacy Services
~ DBA KCCARE Health Center
For nearly 50 years, the DBA KCCARE Health Center has served as a healthcare lifeline for Kansas City’s most vulnerable populations. As a private, nonprofit, and Federally Qualified Health Center (FQHC) organization, it offers a comprehensive range of services, including primary care, HIV care, dental services, behavioral health support, and an in-house pharmacy. The Health Center serves over 21,797 patients across four locations and two mobile units, addressing the needs of underserved and uninsured communities.
An important development in DBA KCCARE’s service offerings came in 2015 when the Health Center recognized the need to integrate pharmacy services into its care model. They made the strategic decision to establish an in-house pharmacy to better serve its patient population. To bring this vision to life, the Health Center brought on Vice President of Pharmacy Services Kamile Johnson, PharmD.
“When the Health Center approached me, they understood that having a Pharmacy Services Program was essential to the continuity of care for our patients,” said Dr. Johnson. “Many of our patients can’t easily access or afford prescriptions from outside pharmacies. By offering medications in-house we could make a real difference ”
The timing was ideal, as DBA KCCARE had recently earned FQHC status, qualifying them for the 340B Drug Pricing Program, which helps reduce medication costs for eligible patients. With this program in place, Dr Johnson detailed the requirements for launching the outpatient pharmacy. By March 2016, the Health Center received its pharmacy license, and in September, the pharmacy officially opened its doors.
“100%. Absolutely. I would do it again, and I would do it with ScriptPro.”
Dr. Kamile Johnson, PHARMD Vice President of Pharmacy Services
~ DBA KCCARE Health Center
“The 340B program has been a game changer for us,” said Dr. Johnson. “The savings we generate go directly back into the Health Center, which has allowed us to hire additional staff and offer expanded pharmacy services, such as vaccines. We’re also exploring options for delivery services and adding more specialty care.”
With pharmacy services integrated into the Health Center’s broader care model, prescription adherence improved. “Having our pharmacy in-house gives us access to our patients’ health records, enabling us to closely track outcomes and ensure compliance with treatment plans,” said Dr. Johnson. “As a FQHC organization, and a patient-centered medical home, we already track key health metrics like hypertension and diabetes. I’m eager to see how the addition of our Pharmacy Services Plan will positively impact our patients’ heath over time.”
The DBA KCCARE Health Center’s patient base is diverse, including the uninsured to the under-insured, such as small business owners and hourly wage earners, as well as those fully insured through private companies. The pharmacy also assists with patient copays via a Medication Assistance Fund, supported by donations from local community members and companies.
By 2022, the demand for DBA KCCARE’s pharmacy services outpaced the physical space available. Longer wait times and cramped conditions prompted Dr. Johnson and her team to explore expansion opportunities. A larger space adjacent to the current pharmacy became available, but the complexity of managing multiple vendors created challenges.
That’s when DBA KCCARE turned to ScriptPro, a trusted partner in pharmacy automation, to manage the expansion. “Juggling multiple vendors is a daunting task,” Dr. Johnson explains. “ScriptPro made everything easier by coordinating the process from start to finish.”
The redesign project was a collaborative effort and a true partnership. ScriptPro worked closely with DBA KCCARE to create an optimized layout that improved both efficiency and patient experience. Within 24 hours, ScriptPro delivered a design plan featuring new cabinetry, shelving, conveyors, and a space that maximized the use of the Health Center’s existing automation systems.
The pharmacy is now equipped with ScriptPro’s SP 200 Robot, ScriptPro Pharmacy Management System, and 340B Management Package with TPMS, ScriptPro’s thirdparty reconciliation solution. These tools have streamlined operations, ensuring accurate dispensing and management of medications.
Learn more about how ScriptPro transformed
DBA KCCARE’s pharmacy operations and patient care.
In April 2023, DBA KCCARE proudly opened the doors to its newly redesigned pharmacy, and the patient response was overwhelmingly positive. “They love the new space — it’s bright, welcoming, and equipped with the latest technology,” said Dr. Johnson. “It’s a place that makes them feel valued.”
DBA KCCARE’s partnership with ScriptPro has been integral to its ongoing mission of providing quality care and promoting wellness in the community.
“Partnering with ScriptPro was a no-brainer,” said Dr. Johnson. “Their solutions allow my pharmacists to focus on clinical work, while my technicians can devote more time to patient care. Plus, with their comprehensive offerings, we have everything we need to grow, all in one place.”
The DBA KCCARE Health Center (formerly the Kansas City Free Health Clinic) is one of the oldest and largest charitable care clinics in the nation. Founded in 1971, the Health Center provides care, access, research, and education for the underserved and all people in the Kansas City community. The DBA KCCARE Health Center’s clinical services include adult general primary care, HIV primary care, pediatric care, oral healthcare, and behavioral health services which are enhanced by supportive services such as case management, care coordination, and community screenings and health education.
ScriptPro is the worldwide leader in pharmacy automation. We offer a comprehensive line of over 200 pharmacy automation and management system products that have revolutionized pharmacy operations in the United States and around the world. ScriptPro systems operate in thousands of independent chain, hospital, supermarket, and government pharmacies. From independent retail pharmacies to large health systems, ScriptPro technology and expertise enable pharmacies to participate in the healthcare system at the highest levels.
Vice President of Pharmacy Services Dr. Kamile Johnson, at DBA KCCARE Health Center, has 17 years of experience as a community pharmacist. She earned her PharmD from the University of Pittsburgh and helped establish DBA KCCARE’s in-service pharmacy, improving patient access and healthcare services.
Left: GM7030 PATT2®, Personal Aseptic Technique test kit, 3mL ampules, 20mL vials, 100mL partially lled minibag. Below: ET1000 EnviroTest® TSA with Lecithin & Tween 80 growth media paddles for surface, air, or glove ngertip sampling.
President & CEO: Brady K. Schwarz
Founded: 1992
Toll-Free Phone: (800) 837-8361
Phone: (530) 272-8700
Fax: (530) 272-8702
Providing quality assurance products to hospitals and pharmacies practicing sterile compounding, with a singular focus on pharmacy compliance. Our long-standing regional distribution partners are able to provide exceptional in-person service and training.
Address: 1415 Whispering Pines Lane, Suite 150 Grass Valley, CA 95945
Website: www.qimedical.com
Q.I. Medical, Inc. was founded in 1992 with a focus on providing the sterile compounding industry with testing kits and products to assure proper technique and quality is maintained in their facility. We have a broad network of distribution partners throughout North America, Canada, and other international markets. These distribution partners provide in-person servicing and education to accounts to comply with USP guidelines.
Our cost-effective, disposable products are available for various needs in the compounding pharmacy. Aseptic technique validation kits are available for low, medium, and high-risk settings. We also sell multiple à la carte sizes of vials, bags, tubes, and syringes of growth media for facilities looking to create a custom media fill test that mimics their day-to-day practice. In regard to environmental monitoring/gloved fingertip sampling, our EnviroTest™ paddle is ideal for both. The rectangle shape and built-in hinge allow for testing critical areas such as the edges and corners of a hood and behind latch handles. Sterility testing products are available in both USP <71> approved methods of testing. For the full filtration method, the QT Micro™ and QT Junior™ systems work for both small and large volume solutions. For the direct inoculation methods, our TuffTest 2™ product is ideal.
All Q.I. Medical growth media is challenged with a battery of USP specified organisms and lot specific Certificate of Analysis (CofA) are available for download.
All products are sold through regional stocking distributors in order to provide fast local service and support.
Additional products are available for validation of hazardous drug handling, automated compounder manipulation validation, filter integrity testing, and vial adaptors.
n Support Equipment Includes:
• Incubators
• Sterile Filters
• Vial Blocks
• UV Lights
To learn more about how Q.I. Medical, Inc. can help your facility, please contact us at (800) 837-8361 or email info@qimedical.com.
Amoxicillin / Clavulanate Potassium is ready to help fight against bacterial infections
American Health Packaging (AHP) provides important medications in the doses you need to help change patients’ lives for the better. Get Amoxicillin / Clavulanate Potassium today in the following dosage levels only from AHP.
*Augmentin is a licensed trademark of GlaxoSmithKline LLC.
Click here to explore our 600+ products and learn how to order this item from your preferred wholesaler today.
With a responsive line of barcoded unit-dose oral solutions, a growing liquid unit-dose offering, as well as individually wrapped inhalants, AHP continues to deliver on it’s commitment to supporting pharmacy efficiency.
Senior VP &
General Manager: Sasha Kellerman
Toll-Free Phone: (800) 707-4621
Address: Columbus, OH 43217
Website: www.americanhealthpackaging.com
Located in Columbus, Ohio, American Health Packaging (AHP) is an industry leader in manufacturing serialized, barcoded unit-dose (UD) medications provided for the healthcare marketplace. As a UD manufacturer, AHP’s commercially-available UD products are available to hospital, institutional, and long-term care pharmacies nationwide through partner GPOs and wholesalers.
