
9 minute read
HeidelbergCement Das neue
Mehr als 240 000 m3 Beton werden allein für das Terminal-Hauptgebäude – die Piers nicht eingerechnet –verbaut, zum Teil bis zu 3 600 m3 Beton pro Betonage.
Das neue Terminal wächst zusammen
Advertisement
t HEIDELBERG CEMENT – Trotz Corona-Krise läuft die Baustelle des »Terminal 3« im Süden von Frankfurts Flughafen auf Hochtouren. Angesichts der großen zu verbauenden Betonmengen sind Rohstoffqualität und eine intakte Lieferkette immens wichtig. Dafür hat HeidelbergCement gesorgt.
Lieferkette
Jedes Detail der Lieferkette muss stimmen: So muss immer ausreichend Zement vorhanden, und die Leistung der mobilen Mischanlage muss entsprechend hoch sein, beispielsweise rund 135 m³/h. Ebenso müssen die Fahrer der Betonmischfahrzeuge und des Radladers auf engstem Raum manövrieren können.
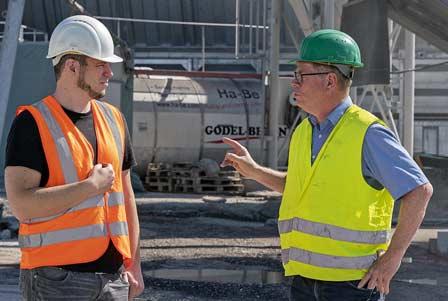
Dutzende Krane ragen in den Frankfurter Himmel. Auf Deutschlands größter Flughafenbaustelle wird Beton gepumpt, gegossen und bewehrt, »was das Zeug hält«. Mit dem Bauprojekt möchte der Fraport langfristig für den steigenden Passagierverkehr gewappnet sein und den Frankfurter Flughafen in die Spitzengruppe der weltweit größten Flughäfen katapultieren. Zwar sind die Passagierzahlen aufgrund der Corona-Krise aktuell eingeknickt, aber in einigen Jahren sollten die zusätzlichen Kapazitäten dringend benötigt werden, prognostizieren die Fraport-Verantwortlichen.
Hand-in-HandArbeiten Für die Fraport AG ist es die bislang größte Einzelinvestition. Rund 500 Firmen sind am Bau beteiligt, darunter Dechant Hoch- und Ingenieurbau, Betonlieferant Godel Beton sowie die HeidelbergCement AG, die den Zement bereitstellt. Als einer der Haupt-Player wurde Dechant unter anderem mit dem Bau des TerminalHauptgebäudes beauftragt. »Bei einem solch großen Projekt kommt es auf eine gute Zusammenarbeit an. Weil wir ja vorher nicht die Zeit hatten, Prozesse einzuschleifen, musste das Hand-in-Hand-Arbeiten von vornherein funktionieren. Bei uns hat das Zusammenspiel mit Godel Beton sehr gut geklappt«, erklärt Stefan Schorn, einer der Projektleiter von Dechant Hoch- und Ingenieurbau. Der Bau schreite rasch voran und alles laufe unter den gegebenen Umständen nach Plan.
Mehr als 240000 m³ Beton werden für das Terminal-Hauptgebäude – die Piers nicht eingerechnet – verbaut, auf einer Grundfläche, die etwa der Größe von 13 Fußballfeldern entspricht. »Beim Bau der Bodenplatten haben wir in einer zusammenhängenden Betonage bis zu 3 600 m³ Beton eingebaut. Da waren wir froh,
HEIDELBERGCEMENT AG/CHRISTIAN BUCK
Klaus Felsch, Produkt-Manager Verkehrswegebau HeidelbergCement (re.) im Gespräch mit Daniel Butterfaß, Werkleiter Godel Beton (li.).
dass wir auf zwei Mischanlagen unseres zuverlässigen Partners vor Ort zurückgreifen konnten«, betont Stefan Schorn.
Wie wichtig es ist, ausreichend Mischkapazität und Material, dazu zählen Zement sowie Sande und Gesteinskörnungen, vorzuhalten, bestätigt auch Daniel Butterfaß, Werkleiter Godel Beton: »Damit keine Lieferengpässe entstehen, haben wir von vornherein für ausreichend Pufferspeicher beim Zement und bei den Gesteinskörnungen gesorgt. Gerade bei Großbetonagen geht es Schlag auf Schlag. Für vier Bodenplattenabschnitte wurden über 3 000 m³ Beton benötigt; dadurch mussten wir rund um die Uhr liefern«, berichtet Butterfaß.
