SOMIC Issue 5, 2022 Partnerships are thriving with customers throughout the USA States Of Success See what we have in store for PACK EXPO. pg. PACK2 ChicagoEXPOEdition Machine PrinciplesDesigntoLive by. pg. 8 US - EU pg.ExchangeTechnicianSuccesses.6
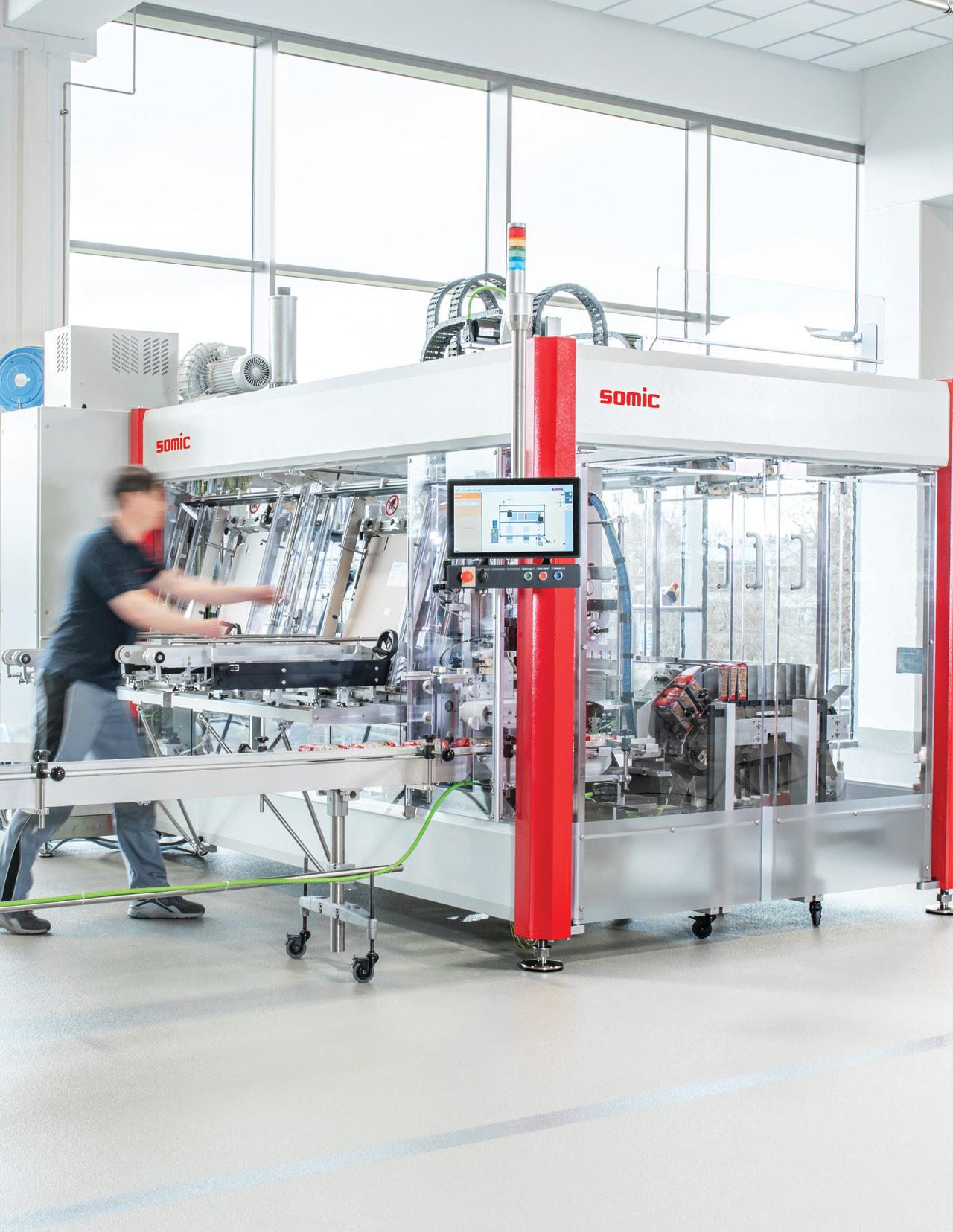
Retail Ready Magazine2
Minnesota, you learn to savor the summertime since the majority of the year typically includes cold temperatures, snow and ice. It's been warmer than usual this year and hard to believe PACK EXPO is only weeks away.
LETTER FROM THE CHIEF EXECUTIVE OFFICER
Another thing that remains red hot is the pace of activity at our office. We ended 2021 on a high note and it carried over into the first half of this year. Business is doing very well, with new orders and the increased amount of new equipment arriving from the SOMIC factory in Germany. We are fortunate to have a full and balanced schedule of Factory Acceptance Tests as part of our commissioning process for the remainder of 2022.

See the SOMIC 424 W3CaseWraparoundPackerinOurBooth.
Also keeping us at the top of our game is the amount of preparation required for PACK EXPO. We are in the process of finalizing our list of what needs to be done for the show in Chicago. Countless hours have been devoted to making sure everything runs smoothly all four days, and the proof will be what you see demonstrated in our spectacular new booth on the upper floor of the Lakeside building.
In
Somic Packaging, Inc. Invites You to use our Comp Code: 29W83
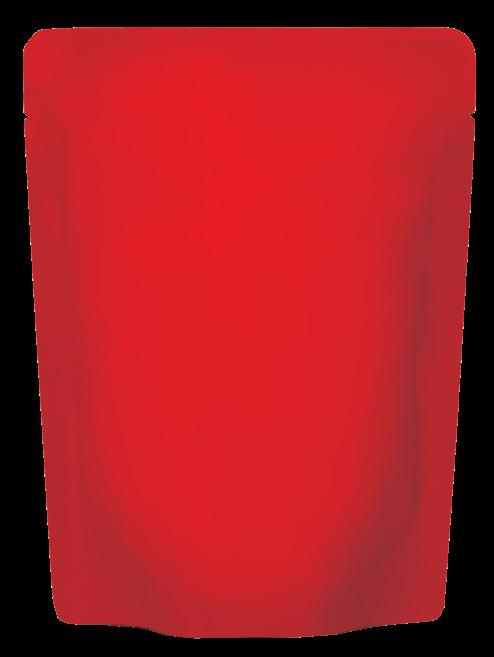
The Quest for Improvement Continues at PACK EXPO
In our last issue, I mentioned we were beginning the process of implementing some changes to our business model. We made significant progress in the last eight or nine months, and you have my word that we will challenge ourselves to better
PACK EXPO Oct. 23 – 26, 2022 Chicago, IL Booth LU-8135
Retail-Ready Magazine is published by SOMIC America, focusing on the Retail-Ready industry.


