BRITISH COLUMBIA
Canada Green Building Council
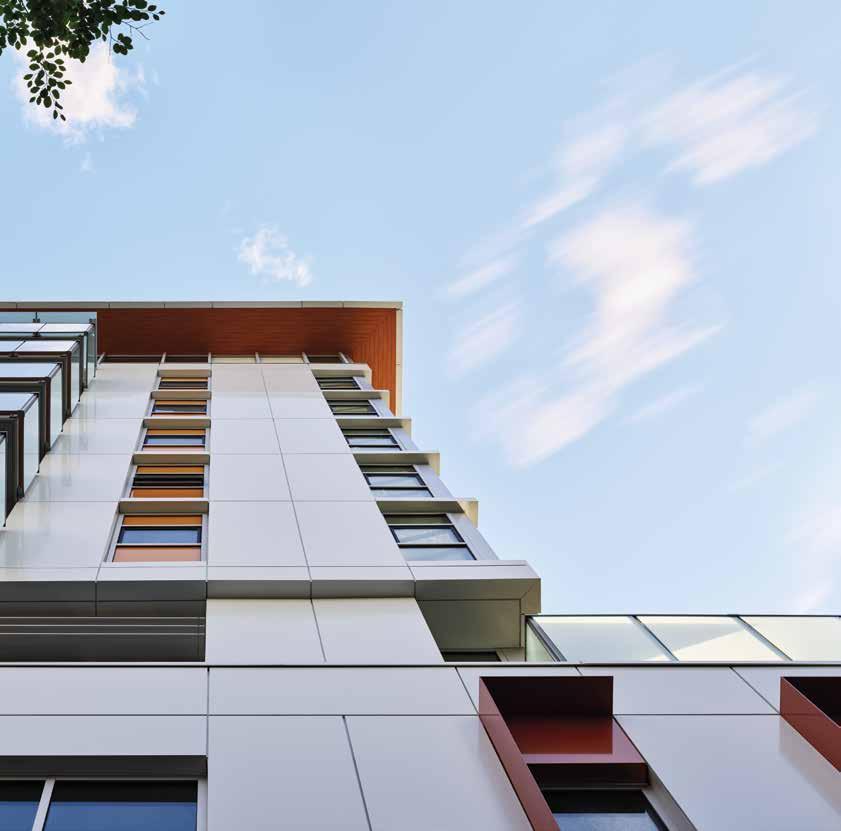
Canada Green Building Council
Building of best environmental practices supports youth
T5M CONNECT Missing middle housing takes envelope-first approach
ZCB-DESIGN STANDARD A guide to ambitious market transformation
THE WINNING TEAMS 2024 SABMag Canadian Green Building Awards
Like biogas captured from cow manure to create Renewable Natural Gas1 (RNG). It’s a low-carbon2 energy that can be used in homes and businesses across the province—and we’re adding more to our supply every year.
Our gas system can provide RNG to buildings and developments to reduce greenhouse gas emissions. This means buildings can meet strict emissions guidelines without expensive upgrades or retrofits.
Find out more about RNG at fortisbc.com/rngbuild. 1Renewable Natural Gas (also called RNG or biomethane) is produced in a different manner than conventional natural gas. It
organic waste from landfills, agricultural waste and wastewater from treatment facilities. The biogas
gas system, it mixes with conventional natural gas. This means we’re unable to direct RNG to a
gas is needed, thereby reducing the use of fossil fuels and overall greenhouse gas emissions. 2When
emission factor of FortisBC’s current Renewable Natural Gas (also called RNG or biomethane) portfolio
FortisBC’s
Hydrogen Strategy.
FortisBC uses the FortisBC name and logo under license from Fortis Inc. (24-114.6 05/2024) Connect with us @fortisbc
SITE | LANDSCAPING | RAINWATER HARVESTING
ACO Systems
Visit our on-line Directory to see hundreds of listings of companies which supply products and services for sustainable, high-performance building. Listings are organized by Product Category and by LEED Category. Our LEED v4.1 Directory is created with the help of our partner:
Filterra Bioretention Systems/Langley Concrete Group
Molok North America Ltd.
Roth North America
Wishbone Site Furnishings
STRUCTURE & EXTERIOR ENVELOPE
Airfoam Industries
Arriscraft
Canada Brick
CAYAKI Charred Wood/ CFP Woods
CBC Specialty Metals and Processing
Engineered Assemblies
Fraser Wood Siding
475.Supply
International Timberframes
Live Roof Ontario
LP SmartSide
MAPEI Canada
N.A.T.S. Nursery Ltd.
Radon Environmental
Sapphire Balconies Ltd.
Siga
Thames Valley Brick & Tile
Tremco CPG Inc.
THERMAL, WINDOWS & DYNAMIC GLASS
Cascadia Windows & Doors
Duxton Windows & Doors
Inline Fiberglass Ltd.
Innotech Windows + Doors
JELD-WEN Windows & Doors
KALWALL
Kohltech Windows & Entrance Systems
NZP Fenestration passivhaus windows and doors
Unicel Architectural Corp.
VETTA Windows & Doors
COATINGS AND INTERIOR
Century Wood Products Inc.
Dulux/PPG
Eco Building Resource
Forbo Flooring Systems
ELECTRICAL | PLUMBING | HVAC | RENEWABLES
Aqua-Tech Sales and Marketing Inc.
Big Ass Fans
Daikin Applied
Ecopilot Real-Time Energy Management System
Fantech Canada Ltd
Mitsubishi Electric Sales Canada Inc.
RadiantLink In-wall Heating
Sharc Energy
Sloan Valve
Tempeff Inc.
Teritt Indoor Environmental
TRANE
Viessmann Manufacturing Company Inc.
GREEN DESIGN SUPPORT + PROFESSIONALS
Canada Green Building Council
Canadian Precast Concrete Quality Assurance
Certification Program
Efficiency Nova Scotia
Entuitive
FABRIQ architecture
Green Building Initiative
Save EnergyNB
I am pleased to welcome you to the latest issue of FOCUS BC, part of a series of regional publications from CAGBC and Sustainable Architecture & Building Magazine.