Jeder Kran ist eine Baustelle für sich Dechant hat auf der Baustelle 18 Krane in Betrieb. Jeder Kran sei eine Baustelle für sich, mit einem eigenen Team, einer eigenen Betonage und eigenen Mengenanforderungen. Da gelte es, jeden Bauabschnitt punktgenau mit der benötigten Menge zu beliefern. »Das hat sehr gut geklappt. Dazu muss allerdings jedes Detail in der Lieferkette stimmen«, betont Butterfaß. So muss immer ausreichend Zement vorhanden, und die Leistung der mobilen Mischanlage muss entsprechend hoch sein, beispielsweise rund 135 m³/h. Ebenso müssen die Fahrer der Betonmischfahrzeuge und des Radladers auf engstem Raum manövrieren können.
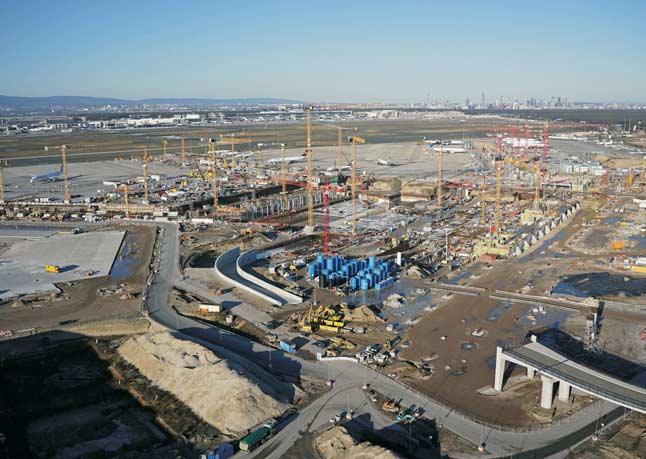
Nachschubsicherung mit Blick auf den Rhein-Pegel Letztlich müssen auch die Nachschubwege gesichert sein – hier kommt HeidelbergCement mit seiner Erfahrung im Sicherstellen von Lieferketten ins Spiel. So bezieht das Mahlwerk in Mainz Klinker und Hüttensande zur Herstellung der Zemente über den Wasserweg. Das heißt, hier gilt es, den Pegelstand des Rheins genauestens im Blick zu haben. Denn bei Niedrigwasser darf ein Schiff nur die Hälfte des sonst zulässigen Frachtgewichts laden, was die Transportkosten pro Einheit erheblich erhöht. Von daher muss HeidelbergCement stets den richtigen Zeitpunkt abwarten und bestellen. Gleiches gilt für die Lieferung des Zements, der aus den Werken in Mainz (CEM III A) und Lengfurt (CEM II ALL) stammt. t
) FRAPORT AG ( 2
Blick auf die Baustelle am 19. Mai 2020: Mit dem Bau von »Terminal 3« im Süden des Flughafens sollen bis 2024 zusätzliche Kapazitäten für etwa 19 Mio. Reisende pro Jahr entstehen.
FAKTEN

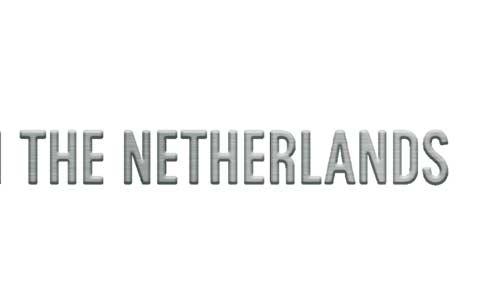
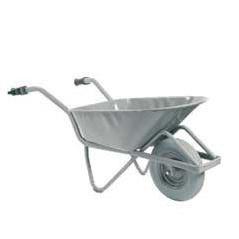
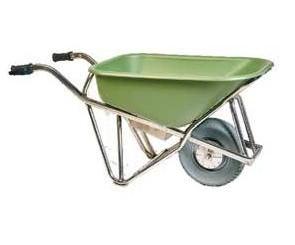

Objektsteckbrief > Projekt: Neubau »Terminal 3« am Frankfurter Flughafen > Hauptauftraggeber: Fraport Ausbau Süd GmbH > Bauleitung Abfertigungsgebäude (Gründung, Fundamente, Tiefgaragen, Hochbau):
Dechant Hoch und Ingenieurbau, Weismain > Betonherstellung: Godel Beton, Stuttgart > Zementlieferanten: HeidelbergCement, Werke Mainz und Lengfurt > Zemente: CEM III A (Lieferwerk Mainz), CEM II ALL (Lieferwerk Lengfurt) > HeidelbergCementProjektbetreuung: Dr. Klaus Felsch
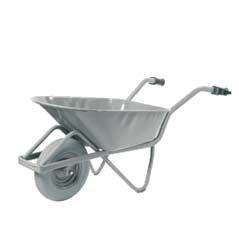




Liebherr 42 XXT beim Einsatz im Liebherr-Werk Ehingen.

