HARDY BEVERAGES PREPARES FOR TAKEOFF
Memphis Beverage Customer Upgrades to Automated Packing — pg. 10
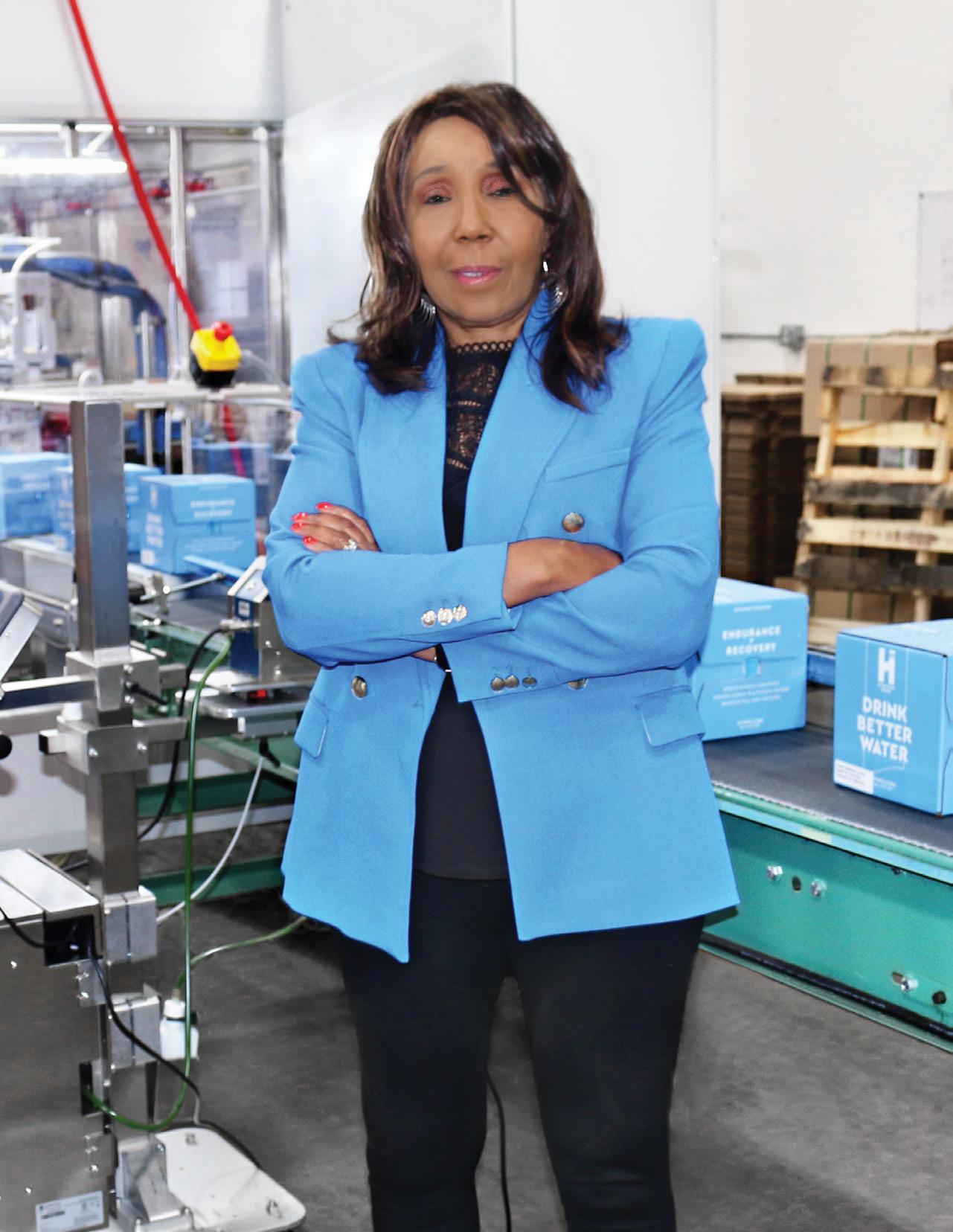
SOMIC expands to Asia with new Thailand facility pg. 2
Learn about the new SOMIC ICATT Apprentice Program pg. 13
Memphis Beverage Customer Upgrades to Automated Packing — pg. 10
SOMIC expands to Asia with new Thailand facility pg. 2
Learn about the new SOMIC ICATT Apprentice Program pg. 13
“If what we are doing is not a direct benefit to our customers, then we should not be doing it.”
