ATLANTIC

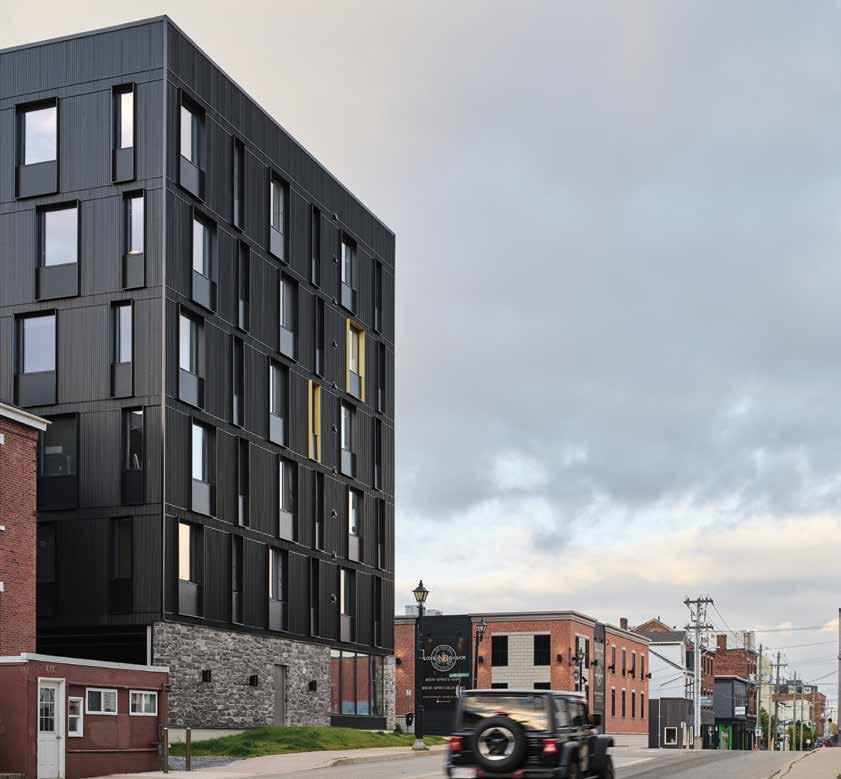
Good design, high performance break affordable housing stereotype
MACKINTOSH DEPOT
City facility combines functionality and energy efficiency
THE NEEDS AND BARRIERS FOR DEEP BUILDING RETROFITS: CAGBC report
ROSS CREEK ANNEX
Deep energy retrofit delivers distinctive community building
CONFERENCE GUIDE INSIDE
Unrivaled Service | Unparalleled Expertise | Bold Innovation
Why Galvanize?
✔ Maximum Protection
✔ Durability & Adaptability
✔ Longest Life Coating
✔ Best Return on Investment
✔ Eliminate Maintenance
Corbec Specializes in Galvanizing a Wide Range of Structures and Metal Products, Including: and more!
Buildings
Bridges
Galvanized Rebar
Towers & Electric Power Grids
Steel Structures
OEM Products
To Corbec What Matters Is:
▪ Galvanizing Better
▪ Quality & Innovation
▪ Expertise & Quality Assurance
▪ Service - Pre-During and After the Project
▪ Collaboration and Assistance to the Project Team
State-of-the-art Facilities
Hamilton | Montreal | Quebec | Halifax
Publishing with CSA, the first-ever Environmental Product Declarations (EPDs).
The first in Canada for Galvanized Steel
The first in North America for Galvanized Rebar
Environmental Product Declarations (EPDs)
EPDs are critical in assessing the environmental footprint of materials, assisting in making informed decisions and effects the scope for considerations and design for sustainable construction projects. Why EPDs Matter?
Advantages of Using EPDs
▪ Leverage long-term cost savings
▪ Gain a competitive edge
▪ Reduce Environmental Footprints
▪ Enhanced Life Cycle Assessment
▪ Achieve Green Building Certifications
▪ and more
Utilizing EPDs in Your Project
▪ Material Selection
▪ Design Optimization
▪ Establish Clear Sustainable Targets
▪ Life Cycle Assessment
▪ Transparent Reporting
Simplify your design with the adaptable FIT80E Series ERV, perfect for both standard and mirrored layouts in sustainable multi-family projects. Learn about the FIT Series and more at Fantech.net.
CAGBC is proud to support Sustainable Architecture & Building Magazine’s regional FOCUS publications. It’s a great opportunity to share how Canadian regions are advancing green building. The Spring issue is timed well, as we look ahead to Building Lasting Change, our annual national conference.