This issue comes to you on the heels of Building Lasting Change, our annual national conference, an appearance at the Retrofit Canada Conference, and a trip to London, England to participate in the World Green Building Council’s Leadership Summit. Each of these events demonstrates for me that transforming buildings at scale is a massive effort which requires all players to make connections and learn to work collaboratively.
CAGBC is playing its part by ensuring that Canada’s building sector has the tools and training needed to implement green building solutions for their projects and portfolios, including the launch of the latest Zero Carbon Building – Design Standard at BLC. We’re also working with policymakers and industry representatives, green building councils and other organizations from across the globe to discuss practical next steps in leveraging buildings to address climate change and promote resilience.
A great example of this needed collaboration is CAGBC’s Low Carbon Training initiative, which wrapped earlier this year. The program forged unprecedented national connections with partnerships between CAGBC, Real Estate Property Association of Canada (REALPAC), the Royal Architectural Institute of Canada (RAIC), the Climate Risk Institute, the Canadian Construction Association, and Building Owners and Managers Association Canada (BOMA Canada). Together we delivered low-carbon training to thousands of professionals from a broad range of backgrounds and set the stage for greater collaboration on capacity building and workforce development.
Attending events like BLC, the Retrofit Conference, and global events like the Leadership Summit shows how our collective efforts have tangible impacts as we strive to address climate, energy, affordability, and resilience. And CAGBC is the hardworking partner Canada’s building sector needs to advance on all fronts through our standards, certifications, training, research, and advocacy efforts.
I hope you’ll enjoy this new issue. In it, you’ll hear more about our latest ZCB-Design standard, and some of the exciting take aways from the Building Lasting Change Conference, which returns to Vancouver in 2025. I hope to see you there.
Sincerely,
Thomas Mueller President & CEO, Canada Green Building Council
The Building Lasting Change (BLC) conference rallied Canada’s green building leaders, demonstrating momentum and commitment for low-carbon and resilient green buildings.
“Building Lasting Change is where the green building sector comes together once a year to advance sustainability actions,” said CAGBC President and CEO Thomas Mueller. “This year, the conference offered a platform to announce the innovative solutions, new projects, and commitments of our partners and collaborators that we need to make Canada’s decarbonization goals a reality.”
In addition to the announcement of the winners of the CAGBC Awards, several important announcements from CAGBC, members, partners and government bodies were made during the conference. Here is a brief recap:
Minister Anand shares details of the federal government’s greening strategy
The Honourable Anita Anand, President of the Treasury Board of Canada participated in the BLC opening keynote, announcing updates to the federal government’s work to green its operations. The updates she shared including requiring Crown corporations to align their operations with the Greening Government Strategy, strengthening commitments to decarbonize real property, fleet and procurement, and accelerating climate resilience commitments to address the increasing impacts of climate change on critical federal assets, operations and activities by 2035.
CAGBC introduced the latest version of its Zero Carbon Building –Design Standard™ (ZCB-Design). The updated version takes advantage of new technologies and processes to accelerate carbon emissions reductions, focusing on embodied carbon, resiliency, good grid citizenship, refrigerants, and Zero Carbon transition plans.
Efficiency Capital secures $50 million investment from Canada Infrastructure Bank
MP Julie Dabrusin was at BLC to introduce CIB's panel discussion.
Efficiency Capital, one of Canada’s first Energy-as-a-Service (EaaS) companies, secured $50M investment from the Canada Infrastructure Bank (CIB). The financing partnership will help support small and medium-sized businesses across Canada decarbonize their buildings. MP Julie Dabrusin, Parliamentary Secretary to the Minister of Environment and Climate Change and to the Minister of Energy and Natural Resources was on hand for the announcement.
Michael Brooks, CEO of the Real Property Association of Canada (REALPAC) shared a new report at BLC. The Sustainability Industry Report captures the state of the commercial real estate market is rising to the challenge presented by changes brought on by climate, government and regulatory changes. This is REALPAC’s second report of the Canadian Commercial Real Estate industry’s sustainability performance. It recognizes progress, provides useful benchmarks, and identifies opportunities and challenges for the industry.
The Climate Smart Buildings Alliance (CSBA), a joint project between EllisDon, RBC, and Mattamy Homes formally announced the Responsible Buildings Pact, a new cross-industry agreement aimed at increasing the use of low-carbon materials in the built environment. The announcement marked the first 21 signatories committing to support the first year of the collective industry effort.
The Industry Innovation + Transformation Council (I+T Council), convened by R-LABS, announced a continued expansion of pledges to drive innovation and transformation. Building on the recently unveiled 2024 Industry Innovation Agenda (IIA), Canadian real estate leaders and entrepreneurs are strengthening their commitment to tackle pressing challenges in the sector.
CAGBC announced its upcoming project ‘Transition Planning: A Tool for Accelerating High Performance Building Codes’. This project will help facilitate the transition to net-zero emissions for new and existing buildings by supporting building owners across Canada in developing customized transition plans. Supported by REALPAC, the project will include development of a Transition Plan Guide, a Transition Plan Playbook and workshops to help owners through their projects.
Purpose Building Inc., with support from CAGBC announced the development of ‘The Purpose Accelerator: Canada’s Private Sector Retrofit Accelerator’, a new initiative to advance net-zero emissions goals. The project will guide building owners and managers through their deep retrofit journey, providing crucial services and support for pre-development, development, and implementation of decarbonization project phases. Targeted buildings include commercial (e.g., office, warehouse/distribution, retail), and mid- or high-rise multiunit residential buildings, and support for low-income and Indigenous communities.