500 Lone Oak Road Suite Eagan,#200MN p.fox@somic.ussomic-packaging.com+1.651.419.605055121
somic-packaging.com 3

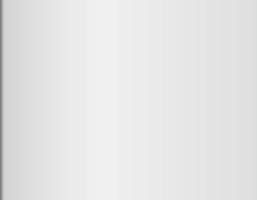
Follow us on LinkedIN for updated material and conversations.
Officer
Produces up to 25 cases per minute Simple.

You won't find a more efficient automated case packaging system. Smooth.
See live at our booth.
serve you as our company expands. We continue to introduce new principles and guidelines that raise the bar, so we can do even better.
We started a new Service Technician Exchange Program and the first wave of sharp, technicalsavvy people have already arrived.
Our newest technology ensures consistent, trouble-free operation. Space-Saving.

I mention this because of our story about packaging machine design principles. I travel several times a year to visit our headquarters and factory in Germany, and it’s always interesting to see what some of the customers there are doing with our equipment. It certainly provides a new perspective and helps keeps the ideas flowing for what’s possible for our North American customers.
I hope you enjoy reading this issue. From time to time, I get requests from industry magazine editors to comment on stories they are preparing that are related to the
To help with this situation, we are in the process of hiring more staff. Three management level people joined us in August, and we also hired a pair of top-notch sales professionals. Stacy Schmeiser is handling our western region and Rosann Bagin is our new Midwest representative. Both will be in the booth at PACK EXPO.
latest in automated packaging. It often reminds me how our early experience with retail-ready machinery in Europe, especially with the tray and hood designs, has put SOMIC ahead of competitors here in the U.S.

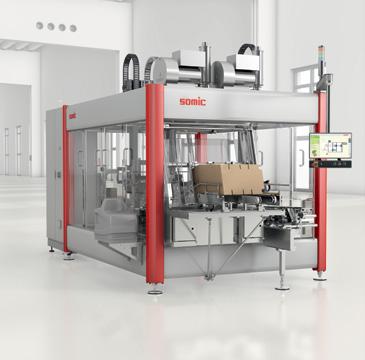
Purchasing packaging machines is a big investment. Finding the right answers starts by asking the right questions. Begin the process with the SOMIC Packaging Buyer’s Guide.
Based in Eagan, MN, SOMIC Packaging manufactures advanced mechatronic case-packing systems that collate, unitize and load cartons, trays, retail-ready packages, and wraparound cases.
See how SOMIC can bring new efficiencies to your packaging line.






Wraparound Packer SOMIC 424 W3 for single-component packaging
They talk about equipment, their goals and thoughts on living in America that I think you’ll find That'sinteresting.itfor now. I hope to see you in our booth (LU-8135) at McCormick Place in PeterRespectfully,Chicago.Fox,ChiefExecutive
One look at our list of installations taking place between now and the end of the year will give you a better understanding of why the office coffee pots are rarely empty. Every week is already spoken for with a machine arriving, going through the commissioning process, or having customers on site for their Factory Acceptance Test.
Make the most of your floor space with a compact footprint design that assures a user-friendly experience.
Download the SOMIC Buyer’s Guide and see us at PACK EXPO.