For Building Lasting Change, we’ll be returning to Vancouver from June 18-20. As always, the CAGBC team is putting together a remarkable program, with two full days of business and technical sessions, as well as several forums, the CAGBC Awards Gala, and the Annual General Meeting. It’s a packed agenda so I encourage you to visit cagbc. org/BLC for more information. These forums provide an in-depth look at specific topics like sustainable affordable housing and the launch of LEED v5 in Canada.
In these tumultuous times, it is easy to get distracted from our mission. Let’s not forget that investment in buildings is for the long term, and speaking with industry leaders, we see growing recognition that decarbonization, resilience and sustainability can reduce risk for building developers and owners. We are committed to helping Canada’s building sector unlock the value of green buildings – by prioritizing operational savings, return on investments, lower insurance rates, higher valuations, occupant and environmental benefits.
We’re also helping building owners accelerate retrofits. With funding from Natural Resources Canada, we launched RetrofitsNow.ca and a report exploring the challenges and opportunities of Canada’s retrofit market. You can read about the initiative in this issue, and the exciting tools, case studies and insights to come.
You can also read about the results of CAGBC’s inaugural National Embodied Carbon Summit. This report consolidates the over 600 suggestions shared by industry experts during the Summit last spring. Together, we are working toward actionable industry-driven solutions to reduce embodied carbon in construction.
In this issue, you’ll also read about recent high-efficiency projects – a multi-bay works garage, a retrofit, and a mixed income multiunit residential apartment - as creative examples of sustainable building design. I hope you’ll enjoy this new issue, and that I will see you later this spring at Building Lasting Change in Vancouver.
Sincerely,
Thomas Mueller President & CEO, Canada Green Building Council
Save on and on with energy efficiency rebates
Save on all your projects, from equipment upgrades to new construction.
• Up to $1.5 million in rebates.
• 25% cash back on equipment.
• Up to $75 per square meter for new construction.
• Get up to 100% back on your energy audit.
• Incentives for renewable energy.
Save on and on with improved efficiency. Boost your productivity and enjoy ongoing energy savings that benefit your bottom line.
With upfront and long-term savings, efficiency rebates really add up!
L’efficacité énergétique permet d’économiser en continu
Économisez sur tous vos projets, de la modernisation de l’équipement à la construction de nouveaux bâtiments.
• Jusqu’à 1,5 million $ de remises.
• Remise en argent de 25 % sur l’équipement.
• Jusqu’à 75 $ par mètre carré pour les nouvelles constructions.
• Récupérer jusqu’à 100 % du coût de votre évaluation énergétique.
• Incitatifs pour les énergies renouvelables. Économisez en continu grâce à une meilleure efficacité. Augmentez votre productivité et profitez d’économies d’énergie continues qui profitent à vos résultats.
Avec des économies immédiates et à long terme, les remises sur l’efficacité énergétique s’additionnent vraiment !
New CAGBC report highlights critical needs and barriers for scaling up deep building retrofits
Despite significant progress in recent years, industry still has a long way to go to accelerate investments that improve the performance of existing buildings. The Canada Green Building Council (CAGBC) estimates that hundreds of millions of square meters of existing Canadian building space requires retrofitting to meet climate and energy efficiency targets. However, challenges and uncertainties about the best path forward are causing delays in adopting the types of asset transition plans needed to accelerate deep retrofits.
According to CAGBC’s new market report, Rapidly Scaling Canada’s Deep Retrofit Market: Stakeholder Insights into Barriers and Opportunities, among industry participants surveyed, only a slight majority (54%) were planning to undertake new transition projects this year.
“We know the pressure to decarbonize and improve energy efficiencies is being felt across the industry at all levels. At the same time there are still many barriers for delivering deep retrofits efficiently at scale,” said Laurna Strikwerda, Director, Project Development and Research at CAGBC. “As a critical first step to accelerating the planning, financing and implementation of deep retrofits, we wanted to first better understand what’s currently getting in the way, and how we can better support the industry scale up their efforts.”
The report features perspectives from a broad range of Canadian building professionals gathered during a series of in-person and online workshops in 2024 targeting stakeholders with commercial, multi-unit residential, warehouse and retail buildings. Insights were gathered from over 350 participants.
The report is now available on Retrofits Now (retrofitsnow.ca), a new industry-focused resource being developed by CAGBC to provide the latest information and tools to support real estate transition planning. Retrofits Now is supported by Purpose Building as part of their Purpose Accelerator: Canada’s Private Sector Retrofit Accelerator, funded by Natural Resources Canada (NRCan).
“Drawing on our years of experience planning and delivering deep retrofits, we will provide practical insights that give building owners confidence in their ability to deliver outcomes well beyond what they thought was possible,” said Eric Chisholm, CoFounder and Principal of Purpose Building.
The Rapidly Scaling Canada’s Deep Retrofit Market report is published on the new website, and features key insights that explore market barriers and needs, including:
• Access to data and technology.