AHP’s reputation for quality is supported by a 30+ year history of broad manufacturing expertise — operating a facility that is registered with the FDA, fully adherent to cGMP guidelines, and licensed by the DEA to package Schedule II-V controlled substances. Synonymous with unit dose, following years of success and leadership in the production of oral solids, AHP expanded their offering and now includes liquid unit-dose cups, inhalants, and powder/granule oral suspension.
AHP is committed to supporting pharmacy efficiency through a diverse range of both high-utilization and niche treatments. Producing over 600 UD oral solid SKUs for the healthcare marketplace, AHP’s broad selection of products are produced with quality components and printed with legible barcodes that facilitate effective execution of BCMA initiatives. Their wide selection of products reduces the gap between what pharmacies are forced to repackage themselves, and what is commercially available on the market — supporting health systems nationwide in their efforts to create efficiencies throughout the chain of care.
AHP’s tailored offering of UD oral liquids provide similar efficiency, safety, and cost-savings benefits as their oral-solids products. Product features include right-sized packaging, thoughtful tray design, differentiated labelling, and accurate barcodes. AHP’s unit-dose inhalants provide efficiency and feature individually-wrapped vials and pouches barcoded to the dose level. AHP oral solids, liquids, and inhalants include major therapeutic classes and product groups to meet unique pharmacy needs. They are continuously evolving to meet the changing demands of caregivers and staff to support more effective medication procurement strategies.
As facilities nationwide compete to demonstrate they provide the highest quality of care, AHP UD supports caregivers as they strive to promote positive outcomes for patients. Pharmacies simultaneously strive to be cost-effective as they provide necessary resources for caregivers.
AHP UD supports these objectives while providing cost-savings opportunities. Sourcing pre-packaged UD allows pharmacies to obtain adequate supply while mitigating capital expenses, such as those related to repackaging equipment, bulk supply, and labor.
n Patient Safety: Ensuring the right medication is given to the right patient at the right time — and in the right strength — is imperative. Pharmacies can facilitate effective execution of these “rights” by providing caregivers with as many products in a pre-packaged UD format as possible. Removing repackaging tasks from the pharmacy eliminates a potential point of failure during the UD process as medications arrive to pharmacies ready to dispense.
n Pharmacy Efficiency: Pharmacies strive to process orders and supply the proper medications to caregivers for their patients as quickly as possible. Adding potentially-complex repackaging steps to the procurement process not only harms the ability of pharmacy to supply caregivers effectively, but also removes clinicians from their core patient care competencies. In addition, pre-packaged UD often allows for products to be sourced more quickly than third-party repackaging can support.
n Cost-Savings Opportunity: Health systems that choose to package onsite must consider all direct costs, such as purchasing capital equipment for packaging areas and paying highly trained clinical professionals to perform, manage, and support non-core work. AHP UD products allow for pharmacies to avoid these costs while also shifting the potential costs associated with packaging errors. The pre-packaged format also prevents additional fees that may result from utilizing third-party repackaging services.
n Liability Management: Pharmacy repackaging operations can be subject to distractions from a variety of sources. An active pharmacy environment can encourage lapses in concentration and present opportunities for staff error. Since these errors may vary in gravity and place liability on the facility and caregivers, mitigation of risk is key. Unit dose from American Health Packaging can help shift liability burden away from staff.
Effective execution of BCMA initiatives require medications that scan correctly at the bedside. With a robust, growing, unit-dose portfolio AHP provides reliable access to UD treatments. AHP products promote safety towards BCMA and efficiency in pharmacy while freeing up internal resources. AHP UD supports pharmacies as they strive for compliance with USP General Chapter <800> guidelines. As pharmacies craft effective procurement strategies to meet the needs of their facilities, protecting patients and caregivers alike from potential harm while handling hazardous drugs is a priority. AHP’s UD portfolio has a number of NIOSH/USP <800> products already packaged for bedside dispensing which supports compliance to USP <800> handling procedures.
A US-based company with strong roots in generic pharmaceuticals, Amneal is growing its injectables portfolio to include ready-to-use bags, pre-filled syringes, and other presentations to streamline your workflow so you can concentrate on the most important priority: your patients’ health.
We’re committed to building our line of ready-to-administer products, ensuring quality, convenience and availability for years to come. This is how we make healthy possible.
Scan the code to see Amneal’s extensive catalog including our growing line of ready-to-use injectables.
• Cold Seal
• Tamper-Evident
• Moisture Resistant
• Ultraviolet Inhibitant
Dose, Bar PharmacyCoding, & NursingExperts!Supply Unit Dose, Bar PharmacyCoding, & NursingExperts!Supply
• Reduces Cross Contamination
• Ideal for Meds Covered by USP 800
• 6 and 12-month Beyond-Use Dating
• 1-D and 2-D Bar Coding
• Flexible Label and Report Formatting
• Multiple Sizes and Shapes to Fit Your Meds & Storage Needs
President: Robert Braverman
Founded: 1971
Employees: Private
Toll-Free Phone: (800) 523-8966
Phone: (215) 396-8600
Toll-Free Fax: (800) 323-8966
Address: 70 Industrial Drive Ivyland, PA 18974
Website: www.medidose.com
Company Background
Improve your Solid Oral Unit Dose needs with our comprehensive Bar Coding, Packaging, and Labeling Solutions — designed by healthcare professionals, for healthcare professionals.
Features & Options
n Packaging and Labeling Solutions
• Simple to use — no extensive training needed.
• 1-D and 2-D bar coding — including NDC, lot numbers, and expiration dating.
• Ideal for hazardous medications and USP 800 drugs.
• Tall Man Lettering and dynamic formatting options.
• Built-in NDC lookup database and extensive image library.
• Packaging logs and error reporting.
• Six-month and one-year beyond-use dating.
• UV and moisture resistance.
Medi-Dose/EPS was founded in 1971 when Milton Braverman, a former pharmaceutical company territory manager, saw the need for inexpensive, manual unit dose packaging allowing a hospital to convert from traditional dispensing. He developed the Medi-Dose System to package, handle, and dispense predetermined amounts of medication so they would be accessible for one regular dose. Comprehensive bar coding and labeling identification is accomplished using our innovative MILT 4 software. Because of the continued success of the MediDose System, Medi-Dose/EPS expanded its product line to include the TampAlerT System, offering tamper-evident liquid packaging without the need for heat tunnels and accessory sealing equipment, as well as a full line of supplies and disposable products designed specifically for the pharmacy and health care professional.
Product Overview
Medi-Dose provides Tamper-Evidence as well as UV and Moisture Resistance for one-year beyond-use dating. Our MILT® 4 software maintains packaging logs and lets you design and print your Lid-Label® Covers with color, bar codes, tall man lettering, and graphics. You can format the labels any way you want, directly from your own computer and printer!
Medi-Dose works well in any pharmacy operation and can be used with all classifications of drugs (meds covered by USP 800, chemo meds, compounded drugs, controlled substances, etc.). It’s affordably priced for all pharmacy budgets. For the best in manual unit dose packaging, check out Medi-Dose!
• Tamper-Evidence
• 15 styles of blisters to accommodate virtually all meds.
• MPB® — Multi-purpose blisters to easily package large medications, compounded drugs, double and triple “0” capsules, unit-of-use packaging, repackaged medications, and suppositories.
• New Ointment Lid-Label Covers to package ointments in all Medi-Cup Blisters.
• No machinery or space requirements.
• Inexpensive — no capital outlay required.
Product Specifications
n Accompanying Labeling Software
• MILT 4
• MILT 3.0
• MILT 2.6
• Medi-Dose 2000
Trade Shows/Meetings Attended
ASHP Midyear, ASHP Summer, HCP Pharmacy & Pharmacy Purchasing Meeting, Joint Forces Pharmacy Seminar, National Pharmacy Purchasing Association, EAHP, IACP, and various state, regional, and pharmacy compounding conferences.
Ordering Information
For additional information, please contact us at (800) 523-8966, visit our website at www.medidose.com, or email us at info@medidose.com.
Improving Patient Care: Union Health Implements Systemwide Specialty Pharmacy Services
AUTHOR: CPS
SUBJECT: Specialty Pharmacy
SUMMARY: Union Health, an integrated health system serving western Indiana and eastern Illinois, partnered with CPS Solutions to create an onsite specialty pharmacy, streamlining access to complex therapies and financial assistance for patients while reducing administrative burdens for providers.