NEW MARKETS 4 Retail Ready Magazine
EXPOcontinuecurrentlyHere’sconfigurations.”Retail-Readyarundownofwhatistakingplaceandwillinthelead-uptoPACKinChicago:
2022 Is a Year of Many Growing Partnerships
Several Midwest-based cheese manufacturers will be accepting delivery of a variety of 424 series machines. One ordered a thermoformed tray cover machine with a wraparound carton feature. Another chose a machine to handle stand-up pouches of shredded cheese that will group them in pairs before being fed into a handle applicator.
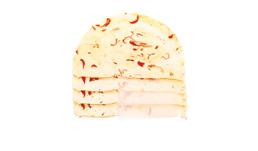
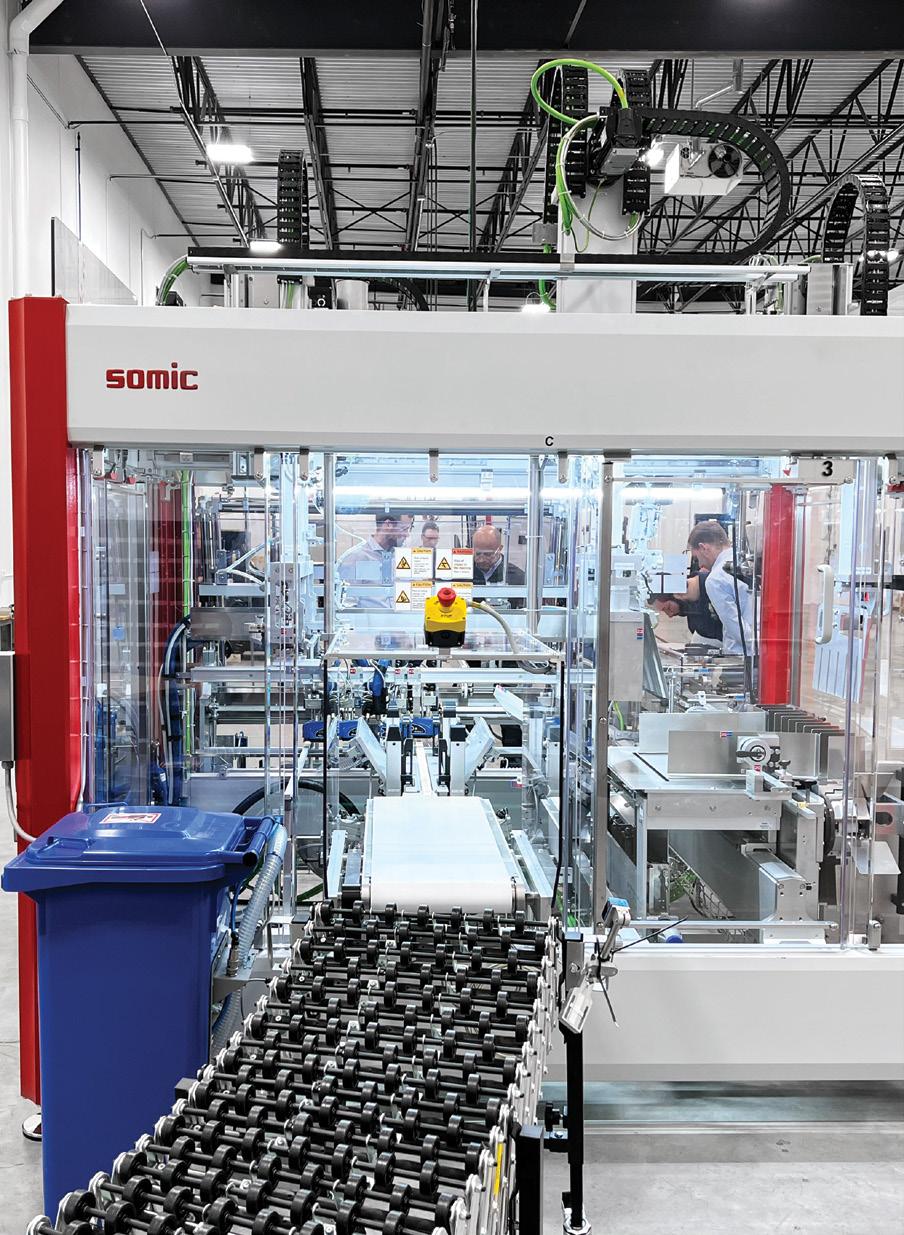
The
“The fundamental driver for our growth the last few years – and especially now – is having the ability to configure our standard 424 machine platform to the unique needs of our customers,” said Chief Executive Officer Peter Fox. “We are using standard functional groups to achieve these requirements, not a new, one-off design. This gives our customers and us the flexibility to change for future needs. Our machines also can run standard case configurations to adapt to the demand for
first half of 2022 was easily the most active and transitional period of time since we moved to Minnesota, and the pace has not slowed. Our Installation team is hard at work on a large number of projects, and the excitement keeps on coming. Every time a FAT is completed and the machine is shipped to its new owner, another is coming through our door from Germany.
FAT for GOYA Foods at SOMIC Packaging is in Minnesota.
Small Spaces, Big Results
Hardy Beverages is a Memphis-based maker of healthy lifestyle beverages. Their products include hydrogenfused and enhanced water for the physical well-being of both humans and canines. The 424 case packing machine they purchased is on schedule to be delivered soon.
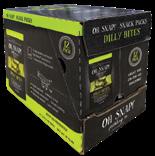
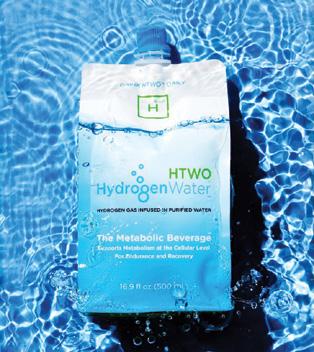
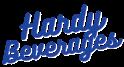
“The main reasons for these specific cheese installations are flexibility and our small footprint,” continued Fox. “These machines are used in very small production areas and it was a critical component. The flexibility to add future formats played a major role too.”
The Ferrara Candy Company in suburban Chicago has ordered three new 424 T2(D)+ machines to handle pouches of gummy candies. These are the same series of machines that Ferrara installed three years ago. Those four case packers run 23-25 cases per minute and produce over 125 pounds of Trolli Sour Bite Worms every minute. The new machines are expected to ship in November.
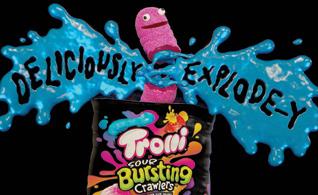
OH SNAP! is the central Wisconsin company that has employed a trio of SOMIC retail-ready machines since 2019. A division of GLK Foods in Appleton, they have utilized 424 W3 wraparound case packers to manage their supply of refrigerated brine-less picked vegetables. These single-serving items are so popular they recently added a fourth system to handle increasing consumer demand, since the first three machines were previously running 24/6 to produce over two million packages per week.
We just completed the FAT on the unit for LT Foods at the end of July. The consumer food company, regarded as the top specialty food brand in the U.S. and the leading processor of rice in India, sells products in over 60 countries.
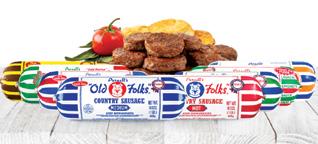
Weber, Inc. is a German company that we are working with. Weber is providing an automated system for a sandwich manufacturing line being installed at a West Liberty Foods facility in the Midwest. West Liberty is an Iowa-based producer of prepared meats for large national foodservice and grocery retail customers. Three variations of the 424 series have been ordered, with the first scheduled to begin the commissioning process in the fourth quarter.
One of the world's largest food service manufacturers has purchased their third machine, a 424 T2+ version for thermoformed packages of cracker cut cheese in wraparound cases. The Midwest company is a leading producer of packaged consumer foods, and commissioning of the machine is expected to be completed soon.
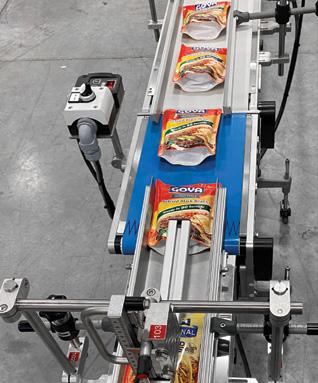
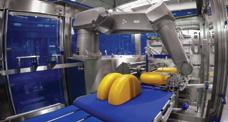
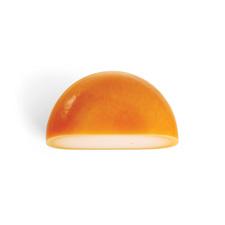
The Future Is Bright
Delivering On Higher Demand
Purnell’s Old Folks Country Sausage in Kentucky will be receiving their machine in November after it is demonstrated in our booth at PACK EXPO in Chicago. Located on the eastern outskirts of Louisville, it’s been a family-owned and operated company for more than 70 years. The company’s popularity expands way beyond the South. They produce over 100,000 pounds of sausage daily to satisfy demand from grocery store and restaurant clients.
somic-packaging.com