• Dealing with a complex business case.
• New building codes and regulations.
• Leadership buys in.
• Standardized approaches across industry and asset classes.
To download the full report visit retrofitsnow.ca.
By Stephen Outerbridge
The new Mackintosh Depot of the Halifax Regional Municipality replaces three existing buildings. The original mandate demanded a new 4,149 sq.m facility on two levels. During design the mandate changed by adding a third-floor office level to provide space for a fourth client group within the facility and increasing the footprint to 4,695 sq.m.
We provided 3D rendered views and three layout options for a better sense of the building geometry and functionality. Within the design parameters, we provided the “best possible” design solution along with an optimal cost-effective construction solution for the site.
Functional efficiency and ease of use, including sensitivity to the operational relationship between the four municipal agencies using the building, were incorporated into the warehouse and office building design. The building has a convenient vehicle drive-through arrangement, accommodating a future 2-tonne monorail crane, 14 vehicle bays, three floors of offices, a gas detection system, and a racking system storage area.
Innovations include the CO2 sequestered concrete tilt-up walls; switching internal concrete block walls and elevator shafts also to tilt-up; carrying out critical inventory of existing facility equipment to reduce the size and efficiency of the storage area; repurposing the existing facility’s garage to store salt trucks and brine; and relocating wash bays to the existing facility. We were also able to limit excavation around the new Depot site while improving access to the existing facility.
Sustainability and longevity, low maintenance and high reliability solutions, with minimized effect on the environment, were paramount to design outcome. Occupant wellbeing, acoustic comfort and privacy were also integrated, with accessible design.
The project planning encouraged the City to work on increasing the availability of bus routes and bike lanes adjacent to the property which is in proximity to the downtown. An interior bike storage room, showers and locker rooms accommodate and welcome bike commuters to the new facility. The building is currently registered LEED v4 BD+C NC under CAGBC, with possible LEED Gold certification, carrying slightly over 70 points recorded.
We reviewed two sites during the Schematic Design Process and chose the Mackintosh Street property, which saved $1 million on the project. Poor fill was replaced with structural fill above the bedrock without need for piles. The existing fill removal represented the opportunity to remediate previous brownfield activities, which included earlier municipal site demolition fill and the remnants of an abandoned previous temporary ready-mix plant and demolition of an old abandoned HRM facility on the site.
The excavation afforded the opportunity to accommodate two large integrated underground storm water management chambers and discharge beds, with the integration of slopes and strategically positioned retaining walls to allow for a flat site; with both ends of the building matching two level street access points.
A garden with seating overlooking the Bedford Basin is strategically located within the office parking area. The existing forested area along the entire back embankment of the project site was preserved during construction to minimize erosion along the perimeters of adjacent properties. Storm water discharge was strategically placed to limit erosion of the embankment.
2. CO2 sequestered concrete tilt-up walls, constructed on site, provide a resilient structure and can be disassembled at the end of service life.
3. Detail at the garage doors. During the excavation two large integrated underground storm water management chambers and discharge beds were installed.
The office area, spread vertically across three levels and designed for collaboration and productivity, is flooded with natural light and controlled from glare using both sunshades and light diffusing PV modules to create inviting comfortable workspaces. Windows are strategically placed within the office spaces along the perimeter of the building on all three levels resulting in 77.2% of occupied space being within 7 metres of an operable window.
The mechanical layout, designed to integrate with the building architecture and interior design, consists of cost effective, energy efficient systems that perform reliably, providing quiet, controlled comfort, and excellent indoor air quality.
The facility is served by two air handling units with internal isolation, centrifugal fans and 90-95% efficient filters. The air handling units create a constant volume 100% outside ventilation unit, complete with a heat recovery device. The air supply unit serving the office areas is equipped with a humidifier. Truck Bays have carbon monoxide detection and immediate extraction systems should levels exceed 100 ppm.
PROJECT
CLIENT Halifax Regional Municipality
ARCHITECT EXP Architects Inc.
CONTRACTOR Bird Construction
ELECTRICAL/MECHANICAL ENGINEER M&R
Engineering
STRUCTURAL/CIVIL ENGINEER EXP Services Inc.
LANDSCAPE ARCHITECT Gordon Ratcliffe
Landscape Architects
COMMISSIONING AGENT WSP Canada Inc.
PHOTOS Julian Parkinson/Stephen Outerbridge
Sustainability and energy efficiency were of paramount consideration. In-floor heating is energized by natural gas boilers and the building was designed to incorporate load shedding, with LED light fixtures and 148 roofmounted PV modules achieving 10% of the building load. The inclusion of underground storm water storage, and three EV charging stations reflects the City’s dedication to reducing environmental impact.
