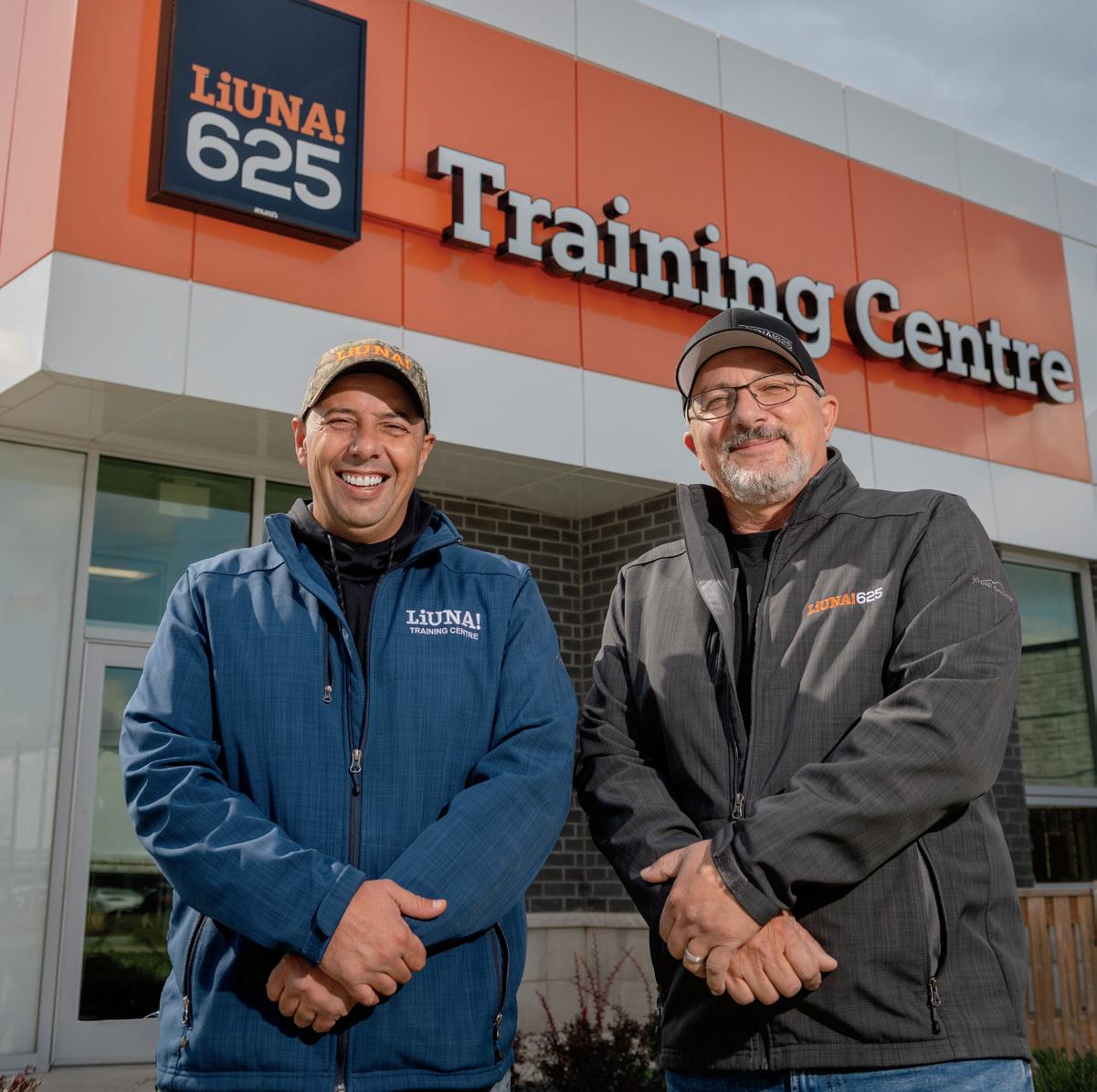
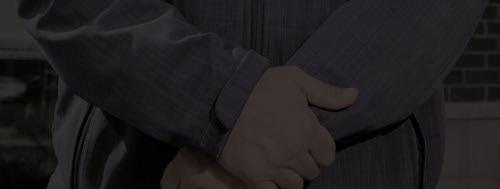
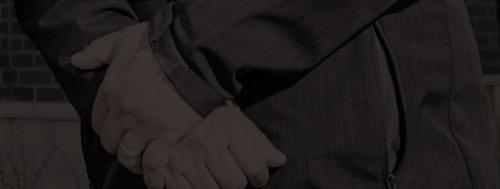
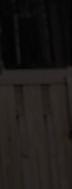
Creating new solutions as the automotive industry evolves.