CAGBC announced a forthcoming white paper, planned for release in early fall, which starts the conversation on a national vision of reducing embodied carbon in the built environment. This white paper will be a summarization of the ideas shared at the National Embodied Carbon Summit. The summit had cross-industry representation, taking embodied carbon conversations national with the goal of developing a common vision for 2030, establish the next steps needed to get there, and outline how together we can align and enable this conversation to continue and expand.
By Larry Adams and Kenneth Wong
Covenant House Vancouver (CHV) is the main provider of residential and outreach services for homeless youth and at-risk youth aged 16-24 in Vancouver. This project is the second phase of three buildings in an ambitious expansion of housing and supports.
CHV Phase 2 replaces the existing two-storey CHV shelter and houses the Crisis Program which provides shelter and support services for 75 youth. Staff and volunteers provide male, female, and transgendered youth with the help that they need to move away from life on the streets or from an untenable home environment.
When first entering the program, youth have basic needs met: a safe place to sleep, nutritious food, warm clothing, and access to showers. Once settled, they can connect to different support programs that improve their physical and mental health on a path towards independence.
Support spaces (main to fourth floor) include classrooms, a library/computer room, an art therapy room, lounges, a gym, and a fitness room. Meeting spaces are located throughout the building. The commercial kitchen, dining room, and patio are located on the fourth floor. The shelter component (fifth to ninth floors) consists of sleeping rooms, a lounge, meeting rooms and staff operations room. The tenth floor contains administrative workspaces where the staff can meet with visitors and supporters. Provision of a variety of spaces allows individuals to choose between social contact or privacy.
1. Located in downtown Vancouver at the intersection of Seymour and Drake Streets, an area of residential towers, street-level commercial and landscaped public realm, Covenant House Phase 2 is seen at left and the 2019 Covenant House Phase 1 is at right.
We strove for a simple and practical design and sustainability measures to facilitate a cost effective, low maintenance, efficient building. The project has achieved LEED Gold (LEED Canada NC 2009). Sustainable design strategies include:
• Optimizing exterior wall assemblies / low window-to-wall ratio
• High degree of daylighting throughout the building
• Energy recovery ventilation
• Reducing lighting power density
• Reducing domestic water usage
The building program and design came about through information gathering sessions with youth and staff. The design of the building was intended to be welcoming and recognizable to street youth while also establishing a relationship to the Phase 1 building immediately across the street.
The previous CHV building on the site was built to the property lines, resulting in narrow sidewalks and minimal space for landscaping. The new building setbacks on the south and west reflect the Downtown South Design Guidelines and allow space for mature landscaping.
Although the small 836 sq.m site and building footprint limited site planning opportunities, we were able to deconstruct and recycle the existing building, plant 180 sq.m of shrubs and groundcover, and incorporate an 82 sq.m vegetated roof on the upper roof.
An on-site water cistern regulates discharge of stormwater into the municipal system. The use of low-flow sinks, showers and toilets, provision of controllers/timers for the irrigation system, and the selection of drought-tolerant plants has allowed a 40% reduction in potable water demand.
Occupied spaces are placed at the west, south and east sides of the building and receive a significant amount of natural light. Corridors and elevator lobbies have operable windows, and all shelter suites are mechanically vented with a ventilation rate of 7.5 L/s per occupant. Occupancy and daylight sensors used throughout (excluding youth sleeping rooms) have reduced lighting energy by 36% as compared to NECB 2015.
The layout of rooms provides views into adjacent spaces and to the exterior to minimize resident anxiousness from enclosure. Operable windows allow for individual choice and control, while natural wood on ceilings and walls provide a warm character to spaces.
The provision of meals to youth in the Crisis and Drop-In Programs is a critical component of the work of CHV. Cost benefit analysis coupled with availability of equipment during COVID, led to the decision to use natural gas appliances in the commercial kitchen.
Meeting
Reception
Lobby
18. Bicycle/ Board
Office
20. Storage
Mechanical 22. Staff bicycle 23. Substation
Program vehicle
Selection of other mechanical equipment was made to offset the effects of the natural gas kitchen equipment as much as possible. Modelled energy cost savings of 28% result from energy reduction features such as:
• High efficiency VRF heat recovery heat pump system for heating and cooling
• 75% sensible high efficiency Heat Recovery Ventilators
• Demand controlled ventilation for commercial kitchen exhaust to reduce natural gas and electricity use
• Demand controlled ventilation for outdoor air supply to Levels 5 to 9 to reduce overall energy use
• Domestic hot water heat pumps capable of operating at below 0°C temperatures provided a significant reduction in natural gas use for domestic water heating allowing the project to achieve a GHGI intensity of 10.1 kgCO2e/m2 when modeled as per ASHRAE 90.1-2007 Appendix G
• Enhanced commissioning
Durable, maintainable building components were selected for a 60-year service life under a Building Durability Plan informed by CSA Standard S4788-95. Education and information sharing underpin the design and operation of Covenant House. The building has been visited by numerous local, national, and international organizations to understand the value of the project in supporting youth as well as providing a template for energy and environment strategies that can be incorporated into buildings that have strong social goals.
LARRY ADAMS AND KENNETH WONG ARE WITH NSDA ARCHITECTS.
4. The tenth floor contains office and meeting spaces for staff and visitors. Staff can choose from several types of workspaces and can control windows and blinds to suit their preference.
5. The fourth-floor commercial kitchen and dining space for youth and staff. The dining area opens to a landscaped patio for additional seating, group activities, and urban agriculture.
PROJECT
CLIENT Covenant House Vancouver Phase 2
ARCHITECT NSDA Architects
DEVELOPMENT CONSULTANT CitySpaces Consulting Ltd.
STRUCTURAL ENGINEER Fast + Epp
MECHANICAL AND ELECTRICAL ENGINEER Integral Group (Currently Introba)
CIVIL ENGINEER R.F. Binnie and Associates
COMMISSIONING AGENT CES Engineering Ltd.
SUSTAINABILITY CONSULTANT Blue Camas Consulting Ltd.
BUILDING ENVELOPE CONSULTANT EXP Services Inc.