The building automation systems were carefully planned and controlled to blend seamlessly with the building elements, ensuring optimal performance and energy efficiency. An energy analysis was performed on the building to verify energy targets for LEED and NECB 2017. The Depot exceeds NECB 2017 targets by 29.5%, demonstrating commitment to sustainable design practices. Halifax strategically pursued LEED Gold for water efficiency, indoor air quality, and energy optimization, substantially enhancing the building’s environmental performance. Credits related to electrical include location and transportation, light pollution reduction, building level energy monitoring, and advanced energy metering.
Finally, the building utilized locally made products as much as possible, including the structural tilt-up panels, which were site cast and tilted into place, and the large-span vehicle bay trusses which were fully fabricated within 15 kilometres of the site. The tilt-up panels can be disassembled and the steel components recycled at the end of the building’s service life.
ASHRAE
APRIL
8:00 AM12:00 PM
LOCAL ENERGY EFFICIENCY PARTNERSHIPS (LEEP)
9:00 AM12:00 PM ROOM 5
CAGBC - ZERO CARBON BUILDING ESSENTIALS
Mark Hutchinson, CAGBC & Will Marshall, LMMW
1:00 PM4:00 PM ROOM 5
ASHRAE - INTRODUCTION TO BUILDING DECARBONIZATION
Doug Cochrane, Independent Consultant
7:30 AM4:00 PM
5:00 PM7:00 PM
ROOM 6
PHIUS & BER - THE PATH TO ZERO: HIGH PERFORMANCE BUILDING ASSEMBLIES
Natasha Brooks, BER
ROOM 6
HCi3 - FUNDING & FINANCING FOR DEEP ENERGY RETROFITTING
Rochelle Owen, Rochelle Owen Consulting & Julia Sable, HCi3
HALIFAX CONVENTION CENTRE - ROOM 605
9:00 am4:00 pm CARIBBEAN DELEGATION BUILDING TOURS & SITE VISITS
AGENCY ART LOFTS, NOVA SCOTIA POWER HEAD OFFICE, RONALD MCDONALD HOUSE
Bus Departs from & returns to The Hampton Inn
PM BUILDING TOURS
AGENCY ART LOFTS, NOVA SCOTIA POWER HEAD OFFICE, RONALD MCDONALD HOUSE
Bus Departs from & returns to The Hampton Inn AM BUILDING TOURS
ASHRAE Region II Regional Planning Meeting & President Elect Training
LOT SIX BAR & RESTAURANT
BUILDGREEN ATLANTIC OPENING RECEPTION
TUESDAY, APRIL 29
Chris Benjamin & Hannah Minzlo , Ecology Action Centre
Tyler Hayden, emcee Vicki Worden, Green Building Initiative 1685 Argyle St, Halifax lotsix.ca
Osmond,
2:40 PM2:50 PM
GREEN ROOFS IMPACT ON A LID (LOW IMPACT DEVELOPMENT) STORMWATER MANAGEMENT PLAN
DEEP RETROFITS OF AFFORDABLE MULTI-FAMILY BUILDINGS: FROM ANALYSIS TO IMPLEMENTATION
Roxanne Miller, Soprema
Caleb Lamrock, Carlos Leon & Wahib Toulany, Stantec
DEEP RETROFITS –CARBON REDUCTION AND RESILIENCE STRATEGIES FOR FUTURE-READY HOUSING
Scott Armstrong & Hannah Cameron, WSP
EAC GREEN JOBS REPORT
RENEWABLE ENERGY AND NOVA SCOTIA’S PATH TO 2030
SMART ENERGY MANAGEMENT SOFTWARE –INDUSTRY LEADING PRACTICES
Martin Rovers, Nova Scotia Power
Chris Benjamin, Ecology Action Centre
THE CORROSION SOLUTION, WITH THE LOWEST GLOBAL WARMING POTENTIAL (GWP) – GALVANIZING
Hellen Christodoulou, Corbec
Matthew Winter, Arcelor Mittal Dofasco TRADESHOW VISIT OUR 50 EXHIBITORS TRADESHOW VISIT OUR 50 EXHIBITORS CONVENTION
CONVENTION HALL C1-C2
Anne Lombardi, Integral Energy Performance & Scott Wellard, The Housing Trust of Nova Scotia 5:00 PM6:30 PM
DOMESTIC HOT WATER HEAT PUMPS
Mike MacKenzie, ITC Technologies
STRATEGIES TO REDUCE THE EMBODIED CARBON IN THE ENVELOPE
Josh Havin, Vicwest
ENERGY RETROFITSELECTRIFYING WITH MODERN HYDRONICS
Dan Richer & Mike MacKenzie, ITC Technologies
ENERGY RETROFITS AS A GOLDEN OPPORTUNITY FOR IMPROVING INDOOR ENVIRONMENTAL QUALITY
Kaitlyn Gillis, Human Nature Connections & Sara Nikoofard, BC Ministry of Energy & Climate Solutions
ADVANCING DECARBONIZATION IN NON-PROFIT COMMUNITY CENTRES
Liam Cook, Navigate Energy & Andy Thompson, Aging Well Nova Scotia
AFFORDABLE NBC2020 PERFORMANCE PATH COMPLIANCE WITH PASSIVE HOUSE
Natasha Brooks, BER
CASE STUDY: USE OF LOW CARBON CONCRETE FOR AFFORDABLE HOUSING
Joel Westin, Bridgewater Ready Mix
PRACTICAL GUIDELINES & BEST PRACTICES FOR LOW CARBON EMISSION STEEL
CLOSING PLENARY: MOVING FASTER TOGETHER – COLLABORATION FOR NET-ZERO Hosted by Building to Zero Exchange (BTZx)
CONVENTION HALL
David Molinaro, Ameresco Asset Sustainability Group
BUILDING CERTIFICATIONS
Vicki Worden, Green Building Initiative, Mark Hutchinson, CAGBC & Bala Gnanam, BOMA Canada