Into the Future with Baxter’s DoseEdge Pharmacy Workflow Manager System
AUTHOR: Baxter
SUBJECT: IV Sterile Compounding
SUMMARY: The introduction of IV Workflow Management systems (IVWFM) has improved pharmacists’ ability to ensure accurate, timely sterile compounding, while staying compliant with increasingly strict regulations and reducing errors.
Christus Health Expands Use of Innovative RFID Pharmacy Tech
AUTHOR: Cencora
SUBJECT: RFID Inventory Management Solution
SUMMARY: Christus Health partners with Cencora (AmerisourceBergen) to automate and standardize pharmacy inventory management across enterprise.
Prescription for Safety: Technology is Imperative to Detect and Prevent Drug Diversion
AUTHOR: Bluesight
SUBJECT: Drug Diversion
SUMMARY: Sentara collaborated with Bluesight to protect patients, staff, and the community using advanced medication intelligence software to detect and prevent drug diversion, across its 12 hospitals.
Taking Operational Excellence to the Next Level — One Business Area at a Time
AUTHOR: CPS
SUBJECT: Pharmacy Management
SUMMARY: Goshen Health, a non-profit community hospital, partnered with CPS to enhance pharmacy management, rehabilitation therapy, and supply chain operations, resulting in significant cost savings, improved patient outcomes, and increased efficiency across the organization.
The Role of Probiotics in Healthcare: Past, Present, and Future
AUTHOR: i-Health
SUBJECT: Culturelle® Probiotics
SUMMARY: Hear from three healthcare professionals as they discuss their experience and research toward the value of probiotics.
President & CEO: Nick Culbertson
Founded: 2014
Employees: 100
Phone: (410) 995-8811
Fax: (410) 995-8842
Utilize artificial intelligence and advanced analytics to audit 100% of medication use transactions — reducing the risk to your workforce, organization, and, most importantly, patients.
Address: 3030 Greenmount Avenue, Suite 300, #914524 Baltimore, MD 21218-6907
Website: www.protenus.com
Founded in 2014, Protenus is an innovative, technology-first company headquartered in Baltimore, MD. Our team of problem solvers, subject matter experts, and support stewards spans the entire country. Protenus was born of a determination to solve problems in healthcare that would provide better patient outcomes and increase patient trust in the healthcare organizations where they sought care.
Although hospitals in the U.S. spend $39 billion per year to maintain compliance, most of it goes towards time-consuming, inefficient manual tasks. We thought the money could be better allocated to improving patient outcomes, so through innovation we began to tackle common healthcare compliance challenges. First focusing on protecting patient privacy, we then broadened our scope to issues of healthcare workers stealing or misusing controlled substances. In the years since, we’ve empowered hundreds of healthcare organizations to reduce risk. We’ve also cultivated the largest collaborative user community of healthcare compliance peers and experts from Protenus, PANDAS, that continues to move healthcare forward. That same innovation, determination, and community are still the pillars of Protenus today and carry us forward in our belief that the delivery of care should be without risk.
It’s important to partner with a vendor who understands current industry drivers and challenges, is aligned with your organization’s compliance and risk strategies, and is focused on providing the guidance and solutions to help you achieve your goals. Our powerful healthcare compliance platform harnesses the power of artificial intelligence (AI) to identify and surface inappropriate behavior that may otherwise go unnoticed as it happens, reducing risk to your workforce, your organization, and, most importantly, the patients you serve.
When you choose Protenus as your partner, you are choosing a company that makes a commitment to innovation, determination, and community to better protect your organization, workforce, and patients. When working with Protenus, you will benefit from cutting-edge technology and a team that is dedicated to helping you navigate the complex landscape of healthcare compliance and risk management.
Who We Serve: Our sole focus is on healthcare organizations such as hospitals, health systems, AMCs, and large physician groups, supporting their risk elimination and compliance efforts as well as strategic initiatives like reducing costs, maintaining a stellar organizational reputation, and protecting their patients, workforce, and community at-large.
Our Vision: We believe that the delivery of care should be without risk. Our Mission: We empower healthcare organizations with AI-powered, scalable risk-reduction solutions built to deliver cohesive and actionable data when and where needed. Ultimately, protecting the delivery of care while challenging the industry to focus on what matters most by driving the safest, highest quality patient outcomes.
Drug Diversion Surveillance, developed by Protenus, identifies and helps prevent clinical drug diversion incidents that occur within healthcare organizations. Awarded 2023 and 2024 Best in KLAS for Drug Diversion Monitoring, the Protenus solution uses the power of artificial intelligence (AI) to monitor up to 100% of medication use transactions, it identifies unseen behavior as it happens, reducing risk to workforces, organizations, and, most importantly, patients.
n Protenus Drug Diversion Surveillance Offers
• Visibility Into Incident Generation: Platform is powered by data covering 100% of medication use transactions to give investigators complete visibility into potential drug diverters’ behavior patterns that may otherwise go unnoticed.
• Time Savings and Efficiencies: Each incident is surfaced along with clear and concise background information to allow investigators to resolve incidents quickly. Customers have reported a five to 15 minute incident evaluation time using the Protenus platform.
• Flexible, User-Friendly Analytics and Dashboards: Userfriendly dashboards reduce the need for manual analytics and report creation. Our File and Error Delivery dashboards empower IT end users to monitor and troubleshoot the robust set of data feeds that power the Protenus platform.
• Commitment to Continuous Innovation: Our product and engineering teams partner to receive feedback directly from our customers and deliver maximum value. Customers have forward-looking visibility into planned feature and functionality enhancements.
“Thanks to implementing Protenus in our procedural spaces, our drug diversion prevention at the health system has improved dramatically, providing us with unparalleled confidence in our monitoring and detection capabilities.”
— Christopher Hall, PharmD, MS, BCPS, ACE
The University of Kansas Health System
Key Business Partners/Supplier Contracts
Business Partner: Inmar Intelligence | Supplier Contract: Premier Inc.
Sales & Contracts
Manager: Fred Hauth
Founded: 2010
Toll-Free Phone: (800) 797-1405
Fax: (951) 547-1681
Address: 1220 Graphite Drive Corona, CA 92881
Website: www.iso-med.com
Company Background
As a leading provider of pharmacy cleanroom supplies, ISO-MED is dedicated to offering an unparalleled selection of specialized medical, compounding, and cleanroom supplies. We understand the importance of meeting the requirements of USP, accreditation organizations, State BoPs, and the FDA.
Since 2010, ISO-MED has been a medical supply distributor and trusted supplier, offering quality, selection, and convenience. We’re committed to providing top-quality products for cleanrooms (503A, 503B, and manufacturers), laboratories, home care, infusion centers, cancer centers, retail pharmacies, veterinaries, and other medical industries in the USA.
At ISO-MED, we are dedicated to helping you achieve and maintain sterile and non-sterile compounding environments. Our goal is to ensure the safety of your products, your workers, and your compliance with regulations.
Product Overview
ISO-MED maintains an extensive portfolio of on-the-shelf warehouse supplies.
We offer customized supply plans, a seamless e-commerce customer experience, easy ordering with matching manufacturers, and dependable purchasing/supplier aggregation services.
With one-on-one scheduled training services, we increase the efficacy of your purchasing processes, consolidate your portfolio, and link your onsite supply demand to your inventory management processes.
Offering value-added services, we provide consistent customer service and are driven to help our customers save money without compromising quality.
Features & Options
In addition to compounding, cleanroom, and laboratory supplies, ISO-MED offers the following testing to supplies.
Environmental Monitoring Contact Plates
Surface sampling plates evaluate facility and material handling procedures, work surface cleaning and disinfectant procedures, and personnel competency.
n ICR plus TSA LT
n TSA with Lecithin and Tween® (Polysorbate 80), USP
These Hardy Diagnostic contact plates are recommended for cultivating microorganisms from environmental surfaces and feature a Lok-Tight™ lid that securely fastens to the base.
n Category of products include:
• PPE: Various USP-compliant shoe covers, head covers, facial hair covers, face masks, gowns, coveralls, and gloves.
• Wipers
• Agents: Cleaning and Disinfectant Solutions
• Mopping Systems: Handles and Covers
• Sterile Compounding Supplies: Includes chemo mats, syringe and IV caps, IV port, and vial seals.
• Aseptic Testing Supplies
• Hazardous Drug (HD) Surface Sampling Kit
• HD Spill Kit
• Medication Disposal
Markets Served
• 503A Compounding Pharmacies (e.g., Hospitals, Veterinary, Infusion, and Cancer Centers)
• 503B Outsourcing Facilities
• Manufacturers
• Retail
Ordering Information
Contact us by phone at (800) 797-1405 or email sales@iso-med.com to gain access to our exclusive online ordering platform.