Working alongside the auto sector to revolutionize the future of the automotive industry by improving how cars are produced.
These are just some of the ways UWindsor Engineering is designing the future.
DAVE HUNTER
MCGINTY..................................................
BEECROFT
ROBILLARD
MATT ST. AMAND
BRIGNALL-STRONG
MAYOR DREW DILKENS
LANGEMANN
BOOTH
David Hunter – Vice President,
- 519-816-0874
Breanne McGinty –
Cell - 519-819-4697 bmcginty@thedrivemagazine.com
of
City of Windsor remains proud of its reputation in the community and around the world for our work in design, construction, tool and die, research and development, automotive, and many other key sectors that form the broader manufacturing industry. Our strengths as a manufacturing and automotive powerhouse have placed us on the world stage as a leader in the field of automation.
Two years ago, City Council unanimously adopted the bold new Windsor Works strategy for economic diversification and development, seeking to create the conditions for investment attraction, job creation and retention of homegrown talent all important benefits to our local manufacturing businesses. Thanks to that plan, less than a year later we welcomed a major investment from LG Energy Solution, Stellantis, Canadian Innovation, and the Ontario Government for the over $5 billion NextStar EV battery manufacturing facility. This will be the first domestic facility of its kind, the largest investment in Canada’s auto industry, and one of the largest investments in Windsor in a century. The game changing new facility will create about 3,000 new jobs, as well as countless new opportunities for all those in supporting sectors. With this announcement, we secured the future for thousands of local workers as well as Windsor’s strategic location as the home of Canada’s electric vehicle future.
At the City of Windsor, we continue to support our rapidly changing global marketplace, positioning our region as a leader in the next industrial revolution. As the world pivots to EVs, Windsor-Essex will be the ‘Automobility Capital of Canada’ . We are at a crucial point of unprecedented growth and opportunity, with more large scale corporations, mid size companies, small businesses, families and individuals looking at Windsor as the ideal place to invest, work, live, and lay down roots.
Our manufacturers, our tradespeople, our innovators and dreamers are all part of this booming present and electrifying future, and I am sincerely grateful for their continued support in building a strong and prosperous community.
Sincerely,
DilkensWhat is the most valuable commodity in business? Time.
“Performance Painting has been in business for twenty years,” says Jeff Batten, President at Performance Painting & Floor Coating Ltd. “We’re way past beginner’s luck by now!” he says with a laugh.
He continues: “I started back when I was sixteen years old, working for a family business that was in industrial painting. After working my way up through the ranks, I branched off on my own, taking small jobs throughout the Windsor and Cha tham area.”
In an industry where you are only as good as your last job, Performance Painting’s reputation spread by word of mouth.
“We began with five employees,” Jeff recalls, “and we have grown to twenty people working for us between the field and in the office.”
Performance Painting has established itself by being a good steward of its clients’ most valuable commodity: time. Industrial painting is a “go big or go home” industry. When the sprayers arrive to do their work, there is no working around them. Normal operations must stop.
By Matthew St. Amand advertising“It means working a lot of odd hours,” Jeff says. “When one of the tool shops in town calls us in, we will usually begin Fri day afternoon at three thirty, scrubbing surfaces, covering machines with tarps, preparing the location for painting or epoxy application, whatever the case may be.”
Jeff and his team work through the weekend, twenty four hours a day, until Sunday night at 11:59 when the shop needs to resume operation. The timelines are just as tight—or tighter—on new buildings under construction.