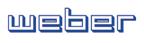
Several orders have already been received that will keep our momentum going full tilt to start 2023. This includes two new machines for an iconic brand company that manufactures food and beverage products. One is a cartoning machine for food pouches and the other is a case packer for stand-up squeeze pouches.
5
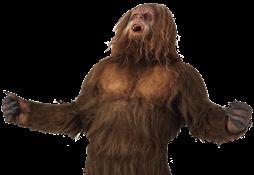
Two machines are being prepared for Jack Link’s . The market leader in the meat snack/jerky segment, Jack Link’s ordered a 424 Duplex cartoner and a standard 424 W3 wraparound case packer after experiencing success with a SOMIC case packing system at its Iowa processing facility. The new machines are expected to be delivered to their plant in Minong, Wis. later this year.
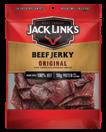
Sweet & Satisfying Productivity
GOYA Foods Engineering Director Disney Arrubla said they have completed installation of their new 424 T2+ case packing system at the Secaucus, N.J. facility. He expects the machine to begin production this month and it will handle wraparound case packing of both stand-up pouches and cartons. GOYA is the nation’s largest Hispanicowned food company.
As part of the Service Exchange program, technicians learn the company philosophy and become familiar with the different approaches to current projects.
Retail Ready Magazine6GLOBAL PERSPECTIVE
over three German colleagues: an Operations Ramp Up Manager, an Installations Manager, and an Engineering Manager.”
“They also learn about our sustainable practices, and how we reduce waste, from saving resources and raw materials to optimizing equipment performance,” he said. “Our compact equipment footprint saves space, which is a big customer advantage. All of the machines run more than one format, so operators need no tooling for changeovers. It's fast, easy, and saves the customer plenty of time.”
“We strive for perfection,” points out Benedikt Englbrechtinger, the new Manufacturing Ramp-Up Manager who arrived in Minnesota last February. “Our goal is to build a perfect machine for our customers. Everyone must be on the same page and have the same way of thinking. We use defined processes, regulations, and standards to achieve our goals.”
Apprenticed in packaging technology at SOMIC Germany, Senior Engineering Manager Thomas Hadersberger made the trip to Minnesota in January 2020. While training in Germany, he realized everyone and everything at SOMIC is committed to building customized, end-of-line packaging equipment incorporating the latest technology.
Most importantly, the technicians learn how to build the case packer models with durability and depend ability for long production runs, go ing over each system, component, nut and bolt, microchip, and procedure.
Customers Benefit from Technical Expertise without Borders
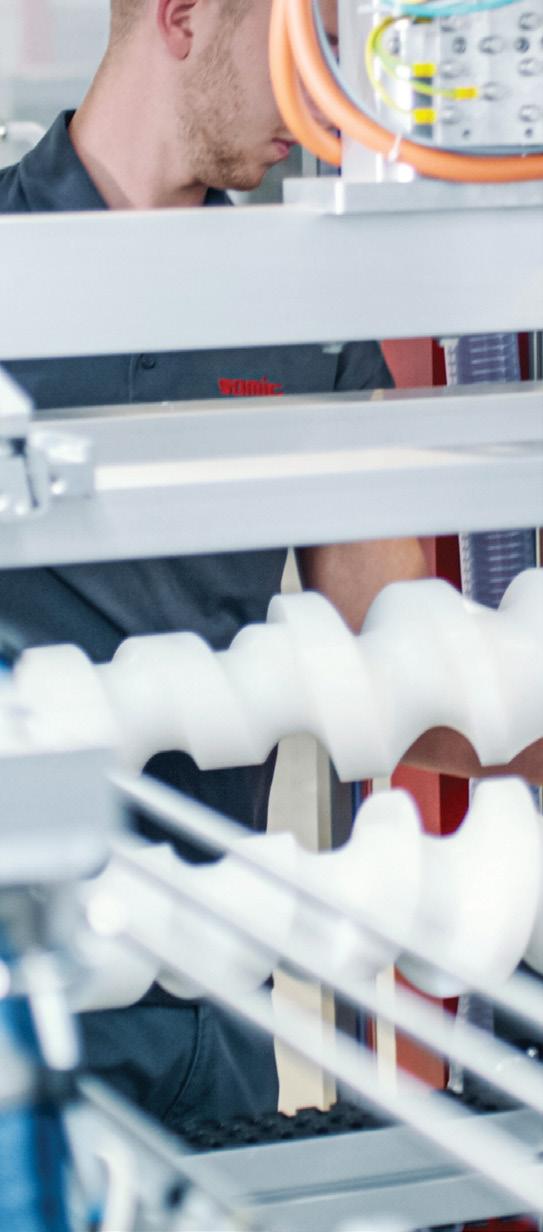
“That’s always in the back of my mind,” Thomas emphasized. “Our team builds machines with the most advanced technology. I enjoy developing this equipment because no two machines are alike. We adapt them to everything the customer requires for automatic case erecting, loading, tray forming, and wraparound casing.”
Striving for perfection
Since we last talked with him in the third issue of Retail-Ready, he has taken on additional responsibilities in Eagan, including those for After Sales
Our
growing customer base means technical services have never been more essential. The recent Service Technicians Exchange Program we have established with SOMIC Germany provides in-depth, cross-training support to make our mechatronics packaging technology seem deceptively simple. Dedicated to continuous improvement, it covers electrical and mechanical engineering, logistics, mechanical and technological installations, and project management. Three people involved in this program shared their thoughts on a wide range of topics.
“SOMICbusiness.Packaging is growing substantially and commissioning machines here meant we needed more support,” he explained. “We hired Minneapolis-based Service Technicians, an Engineering Manager, an After Market and Sales Engineer, and a Logistics Coordinator. We also brought
Working with SOMIC’s Operational Team, Thomas addresses customer needs and technical and design questions and talks with them about their project goals. He supports the quality assurance team, troubleshoots throughout a project’s lifecycle, assists with installation, and also handles customer requests after the sale with customer training and ongoing technical support.
EnglbrechtingerBenediktHadersbergerThomasRuhland somic-packaging.com 7
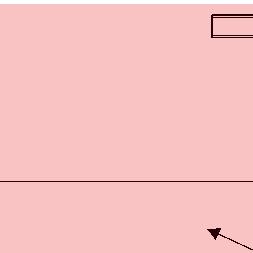
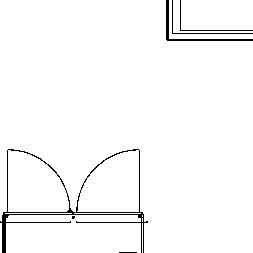
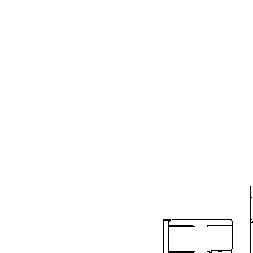
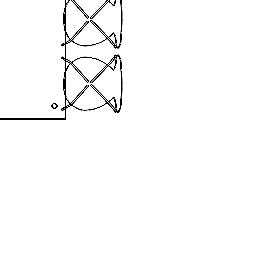
"It’s not easy to fulfill all customer needs. But we work with them as a team to develop the best choice. It’s rewarding to find new ways of using our technology to meet customer challenges and increase system performance. We want to find what’s best for each application as smoothly and easily as possible.”
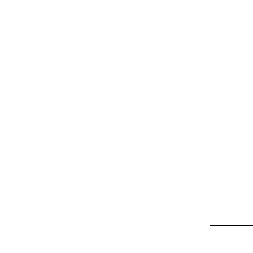
“I joined SOMIC because it’s one of the best packaging machine builders. I always wanted to work with high-tech machinery. My job is exciting and always changing. I love working for a company that builds high-quality, precision packaging equipment for customers all over the world, ensuring their satisfaction.”
Lukas
currently share a house and travel together on weekends, so they learn about things here. The Service Exchange is a two-year program, so I will soon return to Germany. I highly recommend this program opportunity and have cherished my time in BenediktEagan.”andLukas like the Exchange program for its depth of learning experiences. When not working, Lukas plays soccer and travels to new places to learn about different cultures. Benedkit plays music, goes hiking, works out and also enjoys traveling.
theContactteam 1.847.915.9872at
“They like the U.S. so much,” Thomas adds. “I enjoy working with them. We
“It’s interesting work because each machine is custom-built according to each customer’s specifications. All of this confirms the collaboration between our team and the customers is highly effective. Our teams do their jobs well."
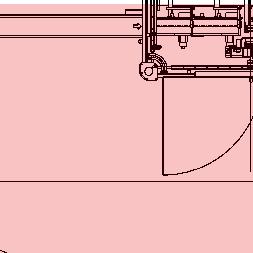
Being in a different country with an unfamiliar culture and language can be a challenge.
Benedikt Englbrechtinger
“My day consists of providing customers with remote support, training other service technicians on how to commission a theandBenedikt“ISOMIC.industrywereinterestedWhilemachinecomponentsandcase-packing/end-of-lineSOMICmachine,testingallsystemelectricalandfunctionsbeforetheisreadyforthecustomer.”heandBenediktwerealwaysinengineering,theyunfamiliarwiththepackaginguntiltheybeganworkingatwasintriguedimmediately,”remembers.“It’sexcitingdynamic.Nodayisthesameasothers.”
He now tests and assembles the machinery and occasionally visits U.S. and Canadian customers.
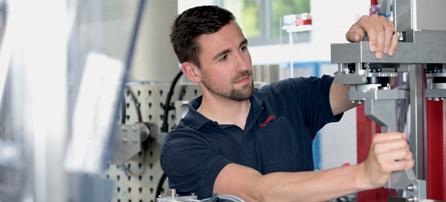
Thomas said the technicians like working and interacting with U.S. and Canadian customers. “Most already have SOMIC equipment, so they’re familiar with it.”
The other team member is Installations Manager Lukas Ruhland, who arrived in Minnesota earlier this year at the same time as Benedikt.
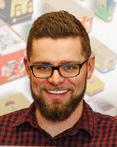
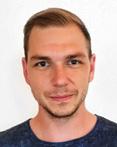
“This gives me a changing work schedule that’s never boring. We are a well-organized, family-owned company with plenty of growth opportunities. I like learning by doing and the various training sessions. I assemble machines and ensure they’re ready for the Factory Acceptance Test (FAT). I help to ensure that the machines pass all required tests and to make the onsite installation as smooth as possible. I also deal with capacity planning (people, space, dates) to properly implement and align our internal processes with departments in Germany and the U.S. "
When not working, the service technicians learn a lot about life here in the U.S., familiarizing themselves with their new location, seeing the sites, traveling to different states, and experiencing their many geographic differences.
Working with SOMIC since 2017, Benedikt was an industrial engineering student in Rosenheim, Germany, when he moved to Eagan as a project manager. “The position was a good opportunity for me because it required technical experience and interpersonal business communications,” he says. “We aim for maximum customer satisfaction, which is our highest goal.”
Lukas began his career in 2013 with an electrician’s apprenticeship at SOMIC in Germany. He was promoted to Field Service Technician when he came to the U.S.
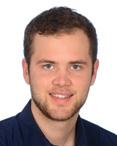
Managing projects throughout their lifecycles and ensuring they stay on schedule and budget can be challenging. But Thomas said they are up to the task with dedication, creative skills, and attention to detail that show in the resulting equipment design layouts.