RXinsider’s Virtual Pharmacy Trade Show
24 / 7 / 365
450+ Booths, 80+ Aisles www.rxinsider.com
ASHP Midyear Clinical Meeting and Exhibition
December 8-12, 2024 | New Orleans, LA ashp.org/meetings-and-conferences/midyear-clinicalmeeting-and-exhibition
340B Coalition Winter Conference
February 24-26, 2025 | San Diego, CA 340bwinterconference.org
APhA2025
March 21-24, 2025 | Nashville, TN pharmacist.com/Conferences/Annual-Meeting
NHIA 2025
March 29 - April 2, 2025 | Washington, DC conference.nhia.org
NACDS Annual Meeting
April 26-29, 2025 | Palm Beach, FL annual.nacds.org
Asembia’s AXS25 Summit
April 27 - May 1, 2025 | Las Vegas, NV asembiasummit.com
ESTECH 2025
May 5-8, 2025 | Orlando, FL iest.org/Meetings/ESTECH
Pharmacy Futures 2025
June 7-11, 2025 | Charlotte, NC ashp.org/meetings-and-conferences/pharmacyfutures
February 24-26, 2025
Join Us!
The only conference dedicated entirely to the 340B program.
As challenges grow, so do opportunities. Dive into insights, connect with experts, and shape the future of 340B.
WHY ATTEND IN SAN DIEGO?
• In-depth sessions on 340B operations and compliance.
• Connect with peers and industry leaders.
• Hear directly from Washington insiders.
... is a
With 80+ aisles, the Virtual Pharmacy Trade Show is pharmacy’s one-stop destination to research and connect with leading providers of products and services throughout every pharmacy category and practice setting.
•
•
•
•
•
Cardinal Health RBC
July 9-12, 2025 | Denver, CO rbc.cardinalhealth.com
McKesson ideaShare July 10-13, 2025 | Nashville, TN mckessonideashare.com
NACDS Total Store Expo August 23-25, 2025 | San Diego, CA tse.nacds.org
ECRM Health System/Institutional Pharmacy Session September 8-11, 2025 | Cape Coral, FL ecrm.marketgate.com/sessions/category/ healthsystems
NCPA Annual Convention October 18-21, 2025 | New Orleans, LA ncpa.org/annual-convention
ASCP 2025 Annual Meeting & Exhibition October 23-26, 2025 | San Diego, CA annual.ascp.com
For listing and advertising details, please contact sales@RXinsider.com
Healthcare is your #1 priority, supporting you is ours.
Nuvem is a leading integrated pharmacy solutions partner empowering healthcare organizations and pharmacies by providing innovative services and tools that promote healthier communities and drive savings.
340B
Technology
•Contract Pharmacy
•Split-Billing
• Advanced Referral Program
Pharmacy Management Program
•In-House Pharmacy Services
•Clinical Programs
•Patient Engagement
We Serve
Optimization & Compliance
Comprehensive 340B Program Management
•ESP Management
HRSA Audit Support
We support Covered Entities of all sizes that provide care to communities facing a variety of barriers to access comprehensive medical care and medication. Providers require innovative technology and specialized expertise to manage a successful pharmacy program, remain compliant, and achieve clinical objectives. Nuvem is the solution.
CEO: Scott Seidelmann
Founded: 2014
Employees: 250+
Toll-Free Phone: (888) 356-6225
Phone: (856) 272-1458
Empowering covered entities to successfully manage all their patient scripts with one holistic pharmacy solution, positively impacting patient health and financial outcomes.
Address: 161 Gaither Drive, Suite 201 Mount Laurel, NJ 08054
Website: www.Nuvem.com
We are committed to prioritizing affordable healthcare, making it accessible to all, and creating a positive impact on society through our services and partnerships. Through a complete technology suite, integrated service delivery, and elevated 340B expertise, Nuvem’s holistic solution yields enhanced drug inclusion, increased financial performance, and improved patient care.
Nuvem’s story began in 2014 and grew quickly into three separate brands: 340Basics, Assent, and Apovia. Together in improving accessibility and adherence to clinical care, but seemingly independent in operation. As the brands grew and expanded, the value of joining forces became clear. In 2023, Nuvem merged their expertise and resources, bringing one comprehensive solution, streamlined experience, and equitable partnership to medically underserved, non-profit healthcare organizations.
Combining all of our solutions and services represents our commitment to facilitating 340B programs — from compliance and optimization to patient engagement and education — through a fully integrated suite of cloud-based pharmacy tools and personalized support.
Product Overview
n 340B Technology: Enhance program management, increase savings, and optimize performance.
Nuvem’s proprietary software empowers all eligible organizations to efficiently manage the complexities of the 340B pharmacy program with a technology suite including TPA services such as contract pharmacy, split-billing, and advanced referrals. Our industry-leading technology solutions, knowledge, training, and service offerings enable healthcare organizations to increase claims capture and optimize their programs’ clinical and financial results.
Our 340B technology suite offers precise attention to detail with flexibility to be customized to each organization’s unique needs.
n Pharmacy Management: Implement a more robust healthcare mission and enhance financial performance.
We offer pharmacy management services to implement and manage in-house pharmacies to improve patient script capture and mitigate the impact of manufacturer blocks. Nuvem offers top to bottom support in building or managing in-house pharmacies by guiding covered entities through the process from credentialing, licensing, and construction to ordering, hiring, and more, so the organization remains focused on providing the best care for their patients.
n Program Optimization and Compliance: Acting as an expansion of your team, our dedicated team of 340B experts do the work, so you can stay focused on providing the best care for your patients.
Our experienced team of 340B program investigators thoroughly review healthcare organizations’ prescription data, policies and procedures, and contracts, then build a solution to maximize savings and maintain HRSA compliance with components that meet a program’s unique needs. Bundling services that reveal opportunities for savings, along with HRSA Audit support into a holistic solution empowers healthcare organizations to have visibility into all areas of their 340B programs.
Our full suite of Optimization and Compliance services includes Comprehensive 340B Program Management, ESP Management, Audit Services and Support, HRSA Corrective Action Plan (CAP) assistance and implementation, Drug Cost Efficacy and Utilization analysis, Policies and Procedures Development & Review, Covered Entity HRSA/ OPAIS registration, and more.
“Your entire team has a wealth of experience matched with a caring heart and a fierce determination which has enabled you to accomplish so much and I thank you for sharing that well-earned insight.”
— Executive Director, Health Center, Brooklyn, NY
President & CEO: Jonathan Bergstrom
Founded: 2015
Phone: (775) 386-6677
Combining expertise and advanced tech, we elevate sterile compounding for 503A and 503B pharmacies. Our solutions enhance safety and effectiveness in custom sterile drugs, addressing FDA shortages for hospitals and patients.
Address: 301 W. 28th Street, Unit F National City, CA 91950
Website: www.medizap.co
MediZap is transforming the compounding industry by addressing the critical need for sterility assurance in compounded sterile drug products. Recognizing the limitations of traditional aseptic filtration, we are pioneering the use of E-Beam and X-Ray terminal sterilization to achieve the highest possible Sterility Assurance Level (SAL). We aim to elevate safety standards and ensure compliance with USP 797 and cGMP guidelines.
With locations in California and Texas, we offer E-Beam and X-Ray terminal sterilization services certified to ISO 13485 and ISO 11137 standards. We are FDA-registered and hold DEA registration for Schedules II-V, providing a robust and reliable sterilization solution. Our DualBeam™ processing system boasts a 99% uptime, guaranteeing swift turnaround times, including standard two-day, rush one-day, and even same-day options. Our dedicated capacity ensures flexibility for manufacturers without requiring advance reservations. Standard formats include IV bags, pre-filled syringes, vials, and syringe push, supporting safe, timely care.
• Superior Sterility Assurance: E-Beam and X-Ray technology provide a remarkable SAL of 10-⁶, surpassing autoclaving’s SAL of 10-³, significantly reducing contamination risk. This level of assurance is vital for safeguarding patient health and minimizing healthcareassociated infections — a top priority for hospital systems.
• Reduce Human Error: Compared to aseptic processes that rely on environmental and human factors, this process reduces contamination risks. It extends drug beyond-use dates, ensuring the stability and availability of critical medications.
• Enhanced Drug Quality: Unlike heat-based sterilization methods, E-Beam and X-Ray are gentler on reducing potency degradation associated with autoclaving. This ensures that compounded drugs retain their efficacy and stability, which is crucial for optimal therapeutic outcomes.
• Operational Efficiency: Our services provide unparalleled speed, flexibility, and responsiveness, which is essential for hospitals that need timely medication access, especially during drug shortages or urgent patient needs.
• Environmental Responsibility: Our technology aligns with sustainability initiatives by eliminating radioactive materials such as Cobalt-60, commonly used in gamma sterilization, thereby supporting hospitals’ environmental goals.