Batten
Jeff also ensures that all products used by Performance Painting contain low or zero VOCs (Volatile Organic Compounds), which is better for people working in the building, and better for the environment in general.
Performance Painting has undertaken some substantial jobs during its two decades in business. Jeff takes a Zen approach to projects that might overwhelm someone with less experience.
“No matter how large the project,” he says, “we work room by room. If you can paint one story of a building, why can’t you paint two or more stories? So, that’s how we approach each job—a piece at a time.”
It helps that all of Jeff’s team are cross trained, so they have a maximum of versatility and flexibility to tackle each job no matter how unique.
“When we hire people, often they already have experience doing residential painting,” Jeff says. “We take every individual and train them to be industrial spray men, epoxy flooring installers, as well as sharpening up their standard brush and roller skills. So, if I need someone to install an epoxy floor, I can pull them from any current project. We like to train our people to know everything paint-related.”
He offers an example that Performance Painting is currently painting in a building under construction on Essex Way, which will be a 160 room assisted living complex. His painters can go from that job over to an asphalt plant and apply spray epoxy there. With a cross trained team, they have the flexibility to get different jobs done.
One of Performance Painting’s largest jobs—completed in a short period of time—occurred at Atlas Tube where they sprayed the interior of the steel mill with polyester dry fall epoxy.
“That was a hundred thousand square feet,” Jeff explains.
They were also sealing heritage timbers in the new French Immersion school under construction on Mercer.
Experience and craftsmanship have pieced together Performance Painting’s sterling reputation for the past two decades. To learn more about what they do, visit performance-painting.ca/gallery. W.E.
Windsor steps up to the challenge of taking on another “first in Canada”.
By Matthew St. Amand Photo by Hub Media Inc.The cutting edge of 21st century technology is coming to Windsor. In fact, the groundwork for the gargantuan plant that will house it is being prepared as this article is being written.
For anyone who wonders “Does anything ever happen in Windsor?” the answer is a resounding “Yes!”
Windsor, Ontario caught the notice of European automaker Stellantis and South Korean battery manufacturer LG Energy Solution (LGES), both of whom came together in March to
announce that they executed a series of binding, definitive agreements to estab lish the first large-scale, domestic, elec tric-vehicle battery manufacturing facility in Canada. They chose Windsor as the site to make this happen. The joint venture company, called NextStar Energy, will pro duce leading edge lithium-ion battery cells and modules to meet a significant portion of Stellantis’ vehicle production require ments in North America.
What does this mean for the area?
It means more than $5 billion being invested here, in our backyard, to estab lish operations, which will include an all-new battery manufacturing plant. Con struction of plant facilities are currently underway, and production operations are planned to launch in the first quarter of 2024. The annual production capacity the NextStar Energy plant aims to achieve will be in excess of 45 gigawatt hours.
“This is massive news, not just for the Canadian auto industry. This is huge for Windsor, the Canadian economy and Canadian jobs," said Brian Kingston, chief executive officer of the Canadian Vehicle Manufacturers’ Association, quoted in local media. “We know the auto industry is going through a significant transfor mation to electrification right now and for Canada to secure an investment of this size and scale into battery manufac turing ... indicates that we are a player in this transition.”
The news has been welcomed by many in Windsor’s auto sector, which has seen sizable job losses in recent years.
Justin Falconer, CEO of Workforce Windsor-Essex, was quoted in local media as saying that on top of the 2,500 jobs the NextStar Energy plant will cre ate, he anticipates “up to 10,000” spinoff jobs. Areas he believes will see job growth include charging stations, sup ply chain partners for electronic compo nents, moulds for the batteries, research and development and transportation for the batteries.
NextStar Energy is already producing miracles: bringing about complete agree
ment among the various government bod ies needed to make the venture happen. Each of the municipal, provincial and fed eral levels of the Canadian government have announced that they are committed to fully supporting the successful opera tion of NextStar Energy.
investments across Stellantis’ 14 brands through 2025.
“Our joint venture with LG Energy Solu tion is yet another steppingstone to achiev ing our aggressive electrification roadmap in the region aimed at hitting fifty percent of battery electric vehicle sales in the U.S. and Canada by the end of the decade,” Tav ares said in a news release. “We are grate ful to the municipal, provincial and federal levels of government for their support and commitment to help position Canada as a North American leader in the production of electric vehicle batteries.”