The weather in Minnesota this year has been anything but normal. Some saw the warm winter weather as a positive, unless you happen to be a snowmobiler or a downhill skier. It’s really all a matter of perspective.
Perspective also applies to business. After working our way through the global lockdowns and followed by the resultant supply chain crisis, the lesson learned is one needs to be adaptable. At SOMIC, we are fortunate that our company was founded with adaptability at the very core of our being.
For quite some time, SOMIC has been applying this principle of adaptability in all that we do. Ten years ago, when we established SOMIC Packaging as the first international subsidiary of SOMIC Verpackungsmaschinen GmbH & Co. KG in the United States, we embarked on the journey of
providing the most sophisticated — and adaptable — automated casepackaging systems to the North American market.
Over the course of the past decade we have listened, learned, and adapted to the unique requirements of this market and most importantly, our customers. As a result, our company, machines and services have evolved into what has become a reflection of our customers’ requirements. As I have said more than a few times, if what we are doing as a company is not a direct benefit to our customers, then we should not be doing it.
The most obvious of the SOMIC changes is the introduction of the next generation of the SOMIC case packer, the 434. This machine platform debuted at Interpack in Dusseldorf, Germany in May 2023 after we listened to the needs of our customers: a desire for faster changeovers; easier accessibility to the machine; and a decentralized control option in Rockwell, all while retaining the multi-format flexibility that has made us the leader in Retail Ready Packaging. The most important feature that we had to retain in this new platform was adaptability!
Based in Eagan, MN, SOMIC Packaging manufactures advanced mechatronic case-packing systems that collate, unitize and load cartons, trays, retail-ready packages, and wraparound cases.
We went a step further by unveiling the CORAS (Carrier-based Orientation Rotation Arrangement System) collection and grouping system, and integrating it into the 434 wraparound case packer. This product collection, distribution, and grouping system provides the opportunity for SOMIC to package variety packs or multi-component cases or cartons in an almost endless array of proportion or orientation. The system utilizes multidimensional, controllable magnetic levitation technology, which demonstrates our ability to not only embrace new technology, but to apply it to real-world applications.
SOMIC’s latest global adventure now includes the addition of our Asia-
500 Lone Oak Road Suite #200 Eagan, MN 55121
+1.651.419.6050 somic.us
info@somic.us
Follow us on Linkedin for updated material and conversations.
Pacific headquarters in Bangkok, Thailand. Last December, we celebrated the grand opening of the facility which houses the APAC sales team, service group, and electrical and mechanical engineering staffs. These headquarters will serve as the Asian hub supporting the region. It can now be said that SOMIC never sleeps at any given time, while busy serving our global customers.
SOMIC Packaging in suburban Minneapolis will soon be moving into a new production facility in nearby Inver Grove Heights. It will increase our physical footprint in the United States by five times, and will enable our U.S. team to assemble the 434 domestically. The extra space will also provide added warehousing of a more complete inventory of replacement parts for the growing installation of machines throughout North America.
This investment demonstrates the SOMIC group’s commitment to our fastest growing global market. The new headquarters and additional engineering and technical staff will enable us to continue to grow while offering unmatched customer support and service. More, Better, Faster!
Earlier I mentioned “perspective”. We emphasize the need to view our business through the eyes of our customers, anticipating and responding to their needs and providing them with the systems
that enable them to focus on their customers. The more flexibility and adaptability we can offer, the more successful they will be.
It may be cliché, but when our customers succeed, we succeed. The investments SOMIC continues to make in the United States are focused on delivering the highest quality and best performing packaging systems in the world.
Enjoy this issue of Retail Ready Magazine. We provide a glimpse of the steps we are taking to build our workforce through the ICATT Apprenticeship program, a success story of a dynamic partner of ours in the beverage industry, and the introduction of some of our key team members.
Respectfully,
Peter Fox, Chief Executive OfficerAs a company, we continue to grow in many dimensions and one key developmental area is our team. We plan to keep you updated in future issues by introducing new associates. At this time, we want you to meet two executive staff members who are driving change here at SOMIC Packaging.
Twenty five years of awardwinning service industry experience makes Brian a perfect fit as the After Sales and Service Manager. After leadership roles at Target, FedEx Office, and Batteries Plus in the Minneapolis area where he managed operations and led logistics, sales and customer service teams, he knew SOMIC was the right place during his first interview.