GENERAL CONTRACTOR VanMar Constructors
INTERIOR DESIGN Aliki Gladwin and Associates
LANDSCAPE ARCHITECT DKL
PHOTOS Andrew Latreille Photography
PROJECT STATISTICS
• SITE AREA 836 m2
• BUILDING GROSS FLOOR AREA 4,220 m2
• ENERGY INTENSITY 224.6 KWhr/m2/year
• REDUCTION IN ENERGY INTENSITY 28 %
• RECYCLED MATERIALS CONTENT 22.29 % by value
• CONSTRUCTION MATERIALS DIVERTED FROM LANDFILL 76.10 %
• WATER CONSUMPTION FROM MUNICIPAL SOURCE 14,828 litres/ occupant/year [Include both base building and process consumption]
• REDUCTION IN WATER CONSUMPTION 43.13 %
Innotech Windows + Doors is a Canadian manufacturer of high-performance windows and doors. The Defender 88PH+ System combines decades of fenestration knowledge to deliver a robust window and door system that is not only Passive House Institute certi ed, but that also delivers the air, water and structural performance required for highly sustainable housing developments.
By Oscar Flechas
The T5M Connect North Glenora project is an innovative building that creates new, environmentally sustainable housing, which is community-oriented and well-integrated into an established neighbourhood of Edmonton.
Creating missing middle housing in a core neighbourhood was a fundamental goal for this project. Through innovative design and thoughtful planning, the project was able to fit the scale of the community while significantly increasing the number of homes on the site. Two single-family home lots were transformed into16 homes providing housing for 36 people.
Community engagement design guide considerations helped to integrate the building into the neighbourhood by ensuring that the building height and setbacks were similar to adjacent structures while also providing a transition to upcoming 4-storey buildings nearby. The rear unit of the building was also lowered in response to the neighbour’s concerns about sunlight for a garden.
The building includes 1-bedroom suites, 2-bedroom flats, 2- bedroom townhomes, 3-bedroom townhomes, and two units that are fully wheelchair accessible and barrier- free. This mix of unit-types was intentionally included in the design to enable a wide variety of people to live there.
In designing this building, a sense of community was important both within the building and with the neighbourhood. The courtyard design and corner-lot orientation ensured that all units are entered from the street, from the courtyard, or from the side pathway rather than from an internal hallway, thus connecting residents to the community at large and to other community members.
1. Roof assembly
- 60mil EPDM
- Overlay board
- R69 Fastened rigid insulation sloped to drain
- Vapour retarder with seal tape
- Sheathing
- Wood truss@19.2” (487mm) o.c.
- One layer gypsum board, taped, filled, sanded, primed, painted
2. Exterior wall
- Cementitious/metal siding/ EIFS system
- 5/8” Strapping or drainage cavity
- Water resistive air barrier membrane
- 14” SIC wall panel w/EPS Type I insulation
- Steel stud 362S162-43@ 16” o.c.
- Fully taped and sealed at junctions
- 6 mil Poly
- 5/8” 45 min - 1 layer 5/8” Type X gypsum board, taped and filled or 1” one HR - 2 layer 1/2” Type X gypsum board, taped and filled
3. Exterior wall
- 4 3/4” EIFS system with drainage board and non-combustible cladding performance
- 2 3/4” ICF - EPS Type 2 insulation
- 8” Reinforced concrete ICF
- 2 3/4” EPS type 2 insulation
- 1/2” one layer Type X gypsum board
4. Exterior wall
- Dimpled membrane
- Waterproofing membrane
- 4 3/4” EPS Type 2 insulation
- 2 3/4” ICF - EPS Type 2 insulation
- 8” Reinforced concrete
- 2 3/4” ICF - EPS Type 2 insulation
- 1/2” One layer Type X gypsum board
5. Floor assemblies
- Floor finish
- 4” Concrete slab
- 15 mil moisture barrier wrap fully taped and sealed at penetrations
- 9” EPS type 2 insulation
- Granular fill
With an envelope-first approach, the building uses super-insulation, airtightness, high quality windows and doors, and efficient mechanical systems to reach Passive House certification, a first for a multifamily building in Alberta. Air source heat pumps and a solar PV system help reduce carbon impacts by 80% compared to a standard building.
The building houses people from all stages of life including students, single professionals, young couples, families, and empty nesters, and the barrier-free units provide much-needed housing for wheelchair users.
As Edmonton prepares to welcome a million more residents, we need housing that makes full use of existing infrastructure and brings a diverse range of people into existing neighbourhoods while respecting the needs and priorities of people already living there.
With T5M Connect North Glenora project we wanted to demonstrate how economic and cultural innovation and collaboration can create housing that is welcoming, environmentally sustainable, and supportive of the social connections among residents and the larger community of our city.
OSCAR FLECHAS, AAA, AIBC, LEED AP IS PRINCIPAL AT FLECHAS ARCHITECTURE.
3. Energy efficiency, through super-insulation, airtightness, high quality windows and doors, and efficient mechanical systems to achieve Passive House certification, is further improved with air source heat pumps and a PV system.
4. The courtyard design and corner-lot orientation ensure that all units can be entered from the street, from the courtyard, or from the side pathway, thus connecting residents to the community at large.
5. and 6. Two units are fully wheelchair accessible and barrier-free. The mix of unit types was intentionally included in the design to accommodate a wide variety of people.
PROJECT TEAM
CLIENT TM5 Connect
ARCHITECT Flechas Architecture
STRUCTURAL ENGINEER Prostatix Engineering
MECHANICAL AND ELECTRICAL ENGINEER Renu Engineering
CIVIL ENGINEER Whitenect Engineering
BUILDING ENVELOPE CONSULTANT Wade Consulting
GENERAL CONTRACTOR HomeStretch Development Corporation
PHOTOS Modern VF Tours
On June 5, the Canada Green Building Council® (CAGBC) introduced the latest version of its Zero Carbon Building – Design Standard™ (ZCB-Design), updated to reflect evolving market needs and take advantage of new technologies and processes to accelerate the reduction of carbon emissions.