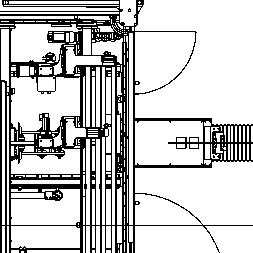

New adventures
“But the North American customers have been great,” Benedkit summarized. “Assembling the equipment and implementing the FATs is so rewarding and gratifying. We have recently completed two successful FATs with very happy customers. It’s interesting work because each machine is custombuilt according to each customer’s specifications. All of this confirms the collaboration between our team and the customers is highly effective. Our teams do their jobs well."
COLLABORATIONLEADSTOPERFECTIONINSOMIC’SMACHINEDESIGNPRINCIPLESPRINRI CUS TO MIZABLE FUTUREAUTOMATIONREADYTURNKEYMANUALRIGID MIZABLE FUTUREAUTOMATIONREADYTURNKEYMANUALRIGID Retail Ready Magazine8CUSTOMIZATION & COLLABORATION SSIZEPEED EFFICIENCY


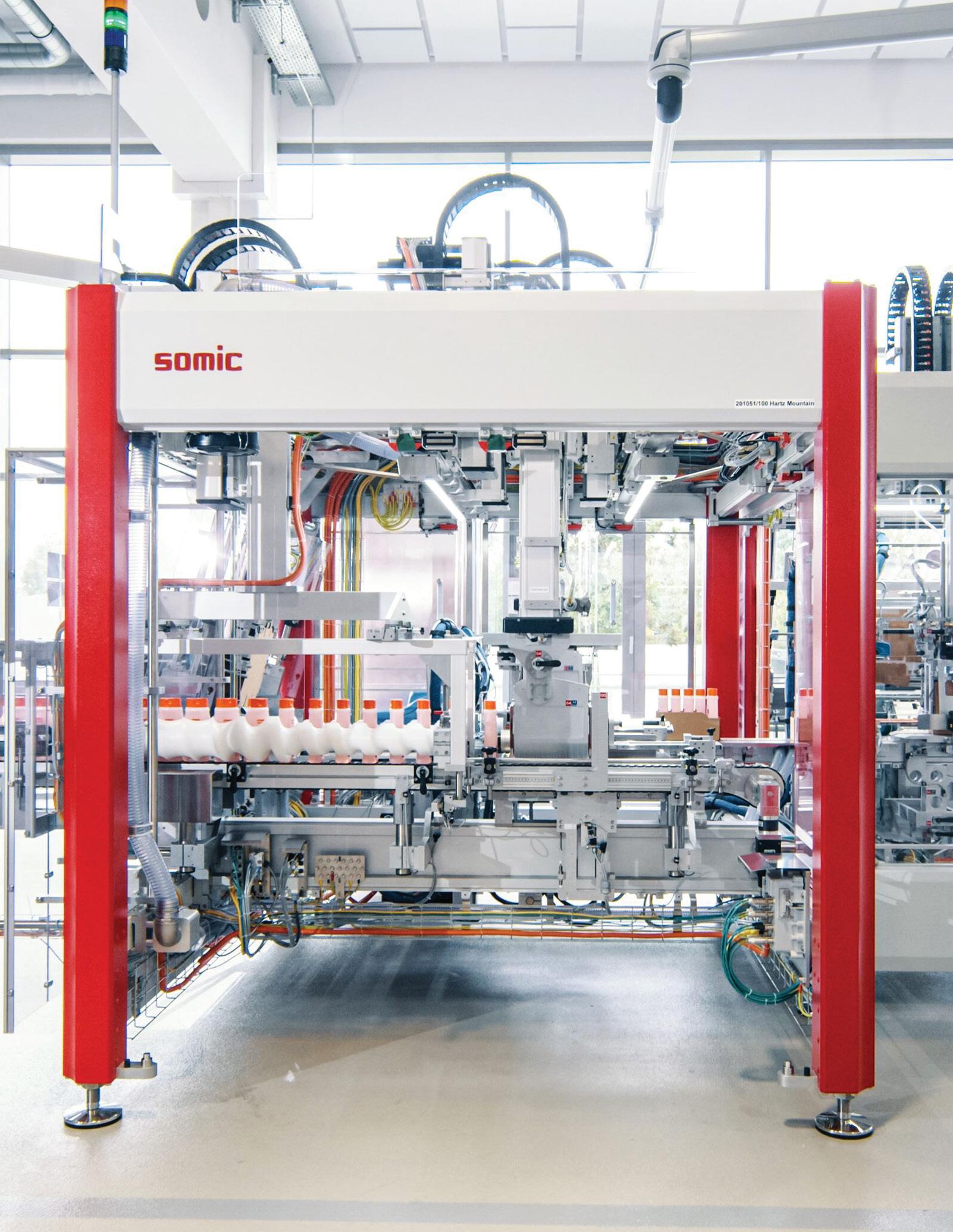
9
There’s no such thing as a minor detail .”
Roswitha Aicher, SOMIC Manager, Systems Engineering
operations. Customizing a case packer to a product, a package and a production line takes careful planning, flexibility and coordination. That’s where SOMIC makes a difference.


Equipment options that deliver solutions

Mostinisagreemanufacturersthatautomationcriticaltosurvivaltoday'sproduction

Designed for multi-component packaging, the SOMIC 424 TD Tray/ Cover Packer collates, groups, and loads products with ease in
With the changing work environment today, manufacturers want fully automatic case packing equipment that saves time and labor while allowing them to reach higher product outputs. A SOMIC fully automatic case-packing system provides these advantages and more. We have been designing and manufacturing high-end packaging machines for food and consumer products since 1974. Our passion for perfection in equipment design and implementation has established us as a preferred global partner in the end-of-line automation market.
When customers convert from manual to automated case packing, we often recommend the SOMIC ReadyPack as a starter system. Suitable for retail-ready applications, ReadyPack masters standard packaging tasks and can be used for single-component packaging, as a tray packer, or as a wraparound case packer. A costeffective option that collates and packs products in open cases, trays, wraparound cases, folding cases, or display cases, ReadyPack occupies a minimum of space and can be delivered and installed quickly. Best of all, it's economical yet meticulous, providing a high return on the investment compared to manual packing methods.
"
such thing as a minor detail," confirms Aicher. "Customers often come to us with an existing shipping case blank, so we must ensure the machine will work smoothly with it, and perhaps with other package blank configurations. We evaluate all product and packaging criteria with the customer and determine if the packaging process will be straightforward or more complex, what the operation's needs are and what the environmental needs are."
• How can the optimum packaging sequences be achieved in the machine?
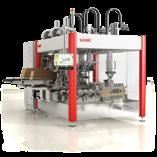
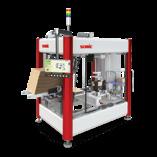
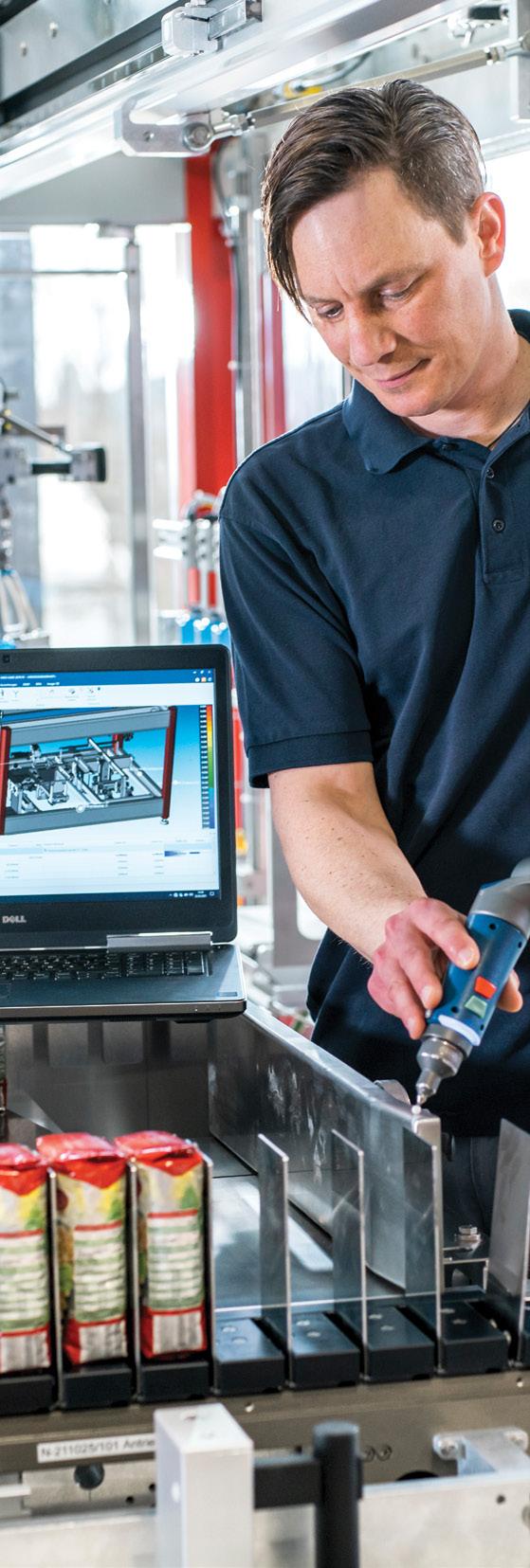
"There'sfuture?no