“The first thing I noticed during my interview was the energy and excitement. Seeing how incredible the SOMIC machine looked, I instantly saw the opportunities in front of me and knew I could make a difference.”
Brian started in mid-December 2021 and went to work on improving processes. He has since tripled parts inventory and doubled the size of SOMIC’s service and support personnel.
“Fast response times keep customers happy because it shows that a business values its customers.”
“My focus this year will be on maintenance contracts, inventory, response time, and customer feedback. As we continue to see expanded machine sales growth, the opportunities in these crucial areas will be critical to both SOMIC’s and our customer’s long term success. Selling a machine is exciting but just
the beginning. Our journey starts with the installation and moves into training and production before heading into maintenance, parts sales, and modifications. We intend to make it a great one.”
His prior experience leading multiple stores has taught him well.
“The cost of acquiring a new customer is five to 10 times more than retaining an existing one. Repeat customers spend on average 65-70% more, so keeping our customers happy is the most important metric that exists. It is not easy to define but when your focus is 100% customer centric, 100% of the time, it begins to define itself. When you are doing it right, the customer will show you in many ways.”
Brian says prioritizing a customer’s needs is essential in doing business.
“People like it when things are in stock. Here at SOMIC, if a customer wants it and needs it now, my job is to do everything possible to fulfill their request. Fast response times keep customers happy because it shows that a business values its customers. I believe it fosters loyalty and strengthens retention. My mission is to have the quickest response time in the industry, and with it the highest quality response.
“Our customers have options, and once we get a customer question or concern, my team has options. Our in-house engineers and technicians are ready to provide support. We can access our machines remotely or at the customer’s location for any level of support.
“Failure is my greatest teacher. Customers who vocalize their concerns provide an instant opportunity to improve. For other
customers, we need to ask. It’s why we recently implemented a post-service survey to gather our customers’ perceptions. We instantly gain feedback regarding wins, losses, and areas for improvement in relation to our service visits. I take customer feedback seriously, and look forward to hearing from them to help make us a stronger team.”
Brian says having a larger parts warehouse and greater capacity with the highest quality parts is for the customer’s benefit, with a diverse range of motors, belts, and other mechanical and manufactured parts.
“Service contracts provide value, not only with the initial discounted rates for service and parts we provide, but long-term. The same reason why you change your automobile’s oil with a high quality brand applies to our machines. Replacing parts that begin to show wear with the highest quality parts available avoids costly shutdowns, saves on labor costs, and ensures the highest level of efficiency within our machine. Our service contracts provide this peace of mind. With the choice of being proactive or reactive, my goal is to be there before something ever becomes a problem.”
Brian has his eye on today, tomorrow and the future.
“There are many busy times ahead and challenges we have not thought of. Our vision and mission remain the same. Every customer is the most important customer we have had the opportunity to work with. We look forward to moving into our new building and it is an exciting time for all of us. It’s amazing to look back at when we started and where we will be in a few months. The hard work and dedication to get to this point has been amazing, and it will continue.”
"Our goal is to create an environment where every employee can thrive."
Trayce Peterson, Head of Organizational Development
Trayce found her dream job when she joined SOMIC Packaging as the Head of Organizational Development in October 2023. Her role is multi-functional, a combination of strategic planning, talent management, employee development, and organizational effectiveness, while reporting to CEO Peter Fox.
She’s almost as busy during her time away from the office. In addition to being a mother and spending time with her granddaughter, Trayce returned to college almost two years ago and is working part-time on a degree in Industrial Organizational Psychology, which applies many of the same workplace principles she is implementing at SOMIC.
It’s the next stage of a successful career that has incorporated various sales, operations, customer service and leadership roles. Trayce first began working for several women’s clothing companies, later pivoting to the beauty industry for over 20 years where she developed a knack for analyzing problems, identifying root causes, and implementing effective solutions.
But it was her last position as the COO and Creative Director for a social media marketing company where she was introduced to the packaging industry.
“I met Peter Fox through a mutual friend and was attracted to SOMIC by the significant growth they are having. My experience in leadership, customer service, sales and marketing were a strong match, and I immediately knew I could make a positive impact.”
In addition to helping plan the company’s upcoming move to new and larger facilities, Trayce is tasked with finding the right individuals to hire and accommodate SOMIC’s current growth phase.
“As of mid-April, we had 40 employees and are actively working to fill an additional 20 positions, including several internships this summer. I look for hardworking, positive, happy and giving humans. When you combine their technical skillsets and specific qualities to the mix, it is a recipe for success.