Like versions before it, the new ZCB-Design v4 prioritizes reductions in operational carbon emissions and embodied carbon, in addition to energy-efficient designs that promote good grid citizenship.
“The Standard goes further than ever before, evolving in lockstep with the market,” said Mark Hutchinson, Vice President of Green Building Programs and Innovation. “Informed by hundreds of zero carbon building projects and the input of our Technical Advisory Committees, this new version of the Zero Carbon Building – Design Standard is raising the bar for requirements on embodied carbon and electrification, reflecting the direction of the Canadian real estate sector. Yet, we’ve retained the flexibility of multiple pathways to zero to ensure every project can begin their decarbonization journey today.”
ZCB-Design Standard v4 addresses the building sector’s increasing need to achieve zero carbon buildings and deep carbon retrofits that can minimize emerging risks related to carbon and safeguard the value of building assets.
“The expectations of investors, tenants and policymakers are changing,” said Thomas Mueller, CAGBC’s President and CEO. “As real estate companies adopt ESG commitments and all levels of government implement climate policies, companies are increasingly required to follow and disclose their carbon emissions. With international carbon accounting and disclosure requirements bearing down on Canada, decarbonizing assets and whole portfolios is becoming a critical business priority. CAGBC is working with the Canadian real estate sector and governments to ensure efforts are aligned to drive toward tangible outcomes.”
The ZCB-Design Standard continues the trend of introducing greater rigour while ensuring flexibility to support the achievement of zero carbon across all buildings and regions.
The updated version takes advantage of new technologies and processes to accelerate carbon emissions reductions, focusing on embodied carbon, resiliency, good grid citizenship, refrigerants, and Zero Carbon transition plans.
With increased access to low-carbon materials, project data, and low-carbon training, ZCB-Design v4 sets more stringent requirements for embodied carbon. Pathways to reducing embodied carbon include improvement against a baseline or meeting an embodied carbon intensity threshold. Given the increase in warehouses and distribution centres pursuing ZCB certification, the new standard also differentiates their unique requirements.
Over 78 percent of Canadian building emissions emanate from fossil fuel combustion for space heating and service hot water. ZCB-Design v4 continues the last version’s focus on eliminating combustion with new limits for space heating and the introduction of limits for service hot water production. Maintaining the Standard’s focus of getting more buildings to zero, faster, the Standard provides flexibility for multi-unit residential buildings, long-term care facilities, and other building types with high hot water demand.
ZCB-Design v4 includes detailed guidance for evaluating future design conditions and assessing the risks of overheating and wildfire smoke.
Good grid citizenship:
As more buildings electrify to avoid carbon emissions, it is important that designs consider the impact of buildings on electrical grids in terms of load and peaking. ZCB-Design v4 introduces four good grid citizenship strategies under the Impact & Innovation requirement.
With the decarbonization of building operations, more attention must be paid to fugitive emissions from refrigerants, which can be a significant source of greenhouse gases. ZCB-Design v4 expands the range of mechanical equipment that must be included and introduces caps for the global warming potential of refrigerants.
Over 75 percent of ZCB-Design certified buildings are fully electric. However, for those buildings that still rely on onsite combustion for some space heating or service hot water, ZCB-Design v4 provides additional guidance and new requirements including the evaluation and pricing of an alternative design approach that does not use onsite combustion. The Standard also includes guidance for buildings connected to district energy systems.
Zero carbon momentum builds:
To meet climate goals and to retain building value, every new building must be zerocarbon. CAGBC’s ZCB Standards help developers, investors, and owners advance their transition to zero. By balancing rigour with flexibility and increasing the requirements as the sector builds low-carbon expertise, CAGBC is helping advance the decarbonization of Canada’s buildings.
By Rory Fulber
411 Railway sits at the heart of Vancouver’s historic Railtown, an area that is experiencing an ongoing transformation in response to new demands. The project embodies the essence of this evolution, embracing the shift from traditional industry to creative manufacturing.
The project sets a precedent for Railtown’s recently defined City of Vancouver Historic Industrial Zoning, which introduced the creative products manufacturing use. Light industry has historically been forced to look outside the city for workspaces, often in older buildings with limited amenities. The new zoning addresses the desire for inner-city, modernized, and health-forward workspaces, with 411 Railway as its champion.
The office of mcfarlane biggar architects + designers was commissioned by Niels, Bendtsen, a Danish-Canadian furniture designer and manufacturer, to design a sixstorey, 112,000 sq.ft. building that houses a curated a mix of highly successful Vancouver-based businesses including Bensen, Inform Projects, Aritzia, bulthaup, Above 90 Lighting, Cesar Vancouver, Form3, A-OK Café by Aritzia, and ALL Studio which offers Pilates classes.
The form of the building responds to its context through a shift in massing that acknowledges its historic neighbour to the west, while anticipating future-density to the east. Two volumes embrace a central atrium that is fully glazed on the north and south, visually connecting the user’s activities with the street, and framing dynamic views of the city, rail lines, and port. Two generous exit stairs flank the south end of the atrium, offering light-filled spaces that invite regular use while animating the streetscape.
1. Entrance Vestibule
2. Suite 1 (Showroom)
3. Suite 2 (Showroom)
4. Suite 3 (Creative Products Manufacturing)
5. Ground-Floor Terrace
6. Suite 4 (Movement Studio)
7. Suite 5 (Cafe)
8. Suite 6 (Office Space)
9. Sub-electrical Room
10. Sub-communication Room
11. Universal Washroom
1. Suite 1 (Creative Products Manufacturing) 2. Suite 2 (Creative Products Manufacturing)
Douglas fir glue-laminated timber bridges span between the walls of the atrium connecting the two cores and providing egress between the two exit stairs. The heft of the bridges expresses the structural capacity of the GLT and the charredundancy to achieve a 2-hour fire-rating. Chases in the underside of the bridges conceal mechanical and electrical infrastructure. The orientation of the bridges shifts on each floor, creating a geometric foil to the strict grid of the concrete walls.