DO YOU EVEN NETWORK? LEARN HOW TO WORK THE ROOM
Abhishek Khurana, Voyager Buildings
REVOLUTIONIZING EARLY DESIGN: AI AND COMPUTATIONAL INNOVATIONS FOR EFFICIENCY
Goncalo Pedro, RWDI
2020 NBCC AND KEY CONSIDERATIONS FOR MASS TIMBER DESIGN
Tom Joyce, University of New Brunswick & David Porter, WoodWorks Atlantic
CARIBBEAN DELEGATIONINFRASTRUCTURE EXPORT OPPORTUNITIES IN THE CARIBBEAN
Join members of the incoming mission from the Caribbean for a discussion about export opportunities for Atlantic Canadian businesses in the sustainable building sector who manufacture goods or provide services
The Ross Creek Annex is a music and food-focused community venue in the village of Canning, Nova Scotia, designed for Ross Creek Centre for the Arts as well as the larger surrounding community.
The building is a deep-energy retrofit of the previously decommissioned St Lawrence Church. The main church hall is transformed into a flexible music performance space that can also be used for a variety of events and gatherings. The building also houses a new recording studio, multi-purpose room and community kitchen on the newly accessible lower level.
The most significant sustainability strategy was renovating an existing building instead of demolishing and building new, saving 26.9 tonnes of carbon emissions by extending the life of the existing structure.
The church was an ideal candidate for the retrofit as no additions were needed to fulfill the project space requirements and therefore the surrounding forest was able to be maintained. The layout of the existing church with the large, open nave space and additional space in the basement was well set up for conversion to community gathering spaces with minimal changes. Extending the life of the existing structure reduced construction costs and saved a historic, beautiful and familiar landmark in the community.
Significant project budget was allocated for two ramps to ensure both the main and basement levels are accessible to all visitors. The exterior ramps to both levels are integrated into the front façade as a feature that encourages them to be used by everyone, instead of being a peripheral element.
1. The owners had a clear desire to convert the decommissioned St Lawrence Church to a new, welcoming and accessible venue for the local community.
Site plan 1. Renovated building 2. Community garden
On the main floor, the community hall is a large open, brightly lit space with a stage at one end. Lighting and sound equipment are effectively placed for an ideal performance setting. It encourages community interaction as the perfect space for all types of gatherings and events hosted by Ross Creek or other groups who wish to rent the space.
In the basement, a multi-purpose room and kitchen bring people together around food. A community garden located in the rear yard, supports the commercial grade kitchen with healthy fresh produce. The soundproof recording studio allows for recording on the main or lower levels and is the only one of its kind in the community.
The design works within the constraints of the existing building to maximize passive design strategies. The building’s orientation with an elongated, high gable roof running east-west provided an advantage in many ways. The uninterrupted south roof allows for maximum solar gains. The new bank of south windows provides a great quality of light to the main gathering spaces. Both measures reduce loads on the mechanical and electrical systems.
Operable new triple-pane windows provide passive cross ventilation through the spaces. 100% of the occupied floor area is within 7 metres of an operable window for excellent daylighting. All LED light fixtures were used including for the stage lighting system.
A new electric HVAC system with cold climate heat pumps, and a high-efficiency ventilation system supplements the passive heating, cooling and ventilation strategies. The two levels can be controlled individually when occupied.
The conversion from oil to electric sets the building up for future reductions in fossil fuel consumption as the Nova Scotia power grid becomes cleaner. To reduce the building’s dependency on the power grid, 51 460W PV modules were installed on the roof, which offsets the building energy use by 50%. (Continue p 18).