“My role is a combination of strategic planning, talent management, employee deployment, and organizational effectiveness. Our goal is to create an environment where every employee can thrive, manage organizational development strategies and processes, optimize our resources and operations, and support and develop the growth and effectiveness of SOMIC."
Trayce said that as a problem solver who is relationship driven, it all comes up to people, processes and project management.
To help, she’s planning to implement an Entrepreneurial Operating System (EOS) in 2024.
“EOS is a set of tools and processes to help businesses run more efficiently and effectively. It provides a framework for defining goals, clarifying roles and responsibilities, solving problems, and improving communication within an organization. This process aims to increase accountability, streamline operations, and drive overall growth and success.”
For all service or career opportunities, contact SOMIC sales and service service@somic.us and HR@somic.us.
RETAIL READY TAKES THE NEXT
With the unveiling of the next-generation 434 system, advanced features in product sorting and alignment technology afford even greater flexibility in grouping end-of-line case, tray, and carton packing products.
FFaster changeovers than previous systems.
Cartons per minute in a single mode. Up to
Levitating CORAS carriers rotate at this level to unload or unload.
lexible and adaptable to various products ranging from food, pet food, pharmaceutical, to healthcare, and non-food industries, the SOMIC 434 packs containers in single or multiple rows. It also stacks single or multilayer products in a vertical or horizontal alignment, and gently loads them in one- and two-piece cartons, corrugated cases, wraparound, trays, or trays with covers.
SOMIC Packaging, Inc. CEO Peter Fox, says the new generation opens up new dimensions in flexibility, efficiency and ergonomics.
“Our development team has once again taken SOMIC technology to the next level. We have made exceptional progress in machine development and technology to assist customers in their secondary packaging needs.
“This next-generation system exemplifies user-friendliness and is the perfect choice for companies that need a larger format packaging solution,” continued Fox. “Just like our 424 machine, it accommodates flat sachets, stand-up flexible pouches, cans, cups, trays, jars, bottles, tubes and blister-packs.”
SOMIC designed the servo-driven 434 for a wider choice of sequencing options in the packing process. This is characterized by a compact, space-saving footprint, improved accessibility, easier cleaning and maintenance capabilities, and automatic format adjustments.
Fox indicated that based on a linear arrangement of stations — from carton-forming to closing modules — this slim machine easily fits into most filling and packaging
production lines. Depending on product size and the secondary packaging being run, plus the number of stations a customer requires, the standard footprint varies. The carton infeed, forming, product loading and closing stations are all streamlined in a neat, linear configuration.
Solidly built for years of operation, this modular mechatronic machine can be adapted to suit every functional need. Electrical cables are integrated within the sturdy frame design. The frame’s support structure was moved inside and is now made of easy-to-clean stainless steel, which suits standards in food production facilities.
The ergonomic framing also includes machine-height guard doors that open 180 degrees for unimpeded access to the machine’s exterior. The higher ceiling clearance allows an operator to easily and safely walk in and out, facilitating daily inspection, maintenance, cleaning and changeovers.
All machine functions are userfriendly and can be easily accessed. Clearly visible LED lights on the corner columns indicate the machine’s operational state, even from a distance. Instead of a single signal light on a machine frame, these corner lights make the machine even brighter on the inside and are helpful during changeovers.
All machine settings can be programmed and entered via intuitive touchscreen controls on an easy-to-use Human Machine Interface (HMI) panel. The HMI control stores all product format programs that operators can easily change to a different format when needed. A single outer cabinet
combines the programmable logic controls (PLC) and supplies for quiet operation. The supply cabinet now incorporates the adhesive granulates, which can be conveniently refilled from outside the machine.
The 434’s changeover technology is based on the SOMIC QuickChange tool-less changeover system, which includes comprehensive operating instructions and easily identifiable Change Parts, quick-changing disconnects, and locking systems. To streamline changeovers, servodriven format adjustments are now made automatically, therefore reducing manual errors that can occur.
Distributed servo motors also control the automated format adjustment of the folding tools, gluing positions, and the carton/case blank magazine, increasing precision and accuracy while eliminating the need for positioning aids.
“Line operators,” says Fox, “can dial in settings from one product or package to another automatically, on-the-fly. A customer can have as many formats as they want and the HMI control stores all productchange programs.”