Work at the future site of the Next Star Energy electric vehicle battery plant is moving along, bringing with it substan tial changes to the landscape. Berms are being created around the northern perim eter of the property and new pavement has gone down in a cargo area at the Twin Oaks location off Banwell Road, south of E.C. Row expressway.
In June, Danies Lee was appointed chief executive officer of NextStar Energy, who remarked: “I am extremely humbled by this appointment and look forward to putting in place the senior leadership team of NextStar Energy who will help me achieve our vision of producing lead ing-edge lithium-ion battery cells and modules to meet a significant portion of Stellantis’ vehicle production require ments in North America.”
It only makes sense that NextStar Energy is setting up shop in Windsor, home to Canada’s largest automotive clus ter. The company expects the plant will serve as a catalyst for establishing a strong battery supply chain in the region. It must be remembered that Canada is commit ted to establishing a broad, local battery ecosystem by leveraging—among other things—its leadership in the generation of electricity from renewable sources.
In a statement, Stellantis CEO Carlos Tavares spoke of the company’s plans— which include $35 billion in EV-related
“I’m flabbergasted with how quickly things are progressing,” said Jelena Payne, the city’s commissioner of economic devel opment and innovation.
The 220 acre parcel of land in the pro cess of being prepared for building the 4.5 million square-foot facility. Nearly 100 workers are currently on site, and another 500 workers are expected to be on site in the coming months.
“There is great excitement in the short term with all of the construction jobs over the next couple of years,” said Windsor mayoral candidate, Drew Dilkens. “But the real impact will be felt long term where we have 3,000 people from our community working in this new factory, building the batteries that will power the cars of the future.”
One need look no further than the pages of this magazine to know that Windsor is up to the challenge, ready and able to deliver on whatever is necessary to make the first large-scale lithium-ion battery production plant in Canada a success. W.E.
The real impact will be felt long term where we have 3,000 people from our community working in this new factory, building the batteries that will power the cars of the future.
The future of higher education is here and its name is Nexus.
With the recent unveiling of Canada’s largest esports facility, St. Clair College is once again upping the ante both academically and in terms of student life; enhancing the campus experience and ushering in a new era of tech-based career options.
The state-of-the-art facility, dubbed ‘Nexus’, is located in the newly renovated Don France Student Commons and features a 15,000-square foot arena with eight pods of PlayStation 5, Xbox One, and Nintendo Switch consoles, three virtual reality bays, and an open gaming lounge with over 40 computers. It also includes a broadcasting facility for the Esports Administration and Entrepreneurship program.
“It’s really come full circle,” says St. Clair Student Representative Council General Manager Ryan Peebles. “The college president (Patti France) and the administration always had a vision of becoming a destination location, bringing students in from across the world and making sure they had everything they needed on campus.”
“They’ve got the Sports Park which is brand new, they’ve got the Sportsplex, and now they have the esports arena, so it’s really helped enrich student life.”
Esports, short for electronic sports, is the next multi-billion dollar global industry. It’s a form of competitive gaming that essentially turns online video gaming into a spectator sport; allowing audiences to watch professional players compete against each other in organized multiplayer competitions.
The budding industry first came onto the college’s radar back in 2005.
“We had a student club that asked us to open up the computer lab to gaming,” explains Peebles. “At the time, the college’s IT Department was a little hesitant but then said, ‘Why don’t we build a room where they can play and open up the system to allow for more gaming?’”
The original space featured 30 computers in a small room at the back of the computer lab. Then, in 2016, a local organization came forward asking if they could host a LAN (local area network) party for students on campus.
“We jumped on board and it kind of took off from there,” recalls Peebles.
“May of 2017 was one of our larger LAN parties with over 400 individuals that played at the Sportsplex. We took over the Sportsplex for the whole weekend; it was a 3 day tournament and they played 24-hours a day for three days.”