modules include 424 KA, for open-topped containers and trays (with or without cover flaps), shipping cases and cartons with mechanical locks and flat or stackable crates, the 424 DA Box Coverer, and the 424 VM Closing Machine for wraparound cases and folding boxes. We also manufacture a choice of product handling and transport devices.
• Will the machine run several containers and product configurations or just one?
In the design stage, many questions are asked including:
• What energy, environmental, and maintenance requirements are there?
Among other things, we established effortless formability of the case blank in the folding station, precise folding of the case/carton flaps as the package travels through the machine, the optimum number and length of glue dots, and secure sealing of the flaps. "We perfect these
• Will the system need to adapt to changing circumstances in the
SOMIC considers several factors when developing turnkey equipment for high-volume applications. The shipping case gives the retailer or consumer their first impression of the product and its manufacturer. SOMIC adjusts case dimensions and functionality as needed when configuring the machine for efficient palletizing, product protection, attractive presentation on store shelves, and easy shipping case handling and opening.
open-topped cases or trays with an outer cover. The compact size of the 424 TD is a bonus for existing production facilities with little room at the end of the line. Equipped with individually produced format tools, the 424 TD provides maximum flexibility for various product and case types at speeds up to 600 products per minute (depending on the product) and up to 25 cases per minute. The 424 also comes in a Tray Packer model, a Wraparound (424 W3), and a Cover/Tray Packer (424 Case-erectingDT).
424 TD 424 KA
Retail Ready Magazine10
• Does the case fit the desired packaging task and future tasks?
For large volumes and high speeds, the sophisticated SSL 800 Bar Packaging Machine packs up to 800 products per minute. Ergonomic, user-friendly, and intuitive, the SSL 800 offers transparent safety doors for viewing the entire packaging process, precise gluing, and accurate folding while its gentle carton-loading components present products perfectly on the store shelf. Incorporating advanced technologies and mechatronic functional blocks developed and constructed in our factory in upper Bavaria, each case-packing system configuration is designed to the customer's specific product and packaging requirements. Collaboration between all SOMIC teams and the customers’ teams is crucial. "Coordinating with our customers throughout the selection and development processes ensures their case-packed products arrive to retailers safely and in top condition," says SOMIC's Roswitha Aicher, Manager, Systems Engineering.
Every detail matters
for installation at the customer's property and ensures a smooth transition for immediate production capability. Years ago, the first look at a new case-packing machine was often in a face-to-face visit. Now, they can evaluate the machinery by an online appointment.