2. The deep energy retrofit includes a heat pump heating and cooling system and natural cross- and stack ventilation.
3. The decommissioned St Lawrence Church before the renovation. Upgrades to the exterior envelope included economical Truefoam Type 2 EPS (TF200) to eliminate thermal bridging. One of the most environmentally-friendly rigid insulation products available, it is suited for below concrete floors and concrete walls.
4. Kentville, NS-based Skylit Energy Solutions installed 51 premium 415W solar modules with microinverters, using black-framed panels with all-black attachments to fit into the building’s new aesthetics. Premier Metals supplied the durable standing-seam metal roofing and cladding.
A deep energy retrofit approach to the exterior envelope reduced the energy consumption of the building significantly. There was previously minimal insulation in the exterior walls and no insulation in the roof. All exterior walls and the above grade foundation were wrapped in three inches of Type-2 EPS foamboard insulation and new airtight weather barrier. The existing exterior wood stud wall was filled with mineral insulation. Six inches of XPS low GWP foamboard insulation and a new airtight weather barrier were added to the roof.
Where possible existing interior finish materials were maintained or salvaged materials were used. Maple hardwood and marmoleum flooring were chosen for their durability and low carbon footprint. By retaining the foundation, floor, walls, and roof of the existing building, 26.9 tonnes of carbon emissions were avoided, equivalent to driving 192,000 km in a car, and 144 tonnes of material waste was diverted from the landfill.
Floor plans
1. Community hall
2. WC
3. Main vestibule
4. Multi-purpose room
5. Lower vestibule
6. Community kitchen
7. Recording studio
As a community building, the Annex is a public demonstration of how decommissioned churches can be renovated, repurposed and used as community hubs for generations to come. The distinct red shiplap wood exterior cladding distinguishes it as a new sustainable landmark in the Annapolis Valley.
BRONWYN COLFORD, INTERN ARCHITECT, IS WITH SOLTERRE DESIGN.
1. Community hall
2. Exterior ramp
3. Multi purpose room
4. Cross ventilation
5. Summer solstice
6. Winter solstice
7. Stack effect ventilation
8. Solar PV panels
ARCHITECT Solterre Design (David Gallaugher, Architect)
CONTRACTOR Cripple Creek Carpentry
ELECTRICAL ENGINEER Emtech Consulting Engineers Ltd.
MECHANICAL ENGINEER M. Lawrence Engineering Ltd.
STRUCTURAL ENGINEER Andrea Doncaster Engineering Ltd.
PHOTOS Chris O’Neill, Acorn Art & Photography
Findings from the first National Embodied Carbon Summit identify key gaps, solutions, and next steps
Embodied carbon is widely recognized as the next frontier in building decarbonization, but where to begin? CAGBC has released a new white paper, charting a path forward: Reducing Embodied Carbon in Canada’s Buildings. The report summarizes insights from the inaugural National Embodied Carbon Summit, held last year in Toronto.
Hosted by CAGBC, the event brought together over 60 professionals from across the building sector—including representatives from leading architectural firms, engineering companies, construction management firms, sustainability consultants, and building material industry associations, as well as governments, agencies, non-governmental organizations (NGOs), and academic institutions, among others—to identify key gaps and barriers, propose solutions, and mapping the next steps for reducing embodied carbon in Canada’s built environment.
Based on the collective brainstorming of participants, this white paper captures the top industry priorities and actionable next steps that will help drive alignment, innovation, and needed government and industry support to scale up low-carbon construction across the country. A national conversation whose time has come
While progress has been made in reducing operational emissions from buildings, embodied carbon has only gained significant attention in recent years and tackling it will require industry collaboration and cooperation.
Over the course of the Summit, participants identified hundreds of gaps and barriers, which were then consolidated and prioritized into the following key areas:
• Framework for whole building life cycle assessment (wbLCA)
• Tools and data
• Awareness, training, and education
• Embodied carbon requirements in codes and certifications
• Economic considerations and incentives
• Research, development, and commercialization
• Availability of verified low-carbon products
“The Summit was instrumental in distilling these key challenges and developing corresponding solutions for reducing embodied carbon,” said Mark Hutchinson, Senior VP of Green Building Programs & Innovation at CAGBC. “The white paper summarizes that work, develops a structure to guide future efforts, and provides the industry with a clear path to accelerate progress.”
You can download the report at cagbc.org/embodiedcarbon.
1. The Wellington entrance and restaurant space. The stone-clad podium level with a wood entrance wall, and glazing pattern above, are aesthetic departures from the standard box that often characterizes low-cost development.
By Stephen Kopp
Located at the historic intersection of Union & Wellington streets in the heart of Saint John, The Wellington is a 6-storey mixed-use development, with ground floor commercial space and 5 upper floors containing a total of 47 affordable and market rate apartment units.