“The organization had come forward and said, ‘This is the way of the future.’ If you go to Japan, Korea…this is the next dimension of sports. A lot of individu als are going that route; NBA players are purchasing teams and doing this on the side. It’s the next billion dollar industry.”
After that, Peebles says, the college decided to go all in; becoming the first post-secondary institution in Canada to offer a two-year Esports Administration and Entrepreneurship diploma program.
“When the school launched the esports program, they wanted to ensure that the students also had the ability to not just play in the industry, but also work in the industry; managing a team, coaching a team, selling advertising.”
“If you look at other colleges or uni versities across Canada, there were some schools that had some smaller club teams at the time, but not varsity level that was supported by the collegiate side,” he adds.
Today, there are nearly 40 students who compete on the varsity level and 115 junior varsity academy players who play in and out of the arena for the Saints Gaming team.
“It’s really enhanced our student life on campus because you can play typical sports; badminton, tennis, baseball, bas ketball, soccer, volleyball; and now there’s esports,” says Peebles. “It really encour ages our students to have that full experi ence and get involved with a team.”
“Not everyone’s an athlete that plays basketball or soccer, some people like to watch sports or play video games as a sport and that’s where we’ve seen it grow.”
Nexus has also become a gathering space for students; a place to go to relax after a long day of school work.
“People just hang out there; there are couches, tables, board games, and ping
pong tables. It’s all encompassing. It’s pretty steady each day and even on week ends it’s full,” he shares. “It’s more of just a fun atmosphere to come hang out and de-stress from campus.”
The facility is accessible for free to all students via their student card, but it’s also open to the public for a small hourly fee.
Nexus is managed by the SRC and a full team including Esports Director Shaun Byrne and three full-time staff: a Broad casting Coordinator who helps broad cast the games on the college’s Twitch stream, an Assistant Esports Director, and a Computer Lab Coordinator.
“On top of that we have volunteer coaches; they come back either as a stu dent or as a graduate and volunteer to help facilitate the teams,” notes Peebles.
Now running like a well-oiled machine, the state-of-the-art arena will set a new standard for all subsequently developed esports facilities of its kind in North America.
“I just think it’s a great program and it’s tied to a great administration pro gram on the school side so students can also learn at the same time they’re play ing,” adds Peebles. “When you come to school, obviously you want to come for educational reasons but you don’t imagine coming to school and seeing this large facility where you can play video games.” W.E.
At the LiUNA Training Centre, Windsor campus, Trainers are sharing that power to help build communities. Since 2009, the training centre has been transforming students into skilled versatile workers who are ready for the labour force and sought after by employers.
The Labourers’ International Union of North America (LiUNA) Local 625 was established in Windsor in 1945. It is one of 11 LiUNA locals in Central and Eastern Canada. LiUNA is one of the fastest growing, most progressive, and highly respected unions in Canada with approximately 100,000 members, and tens of thousands of retirees.
Since 2009, the LiUNA! 625 Training Centre has been training the next generation of Construction Craft workers.
The Construction Craft Worker pro gram offered by the LiUNA Training Centre, Windsor campus, offers over 30 skills, all of which help prepare candi dates for a secure, high paying job. The course is free to all qualified participants.
Carmelo Calcara coordinates the Training Centre. He has been a LiUNA member for 25 years and Training Director for the past six years. He brings a strong work ethic and knowledge to this role, and possesses a solid under standing of what it takes to succeed in the field.
In order to qualify for the Construc tion Craft Worker Apprenticeship, par ticipants must be 18 years of age, have
their Grade 12 certificate, their G2 driv er’s license, and successfully complete one day of aptitude and skills testing.
“Aside from these qualifications, all we require of participants is a will ingness to learn and a good attitude,” says Carmelo.
“The Construction Craft Worker training program is a great pathway for young people to enter the labour force,” Carmelo continues. “Our goal at the training centre is to teach participants numerous skills so that when they join the workforce, they can sustain their employment, and work safely.”
Multiple skill sets are touched upon during the course.
“Working with concrete and asphalt,” Carmelo says, “setting forms, installing water mains, storm sew ers, road work, bridge work, survey ing, demolition. As construction craft workers, we also have to be operators. We teach candidates how to operate mini excavators, fork lifts, genii booms, boom trucks, scissor lifts. On job sites, we may also have to do welding and torch cutting for demolition. So, we cover a great number of skills that these workers will need.”