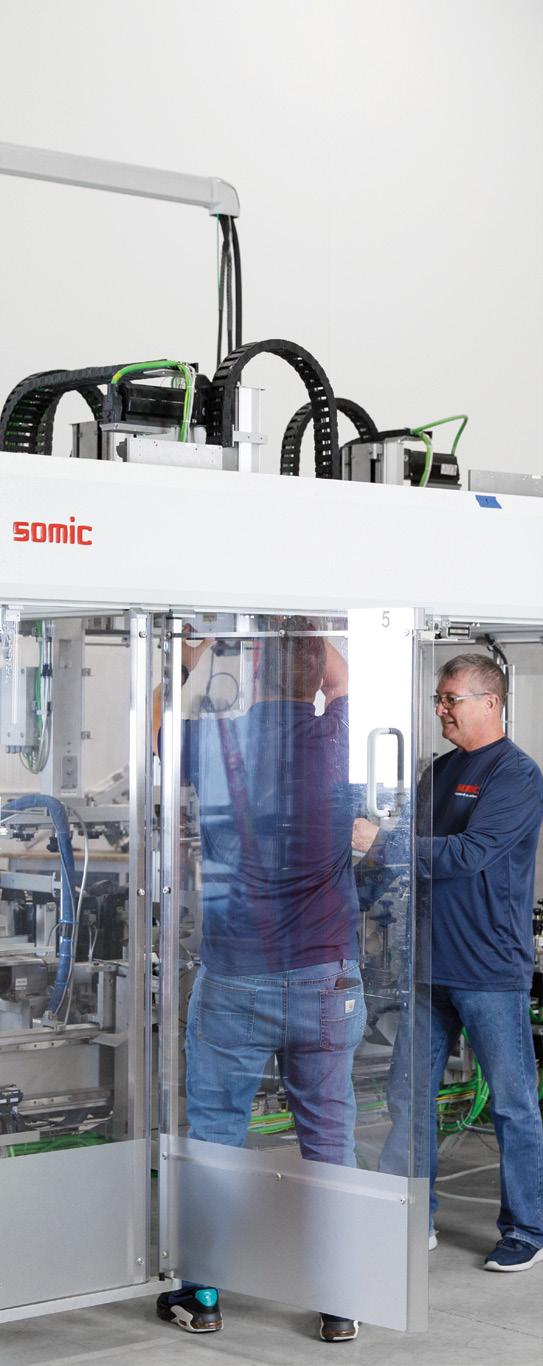
Our FAT reviews each component and tool step-by-step by video. "We show the customer all the packaging functions," Aicher says. "That way, they get an accurate impression of the test procedures before the machine makes its way to their production facilities."
See our versatile case packing systems at PACK EXPO in Chicago - booth LU8135 - October 23-26.
Aicher indicated that an approval committee confirms that the machinery meets all customer requirements and completes all safety and quality tests to customer satisfaction before the customer selects their desired time of delivery.
Shortly before delivery, SOMIC's online Factory Acceptance Test (FAT) takes place. The FAT process validates that the equipment is ready
In addition, our team is onsite to commission the machine at the customer's facility. Individual training programs and instructions can be organized for customer personnel so that everything runs smoothly from the first day of production. These procedures may sound complicated, but they can eliminate any confusion and production downtime later. "The result is dependable, consistent machine performance for our customers’ needs,” says Aicher. “It's a win-win all around."
and much more when preparing the final system, coordinating with our customers so they get what they want," Aicher adds.
The crucial last steps
Testing leads to perfection
somic-packaging.com 11
Or do a virtual tour user_upload/messewww.somic-packaging.com/fileadmin/at
Factory Acceptance Test (FAT)
can be conducted face-to-face or online.
Depending on the product and packing/grouping specifications, the team extensively tests and evaluates every machine component selected. This ranges from feeders, ejectors, and collators to guides, pickers, grippers, and transfer devices, all the while monitoring their performance before the packaging machine ever leaves the SOMIC factory in Germany. Tolerances are set for all product and package dimensions, taking any deviations into account.
Joint meetings between the SOMIC and customer teams usually occur in an idea-generating workshop atmosphere. Our team performs meticulous technical analysis and creates component samples for a high-quality result. "Many customers ask for advice on their applications," Aicher recalls. "One asked to pack potted herb plants in cartons, which is not the easiest application. We developed a modular machine that was both flexible and durable."
Whether you desire a standard wraparound box, an eye-catching shelf display, or a multi-piece shipping container, SOMIC has you covered!
For realistic production simulations, we use the RealSource computerized virtual Simulation Development system. It combines the original packaging machine controls with a lifelike 3D construction model to produce superior results. As the equipment design nears completion, internal tests continue to be performed in a realistic production scenario with the original products "to perfect the results," Aicher notes.
Functional tests of the mechanical and electrical components, a "dry" cycle run, and format changeovers precede more specific case-packing format changes and final test runs of the system with packaged products.
Download the SOMIC Buyer’s Guide and see us at PACK EXPO. Purchasing packaging machines is a big investment. We want to ensure that you have everything you need to make the best decision. We’ve created a Buyer’s Guide to help you identify the most important criteria for selecting the right end-of-line equipment. It also contains information about your available options.
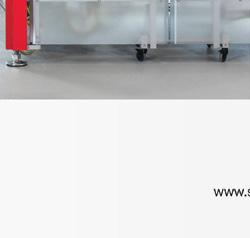
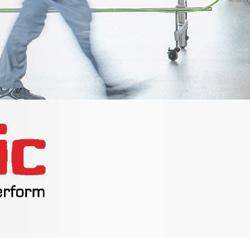
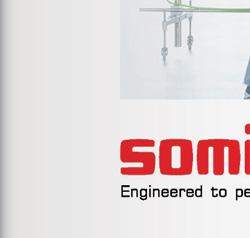
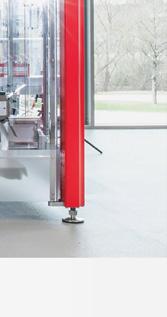
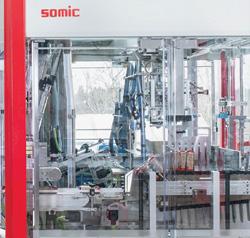
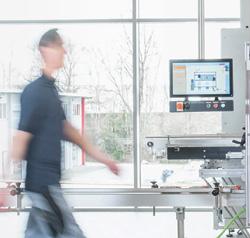
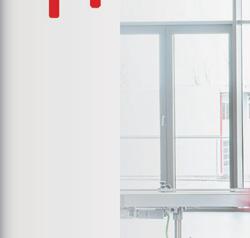