• Advanced Sterilization Expertise: We offer a dedicated solution to achieve the highest sterility standards, with expertise in validating sterilization processes according to ISO 11137 guidelines. This commitment is crucial for regulatory compliance and ensures the safety and efficacy of compounded drugs in healthcare settings.
• Streamlined Packaging Solutions: Understanding the challenges hospitals face with packaging, we provide pre-validated primary and secondary packaging options explicitly designed for E-Beam and X-Ray sterilization. This eliminates the need for costly, time-consuming sourcing and validation studies, allowing hospitals to focus on operational efficiencies.
• Compliance Support: We help hospital systems navigate regulatory complexities with a team of experts guiding compliance with USP, cGMP, and ISO standards. We also provide best practice documentation to ensure compounded drug production meets the highest quality and safety benchmarks, maintaining impeccable document control.
Additional Resources
Our resource center is a comprehensive knowledge hub, offering Zap+Learn webinars, articles, video library, and white papers.
As a proud sponsor of the Alliance for Pharmacy Compounding (APC), we are committed to promoting and protecting the practice of pharmacy compounding. We actively support APC’s efforts to address drug shortages and advocate for access to compounding, including lobbying activities on Capitol Hill. We are also a member of the Outsourcing Facilities Association (OFA), representing FDA-registered 503B outsourcing facilities. OFA works with industry partners, government agencies, and healthcare providers to ensure access to safe, effective compounded medications.
MediZap participates in various trade shows, such as the ASHP MidYear Clinical Conference, American Academy of Anti-Aging Medicine (A4M), and Parenteral Drug Association (PDA) events, to showcase our innovative solutions and expand our market presence. We partner with Complete Group Services (CGS), the first and only GSO dedicated to compounding and manufacturing pharmaceutical products.
Contact a MediZap sales representative at customerservice@medizap.co.
Ndidiamaka (Didi) Okpareke, PharmD RPh Pharmacist, Founder
~ Olive Tree Compounding Pharmacy
After graduating with honors from the University of New Mexico College of Pharmacy, Ndidiamaka (Didi) Okpareke, PharmD, RPh spent nearly a decade in various retail and hospital pharmacy roles. She returned to New Mexico in 2016 to begin working toward realizing her dream of becoming an entrepreneur. A year later, Okpareke opened the doors of the Olive Tree Compounding Pharmacy in Rio Rancho.
As founder and sole pharmacist, Okpareke began by compounding non-sterile medications for families and pets. From the start, the pharmacy followed all relevant US Pharmacopeia (USP) guidelines, including USP 795 for non-sterile preparations and USP 800 for hazardous materials necessary for compounding medications. Over time, Okpareke hired a pharmacy assistant and pharmacy technician. “Together, the three of us built Olive Tree from the ground up,” she says. “It was really like a grassroots movement.” In fact, they were so successful she realized they could achieve more.
To continue growing, Okpareke knew they would need a bigger space — but the entrepreneur in her also knew she wanted it to be her own space. So, in 2020, she began building a commercial real estate practice that led to a new facility. Still located in Rio Rancho, the 6,000-square-foot building houses Olive Tree and has additional space for rent.
Okpareke’s vision was to add compounded sterile medications to Olive Tree’s offering. To support that, she decided to build a clean room suite that included a clean room, an ante-room, and a room for compounding hazardous materials. “To me, having an amazing environmental monitoring system is essential to building a clean room suite,” she says.
In their previous space, they monitored pressure and temperature manually using a data logger. “We would dock the logger every morning, and it would tell us what the temperature and pressure had been for the last 24 hours,” she explains. While this worked well for their needs at the time, with the
plan to expand into sterile medications — Okpareke knew she wanted to automate as many processes as possible. Her plan was to install a system that monitored the pressure and temperature as well as humidity continuously.
When construction on the facility was wrapping up in April of 2024, Okpareke visited the site and found that the HVAC subcontractor had only installed a HEPA filter. “I asked when the environmental monitoring system would be going in — and realized pretty quickly he didn’t understand what I needed,” Okpareke recalls. The problem? The State Board of Pharmacy was due to inspect Olive Tree’s new space in less than a week. That’s when she remembered meeting a representative from Rees Scientific at a recent APC event. “The rep walked me through everything at the show and I thought it was very cool,” she says. “Honestly, though, I thought it was probably more sophisticated than anything we’d ever need.” She walked away thinking Rees’ systems were meant for government labs and other large, high-level operations.
Still, Okpareke knew they’d be able to help her — even if that meant simply pointing her in the right direction, so she decided to reach out. “I literally sent an email while I was sitting in the parking lot of my new building, minutes after my conversation with the HVAC contractor.” As it turned out, there was a Rees representative in Albuquerque that day who could meet her within hours.
What happened next was nothing short of a miracle.
“I told the rep from Rees what I was looking for and that it needed to be fast to install and easy to use,” explains Okpareke. “He knew exactly what would work for us, and I had a quote in my hand before the end of the day — which I approved right away.”
Two days later, a Rees technician came to the site with all the necessary equipment and installation began. “Everything was in place and working in time for the State Board of Pharmacy inspection,” she adds. “I still can’t believe it.”
Okpareke had her pharmacy tech go through the training process with Rees on how to use the system. However, she says once she got through the inspection and logged on for the first time — she found it all pretty intuitive. “Even though I didn’t go through any formal training — I got the hang of it pretty quickly. With a few clicks, I can see the readouts I need on all the environmental markers we are measuring.”
The Rees monitoring system is already doing its job. “Almost immediately, the system was telling me that the pressure in our USP 800 room was too low,” explains Okpareke. That means Olive Tree can’t start compounding anything that involves hazardous materials because it puts whoever is working in the room at risk of absorbing harmful particles. Rees sent a technician to re-evaluate the system and confirm it was working properly.
“I have to say, I was impressed by her thoroughness,” Okpareke says. “She didn’t just check that everything was plugged in and running ‚— she looked at every single connection.” The next step is for her contractor to conduct a Testing, Adjusting and Balance assessment to check airflow in the HVAC system so they can map back to the original plan and determine what’s causing the issue.
“With a system like this in place, I know I can grow in the right way — not only in terms of compliance but also for the safety of our patients and staff.”
Ndidiamaka (Didi) Okpareke, PharmD RPh
Pharmacist,
Founder
~ Olive Tree Compounding Pharmacy
In addition to complying with USP 795, 800 — and now 797 for sterile compounding — Olive Tree also follows all Federal Drug Administration (FDA) and Drug Enforcement Agency (DEA) as well as State Board of Pharmacy requirements. The pharmacy goes through an external certification process every six months for the rooms and hoods used for compounding. This includes taking air samples and samples from the hood to verify there is no bacterial growth, as well as measuring pressure to ensure it is in range.
Today, Olive Tree has nine employees — and Okpareke says there’s so much more they want to do. “Once we start compounding sterile medications, I think we will grow quickly. It’s wonderful knowing I have a partner I can trust.” That, she says, comes down to the people at Rees. “From the first day, I’ve received nothing less than white glove service, and everyone I’ve encountered has been very professional and highly knowledgeable.”
Of course, the ease-of-use and reliability of the system itself is critical. “With a system like this in place, I know I can grow in the right way — not only in terms of compliance but also for the safety of our patients and staff.” What’s more, she adds that because Rees has so many options, she can definitely see upgrading as the pharmacy continues to expand its scope.
Okpareke’s advice to others? “No matter how small your operation or how big you want to grow it — Rees has a solution that will take manual environmental monitoring off your plate. Plus, you’ll have a knowledgeable, responsive team behind you that supports your vision and goals every step of the way. That’s invaluable.”
Real-time Alerts and Alarm Notifications via interactive phone, texts & e-mail
Risk Management and Preventative Maintenance safeguard products & facilities, identify critical trends & facilitate operational strategies
Rapid Service and System Support ensure quick response times with regional service technicians & 24/7/365 technical support
Data Integrity and Traceability accurately record & securely store environmental monitoring data
Maintain Product Quality and Minimize Loss reduce risks of product contamination or loss by monitoring temperature, humidity, differential pressure & more
Compliance with Regulatory Standards ASHP, <USP> 797, <USP> 800, cGMP, GxP, VFC FDA, & more
Customization and Scalability tailor a monitoring solution to different needs that can grow & adapt with a facility
Operational Efficiency and Cost Savings reduce the need for manual monitoring, save labor costs & minimize human error
THREE STERILITY TESTING OPTIONS, THREE STERILITY TESTING OPTIONS, THREE STERILITY TESTING OPTIONS, ONE STANDARD OF EXCELLENCE ONE STANDARD OF EXCELLENCE ONE STANDARD OF EXCELLENCE
Turnaround Time: 1 - 3 days
Uses direct fluorescence and solid-phase laser scanning cytometry to detect microorganisms
Validated alternative method per <1223> that is non-inferior to <71> testing
Membrane Filtration
Method Suitability Required (3.5x Sterility Volume)
Can test filterable products only
Turnaround Time: 6 days
Uses ATP-based bioluminescence to detect microorganisms
Validated alternative method per <1223> that is non-inferior to <71> testing
Closed Membrane Filtration or Direct Inoculation
Method Suitability Required (4x Sterility Volume)
Can test all sample types
USP <71>
Turnaround Time: 14 - 18 days
Visual examination of growth media for turbidity
Closed Membrane Filtration or Direct Inoculation
Method Suitability Required (3x Sterility Volume)
Can test all sample types
Get sterility test results in as little as four hours with rapid test methods.