On a tight urban site, the building massing steps back in three volumes to reveal the neighbouring landmark Loyalist House, views of historic church towers on Germain Street, and the leafy maples of Queen Square in the distance. A quarried stone-clad podium level with a wood entrance wall, together with the striking glazing pattern above are aesthetic departures from the standard box that often characterizes low-cost development.
In the city of Saint John 22.5% of people live in poverty. There are many barriers to people breaking the cycle of poverty, at the heart of which is access to affordable housing. Affordable housing projects often look low-cost, resulting in residents being further ostracized by their communities. These realities reinforce acre Architects’ conviction that modern housing should encompass sustainability, affordability and accessibility, and at the same time counter the stereotype that affordability and good design are mutually exclusive.
Designed to international Passive House standards, The Wellington is the first (soon to be) PH certified affordable housing project completed in Atlantic Canada. The building employs the main tenets of Passive House design, and while not unique in its approach, the building exceeded performance expectations during its multiple testing periods. As such, it has set an important precedent for the Maritimes.
In keeping with Passive House standards, Acre Architects created an envelope with a balance of airtight design, high insulation value, and carefully considered window details. Beyond the base wall assembly, which achieves a min. R-value of 55 for the roof and 37 for the walls, coordination with mechanical and electrical consultants was critical to minimize penetrations through the building envelope.
Internally, the heating and cooling system for the Wellington employs a highly efficient variable refrigerant flow (VRF) design that is able to deliver simultaneous heating and cooling year round. Each suite is equipped with a wall mounted evaporator unit that is integrated into the central VRF system. The system is able to meet the heating targets even on the coldest days of the year. On exceptionally cold days, the building is equipped with electric baseboard heaters that supplement the heating load if required.
Saint John is known for its historic masonry structures. When developing the exterior expression of The Wellington, Acre was inspired by the layered façade articulations of these rich, textured vernacular examples in their creation of a new, modern look and feel. 2
The aesthetic objective was an emphatic departure from the typical affordable housing model of stacked and flat window facades. Instead, a staggered window pattern was designed within the confines of a typical built-up header system; paired with a simple yet playful exterior extrusion. This disguises the fact that the exterior walls are load bearing (one of the hallmarks of six-storey wood construction). The lively pattern of gold-coloured window frames against a background of black corrugated metal panels changes in intensity as one approaches the building.
One of the key components of Passive House design is to eliminate thermal bridging at the window frames. In multiunit buildings window frames can become a particular area of concern. Accordingly, Acre set out to source high-performing windows and frames, with the additional ambition of finding a thin, low-profile frame; in contrast to the often ‘chunky’ units used in sustainable building projects. Following a lengthy research period, fibreglass windows were specified as they met the selection criteria and were also available in the larger sizes the design required.
Around the building, there is no difference in window sizes. Different calculations for solar heat gain were completed during design development but there was negligible difference in overall energy consumption, in large part due to the high performing windows (in concert with the wall assemblies). However, higher performance emissivity coatings were used on the south and west facades.
An important benefit of Passive House buildings is that the considerable savings on energy costs can translate into lower rents than a standard code-compliant building would allow. Aligning with the affordability ambitions of The Wellington, the heating and ventilation systems described above were designed with this in mind.
3 1/2" semi-rigid mineral wool insulation board (r15), staggered joints
Sheathing complete with integrated air and water-resistive barrier. tape all seams, typ.
2x6 wood studs @ 16" o/c
5/8" gypsum wall board, painted
Mineral wool batt insulation (r22 )
Solid wood baseboard, typ.
Provide 1/8" gap for acoustic seperation, typ.
Finish flooring material
2 layers 5/8" osb floor sheathing, staggered joints
1 1/2" sound dampening panel system
Rigid xps insulation
Vertical corrugated metal siding, black, on plywood strapping @ 16" o/c c/w stainless steel fasteners
Pre-finished metal trim to match metal siding, typ.
Self-adhered vapour permeable and air membrane
3/4" t&g csp plywood sheathing
2x8 nail-laminated timber, exposed to underside
Gypsum wall board end bead, typ.
Acoustic membrane @ top and bottom plates, typ.
Accessible residential design was an integral part of the project mandate from the beginning, in recognition of our aging population. All the residential units in The Wellington were designed to Universal Design standards (with two being entirely barrier free). It was important for this project to accommodate ageing-in-place to actively make the statement that fully inclusive design can be enjoyed by everyone safely, with ease, and with dignity.
3. Each suite is equipped with a wall mounted evaporator unit that is integrated into the central variable refrigerant flow (VRF) system, all supplied by Mitsubishi Electric Sales Canada Inc., to deliver simultaneous heating and cooling year round.
PROJECT CREDITS
OWNER/DEVELOPER Saint John Non-Profit Housing Inc.