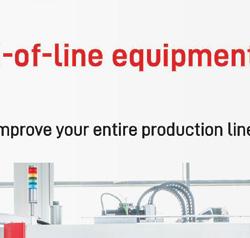
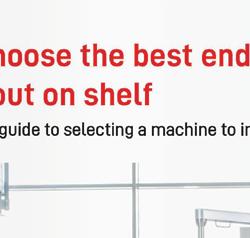

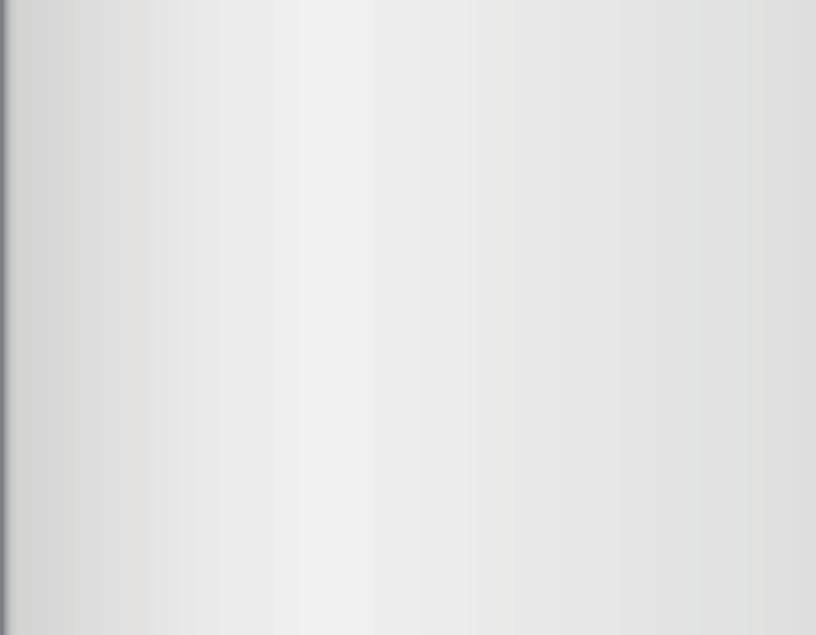
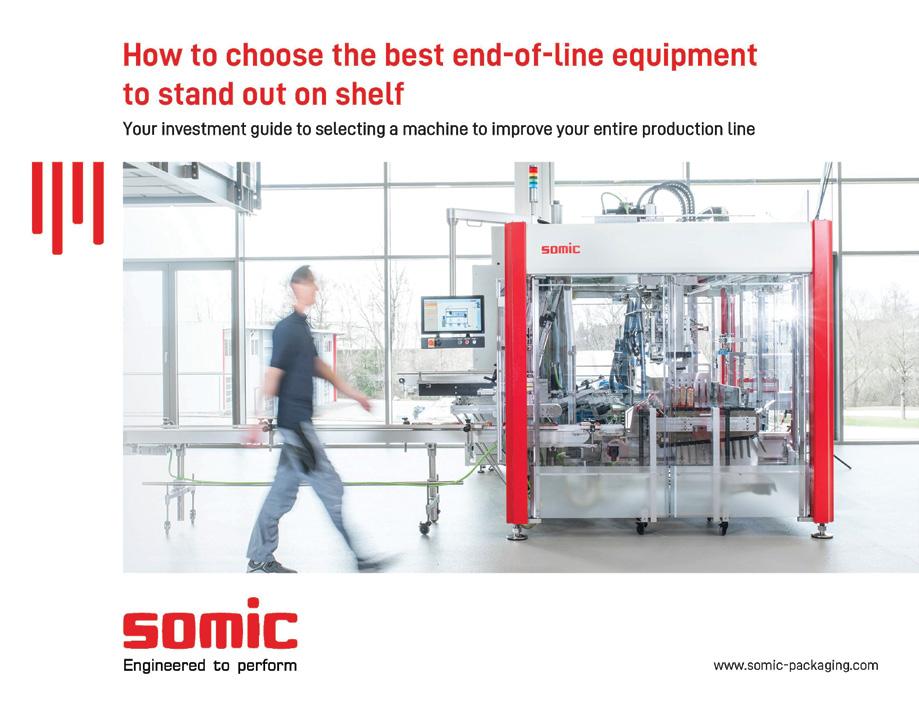
See SOMIC Packaging in action at PACK E XPO Chicago, booth LU-8135 at McCormick Place. Learn more by calling 1.847.915.9872 or visitYoursomic-packaging.com.searchfor
the right equipment begins with this guide.