The Training Centre, located in Old castle, is a hive of activity every day.
Carmelo continues: “We also have four acres for use in training—breaking
up concrete, placing concrete, setting forms, scaffolding, learning on equip ment, placing asphalt. We do a lot of hands-on here. And it’s not only LiUNA members, but City of Windsor workers here, getting their red seal.”
The work is not easy. Participants have to enjoy working with their hands. Jobs are often located outside, and workers are often not doing the same job, day after day. This type of occupa tion can have workers moving around the region, on sites out of town.
“There are eighteen sectors of con struction areas,” Carmelo goes on, “such as water main, sewers, and build ings. Our students get the skills to be versatile. The possibilities are great. Someone who joins Windsor LiUNA can move east or west, and just transfer to that local. Train in your home city, and then transfer to the LiUNA where you end up.”
“Our students range from eighteen years of age to fifty years old. We had a recent grad who was forty-eight years old,” says Nuno Meca, an ANSI certi fied instructor at the Training Centre. “Many of our students are readying for their first career, but others have already had careers and are seeking a change. There are no limitations here. We do not discriminate. It’s an equal opportunity for everybody.”
“The program is ten weeks in-class,” says training administrator Cassandra Meca. “For pre-apprentices, classes begin in May and in July. We inter view potential candidates at the begin ning of the year in order to select the applicants. One big consideration is that, while the course is free of charge to pre-apprentices, they also won’t be earning any money during that time.”
Following the completion of the 10 week program, participants embark on a 12 week work placement where they gain real world experience on actual job sites, while earning a pay cheque.
“People who are interested can apply online on the LiUNA!625 website,” Cas
sandra says, “or they can just come in. Sometimes it’s better if they come in. If Carmelo’s free, he can explain directly what happens in the classroom.”
Lead instructor, Nuno, has almost 30 years of experience as a construction craft worker. He has been an instructor at the LiUNA Training Centre, Windsor campus since 2016.
Carmelo concedes. “Our safety courses are taught by experienced trainers. We offer seventeen safety certifications, which include: working at heights, asbestos removal, training on all the machinery, first aid training, hoisting rigging, lockout tag out, traffic control, propane, electrical safety, confined space, chainsaw.”
When asked about success stories, Nuno says he considers every student who completes the course a success story. “Our passing rate is nearly one hundred percent,” he says.”
Carmelo remembers a student: “Kate trained here in Windsor and was working at the new bridge, on concrete forming crews. Now she is in Ottawa working on light rail systems. She is doing fantastic.”
He also recalls: “Priscilla came through the program and she is now, probably, one of the best directional drillers in Windsor. She earned her red seal, and is doing fantastic. She had a great attitude!”
“We instill our values in our stu dents,” Nuno says, “teaching them what we think the contractors are looking for. We give our students the best shot at employment and the versatility to remain employed. Construction craft workers are the most skilled workers on any job site. They branch out into so many directions.”
Nuno knows of what he speaks. During his career, he worked on some major league projects. Not the least of which—the Herb Gray Parkway.
“The Parkway was entirely built by construction craft workers,” Nuno says. “The only other skilled trades on the job were the operating engineers.”
Not only do students learn job skills, but they also receive extensive safety training.
“It can be dangerous on a job site if you don’t know what you’re doing,”
Asked about the success of the program, Nuno says: “It begins with Rob.” Rob Petroni, Business Manager of LiUNA!625 since 2009. He’s well known in the community not just for the work his thousands of members are doing, but for LiUNA’s extensive philanthropic efforts.
“We try to give back to the commu nity as much as we can” said Petroni. “It’s important to us that the phrase ‘We build communities’ doesn’t just apply to bricks and mortar, so we’re always doing what we can for various charities around Windsor Essex.”
“He is our leader,” Nuno contin ues. “He gives us the freedom to run this place effectively. Rob gives us the support to be creative and our success comes from that creativity.”
That success is clear to anyone who enters the Training Centre.