t LIEBHERR – Nach der Vorstellung der Liebherr-Neuheit Powerbloc auf der letzten Bauma konnte die Autobetonpumpe 42 XXT mit der PowerblocPumpeinheit ihr Können inzwischen vielfach unter Beweis stellen. Seit zwei Jahren ist die Autobetonpumpe 42 M5 XXT bei der Betonpumpen-Union (BPU) in und um Ulm stetig im Einsatz. Zuletzt gar bei der Betonage einer massiven Bodenplatte im Liebherr-Werk Ehingen, wo Mobil- und Raupenkrane hergestellt werden.
Christian Klafszky, Geschäftsführer der BPU Ulm Um die hohe Qualität der Liebherr-Krane sicherzu stellen, ist eine hoch tragfähige Testfläche notwendig. Hierfür wurde mithilfe der Autobetonpumpe 42 M5 XXT eine Prüfplatte, bestehend aus rund 750 m³ Beton gepumpt. Die kompletten Betonagearbeiten konnten innerhalb eines Arbeitstages abgeschlossen werden. Vor Ort war zusätzlich mit der 37 XXT noch eine weitere Autobetonpumpe aus dem Hause Liebherr.
Vollständige Integration Als wesentlicher Pluspunkt der neuen 42 M5 XXT gilt deren neu entwickelte Antriebseinheit LiebherrPowerbloc. Diese soll sich insbesondere durch die vollständige Integration aller hydraulischen Schalt- und Messelemente auszeichnen. Dadurch werden zahlreiche zuvor noch notwendige Hydraulikschläuche sowie weitere Bauteile überflüssig. Die herausragenden Eigenschaften des neuen Systems sind allen voran die hohe Robustheit und Leistung sowie die Laufruhe im Betrieb.
Christian Klafszky, Geschäftsführer der BPU Ulm, ist von der Betriebseinheit nach rund eineinhalb Jahren Baustelleneinsatz überzeugt und bestätigt: »Was mir an dieser Maschine besonders gut gefällt, ist der ruhige und kraftvolle Betrieb der Pumpeinheit. Dies ist möglich dank des neuen Powerbloc-Systems.«
Ergänzt wird die Antriebseinheit durch einen neu konzipierten halbgeschlossenen Ölkreislauf, der sämtliche Antriebe permanent sowohl zuverlässig als auch kraftvoll mit hydraulischer Energie versorgt.
Dem von Liebherr entwickelten System gelingt nach Herstellerangaben damit die optimale Verschmelzung aller Vorteile der am Markt aktuell erhältlichen offenen und geschlossenen Kreise ohne deren jeweilige Nachteile. Infolgedessen könne das Ölvolumen erheblich reduziert werden. Derzeit ist der Powerbloc noch lediglich in Kombination mit der 42 M5 XXT Autobetonpumpe verfügbar. Liebherr arbeitet daran, das System in naher Zukunft für weitere Betonpumpentypen anzubieten. t

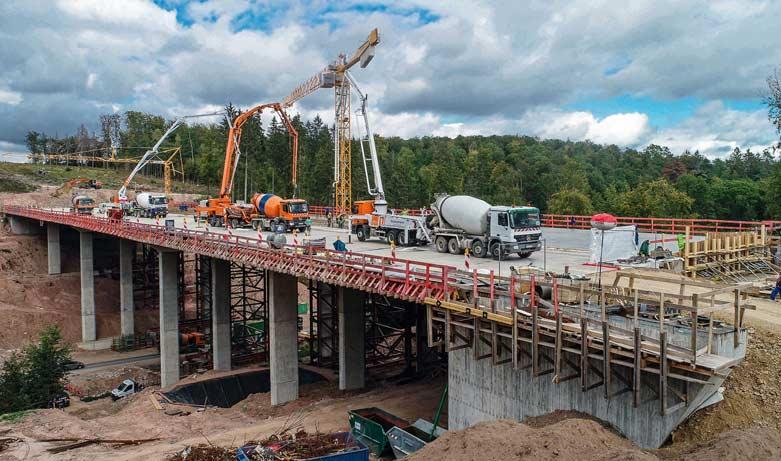
Ökologisch und schnell –der digitale Lieferschein
Auf der Baustelle wissen die Verantwortlichen genau, wann die benötigten Lieferungen eintreffen.
t PRAXIS AG – Die Digitalisierung – auch in der Baustoffbranche – ist nicht mehr aufzuhalten, auch wenn sie – wie in vielen anderen Bereichen – aus den verschiedensten Gründen manchmal nur schleppend vorankommt. Dabei ist nur ein wenig Mut gefragt und auch der Wille, eingefahrene Gleise zu verlassen. Dazu zählt auch das Lieferschein-Management. Hier sind noch viel Papier und manuelle Arbeit an der Tagesordnung. »Es geht aber auch anders – wesentlich komfortabler, schneller und vor allem ökologischer«, weiß Beate Volkmann, Vorstandsmitglied der PRAXIS EDV-Betriebswirtschaft- und Software-Entwicklung AG aus Pferdingsleben in Thüringen –einem der Marktführer in der Digitalisierung der Baustoffbranche.