ARCHITECT Acre Architects
GENERAL CONTRACTOR John Flood & Sons Construction
COMMISSIONING (PHIUS VERIFICATION) RDH Building Science
ENERGY MODELLING ZON Engineering
LANDSCAPE ARCHITECT Brackish Landscape Studio
CIVIL ENGINEER Fundy Engineering & Consulting
ELECTRICAL/ MECHANICAL ENGINEER Fundy Engineering & Consulting
STRUCTURAL ENGINEER Blackwell Structural Engineers
FIRE PROTECTION RJ Bartlett Engineering Ltd.
PASSIVE HOUSE CONSULTANT Zon Engineering
PHOTOS Julien Parkinson
PROJECT PERFORMANCE
ENERGY INTENSITY REDUCTION RELATIVE TO REFERENCE BUILDING (DESIGN CALCULATION UNDER 2015 NECB) = 57% *
ENERGY INTENSITY (HEATING AND COOLING) = 10.1 KWhr/m2/year ENERGY INTENSITY (HEATING) = 6.8 KWh/m2/year
INTENSITY (COOLING) = 3.2 KWh/m2/year
Supplied and installed the Aluminum Composite Panel System for the Mackintosh Depot (left) and the Metal Cladding System for the Passive House Wellington Building (right). paneltech.ca
Floor plans
1. Vestibule
2. Commercial Rental Unit
3. Parcel Room
4. Lounge
5. Vestibule
6. Corridor
7. Vestibule
8. Garbage/Recycling
9. Elevator
10. Lobby
11. Vestibule
12. Washroom
13. Storage
14. Community Room
15. Commercial Rental Unit
16. One bedroom Unit
17. Two bedroom Unit
18. Accessible Unit
19 . Corridor
20. Laundry
21. Elevator
The intentional mix of 24 market rate units and 23 affordable units is designed to encourage a diverse tenant demographic; further bolstered by the participation of the L'Arche Connects program and the project’s dedicated accessible units.
L’Arche is a supported independent-living model for adults with intellectual disabilities and The Wellington provides an infrastructure that helps foster independence for its tenants regardless of their varied needs.
Passive House projects consume up to 90% less heating and cooling energy when compared to conventional buildings. How does the ability to heat a unit with the energy equivalent to powering a single lightbulb translate into helping break the poverty cycle?
The social and economic benefits are leveraged on the premise that high energy savings through strict building design criteria can greatly reduce the cost of living. This is at the core of The Wellington’s success in meeting the sustainability, accessibility, and inclusivity objectives established at the outset of the project.
Stephen Kopp is Co-founder and Principal of Acre
Visit our on-line Directory to see hundreds of listings of companies which supply products and services for sustainable, high-performance building. Listings are organized by Product Category and by LEED Category. Our Directory is created with the help of our partner:
SITE | LANDSCAPING |
RAINWATER HARVESTING
ACO Systems
Filterra Bioretention Systems/Langley Concrete Group
Make Way Environmental Technologies
Molok North America Ltd.
Roth North America
Wishbone Site Furnishings
STRUCTURE & EXTERIOR ENVELOPE
Airfoam Industries
Arriscraft
Canada Brick
CAYAKI Charred Wood/ CFP Woods
CBC Specialty Metals and Processing
Corbec
Engineered Assemblies
475.Supply
International Timberframes
Live Roof Ontario
MAPEI Canada
Radon Environmental
Sapphire Balconies Ltd.
Siga
Thames Valley Brick & Tile
Unitiwall
THERMAL, WINDOWS & DYNAMIC GLASS
Cascadia Windows & Doors
Duxton Windows & Doors
Inline Fiberglass Ltd.
Innotech Windows + Doors
JELD-WEN Windows & Doors
KALWALL
Kohltech Windows & Entrance Systems
Our 2025 Partners
NZP Fenestration passivhaus windows and doors
Silex Fiberglass Windows and Doors
Unicel Architectural Corp.
VETTA Windows & Doors
COATINGS AND INTERIOR FINISH PRODUCTS
Dulux/PPG
Eco Building Resource
Forbo Flooring Systems
MAPEI Canada
Rockfon
ELECTRICAL | PLUMBING | HVAC | RENEWABLES
AquaTech Sales and Marketing Inc.
Daikin Applied
Fantech Canada Ltd
Mitsubishi Electric Sales Canada Inc.
Sharc Energy
Sloan Valve/Dobbins Sales
Tempeff Inc.
Teritt Indoor Environmental
TRANE
GREEN DESIGN SUPPORT + PROFESSIONALS
Alberta Ecotrust
Canada Green Building Council
Canadian Precast Concrete Quality Assurance
Certification Program
Evolve Builders Group
FABRIQ architecture
Green Building Initiative
Pretium Engineering
Save EnergyNB