Fox said the 434 also performs changeovers up to 70% faster than previous systems. Fully automatic format adjustments means there is less for the operators to be concerned with. “If operators find a system easier to use, the better the workflow and the faster and smoother the throughput. This helps machine set-up and reducing downtime.”
The machine is available with a standard lamella chain producttransfer conveyor, which gently moves the required number of products and positions them for loading onto an open tray, carton or case. As finished packages reach the discharge station, the system checks for the correct number of products per carton before the filled and neatly sealed carton is ejected as a finished package.
The revolutionary CORAS (Carrier-based Orientation Rotation Arrangement System) is a game changer for variety packs.
The 434 currently can operate at speeds up to 34 cartons per minute in a single mode, or 60 per minute in a double mode. All performances depend on the product type, arrangement, count and carton size.
Next generation product collection and grouping
SOMIC has developed a breakthrough alternative to the proven lamella chain that takes product handling to a new level.
Fox says the company listened to customers’ growing demands for packaging machines with superior flexibility and versatility, and their needs to accommodate a large array of products and secondary packaging.
“This feedback influenced the design of our new cutting-edge product collating, orienting and grouping technology for the 434 system.”
Offering nearly limitless possibilities for mixing, sorting and grouping products, the revolutionary CORAS ® (Carrier-based Orientation Rotation Arrangement System) is a game changer for variety packs. Based on contact-free, planar technology, the linear multidimensional system incorporates magnetic levitation product carriers with nearly unlimited possibilities for unrestricted mixing, sorting and product grouping.
The track-based “floating” carriers move primary products without touching anything on an electromagnetic field on which they ride. These carriers can be customized for products, negating the need for a conventional pick-andplace sorting unit. Each track can load or unload about 30 carriers per minute. The carriers do not generate dust or particles, so nothing prevents them from moving.
The carriers rotate 360 degrees along the vertical axis and can be programmed to place products in a desired order. Once the system groups products, they are transferred to the carton or case-packing station and gently handles various items. Fox says the CORAS module is integrated within a separate frame, increasing the machine’s flexibility when changing packaging configurations.
“Linear servo track systems have come into view in highly automated packaging applications. Our pioneering CORAS system completes product sorting and grouping tasks quickly,” he said. “This is done in any configuration in a fraction of the space required by standard pick-andplace units. The product grouping options are nearly endless.”
While it can often be difficult for most product handling devices
to rearrange and reorient mixed product formats in multiple configurations simultaneously, this is where the CORAS system excels.
It may be difficult but picture in your mind multiple product in-feeds delivering bags of different flavors of potato chips to a cartoner or case packer. Now imagine they are mixed variety packs and they are being sent as very different frequencies; one in-feed might be extra fast and another could be very slow.
The 434 CORAS module can arrange the bags in different patterns via the levitating carriers, which can change the orientation of different stacks of bags inside the secondary cases without using robotic pick-and-place systems. All 434 systems are built for flexibility and upgraded as needed. Our experienced technicians will help with installation, training and ongoing technical support, making this machine a wise choice for meeting the challenges of today and in the future.
Adaptable for various packaging configurations:
• Single/multi-row grouping and multi-layer stacking
• Format adjustments up to 70% faster
• Compact ergonomic footprint
• Side-mounting grouping unit for straight line case and tray packing/cartooning
• Machine-height safety doors with improved accessibility
• Stainless steel frame with integrated electrical installation
• LED corner lighting for enhanced visibility
Powerful collecting, grouping and mixing of products:
• Contact-free magnetic levitation for product mixing and unlimited grouping options
• Low maintenance and wear-free gentle product handling
• High performance with maximum flexibility
• Space-saving solution for buffering, mixing products and line merging
• Energy efficient operation without compressed air and vacuum
Aself-described serial entrepreneur, Carolyn Hardy is known as one of the top business executives in Memphis. Deeply engaged in her community with years of packaging leadership and success, she has set ambitious goals this year for her family-operated, hydrogen-infused water bottling company.
One astute determination she made was realizing the marketplace changed and is more consumerdriven after the COVID-19 pandemic. By switching from hand packing product to installing an automated SOMIC Packaging 424 wraparound case packer two years ago, Hardy Beverages now has the flexibility to meet unique challenges while growing the business.
“Carolyn is very knowledgeable and her experience in the beverage world is impressive. She is an accomplished professional who has earned the respect of her peers and the Memphis business community,” acknowledged Peter Fox, SOMIC Packaging’s CEO.