The project exhibits a raw sophistication through the reinterpretation and refinement of incumbent industrial materials and techniques. Post-tensioned concrete slabs maximize ceiling heights with long spans and no drop beams. Concrete is celebrated through careful coordination of formwork and its residual marks. Unitized curtainwall is leveraged for its speed of installation and precise manufacturing. Local timber provides a regional sensibility that adds warmth.
2. The project sets a precedent for Railtown’s recently defined City of Vancouver Historic Industrial Zoning which addresses the desire for inner-city, modernized, and health-forward workspaces, with 411 Railway as its champion.
3. Post-tensioned concrete slabs maximize ceiling heights with long spans and no drop beams.
• 411 Railway is a driver for economic and social sustainability. The site is intensified by a rich mix of tenancies and industrial workspace that bolster Railtown’s socioeconomic landscape. It advocates for individual well-being, celebrates diverse cultures, and enriches the community by housing collaborative spaces.
• Principal aspects of labour, raw material, production, and assembly were sourced locally to reduce the carbon footprint and engage with the local economy.
• Triple-glazed curtain walls and concrete fins at grade minimize solar heat-gain, and owner-provided LED lighting significantly reduces energy consumption.
• The selection and treatment of robust materials ensures long-term durability, reducing future renovations.
• Sophisticated mechanical and electrical systems allow optimal temperature control and improved air-quality.
PROJECT CREDITS
CLIENT Niels Bendtsen
ARCHITECT mcfarlane biggar architects + designers
STRUCTURAL ENGINEER fast + epp
MECHANICAL ENGINEER AME
ELECTRICAL ENGINEER PBX Engineering
CIVIL ENGINEER R.F. Binnie & Associate
GENERAL CONTRACTOR Etro Construction
PHOTOS Ema Peter
4. The project exhibits a raw sophistication through the reinterpretation and refinement of incumbent industrial materials and techniques.
5. and 7. The orientation of the Douglas fir glue-laminated timber bridges, which span the atrium to connect the two cores, creates a geometric foil to the strict grid of the concrete walls.
6. The central atrium between the two building volumes is fully glazed on the north and south to frame dynamic views of the city, rail lines, and port.
At grade, curtainwall fills the void between the concrete structural fins. Starting at the second level, the structure is wrapped in a blanket of triple-glazed unitized curtainwall with integrated fins. The 265mm deep fins create a regular grid that produces a dynamic effect; when approached obliquely, the façade appears opaque, but when viewed head-on it reveals itself as fully glazed. Interior spaces are configured to maximize flexibility and durability. The floors provide all the qualities that designers love about historic brick and beam workplaces without the dust, draughts, poor acoustics, energy inefficiency, and obtrusively placed pipes and cables which can occur in adaptive reuse projects.
411 Railway was conceived by creatives, for creatives. It stands proud as a leader for the evolving Railtown neighbourhood, reflecting an important past and advocating for a sustainable future.
RORY FULBER, ARCHITECT AIBC IS AN ASSOCIATE AT MCFARLANE BIGGAR ARCHITECTS + DESIGNERS.
The Canada Green Building Council (CAGBC) unveiled the 2024 winners of the CAGBC Awards during the Building Lasting Change conference. The annual awards celebrate the innovative projects, teams, and individuals making positive contributions to Canada’s green building sector.
“The CAGBC Awards are a showcase of the market’s commitment to, green building,” said Thomas Mueller, CAGBC’s president and CEO. “This year’s winners represent the best of Canada’s sustainability leaders and the most innovative green and low-carbon projects in the country. Together they prove that green buildings are better buildings with reduced carbon emissions, enhanced resiliency and long-term business value.”
The CAGBC Awards consist of two categories: Green Building, highlighting Canada’s most efficient, effective, and impactful buildings, and Leadership, honouring the outstanding individuals and teams who contribute to the success of Canada’s green building sector. In addition to the CAGBC Awards, CAGBC also presented its annual Lifetime Achievement honour to 2024 recipient, Josée Lupien, President and Founder of Vertima.
“LEED Fellow Josée Lupien is a visionary and pioneer who, over her 20-plus year career, has advanced green building in Québec and Canada,” Mueller said. “She has been a driving force for CAGBC in Québec, a stalwart supporter of LEED and our Zero Carbon Building Standards.”
Lupien is the co-founder of Vertima, a company that helps guide environmental strategies to improve client’s market positioning and improve the environmental performance of businesses, products, services and buildings. Founded in 2008, Vertima has completed more than 110 certified projects, including many certified under LEED® and the Zero Carbon Building Standards™.
The CAGBC Awards recognize the best of the best in the green building sector. This year’s submissions show a strong commitment to reducing impacts on the environment and climate through innovative, resilient, and low-carbon buildings.
Zero Carbon Design
Sponsored by East Port Properties
Winner: Neil Campbell Rowing Centre
Location: St. Catherines, ON
CAGBC Awards winners announced at Canada’s green building conference, Building Lasting Change.
The Neil Campbell Rowing Centre demonstrates how simple, elemental, and respectful design can support a broad spectrum of uses and enhance the identity of a venerable place, while also achieving Net-Zero Energy benchmark and certification under the Zero Carbon Building –Design Standard.
Winner: 25 St. Clair Avenue East Rehabilitation
Location: Toronto, ON
The 25 St. Clair Avenue East project is a major renovation of an existing a ten-storey federal office building in Toronto, Ontario and certified under CAGBC’s Zero Carbon Building – Design Standard.
Sponsored by Morguard Investments
Winner: The Centennial College A-Building Expansion
Location: Scarborough, ON
Sponsored by Enbridge
Winner: SFU Affordable Housing
Location: Burnaby, BC
SFU Affordable Housing is a high-performance, community-oriented housing project in the UniverCity neighborhood at Simon Fraser University’s Burnaby campus.