Alles beginnt normalerweise mit einer Kundenanfrage nach Baustoffen. Dazu zählen hier neben Massenrohstoffen wie Sand und Kies auch daraus hergestellte Produkte wie Beton oder Mörtel. Danach wird ein Prozess mit etlichen Beteiligten in Gang gesetzt mit dem Ziel, dass die gewünschte Lieferung genau zu dem Zeitpunkt an der Baustelle ankommt, wenn sie benötigt wird. Beteiligt an diesem Materialabruf sind der Rohstoffproduzent (Lagermenge), der Spediteur (Transport) und der Kunde (Baustelle) und die jeweiligen Verwaltungen. Dabei können auch Betonwerke eingebunden sein.
Die Art und Weise der Abwicklung ist sehr unterschiedlich. Telefonate, Papierlieferscheine mit mehreren Durchschlägen, das Eingeben der Daten per Hand in den Computer sind teilweise mit schon vorhandenen digitalen Lösungen gekoppelt. Persönlich übergebene ausgedruckte Lieferscheine beim Wäger/Mischmeister, Wartezeiten der Fahrzeuge an der Baustelle bis zum Abladen, Unterschriften des Bauleiters, Übergabe der Papiere in die Verwaltung und manuelle Abrechnung der Aufträge und Speditionen – so sieht der Alltag in vielen Unternehmen der Branche aus.
Stapel so groß wie ein sechsstöckiges Haus Beispielsweise 280 000 Lieferscheine aus Papier – die für ein mittelständisches Unternehmen im Jahr durchaus üblich sein können – ergeben übereinander gelegt einen Stapel so groß wie ein sechsstöckiges Haus. 50 000 l Wasser, 2,5 t Holz und etwa 10 000 kWh Elektroenergie werden dafür verbraucht. Rechnet man den Aufwand für die gesetzlich geforderte Archivierung des Papiers in einem Archiv dazu, ergeben sich Kosten von etwa 1,50 Euro pro Lieferschein – ohne
Sich Betonstapelsteine vor Ort produzieren lassen
t MV-QUADRAT/HEDKE –Mitder selbstfahrenden Betonmischanlage Carmix3.5TT hat das in Mecklenburg-Vorpommern ansässige Unternehmen MV-Quadrat eine Lösung geschaffen, Betonstapelsteine vor Ort bei seinen Kunden zu produzieren. Zuständiger CarmixHändler für Deutschland ist das Unternehmen Hedke im fränkischen Veitshöchheim.

Mit dem CarmixSystem kann MVQuadrat ohne Rüstzeiten direkt bei Kunden Betonstapelsteine fertigen. Das Unternehmen ist mit seinem Angebot inzwischen bundesweit aktiv, um hochpräzise Schalungssysteme mit 100 % Wiederholungsgenauigkeit vor Ort zu produzieren. Bauseitig vorhandene RCMaterialien lassen sich ebenso verarbeiten.
Ausgangspunkt der Produktion ist der selbstladende Betonfahrmischer Carmix 3.5TT mit Wiegeeinrichtung. Der Mischer lädt die Aggregate, mischt per Freifallmischerprinzip und entlädt den Beton direkt in die Schalungen. Die geforderte Betongüte wird durch genaues Einwiegen der Zuschlagstoffe garantiert und per Chargenbericht dokumentiert.
Das Setzen der Betonstapelsteine mit einer maximalen Größe von 1 600 mm x 800 mm x 800 mm erfolgt nach dem Ausschalen mit einer von Steinweg für MVQuadrat gefertigten Hydraulikzange und einer Tragfähig
MV-QUADRAT
Das Setzen der Betonstapelsteine mit einer maximalen Größe von 1 600 mm x 800 mm x 800 mm erfolgt nach dem Ausschalen mit einer von Steinweg für MV-Quadrat gefertigten Hydraulikzange mit einer Tragfähigkeit von 2,45 t.
keit von 2,45 t. Die Betonstapelsteine werden beispielsweise bei der Errichtung von Schüttgutboxen, als Sichtund Schallschutzwände oder als Mauern von Fahrsilos eingesetzt. t