“She was very thorough in her equipment analysis and requirements. Her compact machine allows them to make the most of their floor space, and it can be adapted for any purpose.”
A true pillar in the Memphis business community
Hardy had to overcome hard times when she was young. The seventh in a family of 16 children, it shaped who she would become and achieve a wealth of success stories.
“My family was evicted more times than I can remember,” she recalled. “We were impacted by poverty, our house burned down while I was in elementary school, and I saw a family member die due to a lack of access to healthcare.”
Education helped fuel her passion. Hardy’s packaging experience began over 30 years ago when she joined the J.M. Smucker Co. in Memphis after earning her MBA from the University of Memphis. She later left her plant manager position for a bigger opportunity at Coors Brewing Company.
In 2005 when she was the Coors VP of Operations, leadership in Colorado informed her of their decision to shut down the Memphis facility the next year. In an effort to keep her team motivated, she and her team devised a strategy and
won Coors’ Environmental Health & Safety Award as the company’s most efficient facility that year.
Due to the merger with Molson Canada, Coors still sold the facility to Hardy. It allowed her to keep the plant open and save over 400 jobs. More success would follow.
She started Hardy Bottling in 2006, producing non-alcoholic beverages for companies such as AriZona Beverages, Coca-Cola and 7-Eleven Select. They also handled energy and organic products for Rockstar, FRS, Cintron, Apple & Eve and others. The facility and assets were sold for $30 million in 2011 to City Brewery of Lacrosse, Wis.
Hardy has since expanded her entrepreneurial interests. In addition to owning Henderson Transloading Services — an agri-logistics intrastate freight company — she is a public speaker and the author of three books . She supports many non-profit boards and is currently Chairman of the Eighth District Federal Reserve.
“Over the years I learned the business opportunity must be properly capitalized to survive, prosper and grow nationally. The economy is fluid and unpredictable as demonstrated by COVID, when a lack of access to capital caused many businesses to fold,” she observed.
“Quality, customer service and cost does not guarantee success but are critical factors. Being the best only gets you to first base. For a service or product to score requires developing and leveraging relationships. Business owners must speak up for what they want and need.”
Carolyn Hardy along with the SOMIC 424 case-packer that was installed in late 2022 and runs four brand products.As CEO of Hardy Beverages, she is turning those beliefs into action. One of her main goals is to create positive change and expand the Minority Business Enterprise and Women Business Enterprise presence in manufacturing and retail.
“I have worked at different companies for many years and been an advocate for the underserved my entire career,” said Hardy. Her husband, Marino, is the managing partner who runs operations at Hardy Beverages. Jeff Lightfoot, a former Coca-Cola manager, is the operating manager, and her sister, Doris Hardiman, is the operations coordinator.
Her experience and commitment to the community impacted the decision where to house Hardy Beverages in Memphis, regarded as the biggest distribution center in the United States. The 30,000 square-foot company building is located about seven miles east of Memphis International Airport, the second busiest cargo airport in the world and home to FedEx world headquarters.
There is also accessibility via the nearby Port of Memphis on the Mississippi River, and Interstates 40 and 55 ensure nationwide mobility for trucking companies. All told, her family of companies has invested over $15 million in the Hickory Hill community with hopes of revitalizing the area.
“This community has approximately 15% unemployment while the national unemployment rate is 3.8%,” she says. “Like many communities in the U.S., it needs manufacturing to lift people. I love being a role model for women and minority businesses in areas that are traditionally underrepresented. What better location can there be than being in the middle of a major need?”
Automated packaging to meet today’s challenges
Hardy learned of SOMIC Packaging in 2020 when her filler manufacturer from Germany introduced them.
“I have worked with many packer brands and wanted to avoid the problems I’ve experienced with them
in the past.I was initially concerned with equipment built outside the U.S. due to a lack of parts availability and service,” she indicated. “When we did site visits to observe the machine in operation, we learned SOMIC has a dedicated team of service technicians here in the States. I felt confident they not only had a superior case-packing system, but a technical team to support us.”
The SOMIC 424 case packer was installed in October 2022 and Hardy immediately began running the machine.
“Before installing the SOMIC packer, we could only pack 100 units-perminute (UPM) because we could not source enough temporary labor to hand pack at the filler’s capability,” she acknowledged. “Our filler is capable of over 180 UPMs, and this year we plan to run a ten hour shift, three days a week. As we reach our sales goals, I anticipate adding more shifts.”