President & CEO: Thomas C. Kupiec, PhD
Founded: 1998
Employees: 300+
Toll-Free Phone: (800) 393-1595
Phone: (405) 271-1144
Fax: (405) 271-1174
Email: info@arlok.com
Address: 840 Research Parkway, Suite 546 Oklahoma City, OK 73104
Website: www.arlok.com
ARL Bio Pharma is a contract laboratory that provides analytical and microbiological testing for health-system pharmacies. Since 1998, ARL has supported the industry-wide commitment to deliver high-quality drug products by providing guidance and test services for all phases of the product lifecycle following USP and FDA guidelines. ARL is ISO 17025:2017 accredited, FDA-registered and audited, and DEA licensed for Schedules I through V.
Sterility testing of compounded sterile preparations is crucial to prevent patient harm from microbial contamination. USP <797> requires sterility testing for:
• Category 2 CSPs which are assigned a beyond use date (BUD) that requires sterility testing.
• All category 3 CSPs.
The Food and Drug Administration (FDA) requires 503B outsourcing facilities to perform sterility testing for all drugs reported to be sterile and/or non-pyrogenic.
Sterility testing must be performed according to USP <71> or a validated alternative method per USP <1223> that is noninferior to USP <71>. Method suitability must be demonstrated for each drug product with correct sample quantities tested according to the chapter. Sterility failures must be investigated and include the identification of contaminating microorganism(s) with documentation of the investigation and corrective action.
n USP <71> Sterility Test Method: 14-18 Day Turnaround
This sterility method is a growth based test method that requires at least 14 days incubation time for microorganism growth to occur. ARL uses either a closed membrane filtration method (the preferred method) or a direct inoculation method for unfilterable sample types. At the conclusion of the test, if there is no evidence of growth, the drug product complies with the USP <71> test for sterility.
Rapid sterility testing allows for shortened incubation times compared to the traditional sterility test method. By reducing sterility test wait times, rapid sterility methods offer many supply chain advantages, faster product release schedules, and quick contamination investigations.
n Celsis ATP Bioluminescence Method: 6 Day Turnaround
This growth-based sterility test detects microbial contamination based on the presence of microbial Adenosine Triphosphate (ATP) in a sample. Results are objective and based on instrument analysis.
n ScanRDI Solid Phase Cytometry Method: 1-3 Day Turnaround
This non-growth-based sterility test detects microbial contamination based on cytometry, which detects and quantifies microorganisms in as little as four hours.
ARL’s rapid sterility validation protocol includes all required parameters listed in USP <1223> including specificity, limit of detection, repeatability, and equivalency. For the growth-based method, the recovery of stressed/injured microorganisms is also assessed, which is considered imperative as injured microorganisms are more representative of potential contaminants that may be present in preparations tested.
Request a Quote: info@arlok.com
ARL Bio Pharma Client Portal: portal.arlok.com
ARL’s client portal allows users to submit samples online, receive test results in real-time, and analyze test data trends.
The TruDelivery® RTU portfolio helps meet the real-world challenges of hospital pharmacies—and is ready when you need it. It’s about time.
The
TruDelivery® RTU portfolio
helps meet the
real-world
challenges of hospital
pharmacies
— and is always ready when you are. It’s about time.
Employees: 3,000
Toll-Free Phone: (800) 462-ENDO (3636)
Website: www.endo.com www.TruDelivery.com
Endo focuses on developing and delivering specialty pharmaceutical products — many of which are complex in nature and require unique expertise, technology, and equipment. We focus on medical therapeutics, specifically in the areas of urology, orthopedics, and endocrinology, and on sterile injectables for hospitals and health systems, along with generics. Our Endo Injectable Solutions business unit works with hospitals and healthcare systems to reduce complexity through operational efficiencies, innovating together to add value where it matters — from manufacturing to treatment — so that healthcare providers can focus on patient care. Our aseptic product portfolio spans various therapeutic categories and includes both branded and generic injectables.
Our RTU products, available through our TruDelivery® platform (TruDelivery.com), streamline hospital operations by eliminating the need for preparation time or transfer before patient administration. This can reduce preparation time, enhance convenience and workflow, and minimize potential preparation errors. All these advantages support quality care for patients in hospitals, clinics, and home health and long-term care systems. TruDelivery® RTU products require no compounding, diluting, or mixing1-5 and provide extended dating compared with compounded products.6-10,11* Most hospital pharmacy buyers can purchase TruDelivery® RTU products with their routine daily wholesale orders. These TruDelivery® RTU products are already available through your health system’s full-line wholesaler and on your group purchasing organization (GPO) contract.
TruDelivery® RTU products are designed to help address some of the challenges facing hospital pharmacies. Products that require the use of a separately packaged diluent, or that require mixing, compounding, or transferring to another container for administration, all require multiple steps before the medication can be administered to a waiting patient. Even under the best
circumstances, extra steps may introduce risk of error.12-16 In the Food and Drug Administration’s (FDA) guidance to medication manufacturers, the agency encourages the manufacture of products specifically designed to minimize medication errors. Reducing the steps required for preparation and administration may help reduce risk of medication errors.15
Contact your Endo Key Account Manager for more information on the below TruDelivery® products:
• Bivalirudin Injection RTU Bottles
• Dexmedetomidine Hydrochloride Injection RTU Bottles
• Ephedrine Sulfate Injection RTU Vials
• PREVDUO® (Neostigmine Methylsulfate and Glycopyrrolate) Injection RTU Prefilled Syringes
• Vasostrict® (Vasopressin Injection, USP) RTU Bottles
*For Category 3 compounded sterile preparations (CSP), the maximum beyond-use date (BUD) is 90 days at controlled room temperature (CRT), 120 days in refrigerator, and 180 days in freezer11 versus shelf life of two years at CRT for Dexmedetomidine, Ephedrine, and PREVDUO®7-9; 12 months at CRT and two years in refrigerator for Vasostrict®6; 72 hours at CRT and 18 months in refrigerator for Bivalirudin.5,10
References:
1. Vasostrict®. Prescribing Information. Endo USA, Inc. 2. PREVDUO®. Prescribing Information. Endo USA, Inc. 3. Ephedrine Sulfate Injection. Prescribing Information. Endo USA, Inc. 4. Dexmedetomidine Hydrochloride Injection. Prescribing Information. Endo USA, Inc. 5. Bivalirudin Injection. Prescribing Information. Endo USA, Inc. 6. Data on file. DOF-VS-02. Endo USA, Inc.; September 20, 2023. 7. Data on file. DOF-PRVD-01. Endo USA, Inc.; July 20, 2023. 8. Data on file. DOF-EH-01. Endo USA, Inc.; July 31, 2023. 9. Data on file. DOF-DX-01. Endo USA, Inc.; July 26, 2023. 10. Healthcare Distribution Alliance. Standard pharmaceutical product and medical device information: Bivalirudin Injection. July 10, 2023. 11. The United States Pharmacopeial Convention. USP compounding standards and beyond-use-dates. https://go.usp.org/2022_Revisions_795_797. Accessed April 29, 2024. 12. Fanikos J, Burger M, Canada T, et al. An assessment of currently available i.v. push medication delivery systems. Am J Health-Syst Pharm. 2017;74(9):e230235. 13. Institute for Safe Medication Practices. ISMP safe practice guidelines for adult IV push medications. https://www.ismp.org/sites/default/files/attachments/2017-11/ISMP97Guidelines-071415-3.%20FINAL.pdf. Accessed April 29, 2024. 14. Hertig JB, Degnan DD, Scott CR, Lenz JR, Li X, Anderson CM. A comparison of error rates between intravenous push methods: a prospective, multisite, observational study. J Patient Saf. 2018;14(1):60-65. 15. U.S. Food & Drug Administration, Department of Health and Human Services, Center for Drug Evaluation and Research. Safety considerations for product design to minimize medication errors: guidance for industry. https://www.fda.gov/media/84903/ download. Published April 2016. Accessed April 29, 2024. 16. American Society of Health-System Pharmacists. ASHP guidelines on preventing medication errors in hospitals. Am J HealthSyst Pharm. 2018;75(19):1493-1517.