Winner: Sarah Petrevan, Cement Association of Canada
Sarah Petrevan is a leader in the embodied carbon conversation. Sarah is an active member of the Alliance and participates in CAGBC’s Advisory Panel on Carbon Capture and Utilization in Cementitious Building Materials.
Winner: The Humber College Institute of Technology & Advanced Learning
The team at Humber College has led several key initiatives, including releasing its 2023 Green Building Standards with stringent sustainability requirements for all development.
Sponsored by Stantec
Winner: Region of Peel – Office of Climate Change and Energy Management
The team at the Office of Climate Change and Energy Management (OCCEM) at the Region of Peel has developed and implemented a corporate net zero energy building policy and standard for new construction, enabling zero carbon growth and setting a precedent for other municipalities. (Pictured – Hemant Grover, Manager, Office of Climate Change and Energy Management, Region of Peel)
Sponsored by DIALOG
Winner: Shefali Panse, Certainteed
Shefali Panse began her sustainability journey while pursuing her M.S. in Chemical Engineering at UC Berkeley in 2016.
Winner: Lyle Scott, Footprint
Lyle Scott has been a long-time and dedicated volunteer to CAGBC, most recently working with staff to re-shape the technical committees to support CAGBC’s goals for the future, serving as the first chair of the new LEED Advisory Committee.
The CAGBC Awards committee extends its appreciation to all firms, individuals, and projects who made a submission to this year’s competition, as well as our selection committee for their time and dedication and the contributions of our award sponsors. 2025 CAGBC Awards nominations open in January 2025.
By Alfredo Carrato
When it comes to limiting the amount of carbon emissions globally responsible for advancing climate change, the construction sector has a substantial role to play. Overall, construction is responsible for more than onetenth of total carbon emissions around the world, and a large portion of this carbon footprint comes from the manufacturing of building materials such as cement, the second-most consumed material in the world after water.
1
However, the past decade or so has seen significant advancements in methodologies for reducing carbon emissions in the cement production process. One of the most promising and rapidly growing methodologies is called Carbon Capture, Utilization, and Storage (CCUS), representing a suite of technologies designed to prevent the carbon dioxide that manufacturing processes produce from going into the atmosphere.
Several leading organizations, such as the International Energy Agency, the International Renewable Energy Agency, and the Intergovernmental Panel on Climate Change, have released long-term initiatives that rely on the expansion of CCUS to limit the global temperature rise to just 1.5 degrees Celsius. The IEA has also cited CCUS among the most cost-effective options for the decarbonization of carbon-heavy industries, many of which operate across the construction value chain.
Before outlining the specific CCUS methodologies that are gaining real momentum today, it’s important to clarify exactly how it works and the various ways it promises to lower the carbon impact of cement production.
Carbon emissions are an unavoidable byproduct of traditional cement production. This is because a core component of Portland cement – the most widely used cement today – is limestone. When this mineral is heated, the carbon trapped inside the limestone is usually released.
CCUS allows cement manufacturers to capture this carbon byproduct from points of emission within the manufacturing facilities or directly from the air. Such captured emissions can then be safely stored underground in geological formations, injected into concrete to strengthen it, or used to make other valuable products.
Though CCUS has only gained widespread attention fairly recently, the technology has been achieving real results for several decades. In 1996, the first large-scale CCS project was commissioned at the Sleipner offshore gas facility in Norway. At Sleipner and Snøhvit, another leading project in Norway, over 20 million tons of CO2 have been safely stored to date.
Today, more than 30 cement CCUS projects are in different development stages worldwide, the majority of which are based in Europe. In the United States, the U.S. Department of Energy is currently conducting feasibility studies for multiple projects in California, Colorado, Texas, Missouri and Indiana, among others. However, much of the CCUS progress worldwide is taking place at the startup level, often thanks to collaborations with sustainability-focused venture capital firms.
In England, a startup called Carbon Clean has developed proprietary technology that captures carbon emissions from the flue gas that gets released through a cement plant’s smokestack. The technology is currently in use at cement facilities in several countries such as India and more recently Germany, where the goal is to standardize carbon capture and achieve cost-competitive carbon neutrality across so-called hard to abate industries before 2030.
This is just one of the myriad CCUS-related startups that has garnered considerable venture funding as of late, which reflects the increasing prioritization of sustainability in the global construction sector.
The biggest drawbacks to CCUS are the high upfront capital costs for the equipment to separate the carbon, the high energy costs of keeping the equipment running, and the costs related to transportation and safe storage of the captured CO2. According to a recent report from the U.S. Department of Energy, to cover these expenses a cement manufacturing organization would need to spend another $22 to $55 for every metric ton of cement produced.
Fortunately, in the United States, the Inflation Reduction Act offers tax credits of up to $85 per metric ton of captured carbon emissions. That’s a great start, but it doesn’t account for the additional costs of transporting and storing the captured carbon. Also, there’s the logistical issue of where to store all that reclaimed carbon if it is not reused. Companies that introduce CCUS need to have access to some kind of underground geological formation that’s capable of storing large amounts of carbon for centuries on end.
To counteract the increased costs of CCUS, many startups are developing cheaper and smaller carbon capture systems. For example, the simplified and ultra-efficient design of modular CCUS equipment is a considerable improvement over the expensive earlier systems and has the potential to make CCUS dramatically more accessible across the globe.
In addition, governments all over the world are issuing more and more grants for all sorts of sustainability initiatives in the construction sector, including CCUS. In August 2022, the Biden administration announced an investment of more than $96 million to support commercial carbon capture, utilization, and storage projects, and in Canada, the federal government launched the Energy Innovation Program - Carbon Capture, Utilization and Storage RD&D Call. Through this initiative launched in 2021, the Canadian government intends to invest CA$319 million over seven years in research, development, and demonstrations to advance the commercial viability of CCUS technologies.