To learn more about LiUNA!625 and the LiUNA training centre, visit liuna625.ca. W.E.
Our goal at the training centre is to teach participants numerous skills so that when they join the workforce, they can sustain their employment, and work safely.
By the year 2025, one in five jobs in Ontario will be in the skilled trades. It’s my mission to get more people moving toward those important, well-paying jobs.
A new agency has been formed in Ontario to help fi ll the shortfall in skilled trades jobs.
Ontario’s Minister of Labour, Training and Skills Devel opment, Monte McNaughton, has a message for the prov ince: “The greatest economic challenge we face today is the labour shortage created by people in skilled trades retiring with too few young people lined up to fill their roles.”
Far from being a dire declaration, it is a positive reminder that there are jobs to be had in skilled trades, which are sat isfying, lucrative, and lifelong.
“By the year 2025,” Minister McNaughton continues, “one in five jobs in Ontario will be in the skilled trades. It’s my mission to get more people moving toward those import ant, well-paying jobs.”
The Ontario government, through its Ministry of Labour, has taken tangible steps to make this happen by launching “Skilled Trades Ontario”, a new Crown agency, to improve trades training and simplify services. Among this agency’s goals is promoting and marketing the trades, developing the latest training and curriculum standards, and providing a streamlined user-friendly experience for tradespeople.
“We’re redrawing the system to address Ontario’s labour shortage and make the trades a career of choice for more people,” Minister McNaughton is quoted in the agency’s press release. “The skilled trades provide well-paying and rewarding careers that are vital for our economy. By cre ating this new agency, we are working for workers and delivering the generational change that labour leaders and employers have been calling for.”
“Previously, it took sixty days to register as an appren tice,” Minister McNaughton points out. “Now, it takes twelve days.”
As well, under the old system, run by the Ontario Col lege of Skilled Trades (OCST), log books were all paper docu ments. The new Skilled Trades Ontario agency is launching a portal where these will be available in digital format, increasing ease of access.
“Industry needs more of a voice,” Minister McNaugh ton says. “The new Skilled Trades Ontario agency is indus try led. Employers have a seat at the table, offering input to ensure we’re training people for jobs that exist, and that the training keeps pace as industry technology advances.”
Jim Hogarth, President, Provincial Building and Con struction Trades Council of Ontario, says of the new agency: “[We] welcome the establishment of Skilled Trades Ontario. We look forward to working with their leadership team to promote and strengthen the construction trades, and to ensure that Ontario leads the way with the best, safest, and most up-to-date training standards in Canada.”
The spirit of the Skilled Trades Ontario agency has three distinct pillars: (1) Ending the stigma associated with jobs in skilled trades; (2) Simplifying entry into apprenticeship pro grams; (3) Encouraging employers to bring on apprentices so they can learn from experienced trades people in realworld environments.
“One of the things the new agency will do is coordinate more closely with businesses,” Minister McNaughton says. “For instance, if businesses want to donate tools and equip ment to a school or training program, Skilled Trades Ontario will help with that. The idea is to knock down barriers.”
“The skilled trades are the backbone of our province –offering 144 well-paying and in-demand careers for peo ple to choose from,” says Skilled Trades Ontario CEO and Registrar, Melissa Young. “I commend this government for bringing generational change that will remove the stigma surrounding the trades, cut down on red tape, and ensure all young people know these jobs offer a clear path to a better life.”
More information about this new agency can be found at skilledtradesontario.ca. W.E.
A�ter they trained me on CMM, I was the only person doing those inspections. At times, they had me under pressure because every project has to be on time. I told them: ‘You can have the other guy do it.’ But my foreman said: ‘No, you are totally capable of doing it.
The people of Ontario have heard it before—most recently from the Min ister of Labour, Training and Skills Development, Monte McNaughton: “The greatest economic challenge we face today is the labour shortage cre ated by people in skilled trades retiring with too few young people lined up to fill their roles.”
No one has heeded this warning as proactively as Jason Lepain and the administrators of the Ontario Youth Apprentice Program (OYAP). OYAP is a school-to-work program that opens doors for students to explore and work in apprenticeship occupations through the Cooperative Education program. Students can become registered apprentices and work towards becom ing certified journeypersons in a skilled trade while completing their secondary school diplomas.