In the realm of healthcare, pharmacy teams stand as crucial contributors whose primary goal is to improve patients’ lives through optimal medication management. They act as vital intermediaries, ensuring patients receive the correct medications, are protected from potentially harmful ones, and can gain access to the products they need at the right time. These professionals offer more than mere dispensing of drugs; they provide invaluable clinical expertise, collaborate with other healthcare professionals in comprehensive treatment planning, and play a pivotal role in patient education, particularly in areas where treatment knowledge is lacking.
In their critical role, however, pharmacy teams are often hampered by manual, time-consuming processes that divert their attention from patient care. Tasks such as manually tracking medication inventories, processing drug recalls, and managing shortages require extensive coordination across disparate systems, reducing efficiency and limiting their ability to provide timely interventions. These administrative burdens, compounded by the need for constant communication with suppliers and healthcare providers, leave pharmacy teams with less time to apply their clinical expertise, collaborate in treatment planning, and educate patients. This reactive approach not only strains their workflow but also hinders their capacity to fully contribute to optimal patient outcomes. Supply chain digitalization offers a powerful solution to these challenges by automating and integrating the various processes that currently burden pharmacy staff.
By streamlining time consuming administrative tasks and improving supply chain visibility
through end-to-end healthcare supply chain digitalization, pharmacy personnel are able to free up valuable time, allowing them to focus more on direct patient care and personalized health outcomes. This comprehensive approach underscores their commitment to maintaining the highest quality, safety, and integrity standards in patient care.
Today’s healthcare supply chain faces numerous challenges, including frequent drug recalls, shortages, and the increasing complexity of compliance regulations. Managing recalls often requires manual tracking across multiple systems and locations, while shortages force pharmacies to continuously communicate with suppliers and find alternatives, leading to delays in patient care. Compliance adds further strain as pharmacies must adhere to evolving regulations, increasing the risk of errors and operational slowdowns. These challenges also contribute to labor shortages as the growing complexity of supply chain management leads to burnout and higher turnover. In addition, these inefficiencies drive escalating costs, with pharmacies dedicating significant resources to managing shortages, recalls, and compliance. This strain ultimately impacts patients by delaying care.
Gaining full visibility into the healthcare supply chain is another key challenge. Full visibility is essential for ensuring product availability, safety and compliance. It allows healthcare organizations to track and authenticate products in real time, reducing the risk of counterfeiting and ensuring regulatory compliance. With better visibility, organizations can prevent shortages by monitoring inventory levels and managing
demand proactively, while also optimizing stock to minimize waste. This transparency enables quicker responses to disruptions, enhances collaboration across the supply chain, and ultimately improves patient care by ensuring timely access to critical medicines and supplies. However, gaining full visibility into the healthcare supply chain is challenging due to fragmented systems where different stakeholders use incompatible technologies, and data silos prevent seamless information sharing. Complex regulatory requirements, like DSCSA compliance, add further complexity, as tracking and tracing medications involve multiple layers of oversight. Additionally, global dependencies create logistical barriers, such as varying standards across borders, making it difficult to monitor products in real time.
The healthcare supply chain is often trapped in a reactive and manual mode of operation due to its reliance on outdated systems and fragmented processes. Pharmacies typically depend on manual processes to enter data into inventory management systems, causing outdated demand and supply plans. This slows decision-making and causes inefficiencies like stockouts, delayed shipments, and inventory imbalances, which are often only addressed after they occur. Without integrated, automated, data-sharing systems across the supply chain, pharmacies frequently react to emergencies — such as medication shortages — rather than anticipate and prevent them. As a result, costly last-minute orders or overstocking of less urgent medications occurs, leading to waste and increases in working capital.
These supply chain breakdowns have a significant downstream impact on pharmacies
and patient care. As pharmacies struggle to manage inventory, respond to shortages, and ensure timely medication availability, patients often experience delays in treatment due to stockouts or unavailability of critical drugs. Pharmacy professionals, who are crucial to patient safety and care, are increasingly burdened with administrative tasks like managing recalls and sourcing alternative medications, pulling them away from their primary responsibilities of medication counseling and personalized care. This reactive approach impacts the overall quality of care, as pharmacy teams have less time to focus on patient outcomes.
Furthermore, these supply chain challenges drive higher operational costs, which can trickle down to patients in the form of increased cost of care. In severe cases, limited access to essential medications during shortages can worsen patient health outcomes.
The combination of manual, fragmented supply chain processes and their downstream effects creates a domino effect, disrupting pharmacy operations and directly affecting patient care and safety. Addressing these challenges requires the adoption of digital solutions, including multi-enterprise network platforms, to enhance visibility, automate processes, and improve the responsiveness of the healthcare supply chain, ultimately allowing pharmacy teams to refocus on delivering high-quality patient care.
The shift towards a digitalized supply chain has been hindered by the inability to link systems and processes across the supply chain and maintain those links cost effectively. However, compliance regulations such as the DSCSA have created opportunities to create digital twins of medicines and digitalize supply chain processes. However, current methods for supply chain data exchange using point-to-point integration models have proven to be too costly and fragile, which has led to a reliance on manual and paperbased solutions. Additionally, the lack of uniform data standards and real-time visibility makes it difficult to respond quickly to disruptions, while the rigid nature of the model hinders flexibility and adaptation to new technologies or changing business needs. Overall, the point-to-point model is costly and inefficient, particularly in complex sectors like healthcare, where seamless collaboration and real-time data are essential for success.
It’s time for the healthcare supply chain to move away from a point-to-point model and adopt
a multi-enterprise network platform. This is a powerful digital ecosystem that connects various stakeholders, including manufacturers, suppliers, distributors, healthcare providers, and regulatory bodies, on a unified platform. This network enables seamless data sharing and collaboration across all participants in the supply chain, which is essential for ensuring the timely and efficient production, distribution, and delivery of pharmaceutical products — and improved patient care. When the unified platform is combined with a network-wide data model, the result is a clean and actionable data set that eliminates time-consuming manual processes for data cleansing. With a clean, real-time data set, visibility is attained and intelligence and decision making is accelerated. In addition, supply chain digitalization introduces several key features that transform how businesses manage complex, multi-enterprise operations. For example, nocode design environments empower non-technical business users to configure workflows independently. This saves valuable time that can be redirected to focusing on patient care. Another example is the introduction of more robust, integrated reports and dashboards, offering complete end-to-end visibility of supply chain processes. These innovations help organizations reduce out-of-stocks, optimize inventory, and improve overall supply chain efficiency, offering new levels of transparency and collaboration and giving time and resources back to the patients.
The healthcare industry is at a pivotal juncture where the adoption of a fully digitized, multienterprise network model is crucial. This model is not just a technological upgrade but a strategic necessity to mitigate the myriad risks associated with the current state of the industry. By embracing this multi-enterprise network model, the pharmaceutical and healthcare sectors can effectively navigate the challenges posed by limited resources, complex operational landscapes, increasing costs, and unpredictable market dynamics.
Envision a future where pharmacy resources are seamlessly integrated into an advanced system that efficiently manages recalls and product shortages. In this system, when a recall is issued, a notification is instantly received, but only for those products they have purchased or dispensed. This alert comes complete with detailed recall information, ready to be communicated to prescribers or patients and enriching thirdparty systems, eliminating the need for extra administrative effort.
Picture a scenario where pharmacy teams are proactively alerted about potential shortages, informed by their historical ordering patterns. They receive continuous, real-time updates on product statuses directly within the system, sparing them from time-consuming internet searches for alternative suppliers.
Imagine a world where safety and compliance are effortlessly maintained through technology. Counterfeit or recalled products are automatically identified and flagged before dispensation, ensuring the highest level of confidence in the medications provided. This is achieved with no requirement for manual or administrative intervention.
As technology rapidly advances, we are swiftly approaching the realization of these ideals. The integration of sophisticated systems in pharmacy management is no longer a distant dream but an impending reality, poised to revolutionize the way pharmacy teams ensure the safety and well-being of their patients.
In conclusion, the role of emerging technologies in transforming the pharmaceutical and healthcare supply chains is undeniable. To truly unlock their potential, the industry must transition from the outdated point-to-point data exchange model to a multi-enterprise supply chain orchestration network model. This shift brings the future closer than you think by enabling real-time visibility, seamless collaboration, and data-driven decisionmaking across the end-to-end supply chain. For pharmacy professionals, it’s not just about enhancing operational efficiency — it’s about ensuring optimal patient care and outcomes through proactive responses to disruptions and streamlined regulatory compliance, such as DSCSA requirements. As the industry evolves, embracing these network models and advanced technologies will be pivotal in overcoming current and future challenges, paving the way for a more advanced, efficient, and patient-centered pharmaceutical landscape. The opportunity to shape the future is at hand, and it must be pursued with foresight and commitment.