The company has a state-of-the-art proprietary beverage process that allows them to produce hydrogen infused products. Flagship brand HTWO is a ready-to-drink beverage with unique aluminum packaging. It not only holds hydrogen gas longer but contains no microplastics and is BPA-free.
Nightlyfe contains electrolytes to help performers and the latenight crowd to recover faster. Skhy combines hydrogen and CBD with vitamins and minerals for mental and physical well-being. And Rallie is an enhanced water solution exclusively for dogs.
Hardy says her SOMIC 424 case packer provides advantages for today and the future.
“I’m very satisfied with the flexibility of our machine. We can produce many different package types in the 6, 12, 18 and 24-pack range,” she revealed about the 16.9 ounce bottles. “I also like its ease of operation and having the ability to source parts and receive technical support quickly when needed.”
Hardy tested those abilities last year and SOMIC passed with flying colors.
“Memphis is very humid in the summertime and last year was no different,” she recalled. “The trays tend to warp, especially if the bands in place are too tight. I called SOMIC and they recommended adding an extension roll-down arm to keep things in check. They did and we were able to reduce our reject rate by 90%.”
This summer, the ambitious forecast she planned hopefully means adding more workers to keep up with demand.
“In the first two years of operation, Hardy Beverages expanded from one brand to three and from two SKUs to 18. In 2023 we presented our flagship brand, HTWO, to every retail sector in the U.S. and reached out to international prospects,” she said.
“This year, HTWO will extend sales to U.S. retailers in mass retail, pharmacies and hardware stores. We have begun international sales starting in Kuwait and plan to increase sales by 100% year-overyear for the next five years through strategic marketing programs and promotions.”
Training and development through SOMIC’s ICATT Apprenticeship Program plays a central role in its engineers’ successful careers. A collaborative approach and a passion for high technology and flawless innovation are vital factors in the program's benefits to the company’s customers and local community.
For high-tech equipment manufacturers and businesses involved with complex technologies and logistics, finding the right talent can not only be overwhelming but incredibly arduous. SOMIC Packaging is striving to bridge the skills gap, facilitating the development of well-rounded technical professionals who become invaluable technicians in the field for in-house installations, and great assets to the workforce of the future.
Since late 2022, SOMIC offers apprenticeships through the Industry Consortium for Advanced Technical Training or ICATT program, which
is focused exclusively on hightech manufacturers and complex business administration processes.
The ICATT Apprenticeship Program is the only one in the Midwest fully benchmarked on the German Dual Education System of vocational training, a time-tested program that combines company-specific knowledge, theory, and handson learning to train a globally competitive workforce.
The ICATT Apprenticeship Program was created by the German American Chamber of Commerce in Chicago and its member companies. Open to any company that wishes to develop their own skilled workforce, the program offers apprentices the opportunity to earn while they learn and build a career path for the long term. A sustainable solution that provides a pipeline of talent over time, SOMIC’s program provides a fair living wage, a debt-free associate degree, and an industry-aligned education.
SOMIC’s three-year apprenticeship educational model integrates college coursework and on-the-job training. It is based on the broader ICATT framework, which offers 21 distinct fields in total, and is open to high school graduates and individuals who earned their GED.
SOMIC’s version combines companyspecific knowledge, theory, and real-world instruction with a concentration of mechatronics. A valuable resource for today's fastevolving technological landscape, the program's structured approach allows students to gain an industryaligned education with hands-on training and guidance in high-tech fields. The immediate result is having professionals with in-demand skills for the packaging industry.
Peter Fox, SOMIC Packaging’s CEO, says the program is another example of how the company maintains partnership-based, long-term relationships with its employees, suppliers, and customers.
“This collaborative approach helps us create sustainable partnerships. Our passion for high technology and
flawless innovation combines with our focus on people,” said Fox.
“We develop highly qualified technicians who meet the specific needs of the fast-growing packaging industry. Along with technical training, they are educated in the essential knowledge like submitting weekly reports detailing their activities. This helps to build their soft skillsets such as communication and accountability expertise, and sets the foundation for professional success. Technology is extremely important today. Technicians who are equipped with knowledge of the tools, processes, and devices essential in various fields of engineering will always be important.”
Real-world experiences form a cornerstone of the SOMIC program. Two days a week, SOMIC’s apprentices take classes at Hennepin County Technical College in nearby Brooklyn Park. The other three days, they receive practical training at SOMIC’s facility, which is equipped with cutting-edge technology and provides the students with a dynamic learning environment.