Canadian start-up Carbon Upcycling is a great example of government support for the transition to net-zero emissions by 2050. Last year UK Research and Innovation (UKRI) awarded the startup £2.3 million to manufacture a climate-resilient cement alternative from waste glass and CO2 and in February 2023, Emissions Reduction Alberta (ERA) granted Carbon Upcycling CA$4.4 million for two commercial-scale projects within the Albertan construction sector.
Of course, CCUS is just one of many methodologies for reducing carbon emissions in cement manufacturing. Another strategy is producing cement with lower carbon content by replacing what’s called clinker – a key component of cement – with what are called substitute cementitious materials, or SCMs.
SCMs are typically by-products of industrial processes, such as waste from steel production or coal-fired power generation. SCMs can account for up to 50 percent of the cement that’s used to make concrete, which reduces carbon emissions from this process by up to 30 percent.
What’s more, numerous start-ups have developed their own technologies for converting waste from cement production into SCMs that can then be used by that same facility. These technologies could become particularly vital in the coming years, especially should SCMs become increasingly scarce.
Similarly, cement manufacturers can reduce carbon emissions even further by using alternative clean fuels, such as Spanish startup WtEnergy’s synthesis gas alternative, and renewable energy sources to heat the manufacturing process. In the solar energy sector, some startups have created technology capable of generating solar fuel that’s powerful enough to drive industrial processes like cement manufacturing or fuel production.
Now that CCUS and other decarbonization methods are becoming more accessible, it’s up to governing bodies to develop new policies and regulations that incentivize companies to invest in these technologies and for leading cement manufacturers to take the initiative in deploying and scaling promising start-up solutions. The Inflation Reduction Act is a significant step forward, but this is only the beginning of the incentives that manufacturers are going to need.
In all likelihood, the key to lowering the construction sector’s carbon footprint will come from uniting all stakeholders in the construction value chain around a common goal, which governments must support by fostering innovation.
ALFREDO CARRATO IS A TRAINED ARCHITECT, BIM ENTHUSIAST AND COLLEGE PROFESSOR WHO SCOUTS FOR BREAKTHROUGH DECARBONIZATION TECHNOLOGIES FOR THE CONSTRUCTION INDUSTRY. AS AN INVESTMENT AND OPEN INNOVATION ADVISOR, HE OVERSEES INVESTMENT ACTIVITIES AND PARTNERSHIPS AT CEMEX VENTURES, WITH A FOCUS ON TACKLING THE CARBON FOOTPRINT CHALLENGE OF THE CONSTRUCTION SECTOR.
Institutional (Large) Award: UBC MacLeod Building Renewal, Proscenium Architecture and Teeple Architects. Top left : Proscenium Architecture + Interiors (l to r) : Ben Nielsen, Alissa Foss, Kori Chan, James Bligh. Top right : Teeple Architects (l to r) : Myles Craig, Avery Guthrie, Stephen Teeple.
Institutional (Small) Award: Windermere Fire Station 31, S2Architecture and GH3* Architects.
Top left: S2Architecture (l to r): Linus Murphy and Erin Jess.
Top right: gh3 Architects (l to r): Mark Kim, Pat Hanson, Raymond Chow, Joel Di Giacomo.
Bottom: EcoAmmo (l to r): Angela Li, Andriana Beauchemin, Steph Carter, Madeleine Drake, Tim Tewsley, Hannah Li.
The annual program to recognize excellence in the design and execution of all types of sustainably-designed, high-performance Canadian residential and non-residential buildings and interiors, both new and renovated.
Residential (Small) Award: Heimaklettur House, MOTIV Architects Inc. ( l to r) Madeleine Cardin, Jackie Rosborough, Asher deGroot, Kristina Le, Tracey Mactavish.
Residential (Small) Award: Bird’s Wing Passivhaus Duplex, ONE Seed Architecture. (l to r) Allison Holden-Pope, Hannah Griffiths, and Emily Reddy.
Mixed Use Award: Cheko’Nien House, Perkins&Will.
The Perkins&Will design team : Alex Minard, Kaz Bremner, Jana Foit, Adrian Watson, and David Damon with Kimberly Baba, Prachi Bhinde, Markus Brown, Aidan Carruthers, Cheney Chen, Cillian Collins, Paul Cowcher, Mahdiar Ghaffarianhoseini, EJ Hamilton, Jessica Kim, Rafaela Kirloss, Neal Li, Manuela Londono, Khuyen Luong, Heather Miller, Jennifer Miller, Nariman Mousavi, Rick Piccolo, Adrienne Rademaker, and Spencer Todd.
Technical Award: BC Ministry of Children and Family Development, J. Robert Thibodeau Architecture + Design Inc.
(l to r) : Harsh Mehra, J.Robert Thibodeau, Marjorie Beaulieu.
Residential (Large) Award: Foxglove Supportive Housing and Shelter, NSDA Architects. (l to r): Larry Adams and Ken Wong.
Technical Award: Gabion House, Waymark Architecture. (l to r): Mizraim Garduño, Will King, Graeme Verhulst, Sarah King, Stephen Sprenkle, Ana Ahumada, and Shari Khadem.
Existing Building Upgrade Award: Little by Little Studios, pico ARCHITECTURE inc.. (l to r) : Michelle Peake, Tim Horton, Gail Little, Evan Jameson, Bobbi MacLennan. Missing: Jon Ferreira, Julia Evancio, Diego Kerzer. Photo by Douglas Little Photography.
Sindhu Mahadevan
Studio Lead and Head of R&D at MGA Michael Green Architecture (MGA), Vancouver
Daniel Ling
Director and Principal, Montgomery Sisam Architects OAA, AIBC, SAA, AANB, NSAA, AIA, MRAIC, LEED AP
National Sponsors
Category Sponsors
Peter Osborne
Architect, AIBC, AAA, SAA, MAA, OAA, FRAIC, LEED ® AP Partner, GEC Architecture, Toronto