Contributed
by
Dan Walles, General Manager of Traceability & Compliance, TraceLink
Founder: Walt Schum
Founded: 1959
Phone: (513) 772-9410
Address: 10310 Spartan Drive Cincinnati, OH 45215
Website: www.so-low.com
Email: sales@so-low.com
For over 65 years, So-Low has been manufacturing ULT freezers and medical-grade refrigeration equipment. Our goal is to provide the highest quality cold storage equipment with a personalized customer service experience.
Since 1959, So-Low Environmental has been manufacturing ultralow temperature freezers, and laboratory and medical cold storage equipment. Based in Cincinnati, Ohio, the family owned and operated company has shipped equipment worldwide to over 130 countries. Our goal is to provide the highest quality cold storage equipment with a personalized customer service experience.
Product Overview
So-Low Environmental offers a comprehensive line of ultralow temperature freezers to -85°C, along with medical-grade refrigerators and freezers designed to meet the demanding storage needs of sensitive medications and vaccines. Our refrigeration systems are designed to keep your valued content in a uniform and stable temperature environment. Select models are tested and verified to Lab Grade Refrigerator and Freezer Energy Star® certification to help minimize operating costs. Our equipment is built to last using the highest quality materials. Precise and userfriendly digital controls have all the alarm features you depend on to be informed when intervention is needed. Built in portholes allow access to the chamber for third-party probes for additional data recording and monitoring. We offer upright and chest style equipment to fit your space and storage requirements. Sizes range from small undercounters to large three door units with custom sizes available upon request.
So-Low Environmental is the U.S. distributor of Liebherr Scientific and Healthcare cold storage equipment. We believe all medical and scientific professionals should have access to the highest quality cold storage equipment. Liebherr products grow our catalog to ensure our customers have the highest quality choice for their cold storage.
Product Specifications
n Temperature Ranges
• 2°C to 8°C Refrigerators
• -25°C Freezers
• -45°C Freezer
• -85°C Freezers
n Product Styles
• Undercounter
• Chest
• Upright: Single, Double, and Triple Door
• Passthrough: Single, Double, and Triple Door
• Combination Refrigerator and Freezer
n Safety
• Audible and Visual Alarms
• High and Low Temperature
• Remote Alarm Contacts
• Third-Party Probe Access Port
• Temperature Recording
n Certifications
• UL, ETL, CSA, Energy Star®, and SNAP Compliant
Ordering Information
To request a quote, please contact our office by phone at (513) 772-9410 or email us at sales@so-low.com.
Simplifi 797® IV Worfklow Management
MedTrays
MedStorage
Pharmacy Surveillance
Drug Diversion
Infection Prevention
Simplifi+® Pharmacy Compliance and Sentri7 ® Clinical Surveillance—Designed by pharmacists for pharmacists. Access our turnkey applications on the SoleSource platform with Simplifi+ and Sentri7 to:
Introducing a comprehensive suite of pharmacy compliance and clinical surveillance solutions designed by pharmacy experts, on a single platform, with tailored workflows, and reporting.
With Simplifi+ and Sentri7, expect the innovation and expert support of Wolters Kluwer every step of the way.
• Use AI to detect drug diversion quickly to keep patients and staff safe
• Drive proactive medication intervention to reduce costs and risks
• Streamline USP compliance
• Enhance IV workflow management
• Automate drug inventory oversight
• Keep medication storage compliant
President & CEO: Nancy McKinstry
Founded: 1836
Employees: 21,400+
Stock Symbol: WTKWY
Simplifi+® and Sentri7® applications on one powerful SoleSource® platform help to standardize clinical, pharmacy, and compliance programs. Customers access evidenced-based content, tailored workflows, and robust analytics to improve patient care, quality, and safety.
Phone: (608) 829-7300, Ext. 2
Address: 525 Junction Road, Suite 5000, Madison, WI 53717
Website: www.wolterskluwer.com
Wolters Kluwer provides trusted clinical technology and evidencebased solutions that engage clinicians, patients, researchers, and the next generation of healthcare providers. More than 6.5 million clinicians use Wolters Kluwer’s expert solutions to reduce the variability that stands in the way of effective care around the world. Solutions include Sentri7 clinical surveillance and Simplifi+ pharmacy compliance to deliver the best knowledge and evidence into the hands of the people who need it most.
Wolters Kluwer’s clinical surveillance and compliance applications are deployed on a single platform for easy integration with EHRs or into existing workflows, minimizing the impact on resource-strapped IT and clinical teams. Customers can scale and standardize programs for maximum impact on patient safety, quality care measures, and financial performance.
n Simplifi+ Pharmacy Compliance
• Simplifi 797® : Ensure USP Chapters 795, 797, and 800 compliance with confidence.
• Simplifi+ IV Workflow: Streamline USP compliance and meet all ISMP and THRIV guidelines.
• Simplifi+ MedTrays: Standardize the configuration of medication trays and improve inventory oversight.
• Simplifi+ MedStorage: Improve medication storage compliance outside the pharmacy.
“Using Simplifi 797 and IV Workflow Management with Assure-Trak helps streamline our compliance efforts and aids our team with both competency instructions and documentation. It also gives pharmacy more control, with less reliance on IT. It just makes sense.”
— Ryan Brown, PharmD, Pharmacy Manager at Conway Regional Health System
n Sentri7® Clinical Surveillance
• Sentri7 Infection Prevention: Reduce time spent identifying patients at risk for HAIs and access one-click submissions to NHSN.
• Sentri7 Pharmacy with Antimicrobial Stewardship, Opioid Stewardship, and Bayesian dosing: Sophisticated pharmacy workflows and analytics to optimize medication therapy, patient outcomes, and cost savings. Turnkey regulatory reporting including AUR.
• Sentri7 Drug Diversion: AI detection of potential drug diversion early and accurately from purchase to patient.
“Using the Sentri7 Drug Diversion solution, my team is in a better position to be proactive in our drug diversion surveillance, ultimately supporting heightened safety across our organization.”
— Tammy Burns, PharmD, Director of Pharmacy Services, Mary Lanning Healthcare
n Help Ensure Compliance
• Simplifi+ IV Workflow, together with Simplifi 797, delivers a complete compounding solution that helps ensure USP compliance, meets all ISMP and THRIV guidelines, and includes policies, procedures, tasks, training, continuing education, and competencies.
• Ensure compliance with CDC and The Joint Commission AMS best practices and reporting requirements and The Joint Commission’s Pain Management Standards with Sentri7 Pharmacy.
n Save Time in Pharmacy-Tailored Workflows
• Streamline detection and investigation of potential diversion with Sentri7 Drug Diversion.
• Access workflows that drive standardization and improve productivity with Sentri7 Pharmacy and Simplifi 797 with IV Workflow.
• Delivering policies into pharmacists’ workflows saves time and provides quick access to the latest evidence-based guidance with Simplifi + MedStorage and Simplifi + MedTrays.
n Improve Patient Safety
• Avoid adverse drug events, limit medication errors, and manage opioids and antimicrobials with Sentri7 Pharmacy.
• Uncover patterns of potential diversion to intervene earlier with Sentri7 Drug Diversion.
• Elevate patient and staff safety by using streamlined real-world workflows, risk management, and quality assurance practices, reporting, policies, procedures, and training with the Simplifi+ compliance suite.
n Optimize Medication Management
• Optimize the use of high-cost drugs, antimicrobials, and opioids to improve clinical outcomes and reduce costs with Sentri7 Pharmacy.
• Improve drug inventory oversight and ease inspections by documenting from anywhere with Simplifi + MedTrays and Simplifi + MedStorage.
“With Simplifi+ MedTrays, in the world of shortages nowadays, it has been extremely helpful to know what we still have in stock and expiration dates right on a computer screen instead of manually inventorying things …”
— Jennie Luter, PharmD, Clinical Pharmacy Coordinator, Southwest Mississippi Regional Medical Center
Pharmacist ... is a Great Resource
Take an in-depth look at specific products and services that help pharmacies improve patient care, profitability, and cost containment. Available in our digital library and within each issue of 20Ways.
INTRODUCING THE NEW INFINITY SERIES ™ WITH PRECISE, PATENTED TEMPERATURE CONTROL
Variable Speed Temperature Control
Patented infinite speed control technology delivers only the precise amount of refrigeration needed to reduce energy consumption without sacrificing performance.
Durable Design
Our cold storage solutions deliver uncompromising performance and lasting peace of mind over years and years of continuous use.
Flexible Storage
Interior cabinet space can be configured to your exact needs.