Apprentices also receive a consistent, competitive hourly wage throughout their studies, along with an attractive benefits package. They undertake a variety of projects that test their skills in areas such as metal filing, measurement techniques, and blueprint reading.
The training goes beyond the acquisition of industry-specific certifications. Upon successful completion, every apprentice earns a debt-free Associate degree, a journeyman card in mechatronics, and a tailored knowledge about the packaging industry. Apprentices are also guaranteed one year of employment with SOMIC, setting the stage for a promising career.
Dr. Tim Blaeser, who joined SOMIC as the ICATT program training and development leader in March 2023, said applicants undergo an interview process where the candidates with the highest potential are selected. After graduation, SOMIC offers them the possibility to absolve an
internship where they participate in basic tasks that enable an assessment regarding their suitability for the program and the team. Those selected for the program begin their apprenticeship journey the following Fall at school, which they must attend regularly and produce the requisite products for class.
“Our teaching strategies are akin to a "Crawl, Walk, Run" tiered progression method, and often employed to gradually but solidly build the apprentices’ expertise,” explained Dr. Blaeser, an engineer with over 30 years of experience in control systems, PLCs, and drives.
“Currently, the program is involved in mechatronics. The apprentices train with our new field service technicians from the ground up. The first weeks at SOMIC and school are quite different, but the apprentices are kept busy. We choose their curricula for ICATT. SOMIC strives to add ‘real-world realism’ to the curricula, so for example, when the apprentices take metal shop they learn how to use high-speed mills and lathes to make objects like a vise. After they complete the mechanical portion of the program, they progress to a pneumatic block of instruction, followed by an electrical section of study.”
Through the tiered progression, the beginners gain both confidence and competence, preparing them for their first ICATT test where they demonstrate their newly acquired skills and functionalities. They receive a robust framework of information that helps companies build a sustainable workforce.
As they navigate real-world scenarios, the students are coached and supported with everything from academic advice to emotional reinforcement, homework assistance, project discussions, and how to deal with intricate administrative and logistical operations as they learn and grow. Blaeser said it is very gratifying to see when all the instruction clicks.
Upon full-time employment, the apprentices have opportunities to explore various branches of engineering at SOMIC.
“SOMIC is committed to ensuring our apprentices' academic and professional success,” says Fox. “Not only do the apprentices grow and find a career path suited to them, but our company grows as well. By attracting individuals who soon will start to love mechatronics, robotics, and other complex machinery technologies, they will emerge from a platform that develops their unique skills and furthers their careers. It’s very gratifying to see their enthusiasm and eagerness.”
The apprenticeship program has already yielded tangible results for SOMIC with the addition of two new employees. This summer, Fox says the goal is to bring in five more apprentices.
“One of the program's most rewarding aspects is the chance to shape these young talents into future leaders of field service technicians,” he stated. “We look forward to annual graduation ceremonies, welcoming a new set of fully trained SOMIC technicians and signifying the program’s sustained growth and success.”
When U.S. headquarters move to a larger facility a few miles from its current location this summer, Fox indicated the new workspace will have a dedicated classroom and training lab, and include additional equipment to accommodate an increasing number of ICATT apprentices. The expectation is to add more apprentices each year for the foreseeable future.
“The ICATT program at SOMIC has been quite successful, both for us and the apprentices here in the United States, summed up Fox. “More importantly, the ICATT approach to skill development, workforce readiness, and long-term career advancement is a level playing field and gives local people a leg up on employment. The programs support the creation and expansion of highquality apprenticeship pathways and related technical education here in the U.S.”
More information on the SOMIC ICATT program is available by scanning the QR Code.
Make rapidly changing markets your time of growth.
You can’t fully predict the future, but you can be fully prepared to adapt and thrive in the shifting market. You can customize individual units and achieve format changeovers up to 70% faster with the SOMIC 434. It is helping companies in a variety of industries meet rapidly changing demands with Retail Ready packaging. Choose between two technologies for product grouping - the SOMIC Lamella Chain or the new SOMIC CORAS magnetic planar technology. Visit our website to learn more about the groundbreaking SOMIC CORAS multi-dimensionally controllable magnetic levitation technology.
Learn how the SOMIC 434 offers future-proof flexibility. Call 651.419.6050 or visit somic.us. See SOMIC in action at PACK EXPO Chicago, #N-6148.