According to Minister McNaugh ton: “By the year 2025, one in five jobs in Ontario will be in the skilled trades.”
OYAP inspires young people to give skilled trades serious consideration as a career choice. The program abounds with success stories. One that is par ticularly illustrative involves a sev enteen-year-old Walkerville student named Caidence who gave OYAP a try and found a passion she didn’t realize she had.
“I heard about OYAP through the Create Your Future program,” Caid ence explains. “My teachers at Walker ville thought OYAP would be a good fit.”
It was a brave choice for Caidence because joining OYAP meant splitting her time between her familiar home school, Walkerville, and W. F. Herman Secondary School where the Depart ment of Technology Studies is located. This pushed her out of her comfort zone. With the support and encourage ment of her teachers, however, such as Natalie Browning-Morgan, Caidence took the leap. Among the challenges she faced was finding transportation from Walkerville to Herman.
“This is a gap,” says Natalie Brown ing-Morgan. “Caidence struggled with it at first, but she overcame it.”
Although hesitant at the start, Caid ence was determined to give OYAP a fair shot.
“At first, I didn’t think I would like it,” she says, “but then I met Mr. Kote vich at Herman, and he showed me that this was something I could do.”
Caidence did her General Machinist apprenticeship at Nickleson Machine & Tool in Windsor.
“When I first started, I was nervous about using the CMM machine,” she says. “Some of the other machines were the size of a house. Some boring mills were just huge, radial drills, huge rotary surface grinders the size of a shed.”
Sixteen years of age the time, Caid ence was the first female Nickleson had on the shop floor. She saw that the floor personnel were very close and won dered if they would accept her. They did.
Caidence’s foreman, Darren Roy, wasted no time beginning her training. She started on the CMM machine (Coor dinate Measuring Machine), which is a tool used for measuring the dimensions of machine/tool parts using coordinate technology. The dimensional measure ments the CMM records include height, width, and depth in the X, Y, and Z axis. It is used for inspecting parts before shipping to customers.
“After they trained me on CMM,” Caidence says, “I was the only person doing those inspections. At times, they had me under pressure because every project has to be on time. I told them: ‘You can have the other guy do it.’ But my foreman said: ‘No, you are totally capable of doing it.”
After working on her General Machinist apprenticeship, Caidence gained enough experience to realize it really wasn’t the direction for her.
“After completing my first year, I decided I preferred tool making,” she says. “It was more hands-on.
Every day it was something different. I had to bring my own creativity and problem-solving.”
As a result of OYAP, if Caidence maintains her academic average, she’ll have a Level I apprenticeship when she graduates from Walkerville in June. She will work the summer at Nickleson and continue working on her appren ticeship through St. Clair College in the fall. Students pay for their courses upfront, but if they successfully com plete them, they are reimbursed those costs through grants.
Following her time at Nickleson, Caidence’s co-workers missed her.
“The employer had so many great things to say about Caidence,” Jason Lepain confirms. “They really miss hav ing her. She did so many things there.”
Caidence sums up her experience with OYAP, saying: “It has been amaz ing. I love working in my field. I was so lucky with my placement at Nickleson. They really took me in and taught me so much. My foreman did a great job help ing me. He saw that I got a wide variety of training, experience. I tried almost every machine in there. I can’t wait to go back.”
The skilled trades are fast becoming the career of choice among many young people. OYAP is a proven pathway into satisfying, well-paying jobs. For more information, please contact Jason Lep ain or Justin St. Pierre to explore the many different OYAP or Specialist High Skills Major (SHSM) programs offered at the GECDSB that could lead an excit ing career in the skilled trades. If you are an employer looking for GEDCSB COOP students in Manufacturing or any other sector, please reach out to us as well. More information on SHSM program can be found at ontario.ca/ SHSM W.E.
Justin St. Pierre – Justin.St.Pierre@ publicboard.ca 519-791-7166
Jason Lepain – Jason.Lepain@pub licboard.ca 519-816-6170